常减压电脱盐操作流程共27页文档
常减压装置操作规程

第一章装置概述及主要设计依据本装置由闪蒸、常压蒸馏、减压蒸馏、电脱盐、、三注等部分组成。
主要产品为:汽油馏分、柴油、重柴油、减压馏分和燃料油。
一、本装置主要以下技术特点1、该装置采用二级交直流电脱盐、水技术,并采用在各级电脱盐罐前注破乳剂和注水等技术措施,以满足装置原料含盐、含水量、含硫、含酸的要求,电脱盐部分的主要技术特点为:(1)在电脱盐罐前设混合阀,以提高操作的灵活性并达到混合均匀的目的;(2)交流全阻抗防爆电脱盐专用变压器,以保护电脱盐设备安全平稳操作;(3)不停工冲洗,可定期排污;(4)采用组合式电极板;(5)设低液位开关,以保证装置操作安全;3、装置设置了闪蒸塔,以减少进常压炉的轻组分,并使原油含水在闪蒸塔汽化,避免对常压塔操作负荷的冲击。
4、在闪蒸塔、常压塔、减压塔顶采用注水、注中和缓蚀剂等防腐措施。
5、常压塔加热炉分别设空气预热器和氧含量检测、控制仪表,不凝汽引入加热炉燃烧,以节约能源并减少污染。
6、采用低速减压转油线,降低了转油线压降,以提高拔出率。
7、为了有效利用热能,对换热流程进行了优化设计,提高了换后温度,降低了能耗。
部分换热器管束采用了螺纹管和内插物等高效换热器,提高传热强度,减少设备台位,降低设备投资。
8、采用全填料干式减压蒸馏工艺,降低能耗,提高蜡油拔出率。
减压塔采用槽盘式分布器、辐射式进行分布器、无壁流规整填料等多项专利技术,可改善减压塔的操作状况、优化操作参数,提高产品质量。
9、减一中发生器蒸汽,供装置汽提用,较好地利用装置的过剩蒸汽,降低了装置能耗。
10、常压塔、常压汽提塔采用立式塔盘。
11、常顶油气与原油换热,提高低温位热量回收率。
12、采用浙大中控DCS软件进行流程模拟,优化操作条件。
二、装置能耗装置名称:60万吨/年常减压装置。
设计进料量:60万吨/年。
装置组成:电脱盐、常减压蒸馏、常减炉。
第二章工艺流程一、工艺流简述1、工艺流程说明约40℃的原油由设在罐区的原油泵(P-101/1.2)送入装置,原油进入装置后进入原油—常顶油气换热器(E-101/1.2)、然后分成两路换热网络,一路由原油—常一线换热器(E-102)、原油—常三线(二)换热器(E-103)、原油-常二线换热器(E-104/1.2)换热到122℃,在第二路原油经原油—减一线及减顶循换热器(E-105/1.2)、原油—减二线换热器(E-106/1.2)、原油—减三线换热器(E-107/1.2)换热到137℃,原油出换热网络I段后合并成一路原油升温至130℃进入电脱盐脱水系统,原油脱盐脱水系统采用二级交直流电脱盐工艺进行深度脱盐脱水。
电脱盐操作规程

电脱盐操作规程1.1 电脱盐系统严格执行电脱盐岗位的工艺操作指南,电脱盐岗位负责从原油入电脱盐罐到出电脱盐罐的全部流程,包括:原油流程、新鲜水(或净化水)流程、软化水、反冲洗线、破乳剂线及其附属设备的操作与维护。
电脱盐岗位的平稳操作是常压岗位安全平稳生产的前提和保障。
电脱盐原理:原油中含有水,NaCl、CaCl2、MgCl2等盐类,这些盐和水存在,给炼油装置的平稳操作,设备,产品质量带来了严重危害,必须加以脱除,电脱盐系统是将换热到一定温度的原油注入适量的破乳剂及新鲜水,在高压电场的作用下,将原油中微小水滴聚结成大水滴,靠油水密度差将水分离,达到脱盐脱水的目的。
电脱盐工艺过程简述:原油进装置后,注入20-50ppm(占原油)的破乳剂(油溶性),由脱前换热器(7台)进行换热,换热后温度达130℃左右,然后注入新鲜水,最后经混合阀使原油、水、破乳剂(水溶性)、杂质充分进行混合,进入电脱盐,电脱盐罐压力控制在1.1MPa左右,电脱盐脱盐水原理:罐内设有金属电极板,上层接地,下层接电,在电极板之间形成高压电场,在破乳剂和高压电场作用下,产生破乳剂和水滴极化,小水滴聚成大水滴,具有一定的质量后,由于油水密度差,水穿过油层落于罐底,由于水具有导电性,下层接电极板与水层之间又形成一弱电场,促使油水进一步分离,从而达到脱除水和溶解于水中盐的目的,罐底的水通过自动控制连续地自动排出,脱盐后油从罐顶集合管流出,进入脱盐原油换热部分。
1.2 电脱盐进料温度控制原油温度高低对于脱盐效率高低影响较大,为此应避免原油温度突然大幅度波动,变化温度不应超过5℃/15分钟,最佳温度为130±5℃。
