光刻版数据处理中的工艺涨缩问题
光刻机对于半导体器件尺寸缩小的影响与挑战
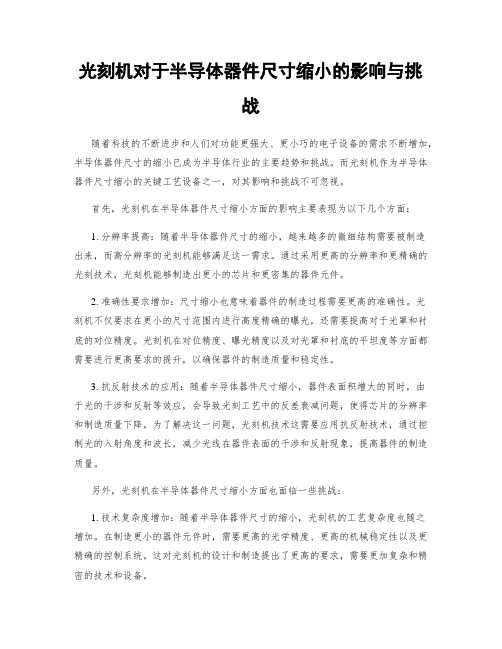
光刻机对于半导体器件尺寸缩小的影响与挑战随着科技的不断进步和人们对功能更强大、更小巧的电子设备的需求不断增加,半导体器件尺寸的缩小已成为半导体行业的主要趋势和挑战。
而光刻机作为半导体器件尺寸缩小的关键工艺设备之一,对其影响和挑战不可忽视。
首先,光刻机在半导体器件尺寸缩小方面的影响主要表现为以下几个方面:1. 分辨率提高:随着半导体器件尺寸的缩小,越来越多的微细结构需要被制造出来,而高分辨率的光刻机能够满足这一需求。
通过采用更高的分辨率和更精确的光刻技术,光刻机能够制造出更小的芯片和更密集的器件元件。
2. 准确性要求增加:尺寸缩小也意味着器件的制造过程需要更高的准确性。
光刻机不仅要求在更小的尺寸范围内进行高度精确的曝光,还需要提高对于光罩和衬底的对位精度。
光刻机在对位精度、曝光精度以及对光罩和衬底的平坦度等方面都需要进行更高要求的提升,以确保器件的制造质量和稳定性。
3. 抗反射技术的应用:随着半导体器件尺寸缩小,器件表面积增大的同时,由于光的干涉和反射等效应,会导致光刻工艺中的反差衰减问题,使得芯片的分辨率和制造质量下降。
为了解决这一问题,光刻机技术这需要应用抗反射技术,通过控制光的入射角度和波长,减少光线在器件表面的干涉和反射现象,提高器件的制造质量。
另外,光刻机在半导体器件尺寸缩小方面也面临一些挑战:1. 技术复杂度增加:随着半导体器件尺寸的缩小,光刻机的工艺复杂度也随之增加。
在制造更小的器件元件时,需要更高的光学精度、更高的机械稳定性以及更精确的控制系统。
这对光刻机的设计和制造提出了更高的要求,需要更加复杂和精密的技术和设备。
2. 成本增加:尺寸缩小和技术复杂度增加使得光刻机的制造成本不断上升。
在提高分辨率和准确性的同时,同时需要昂贵的材料和先进的光学技术,以及更精密的控制系统。
这种成本的增加可能会由于市场需求和经济压力的变化而带来更大的挑战。
3. 新材料的应用:随着半导体器件尺寸的缩小,也需要使用更多新材料来满足制造要求。
涨缩原理及补偿介绍
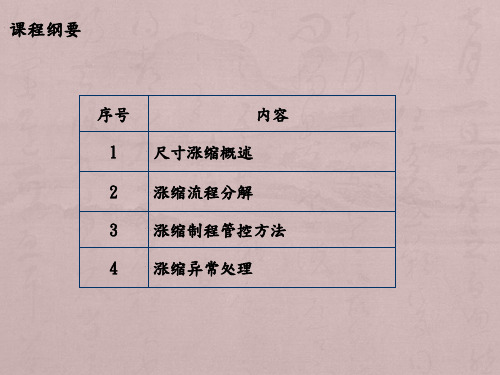
湿度的影响 : 在相对温度下,菲林的尺寸随着湿度的上升而涨大,相对湿度的降低而 缩小,湿涨变形系数在10ppm/%RH右,也就是说当湿度度发生 1℃的变化 时,50cm长的菲林会发生5um的变化(或20寸中的0.20mil).
1.尺寸涨缩概述
底片尺寸涨缩的原因: (4)曝光机温升过高.
底片尺寸涨缩的控制方法: (4)采用冷光源或有冷却装置的曝光机及不断更换备份底片.
1.尺寸涨缩概述
底片尺寸涨缩的原因: (1)底片从真空包装拆包后静置时间不足;
底片尺寸涨缩的控制方法: (1)黑片从真空包装中拆封后需静置24小时,棕片需静置8小时;
1.尺寸涨缩概述
底片尺寸涨缩的原因: (2)底片绘制完成后静置时间不足直接用于生产;
底片尺寸涨缩的控制方法: (2)底片绘制完成后静置时间必须大于2小时才可用于生产;
孔位檢查
底片上机前 后变化
底片单张差异 底片每套间差异 底片使用次数
后烤前后变 化
3.尺寸涨缩管制方法
IQC进料对基板的玻布厂牌、进料尺寸安定性状况进行记录.
