硬脆材料超精密加工关键技术研究
精密和超精密加工技术

电子材料,磁性材料的镜面磨削:大尺寸硅片;铁金氧磁头 光学材料的镜面磨削:记录用光学材料,光学镜片研磨抛光前 陶瓷材料的镜面磨削 高精度钢铁材料及复合材料,硬质合金
4、脆性材料精密磨削
尖锐压头下的材料变形过程
(a) 初始加载: 接触区产生—永久塑性变形区,没有任何 裂纹破坏。变形区尺寸随载荷增加而变大。 (b) 临界区: 载荷增加到某一数值时,在压头正下方应力 集中处产生中介裂纹(M edian Crack)。 (c) 裂纹增长区: 载荷增加, 中介裂纹也随之增长。 (d) 初始卸载阶段: 中介裂纹开始闭合,但不愈合。 (e) 侧向裂纹产生: 进一步卸载,由于接触区弹塑性应力 不匹配,产生一个拉应力叠加在应力场中,产生系列向侧 边扩展的横向裂纹(L ateral Crack)。 (f) 完全卸载: 侧向裂纹继续扩展,若裂纹延伸到表面则 形成破坏的碎屑。
精密、超精密磨削、镜面磨削形成的零散刻痕
1、精密和超精密磨削加工基础
精密和超精密磨削分类
将磨料或微粉与结合剂粘合在一起, 形成一定的形状并具有一定强度,再 采用烧结、粘接、涂敷等方法形成砂 轮、砂条、油石、砂带等磨具。
精密和超精 密磨料加工 固结磨 料加工
磨料或微粉不是固结在一起, 而是成游离状态。
3、在线电解磨削技术
ELID磨削的特点
磨削过程具有良好的稳定性; ELID修整法使金刚石砂轮不会过快的磨耗,提高了贵重磨料的利用率; ELID修整法使磨削过程具有良好的可控性;
采用ELID磨削法,容易实现镜面磨削,并可大幅度减少超硬材料被磨零件的 残留裂纹。
3、在线电解磨削技术
1、精密和超精密磨削加工基础
切削和磨削的比较
硬脆材料的超光滑高平面度抛光工艺
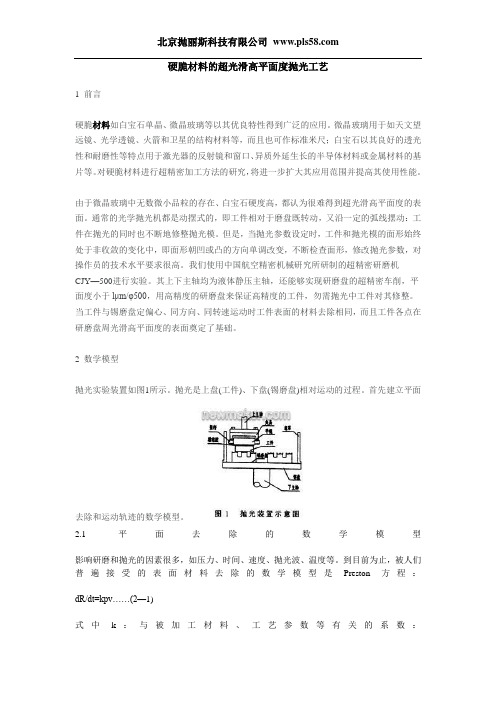
硬脆材料的超光滑高平面度抛光工艺1 前言硬脆材料如白宝石单晶、微晶玻璃等以其优良特性得到广泛的应用。
微晶玻璃用于如天文望远镜、光学透镜、火箭和卫星的结构材料等,而且也可作标准米尺;白宝石以其良好的透光性和耐磨性等特点用于激光器的反射镜和窗口、异质外延生长的半导体材料或金属材料的基片等。
对硬脆材料进行超精密加工方法的研究,将进一步扩大其应用范围并提高其使用性能。
由于微晶玻璃中无数微小品粒的存在、白宝石硬度高,都认为很难得到超光滑高平面度的表面。
通常的光学抛光机都是动摆式的,即工件相对于磨盘既转动,又沿一定的弧线摆动:工件在抛光的同时也不断地修整抛光模。
但是,当抛光参数设定时,工件和抛光模的面形始终处于非收敛的变化中,即面形朝凹或凸的方向单调改变,不断检查面形,修改抛光参数,对操作员的技术水平要求很高。
我们使用中国航空精密机械研究所研制的超精密研磨机CJY—500进行实验。
其上下主轴均为液体静压主轴,还能够实现研磨盘的超精密车削,平面度小于lμm/φ500,用高精度的研磨盘来保证高精度的工件,勿需抛光中工件对其修整。
当工件与锡磨盘定偏心、同方向、同转速运动时工件表面的材料去除相同,而且工件各点在研磨盘周光滑高平面度的表面奠定了基础。
2 数学模型抛光实验装置如图1所示。
抛光是上盘(工件)、下盘(锡磨盘)相对运动的过程。
首先建立平面去除和运动轨迹的数学模型。
2.1 平面去除的数学模型影响研磨和抛光的因素很多,如压力、时间、速度、抛光波、温度等。
到目前为止,被人们普遍接受的表面材料去除的数学模型是Preston方程:dR/dt=kpv……(2—1)式中k:与被加工材料、工艺参数等有关的系数:p:表面上某一点在t瞬时与研具间的压力;v:该点在t瞬时与工具间的相对运动速度。
DR/dt:单位时间内材料去除量;为了预测研抛试验中材料去除量与运动形式的关系,对(2—1)做如下假设:(1)材料的去除量仅由工件与研具的相互作用引起。
硬脆材料超声波精密加工机理及影响因素研究

硬脆 材料 ( 如人工 晶体 、 学玻璃 、 光 工程 陶瓷 ) 的使
用越 来越 广 泛, 有 高硬 度 、 磨 损 、 高 温 、 学 稳 具 耐 耐 化
定性好 、 不易氧 化 、 耐腐 蚀等优 点 。 而, 然 由于人工 晶体
等难加 工材料 具有 极高 的硬度 和脆 性,其 成形加 工 十 分 困难 。硬脆 材料 的精 密 、 精密 加工, 先进 制造 技 超 是
肖强 t, , 李言 , 2 李淑娟 1
(. 安 理 工 大学 机 械 与精 密 仪 器 工程 学 院 , 西 西安 7 04 ;. 安 工 业 大 学 机 电工 程 学 院 , 西 西 安 7 0 3 ) 1 西 陕 10 8 2 西 陕 10 2 摘 要 硬 脆材 料 具 有很 高 的硬 度 和脆 性 , 了提 高硬 脆 材 料研 磨 效 率 , 理 论 上 分析 超 声 波 研磨 加工 硬 脆 材 料 机 理 , 细 为 从 详
h r d b il tra ad a r t mae l n te i
X A i g, L a L h ja I O Q a  ̄,I n,I uun n Z Y S
( .c o l fMe h nc l n rcs n Is u n n ie r g Xi nUnv ri fT c n lg Xi n7 0 4 C ia 1S h o c a ia d Pe ii nt me tE gn e n , iest o eh oo y, 1 0 8, hn ; o a o r i a y a
超精密加工的关键技术及发展趋势

车辆工程技术90机械电子1 超精密加工的技术范畴 在工业的加工领域当中,通常情况下按照加工的精度来划分的话,可以将机械加工一般可以分为三类,分别是:一般加工、精密加工和超精密加工。
随着生产技术的飞速发展,关于加工精度的划分标准也在随着时间的发展而变化,加工的进程也会随之而向前推移,可能过去的精密加工已经沦落为现今社会当中的一半加工的程度了。
因此,可以知道这个划分界限并不是一定的,它是会随着科学技术的发展而提高的,毕竟在如今的数据记录当中并没有主体的数值限制。
