吹塑模具
吹塑模具生产技术要求

吹塑模具生产技术要求
吹塑模具是塑料制品生产中必不可少的工具,它的制造技术要求非常高。
本文将从模具材料、设计要求、加工工艺等方面介绍吹塑模具的生产技术要求。
吹塑模具的材料要求具有一定的硬度和耐磨性。
常见的模具材料有工具钢、合金钢等。
这些材料具有良好的耐磨性和耐腐蚀性,能够在长时间的使用中保持模具的准确度和稳定性。
吹塑模具的设计要求非常重要。
模具设计应根据产品的形状和尺寸来确定,确保产品能够在模具中得到准确的成型。
设计时应考虑产品的收缩率、壁厚均匀性、结构强度等因素,以确保产品的质量和稳定性。
吹塑模具的加工工艺也是关键。
模具加工应采用精密的数控机床进行,以保证模具的精度和表面质量。
加工过程中还需要经过多道工序,如车削、铣削、磨削等,以确保模具的精度和表面光洁度。
吹塑模具生产技术的要求还包括模具的维护和保养。
模具在使用过程中会受到磨损和腐蚀,需要定期进行维修和保养,以延长模具的使用寿命。
维护工作包括清洁模具表面、修复损坏部分、涂覆防锈剂等。
吹塑模具生产技术还需要注意模具的冷却系统。
模具的冷却系统应
设计合理,确保在模具制造过程中能够有效地冷却模具,并在使用过程中能够快速冷却产品,以提高生产效率和产品质量。
吹塑模具生产技术要求非常严格,涉及到材料选择、设计要求、加工工艺等多个方面。
只有按照这些要求进行生产,才能制造出高质量的吹塑模具,满足塑料制品生产的需求。
希望本文的介绍能够对吹塑模具生产技术有所帮助。
多口瓶吹塑模具设计方案
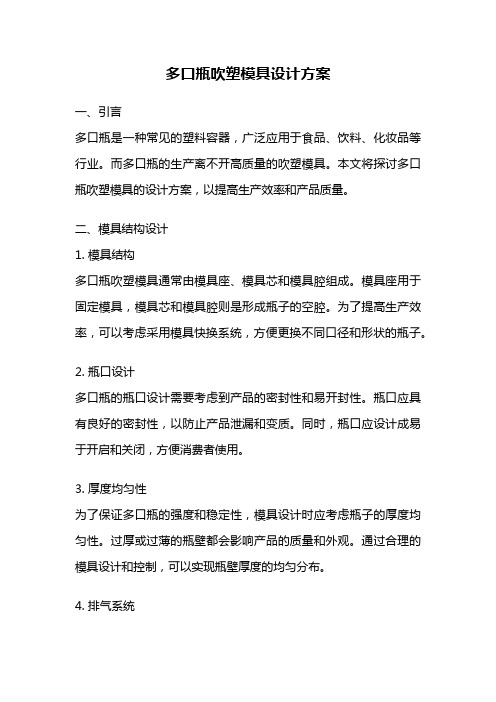
多口瓶吹塑模具设计方案一、引言多口瓶是一种常见的塑料容器,广泛应用于食品、饮料、化妆品等行业。
而多口瓶的生产离不开高质量的吹塑模具。
本文将探讨多口瓶吹塑模具的设计方案,以提高生产效率和产品质量。
二、模具结构设计1. 模具结构多口瓶吹塑模具通常由模具座、模具芯和模具腔组成。
模具座用于固定模具,模具芯和模具腔则是形成瓶子的空腔。
为了提高生产效率,可以考虑采用模具快换系统,方便更换不同口径和形状的瓶子。
2. 瓶口设计多口瓶的瓶口设计需要考虑到产品的密封性和易开封性。
瓶口应具有良好的密封性,以防止产品泄漏和变质。
同时,瓶口应设计成易于开启和关闭,方便消费者使用。
3. 厚度均匀性为了保证多口瓶的强度和稳定性,模具设计时应考虑瓶子的厚度均匀性。
过厚或过薄的瓶壁都会影响产品的质量和外观。
通过合理的模具设计和控制,可以实现瓶壁厚度的均匀分布。
4. 排气系统多口瓶在吹塑过程中,需要通过排气系统排出模具腔内的空气,以避免瓶子出现气泡和瑕疵。
因此,模具设计时应合理设置排气系统,确保充分排出空气,从而得到高质量的产品。
三、材料选择1. 塑料材料多口瓶通常采用聚乙烯(PE)、聚丙烯(PP)等塑料材料制成。
不同的塑料材料具有不同的特性和适用范围,因此在模具设计时需要根据产品的具体要求选择合适的材料。
2. 模具材料多口瓶吹塑模具通常采用优质的耐磨合金钢制成,以保证模具的耐用性和精度。
模具材料的选择应考虑到模具的使用寿命、生产效率和成本等因素,以达到性价比最优化。
四、模具生产工艺1. 模具加工多口瓶吹塑模具的加工需要采用精密的数控机床和先进的加工工艺,以确保模具的精度和质量。
模具加工过程中需要严格控制尺寸和表面光洁度,以满足产品的要求。
2. 热流道系统为了提高多口瓶的生产效率和减少废品率,可以考虑采用热流道系统。
热流道系统可以使塑料材料在模具腔内均匀流动,减少冷料的产生,从而提高产品的质量和产量。
3. 模具调试模具生产完成后,需要进行模具调试。
吹塑模具工作原理

吹塑模具工作原理
吹塑模具是一种特殊的塑料成型工具,它的工作原理是将熔化后的塑料通过压力送入模具中,然后通过模具内部的空气压力将塑料吹制成所需要的形状。
吹塑模具的制作需要使用先进的数控机床和激光成型技术,以保证模具的高精度和高质量。
在模具的设计中,需要考虑到产品的形状、尺寸、厚度、壁厚等因素,以及模具的材质和结构,以确保生产出的塑料制品具有良好的外观和性能。
通常情况下,吹塑模具是由两个模具组成:一个是内模,一个是外模。
在模具关闭后,塑料通过喷嘴进入模具,然后在模具内部被加热软化。
接着,通过加压将空气送入模具内部,使得塑料在模具内部成型。
随着空气的压力不断增加,塑料的形状也随之改变,最终成为所需的产品形状。
吹塑模具广泛应用于各种塑料制品的生产中,包括瓶子、桶子、盆子、玩具等。
它具有生产效率高、成本低、产品质量好等优点,是现代工业生产中不可或缺的一种工具。
- 1 -。
气辅成型模具
