超高速超精密加工技术主要内容
磨削技术论文:超高速磨削及其优势探析
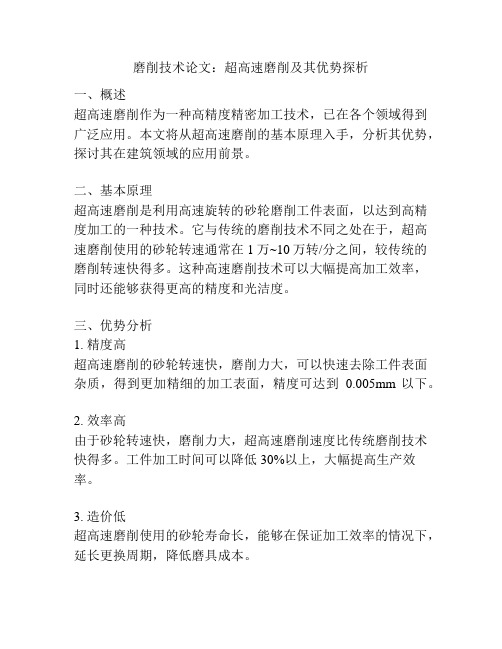
磨削技术论文:超高速磨削及其优势探析一、概述超高速磨削作为一种高精度精密加工技术,已在各个领域得到广泛应用。
本文将从超高速磨削的基本原理入手,分析其优势,探讨其在建筑领域的应用前景。
二、基本原理超高速磨削是利用高速旋转的砂轮磨削工件表面,以达到高精度加工的一种技术。
它与传统的磨削技术不同之处在于,超高速磨削使用的砂轮转速通常在1万~10万转/分之间,较传统的磨削转速快得多。
这种高速磨削技术可以大幅提高加工效率,同时还能够获得更高的精度和光洁度。
三、优势分析1. 精度高超高速磨削的砂轮转速快,磨削力大,可以快速去除工件表面杂质,得到更加精细的加工表面,精度可达到0.005mm以下。
2. 效率高由于砂轮转速快,磨削力大,超高速磨削速度比传统磨削技术快得多。
工件加工时间可以降低30%以上,大幅提高生产效率。
3. 造价低超高速磨削使用的砂轮寿命长,能够在保证加工效率的情况下,延长更换周期,降低磨具成本。
4. 应用范围广超高速磨削是一种高效、环保、精细化的磨削技术,可适用于各种材料的加工,包括金属、非金属材料、陶瓷材料等。
5. 环保超高速磨削使用的是无毒、无害、无污染的磨料,减少了对环境的污染。
四、应用前景在建筑领域,超高速磨削技术可以用于加工各类构件。
它能够大幅节约加工时间,提高生产效率。
同时,它还能精细加工各类构件表面,达到工艺标准,节约原材料,降低生产成本。
在未来,超高速磨削技术有望得到更加广泛的应用。
五、案例分析1. XXX公司的构件加工中,采用超高速磨削技术,成功优化了加工效率,降低了产品成本,得到了客户的一致好评。
2. XX公司将超高速磨削技术应用于钢筋加工中,减少了加工时间,提高了钢筋的精度和尺寸的一致性,受到了建筑公司的赞扬。
3. XX公司采用超高速磨削技术加工门窗构件,成功提高了构件的表面精度和光洁度,降低了产品的废品率,提高了客户的满意度。
4. XX公司采用超高速磨削技术加工凸轮、传动齿轮等构件,减少了加工时间,提高了精度和表面光洁度,获得了广泛应用。
_超高速加工技术

2、超高速主轴系统动态特性及热态特性研究:动刚度、固有 频率等参数的影响。 3、超高速主轴系统的润滑和冷却技术研究:润滑充分问题、 冷却效果问题。 4、超高速主轴系统多目标优化设计、虚拟设计技术研究。
第四节 超高速加工进给单元制造技术
超高速加工进给单元是超高速加工机床的重要组成部分。 一、超高速加工进给单元的基本要求: 1、要求具有大的加、减速度:在瞬时达到高速,瞬时准停。 2、要求具有搞的定位精度:能精确控制零件的尺寸精度。 二、超高速加工进给单元的关键技术: 1、高速位置环芯片研制;
4、超高速加工中工件状态的测试技术; 5、超高速加工中自适应控制技术; 6、超高速加工中智能控制技术。
第五节 超高Βιβλιοθήκη 加工测试技术从某种意义上讲,超高速加工测试技术是超高速加工得到应 用的技术关键。 一、超高速加工测试技术的概念: 主要是指在超高速加工过程中,通过传感、分析、信号处理 等,对超高速机床及系统的状态进行实时在线监测和控制的监测 技术。 监测主要基于对切削力、声发射、切削功率和温度等信息参 数检测,来监测加工状态。 二、超高速加工测试的关键技术: 1、基于监控参数的在线检测技术; 2、超高速加工的多传感器融合检测技术; 3、超高速加工机床中各单元系统功能部件的测试技术;
