氰化提金工艺
氰化提金工艺及污水处理
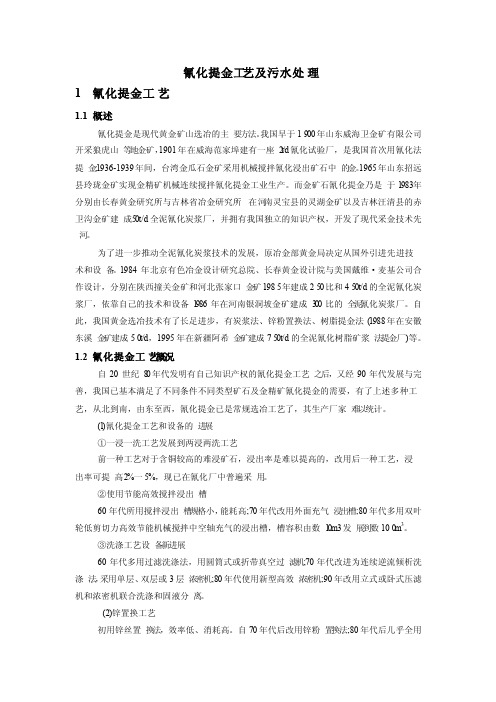
氰化提金工艺及污水处理1 氰化提金工艺1.1 概述氰化提金是现代黄金矿山选冶的主要方法。
我国早于1900年山东威海卫金矿有限公司开采狼虎山等地金矿,1901年在威海范家埠建有一座2t/d氰化试验厂,是我国首次用氰化法提金;1936-1939年间,台湾金瓜石金矿采用机械搅拌氰化浸出矿石中的金。
1965年山东招远县玲珑金矿实现金精矿机械连续搅拌氰化提金工业生产。
而金矿石氰化提金乃是于1983年分别由长春黄金研究所与吉林省冶金研究所在河南灵宝县的灵湖金矿以及吉林汪清县的赤卫沟金矿建成50t/d全泥氰化炭浆厂,并拥有我国独立的知识产权,开发了现代采金技术先河。
为了进一步推动全泥氰化炭浆技术的发展,原冶金部黄金局决定从国外引进先进技术和设备。
1984年北京有色冶金设计研究总院、长春黄金设计院与美国戴维·麦基公司合作设计,分别在陕西撞关金矿和河北张家口金矿1985年建成250比和450t/d的全泥氰化炭浆厂,依靠自己的技术和设备1986年在河南银洞坡金矿建成300比的全泥氰化炭浆厂。
自此,我国黄金选冶技术有了长足进步,有炭浆法、锌粉置换法、树脂提金法(1988年在安徽东溪金矿建成50t/d,1995年在新疆阿希金矿建成750t/d的全泥氰化树脂矿浆法提金厂)等。
1.2 氰化提金工艺概况自20世纪80年代发明有自己知识产权的氰化提金工艺之后,又经90年代发展与完善,我国已基本满足了不同条件不同类型矿石及金精矿氰化提金的需要,有了上述多种工艺,从北到南,由东至西,氰化提金已是常规选冶工艺了,其生产厂家难以统计。
(l)氰化提金工艺和设备的进展①一浸一洗工艺发展到两浸两洗工艺前一种工艺对于含铜较高的难浸矿石,浸出率是难以提高的,改用后一种工艺,浸出率可提高2%一5%,现已在氰化厂中普遍采用。
全泥氰化提金工艺简介.
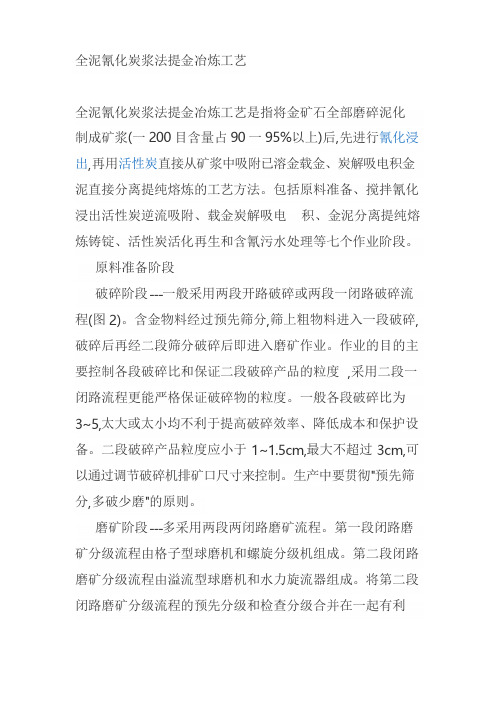
全泥氰化炭浆法提金冶炼工艺全泥氰化炭浆法提金冶炼工艺是指将金矿石全部磨碎泥化制成矿浆(一200目含量占90一95%以上)后,先进行氰化浸出,再用活性炭直接从矿浆中吸附已溶金载金、炭解吸电积金泥直接分离提纯熔炼的工艺方法。
包括原料准备、搅拌氰化浸出活性炭逆流吸附、载金炭解吸电积、金泥分离提纯熔炼铸锭、活性炭活化再生和含氰污水处理等七个作业阶段。
原料准备阶段破碎阶段---一般采用两段开路破碎或两段一闭路破碎流程(图2)。
含金物料经过预先筛分,筛上粗物料进入一段破碎,破碎后再经二段筛分破碎后即进入磨矿作业。
作业的目的主要控制各段破碎比和保证二段破碎产品的粒度,采用二段一闭路流程更能严格保证破碎物的粒度。
一般各段破碎比为3~5,太大或太小均不利于提高破碎效率、降低成本和保护设备。
二段破碎产品粒度应小于1~1.5cm,最大不超过3cm,可以通过调节破碎机排矿口尺寸来控制。
生产中要贯彻"预先筛分,多破少磨"的原则。
磨矿阶段---多采用两段两闭路磨矿流程。
第一段闭路磨矿分级流程由格子型球磨机和螺旋分级机组成。
第二段闭路磨矿分级流程由溢流型球磨机和水力旋流器组成。
将第二段闭路磨矿分级流程的预先分级和检查分级合并在一起有利于提高磨矿效率和保证产品细度。
破碎好的含金物料经过第一段闭路磨矿分级流程后,矿浆中一200目含量为55%一65%。
再经过第二段闭路磨矿分级流程后矿浆中一200目物料含量就可达90%一95%以上,符合全泥氰化工艺的细度要求。
本段作业主要控制磨矿浓度、溢流浓度和溢流细度。
一般磨矿浓度:第一段为75%一80%,第二段为60%~65%;溢流浓度:第一段为25%~30%,第二段为14%一20%;溢流细度(一200目含量):第一段为55%~65%,第二段为90写一95%以上。
磨矿浓度的控制主要通过调节给水量、给矿量和返砂比等,若磨矿浓度偏高,则增加给水量、减少给图3两段两闭路磨矿流程矿量,增大返砂比等,反之亦然。
黄金矿石氰化工艺流程

黄金矿石氰化工艺流程
黄金矿石氰化工艺是一种常用的黄金提取方法,通常包括以下几个步骤:
1. 破碎和磨矿:将黄金矿石经过破碎和磨矿处理,使其细碎成适当的颗粒大小,便于后续的处理。
2. 浸矿:将磨碎的矿石放入浸矿槽(也称为浸矿池或浸没槽),并加入含有氰化物的溶液。
常用的氰化物是氰化钠(NaCN)。
3. 溶液搅拌:通过搅拌设备,使氰化物溶液与矿石充分接触,以促进黄金的溶解。
4. 氧化:为了加速黄金的氧化反应,可以向氰化槽中通入空气或氧气。
氧化有助于黄金的氧化还原反应,使黄金溶解速度增加。
5. 吸附:在溶液中,黄金以氰化物配合物(如Au(CN)2-)的形式存在。
为了将黄金从溶液中分离出来,使用活性炭吸附剂,将黄金配合物吸附到活性炭上。
6. 脱附:经过一段时间的吸附,活性炭上富集了大量的黄金。
然后,通过脱附过程,将黄金从活性炭上解吸下来。
通常使用热碱溶液(如氢氧化钠)或其他脱附剂进行脱附。
7. 脱氰:脱附后得到含有黄金的溶液,其中还含有氰化物。
为了回收氰化物,需要对溶液进行脱氰处理。
常用的方法是将溶液经过多级氧化处理,将氰化物转化为无害的氰酸盐。
8. 沉淀和纯化:经过脱氰处理后,得到的黄金溶液中含有金离子。
通过加入沉淀剂(如二硫化钠、水合硫酸亚铁等),使金离子还
原成金属黄金沉淀出来。
然后,对沉淀的黄金进行洗涤、过滤、干燥等工艺步骤,以得到纯净的黄金产品。