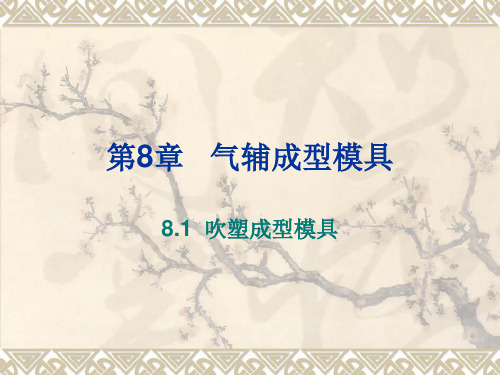
(2)无螺纹瓶颈 不采用螺纹瓶盖的一次性用瓶,多做成无螺纹的瓶 颈。瓶颈嵌件的做法与有螺纹瓶颈基本相同,不过 由于没有螺纹,分型面上的余料痕要求可以放宽。 (3)大口径瓶颈 瓶颈直径与瓶体直径之差很少。这种瓶颈需要和瓶 体同时吹成,在模具上另设吹口板。吹口板到瓶口 的一部分,在开模前被切掉。
瓶底切口设计的适当与否,直接影响到瓶底部的融合质量。 如图8-12(a)切口角度合适,瓶底缝融合良好,图8-12(b)切 口角度不合适,瓶底缝融合不够好。
图8-12 瓶底缝的融合情况
(2)注射吹塑时瓶底的成型
注射吹塑时,瓶坯是由瓶底部进料注射成的。
塑料熔体由瓶坯模的瓶底部注入,在瓶口部 成型螺纹。瓶坯模也是由两个半模合成,其 底部为注射瓶坯时的浇口。有些特殊形状的 瓶底,在做成瓶坯时已经将它预制而成。注 射吹塑的瓶底不存在切除余料问题,所以无 须做出切口。
中空零件以瓶类制品最为典型, 其规格和形状也十分繁多。所以, 本节将以瓶类制品为例,介绍吹 塑成型模具。无论采用何种吹塑 方法,所使用的模具结构均为由 两个半模组成,图8-1为吹塑模 的外观。两个半模各由三部分组 成,即:瓶颈部、瓶体部和瓶底 部,每个半模都有单独的冷却水 通路。
吹塑模具外观
1.瓶颈
吹塑模瓶颈部是与吹管配合的部位,同时又是形成不同形状 瓶颈的部位。瓶颈部的形状依设计方案而异,大致可分为有 螺纹瓶颈与无螺纹瓶颈两类。 (1)有螺纹瓶颈 用于旋上瓶盖的瓶颈。瓶盖可以是塑料的, 也可以是金属的。由于普通螺纹在两半模分开时易产生干涉 现象,损坏螺纹,所以吹塑瓶颈的螺纹设计成特殊截面形状。 塑料瓶螺纹截面形状分为两种。 ①通用螺纹 用于各种塑料瓶口,截面为梯形,螺纹有一圈、 一圈半和两圈三种; ②修正螺纹 用于瓶盖旋紧后有一定内压的瓶口,截面为斜 梯形。 (2)无螺纹瓶颈 用于一次性使用的瓶,瓶口有多种形式。
吹塑模具的基本结构及材料选用
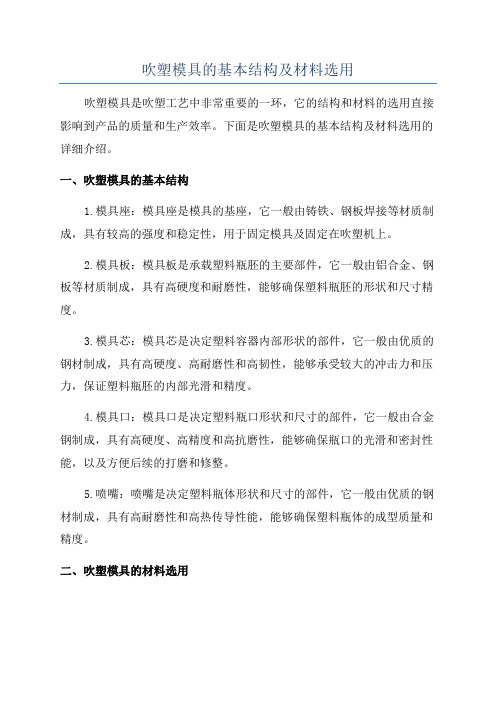
吹塑模具的基本结构及材料选用吹塑模具是吹塑工艺中非常重要的一环,它的结构和材料的选用直接影响到产品的质量和生产效率。
下面是吹塑模具的基本结构及材料选用的详细介绍。
一、吹塑模具的基本结构1.模具座:模具座是模具的基座,它一般由铸铁、钢板焊接等材质制成,具有较高的强度和稳定性,用于固定模具及固定在吹塑机上。
2.模具板:模具板是承载塑料瓶胚的主要部件,它一般由铝合金、钢板等材质制成,具有高硬度和耐磨性,能够确保塑料瓶胚的形状和尺寸精度。
3.模具芯:模具芯是决定塑料容器内部形状的部件,它一般由优质的钢材制成,具有高硬度、高耐磨性和高韧性,能够承受较大的冲击力和压力,保证塑料瓶胚的内部光滑和精度。
4.模具口:模具口是决定塑料瓶口形状和尺寸的部件,它一般由合金钢制成,具有高硬度、高精度和高抗磨性,能够确保瓶口的光滑和密封性能,以及方便后续的打磨和修整。
5.喷嘴:喷嘴是决定塑料瓶体形状和尺寸的部件,它一般由优质的钢材制成,具有高耐磨性和高热传导性能,能够确保塑料瓶体的成型质量和精度。
二、吹塑模具的材料选用1.模具座材料选用:模具座需要具备高强度和稳定性,一般选用铸铁、钢板焊接等材质。
铸铁具有较高的强度和耐腐蚀性,钢板焊接具有较好的稳定性和韧性,能够满足模具固定和吹塑操作的需求。
2.模具板材料选用:模具板需要具备高硬度和耐磨性,一般选用铝合金、钢板等材质。
铝合金具有较高的硬度和轻量化特点,能够减轻模具的重量和提高生产效率;钢板具有较好的稳定性和耐腐蚀性,能够确保塑料瓶胚的形状和尺寸精度。
3.模具芯材料选用:模具芯需要具备高硬度、高耐磨性和高韧性,一般选用优质的钢材。
优质的钢材具有高硬度和优良的耐磨性,能够保证模具芯的使用寿命和塑料瓶胚的内部精度;高韧性能够承受较大的冲击力和压力,确保模具的稳定性和可靠性。
4.模具口材料选用:模具口需要具备高硬度、高精度和高抗磨性,一般选用合金钢。
合金钢具有很高的硬度、高精度和高抗磨性,能够确保瓶口的光滑和密封性能,以及方便后续的打磨和修整。
吹塑模具工作原理
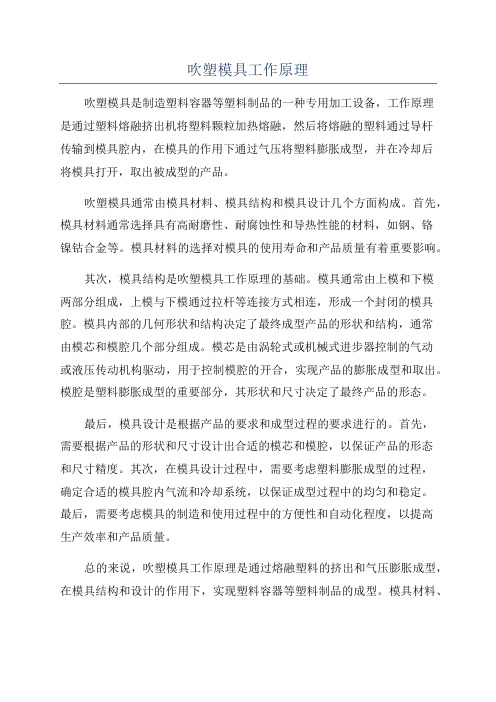
吹塑模具工作原理吹塑模具是制造塑料容器等塑料制品的一种专用加工设备,工作原理是通过塑料熔融挤出机将塑料颗粒加热熔融,然后将熔融的塑料通过导杆传输到模具腔内,在模具的作用下通过气压将塑料膨胀成型,并在冷却后将模具打开,取出被成型的产品。
吹塑模具通常由模具材料、模具结构和模具设计几个方面构成。
首先,模具材料通常选择具有高耐磨性、耐腐蚀性和导热性能的材料,如钢、铬镍钴合金等。