廠牌
板厚
銅厚 生產日期 進料日期 進料批號
玻 布
TG點
尺安測試值 經向(Warp緯) 向(Fill)
IC制造中硅片边缘上光刻工艺的波动问题分析参考Word
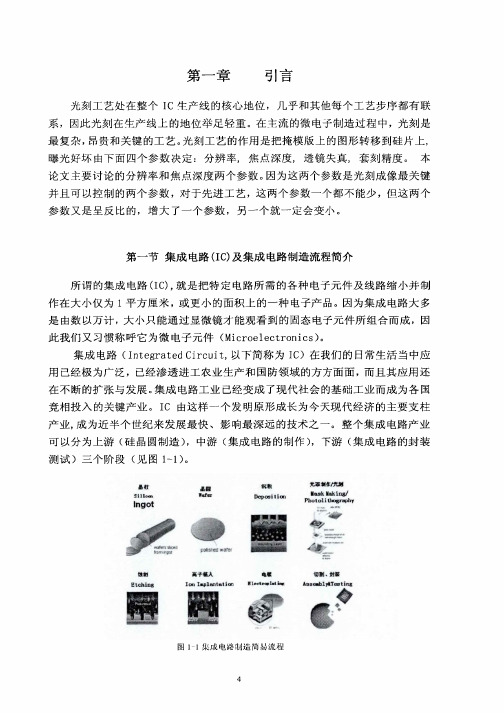
如不慎侵犯了你的权益,请联系我们告知!第一章引言光刻工艺处在整个IC 生产线的核心地位,几乎和其他每个工艺步序都有联系,国此光刻在生产线上的地位举足轻重。
在主流的微电子制造过程中,光刻是最复杂,昂贵和关键的工艺。
光刻工艺的作用是把掩模版上的图形转移到硅片上,曝光好坏由下面四个参数决定: 分辨率,焦点深度,透镜失真,套刻精度。
本论文主要讨论的分辨率和焦点深度两个参数。
因为这两个参数是光刻成像最关键并且可以控制的两个参数,对于先进工艺,这两个参数一个都不能少,但这两个参数又是呈反比的,增大了一个参数,另一个就一定会变小。
第一节集成电路 (IC )及集成电路制造流程简介所谓的集成电路(IC) ,就是把特定电路所需的各种电子元件及线路缩小并制作在大小仅为1 平方厘米,或更小的面积上的一种电子产品。
因为集成电路大多是由数以万计,大小只能通过显微镜才能观看到的固态电子元件所组合而成,因此我们又习惯称呼它为微电子元件(M ie r o e le c tr o n ie s ) 。
集成电路( 工nt eg r at ed C irc ui t,以下简称为1C ) 在我们的日常生活当中应用己经极为广泛,己经渗透进工农业生产和国防领域的方方面面,而且其应用还在不断的扩张与发展。
集成电路工业已经变成了现代社会的基础工业而成为各国竞相投入的关键产业。
IC 由这样一个发明原形成长为今天现代经济的主要支柱产业,成为近半个世纪来发展最快、影响最深远的技术之一。
整个集成电路产业可以分为上游 (硅晶圆制造) ,中游(集成电路的制作 ),下游( 集成电路的封装测试) 三个阶段( 见图1一1 )。
允. 翻作从洲多.,心口伪珍. 1 . 1. …k .比 1。
砂玲。
一0 11 目加甲. 目.,!n g o t神护只,燕,. 御于-位侧面子桩人二匆侧、封绍已t 比1习日 1 . 1 即 1 . t. l 五国,l o d .,,盆目洛. 如二山1 润I .T t i飞! I 犷‘夕图1一l 集成电路制造简易流程如不慎侵犯了你的权益,请联系我们告知!集成电路制作部分流程非常复杂,工艺流程一般都有几百上千个步骤,从开始流片到可以切割封装动辄需要几个月的时间。
涨缩原理及补偿介绍
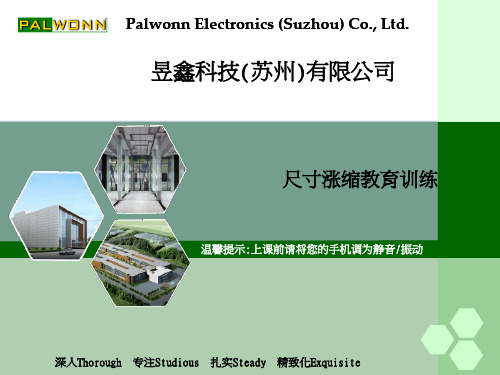
6
1.尺寸涨缩概述
基板尺寸涨缩的原因: (3)刷板时由于采用压力过大,致使产生压拉应力导致基板变形.
基材尺寸涨缩的控制方法:
(3)应采用试刷,使工艺参数处在最佳状态,然后进行刷板.对薄型基材,
清洁处理时应采用化学处理或喷砂处理.
2020/4/2
7
1.尺寸涨缩概述
基板尺寸涨缩的原因: (4)多层板在层压前,因基板有吸湿性,使薄基板或半固化片吸湿,造 成尺寸稳定性差,基板中树脂未完全固化,导致尺寸变化.
30sht/叠,150度4小时 烤箱温度均勻性监控 烘烤后冷却时间监控
先进先出管 理
暂存要求
内层涂布前 后差异
有效期点检: 基板: P.P:
曝光机內部温湿 度变化
铆合与热熔
同心圆对准 度检测 压合程式 热压/冷压 钻靶
上PIN作业
Run Out值 检测
X-Ray偏孔 檢查
2020/4/2
底片上机前后变 化
2020/4/2
12
1.尺寸涨缩概述
温度的影响 : 在相对湿度下,菲林的尺寸随着温度的上升而涨大,温度下降
而缩小,其热发生1℃的 变化时,50cm长的菲林会发生9um的变化(或20寸中的0.36mil).
湿度的影响 :
在相对温度下,菲林的尺寸随着湿度的上升而涨大,相对湿度的降低而
(5)需进行工艺试压,调整工艺参数然后进行压制.同时还可以根据
半固化的特性,选择合适的流胶量.
2020/4/2
9
1.尺寸涨缩概述
底片尺寸涨缩的原因: (1)底片从真空包装拆包后静置时间不足;
底片尺寸涨缩的控制方法: (1)黑片从真空包装中拆封后需静置24小时,棕片需静置8小时;
光刻机曝光过程中的热变形分析与校正

光刻机曝光过程中的热变形分析与校正光刻技术在现代微电子制造领域扮演着重要的角色。
光刻机是光刻技术的核心设备,其曝光过程中的热变形对光刻图形的精度和品质有着显著影响。
本文将对光刻机曝光过程中的热变形进行分析,并探讨相应的校正方法。
1. 热变形的原因分析光刻机在高强度曝光过程中会产生大量的热量,使光刻机的材料产生热胀冷缩,从而导致机台和掩模的形变。
主要的热变形因素包括光刻机结构的材料特性、光刻机使用环境以及曝光光源的热辐射等。
2. 热变形对曝光图形的影响热变形会导致曝光图形的尺寸、形状和位置产生误差,甚至影响到芯片的性能和可靠性。
特别是在微纳尺度下,热变形对曝光图形的影响更为明显。
3. 热变形的测量方法为了准确评估曝光过程中的热变形,需要采用合适的测量方法。
常用的方法有激光干涉技术、电子束检测技术和光栅法等。
这些方法能够实时监测光刻机结构的热变形情况,并记录下热变形的参数。
4. 热变形校正的方法热变形校正是减小热变形对曝光图形影响的重要手段。
其中,机台的设计优化与制造工艺显得尤为关键。
通过合理的材料选择和结构设计,可以减少材料的热胀冷缩,降低热变形的程度。
此外,也可以利用热补偿技术来实时校正光刻机的热变形。
5. 热变形校正的展望随着微纳尺度技术的不断发展,对高精度和高稳定性的光刻机要求也越来越高。
未来的研究将着重于热变形的理论分析和实验研究,以进一步提高光刻机的精度和可靠性。
结论光刻机曝光过程中的热变形是影响光刻图形精度的重要因素。
通过深入研究热变形的原因和测量方法,以及有效地进行热变形校正,可以提高光刻机的曝光精度。
未来的研究将进一步推动光刻技术在微电子制造领域的应用。
高级精密线路板PCB涨缩异常处理方式

判定量测比例与底 片比例是否相符
相符
不符
按照计算比例绘 制新底片 确认首件
重绘底片
正常生产
申请后制程治工具
结束
20
四:防焊涨缩异常处理方法及步骤
4.2. 防焊板子涨缩量测方法
X
Y
示意图
实物图
21
四:防焊涨缩异常处理方法及步骤
4-3. 防焊板子涨缩比例计算方法:
CAM规格*比例 板子 X (D) 涨缩 (E=D-C) Y (D1) 涨缩 (E=D1-C1) X Y (C=A*A1) (C1=B*B1) 14.9901 14.9901 CAM规格 X (A) Y (B) 生产底片比例 X (A1) Y (B1)