3、超高速进给单元制造技术; 4、超高速加工用刀具和磨具材料; 5、超高速机床支承; 6、超高速加工测试技术。
二、超高速切削机理: 1、萨洛蒙超高速切削理论: 三个切削速度区: ⑴ 常规的切削速度区:现行的切削加工速度范围; ⑵ 不能切削区:此区切削速度下,切削温度过高,刀具不能 承受; ⑶ 高速切削区:当切削速度达到某一数值后,切削温度不再 升高,反而随切削速度继续增加,切削温度呈下降趋势,切削 温度降到刀具能承受的切削速度时,即为高速切削的最低速度。 试验表明,萨洛蒙超高速切削理论并不适用于所有的加工 材料,有些材料在超高速切削时不存在不能切削区。 2、超高速磨削最大切屑厚度hmax理论: 在保持其它参数不变,仅增大磨削速度情况下, hmax会减 小,每个磨削刃上的作用切削力也会减小。
超高速超精密加工技术主要内容

加工方法及机理研究 刀具、 刀具、磨具的研究 加工装备技术研究 测量技术研究
超精密加工技术的应用 超精密加工技术的发展趋势
作 业
(1)超高速、超精密加工技术二者选择其一。 超高速、超精密加工技术二者选择其一。 (2)按照上述提纲要求查阅文献,然后归纳总结写出 按照上述提纲要求查阅文献, 文献综述” “文献综述”。 (3)要求条理清晰,内容精练,3000~5000字。 要求条理清晰,内容精练,3000~5000字 (4)必需手写,不能打印。 必需手写,不能打印。 (5)该作业作为本课程平时成绩的一部分,占15%。 该作业作为本课程平时成绩的一部分, 15%。
超高速超精密加工技术主要内容
一 超高速加工技术
超高速加工技术的内涵 超高速加工技术的关键技术(重点) 超高速加工技术的关键技术(重点)
加工机理研究 主轴单元制造技术研究 进给单元制造技术研究 刀具、 刀具、磨具研究
Байду номын сангаас
超高速加工技术的应用 超高速加工技术的发展趋势
二 超精密加工技术
超精密加工技术的内涵 超精密加工技术的关键技术(重点) 超精密加工技术的关键技术(重点)
高速加工与超高速加工

轴承润滑:油脂润滑、油雾 润滑、油气润滑等。
1.2 超高速切削加工关键技术
2.超高速切削的主轴系统
主轴轴承: 气浮轴承--高回转精度、高转速、低温升,承载能力低。
1.2 超高速切削加工关键技术
2.超高速切削的主轴系统
主轴轴承: 液体静压轴承--运动精度高,动态刚度大,有油升影响。
1.3 超高速磨削技术
超高速磨削砂轮 砂轮基体--必须考虑高速离心力作用; 砂轮磨粒--立方氮化硼、金刚石。
高速砂轮典型结构 变截面等力矩腹板结构,无中心法兰孔, 通过多个小螺孔与主轴安装固定,以降低法兰孔应力。
1.3 超高速磨削技术
超高速磨床结构 具有高动态精度、
高阻尼、高抗振性和 热稳定性。
时,刀具的主要失效形式为刀尖破损,设计时应 着重考虑提高刀尖的抗冲击强度。 超高速铣削刀具材料:有整体硬质合金、涂层硬 质合金、陶瓷、硬质合金和立方氮化硼等。
思考与练习
1. 在怎样的速度范围下加工属于高速加工?分析 高速切削加工所要解决的关键技术。 2. 超高速切削包含哪些相关技术? 3. 简述超高速磨削特点及关键技术。 4. 简述超高速铣削特点及关键技术。
1. 高速与超高速加工技术
1.1 高速与超高速切削技术概述 1.2 超高速切削加工关键技术 1.3 超高速磨削技术 1.4 超高速铣削技术
1.1 高速与超高速切削技术概述
“高速加工”的起源
Salomon切削理论: 工件材料均有一个
临界切削速度,在该速 度下有最高切削温度。
为什么要进行高速加工?