需要注意的是,黄金矿石氰化工艺涉及到氰化物的使用,氰化物具有一定的毒性,操作时需要严格控制环境和工艺条件,确保操作安全。
提金技术工艺大全(专利)
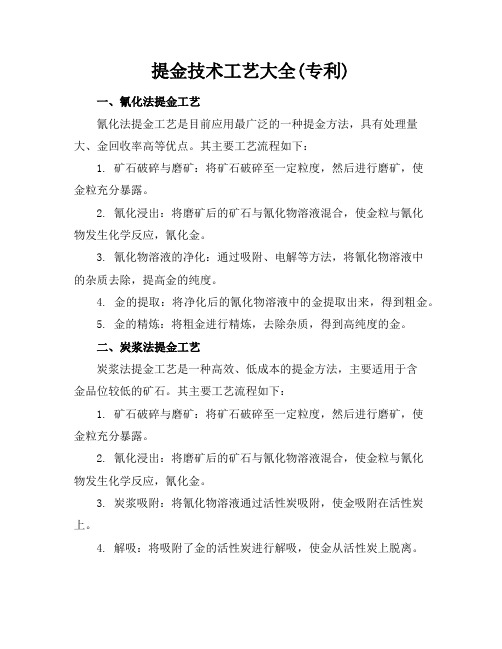
提金技术工艺大全(专利)一、氰化法提金工艺氰化法提金工艺是目前应用最广泛的一种提金方法,具有处理量大、金回收率高等优点。
其主要工艺流程如下:1. 矿石破碎与磨矿:将矿石破碎至一定粒度,然后进行磨矿,使金粒充分暴露。
2. 氰化浸出:将磨矿后的矿石与氰化物溶液混合,使金粒与氰化物发生化学反应,氰化金。
3. 氰化物溶液的净化:通过吸附、电解等方法,将氰化物溶液中的杂质去除,提高金的纯度。
4. 金的提取:将净化后的氰化物溶液中的金提取出来,得到粗金。
5. 金的精炼:将粗金进行精炼,去除杂质,得到高纯度的金。
二、炭浆法提金工艺炭浆法提金工艺是一种高效、低成本的提金方法,主要适用于含金品位较低的矿石。
其主要工艺流程如下:1. 矿石破碎与磨矿:将矿石破碎至一定粒度,然后进行磨矿,使金粒充分暴露。
2. 氰化浸出:将磨矿后的矿石与氰化物溶液混合,使金粒与氰化物发生化学反应,氰化金。
3. 炭浆吸附:将氰化物溶液通过活性炭吸附,使金吸附在活性炭上。
4. 解吸:将吸附了金的活性炭进行解吸,使金从活性炭上脱离。
5. 金的精炼:将解吸后的金进行精炼,去除杂质,得到高纯度的金。
三、树脂法提金工艺树脂法提金工艺是一种新型、高效的提金方法,具有处理量大、金回收率高等优点。
其主要工艺流程如下:1. 矿石破碎与磨矿:将矿石破碎至一定粒度,然后进行磨矿,使金粒充分暴露。
2. 氰化浸出:将磨矿后的矿石与氰化物溶液混合,使金粒与氰化物发生化学反应,氰化金。
3. 树脂吸附:将氰化物溶液通过树脂吸附,使金吸附在树脂上。
4. 解吸:将吸附了金的树脂进行解吸,使金从树脂上脱离。
5. 金的精炼:将解吸后的金进行精炼,去除杂质,得到高纯度的金。
四、生物法提金工艺生物法提金工艺是一种环保、低成本的提金方法,主要适用于含金品位较低的矿石。
其主要工艺流程如下:1. 矿石破碎与磨矿:将矿石破碎至一定粒度,然后进行磨矿,使金粒充分暴露。
2. 生物氧化:将磨矿后的矿石与生物氧化剂混合,使金粒与氧化剂发生反应,可溶性金。
几种氰化法提金介绍

1.氰化法提金概述氰化法提金是以氰化物的水溶液作溶剂,浸出含金矿石中的金,然后再从含金浸出液中提取金的方法。
氰化法提金主要包括如下两个步骤:(1)氰化浸出:在稀薄的氰化溶液中,并有氧(或氧化剂)存在的条件下,含金矿石中的金与氰化物反应生成一价金的络合物而溶解进入溶液中,得到浸出液以氰化钾为例,反应式为:4Au+8KCN+2H2O→4KAu(CN)2+4KOH氰化浸出金的工艺方法有槽浸氰化法和堆浸氰化法两类。
槽浸氰化法是传统的浸金方法,又分渗滤氰化法和搅拌氰化法两种;堆浸法是近20年来才出现的新技术,主要用于处理低品位氧化矿。
自1887发现氰化液可以溶金以来,氰化法浸出至今已有近百年的生产实践,工艺比较成熟,回收率高,对矿石适应性强,能就地产金,所以至今仍是黄金浸出生产的主要方法。
(2)沉积提金:从氰化浸出液中提取金。
工艺方法有加锌置换法(锌丝置换法和锌粉置换法)、活性炭吸附法(炭浆法CIP和炭浸法CIL)、离子交换树脂法(树脂矿浆法RIP和RIL)、电解沉积法、磁炭法等。
锌粉(丝)置换法是较为传统的提金方法,在黄金矿山应用较多;炭浆法是目前新建金矿的首选方法,其产金量占世界产金量的50%以上;其余方法在黄金矿山也正日渐得到应用。
2.渗滤氰化法渗滤氰化法是氰化浸出的工艺方法之一,是基于氰化溶液渗透通过矿石层而使含金矿石中的金浸出的方法,适用于砂矿和疏松多孔物料。
渗滤氰化法的主要设备是渗滤浸出槽。
渗滤浸出槽通常为木槽、铁槽或水泥槽。
槽底水平或稍倾斜,呈圆形、长方形或正方形。
槽的直径或边长一般为5~12米,高度一般为2~米,容积一般为50~150吨。
渗滤氰化法的工艺过程:(1)装入矿砂及碱:要求布料均匀,粒度一致,疏松一致。
有干法和湿法两种装法。
干法适于水分在20%以下的矿砂,可用人工或机械装矿。
湿法是将矿浆用水稀释后,用砂泵扬送或沿槽自流入槽内。
(2)渗滤浸出:装料完毕后即可把氰化液送入槽中。
氰化液在槽中的流向有两种:一种是上进下出。
几种氰化法提金介绍备课讲稿
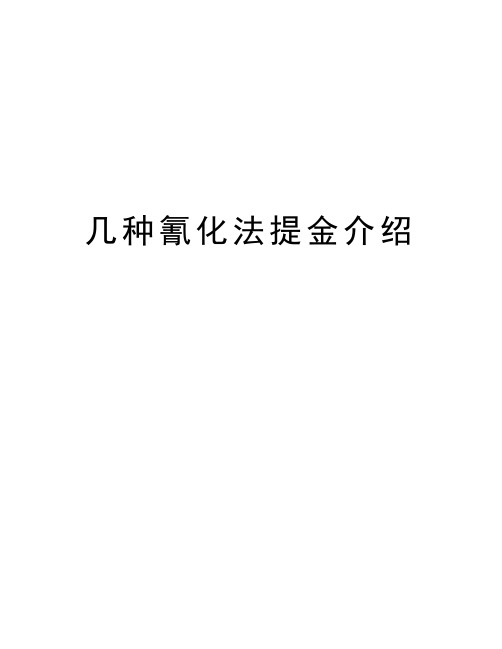
几种氰化法提金介绍2016-12-06 廖德华紫金矿业HOT全球矿业资讯1.氰化法提金概述氰化法提金是以氰化物的水溶液作溶剂,浸出含金矿石中的金,然后再从含金浸出液中提取金的方法。
氰化法提金主要包括如下两个步骤:(1)氰化浸出:在稀薄的氰化溶液中,并有氧(或氧化剂)存在的条件下,含金矿石中的金与氰化物反应生成一价金的络合物而溶解进入溶液中,得到浸出液以氰化钾为例,反应式为:4Au+8KCN+2H2O→4KAu(CN)2+4KOH氰化浸出金的工艺方法有槽浸氰化法和堆浸氰化法两类。
槽浸氰化法是传统的浸金方法,又分渗滤氰化法和搅拌氰化法两种;堆浸法是近20年来才出现的新技术,主要用于处理低品位氧化矿。
自1887发现氰化液可以溶金以来,氰化法浸出至今已有近百年的生产实践,工艺比较成熟,回收率高,对矿石适应性强,能就地产金,所以至今仍是黄金浸出生产的主要方法。
(2)沉积提金:从氰化浸出液中提取金。
工艺方法有加锌置换法(锌丝置换法和锌粉置换法)、活性炭吸附法(炭浆法CIP和炭浸法CIL)、离子交换树脂法(树脂矿浆法RIP和RIL)、电解沉积法、磁炭法等。
