加氢、催化裂化反应器
加氢催化剂、加氢反应器基础知识
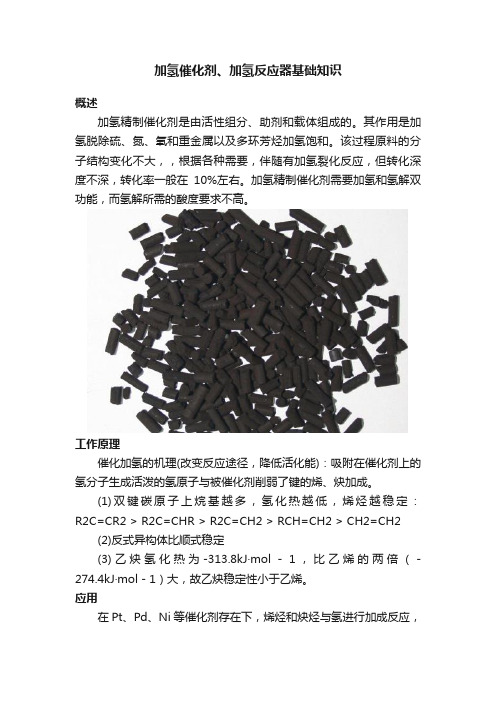
加氢催化剂、加氢反应器基础知识概述加氢精制催化剂是由活性组分、助剂和载体组成的。
其作用是加氢脱除硫、氮、氧和重金属以及多环芳烃加氢饱和。
该过程原料的分子结构变化不大,,根据各种需要,伴随有加氢裂化反应,但转化深度不深,转化率一般在10%左右。
加氢精制催化剂需要加氢和氢解双功能,而氢解所需的酸度要求不高。
工作原理催化加氢的机理(改变反应途径,降低活化能):吸附在催化剂上的氢分子生成活泼的氢原子与被催化剂削弱了键的烯、炔加成。
(1)双键碳原子上烷基越多,氢化热越低,烯烃越稳定:R2C=CR2 > R2C=CHR > R2C=CH2 > RCH=CH2 > CH2=CH2(2)反式异构体比顺式稳定(3)乙炔氢化热为-313.8kJ·mol-1,比乙烯的两倍(-274.4kJ·mol-1)大,故乙炔稳定性小于乙烯。
应用在Pt、Pd、Ni等催化剂存在下,烯烃和炔烃与氢进行加成反应,生成相应的烷烃,并放出热量,称为氢化热(heat of hydrogenation,1mol不饱和烃氢化时放出热量)。
催化加氢的机理(改变反应途径,降低活化能):吸附在催化剂上的氢分子生成活泼的氢原子与被催化剂削弱了键的烯、炔加成。
分类1、加氢裂化催化剂加氢裂化催化剂(hydrocracking catalyst)是石油炼制过程中,重油在360~450℃高温,15~18MPa高压下进行加氢裂化反应,转化成气体、汽油、喷气燃料、柴油等产品的加氢裂化过程使用的催化剂。
加氢裂化过程在石油炼制过程属于二次加工过程,加工原料为重质馏分油,也可以是常压渣油和减压渣油,加氢裂化过程的主要特点是生产灵活性大,产品的分布可由操作条件来控制,可以生产汽油、低凝固点的喷气燃料和柴油,也可以大量生产尾油用作裂解原料或生产润滑油。
所得的产品稳定性好,但汽油的辛烷值不高,。
由于操作条件苛刻,设备投资和操作费用高,应用不如催化裂化广泛。
加氢裂化工艺流程介绍

加氢裂化工艺流程介绍加氢裂化工艺是炼油(石油加工)领域中的一种常用工艺,主要用于将重质石油馏分转化为较轻质的高附加值产品,如汽油和润滑油等。
以下是对加氢裂化工艺流程的介绍。
加氢裂化工艺是一种在高温高压下进行催化裂化反应的技术。
该工艺可以将重质石油馏分分解成轻质零部件,其中包括液化气、汽油、柴油和润滑油等。
在加氢裂化过程中,石油馏分首先经过预热,使其达到反应温度(通常为500-550摄氏度)。
然后,经过高压氢气的加氢作用,将石油分子中的一些碳链断裂成更短的碳链,从而产生较轻质的产品。
加氢裂化的反应器通常采用催化剂床,催化剂床中放置着由金属氧化物和酸性氧化物组成的催化剂。
加氢裂化反应器中的催化剂具有催化裂化反应的活性,能够促进碳链断裂和氢气的加氢反应。
催化剂床中的催化剂能够在高温高压下,将石油分子中的碳链断裂成较轻质的碳链,并捕获并催化裂化反应中产生的不稳定的分子中间体。
在加氢裂化过程中,石油馏分经过反应器后,会进入分离器进行分离。
分离器用于将产物中的不同组分进行分离和纯化。
在分离器中,液相产物被分离出来,并通过蒸汽冷凝器进行冷却,得到液体产品。
而气相产物则通过气体分离装置进行分离,得到液化气等产品。
加氢裂化工艺的设备通常还包括氢气压缩装置、再生装置和废气处理装置等。
氢气压缩装置用于将氢气压缩到加氢裂化过程所需的高压,并输送至反应器中。
再生装置用于再生催化剂,以维持催化剂的活性。
废气处理装置用于处理加氢裂化过程中产生的废气,以达到环保要求。
加氢裂化工艺是一种重要的炼油工艺,可将重质石油馏分转化为较轻质的高附加值产品。
这种工艺通过在高温高压下进行催化裂化反应,将石油分子的碳链断裂成较轻质的碳链。
这种工艺在提高石油利用率、改善燃料质量和减少环境污染方面具有重要意义。
催化裂化(LTAG+MIP)技术工业应用

催化裂化( LTAG+MIP)技术工业应用摘要:某炼化企业新建催化裂化装置,采用LTAG工艺技术,配置有催化柴油加氢改质装置,双反应器共用再生器,主反应器进料为加氢蜡油与低硫渣油混合进料,副反应器进料为加氢后催化柴油。
主反应器采用MIP技术,提升管分第一、第二反应区。
LTAG+MIP技术的应用,多生产高辛烷值汽油组分及化工原料,提高轻油收率,全厂柴汽比降至1以下。
关键词:催化裂化双器柴汽比轻油收率化工原料目前,汽油需求增长缓慢,柴油需求有下降趋势,航空煤油需求保持相对稳定增长,化工原料需求增长迅速,炼油产能过剩,为可持续发展,提高经济效益,需要炼化企业提高轻油收率,减少柴油生产,多生产化工原料。
向“油产化、油转化、油转特”方向发展。
根据公司自身状况,合理利用原有装置流程,选用(LTAG+MIP)技术催化裂化装置,灵活调整产品结构,以适应市场需求。
1装置概况及技术特点某炼化公司新建120×104t/a催化裂化装置,同时配置65×104t/a催化柴油加氢改质装置。
采用中国石化股份有限公司石油化工科学研究院的MIP技术和LTAG技术,以生产高辛烷值低烯烃的汽油、富含丙烯的液化气为主,催化剂为CGP专用催化剂。
再生部分采用单段逆流高效再生技术。
重油沉降器、柴油沉降器、再生器并列式三器布置。
重油提升管加工加氢蜡油与低硫渣油,加工规模80×104t/a。
