甲醇精馏装置系统运行总结
甲醇合成精馏装置的节能降耗措施及运行总结

甲醇合成精馏装置的节能降耗措施及运行总结陕西精益化工有限公司陕西省榆林市神木市 719300摘要:本文主要介绍了甲醇合成精馏装置的生产工艺,以及装置在生产过程中存在的一些问题及解决措施,以达到节能降耗,降低生产成本,提高经济效益的目的。
通过对甲醇合成精馏装置进行节能降耗改造,可以降低生产过程中蒸汽消耗,减少尾气排放,提高甲醇品质,降低甲醇消耗,达到节能降耗目的。
同时本文还分析了甲醇合成精馏装置在运行过程中存在的问题和不足之处,并提出了相应的解决措施。
最后通过对甲醇合成精馏装置进行运行总结可以看出这些措施是有效的、可行的,对于甲醇合成精馏装置今后的安全、平稳、长周期运行具有重要意义。
关键词:甲醛;节能;生产工艺1.前言甲醇合成精馏装置是指用甲醇生产过程中的废液和废气经净化处理后作为原料进行合成,在一定温度下甲醇和水被分离,形成合格的成品。
精馏装置是甲醇生产过程中必不可少的部分,它是生产中主要的单元操作之一。
精馏装置主要包括汽提塔和精馏塔,其基本组成为甲醇和水。
合成气经变换单元后,生成高纯度的工业气体即甲醇。
合成气经过塔后与塔顶和塔釜进行混合,最后进入精馏塔进行分离和精馏。
该装置可生产出质量分数为90%以上的工业级甲醇产品,满足国家规定的标准要求。
它是工业生产中不可缺少的单元操作之一,同时也是工业生产中主要能耗之一,在实际生产过程中应尽可能采取有效措施来降低能耗。
1.工艺流程简介甲醇合成精馏装置所用工艺路线为:甲醇压缩机将粗甲醇加压(压力为1.6 MPa)至180~210℃,并送入粗甲醇精馏塔和精馏塔。
粗醇经过塔顶汽提后进入精馏塔,由于压力较低,从塔顶排出的尾气被送到火炬燃烧;精馏塔由低压蒸汽加热,使蒸汽量达到100t/h。
粗醇经过精馏塔后的尾气和蒸汽进入火炬燃烧系统,然后将剩余的尾气送至天然气储罐。
1.装置生产中存在的问题及采取的措施塔盘腐蚀问题。
针对塔盘腐蚀问题,对塔盘喷淋装置进行改造,新安装了喷淋管,对塔盘和整个甲醇合成塔进行喷淋,防止塔盘内壁腐蚀。
甲醇合成装置优化运行总结
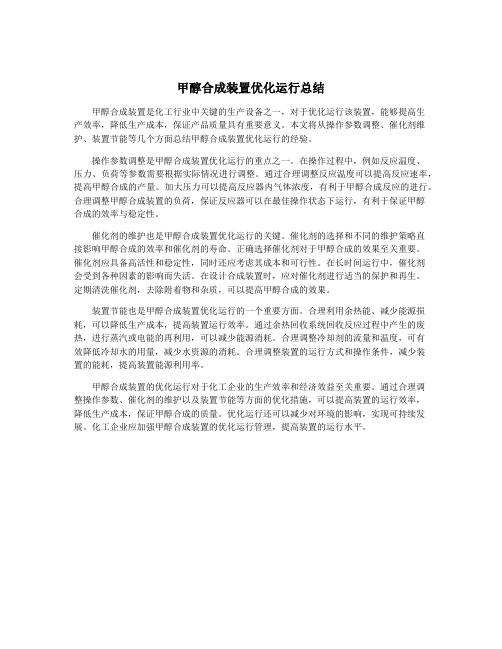
甲醇合成装置优化运行总结甲醇合成装置是化工行业中关键的生产设备之一,对于优化运行该装置,能够提高生产效率,降低生产成本,保证产品质量具有重要意义。
本文将从操作参数调整、催化剂维护、装置节能等几个方面总结甲醇合成装置优化运行的经验。
操作参数调整是甲醇合成装置优化运行的重点之一。
在操作过程中,例如反应温度、压力、负荷等参数需要根据实际情况进行调整。
通过合理调整反应温度可以提高反应速率,提高甲醇合成的产量。
加大压力可以提高反应器内气体浓度,有利于甲醇合成反应的进行。
合理调整甲醇合成装置的负荷,保证反应器可以在最佳操作状态下运行,有利于保证甲醇合成的效率与稳定性。
催化剂的维护也是甲醇合成装置优化运行的关键。
催化剂的选择和不同的维护策略直接影响甲醇合成的效率和催化剂的寿命。
正确选择催化剂对于甲醇合成的效果至关重要。
催化剂应具备高活性和稳定性,同时还应考虑其成本和可行性。
在长时间运行中,催化剂会受到各种因素的影响而失活。
在设计合成装置时,应对催化剂进行适当的保护和再生。
定期清洗催化剂,去除附着物和杂质,可以提高甲醇合成的效果。
装置节能也是甲醇合成装置优化运行的一个重要方面。
合理利用余热能、减少能源损耗,可以降低生产成本,提高装置运行效率。
通过余热回收系统回收反应过程中产生的废热,进行蒸汽或电能的再利用,可以减少能源消耗。
合理调整冷却剂的流量和温度,可有效降低冷却水的用量,减少水资源的消耗。
合理调整装置的运行方式和操作条件,减少装置的能耗,提高装置能源利用率。
甲醇合成装置的优化运行对于化工企业的生产效率和经济效益至关重要。
通过合理调整操作参数、催化剂的维护以及装置节能等方面的优化措施,可以提高装置的运行效率,降低生产成本,保证甲醇合成的质量。
优化运行还可以减少对环境的影响,实现可持续发展。
化工企业应加强甲醇合成装置的优化运行管理,提高装置的运行水平。
甲醇合成装置优化运行总结
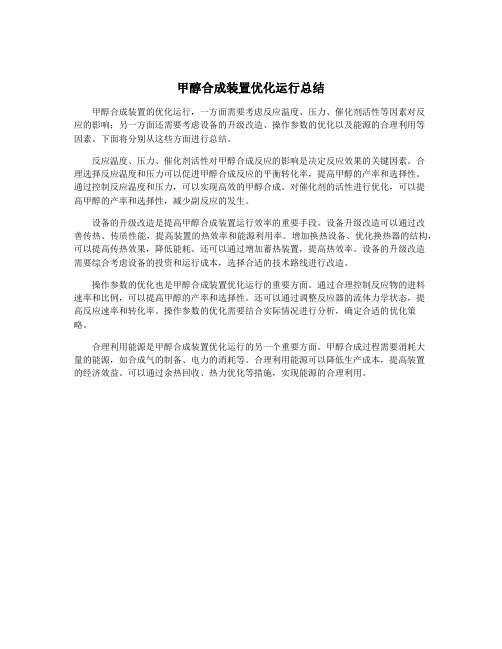
甲醇合成装置优化运行总结
甲醇合成装置的优化运行,一方面需要考虑反应温度、压力、催化剂活性等因素对反
应的影响;另一方面还需要考虑设备的升级改造、操作参数的优化以及能源的合理利用等
因素。
下面将分别从这些方面进行总结。
反应温度、压力、催化剂活性对甲醇合成反应的影响是决定反应效果的关键因素。
合
理选择反应温度和压力可以促进甲醇合成反应的平衡转化率,提高甲醇的产率和选择性。
通过控制反应温度和压力,可以实现高效的甲醇合成。
对催化剂的活性进行优化,可以提
高甲醇的产率和选择性,减少副反应的发生。
设备的升级改造是提高甲醇合成装置运行效率的重要手段。
设备升级改造可以通过改
善传热、传质性能,提高装置的热效率和能源利用率。
增加换热设备、优化换热器的结构,可以提高传热效果,降低能耗。
还可以通过增加蓄热装置,提高热效率。
设备的升级改造
需要综合考虑设备的投资和运行成本,选择合适的技术路线进行改造。
操作参数的优化也是甲醇合成装置优化运行的重要方面。
通过合理控制反应物的进料
速率和比例,可以提高甲醇的产率和选择性。
还可以通过调整反应器的流体力学状态,提
高反应速率和转化率。
操作参数的优化需要结合实际情况进行分析,确定合适的优化策
略。
合理利用能源是甲醇合成装置优化运行的另一个重要方面。
甲醇合成过程需要消耗大
量的能源,如合成气的制备、电力的消耗等。
合理利用能源可以降低生产成本,提高装置
的经济效益。
可以通过余热回收、热力优化等措施,实现能源的合理利用。
甲醇精馏系统设计总结
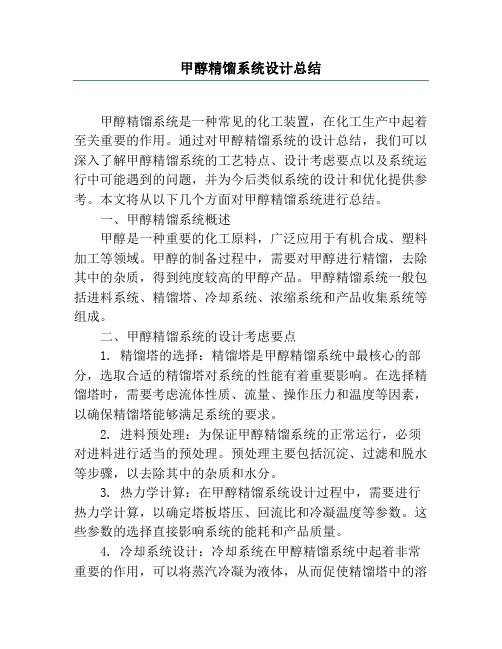
甲醇精馏系统设计总结甲醇精馏系统是一种常见的化工装置,在化工生产中起着至关重要的作用。
通过对甲醇精馏系统的设计总结,我们可以深入了解甲醇精馏系统的工艺特点、设计考虑要点以及系统运行中可能遇到的问题,并为今后类似系统的设计和优化提供参考。
本文将从以下几个方面对甲醇精馏系统进行总结。
一、甲醇精馏系统概述甲醇是一种重要的化工原料,广泛应用于有机合成、塑料加工等领域。
甲醇的制备过程中,需要对甲醇进行精馏,去除其中的杂质,得到纯度较高的甲醇产品。
甲醇精馏系统一般包括进料系统、精馏塔、冷却系统、浓缩系统和产品收集系统等组成。
二、甲醇精馏系统的设计考虑要点1. 精馏塔的选择:精馏塔是甲醇精馏系统中最核心的部分,选取合适的精馏塔对系统的性能有着重要影响。
在选择精馏塔时,需要考虑流体性质、流量、操作压力和温度等因素,以确保精馏塔能够满足系统的要求。
2. 进料预处理:为保证甲醇精馏系统的正常运行,必须对进料进行适当的预处理。
预处理主要包括沉淀、过滤和脱水等步骤,以去除其中的杂质和水分。
3. 热力学计算:在甲醇精馏系统设计过程中,需要进行热力学计算,以确定塔板塔压、回流比和冷凝温度等参数。
这些参数的选择直接影响系统的能耗和产品质量。
4. 冷却系统设计:冷却系统在甲醇精馏系统中起着非常重要的作用,可以将蒸汽冷凝为液体,从而促使精馏塔中的溶质凝聚。
在冷却系统的设计中,需要考虑冷凝器的换热面积、冷却介质的选择以及冷凝水的排放等问题。
5. 安全措施:在甲醇精馏系统设计过程中,必须重视安全问题。
甲醇具有易燃、易爆和有毒的特性,因此需要在系统设计中考虑到这些特点,合理配置防爆设备和防火措施,并确保系统在运行中具有良好的安全性能。
三、甲醇精馏系统设计中可能遇到的问题1. 能耗高:甲醇精馏系统在操作过程中容易产生大量废热,导致能耗较高。