注意事项: 1:必须以中心为原点 2:板子开几槽就在板子三孔处加几个孔 3:板子开几槽就命名为几AO
15
二:钻孔涨缩异常处理方法及步骤
b:首件制作OK后,申请后制程治工具
注意事项: 1:钻带申请时板子三孔加几孔为几孔,后制程底片就命名为几孔 2:量产申请半自动菲林,量产超过一百PNL申请全自动菲林, 3:样品申请后制程治工具时,旧治工具要构其他,并注明回收
底片
网版
25
六:压合前后涨缩量测数据收集
压合前后涨缩数据收集
收文单位: □ 研发 客户料号: □样品: 设计厂牌: 叠构: 压合板厚: 内层补偿系数: 压合程式: 设计靶据: X : L2-L3 Y □ 品保 □ 品管 □制作 厂内料号: □量产: 发料厂牌: □其他
Y: 蚀刻后量测值 靶 X
□混压,混压料号: 靶: 量测人: L4-L5 Y 压合后量测 板子 Y
量测靶间距Y -2mil≦Y≦2mil 2mil﹤Y≦6mil 6mil﹤Y≦10mil -10mil≦Y﹤-6mi
PCB电路板为什么会出现涨缩_如何应对PCB尺寸涨缩-华强pcb
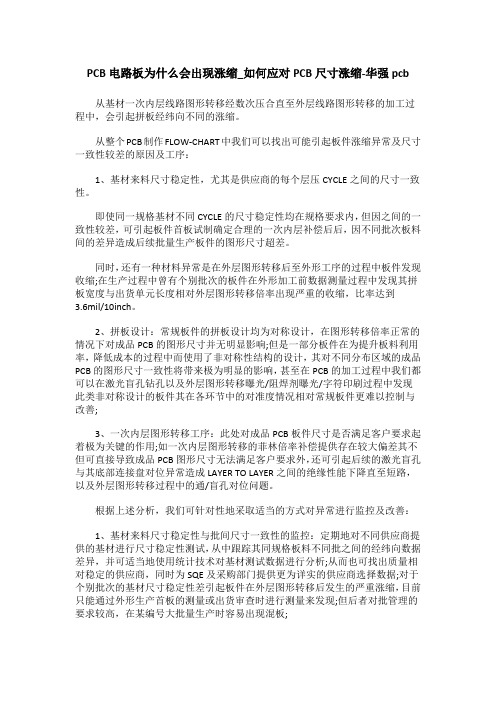
PCB电路板为什么会出现涨缩_如何应对PCB尺寸涨缩-华强pcb从基材一次内层线路图形转移经数次压合直至外层线路图形转移的加工过程中,会引起拼板经纬向不同的涨缩。
从整个PCB制作FLOW-CHART中我们可以找出可能引起板件涨缩异常及尺寸一致性较差的原因及工序:1、基材来料尺寸稳定性,尤其是供应商的每个层压CYCLE之间的尺寸一致性。
即使同一规格基材不同CYCLE的尺寸稳定性均在规格要求内,但因之间的一致性较差,可引起板件首板试制确定合理的一次内层补偿后后,因不同批次板料间的差异造成后续批量生产板件的图形尺寸超差。
同时,还有一种材料异常是在外层图形转移后至外形工序的过程中板件发现收缩;在生产过程中曾有个别批次的板件在外形加工前数据测量过程中发现其拼板宽度与出货单元长度相对外层图形转移倍率出现严重的收缩,比率达到3.6mil/10inch。
2、拼板设计:常规板件的拼板设计均为对称设计,在图形转移倍率正常的情况下对成品PCB的图形尺寸并无明显影响;但是一部分板件在为提升板料利用率,降低成本的过程中而使用了非对称性结构的设计,其对不同分布区域的成品PCB的图形尺寸一致性将带来极为明显的影响,甚至在PCB的加工过程中我们都可以在激光盲孔钻孔以及外层图形转移曝光/阻焊剂曝光/字符印刷过程中发现此类非对称设计的板件其在各环节中的对准度情况相对常规板件更难以控制与改善;3、一次内层图形转移工序:此处对成品PCB板件尺寸是否满足客户要求起着极为关键的作用;如一次内层图形转移的菲林倍率补偿提供存在较大偏差其不但可直接导致成品PCB图形尺寸无法满足客户要求外,还可引起后续的激光盲孔与其底部连接盘对位异常造成LAYER TO LAYER之间的绝缘性能下降直至短路,以及外层图形转移过程中的通/盲孔对位问题。
根据上述分析,我们可针对性地采取适当的方式对异常进行监控及改善:1、基材来料尺寸稳定性与批间尺寸一致性的监控:定期地对不同供应商提供的基材进行尺寸稳定性测试,从中跟踪其同规格板料不同批之间的经纬向数据差异,并可适当地使用统计技术对基材测试数据进行分析;从而也可找出质量相对稳定的供应商,同时为SQE及采购部门提供更为详实的供应商选择数据;对于个别批次的基材尺寸稳定性差引起板件在外层图形转移后发生的严重涨缩,目前只能通过外形生产首板的测量或出货审查时进行测量来发现;但后者对批管理的要求较高,在某编号大批量生产时容易出现混板;2、拼板设计方面应量采用对称结构的设计方案,使拼板内的各个出货单元涨缩保持相对一致;如可能,应与客户沟通建议其允许在板件的工艺边上以蚀刻/字符等标识方式将各出货单元在拼板内的位置进行具体标识;此方法在非对称方式设计的板件内效果将更明显,即使每拼板内因图形不对称引起各别单元出现尺寸超差,甚至是因此引起的局部盲孔底部连接异常亦可极为方便地确定异常单元并在出货前将其挑出处理,不至于流出造成客户封装异常而招致投诉;3、制作倍率首板,通过首板来科学地确定生产板件的一次内层图形转移倍率;在为降低生产成本而变更其它供应商基材或P片时,此点尤为重要;当发现有板件超出控制范围时应根据其单元管位孔是否为二次钻孔加工;如为常规加工流程板件则可根据实际情况放行至外层图形转移通过菲林倍率进行适当调整;如是二次钻孔板件,则对异常板件的处理需特别谨慎以确保成品板件的图形尺寸与标靶至管位孔(二次钻孔)距;附二次积层板件首板倍率收集清单;4、过程监控:利用外层或次外层板件在其层压后的X-RAY生产钻孔管位孔时所测量的板件内层标靶数据,分析其是否在控制范围内且与合格首板所收集的相应数据进行对比以判断板件尺寸是否有涨缩异常,下有附表可参考;经过理论计算,通常此处的倍率应控制在+/-0.025%以内才能满足常规板件的尺寸要求。
菲林涨缩不良报告
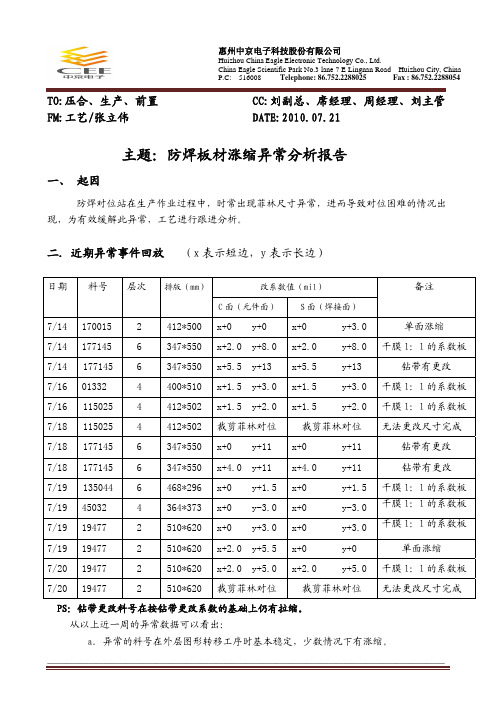
Fa同一个料号有多个拉缩系数,有拉长或缩短,如 115025、177145、19477, 每次来料均要更改系数方可生产。
c. 部分料号存在单面涨缩,即某一面用 1:1 菲林可以生产,另一面要更改系数生产。 d. 个别料号有时无法更改菲林尺寸,如 19477,主要原因为两边可以对正,但中间
7/20 19477
2 510*620 裁剪菲林对位 裁剪菲林对位 无法更改尺寸完成
PS:钻带更改料号在按钻带更改系数的基础上仍有拉缩。 从以上近一周的异常数据可以看出: a. 异常的料号在外层图形转移工序时基本稳定,少数情况下有涨缩。
__________________________________________________________________________________________________________
钻带有更改
7/16 01332
4 400*510 x+1.5 y+3.0 x+1.5 y+3.0 干膜 1:1 的系数板
7/16 115025 4 412*502 x+1.5 y+2.0 x+1.5 y+2.0 干膜 1:1 的系数板
7/18 115025 4 412*502 裁剪菲林对位 裁剪菲林对位 无法更改尺寸完成
Huizhou China Eagle Electronic Technology Co., Ltd.