柴油提升管加工加氢后催化柴油,加工规模40×104t/a。
主副反应器顶反应油气管线合并后进入分馏塔。
主要产出物料有干气、液化气、稳定汽油、柴油、油浆。
简要流程见图1。
图1 反应再生系统简图2原料性质装置3股原料,其中柴油及蜡油2股原料经过加氢处理,渣油原料采用低硫渣油,原料性质提高,大幅降低原料硫含量、多环芳烃、残碳、金属含量等指标,在催化剂及高温条件下尽量向预想方向进行反应,既可达到理想收率,又能提高产品性质。
低硫原料也降低催化装置烟气脱硫设施负担。
催化裂化工艺流程
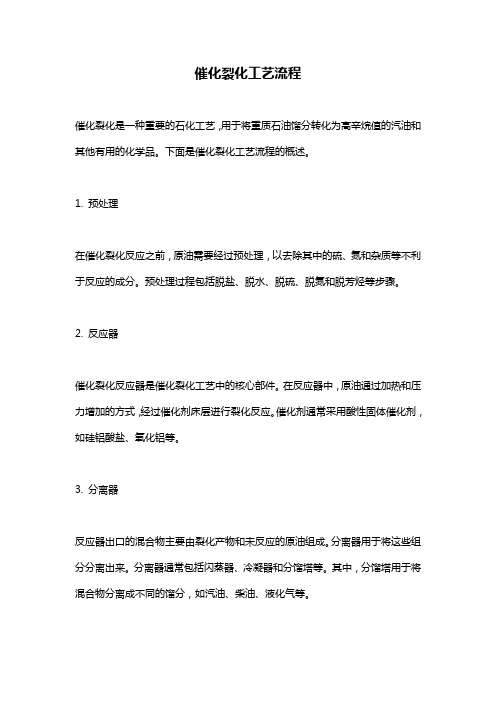
催化裂化工艺流程
催化裂化是一种重要的石化工艺,用于将重质石油馏分转化为高辛烷值的汽油和其他有用的化学品。
下面是催化裂化工艺流程的概述。
1. 预处理
在催化裂化反应之前,原油需要经过预处理,以去除其中的硫、氮和杂质等不利于反应的成分。
预处理过程包括脱盐、脱水、脱硫、脱氮和脱芳烃等步骤。
2. 反应器
催化裂化反应器是催化裂化工艺中的核心部件。
在反应器中,原油通过加热和压力增加的方式,经过催化剂床层进行裂化反应。
催化剂通常采用酸性固体催化剂,如硅铝酸盐、氧化铝等。
3. 分离器
反应器出口的混合物主要由裂化产物和未反应的原油组成。
分离器用于将这些组分分离出来。
分离器通常包括闪蒸器、冷凝器和分馏塔等。
其中,分馏塔用于将混合物分离成不同的馏分,如汽油、柴油、液化气等。
4. 产品处理
裂化产物需要进一步加工处理,以满足市场需求。
处理过程包括脱硫、脱氮、脱蜡、加氢、重整等步骤。
总的来说,催化裂化是一种复杂的工艺流程,需要各种设备和催化剂的协同作用,以实现高效、稳定和可控的反应。
加氢反应器介绍
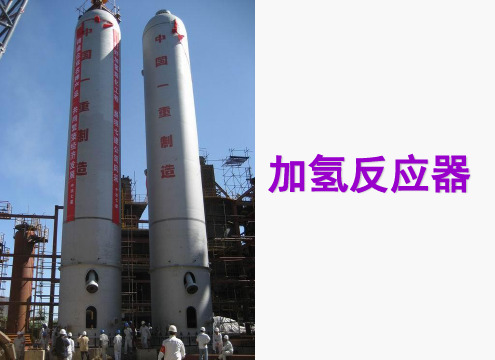
在催化剂床层上面,采用分配盘是为了均布反应介质,改善其流动状况,实 现与催化剂的良好接触,进而达到径向和轴向的均匀分布。
反应器顶部分配盘
3. 积垢篮
由不同规格的不锈钢金属网和骨架构成的篮框,置于反应器上部催化剂床层的顶 部,可为反应物流提供更大的流通面积,在上部催化剂床层的顶部扑集更多的机 械杂质的沉积物,而又不致引起反应器压力降过快地增长;积垢篮框在反应器内 截面上呈等边三角形均匀排列,其内是空的(不装填催化剂或瓷球),安装好后 要须用不锈钢链将其穿连在一起,并牢固地拴在其上部分配盘地支撑梁上,不锈 钢金属链条要有足够地长度裕量(按床层高度下沉5%考虑),以便能适应催化剂 床层的下沉。
括循环氢与新氢气)混合后一起进入换热器与反应生成物换热至300℃
左右,然后进加热炉预热(另一种流程是原料油不进加热炉而只有循 环氢进加热炉预热,在炉出口与换热后的原料油混合,这种流程可以
减少炉管结焦),预热后从反应器顶部进入,在反应器内反应后由底
部排出,经与新鲜原料、循环氢换热后再进入空冷器冷却,冷凝下来 的油和不冷凝的油气和氢气进入高压分离器,油气分离,氢气从高压
4)应力的影响 在高温氢腐蚀中,应力的存在肯定会产生不利的影响。在高温氢 气中蠕变强度会下降。特别是由于二次应力(如热应力或由冷作加工所 引起的应力)的存在会加速高温氢腐蚀。
高温氢腐蚀的防止措施 高温高压氢环境下高温氢腐蚀的防止措施主要是选用耐高温氢腐 蚀的材料,工程设计上都是按照原称为“纳尔逊(Nelson)曲线”来选 择的。 尽量减少钢材中对高温氢腐蚀不利影响的杂质元素(Sn、Sb)。 制造及在役中返修补焊后必须进行焊后热处理。 操作中严防设备超温。 控制外加应力水平。
防止氢脆的若干对策 要防止氢脆损伤发生,主要应从结构设计上、制造过程中和生 产操作方面采取如下措施: (1)尽量减少应变幅度,这对于改善使用寿命很有帮助。 (2)尽量保持TP347堆焊金属或焊接金属有较高的延性。为此,一是 要控制TP347中δ—铁素体含量,以避免含量过多时在焊后最终热处理 过程转变成较多的相而产生脆性;二是对于前述那些易发生氢脆的部 位,应尽量省略TP347堆焊金属或焊接金属的焊后最终热处理,以提 高其延性。 (3)装置停工时冷却速度不应过快,且停工过程中应有使钢中吸藏的 氢能尽量释放出去的工艺过程,以减少器壁中的残留氢含量。 (4)尽量避免非计划紧急停工(紧急放空)。
加氢反应器及催化裂化反应器介绍
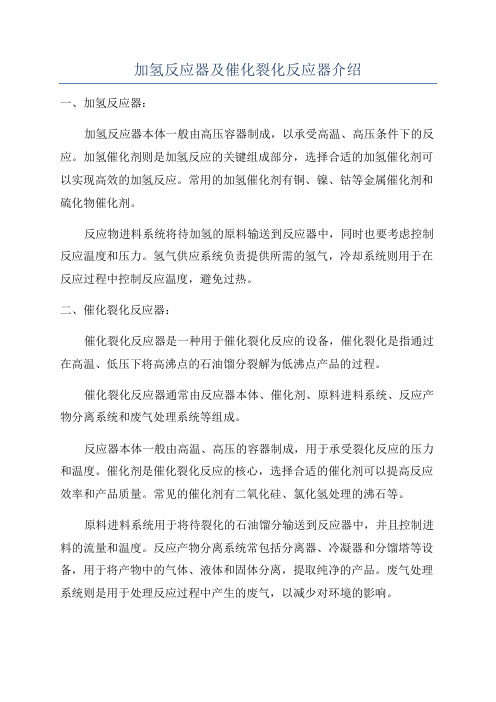
加氢反应器及催化裂化反应器介绍一、加氢反应器:加氢反应器本体一般由高压容器制成,以承受高温、高压条件下的反应。
加氢催化剂则是加氢反应的关键组成部分,选择合适的加氢催化剂可以实现高效的加氢反应。
常用的加氢催化剂有铜、镍、钴等金属催化剂和硫化物催化剂。
反应物进料系统将待加氢的原料输送到反应器中,同时也要考虑控制反应温度和压力。
氢气供应系统负责提供所需的氢气,冷却系统则用于在反应过程中控制反应温度,避免过热。
二、催化裂化反应器:催化裂化反应器是一种用于催化裂化反应的设备,催化裂化是指通过在高温、低压下将高沸点的石油馏分裂解为低沸点产品的过程。
催化裂化反应器通常由反应器本体、催化剂、原料进料系统、反应产物分离系统和废气处理系统等组成。
反应器本体一般由高温、高压的容器制成,用于承受裂化反应的压力和温度。
催化剂是催化裂化反应的核心,选择合适的催化剂可以提高反应效率和产品质量。
常见的催化剂有二氧化硅、氯化氢处理的沸石等。