为了解决这个问题,可以采取适当的措施,如增加热耗散装置和优化换热设备等。
2. 运行不稳定:甲醇精馏系统的精馏塔易受到进料质量波动的影响,容易出现运行不稳定的情况。
甲醇精馏装置扩能改造运行总结
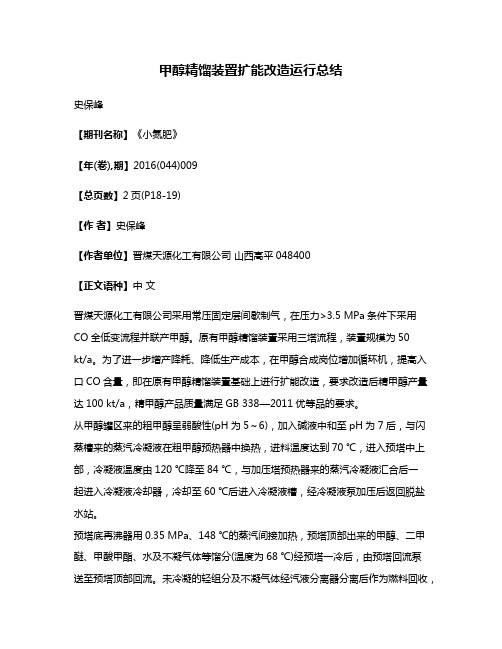
甲醇精馏装置扩能改造运行总结史保峰【期刊名称】《小氮肥》【年(卷),期】2016(044)009【总页数】2页(P18-19)【作者】史保峰【作者单位】晋煤天源化工有限公司山西高平048400【正文语种】中文晋煤天源化工有限公司采用常压固定层间歇制气,在压力>3.5 MPa条件下采用CO全低变流程并联产甲醇。
原有甲醇精馏装置采用三塔流程,装置规模为50kt/a。
为了进一步增产降耗、降低生产成本,在甲醇合成岗位增加循环机,提高入口CO含量,即在原有甲醇精馏装置基础上进行扩能改造,要求改造后精甲醇产量达100 kt/a,精甲醇产品质量满足GB 338—2011优等品的要求。
从甲醇罐区来的粗甲醇呈弱酸性(pH为5~6),加入碱液中和至pH为7后,与闪蒸槽来的蒸汽冷凝液在粗甲醇预热器中换热,进料温度达到70 ℃,进入预塔中上部,冷凝液温度由120 ℃降至84 ℃,与加压塔预热器来的蒸汽冷凝液汇合后一起进入冷凝液冷却器,冷却至60 ℃后进入冷凝液槽,经冷凝液泵加压后返回脱盐水站。
预塔底再沸器用0.35 MPa、148 ℃的蒸汽间接加热,预塔顶部出来的甲醇、二甲醚、甲酸甲酯、水及不凝气体等馏分(温度为68 ℃)经预塔一冷后,由预塔回流泵送至预塔顶部回流。
未冷凝的轻组分及不凝气体经汽液分离器分离后作为燃料回收,或经液封槽高点放空。
预塔底部为脱醚后的甲醇(82 ℃),预塔回流槽和汽液分离器可采出少量轻馏分进入异丁基油槽。
脱醚后甲醇由预后泵送至加压塔预热器,将进料温度加热至110 ℃后再送至加压塔中下部。
加压塔预热器用闪蒸槽来的低压蒸汽为热源,冷凝温度为120 ℃;加压塔再沸器也采用0.35 MPa蒸汽间接加热,加压塔顶部出来的甲醇蒸气进入冷凝再沸器冷凝,冷凝液进入常压塔中下部;加压塔上部侧线采出精甲醇,经加压塔冷却器冷却后进入精甲醇中间槽。
常压塔底部的冷凝再沸器作为塔底再沸器,使用加压塔顶部甲醇蒸气冷凝热作为再沸热源。
甲醇装置设备工作总结与工作计划 煤化公司
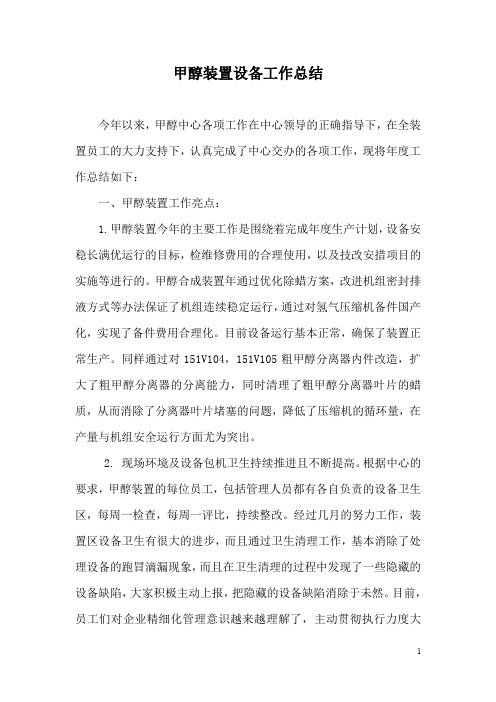
甲醇装置设备工作总结今年以来,甲醇中心各项工作在中心领导的正确指导下,在全装置员工的大力支持下,认真完成了中心交办的各项工作,现将年度工作总结如下:一、甲醇装置工作亮点:1.甲醇装置今年的主要工作是围绕着完成年度生产计划,设备安稳长满优运行的目标,检维修费用的合理使用,以及技改安措项目的实施等进行的。
甲醇合成装置年通过优化除蜡方案,改进机组密封排液方式等办法保证了机组连续稳定运行,通过对氢气压缩机备件国产化,实现了备件费用合理化。
目前设备运行基本正常,确保了装置正常生产。
同样通过对151V104,151V105粗甲醇分离器内件改造,扩大了粗甲醇分离器的分离能力,同时清理了粗甲醇分离器叶片的蜡质,从而消除了分离器叶片堵塞的问题,降低了压缩机的循环量,在产量与机组安全运行方面尤为突出。
2. 现场环境及设备包机卫生持续推进且不断提高。
根据中心的要求,甲醇装置的每位员工,包括管理人员都有各自负责的设备卫生区,每周一检查,每周一评比,持续整改。
经过几月的努力工作,装置区设备卫生有很大的进步,而且通过卫生清理工作,基本消除了处理设备的跑冒滴漏现象,而且在卫生清理的过程中发现了一些隐藏的设备缺陷,大家积极主动上报,把隐藏的设备缺陷消除于未然。
目前,员工们对企业精细化管理意识越来越理解了,主动贯彻执行力度大了,对设备操作维护的精细意识也越来越强了。
3 做好本安体系设备管理专业的工作。
①甲醇成品罐区属于甲醇装置责任区,也是每次本安体系检查和其它安全检查的重点区域。
由于项目建设标准低,遗漏下好多安全隐患,结合安全评价检查和每季度本安体系检查组专家的意见和我们日常检查发现的隐患,我们分开轻重缓急,逐步整改,年底全部完成安措项目的整改。
罐区面貌大有改观,安全隐患逐步降低。
②本年度,甲醇装置完成俩项重大安措整改项目,⑴.成品罐区甲醇成品储罐入口阀门增设电动头;⑵.甲醇装置蒸汽过热炉增加火焰检测装置,此项是集团公司级的隐患治理项目。
甲醇精馏系统自循环操作运行小结

新能凤凰 (滕州) 能源有限公司 (简称新 能凤凰) 有 2套 360kt/a甲醇装置。对置式四喷 嘴水煤浆加压气化炉生产的水煤气,经变换、低 温甲醇洗后进入甲醇合成系统;甲醇合成系统、 甲醇精馏系统各为 2套,2套系统并联运行,甲 醇合成系统产出的粗甲醇分别进入 2套甲醇精馏 系统 (简称精馏Ⅰ系统、精馏Ⅱ系统),粗醇经 精馏后送往中间罐区暂时储存,分析合格后送罐 区储槽 (对外销售)。正常生产中,2套甲醇精 馏系统分别与 2套甲醇合成系统相对应,也可以 相互切换,即一期甲醇合成系统和二期甲醇合成 系统的粗醇可以互送,避免甲醇精馏系统因各种 原因停车,达到不影响前系统运行、不降低系统 负荷的目的。
新能凤凰的甲醇精馏系统年运行时间设计为
[收稿日期]20180418 [修稿日期]20180424
8000h,目前单套甲醇精馏系统产能 500kt/a,
[作者简介]赵兰刚(1984—),男,山东滕州人,高级技师。
双套为 1000kt/a(2015年为提高市场竞争力、
櫅櫅櫅櫅櫅櫅櫅櫅櫅櫅櫅櫅櫅櫅櫅櫅櫅櫅櫅櫅櫅櫅櫅櫅櫅櫅櫅櫅櫅櫅櫅櫅櫅櫅櫅櫅櫅櫅櫅櫅櫅櫅櫅櫅
第 6期 2018年 11月
中 氮 肥 MSizedNitrogenousFertilizerProgress
甲醇精馏系统自循环操作运行小结
No6 N有限公司,山东 滕州 277527]
[摘 要]新能凤凰 (滕州) 能源有限公司 2×360kt/a甲醇装置精馏系统采用节能型三塔精馏工艺, 自 2013年实现甲醇装置长周期运行以来,创出了单套系统连续运行超过 500d、2套系统连续运行超过 300d 的纪录,生产中出现的问题基本上可进行在线处理;同时,经过多年的经验积累,在气化炉倒炉、更换烧 嘴或是因其他原因导致蒸汽供应不足的情况下,摸索出甲醇精馏系统采取停止进料、停止采出的方式建立 物料三塔自循环的操作方法,此法可使甲醇精馏系统在蒸汽满足生产所需时开车 (加蒸汽,进料) 后产品 快速合格,从而降低系统蒸汽消耗,提高甲醇收率,降低开停车过程对设备造成的影响,实现甲醇精馏系 统的连续、环保、经济运行。
甲醇合成装置优化运行总结

甲醇合成装置优化运行总结甲醇是一种广泛应用的有机化工产品,其合成装置的优化运行对于提高甲醇生产效率、降低能耗、提升产品质量具有重要意义。
本次运行总结主要包括以下几个方面的内容。
针对甲醇合成反应器的优化运行。
反应器是整个合成装置的核心部分,其运行状态直接影响甲醇的合成效果。
在本次运行中,我们对反应器的温度、压力、催化剂的投料速度和搅拌速度等参数进行了优化调整。
通过合理地控制这些参数,提高了甲醇的产率和选择性,降低了副产物的生成率。
我们还注意到反应器内催化剂的老化问题,及时对老化催化剂进行更换,保证了反应的高效进行。
针对甲醇合成装置的能耗优化。
合成甲醇过程中能耗是一个重要的经济指标。
通过对装置的能耗进行全面的分析和评估,我们发现了一些能耗较高的环节,冷凝器的工作温度过高、泵的运行效率偏低等。
针对这些问题,我们采取了相应的措施,改善了能耗状况。
对冷凝器进行了维修和改造,减少了冷却水的使用量,降低了能耗。
我们还对泵进行了调试和优化,提高了泵的运行效率,降低了能耗。
针对甲醇产品质量的优化。
甲醇的产品质量对于其应用领域的不同有着不同的要求。
在本次运行中,我们注重了甲醇产品质量的监测和控制。