超精密加工的环境是在机床设备上进行的,利用刀具与零件之间产生的具有严格约束性的相对运动,从而达到加工出精度超高的产品,接着需要对加工好的材料进行相应的摩擦和去除毛刺,从而获得高形状、高精度的零件。
一般在学术界领域,超精度加工的加工精度通常在0.1μm 以上的,其表面的粗糙度也都是低于0.025μm的。
近年来,随着纳米技术的兴起,超精密加工目前已经进入纳米级精度阶段,逐渐的出现了纳米加工及其相关联的纳米技术。
经过近年来对纳米技术的使用和完善,这项技术已经逐渐的走向成熟,形成了一整套的超精密加工体系,其中包含了超精密切削、超精密磨削、超精密微细加工以及超精密计量等等,慢慢的向更高层次进行突破。
但是影响超精密加工的因素很多,目前只有在现有的基础上,经过研究和采用各种各样新型的技术、并且能够在各个方面融入这些新型技术,真正做到精益求精,达到更高的精度,才能突破传统加工模式的加工精度的界限。
实际上超精密的加工技术就是超精度切削、磨削和细微加工技术的综合应用。
2 超精密加工的关键技术2.1 主轴 目前阶段,在超精密加工机床的使用过程中,使用最高精度的主轴是空气静压轴承主轴,就我国制作出来的磁悬浮列车的轴承也远远达不到空气静压轴承主轴的加工精度,因此磁悬浮列车至今为止还是需要利用空气轴承。
就目前的超精密加工技术而言,空气静压轴承主轴的精度可以达到0.05μm,国内已经达到了这个加工精度的水平,然而国外甚至可以达到0.03μm,即使已经达到了如此精确的加工精度,却依旧不能满足纳米加工技术对于主轴的加工精度要求。
超精密制造技术论文
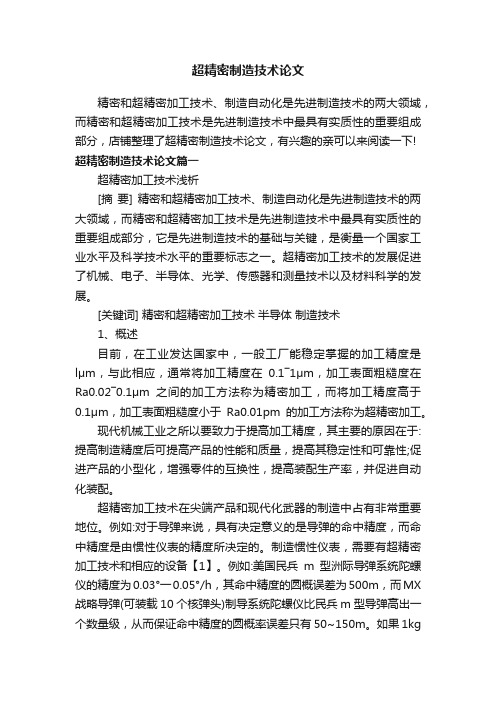
超精密制造技术论文精密和超精密加工技术、制造自动化是先进制造技术的两大领域,而精密和超精密加工技术是先进制造技术中最具有实质性的重要组成部分,店铺整理了超精密制造技术论文,有兴趣的亲可以来阅读一下! 超精密制造技术论文篇一超精密加工技术浅析[摘要] 精密和超精密加工技术、制造自动化是先进制造技术的两大领域,而精密和超精密加工技术是先进制造技术中最具有实质性的重要组成部分,它是先进制造技术的基础与关键,是衡量一个国家工业水平及科学技术水平的重要标志之一。
超精密加工技术的发展促进了机械、电子、半导体、光学、传感器和测量技术以及材料科学的发展。
[关键词] 精密和超精密加工技术半导体制造技术1、概述目前,在工业发达国家中,一般工厂能稳定掌握的加工精度是lμm,与此相应,通常将加工精度在0.1―1μm,加工表面粗糙度在Ra0.02―0.1μm之间的加工方法称为精密加工,而将加工精度高于0.1μm,加工表面粗糙度小于Ra0.01pm的加工方法称为超精密加工。
现代机械工业之所以要致力于提高加工精度,其主要的原因在于:提高制造精度后可提高产品的性能和质量,提高其稳定性和可靠性;促进产品的小型化,增强零件的互换性,提高装配生产率,并促进自动化装配。
超精密加工技术在尖端产品和现代化武器的制造中占有非常重要地位。
例如:对于导弹来说,具有决定意义的是导弹的命中精度,而命中精度是由惯性仪表的精度所决定的。
制造惯性仪表,需要有超精密加工技术和相应的设备【1】。
例如:美国民兵m型洲际导弹系统陀螺仪的精度为0.03°一0.05°/h,其命中精度的圆概误差为500m,而MX 战略导弹(可装载10个核弹头)制导系统陀螺仪比民兵m型导弹高出一个数量级,从而保证命中精度的圆概率误差只有50~150m。
如果1kg重的陀螺转子,其质量中心偏离其对称轴0.5nm,则会引起100m的射程误差和50m的轨道误差。
惯性仪表中有许多零件的制造精度都要求达到小于微米级。
硬脆材料高效精密磨粒加工技术研究

先 进 陶 瓷 、单 晶 硅 . 人 工 晶 粒 浸 入 工 件较 深 ,磨 屑 主要 以脆 性 去除为主 ,去除机理将从微观 角度来
体 、红 蓝 宝 石 、 石材 等 硬 脆 材 料 的 断 裂 形 式 完成 。超 高速 磨 削单 位 时 分析 研究。 目前 ,延性磨 削作 为硬 脆
机 械 加 工 非 常 困难 、效 率 低 ,加 工 间内 参 加磨 削 的磨 粒 数 大大 增 加 ,
的技术方案 。
■
■
青 岛理工大 学 盛卫卫
西 安交通大 学 李长河
丁玉成
1言 前
随着 现 代 高 新 技 术 的发 展 ,具
呈 雾
式
材 料 可 以 获 得 良好 的 磨 削 加 工 性 能 。在4 届 国际 生产 工 明
用 的 关 键 因 素 。世 界 各 发达 国 家对 形 式产 生 磨 屑 ,大 大提 高磨 削 表面 工业大 学、哈尔滨工 业大学等也开展 硬脆 材料加 工都给 予了高度 重视 。
质 量 和效 率 。 因此 ,超 高速 磨 削 能 了硬脆 材料延性磨 削理论与关键 技术
美国上 世纪9 年代 投入5 0 0 0 0 万 实现 对 硬 脆 材 料 的 延性 域 磨 削 。例 的研究 工作 。
材料 高质量高精 度零件 的重要加 工方
成 本 占制品 总成本 的3 %- 5 0 7 %,有 单 个 磨粒 的切 削 厚 度极 薄 ,容 易使 法 已引起工业界 的特 别关注 。国内天
些 甚 至达  ̄ 9 % ,是 影 响其 推广 应 陶 瓷 、玻 璃 等 硬 脆 材料 以塑 性 变 形 津大 学 .湖南大 学、东北大学 、西北 J =0
随 着现 代 高 科 学 技 术 及 产 业 化 削技术的重 要应 用领域 。
《精密和超精密加工技术(第3版)》第3章精密磨削和超精密磨削
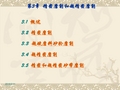
2018/3/11
第1节 概述
二、精密和超精密砂轮磨料磨具
磨料及其选择
超硬磨料制作的磨具在以下几方面能够满足精密加工和超精密加工 的要求,因此使用广泛。
1)磨具在形状和尺寸上易于保持,使用寿命高,磨削精度高。
2)磨料本身磨损少,可较长时间保持切削性,修整次数少,易于保持精度。
3)磨削时,一般工件温度较低,因此可以减小内应力、裂纹和烧伤等缺
磨具的形状和尺寸及其基体材料
根据机床规格和加工情况选择磨具的 形状和尺寸。 基体材料与结合剂有关。