温度过低,脱盐率下降,温度过高,会因原油汽化或导电率增大而引起操作不正常,因原油导电性随温度升高而增大,这样电流的增加就会使电极板上的电压降低,会影响脱盐效果。
渣油量及渣油温度变化,各侧线量及侧线温度变化,原油含水情况等因素都将影响进料温度和换热终温。
常减压装置操作规程完整

.第一章装置概述及主要设计依据本装置由闪蒸、常压蒸馏、减压蒸馏、电脱盐、、三注等局部组成。
主要产品为:汽油馏分、柴油、重柴油、减压馏分和燃料油。
一、本装置主要以下技术特点1、该装置采用二级交直流电脱盐、水技术,并采用在各级电脱盐罐前注破乳剂和注水等技术措施,以满足装置原料含盐、含水量、含硫、含酸的要求,电脱盐局部的主要技术特点为:〔1〕在电脱盐罐前设混合阀,以提高操作的灵活性并到达混合均匀的目的;〔2〕交流全阻抗防爆电脱盐专用变压器,以保护电脱盐设备平安平稳操作;〔3〕不停工冲洗,可定期排污;〔4〕采用组合式电极板;〔5〕设低液位开关,以保证装置操作平安;3、装置设置了闪蒸塔,以减少进常压炉的轻组分,并使原油含水在闪蒸塔汽化,防止对常压塔操作负荷的冲击。
4、在闪蒸塔、常压塔、减压塔顶采用注水、注中和缓蚀剂等防腐措施。
5、常压塔加热炉分别设空气预热器和氧含量检测、控制仪表,不凝汽引入加热炉燃烧,以节约能源并减少污染。
6、采用低速减压转油线,降低了转油线压降,以提高拔出率。
7、为了有效利用热能,对换热流程进展了优化设计,提高了换后温度,降低了能耗。
局部换热器管束采用了螺纹管和插物等高效换热器,提高传热强度,减少设备台位,降低设备投资。
8、采用全填料干式减压蒸馏工艺,降低能耗,提高蜡油拔出率。
减压塔采用槽盘式分布器、辐射式进展分布器、无壁流规整填料等多项专利1 / 76技术,可改善减压塔的操作状况、优化操作参数,提高产品质量。
9、减一中发生器蒸汽,供装置汽提用,较好地利用装置的过剩蒸汽,降低了装置能耗。
10、常压塔、常压汽提塔采用立式塔盘。
11、常顶油气与原油换热,提上下温位热量回收率。
12、采用浙大中控DCS软件进展流程模拟,优化操作条件。
二、装置能耗装置名称:60万吨/年常减压装置。
设计进料量:60万吨/年。
装置组成:电脱盐、常减压蒸馏、常减炉。
.第二章工艺流程3 / 76一、工艺流简述1、工艺流程说明约40℃的原油由设在罐区的原油泵〔P-101/1.2〕送入装置,原油进入装置后进入原油—常顶油气换热器〔E-101/1.2〕、然后分成两路换热网络,一路由原油—常一线换热器〔E-102〕、原油—常三线〔二〕换热器〔E-103〕、原油-常二线换热器〔E-104/1.2〕换热到122℃,在第二路原油经原油—减一线及减顶循换热器〔E-105/1.2〕、原油—减二线换热器〔E-106/1.2〕、原油—减三线换热器〔E-107/1.2〕换热到137℃,原油出换热网络I段后合并成一路原油升温至130℃进入电脱盐脱水系统,原油脱盐脱水系统采用二级交直流电脱盐工艺进展深度脱盐脱水。
脱盐水操作规程

目录1适用范围及职责范围 (1)1.1适用范围 (1)1.2岗位的任务和管辖范围 (1)1.2.1岗位的任务 (1)1.2.2 岗位的管辖范围 (1)1.3职责范围(从属关系) (1)2工艺原理及工艺流程叙述 (1)2.1工艺原理 (1)2.1.1自清洗过滤器工艺原理 (1)2.1.2超滤装置工艺原理 (2)2.1.3保安过滤器工艺原理 (2)2.1.4反渗透工艺原理 (2)2.1.5脱碳器工艺原理 (2)2.1.6混床工艺原理 (3)2.2工艺流程叙述 (3)2.3 系统辅助流程 (4)3工艺指标及质量要求 (5)3.1 工艺指标 (5)3.1.1进水水质 (5)3.1.2主要技术参数 (7)3.1.3流量 (10)3.1.4温度 (10)3.1.5压力 (10)3.1.6液位 (11)3.1.7电导率仪 (11)3.1.8在线分析 (12)3.2质量要求 (12)3.2.1 生产能力 (12)3.2.2 产品及副产品质量 (12)3.2.3 消耗定额及能耗 (12)4.