通过对甲醇产品进行多次的取样和分析,我们发现了一些质量问题,如杂质含量过高、甲醇含量波动较大等。
通过调整原料的配比比例、优化催化剂的选择和控制反应温度等措施,我们改善了甲醇产品的质量,满足了用户的需求。
针对安全和环保问题的优化。
在甲醇合成装置的运行中,安全和环保问题是至关重要的。
我们始终把安全和环保放在首位,采取了一系列的措施来保障生产过程的安全和环境的保护。
加强了现场人员的安全培训,提高了员工的安全意识;加强了废水和废气处理设施的运行维护,降低了对环境的污染。
通过对甲醇合成装置的优化运行,我们提高了甲醇的生产效率、降低了能耗、提升了产品质量,同时确保了生产过程的安全和环保。
仍然存在一些问题和不足之处,例如催化剂的寿命仍有待进一步提高,能耗仍有一定的改进空间。
高效节能甲醇精馏运行总结
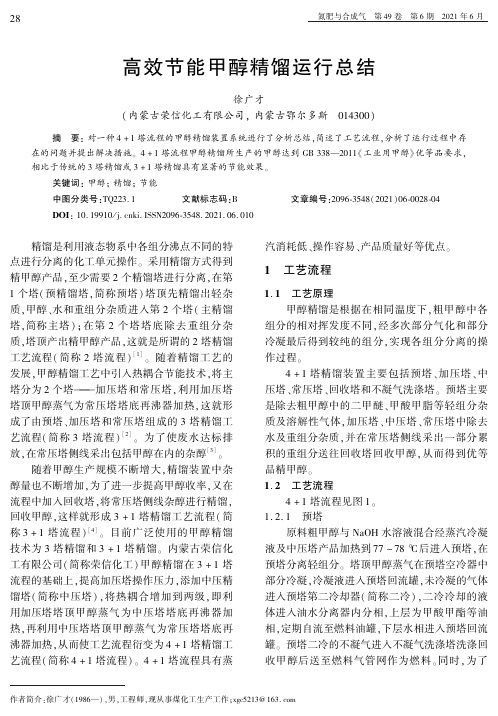
高效节能甲醇精馏运行总结徐广才(内蒙古荣信化工有限公司ꎬ内蒙古鄂尔多斯㊀014300)㊀㊀摘㊀要:对一种4+1塔流程的甲醇精馏装置系统进行了分析总结ꎬ简述了工艺流程ꎬ分析了运行过程中存在的问题并提出解决措施ꎮ4+1塔流程甲醇精馏所生产的甲醇达到GB338 2011«工业用甲醇»优等品要求ꎬ相比于传统的3塔精馏或3+1塔精馏具有显著的节能效果ꎮ㊀㊀关键词:甲醇ꎻ精馏ꎻ节能㊀㊀中图分类号:TQ223.1㊀㊀㊀㊀㊀文献标志码:B㊀㊀㊀㊀㊀文章编号:2096 ̄3548(2021)06 ̄0028 ̄04㊀㊀DOI:10.19910/j.cnki.ISSN2096 ̄3548.2021.06.010㊀㊀精馏是利用液态物系中各组分沸点不同的特点进行分离的化工单元操作ꎮ采用精馏方式得到精甲醇产品ꎬ至少需要2个精馏塔进行分离ꎬ在第1个塔(预精馏塔ꎬ简称预塔)塔顶先精馏出轻杂质ꎬ甲醇㊁水和重组分杂质进入第2个塔(主精馏塔ꎬ简称主塔)ꎻ在第2个塔塔底除去重组分杂质ꎬ塔顶产出精甲醇产品ꎬ这就是所谓的2塔精馏工艺流程(简称2塔流程)[1]ꎮ随着精馏工艺的发展ꎬ甲醇精馏工艺中引入热耦合节能技术ꎬ将主塔分为2个塔 加压塔和常压塔ꎬ利用加压塔塔顶甲醇蒸气为常压塔塔底再沸器加热ꎬ这就形成了由预塔㊁加压塔和常压塔组成的3塔精馏工艺流程(简称3塔流程)[2]ꎮ为了使废水达标排放ꎬ在常压塔侧线采出包括甲醇在内的杂醇[3]ꎮ随着甲醇生产规模不断增大ꎬ精馏装置中杂醇量也不断增加ꎬ为了进一步提高甲醇收率ꎬ又在流程中加入回收塔ꎬ将常压塔侧线杂醇进行精馏ꎬ回收甲醇ꎬ这样就形成3+1塔精馏工艺流程(简称3+1塔流程)[4]ꎮ目前广泛使用的甲醇精馏技术为3塔精馏和3+1塔精馏ꎮ内蒙古荣信化工有限公司(简称荣信化工)甲醇精馏在3+1塔流程的基础上ꎬ提高加压塔操作压力ꎬ添加中压精馏塔(简称中压塔)ꎬ将热耦合增加到两级ꎬ即利用加压塔塔顶甲醇蒸气为中压塔塔底再沸器加热ꎬ再利用中压塔塔顶甲醇蒸气为常压塔塔底再沸器加热ꎬ从而使工艺流程衍变为4+1塔精馏工艺流程(简称4+1塔流程)ꎮ4+1塔流程具有蒸汽消耗低㊁操作容易㊁产品质量好等优点ꎮ1㊀工艺流程1.1㊀工艺原理甲醇精馏是根据在相同温度下ꎬ粗甲醇中各组分的相对挥发度不同ꎬ经多次部分气化和部分冷凝最后得到较纯的组分ꎬ实现各组分分离的操作过程ꎮ4+1塔精馏装置主要包括预塔㊁加压塔㊁中压塔㊁常压塔㊁回收塔和不凝气洗涤塔ꎮ预塔主要是除去粗甲醇中的二甲醚㊁甲酸甲脂等轻组分杂质及溶解性气体ꎬ加压塔㊁中压塔㊁常压塔中除去水及重组分杂质ꎬ并在常压塔侧线采出一部分累积的重组分送往回收塔回收甲醇ꎬ从而得到优等品精甲醇ꎮ1.2㊀工艺流程4+1塔流程见图1ꎮ1.2.1㊀预塔原料粗甲醇与NaOH水溶液混合经蒸汽冷凝液及中压塔产品加热到77~78ħ后进入预塔ꎬ在预塔分离轻组分ꎮ塔顶甲醇蒸气在预塔空冷器中部分冷凝ꎬ冷凝液进入预塔回流罐ꎬ未冷凝的气体进入预塔第二冷却器(简称二冷)ꎬ二冷冷却的液体进入油水分离器内分相ꎬ上层为甲酸甲酯等油相ꎬ定期自流至燃料油罐ꎬ下层水相进入预塔回流罐ꎮ预塔二冷的不凝气进入不凝气洗涤塔洗涤回收甲醇后送至燃料气管网作为燃料ꎮ同时ꎬ为了作者简介:徐广才(1986 )ꎬ男ꎬ工程师ꎬ现从事煤化工生产工作ꎻxgc5213@163.com1 预塔ꎻ2 加压塔ꎻ3 中压塔ꎻ4 常压塔ꎻ5 回收塔ꎻ6 不凝气洗涤塔ꎮ图1㊀4+1塔流程保证分离效果ꎬ在预塔回流槽加入一定量萃取水ꎬ以保证产品质量ꎮ1.2.2㊀加压塔去除了轻组分的粗甲醇从预塔塔底排出(含甲醇质量分数约89%ꎬ下同)ꎬ加压后经2台预热器预热(2台预热器热源分别为加压塔塔底液和蒸汽凝液)ꎬ加热至134~135ħ进入加压塔ꎬ进行精馏ꎮ加压塔塔顶甲醇蒸气为中压塔再沸器供热ꎬ换热㊁冷凝后ꎬ一部分采出送至回收塔再沸器ꎬ作为回收塔再沸器热源ꎬ换热后进一步冷却作为精甲醇产品ꎬ一部分作为回流ꎬ回流比控制在2.5~3.0ꎮ1.2.3㊀中压塔加压塔塔底醇水溶液(含甲醇质量分数约85%)换热后送往中压塔进行精馏ꎬ中压塔塔顶甲醇蒸气为常压塔再沸器供热ꎬ换热㊁冷凝后的甲醇液一部分采出送至预塔进料预热器ꎬ换热后进一步冷却作为精甲醇产品ꎬ一部分作为回流ꎬ回流比控制在2.4~2.9ꎮ1.2.4㊀常压塔中压塔塔底醇水溶液(含甲醇质量分数约73%)送往常压塔进行精馏ꎬ常压塔塔顶甲醇蒸气经冷凝后一部分作为精甲醇产品ꎬ一部分作为回流ꎬ回流比控制在2.2~2.6ꎮ塔底废水(残留甲醇质量分数ɤ0.01%)送入气化工段作为磨煤水使用ꎮ为保证产品质量ꎬ在常压塔设侧线ꎬ采出杂醇ꎮ1.2.5㊀回收塔由常压塔侧线采出的杂醇油ꎬ用泵送入回收塔回收甲醇ꎮ回收塔塔顶采出甲醇㊁乙醇等混合液作为燃料油出售ꎬ塔底废水(残留甲醇质量分数ɤ0.01%)送入气化工段作为磨煤水使用ꎮ1.2.6㊀不凝气洗涤塔预塔二冷后的不凝气进入不凝气洗涤塔底部ꎬ在塔顶加入脱盐水ꎬ溶解吸收气相中的甲醇ꎬ不溶于水的不凝气送入燃料气管网ꎮ洗涤后的含醇水进入油水分离器ꎮ2㊀生产运行效果不同流程的精馏塔设计大同小异ꎬ节能降耗的主要手段为合理进行填料的分段和高度的设计ꎬ使混合物的气液相的单元操作合理进行ꎻ同时优化流程ꎬ调整部分工艺指标ꎬ合理利用物料的热量ꎮ4+1塔流程的主要工艺指标见表1ꎮ2.1㊀蒸汽消耗4+1塔流程充分利用系统物料热量的回收利用ꎬ一是中压塔再沸器使用加压塔塔顶甲醇蒸表1㊀4+1塔流程的主要工艺指标项目预塔加压塔中压塔常压塔回收塔塔顶压力/kPa45~551390~1410640~66025~3525~35塔底压力/kPa65~751400~1420650~67045~5535~45塔顶温度/ħ79ʃ1153ʃ2125ʃ271ʃ173ʃ1塔底温度/ħ81ʃ1157ʃ2132ʃ2110ʃ1110ʃ1回流比2.5~3.02.4~2.92.2~2.61.6~2.6气来加热中压塔塔底液ꎻ二是常压塔再沸器使用中压塔塔顶甲醇蒸气来加热常压塔塔底液ꎻ三是利用加压塔再沸器蒸汽凝液为加压塔进料进行预热ꎬ然后将换热后的蒸汽凝液作为预塔其中一个再沸器的热源ꎻ四是加压塔和中压塔精甲醇采出产品温度都在125ħ以上ꎬ用这两股精甲醇作为回收塔再沸器和预塔进料二次预热的热源ꎮ通过以上优化ꎬ每吨精甲醇消耗蒸汽约0.9~1.0tꎬ与传统的3塔或3+1塔精馏相比ꎬ吨精甲醇蒸汽消耗降低0.2~0.3tꎮ4+1塔流程的蒸汽消耗数据见表2ꎬ其中0.5MPa蒸汽运行时压力稳定在(0.5ʃ0.01)MPaꎬ1.0MPa蒸汽运行时压力稳定在(0.95ʃ0.02)MPaꎮ表2㊀4+1塔流程的蒸汽消耗数据日期进料质量/t采出质量/t0.5MPa蒸汽消耗质量/t1.0MPa蒸汽消耗质量/t吨精甲醇蒸汽消耗/t2020 ̄01 ̄17140.8126.234840.942020 ̄01 ̄16140.8131.738860.942020 ̄01 ̄15134.8127.237860.962020 ̄01 ̄14133.6113.937851.032020 ̄01 ̄13140.0125.736860.972020 ̄01 ̄12128.1124.038861.002020 ̄01 ̄11148.0135.036870.912.2㊀产品质量精甲醇产品经化验分析ꎬ各项指标均符合GB338 2011«工业用甲醇»优等品要求ꎬ具体数据见表3ꎮ表3㊀精甲醇分析数据日期项目水混溶试验结果水分质量分数/%KMnO4试验变色时间/min乙醇质量分数密度/(g cm-3)酸度(以甲酸计)羰基物质量分数(以甲醛计)色度2020 ̄01 ̄17加压塔1+30.01>50113.96ˑ10-60.7926ˑ10-611ˑ10-6ɤ5中压塔1+30.01>509.12ˑ10-60.7916ˑ10-64ˑ10-6ɤ5常压塔1+30.01>5041.36ˑ10-60.7916ˑ10-615ˑ10-6ɤ52020 ̄01 ̄14加压塔1+30.01>5088.50ˑ10-60.7916ˑ10-66ˑ10-6ɤ5中压塔1+30.01>508.57ˑ10-60.7916ˑ10-65ˑ10-6ɤ5常压塔1+30.01>5045.30ˑ10-60.7916ˑ10-65ˑ10-6ɤ52020 ̄01 ̄11加压塔1+30.01>5098.47ˑ10-60.7926ˑ10-66ˑ10-6ɤ5中压塔1+30.01>5012.69ˑ10-60.7916ˑ10-62ˑ10-6ɤ5常压塔1+30.01>5054.30ˑ10-60.7916ˑ10-67ˑ10-6ɤ52.3㊀系统运行精馏塔采用高效波纹板规整填料+导向梯形浮阀ꎬ在结构上使气液流路得到优化ꎬ传质效率提高ꎬ系统阻力降低ꎬ相对提高了理论塔盘数ꎮ在实际生产中ꎬ产能可达设计值的120%左右ꎬ并且运行稳定ꎬ各项操作指标均在可控范围内ꎮ影响系统运行稳定的主要因素有以下3个方面:(1)蒸汽压力波动ꎮ该装置1.0MPa蒸汽主要由变换工段副产蒸汽提供ꎬ副产蒸汽不足时由2.0MPa饱和蒸汽减压提供ꎮ由于前系统开车负荷波动ꎬ导致蒸汽压力变化较快ꎬ产品质量频繁出现反复ꎮ另外ꎬ在使用2.0MPa蒸汽减压时ꎬ蒸汽存在一定过热度ꎬ再沸器换热效果差ꎮ随着前系统逐渐稳定ꎬ消除蒸汽波动带来的影响后ꎬ系统运行整体趋于稳定ꎮ(2)负荷匹配ꎮ开车初期装置负荷较低ꎬ为缩短产品合格时间ꎬ加压塔和中压塔回流量偏大ꎬ2塔采取精甲醇较多ꎬ导致中压塔塔底液甲醇含量低(设计含醇质量分数为73%ꎬ实际含醇质量分数约为60%)ꎬ常压塔难以稳定操作ꎬ产品质量不合格ꎮ通过调整加压塔和中压塔的回流比ꎬ控制中压塔塔底液含醇质量分数在70%以上后ꎬ系统逐渐趋于稳定ꎮ(3)粗甲醇质量ꎮ该装置合成工段采用庄信万丰甲醇合成技术ꎬ床层温度高导致粗甲醇中杂质含量较高ꎬ特别是乙醇质量分数>2400ˑ10-6ꎬ严重影响精馏操作ꎮ针对这种情况ꎬ在调整合成操作的同时ꎬ加大分析频次ꎬ对粗甲醇中的杂质进行定性和定量分析ꎬ并根据分析结果调整萃取水的加入量和回流比ꎬ精馏产品质量得到很好的改善ꎮ3㊀生产过程出现的问题及处理措施3.1㊀预塔轻组分溢流采出口设置过高预塔轻组分在预塔回流罐和油水分离器溢流采出ꎬ由于设计原因ꎬ采出口的位置在液位90%以上的位置ꎬ正常液位在50%~60%时轻组分无法采出ꎮ这些物质在预塔积累ꎬ随着时间推移ꎬ杂质逐渐向下扩散至塔釜内ꎬ带入后塔ꎬ这些杂质又以同样的方式聚集于塔顶ꎬ造成产品水溶性不合格ꎮ在运行过程中ꎬ将油水分离器液位控制在90%以上ꎬ保证预塔轻组分能够顺利采出ꎬ保证产品质量ꎮ另外ꎬ计划在系统停车检修时对油水分离器进行改造ꎬ将采出口降低至液位50%~60%处ꎮ3.2㊀常压塔冷凝器液相管形成液封常压塔采用空冷加水冷的形式ꎬ空冷后的甲醇气液混合物进入水冷器再进一步冷却ꎮ水冷器工艺物料采用下进上出的形式ꎬ导致水冷器甲醇进口管线形成一个液袋ꎬ在开车时一旦有甲醇开始冷凝ꎬ在常压塔和回流槽之间形成液封ꎬ导致常压塔内氮气不易排出ꎬ常压塔压力波动较大ꎬ系统紊乱ꎮ为了解决该问题ꎬ在空冷器排气口和回流槽之间直接增加一路平衡管ꎬ开车时塔内氮气可顺利排出ꎬ常压塔指标控制比较稳定ꎮ3.3㊀杂醇油中间罐平衡管设计不合理常压塔侧线采出的杂醇油先进入杂醇油中间罐再经泵加压送入回收塔回收甲醇ꎮ原设计在中间罐和回流槽之间设置平衡管ꎬ在运行过程中由于回流槽压力远低于中间罐压力ꎬ中间罐中的杂质蒸气被吸入回流槽中ꎬ导致产品质量不合格ꎮ经排查确认后将平衡管隔断ꎬ产品质量随即好转ꎮ3.4㊀常压塔水溶性不稳定开车以来ꎬ合成塔入口氢碳比受前工段的制约波动很大ꎬ造成粗甲醇组分变化较大ꎬ常压塔多次出现水溶性波动ꎮ通过加大萃取水量控制预精馏塔后甲醇质量分数在80%~85%ꎬ提高预塔不凝气放空温度在50~55ħꎬ加大常压塔杂醇油采出量并适当调整采出口位置ꎬ产品质量得到改善ꎮ4㊀结语(1)4+1塔甲醇精馏相比较于传统的3塔精馏或3+1塔精馏具有显著的节能效果ꎬ精甲醇蒸汽单耗同比可节省0.20t以上ꎬ符合国家大力推行的节能减排号召ꎬ并且系统运行稳定ꎬ操作灵活ꎮ(2)与传统的3塔精馏或3+1塔精馏相比ꎬ4+1塔精馏的流程复杂ꎬ特别是换热网络ꎬ因此在操作过程中更应优化操作ꎬ确保每个塔的操作条件与设计吻合ꎬ保证合适的回流比ꎬ才能在保证产品质量的前提下降低能耗ꎮ(3)该装置处于开车初期ꎬ蒸汽消耗相比传统工艺有所降低ꎬ但仍有优化的空间ꎮ精馏装置除了采用先进的工艺ꎬ在实际运行中ꎬ还需要不断地优化工艺指标ꎬ进一步提高甲醇收率和降低能耗ꎮ参考文献[1]㊀宋维端ꎬ肖任坚ꎬ房鼎业.甲醇工学[M].北京:化学工业出版社ꎬ1991:270 ̄278.[2]㊀张晓卫ꎬ师泽ꎬ张伟.浅谈双效精馏与热泵节能技术在甲醇精馏工艺中的应用[J].中国化工贸易ꎬ2017ꎬ9(20):131.[3]㊀李志娟.甲醇精馏工艺流程分析及优化[J].中国化工贸易ꎬ2018ꎬ10(11):63.[4]㊀方勇进ꎬ刘成. 3+1 塔甲醇精馏工艺优化浅析[J].中国化工贸易ꎬ2013ꎬ5(9):65 ̄66.(收稿日期㊀2020 ̄03 ̄16)。
甲醇装置工作总结范文
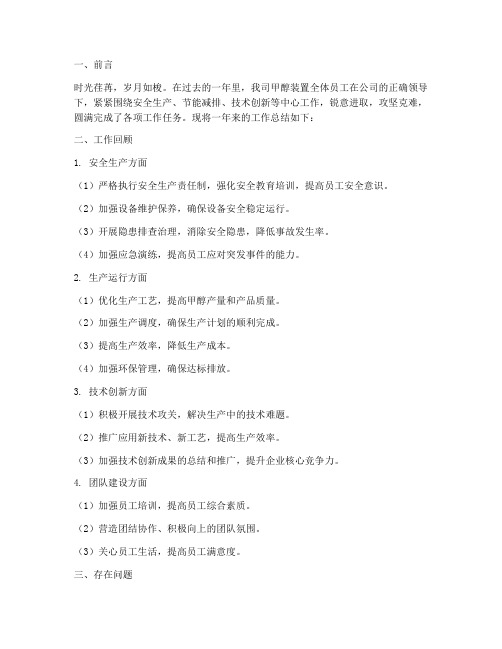
一、前言时光荏苒,岁月如梭。
在过去的一年里,我司甲醇装置全体员工在公司的正确领导下,紧紧围绕安全生产、节能减排、技术创新等中心工作,锐意进取,攻坚克难,圆满完成了各项工作任务。
现将一年来的工作总结如下:二、工作回顾1. 安全生产方面(1)严格执行安全生产责任制,强化安全教育培训,提高员工安全意识。
(2)加强设备维护保养,确保设备安全稳定运行。
(3)开展隐患排查治理,消除安全隐患,降低事故发生率。
(4)加强应急演练,提高员工应对突发事件的能力。
2. 生产运行方面(1)优化生产工艺,提高甲醇产量和产品质量。
(2)加强生产调度,确保生产计划的顺利完成。
(3)提高生产效率,降低生产成本。
(4)加强环保管理,确保达标排放。
3. 技术创新方面(1)积极开展技术攻关,解决生产中的技术难题。
(2)推广应用新技术、新工艺,提高生产效率。
(3)加强技术创新成果的总结和推广,提升企业核心竞争力。
4. 团队建设方面(1)加强员工培训,提高员工综合素质。
(2)营造团结协作、积极向上的团队氛围。
(3)关心员工生活,提高员工满意度。
三、存在问题1. 安全生产方面:个别员工安全意识淡薄,存在违章操作现象。
2. 生产运行方面:部分设备老化,维护保养不到位。
3. 技术创新方面:技术创新能力有待提高。
四、下一步工作计划1. 深入开展安全生产教育培训,提高员工安全意识。
2. 加强设备维护保养,提高设备运行效率。
3. 积极开展技术创新,提高企业核心竞争力。
4. 加强团队建设,提高员工综合素质。