2018/3/11
第1节 概述
三、精密和超精密涂覆磨具
涂覆磨具分类
根据涂覆磨具的形状、基底材料和工作条件与用途等,分类见下表
涂 覆 磨 具
工 作 条 件
基 底 材 料
形 状
耐 水 (N)
2018/3/11
精密砂带磨削:砂带粒度F230~F320,加
工精度1μm,Ra0.025; 超精密砂带磨削:砂带粒度W28~W3,加工精 度0.1μm,Ra0.025~0.008μm。
2018/3/11
第1节 概述
一、精密和超精密加工分类
游离磨料加工
磨料或微粉不是固结在一起, 而是成游离状态。 传统方法:研磨和抛光 新方法:磁性研磨、弹性发射 加工、液体动力抛光、液中研 抛、磁流体抛光、挤压研抛、 喷射加工等。
第3章 精密磨削和超精密磨削 3.1 概述
3.2 精密磨削 3.3 超硬磨料砂轮磨削
3.4 超精密磨削
3.5 精密和超精密砂带磨削
2018/3/11
第1节 概述
精密和超精密磨料加工是利用细粒度的磨粒和 微粉对黑色金属、硬脆材料等进行加工,得到高 加工精度和低表面粗糙度值。对于铜、铝及其 合金等软金属,用金刚石刀具进行超精密车削是 十分有效的,而对于黑色金属、硬脆材料等,用 精密和超精密磨料加工在当前是最主要的精密 加工手段。
ELID超精密磨削技术综述

.. ELID超精密磨削技术综述蔡智杰天津大学机械工程学院机械工程系2014级硕士生摘要:金属基超硬磨料砂轮在线电解修整(Electrolytic In-process Dressing, 简称ELID)磨削技术作为一种结合传统磨削、研磨、抛光为一体的复合镜面加工技术,开辟了超精密加工的新途径,具有广发的应用价值。
本文将从工作原理、磨削机理、工艺特点、影响因素及磨削机床的分类等方面系统地介绍ELID超精密磨削技术,并通过分析国外研究应用状况,阐述该技术在精密加工制造行业的应用发展前景。
关键词:在线电解修整(ELID) 超精密镜面加工金属基超硬磨料砂轮硬脆材料磨削机理0 引言随着制造行业的飞速发展,硬质合金、工程瓷、光学玻璃、玻璃瓷、淬火钢及半单晶硅等硬脆难加工材料得到广泛应用,寻求低成本、高效率的超精密加工技术的研究工作正在广泛开展。
超精密镜面磨削技术是一种借助高性能的机床、良好的工具(砂轮)、完善的辅助技术和稳定的环境条件,控制加工精度在0.1μm级以下、表面粗糙度Ra<0.04μm甚至Ra<0.01μm的磨削方法[1]。
然而,由于传统磨削工艺效率低、磨削力大、磨削温度高,且砂轮极易钝化、堵塞而丧失切削性能,从而造成加工面脆性破坏,加工质量恶化,难以满足高精度、高效率的加工要求。
随着砂轮精密修整技术的发展及超微细粒度砂轮的使用,将磨削加工的材料去除工作引入到一个新的领域。
ELID磨削技术是应用电化学反应的非传统材料去除技术来解决金属基超硬磨料砂轮的修整问题的超精密镜面加工技术,以其效率高、精度高、表面质量好、加工装置简单及适应性广等特点,已较广泛用于电子、机械、光学、仪表、汽车等领域。
1 ELID磨削的基本原理ELID(Electrolytic In-process Dressing)磨削是在磨削过程中,利用非线性电解修整作用使金属结合剂超硬磨料砂轮表层氧化层的连续修整用与钝化膜抑制电解的作用达到动态平衡。
ELID超精密磨削技术综述

先进制造技术课程大作业2014年10月ELID超精密磨削技术综述蔡智杰天津大学机械工程学院机械工程系2014级硕士生摘要:金属基超硬磨料砂轮在线电解修整(Electrolytic In-process Dressing, 简称ELID)磨削技术作为一种结合传统磨削、研磨、抛光为一体的复合镜面加工技术,开辟了超精密加工的新途径,具有广发的应用价值。
本文将从工作原理、磨削机理、工艺特点、影响因素及磨削机床的分类等方面系统地介绍ELID超精密磨削技术,并通过分析国内外研究应用状况,阐述该技术在精密加工制造行业的应用发展前景。
关键词:在线电解修整(ELID) 超精密镜面加工金属基超硬磨料砂轮硬脆材料磨削机理0 引言随着制造行业的飞速发展,硬质合金、工程陶瓷、光学玻璃、玻璃陶瓷、淬火钢及半单晶硅等硬脆难加工材料得到广泛应用,寻求低成本、高效率的超精密加工技术的研究工作正在广泛开展。
超精密镜面磨削技术是一种借助高性能的机床、良好的工具(砂轮)、完善的辅助技术和稳定的环境条件,控制加工精度在0.1μm级以下、表面粗糙度Ra<0.04μm甚至Ra<0.01μm的磨削方法[1]。
然而,由于传统磨削工艺效率低、磨削力大、磨削温度高,且砂轮极易钝化、堵塞而丧失切削性能,从而造成加工面脆性破坏,加工质量恶化,难以满足高精度、高效率的加工要求。
随着砂轮精密修整技术的发展及超微细粒度砂轮的使用,将磨削加工的材料去除工作引入到一个新的领域。
ELID磨削技术是应用电化学反应的非传统材料去除技术来解决金属基超硬磨料砂轮的修整问题的超精密镜面加工技术,以其效率高、精度高、表面质量好、加工装置简单及适应性广等特点,已较广泛用于电子、机械、光学、仪表、汽车等领域。
1 ELID磨削的基本原理ELID(Electrolytic In-process Dressing)磨削是在磨削过程中,利用非线性电解修整作用使金属结合剂超硬磨料砂轮表层氧化层的连续修整用与钝化膜抑制电解的作用达到动态平衡。
ELID磨削_硬脆材料精密和超精密加工的新技术

EL ID磨削硬脆材料精密和超精密加工的新技术张飞虎 朱 波 栾殿荣 袁哲俊( 哈尔滨工业大学机械工程系 哈尔滨 150001 )文 摘 金属基超硬磨料砂轮在线电解修整(E lectrolytic In2process Dressing,简称E L ID)磨削技术是国外近年发展起来的一种硬脆材料精密和超精密加工新技术。
本文介绍了E L ID磨削技术的基本原理、工艺特点和国内外研究应用情况。
应用E L ID磨削技术,可对工程陶瓷等硬脆材料实现高效率磨削和精密镜面磨削。
