冷轧辊的失效分析上课讲义
冷轧培训讲义讲解

第六章 冷轧调整
? 送进制度: ? 合理选择管料的送进量是保证生产达到高产、优质、低消耗的重要途
径。生产实践表明,在一定范围内,送进量越大,生产率越高。 但超 过一定的值,就会产生相反的结果。送进量过大会增加轧机的负荷, 破坏更严重的是会恶化钢管的表面质量,如:产生飞边、波纹、壁厚 不均、外径精度不高。送进量的大小根据:钢种、成品精度来确定。 一般情况下,轧制T23 、T91 、钢102 送进量小于6mm ;轧制 12Cr1MoVG 送进量小于8mm ;轧制其他钢种小于10mm 。 ? 2、轧机的调整 ? 轧机的调整是轧制工艺的重要组成部分。调整的正确与否直接影响钢 管的质量、工具的寿命、轧机的生产率。 ? 2.1 轧辊中心的调整(更换新的轧辊总成时,才需调整) ? 西重所轧机:上轧辊的辊环左侧边到机架的距离为 75mm 。
? 4、受工具和工艺要求的限制,品种不能多样化,宜于单一品种的大 批量生产。这主要是指冷轧机受轧辊规格及更换不方便而限制的。目 前,我们分厂引进的冷轧机主要是西安重型研究所冷轧机和上海攀枝 花冷轧机,而西安重型研究所冷轧机包括一台 LG60 冷轧机,一台 LG90 冷轧机;上海攀枝花冷轧机包括 8台LG60 冷轧机,4台 LG110 冷轧机。
第四章 冷轧钢管的变形
? 冷轧பைடு நூலகம்管的变形
预精整2°0
减径段
m
m
第四章 冷轧钢管的变形
? 当工作机架在后死点时,管料被送进一段 m,工作锥的内表面与芯棒 脱离,形成间隙,当机架向前移动,工作锥的外径先减小到内表面与 芯棒接触,然后外径和壁厚才同时压缩,轧制过程中,工作锥的内表 面与芯棒总存在间隙,间隙从管坯到成品是逐渐减小的。当机架到前 死点时,一个正行程结束。回转一个角度后,进行返行程。这就是一 个轧制循环。
分析冷轧轧辊的失效及维护
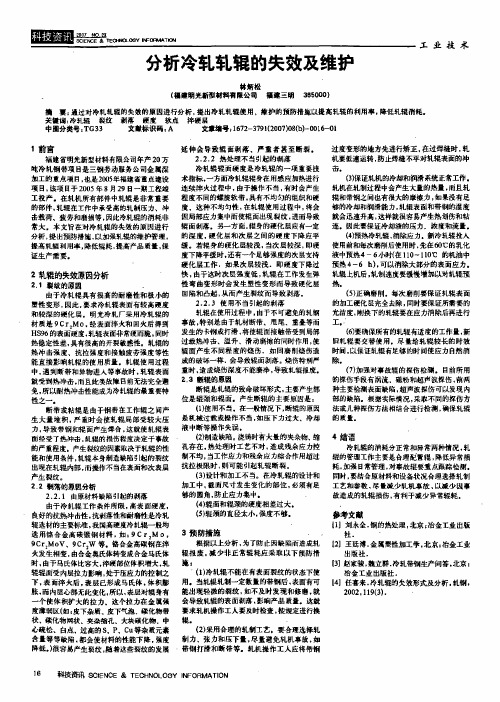
S}N E!COFF}件 CC.T lLVOT o o QOI M IN. EE A
—
林 炳松
工业技、
分 析 冷 轧 轧 辊 的 失 效 及 维 护
‘ 福趁明光断型材料有: 通过对冷轧轧辊的失效的原因进行分析, 提出冷轧轧辊使用、 维护的预防措施以提高轧辐的利用率 , 降低轧辊消耗. 关锐词 冷轧辊 裂纹 剥落 硬度 软点 淬硬层 中图分类号: TG33 文欲标识码: A 文班编号:1672- 3791(2007)08(b卜0016- 0 1 延伸会导致辊面剥落、严重者甚至断裂。 过度变形的地方先进行矫正, 在过焊缝时, 轧 2 .2 .2 热处理不当引 起的剥落 机要低速运转 , 防止焊缝不平对轧辊表面的冲 冷轧辊辊面硬度是冷轧辊的一项重要技 击。 术指标一 方面冷轧辊辊身在用感应加热进行 (3)保证轧机的冷却和润滑系统正常工作. 连续淬火过程中, 由于操作不当 , 有时会产生 轧机在轧制过程中会产生大t 的热I , 而且轧 程度不同的螺旋软带.具有不均匀的组织和硬 辊和带钢之间也有很大的章擦力, 如果没有足 度、这种不均匀性, 在轧辊使用过程中, 将会 够的冷却和润滑能力 轧辊表面和带钢的温度 因局部应力集中而使辊面出现裂纹, 进而导致 就会迅速升高, 这样就很容易 产生热划伤和粘 辊面剥落. 另一方面, 提身的硬化层应有一定 连。因此要保证冷却液的压力,浓度和流t . 的深度, 硬化层和次层之间的硬度下降应平 (4)预热冷轧辊,消除应力。新冷轧辊投人 缓。若辊身的硬化层较浅. 当次层较深, 即硬 使用前和每次磨削后使用时 先在60℃的乳化 度下降平缓时, 还有一个足够强度的次层支持 液中预热4 一6 小时(在110 - 110℃ 的机油中 证 生产 需 要. 硬化层工作. 如果次层较浅. 即硬度下降过 预热 4 - 6 h ) 。 可以消除大部分的表面应力. 快, 由于这时次层强度低, 轧辊在工作发生弹 轧辊上机后, 轧制速度要缓慢增加以对轧银预 2 轧辊的失效原因分析 性有曲变形时会发生塑性变形而导致硬化层 热。 2. 1 裂纹的原因 凹陷和凸起, 从而产生裂纹而导致剥落。 (5)正确磨削。每次磨削要保证轧辊表面 由子冷轧辊具有很高的耐磨性和极小的 2 . 2. 3 使用不当引起的剥落 的加工硬化层完全去除 , 同时要保证所需要的 塑性变形, 因此, 要求冷轧辊表面有较高硬度 轧辊在使用过程中, 由于不可避免的轧钢 光洁度, 刚换下的轧辊要在应力消除后再进行 和较深的硬化层。明光冷轧厂采用冷轧辊的 特别是由于轧材断带、甩尾,重盛等而 工。 材 质是9Cr,Mo, 经表 火和回 后得到 事故, 面淬 火 将使辊面接触带受到局部 (6)要确保所有的轧辊有适度的工作最, 新 HS96 的表面硬度, 轧辊表面非常硬而脆, 同时 发生的卡钢或打滑 , 滑动磨擦的同时作用, 使 旧轧辊要交替使用. 尽量给轧辊较长的时效 热德定性差, 具有很高的开裂敏感性。轧辊的 过载热冲击,温升 、 辊面产生不同程度的烧伤 如同磨削烧伤造 时间. 以保证轧辊有足够的时间使应力自 然消 热冲击强度、抗拉强度和接触疲劳强度等性 烧伤特别严 除。 能直按影响轧辊的使用质且。轧辊使用过程 成的破坏一样. 会导致辊面剥落。 重时, 造成烧伤深度不能磨净, 导致轧辊报废。 (, )加强对事故辊的探伤检测. 目 前所用 中, 遇到断带和异物进人等事故时, 轧辊表面 的裸伤手段有涡流 磁粉和超声波探伤, 前两 就受到热冲击, 而且此类故陈目前无法完全遴 2 .3 断辊的原因 断辊是轧辊的致命破坏形式 , 主要产生部 种主要检测表面缺陷, 超声波探伤可以发现内 免, 所以耐热冲击性能成为冷轧辊的最重要特 位是辊颈和辊面。产生断辊的主要原因是: 性之一 。 部的缺陷。根据实际情况, 采取不同的探伤方 (1)使用不当。在一般情况下, 断辊的原因 法或几种探伤方法相结合进行检测, 确保轧辊 断带或粘辊是由于钢带在工作辊之间产 是机械过载或操作不当, 如压下力过大、冷却 的 质t . 生大I 堆积, 严重时会使轧辊局邹受较大压 力, 导致带钢和辊面产生焊合, 这就使轧辊表 掖 中断等操作失误。 (2)制造缺陷。 浇铸时有大量的夹杂物、 缩 4 结语 面经受了热冲击, 轧粗的损伤程度决定于事故 孔存在, 热处理时工艺不对 , 造成残余应力控 的严重程度. 产生裂纹的因泰取决于轧辊的性 冷轧辊的消耗分正常和异常两种情况, 轧 当工作应力和残余应力综合作用超过 辊的管理工作主要是合理配置辊 , 降低异常损 能和使用条件, 轧辊本身制造缺陷引起的裂纹 制不均, 耗.加强日 常管理, 对卒故辊要重点服踪检测. 出现在轧辊内部, 而操作不当在表面和次表层 抗拉极限时 则可能引起轧辊断裂。 (3)设计和加工不当。在冷轧辊的设计和 产生 裂纹 。 同时 , 要结合原材料和设备状况合理选择轧制 加工中, 截面尺寸发生变化的部位, 必须有足 2.2 侧落的原因分析 工艺和参数, 尽垦减少轧机事故、 以减少因事 够的圆角, 防止应力集中。 故造成的轧辊损伤 , 有利于减少异常辊耗。 2. 2. 1 由原材料缺陷引起的剥落 (4)辊面和辊颈的硬度相差过大。 由于冷轧辊工作条件所限, 高表面硬度, (5)辊颈的直径太小 .强度不够。 良好的杭热冲击 , 性 抗剥落性和耐磨性是冷轧 参考文献 辊选材的主要标准, 我国高硬度冷轧辊一般均 川 刘永全.钢的热处理, 北京:冶金工业出版 3 预 防措施 社. 选 铬 金 碳 钢 料 如 Cr 2 , 用 合 高 锻 材 , :9 Mo 根据以上分析, 为了防止因缺陷而造成轧 [2」王廷薄.金属塑性加工学, 北京:冶金工业 9Cr2 MoV, 9Cr,W等 铬 金 碳 在 . 合高钢淬 辊报废, 减少非正常辊耗应采取以下预防措 火发生相变 , 由合金奥氏体转变成合金马氏体 出版社 . 时, 由于马氏体比容大, 淬硬部位体积增大, 轧 施: [3] 赵家骏, 魏立群.冷轧带钢生产问答.北京: (1)冷轧辊不能在有表面裂纹的状态下使 辊辊面受内层拉力影响, 处于压应力的控制之 冶金工业 出版社. 下, 表面淬火后, 表层已形成马氏体, 体积膨 用。当轧恨轧制一定数I 的带钢后, 表面有可 [4〕任喜来.冷轧辊的失效形式及分析.轧钥, 胀, 而内层心部无此变化, 所以, 表层对辊身有 能出现轻微的裂纹 , 如不及时发现和修磨, 就 2002. 119(3) . 会导致轧辊的表面剥落.影响产品质t . 这就 一个使体积扩大的拉力、这个拉力在金属强 度薄弱区(如:皮下杂质、皮下气泡. 碌化物带 要求轧机操作工人要及时检查, 按规定进行换 状、 碳化物网状、夹杂缩孔、 大块碳化物. 中 辊。 (2)采用合理的轧祠工艺. 要合理选择轧 心硫松、白点、过高的S, P , Cu 等杂质元素 含f 等等缺陷, 都会使材料的性能下降, 强度 制力、张力和压下f . 尽1 7 免轧机事故, A 如 降低。 )很容易产生裂纹, 随着这些裂纹的发展 带钢打滑和断带等。轧机操作工人应将带钥 ,前言 福建省明光新型材料有限公司年产20 万 吨冷轧钢带项 目 是三钢劳动服务公司金属深 加工的重点项 目, 也是2005年福建省孟点建设 项目, 该项目于2005 年8 月29 日一期工程竣 工投产。在轧机所有部件中轧辊是非常重要 的部件, 轧辊在工作中承受高的轧制压力、冲 击载荷、疲劳和磨损等, 因此冷轧辊的消耗非 常大. 本文旨在对冷轧辍的失效的原因进行 分析, 提出预防措施, 以加强轧辊的维护管理, 提高轧辊利用率, 降低辊耗, 提高产品质I , 保 L 16 科 技资讯 S CIEN & TECHN CE OLOGY IN O ATION F RM
轧辊失效方式及其原因分析

