自卸车T式举升机构的设计
T型举升机构的设计和计算软件开发

T型举升机构的设计和计算软件开发作者:张建平俞东海王德松来源:《专用汽车》 2010年第4期张建平俞东海王德松陕汽集团宝鸡华山工程车辆有限公司陕西宝鸡721013摘要:介绍了T式举升机构的设计方法,通过对机构的分析,建立了举升机构的数学模型,在总结多年实践经验的基础上,运用计算机语言开发了一套专门用于T式自卸举升机构设计计算的辅助软件。
本软件能快速计算出自卸举升机构各铰点在不同的举升角度下的坐标、受力大小及方向,并可运用EXCEL电子表格生成各点受力曲线和举升机构的总体参数。
关键词:自卸车举升机构设计计算软件开发Abstract This article describes the design method of lifting mechanism of T-type dump truck, a mathematical model of lifting mechanism was established through the mechanism analysis. Based on years of practical experience, using a set of supporting software of design and calculation of lifting mechanism of T-type dump truck which developed from computer language. Coordinates, size and direction of the force on each hinge joint in the different angles can be quickly calculated. By using EXCEL, the barrier force of each point and the overall parameters of lifting mechanism were concluded.Key words dump truck; lifting mechanism; design and calculation; software development中图分类号: U463.92.02文献标识码:A论文编号:1004-0226(2010)04-0057-031 前言举升机构是自卸汽车的关键装置,机构各点布置是否合理,直接影响自卸车的性能及整车布置。
自卸汽车举升机构的机械及液压系统设计
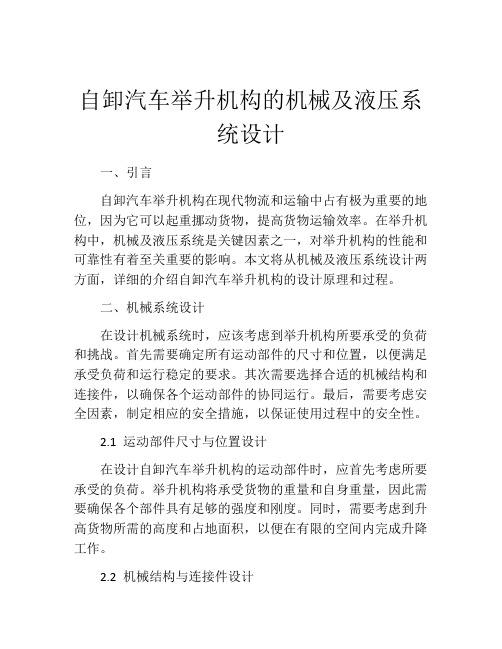
自卸汽车举升机构的机械及液压系统设计一、引言自卸汽车举升机构在现代物流和运输中占有极为重要的地位,因为它可以起重挪动货物,提高货物运输效率。
在举升机构中,机械及液压系统是关键因素之一,对举升机构的性能和可靠性有着至关重要的影响。
本文将从机械及液压系统设计两方面,详细的介绍自卸汽车举升机构的设计原理和过程。
二、机械系统设计在设计机械系统时,应该考虑到举升机构所要承受的负荷和挑战。
首先需要确定所有运动部件的尺寸和位置,以便满足承受负荷和运行稳定的要求。
其次需要选择合适的机械结构和连接件,以确保各个运动部件的协同运行。
最后,需要考虑安全因素,制定相应的安全措施,以保证使用过程中的安全性。
2.1 运动部件尺寸与位置设计在设计自卸汽车举升机构的运动部件时,应首先考虑所要承受的负荷。
举升机构将承受货物的重量和自身重量,因此需要确保各个部件具有足够的强度和刚度。
同时,需要考虑到升高货物所需的高度和占地面积,以便在有限的空间内完成升降工作。
2.2 机械结构与连接件设计自卸汽车举升机构的机械结构和连接件要求具有足够的强度和稳定性,以保证各个运动部件之间的协同运行。
常用的机械结构包括点式连杆机构、摆杆机构、旋转机构等,连接件包括螺栓、销子、铰链等。
在选择机械结构和连接件时,应当根据实际工作情况和要求,进行合理的选择和安排。
2.3 安全措施设计在自卸汽车举升机构中,安全永远是重中之重。
设计安全措施是确保机构在工作期间的正确且稳定运行的必要条件。
一些常规的安全措施包括安装安全带、加强运动部件的抗摆性、设置限制器等。
任何的失误或差错都可能导致安全问题,因此一定要在设计阶段充分考虑和采取必要的安全措施。
三、液压系统设计在自卸汽车举升机构中,液压系统是将机械的能量转换为液体压力能量的关键,其主要功能是控制升降运动和保持稳定平衡。
液压系统设计的目的是保证油液的压力、流量、温度和清洁度等指标,在一定的工作条件下保持稳定运行,满足设备使用的需要。
自卸农用三轮车举升机构的总体设计

第一章 绪 论§1.1 课题背景自卸车是利用发动机动力驱动液压举升机构,将车厢倾斜一定角度从而达到自动卸货的目的,并依靠货箱自重使其复位的专用汽车。
按不同的用途自卸车可分为两大类:一类是非公路运输用的重型和超重型(额定装载质量在20t 以上)自卸汽车。
另一类是公路运输用的轻、中、重型(装载质量在2~20t)普通自卸汽车。
这种自卸车主要承担着泥土、砂石、煤炭等松散货物的运输工作,它通常也是与装载机械配套使用的。
就本设计而言根据市场需要,确定最大载重量为2t ,最大卸料角度30度的自卸车为轻型的。