关键词 精密和超精密加工,磨削,砂轮,修整EL ID Grinding A New Technology for Precision andUltraprecision Machining of Hard and Brittle MaterialsZhang Feihu Zhu Bo Luan Dianrong Yuan Zhejun( Department of Mechanical Engineering,Harbin Institute of Technology Harbin 150001 )Abstract EL ID grinding which applies metal bonded grinding wheel with superhard abrasives and electrolytic in2process dressing is a newly developed technology for precision and ultraprecision machining of hard and brittle ma2 terials.In this paper the basic principle,characteristics,research and application of EL ID grinding are introduced.By EL ID,efficient grinding and mirror surface grinding of ceramics and other hard and brittle materials can be realized.K ey w ords Precision and ultraprecision machining,Grinding,Grinding wheel,Dressing1 引言金刚石、CBN超硬磨料具有硬度高、耐磨性好等优良的切削性能,自美国GE公司1957年和1969年批量生产人造金刚石、CBN磨料以来,除少数做成刀具外,大部分都用于制造磨具。
精密和超精密加工技术
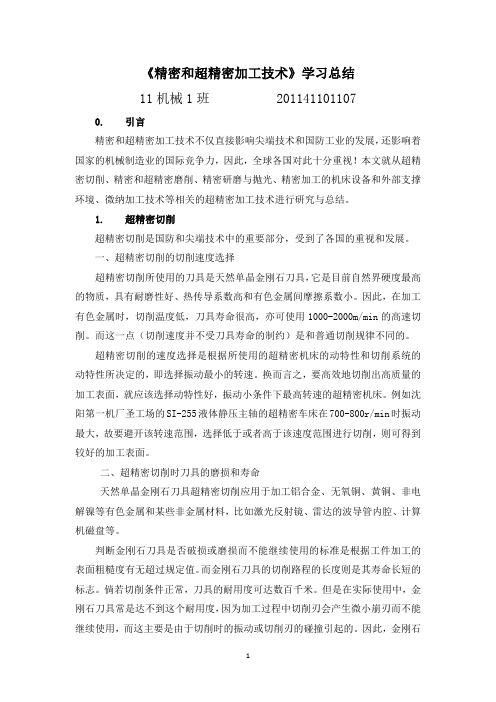
《精密和超精密加工技术》学习总结11机械1班 2011411011070. 引言精密和超精密加工技术不仅直接影响尖端技术和国防工业的发展,还影响着国家的机械制造业的国际竞争力,因此,全球各国对此十分重视!本文就从超精密切削、精密和超精密磨削、精密研磨与抛光、精密加工的机床设备和外部支撑环境、微纳加工技术等相关的超精密加工技术进行研究与总结。
1. 超精密切削超精密切削是国防和尖端技术中的重要部分,受到了各国的重视和发展。
一、超精密切削的切削速度选择超精密切削所使用的刀具是天然单晶金刚石刀具,它是目前自然界硬度最高的物质,具有耐磨性好、热传导系数高和有色金属间摩擦系数小。
因此,在加工有色金属时,切削温度低,刀具寿命很高,亦可使用1000-2000m/min的高速切削。
而这一点(切削速度并不受刀具寿命的制约)是和普通切削规律不同的。
超精密切削的速度选择是根据所使用的超精密机床的动特性和切削系统的动特性所决定的,即选择振动最小的转速。
换而言之,要高效地切削出高质量的加工表面,就应该选择动特性好,振动小条件下最高转速的超精密机床。
例如沈阳第一机厂圣工场的SI-255液体静压主轴的超精密车床在700-800r/min时振动最大,故要避开该转速范围,选择低于或者高于该速度范围进行切削,则可得到较好的加工表面。
二、超精密切削时刀具的磨损和寿命天然单晶金刚石刀具超精密切削应用于加工铝合金、无氧铜、黄铜、非电解镍等有色金属和某些非金属材料,比如激光反射镜、雷达的波导管内腔、计算机磁盘等。
判断金刚石刀具是否破损或磨损而不能继续使用的标准是根据工件加工的表面粗糙度有无超过规定值。
而金刚石刀具的切削路程的长度则是其寿命长短的标志。
倘若切削条件正常,刀具的耐用度可达数百千米。
但是在实际使用中,金刚石刀具常是达不到这个耐用度,因为加工过程中切削刃会产生微小崩刃而不能继续使用,而这主要是由于切削时的振动或切削刃的碰撞引起的。
因此,金刚石刀具只能使用在机床主轴转动非常平稳的高精度机床上,而刀具的维护对机床的要求亦是如此。
典型硬脆材料的超精密加工

电火花加工氮化硅基陶瓷材料表面
电火花加工氧化铝基陶瓷材料的横截面
陶瓷材料的超声波加工
ULTRA SONIC MACHINING (USM)
原理:磨料冲击。
与陶瓷材料的绝缘与否无关
加工效率较低,加工表面质量高
陶瓷材料的超声波加工设备
超声波加工陶瓷材料表面
陶瓷材料的金刚石锯片的切割加工
钻石
星光蓝宝石
星光红宝石
祖母绿
金绿猫眼
欧泊
翡翠
蓝宝石
红宝石
电气石
海蓝宝石
黑珍珠
紫晶
硅线石猫眼
黄玉
宝石的类型
宝石类型
宝石加工用磨料、磨具
磨料:金刚石、SiC、氧化铝、氧化铁等。 砂轮:金刚石砂轮、SiC砂轮、氧化铝砂轮。 切割锯:圆锯、带锯等,利用固定在工具上的磨料
对宝石进行加工。
宝石的加工方法
首先,宝石学家根据不同种类宝石的光学性能和折 射率,设计各种宝石的特色款式。
宝石加工
宝石一般较小,只有数克拉,对它们的加工量往往 只有零点几克拉。因此,加工余量一般很小。
宝石加工属于超精密加工范畴。俗话说宝石的价值 是三分材料七分加工,宝石加工质量不同,其光学 效应相差很远,其价值也相差很大。
磨料:金刚石、B4C、SiC等磨料。金刚石的研磨效 率最大。
磨料大小选择:需要根据加工余量和所要求的表面 粗糙度选择。
研磨液:大多用水。
陶瓷材料的精密研磨
陶瓷材料的精密抛光
宝石加工
定义:在矿物质中,既硬又美且稀少的东西被人们 称为宝石,极其珍贵。
宝石集装饰、收藏和保值于一体,既有观赏价值, 又有经济价值。
陶瓷涂层
高硬度、耐磨、耐热、抗氧化
硅晶片的超精密加工

硅晶片的超精密加工摘要:归纳总结了硅晶片的加工原理、加工方法,分析加工硅晶片的技术要求其精密制造过程,并通过对国外技术装备的分析,指出硅晶片高效精密加工技术的发展趋势。
关键词:硅晶片超精密加工磨削抛光前言硅是具有金刚石晶体结构,原子以共价键结合的硬脆材料,其硬度达到1000HV,但断裂强度很低,所以超精密加工晶体硅有一定的难度。