总之,过去的一年,甲醇装置全体员工在公司的正确领导下,取得了显著的成绩。
在新的一年里,我们将继续努力,以更加饱满的热情、更加务实的作风,为实现公司发展目标而努力奋斗。
甲醇合成装置优化运行总结

甲醇合成装置优化运行总结甲醇是一种重要的有机化工产品,广泛应用于化工、能源和化肥等领域。
甲醇的合成是一个复杂的工艺过程,涉及到催化剂、反应器、蒸馏塔等多个单元操作。
为了提高甲醇合成装置的运行效率和降低成本,需要对其进行优化运行。
本文将着重分析甲醇合成装置的优化运行总结,主要包括以下几个方面:一、催化剂的选择和管理催化剂是甲醇合成装置的关键组成部分,直接影响着合成反应的效率和产品质量。
为了优化甲醇合成装置的运行,需要选择合适的催化剂,并对其进行有效的管理。
需要选取活性高、稳定性好的催化剂,以提高甲醇合成的转化率和选择性。
需要对催化剂进行定期检查和维护,及时更换老化或失活的催化剂,以保证其稳定的使用和催化效果。
还需要对催化剂的再生和回收进行有效的管理,以减少催化剂的浪费和降低成本。
二、反应器操作条件的优化反应器是甲醇合成装置中的关键设备,直接影响着反应过程的效率和产品质量。
为了优化反应器的运行,需要对其操作条件进行有效的优化。
需要确保反应器的温度、压力和流速等参数处于合适的范围,以提高反应过程的效率和产品质量。
需要对反应器的热力学和动力学特性进行深入研究,以找到最佳的操作条件。
还需要对反应器进行有效的监控和控制,及时发现和解决潜在的问题,以确保其稳定的运行和高效的生产。
三、蒸馏塔的性能优化蒸馏塔是甲醇合成装置中的重要分离设备,直接影响着产品纯度和收率。
为了优化蒸馏塔的运行,需要对其性能进行有效的优化。
需要对蒸馏塔进行有效的设计和布置,以提高其分离效率和经济性。
需要对蒸馏塔的操作条件进行合理调控,以确保产品的纯度和收率。
还需要对蒸馏塔进行有效的清洗和维护,以保证其稳定的运行和高效的分离。
四、能源消耗的减少甲醇合成装置在生产过程中需要消耗大量的能源,为了降低能源成本和减少环境污染,需要对其能源消耗进行有效的管理和优化。
需要对能源消耗进行全面的分析和评估,找到能源的浪费和瓶颈,并采取有效的措施进行改善。
需要引入先进的节能技术和设备,以降低能源的消耗和提高能源利用率。
煤制乙二醇装置甲醇精馏运行总结
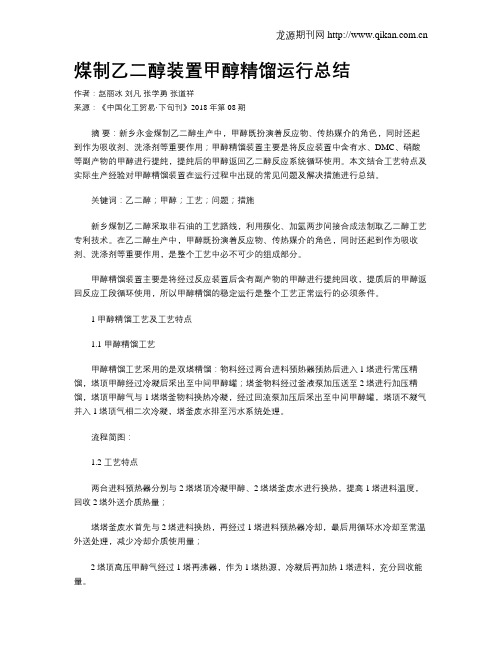
煤制乙二醇装置甲醇精馏运行总结作者:赵丽冰刘凡张学勇张道祥来源:《中国化工贸易·下旬刊》2018年第08期摘要:新乡永金煤制乙二醇生产中,甲醇既扮演着反应物、传热媒介的角色,同时还起到作为吸收剂、洗涤剂等重要作用;甲醇精馏装置主要是将反应装置中含有水、DMC、硝酸等副产物的甲醇进行提纯,提纯后的甲醇返回乙二醇反应系统循环使用。
本文结合工艺特点及实际生产经验对甲醇精馏装置在运行过程中出现的常见问题及解决措施进行总结。
关键词:乙二醇;甲醇;工艺;问题;措施新乡煤制乙二醇采取非石油的工艺路线,利用羰化、加氢两步间接合成法制取乙二醇工艺专利技术。
在乙二醇生产中,甲醇既扮演着反应物、传热媒介的角色,同时还起到作为吸收剂、洗涤剂等重要作用,是整个工艺中必不可少的组成部分。
甲醇精馏装置主要是将经过反应装置后含有副产物的甲醇进行提纯回收,提质后的甲醇返回反应工段循环使用,所以甲醇精馏的稳定运行是整个工艺正常运行的必须条件。
1 甲醇精馏工艺及工艺特点1.1 甲醇精馏工艺甲醇精馏工艺采用的是双塔精馏:物料经过两台进料预热器预热后进入1塔进行常压精馏,塔顶甲醇经过冷凝后采出至中间甲醇罐;塔釜物料经过釜液泵加压送至2塔进行加压精馏,塔顶甲醇气与1塔塔釜物料换热冷凝,经过回流泵加压后采出至中间甲醇罐,塔顶不凝气并入1塔顶气相二次冷凝,塔釜废水排至污水系统处理。
流程简图:1.2 工艺特点两台进料预热器分别与2塔塔顶冷凝甲醇、2塔塔釜废水进行换热,提高1塔进料温度,回收2塔外送介质热量;塔塔釜废水首先与2塔进料换热,再经过1塔进料预热器冷却,最后用循环水冷却至常温外送处理,减少冷却介质使用量;2塔顶高压甲醇气经过1塔再沸器,作为1塔热源,冷凝后再加热1塔进料,充分回收能量。
综上所述:①工艺设计最大的特点就是实现了能量的多级利用,降低装置能量消耗;②正是因为装置的节能设计使得整个装置的操作重点集中在2塔,2塔稳定,系统就稳定;2塔波动,整个装置都要随之调整。
甲醇合成装置优化运行总结
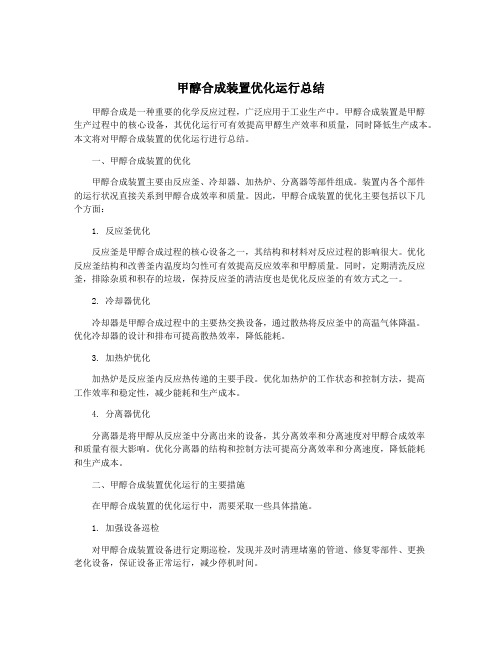
甲醇合成装置优化运行总结甲醇合成是一种重要的化学反应过程,广泛应用于工业生产中。
甲醇合成装置是甲醇生产过程中的核心设备,其优化运行可有效提高甲醇生产效率和质量,同时降低生产成本。
本文将对甲醇合成装置的优化运行进行总结。
一、甲醇合成装置的优化甲醇合成装置主要由反应釜、冷却器、加热炉、分离器等部件组成。
装置内各个部件的运行状况直接关系到甲醇合成效率和质量。
因此,甲醇合成装置的优化主要包括以下几个方面:1. 反应釜优化反应釜是甲醇合成过程的核心设备之一,其结构和材料对反应过程的影响很大。
优化反应釜结构和改善釜内温度均匀性可有效提高反应效率和甲醇质量。
同时,定期清洗反应釜,排除杂质和积存的垃圾,保持反应釜的清洁度也是优化反应釜的有效方式之一。
2. 冷却器优化冷却器是甲醇合成过程中的主要热交换设备,通过散热将反应釜中的高温气体降温。
优化冷却器的设计和排布可提高散热效率,降低能耗。
3. 加热炉优化加热炉是反应釜内反应热传递的主要手段。
优化加热炉的工作状态和控制方法,提高工作效率和稳定性,减少能耗和生产成本。
4. 分离器优化分离器是将甲醇从反应釜中分离出来的设备,其分离效率和分离速度对甲醇合成效率和质量有很大影响。
优化分离器的结构和控制方法可提高分离效率和分离速度,降低能耗和生产成本。
二、甲醇合成装置优化运行的主要措施在甲醇合成装置的优化运行中,需要采取一些具体措施。
1. 加强设备巡检对甲醇合成装置设备进行定期巡检,发现并及时清理堵塞的管道、修复零部件、更换老化设备,保证设备正常运行,减少停机时间。
2. 协调调配原材料与催化剂比例甲醇合成所需原料如氢气、碳氢化合物等比例的调配和醇/醚的组合比例也应予以调整,以提高反应的产率和避免甲醇质量下降。
3. 控制总合成压力与温度甲醇合成装置的压力和温度对反应效率和产率有直接影响。
在优化运行中,应控制总合成压力和温度,减少浮动范围,尽可能保持稳定。
4. 合理选用催化剂催化剂的选择对甲醇合成反应的效率和质量有很大影响。
三塔甲醇精馏系统运行总结

8
小氮肥 第
36 卷 第 6 期 2008 年 6 月
量控制在粗醇的 0. 4% (质量分数 ) 左右 , 经冷却 后去杂醇油贮槽 。
3 系统运行情况
三塔甲醇精馏系统于 2007 年 4 月一次开车 成功 。通过 8 个月的生产运行 , 不管是低负荷还 是高负荷运行 ,系统都表现出良好的稳定性 ,其蒸 汽消耗低 ,操作弹性也很大 ,加压精馏塔和常压精 馏塔的回流比较低 ,节能效果很明显 ,产品质量都 能达到 优 等 品 指 标 , 甲 醇 回 收 率 也 很 高 , 达 到
表 2 三塔测温点温度
时 间
2007 2 10 2 26T12 ¬ 00 2007 2 10 2 26T24 ¬ 00 2007 2 10 2 27T12 ¬ 00 2007 2 10 2 27T24 ¬ 00 2007 2 10 2 28T12 ¬ 00 2007 2 10 2 28T24 ¬ 00
1 1 1
用自身热能的回收利用 , 一是常压精馏塔再沸器 采用加压精馏塔塔顶甲醇蒸气来加热常压精馏塔 釜液 ,二是脱醚塔预热器采用加压精馏塔采出精 醇预热粗醇 ,因此蒸汽消耗和冷却水用量都较低 。 通 过几个月的生产统计 , 每吨精醇消耗蒸汽约