轧辊失效方式及其原因分析轧机在轧制生产过程中,轧辊处于复杂的应力状态。
热轧机轧辊的工作环境更为恶劣:轧辊与轧件接触加热、轧辊水冷引起的周期性热应力,轧制负荷引起的接触应力、剪切应力以及残余应力等。
如轧辊的选材、设计、制作工艺等不合理,或轧制时卡钢等造成局部发热引起热冲击等,都易使轧辊失效。
轧辊失效主要有剥落、断裂、裂纹等形式。
任何一种失效形式都会直接导致轧辊使用寿命缩短。
因此有必要结合轧辊的失效形式,探究其产生的原因,找出延长轧辊使用寿命的有效途径。
1 、轧辊剥落(掉肉)轧辊剥落为首要的损坏形式,现场调查亦表明,剥落是轧辊损坏,甚至早期报废的主要原因。
轧制中局部过载和升温,使带钢焊合在轧辊表面,产生于次表层的裂纹沿径向扩展进入硬化层并多方向分枝扩展,该裂纹在逆向轧制条件下即造成剥落。
1.1 支撑辊辊面剥落支撑辊剥落大多位于轧辊两端,沿圆周方向扩展,在宽度上呈块状或大块片状剥落,剥落坑表面较平整。
支撑辊和工作辊接触可看作两平行圆柱体的接触,在纯滚动情况下,接触处的接触应力为三向压应力。
在离接触表面深度为 0.786b 处 ( b 为接触面宽度之半 ) 剪切应力最大,随着表层摩擦力的增大而移向表层。
疲劳裂纹并不是发生在剪应力最大处,而是更接近于表面,即在 Z 为 0.5b 的交变剪应力层处。
该处剪应力平行于轧辊表面,据剪应力互等定理,与表面垂直的方向同样存在大小相等的剪应力。
此力随轧辊的转动而发生大小和方向的改变,是造成接触疲劳的根源。
周期交变的剪切应力是轧辊损坏最常见的致因。
在交变剪切应力作用下,反复变形使材料局部弱化,达到疲劳极限时,出现裂纹。
另外,轧辊制造工艺造成的材质不均匀和微型缺陷的存在,亦有助于裂纹的产生。
若表面冷硬层厚度不均,芯部强度过低,过渡区组织性能变化太大,在接触应力的作用下,疲劳裂纹就可能在硬化过渡层起源并沿表面向平行方向扩展,而形成表层压碎剥落。
支撑辊剥落只是位于辊身边部两端,而非沿辊身全长,这是由支撑辊的磨损型式决定的。
轧辊的失效及其修复技术