开车程序 (12)4.1原始开车程序 (12)4.1.1开车前的准备工作 (12)4.1.2自清洗过滤器 (13)4.1.3超滤系统 (13)4.1.4反渗透系统 (14)4.1.5混床系统 (16)4.2 短期停车后的开车(详见长期停车后的开车) (16)4.3 长期停车后的开车 (16)4.3.1自清洗过滤器手动启动 (16)4.3.2自清洗过滤器的程序启动 (16)4.3.3 超滤组件手动启动 (16)4.3.4超滤系统的程序启动 (16)4.3.5反渗透系统手动启动 (17)4.3.6反渗透系统程序启动 (17)4.3.7混床系统手动启动 (17)4.3.8混床系统的程序开车 (17)5 正常操作及维护 (18)5.1自清洗过滤器的操作和维护 (18)5.1.1投运 (18)5.1.2停运 (18)5.1.3反洗 (18)5.1.4 维护 (18)5.2超滤装置的操作和维护 (19)5.2.1投运 (19)5.2.2停运 (19)5.2.3反洗 (19)5.2.4反洗步骤 (19)5.2.5化学清洗 (20)5.2.6维护 (20)5.3保安过滤器的维护 (21)5.4反渗透系统的操作 (21)5.4.1运行 (21)5.4.2停运 (22)5.4.3冲洗 (22)5.4.4化学清洗 (22)5.4.5维护 (25)5.5混床装置的正常操作 (26)5.5.1投运 (26)5.5.2停运 (26)5.5.3混床再生 (26)5.5.4维护 (27)6 停车程序 (29)6.1 计划停车程序 (29)6.1.1混床系统停车 (29)6.1.2反渗透系统停车 (29)6.1.3超滤停车 (29)6.2 紧急停车程序 (30)6.3 事故停车程序 (30)7 事故处理 (30)7.1反渗透系统故障处理 (30)7.2混床系统故障处理 (32)8 主要运转设备的开、停车操作程序 (33)8.1离心泵的开、停车操作 (33)8.1.1离心泵的开车 (33)8.1.2离心泵的停车 (34)8.1.3维护/检查 (34)8.1.4故障及其排除 (35)8.2风机的开、停车操作 (36)8.2.1风机开车 (36)8.2.2风机停车 (36)8.3计量泵操作规程 (36)9 安全生产要点 (39)9.1 人身安全要点 (39)9.2安全巡检与设备安全要求 (39)9.3主要防范措施 (40)10 巡回检查内容及要求 (40)10.1巡检频率 (40)10.2巡检要求 (40)10.3巡检路线 (41)10.4巡检内容 (41)11 特殊操作方案 (42)11.1卸酸操作规程 (42)11.1.1运行前准备工作 (42)11.1.2卸酸 (42)11.1.3停止卸酸 (42)11.1.4维护 (42)11.2卸碱操作规程 (43)11.2.1运行前准备工作 (43)11.2.2卸碱 (43)11.2.3停止卸碱 (43)11.2.4维护 (43)12 冬季防冻要点 (43)13 附录 (43)13.1污染指数(SDI)测定方法 (43)13.2工艺流程图 (45)13.3 化学水平衡图(另发) (45)13.4 连锁说明及连锁值一览表 (46)13.5分析项目及频率一览表 (47)13.6设备一览表 (48)1适用范围及职责范围1.1适用范围本规程适用于229#界区内所有的管线、仪表、转动设备和静止设备的操作及日常维护管理。
常减压电脱盐装置原则流程图

补充吸收泵
催化吸收稳定部分流程图
烟气再生器来 三级旋分器
四旋及催化剂 细粉收集罐
催化剂细粉贮罐
双动滑阀 降压孔板室
锅炉放空水封罐
烟囱
临界流速喷嘴 烟机出口水封罐
烟气锅炉 锅炉入口水封罐
主风至再生器
烟机
主风机 变速箱 电动发电机
备用风机 变速箱 电动发电机
催化装置烟气回收部分流程图
干气自催化来
干气自加氢裂化来 干气自重整来
至常顶产品罐
轻烃回收装置原则流程
压缩干气 不凝气
液化气
常
石脑油至罐区
顶 油
石脑油至重整
K-102
K-101H2来自管网 低分气至PSA
R-101 F-101
冷H2
C-101 注水
E-102
A-101 E-103
A-102
D-103
R-102
渣油
E-101
D-114
E-105
D-104
D-101
D-102
P-77
P-102
D-105
D-106
SR-101
RDS 装置流程图
C-102
E-208
D-201 石脑油出装置 P-204
C-201
C-202
柴油出装
加氢尾油至FCC
F-201
高分排放气 脱硫低分气 重整氢
原料气自界区外来
PSA 装置流程图
产品氢去界区外 去火炬
尾气去制氢 解吸气压缩机
补充新氢
补充碱液过滤器
碱
氧化空气
空气 过滤器
液 氧 化
塔
碱液自催化液
化气脱硫醇部分 碱液自常减压液 化气脱硫醇部分