加压精馏塔 / ℃ 塔釜
77. 3 77. 5 77. 6 77. 0 76. 7 77. 4
(以甲醛计 ) / %
≤0. 10
≤0. 15
≤0. 027
≤0. 001 5 ≤0. 003 0 ≤0. 001 1 ≤0. 002 ≤50 供需双 方协商 ≤0. 005 ≤50 未检出
硫酸洗涤试验 /Hazen 单位
(铂 - 钴色号 )
≤40 ≤80 × 10 - 6
甲醇合成装置优化运行总结
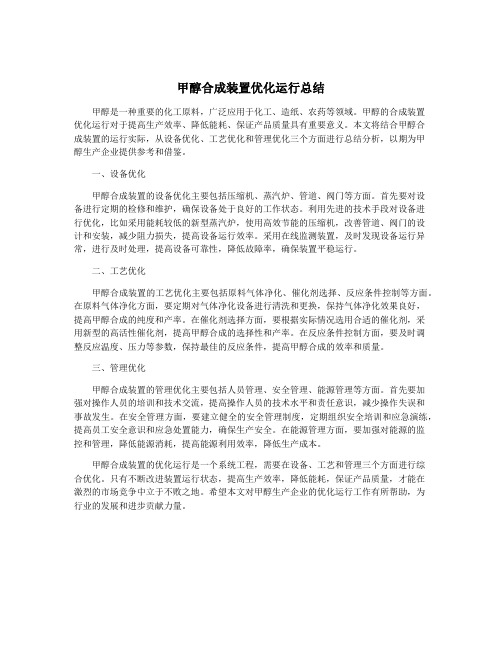
甲醇合成装置优化运行总结甲醇是一种重要的化工原料,广泛应用于化工、造纸、农药等领域。
甲醇的合成装置优化运行对于提高生产效率、降低能耗、保证产品质量具有重要意义。
本文将结合甲醇合成装置的运行实际,从设备优化、工艺优化和管理优化三个方面进行总结分析,以期为甲醇生产企业提供参考和借鉴。
一、设备优化甲醇合成装置的设备优化主要包括压缩机、蒸汽炉、管道、阀门等方面。
首先要对设备进行定期的检修和维护,确保设备处于良好的工作状态。
利用先进的技术手段对设备进行优化,比如采用能耗较低的新型蒸汽炉,使用高效节能的压缩机,改善管道、阀门的设计和安装,减少阻力损失,提高设备运行效率。
采用在线监测装置,及时发现设备运行异常,进行及时处理,提高设备可靠性,降低故障率,确保装置平稳运行。
二、工艺优化甲醇合成装置的工艺优化主要包括原料气体净化、催化剂选择、反应条件控制等方面。
在原料气体净化方面,要定期对气体净化设备进行清洗和更换,保持气体净化效果良好,提高甲醇合成的纯度和产率。
在催化剂选择方面,要根据实际情况选用合适的催化剂,采用新型的高活性催化剂,提高甲醇合成的选择性和产率。
在反应条件控制方面,要及时调整反应温度、压力等参数,保持最佳的反应条件,提高甲醇合成的效率和质量。
三、管理优化甲醇合成装置的管理优化主要包括人员管理、安全管理、能源管理等方面。
首先要加强对操作人员的培训和技术交流,提高操作人员的技术水平和责任意识,减少操作失误和事故发生。
在安全管理方面,要建立健全的安全管理制度,定期组织安全培训和应急演练,提高员工安全意识和应急处置能力,确保生产安全。
在能源管理方面,要加强对能源的监控和管理,降低能源消耗,提高能源利用效率,降低生产成本。
甲醇合成装置的优化运行是一个系统工程,需要在设备、工艺和管理三个方面进行综合优化。
只有不断改进装置运行状态,提高生产效率,降低能耗,保证产品质量,才能在激烈的市场竞争中立于不败之地。
希望本文对甲醇生产企业的优化运行工作有所帮助,为行业的发展和进步贡献力量。
甲醇装置工程总结
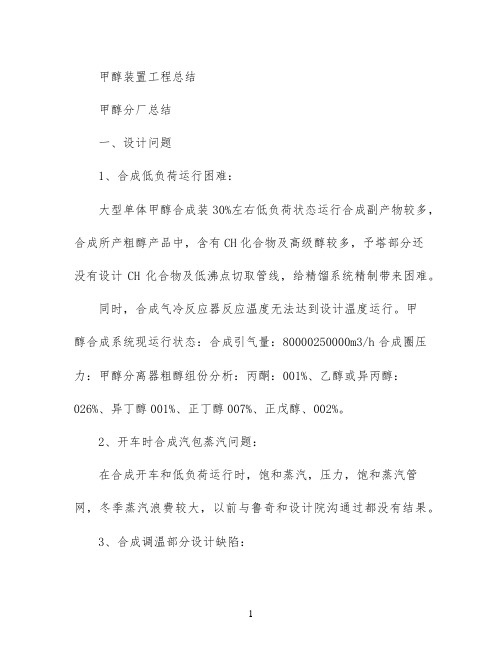
甲醇装置工程总结甲醇分厂总结一、设计问题1、合成低负荷运行困难:大型单体甲醇合成装30%左右低负荷状态运行合成副产物较多,合成所产粗醇产品中,含有CH化合物及高级醇较多,予塔部分还没有设计CH化合物及低沸点切取管线,给精馏系统精制带来困难。
同时,合成气冷反应器反应温度无法达到设计温度运行。
甲醇合成系统现运行状态:合成引气量:80000250000m3/h合成圈压力:甲醇分离器粗醇组份分析:丙酮:001%、乙醇或异丙醇:026%、异丁醇001%、正丁醇007%、正戊醇、002%。
2、开车时合成汽包蒸汽问题:在合成开车和低负荷运行时,饱和蒸汽,压力,饱和蒸汽管网,冬季蒸汽浪费较大,以前与鲁奇和设计院沟通过都没有结果。
3、合成调温部分设计缺陷:合成调温空冷和水冷部分应设计手阀保证低负荷状态下有效隔断,或增加新鲜气和循环气增加一台入塔气预热器(带旁路的满负荷时不用)可以有效利用压缩机出口气温度,提高气冷反应器入口温度。
4、常压塔开车升温时间较长:甲醇精馏常压塔塔底开车时温度提升较慢,开车时间较长,废水排放不了,只能返回闪蒸槽内,给后续精制带来困难。
同时加压塔进料泵增加至常压塔进料管线,以减少开车加压塔使用的氮气。
5、常压塔塔底废水达标问题:甲醇常压塔塔底温度控制在108℃-111℃,塔底工艺废水也很难达到指标≤015%。
(怀疑高级醇较多影响含量87%)主要是甲醇精馏常压塔塔底开车时温度提升较慢引起的。
6、甲醇合成气冷反应温度较低问题:从组份变化来看反应不好。
在这种情况下势必影响催化剂活性,同时杂质产生较多,现在甲醇分离器D5201*液相出口每3天就清一次,过滤器滤网上全部是石蜡。
7、鲁奇公司提供的公式问题:对于精馏系统鲁奇提供的予塔T53001甲醇浓度换算公式还是存在问题。
同时甲醇三塔热负荷换算公式无法应用于精馏实际控制(见Com3/h以下的3/h进料,加水15Nm3/h左右,废水泵排量不足,有时泵电机出现超流现象。
甲醇合成装置优化运行总结

甲醇合成装置优化运行总结甲醇合成装置是煤炭化工产业中的一种重要装置,其稳定运行对提高产能和降低能耗具有重要意义。
近期,本单位对甲醇合成装置进行了优化运行,将优化结果总结如下。
一、优化前情况甲醇合成装置优化前,存在以下问题:1. 产能低下。
甲醇产量较低,不能满足市场需求。
2. 能耗较高。
甲醇合成过程中的能源消耗较大,能源利用率不高。
二、优化措施针对以上问题,我们采取了以下优化措施:1. 增加催化剂活性。
更换新的催化剂,并进行合理的催化剂喂料量控制,提高催化剂的利用率和活性。
2. 优化反应条件。
通过调整反应温度、压力等参数,优化反应条件,提高反应速率和选择性。
3. 改进热平衡。
优化换热器的设计和操作,增强热交换效果,降低能耗。
4. 提高原料纯度。
优化原料预处理流程,降低杂质含量,减少催化剂中毒,提高甲醇合成效率。
三、优化结果通过对甲醇合成装置的优化运行,取得了如下结果:1. 产能提升。
甲醇合成装置的产能得到明显提升,可以满足市场需求。
2. 能耗降低。
采取的优化措施使能耗明显降低,能源利用效率得到提高。
3. 产品质量稳定。
优化后,甲醇合成产品的纯度和稳定性得到提升,符合相关标准要求。
四、存在问题及改进方案在优化运行过程中,也发现了一些问题:1. 催化剂寿命较短。
催化剂的使用寿命较短,需要频繁更换。
2. 反应器压力波动。
反应器内压力存在波动现象,影响了反应效果。
针对上述问题,我们拟定了如下改进方案:1. 寻找更优催化剂。
加大催化剂研发力度,寻找具有更长寿命和更高活性的催化剂。
2. 优化反应器控制策略。
改进反应器的控制系统,提高压力稳定性,减少波动。
五、未来工作展望针对以上问题和改进方案,我们将继续开展以下工作:1. 加强与科研机构的合作。
与科研机构合作,共同开展催化剂研发和反应器技术研究,提升装置性能。
2. 大力推行节能减排。
通过技术改造和管理创新,进一步提高能源利用效率,减少对环境的影响。
3. 加强运行监控。
甲醇合成装置优化运行总结

甲醇合成装置优化运行总结随着科学技术的不断发展,甲醇合成技术也得到了很大的提升。
甲醇合成装置作为发展甲醇技术的核心要素之一,在生产中的运行优化显得尤为重要。
本文将对甲醇合成装置进行优化运行总结,以期在生产中更好地利用优化技术,确保生产效益的最大化。
一、合理调整甲醇合成装置工艺流程甲醇合成装置的工艺流程直接影响着催化剂的选择、催化反应的效率、设备运行的稳定性等因素,因此对工艺流程的调整非常重要。
首先,要考虑反应的温度、压力、气体比等因素,使之达到最合适的条件。
甲醇反应的适宜温度一般在240-300摄氏度之间,适宜压力在40-100Mpa之间,而对H2和CO的配比也会影响反应的效率。
其次,可以通过调整催化剂,改变反应物质在催化剂上的反应势能,提高反应速率和选择性。
最后,通过适当的工艺流程调整,合理地设置中间设备,并对设备进行优化加工,提高流程的连续性、稳定性和运行效率。