模具材料的选择对模具的使用寿命和产品质量有着重要影响。
其次,模具结构是吹塑模具工作原理的基础。
模具通常由上模和下模两部分组成,上模与下模通过拉杆等连接方式相连,形成一个封闭的模具腔。
模具内部的几何形状和结构决定了最终成型产品的形状和结构,通常由模芯和模腔几个部分组成。
模芯是由涡轮式或机械式进步器控制的气动或液压传动机构驱动,用于控制模腔的开合,实现产品的膨胀成型和取出。
模腔是塑料膨胀成型的重要部分,其形状和尺寸决定了最终产品的形态。
最后,模具设计是根据产品的要求和成型过程的要求进行的。
首先,需要根据产品的形状和尺寸设计出合适的模芯和模腔,以保证产品的形态和尺寸精度。
其次,在模具设计过程中,需要考虑塑料膨胀成型的过程,确定合适的模具腔内气流和冷却系统,以保证成型过程中的均匀和稳定。
最后,需要考虑模具的制造和使用过程中的方便性和自动化程度,以提高生产效率和产品质量。
总的来说,吹塑模具工作原理是通过熔融塑料的挤出和气压膨胀成型,在模具结构和设计的作用下,实现塑料容器等塑料制品的成型。
模具材料、模具结构和模具设计是影响吹塑模具工作原理的重要因素,合理的选择和设计可以提高成型效率和产品质量。
吹塑模具工作原理
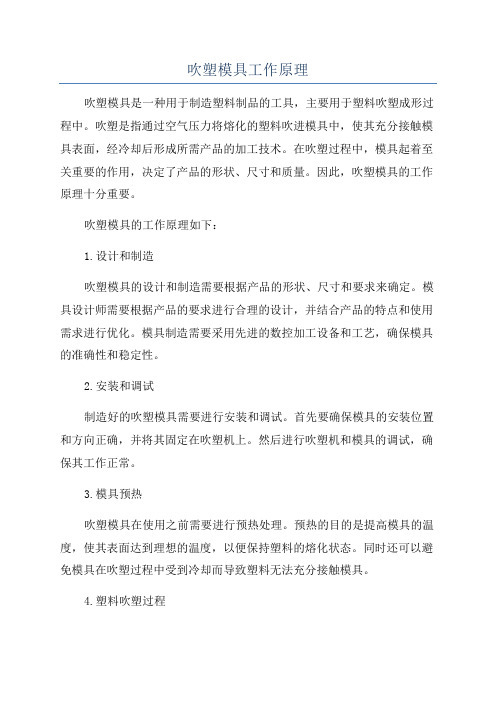
吹塑模具工作原理吹塑模具是一种用于制造塑料制品的工具,主要用于塑料吹塑成形过程中。
吹塑是指通过空气压力将熔化的塑料吹进模具中,使其充分接触模具表面,经冷却后形成所需产品的加工技术。
在吹塑过程中,模具起着至关重要的作用,决定了产品的形状、尺寸和质量。
因此,吹塑模具的工作原理十分重要。
吹塑模具的工作原理如下:1.设计和制造吹塑模具的设计和制造需要根据产品的形状、尺寸和要求来确定。
模具设计师需要根据产品的要求进行合理的设计,并结合产品的特点和使用需求进行优化。
模具制造需要采用先进的数控加工设备和工艺,确保模具的准确性和稳定性。
2.安装和调试制造好的吹塑模具需要进行安装和调试。
首先要确保模具的安装位置和方向正确,并将其固定在吹塑机上。
然后进行吹塑机和模具的调试,确保其工作正常。
3.模具预热吹塑模具在使用之前需要进行预热处理。
预热的目的是提高模具的温度,使其表面达到理想的温度,以便保持塑料的熔化状态。
同时还可以避免模具在吹塑过程中受到冷却而导致塑料无法充分接触模具。
4.塑料吹塑过程当模具预热达到一定温度后,将熔化的塑料注入吹塑机的储料筒中。
随着储料筒内压力的增加,塑料被推送到吹塑机的机筒中。
然后,通过螺杆的旋转和推动,将熔化的塑料送入模具的腔室中。
5.模具闭合和成形当熔化的塑料进入到模具腔室中后,模具开始闭合。
模具的闭合有两个作用,一是将塑料固定在模具中,避免其流动或拉伸;二是模具的闭合可以通过一定的空气压力将塑料与模具接触紧密,以形成产品的形状和尺寸。
6.模具冷却和脱模在塑料进入模具之后,模具需要进行一段时间的冷却,使塑料变硬并保持固态。
冷却时间的长短取决于塑料的种类和产品的尺寸。
当塑料冷却完成后,模具开始脱模。
这时,模具开启,将成品从模具中取出。
7.清洁和维护吹塑模具使用完毕之后,需要进行清洁和维护。
首先要彻底清洁模具的腔室和表面,保持其干净。
然后进行模具的维护,检查和修复可能存在的损坏或磨损。
这样可以延长模具的使用寿命和保证产品的质量。
吹塑机模具的用途

吹塑模具是一种用于制造塑料制品的工具,主要用于塑料成型工艺中的吹塑工艺。
该工艺通过在闭合的模具内吹入压缩空气,使材料向四周扩散,从而紧贴模具内壁形成中空状态。
具体来说,吹塑模具可以用于生产各种中空容器,如瓶子、罐子、桶等,以及套管部件,如电视外壳、冰箱外壳等。
此外,吹塑模具还可以应用于食品、化妆品和医疗等行业,用于生产食品包装瓶、塑料杯、化妆品瓶、盖子、药品瓶和口腔水杯等。
吹塑模具的出现不仅提高了塑料制品的生产效率,同时也提高了产品的质量。
其制作过程涉及计算机辅助设计、数控机床加工、雕铣、线切割、电火花等技术,保证了模具的尺寸精度和表面质量,从而确保了塑料制品的一次成型效果。
吹塑模具一般由一对模具组成,有上下两个部分,上下模具通过压力形成成型腔。
根据制品形状和生产工艺的不同,吹塑模具可以分为不同的类型,如中空容器吹塑模具和套管吹塑模具等。
同时,吹塑模具材料的选择也非常重要,一般采用耐磨、耐腐蚀的工具钢。
总的来说,吹塑模具是塑料加工行业中不可或缺的重要工具,其应用范围广泛,对于提高塑料制品的生产效率和产品质量具有重要意义。
吹塑模具设计要点概要

吹塑模具设计要点概要1.产品设计要点:在进行吹塑模具设计之前,首先需要对要生产的产品进行深入的分析和了解。