该普通自卸车辆有多种分类方法,按运输货物倾卸方向分为:后倾式、侧倾式、三面倾式和底卸式自卸汽车;按货箱栏板结构分为:栏板一面开启式、栏板三面开启式和簸箕式(即无后栏板式)汽车;按装载质量分为:轻型自卸汽车(e m <3.5t)、中型自卸汽车(3.5t ≤e m <8t)和重型自卸汽车(e m ≥8t)。
度的轻型农用自卸车是随着我国农村经济的不断发展,轻型农用自卸车以其灵活机动、价格低廉的优点得到了广泛的应用。
在轻型农用自卸车的设计当中,液压举升操纵机构的设计一直处于重要的地位。
这是因为液压举升操纵机构是轻型农用自卸车的重要工作系统,其设计方案的优劣直接影响着汽车的多个主要性能指标;应用最优化方法进行液压举升机构的设计,可以一次寻求得到最有的设计方案,对提高液压举升机构的设计质量和效率具有重要的意义。
§1.2课题的实际意义对于液压举升机构考虑到工作环境、工作性质及工作内容等的要求,在设计液压举升机构时应满足的性能有较强的免维护性 、良好的动力性、平稳性、卸料性、紧凑性、协调性。
目前大多数企业一直沿用传统的“类比作图试凑法”进行设计,这种方法存在效率低、工作量大以及设计方案难以达到最优的缺点,设计方案难以同时兼顾以上各性能要求。
这与当今高科技环境下的相关领域相比,缺少科学性,人的主观经验决定了车辆的性能。
自卸车举升机构的设计与分析

自卸车举升机构的设计与分析摘要根据使用要求确定举升机构的结构及参数,通过计算机对该结构进行设计及分析,最终完成设计。
关键词自卸车举升机构设计分析中图分类号:u469 文献标识码:a自卸车举升机构是自卸车上的核心机构,设计时既要考虑机构运动,又要考虑机构强度。
现在开发一款主要针对装载细沙和石灰石的自卸车,整车轴距3500,货箱内部最大尺寸4000??100??00,整车最大装载质量10500kg。
为满足整车性能及使用要求,对车箱举升机构进行设计优化。
1举升机构结构的形式杆系倾卸式一般是由三角臂、副车架和车箱等构成的连杆机构与油缸组合而成以实现车箱的倾卸功能。
本车采用比较常用的油缸前推连杆组合形式,其布置灵活并能使油缸行程成倍放大,举升力系数小省力,油压特性好。
2举升机构整体参数的初步选取2.1车箱倾斜角的要求举升机构要保证车箱具有一定的倾斜角,只有当举升角大于货物的安息角时,货物才能倾泻干净。
针对细沙和石灰石的使用,我们选取货箱最大倾斜角为45?啊?2.2对油缸活塞行程的要求油缸活塞行程应尽可能小,以利于缩短倾卸时间,提高工效,降低油缸的制造成本,减轻机构的质量。
油缸行程580mm<h<630mm。
2.3对建造纵深的要求建造纵深是指连杆组合式举升机构在自卸车车箱下部空间中所要求的深度,要求尽可能小,机构紧凑,降低车箱高度,提高整车稳定性,也利于组合式连杆举升机构的总体布置。
设计车箱纵梁高度120mm,主车架纵梁高度240mm,副车架高度120mm,总高度和为480mm。
举升机构建造纵深l<480。
2.4对举升油缸的要求因车箱不断倾斜,装载货物随之卸出,所以车箱启动时的举升力最大,通常要求活塞以尽可能小的举升力来启动车箱,以利于减小举升机构的体积和重量。
暂定参数:油泵额定工作压力=20mp,需要油泵的最小理论流量=40l/min;活塞推力f=40t;油缸缸径=160mm;油缸行程=610mm。
T式举升机构
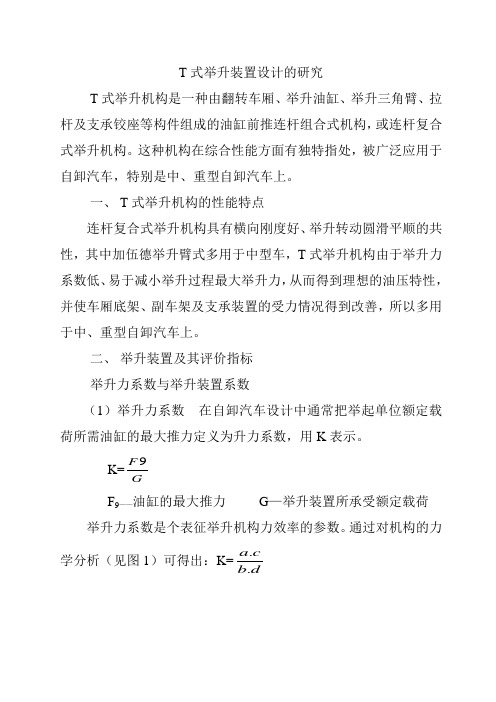
T 式举升装置设计的研究T 式举升机构是一种由翻转车厢、举升油缸、举升三角臂、拉杆及支承铰座等构件组成的油缸前推连杆组合式机构,或连杆复合式举升机构。
这种机构在综合性能方面有独特指处,被广泛应用于自卸汽车,特别是中、重型自卸汽车上。
一、 T 式举升机构的性能特点连杆复合式举升机构具有横向刚度好、举升转动圆滑平顺的共性,其中加伍德举升臂式多用于中型车,T 式举升机构由于举升力系数低、易于减小举升过程最大举升力,从而得到理想的油压特性,并使车厢底架、副车架及支承装置的受力情况得到改善,所以多用于中、重型自卸汽车上。
二、 举升装置及其评价指标举升力系数与举升装置系数(1)举升力系数 在自卸汽车设计中通常把举起单位额定载荷所需油缸的最大推力定义为升力系数,用K 表示。
K=G F 9F 9——油缸的最大推力G —举升装置所承受额定载荷 举升力系数是个表征举升机构力效率的参数。
通过对机构的力学分析(见图1)可得出:K=d b ca ..举升力系数K与机构的结构型式有关,通常直推式举升机构K 值在1~1.5左右;T式举升机构在1.5~2左右;加伍德举升臂式举升机构在2.4~2.8左右。
当然,在机构选型时K值不是唯一的指标,还需综合考虑横向刚度、机构质量利用系数、工作可靠性、平稳性、成本等方面的因素。
对同一种举升机构,K值与结构尺寸和机构的布置有关。
所以利用举升力系数可以对各种车型的举升机构进行综合比较与评价。
(2)举升装置系数对举升力系数的研究可以发现,用K 值进行评价的举升机构包括、油缸、举升三角臂、连杆和支架支铰等构件。
但在设计中,对车厢的考虑是以满足额定容积、整车轴荷分配、举升状态车厢后沿最小离地间隙等为设计条件。
在其他构件布置时,车厢位置(即a值)是作为不便参数考虑的,只有在K值达不到设计要求时再考虑调整,所以除车厢以外的举升构件是举升机构设计的主要研究对象,把这些构件称之为举升装置,以区别于包括车厢在内的举升机构。
T型自卸车举升机构的设计和计算软件开发