锌粉(丝)置换法是较为传统的提金方法,在黄金矿山应用较多;炭浆法是目前新建金矿的首选方法,其产金量占世界产金量的50%以上;其余方法在黄金矿山也正日渐得到应用。
2.渗滤氰化法渗滤氰化法是氰化浸出的工艺方法之一,是基于氰化溶液渗透通过矿石层而使含金矿石中的金浸出的方法,适用于砂矿和疏松多孔物料。
渗滤氰化法的主要设备是渗滤浸出槽。
渗滤浸出槽通常为木槽、铁槽或水泥槽。
槽底水平或稍倾斜,呈圆形、长方形或正方形。
槽的直径或边长一般为5~12米,高度一般为2~2.5米,容积一般为50~150吨。
渗滤氰化法的工艺过程:(1)装入矿砂及碱:要求布料均匀,粒度一致,疏松一致。
有干法和湿法两种装法。
干法适于水分在20%以下的矿砂,可用人工或机械装矿。
湿法是将矿浆用水稀释后,用砂泵扬送或沿槽自流入槽内。
几种氰化法提金介绍
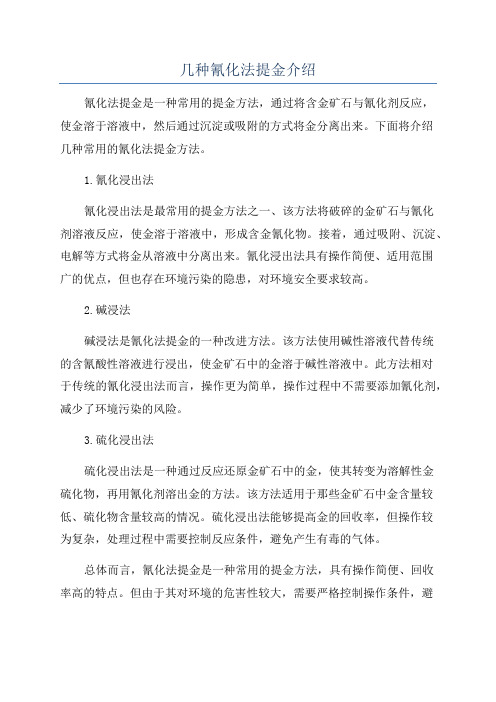
几种氰化法提金介绍
氰化法提金是一种常用的提金方法,通过将含金矿石与氰化剂反应,
使金溶于溶液中,然后通过沉淀或吸附的方式将金分离出来。
下面将介绍
几种常用的氰化法提金方法。
1.氰化浸出法
氰化浸出法是最常用的提金方法之一、该方法将破碎的金矿石与氰化
剂溶液反应,使金溶于溶液中,形成含金氰化物。
接着,通过吸附、沉淀、电解等方式将金从溶液中分离出来。
氰化浸出法具有操作简便、适用范围
广的优点,但也存在环境污染的隐患,对环境安全要求较高。
2.碱浸法
碱浸法是氰化法提金的一种改进方法。
该方法使用碱性溶液代替传统
的含氰酸性溶液进行浸出,使金矿石中的金溶于碱性溶液中。
此方法相对
于传统的氰化浸出法而言,操作更为简单,操作过程中不需要添加氰化剂,减少了环境污染的风险。
3.硫化浸出法
硫化浸出法是一种通过反应还原金矿石中的金,使其转变为溶解性金
硫化物,再用氰化剂溶出金的方法。
该方法适用于那些金矿石中金含量较低、硫化物含量较高的情况。
硫化浸出法能够提高金的回收率,但操作较
为复杂,处理过程中需要控制反应条件,避免产生有毒的气体。
总体而言,氰化法提金是一种常用的提金方法,具有操作简便、回收
率高的特点。
但由于其对环境的危害性较大,需要严格控制操作条件,避
免对生态环境造成污染。
在实际应用中,还可以结合其他方法,如浮选、压磨等,来提高金的提取率和回收率,降低环境风险。
氰化法提金工艺
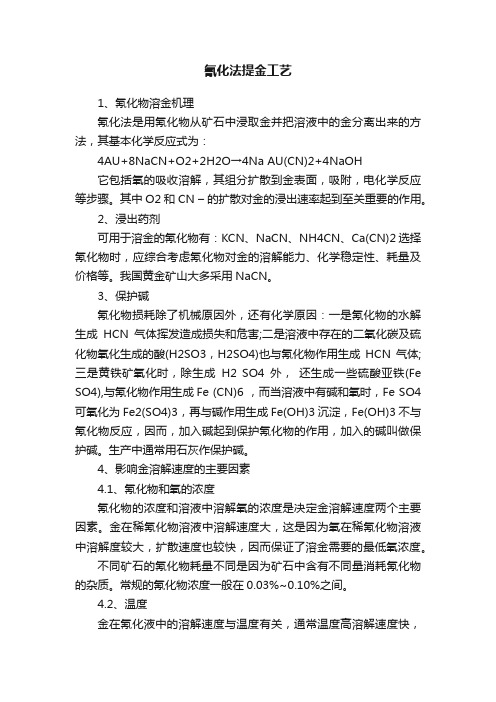
氰化法提金工艺1、氰化物溶金机理氰化法是用氰化物从矿石中浸取金并把溶液中的金分离出来的方法,其基本化学反应式为:4AU+8NaCN+O2+2H2O→4Na AU(CN)2+4NaOH它包括氧的吸收溶解,其组分扩散到金表面,吸附,电化学反应等步骤。
其中O2和CN –的扩散对金的浸出速率起到至关重要的作用。
2、浸出药剂可用于溶金的氰化物有:KCN、NaCN、NH4CN、Ca(CN)2选择氰化物时,应综合考虑氰化物对金的溶解能力、化学稳定性、耗量及价格等。
我国黄金矿山大多采用NaCN。
3、保护碱氰化物损耗除了机械原因外,还有化学原因:一是氰化物的水解生成HCN气体挥发造成损失和危害;二是溶液中存在的二氧化碳及硫化物氧化生成的酸(H2SO3,H2SO4)也与氰化物作用生成HCN气体;三是黄铁矿氧化时,除生成H2 SO4外,还生成一些硫酸亚铁(Fe SO4),与氰化物作用生成Fe (CN)6 ,而当溶液中有碱和氧时,Fe SO4可氧化为Fe2(SO4)3,再与碱作用生成Fe(OH)3沉淀,Fe(OH)3不与氰化物反应,因而,加入碱起到保护氰化物的作用,加入的碱叫做保护碱。
生产中通常用石灰作保护碱。
4、影响金溶解速度的主要因素4.1、氰化物和氧的浓度氰化物的浓度和溶液中溶解氧的浓度是决定金溶解速度两个主要因素。
金在稀氰化物溶液中溶解速度大,这是因为氧在稀氰化物溶液中溶解度较大,扩散速度也较快,因而保证了溶金需要的最低氧浓度。
不同矿石的氰化物耗量不同是因为矿石中含有不同量消耗氰化物的杂质。
常规的氰化物浓度一般在0.03%~0.10%之间。
4.2、温度金在氰化液中的溶解速度与温度有关,通常温度高溶解速度快,在无特殊工艺要求的条件下,使矿浆温度维持在150C~250C即可满足浸出的要求。
4.3、金粒的大小和形状金的溶解速度与金粒暴露的表面积成正比,因此氰化作业的磨矿粒度要比浮选更细一些。
4.4、矿浆浓度和矿泥矿浆浓度和矿泥含量直接影响溶剂的扩散速度和溶剂与金粒的接触。
全泥氰化提金工艺设计与生产实践

全泥氰化提金工艺设计与生产实践一、工艺流程设计泥氰化提金工艺是一种常用的金属提取工艺,主要用于提取含金废物中的金属成分。
下面是一个典型的泥氰化提金工艺流程设计:1.前处理:将含金废物进行粉碎与破碎,使其颗粒大小均匀,并去除其中的杂质和有机物。
2.浸泡:将经过前处理的含金废物浸入氰化溶液中,进行化学反应。
反应时间根据废物的性质和废物含金量而定,一般为24小时至72小时。
3.沉淀:将反应后的溶液经过沉淀处理,使其中的金属成分沉淀下来。
4.过滤:将沉淀后的溶液进行过滤,去除其中的固体杂质。
5.再溶解:将过滤后的固体沉淀添加到盐酸等溶液中进行再溶解,使其中的金属成分溶解于溶液中。
6.萃取:将再溶解后的溶液进行萃取处理,利用有机溶剂提取其中的金属成分。
萃取条件为温度控制在50-70摄氏度,时间控制在2-4小时。
7.还原:将经过萃取的有机溶剂中的金属成分进行还原处理,得到金属纯度较高的金属产品。