轧辊的失效及其修复技术摘要:轧辊生产率与生产成本都取决于轧制的生产质量,当轧辊不足供应,价格高时,整个轧辊都会磨损失效,这会导致大量的材料报废。
轧辊的修复是轧辊行业的主要问题。
过早磨损最常见轧辊失效的原因,轧辊的工作表面的硬度取决于耐磨性,正确的热处理符合辊的硬度要求。
轧机是轧辊变形的主要工具。
通过自己的材料和恶劣的工作条件,延长寿命需要修复技术,失效甚至报废。
概述了轧辊的工作条件、材料和失效,介绍了几种常见的修复技术。
关键词:冷轧辊热轧辊;失效修复;表面改性技术引言激光处理技术在钢铁工业中的应用越来越多。
随着钢铁工业的复苏和世界钢需求量的增加,我国的钢铁产量目前地位领先。
轧辊消费量大幅增加,进一步提高了产量和质量。
与此同时,各种新角色正在应用于钢铁行业。
因此,轧辊的修复和化是钢铁工作者和激光设备的一个重要问题。
减少组件消耗会对企业的生产成本和经济性产生积极影响,并提供显着的成本节约机会。
目前,激光用于加固和修复辊面,引起了业界的关注。
1轧辊的损坏形式1.1正常磨损轧辊金属微粒在轧制和磨削过程中辊身分离,工作层变薄,直径较小,吨位随磨辊次数的增加而减小。
如果直径太小,以致于表面硬度降低到某个特定值,则即使没有其他缺陷(自然磨损或正常磨损),辊也无法继续工作。
这种磨损是可预见的,也是有风险的,最危险的损害通常是非正常磨损。
1.2非正常损坏如果辊的直径和表面硬度仍处于连续运转状态,则由于另一个缺陷甚至断裂,无法使用,这称为“非正常”和“特殊损坏”,具体由:(1)表面裂纹。
冷轧辊的裂纹分别为60%和20%,且裂纹的区域通常位于辊的中心。
裂缝有所不同的概率大致相同。
轧辊的制造质量对裂缝的形成和扩大至关重要。
因此,减少裂纹是提高轧辊的制造质量的关键。
例如,碎裂是轧槽经轧制过程中的冷热影响以及钢坯的磨损较低,导致轧槽表面上出现网格裂纹,从而导致断裂。
冷却水压力不足可能导致裂内部的汽化扩张力大,有助于增加裂缝。
包钢薄板厂冷轧工作辊剥落失效分析

i p vd m aue l h s c o , dn cn ea dr l m ae e t m r e esls i t i p t n  ̄n g t h i l n ng m n . o ' O e ne i i e q n o u
Ke wo d : r l o od r i n ; p lig;mp v d m e s rs y r s wok r sf rc l lg s al o o i n i r e a u e o
W N og—y n Z A G Qa Y N u A GH n a ,H N i n,A GJ n—x ̄t ur
( S ln o t l no o 1d o atuS e Gop o , at 10 0 N i ng l C ia C P PatfSe i C .z . eU n fB o t l( ru )C r B o u04 1 , e Mog o , hn ) o e p. o
看出,支剥落轧辊都是 5 r 3 C 锻钢轧辊 , 都曾经历过断带或 粘钢事故 , 事故后轧辊的磨削量(, 1 r ) 比正常磨削 49 3 唧 都 , 量(. 砌 ) O2 5 大得多。磨削后 的轧辊都是经过涡流探伤检 测合格才 E 机使用的。检查轧辊换辊卡片 , 表明轧辊都是
按要求的换辊周期换辊, 没有超期服役的现象。
呈放 射状 、 与辊面 成小 角度倾 斜 的瞬 间断裂 区, 是 像 蝴蝶 的一对 翅膀 。 12 剥落轧 辊 的数据 调查 . 剥落轧辊的生产数据调查情况表见表 1由表 1 , 可以
两种 材质 的轧 辊 。2 0 0 6年 8月 , 轧机 组 断 带 和粘 冷 钢 事故频 繁 , 接连 发生 了 3支 工作辊 剥落 的事故 , 直 接导 致轧 辊报 废 , 轧 辊 辊耗 急 剧 上 升 。本 文就 对 使 这 3 冷 轧工作 辊 的剥落 原 因进 行 分析与研 究 。 支
轧辊轴承失效分析及处理措施

动装置,其 中工作机坐由轧辊 、轧辊轴承
、
机架 、轨 座 、轧辊调 整装 置 以及 上轧辊
平衡装置和换辊装置等组成 . 轧辊轴承支 承 轧辊 并 保持 轧辊 在 机架 中的 固定位 置 。 轧 辊轴 承工作 负荷重而 变化 大 ,因此要求 轴 承摩 擦 系数小 ,具有 足够 的强度 和刚度 而且要便于更换轧辊。不同的轧机选用 不同类型的轧辊轴承。滚动轴承的刚性大 摩擦 系数 较小 ,但承 压能力 较小 ,且外 形 尺寸较 大 ,多用 于板 带轧机 工作辊 。滑 动 轴承有半 干 摩擦与液 体摩擦 两种 。半干 摩 擦轧辊轴 承 主要是胶 木 、铜 瓦 、尼龙瓦 轴 承 ,比较 便宜 ,多用 于型材 轧机 和开坯 机 。液体摩 擦轴 承有动 压 、静 压和静 一 动 压 三种 。优 点是 摩擦 系数 比较 小 ,承压能 力 较大 ,使 用工 作速度 高 ,刚性好 ,缺点 是 油膜厚度 随 速度而变 化 。液体摩 擦轴 承 多 用于板 带轧机 支承辊 和其 它高速 轧机 。
成轧 机 中的轧 辊轴 承的 失效原 因进 行分 析介 绍并提 出 了一 些应 对措 施 。 关键 词 :轧辊 轴承 ;失 效 ;应 对措 施 中圈分类 号 :T H 1 3 文献标 识码 :A ( 2) } 闰 滑 管路 布设不 当造 成的油 路不 畅 ,
我 国 是 一个 新 兴 的发 展 中 国家 ,在 柱滚子 轴承 和单列 向心 球轴 承等组 成 ,在
Hale Waihona Puke 国家的建设过程 中对于钢材的需求量巨 大 ,轧 机 是 实 现 金 属 轧 制 过 程 的 设 备 , 在 钢材 的成 型方 面 起 着非 常重 要 的作 用 , 轧辊 轴承作 为轧机 中的重要组 件 ,在 使用 过程 中会 由于各 种原 因造成失 效 ,从 而影 响轧机的正常使用 ,本文将对轧机轧辊轴 承 的失效原 因 以及 应对 措施等 进行介 绍 。 1 轧 机的轧辊 轴 承简介 轧 机 是 实 现金 属 轧 制 过 程 的设 备 。 泛指 完成轧 材生 产全过 程 的装 备 ,包 括有 主要 设备 、辅 助设 备 、起 重运 输设 备和附
轧辊失效方式及其原因分析