电脱盐操作

电脱盐岗位操作原油是由不同烃类化合物组成的混合物,其中还含有少量其他物质,主要是少量金属盐类、微量重金属、固体杂质及一定量的水。
所含的盐类除少量以晶体状态悬浮于油中外,大部分溶于原油所含水中,形成含盐水并与原油形成乳化液。
在这种乳化液中,一般含盐水为分散相,而原油则为连续相,形成油包水型乳化液。
这些物质的存在会对原油加工产生一系列的不利影响。
因此,应在加工之前对原油进行预处理,以除去或尽量减少这些有害物质。
一、原油中含盐、含水对常减压装置及下游装置加工带来的危害1、影响常减压装置蒸馏的平稳操作:原油中的少量水被加热汽化后体积会急剧增加,占用大量的管道、设备空间,相应地减少了装置的加工能力。
另外,水的突然汽化还会造成系统压降增加,泵出口压力升高,动力消耗增加。
同时,也会使原油蒸馏塔内气体速度增加,导致操作波动,严重时还会引起塔内超压和冲塔事故。
2、增加常减压装置蒸馏过程中的能量消耗:3、造成设备和管道的结垢或堵塞4、造成设备和管道腐蚀5、造成后续加工过程催化剂中毒6、影响产品质量一、脱盐脱水原理原油中的盐,太多数溶于水中,少部分以固体存在。
由于原油中有环烷酸等乳化剂,使原油与水形成较稳定的油包水乳化液。
我们在原油中加水(软化水)是为了溶解原油中的固体盐,然后把原油中的水脱掉,盐也就脱掉了。
但因原油与其形成的乳化液很稳定,不好脱,我们就用电破乳法将乳化液通过高压电场时,水滴就因为感应或其它原因带上电荷。
有的带上正电荷,有的带上负电荷,有的则是原有带的电荷,有的水滴一端可能带正电荷,另一端带负电荷。
在高压电场作用下,带正电荷的水滴向负极运动,而带负电荷的则向正极运动。
在移动过程中,在介质阻力的作用下,原为球形的液滴变成卵形。
表面形状的改变,使薄膜各处所受的张力不等而被削弱,甚至破坏。
不同电荷的水滴又相互吸引、碰撞,小水滴合并为大水滴。
在重力作用下逐渐沉降下来,进入水相脱除。
二、工艺卡片压力:≯1.0MPa,≮0.6Mpa温度: 110-140℃混合阀前后差压: 0.01-0.1 MPa油水界位: 30-60%注水量:一级:3~5%;二级:4~6%(对原油)脱后含盐: ≯3mg/l脱后含水:≤0.5%切水含油:≯150 mg/l相电流:≯额定电流。
常减压操作规程

常减压装置操作规程目录概述:第一章本装置的工艺原理及生产数据-----------------------------------------------------第一节工艺原理---------------------------------------------------------------------------第二节生产数据---------------------------------------------------------------------------第二章工艺流程------------------------------------------------------------------------------ 附:工艺流程图、装置平面布置图、供排水图、精制、脱盐流程图第三章设备一览表------------------------------------------------------------------------------- 第一节塔------------------------------------------------------------------------------------- 第二节加热炉-------------------------------------------------------------------------------- 第三节容器----------------------------------------------------------------------------------- 第四节换热器、冷却器-------------------------------------------------------------------- 第五节机泵----------------------------------------------------------------------------------- 