8.精炼:将还原后的金属产品进行精炼处理,提高其纯度。
以上是一个典型的泥氰化提金工艺流程设计,根据实际情况,工艺流程中的各个环节还可以进行调整,以提高提金效率和产品的纯度。
二、生产实践在实际生产过程中,需要注意以下几个方面:1.设备选择:根据生产规模和工艺流程要求,选择合适的设备,如破碎机、浸泡槽、沉淀槽、过滤设备、萃取塔等。
设备选择要考虑生产效率、产品质量、安全性和经济性等因素。
2.溶液控制:泥氰化提金工艺中的浸泡和萃取环节涉及到溶液控制,需要严格控制溶液的温度、浓度、pH值等参数,以提高金属提取率和产品纯度。
3.杂质处理:在泥氰化提金过程中,含金废物中通常会存在一些杂质,如铜、银、铅等,需要根据具体情况采取相应的处理方法,如溶解、沉淀、萃取等,以提高产品的纯度。
4.安全保护:在泥氰化提金生产中,由于涉及到氰化物的使用,需要加强安全保护工作,严格遵守操作规程,提供足够的通风和防护设施,确保操作人员和环境的安全。
5.产品质量检测:在生产过程中,需要对产品的质量进行检测,包括金属纯度、杂质含量、产品外观等指标的检测,以确保产品符合质量要求。
【河南黄金研究院】从氰化浸出液中提金的方法有哪些?
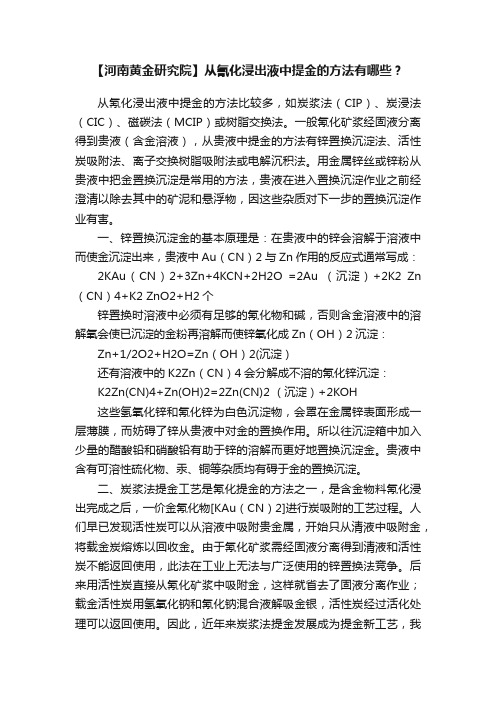
【河南黄金研究院】从氰化浸出液中提金的方法有哪些?从氰化浸出液中提金的方法比较多,如炭浆法(CIP)、炭浸法(CIC)、磁碳法(MCIP)或树脂交换法。
一般氰化矿浆经固液分离得到贵液(含金溶液),从贵液中提金的方法有锌置换沉淀法、活性炭吸附法、离子交换树脂吸附法或电解沉积法。
用金属锌丝或锌粉从贵液中把金置换沉淀是常用的方法,贵液在进入置换沉淀作业之前经澄清以除去其中的矿泥和悬浮物,因这些杂质对下一步的置换沉淀作业有害。
一、锌置换沉淀金的基本原理是:在贵液中的锌会溶解于溶液中而使金沉淀出来,贵液中Au(CN)2与Zn作用的反应式通常写成:2KAu(CN)2+3Zn+4KCN+2H2O =2Au (沉淀)+2K2 Zn (CN)4+K2 ZnO2+H2个锌置换时溶液中必须有足够的氰化物和碱,否则含金溶液中的溶解氧会使已沉淀的金粉再溶解而使锌氧化成Zn(OH)2沉淀:Zn+1/2O2+H2O=Zn(OH)2(沉淀)还有溶液中的K2Zn(CN)4会分解成不溶的氰化锌沉淀:K2Zn(CN)4+Zn(OH)2=2Zn(CN)2 (沉淀)+2KOH这些氢氧化锌和氰化锌为白色沉淀物,会罩在金属锌表面形成一层薄膜,而妨碍了锌从贵液中对金的置换作用。
所以往沉淀箱中加入少量的醋酸铅和硝酸铅有助于锌的溶解而更好地置换沉淀金。
贵液中含有可溶性硫化物、汞、铜等杂质均有碍于金的置换沉淀。
二、炭浆法提金工艺是氰化提金的方法之一,是含金物料氰化浸出完成之后,一价金氰化物[KAu(CN)2]进行炭吸附的工艺过程。
人们早已发现活性炭可以从溶液中吸附贵金属,开始只从清液中吸附金,将载金炭熔炼以回收金。
由于氰化矿浆需经固液分离得到清液和活性炭不能返回使用,此法在工业上无法与广泛使用的锌置换法竞争。
后来用活性炭直接从氰化矿浆中吸附金,这样就省去了固液分离作业;载金活性炭用氢氧化钠和氰化钠混合液解吸金银,活性炭经过活化处理可以返回使用。
因此,近年来炭浆法提金发展成为提金新工艺,我国在河南省灵湖金矿和吉林省赤卫沟金矿等建成了应用炭浆法提金工艺的生产工厂。
几种氰化法提金介绍
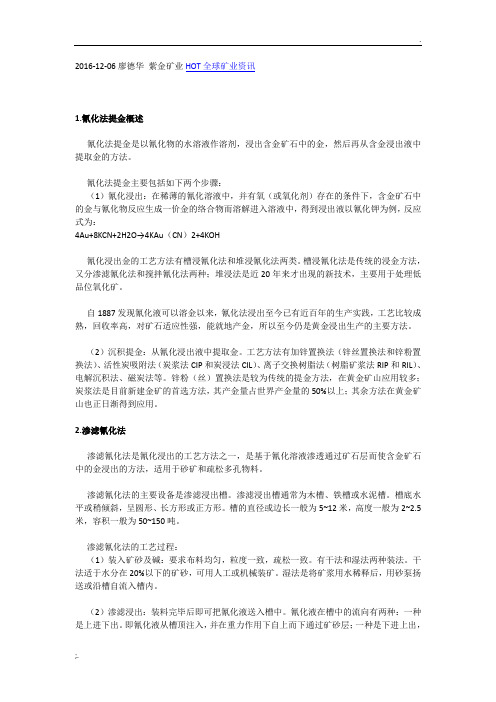
2016-12-06 廖德华紫金矿业HOT全球矿业资讯1.氰化法提金概述氰化法提金是以氰化物的水溶液作溶剂,浸出含金矿石中的金,然后再从含金浸出液中提取金的方法。
氰化法提金主要包括如下两个步骤:(1)氰化浸出:在稀薄的氰化溶液中,并有氧(或氧化剂)存在的条件下,含金矿石中的金与氰化物反应生成一价金的络合物而溶解进入溶液中,得到浸出液以氰化钾为例,反应式为:4Au+8KCN+2H2O→4KAu(CN)2+4KOH氰化浸出金的工艺方法有槽浸氰化法和堆浸氰化法两类。
槽浸氰化法是传统的浸金方法,又分渗滤氰化法和搅拌氰化法两种;堆浸法是近20年来才出现的新技术,主要用于处理低品位氧化矿。
自1887发现氰化液可以溶金以来,氰化法浸出至今已有近百年的生产实践,工艺比较成熟,回收率高,对矿石适应性强,能就地产金,所以至今仍是黄金浸出生产的主要方法。
(2)沉积提金:从氰化浸出液中提取金。
工艺方法有加锌置换法(锌丝置换法和锌粉置换法)、活性炭吸附法(炭浆法CIP和炭浸法CIL)、离子交换树脂法(树脂矿浆法RIP和RIL)、电解沉积法、磁炭法等。
锌粉(丝)置换法是较为传统的提金方法,在黄金矿山应用较多;炭浆法是目前新建金矿的首选方法,其产金量占世界产金量的50%以上;其余方法在黄金矿山也正日渐得到应用。
2.渗滤氰化法渗滤氰化法是氰化浸出的工艺方法之一,是基于氰化溶液渗透通过矿石层而使含金矿石中的金浸出的方法,适用于砂矿和疏松多孔物料。
渗滤氰化法的主要设备是渗滤浸出槽。
渗滤浸出槽通常为木槽、铁槽或水泥槽。
槽底水平或稍倾斜,呈圆形、长方形或正方形。
槽的直径或边长一般为5~12米,高度一般为2~2.5米,容积一般为50~150吨。
渗滤氰化法的工艺过程:(1)装入矿砂及碱:要求布料均匀,粒度一致,疏松一致。
有干法和湿法两种装法。
干法适于水分在20%以下的矿砂,可用人工或机械装矿。
湿法是将矿浆用水稀释后,用砂泵扬送或沿槽自流入槽内。
氰化提金工艺
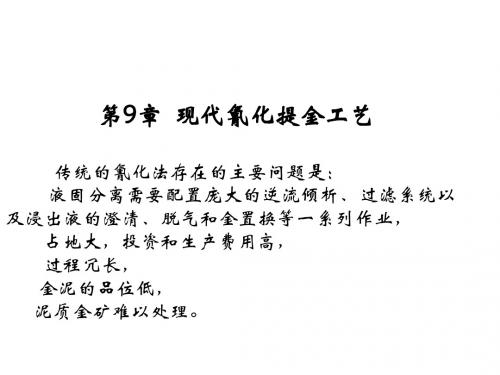