萨洛蒙曲线
常用结构有龙门式、并联式机床结构。
1.2 超高速切削加工关键技术
高速加工机床及其关键技术
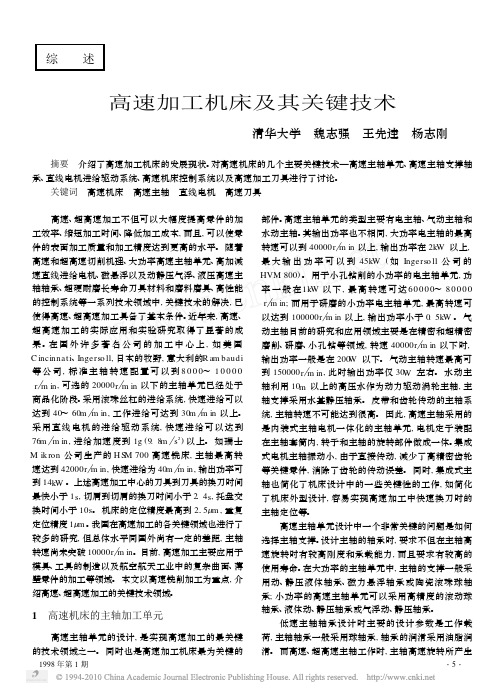
综 述高速加工机床及其关键技术清华大学 魏志强 王先逵 杨志刚 摘要 介绍了高速加工机床的发展现状。
对高速机床的几个主要关键技术—高速主轴单元、高速主轴支撑轴承、直线电机进给驱动系统、高速机床控制系统以及高速加工刀具进行了讨论。
关键词 高速机床 高速主轴 直线电机 高速刀具 高速、超高速加工不但可以大幅度提高零件的加工效率、缩短加工时间、降低加工成本,而且,可以使零件的表面加工质量和加工精度达到更高的水平。
随着高速和超高速切削机理、大功率高速主轴单元、高加减速直线进给电机、磁悬浮以及动静压气浮、液压高速主轴轴承、超硬耐磨长寿命刀具材料和磨料磨具、高性能的控制系统等一系列技术领域中,关键技术的解决,已使得高速、超高速加工具备了基本条件。
近年来,高速、超高速加工的实际应用和实验研究取得了显著的成果。
在国外许多著名公司的加工中心上,如美国C incinnati、Ingerso ll,日本的牧野,意大利的R am baudi 等公司,标准主轴转速配置可以到8000~10000 r m in,可选的20000r m in以下的主轴单元已经处于商品化阶段。
采用滚珠丝杠的进给系统,快速进给可以达到40~60m m in,工作进给可达到30m m in以上。
采用直线电机的进给驱动系统,快速进给可以达到76m m in,进给加速度到1g(9.8m s2)以上。
如瑞士M ik ron公司生产的H S M700高速铣床,主轴最高转速达到42000r m in,快速进给为40m m in,输出功率可到14k W。
上述高速加工中心的刀具到刀具的换刀时间最快小于1s,切屑到切屑的换刀时间小于2.4s,托盘交换时间小于10s。
机床的定位精度最高到215Λm,重复定位精度1Λm。
我国在高速加工的各关键领域也进行了较多的研究,但总体水平同国外尚有一定的差距,主轴转速尚未突破10000r m in。
目前,高速加工主要应用于模具、工具的制造以及航空航天工业中的复杂曲面、薄壁零件的加工等领域。
七.先进加工技术
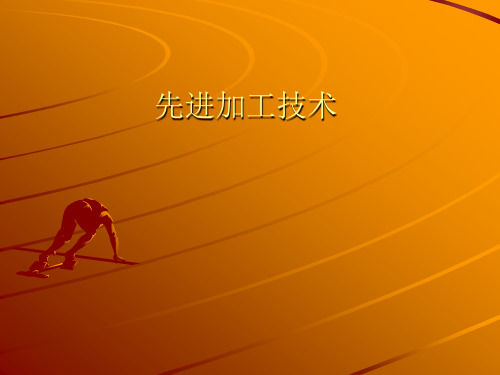
生物工程
Bioengineering
制造工程
Manufacturing Engineering
生物制造
Biomanufacturing
组织和器官之假体与活体制造
பைடு நூலகம்
目的: 1. 提高生产率 2. 改善加工情况 实现: 1. 主轴的零传动:高速主轴单元——电主轴 2. 进给的零传动:直线电机
超高速加工的优点:
1. 显著提高生产效率 2. 切削力可以降低30%以上 3. 切削过程迅速,95%以上的切削热被切
屑带走,工件可以保持冷态。
4. 工作稳定振动小,远离了“机床——工 件——刀具”工艺系统的固有频率范围, 可加工非常精密,光洁的零件。
5. 表面残余应力很小。
不足: 目前只在铝合金和铸铁加工方面应用。 钢的超高速加工还有一些困难
四、超精密加工技术:
分为三种:一般加工、精密加工、超精密加工 动态变化的: 目前标准: 尺寸精度高于0.1μm 表面粗糙度高于0.025μm 形位精度高于0.1μm 从亚微米级向纳米级发展 机械去除法的极限:0.01μm。金刚刀车刀加工有
变形加工:热流动:锻造 粘滞流动:铸造、等静压成形、压铸、注塑 分子定向:液晶定向
超精密加工的要求: 高精度:静态和动态 高刚度:静刚度和动刚度 高稳定性 高度自动化,智能化:减少人为因素
目前超精密加工的主要手段: 1. 金刚石刀具超精密切削 2. 金刚石砂轮和CBN砂轮超精密磨削 3. 超精密研磨和抛光 4. 精密特种加工和复合加工
实现超精密加工的主要条件: 1. 超精密加工机床与装、夹具 2. 刀具、刀具材料、刃磨技术 3. 加工工艺 4. 加工环境控制(恒温、隔振、洁净控制等) 5. 测控技术