二、优化甲醇合成装置的控制策略甲醇合成装置的控制策略主要包括温度、压力、反应物配比等因素的控制。
针对这些控制因素,可以通过优化控制系统,实现动态优先、优先采用最佳控制以及最大化控制等控制策略,以进一步提高甲醇合成装置的运行效率。
例如,在控制温度方面,通过实时反馈温度数据,并自动调整温度控制器的调节参数,以达到更加准确的控制。
在控制压力方面,可以使用PID控制算法,控制压力在设定值范围内波动,实现压力稳定控制。
在控制反应物配比方面,可以采用组合控制策略,结合模糊控制、神经网络控制等多种控制算法,以实现最优控制。
三、加强甲醇合成装置的设备维护甲醇合成装置中设备的状态对反应的效率和装置的运行稳定性至关重要。
因此,加强设备的维护保养显得尤为重要。
首先,要对设备进行定期维护保养,掌握设备的运行状态和健康状况,及时检修、更换受损部件。
其次,要加强设备监测、数据采集和分析,及时响应生产状况的变化,小范围调整装置产量和质量。
最后,对设备耗材要有严格的管理控制,确保耗材的质量稳定且使用寿命有保障,从而确保设备的正常靠谱运行。
甲醇合成装置优化运行总结
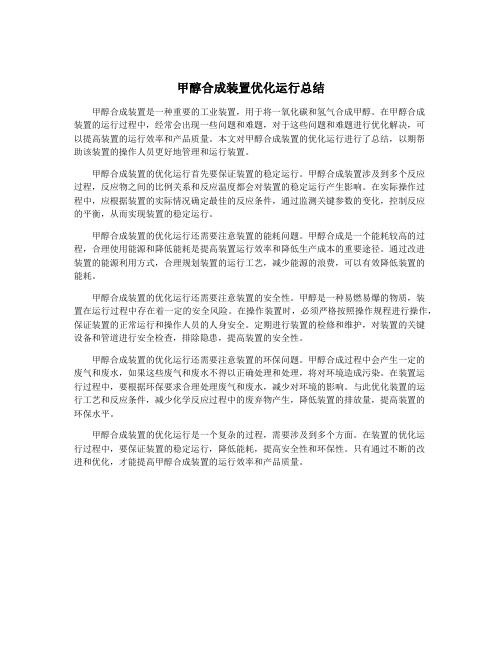
甲醇合成装置优化运行总结甲醇合成装置是一种重要的工业装置,用于将一氧化碳和氢气合成甲醇。
在甲醇合成装置的运行过程中,经常会出现一些问题和难题,对于这些问题和难题进行优化解决,可以提高装置的运行效率和产品质量。
本文对甲醇合成装置的优化运行进行了总结,以期帮助该装置的操作人员更好地管理和运行装置。
甲醇合成装置的优化运行首先要保证装置的稳定运行。
甲醇合成装置涉及到多个反应过程,反应物之间的比例关系和反应温度都会对装置的稳定运行产生影响。
在实际操作过程中,应根据装置的实际情况确定最佳的反应条件,通过监测关键参数的变化,控制反应的平衡,从而实现装置的稳定运行。
甲醇合成装置的优化运行还需要注意装置的能耗问题。
甲醇合成是一个能耗较高的过程,合理使用能源和降低能耗是提高装置运行效率和降低生产成本的重要途径。
通过改进装置的能源利用方式,合理规划装置的运行工艺,减少能源的浪费,可以有效降低装置的能耗。
甲醇合成装置的优化运行还需要注意装置的安全性。
甲醇是一种易燃易爆的物质,装置在运行过程中存在着一定的安全风险。
在操作装置时,必须严格按照操作规程进行操作,保证装置的正常运行和操作人员的人身安全。
定期进行装置的检修和维护,对装置的关键设备和管道进行安全检查,排除隐患,提高装置的安全性。
甲醇合成装置的优化运行还需要注意装置的环保问题。
甲醇合成过程中会产生一定的废气和废水,如果这些废气和废水不得以正确处理和处理,将对环境造成污染。
在装置运行过程中,要根据环保要求合理处理废气和废水,减少对环境的影响。
与此优化装置的运行工艺和反应条件,减少化学反应过程中的废弃物产生,降低装置的排放量,提高装置的环保水平。
甲醇合成装置的优化运行是一个复杂的过程,需要涉及到多个方面。
在装置的优化运行过程中,要保证装置的稳定运行,降低能耗,提高安全性和环保性。
只有通过不断的改进和优化,才能提高甲醇合成装置的运行效率和产品质量。
甲醇合成装置优化运行总结

甲醇合成装置优化运行总结为确保甲醇合成装置的优化运行,我们需要不断总结经验并进行不断的改进。
本文将总结甲醇合成装置的优化运行经验,并提出相关改进意见。
1. 技术装备优化:优化设备组合、改进工艺流程、调整设备参数等方面,不断开展技术装备优化,确保生产效率和产品质量。
2. 生产操作优化:优化生产操作流程,不断改进操作技能和操作标准,提高操作效率和工作质量。
同时,加强设备保养和维护,确保设备的稳定运行。
3. 数据监测系统建设:建立全面、准确的数据监测系统,对整个生产过程进行实时监测,及时发现问题并迅速解决。
4. 质量管控体系建立:建立完善的质量管控体系,从设备操作、生产技术、产品质量等多个方面对生产过程进行管控,确保产品质量达到标准要求。
5. 紧急故障处理方案制定:建立完善的紧急故障处理方案,及时应对突发问题。
同时,加强员工培训和技能提升,提高对各类故障的诊断和排除能力。
1. 加强装置自动化程度:加强自动化控制,提高数据采集和处理的准确性和速度,进一步实现系统网络化、信息化和智能化。
2. 熟练掌握工艺参数及设备运行规律:生产操作人员要深入了解工艺参数及设备运行规律,熟练掌握设备操作方式和技能方法,做到“细节决定成败”,不断提高运行效率。
3. 加强质量管理:在加强生产运行的同时,要进一步强化质量管理,增强标准化生产水平,加强质量检测和管控,提高产品质量和工艺指标。
4. 引入新技术:不断引入新技术,加强研发创新,提高生产自动化水平和生产效率,实现工程化、自动化和数字化生产。
5. 建立长效机制:建立长效机制,开展持续运营管理,持续推进优化运行,不断提高生产效率和产品质量,保障生产安全和环境保护。
- 1、下载文档前请自行甄别文档内容的完整性,平台不提供额外的编辑、内容补充、找答案等附加服务。
- 2、"仅部分预览"的文档,不可在线预览部分如存在完整性等问题,可反馈申请退款(可完整预览的文档不适用该条件!)。
- 3、如文档侵犯您的权益,请联系客服反馈,我们会尽快为您处理(人工客服工作时间:9:00-18:30)。
������������������������������������������������������������������������������������������������������������������������������������������������������������������������������������������������������������������������������������������������������������������������������������������������������������������ (上接第 61 页)
另一部分经离子交换器(D-53007)或通过副线送往精 甲醇中间储槽。
加压精馏塔塔顶甲醇蒸汽作为常压塔再沸器的热 源,为降低常压塔底高沸点物的含量(主要是杂醇油), 从塔下部塔板采出部分高沸点有机物,经 E-53009 冷 却后送入侧线槽;经侧线泵(P-53008)送至杂醇储槽 TK—53001,再经杂醇泵 P-53009 装车销售。常压精 馏塔塔底排出的含少量甲醇的废水由回收塔给料泵 (P-53005)加压后送往废水处理装置。 2 运行过程中存在的问题
预 塔 底 排 出 液(90 ℃ )由 加 压 塔 给 料 泵 (P-53001A/B)加 压 后 送 往 加 压 精 馏 塔 (T-53002) 精 馏。塔顶甲醇蒸汽去常压精馏塔再沸器(E-53006A/ B)作热源,冷凝液进入加压塔回流槽(D-53003),一部 分由加压塔回流泵(P-53003 A/B)加压后作加压精馏塔 回流液,另一部分经冷却器 E-53007 冷却后,或通过离 子交换器(D-53007)脱除甲基胺或直接通过副线送精 甲醇中间储槽。
甲醇精馏装置在 2011-06 开车一次成功,并产出 7 000 t 的优等甲醇。但是在本次开车过程中多次出现 精甲醇高锰酸钾试验﹤30 min、水溶性、残液中甲醇含 量不合格等问题。 2.1 水溶性不合格的原因分析
根据甲醇杂质的物理性质,就其在水及甲醇溶液 中的溶解度而言,大致可分为水溶性、醇溶性和不溶性 三类[2]。1)水溶性杂质:醚、C1-C5 醇类、醛、酮、有机 酸、胺等,在水中都有较高的溶解度,当甲醇溶液被稀 释时,不会被析出或变浑浊。2)醇溶性杂质:C6-C16 烷烃、C6-C16 醇类。这类杂质只有在浓度很高的甲醇 中被溶解,当溶液中甲醇浓度降低时就会从溶液中析 出,或使溶液变得浑浊。3)不溶性杂质:C16 以上烷烃 和 C10 以上醇类,在常温下不溶于甲醇和水,使溶液变 浑浊。