9.1.5 载金活性炭的解吸
从矿浆分离出来的载金活性炭,经洗涤和除去木屑等杂物 后送去解吸金(银)。载金活性炭的主要解吸方法有:
⑴常压解吸法
这一方法是最早在工业上应用的载金活性炭解吸方法,它是 由美国矿业局的Zadra研究成功的,因此,常称为扎德拉(Zadra) 法。 用0.1~0.2%的氰化钠和1%的氢氧化钠混合溶液,在 85~950C下从载金炭上解吸金。解吸液用电积法回收金。解吸 液与载金炭的体积比为8~15,并采用解吸液和电积溶液循环的 方式,解吸槽流出的含金贵液经预热并加热到所需的温度,以 每小时1~2柱床体积的流速给入解吸柱内,在常压下解吸 24~26h,即可将炭解吸到充分低的金品位。
8.1.2 活性炭吸附金的机理
⑴ 以金属形态被吸附 活性炭从金氯配合物(AuCl4-)溶液中吸附金后,可明显地看到 在炭的表面有黄色的金属金。以此推断金氰配合物也可被炭还 原。这种观点认为,炭上吸附的还原气体,如CO,可把金还原。
采用现代的分析技术X射线光电子能谱(XPS)对炭上被吸 附物中的金的价态的研究表明,被吸附的金的表观价态为 +0.3价。
0.7~0.8 97~99 1.16~2.35(14~8) 2~4 1~4
1050~1200 1000~1500 60~70 36~40
选用炭浆法活性炭最重要的条件,一是它对金应具有 良好的吸附性能,二是炭粒应当具有很强的耐磨性能。良好 的炭浆法活性炭,除了具备表9-1的性能外,通常还可用下列 三项技术指标来确定。 ⑴ 在含金1mg/L溶液中平衡吸附24h,活性炭的载金容 量应达25g/kg。 ⑵ 在含金10mg/L溶液中搅拌吸附1h,活性炭对金的吸 附率应达60%。 ⑶ 将活性炭臵于瓶中在摇滚机上翻滚24h,磨损率应小于 2%。
金矿生产线——氰化工艺流程详解
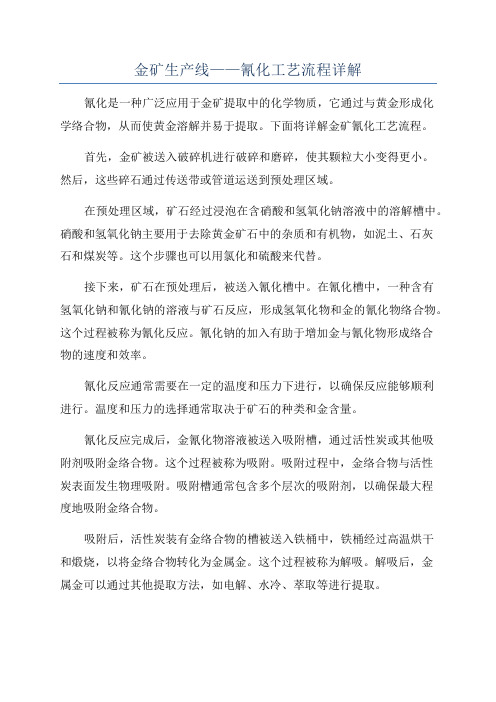
金矿生产线——氰化工艺流程详解氰化是一种广泛应用于金矿提取中的化学物质,它通过与黄金形成化学络合物,从而使黄金溶解并易于提取。
下面将详解金矿氰化工艺流程。
首先,金矿被送入破碎机进行破碎和磨碎,使其颗粒大小变得更小。
然后,这些碎石通过传送带或管道运送到预处理区域。
在预处理区域,矿石经过浸泡在含硝酸和氢氧化钠溶液中的溶解槽中。
硝酸和氢氧化钠主要用于去除黄金矿石中的杂质和有机物,如泥土、石灰石和煤炭等。
这个步骤也可以用氯化和硫酸来代替。
接下来,矿石在预处理后,被送入氰化槽中。
在氰化槽中,一种含有氢氧化钠和氰化钠的溶液与矿石反应,形成氢氧化物和金的氰化物络合物。
这个过程被称为氰化反应。
氰化钠的加入有助于增加金与氰化物形成络合物的速度和效率。
氰化反应通常需要在一定的温度和压力下进行,以确保反应能够顺利进行。
温度和压力的选择通常取决于矿石的种类和金含量。
氰化反应完成后,金氰化物溶液被送入吸附槽,通过活性炭或其他吸附剂吸附金络合物。
这个过程被称为吸附。
吸附过程中,金络合物与活性炭表面发生物理吸附。
吸附槽通常包含多个层次的吸附剂,以确保最大程度地吸附金络合物。
吸附后,活性炭装有金络合物的槽被送入铁桶中,铁桶经过高温烘干和煅烧,以将金络合物转化为金属金。
这个过程被称为解吸。
解吸后,金属金可以通过其他提取方法,如电解、水冷、萃取等进行提取。
最后,解吸后的活性炭可再生并重复使用。
为了进一步提取金属金,溶液经过中和、沉淀和过滤等步骤进行处理。
除金矿氰化工艺流程外,还有其他一些涉及到金的提取和分离的工艺流程,如浮选、磁选和重选等。
这些技术可以根据矿石的特性和黄金含量的不同进行选择和组合使用,以达到最大的金提取效益。
总结起来,金矿氰化工艺流程涉及到矿石的破碎、预处理、氰化、吸附、解吸和提取等多个步骤。
通过这些步骤,金能够从矿石中被转化为金属金,并可进一步提炼和应用于各种金属加工和制造业。
氰化法提金工艺

氰化法提金工艺(一)传统的氰化法提金工艺主要包括浸出、洗涤、置换(沉淀)三个工序。
①浸出——矿石中固体金溶解于含氧的氰化物溶液中的过程。
②洗涤——为回收浸出后的含金溶液,用水洗涤矿粒表面以及矿粒之间的已溶金,以实现固液分离的过程。
③置换——用金属锌从含金溶液中使其还原、沉淀,回收金的过程。
20世纪以来,从氰化矿浆中回收金是先进行矿浆的洗涤,然后进行贵液的澄清、除气。
从澄清的贵液中沉淀金,一直沿用锌置换法。
20世纪60年代以来才发展起来的向矿浆中加入活性炭的“炭浆法”发展很快。
随着对离子交换剂应用的研究,采用离子交换树脂从氰化液或氰化矿浆中吸附金的方法亦具有重要的实用价值。
在氰化液的溶剂萃取提金方面也作过一些研究。
当往氰化含金液中加人硫酸时,可用异戊醇来萃取金,萃取率随硫酸浓度的升高而增加。
如在2mol/L的硫酸液中进行萃取,还可使金与砷、铁等杂质分离。
使用氧代烷氧基磷酸酯从氰酸盐碱性液中萃取金,萃取指标令人满意;使用亚硫酸钠反萃取也获得了较好的结果等等。
1.氰化浸金用含氧的氰化物溶液把矿石中的金溶解出来的过程叫氰化浸出。
目前,无论从工艺、设备、管理或操作等方面都已日臻完善。
如前所述,金在含有氧的氰化物溶液中的溶解,实质上是一个电化学腐蚀过程。
浸出过程中主要使用的药剂是氰化物和保护碱两种。
1)氰化物工业上用于氰化法浸出金的氰化物主要有氰化钾(KCN)、氰化钠(NaCN)、氰化钙[Ca(CN)2]和氰化铵(NH4CN)四种。
它们对金的相对溶解能力见表1。