China Eagle Scientific Park No.3 lane 7 E Lingnan Road Huizhou City, China
P.C: 516008 Telephone: 86.752.2288025
Fax : 86.752.2288054
光刻工艺资料整理

光刻工艺资料整理光刻工艺资料整理上一篇/ 下一篇 2007-12-10 20:10:25 / 个人分类:光刻查看( 121 ) / 评论( 0 ) / 评分( 0 / 0 )光刻工艺资料整理概述:光刻技术是集成电路的关键技术之一,在整个产品制造中是重要的经济影响因子,光刻成本占据了整个制造成本的35%。
光刻也是决定集成电路按照摩尔定律发展的一个重要原因,如果没有光刻技术的进步,集成电路就不可能从微米进入深亚微米再进入纳米时代。
所以说光刻系统的先进程度也就决定了光刻工程的高低。
1.光刻工艺简介光刻是通过一系列生产步骤将晶圆表面薄膜的特定部分除去的工艺。
在此之后,晶圆表面会留下带有微图形结构的薄膜,被除去的部分可能形状是薄膜内的孔或是残留的岛状部分。
光刻工艺也被称为大家熟知的Photomasking, masking, photolithography, 或microlithography。
在晶圆的制造过程中,晶体三极管、二极管、电容、电阻和金属层的各种物理部件在晶圆表面或表层内构成。
这些部件是每次在一个掩膜层上生成的,并且结合生成薄膜及去除特定部分,通过光刻工艺过程,最终在晶圆上保留特征图形的部分。
光刻生产的目标是根据电路设计的要求,生成尺寸精确的特征图形,并且在晶圆表面的位置正确且与其它部件(parts)的关联正确。
光刻是所有四个基本工艺中最关键的。
光刻确定了器件的关键尺寸。
光刻过程中的错误可造成图形歪曲或套准不好,最终可转化为对器件的电特性产生影响。
图形的错位也会导致类似的不良结果。
光刻工艺中的另一个问题是缺陷。
光刻是高科技版本的照相术,只不过是在难以置信的微小尺寸下完成。
在制程中的污染物会造成缺陷。
事实上由于光刻在晶圆生产过程中要完成5层至20层或更多,所以污染问题将会放大。
光刻工艺过程包括有:涂胶、前烘、曝光、显影、坚膜、腐蚀、去胶等。
课程内容:1 光刻前的准备工作1.1 准备要求1.2 准备方法1.2.1 光刻前待光刻片子置于干燥塔中1.2.2 氧化片出炉后可立即送光刻工序涂胶1.2.3 对氧化片可在涂胶前重吹段时间干氧(氧化温度)1.2.4 涂胶前片子置于80度烘箱中烘30分钟2 涂胶2.1 涂胶的要求2.2 涂胶的方法2.2.1 旋转涂胶法2.2.2 喷涂法2.2.3 浸涂法3 前烘3.1 前烘要求3.2 前烘的方法3.2.1 在80度烘箱中烘15分钟-20分钟3.2.2 在红外烘箱中烘3分钟-5分钟4 曝光4.1 曝光的要求4.2 曝光的方法5 显影5.1 显影的要求5.2 显影的方法6 坚膜6.1 坚膜的要求6.2 坚膜的方法6.2.1 置于恒温箱中,在180度烘30 分钟左右6.2.2 置于红外烘箱中烘10分钟左右7 腐蚀7.1 腐蚀的要求7.2 腐蚀的方法7.2.1 腐蚀二氧化硅的方法7.2.2 腐蚀铝电极的方法8 去胶8.1 去胶的要求8.2 去胶的方法课程重点:本节介绍了光刻工艺及对各光刻工艺步骤的要求。
光刻机工艺参数优化提高芯片制造一致性

光刻机工艺参数优化提高芯片制造一致性在芯片制造过程中,光刻技术起到了至关重要的作用。
光刻机是一种常用的光学仪器,用于将芯片设计图案转移到光刻层并形成准确的图案。
然而,由于光刻机工艺参数的设置不同,可能会导致生产出的芯片出现一致性差异。
为了提高芯片制造的一致性,需要对光刻机工艺参数进行优化。
一、光刻机工艺参数的作用光刻机工艺参数是指在光刻过程中调整的一些参数,包括光源能量、曝光时间、焦距调节、曝光模式等等。
这些参数对芯片的制造过程有着重要的影响。
1. 光源能量光源能量是指光刻机所使用的紫外光在单位面积上的能量值。
光源能量的大小直接影响着曝光的效果和芯片的分辨率。
若光源能量过高,容易造成图形形变或者产生曝光过度的现象;若光源能量过低,则可能无法完全曝光。
因此,调整光源能量可以在一定程度上优化芯片的制造一致性。
2. 曝光时间曝光时间是指芯片在光刻机中暴露在光源下的时间长短。
曝光时间的设置直接影响着芯片的光刻深度和光刻图案清晰度。
合理调整曝光时间可以提高芯片的制造一致性。
3. 焦距调节焦距调节是指通过调整光刻机的镜片焦距,来实现光源光斑与样品表面的最佳聚焦状态。
焦距的调整不仅影响芯片图案的清晰度,还会对芯片制造的一致性产生影响。
4. 曝光模式曝光模式是指光刻机中的曝光方式,通常分为连续曝光和间断曝光两种。
连续曝光模式适用于光刻图案较简单的情况,而间断曝光模式适用于光刻图案较复杂的情况。