超高速加工技术 2

粗加工
传统加工方法 精加工
高速切削 少量手工精修
手工精修
加工时间 100 % 图 采用高速加工缩短模具制作周期(日产汽车公司)
精选课件
12
电极制造
1毛坯 → 2粗铣 → 3半精铣 → 4热处理 →5电火花加工→6精铣→7手工磨修
a)传统模具加工的过程
1硬化毛坯→2粗铣→3半精铣→4精铣→5手工磨修 b)高速模具加工的过程
超高速加工技术
超高速加工的基本概念 超高速加工的内涵
高速加工切削速度的范围
超高速加工的特点
超高速加工的应用
超高速加工的关键技术
高速磨削加工精选课件
1
超高速加工的基本概念
高速加工技术:
采用超硬材料的刀具和磨具,能可靠地实现高速运动的自 动化制造设备,极大地提高材料的切除率,并保证加工精度和 加工质量的现代制造加工技术。
精物理学家萨洛蒙(Carl Salomon)博士于1931年提出的著名切削理 论认为:一定的工件材料对应有一个临界切 削速度,在该切削速度下其切削温度最高。
在常规切削速度范围内,切削温度温度 随着切削速度的增加而提高。在切削速度达 到临界切削速度后,随着切削速度的增大切 削温度反而下降。
➢工艺系统振动小 在超高速加工中,由于机床主轴转
速很高,激励振动的频率远离机床固有振动频率,因此
可使工艺振动减小,提高加工质量。
精选课件
8
超高速加工的特点
➢ 高精度 切削激振频率远高于机床系统固有频率,加 工平稳、振动小;
➢ 热变形小 温升不超过3ºC,90%切削热被切屑带走;
A为高速切削加工时的热传导过程 B为传统加工的热传导过程
◎钛(Ti):100-1000m/min
机械制造的新工艺和新方法
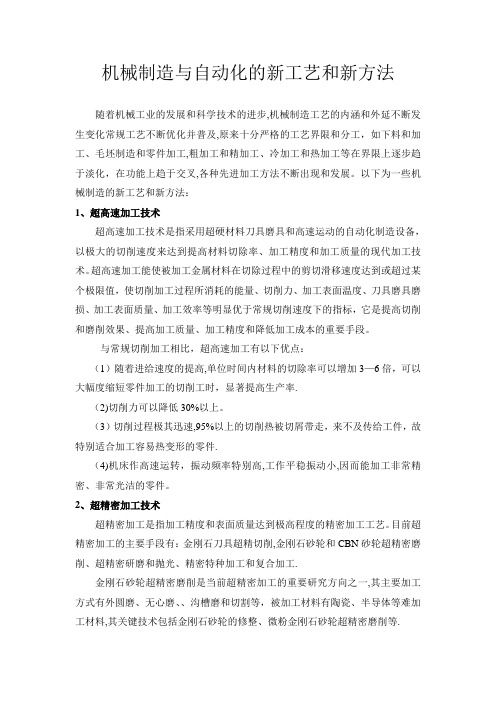
机械制造与自动化的新工艺和新方法随着机械工业的发展和科学技术的进步,机械制造工艺的内涵和外延不断发生变化常规工艺不断优化并普及,原来十分严格的工艺界限和分工,如下料和加工、毛坯制造和零件加工,粗加工和精加工、冷加工和热加工等在界限上逐步趋于淡化,在功能上趋于交叉,各种先进加工方法不断出现和发展。
以下为一些机械制造的新工艺和新方法:1、超高速加工技术超高速加工技术是指采用超硬材料刀具磨具和高速运动的自动化制造设备,以极大的切削速度来达到提高材料切除率、加工精度和加工质量的现代加工技术。
超高速加工能使被加工金属材料在切除过程中的剪切滑移速度达到或超过某个极限值,使切削加工过程所消耗的能量、切削力、加工表面温度、刀具磨具磨损、加工表面质量、加工效率等明显优于常规切削速度下的指标,它是提高切削和磨削效果、提高加工质量、加工精度和降低加工成本的重要手段。
与常规切削加工相比,超高速加工有以下优点:(1)随着进给速度的提高,单位时间内材料的切除率可以增加3—6倍,可以大幅度缩短零件加工的切削工时,显著提高生产率.(2)切削力可以降低30%以上。
(3)切削过程极其迅速,95%以上的切削热被切屑带走,来不及传给工件,故特别适合加工容易热变形的零件.(4)机床作高速运转,振动频率特别高,工作平稳振动小,因而能加工非常精密、非常光洁的零件。
2、超精密加工技术超精密加工是指加工精度和表面质量达到极高程度的精密加工工艺。
目前超精密加工的主要手段有:金刚石刀具超精切削,金刚石砂轮和CBN砂轮超精密磨削、超精密研磨和抛光、精密特种加工和复合加工.金刚石砂轮超精密磨削是当前超精密加工的重要研究方向之一,其主要加工方式有外圆磨、无心磨、、沟槽磨和切割等,被加工材料有陶瓷、半导体等难加工材料,其关键技术包括金刚石砂轮的修整、微粉金刚石砂轮超精密磨削等.金刚石砂轮的修整包括整形和修锐两部分,对于密实型无气孔的金刚石砂轮,如金属结合剂金刚石砂轮,一般在整形后还需要修锐;有气孔型陶瓷结合剂金刚石砂轮在整形后即可使用。
先进制造技术第4章超高速加工技术

目前市场上出现的铣削加工机床主轴转速在 20000~60000r/min,最高达到150000 r/min;