表1 四种氰化物的性质对金的相对溶解能力在生产中常用的氰化物是氰化钠,它是一种剧毒的白色粉末,商品氰化钠一般压制成球状或块状。
工业上也有用氰熔体作为浸出药剂的。
它是将氰化钙、食盐和焦炭混合后在电炉中熔化而成的一种混合物。
除了含40%~45%的Ca(CN)2和NaCN以外,还含有一些对氰化过程有害的杂质,如可溶性硫化物、碳以及一些不溶性杂质等。
其特点是价格便宜,但用量大,约为氰化钠的2~2.5倍。
金矿选矿之氰化法提金法
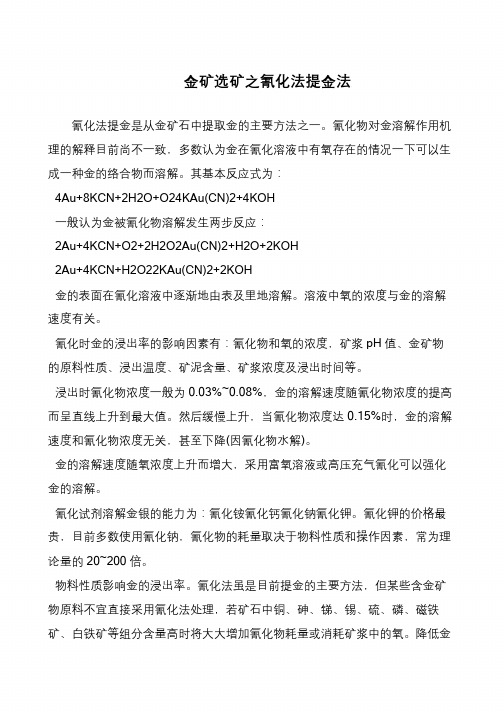
书山有路勤为径,学海无涯苦作舟
金矿选矿之氰化法提金法
氰化法提金是从金矿石中提取金的主要方法之一。
氰化物对金溶解作用机理的解释目前尚不一致,多数认为金在氰化溶液中有氧存在的情况一下可以生成一种金的络合物而溶解。
其基本反应式为:
4Au+8KCN+2H2O+O24KAu(CN)2+4KOH
一般认为金被氰化物溶解发生两步反应:
2Au+4KCN+O2+2H2O2Au(CN)2+H2O+2KOH
2Au+4KCN+H2O22KAu(CN)2+2KOH
金的表面在氰化溶液中逐渐地由表及里地溶解。
溶液中氧的浓度与金的溶解速度有关。
氰化时金的浸出率的影响因素有:氰化物和氧的浓度,矿浆pH 值、金矿物的原料性质、浸出温度、矿泥含量、矿浆浓度及浸出时间等。
浸出时氰化物浓度一般为0.03%~0.08%,金的溶解速度随氰化物浓度的提高而呈直线上升到最大值。
然后缓慢上升,当氰化物浓度达0.15%时,金的溶解速度和氰化物浓度无关,甚至下降(因氰化物水解)。
金的溶解速度随氧浓度上升而增大,采用富氧溶液或高压充气氰化可以强化金的溶解。
氰化试剂溶解金银的能力为:氰化铵氰化钙氰化钠氰化钾。
氰化钾的价格最贵,目前多数使用氰化钠,氰化物的耗量取决于物料性质和操作因素,常为理论量的20~200 倍。
物料性质影响金的浸出率。
氰化法虽是目前提金的主要方法,但某些含金矿物原料不宜直接采用氰化法处理,若矿石中铜、砷、锑、锡、硫、磷、磁铁矿、白铁矿等组分含量高时将大大增加氰化物耗量或消耗矿浆中的氧。
降低金。
全泥氰化提金工艺设计与生产实践

品位的比较,当品位下调为 25% 左右的时候,针对于露天进 行的采矿,试样与地质品位都应该下调 10% 左右为最佳。试 验要经过氰化浸出,之后完成矿浆的沉降速度试验,要保障 矿浆浓度、工业生产矿浆浓度保持一致,这样才能够满足全 泥氰化提金工艺设计中设备选择的需求。针对具有碳物质矿 样进行的炭浆法试验的时候,就应该对工艺流程进行方案的 对比,突出工艺竞争吸附效果,提升浸出指标。
原则流程是全泥氰化提金工艺设计的重要环节,也是进 行选矿的关键,因此,要注重全泥氰化提金工艺设计工作。全 泥氰化提金工艺设计当中要确定流程,能够符合矿石特点,根 据设计原则并且要在较长的时间当中维持生产的稳定性,避 免出现投产之后进行流程改造。
1 矿石可选性试验 矿石可选性试验能够为全泥氰化提金工艺设计提供数
据中国黄金协会数据统计,2020 年,我国黄金产量为 479.50 吨,较 2019 年下降 4.2%,但仍是全球最大黄金产出 国,受珠宝首饰需求、国民投资需求、工业制造需求、黄金储 备需求等因素拉动,我国黄金产销量大,均位居全球第一。 氰化法提金工艺主要包括渗滤氰化法提金、搅拌氰化法提 金、堆浸氰化法提金、锌置换法、炭浆法、离子交换树脂法、 电积法等。具体来看,渗滤氰化法提金主要用于处理金精矿、 金汞混合矿方面 ;搅拌氰化法提金主要用于处理泥质氧化金 矿方面 ;堆浸氰化法提金主要用于处理低品位金矿方面。
方式。但是与其他国家相比,在氰化工艺设计上还存在一定的差距,生产指标较低,设备性能、检测控制等方面还存在
不足,而且氰化物属于剧毒。本文对全泥氰化提金工艺设计中注意事项进行分析,对常见流程结构特点进行说明,通过
氰化提金工艺

圆筒扎德拉电解槽:3槽串联,91×120cm;
阴极装:7.2 kg钢棉/个;
阳极:不锈钢圆筒形筛网;
金总回收率:~95%;
图 美国霍姆斯特克矿业公司莱德矿炭浆法生产工艺流程 黄金产量:~8 t/a
20
9.5 磁炭法
磁炭法:磁性炭浆法。
操作与炭浆法和炭浸法基本相同,但由于可采用弱磁选机回收浸出吸 附尾浆中的载金细粒炭,因此磁炭工艺可克服活性炭易磨损而造成细粒载 金炭损失的缺点。
小规模常采用吸附塔:装活性炭25-30 kg。
9
9.4 炭浆工艺
把氰化浸出槽排出的矿浆,送到吸附槽用活性炭吸附矿浆中的 金银的方法,称为炭浆法(CIP)。
把活性炭投入氰化浸出槽中,使氰化浸出金与炭吸附金在同一 槽中进行的方法,称为炭浸法(CIL)。
当前,它已成为新建金矿的首选方法,世界产金量一半以上是 用该法生产的。
1
18
0.72
11250
62.5
2
18
0.27
4500
85.9
3
24
0.06
2550
96.9
4
24
0.015
600
99.2
16
3、解吸 (1)常压解吸法
85 0C下,用1%氰化钠和1%氢氧化钠,24-60h解吸。 或95 0C下,用4%氰化钠和2%氢氧化钠,12-14h解吸。 (2)酒精解吸法 80 0C常压下,用0.1%氰化钠、1%氢氧化钠、20%体积 的酒精,5-6h解吸。缺点是易燃,费用高,需回收。 (3)高压解吸法 160 0C、3.5*105Pa下,用0.1%氰化钠、1%氢氧化钠、 2-9h解吸,或用含1%氰化钠和5%氢氧化钠溶液预处理后5倍 炭体积热水解吸 优点是试剂消耗少解吸时间短,但需高压,减压前需冷却。
贵金属选冶理论与技术第三章氰化法提金工艺.