第六节安全阀-------------------------------------------------------------------------------- 第七节仪表量程及调节器的作用--------------------------------------------------------第四章开停工操作-------------------------------------------------------------------------- 第一节开工操作----------------------------------------------------------------------第二节停工操作----------------------------------------------------------------------------- 第三节装置开工中容易出现的事故及原因--------------------------------------------第五章岗位操作规程---------------------------------------------------------------------------- 第一节常压岗位操作法-------------------------------------------------------------------- 第二节减压岗位操作法------------------------------------------------------------------- 第三节加热炉岗位操作法----------------------------------------------------------------- 第四节司泵岗位操作法--------------------------------------------------------------------- 第五节精制岗位操作法--------------------------------------------------------------------- 第六节脱盐岗位操作法--------------------------------------------------------------------- 第六章事故处理--------------------------------------------------------------------------------第七章安全规程------------------------------------------------------------------------------------- 第一节冬季防冻凝规定--------------------------------------------------------------------- 第二节硫化氢安全知识---------------------------------------------------------------------- 第三节防火防爆规定-------------------------------------------------------------------------- 第四节检修操作及人身安全规定---------------------------------------------------------- 第八章环境保护规定-----------------------------------------------------------------------------概述第一章本装置的工艺原理及生产数据第一节工艺原理原油是一种由碳氢化合物组成的混合物,它们的沸点不同,常减压装置主要利用混合物的沸点差,把原油通过加热炉加热在精馏塔内产生汽化,精馏塔内在有回流的情况下,上升气体穿过塔板液相时,汽液两相进行热交换,汽体中的重组份被冷凝下来,留在塔板液相液体中,轻组份被上升气体加热后重新汽化,上升至上层塔板。
常减压操作规程

常减压装置概述装置概况1.1本装置由换热初馏、常压蒸馏、减压蒸馏、加热炉、电脱盐、三注、电精制部分组成。