20世纪80年代,计算机控制的自动化生产技术的 高速发展成为国际生产工程的突出特点,工业发达国 家机床的数控化率已高达70%~80%。随着数控机 床、加工中心和柔性制造系统在机械制造中的应用, 使机床空行程动作(如自动换刀、上下料等)的速度和 零件生产过程的连续性大大加快,机械加工的辅助工 时大为缩短。在这种情况下,再一味地减少辅助工时, 不但技术上有难度,经济上不合算,而且对提高生产 率的作用也不大。这时辅助工时在总的零件单件工时 中所占的比例已经较小,切削工时占去了总工时的主 要部分,成为主要矛盾。只有大幅度地减少切削工时, 即提高切削速度和进给速度等,才有可能在提高生产 率方面出现一次新的飞跃和突破。这就是超高速加工 技术(Ultra-high speed machining UHSM)得以 迅速发展的历史背景。。
日本约在20世纪60年代开始了对超高速切削机 制的研究,田中义信利用来复枪改制的超高速切削 装置,实现了高达200~700m/s的超高速切削,对主 切削力和加工表面的变形层性能进行研究。指出: 超高速切屑形成完全是剪切作用的结果,随着切削 速度的提高,剪切角急剧增大,工件材料的变质层 厚度与普通速度下相比降低了50%。
W9Mo3Cr4V等。
硬质合金:是由高硬难熔金属碳
化物粉末,以钴或镍为粘接剂,用粉末
冶金的方法制成的。它的硬度可达
74 ~82(90)HRC。目前多用于制 造各种简单刀具,如车刀、铣刀、刨刀 的刀片等。
超高速加工技术
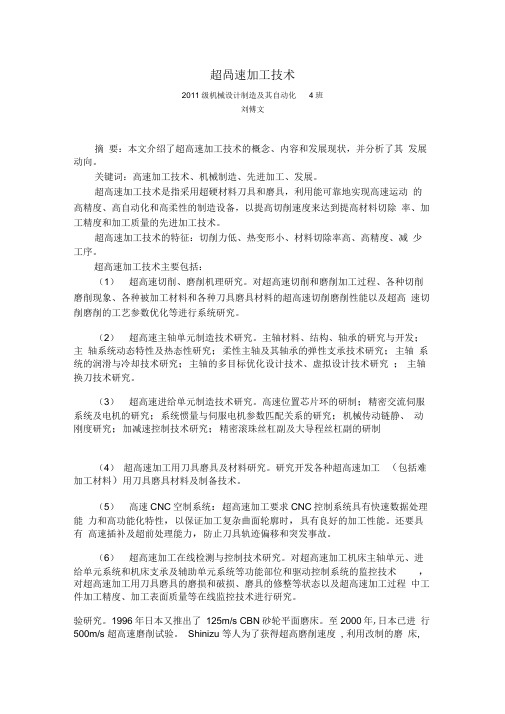
超咼速加工技术2011级机械设计制造及其自动化4班刘傅文摘要:本文介绍了超高速加工技术的概念、内容和发展现状,并分析了其发展动向。
关键词:高速加工技术、机械制造、先进加工、发展。
超高速加工技术是指采用超硬材料刀具和磨具,利用能可靠地实现高速运动的高精度、高自动化和高柔性的制造设备,以提高切削速度来达到提高材料切除率、加工精度和加工质量的先进加工技术。
超高速加工技术的特征:切削力低、热变形小、材料切除率高、高精度、减少工序。
超高速加工技术主要包括:(1)超高速切削、磨削机理研究。
对超高速切削和磨削加工过程、各种切削磨削现象、各种被加工材料和各种刀具磨具材料的超高速切削磨削性能以及超高速切削磨削的工艺参数优化等进行系统研究。
(2)超高速主轴单元制造技术研究。
主轴材料、结构、轴承的研究与开发;主轴系统动态特性及热态性研究;柔性主轴及其轴承的弹性支承技术研究;主轴系统的润滑与冷却技术研究;主轴的多目标优化设计技术、虚拟设计技术研究;主轴换刀技术研究。
(3)超高速进给单元制造技术研究。
高速位置芯片环的研制;精密交流伺服系统及电机的研究;系统惯量与伺服电机参数匹配关系的研究;机械传动链静、动刚度研究;加减速控制技术研究;精密滚珠丝杠副及大导程丝杠副的研制(4)超高速加工用刀具磨具及材料研究。
研究开发各种超高速加工(包括难加工材料)用刀具磨具材料及制备技术。
(5)高速CNC空制系统:超高速加工要求CNC控制系统具有快速数据处理能力和高功能化特性,以保证加工复杂曲面轮廓时,具有良好的加工性能。
还要具有高速插补及超前处理能力,防止刀具轨迹偏移和突发事故。
(6)超高速加工在线检测与控制技术研究。
对超高速加工机床主轴单元、进给单元系统和机床支承及辅助单元系统等功能部位和驱动控制系统的监控技术,对超高速加工用刀具磨具的磨损和破损、磨具的修整等状态以及超高速加工过程中工件加工精度、加工表面质量等在线监控技术进行研究。
验研究。
超高速加工技术作业

超高速加工技术研究内容
1.超高速切削原理
在机械加工中, 切
削温度是一个重要的
制约参数。根据德国
著名切削物学家萨洛
蒙的超高速切削理论,钢材的切削来自度与切削温度可用萨洛蒙曲
线来表示(参见图),曲
线表明切削速度和切
图1
削温度不是呈线性的。
萨洛蒙曲线
图2 切削速度与摩擦系数关系
3.高速加工的特点
➢切削力低 切削变形小,切屑流出速度加快,切削力 比常规降低30-90%,可高质量地加工出薄壁零件;