同时,硅又是一种很好的材料,构成集成电路半导体晶片的90%以上都是硅晶片。
随着电路芯片的集成度不断提高,而加工特征尺寸和加工成本逐步缩小,如下表。
为了能在硅晶片上印刷集成电路,与其他元件结合紧密,硅晶片的表面必须平直,特别是随着集成电路的集成程度的提高,对硅晶片的表面的线宽、硅晶片的平直度提出了越来越高的要求,故实现优质,低耗,高精度的硅晶片的超精密加工具有极其重要的意义。
1992 1995 1998 2001 2004 2005 硅晶片尺寸/mm 200 200 200/300~400 300~400 300~400 300~400 存储空间16M 64M 256M 1G 4G 18G 加工成本($/cm2) 4.0 3.9 3.8 3.7 3.6 3.5 缺陷密度(N/cm2) 0.1 0.05 0.03 0.01 0.004 0.002 特征尺寸/um 0.5 0..35 0.25 0.18 0.12 0.10[2]硅晶片加工是IC制造系统重要的基础环节,硅片的加工精度、表面粗糙度和表面完整性直接影响IC的线宽和IC的性能,对于<200mm的硅片,传统的加工工艺过程为:切片→倒角→研磨→腐蚀→清洗→抛光(如图1)。
由于采用内圆金刚石锯片切割会产生较大的翘曲变形,最大翘曲量达到37um,硅片表面还会残留切痕和微裂痕,损伤层深度可达10~50um,经双面研磨机平整化加工后可使硅片厚度公差小于3um,总厚度变化TTV<1um,平整度<1um,但表面粗糙度为0.1~0.2um,达不到要求,需经过后续的腐蚀去除研磨所产生的表面损伤层,最后经过化学机械抛光获得超光滑无损伤表面。
超精密切削加工技术
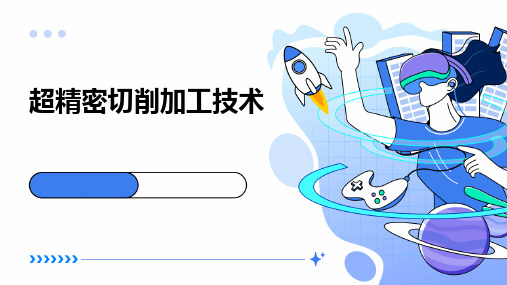
技术发展趋势
1 2
智能化控制
利用传感器和智能算法,实时监测切削过程和工 件表面质量,实现超精密切削加工过程的智能控 制。
复合加工技术
结合多种加工技术,如磨削、抛光和电加工等, 以提高超精密切削加工的效率和表面质量。
3
新材料应用
探索和开发适用于超精密切削加工的新材料,以 提高刀具的耐磨性和工件的表面完整性。
04
超精密切削加工技 术的挑战与解决方 案
技术瓶颈
刀具磨损
超精密切削加工过程中, 刀具与工件的高速摩擦导 致刀具快速磨损,影响加 工精度和效率。
工件表面完整性
超精密切削加工后,工件 表面容易出现微裂纹、残 余应力和加工硬化等表面 完整性问题。
切削液的纯净度
超精密切削加工需要高纯 净度的切削液以减小误差, 但切削液的纯净度控制难 度较大。
应对策略
刀具材料与涂层
采用高硬度、高耐磨性的刀具材料和涂层技术,提高刀具的耐久 性和切削性能。
切削参数优化
根据不同材料和加工条件,优化切削速度、进给速度和切削深度等 参数,以减小刀具磨损和工件表面完整性问题。
切削液纯净度控制
采用高精度过滤设备和检测技术,确保切削液的纯净度满足超精密 切削加工的要求。
精密仪器制造
光学仪器
精密机械
超精密切削加工技术可用于制造高精 度光学仪器,如显微镜、望远镜等, 以提高其成像质量和稳定性。
超精密切削加工技术可用于制造精密 机械,如钟表、精密机床等,以提高 其运动精度和稳定性。
测量仪器
超精密切削加工技术可用于制造高精 度测量仪器,如传感器、测微器等, 以提高其测量准确性和可靠性。
微电子行业
集成电路
超精密切削加工技术可用于制造 集成电路,如芯片、微处理器等,
硬脆材料加工技术的研究

环形 锯条 。最早 出现在 市场上 的金刚石 带锯是在 2 0 世纪 5 年代 ,我 国在 2 O 0世纪 8 0年代前后才 逐渐开 始研制 出该类设 备。这种切割方 式的优点是锯 口小 、
锯切速度快 、 刀具材料消耗小 、 噪音小 。 缺点是对荒料
压痕 断裂力学模 型是 把硬脆 性材料 加工 中磨粒
与工件之间的相互作用看作小规模的压痕现象 , 它是
基于压痕断裂力学模型产生 的 , 图 2 如 所示 。当磨粒 与加工材料接触时 , 磨粒下方工件 的材料在压应力 的
要求规 整 、 不能进行 多片切割等 。钢片切割机的原理
类似 于钢砂锯 , 它利用 一排一定间隙 的张紧 的钢片在 工件上作往复运动进行切割 。 在钢片与工件 的接触部
料 内部一定 的深度 , 并且 观察 材料的变形情 况 。可以 得 出如下结论 : 在很小 载荷作用下 , 即使是 硬脆材 料
也会产生 塑性变形 。当增加 载荷 时 , 材料的变形方式
由塑性 向脆性破 坏转变并且 在材料的表面 、 内部均产 生 由于脆性破坏 引起 的裂纹。在整个 转变的过程 中,
t t
c
属加热使金属 达到熔融状 , 再利用高速工作将熔融金 。 属从工件表面剥离 。电熔 爆技术 主要特点如下 。 一 ( ) 电容爆加工技术 同传 统加工技术相 比 ,加工碳 0 1 化钨 、 高铬合 金 、 镍基合金 、 稀土合金 、 金属 陶瓷 、 钛合 金等各种硬脆性 材料 , 具有效率高 、 能耗低 、 成本小等
硬 脆材料加工难 度很 大 , 加工时稍不 注意就会引
大 的片状切屑 , 并在被切削表面 留下凹痕或裂 纹。
硬脆性材料复合加工技术综述

加工 是基 于磨 料 流运 动 ,无研 具 约束 ,能根 据 与工 件 的接触 情 况
塑性 , 以改善切削加工性能。 它是
对铸造高锰钢 、无磁钢和不锈钢
等难切削材料进行高效率切削的
方法 ,如 激 光加 热 辅 助车 削 和等
用 多 种 制 造 方 法 , 尽 可 能 多 地
的研究 。复 合 加 工 技 术 ( M , C T
C mbn d o ie Ma hnn e h oo y) c iig T c n lg
21 0 0年 第 3 6聋 舞 3期
Vo。6 No3 J n 2 1 l . u . 0 0 3
关键 词 : 制造技术 ; 复合加工 ; 特种加工 ; 脆性材料
Ov r iw fCo pe r c s ig T c n lg eve o m lx P o e sn e h oo y f r il ae iI orHa d Br e M t r d a