原料油以新疆库西外输混合原油为主,主产品主要有:100#、140#、180#道路沥青(减压渣油),副产品为:(汽油)、溶剂油、轻柴油、重柴油、减压蜡油等。
1.2装置布置在厂区的中央地带,西邻辅助区,东靠储油区,南北各预留一装置,全装置占地面积3652㎡。
本装置采用以微计算机技术为基础的具有高灵活性和高可靠性的集散型控制系统(DCS)。
1.2.1该装置采用二级交直流电脱盐、脱水技术,采取在各级电脱盐罐前注破乳剂和注水等技术措施,以满足装置原料含盐、含水的要求,其主要特点有:1.2.1.1电脱盐罐前设混合调节阀,以提高操作的灵活性并达到混合均匀的目的1.2.1.2采用交流全阻抗防爆电脱盐专用变压器,以保证电脱盐设备的安全平稳操作1.2.1.3不停工冲洗,可定期排污1.2.1.4采用组合式电极板1.2.1.5设低液位开关,以保证装置操作安全。
1.2.2装置设置初馏塔,以减少进常压炉的轻组分,从而降低了加热炉负荷,并使原油含水在初馏塔汽化,避免对常压塔操作负荷的冲击。
初馏塔设侧线抽出溶剂油产品,并采用专利技术将常压塔顶油引入初馏塔,增加初顶冷回流量,提高了溶剂油产品的质量和产量。
1.2.3在初馏塔、常压塔、减压塔顶采用注水,注氨气、注缓蚀剂等防腐措施。
1.2.4加热炉设空气预热器和氧含量检测控制仪表,不凝气引入加热炉燃烧以节约能源并减少污染。
1.2.5减压系统采用低速转油线,转油线热膨胀由炉管吸收,降低了转油线压降、温降,以提高拔出率。
1.2.6为了有效利用热能,采用窄点分析技术对换热流程进行了优化设计,以提高换后温度,降低能耗,部分换热器采用了折流杆、螺纹管和内插物等强化传热措施,提高传热强度,减少设备台位,降低设备投资。
1.2.7采用全填料干式减压蒸馏工艺,减压塔采用槽盘式分布器,辐射式进料汽液分布器,规整填料等多项新技术。
电脱盐操规程

电脱盐操作规程1、电脱盐的基本原理原油脱盐、脱水装置的主要任务是将油中的分散的很细、并被一层牢固乳化膜包围的水滴进行聚结、脱除。
由于单纯依靠重力作用难以沉降脱除,因此一般采用加热、加入化学药剂和高压电场三个破乳手段。
对炼厂来说,这三个手段同时采用,但后者是主要的。
采用加热的办法,提高温度可以降低乳化液滴表面膜的强度,但是只有在石蜡占优势的天然乳化剂的石油乳化液中,在加热时,油水方能分层,而这类乳化液为数不多。
实际上,常常是通过加入破乳剂来进行破乳。
其实质就是降低表面膜的结构——机械“栅栏”的能量,使表面膜破坏。
从而使微小的乳化的水滴而结成大的水滴而沉降下来。
一般认为,化学破乳剂在破乳过程中分为四个阶段:1)把药剂加到原油中,并使之分布到整个油相中,进入到被乳化的水滴上;2)药剂渗入到到被乳化的水滴的保护层,并使保护层破坏;3)保护层破坏后,破乳化的水滴互相接近和接触;4)液滴聚结,破乳化的水滴从连续相分离出来。
高压电场破乳的机理在于它能使水滴产生诱导偶极,或带上静电荷,从而在水滴与水滴间,水滴与电极间产生静电力。
水滴受力的作用,运动速度增大,动能增加。
当水滴互相碰撞时,其动能和静电引力能够克服乳化膜的障碍而彼此聚结起来。
在聚结作用的同时,电场还会使水滴发生分散作用,即由于偶极矩的增大,水滴变形加剧导致在电场作用下最后分裂开。
在正常操作条件下,水滴的聚结是主要的,而只有电位梯度相当高时,水滴的电分散趋势不可忽视。
水滴迅速聚结直径变大后,在其重力的作用下,克服了原油自下向上的流动的作用力逐渐沉降到罐下部来。
见图高压电场对油中水滴的作用示意图1——被极化变形而带感生电荷的水滴;2——两水滴在偶极间力作用下碰撞;3——接触电极而带静电荷的水滴,在静电力下向另一极运动;4——较大水滴因静电力而拉长;5——拉长时的水滴在电场作用下分裂成小水滴。
一般情况下,原油中的盐是溶于水的。
当沉积到罐下部的水被脱除时,原油中部分盐溶于水随之脱除。
常减压流程介绍

常减压流程介绍1. 装置流程简述原油泵P101A/B抽罐区的原油,到装置内经过三路换热,到电脱盐罐经过脱盐、脱水,脱后原油继续经过两路换热后进入初馏塔T101,T101顶出重整料,不凝气去原油稳定,当原油稳定停工时去加热炉烧掉。
T101底油经泵P104A/B抽出,经过两路换热到300℃后到常压炉被加热到365℃左右进入常压塔T102第四层上方。
经过常压塔精馏后,常压塔顶油汽经过冷凝冷却后的汽油一部分打入塔顶,一部分作为常顶汽油出装置,不凝气到常压炉烧掉。