T型自卸车举升机构的设计和计算软件开发1 前言举升机构是自卸汽车的关键装置,它直接关系到自卸汽车的性能及整车布置。
举升机构设计计算十分重要,其机构各点布置是否合理,直接影响自卸车使用性能。
传统自卸机构设计多采用利用CAD制图软件绘制自卸机构从零度到最大举升角各角度下机构的运动状态,再测量机构尺寸手工计算各点受力,这种方法不仅要花费大量时间,而且要调整任何一各(各字是否该删去?)参数都需要重新绘图计算,极不方便容易出错效率低(不太通顺)。
随着计算机的发展,如果利用程序语言开发出专业软件,将大大提高工作效率,降低设计成本和三包费用。
市场有同类软件售价9800元,但其不能输出数据表和打印机构各点受力曲线。
(这部分内容也不合适放在文章中)本软件能够计算出了(出了是否该删去?)举升机构各点在不同的举升角度下的坐标、受力等基本数据和举升机构的总体参数、液压缸的特性等等。
调用EXCEL软件,利用其图表和光滑曲线等形式输出数据,更便于对机构运动的理解和相零(邻)部件选型设计。
2 举升机构设计[1](此处[1]是否改为上标?)2.1 方案的选择自卸汽车举升机构分为两大类,即:直推式举升机构和连杆组合式举升机构。
它们均采用液体压力作为举升动力。
2.1.1 直推式举升机构利用液压油缸直接举升车厢倾卸。
该机构布置简单、结构紧凑、举升效率高,但液压油缸工作行程长,因此,一般要求采用单作用的2级或多级伸缩式套筒油缸。
另外单缸系统其横向刚度不足,系统倾卸稳定性差,还存在工作寿命短(这句话是否该改一下?我觉得前顶自卸车不存在寿命短的问题)、成本高等缺点。
2.1.2 连杆组合式举升机构具有举升平顺、油缸活塞的工作行程短、机构布置灵活等优点。
该机构又分油缸后推式和油缸前推式两种:油缸后推式机构举升力系数适中,结构紧凑,但各部件布置集中在后部,车厢底板受力大,适用于中型自卸汽车;油缸前推式又称“T”式举升机构,其举升力系数小、省力、油压特性好,适用于重型自卸汽车。
自卸汽车举升机构设计概述

分类号编号烟台大学毕业论文(设计)T式自卸汽车举升机构设计The design of T- type column hydraulic car lift申请学位:工学学士学位院系:机电汽车工程学院专业:机械设计制造及其自动化姓名:学号:指导老师:2014年6月1日烟台大学.T式自卸汽车举升机构设计姓名:指导教师:2014年6月1日烟台大学摘要随着国民经济的增长,我国专用汽车市场进入了快速成长期。
2005 年专用汽车生产企业已经有 628 家,专用汽车品种已经达到 4900 多个,2005 年专用汽车产量达70 万辆,占载货汽车总产量的 40%。
作为专用汽车中一个分支的自卸汽车,陆续出现了多种多样的型式,其中最常见的是后倾式自卸汽车。
本文首先对自卸汽车国内外发展现状及设计内容作了相关的概述。
接着,按照自卸车举升机构的设计过程,完成了对机构的选型、机构的受力分析也计算、液压回路系统的设计与运动仿真分析。
关键字:专用汽车,自卸汽车,举升机构,运动仿真AbstractWith the national economic growth, China's auto market has entered a special rapid gro wth. 2005 Special Purpose Vehicle manufacturers have been 628, Special PurposeVehicle has reached more than 4900 varieties,2005 special vehicle production reached 700,000, Accounting f or 40% of total truck. As a Special Purpose Vehicle in a branch ofthe dump truck, has been found in a wide variety of types , of which the most common isBack ward curved dump truck.In this paper, firstly, I made a general about the auto unload vehicle design and itsdevelopment domestic and abroad. Then, according to the process of the design of lifting mechanism of dump truck, completed the analysis of mechanism selection, mechanism of stress analysis are also calculated, h ydraulic system design and motion simulation.Key words: Special Purpose Vehicle, Dump Truck, Lifting mechanism, motion simulation目录第一章绪论 (1)1.1引言 (1)1.2 国内外专用车辆的发展概况 (1)1.2.1 国外专用车辆发展概况 (1)1.2.2 我国专用汽车的发展状况 (2)1.3自卸车概述 (2)第二章自卸车举升机构选型 (4)2.1自卸车载重与车厢举升角的确定 (4)2.1.1自卸车载重 (4)2.1.2车厢举升角的确定 (4)2.2举升机构结构选型 (4)第三章自卸汽车举升机构的结构与设计 (7)3.1T 式举升机构运动与受力的解析计算 (7)第四章液压系统设计 (12)4.1确定系统方案 (12)4.1.1液压回路系统的设计 (12)4.2液压系统主要元件的性能参数计算与选型 (13)4.2.1举升油缸的性能参数计算与选型 (13)4.2.2液压油泵性能参数计算与选型 (14)4.2.3管路选择 (15)4.2.4油箱容积设计 (15)第五章T式自卸汽车举升机构的动力学仿真 (16)5.1 T式自卸汽车举升机构系统实体模型的建立 (16)5.2举升机构的动力学仿真 (18)5.2.1 模型导入 (18)5.2.2编辑模型构件 (19)5.2.3运动副建立 (19)5.3对三维模型进行运动仿真分析 (20)5.3.1设置运动仿真解算方案 (20)5.3.2仿真曲线输出。
自卸车举升机构的设计与分析

点布置在靠近车箱 的前部 ,但过于靠前会在一定的倾斜 角度 时导致 油缸行程 的增加。另外 ,B点位置靠前可以提高货箱
举 升机 构 要 保 证 车 箱 具 有 一 定 的 倾 斜 角 ,只 有 当举 升 角 举升时的横 向稳定性 , 有 利于提高车箱强度 。 C点是油缸 的上支点 , C点的位置布置偏上, 就会使 油缸 大于货物的安息角时 ,货物才能倾泻干净。针对细沙和石灰 石的使用, 我 们选 取 货箱 最 大倾 斜 角 为 4 5 。 。 2 . 2对 油 缸 活 塞行 程 的要 求
E点是连杆系与副车架的铰接 点, E点的位置将影响举升 建造纵深是指连 杆组合式举升机构在 自卸车车箱下部空 时是 否 省 力 。 间中所要求 的深度, 要求尽可能小, 机构紧凑, 降低车箱高度 , 0点是车箱 与车架 的铰接 点, 应将 O点的位置尽量靠近
提 高整 车稳 定 性 , 也 利 于 组 合 式 连 杆举 升机 构 的 总 体 布置 。 设 车箱 中心, 因此在满足轴荷要 求情况下, 应将货箱尽可能靠后
自卸车举升机构的设计与分析
蒋 宏 宇
( 沈 阳金 杯 车辆制 造有 限公 司重 型车设 计处
摘 要 关键词 自卸车 举升机构 中 图分 类 号 : U 4 6 9 设计 分析 文 献标 识 码 : A
3 . 2调 整 并确 定 各 点 的 位 置 通过 草 图的 绘制 , 各 点位置 已经 初 定但仍 需要进一 步调 整 。
载细沙和石灰石的 自卸车 , 整车轴距 3 5 0 0 , 货箱内部最大尺寸 性能及使用要求, 对车箱举升机构进行设 计优化 。
A点是油缸 的下支点 , 确 定 A点的位置时, 通常要考虑油 活塞的行程 , 尽可能的使 A点的位置靠近车箱的尾部, 但是 A
基于虚拟样机的自卸汽车T式举升机构优化设计

Keywords: dump truck; lifting mechanism; virtual prototype; optimized design; generalized gradient algorithm
变量 优化前 优化后
表3第二次优化数据结果 单位:mm
DV_3
DV_5
DV_7
DV_8
DV_9
-I00
266
-128 4 742
165
-95
260
-140 4 670
240
3.3 T式举升机构优化前、后结果对比
通过ADAMS/View软件的优化设计模块完成对自卸 汽车T式举升机构的优化设计,优化设计得到的结果值确 定了优化后T式举升机构各较接点位置坐标,优化前、后 举升机构中油缸驱动力的输出曲线如图4所示。
T式举升机构在自卸汽车中应用广泛,对于举升机构 的设计,早期主要采用作图法进行分析。这种方法工作量 大,在产品的设计优化过程中需要多次进行复杂的作图分 析计算,而且精度较差。近年来,随着计算机技术的不断 进步,一些学者和企业开始利用虚拟样机技术来开展产品 的性能研究、优化设计等研究工作[2-I0]。通过虚拟样机模 型在设计阶段就能完成预测、评价产品的各项性能,不仅 缩短了产品开发周期,而且能够大幅减少研发成本。基于 此,本文利用多体动力学软件ADAMS对T式自卸汽车举 升机构进行参数化设计,获得举升机构主要较接点的最佳 位置,为自卸汽车的优化设计提供了新途径,同时也为提 高举升机构的工作性能提供了依据。
0引言
1 T式举升机构的建模与仿真
自卸汽车是通过发动机驱动液压机构从而驱动举升 机构倾斜到一定角度实现自动卸货,并靠自重回位的工程 车辆,广泛应用于各种复杂路况的运输工作。举升机构作 为自卸汽车的核心机构,其设计的好坏,直接影响到自卸 车的使用性能。因此举升机构的分析、优化对于自卸汽车 的设计研发具有重要意义[|]。
基于SolidWorks的自卸车举升机构设计

58|Agriculture Mechanization Research》农机化研究|(2020年10月上)基于SolidWorks的自卸车举升机构设计岳庆超,郑义(青岛黄海学院智能制造学院,山东青岛266427)摘要:随着国民经济的大力发展,自卸车近几年的需求量急剧上升,在运输以及装卸货物的过程中发挥着巨大的作用,经常在恶劣的环境中工作,所以举升机构的工作寿命可能有所限制。