选择合适的曝光模式可以提高芯片制造的一致性。
二、光刻机工艺参数优化方法为了提高芯片制造的一致性,可以通过以下几个方面对光刻机工艺参数进行优化。
1. 实时监测和反馈在光刻过程中,应实时监测光刻机的工艺参数,并对实际制造效果进行反馈。
通过比较实际制造出的芯片与设计图案的差异,可以及时调整光刻机的工艺参数,从而提高芯片的一致性。
2. 优化光刻机设备选择性能优秀、稳定可靠的光刻机设备是提高芯片制造一致性的关键。
光刻机的稳定性和精度对工艺参数的调整和优化有着重要影响。
制程涨缩管控制度
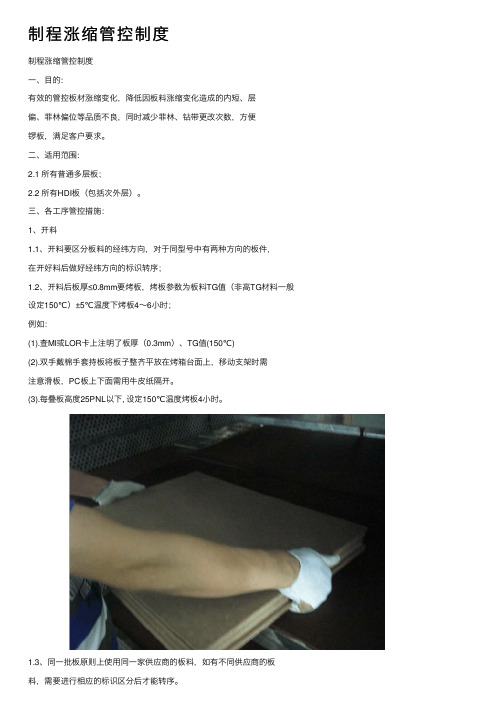
制程涨缩管控制度制程涨缩管控制度⼀、⽬的:有效的管控板材涨缩变化,降低因板料涨缩变化造成的内短、层偏、菲林偏位等品质不良,同时减少菲林、钻带更改次数,⽅便锣板,满⾜客户要求。
⼆、适⽤范围:2.1 所有普通多层板;2.2 所有HDI板(包括次外层)。
三、各⼯序管控措施:1、开料1.1、开料要区分板料的经纬⽅向,对于同型号中有两种⽅向的板件,在开好料后做好经纬⽅向的标识转序;1.2、开料后板厚≤0.8mm要烤板,烤板参数为板料TG值(⾮⾼TG材料⼀般设定150℃)±5℃温度下烤板4~6⼩时;例如:(1).查MI或LOR卡上注明了板厚(0.3mm)、TG值(150℃)(2).双⼿戴棉⼿套持板将板⼦整齐平放在烤箱台⾯上,移动⽀架时需注意滑板,PC板上下⾯需⽤⽜⽪纸隔开。
(3).每叠板⾼度25PNL以下, 设定150℃温度烤板4⼩时。
1.3、同⼀批板原则上使⽤同⼀家供应商的板料,如有不同供应商的板料,需要进⾏相应的标识区分后才能转序。
2、内层2.1、前处理磨板⽅向:同⼀型号同⼀机器同放板⽅向⽣产;2.2、菲林涨缩控制:2.2.1、内层所有菲林在上机前需要经过⼆次元测量合格(单⾯偏差±1mil,层偏1.2mil,⼆次元精度±0.2mil);2.3、PE值控制控制在 ±50um2.4、ME值控制控制在 ±25um2.5、层偏控制2.5.1、菲林上机前测量菲林的长度,上下菲林的长度差异值須控制在±35um以內,单张菲林的长度值与⼯程的理论预放值相差在±30um以內,超出以上的偏差范围需重新申请菲林;2.5.2 、菲林不使⽤时应将菲林膜⾯对膜⾯存放在专⽤的菲林袋中,放于菲林柜中,存放环境温度为22±2℃,湿度为55±5 %;2.5.3、内层线路图形层间对准度检验⽅法:⽣产⾸件及制程抽检(蚀刻后的板)由QA拍X-RAY,最低接受标准:同⼼圆偏差不能超过设计间距1/2 (按1/2 OZ底铜算蚀刻后的板约增加线路的补偿0.8-1mil间距),即同⼼圆偏差不超过1.5 mil,作好相关记录;(⼯程图转对位同⼼圆设计规则:相邻同⼼圆菲林设计间距为2.0mil。
光刻机显影过程优化实现微细加工高品质工艺

光刻机显影过程优化实现微细加工高品质工艺光刻技术是微电子制造过程中不可或缺的一项关键技术,而光刻机显影过程是光刻技术中的核心环节。
针对微细加工的需求和高品质工艺的要求,光刻机显影过程的优化显得尤为重要。
本文将探讨一些优化措施,以实现微细加工的高品质工艺。
1. 显影液的选择与优化光刻机显影过程中,显影液起着扩大图形尺寸并去掉曝光时产生的无用光刻胶的作用。
选择合适的显影液对于实现微细加工至关重要。
一般而言,酸性显影液适用于负光刻胶,而碱性显影液适用于正光刻胶。
此外,显影液的浓度、温度和显影时间也需要进行优化,以获得最佳的显影效果。
2. 显影参数的控制与调整显影参数的控制与调整是光刻机显影过程优化的关键步骤。
首先,曝光剂的剂量和光刻胶的厚度应相匹配,以确保曝光能够穿透光刻胶并形成清晰的图案。
其次,显影时间的控制需要根据光刻胶的类型和厚度进行调整。
如果显影时间过长,可能导致图案形变或失真;而显影时间过短,则可能导致图案不完全显影或被破坏。
此外,显影过程中的液体流速、气泡和杂质的控制也会影响显影结果的质量,需要密切关注和调整。
3. 显影机的维护与升级光刻机显影过程的优化还包括显影机的维护与升级。
定期的设备维护能够保持显影机的正常运行,减少设备故障对显影过程的影响。
并且,随着技术的发展,新型的显影机设备也在不断推出。
对于实现更高品质工艺的微细加工,升级显影机设备成为一个重要的选择,新的设备可能具备更稳定的显影条件和更先进的显影控制系统,从而提高整体工艺质量。
4. 光刻胶的选择与优化光刻胶作为光刻工艺的关键材料,直接影响着微细加工的质量和效果。
选择合适的光刻胶是优化显影过程的重要环节。
对于微细加工,常常要求更高的分辨率和更好的边缘清晰度。
因此,光刻胶的分辨率和边缘清晰度是选择的关键指标,同时还需要考虑耐化学性、工艺兼容性等因素。
此外,通过合适的曝光剂和显影液的搭配,也能够进一步优化光刻胶的性能和显影效果。