原料进料系统用于将待裂化的石油馏分输送到反应器中,并且控制进料的流量和温度。
反应产物分离系统常包括分离器、冷凝器和分馏塔等设备,用于将产物中的气体、液体和固体分离,提取纯净的产品。
废气处理系统则是用于处理反应过程中产生的废气,以减少对环境的影响。
催化裂化反应器在石油炼制工艺中起到重要作用。
它可以将重质石油馏分裂解为轻质馏分,如汽油、柴油和液化石油气等,提高石油产品的附加值和利用率。
总结:加氢反应器和催化裂化反应器是石油化工领域常见的反应设备。
加氢反应器主要用于将不饱和化合物加氢饱和,提高产品质量;催化裂化反应器主要用于将高沸点的石油馏分裂解为低沸点产品,提高产品附加值。
了解这两种反应器的结构和工作原理对于研究和优化石油化工过程具有重要意义。
多相反应器的分类及适用的单元操作过程

多相反应器的分类及适用的单元操作过程多相反应器是一种用于进行非均相催化反应的设备,通过将气体或液体的反应物质与固体催化剂接触,实现催化反应的进行。
根据其结构和工作原理,多相反应器可以分为多种类型,并且适用于不同的单元操作过程。
本文将逐步介绍多相反应器的分类以及适用的单元操作过程。
一、多相反应器的分类根据反应器结构和形式的不同,可以将多相反应器分为以下几种类型:1. 固定床反应器:固定床反应器是一种最常见的多相反应器类型。
它由一个固定的催化剂床层组成,催化剂固定在反应器内部的填料、网格或支撑物上。
反应物流经固定床后,与催化剂发生反应。
固定床反应器具有体积大、操作方便等优点。
2. 流动床反应器:流动床反应器是一种将液体或气体的反应物以流动的形式通过催化剂床层的装置。
在流动床反应器中,反应物进入反应器床层后,与催化剂接触并发生反应,反应产物从反应器中流出。
流动床反应器具有处理大量物质、操作灵活等优点。
3. 移动床反应器:移动床反应器是一种将固体或液体的反应物经过固体催化剂床层的载体上方运动的装置。
在移动床反应器中,反应物在固体催化剂床层上发生反应,反应产物沿床层向下流动,催化剂从反应器底部取出并再次注入到床层顶部。
移动床反应器适用于处理粒状固体及高粘度液体。
4. 进料床反应器:进料床反应器是一种将气体或液体的反应物与固体催化剂通过进料装置分别输入反应器的装置。
在进料床反应器中,反应物通过进料装置进入反应器,与固体催化剂在反应器内部发生反应。
进料床反应器适用于处理粒状固体及高粘度液体。
5. 旋转床反应器:旋转床反应器是一种通过旋转反应器床层或反应器本身来实现反应物与固体催化剂接触的装置。
旋转床反应器具有较高的传质速率和传热速率,适用于气体-固体反应等。
二、适用的单元操作过程多相反应器适用于许多不同的单元操作过程,其中一些常见的单元操作过程包括:1. 吸附:吸附是指将气体或液体的分子吸附到固体表面上的过程,多相反应器中的固体催化剂常常具有很高的吸附能力。
加氢反应器及催化裂化反应器介绍

2. 分配盘
目前,国内加氢反应器所使用的反应物流分配器,按其作用原理大致可分为溢流 式和抽吸喷射式两类;反应物流分配盘应不漏液,安装后须进行测漏试验,即在 分配盘上充水至100mm高,在5分钟内其液位下降高度,以不大于5mm为合格;分配 盘安装的水平度要求,对于喷射式的分配器,包括制造公差和在载荷作用下的绕 度在内,其分配盘的水平度应控制为±5mm~±6mm;对于溢流式的分配器,其分配 盘安装的水平度要求更严格一些。
反应器内设置有入口扩散器、 积垢篮、卸料管、催化剂支撑盘、 出口捕集器、气液反应物流分配盘、 冷氢箱、熱电偶保护管和出口收集 器等反应器内构件。
• 入口扩散器
来自反应器入口的介质首先经过入口扩散器, 在上部锥形体整流后,经上下两挡板的两层 孔的节流、碰撞后被扩散到整个反应器截面 上。
其主要作用为:一是将进入的介质扩散到反 应器的整个截面上;二是消除气、液介质对 顶分配盘的垂直冲击,为分配盘的稳定工作 创造条件;三是通过扰动,促使气液两相混 合
床层的下沉。
4. 催化剂支撑盘
催化剂支撑盘由T形大梁、格栅和丝网组成。大梁的两边搭在反应器 器壁的凸台上,而格栅则放在大梁和凸台上。格栅上平铺一层粗不锈钢丝 网,和一层细不锈钢丝网,上面就可以装填磁球和催化剂了。
催化剂支撑大梁和格栅要有足够的高温强度和刚度。即在420℃高温 下弯曲变形也很小,且具有一定的抗腐蚀性能。因此,大梁、格栅和丝网 的材质均为不锈钢。在设计中应考虑催化剂支撑盘上催化剂和磁球的重量、 催化剂支撑盘本身的重量、床层压力降和操作液重等载荷,经过计算得出 支撑大梁和格栅的结构尺寸。
冷氢加入系统的作用和要求是: 均匀、稳定地供给足够的冷氢量; 必须使冷氢与热反应物充分混合,在进入下一床层时有一 均匀的温度和物料分布。 冷氢管按形式分直插式、树枝状形式和环形结构。 对于直径较小的反应器,采用结构简单便于安装的直插式 结构即可。 对于直径较大的反应器,直插式冷氢管打入的冷氢与上层 反应后的油气混合效果就不好,直接影响了冷氢箱的再混合效 果。这时就应采用树枝状或环形结构。
加氢裂解反应器
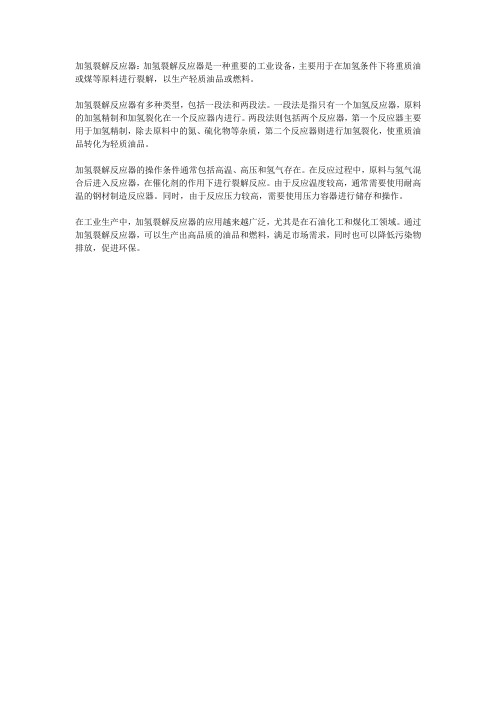
加氢裂解反应器:加氢裂解反应器是一种重要的工业设备,主要用于在加氢条件下将重质油或煤等原料进行裂解,以生产轻质油品或燃料。
加氢裂解反应器有多种类型,包括一段法和两段法。