包括产品的形状、尺寸、容量、材质等要求。
这些数据将直接影响到模具的设计和制造。
2.模具结构设计要点:吹塑模具通常由芯棒、冷却系统、分模系统和出料系统等部分组成。
在进行模具结构设计时,需要考虑产品的形状和尺寸,并选择合适的结构形式。
如常用的两片式模具、多片式模具、套筒模具等。
3.材料选用要点:吹塑模具通常采用优质合金钢或特殊材料制造,以保证模具的耐磨性、强度和使用寿命。
在选择材料时,需要考虑模具的工作环境和要求,选择合适的材料,同时还需要考虑材料的可加工性和成本。
4.出料系统设计要点:吹塑模具的出料系统用于将熔融的塑料注入模具中,同时将成型品取出。
在出料系统设计时,需要考虑塑料的流动性、冷却性和断面均匀性等因素,以保证产品的质量和生产的效率。
5.冷却系统设计要点:吹塑模具在生产过程中需要进行冷却,以便塑料快速凝固并保持形状。
在冷却系统设计时,需要考虑到产品的不同部位的冷却速度不同,需合理安排冷却系统的布局和设计冷却水路。
6.模具加工要点:吹塑模具的制造需要经过多道工序,包括车床加工、铣床加工、电火花加工、线切割加工等。
在进行模具加工时,需要保证加工工艺和精度,尤其是对于塑件的尺寸和表面光洁度要求较高的模具。
吹塑模具设计的要点总结如上,不同类型的吹塑模具在设计和制造时会有一些特定的要求和注意事项,根据实际情况进行具体的分析和设计。
模具设计师需要熟悉吹塑工艺的原理和要求,结合实际的生产情况,进行综合考虑和优化设计,以提高模具的质量和生产效率。
吹塑模具点检表内容包括
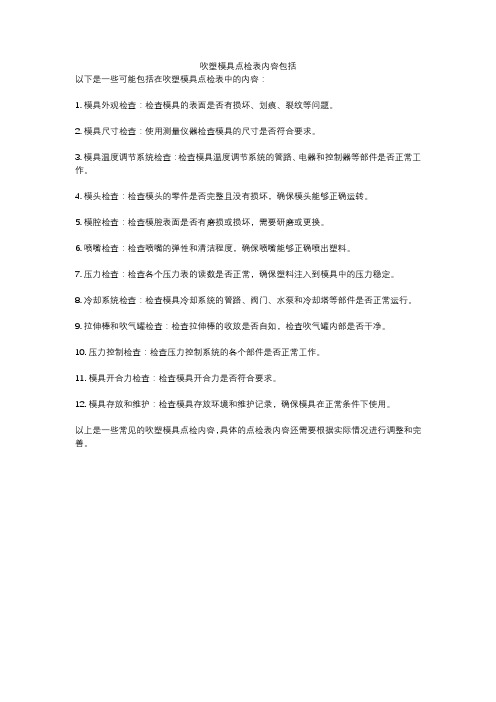
吹塑模具点检表内容包括
以下是一些可能包括在吹塑模具点检表中的内容:
1. 模具外观检查:检查模具的表面是否有损坏、划痕、裂纹等问题。
2. 模具尺寸检查:使用测量仪器检查模具的尺寸是否符合要求。
3. 模具温度调节系统检查:检查模具温度调节系统的管路、电器和控制器等部件是否正常工作。
4. 模头检查:检查模头的零件是否完整且没有损坏,确保模头能够正确运转。
5. 模腔检查:检查模腔表面是否有磨损或损坏,需要研磨或更换。
6. 喷嘴检查:检查喷嘴的弹性和清洁程度,确保喷嘴能够正确喷出塑料。
7. 压力检查:检查各个压力表的读数是否正常,确保塑料注入到模具中的压力稳定。
8. 冷却系统检查:检查模具冷却系统的管路、阀门、水泵和冷却塔等部件是否正常运行。
9. 拉伸棒和吹气罐检查:检查拉伸棒的收放是否自如,检查吹气罐内部是否干净。
10. 压力控制检查:检查压力控制系统的各个部件是否正常工作。
11. 模具开合力检查:检查模具开合力是否符合要求。
12. 模具存放和维护:检查模具存放环境和维护记录,确保模具在正常条件下使用。
以上是一些常见的吹塑模具点检内容,具体的点检表内容还需要根据实际情况进行调整和完善。
塑料吹塑模具操作流程
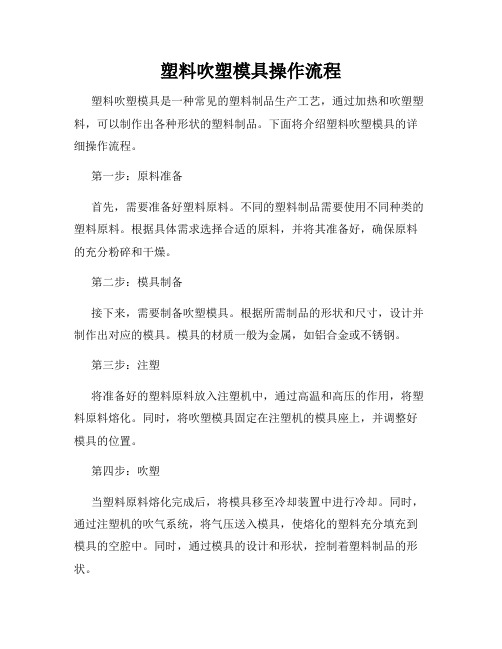
塑料吹塑模具操作流程塑料吹塑模具是一种常见的塑料制品生产工艺,通过加热和吹塑塑料,可以制作出各种形状的塑料制品。
下面将介绍塑料吹塑模具的详细操作流程。
第一步:原料准备首先,需要准备好塑料原料。
不同的塑料制品需要使用不同种类的塑料原料。
根据具体需求选择合适的原料,并将其准备好,确保原料的充分粉碎和干燥。
第二步:模具制备接下来,需要制备吹塑模具。
根据所需制品的形状和尺寸,设计并制作出对应的模具。
模具的材质一般为金属,如铝合金或不锈钢。
第三步:注塑将准备好的塑料原料放入注塑机中,通过高温和高压的作用,将塑料原料熔化。
同时,将吹塑模具固定在注塑机的模具座上,并调整好模具的位置。
第四步:吹塑当塑料原料熔化完成后,将模具移至冷却装置中进行冷却。
同时,通过注塑机的吹气系统,将气压送入模具,使熔化的塑料充分填充到模具的空腔中。
同时,通过模具的设计和形状,控制着塑料制品的形状。
第五步:冷却和固化在塑料填充完成后,模具中的塑料开始冷却和固化。
冷却时间的长短取决于塑料的种类和制品的尺寸。
一般情况下,需要等待一段时间,确保塑料完全冷却和固化。
第六步:模具取出当塑料充分冷却和固化后,将模具从注塑机中取出。
通常需要使用专业工具将模具和塑料制品分开,确保模具的完整性和塑料制品的完美。
第七步:修整和检验将取出的塑料制品进行修整和检验。
通过去除多余的边角和毛刺,使塑料制品的外观更加美观。
同时,进行质量检验,确保制品达到要求的标准。
第八步:包装修整和检验完成后,将塑料制品进行包装。
根据实际情况选择合适的包装材料和方式,以确保制品在运输和储存过程中不受损坏。