综上所述,光刻机显影过程的优化对于实现微细加工的高品质工艺至关重要。
IC制造中硅片边缘上光刻工艺的波动问题分析参考Word
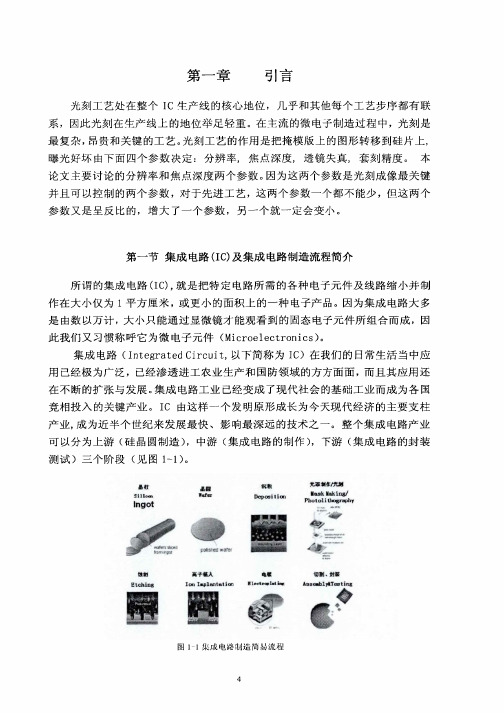
如不慎侵犯了你的权益,请联系我们告知!第一章引言光刻工艺处在整个IC 生产线的核心地位,几乎和其他每个工艺步序都有联系,国此光刻在生产线上的地位举足轻重。
在主流的微电子制造过程中,光刻是最复杂,昂贵和关键的工艺。
光刻工艺的作用是把掩模版上的图形转移到硅片上,曝光好坏由下面四个参数决定: 分辨率,焦点深度,透镜失真,套刻精度。
本论文主要讨论的分辨率和焦点深度两个参数。
因为这两个参数是光刻成像最关键并且可以控制的两个参数,对于先进工艺,这两个参数一个都不能少,但这两个参数又是呈反比的,增大了一个参数,另一个就一定会变小。
第一节集成电路 (IC )及集成电路制造流程简介所谓的集成电路(IC) ,就是把特定电路所需的各种电子元件及线路缩小并制作在大小仅为1 平方厘米,或更小的面积上的一种电子产品。
因为集成电路大多是由数以万计,大小只能通过显微镜才能观看到的固态电子元件所组合而成,因此我们又习惯称呼它为微电子元件(M ie r o e le c tr o n ie s ) 。
集成电路( 工nt eg r at ed C irc ui t,以下简称为1C ) 在我们的日常生活当中应用己经极为广泛,己经渗透进工农业生产和国防领域的方方面面,而且其应用还在不断的扩张与发展。
集成电路工业已经变成了现代社会的基础工业而成为各国竞相投入的关键产业。
IC 由这样一个发明原形成长为今天现代经济的主要支柱产业,成为近半个世纪来发展最快、影响最深远的技术之一。
整个集成电路产业可以分为上游 (硅晶圆制造) ,中游(集成电路的制作 ),下游( 集成电路的封装测试) 三个阶段( 见图1一1 )。
允. 翻作从洲多.,心口伪珍. 1 . 1. …k .比 1。
砂玲。
一0 11 目加甲. 目.,!n g o t神护只,燕,. 御于-位侧面子桩人二匆侧、封绍已t 比1习日 1 . 1 即 1 . t. l 五国,l o d .,,盆目洛. 如二山1 润I .T t i飞! I 犷‘夕图1一l 集成电路制造简易流程如不慎侵犯了你的权益,请联系我们告知!集成电路制作部分流程非常复杂,工艺流程一般都有几百上千个步骤,从开始流片到可以切割封装动辄需要几个月的时间。
光刻机对集成电路制造中的工艺参数调整
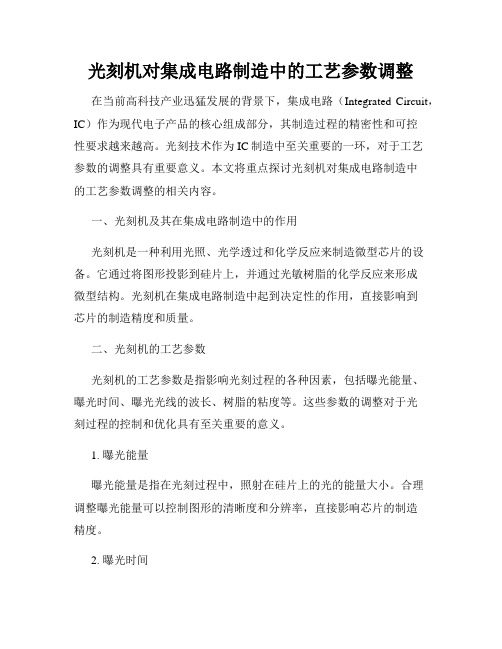
光刻机对集成电路制造中的工艺参数调整在当前高科技产业迅猛发展的背景下,集成电路(Integrated Circuit,IC)作为现代电子产品的核心组成部分,其制造过程的精密性和可控性要求越来越高。
光刻技术作为IC制造中至关重要的一环,对于工艺参数的调整具有重要意义。
本文将重点探讨光刻机对集成电路制造中的工艺参数调整的相关内容。
一、光刻机及其在集成电路制造中的作用光刻机是一种利用光照、光学透过和化学反应来制造微型芯片的设备。
它通过将图形投影到硅片上,并通过光敏树脂的化学反应来形成微型结构。
光刻机在集成电路制造中起到决定性的作用,直接影响到芯片的制造精度和质量。
二、光刻机的工艺参数光刻机的工艺参数是指影响光刻过程的各种因素,包括曝光能量、曝光时间、曝光光线的波长、树脂的粘度等。
这些参数的调整对于光刻过程的控制和优化具有至关重要的意义。
1. 曝光能量曝光能量是指在光刻过程中,照射在硅片上的光的能量大小。
合理调整曝光能量可以控制图形的清晰度和分辨率,直接影响芯片的制造精度。
2. 曝光时间曝光时间是指在光刻过程中图形曝光的时间,它与曝光能量直接相关。
曝光时间过短会导致曝光不足,影响芯片的制造质量;曝光时间过长则会导致曝光过度,影响芯片的制造精度。
3. 曝光光线的波长曝光光线的波长决定了曝光过程中的光的穿透深度和分辨率。
不同的芯片制造工艺对波长有不同的要求,因此根据具体要求调整波长是非常重要的。
4. 树脂的粘度树脂的粘度决定了其在曝光过程中的流动性和扩散性能。
粘度过高会导致图形边缘模糊,而粘度过低则会产生流动不均匀的问题。
合理调整树脂的粘度可以得到高质量的芯片结构。
三、光刻机对工艺参数的调整方法光刻机对于集成电路制造中工艺参数的调整,通常通过以下几种方法来实现:1. 预设参数调整光刻机可以事先根据具体芯片制造工艺的要求,通过预设参数的调整来优化曝光能量、曝光时间、曝光光线波长等工艺参数。
通过合理设置预设参数,可以达到较好的制造效果。
板件涨缩异常分析报告1
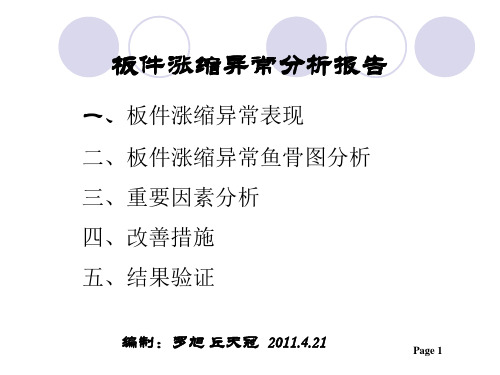
激光钻机:钻孔精度±20um 机械钻机:钻孔精度±3mil 问题点:如何保证钻孔精度,减少偏孔,
减少重出钻带?
