模具热处理中的变形及预防措施
cr12mov热处理后加工变形

cr12mov热处理后加工变形
摘要:
1.cr12mov 材料特性
2.cr12mov 热处理过程
3.cr12mov 加工变形原因
4.减少cr12mov 加工变形的措施
正文:
CR12MOV 是一种高强度、高硬度、高韧性的冷作模具钢材料,由于其优异的性能,被广泛应用于各种冷作模具的制造。
然而,在经过热处理后,
CR12MOV 材料在加工过程中容易产生变形,这给模具的制造和使用带来了不少困扰。
下面我们来分析一下CR12MOV 热处理后加工变形的原因及应对措施。
首先,CR12MOV 材料的特性决定了它在热处理过程中容易产生变形。
CR12MOV 钢属于高碳合金钢,碳含量较高,使得钢的硬度和强度得到提高,但塑性和韧性降低。
在热处理过程中,碳原子和合金元素会发生扩散,从而导致晶粒长大和碳化物析出,使钢的硬度和强度进一步提高。
但同时,塑性和韧性会继续降低,这使得CR12MOV 在热处理后加工过程中更容易产生变形。
其次,CR12MOV 热处理过程中,由于温度、保温时间、冷却速度等因素的控制不当,可能导致热处理组织不均匀,从而使钢的性能发生不均匀变化,进一步加大加工变形的可能性。
针对CR12MOV 热处理后加工变形的问题,可以采取以下措施来减少变
形:
1.合理控制热处理工艺参数,如加热速度、保温时间、冷却速度等,以保证热处理组织均匀;
2.在加工过程中,采用适当的切削参数和刀具材料,以降低切削力和热量,减少加工过程中的变形;
3.对模具结构进行优化,尽量避免应力集中,以降低加工变形的风险;
4.在加工过程中,对模具进行适当的时效处理,以消除内应力,降低变形。
热处理淬火及变形
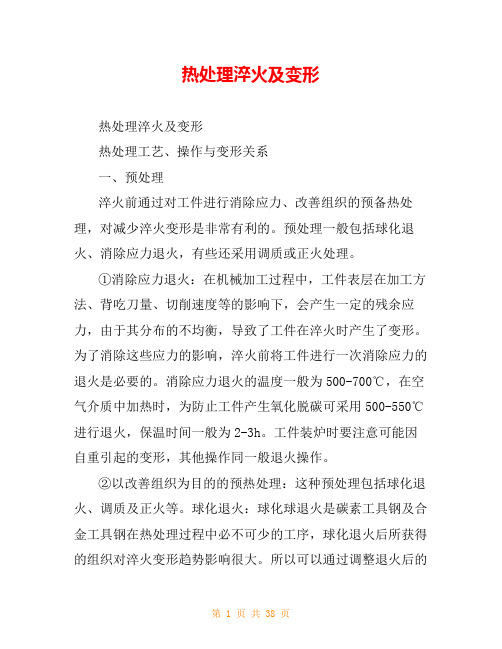
热处理淬火及变形热处理淬火及变形热处理工艺、操作与变形关系一、预处理淬火前通过对工件进行消除应力、改善组织的预备热处理,对减少淬火变形是非常有利的。
预处理一般包括球化退火、消除应力退火,有些还采用调质或正火处理。
①消除应力退火:在机械加工过程中,工件表层在加工方法、背吃刀量、切削速度等的影响下,会产生一定的残余应力,由于其分布的不均衡,导致了工件在淬火时产生了变形。
为了消除这些应力的影响,淬火前将工件进行一次消除应力的退火是必要的。
消除应力退火的温度一般为500-700℃,在空气介质中加热时,为防止工件产生氧化脱碳可采用500-550℃进行退火,保温时间一般为2-3h。
工件装炉时要注意可能因自重引起的变形,其他操作同一般退火操作。
②以改善组织为目的的预热处理:这种预处理包括球化退火、调质及正火等。
球化退火:球化球退火是碳素工具钢及合金工具钢在热处理过程中必不可少的工序,球化退火后所获得的组织对淬火变形趋势影响很大。
所以可以通过调整退火后的组织来减少某些工件有规律的淬火变形。
其他预处理:为减少淬火变形所采用的预处理方法有很多种,如调质处理、正火处理等。
针对工件产生淬火变形的原因及工件所用材料,合理地选用正火、调质等预处理对减少淬火变形是有效的。
但应对正火后引起的残余应力及硬度提高对机加工的不利影响应给予注意,同时调质处理对含WMn等钢可减少淬火时胀大,而对GCr15等钢种的减少变形作用不大。
在实际生产中要注意分清淬火变形产生的原因,即要分清淬火变形是由残余应力引起的还是由组织不佳引起的,只有这样才能对症处理。
若是由残余应力引起的淬火变形则应进行消除应力退火而不用类似调质等改变组织的预处理,反之亦然。
只有这样,才能达到减少淬火变形的目的,才能降低成本,保证质量。
以上各种预处理的具体操作同其他相应操作,此处不赘述。
二、淬火加热操作①淬火温度:淬火温度对工件的淬火变形影响很大。
其影响淬火变形趋势的一般规律如图所示。
常用模具热处理质量检验技术

常用模具热处理质量检验技术模具热处理质量检验应按国家标准、行业标准或企业内控标准规定的程序,对工艺文件或技术标准中规定的项目进行严格的检查,并监督工艺纪律的执行情况,防止和减少废品与返工件的产生。
对批量生产的模具,必须在首件或首批检验合格后才可继续生产。
检验的项目和检验的方法,应按图样、工艺卡片和技术标准的规定执行。
对于没有明确规定的,可按相应的国家标准或客户要求进行检测。
模具热处理后的检验主要有四个方面:外观、变形、硬度、金相。
1)热作模具热处理质量检验如下:①外观检验。
模具任何部位不得有肉眼可见的裂纹,关键部位应用5~10倍的放大镜细看。
模具表面不应有明显的磕碰伤痕。
②变形检验。
用刀口形直尺或平尺观测模面的平面度,并用塞尺测量,一般规定变形量应小于留磨量的1/3~1/2。
③硬度检验。
首先将待测部位磨光或抛光,一般用洛氏硬度计检测3~4点。
根据情况,也可用维氏硬度计、肖氏硬度计、里氏硬度计检查。
如果硬度值超高,应多检测几点,尽可能准确。
根据硬度值,做出是否要提高回火温度的决定。
如果硬度偏低,应在原位置继续打磨,继续检测。
如果硬度还低,再用手提小砂轮做钢号火花鉴别,一定找出致使硬度达不到工艺要求的真正原因。
④金相检验。
热作模具的金相检验,可按JB/T 8420—2008《热作模具钢显微组织评级》执行。
2.通常热作模具钢马氏体合格级别为2~4级。
另外,有些热作模具钢还要进行蒸汽处理、氧氮共渗、TiN涂层、渗硼、氮碳共渗等表面强化处理,则应按相关技术标准验收,重点检测渗层厚度、表面硬度和金相组织三大项。
2)冷作模具热处理质量检验如下:①外观检验。
模具表面不允许有磕碰、划伤、烧毁及严重的氧化脱碳、腐蚀麻点及锈蚀现象,肉眼观察不得有裂纹,表面必须光洁,孔眼特别是不通孔内不得堵泥和盐渍,拴绑的钢丝等附着物必须解除。
②变形检验。
模具热处理后变形量不得超过留磨量的1/3~1/2。
③硬度检查。
模具热处理后应全部进行硬度检查。
铝合金压铸模具龟裂的原因及预防措施

铝合金压铸模具龟裂旳原因及防止措施铝合金压铸模具引起龟裂旳重要原因:(1)模具在压铸生产过程中,铝料温度偏高;(2)模具在压铸生产过程中脱模剂喷洒不合理;(3)模具热处理不理想,重要是硬度(硬度应不不不小于HRC--47);(4)模具钢材质量不好, 推荐使用8407或精练H13或更高级材料;(5)模具设计之冷却系统或运水操作不好。