通过以上的操作流程,塑料吹塑模具制品完成了从原料准备到包装的全过程。
这一流程中需要严格控制每一步的操作,确保制品的质量和形状满足要求。
塑料吹塑模具的应用非常广泛,包括食品包装容器、日用品、工业零件等。
随着科技的不断进步,塑料吹塑模具的工艺和设备也在不断更新,使得制品的质量和效率得到了进一步的提高。
注塑和吹瓶模具基础知识
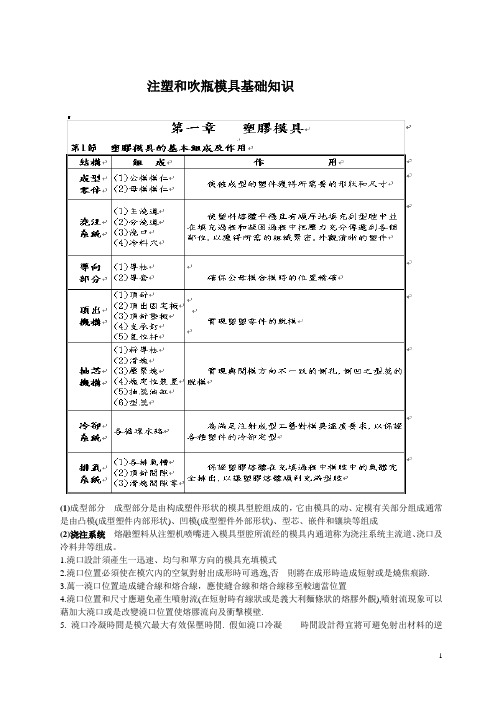
注塑和吹瓶模具基础知识(1)成型部分成型部分是由构成塑件形状的模具型腔组成的,它由模具的动、定模有关部分组成通常是由凸模(成型塑件内部形状)、凹模(成型塑件外部形状)、型芯、嵌件和镶块等组成(2)浇注系统熔融塑料从注塑机喷嘴进入模具型腔所流经的模具内通道称为浇注系统主流道、浇口及冷料井等组成。
1.澆口設計須產生一迅速、均勻和單方向的模具充填模式2.澆口位置必須使在模穴內的空氣對射出成形時可逃逸,否則將在成形時造成短射或是燒焦痕跡.3.萬一澆口位置造成縫合線和熔合線,應使縫合線和熔合線移至較適當位置4.澆口位置和尺寸應避免產生噴射流(在短射時有線狀或是義大利麵條狀的熔膠外觀),噴射流現象可以藉加大澆口或是改變澆口位置使熔膠流向及衝擊模壁.5. 澆口冷凝時間是模穴最大有效保壓時間. 假如澆口冷凝時間設計得宜將可避免射出材料的逆6.澆口位置應置於成形品最厚的區域, 最好是在不影響模製品的功能和外觀之處.(3)导向定位机构为了确保动、定模之间的正确导向与定位,通常在动、定模部分采用导柱、导套或在动、定模部分设置互相吻合(4.1)侧向抽芯旋转机构塑件上的侧向如有凹、凸形状的孔或凸台,这就需要有侧向的凹、凸模或型芯来成型。
在塑件被推出之前,必须先拔出侧向凸模或抽出侧向型芯,然后方能顺利脱出。
使侧向凸模或侧向型芯移动的机构称为侧向抽芯机构。
(5.2)顶出机构顶出机构是指模具分型以后将塑件顶出的装置(又称脱模机构)杆、复位杆、顶杆固定扳、顶板、主流道拉料杆等组成。
(6)冷却加热系统(温控) 1.提高生產力. 2.保証一幅模具的有效利用在熱塑性塑膠射出成型的周期中,模具的冷卻時間占整個周期的三分之二以上.有效的冷卻迴路設計可減少冷卻時間,因而增加總生產量;再者,均勻的冷卻可降低因熱傳不均而產生的殘余應力.從而控制成品翹曲,以維持成形品尺寸的精準度和穩定性,進而改善產品的品質.为了使熔融塑料在模具型腔内尽快固化成型,提高生产效率,一些塑料成型时必须对模具进行冷却,通常是在模具上开设冷却水道,当塑料充满型腔并经一定的保压时间后,水道通以循环冷水对模具进行冷却。
吹塑模具工作原理

吹塑模具工作原理吹塑模具是一种用于塑料制品生产的专用模具,它是塑料制品加工中不可或缺的工具之一、吹塑模具的工作原理是通过将加热软化的塑料吹入模具腔体,并通过压缩空气的作用使塑料在模具空腔中迅速冷却成型,最终得到所需的塑料制品。
下面将详细阐述吹塑模具的工作原理。
首先,吹塑模具由模具上、下两个部分组成。
上模具和下模具之间有一个模具腔体,模具腔体的形状和尺寸决定了最终塑料制品的形状和尺寸。
上模具上有一个供塑料进料的喷嘴,下模具上有一个供模具腔体排气的出气口。
模具腔体是由上模具和下模具闭合时形成的,它是塑料制品的外形。
接下来,选择适当的塑料料粒加热至软化点,通常采用的加热方式有热疑炉加热、电加热和红外线加热三种。
加热后的塑料料粒塞进模具的喷嘴中,通过挤压机或搅拌器将塑料料粒塞进模具。
然后,模具上下两个部分闭合,形成模具腔体。
此时,上模具的喷嘴与下模具的出气口相对应,通过模具的喷嘴进气口,将压缩空气注入模具腔体。
压缩空气的作用有两个方面:首先,它使塑料在模具腔体中均匀地贴附于模具腔体壁面,并且充满整个模具腔体;其次,压缩空气的注入也使塑料快速冷却,使其获得所需的形状。
随着模具腔体中的塑料冷却固化,模具腔体逐渐打开,模具上下两个部分分离。
此时,塑料制品与模具腔体分离,进一步加工处理即可得到最终所需的塑料制品。
需要指出的是,吹塑模具的具体工作原理根据不同的产品而有所差异,例如注塑家具、注塑日用品等。
不同的产品对吹塑模具的形状、尺寸、材料等都有不同的要求,因此吹塑模具的工作原理也会有所不同。
吹塑模具工作原理的关键是通过加热软化的塑料吹入模具腔体,并通过压缩空气的作用使塑料在模具空腔中迅速冷却成型。
通过不断改进和完善吹塑模具的设计和制造工艺,可以生产出更加复杂、精确的塑料制品,满足不同行业和领域的需求。
吹塑机模具材料的选择和性能比较

吹塑机模具材料的选择和性能比较吹塑机模具是一种专门用于吹塑加工的工具,其质量和性能直接影响到吹塑产品的成型效果和质量。
在选择和使用吹塑机模具时,合理的材料选择是十分重要的。