轧辊失效方式及其原因分析摘要:介绍了轧辊存在剥落、断裂、裂纹等几种失效方式,并重点分析了轧辊剥落和断裂产生的机理,为分析生产实践中轧辊失效原因和采取相应改进措施以提高轧辊使用寿命提供了依据。
关键词:轧辊;失效原因;剥落;断裂;裂纹1 前言轧机在轧制生产过程中,轧辊处于复杂的应力状态。
热轧机轧辊的工作环境更为恶劣:轧辊与轧件接触加热、轧辊水冷引起的周期性热应力,轧制负荷引起的接触应力、剪切应力以及残余应力等。
如轧辊的选材、设计、制作工艺等不合理,或轧制时卡钢等造成局部发热引起热冲击等,都易使轧辊失效。
轧辊失效主要有剥落、断裂、裂纹等形式。
任何一种失效形式都会直接导致轧辊使用寿命缩短。
因此有必要结合轧辊的失效形式,探究其产生的原因,找出延长轧辊使用寿命的有效途径。
2 轧辊的失效形式2.1 轧辊剥落轧辊剥落为首要的损坏形式,现场调查亦表明,剥落是轧辊损坏,甚至早期报废的主要原因。
轧制中局部过载和升温,使带钢焊合在轧辊表面,产生于次表层的裂纹沿径向扩展进入硬化层并多方向分枝扩展,该裂纹在逆向轧制条件下即造成剥落。
2.1.1支撑辊辊面剥落支撑辊剥落大多位于轧辊两端,沿圆周方向扩展,在宽度上呈块状或大块片状剥落,剥落坑表面较平整。
支撑辊和工作辊接触可看作两平行圆柱体的接触,在纯滚动情况下,接触处的接触应力为三向压应力,如图1所示。
在离接触表面深度(Z)为0.786b处(b为接触面宽度之半)剪切应力最大,随着表层摩擦力的增大而移向表层。
图1 滚动接触疲劳破坏应力状态疲劳裂纹并不是发生在剪应力最大处,而是更接近于表面,即在Z为0.5b的交变剪应力层处。
该处剪应力平行于轧辊表面,据剪应力互等定理,与表面垂直的方向同样存在大小相等的剪应力。
此力随轧辊的转动而发生大小和方向的改变,是造成接触疲劳的根源。
周期交变的剪切应力是轧辊损坏最常见的致因。
在交变剪切应力作用下,反复变形使材料局部弱化,达到疲劳极限时,出现裂纹。
另外,轧辊制造工艺造成的材质不均匀和微型缺陷的存在,亦有助于裂纹的产生。
轧辊失效分析

轧辊缺陷引发失效有三个原因:制造商轧机轧辊维护及管理(管理指磨辊)失效后数据收集要了解:1. 事故段的轧制压力,电压,水压等2. 事故发生时的操作情况3. 轧制废品种规格4. 对最后轧制的板卷暂时保存用于对事故产生原因分析失效分析要点1.辊身剥落为CVC形态,基本为表面缺陷较垂直延伸至结合层,四周快速发展2.剥落区一侧垂直,另一侧逐步过渡至表面,基本剥落区为出口3.多处小块掉肉,掉肉面为棘齿形态,是硬块疲劳裂纹造成4.弧形掉肩通常是支撑辊倒角设计不合理5.断口端面由内向外四周散射,是心部缺陷或强度不够造成的断裂6.近辊身端部环形剥落且在环形带为多元发展源,单侧异常超负荷制造厂轧辊质量引发事故分析元宝形大剥落1.结合层严重非金属夹渣引起的轧辊剥落蜂窝状且色发黑为非金属价夹渣:如,钢水渣,耐火砖,测温管等辅助材料的掉入大块的非金属夹渣只要存在于复合辊的结合层2.金属夹杂引发轧辊剥落剥落后表面发亮成块状,颗粒状:金属原料没有充分熔化,或非原料的金属夹入3.异常发展引发断辊(内部金属夹杂)微小的轧辊夹杂早期在辊身暴露会使轧制的板材产生凸块,使钢材表面质量受到影响4.辊身硬度不均匀形成裂纹—裂纹平行,斜纹,不规则如果裂纹未能磨削干净,会使裂纹扩展5.应力造成轧辊开裂,裂纹环带有的可贯穿整个轴向和颈开裂内应力过大引起的断辊和开裂内应力造成轧辊使用中轴向爆裂为两半(中心向四周扩撒)由于过大的残余内应力,径向断裂多从心部成中心附件,显示放射状痕迹,断面垂直于轧辊轴心,断面起源常位于辊身辊身表面和心部的最大温度差有关---产生残余应力危害:运输中爆裂在磨削过程中爆裂在使用过程中发生爆裂(处理时间长)制造商在热处理,调质处理后的严格按工业技术程序执行,出厂前做应力测试,以消除内应力。
可以买回新辊,放仓库先释放应力。
首次使用的轧制周期不要过长6.黑斑:石墨球化不良铸造时浇铸时间,速度不当造成元素分布不均匀引起7.内部缺陷扩展,引发大的剥落,剥落处可看见一处原地向四周发展预防:结合层缺陷,用UT测试8.工作层厚薄不均匀引发剥落,工作层(精轧)余量8MM, 但实际工作辊余量还要大些9.结合层碳化物平行发展引发轧辊轧制事故10.工作层强度降低(原因:石墨比较大)11.辊颈抗拉强度低造成断辊(牛眼状铁素体,保证轧辊强度)12.辊颈铸接不良,辊颈折断13.卡刚,异物掉入引发大剥落(轴向,径向产生裂纹)14.粘钢引起掉肉。
冷轧工作辊失效分析及其控制

冷轧工作辊失效分析及其控制
1. 前言
冷轧工作辊是冷轧轧机的关键部件,其失效会导致整个轧机停工,造成巨大的
经济损失。
因此,研究冷轧工作辊的失效原因及其控制方法,对于保障生产安全和提高生产效率具有重要意义。
2. 冷轧工作辊失效原因
2.1 疲劳裂纹
冷轧工作辊经过长期反复载荷作用后容易出现疲劳裂纹,引起辊套与轴颈接口
处局部应力增大,导致工作辊失效。
2.2 表面烧伤
在冷轧过程中,由于磨擦和压力等原因,工作辊表面容易出现高温,引起表面
烧伤,进而加速辊套材料的软化和疲劳裂纹的产生。
2.3 化学腐蚀
冷轧工作辊在冷轧过程中,由于长期浸泡在冷轧液中,易受化学物质的腐蚀,
导致表面出现蚀刻、穿孔等损伤,甚至引起裂纹。
3. 冷轧工作辊失效控制方法
3.1 合理选择材料
冷轧工作辊应选择高强度、高韧性、耐疲劳、耐磨损的材料以提高其使用寿命。
3.2 加强表面保护
冷轧工作辊表面应进行抛丸喷砂处理,形成均匀的抗疲劳层,延长工作辊的使
用寿命。
3.3 加强冷轧液管理
严格控制冷轧液的PH值、温度、浓度等参数,并及时更换冷轧液,减少化学
腐蚀。
4. 结论
冷轧工作辊失效是制约冷轧工艺高效稳定发展的主要障碍。
在实际生产过程中,可以通过合理材料选择、加强表面保护以及加强冷轧液管理等多种方法,有效控制冷轧工作辊失效,延长轧机设备使用寿命,降低生产成本,提高经济效益。
马钢冷轧轧辊缺陷的分析及防范措施

马钢冷轧轧辊缺陷的分析及防范措施
马钢冷轧轧辊缺陷已成为冷轧工艺中的一个严重问题,严重影响操作和生产效率,并影响质量。
本文旨在分析轧辊缺陷及其发生原因,以及探讨有效防范措施。
1、轧辊缺陷分析
轧辊缺陷是指轧辊磨损,型面凹陷,表面裂纹,焊接部失效等现象。
它们的存在会影响轧辊的正常使用,影响冷轧过程的质量,缩短轧辊的使用寿命,并增加维修成本。
在实际生产中,轧辊缺陷常见原因主要有:
(1)轧辊质量不合格:因结构设计不合理,选用和制备材料不合格,加工工艺不合格等原因,提高了轧辊缺陷的可能性。
(2)轧辊磨损:由于滚压过程中的轧辊振动、局部过热、轧件本身结构不均匀等原因,导致轧辊表面磨损等缺陷的产生。
(3)焊接失效:由于焊接技术不足或焊缝质量不合格等原因,造成焊缝失效或断裂,从而使轧辊表面出现缺陷。
2、防范措施
(1)增强轧辊质量控制:在轧辊的设计、加工、焊接、组装等各个方面都应严格把关,加强对轧辊质量的控制,以确保轧辊质量稳定,减少轧辊缺陷。
(2)提高滚压过程控制:应采用合理的滚压参数,加强对滚压压力、温度及轧件材料等的控制,适当减小滚压力,以降低滚压过程中轧辊的磨损,防止轧辊损坏。
(3)加强焊接质量控制:应按照焊接技术标准,严格把关焊接技术操作,确保焊接缝的质量符合要求,避免轧辊出现焊接失效的缺陷。
3、结论
轧辊缺陷是影响工艺效率和产品质量的主要因素,应采取有效的措施来防范和消除其存在。
针对轧辊缺陷的发生,应加强轧辊的质量控制,提高滚压过程的控制,加强焊接质量控制,以最大程度地减少轧辊缺陷及其造成的损失。
轧辊技术讲座 2010