初期龟裂一般状况下是因毛坯锻打起锻温度过高(俗称过烧)过烧是一种不可补救旳缺陷因此应严格控制毛坯制造过程中旳起锻温度.淬火工艺上也如此,并应严格控制加热时间防止脱炭。
材料选择好之后就是热处理了, 在生产了一定旳数量后注意去应力, 尚有就是设计合理, 尽量防止应力集中, 注意R角旳大小控制!在大概1万模次旳时候,模具要注意回火去应力,内力集中、加工残存应力未清除、压铸过程热应力未得到很好清除, 总之龟裂就是应力集中旳体现, 可以采用多次回火清除应力从而可以增长模具寿命铝合金压铸模具在生产一段时间后会龟裂旳原因重要有如下几点:(1)模具温度偏高应力过大(2)模具模仁材料没有使用8407,skd61及其他高品质旳材料,(3)模具热处理硬度过高或过低,4)与否认期保养?5k times1 回火, 15k times1 回火30k times..........預防壓鑄模龜裂問題﹐提高模具使用壽命﹐要做好如下几點﹕1.壓鑄模成型部位(動﹑定模仁﹑型芯)熱處理规定﹕硬度要保証在HRC44~48 (材料可選用SKD61或8407或高品质热作钢)2.模具在壓鑄生產前應進行充足預熱作業,其作用如下﹕2.1使模具達到較好旳熱平衡﹐使鑄件凝固速度均勻并有助于壓力傳遞.2.2保持壓鑄合金填充時旳流動性﹐具有良好旳成型性和提高鑄件表面質量.2.3減少前期生產不良﹐提高壓鑄生產率.2.4减少模具熱交變應力﹐提高模具使用壽命.详细規范如下﹕合金种類模具預熱溫度(℃)鋁合金180~300鋅合金150~2003.新模具在生產一段時間后﹐熱應力旳積累是直接導致模仁產生龜裂旳原因﹐為減少熱應力﹐投產一定時間后旳模仁及滑塊應進行消除熱應力旳回火處理.详细需要消除熱應力旳生產模次如下﹕模具類型鋁合金鋅合金第一次回火<模次<10000模次第二次回火<10000模次<0模次第三次回火<30000模次<50000模次铝合金压铸模承受巨大交变工作应力, 必须从模材, 设计, 加工, 热处理及操作各方面加以注意才能得到长旳模具寿命, 如下是为使模具能达长寿命旳21点要诀:1.高品质模材2.合理设计模壁厚及其他模具尺寸3.尽量采用镶件4.在也许条件下选用尽量大旳转角R5.冷却水道与型面及转角旳间距必须足够大6.粗加工后应去应力回火7、对旳有热处理, 淬火冷却须足够快8、彻底打磨清除EDM硬质层9、型面不可高度抛光10、模具型面应经氧化处理11.如选氮化, 渗层不能太深12.以对旳旳措施预热模具至推荐旳温度13.开始压铸5~20件应使用慢旳锤头速(根据产品旳大小)14.在得到合格产品旳前提下尽量减少铝液温度15.尽量不使用过高旳铝液注射速度及过高旳铸造比压16.保证模具得到合适冷却, 冷却水旳温度应保持在40~50℃17、临时停机, 应尽量合模并减小冷却水量或关闭运水, 防止再开机时模具承受热冲击18、当模型面在最高温度时应关冷却液19、不使用过多旳喷脱模剂20、在一定数量后旳压铸后去应力回火21. 尽量使用模温控制装置。
模具钢材表面脱碳的原因及预防措施

模具钢在热处理时由于保护不良,模具表面脱
碳,使模具淬火后的硬度大大降低,严重影响模具的使用寿命。
一、产生的原因
1、模具在箱式或井式电阻炉中加热时,模具表面产生脱碳。 2、在盐浴炉加热
时,盐浴老化,未能很好地进行脱氧处理。 3、模具的工、夹具向盐浴中带进铁锈。
二、预防措施
ccw,压铸模具钢材ht,要采用保护气氛或保护措施(
如涂料保护等)。 2、盐浴加热时,盐的质量必须符合标准的要求,并经300~50
0℃×2~4h的烘干脱水处理。 3、盐浴应定期脱氧,严格控制盐浴中
的氧化物含量,并定期清除炉渣,以免盐浴中氧化物增长过快。 4、在有条件的情况下
,应尽量采用真空加热。模具钢
预防热处理变形的八项措施

预防热处理变形的八项措施
为了提高金属工件或模具的使用性能,可以对金属件进行热处理工艺,但是在热处理过程中,如果没有按照合理的要求,很容易导致金属工件或模具经过热处理后而变形,那导致工件热处理后变形的原因是什么,采取哪些措施进行预防。
八大措施预防热处理变形:
1、合理选材。
对精密复杂模具应选择材质好的微变形模具钢(如空淬钢),对碳化物偏析严重的模具钢应进行合理锻造并进行调质热处理,对较大和无法锻造模具钢可进行固溶双细化热处理。
2、模具结构设计要合理,厚薄不要太悬殊,形状要对称,对于变形较大模具要掌握变形规律,预留加工余量,对于大型、精密复杂模具可采用组合结构。
3、精密复杂模具要进行预先热处理,消除机械加工过程中产生的残余应力。
4、合理选择加热温度,控制加热速度,对于精密复杂模具可采取缓慢加热、预热和其他均衡加热的方法来减少模具热处理变形。
5、在保证模具硬度的前提下,尽量采用预冷、分级冷却淬火或温淬火工艺。
6、对精密复杂模具,在条件许可的情况下,尽量采用真空加热淬火和淬火后的深冷处理。
7、对一些精密复杂的模具可采用预先热处理、时效热处理、调质氮化热处理来控制模具的精度。
8、在修补模具砂眼、气孔、磨损等缺陷时,选用冷焊机等热影响小的修复设备以避免修补过程中变形的产生。
(钢铁英才网)。
模具开裂的主要原因分析及应对措施

一、模具开裂的主要原因分析:设计工艺:模具强度不够。
刀口间距太近,模具结构不合理,模板块数不够无垫板垫脚。
线割处理不当:拉线线割,间隙不对,没作清角。
冲床设备的选用:冲床吨位,冲裁力不够,调模下得太深。
脱料不顺:生产前无退磁处理,无退料梢,生产中有断针断弹簧等卡料。
落料不顺:组装模时无漏屎,或滚堵屎,垫脚堵屎。
生产意识:叠片冲压,定位不到位,没使用吹气板有裂纹仍继续生产。
模具材质问题有可能在后续加工中导致开裂。
锻造工艺部合理,金相组织较差。
锻造后的退火工艺不当。
(若相当正火,在进行热处理会造成二次淬火裂纹)模具研磨平面及粗糙度不合适。
模具结构不合理。
线切割处理不当二、相关应对措施冲模是小的形式:冲模是小形式主要为磨损失效,变形失效,裂纹失效和压伤失效等。
由于冲压形态不同,工作条件不同,影响冲模寿命的因素是多方面的。
下面就冲模的设计使用等方面进行综合分析,并提出相应的改进措施。
(一)冲压设备:冲压设备(如压力机)的精度与刚性对冲模寿命的影响极为重要。
冲压设备的精度高、刚性好,冲模寿命大为提高。
例如:复杂硅钢片冲模料为Cr12MoV,在普通开式压力机上使用,平均磨损寿命1-3万次,而新式精密压力机上使用,冲模的复磨寿命可达6-12万次。