本文将就吹塑机模具材料的选择和性能进行比较,帮助读者更好地理解和应用吹塑机模具。
一、吹塑机模具材料的选择1. 钢材钢材是一种常见的吹塑机模具材料,具有耐磨、耐腐蚀、高强度等优点。
常用的钢材有45#钢、P20钢等。
45#钢具有较好的强度和硬度,适用于一般吹塑产品的模具制作。
P20钢具有优良的耐磨性和硬度,适用于高要求的吹塑产品的模具制作。
钢材模具的制作成本较低,使用寿命较长,但相对较重。
2. 铝合金铝合金是一种轻质、高强度的吹塑机模具材料。
常用的铝合金有6061铝合金、7075铝合金等。
铝合金制作的模具具有较好的导热性能,利于产品的冷却和加工速度的提高。
此外,铝合金材料还具有良好的韧性和耐腐蚀性能,适用于一些特殊要求的吹塑产品。
然而,铝合金材料相对较软,容易受到机械冲击和磨损。
3. 聚合物材料聚合物材料是近年来出现的一种新型吹塑机模具材料。
具有重量轻、易加工、耐磨性良好等特点。
常用的聚合物材料有聚丙烯、聚碳酸酯等。
聚合物材料制作的模具不仅具有良好的耐磨性,还具有较高的耐腐蚀性能,能够更好地适应复杂的吹塑产品需求。
然而,聚合物材料相对较软,容易形成划痕和变形。
二、吹塑机模具材料性能比较1. 强度和硬度钢材具有较高的强度和硬度,能够承受较大的机械冲击和压力。
而铝合金材料的强度和硬度相对较低,不适用于承受较大压力的吹塑加工。
聚合物材料的强度和硬度也较低,容易受到机械冲击和磨损。
2. 耐磨性钢材和聚合物材料具有较好的耐磨性,能够在长时间的吹塑加工中保持较好的表面质量。
铝合金材料的耐磨性相对较差,容易发生磨损和划痕。
3. 导热性能铝合金材料具有较好的导热性能,能够更快地冷却吹塑产品,提高加工速度和效率。
而钢材和聚合物材料的导热性能相对较差,冷却速度较慢。
塑料吹塑模具操作流程

塑料吹塑模具操作流程塑料吹塑是一种常见的塑料加工方法,通过模具在加热软化的塑料管材上施加气压,使其膨胀成型。
在进行塑料吹塑加工时,正确的操作流程对于产品质量和生产效率至关重要。
下面将详细介绍塑料吹塑模具的操作流程。
1. 设计模具与准备材料在进行塑料吹塑加工之前,首先需要设计并准备好合适的吹塑模具。
吹塑模具根据产品的形状和尺寸来设计,需要保证模具表面光滑,尺寸准确。
同时,还需准备好合适的塑料原料,确保材料质量符合要求。
2. 加热塑料管材将准备好的塑料管材放入吹塑机中进行加热。
加热的温度和时间需要根据塑料的类型和厚度来确定,确保塑料可以达到软化状态,便于塑料在模具中膨胀成型。
3. 模具装配与调整将设计好的吹塑模具进行装配,并根据产品要求进行调整。
确保模具之间的间隙合适,避免产品出现变形或瑕疵。
同时,还需调整模具温度和气压等参数,确保产品膨胀成型的质量和效率。
4. 开始吹塑生产当塑料管材达到软化状态并完成模具调整后,开始施加气压进入模具进行吹塑成型。
此时需要确保气压的均匀施加,以避免产品出现厚薄不均或气泡等质量问题。
同时,还需控制好吹塑的速度和时间,确保产品尺寸和形状的准确度。
5. 取出成品与检验当吹塑过程完成后,将成型的产品从模具中取出。
对产品进行外观检查,确保表面光滑,尺寸符合要求。
同时还需进行物理性能测试,如拉伸强度、耐磨性等,确保产品质量达标。
6. 包装与入库最后,对合格的产品进行包装并入库。
包装要求根据产品的特性来确定,确保产品在运输和储存过程中不受损坏。
同时,还需做好产品信息记录,方便追溯和管理。
通过以上的操作流程,可以保证塑料吹塑模具在生产过程中的质量和效率。
正确的操作流程不仅能够提高产品质量,还能够提升生产效率,为企业带来更多的经济效益。
因此,在进行塑料吹塑加工时,务必按照规范的操作流程进行操作,做好每个环节的控制和调整,确保产品达到最佳效果。
吹塑模具结构特点与基本结构(新).

主讲人:何 亮
广东轻工职业技术学院高分子教研室 广东高校高分子材料加工工程二.中空吹塑模具的基本结构
中空吹塑成型模具实体
中空吹塑成型模具实体
200LB双L环闭口桶模具
160升直口蓝桶模具
一、中空吹塑成型模具特点
吹塑模的特点:
(1)一般只有阴模; (2)没有浇注系统和顶出系统 (2)型腔受到的吹胀压力很低,一
般为0.2~1.0MPa;
(3)一般型腔表面不需经硬化处理; (4)模腔的磨损较低; (5)吹塑制品上即使有较深的凹型,
一般不要滑动嵌块也能脱模。
二.中空吹塑模具的基本结构
挤出吹塑模具的结构 1,2—动模 3—水管接头 4—上刃口
5—余料槽 6—下刃口 7—导柱 8—螺钉
二.中空吹塑模具的基本结构
瓶颈部
瓶体部
瓶底部
二.中空吹塑模具的基本结构
上余料切刀 下余料切刀
谢
谢!