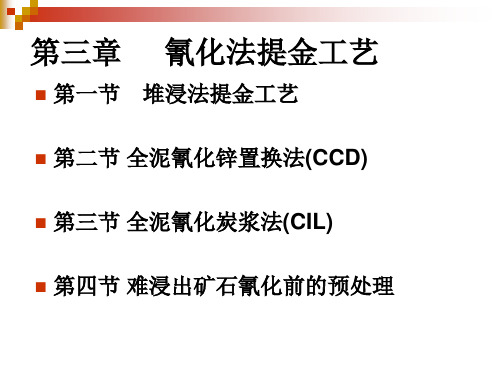
6、贵液中的杂质
溶液中所含杂质如铜、汞、镍及可溶性硫化物等都是置换金的 有害杂质。
(1)铜的络合物与锌反应时,铜被置换而消耗锌,同时铜在锌的 表面形成薄膜防碍金的置换,其反应式:
2Na2Cu(CN)3 + Zn = 2Cu + Na2Zn(CN)4 + 2NaCN (2)汞与锌发生反应生成的汞与锌合金使锌变脆,影响金的置换
一、堆浸法提金生产的主要经验
(1)破碎。根据矿石性质及工艺要求,实行不同的破 碎工艺流程。经过对堆浸矿山的调查,主要分三种 情况:废矿石堆浸一般不破碎(占30%),二段破 碎后矿石粒度为30~50mm(占53%),三段破碎后 矿石粒度为9~19mm(占17%)。
实践证明:破碎是保证矿石具有良好渗透性,提高 金的浸出率的关键技术环节之一。
锌粉置换:氰浓度为0.03~0.06%,碱浓度为0.01~0.03%。
2、氧的浓度
金在氰化物中溶解必须有氧参加,而置换是金溶解 的逆相过程,置换过程中的溶解氧对置换是有害的。 氧的存在会加快锌的溶解速度,增加锌耗,大量产 生氢氧化锌和氰化锌沉淀而影响置换。
溶氧量:生产中,一般控制溶液中的溶解氧时在 0.5mg/L以下。
(2)若溶液中CN-低浓度时,氰锌络合物分解并生成不溶解的氰 化锌(白色沉淀):
Zn(CN)2-4 + Zn(OH)2 = 2Zn(CN)2 +2OH总之:上述反应中生成的氢氧化锌和氰化锌沉淀会沉积在锌的
表面妨碍金的置换,所以在金的置换过程中,要保持溶液中 有一定的氰化物和碱的浓度,避免Zn(OH)2 和 Zn(CN)2的生 成,使金的置换过程顺利进行。
第三章 氰化法提金工艺
- 1、下载文档前请自行甄别文档内容的完整性,平台不提供额外的编辑、内容补充、找答案等附加服务。
- 2、"仅部分预览"的文档,不可在线预览部分如存在完整性等问题,可反馈申请退款(可完整预览的文档不适用该条件!)。
- 3、如文档侵犯您的权益,请联系客服反馈,我们会尽快为您处理(人工客服工作时间:9:00-18:30)。
(4) 以AuCN被吸附:由氧化或酸分解作用产生AuCN,pH越低吸附容
量越大。
5
综合机理:
(1)在炭的巨大内表面上或微孔中,吸附 Mn+[Au(CN)2]n-离子对或中性分子,并随即排出 Mn+; (2) Au(CN)2-化学分解成 不溶性AuCN , 并保留在微孔中; (3) AuCN混合物部分还原成某种0价或1 价的金原子。
6
9.3 从氰化物溶液中吸附金
堆浸或渗滤浸出的含金、银浓度低且杂质含量高。用锌置换或 离子交换树脂法沉金效果都不好。而活性碳具有较高的选择性, 且吸附彻底。 吸附方法: 2、沸腾层吸附法 要考虑四个因素。 每吨活性炭吸附2-5 kg金或银比较合适。 3.35-1.0 mm炭粒悬浮流速17 L/(m2· s) 1.4-0.6 mm 10 L/(m2· s)
1
2 3 4
18
18 24 24
0.72
0.27 0.06 0.015
11250
4500 2550 600
62.5
85.9 96.9 99.2
16
3、解吸 (1)常压解吸法 85 0C下,用1%氰化钠和1%氢氧化钠,24-60h解吸。
或95 0C下,用4%氰化钠和2%氢氧化钠,12-14h解吸。
(2)酒精解吸法 80 0C常压下,用0.1%氰化钠、1%氢氧化钠、20%体积 的酒精,5-6h解吸。缺点是易燃,费用高,需回收。 (3)高压解吸法 160 0C、3.5*105Pa下,用0.1%氰化钠、1%氢氧化钠、 2-9h解吸,或用含1%氰化钠和5%氢氧化钠溶液预处理后5倍 炭体积热水解吸
将活性炭在间接加热的回转窑中隔绝空气加热至6500C
左右,持续30分钟,后经风冷或水冷。20目过筛,水洗。
18
2.6.3 炭浆工艺的主要影响因素 炭浆工艺氰化浸出系统的影响因素与搅拌氰化浸出相同。 炭浆工艺吸附系统的影响因素:
磨比 表 面 大 、 吸 附 活高 性的 粒 状 。 (1)活 性 炭 类 型 : 坚 硬 耐 、 用壳 炭 、 杏 核 炭 ; 常 椰 ( 2)活 性 炭 粒 度 : 粒 级 范 围 3.327 ~ 0.991 mm、 3 .327 ~ 1.397 mm、 1.397 ~ 0.543 mm; ( 3)矿 浆 中 炭 的 浓 度 : 取 于 决炭 浆 中 已 溶 金 浓 度排 和出 矿 浆 中 已 溶 金 的度 浓, 一 般 为 10 ~ 20 g / t; 与级 已 溶 金 的 量 及 活炭 性的 载 金 量 有 关 , (4)炭 移 动 的 相 对 速 度 : 该 如 : 灵 湖 为 2 kg / h; 4 级 , 也 可5 ~ 7 级 ; (5)吸 附 级 数 : 一 般 为 (6)每 级 吸 附 的 停 留 时 间 : 20 ~ 60分 钟 , 平 均 30 分 钟 ; (7)活 性 炭 的 损 失 量 : 椰 炭 壳的 损 失 量 为 0.1 kg炭 / t 矿 石 ; 19 :附 亲 和 力 为 金 银 碱金属。 (8)其 它 金 属 离 子 的 吸 附 吸
炭浆工艺范例 (美国霍姆斯特克矿业公司莱德矿)
原矿品位:5.5 g/t 矿石; 破碎设备:棒磨机-中磨; 球磨机细磨; 石灰用量:1 kg/t 矿石;空气调浆; 空气搅拌浸出槽:6台Ф9×6.6m , 1台Ф10.5×5.4m ; 初始氰化物:NaCN 0.04%~0.05%; pH 10.5; NaCN耗用量:0.4~0.5 kg/t矿石; 空气搅拌吸附槽:5台Ф5.4×4.8m ; 金的吸附量:12 ~15 kg金 / t炭; 活性炭:6~16目椰壳炭; 活性炭耗量:0.015 kg / t矿石; 载金炭洗涤:振动筛; 锥形解吸柱:3台,容量909 kg炭/柱; 解吸液:1NaOH%+0.2%NaCN,90℃, 流量:~2.7m3/h,解吸时间:~50h; 解吸后炭含金:150 g / t炭; 回转窑: Ф0.5×3.8m; 炭再生条件:600℃,15min; 圆筒扎德拉电解槽:3槽串联,91×120cm; 阴极装:7.2 kg钢棉/个; 阳极:不锈钢圆筒形筛网; 金总回收率:~95%; 黄金产量:~8 t/a