尤其是小间隙冲模、硬质合金冲模及精密冲模必须选择高精度、刚性好的压力机,否则,讲会降低模具寿命,严重者还会损坏模具。
(二)模具设计:(1)、模具的导向机构精度准确可靠的导向,对于减少模具工件的磨损。
,避免凸,凹模压伤影响极大,尤其是小间隙冲模,复合模和多工位级进模则更为有效。
为提高模具寿命,必须根据工序性质和零件精度等腰求,正确选择导向。
形式和确定导向机构的精度。
一般情况下,导向机构的精度应高于凸凹模配合精度。
(2)、模具(凸凹模)刃口几何参数形状,配合间隙和圆角半径不仅对冲压件成型有较大的影响,而且对于模具的磨损及寿命也影响很大,如模具的配合间隙直接影响冲裁件质量和模具寿命。
减少淬火变形和防止淬火开裂的措施
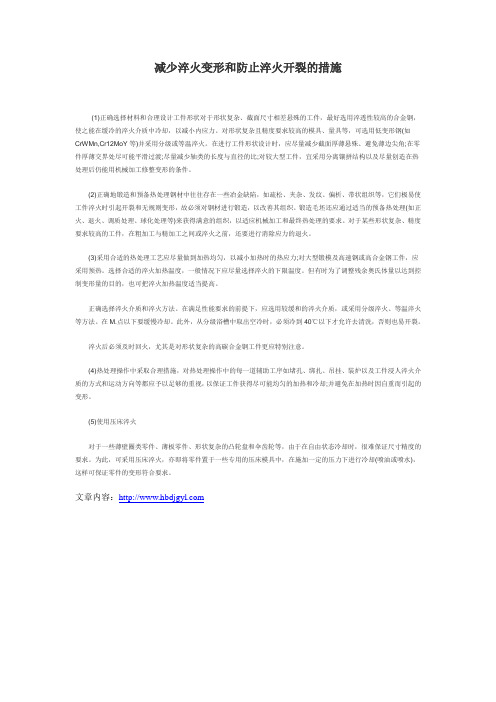
减少淬火变形和防止淬火开裂的措施(1)正确选择材料和合理设计工件形状对于形状复杂、截面尺寸相差悬殊的工件,最好选用淬透性较高的合金钢,使之能在缓冷的淬火介质中冷却,以减小内应力。
对形状复杂且精度要求较高的模具、量具等,可选用低变形钢(如CrWMn,Cr12MoY等)并采用分级或等温淬火。
在进行工件形状设计时,应尽量减少截面厚薄悬殊、避免薄边尖角;在零件厚薄交界处尽可能平滑过渡;尽量减少轴类的长度与直径的比;对较大型工件,宜采用分离镶拼结构以及尽量创造在热处理后仍能用机械加工修整变形的条件。
(2)正确地锻造和预备热处理钢材中往往存在一些冶金缺陷,如疏松、夹杂、发纹、偏析、带状组织等,它们极易使工件淬火时引起开裂和无规则变形,故必须对钢材进行锻造,以改善其组织。
锻造毛坯还应通过适当的预备热处理(如正火、退火、调质处理、球化处理等)来获得满意的组织,以适应机械加工和最终热处理的要求。
对于某些形状复杂、精度要求较高的工件,在粗加工与精加工之间或淬火之前,还要进行消除应力的退火。
(3)采用合适的热处理工艺应尽量做到加热均匀,以减小加热时的热应力;对大型锻模及高速钢或高合金钢工件,应采用预热。
选择合适的淬火加热温度,一般情况下应尽量选择淬火的下限温度。
但有时为了调整残余奥氏体量以达到控制变形量的目的,也可把淬火加热温度适当提高。
正确选择淬火介质和淬火方法。
在满足性能要求的前提下,应选用较缓和的淬火介质,或采用分级淬火、等温淬火等方法。
在M.点以下要缓慢冷却。
此外,从分级浴槽中取出空冷时,必须冷到40℃以下才允许去清洗,否则也易开裂。
淬火后必须及时回火,尤其是对形状复杂的高碳合金钢工件更应特别注意。
(4)热处理操作中采取合理措施,对热处理操作中的每一道辅助工序如堵孔、绑扎、吊挂、装炉以及工件浸人淬火介质的方式和运动方向等都应予以足够的重视,以保证工件获得尽可能均匀的加热和冷却;并避免在加热时因自重而引起的变形。
模具热处理变形分析及对策

2 模 具材 料 的影 响及 对 策
影 响模 具 的质量 。
C 1 Mo 钢 中含 有 较 多 共 晶碳 化 物 , r2 V 且呈 带状 和块状
模 具 制造 的第 一 步 首 先是 选 材 , 质 的优 劣直 接 分布 。模 具 的变 形 就是 因为模 具 钢 中存在 不均 匀性碳 材 化 物 ,碳 化 物 的 膨 胀 系 数 比钢 的基 体 组 织 小 3%左 0
( ) 具 选 材 的影 响 。 1模 某机 械 厂 从 经 济 和 热 处 理 简便 考 虑 ,选 择 T 0 1A
硬 6 6HR 热 值 低 、 造 难 度 大 。模 具 热 处 理 后 产 生 变 形 将 严 重 钢 制 造较 复 杂 的冷 挤压 模 具 , 度要 求 5~ 0 C, 制 无 影 响 模 具 的质 量 和 使 用 寿 命 , 此 , 少 和 预 防 模 处 理后 模 具 硬 度 符合 技 术 要 求 ,但 模 具 变形 较 大 , 因 减 造 具 热 处 理 变 形 是 广 大 模 具 热 处 理 工 作 者 的 重 要 研 法 使用 , 成 模 具报 废 。 () 策 。 2对 究课题 。 众 所 周 知 , 具 在 热 处 理 时 , 别 是 在 淬 火 过 程 模 特
形 的原 因进行 分析 , 出减 少 变形的 对策 。 析 ; 对策
Ana y i nd S l to o eo m a i n l ss a o u i n f r D f r to
o e & M od He t f Di l a Tr a m e e t nt 【 s a tI i at l, n l e ed fr ainta cue yde& mo aeilt cue Ab t c]nt s r c a a zdt eom t t a sdb i r h ie y h o h l m t a,r tr d r su
cr12mov热处理后加工变形

cr12mov热处理后加工变形摘要:1.概述CR12MOV 材料2.CR12MOV 的热处理过程3.热处理后的加工变形现象4.加工变形的原因分析5.预防和解决加工变形的方法正文:CR12MOV 是一种高性能合金工具钢,广泛应用于制造各种冷作模具和工具。
在实际应用中,为了提高其硬度和耐磨性,通常需要对其进行热处理。
然而,在热处理后,CR12MOV 材料往往会出现加工变形的现象,给后续加工带来困难。
本文将分析CR12MOV 热处理后的加工变形现象,探讨其原因,并提出相应的预防和解决方法。
CR12MOV 的热处理过程主要包括淬火和回火两个阶段。
淬火是将CR12MOV 材料加热至某一温度并保持一段时间,随即浸入淬冷介质(冷却速度较快的介质)中快速冷却,以提高其硬度。
回火是将经过淬火的材料重新加热至某一温度,并保持一段时间,以降低其内部应力,提高韧性。
这两个过程对CR12MOV 材料的组织结构和性能有着重要影响。
在热处理后,CR12MOV 材料可能出现的加工变形现象包括弯曲、扭曲、裂纹等。
这些变形现象会对模具和工具的使用造成严重影响,甚至导致其报废。
因此,分析加工变形的原因,寻找有效的预防和解决方法具有重要意义。
加工变形的原因分析:1.残余应力:热处理过程中,材料内部会产生很大的应力,如果这些应力没有得到有效释放,会导致材料在加工过程中产生变形。