本文以自卸车举升机构为研究对象,通过了解自卸车的整体结构参数以及举升结构的类型选择,在获得一定的设数,对自卸车举升机构。
然后以SolidWorks为本文关键的建模软件,建立举升机构各零部件的三模型,体装配。
设用、定的举升机构,自卸车顺利的装卸货物。
关键词:自卸车;举升机构;三建模;有限中图分类号:U469.4文献标志码:A文章编号:1672-3872(2020)19-0058-03自卸车是经过液压系统或机械举升而自行装卸货物的车辆,通常和挖掘机、装载机等机械一起工作,形成一条完整的生产线,进行各种货物或材料的装卸运输工作叫通过利用汽车发动机驱动液压装置和举升机构,可以使车厢在一定角度装卸货物,并通过自身重力和液压装置进行复位。
可以实现机械化装卸,减少劳动力的使用,减少人工成本,提高装卸效率[2-34。
因为自卸车经常工作在路况非常不好的现实,经常现路况车辆运行的情况,以工作性能有严格地要求。
$举升机构总体方案设计在自卸车常见的举升机构就是液压举升机构,根车厢不:和$用液压力作为举升动力I。
举升机构用液压举升车厢倾卸。
该机构布置、构、举升效率高。
液压工作行,以一要求用2或3。
置的位置不同,举升机构分成了前置和置种。
置式一用,置为双。
在举升载,置要的举升力,举升时车厢横向刚度大,行程长;后置式的好相图1直推式举升机构连杆组合式举升机构用厢和连杆机构相连接来实现倾卸27-94。
机构有举升、的工作行,举升机构置等,因在生产生作者简介:岳庆超(1981—),男,山东临沂人,本科,副教授,研究:机械设制,制。
举升机构的设计说明书
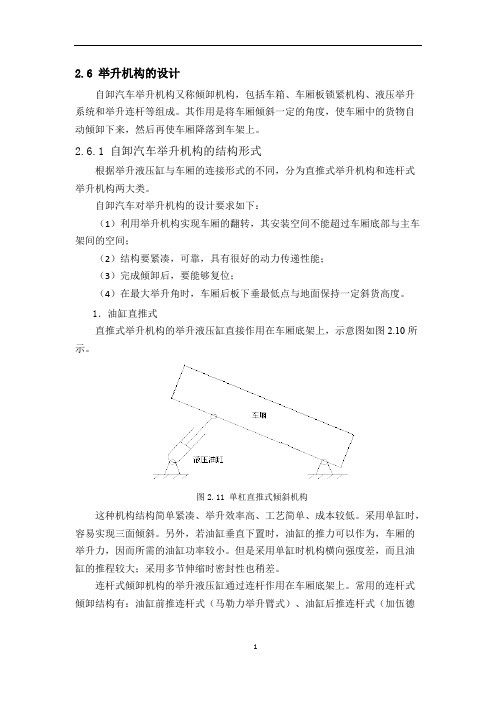
2.6 举升机构的设计自卸汽车举升机构又称倾卸机构,包括车箱、车厢板锁紧机构、液压举升系统和举升连杆等组成。
其作用是将车厢倾斜一定的角度,使车厢中的货物自动倾卸下来,然后再使车厢降落到车架上。
2.6.1 自卸汽车举升机构的结构形式根据举升液压缸与车厢的连接形式的不同,分为直推式举升机构和连杆式举升机构两大类。
自卸汽车对举升机构的设计要求如下:(1)利用举升机构实现车厢的翻转,其安装空间不能超过车厢底部与主车架间的空间;(2)结构要紧凑,可靠,具有很好的动力传递性能;(3)完成倾卸后,要能够复位;(4)在最大举升角时,车厢后板下垂最低点与地面保持一定斜货高度。
1.油缸直推式直推式举升机构的举升液压缸直接作用在车厢底架上,示意图如图2.10所示。
图2.11 单杠直推式倾斜机构这种机构结构简单紧凑、举升效率高、工艺简单、成本较低。
采用单缸时,容易实现三面倾斜。
另外,若油缸垂直下置时,油缸的推力可以作为,车厢的举升力,因而所需的油缸功率较小。
但是采用单缸时机构横向强度差,而且油缸的推程较大;采用多节伸缩时密封性也稍差。
连杆式倾卸机构的举升液压缸通过连杆作用在车厢底架上。
常用的连杆式倾卸结构有:油缸前推连杆式(马勒力举升臂式)、油缸后推连杆式(加伍德举升臂式)、油缸前推连杆式、油缸后推连杆式、油缸浮动连杆式、油缸俯冲连杆式。
表2-11自卸汽车举升机构特性比较结构型式车型举例性能特征结构示意图油缸前推连杆组合式五十铃TD50ALCQD 、QD362举升力系数小,省力,油压特性好,但缸摆角大活塞行程稍大。
油缸后推连杆组合式五十铃TD50A-D 、QD352、HF352转轴反力小,举升力系数大,举升臂较大,活塞行程短。
油缸后推连杆组合式日产PTL81SD 举升力适中,杆系受力比较小,举升过程中油缸的摆动角度很小,油缸的行程也比较短,但因为机构集中在车后部,车厢底板受力大。
油缸浮动连杆式YZ-300油缸进出油管活动范围大,油管长,举升力系数较小。
自卸车举升机构的设计与分析
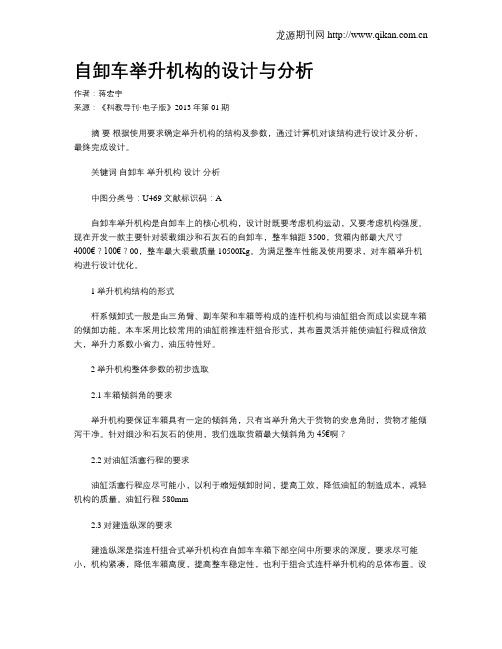
自卸车举升机构的设计与分析作者:蒋宏宇来源:《科教导刊·电子版》2013年第01期摘要根据使用要求确定举升机构的结构及参数,通过计算机对该结构进行设计及分析,最终完成设计。
关键词自卸车举升机构设计分析中图分类号:U469 文献标识码:A自卸车举升机构是自卸车上的核心机构,设计时既要考虑机构运动,又要考虑机构强度。
现在开发一款主要针对装载细沙和石灰石的自卸车,整车轴距3500,货箱内部最大尺寸4000€?100€?00,整车最大装载质量10500Kg。
为满足整车性能及使用要求,对车箱举升机构进行设计优化。
1举升机构结构的形式杆系倾卸式一般是由三角臂、副车架和车箱等构成的连杆机构与油缸组合而成以实现车箱的倾卸功能。
本车采用比较常用的油缸前推连杆组合形式,其布置灵活并能使油缸行程成倍放大,举升力系数小省力,油压特性好。
2举升机构整体参数的初步选取2.1车箱倾斜角的要求举升机构要保证车箱具有一定的倾斜角,只有当举升角大于货物的安息角时,货物才能倾泻干净。
针对细沙和石灰石的使用,我们选取货箱最大倾斜角为45€啊?2.2对油缸活塞行程的要求油缸活塞行程应尽可能小,以利于缩短倾卸时间,提高工效,降低油缸的制造成本,减轻机构的质量。
油缸行程580mm2.3对建造纵深的要求建造纵深是指连杆组合式举升机构在自卸车车箱下部空间中所要求的深度,要求尽可能小,机构紧凑,降低车箱高度,提高整车稳定性,也利于组合式连杆举升机构的总体布置。
设计车箱纵梁高度120mm,主车架纵梁高度240mm,副车架高度120mm,总高度和为480mm。