C HEN io-h X a
2 0 3磷第 期 V1 o u. 1 0 年舞 6 3 o 6N.Jn 0 1 . 3 20 3
5 6 /5 7
硬 脆性 材料 复合 加工 技术综述
陈小 丽
( 中国燃气涡轮研究院 , 四川 江 油 6 1 0 2 7 3)
摘要 : 重点介绍 了各类硬脆 性材料复合加工技术 , 简要描述 了其特点和发展趋势。
本 文 描 述 硬 脆 性 材 料 复 合
加 工 技 术 的 应 用 和 未 来 发 展 趋
械 能 源 的 切 削 加 工 方 法 ,也 包 括 其 他 能 源 , 电 火 花 、 光 和 如 激 超 声 波 等 特 种 加 工 方 法 , 至包 甚 括 焊 接 和成形 加 工 等其 他 工 艺 制
脆性材料塑性域超精密加工的研究现状

脆性材料塑性域超精密加工的研究现状来源:数控机床网 作者:数控车床 栏目:行业动态 引言随着现代科学技术的发展,脆性材料在现代高技术行业的诸多领域,特别是在航空航天、光学及电子领域中具有十分重要的作用,而且往往对工件的加工精度和表面质量有非常高的要求。
但是到目前为止,脆性材料的加工仍然是一件困难的事情。
因为它们最突出的一个特性就是材料的脆性高,断裂韧性低,材料的弹性极限和强度非常接近。
当材料所承受的载荷超过弹性极限时就发生断裂破坏,在已女口工表 面产生裂纹和凹坑,严重影响其表面质量和性 能 [12,13],所以脆性材料的可加工性极差。
过去, 人们一直沿用古老的研磨、抛光工艺对脆性材料进行光整加工。
这些加工方法生产效率低,加工精度不易保证,而且加工过程不易实现计算机控制,对于曲面形状复杂的工件甚至无法加 工,因此已经远远不能适应现代高科技发展和 高效率的要求。
近年来,人们对峙性材料的加工做了大量 的探索和尝试。
待别是随着科学技术的高速发展,金刚石刀具和超精密机床的制造技术都已发展到极高的水平,使得对脆性材料进行超精密切削加工成为可能。
单纯通过金刚石切削脆性材料表面是近十几年来才发展起来的新兴技术,它主要是通过对脆性材料实现塑性域的超精密切削来获得高质量表面。
这种方法由于具有生产效率高、生产过程易于控制、可加工曲面形状复杂的工件等优点,有着十分广泛的应用前景。
本文对脆性材料超精密加工的研究现状进行了全面的总结,并分析了其中存在的一些问题,希望对脆性材料塑性域加工的进一步 研究有所启示。
1 尖锐压头对脆性材料印压实验的脆塑变形理论用锋利的金刚石刀具对脆性材料的超精密 车削的可能性是以脆性材料在尖锐的金刚石压头下能够产生塑性变形为基础的。
在过去的几十年里,许多学者对各种硬脆材料进行了大量的印压实验,即以一定的垂直力将金刚石压头压入材料内部一定的深度,观察材料的变形情况。
在印压实验的加载到卸载一个完整的循环中,破坏裂纹由产生到扩展的过程如图1所 示 [1] 。
课件《精密加工技术》第六章-脆硬非金属材料精密加工

第六章 脆硬非金属材料精密加工
四、精密加工金刚石
金刚石有多种晶体结构,其中最基本的为正八面体结构
以莫氏硬度表示,金刚石硬度为10,刚玉为9。 金刚石的三种晶相中以111面最硬,也最难加工。
常用的三种 硬度指标
金刚石导热性能好,热膨胀系数小。
*
第六章 脆硬非金属材料精密加工
一、陶瓷的精密加工
1. 研磨陶瓷
研具一般为铸铁或者钢。从加工效率的角度讲,研具硬度高,加 工效率高;从被研磨陶瓷的表面粗糙度角度看,研具越软,被加 工表面Ra越小。
研磨陶瓷所用的磨料一般为碳化硅、氧化铝和金刚石微粉。
一般使用水作为研磨液,为了不使磨料在研磨液中结团,往往需 要加分散剂。
二、光栅的精密加工
?数控机床中使用的光栅 ?如何计算光栅莫尔条纹宽度
光
扭头刨床式刻线机
栅 ① 机械刻线方法
的
龙门刨床式刻线机
加
工
方 ② 激光干涉条纹方法
法
:
光栅的结构:底部 为玻璃板,上层为 金属镀膜。
机械式光栅刻线实际上是使用挤压的方式使被加工材料发生塑 性变形形成光栅沟。
第六章 脆硬非金属材料精密加工
精密加工技术
第六章 脆硬非金属材料精密加工
一、陶瓷的精密加工
?什么是陶瓷?陶与瓷区别在哪? ?日常生活中都会接触哪些陶瓷
① 一般陶瓷的密度低于金属。
② 陶瓷与金属相比硬度要高得多。
陶 瓷
③ 陶瓷的弹性模量大。
特 ④ 陶瓷熔点一般高与金属,但常温下没有固定的熔点。
点
⑤ 热导率一般较低。
⑥ 热膨胀系数小。
千米时所加工表面质量不能有明显的下降。 金刚石刀具一般不采用尖刃刀尖。
硬脆材料端面微磨削的磨削力及试验研究

硬脆材料端面微磨削的磨削力及试验研究王克军;刘璇;李辉;王力影【摘要】端面微磨削对于加工硬脆材料具有显著的优势.磨削力是磨削机理研究的主要参数之一.本文基于微磨削的特点和逆磨与顺磨的不同,建立了磨削力模型.采用石英玻璃对端面微磨削进行实验研究.通过实验数据对理论模型参数值进行确定,完善并修正磨削力模型.通过实验测得的数据验证磨削力理论模型的正确性,并分析误差产生的原因.%Micro end grinding has significant advantages for processing hard and brittle materials.Grinding forces are important characteristic parameters of micro grinding mechanism research.A theoretical model of the grinding force is built which considers micro grinding characteristics and the differences between up grinding and down grinding.The silica glass is used for grinding experiment research.Through the experiment data, parameter values of the theoretical model can be determined, and the grinding force model can be perfected.The experimental data verifies the theoretical model of grinding force and the error is analyzed.