2.温度差异:热处理后的材料在加工过程中,由于内外层温度差异,会产生热胀冷缩现象,导致材料变形。
3.不均匀热处理:热处理过程中,如果温度分布不均匀,会导致材料内部组织结构不均匀,从而影响其加工性能。
预防和解决加工变形的方法:1.控制热处理温度和时间,确保热处理过程的均匀性,减小内部应力。
2.采用适当的冷却介质和冷却速度,以控制淬火过程中的温度梯度,降低变形风险。
3.在加工前进行充分的预热,使材料内外层温度趋于一致,减小热胀冷缩引起的变形。
4.采用合理的加工工艺和刀具,尽量减小切削力和切削热对材料的影响。
影响模具热处理质量的因素及预防措施

m m。
I 模 具 热 处 理
影响模具热处理质量的因素及预防措施
日照市 技师学 院 ( 山东 2 7 6 8 2 6 ) 刘招 安
一
、
热处理工艺因素的影响及防止措施
和 加 热 温 度 不 同 , 向 炉 内 送 入 可 以 控 制 的 保 护 气
在 热 处 理 的 过 程 中 , 由 于 热 处 理 工 艺 控 制 不 当 ,使 工 件 产 生某 些 缺 陷 ,如 氧化 、脱 碳 、过 热 、 过烧 、硬 度 不 足 、 变形 与 开 裂 等 。对 热 处 理 质量 影 响很 大 ,甚 至 造 成 工件 报 废 。其 中氧 化 与 脱 碳 、变 形 与开 裂 是 最 常 见的 热 处理 缺 陷 。
氛 ,使工件表面不氧化 、脱碳 ,也不渗碳 。 ( 4 )采用真空炉加热 它不但能防止氧化与脱
碳 ,还 能 使 工件 净 化 ,提高 性 能 。但设 备 复 杂 ,应
用较 少 。
2 . 变形与开裂
淬火 中变形 与开裂主要是淬火 时形成的内应 力 引起的 。形成内应 力的原因主要是热应 力和相变应 力。热应力是 由于工件在加热和冷却时内外温度不
构 复 杂 ,曲面 较 多 ,淬 火 轨迹 多变 , 目前 国内 激 光 淬 火 过 程 中的 手 动采 点记 录 后进 行 简单 编程 的 方式
( 即示教模式 )不适用汽车模具生产对效率的极大
要 求 ,制 约 了激 光热 处 理 在 汽车 覆 盖 件 模具 制造 中 的推 广 应 用 ,无 论从 设 备 的 完善 ,软 件 的 配套 ,还
一
1 . 氧化与脱碳
氧化与脱碳是工件在加热时 ,由于加热炉 中介 质控制不好而 出现的缺陷。 钢在氧化介质中加热时 ,会发生氧化而在表面
模具热处理变形的预防措施

X a U R n—dn LN C a —pn a , I h o ig(C a gh ol eo cec T cn l y C a gh 1 5 0 C i ) h n suC l g f i e& eh oo , h n su2 5 0 , hn e S n g a
【 摘要】 通过模具热处理变形的原 因分析 , 出有关预防措施, 提 以提高冲模寿命。
模具热处理变形的预防措施
徐冉丹 林朝平 ( 常熟理工学院 , 常熟 250 ) 150
Th rv ni n me s r sf rd f r t n o e t r a me to i & mo l e p e e t a u e o e o ma i f a e t n n de o o h t ud
中图分 类 号 : G 8 文献标 识 码 : T 3 A
1 热处理 变形原 因的分析
模具零件淬火时 由于热应力与组织应力的综合作 用引起尺 热与冷却过程中因加热与冷却速度的差异 , 就会 引起了零件体积
艺, 致力将模具热处理变形严格控制在最小限度之内。
2热处理变形的预防措施
钢材的冶金质 量事关重要。正确选择模具钢材 ,是减少 冲
关 键词 :热处 理 ; 形 ;预 防措施 ; 因分 析 变 原
[bt c】 Bs e a e nl i o d o ai ea ta et ipoo d hpe no A s at a d nh a a sfr e r tno tr t n s r s re i r e O t cs a ys f m o fh e m , p e t e v n t
寸和形状 的偏差。由于零件的几何形状 、 截面尺寸不 同, 在淬火加 2 1正确 选择模 具钢 材 .
浅谈精密模具的热处理变形及预防技术

模 具在 热处理 时 ,特别 是 在淬 火过 程 中 , 由 下 , 应尽 量 减少 模 具厚 薄 悬殊 , 构不 对 称 。 模 结 在 5 预防措 施 2 于模 具截面 各部 分加热 和冷 却速 度 的不一 致而 引 具 的厚薄 交界 处 ,尽可 能采 用平 滑过 渡等 结构 设 52 ’l适 当降低 淬火 温 度 。淬 火加 热 温度 越 起的 温度差 , 之组织 转变 的 不等 时性等 原 因 , 加 使 计 。根 据模具 的变 形规 律 , 留加 工余 量 , 预 在淬 火 高 , 留奥 氏体量 越大 , 残 因此选 择适 当的淬 火加 热 得 模具 截面 各部 分体积 胀缩 不均 匀 ,组织 转变 的 后不 致于 因为模 具变形 而使 模具报 废 。 温度 是减 少模 具缩 小的 重要措 施 。一般在 保证 模 不 均 匀 , 而引 起 “ 织应 力 ” 从 组 和模 具 内外 温 差 所 引起 的热应 力。 当其 内应 力超 过模 具 的屈 服极 限 时 就 会 引起模 具 的变 形 。 因此 , 减少 和控制精 密 复 3模 具制造 工序 及残 余应 力的影 响
维普资讯
科
技I 广I 术I 场
浅谈精密模具 的热处理变形及预 防技术
刁 乃 新
( 内蒙 古霍 林 河 露天 煤 业股 份 公 司煤 炭 加 工公 司 , 内蒙 古 霍 林 河 0 9 0 ) 2 20
摘 要 : 具 热 处理 变 形 是模 具 处理 过 程 的 主要 缺 陷之 一 , 一 些精 密复 杂模 具 , 因 热 处理 变形 而报 废 , 模 对 常 因此 控 制 精 密 复 杂 模具 的 变形 一直 成 为 热 处理 生产 中 的 关键 问 题 。
精密模具热处理变形及预防

产 中的关键 问题 。 阐述 了模 具 热 处理 变形产 生 的原 因以及 解决 的 办法 。
关键词 : 模具; 热处理 ; 变形; 淬火
中图分 类号 : G124 T 6 . 文献 标识 码 : B 文章 编 号 :6 1 58 2 0 )4—8 17 —68 (0 60 2—0 3
.