第9章 炭浆法
9.1 活性炭 9.2 活性炭吸附金的机理 9.3 从氰化物溶液中吸附金
9.4 炭浆工艺
9.5 炭磁法
1
炭浆法氰化提金简史
1847年,莱扎斯基首次发现活性炭能从含金溶液中吸附金;
1880年,澳大利亚广泛使用活性炭从溶液中吸附回收金;但仍不能解决 传统氰化法中的液固分离问题。
1934年,齐普曼直接加木炭从氰化浸出矿浆中吸附金,炭不循环使用; 1952年,扎德拉(Zadra)发现:热NaOH+NaCN溶液可从载金炭上 解吸金。奠定了当代炭浆工艺的基础活性炭实现了循环使用; 1961年,美国科罗拉多洲卡林顿选金厂首次用炭浆工艺进行小规模生产; 1973 年,美国南达科它洲霍姆斯特克金矿选矿厂首次用炭浆 法 进行生产,矿石处理量为 2250 t/d; 之后,在美国、南非、菲律宾、澳大利亚、津巴布韦等 国相继建成几十座炭浆提金厂; 1985年,我国在灵湖矿和赤卫沟矿建成炭浆提金厂, 此后,相继建成十几座炭浆提金厂。
1、渗滤法 活性碳用量少,但如果有矿泥等细物料会堵塞炭层。
静止时活性炭的高度不大于直径的3倍,塔高为炭层高度的 2.5-3倍 7
日处理5000t矿石氰化浸出时的金分布图
8
大规模堆积使用吸附槽:高度为1.5 m,炭层0.6-0.7 m,炭重290-370kg/m2。 流速保持在600-1200 L/m2· min。 小规模常采用吸附塔:装活性炭25-30 kg。
2
9.1 活性炭
活性炭:多孔的炭质吸附剂。 制备活性炭的材料:煤质类、果壳类、木质类及高分子类等 制备的方法:在隔绝空气条件下加热到800-900 oC 微孔直径0.5-2 mm,比表面400-1000 m2/g。
3
4
9.2 活性炭吸附金的机理
(1)以金属被吸附: 表明有黄色金属金,X射线光电光谱中金的表观
优点是试剂消耗少解吸时间短,但需高压,减压前需冷却。
17
4、电解
略
5、炭再生
活性炭再生的原因:炭粒污染,对贵金属的吸附活性降低。
炭的再生分两步进行: 第一步 酸洗除去CaCO3及大部分贱金属络合物。 用 稀HCl或HNO3浸洗活性炭,后经中和、水洗至中性。
可安排在三个地方。
过程中可能会产生剧毒的HCN气体,应加以防护。 第二步 加热活化,除去炭粒中的其它无机和有机杂质。
15
炭吸附系统设备要求: (1)在吸附槽内炭和矿浆最充分的接触。 (2)载金炭和矿浆在筛上进行最有效的分离。 (3)尽可能地减少整个吸附系统内炭粒的磨损。 (4)在吸附槽内应尽量避免矿浆发生短路现象。
表 吸附工艺参数 (6~16目的椰壳活性炭,炭消耗量0.015kg/t矿石)
吸附级数 炭浓度(g/t) 溶液含金 (g/t) 炭吸附量 (g/t) 累计吸附率(%)
9
9.4 炭浆工艺
把氰化浸出槽排出的矿浆,送到吸附槽用活性炭吸附矿浆中的
金银的方法,称为炭浆法(CIP)。
把活性炭投入氰化浸出槽中,使氰化浸出金与炭吸附金在同一
槽中进行的方法,称为炭浸法(CIL)。
当前,它已成为新建金矿的首选方法,世界产金量一半以上是
用该法生产的。
10
吸附提金的优点:
1. 取消了繁杂昂贵的浮选富集工序和矿浆固液分离工序。 占地少,基建投资可节省10%。 2. 在处理低品位难选原矿时,可获得较高的金回收率,尤 其适合处理含泥多、难于沉降和过滤、细泥吸附已溶金 的矿石。即使对含铜等杂质较多的溶液,对锌置换不利, 但不影响吸附。 3. 金的纯度高,熔炼是熔剂消耗少,金随炉渣和烟气的损 失也少。
14
吸附系统的影响因素:
磨比 表 面 大 、 吸 附 活高 性的 粒 状 。 (1)活 性 炭 类 型 : 坚 硬 耐 、 用壳 炭 、 杏 核 炭 ; 常 椰 ( 2)活 性 炭 粒 度 : 粒 级 范 围 3.327 ~ 0.991 mm、 3 .327 ~ 1.397 mm、 1.397 ~ 0.543 mm; ( 3)矿 浆 中 炭 的 浓 度 : 取 于 决炭 浆 中 已 溶 金 浓 度排 和出 矿 浆 中 已 溶 金 的度 浓, 一 般 为 10 ~ 20 g / t; 与级 已 溶 金 的 量 及 活炭 性的 载 金 量 有 关 , (4)炭 移 动 的 相 对 速 度 : 该 如 : 灵 湖 为 2 kg / h; 4 级 , 也 可5 ~ 7 级 ; (5)吸 附 级 数 : 一 般 为 (6)每 级 吸 附 的 停 留 时 间 : 20 ~ 60分 钟 , 平 均 30 分 钟 ; (7)活 性 炭 的 损 失 量 : 椰 炭 壳的 损 失 量 为 0.1 kg炭 / t 矿 石 ; :附 亲 和 力 为 金 银 碱金属。 (8)其 它 金 属 离 子 的 吸 附 吸
精炼厂
电解沉积 金泥 熔铸 合质金阳极 电解精炼 熔铸 金锭
浓密机浓缩 调整槽调整矿浆pH 氰化浸出 活性炭吸附
筛下炭
筛上炭 过筛
尾浆
废弃
载金炭
NaCN+NaOH
再生炭 解吸炭再生
解吸槽解吸
解吸后的炭 解吸贵液
12
图9-4 典型炭浆法流程示意图
水力旋流器
整槽 氰化浸出槽 浸出矿浆 20目 20目 20目 氰化浸出槽 炭筛20目 解吸槽 解吸液 尾矿处理
价态为+0.3价,解吸剂非氰化物不可。但一氧化碳和碳都不能还原 Au(CN)2-。
(2)以Au(CN)2-离子吸附:活性炭与氧接触,形成具有碱性特征的表
面氧化物,氧结合不牢固,以电离出氢氧根,使炭表面存在带正电荷的格