举升机构建造纵深L2.4对举升油缸的要求因车箱不断倾斜,装载货物随之卸出,所以车箱启动时的举升力最大,通常要求活塞以尽可能小的举升力来启动车箱,以利于减小举升机构的体积和重量。
暂定参数:油泵额定工作压力=20Mp,需要油泵的最小理论流量=40L/min;活塞推力F=40t;油缸缸径=160mm;油缸行程=610mm。
自卸汽车举升机构的机械及液压系统设计-参考模板
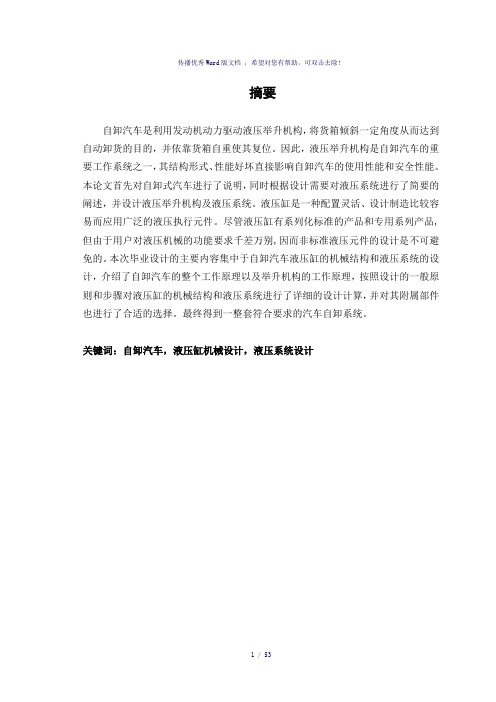
摘要自卸汽车是利用发动机动力驱动液压举升机构,将货箱倾斜一定角度从而达到自动卸货的目的,并依靠货箱自重使其复位。
因此,液压举升机构是自卸汽车的重要工作系统之一,其结构形式、性能好坏直接影响自卸汽车的使用性能和安全性能。
本论文首先对自卸式汽车进行了说明,同时根据设计需要对液压系统进行了简要的阐述,并设计液压举升机构及液压系统。
液压缸是一种配置灵活、设计制造比较容易而应用广泛的液压执行元件。
尽管液压缸有系列化标准的产品和专用系列产品,但由于用户对液压机械的功能要求千差万别,因而非标准液压元件的设计是不可避免的。
本次毕业设计的主要内容集中于自卸汽车液压缸的机械结构和液压系统的设计,介绍了自卸汽车的整个工作原理以及举升机构的工作原理,按照设计的一般原则和步骤对液压缸的机械结构和液压系统进行了详细的设计计算,并对其附属部件也进行了合适的选择。
最终得到一整套符合要求的汽车自卸系统。
关键词:自卸汽车,液压缸机械设计,液压系统设计目录1 绪论 (1)1.1 自卸汽车的作用 (1)1.2 自卸汽车的分类 (1)1.3 常见自卸汽车分类举例 (2)1.4 自卸汽车的举升机构 (3)1.5 自卸汽车的结构特点 (3)1.6 小结 (4)2 液压系统设计 (5)2.1 液压概述 (5)2.1.1 液压技术的发展 (5)2.1.2 液压传动 (5)2.2 自卸汽车液压系统设计 (6)2.2.1 液压缸概述 (6)2.2.2 液压系统原理图 (7)2.2.3 液压系统图 (8)2.3 小结 (9)3 液压缸结构设计 (10)3.1 液压缸结构设计的依据、原则和步骤 (11)3.1.1 设计依据 (11)3.1.2 设计的一般原则 (12)3.1.3 设计的一般步骤 (12)3.2 液压缸基本结构参数及相关标准 (13)3.2.1 液压缸的液压力分析和额定压力的选择 (14)3.2.2 液压缸内径D和外径D (16)13.2.3 活塞杆外径(杆径)d (17)3.2.4 液压缸基本参数的校核 (18)3.3 液压缸综合结构参数及安全系数的选择 (19)3.3.1 液压缸综合结构参数 (19)3.3.2 安全系数的选择 (19)3.4 液压缸底座结构设计 (21)3.5 缸体设计与计算 (22)3.5.1 缸筒设计 (23)3.5.2 缸头和油口设计 (26)3.6 活塞组件设计 (28)3.6.1 活塞杆设计 (28)3.6.2 活塞设计 (30)3.6.3 活塞与活塞杆的连接结构 (31)3.7 缸盖设计 (32)3.7.1缸盖材料和技术要求 (32)3.7.2 缸盖的结构设计 (33)3.8 焊接强度及螺纹连接计算 (34)3.8.1焊接强度计算 (32)3.8.2缸盖螺栓连接强度计算 (35)2.9 小结 (35)4 液压原件选择 (36)4.1 液压泵的确定 (36)4.2 阀类元件的确定 (37)4.2.1 选择阀类元件应注意的问题 (37)4.2.2 阀类元件的选择 (38)4.3 油箱的选择 (39)4.4 滤油器的选择 (39)4.5 管路的选择 (39)4.6 小结 (40)设计小结 (41)致谢辞 (42)参考文献 (44)1 绪论1.1 自卸汽车的作用自卸车的出现是随着时代的发展,搬运工作已经不是人力可以解决的情况下,使用高科技而开发的搬运器械。
自卸汽车举升机构的设计

让自卸汽车举升更便捷-独特的设计自卸汽车是货运行业中的重要组成部分。
但是,在装卸货物时,
往往需要将自卸箱体抬高,以便于货物的顺利卸下。
因此,自卸汽车
举升机构的设计显得尤为重要。
本文将介绍一种全新的设计方案,让
自卸汽车举升更加便捷。
该设计方案的核心在于将自卸汽车举升机构集成于车身底部。
这样,在需要使用举升机构时,只需将车辆停在举升区域,便可以通过
遥控操作将举升支架自动伸出。
之后,只需轻松的将自卸箱体卸下即可。
该设计方案的优点显而易见。
首先,它可以避免在使用传统举升
机构时需要单独设置卸货区域,节省了重要的空间资源。
同时,集成
在车身底部的举升机构也可以避免传统举升机构闪烁的问题,提高了
操作的安全性和稳定性。
该设计方案还有一个非常实用的功能,那就是可以通过遥控来控
制举升机构的伸缩。
这就意味着,在需要举升时,操作人员可以在自
卸汽车旁边远程操作举升机构,并可以通过遥控器精准控制举升机构
的伸缩速度和高度,大大提高了操作的便捷性。
总的来说,该设计方案的优点显而易见,无疑将会成为未来自卸
汽车举升机构的趋势。
本文建议对该设计方案的应用进行更进一步的
研究以及推广,以便更多的企业可以享受到它所带来的便利与实用性。
基于遗传算法的自卸汽车T式举升机构优化设计
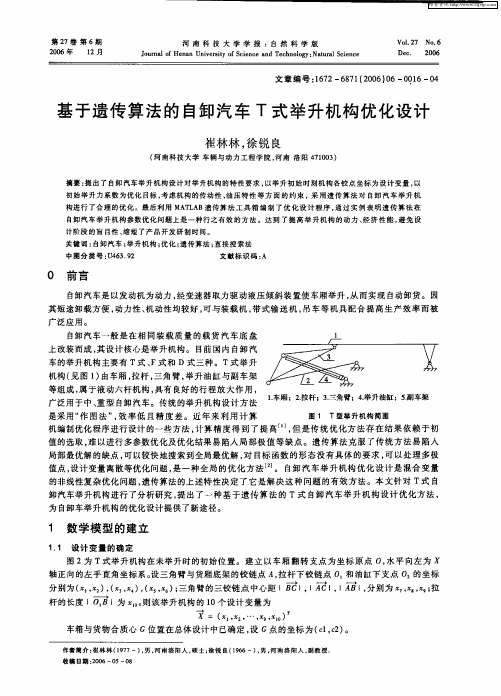
中 图分 类 号 :4 3 9 U 6 .2
^ . 】L .L .