Page 17
三、重要因素分析
(四)方法 1、基板是否烤板、及烤板参数
目前烤板参数:160℃*4小时 叠板厚度≤5cm
问题点:烤板参数是否合适,工序是否按 要求烤板,特别是叠板厚度?
Page 26
四、改善措施
(四)线路暗房 4、试验增加人员,用二维机预先测量每个料
号次外层、外层磨板后的板件,计算使用 菲林的倍率,并寻找菲林进行测量,找到 合适菲林( ±0.01% 可不重出);如无合 适菲 林,则根据测量板件的倍率重出菲林 5、工艺测量不同板厚次外层、外层钻孔后到 磨板后的板件涨缩变化,使预放更准确。
Page 10
三、重要因素分析
(三)设备 1、光绘房
光绘机:光绘菲林精度 贴保护膜机:贴膜参数:速度、压力 二维机:测量精度 问题点1:光绘机、二维机精度有偏差或贴保护
膜机参数有变化,将影响菲林尺寸。 光绘机、二维机精度有无定期校正?
Page 11
三、重要因素分析
(三)设备 1、光绘房
问题点2:内层菲林涨缩管控±2mil,上下菲林 对应边偏差≤1.5mil,光绘后抽测, 返单板全测。公差±2mil是否偏大? 抽测内层菲林,实际有超出±2mil。
问题点2:温度恒定时,湿度升高,菲林尺寸 膨胀,变化率0.001%/1% ,不可逆
Page 6
三、重要因素分析
(二)环境 1、菲林房温湿度: 温度22±2℃
湿度 55±5% 2、线路暗房温湿度:同上 3、阻焊暗房温湿度:同上 问题点:线路、阻焊暗房和菲林房温湿度若
集成电路工艺缩小的定义
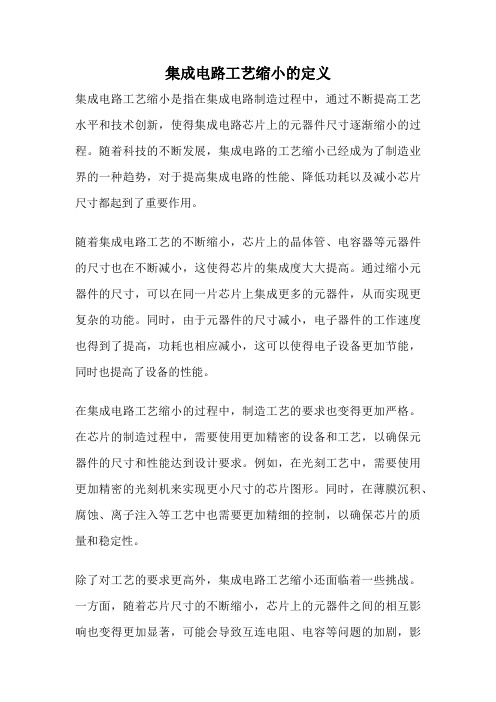
集成电路工艺缩小的定义集成电路工艺缩小是指在集成电路制造过程中,通过不断提高工艺水平和技术创新,使得集成电路芯片上的元器件尺寸逐渐缩小的过程。
随着科技的不断发展,集成电路的工艺缩小已经成为了制造业界的一种趋势,对于提高集成电路的性能、降低功耗以及减小芯片尺寸都起到了重要作用。
随着集成电路工艺的不断缩小,芯片上的晶体管、电容器等元器件的尺寸也在不断减小,这使得芯片的集成度大大提高。
通过缩小元器件的尺寸,可以在同一片芯片上集成更多的元器件,从而实现更复杂的功能。
同时,由于元器件的尺寸减小,电子器件的工作速度也得到了提高,功耗也相应减小,这可以使得电子设备更加节能,同时也提高了设备的性能。
在集成电路工艺缩小的过程中,制造工艺的要求也变得更加严格。
在芯片的制造过程中,需要使用更加精密的设备和工艺,以确保元器件的尺寸和性能达到设计要求。
例如,在光刻工艺中,需要使用更加精密的光刻机来实现更小尺寸的芯片图形。
同时,在薄膜沉积、腐蚀、离子注入等工艺中也需要更加精细的控制,以确保芯片的质量和稳定性。
除了对工艺的要求更高外,集成电路工艺缩小还面临着一些挑战。
一方面,随着芯片尺寸的不断缩小,芯片上的元器件之间的相互影响也变得更加显著,可能会导致互连电阻、电容等问题的加剧,影响芯片的性能。
另一方面,芯片制造过程中的杂质、缺陷等问题也会变得更加严重,可能会导致芯片的故障率增加,影响芯片的可靠性。
为了克服这些挑战,制造商不断进行技术创新,推动集成电路工艺的进步。
例如,引入新的材料、工艺,优化制造流程,改进设备等措施,都可以帮助提高芯片的质量、稳定性和性能。
同时,通过模拟仿真、实验验证等手段,也可以及时发现和解决潜在的问题,确保芯片制造过程的顺利进行。
总的来说,集成电路工艺缩小是集成电路制造领域的一种趋势,通过不断提高工艺水平和技术创新,可以实现芯片性能的提升、功耗的降低以及芯片尺寸的减小。
虽然在工艺缩小的过程中会面临一些挑战,但通过技术创新和不断努力,相信集成电路制造业会迎来更加美好的未来。
- 1、下载文档前请自行甄别文档内容的完整性,平台不提供额外的编辑、内容补充、找答案等附加服务。
- 2、"仅部分预览"的文档,不可在线预览部分如存在完整性等问题,可反馈申请退款(可完整预览的文档不适用该条件!)。
- 3、如文档侵犯您的权益,请联系客服反馈,我们会尽快为您处理(人工客服工作时间:9:00-18:30)。
光刻版数据处理中的工艺涨缩问题
1引言
集成电路(IC)是现代信息技术的核心和电子整机的心脏。
硅基集成电路的平面工艺和图形光刻仍然是当今大规模集成电路生产中的主流技术。
集成电路制造公司采用光刻机将光刻版上的图形投影到硅片或其他半导体材质上。
一般一个集成电路芯片的生产需要许多光刻版套刻而成(常常是6到20多层)。
光刻版是集成电路生产中的关键工具,其质量直接决定了最终集成电路产品的成败。
光刻版,有时也称为光掩模或者光罩,通常为高纯度精密石英玻璃版,上面载有金属铬形成的集成电路图形。
2 光刻版数据处理
在集成电路设计公司将集成电路设计出带(Tapeout)后,就可以从版图得到光刻图形生产光刻版了。
从设计公司出带的版图得到生产光刻版所需要的光刻图形的过程称为光刻版数据处理。
从版图图形到光刻版图形有下列方法:
●直接对应
一块光刻版直接与版图中的某一层直接对应。
例如,金属层对应某版图中的第7层。
●逻辑运算
一块光刻版与版图中的某些层对应,是它们逻辑运算的结果。
例如,通常p+注入层与N+注入层的图形是互补的。
这样在版图中可能只有P+注入层(PPLUS)的图形,p +注入层的光刻版可以直接从该层版图图形而来,而n +注入层的光刻版则从PPLUS层版图经过逻辑“非”运算就可得到。
在光刻版数据处理中逻辑“非”运算可以通过反转来实现。
有时某层光刻版图形是好几层版图图形相加的结果,则是将这些层进行逻辑“或”运算。
●图形涨缩
一块光刻版由版图中的某种图形拓展而来。
例如,通常在MOS器件的版图中只画有栅区图形而没有栅注入图形,栅注入层的光刻版图形是由版图中的栅区图形拓展一定量得到,在光刻版数据处理中可以通过对栅区图形进行正涨缩处理来得到栅注入层的图形。