一段法是指只有一个加氢反应器,原料的加氢精制和加氢裂化在一个反应器内进行。
两段法则包括两个反应器,第一个反应器主要用于加氢精制,除去原料中的氮、硫化物等杂质,第二个反应器则进行加氢裂化,使重质油品转化为轻质油品。
加氢裂解反应器的操作条件通常包括高温、高压和氢气存在。
在反应过程中,原料与氢气混合后进入反应器,在催化剂的作用下进行裂解反应。
由于反应温度较高,通常需要使用耐高温的钢材制造反应器。
同时,由于反应压力较高,需要使用压力容器进行储存和操作。
在工业生产中,加氢裂解反应器的应用越来越广泛,尤其是在石油化工和煤化工领域。
通过加氢裂解反应器,可以生产出高品质的油品和燃料,满足市场需求,同时也可以降低污染物排放,促进环保。
加氢反应器及催化裂化反应器介绍

反应条件控制
利用新型合金和高性能陶瓷等材料,提高反应器的耐腐蚀性能和使用寿命。
高强度耐腐蚀材料
研发新型高温和高压材料,满足加氢反应器和催化裂化反应器在高温高压下的操作需求。
耐高温和高压材料
探索具有特殊功能的材料,如光催化材料、电催化材料等,为加氢和催化裂化过程提供新的解决方案。
功能材料
THANKS
石油化工
煤化工
环保领域
在煤化工领域,加氢反应器可用于煤焦油加氢、煤液化等过程,生产清洁燃料和化学品。
加氢反应器还可用于处理含硫、氮、氧等杂质的废弃物,实现环保减排。
03
02
01
优点
加氢反应器能够脱除原料油中的硫、氮、氧等杂质以及重金属元素,提高油品质量;能够生产高清洁油品,满足环保要求;具有较高的处理能力和较低的投资成本。
缺点
催化裂化反应器需要使用催化剂,且催化剂容易失活和中毒,需要定期更换或再生。此外,催化裂化技术还需要消耗大量的能量和原料,生产成本较高。
加氢反应器与催化裂化反应器的比较
CATALOGUE
03
加氢反应器的工作原理是通过加氢反应将原料中的有害物质转化为无害物质,而催化裂化反应器则是通过催化剂的作用将重质油转化为轻质油。
总结词
加氢反应器主要用于石油化工和煤化工领域,如煤制油、柴油加氢精制、润滑油加氢精制等。而催化裂化反应器则广泛应用于炼油工业,将重质油转化为轻质油、气体和焦炭等,是炼油工业中最重要的加工方法之一。
详细描述
总结词:加氢反应器的优点在于能够提高产品质量、减少环境污染,缺点是工艺复杂、投资成本高。催化裂化反应器的优点在于能够将重质油转化为轻质油,缺点是会产生较多的副产品和废弃物。
加氢反应器和催化裂化反应器的未来发展
化工装备行业四大类产品解析
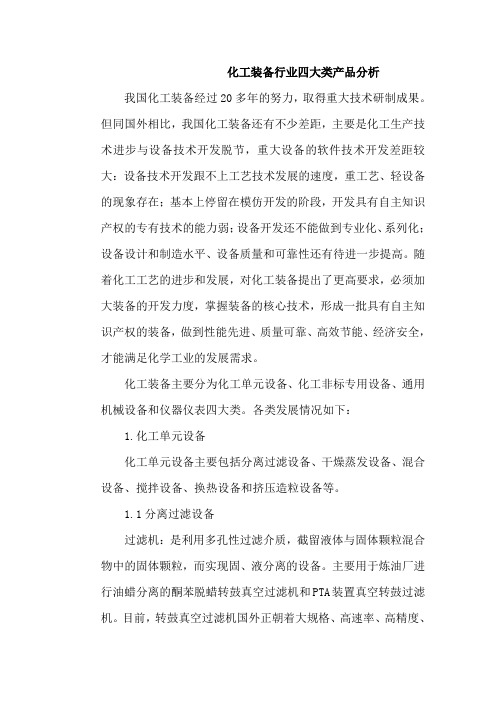
化工装备行业四大类产品分析我国化工装备经过20多年的努力,取得重大技术研制成果。
但同国外相比,我国化工装备还有不少差距,主要是化工生产技术进步与设备技术开发脱节,重大设备的软件技术开发差距较大:设备技术开发跟不上工艺技术发展的速度,重工艺、轻设备的现象存在;基本上停留在模仿开发的阶段,开发具有自主知识产权的专有技术的能力弱;设备开发还不能做到专业化、系列化;设备设计和制造水平、设备质量和可靠性还有待进一步提高。
随着化工工艺的进步和发展,对化工装备提出了更高要求,必须加大装备的开发力度,掌握装备的核心技术,形成一批具有自主知识产权的装备,做到性能先进、质量可靠、高效节能、经济安全,才能满足化学工业的发展需求。
化工装备主要分为化工单元设备、化工非标专用设备、通用机械设备和仪器仪表四大类。
各类发展情况如下:1.化工单元设备化工单元设备主要包括分离过滤设备、干燥蒸发设备、混合设备、搅拌设备、换热设备和挤压造粒设备等。
1.1分离过滤设备过滤机:是利用多孔性过滤介质,截留液体与固体颗粒混合物中的固体颗粒,而实现固、液分离的设备。
主要用于炼油厂进行油蜡分离的酮苯脱蜡转鼓真空过滤机和PTA装置真空转鼓过滤机。
目前,转鼓真空过滤机国外正朝着大规格、高速率、高精度、全自动方向发展。
国内是从意大利EIMCO公司引进的设计、制造技术,经消化吸收和改进,形成了一整套加工、组对、焊接工艺。
相比之下,主要差距在于对市场发展、产品需求认识不够,创新能力低,对引进技术精髓消化较差。
离心机:离心分离机是利用离心力分离液体与固体颗粒或液体与液体的混合物中各组分的机械,又称离心机。
主要有立式和卧式螺旋卸料沉降式离心机。
国外离心机技术发展较快,而且实现了专业化和系列化;国内研制的El、式LWFl000一N型和LWFl050一N型离心机已分别用于7~10万吨/年高密度聚乙烯装置的悬浮液的分离,研制的LWl200x1980型离心机用于22.5万吨/年PTA浆液的脱水,离心机转鼓直径达到φ1200mm。
催化裂化流程
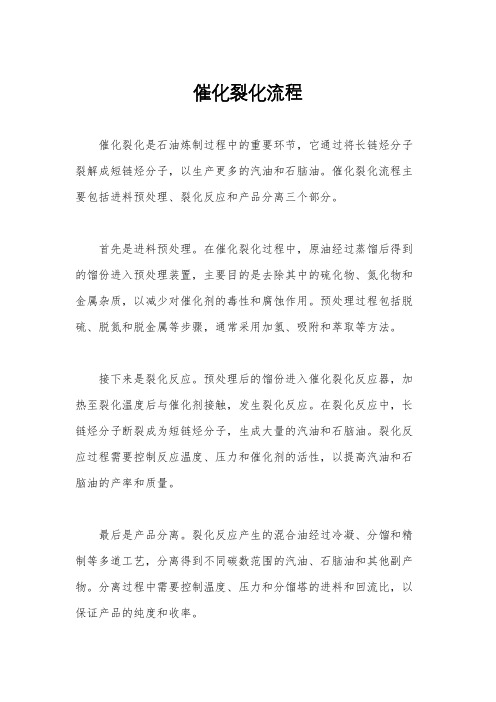
催化裂化流程
催化裂化是石油炼制过程中的重要环节,它通过将长链烃分子裂解成短链烃分子,以生产更多的汽油和石脑油。
催化裂化流程主要包括进料预处理、裂化反应和产品分离三个部分。
首先是进料预处理。
在催化裂化过程中,原油经过蒸馏后得到的馏份进入预处理装置,主要目的是去除其中的硫化物、氮化物和金属杂质,以减少对催化剂的毒性和腐蚀作用。
预处理过程包括脱硫、脱氮和脱金属等步骤,通常采用加氢、吸附和萃取等方法。
接下来是裂化反应。
预处理后的馏份进入催化裂化反应器,加热至裂化温度后与催化剂接触,发生裂化反应。
在裂化反应中,长链烃分子断裂成为短链烃分子,生成大量的汽油和石脑油。