轧辊技术讲座2010轧辊技术讲座(二)刘根社一、什么是检测?(钢铁论坛3/2---05)答:检测是检验与测量的统称。
所谓测量,就是将被测量的量与作为单位或标准的量在数量上进行比较,从而确定二者比值的认识过程。
如果以Q表示被测量,u表示计量单位,二者比值为x=Q/u,则有Q=xu ,即测量所得量值为用计量单位表示的被测的量的数值。
所谓检验,通常是指采用综合量规(如轧辊辊形测量样板),检查被测要素是否在图样上规定的公差带内,从而判断其合格与否,而不要求确切知道被测量要素的具体尺寸。
二、什么要对轧辊实施检测,其基本要求是什么?(钢铁论坛10/2---05)答:在轧机上轧制金属板、带时,轧辊的工作表面磨损较快。
轧辊是直接使轧件产生变形的工具,辊形的变化将直接影响轧材的质量,必须对轧辊的精度(如轧辊的尺寸、变形、热膨胀、磨损及热凸度等)进行精确控制。
正确的检测轧辊是认识轧辊几何形状及其精度状况的基本手段,通过检测可以达到以下目的:(1)正确判断轧辊是否符合精度要求,即判断其合格性。
(2)根据测量得到的尺寸误差值,分析产生误差的原因,从而采取措施改进工艺,以保证和不断提高轧辊的加工精度。
对轧辊检测的基本要求有两条:一是要有准确性。
轧辊的检测结果必须具有一定的可靠性,以实现检测的目的。
二是要有经济实用性,在检测中所花费的代价,是轧辊经济指标的重要组成部分,必须采取合理的方式方法,在保证轧辊质量的同时取得最好的经济效果。
三、(钢铁论坛17/2---05)四、轧辊物理检测包括哪些项目?(钢铁论坛24/2---05)答:轧辊物理检测包括性能检测、显微组织检测和无损检测。
性能检测包括拉力试验、冲击试验、冷热疲劳试验、弯曲疲劳试验等。
显微组织检测包括金相检测、碳化物、石墨、夹杂物等相的定量分析、扫描电镜、电子探针等。
无损探伤包括超声波探伤、磁粉探伤、渗透探伤等。
轧辊理检测主要包括以下检测项目:(1)硬度检测,如肖氏HSD、HSC、里氏HLD、布氏HB、维氏HV及显微硬度;(2)强度检验,如屈服强度、抗拉强度、抗弯强度、抗压强度;(3)塑性指标检验,如伸长率、断面收缩率;(4)韧性指标检验,如冲击功AK、断裂韧性KIC (5)显微组织检验,如金相组织检验、不同组织的定量检验;(6)无损检验,如超声波探伤、着色渗透探伤、磁粉探伤;(7)残余应力检测,如X射线应力检测、钻孔法应力检测、磁粉法应力检测;(8)高倍检测,主要用于锻钢冷轧辊,如碳化物级别、珠光体和马氏体级别;(9)低倍检测,主要用于锻钢冷轧辊,如酸浸、硫印。
失效分析培训教材讲课1

2024/5/29
21
第六部分 热处理失效分析典型案例
案例1 45#零件开裂分析
案例2 零件氮化后尺寸涨大分析
案例3 汽车尾箱盖扣件断裂分析
案例4 轴类零件调质处理后切削性能不良分析
案例5 4Cr13零件断裂分析
案例6 Cr12模具热处理回火开裂分析
案例7 440C圆柱导套磨后表面腐蚀分析
案例8 38CrMoAl齿轮传动轴断裂分析
4、建议放弃真空油淬固溶方法。
2024/5/29
8
案例3 420医疗器械零件真空淬火裂纹
420医疗器械零件真空淬火裂纹案例
一、问题现状 客户医疗器械零件,如图,采用材料为420,要求硬度
HRC47~51,客户在收货检验中发现少数零件存在裂纹,要求 分析原因。
2024/5/29
9
案例3 420医疗器械零件真空淬火裂纹
2024/5/29
7
3.1 真空淬火技术
316不锈钢零件真空油冷固溶后碾压开裂案例(续)
三、分析意见(续) 2、零件芯部组织为奥氏体+铁素体,属正常组织。 3、高温真空油淬对含碳量较低的材料会产生渗碳现象,这
已经是一个共识,这在许多资料中均有论述和记载,不过一般 认为0.02~0.05mm的渗碳几乎没有影响,但由于本零件需要铆 压,表面的硬化层延伸率大大降低,因而引起裂纹。
14
案例4 6150冲针零件使用中断裂
6150冲针零件使用中断裂案例(续)
2.金相检查(续)
2024/5/29
500×,4%硝酸酒精溶液腐蚀 芯部组织:隐针回火马氏体。 芯部硬度为HV1621~634
15
案例4 6150冲针零件使用中断裂
6150冲针零件使用中断裂案例(续)
冷轧六辊可逆轧机工作辊辊面剥落失效分析

《装备维修技术》2021年第8期—53—冷轧六辊可逆轧机工作辊辊面剥落失效分析刘建龙 张迎宾(邯钢集团衡水薄板有限责任公司,河北 衡水 053000)引言:金属在再结晶温度以下进行轧制变形叫做冷轧,该公司冷轧厂是将2-3mm 之间的热轧卷板按照不同的压下率分成多个道次进行可逆轧制,最终通过压上缸作用到支撑辊辊系、中间辊辊系、工作辊辊系将热轧卷板轧薄。
在冷轧生产过程中,轧辊是至关重要的生产工具,因其轧制压力大、速度高,因此要求轧辊必须具有高耐磨、高韧性及抗冲击性能。
轧钢过程中,轧辊处于复杂的受力状态,需要承受上百吨的轧制力。
在轧制过程中轧辊的损伤失效是普遍存在的现象,其中包括勒辊、咯辊造成的辊面裂纹、辊面爆辊造成的剥落、辊颈断裂等形式。
其中,辊面剥落是一种非常严重的事故,不但会使轧辊提前报废退出使用,令轧辊消耗骤然上升,还会造成轧机断带故障,产生废品,断带堆钢还会对轧机设备造成严重冲击,增加了轧机设备维修成本消耗,不利于轧机稳定、高效生产。
造成轧辊辊面剥落的因素有很多,包括轧辊的磨削、事故辊的处理方式、轧制规格的道次分配、换辊周期、工艺润滑等。
按剥落的形式划分,冷轧辊的辊面剥落分为辊面裂纹和轧辊坯料内部缺陷引起的剥落。
随着冶金技术、设备的不断发展创新,冷轧辊坯料生产过程中又有先进的探伤工艺辅助,冷轧辊辊身的内在晶粒组织缺陷、夹杂物得到了可靠的控制。
因此,一般冷轧辊的表面剥落事故还是使用过程中造成的。
近几年来,冷轧产品尤其是镀锡基板,对其性能指标硬度、屈服强度、平整度、粗糙度等提出了更高的要求。
面对如此严格的产品要求,轧辊在使用过程中面临严峻的挑战,轧辊的规范化使用及轧辊准备工序的磨削维护管理必须严格执行,如:轧机工序按规定周期换辊,不得超时使用等。
因此,对轧辊辊面剥落失效进行全面深入的分析有深远的意义,不但可以减少断带事故,提高产品合格率,还可以降低轧辊的非正常消耗和轧机设备维修成本。
1基本情况调查1.1辊面剥落外形特征 该公司冷轧厂轧机为单机架六辊可逆轧机,在2020年上半年期间发生多次工作辊辊面大面积剥落事故,其中一支工作辊,该轧辊轧制时长5小时,过钢量约65吨,当前辊身直径287mm,正常报废尺寸为270mm,辊面剥落区域沿轴向约400mm,周向约150mm,深度已到淬硬层与芯部的过渡区域,剥落处位于轧辊辊身中间位置。
《失效分析》(教学课件)