【期刊名称】《科学技术与工程》【年(卷),期】2016(000)029【总页数】5页(P212-216)【关键词】端面微磨削;磨削力;顺磨;逆磨【作者】王克军;刘璇;李辉;王力影【作者单位】河北工业大学机械工程学院,天津 300130;河北工业大学机械工程学院,天津 300130;河北工业大学机械工程学院,天津 300130;河北工业大学机械工程学院,天津 300130【正文语种】中文【中图分类】TG580.61微磨削技术采用磨头直径小于1 mm的微砂轮,加工尺寸在1 mm以下,加工精度在0.01~0.001 mm的零件,根据所需工件形貌对材料进行机械去除,尤其适用于加工脆硬材料微型零件[1]。
- 1、下载文档前请自行甄别文档内容的完整性,平台不提供额外的编辑、内容补充、找答案等附加服务。
- 2、"仅部分预览"的文档,不可在线预览部分如存在完整性等问题,可反馈申请退款(可完整预览的文档不适用该条件!)。
- 3、如文档侵犯您的权益,请联系客服反馈,我们会尽快为您处理(人工客服工作时间:9:00-18:30)。
硬脆材料超精密加工关键技术研究随着科技的快速发展,超精密加工技术已经成为现代制造业中不可或缺的关键技术之一。
尤其是在硬脆材料的加工中,超精密加工技术的应用显得尤为重要。
本文将详细探讨硬脆材料超精密加工的关键技术,以期为相关领域的研究和应用提供有益的参考。
超精密加工技术是指通过采用高精度的机床、工具和工艺方法,将原材料或半成品加工成精度高、表面质量好的最终产品。
从20世纪60年代开始,随着计算机、激光、新材料等技术的飞速发展,超精密加工技术也不断取得重大突破。
如今,超精密加工技术已经广泛应用于航空、航天、能源、医疗等领域。
在硬脆材料的加工中,超精密加工技术可以有效提高加工效率和产品质量。
例如,利用超精密加工技术可以制造出高精度的光学元件、半导体芯片、陶瓷零件等,这些产品在各自领域都具有重要的应用价值。
硬脆材料由于其硬度高、脆性大等特点,加工过程中容易出现裂纹、崩边、表面粗糙等问题。
因此,在硬脆材料的超精密加工中,需要解决以下难点:裂纹问题:硬脆材料在加工过程中容易产生裂纹,降低产品的合格率。
崩边问题:由于硬脆材料的硬度较高,加工时容易出现崩边现象,影响产品的精度和表面质量。
表面粗糙问题:硬脆材料在加工过程中容易出现表面粗糙的现象,影响产品的性能和使用寿命。
机床和工具的精度问题:由于硬脆材料的加工精度要求高,因此需要高精度的机床和工具来保证。
采用先进的加工工艺和工具,如激光加工、水刀切割、超声波加工等,以减少加工过程中对材料的损伤。
对硬脆材料进行预处理,如加热、冷却、加载等,以改善其加工性能。
采用高精度的机床和工具,并定期进行维护和校准,以保证加工的精度和稳定性。
对加工参数进行优化,如切削速度、切削深度、进给速度等,以提高加工效率和产品质量。
下面以光学元件和陶瓷零件的超精密加工为例,说明超精密加工技术在硬脆材料加工中的应用。
光学元件的超精密加工:光学元件是光学系统的基本组成部分,其精度和表面质量对整个光学系统的性能有着至关重要的影响。
超精密加工技术可以用于制造高精度的光学元件,如透镜、棱镜、反射镜等。
通过采用先进的超精密加工工艺和检测技术,可以保证光学元件的精度和表面质量,提高整个光学系统的性能。
陶瓷零件的超精密加工:陶瓷材料具有高硬度、高耐磨性、高温稳定性等特点,因此在许多领域得到广泛应用。
然而,由于陶瓷材料的硬度和脆性较大,其加工难度也相对较大。
超精密加工技术可以解决陶瓷零件的加工难题,制造出高精度的陶瓷零件,如轴承、密封件、喷嘴等。
通过采用先进的超精密加工工艺和陶瓷专用刀具,可以保证陶瓷零件的精度和表面质量,提高产品的可靠性和使用寿命。
为了验证超精密加工技术在硬脆材料加工中的效果,分别对光学元件和陶瓷零件进行了实验验证。
光学元件的实验验证:采用超精密加工技术制造了10个光学元件,并与传统加工方法制造的光学元件进行了对比实验。
实验结果表明,超精密加工技术制造的光学元件在精度、表面质量和透光率等方面均优于传统加工方法制造的光学元件。
同时,对实验结果进行了量化分析,得出了超精密加工技术可以提高光学元件的质量和性能的结论。
陶瓷零件的实验验证:采用超精密加工技术制造了10个陶瓷零件,并与传统加工方法制造的陶瓷零件进行了对比实验。
实验结果表明,超精密加工技术制造的陶瓷零件在精度、表面质量和耐磨性等方面均优于传统加工方法制造的陶瓷零件。
同时,对实验结果进行了量化分析,得出了超精密加工技术可以提高陶瓷零件的质量和性能的结论。
本文对硬脆材料超精密加工关键技术进行了深入研究,得出了以下超精密加工技术在硬脆材料加工中具有广泛的应用前景,可以制造出高精度、高质量的产品,提高产品的性能和使用寿命。
在硬脆材料超精密加工中,需要解决裂纹、崩边、表面粗糙等难点问题。
本文旨在深入探讨精密磨料水射流加工硬脆材料的冲蚀机理及抛光技术。
简要介绍精密磨料水射流加工硬脆材料的相关背景及其在工业领域的应用前景;接着,详细分析精密磨料水射流加工硬脆材料的冲蚀机理,包括冲蚀过程、影响因素等;对精密磨料水射流加工硬脆材料的抛光技术进行探讨,阐述常规抛光方法及存在的问题。
精密磨料水射流加工是一种新型的加工技术,具有非接触、无热效应、高效节能等特点,被广泛应用于硬脆材料的加工领域。
硬脆材料是指硬度高、脆性大的材料,如玻璃、陶瓷、硬质合金等,这些材料具有优异的性能,如高硬度、高耐磨性、高耐腐蚀性等,因此在工业领域具有广泛的应用前景。
精密磨料水射流加工硬脆材料的冲蚀机理主要是基于高压水射流对材料的冲击作用,使材料表面受到冲击而产生微裂纹,同时磨料在冲击过程中对材料表面进行切削和磨损,从而实现对材料表面的加工。