文 献 标 识 码 : A
U 刖 旨
自卸 汽车 是 以发动 机为 动力 , 经变 速器 取力驱 动 液压 倾斜 装 置使 车厢举 升 , 而 实现 自动卸 货 。因 从 其短 途卸 载方 便 , 动力性 、 动性 均较好 , 与装 载机 , 式输 送 机 , 机 可 带 吊车 等 机具 配 合提 高 生 产 效率 而 被
( ,: … X , 。 。 , 9 ) 。
车箱与 货物 合质 心 G位 置 在总体 设计 中已确定 。 G点 的坐标 为 ( l c ) 设 c ,2 。
作 者筒 介 : 林 林 (9 7一), 。 南 洛 阳人 , 士 ; 锐 良( 9 6一) 男 . 南 洛 阳人 。 崔 17 男 河 硕 徐 16 。 河 副教 授
广泛 应用 。
自卸 汽车 一般 是 在 相 同装 载质 量 的 载 货 汽 车底 盘
上 改装而 成 , 设计 核 心是举 升机 构 。 目前 国内 自卸 汽 其 车的举升 机构 主要 有 T式 、 F式 和 D式 三种 。T式 举 升 机 构 ( 图 1 由车厢 。 见 ) 拉杆 , 角臂 , 升油 缸 与 副车 架 三 举 等 组成 , 于 液 动六杆机 构 , 属 具有 良好 的行 程放 大 作 用 , 广 泛用 于 中、 型 自卸 汽车 。传统 的举 升机 构设 计 方 法 1 重 . 车厢;2 . 拉杆;3 . 三角臂;4 . 举升油缸;5 . 副车架 是 采用 “ 图 法 ” 效 率 低 且 精 度 差 。 近 年来 利 用计 算 作 , 围 1 T型举升机构简围 机 编制优 化 程序进 行设 计 的一些 方 法 , 算 精 度 得 到 了 提 高 … , 是 传 统 优 化方 法 存 在 结 果 依 赖 于初 计 但
211-自卸车T式举升机构受力点分析

自卸车T式举升机构受力点分析摘要:根据油缸T式连杆放大式举升机构在举升过程中各构件的运动特点,运用三角函数和方程相结合的方法建立了举升机构运动学分析数学模型,为自卸汽车T式举升机构运动学分析,性能评价及合理设计提供了理论基础关键词:自卸车 T式结构受力分析1 前言前期售后服务反应我们厂中顶车格尔发的一款底盘,客户在卸货时,前端翘头,现对三角臂及其后翻转座处进行受力分析,为以后对主车翘头研究作为理论依据。
油缸T式举升机构在自卸汽车中是一种常用的举升机构,它实际上是一种演化形式的四杆机构。
由《机械原理》可以得知,分析设计四杆机构的方法有解析法、作图法、试验法等等,本文运用解析法和作图法进行计算。
2 机构原理自卸汽车的车厢要完成举升、中停以及降落等动作, 其运动过程的实现是靠液压系统控制的三角臂组合式液压举升机构来完成的。
如图1所示, 三角臂A B C 为一个整体, 其C点与车厢底架铰接; B 点与油缸OB 铰接, A 点与拉杆A D 铰接。
O 点、D 点固定在中横梁的油缸支座上。
当油缸OB 进油腔通入压力油时,OB 伸长使三角臂绕A 点转动;同时, 由于有拉杆A D 的作用, A点又绕D 点转动。
于是, 上述两个分运动就构成了三角臂的复合运动。
图1 举升机构运动示意图3 机构受力分析三角臂A B C 作为一个独立体系, 它受到三个力的作用: 油缸OB 产生的推力f; 拉杆A D 产生的拉力f1; 车厢对三角臂的反作用力f2。
拉杆A D 及油缸OB 均为二力杆件, 因此, f 及f1的方向均可确定(如图1) , 二力交于R 点, 根据平面力系汇交原理, 则f2必过R 点。
而且, f 与f1、f2的合力f ′大小相等, 方向相反4 机构受力计算公式推导及演算实例建立如图1所示的直角坐标系, 以翻转轴支点K 为坐标原点。
根据自卸车结构及布局可得各点坐标分别为:K(0, 0) D(1988, 61) O(2228, -143)又已知:AB 长l AB= 245mm,B C 长l BC= 810mm AC 长l AC= 955mm ,AD 长l AD= 1480mmck′长l ck′=2342mm,k′k长l k′k= 146mm图2 以翻转轴支点K 为坐标原点建立坐标系且k′k⊥ck′。
T式腹举自卸车使用指南
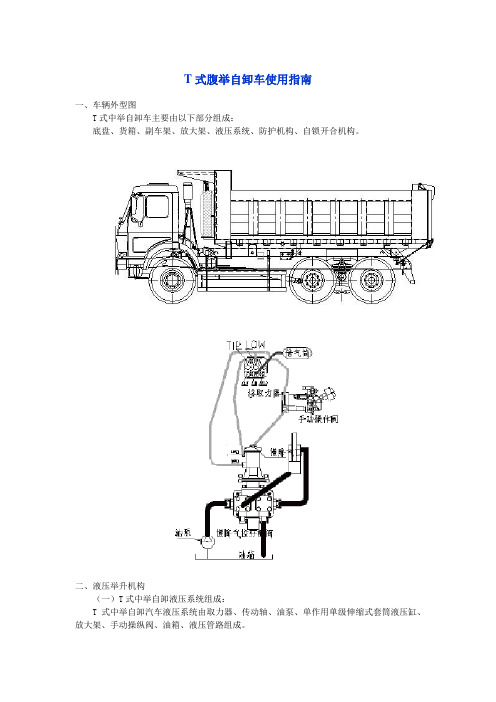