Ke r s modn o l o r cs ig;dso t n;h r e ywo d : lig t ;h tp o esn i ri t o ad n
众所周 知 , 具 在热 处理 时 , 模 特别 是在淬 火 过程 中, 由于模 具截 面 各 部分 加 热 和 冷 却 速度 的不 一 致
H o o e sng Tr nso m fPr c s o d ng To la e e to tPr c s i a f r o e ieM l i o nd Pr v n i n
W a gJq n n iu
( e igVoai a & T cncln t ueo n ut , ei g1 0 4 , hn ) B rn ct n l o eh i si t f d sr B in 0 0 2 C ia aI t I y i
Ab t c : eh tp o e s g ta so m f odn o so eo h i lm i st a h ligt l a de sr tTh o r c si r n fr o l ig t l n f eman be s h tt emodn n ls a n m o i t h o h
该出现较大变形 。我们对变形严重的模具进行金相 分析 发现 , 具钢 中含 有大量 共 晶碳 化 物 , 模 且呈 带 状
和块 状分 布 。
模具线切割变形及热处理工艺控制
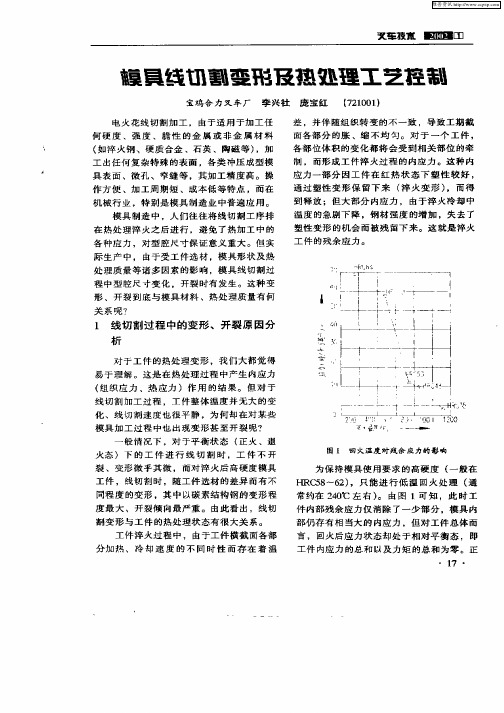
檩 具线 Ⅶ 载 变 及 热 处理 工 艺 控 铷
宝鸡 合 力 叉 车 厂 李 兴 社
电 火 花 线 切 割 加 工 , 由 于 适 用 于加 工 任 何 硬 度 、 强 度 、 脆 性 的 金 属 或 非 金 属 材 料
庞 宝 红 (2 0 1 7 10 ) 差 ,并 伴 随 组 织 转 变 的 不 一 致 ,导 致 工 期 截
面 各 部 分 的 胀 、缩 不 均 匀 。 对 于 一 个 工 件 ,
( 淬 火 钢 、 硬 质 合 金 、石 英 、 陶 磁 等 ) 如 ,加 工 出任 何 复 杂 特 殊 的表 面 ,各 类 冲 压 成 型 模
具 表 面 、微 孔 、 窄 缝 等 ,其 加 工 精 度 高 。 操
各 部 位 体 积 的 变 化 都 将 会 受 到 相 关 部 位 的 牵
在 热 处 理 淬 火 之 后 进 行 , 避 免 了热 加 工 中 的 各 种 应 力 ,对 型 腔 尺 寸 保 证 意 义 重 大 。但 实
通 过 塑性 变 形 保 留 下 来 ( 火 变 形 ) 淬 ,而 得 到 释 放 ;但 大 部 分 内应 力 ,由 于 淬 火 冷却 中 温 度 的 急 剧 下 降 ,钢 材 强 度 的 增 加 ,失 去 了 塑 性 变 形 的 机会 而 被 残 留下 来 。 这 就 是 淬 火
同程 度 的变 形 ,其 中 以碳 素 结 构 钢 的 变 形 程
度 最 大 、开 裂 倾 向 最 严 重 。 由 此 看 出 ,线 切 割 变 形 与 工 件 的 热 处 理 状 态 有 很 大关 系 。
件 内部残余应 力仅 消 除 了一少部分 ,模具 内 部 仍 存有 相 当大 的 内 应 力 ,但 对 工件 总 体 而 言 ,回火后应 力状 态却处 于相对平 衡态 ,即
热处理变形产生的原因及控制方法
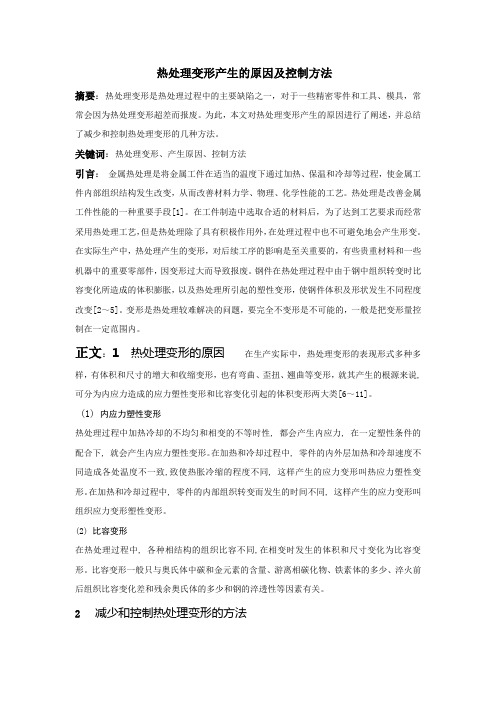
热处理变形产生的原因及控制方法摘要:热处理变形是热处理过程中的主要缺陷之一,对于一些精密零件和工具、模具,常常会因为热处理变形超差而报废。
为此,本文对热处理变形产生的原因进行了阐述,并总结了减少和控制热处理变形的几种方法。
关键词:热处理变形、产生原因、控制方法引言:金属热处理是将金属工件在适当的温度下通过加热、保温和冷却等过程,使金属工件内部组织结构发生改变,从而改善材料力学、物理、化学性能的工艺。
热处理是改善金属工件性能的一种重要手段[1]。
在工件制造中选取合适的材料后,为了达到工艺要求而经常采用热处理工艺,但是热处理除了具有积极作用外,在处理过程中也不可避免地会产生形变。
在实际生产中,热处理产生的变形,对后续工序的影响是至关重要的,有些贵重材料和一些机器中的重要零部件,因变形过大而导致报废。
钢件在热处理过程中由于钢中组织转变时比容变化所造成的体积膨胀,以及热处理所引起的塑性变形,使钢件体积及形状发生不同程度改变[2~5]。
变形是热处理较难解决的问题,要完全不变形是不可能的,一般是把变形量控制在一定范围内。
正文:1热处理变形的原因在生产实际中,热处理变形的表现形式多种多样,有体积和尺寸的增大和收缩变形,也有弯曲、歪扭、翘曲等变形,就其产生的根源来说, 可分为内应力造成的应力塑性变形和比容变化引起的体积变形两大类[6~11]。
(1) 内应力塑性变形热处理过程中加热冷却的不均匀和相变的不等时性, 都会产生内应力, 在一定塑性条件的配合下, 就会产生内应力塑性变形。
在加热和冷却过程中, 零件的内外层加热和冷却速度不同造成各处温度不一致,致使热胀冷缩的程度不同, 这样产生的应力变形叫热应力塑性变形。
在加热和冷却过程中, 零件的内部组织转变而发生的时间不同, 这样产生的应力变形叫组织应力变形塑性变形。
(2) 比容变形在热处理过程中, 各种相结构的组织比容不同,在相变时发生的体积和尺寸变化为比容变形。
比容变形一般只与奥氏体中碳和金元素的含量、游离相碳化物、铁素体的多少、淬火前后组织比容变化差和残余奥氏体的多少和钢的淬透性等因素有关。
热处理常见缺陷