冲蚀过程受到多个因素的影响,如水射流压力、磨料类型和粒度、冲击角度等。
在精密磨料水射流加工硬脆材料的过程中,为了获得更好的加工效果,通常需要进行抛光处理。
常规的抛光方法包括机械抛光、化学抛光和电解抛光等。
然而,这些方法存在一些问题,如加工效率低、抛光效果不佳等。
因此,需要研究更加高效、准确的抛光技术,以提高精密磨料水射流加工硬脆材料的表面质量。
精密磨料水射流加工硬脆材料的应用前景十分广阔。
在航空航天领域,硬脆材料被广泛应用于制造各种零部件,如涡轮发动机叶片、航空框架等,通过精密磨料水射流加工技术可以提高零部件的精度和表面质量,从而提高航空航天器的性能和可靠性。
在汽车制造领域,硬脆材料被用于制造发动机缸体、气缸盖等关键部件,通过精密磨料水射流加工技术可以实现对硬脆材料的高效、精准加工,从而提高汽车的性能和品质。
在能源领域,硬脆材料被用于制造太阳能电池板、核反应堆零部件等,通过精密磨料水射流加工技术可以实现对硬脆材料的精细加工,提高能源利用效率和设备可靠性。
在医疗器械领域,硬脆材料被广泛应用于制造各种高精度医疗设备,如光学仪器、人工关节等,通过精密磨料水射流加工技术可以实现对硬脆材料的精细加工,提高医疗设备的性能和可靠性。
精密磨料水射流加工硬脆材料的技术在工业领域具有广泛的应用前景,深入研究其冲蚀机理及抛光技术对于提高硬脆材料的加工效率和表面质量具有重要意义。
未来,需要进一步研究高效、环保的加工技术,拓展精密磨料水射流加工硬脆材料的应用领域,促进工业制造领域的可持续发展。
微结构阵列的超精密切削加工与测量关键技术研究微结构阵列在众多领域具有广泛应用,如微电子、生物医学和光学等。
微结构阵列的超精密切削加工与测量关键技术对于提高微结构阵列的制造质量和精度具有重要意义。
本文将围绕微结构阵列的超精密切削加工与测量关键技术进行深入探讨。
微结构阵列超精密切削加工技术是一种高精度的制造方法,其主要特点是利用超精密机床和刀具,在微米甚至纳米级别对材料进行切削加工。
为了达到超高的精度,微结构阵列超精密切削加工技术需要解决的关键因素包括机床精度、刀具性能、切削热效应、切削力效应等。
在微结构阵列超精密切削加工过程中,机床精度的提高是实现高精度制造的基础。
同时,刀具的性能也对加工质量产生重要影响,包括刀具的硬度、耐磨性和抗冲击性等。
切削热效应和切削力效应也是影响加工质量的重要因素。
为了解决这些挑战,可以采取以下措施:提高机床的设计和制造精度,采用先进的误差补偿技术,以实现更高精度的加工。
研发高性能的刀具材料和涂层技术,提高刀具的寿命和性能。
探索切削工艺优化方法,以降低切削热效应和切削力效应的影响。
微结构阵列测量技术是确保制造精度和质量的关键手段。
其主要特点是通过各种测量方法和仪器,在微米甚至纳米级别对材料进行尺寸、形状、位置等参数的测量。
为了达到高精度的测量,微结构阵列测量技术需要解决的关键因素包括测量方法的选取、测量设备的精度、环境干扰等。
在微结构阵列测量过程中,测量方法的选取应根据具体的应用场景和要求进行。
例如,光学测量方法具有非接触、高精度和高效率等特点,但在复杂形状和多层结构的测量方面可能受到限制。
而扫描电子显微镜(SEM)和原子力显微镜(AFM)等微观形貌测量方法则可以对复杂结构和多层结构进行高精度测量。
测量设备的精度也对测量结果产生重要影响,因此需要定期进行设备校准和维护。
为了解决这些挑战,可以采取以下措施:根据实际应用需求,选取合适的测量方法,如光学测量、形貌测量等。
提高测量设备的精度和稳定性,采用先进的误差补偿和数据处理技术。
构建稳定的测量环境,降低环境因素对测量结果的影响。
微结构阵列超精密切削加工与测量关键技术之间具有密切的和相互作用。
超精密切削加工技术的进步可以提升微结构阵列的制造精度和质量,而测量技术的提升则可以为超精密切削加工提供准确的反馈和指导。
通过对微结构阵列超精密切削加工与测量关键技术的特点和优势进行分析,可以发现两者之间的协同作用可以进一步提高微结构阵列的制造水平和精度。
超精密切削加工技术的优势在于高精度、高效率和高可靠性,而测量技术的优势在于准确、快速和非接触性。
通过将两者进行有机结合,可以实现微结构阵列制造的高精度、高效率和低成本。
未来发展方向和关键技术路线可以包括以下方面:提升机床和刀具的设计和制造水平,研发更高效的切削工艺,以实现更高精度的超精密切削加工。
拓展测量方法的适用范围和提高测量设备的精度,研发更准确、快速和非接触性的测量技术,以实现更准确的微结构阵列测量。
建立微结构阵列超精密切削加工与测量综合应用平台,将加工和测量过程进行一体化设计,以实现更高效、准确的微结构阵列制造。
加强基础研究,包括机床动力学、刀具磨损、切削热效应、切削力效应等方面,以为微结构阵列超精密切削加工与测量提供更全面的理论和技术支持。
结论本文对微结构阵列的超精密切削加工与测量关键技术进行了深入探讨。
通过对微结构阵列超精密切削加工技术、测量技术以及两者之间的综合应用进行分析,可以发现这些关键技术在微结构阵列制造中具有重要地位和应用价值。
未来,随着科学技术的不断发展和进步,微结构阵列超精密切削加工与测量关键技术必将不断创新和完善,为微结构阵列的高精度制造提供更为强大和有效的支持。
随着科学技术的发展,发动机叶片作为航空发动机的关键部件,其性能和精度的提高对于整个发动机的性能和效率有着至关重要的影响。
精密电解加工技术作为近年来发展迅速的一种加工技术,其高效、高精度、低成本的优势引起了人们的广泛。
本文将围绕发动机叶片精密电解加工关键技术进行展开,旨在提高发动机叶片的制造质量和生产效率。
目前,发动机叶片的制造主要采用传统的切削加工方法,但这些方法存在着刀具磨损、表面粗糙度差、生产效率低等问题。
而精密电解加工技术通过利用电化学反应实现工件的加工,具有无需切削力、加工精度高、表面质量好等优点,因此在发动机叶片制造中具有广阔的应用前景。
发动机叶片精密电解加工关键技术主要包括以下几个方面:电解液的选择与优化:电解液是电解加工的核心要素之一,其选择与优化直接影响到加工过程的稳定性、加工精度和表面质量。