超高速加工技术
• 技术概述 • 研究内容 • 技术应用 • 发展趋势 • 加工刀具
超高速加工技术的概述
• 超高速加工技术是指采用超硬材料的刃具, 通过极大地提高切削速度和进给速度来提 高材料切除率、加工精度和加工质量的现 代加工技术。
• 超高速加工技术主要包括:超高速切削与 磨削机理研究,超高速主轴单元制造技术, 超高速进给单元制造技术,超高速加工用 刀具与磨具制造技术,超高速加工在线自 动检测与控制技术等。
图5 波音公司的F15战斗机的起动减速板
图6 高速铣削典型工件
铝合金整体零件: 整体零件“掏空”,
切除量大 零件有薄壁,要求小
切削力 小直径刀具 较长的刀具悬伸
2.模具制造 当采用高转速、高进给、低切削深度的加工方法
时,对淬硬钢模具型腔加工可获得较佳的表面质量, 可省去后续的电加工和手工研磨等程序。 3.汽车制造
图 3 加工零件
➢ 材料切除率高 单位时间内切除率可提高3-5倍;
➢ 高精度 切削激振频率远高于机床系统固有频率, 加工平稳、振动小;
➢ 热变形小 温升不超过3ºC,90%切削热被切屑带走;
A为高速切削加工时的热传导过程 B为传统加工的热传导过程
超高速超精密加工技术主要内容

高可靠性
超高速超精密加工技术可以保证加 工过程的稳定性和可靠性,减少故 障和误差。
技术挑战
设备成本高
超高速超精密加工设备成本较高,需要大量的资 金投入。
技术难度大
超高速超精密加工技术难度较大,需要高技能的 技术人员操作和维护。
加工材料有限
纳米级加工技术是利用纳米级的加工工具和工艺来制造纳米 级零件和结构的技术。
详细描述
纳米级加工技术采用特殊的加工工具和工艺,如纳米压印、 纳米光刻等,实现纳米级别的加工精度。该技术能够制造出 具有纳米级精度和复杂结构的零件和结构,广泛应用于微电 子、生物医学等领域。
加工设备与工具
总结词
加工设备与工具是实现超高速超精密加工的关键因素之一。
详细描述
加工设备与工具的精度、稳定性和可靠性对超高速超精密加工的加工效果和效率有着至关重要的影响 。先进的加工设备与工具能够提供更高的加工精度和效率,同时减少误差和故障率,提高加工质量和 效率。
04
技术优势与挑战
技术优势
高效率
超高速加工技术可以大大提高加 工效率,缩短加工时间,降低生
产成本。
高精度
微型机械零件
该技术还可以用于制造微型机械零件,如微型传感器、微型执行器等,以满足微电子领域对高精度、小尺寸零件 的需求。
其他ቤተ መጻሕፍቲ ባይዱ域应用案例
医疗器械领域
超高速超精密加工技术可以用于制造医疗器械,如人工关节、牙科种植体等,以提高其 表面质量和生物相容性。
能源领域
该技术还可以用于制造能源设备,如太阳能电池板、燃料电池等,以提高其光电转换效 率和能量密度。
优化切削参数和刀具路径, 提高工件表面完整性和光 洁度。
超精密加工技术概述

超精密加工技术概述摘要:随着社会的发展,工业产品精细化程度逐步提高,传统的机械加工技术已经远远不能满足人们的需求,机械加工向着更高精度的方向发展。
本文主要介绍超精密加工技术的产生背景、概念、国内外的发展状况、几种超精密加工技术和对未来超精密加工技术发展的展望。
关键词:超精密加工技术背景概念发展状况发展趋势一.产生的背景制造技术的发展已经有几千年的历史,石器时代、铜器时代、铁器时代都有着制造技术发展的足迹。
直至近代,随着第一次工业革命的完成,传统的机械制造技术出现了,传统的机械加工技术主要包括车削、铣削、钻削和磨削。
随着人类社会的进一步发展,现代科学技术的迅猛发展,机械工业、电子工业、航空航天工业、化学工业等,尤其是国防工业部门,要求尖端科学技术产品向高精度、高速度、大功率、小型化方向发展,以及在高温、高压、重载荷或腐蚀环境下长期可靠地工作。
为了适应这些要求,各种新结构、新材料和复杂形状的精密零件大量出现,其结构和形状越来越复杂,材料的性能越来越强韧,对精度要求越来越高,对加工表面粗糙度和完整性要求越来越严格,使机械制造面临着一系列严峻的任务:(1)解决各种难切削材料的加工问题。