完整的能直接用于生产的光刻版除了包括与电路一致的图形外还包括许多辅助图形。
常见的辅助图形包括:
●游标
●光刻对准图形
●曝光量控制图形
●关键尺寸监测图形
●测试键图形
●光学对准目标图形
●划片槽图形
●其他辅助图形,例如器件名称、光刻版序号、厂家商标和版号日期等。
这些图形有的是由集成电路设计公司提供,例如大部份的测试键图形, 有的是由集成电路代工厂提供,例如游标,关键尺寸监测图形,曝光量控制图形等,还有的是光刻版工厂自己提供的图形,例如光刻版工厂自己的商标,版号日期等。
对这些图形也要进行相应的数据处理以使他们符合生产工艺的要求。
3正涨缩与负涨缩问题
图形涨缩是光刻版数据处理中重要的一个步骤。
所谓涨缩是指图形上的数据区根据涨缩量向里收缩或向外拓展。
通常图形需要涨缩是基于两方面的要求:
●集成电路设计公司版图设计的要求。
在上面提到的某些层的版图是由另外一层版图经过周边拓展而得到的,这时需要通过涨缩来实现;
●集成电路代工厂工艺的要求。
同样的版图在不同的代工厂之间或同一代工厂不同工艺间,光刻出的图形是有偏差的,这时需要在光刻版上进行对应的补偿。
涨缩包括正涨缩和负涨缩。
进行正涨缩的情形有:
●例如,MOS器件中,由集成电路设计公司
版图设计中,若只有栅区图形,则栅注入图形可以通过栅区图形进行正涨缩得到;
●在集成电路代工厂的生产中,例如对线条图形,在光刻过程中,经过曝光,显影,去胶,后烘,在硅片上得到的最终图形会比光刻版的图形小。
这种偏差可以通过在光刻版上对该层图形进行正涨缩得到补偿,具体的涨缩量由工艺决定。
进行负涨缩的情形有:
●例如,MOS器件中,由集成电路设计公司版图设计中,若只有栅注入图形,则栅区图形可以通过栅注入图形进行负涨缩得到;
●在集成电路代工厂的生产中,例如对孔层图形,在光刻过程中,经过曝光,显影,去胶,后烘,由于光的衍射作用和光刻胶去胶过程中的工艺处理,在硅片上得到的最终图形会比光刻版上的图形大。
这种偏差可以通过在光刻版上对该层图形进行负涨缩得到补偿,具体的涨缩量由工艺决定。
示意图如图1所示:
4涨缩与反转处理的次序问题
在数据处理中,反转也是重要的一个步骤。
例如在上面提到的n+注入层图形可以通过对p +注入层的图形进行反转处理而得到,反之,p +注入层图形可以通过对n+注入层的图形进行反转处理而得到。
另外,有时由于正胶工艺和负胶工艺同时存在,对某些层需要同时制作正版与反版。
进行反转操作时,需要根据芯片尺寸画号反转框,反版可以通过几个方式得到:
●将反转框与原始图形进行异或逻辑运算(XOR),得到反转图形。
这种运算与图形顺序无关。
由于反转框是数据区,用逻辑“1”代表,原始图形用A代表,该逻辑运算表示为:
1 XOR A =(1 AND !A) OR (0 AND A) = !A (1)
A XOR 1 =(A AND 0) OR (!A AND 1) =!A (2)
由上面的推导可知,式(1) 和(2) 式的逻辑运算结果相同,该种逻辑运算能得到反转图形,且与图形顺序无关。
●将反转框与原始图形进行与非逻辑运算(AND NOT) ,得到反转图形。
这种运算与图形顺序相关。
1 AND NOT A =NOT A = !A (3)
A AND NOT 1 =A AND 0 = 0 (4)
由上面的推导可知,式(3) 的逻辑运算能得到反转图形,即反转框在前而原始图形在后。
式(4) 的逻辑运算则得不到反转图形。
当对某层图形需要同时进行涨缩和反转操作时,由于涨缩运算只是在数据区进行,涨缩与反转的次序就会影响最终的图形。
错误的次序将导致严重后果,生产出来的光刻版将是废品。
例如,某层图形需要反转,涨缩量是-0.35mm, 先涨缩再反转和先反转再涨缩的图形示意图如图2所示。
由于涨缩是在数据区发生作用的,两者操作次序导致最终的结果是图形相差达0.7μm。
正确的次序应当是先涨缩再反转。
5涨缩时位于边沿的图形的处理
当图形处于芯片的边沿时,进行涨缩处理时必须考虑这些图形涨缩前后的特性。
进行正涨缩时,这些图形可能超出芯片范围而进行负涨缩时则会使这些图形偏离芯片边沿。
例如在引脚层(PAD) ,各个引脚基本上处于芯片边沿,该层进行正涨缩和负涨缩的示意图如图3所示。
工艺上要求图形在涨缩之后仍然在芯片范围之内而且PAD仍然是紧贴在芯片边沿。
对于正涨缩时图形超出芯片范围和负涨缩时图形偏离芯片边沿,必须进行图形补偿。
另外在图形涨缩之前,必须进行图形合并。
在这里,合并运算是必须进行的一个步骤。
否则负涨缩将导致图形分离,若将这样的光刻版用于集成电路生产,将形成电路的断路,导致产品报废。
图4所示的是合并对负涨缩运算的影响:
6 实际应用
目前已经有些商业EDA软件应用在光刻版数据处理中,例如Numerical Technologies 公司的CATS软件。
另外CADENCE 公司的Virtuoso 软件也可以进行一部份的光刻版数据处理。
在我们自己开发的MaskShop软件中,对图形涨缩,反转等问题进行了专门的处理,其处理出来的光刻版图形已应用在5009和6012两种型号的光刻版生产中,所生产出的光刻版已经得到了集成电路代工厂的认证,用于集成电路的生产。
7 结束语
目前大多数的IC设计EDA软件主要侧重于逻辑综合,布局和布线以及验证,不适合直接用于光刻版数据处理。
已有的专门用于光刻版数据处理的商业EDA软件比较少且价格昂贵,其内部处理机制也属商业秘密范围。
我们通过研究,将光刻版数据处理的特殊性包括在自己开发的EDA软件中并且在实际生产中得到了验证。
当然光刻版数据处理还有许多问题仍需进一步解决,例如芯片布局和图形插入的自动化问题等。
光刻版数据处理EDA软件将朝着更加自动化,智能化的方向发展。