挤出吹塑模具工艺流程【步骤】

一般的,硅含量高的铝合金最适于铸造,而高强度的铝合金不能铸造,要用机械加工方法。
铜铍合金模具有较好的性能。
钢模具多数用机械加工制造,锌合金则易于铸造。
若型腔数量较多、型腔复杂或不规则、型腔尺寸公差要求较低、型腔容积较大或生产批量较少,可采用铸造法来制造模具。
铸造模具的成本较低,但耐用性、导热性能要比机械加工模具的低。
采用某些特种铸造法可制造高性能的模具,例如压力铸造法可以减小铝与铜铍合金的多孔性,保证型腔有较高的精度。
吹塑模具型腔的机械加工方法主要有铣削、磨削等。
模腔的制造方法还有冷挤压、热挤压、电火花加工与焊接。
其中冷挤压法适于小型模具,尤其是多型腔模具,以确保各型腔的一致性。
对大容积(例如3m。
)模腔,可采用机械加工结合焊接方法来制造。
要求吹塑制品有高的尺寸精度时,要采用仿形铣削的方法来制造模腔。
设计模腔尺寸时要考虑收缩率。
对机械加工型腔,收缩率包括吹塑制品的收缩率与模具后加工出现的收缩率;对铸造型腔,还要考虑模具材料铸造过程中的收缩率。
模腔制造的最后阶段为抛光、喷砂或蚀刻。
蚀刻前,尤其在需要蚀刻精细花纹图案时,要去除切削、电火花加工、研磨或挤压加工产生的鳞屑和痕迹,保证有一定的光洁度。
除非生产批量很大时,模腔一般不需经硬化处理,也很少镀覆金属(如镀铬)。
若型腔要经硬化处理或镀铬,应在蚀刻后进行。
夹坯嵌块、拉杆、导柱与导套等多数用钢或铜铍合金通过机械加工制造,还要经硬化处理。
如何确定注射吹塑模具中的模腔数目
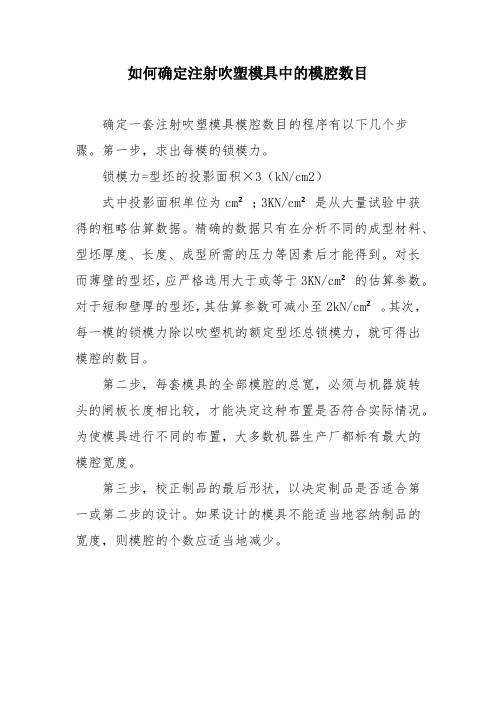
如何确定注射吹塑模具中的模腔数目
确定一套注射吹塑模具模腔数目的程序有以下几个步骤。
第一步,求出每模的锁模力。
锁模力=型坯的投影面积×3(kN/cm2)
式中投影面积单位为cm²;3KN/cm²是从大量试验中获得的粗略估算数据。
精确的数据只有在分析不同的成型材料、型坯厚度、长度、成型所需的压力等因素后才能得到。
对长而薄壁的型坯,应严格选用大于或等于3KN/cm²的估算参数。
对于短和壁厚的型坯,其估算参数可减小至2kN/cm²。
其次,每一模的锁模力除以吹塑机的额定型坯总锁模力,就可得出模腔的数目。
第二步,每套模具的全部模腔的总宽,必须与机器旋转头的闸板长度相比较,才能决定这种布置是否符合实际情况。
为使模具进行不同的布置,大多数机器生产厂都标有最大的模腔宽度。
第三步,校正制品的最后形状,以决定制品是否适合第一或第二步的设计。
如果设计的模具不能适当地容纳制品的宽度,则模腔的个数应适当地减少。
吹塑铝合金模具设计与制造

吹塑铝合金模具设计与制造以吹塑铝合金模具设计与制造为题,本文将从模具设计和制造的角度介绍吹塑铝合金模具的相关知识。
一、吹塑铝合金模具的概述吹塑铝合金模具是一种用于吹塑成型的模具,它采用铝合金材料制造而成。
吹塑成型是一种常见的塑料加工方法,通过将熔化的塑料注入到模具中,经过冷却和固化后得到所需的塑料制品。
铝合金模具由于其优良的导热性能和较低的成本,成为吹塑模具制造中的重要选择。
二、吹塑铝合金模具的设计1. 模具结构设计吹塑铝合金模具的结构设计应考虑到产品的形状、尺寸和生产要求。
模具结构通常包括模具座、模具芯、模具腔等部分,其中模具芯和模具腔是形成产品形状的关键部分。
设计时需要考虑产品的收缩率、壁厚、表面光洁度等因素,确保最终产品的质量。
2. 模具材料选择吹塑铝合金模具的材料选择主要考虑到其导热性能和机械性能。
铝合金具有良好的导热性能,能够快速散热,提高模具的生产效率。
同时,铝合金还具有较高的强度和硬度,能够满足模具在生产过程中的工作要求。
3. 模具制造工艺吹塑铝合金模具的制造工艺主要包括模具结构加工、表面处理和装配等环节。
模具结构加工包括数控加工、线切割、铣削等,通过这些工艺将模具的结构加工成所需的形状。
表面处理则是为了提高模具的耐磨性和防腐性,常见的表面处理方法包括阳极氧化、喷砂、电镀等。
最后,将各个部件装配到一起,确保模具的完整性和可靠性。
三、吹塑铝合金模具的制造1. 设计验证在制造吹塑铝合金模具之前,需要进行设计验证,确保模具的设计符合产品要求。
通过计算和模拟分析,验证模具的结构和尺寸是否满足产品的要求,避免因设计错误导致的生产问题。
2. 材料准备吹塑铝合金模具的制造需要准备相应的铝合金材料。
选择合适的铝合金材料,根据模具的尺寸和形状进行切割和加工,确保材料符合设计要求。
3. 模具制造模具制造包括模具结构加工、表面处理和装配等环节。
根据设计要求,通过数控加工、线切割、铣削等工艺将模具的结构加工成所需形状。
吹塑的模具常识
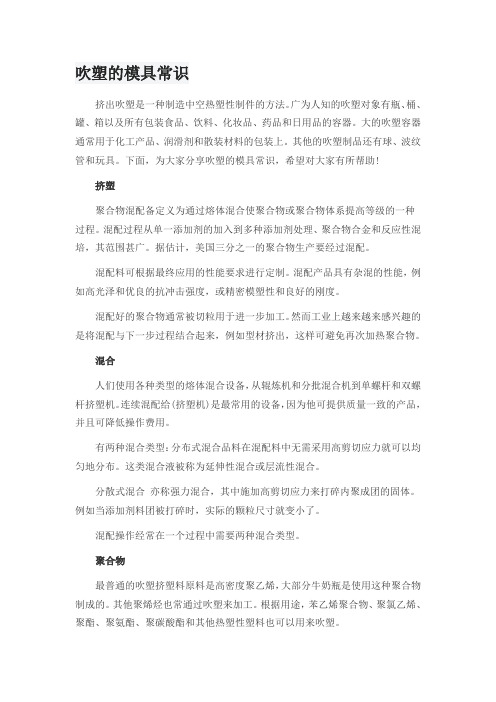
吹塑的模具常识挤出吹塑是一种制造中空热塑性制件的方法。
广为人知的吹塑对象有瓶、桶、罐、箱以及所有包装食品、饮料、化妆品、药品和日用品的容器。
大的吹塑容器通常用于化工产品、润滑剂和散装材料的包装上。
其他的吹塑制品还有球、波纹管和玩具。
下面,为大家分享吹塑的模具常识,希望对大家有所帮助!挤塑聚合物混配备定义为通过熔体混合使聚合物或聚合物体系提高等级的一种过程。