裂化反应过程需要控制反应温度、压力和催化剂的活性,以提高汽油和石脑油的产率和质量。
最后是产品分离。
裂化反应产生的混合油经过冷凝、分馏和精制等多道工艺,分离得到不同碳数范围的汽油、石脑油和其他副产物。
分离过程中需要控制温度、压力和分馏塔的进料和回流比,以保证产品的纯度和收率。
催化裂化流程的优化对提高汽油和石脑油的产率和质量至关重要。
通过改进预处理工艺、优化裂化反应条件和提高产品分离效率,可以降低能耗、减少废物排放,提高产品质量和经济效益。
总的来说,催化裂化流程是炼油工艺中的重要环节,它通过预
处理、裂化反应和产品分离三个部分,将原油转化为更多的汽油和
石脑油。
优化催化裂化流程对提高产率和质量具有重要意义,需要
综合考虑预处理、反应和分离等环节,以实现经济、高效和环保的
生产目标。
反应器的原理及应用

反应器的原理及应用1. 引言反应器是化学工程中一种非常重要的设备,广泛应用于化工生产中。
本文将介绍反应器的原理及应用,通过对反应器的介绍,帮助读者理解反应器的基本工作原理和常见应用场景。
2. 反应器的工作原理反应器是一种用于进行化学反应的设备,其工作原理是利用加热、冷却、搅拌等方式控制反应物质在反应过程中的温度、压力和混合程度。
下面将介绍几种常见的反应器工作原理:2.1 批量反应器批量反应器是最简单的一种反应器,其工作原理是将待反应的物质一次性加入反应器中进行反应。
其优点是操作简单,适用于小规模生产和实验室研究。
然而,由于无法连续供给反应物质,生产效率较低。
2.2 连续流动反应器连续流动反应器是一种持续供给反应物质并连续收集产物的反应器,其工作原理是通过分别将反应物质和催化剂以一定流速供给反应器,使反应在反应器内进行。
连续流动反应器由于可以连续供给反应物质,生产效率较高,适用于大规模生产。
2.3 催化反应器催化反应器是通过添加催化剂来提高反应速率的反应器,其工作原理是将催化剂与反应物质一起放入反应器中进行反应。
催化反应器由于催化剂的作用,可以在较低的温度和压力下进行反应,节省能源和提高反应效率。
3. 反应器的应用反应器在化工生产中有着广泛的应用,下面将列举几个常见的应用场景。
3.1 石油炼制在石油炼制过程中,反应器用于各种催化反应、裂化反应、加氢反应等。
例如,催化裂化反应器用于将重质石油馏分转化为轻质石油产品,加氢反应器用于将硫化氢等有害物质转化为无害物质。
反应器在石油炼制中起到了非常重要的作用。
3.2 化学品生产在化学品生产中,反应器用于各种有机合成反应、聚合反应等。
例如,聚乙烯反应器用于合成聚乙烯,硝化反应器用于合成硝酸等。
反应器不仅可以提高产品的纯度和产量,还可以控制反应物质的选择性。
3.3 生物工程在生物工程领域,反应器用于培养微生物、细胞培养、酶反应等。
例如,发酵反应器用于培养微生物产生乙醇、酸等产物,细胞培养反应器用于培养动物细胞合成蛋白质。
加氢反应器及催化裂化反应器介绍

煤化工
在煤化工领域,加氢反应 器用于煤制油、煤制气等 过程中,提高产品质量和 产量。
精细化工
加氢反应器在精细化工领 域也有应用,如合成香料 、医药中间体等。
催化裂化反应器的应用
重油轻质化
催化裂化反应器可将重质 油转化为轻质油,提高油 品的使用价值。
ห้องสมุดไป่ตู้生产高辛烷值汽油
通过催化裂化反应,可以 生产出高辛烷值的汽油, 满足日益严格的环保要求 。
反应过程
原料油和空气在催化剂床层中发生催化裂化反应,生成轻 质油和裂化气。反应过程中产生的热量通过取热装置移走 。
催化剂再生
催化剂在反应过程中会逐渐失活,需要进行再生处理。再 生过程通常包括烧焦、氧化等步骤,使催化剂恢复活性并 循环使用。
04
CHAPTER
加氢反应器和催化裂化反应 器的比较
原理比较
加氢反应器及催化裂化反应器 介绍
汇报人:XX
目录
CONTENTS
• 引言 • 加氢反应器概述 • 催化裂化反应器概述 • 加氢反应器和催化裂化反应器的比较 • 加氢反应器和催化裂化反应器的应用 • 加氢反应器和催化裂化反应器的发展趋势 • 结论与建议
01
CHAPTER
引言
目的和背景
介绍加氢反应器和催 化裂化反应器的基本 概念、原理、特点及 应用。
THANKS
谢谢
催化裂化反应器
优点包括原料适应性强、轻质油 收率高、操作灵活等;缺点包括 产品质量相对较差、催化剂消耗 量大、设备磨损严重等。
05
CHAPTER
加氢反应器和催化裂化反应 器的应用
加氢反应器的应用
01
02
03
石油加工
加氢反应器在石油加工中 广泛应用,主要用于提高 油品质量、降低硫含量、 改善颜色等。
加氢裂化工艺流程介绍

加氢裂化工艺流程介绍加氢裂化是一种重要的炼油工艺,用于将较重的原油分解成较轻的石油产品。
这种工艺可以将高沸点的烃分子转化为低沸点的烃分子,其中利用高压下加氢作用可使原油中的不饱和烃分子饱和,防止其在裂化过程中极化而产生沉淀,保证反应的稳定性和可靠性。
以下是加氢裂化的工艺流程介绍。
原料进料和预热:经过原油预处理后,原油经过加热器加热至适合反应的温度,并在氢气流中预热,这个温度通常在350-425℃之间。
经过预热后的原料进入反应器。
反应器:反应器通常采用固定床反应器,是炼油厂中最重要的设备之一。
原油经过预热后,进入反应器与催化剂在高压下发生反应。
反应器通常包含多个反应床,每个床上设有反应器催化剂,催化剂用于催化裂化反应。