2
10
7.1 铸造加工缺陷与失效
SiO2夹杂物
石英(六方晶系)、磷石英(斜方晶系)、 方石英(属立方晶系,属四方晶系)。非晶 体SiO2 ,大小不同的典型小球 ,明场中呈深灰 色,常随其中所含的杂质不同而具有不同的色 彩,中心有亮点,边缘有亮环;暗场中无色透 明,鲜明地发亮;偏光下透明并有暗十字。
2
21
7.2 锻造加工缺陷与失效
4、流线不顺
锻件流线不沿零件主要轮廓外形分布,严重时会 形成涡流,穿流或紊流流线。
涡流即锻件流线呈旋涡状或树木年轮状。 穿流即在锻件肋条或凸台根部金属流线被穿断, 破坏了金属流线的连续性。 紊流则呈不规则而紊乱的流线。
2
22
7.2 锻造加工缺陷与失效
5、裂纹 锻件内部的裂纹有两种类型:内部纵向裂纹和内 部横向裂纹。
锻件含铜量过高(>0.2%),并在氧化气氛中加热, 在钢的表面氧化皮下,富集一层熔点低于1100℃的 富铜合金,在锻造加热温度下即熔化,并浸蚀表面层 的晶界,锻造时形成龟裂〔称为铜脆〕。在加热炉中 含有残存的铜杂质时,也会因融熔的铜沿晶界渗入而 引起龟裂。
2
27
7.2 锻造加工缺陷与失效
6、过热与过烧 金属坯加热温度超过始锻温度,或在高温下长时 间保温,致使奥氏体晶粒迅速长大,或终锻温度过 高而剩余变形量(剩余锻造比)又小,这时高温引起的 晶粒长大,不能由剩余变形量对晶粒的破碎作用所 抵消,因而形成粗晶粒组织的现象,称为过热。
内部横向裂纹产生的主要原因是毛坯在加热或锻 造过程中,由于加热不均或工艺参数不当,其表层 金属的变形(如伸长)大于心部金属的变形,而导致 心部受拉应力,当拉应力超过材料自身的抗拉强度 时,心部将出现横向裂纹。
冷轧辊的失效分析及其修复

轧
钢
rEEL R0 LLI G N
冷轧 辊 的 失 效 分析 及 其 修 复
任 喜 来
( 州 第二 钢 厂 ,河 南 郑 郑州 4 19 ) 5 1 1
摘
要 : 介 绍 了 冷 轧 机 轧 辊 存 在 划 伤 、粘 辊 及 剥 落 3种 失 效 方 式 ,重 点 分 析 了 轧 辊 剥 落 的 产 生 机 理 , 并 提
Ab t a t s r c :Th h e al r y eo olf rc l l i e c a c i g s ik n d f k n fr lwe ed s r e Th c a im e t r e fiu e t p fr l o o d mi , . .s r t h n , tc i g a a i o ol l n l g r e c b d. e me h n s i f f k n fr l wa l z d. e p e e t a u e o ol al ea e a a i t o l a k u o l r u o — o a i g o o l sa a y e Th r v n i eme s rs f rr l fi r d ar p r t n me h d f rf i e b c - p r l we e p tf r l s n v u n o o au r
法 设计 ,个 别 尺 寸 通 过 作 图修 正 。K 孔 型 尺 寸
构 成的 主要 原则 :使 l < 6切分 孔 既 充 满 又不 产 生 耳子 ,使 K 立 箱 孔 进 K 8 孔 预 切 分 出充 满 而 规
为 9 . %, 1 角 钢试 轧 中 的技 术 经 济 指 标 见 43 4号
[ ]上 海 市 冶 金 工 业 局 编 . 型设 计 下 册 [ ] . 海 :科 学 技 1 孔 M 上 术出版社.17 . 9 9 [ ]鞍 钢 中型 厂 编 写 组 . 型钢 材 生产 [ ] . 京 : 冶金 工 业 2 中 M 北
马钢冷轧辊失效原因分析及防范措施