混配过程从单一添加剂的加入到多种添加剂处理、聚合物合金和反应性混培,其范围甚广。
据估计,美国三分之一的聚合物生产要经过混配。
混配料可根据最终应用的性能要求进行定制。
混配产品具有杂混的性能,例如高光泽和优良的抗冲击强度,或精密模塑性和良好的刚度。
混配好的聚合物通常被切粒用于进一步加工。
然而工业上越来越来感兴趣的是将混配与下一步过程结合起来,例如型材挤出,这样可避免再次加热聚合物。
混合人们使用各种类型的熔体混合设备,从辊炼机和分批混合机到单螺杆和双螺杆挤塑机。
连续混配给(挤塑机)是最常用的设备,因为他可提供质量一致的产品,并且可降低操作费用。
有两种混合类型:分布式混合品料在混配料中无需采用高剪切应力就可以均匀地分布。
这类混合液被称为延伸性混合或层流性混合。
分散式混合亦称强力混合,其中施加高剪切应力来打碎内聚成团的固体。
例如当添加剂料团被打碎时,实际的颗粒尺寸就变小了。
混配操作经常在一个过程中需要两种混合类型。
聚合物最普通的吹塑挤塑料原料是高密度聚乙烯,大部分牛奶瓶是使用这种聚合物制成的。
其他聚烯烃也常通过吹塑来加工。
根据用途,苯乙烯聚合物、聚氯乙烯、聚酯、聚氨酯、聚碳酸酯和其他热塑性塑料也可以用来吹塑。
最近工程塑料在汽车行业被广泛接受。
材料选择是以机械强度、耐候性、电学性能、光学性能和其他性能为依据的.。
工艺3/4的吹塑制品是由挤出吹塑法制造的。
挤出工艺是强迫物料通过一个孔或模具来制造产品。
挤出吹塑工艺由5步组成:1.塑料型胚(中空塑料管的挤出);2.在型胚上将瓣合模具闭合,夹紧模具并切断型胚;3.向模腔的冷壁吹胀型培,调整开口并在冷却期间保持一定的压力;4.打开模具,卸下被吹的零件;5.修整飞边得到成品。
- 1、下载文档前请自行甄别文档内容的完整性,平台不提供额外的编辑、内容补充、找答案等附加服务。
- 2、"仅部分预览"的文档,不可在线预览部分如存在完整性等问题,可反馈申请退款(可完整预览的文档不适用该条件!)。
- 3、如文档侵犯您的权益,请联系客服反馈,我们会尽快为您处理(人工客服工作时间:9:00-18:30)。
1吹塑模具自动设计系统的研究
抽象的说,设计吹塑模具是一个非常复杂且需要知识量大的过程。
本文介绍了一种基于特征、参数和智能设计系统,用这个系统制作吹塑模具,在完成注塑,吹塑和排出模具之前只需要设置一个最小参数集。
这个吹塑模具设计系统装备有顶级的CAD,由一台机器,腔设置模块、注射设计系统、吹塑设计系统、喷射设计系统、模具设计制作模块、成型数据库和机器的数据库所组成。
通过这些模块,模具设计师能够按照客户的要求创建出一个3D的吹塑模具的设计。
吹塑模具设计主要有注塑、吹塑、推出三个阶段,这个系统不仅能降低吹塑模具的设计时间,还可在通过标准化设计过程中大大提高产品质量。
简介
吹塑成型是世界第三大塑料加工技术,广泛用于生产材料为热塑性塑料的中空薄壁物体。
在过去的20多年来,吹塑成型经历了快速发展,已经被汽车、体育休闲、电子产品、办公用品、自动化设备,包装业等领域所应用。
一般来说,吹塑成型有两种主要类型:挤出吹塑成型和拉伸吹塑成型。
前者广泛用于生产各种尺寸和形状的容器、也适用于生产不规则复杂的中空部件,供给汽车、办公自动化设备,医药业和旅游业等领域。
后者广泛应用于生产商业用塑料瓶,适用于食品、饮料、制药工业等领域。
吹塑产品的设计,加工、注射过程和设计吹塑模具是吹塑产品开发的重要阶段,除了模具结构的高度复杂外,各种设计参数的干扰也使得设计任务非常困难。
因此,大多数人仍然相信。
这一工艺在模具设计中具有举足轻重的作用。
一般来说,要成为一个模具设计专家需要花更多的时间的努力。
在竞争激烈的环境下,我们要在设计模具时,努力减少成本并提高产品质量。
因此,利用计算机辅助设计(CAD)已经成为一个最重要的途经来提高生产力。
然而设计吹塑模具二维设计系统存在许多问题,如下所示:
1尺寸和配置图理解困难
2检查干扰困难
3完成客户需要的注射器的规格困难
4吹塑模具无法完成智能工作
5无法计算产品的重量
6出现不必要的且简单重复的工作
7模具的规范在制作时难以控制
8重绘困难
这些二维设计系统的弊端使他们要花很长时间来学习和使用,最后,这些问题会影响产品的交货,最终导致产品质量的下降为了保持竞争优势,模具制造公司通过三维计算机辅助设计系统缩短设计和制造周期,提高产品质量。
3D计算机辅助设计系统通过解决2D设计系统的问题,采用直观和具体的方法把对象表达给用户。
然而,大多数的三维CAD软件只提供简单的几何模型功能,不能向用户提供充分的设计知识,因此设计自动化,智能化系统长期以来一直是一个积极孤研究课题。
许多研究已应用这类系统设计模具(表一)但还没有开发出用于吹塑模具设计的系统。
为了完成吹塑模具设计过程中运用的科学方法,本文介绍了一种基于特征,参数和智能设计系统用于设计吹塑模具。
设计者只需要输入最小的设计参数,系统会自动完成设计注射部分、吹塑部分和喷射部分吹塑模具。
此外,吹塑模具制造系统在这项研究中保证当设计师修改模具设计时,这些变化可以很容易地进行。
开发该系统是利用Powershape7.0平台上的Visual Basic语言。