反应器床的数目和长度由加氢裂化过程所需的时间和裂化转化率所决定。
分离器:在反应器内的原油在被跟氢的同时产生大量的副产物,包括液体和气态。
这些产物需要经过分离器分离,分离出可用于萃取和转化的产品。
分离器通常采用分板式塔,用于分离气体和液体产物。
净化:在分离过程中,产生的气体含量很高,因此必须经过净化处理,将油气流中的硫化氢、二氧化碳、氮气和其他杂质分离出来。
净化系统通常包括净化塔、废气热交换器、蒸汽压力提升器和催化剂的再生炉。
输送和储存:产生的产品通过管道输送到储罐中进行储存。
这些产物包括轻质油、石脑油、液化气和其他轻质产品。
这些产品可以直接用于生产燃料油、柴油和其他化工产品。
总结:加氢裂化工艺流程涉及的关键步骤包括原料进料、预热、反应器、分离器、净化、输送和储存。
通过这个过程,原油中的高沸点烃类可以转化为低沸点产物,可用于生产各种化工产品。
加氢反应器介绍 ppt课件

2. 分配盘
目前,国内加氢反应器所使用的反应物流分配器,按其作用原理大致可分为溢流 式和抽吸喷射式两类;反应物流分配盘应不漏液,安装后须进行测漏试验,即在 分配盘上充水至100mm高,在5分钟内其液位下降高度,以不大于5mm为合格;分配 盘安装的水平度要求,对于喷射式的分配器,包括制造公差和在载荷作用下的绕 度在内,其分配盘的水平度应控制为±5mm~±6mm;对于溢流式的分配器,其分配 盘安装的水平度要求更严格一些。
按反应器本体结构分类: 分为单层结构、多层结构。单层结构包括钢板卷焊及
锻焊结构;多层结构一般有绕带式及热套式。
煅焊 结构 反应 器制 造过 程
加氢过程由于存在有气、液、 固三相的放热反应,欲使反应进料 (气、液两相)与催化剂(固相) 充分、均匀、有效地接触,加氢反 应器设计有多个催化剂床层,在每 个床层的顶部都设置有分配盘,并 在两个床层之间设有温控结构(冷 氢箱),以确保加氢装置的安全平 稳生产和延长催化剂的使用寿命。
床层的下沉。
4. 催化剂支撑盘
催化剂支撑盘由T形大梁、格栅和丝网组成。大梁的两边搭在反应器 器壁的凸台上,而格栅则放在大梁和凸台上。格栅上平铺一层粗不锈钢丝 网,和一层细不锈钢丝网,上面就可以装填磁球和催化剂了。
催化剂支撑大梁和格栅要有足够的高温强度和刚度。即在420℃高温 下弯曲变形也很小,且具有一定的抗腐蚀性能。因此,大梁、格栅和丝网 的材质均为不锈钢。在设计中应考虑催化剂支撑盘上催化剂和磁球的重量、 催化剂支撑盘本身的重量、床层压力降和操作液重等载荷,经过计算得出 支撑大梁和格栅的结构尺寸。
催化裂化与加氢裂化的异同点
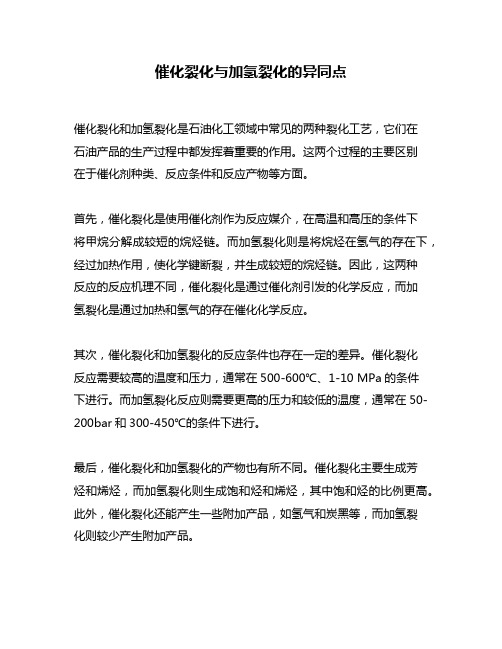
催化裂化与加氢裂化的异同点
催化裂化和加氢裂化是石油化工领域中常见的两种裂化工艺,它们在
石油产品的生产过程中都发挥着重要的作用。
这两个过程的主要区别
在于催化剂种类、反应条件和反应产物等方面。
首先,催化裂化是使用催化剂作为反应媒介,在高温和高压的条件下
将甲烷分解成较短的烷烃链。
而加氢裂化则是将烷烃在氢气的存在下,经过加热作用,使化学键断裂,并生成较短的烷烃链。
因此,这两种
反应的反应机理不同,催化裂化是通过催化剂引发的化学反应,而加
氢裂化是通过加热和氢气的存在催化化学反应。
其次,催化裂化和加氢裂化的反应条件也存在一定的差异。
催化裂化
反应需要较高的温度和压力,通常在500-600℃、1-10 MPa的条件
下进行。
而加氢裂化反应则需要更高的压力和较低的温度,通常在50-200bar和300-450℃的条件下进行。
最后,催化裂化和加氢裂化的产物也有所不同。
催化裂化主要生成芳
烃和烯烃,而加氢裂化则生成饱和烃和烯烃,其中饱和烃的比例更高。
此外,催化裂化还能产生一些附加产品,如氢气和炭黑等,而加氢裂
化则较少产生附加产品。
综上所述,催化裂化和加氢裂化虽然都是裂化工艺,但它们在催化剂种类、反应条件和产物等方面有所不同。
在实际的生产过程中,需要根据不同的原料和生产要求选择适当的裂化工艺。
加氢催化裂化

催化裂化装置阀门——单双动滑阀、塞阀、高温蝶阀、高温闸阀
单动滑阀用在催化裂化两器之间的催化剂循环管线上的一个滑动板的滑阀。
正常操作时用以调节催化剂的循环量。
开、停工或发生事故时,用于快速切断催化剂循环和两器间的连通。
双动滑阀催化剂裂化专用阀门。
有两个阀板,可以同时进行双向开启与关闭的滑阀。
安装在流化催化裂化再生器顶部烟气出口管线上,以控制再生器的压力,使之与反应器压力基本平衡。
操作温度700~780℃,控制灵敏度达1/400,准确度1/100。
塞阀是催化裂化装置的关键设备之一。
按照它在催化裂化(FCC)工艺过程中的作用可分为待生塞阀和再生塞阀,分别安装在再生器底部的待生和再生立管上,用来调节待生和再生催化剂的循环量,以控制气提段料位和提升管出口温度,且在装置开、停工时作为切断阀切断催化剂循环。
高温蝶阀安装在烟气轮机和高温闸阀之间的管道上,作为控制再生器压力和通入烟气轮机烟气流量的调节阀,介质为再生器所产生的含有催化剂的高温烟气。
高温闸阀垂直安装在高温蝶阀前的水平烟气管道上,当烟气轮机正常工作时,此阀全开,停工或事故状态时通过执行机构及时关闭此阀截断烟气,保证烟气轮机的安全和停工检修的需要。
- 1、下载文档前请自行甄别文档内容的完整性,平台不提供额外的编辑、内容补充、找答案等附加服务。