时, 在表 面之 下 位 置 发 生 扩散 , 致 剥 落 的产 生 , 导 这
会 通过 两种 模式 发 生 。
( ) 时模 式 : 作 辊 断 带缠 绕 、 1瞬 工 打滑 或 突 然 停 机 时 突然 发 生赫 兹 应 力 显著 地 提 高 , 过 轧 辊 裂 纹 超
第3 6卷第 5 期
20 0 8年 1 月 O
江 苏 冶 金
Ja g u M eal r y in s t l g u
V0 . 6 No 5 13 . 0C . 0 8j t2 0
马钢 冷 轧辊 失 效原 因分 析及 防范 措 施
任 天 宝 ,严 开 龙 ,孟 文捷
( 钢 ( 肥 ) 铁有限责任公司 , 徽 合肥 马 合 钢 安 201) 30 1
火 温度 时便会 产生 软 点 。导致 产 生软 点现象 的一 些 潜 在“ ” 有 : 热 源 断带 、 打滑 、 机故 障 ( 轧 卡钢或 堆钢 ) 、
不 均匀 的乳化 液冷 却 喷淋 、 制产 品 的厚度 变化 、 轧 冷 却剂 温度 和轧 机速 度 。
() 2 高周 期疲 劳 剥落 : 轧辊 工作应 力低 于轧 辊材 料 强度 的应力 。 应力 作用 频率较 高 , 可导致 裂纹 但 也 发生, 即疲劳产 生 裂纹 导致 剥落 的产生 。 种裂 纹往 这 往非 常小 , 且平 行 分布 于轧 辊表 面的切 线上 , 在应 可 力 区域 内的许 多地 方 发生 , 扩 展 到表 面 直 至剥 落 并
的抗拉 强度 , 并在 轧 制应力 进 一步循 环下 瞬时形 成 , 通 过疲 劳方 式引发 剥 落 的产生 ( 图 3 。 见 )
VCMS冷轧机轧辊失效分析
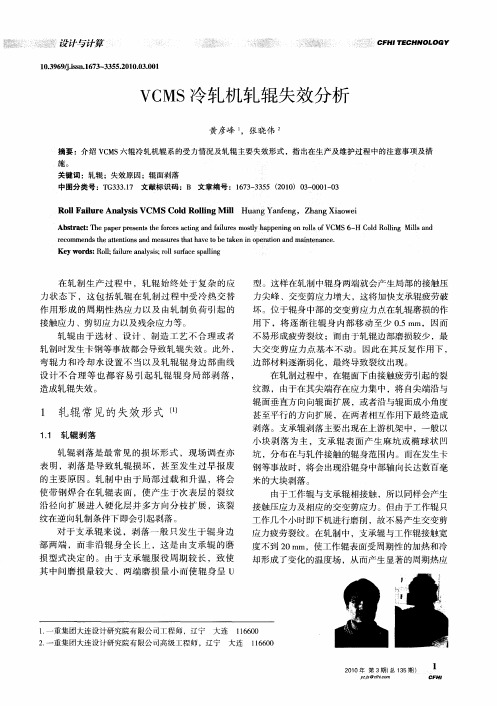
力 。 当热应 力超 过材料 的疲 劳极 限时 ,轧 辊表 面便 会产 生细小 的网状 热 裂纹 ,即通称 的龟裂 。
施。
关键词 :轧辊 ;失效原因 ;辊面剥落 中图分类号 :T 3 31 文献标识码 :B 文章编号 :17 — 3 5 (0 O 3 0 0 — 3 G 3 .7 6 3 3 5 2 l )0 — 0 10
Ro l a l r a y i l F i e An l ssVCM S Co d Ro l gM i Hu n n e g Z a gXi o i u l ln l i l a gYa f n , h n a we
型 。这样 在轧 制 中辊 身两端 就会 产生 局部 的接 触压
力尖 峰 、交变 剪应 力增 大 ,这将 加快 支 承辊疲 劳破
作 用 形 成 的周 期 性 热 应 力 以及 由轧 制 负 荷 引起 的 接 触应 力 、剪切应 力 以及残 余 应力 等 。 轧 辊 由于 选 材 、设 计 、制 造 工 艺 不 合 理 或 者
沿 径 向扩展 进 人 硬 化层 并 多 方 向分 枝 扩 展 ,该 裂 纹在 逆 向轧制 条件 下 即会 引起剥 落 。
米的大块剥落。
由于工作 辊 与支 承辊 相接 触 ,所 以 同样 会产 生
接触 压 应力及 相 应 的交变 剪应 力 。但 由于工 作辊 只
工作 几 个小 时 即下机 进行 磨 削 ,故 不易 产生 交变 剪 应力 疲 劳裂纹 。在 轧制 中 ,支 承辊 与工作 辊 接触宽 度不 到 2 l,使工 作辊 表 面受周 期 性 的加热 和冷 0mi l 却形 成 了变化 的温度 场 ,从 而 产生 显著 的周期 热应
轧 辊 剥 落 是 最 常 见 的 损 坏 形 式 ,现 场 调 查 亦 表 明 ,剥 落 是 导 致 轧 辊 损 坏 ,甚 至 发 生 过 早 报 废 的主 要 原 因 。 轧 制 中 由于 局 部 过 载 和 升 温 ,将 会 使 带 钢 焊 合 在 轧 辊 表 面 ,使 产 生 于 次 表 层 的裂 纹
轧辊破坏常见原因分析及对策.doc