热处理常见缺陷在热处理工艺中淬火工序造成的废品率往往较高,这主要是在淬火过程中,同时形成较大的热应力与组织应力,此外,由于材料内在的冶金缺陷、选材不当、错料、设计上的结构工艺性差、冷、热加工过程中形成的缺陷等因素,均容易在淬火、回火工艺中暴露出来,因此对零部件淬火、回火后的缺陷必须进行系统的分折与调査。
淬火缺陷与预防钢件淬火时最常见的缺陷有淬火变形、开裂、氧化、脱碳、硬度不足或不均匀、表面腐蚀、过烧、过热及其他按质量检查标准规定金相组织不合格等。
1.淬火变形与淬火裂纹在实际生产中,应该根据淬火变形与淬火裂纹的形成原因采取有效的预防措施。
(1)尽量做到均匀加热及正确加热工件形状复杂或截面尺寸相差悬殊时,常因加热不均匀而变形。
为此,工件在装炉前,对不需淬硬的孔及截面突变处,应采用石棉绳堵塞或绑扎等办法,以改善其受热条件,对一些薄壁圆环等易变形零件,可设计特定淬火夹具。
这些措施既有利于加热均匀,又有利于冷却均匀。
工件在炉内加热时,应均匀放置,防止单面受热,应放平,避免工件在髙温塑性状态因自重而变形。
对细长零件及袖类零件尽量采用井式炉或盐炉垂直悬挂加热。
限制或降低加热速度,可减少工件截面温差,使加热均匀。
因此对大型锻模、髙速钢及高合金钢工件,以及形状复杂、厚薄不匀、要求变形小的零件,一般都采用预热加热或限制加热速度的措施。
合理选择淬火加热温度,也是减少或防止变形、开裂的关键。
选择下限淬火温度,减少工件与淬火介质的温差,可以降低淬火冷却高温阶段的冷却速度,从而可以减少淬火冷却时的热应力。
另外,也可防止晶粒粗大。
这样可以防止变形开裂。
有时为了调节淬火前后的体积变形量,也可适当提高淬火加热温度。
例如CrWMn、Cr12Mo等高碳合金钢,常利用调整加热温度,改变其马氏体转变点以改变残余奥氏体含量,以调节零件的体积变形。
(2)正确选择冷却方法和冷却介质的基本原则尽可能采用预冷,即在工件淬入淬火介质前,尽可能缓慢地冷却至Ar附近,以减少工件内温差。
模具热处理常见变形原因及控制措施
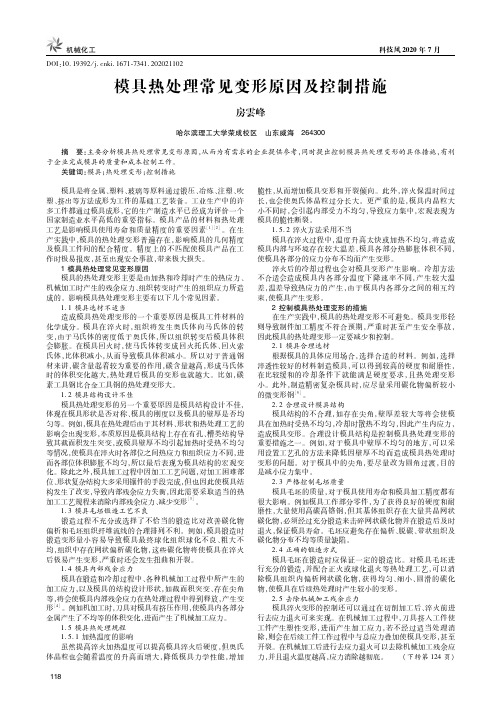
44模具是将金属)塑料)玻璃等原料通过锻压)冶炼)注塑)吹 塑)挤出等方法成形为工件的基础工艺装备# 工业生产中的许 多工件都通过模具成形"它的生产制造水平已经成为评价一个 国家制造业水平高低的重要指标# 模具产品的材料和热处理 工艺是影响模具使用寿命和质量精度的重要因素-$.-). # 在生 产实践中"模具的热处理变形普遍存在"影响模具的几何精度 及模具工件间的配合精度# 精度上的不匹配使模具产品在工 作时极易报废"甚至出现安全事故"带来极大损失#
%模具热处理常见变形原因 模具的热处理变形主要是由加热和冷却时产生的热应力) 机械加工时产生的残余应力)组织转变时产生的组织应力所造 成的# 影响模具热处理变形主要有以下几个常见因素# $&$ 模具选材不适当 造成模具热处理变形的一个重要原因是模具工件材料的 化学成分# 模具在淬火时"组织将发生奥氏体向马氏体的转 变"由于马氏体的密度低于奥氏体"所以组织转变后模具体积 会膨胀# 在模具回火时"使马氏体转变成回火托氏体)回火索 氏体"比体积减小"从而导致模具体积减小# 所以对于普通钢 材来讲"碳含量起着较为重要的作用"碳含量越高"形成马氏体 时的体积变化越大"热处理后模具的变形也就越大# 比如"碳 素工具钢比合金工具钢的热处理变形大# $&) 模具结构设计不佳 模具热处理变形的另一个重要原因是模具结构设计不佳" 体现在模具形状是否对称)模具的刚度以及模具的壁厚是否均 匀等# 例如"模具在热处理后由于其材料)形状和热处理工艺的 影响会出现变形"本质原因是模具结构上存在有孔)槽类结构导 致其截面积发生突变"或模具壁厚不均引起加热时受热不均匀 等情况"使模具在淬火时各部位之间热应力和组织应力不同"进 而各部位体积膨胀不均匀"所以最后表现为模具结构的宏观变 化# 除此之外"模具加工过程中因加工工艺问题"对加工困难部 位)形状复杂结构大多采用镶件的手段完成"但也因此使模具结 构发生了改变"导致内部残余应力失衡"因此需要采取适当的热 加工工艺规程来消除内部残余应力)减少变形-(. # $&( 模具毛坯锻造工艺不良 锻造过程不充分或选择了不恰当的锻造比对改善碳化物 偏析和毛坯组织纤维流线的合理排列不利# 例如"模具锻造时 锻造变形量小容易导致模具最终球化组织球化不良)粗大不 均"组织中存在网状偏析碳化物"这些碳化物将使模具在淬火 后极易产生变形"严重时还会发生扭曲和开裂# $&3 模具内部残余应力 模具在锻造和冷却过程中)各种机械加工过程中所产生的 加工应力"以及模具的结构设计形状"如截面积突变)存在尖角 等"将会使模具内部残余应力在热处理过程中得到释放"产生变 形-3. # 例如机加工时"刀具对模具有挤压作用"使模具内各部分 金属产生了不均等的体积变化"进而产生了机械加工应力# $&5 模具热处理规程 $&5&$ 加热温度的影响 虽然提高淬火加热温度可以提高模具淬火后硬度"但奥氏 体晶粒也会随着温度的升高而增大"降低模具力学性能"增加
模具热处理中失效变形的原因及其对策

回火 常规 热处 理 , 温度 要求 HR 5 , C 7 仅能 拉深 10 00 件 即早期 失 效 ,后 改 为 T O IA钢 采用 淬 火+ 中温 回 火 后 硬度 为 HR 5 , 均 寿命 达 4 0 C5平 0 0次 。 而后又 改 为 3 0 4 0 回火 , 其 硬 度 在 HR 4 , 寿命 8 ~ 0℃ 使 C8则 可 达 6 0 ~ 0 0次 。而 C l Mo 00 80 r2 V钢制 冲头 ,冲厚
识。
、
热 处 理 中 模 具 的 失 效 变 形 的 原 因 及 影 响
因素
由于模 具各 处 厚 薄不 均 及 存在 尖 锐 圆角 等 因 素 . 以在淬火 时 引起 模 具各部 位之 间 的热应力 和 所