- 2、"仅部分预览"的文档,不可在线预览部分如存在完整性等问题,可反馈申请退款(可完整预览的文档不适用该条件!)。
- 3、如文档侵犯您的权益,请联系客服反馈,我们会尽快为您处理(人工客服工作时间:9:00-18:30)。
8. 热电偶
为监视加氢放热反应引起床层温度升高及床层截面温度分布状况 而对操作温度进行监控。
加氢反应器常见损伤与对策
1.高温氢腐蚀
高温氢腐蚀是在高温高压条件下扩散侵入钢中的氢与不稳定的碳 化物发生化学反应,生成甲烷气泡(它包含甲烷的成核过程和成长), 即FeC+2H2一CH4+3Fe,并在晶间空穴和非金属夹杂部位聚集,引起钢 的强度、延性和韧性下降与劣化,同时发生晶间断裂。由于这种脆化 现象是发生化学反应的结果,所以它具有不可逆的性质,也称永久脆 化现象。 高温氢腐蚀有两种形式:一是表面脱碳;二是内部脱碳。 表面脱碳不产生裂纹,在这点上与钢材暴露在空气、氧气或二氧 化碳等一些气体中所产生的脱碳相似,表面脱碳的影响—般很轻,其 钢材的强度和硬度局部有所下降而延性提高。 内部脱碳是由于氢扩散侵入到钢中发生反应生成了甲烷,而甲烷 又不能扩散出钢外,就聚集于晶界空穴和夹杂物附近,形成了很高的 局部应力,使钢产生龟裂、裂纹或鼓包使用的反应物流分配器,按其作用原理大致可分为溢流 式和抽吸喷射式两类;反应物流分配盘应不漏液,安装后须进行测漏试验,即在 分配盘上充水至100mm高,在5分钟内其液位下降高度,以不大于5mm为合格;分配 盘安装的水平度要求,对于喷射式的分配器,包括制造公差和在载荷作用下的绕 度在内,其分配盘的水平度应控制为±5mm~±6mm;对于溢流式的分配器,其分配 盘安装的水平度要求更严格一些。
3.高温硫化氢的腐蚀
在加氢装置中,一般都会有硫化氢腐蚀介质存在。对于以碳钢 或低铬钢制的设备,在操作温度高于 204℃,其腐蚀速度将随着温 度的升高而增加。特别是当硫化氢和氢共存的条件下,它比硫化氢 单独存在时产生的腐蚀还要更为剧烈和严重。氢在这种腐蚀过程中 起着催化剂的作用,加速了腐蚀的进展。 对于在硫化氢和氢共存条件下的材料选择,一是参考相似条件 的经验数据来预计材料的腐蚀率后确定;二是在无经验数据依据时 ,可根据柯珀(Couper)曲线来估算材料的腐蚀率。该曲线是美国腐 蚀工程师学会的一个专门小组通过大量的试验和生产数据经电子计 算机反复回归处理、关联后整理出来的。据验证按此曲线估算出来 的腐蚀率与工业装置的经验比较接近。对于不同铬含量 (O%-9%) 的铬钢的腐蚀率,先按给定的硫化氢浓度和温度从图上求出碳钢的 腐蚀率,然后再乘以相应铬含量的系数 Fcr。加以修正后的值即是 。
影响高温氢腐蚀的主要因素 1)温度、压力和暴露时间的影响 温度和压力对氢腐蚀的影响很大,温度越高或者压力越大发生高 温腐蚀的起始时间就越早。 2)合金元素和杂质元素的影响 在钢中凡是添加能形成很稳定碳化物的元素(如铬、钼、钒、钛、 钨等),就可使碳的活性降低,从而提高钢材抗高温氢腐蚀的能力。 在合金元素对抗氢腐蚀性能的影响中,元素的复合添加和各自添 加的效果不同。例如铬、钼的复合添加比两个儿素单独添加时可使抗 氢腐蚀性能进一步提高。在加氢高压设备中广泛地使用着铬-钼钢系, 其原因之一也在于此。 3)热处理的影响 钢的抗氢腐蚀性能,与钢的显微组织也有密切关系。对于淬火状 态,只需经很短时间加热就出现了氢腐蚀。但是一施行回火,且回火 温度越高,由于可形成稳定的碳化物,抗氢腐蚀性能就得到改善。另 外,对于在氢环境下使用的铬-钼钢设备,施行了焊后热处理同样具有 可提高抗氢腐蚀能力的效果。
2. 移动床反应器
3. 流化床反应器
固定床反应器使用最为广泛(气液并流下流式)
固定床反应器: 床层内固体催化剂处于静 止状态。
特点:催化剂不宜磨损,
催化剂在不失活情况下可 长期使用。 主要适于加工固体杂质、 油溶性金属含量少的油品
移动床反应器: 生产过程中催化剂连 续或间断移动加入或
卸出反应器。
加氢反应器 及催化裂化 反应器介绍
一.加氢反应器
加氢反应器是各类加氢工艺的关键设备
加氢过程分类: 1.加氢处理(进料分子基本无变化,使烯烃饱和及脱硫) 2.加氢精制(约≤10%原料分子降低分子量) 3.加氢裂化(有≥10%原料分子转化为小分子)
加氢反应器分类(按照工艺流程及结构分类)
1. 固定床反应器
4)应力的影响 在高温氢腐蚀中,应力的存在肯定会产生不利的影响。在高温氢 气中蠕变强度会下降。特别是由于二次应力(如热应力或由冷作加工所 引起的应力)的存在会加速高温氢腐蚀。
高温氢腐蚀的防止措施 高温高压氢环境下高温氢腐蚀的防止措施主要是选用耐高温氢腐 蚀的材料,工程设计上都是按照原称为“纳尔逊(Nelson)曲线”来选 择的。 尽量减少钢材中对高温氢腐蚀不利影响的杂质元素(Sn、Sb)。 制造及在役中返修补焊后必须进行焊后热处理。 操作中严防设备超温。 控制外加应力水平。