如硬质合金、钛合金、耐热钢、不锈钢、淬火钢、金刚石、石英以及锗、硅等各种高硬度,高强度、高韧性、高脆性的金属及非加工。
(2)解决各种特殊复杂型面的加工问题。
如喷气涡轮机叶片、整体涡轮、发动机机匣、锻压模等的立体成型表面,各种冲模、冷拔模等特殊断面的型孔,炮管内膛线、喷油嘴,喷丝头上的小孔、窄缝等的加工。
(3)解决各种超精密、光整零件的加工问题。
如对表面质量和精度要求很高的航天航空陀螺仪、精密光学透镜、激光核聚变用的曲面镜、高灵敏度的红外传感器等零件的精细表面加工,形状和尺寸精度要求在0.1皮米以上,表面粗糙度尺寸要求在0.01微米以上。
(4)特殊零件的加工问题。
如大规模集成电路、光盘基片、复印机和打印机的感光鼓、微型机械和机器人零件、细长轴、薄壁零件、弹性元件等低刚度零件的加工。
高速高效加工理论与技术
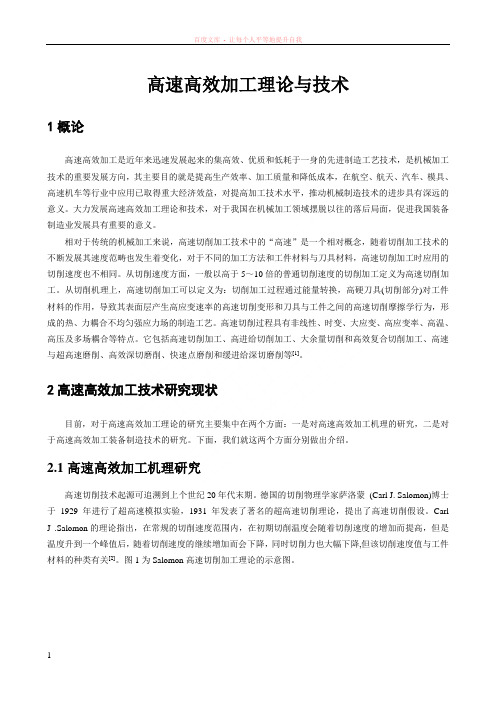
高速高效加工理论与技术1概论高速高效加工是近年来迅速发展起来的集高效、优质和低耗于一身的先进制造工艺技术,是机械加工技术的重要发展方向,其主要目的就是提高生产效率、加工质量和降低成本,在航空、航天、汽车、模具、高速机车等行业中应用已取得重大经济效益,对提高加工技术水平,推动机械制造技术的进步具有深远的意义。
大力发展高速高效加工理论和技术,对于我国在机械加工领域摆脱以往的落后局面,促进我国装备制造业发展具有重要的意义。
相对于传统的机械加工来说,高速切削加工技术中的“高速”是一个相对概念,随着切削加工技术的不断发展其速度范畴也发生着变化,对于不同的加工方法和工件材料与刀具材料,高速切削加工时应用的切削速度也不相同。
从切削速度方面,一般以高于5~10倍的普通切削速度的切削加工定义为高速切削加工。
从切削机理上,高速切削加工可以定义为:切削加工过程通过能量转换,高硬刀具(切削部分)对工件材料的作用,导致其表面层产生高应变速率的高速切削变形和刀具与工件之间的高速切削摩擦学行为,形成的热、力耦合不均匀强应力场的制造工艺。
高速切削过程具有非线性、时变、大应变、高应变率、高温、高压及多场耦合等特点。
它包括高速切削加工、高进给切削加工、大余量切削和高效复合切削加工、高速与超高速磨削、高效深切磨削、快速点磨削和缓进给深切磨削等[1]。
2高速高效加工技术研究现状目前,对于高速高效加工理论的研究主要集中在两个方面:一是对高速高效加工机理的研究,二是对于高速高效加工装备制造技术的研究。
下面,我们就这两个方面分别做出介绍。
2.1高速高效加工机理研究高速切削技术起源可追溯到上个世纪20年代末期。
德国的切削物理学家萨洛蒙(Carl J. Salomon)博士于1929年进行了超高速模拟实验,1931年发表了著名的超高速切削理论,提出了高速切削假设。
Carl J .Salomon的理论指出,在常规的切削速度范围内,在初期切削温度会随着切削速度的增加而提高,但是温度升到一个峰值后,随着切削速度的继续增加而会下降,同时切削力也大幅下降,但该切削速度值与工件材料的种类有关[2]。
先进制造技术讲稿2-先进制造工艺技术
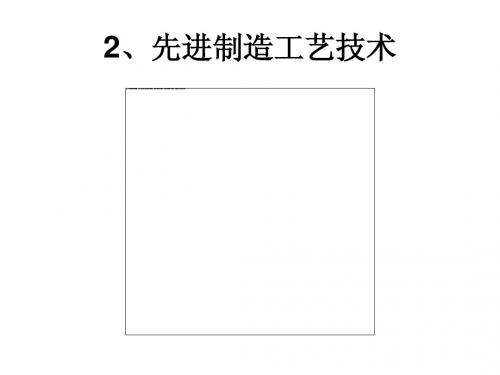
此外,精密加工与特种加工 一般都是计算机控制的自动化 加工。
• “精密加工”的含义:
–加工精度精密化
• 人造卫星的仪表轴承,其圆度、圆柱度、表面粗糙度等 均达纳米级;
–操作尺度细微化
• 基因操作机械,其移动距离为纳米级,移动精度为0.1纳 米级
–物理性能精确化
_物理性能、力学性能、化学性能、生化性能等等
–控制要求纳米化
• 超精密加工
20世纪初:
30年代: 50年代: 70-80年代: 目前:
10微米
1微米 0.1微米 0.01微米 0.001微米
(纳米加工)
• 电子制造: 高精度:控制趋于纳米级 加工趋于亚纳米级 超微细:芯片线宽<100nm 运动副间隙<12nm 高加速度:封装运动>12g 高可靠性:芯片千小时失效率<1/109