CL0501-轧辊破坏常见原因分析及对策案例简要说明:依据国家职业标准和金属材料及热处理技术、材料成型与控制技术专业教学要求,归纳提炼出所包含的知识和技能点,弱化与教学目标无关的内容,使之与课程学习目标、学习内容一致,成为一个承载了教学目标所要求知识和技能的教学案例。
该案例是轧钢设备使用与维护事故案例,体现了轧辊材质及其力学性能等知识点和轧钢工、设备点检工的岗位操作技能,与本专业轧钢机械设备课程中轧辊部分、金属材料与热处理课程中金属材料的性能部分单元的教学目标对应。
轧辊破坏常见原因分析及对策天津冶金职业技术学院王磊该案例发生在承钢热带厂,该厂自1997年建成投产,生产至今已有10多年,在生产初期经常出现轧辊热裂纹、掉肉、局部破坏、外层剥落、甚至轧辊断裂等事故,轧辊发生故障后一般都需要做换辊处理,不仅增加了岗位作业人员的劳动量,而且降低日历作业率,造成废钢,影响成材率,影响轧机产量,同时更造成巨大的经济损失。
通过几年的摸索,对轧辊常见破坏形式进行归纳总结,并给出相应的解决办法。
该案例在教学过程中辅以图片等多媒体资源对学生进行讲解,让学生能够更好地掌握轧制过程中如何更好地延长轧辊的寿命。
1.背景介绍某厂自1997年建成投产,生产至今已有10多年,在生产初期经常出现轧辊热裂纹、掉肉、局部破坏、外层剥落、甚至轧辊断裂等事故,轧辊发生故障后一般都需要做换辊处理,不仅增加了岗位作业人员的劳动量,而且降低日历作业率,造成废钢,影响成材率,影响轧机产量,同时更造成巨大的经济损失。
通过几年的摸索,对轧辊常见破坏形式进行归纳总结,并给出相应的解决办法。
2.主要内容2.1.热应力断裂一、现象描述此类断裂多发生在粗轧机,一般在粗轧换辊后开轧10块钢以内,寒冷的冬季出现的几率更大一些。
轧辊辊身断层呈径向,起源位于或接近轧辊轴线,断裂面与轧辊轴线垂直,一般发生在辊身中部,如图1所示。
图1 热应力断裂断面形状二、轧辊破坏原因这种热应力断裂与轧辊表面和轴心处的最大温差有关。
- 1、下载文档前请自行甄别文档内容的完整性,平台不提供额外的编辑、内容补充、找答案等附加服务。
- 2、"仅部分预览"的文档,不可在线预览部分如存在完整性等问题,可反馈申请退款(可完整预览的文档不适用该条件!)。
- 3、如文档侵犯您的权益,请联系客服反馈,我们会尽快为您处理(人工客服工作时间:9:00-18:30)。
冷轧辊的失效分析
冷轧辊的失效分析
材料工程1306
封骥
2013153
冷轧辊的失效分析
冷轧辊是冷轧机的大宗消耗备品,其能否安全运行将直接影响着轧机的生产率、成材率以及成本控制。
由于冷轧辊从材质、制造工艺、使用、维护及失
效等诸方面与热轧辊有着较大的差异,故对初次进行冷轧生产的单位、轧辊管理者及使用者来说,需要掌握冷轧辊的失效机理及预防措施,通过对冷轧辊失效机理的论述及案例的相关分析,提出降低轧辊消耗的预防措施。
失效:金属装备及其构件在使用过程中,由于压力、时间、温度和环境介质和操作失误等因素的作用,丧失其规定功能的现象。
失效分析:对装备及其构件在使用过程中发生各种形式失效现象的特征及规律进行分析研究,从中找出产生失效的主要原因及防止失效的措施,称为失效分析。
失效分析的一般过程
①深入装备失效现场、广泛收集、调查失效信息,寻找失效构件及相关实物证据。
②对失效构件进行全面深入的宏观分析,通过种类认定推理,初步确定失效件的失效类型。
③对失效件及其相关证物展开必要的微观分析、理化检验,进一步查找失效的原因。
④通过归纳、演绎、类比、假设、选择性推理,建立整个失效过程及其失效原因之间的联系,进行综合性分析。
⑤在可能的情况下,对重大的失效事件进行模拟试验,验证因果分析的正确性。
一、冷轧辊失效机理
冷轧辊特性:目前冷轧厂常用的冷轧辊材质有高碳铬铝系及高碳铬铝钒系,一般生产工艺过程为电渣重熔或钢包精炼——铸锭——锻造——球化退火——粗加-——探伤——调质——精加工——探伤——工频感应淬火——低温回火——精加工成品。
为确保优良的使用性能,其表层组织要求为细针马氏体、隐针马氏体+少量残余奥氏体+粒状碳化物。
冷轧工作辊工作时要承受高的轧制压力、冲击载荷、疲劳及磨损,需要有足够的强度抵抗大的弯深而均匀的表面硬化层及耐磨层,以获得良好的耐磨性;三是要有优良的表层抗裂性及抗剥落性能。
冷轧辊的失效形式:冷轧工作辊工作时处于复杂的应力状态。
受残余应力、接触应力、弯曲应力、扭转应力以及因温度分布不均引起的热应力等的影响,失效形式有早期磨损、粗糙化、略坑、勒痕、裂纹、剥落以及断裂,但工作层剥落是冷轧辊的主要失效形式,占到工作辊正常失效的50%以上,轧辊剥落往往造成轧辊彻底报废。
其剥落按断口可分为疲劳剥落和脆性剥落:按剥落块形状分为贝壳状剥落、带状剥落、区域点状剥落、热冲击剥落:按剥落深浅分为表层剥落及次表层剥落等。
裂纹来源:
(1)热裂纹。
断带、重叠、卡钢及打滑时,轧辊局部剧烈受热温度可高达相变点以上直至800C,在辊身以接触点为中心会产生从外至内一定温差,从而在不同深度组织有所变化,当温升和组织变化引起的热膨胀和来自周围的压应力超过屈服极限时产生塑变,并伴有残余压应力释放和应力重新分布,并出现拉应力,随着拉应力的出现就产生微裂纹。
(2)磨削裂纹。
轧辊修磨时,会因砂轮太硬,钝化未及时修整,砂轮粒度过大,进刀量大,走刀速度快,或冷却不充分等原因,导致辊面烧伤,出现裂纹,这些裂纹在轧辊使用前必须全部消除,否则轧制时继续扩展。
(3)残留裂纹。
换磨的轧辊表面裂纹为微裂纹,通常磨削时可全部消除,但肉眼观察难以确保完全磨削掉,残留的微裂纹在随后的使用过程中将成为疲劳核心,可用表面腐蚀、磁粉探伤等进行判断。
(4)乳化液的影响。
主要用来对轧辊进行润滑和降温,设计浓度一般为
2%~3%,随着使用频率增加,浓度会有所下降;磁性过滤器和撇污装置损坏会造成浓度下降,导致磨擦系数增大,造成轧辊负荷加大;乳化液脏引起冷却性能变差,同时乳化液流量要随轧制速度提高而增大,避免轧制时乳化液喷嘴堵塞和喷射角度变化,使乳化液不能最大限度地喷到轧辊上和进入变形区。
润滑不好,一是加大轧机负荷,二是使最大综合切应力移向表层,三是易使轧辊表面粗糙,降低疲劳强度,促使表面裂纹生成。
(5)咬入挫伤。
轧辊咬入时受冲击,空载时要用平衡装置避免工作辊紧靠在下工作辊上产生热冲击挫伤轧辊。
工作辊与支撑辊接触应力是三向压应力,其切应力最大值离接触表面深度为0.786b ( b为接触面宽度1/2)处,但随表面磨擦力的增大而移向表层,表面磨擦力和切应力迭加,构成了接触磨擦条件下的最大综合切应力,综合切应力大于剪切强度的部位将产生塑变而形成裂纹。
当表面磨擦较小时,最大综合切应力不在表层而在次表层,裂纹也就在次表层产生,导致次表层剥落;当润滑不良,或轧辊硬度低,表面粗糙、辊面有缺陷,裂纹发生在表层,导致表层剥落。
辊面剥落及原因:辊面剥落常以辊身表面裂纹为起点,在接触应力的反复长期作用下发展成疲劳剥落,为确保辊面不发生接触疲劳破坏,接触应力应小于轧辊材料的硬度所决定的许用值。
归纳产生剥落的原因,分为①原材料缺陷造成剥落;②热处理不当引起剥落;③冷加工不当引起剥落;④使用不当引起的剥落。
二、案例分析
1、宏观断口分析
如图1,轧辊损伤于辊身一端约1/3处,出现大面积的剥落,从断口形貌上看,有明显的疲劳辉纹,见图2,这些条纹是疲劳裂纹前沿线间隙扩展的痕迹,每一条条纹是疲劳裂纹在一个给定时间的推进位置,由于裂纹扩展时受到障碍,时而扩展,时而停止,或由于轧机开车停车,加速减速,加载卸载导致
负荷周期性突变而产生的,疲劳扩展区是在交变负荷作用下裂纹扩展的结果。
现从断口附近(图1中新剥落块处)取样对该轧辊的材质、夹杂及组织进行分析。
2、化学成分及硬度测试
从上表1可以看出:碳为9CrzMo材质碳含量的上线,硅含量超9Cr2Mo材质技术要求;硬度相对较高。
3、金相分析
试样抛光后观察,裂纹形貌如图3,裂纹尖端较尖、形态平直,并伴有二次小裂纹形成,说明是一种穿晶冷裂纹;在裂纹附近发现有两种形态的夹杂,分别如图4a、图4b,裂纹与夹杂呈同向分布,说明夹杂与裂纹的产生存在一定的关系。
组织如图5,为细针状马氏体+少量残余奥氏体+粒状渗碳体,图中可见明显的夹杂分布于裂纹一侧,裂纹处组织未发生氧化脱碳现象,这一点充分证实了裂纹为冷裂纹。
4、分析结果
该轧辊为次表层接触疲劳断裂。
从断口明显的疲劳辉纹可以断定是一种疲劳断裂,疲劳断裂与一次负荷断裂不同,它是一种累进式断裂,当材料次表面存在夹杂第二相质点时,该处疲劳抗力下降,在循环应力反复作用下,于此处形成应力集中区,便引发疲劳源,并向表面扩展形成片状剥落。
从该支轧辊存在的夹杂与裂纹的位置来推测,疲劳起源与夹杂相关。
三、防止冷轧辊失效的预防措施
正确使用轧辊。
合理选择轧制力、张力衣压下量,避免打滑、过载、粘钢、断带等原因造咸轧辊表面裂纹及轧辊工作面烧伤。
带钢变形处轧前进行矫正,过焊缝时,轧机低速运转。
从现场轧转的损坏情况来看,因使用异常导致的失效数量较多,轧辊管理者和使用者要引起足够的重视。
做好轧辊管理。
建立轧辊履厉表,修订辊身修磨的检测规范,制定合理的换辊周期,建立事故轧辊处理程序。
不能在有表面裂纹时继续使用,应及时换磨,轧机操作者要及进对轧辊进行检查,出现异常轧制更要引起注意,并作好
按规定换辊。
轧辊在运输及吊运时不能碰撞:做好新旧轧辊交替使用,便于轧辊的时效,使应力得到充分释放。
轧辊存放与使用时温度变化不要太突然。
新换轧辊上机启动时负荷不要太大,特别是冬季东北气温低,考虑轧辊上机前进行预热;刚换下的车l辊要放在放在轧辊台架上,便于轧辊辊温度的均匀释放。
轧辊磨削时防止磨削烧伤及产生磨削裂纹。
磨削裂纹通常细而浅,有时肉眼不易觉察,但借助磁粉探伤、酸洗极易显示,要确保不仅要磨掉裂纹层,还要把所有软化层彻底磨净,以保证轧辊表面材料的抗裂能力。
磨削速度不宜过快,进削量不宜过大,冷却液应充分供应,以便充分冷却,防止出现带状回火区。
制造质量对轧辊失效的影响。
轧辊制造质量包括冶金质量、热处理质量、机加工质量以及轧辊设计质量等,任何一种内在及外在的宏观质量对轧辊的失效影响都是非常巨大的。
轧辊的制造质量直接影响着轧辊的使用,起着至关重要的作用,因此在轧辊的选购时要格外关注,同时在使用过程中要将出现的问题及时与供货厂家进行沟通,求得技术方面支持,以便更适应我公司轧机的需要。