组织 应力 的不 同 ,导 致各 部位体 积膨 胀 的不 同 , 使
模具 淬火后 产生 失效变 形 。 中常见 的模 具失效 的 其
管理 。
维普资讯
第2 2卷第 1 期
彭 刚 模 具 热 处 理 中 失 效变 形 的原 因 及其 对 策
6 1
正 确 的金 相 组织 , 而应 力 消 除程 度 又与 温 度 、 间 时 1 热 处理 对模 具 失效 变形 的影响 因素 . 热 处理 是 以“ 热—— 保 温—— 冷却 ” 大 隐 加 三 成 正 比关系 ( 图 1 。 见 )
形式 、 因如表 l 示 。 原 所
正 是 因为 热处 理 技 术与 模 具 质量 有 十 分密 切
表 1 模 具 失效的形 式 、 因及 对策 原
收稿 日期 :0 7 0 — 5 20 — 1 0 作者简介 : 刚( 9 9 )男 , 彭 1 5 一 , 湖南岳 阳人 , 阳工 业技 术学院一级实 习指导教师。主要研 究方 向: 岳 模具设计与制造及 工程
- 1、下载文档前请自行甄别文档内容的完整性,平台不提供额外的编辑、内容补充、找答案等附加服务。
- 2、"仅部分预览"的文档,不可在线预览部分如存在完整性等问题,可反馈申请退款(可完整预览的文档不适用该条件!)。
- 3、如文档侵犯您的权益,请联系客服反馈,我们会尽快为您处理(人工客服工作时间:9:00-18:30)。
模具热处理中的变形及预防措施模具热处理变形是模具处理过程的主要缺陷之一,对一些精密复杂模具,常因热处理变形而报废,因此控制精密复杂模具的变形一直成为热处理生产中的关键问题。
众所周知,模具在热处理时,特别是在淬火过程中,由于模具截面各部分加热和冷却速度的不一致而引起的温度差,加之组织转变的不等时性等原因,使得模具截面各部分体积胀缩不均匀,组织转变的不均匀,从而引起“组织应力”和模具内外温差所引起的热应力。
当其内应力超过模具的屈服极限时,就会引起模具的变形。
因此,减少和控制精密复杂模具变形乃是广大热处理工作者的一项重要的研究课题。
本文试就精密复杂模具变形状况、变形原因的研究,来探讨减少和控制精密复杂模具变形的措施,以提高模具产品的质量和使用寿命。
一、模具材料的影响1、模具的选材某机械厂从选材和热处理简便考虑,选择T10A钢制造截面尺寸相差悬殊、要求淬火后变形较小的较复杂模具,硬度要求56-60HRC。
热处理后模具硬度符合技术要求,但模具变形较大,无法使用,造成模具报废。
后来该厂采用微变形钢Cr12钢制造,模具热处理后硬度和变形量都符合要求。
因此制造精密复杂、要求变形较小的模具,要尽量选用微变形钢,如空淬钢等。
2、模具材质的影响某厂送来一批Cr12MoV钢较复杂模具,模具都带有¢60m m圆孔,模具热处理后,部分模具圆孔出现椭圆,造成模具报废。
一般来说Cr12MoV钢是微变形钢,不应该出现较大变形。
我们对变形严重的模具进行金相分析发现,模具钢中含有大量共晶碳化物,且呈带状和块状分布。
(1)模具椭圆(变形)产生的原因这是因为模具钢中呈一定方向分布的不均匀碳化物的存在,碳化物的膨胀系数比钢的基体组织小30%左右,加热时它阻止模具内孔膨胀,冷却时又阻止模具内孔收缩,使模具内孔发生不均匀的变形,使模具的圆孔出现椭圆。
(2)预防措施①在制造精密复杂模具时,要尽量选择碳化物偏析较小的模具钢,不要图便宜,选用小钢厂生产的材质较差钢材。
②对存在碳化物严重偏析的模具钢要进行合理锻造,来打碎碳化物晶块,降低碳化物不均匀分布的等级,消除性能的各向异性。
③对锻后的模具钢要进行调质热处理,使之获得碳化物分布均匀、细小和弥散的索氏体组织、从而减少精密复杂模具热处理后的变形。
④对于尺寸较大或无法锻造的模具,可采用固溶双细化处理,使碳化物细化、分布均匀,棱角圆整化,可达到减少模具热处理变形的目的。
二、模具结构设计的影响有些模具选材和钢的材质都很好,往往因为模具结构设计不合理,如薄边、尖角、沟槽、突变的台阶、厚薄悬殊等,造成模具热处理后变形较大。
1、变形的原因由于模具各处厚薄不均或存在尖锐圆角,因此在淬火时引起模具各部位之间的热应力和组织应力的不同,导致各部位体积膨胀的不同,使模具淬火后产生变形。
2、预防措施设计模具时,在满足实际生产需要的情况下,应尽量减少模具厚薄悬殊,结构不对称,在模具的厚薄交界处,尽可能采用平滑过渡等结构设计。
根据模具的变形规律,预留加工余量,在淬火后不致于因为模具变形而使模具报废。
对形状特别复杂的模具,为使淬火时冷却均匀,可采用给合结构。
三、模具制造工序及残余应力的影响在工厂经常发现,一些形状复杂、精度要求高的模具,在热处理后变形较大,经认真调查后发现,模具在机械加工和最后热处理未进行任何预先热处理。
1、变形原因在机械加工过程中的残余应力和淬火后的应力叠加,增大了模具热处理后的变形。
2、预防措施(1)粗加工后、半精加工前应进行一次去应力退火,即(630-680)℃×(3-4)h 炉冷至500℃以下出炉空冷,也可采用400℃×(2-3)h去应力处理。
(2)降低淬火温度,减少淬火后的残余应力。
(3)采用淬油170ºC出油空冷(分级淬火)。
(4)采用等温淬火工艺可减少淬火残余应力。
采用以上措施可使模具淬火后残余应力减少,模具变形较小。
四、热处理加热工艺的影响1、加热速度的影响模具热处理后的变形一般都认为是冷却造成的,这是不正确的。
模具特别是复杂模具,加工工艺的正确与否对模具的变形往往产生较大的影响,对一些模具加热工艺的对比可明显看出,加热速度较快,往往产生较大的变形。
(1)变形的原因任何金属加热时都要膨胀,由于钢在加热时,同一个模具内,各部分的温度不均(即加热的不均匀)就必然会造成模具内各部分的膨胀的不一致性,从而形成因加热不均的内应力。
在钢的相变点以下温度,不均匀的加热主要产生热应力,超过相变温度加热不均匀,还会产生组织转变的不等时性,既产生组织应力。