2、先进制造工艺技术
2.1超精密加工技术和纳米加工技术
• 2.1.1 基本概念
• (1)精密制造技术:精密制造技术是指零件毛坯成 形后余量小或无余量、零件毛坯加工后精度达亚微米 级的生产技术总称。它是近净成形与近无缺陷成形技 术、超精密加工技术与超高速加工技术的综合集成。 • (2)近净成形与近无缺陷成形技术改造了传统的毛 坯成形技术,使机械产品毛坯成形实现由粗放到精化 的转变,使外部质量作到无余量或接近无余量,内部 质量作到无缺陷或接近无缺陷,实现优质、高效、轻 量化、低成本的成形。该项技术涉及到铸造成形、塑 性成形、精确连接、热处理改性、表面改性、高精度 模具等专业领域。
2.3.2 电解加工
电解加工是利用金属在电解液中产生阳极溶解的 电化学腐蚀将工件加工成形,又称电化学加工。 电解加工的工具(阴极)不发生溶解,可长期使 用。可在一个工序内完成复杂形状的加工. 电镀修补。
高速磨削方法简介
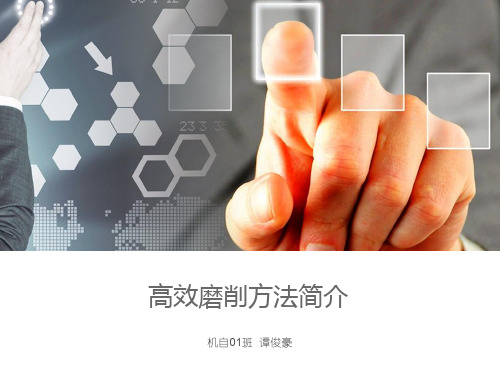
2、应用缓进给强力磨削,在加大砂轮径向 进给量(即磨削深度)的同时,配以缓慢的 工件进给速度,从而增加同时参与切削的 磨粒数。
3、采用砂带磨削或宽砂轮磨削,以增加磨 削宽度达到增加参加切削的磨粒数的效果。
高速磨削简介
(1) 超高速磨削的最大优越性在它能越过磨削“热沟”的影 响,减少传入工件的磨削热,从而可以减少或避免工件表 面的磨削“烧伤”,保证工件的加工质量。而且,超高速 磨削在应用中符合绿色制造的加工原则。
(2) 超高速磨削是提高磨削效率、降低工件表面粗糙度和提 高工件加工质量的先进加工技术,尤其对硬脆材料能实现 延性域磨削,对高强度难磨材料也能取得良好的磨削效果, 这对某些领域是难得可贵的。
高效磨削方法简介
机自01班 谭俊豪
高效磨削方法
高效率磨削加工技术主要包括:高速/超高速磨削、 缓进给深磨、高效深切磨削、强力磨削和强力珩 磨、高速重负荷荒磨、砂带磨削、硬脆/难加工材 料高效率磨削、高效率研磨和抛光等
一、高速磨削 二、强力磨削 三、砂带磨削
提高磨削效率的途径对应的三条:
五、砂带磨削成本低。这主要表现在: (1)与砂轮磨床相比,砂带磨床结构简单,传
动链短。这主要是因为砂带质量轻,磨削力小, 磨削过程中震动小,对机床的刚性及强度要求都 远低于砂轮磨床。
(2)砂带磨削操作简便,辅助时间少。不论是 手动还是机动砂带磨削,其操作都非常简便。从 更换调整砂带到被加工工件的装夹,这一切都可 以在很短的时间内完成。
(6)加工精度和表面粗糙度小。
要求及原理
由于磨削深度大,砂轮与工件的接触弧长比 普通磨削大几倍至几十倍,磨削力、磨削功率和 磨削热大幅度增加,故要求机床刚度好、功率大, 并设有高压大流量的切削液喷射冷却系统,以便有 效地冷却工件,冲走磨屑。
- 1、下载文档前请自行甄别文档内容的完整性,平台不提供额外的编辑、内容补充、找答案等附加服务。
- 2、"仅部分预览"的文档,不可在线预览部分如存在完整性等问题,可反馈申请退款(可完整预览的文档不适用该条件!)。
- 3、如文档侵犯您的权益,请联系客服反馈,我们会尽快为您处理(人工客服工作时间:9:00-18:30)。
超高速超精密加工技术主要内容
一 超高速加工技术
超高速加工技术的内涵
超高速加工技术的关键技术(重点)
加工机理研究
主轴单元制造技术研究 进给单元制造技术研究
刀具、磨具研究
超高速加工技术的应用 超高速加工技术的发展趋势
二 超精密加工技术
超精密加工技术的内涵
超精密加工技术的关键技术(重点)
加工方法及机理研究 刀具、磨具的研究 加工装备技术研究
பைடு நூலகம்测量技术研究
超精密加工技术的应用
超精密加工技术的发展趋势
作 业
(1)超高速、超精密加工技术二者选择其一。
(2)按照上述提纲要求查阅文献,然后归纳总结写出 “文献综述”。
(3)要求条理清晰,内容精练,3000~5000字。 (4)必需手写,不能打印。 (5)该作业作为本课程平时成绩的一部分,占15%。