加压精馏塔塔底排出液进入常压精馏塔 (T-53003)。 塔 顶 甲 醇 蒸 汽 ,经 常 压 塔 空 冷 器 (AE-53002)、水冷器(E-53008)冷却至 40 ℃后,冷凝 液 流 入 常 压 塔 回 流 槽(D-53004),由 常 压 塔 回 流 泵 (P-53004 A/B)加压后,一部分作常压精馏塔回流液,
2.2 山西省物流需求预测实证分析
139 186 万 t,141 998 万 t,147 795 万 t。
以山西省 2001 年到 2010 年的货运量为基准量,表 3 结束语
示物流的实际需求量,构建预测模型;其中数据来源主
通过灰色模型的预测,所将预测结果具有较好精
要通过统计信息网、中国统计年鉴、山西统计年鉴等, 度。根据预测结果,为进一步促进山西省物流业的健
见表 2。按照相应数据,根据灰色模型的计算方法,求 出:a = -0.020 005 538 ;u = 110 942.6 797 .
康发展,提出如下建议:1)相关政府部门应加大力度, 继续创造有利于发展物流的环境。2)加大对物流专
表 2 山西省货运量原始数据
业人才的培养和引用。3)鼓励发展第三方物流,扩大
·62·
第 1 期(总第 125 期)
机 胡械志管涛:理甲醇开精发馏装置系统运行总结
2012 年 2 月
C5-C10 的烷烃类杂质,易与甲醇形成共沸物。其沸点 接近甲醇的沸点,不溶于水。而甲醇与水以任意比例 互溶。这样既提高预塔塔釜的温度又起到萃取的作 用。控制预塔的回流与进料的质量流速比为 0.33,以 维持各部温度与塔、收集槽液面的稳定,即维持塔的物 料与热量平衡。2)控制预塔放空温度。预塔冷凝器 实际起到分凝器的作用,使惰性气及绝大部分低沸点 杂质不致冷凝回到系统中去。本装置的预塔塔顶冷凝 器分两组,第一组通过空冷控制冷凝温度在 60 ℃,冷 凝液作为预塔的回流液;第二组则保持在 40 ℃,可有 效地脱除轻组分。通过采取以上措施,成品甲醇的高 锰酸钾试验达到 1+3 优等品的要求。
0.81~0.82
2.2 采取的措施 分厂采取的措施:1)严格按照设计指标执行。提
高预后比重在 0.84~0.86 之间,这是因为粗甲醇中含有
收稿日期:2011-08-15;修回日期:2011-10-05 作者简介:胡志涛(1975-),男,黑龙江齐齐哈尔人,助理工程师,本科,主要从事甲醇工艺技术工作。E-mail: zhitaohul@
3 结束语 主要工艺指标控制的好坏直接影响产品的质量。
由于此次开车操作人员都是刚毕业的学生,没有实际 工作经验,因预塔塔顶温度控制低使脱除轻组分不彻 底。今后,我们将进一步摸索改造,并加强管理,使精 馏装置长周期稳定运行。
参考文献 [1] 冯 元 琦. 联 醇 生 产 [M]. 北 京 :化 学 工 业 出 版 社 ,1994:
ZHANG Ping-ping
(Economics and Management College,North University of China,Taiyuan 030051,China) Abstract:By using gray prediction theory,according to the data of logistics demand required to index of Shanxi province, establish logistics demand forecasting model,and have conducted a scientific prediction to Shanxi logistics demand.Thus provide theoretical guidance to sustain⁃ able development of the logistics industry. Key words:GM (1,1) model; logistics demand;forecast
物流工程与管理,2010,32(3):17-19. [4] 王维国. 预测与决策[M]. 北京:中国财政经济出版社,2006. [5] 孙艳玲. 灰色预测模型在物流预测中的应用研究[J]. 物流
平台,2007(1):145-146.
Shanxi Logistics Demand Forecasting Analysis Based on Grey System Theory
第 1 期(总第 125 期) No.1(SUM No.125)
机械管理开发 MECHANICAL MANAGEMENT AND DEVELOPMENT
2012 年 2 月 Feb.2012
甲醇精馏装置系统运行总结
胡志涛
(大唐多伦煤化工有限责任公司 技术部,内蒙古 多伦 027300)
摘 要:对大唐多伦煤化工甲醇精馏装置系统进行了分析总结。简述了工艺流程,分析了运行过程中出现的问题 并提出了解决的措施。所生产的成品甲醇达到了优等品的要求。 关键词:甲醇精馏;工艺流程;问题探讨;解决措施 中图分类号:TQ223.12+1 文献标识码:A 文章编号:1003-773X(2012)01-0062-02
物流社会化、专业化的需求。4)加大力度构筑物流发 展平台,提高物流管理技术水平。
参考文献 [1] 陈 森,周 峰. 基于灰色系统理论的物流需求预测模型
[J]. 统计与决策,2006(2):59-60. [2] 李友俊,关欣. 大庆市物流需求量的灰色预测[J]. 产业与科
技论坛,2008,7(1):71-73. [3] 平先秉. 基于灰色系统理论的湖南省物流需求预测分析[J].
+
1) = (x(0)(1) -
u a
)e-ak
+
u a
=
5 639 113e0.0200055k - 5 545 598 .
其中计算可得:C=0.437 ;P=0.9.参照预测精度等
级划分表,表明预测精度合格。从而预测出山西省未
来五年从 2011 到 2015 年的货运量依次为:136 429 万 t,
年份
2001
2002
2003
2004
2005
货运量/万 t 93 515 98 600 106 720 113 000 133 662
年份
2006
2007
2008
2009
2010
货运量/万 t 14ቤተ መጻሕፍቲ ባይዱ 010 155 143 126 864 109 534 124 675
预测模型为:
x̂ (1) (k
181-201. [2] 宋维瑞,肖任坚,房鼎业. 甲醇工艺[M]. 北京:化学工业出
版社,1991.
The Operation Summary of Methanol Rectification System
HU Zhi-tao
(Datang Duolun Coal Chemical Industry LLC Technology Department,Duolun 027300, China) Abstract:Summarize the datang duolun coal chemical industry methanol rectification device system. It resumes the operation process, analyz⁃ es the problem in operation process and presents some solve measures. In production, it makes the finished methanol reach high-class prod⁃