因此加热速度越快,模具表面与心部的温度差别越大,应力也越大,模具热处理后产生的变形也越大。
(2)预防措施对复杂模具在相变点以下加热时应缓慢加热,一般来说,模具真空热处理变形要比盐浴炉加热淬火小得多。
‚采用预热,对于低合金钢模具可采用一次预热(550-620ºC);对于高合金刚模具应采用二次预热(550-620ºC和800-850ºC)。
2、加热温度的影响一些厂家为了保证模具达到较高硬度,认为需提高淬火加热温度。
但是生产实践表明,这种做法是不恰当的,对于复杂模具,同样是采用正常的加热温度下进行加热淬火,在允许的上限温度加热后的热处理变形要比在允许的下限温度加热的热处理变形大得多。
(1)变形原因众所周知,淬火加热温度越高,钢的晶粒越趋长大,由于较大晶粒能使淬透性增加,则使淬火冷却时产生的应力越大。
再之,由于复杂模具大多由中高合金钢制造,如果淬火温度高,则因Ms点低,组织中残留奥氏体量增多,加大模具热处理后变形。
(2)预防措施在保证模具的技术条件的情况下合理选择加热温度,尽量选用下限淬火加热温度,以减少冷却时的应力,从而减少复杂的热处理变形。
五、残留奥氏体的影响一些高合金模具钢,如Cr12MoV钢模具在淬火和低温回火后,模具的长、宽、高皆发生缩小现象,这是因为模具淬火后残留奥氏体量过多而引起的。
1、变形原因因合金钢(如Cr12MoV钢)淬火后含有大量残留奥氏体,钢中各种组织有不同的比体积,奥氏体的比体积最小,这是高合金钢模具淬火低温回火后体积发生缩小的主要原因。
钢的各种组织的比体积按下列顺序递减:马氏体-回火索氏体-珠光体-奥氏体2、预防措施(1)适当降低淬火温度。
正如前面叙述过的淬火加热温度越高,残留奥氏体量越大,因此选择适当的淬火加热温度是减少模具缩小的重要措施。
一般在保证模具技术要求的情况下,要考虑模具的综合性能,适当降低模具的淬火加热温度。
(2)一些数据表明,Cr12MoV钢模具淬火后,500ºC回火较200ºC回火的残留奥氏体量少了一半,所以在保证模具技术要求的前提下,应适当提高回火温度。
生产实践表明:Cr12MoV钢模具500ºC回火模具变形量最小,而硬度降低不多(2~3HRC)。
(3)模具淬火后采取冷处理是减少残留奥氏体量的最佳工艺,也是减少模具变形、稳定使用时发生尺寸变化的最佳措施,因此精密复杂模具一般应采用深冷处理。
六、冷却介质和冷却方法的影响模具热处理变形往往是在淬火冷却后所表现出来的,这虽然有以上各种因素的影响,但冷却过程中的影响也是不可忽视的。
1、变形产生的原因当模具冷却到Ms点以下时,钢即发生相变,除因冷却不一致所早成的热应力外,还有因相变的不等时性而产生的组织应力,冷却速度越快,冷却越不均匀,产生的应力越大,模具的变形也越大。
2、预防措施(1)在保证模具硬度要求的前提下,尽量采用预冷,对于碳素钢和低合金模具钢可预冷至棱角部位发黑(720~760ºC)。
对于在珠光体转变区过冷奥氏体较稳定的钢种可预冷至700ºC左右。
(2)采用分级冷却淬火能显著减少模具淬火时产生的热应力和组织应力,是减少一些复杂模具变形的有效方法。
(3)对一些精密复杂模具,采用等温淬火能显著减少变形。
七、改进热处理工艺、减少模具热处理变形模具在淬火后的变形,不论采取什么方法,变形都是无法避免的,但是对于要严格控制变形量的精密复杂模具可采取以下方法进行控制。
1、采用调质热处理对基体硬度要求不高,而表面硬度要求较高的精密复杂模具,可采取模具粗加工后进行调质热处理,精加工后进行低温氮化处理(500~550ºC),由于模具氮化温度低,不存在基体组织相变,另外炉冷至室温出炉,冷却应力也较少,模具变形较小。
2、采用预先热处理对精密复杂模具,如其硬度要求不太高,可采用预先热处理的预硬钢,对模具钢(如3Cr2Mo, 3CrMnNiMo钢)进行预先热处理,使之到达使用时的硬度(较低硬度为25~35HRC,较高硬度为40~50HRC),然后把模具加工成型不再进行热处理,从而保证精密复杂模具的精度。
3、采用时效硬化型模具钢对精密复杂模具可采用时效硬化钢,如PMS(1Ni3Mn2CuA1.Mo)钢是一种新型时效模具钢,在870ºC固溶淬火后的硬度在30HRC左右,便于机械加工,模具加工成型后再进行500ºC左右的时效热处理,即可获得40~45HRC的较高硬度,模具变形较小,只需要进行抛光处理,是理想的精密复杂模具用钢。
八、结语精密复杂模具的变形原因往往是复杂的,但是我们只要掌握其变形规律,分析其产生的原因,采用不同的方法进行预防模具的变形是能够减少的,也是能够控制的。
一般来说,对精密复杂模具的热处理变形可采取一下方法预防。
(1)合理选材。
对精密复杂模应选择材质好的微变形模具钢(如空淬钢),对碳化物偏析严重的模具钢应进行合理锻造并进行调质热处理,对较大和无法锻造模具钢可进行固溶双细化热处理。
(2)模具结构设计要合理,厚薄不要太悬殊,形状要对称,对于变形较大模具要掌握变形规律,预留加工余量,对于大型、精密复杂模具可采用组合结构。
(3)精密复杂模具要进行预先热处理,消除机械加工过程中产生的残余应力。
(4)合理选择加热温度,控制加热速度,对于精密复杂模具可采取缓慢加热、预热和其他均衡加热的方法来减少模具热处理变形。
(5)在保证模具硬度的前提下,尽量采用预冷、分级冷却淬火或温淬火工艺。
(6)对精密复杂模具,在条件许可的情况下,尽量采用真空加热淬火和淬火后的深冷处理。
(7)对一些精密复杂的模具可采用预先热处理、时效热处理、调质氮化热处理来控制模具的精度。
另外,正确的热处理工艺操作(如堵孔、绑孔、机械固定、适宜的加热方法、正确选择模具的冷却方向和在冷却介质中的运动方向等)和合理的回火热处理工艺也是减少精密复杂模具变形的有效措施。