T式腹举自卸车使用指南一、车辆外型图T式中举自卸车主要由以下部分组成:底盘、货箱、副车架、放大架、液压系统、防护机构、自锁开合机构。
二、液压举升机构(一)T式中举自卸液压系统组成:T式中举自卸汽车液压系统由取力器、传动轴、油泵、单作用单级伸缩式套筒液压缸、放大架、手动操纵阀、油箱、液压管路组成。
(二)T式中举自卸汽车液压举升系统工作原理:液压系统原理简图(气控)工作原理:当把手动操作阀手柄推至“举升”位置,接通取力器开关,使电磁阀导通,储气筒里的压缩空气流向取力器缸,推动取力器齿轮捏合,齿轮泵开始工作。
液压油箱中的液压油经过齿轮泵加压,经单向阀直接进入液压油缸下腔,推动活塞杆,使车厢开始举升。
举升到最大位置后,活塞达到泄油阀,液压油经过泄油阀流回到油箱,此时车厢不再举升,停在最大位置当把手动操作阀手柄推至“下降”位置,液压油缸下腔与油箱直连,车厢靠自重回复原位。
液压系统原理简图(油控)工作原理:当转阀手柄推到举升位置,接通取力器开关使电磁阀导通,储气筒里的压缩空气流向取力器缸,推动取力器齿轮捏合,齿轮泵开始工作。
液压油箱中的液压油经过齿轮泵加压,经单向阀直接进入液压油缸下腔,推动活塞杆,使车厢开始举升。
举升到最大位置后,活塞达到回油口,高压油经过油管流回到油箱,此时车厢不在举升,停在最大位置。
当把手动操作阀手柄推至“下降”位置,液压油缸下腔与油箱直连,车厢靠自重回复原位。
(三)T式中举自卸汽车液压系统操作说明1)打开后门手动锁钩。
2)启动发动机,使气压达到系统工作压力(解放P≥0.6MPa其它P≥0.8M)3)踏下离合器踏板(10秒)4)打开电磁阀开关(取力器开关),把手动操作阀转到举升位置。
5)挂前进一至三档,发动机转速低于1600转/分钟。
6)松开离合器踏板,液压泵开始工作,货厢开始举升,当货厢举升最高点,泄油阀自动打开,这时货厢停止在最大举升高度。
7)踏下离合器踏板(10秒),将档位停止在空位位置。
自卸车举升机构设计
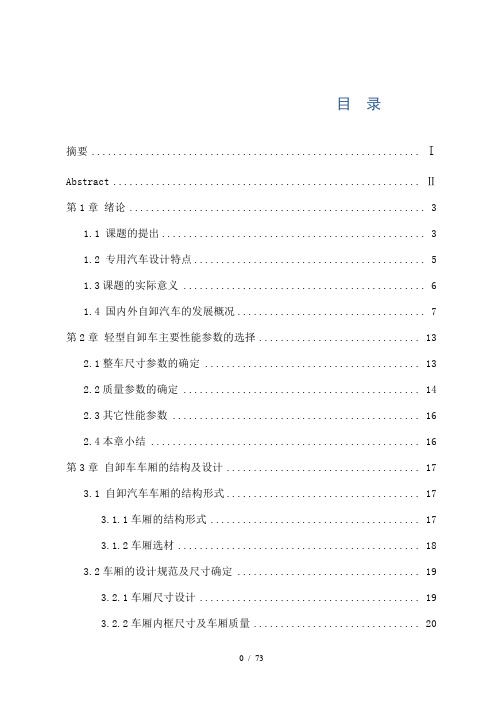
目录摘要............................................................. Abstract (Ⅱ)第1章绪论 (3)1.1 课题的提出 (3)1.2 专用汽车设计特点 (5)1.3课题的实际意义 (6)1.4 国内外自卸汽车的发展概况 (7)第2章轻型自卸车主要性能参数的选择 (13)2.1整车尺寸参数的确定 (13)2.2质量参数的确定 (14)2.3其它性能参数 (16)2.4本章小结 (16)第3章自卸车车厢的结构及设计 (17)3.1 自卸汽车车厢的结构形式 (17)3.1.1车厢的结构形式 (17)3.1.2车厢选材 (18)3.2车厢的设计规范及尺寸确定 (19)3.2.1车厢尺寸设计 (19)3.2.2车厢内框尺寸及车厢质量 (20)3.3车厢板的锁启机构 (17)3.4 本章小结 (17)第4章自卸举升机构的设计 (18)4.1自卸举升机构的选择 (18)4.1.1举升机构的类型 (18)4.1.2自卸汽车倾卸机构性能比较 (21)4.2举升机构运动及受力分析及参数选择 (23)4.2.1机构运动分析 (30)4.2.2举升机构受力分析及参数选择 (32)4.3本章小结 (26)第5章液压系统设计 (27)5.1液压系统工作原理及结构特点 (27)5.1.1工作原理 (27)5.1.2液压系统结构布置 (28)5.1.3 液压分配阀 (28)5.2油缸选型及计算 (29)5.3油箱容积及油管内径计算 (30)5.4取力器的设计 (31)5.5本章小结 (42)第6章副车架的设计 (43)6.1副车架的截面形状及尺寸 (43)6.2副车架前段形状及位置 (44)6.2.1 副车架的前端形状及安装位置 (44)6.2.2 纵梁及横梁的连接设计 (46)6.2.3 副车架及主车架的连接设计 (36)6.3副车架主要尺寸参数设计计算 (37)6.3.1副车架主要尺寸设计 (37)6.3.2副车架的强度刚度弯曲适应性校核 (37)6.4本章小结 (44)结论 (45)参考文献 (46)致谢 (47)第1章绪论1.1 课题的提出专用自卸车是装有液压举升机构,能将车厢卸下或使车厢倾斜一定角度,货物依靠自重能自行卸下或者水平推挤卸料的专用汽车。