4.连多硫酸引起的应力腐蚀开裂 应力腐蚀开裂是某一金属 (钢材)在拉应力和特定的腐蚀介质共同 作用下所发生的脆性开裂现象。奥氏体不锈钢对于硫化物应力腐蚀开 裂是比较敏感的。连多硫酸 (H2Sx06 , x=3-6) 引起的应力腐蚀开裂也 属于硫化物应力腐蚀开裂,一般为晶间裂纹。这种开裂与在高温运转 时由于碳化铬析出在晶界上,使晶界附近的铬浓度减少,形成贫铬区 有关。连多硫酸的形成是由于设备在含有高温硫化氢的气氛下操作时 生成了硫化亚铁,而当设备停止运转或停工检修时,它与出现的水分 和进入设备内的空气中的氧发生反应的结果。即: 3FeS+502----Fe2O3· FeO+3SO2 SO2+H20—---H2SO3 H2S03+1/202----H2S04 FeS十H2SO3——mH2SxO6十nFe’ FeS+H2S04一---FeSO4+H2S H2SO3十H2S-----mH2Sx06十nS FeS十H2Sx06一--FeSx06+H2S
4. 催化剂卸料管
固定床反应器每一催化剂床层下部均安装有若干根卸料管,跨过催化剂支撑盘、 物料分配盘及冷氢箱,通向下一床层,作为在反应器停工卸除催化剂的卸剂通道。
5. 冷氢管
烃类加氢反应属于放热反应,对多床层的加氢反应器来说, 油气和氢气在上一床层反应后温度将升高,为了下一床层继续 有效反应的需要,必须在两床层间引入冷氢气来控制温度。将 冷氢气引入反应器内部并加以散布的管子被称为冷氢管。 冷氢加入系统的作用和要求是: 均匀、稳定地供给足够的冷氢量; 必须使冷氢与热反应物充分混合,在进入下一床层时有一 均匀的温度和物料分布。 冷氢管按形式分直插式、树枝状形式和环形结构。 对于直径较小的反应器,采用结构简单便于安装的直插式 结构即可。 对于直径较大的反应器,直插式冷氢管打入的冷氢与上层 反应后的油气混合效果就不好,直接影响了冷氢箱的再混合效 果。这时就应采用树枝状或环形结构。
2.氢脆 所谓氢脆,就是由于氢残留在钢中所引起的脆化现象。产生了氢 脆的钢材,其延伸率和断面收缩率显著下降。这是由于侵人钢中的原 子氢,使结晶的原子结合力变弱,或者作为分子状在晶界或夹杂物周 边上析出的结果。但是,在一定条件下,若能使氢较彻底地释放出来, 钢材的力学性能仍可得到恢复。这一特性与前面介绍的氢腐蚀截然不 同,所以氢脆是可逆的,也称作一次脆化现象。 氢脆的敏感性一般是随钢材的强度的提高而增加,钢的显微组织 对氢脆也有影响。钢材氢脆化的程度还与钢中的氢含量密切相关。强 度越高,只要吸收少量的氢,就可引起很严重的脆化。 对于操作在高温高压氢环境下的设备,在操作状态下,器壁中会 吸收一定量的氢。在停工的过程中,由于冷却速度太快,钢中的氢来 不及扩散出来,造成过饱和氢残留在器壁内,就可能在温度低于150℃ 时引起亚临界裂纹扩展,对设备的安全使用带来威胁。 在高温高压临氢设备中,特别是内表面堆焊有奥氏体不锈钢堆焊 层的加氧反应器曾发生过一些氢脆损伤的实例。其部位多发生在反应 器支持圈角焊缝上以及堆焊奥氏体小锈钢的梯形槽法兰密封面的槽底 拐角处。
主要适于加工有较高 金属有机化合物及沥 青质的渣油原料,可 避免床层堵塞及催化
剂失活问题。
流化床反应器: 原料油及氢气自反应 器下部进入通过催化
剂床层,使催化剂流
化并被流体托起。 主要也适于加工有较 高金属有机化合物、 沥青质及固体杂质的 渣油原料。
按反应器使用状态分类:
使用状态下高温介质是否与器壁接触,分为冷壁结构
4. 催化剂支撑盘
催化剂支撑盘由T形大梁、格栅和丝网组成。大梁的两边搭在反应器 器壁的凸台上,而格栅则放在大梁和凸台上。格栅上平铺一层粗不锈钢丝 网,和一层细不锈钢丝网,上面就可以装填磁球和催化剂了。 催化剂支撑大梁和格栅要有足够的高温强度和刚度。即在420℃高温 下弯曲变形也很小,且具有一定的抗腐蚀性能。因此,大梁、格栅和丝网 的材质均为不锈钢。在设计中应考虑催化剂支撑盘上催化剂和磁球的重量、 催化剂支撑盘本身的重量、床层压力降和操作液重等载荷,经过计算得出 支撑大梁和格栅的结构尺寸。
在催化剂床层上面,采用分配盘是为了均布反应介质,改善其流动状况,实 现与催化剂的良好接触,进而达到径向和轴向的均匀分布。
反应器顶部分配盘
3. 积垢篮
由不同规格的不锈钢金属网和骨架构成的篮框,置于反应器上部催化剂床层的顶 部,可为反应物流提供更大的流通面积,在上部催化剂床层的顶部扑集更多的机 械杂质的沉积物,而又不致引起反应器压力降过快地增长;积垢篮框在反应器内 截面上呈等边三角形均匀排列,其内是空的(不装填催化剂或瓷球),安装好后 要须用不锈钢链将其穿连在一起,并牢固地拴在其上部分配盘地支撑梁上,不锈 钢金属链条要有足够地长度裕量(按床层高度下沉5%考虑),以便能适应催化剂 床层的下沉。
1. 入口扩散器
来自反应器入口的介质首先经过入口扩散器, 在上部锥形体整流后,经上下两挡板的两层 孔的节流、碰撞后被扩散到整个反应器截面 上。 其主要作用为:一是将进入的介质扩散到反 应器的整个截面上;二是消除气、液介质对 顶分配盘的垂直冲击,为分配盘的稳定工作 创造条件;三是通过扰动,促使气液两相混 合
防止氢脆的若干对策 要防止氢脆损伤发生,主要应从结构设计上、制造过程中和生 产操作方面采取如下措施: (1)尽量减少应变幅度,这对于改善使用寿命很有帮助。 (2)尽量保持TP347堆焊金属或焊接金属有较高的延性。为此,一是 要控制TP347中δ—铁素体含量,以避免含量过多时在焊后最终热处理 过程转变成较多的相而产生脆性;二是对于前述那些易发生氢脆的部 位,应尽量省略TP347堆焊金属或焊接金属的焊后最终热处理,以提 高其延性。 (3)装置停工时冷却速度不应过快,且停工过程中应有使钢中吸藏的 氢能尽量释放出去的工艺过程,以减少器壁中的残留氢含量。 (4)尽量避免非计划紧急停工(紧急放空)。