然后从上到下侧线依次馏出常一线、常二线、常三线、常四线,常一线油进常一线汽提塔T103,通过重沸器加热,其汽相返回到T102,液相抽出经空气预热器E130、脱硫醇系统送出装置,常二、三、四线经汽提塔T104汽提,汽相返回到常压塔,液相经换热、冷却后送出装置。
其中并设有一个顶回流,两个中段回流(常一中、常二中),常底油经过泵P114A/B抽出到减压炉加热到400℃左右后进入减压塔T105第四层上方。
减压塔顶设有两级抽真空系统,减顶油汽经过预冷器和一级抽空器和一级冷却器以及二级抽空器和二级冷却器,不凝气到常压炉烧掉,冷却下来的油水经减顶油水分液罐(V104)进行油水分离,分出的油经泵P115A/B送出装置,减压塔至上而下依次馏出减一线、减二线、减三线、减四线、减五线,减一线油经过换热、冷却后一部分做回流返回塔顶,一部分做为产品送出装置;减二、三、四线自流入汽提塔T106,气相返回减压塔,液相经换热、冷却送出装置;其中减四线一部分返回T105做为洗涤油;减五线油从T105洗涤段填料的集油箱抽出经过换热、冷却送出装置;减底油一部分做为加热炉的燃料,其余的经过两路换热,一部分热料去重催、焦化,另一部分经过冷却做冷渣送出装置。
2. 各系统流程说明(1)原油换热流程45℃原油从罐区进装置,经原油泵P101A/B分四路先和常顶油气换热(E101A-D),然后分三路进行换热。
常减压原料预处理装置操作指南

表1-1 几种典型原油的物理性质
性质
胜利原油
沙特原油
大庆原油
阿曼原油
密度 kg/m3
粘度(50℃)mm2/s
凝点℃
在常温下,甲烷至丁烷的正构烷呈气态;戊烷至十五烷的正构烷呈液态;十六烷以上的正构烷呈蜡状固态(是石蜡的主要成分)。 由于烷烃是一种饱和烃,故在常温下,其化学安定性较好。烷烃的密度最小,粘温性最好,是燃料与润滑油的良好组分。
环烷烃
环烷烃的化学结构与烷烃有相同之处,只是其碳原子相互连接成环状,故称为环烷烃。由于环烷烃分子中所有碳价都己饱和,因而它也是饱和烃。环烷烃的分子通式为CnH2n。 环烷烃具有良好的化学安定性,与烷烃近似但不如芳香烃。其密度较大,自燃点较高,辛烷值居中。它的燃烧性较好、凝点低、润滑性好,故是汽油、润滑油的良好组分。环烷烃有单环烷烃与多环烷烃之分。润滑油中含单环烷烃多则粘温性能好,含多环烷烃多则粘温性能差。
3、原油中的非烃化合物:
硫化物
硫在原油中主要是以元素硫(S)、硫化氢(H2S)、硫醇(RSH)、硫醚、二硫化物、噻吩的形态存在。其中元素硫、硫化氢、硫醇称为活性硫化物,它们的化学性质较活跃,容易与铁发生反应生成硫化亚铁,使工艺管线和设备器壁减薄,穿孔,发生泄漏事故;硫醚、二硫化物、噻吩等属于非活性硫化物,它们对金属的腐蚀性较弱,但是,非活性硫化物受热后可以分解成活性硫化物。硫的腐蚀性在后面专门说明。
还有一种烃类,叫作不饱和烃,如烯烃、炔烃。原油一般不存在不饱和烃,因为这些不饱和烃不稳定,容易氧化生成胶质。举例来说,汽油存放时间长了,颜色慢慢变深,就是里面的烯烃氧化了。但是烯烃的辛烷值较高,凝点较低,是汽油的良好组分。不饱和烃主要存在于二次加工产物里。
常减压操作规程

第一章概述1 装置概述本装置是由中国石化总公司北京设计院设计,年加工大庆原油350万吨的润滑油型常减压蒸馏装置。
全装置共有设备232台,占地面积17100m2,1989年4月破土动工,于1991年7月投产,各项主要技术指标均已达到设计要求。
2 装置特点2.1本装置主要设计要求是能生产出优质润滑油料。
减压蒸馏采用了粗转油线(低速段直径2m)、大塔径(汽化段直径10m,精馏段直径8.2m),高效规整全填料(GEMPAK)等多种技术措施来实现减压操作的低炉温、高真空、窄馏份,提高润滑油料的品质。
2.2本装置生产的减压渣又作丙烷脱沥青装置生产150BS光亮润滑油料,装置总拔出率控制在62%左右。
2.3本装置减压渣油直接送到重油催化裂化装置作原料、对渣油的含盐量有一定限制,因此装置设有电脱盐系统。
2.4 本装置生产航空煤油要求符合3号航煤标准,因此设计了航煤脱硫醇系统。
2.5本装置采用集散型控制系统(DCS),以提高装置的管理水平并实现过程的部分优化控制,提高轻质油收率,降低能耗,确保润滑油质量,提高经济效益。
2.6废水排放:为减少含油污水的排放量,减少了含油污水的排放。
因为加工的是大庆原油,硫含量低,排放的污水无需脱硫,只需进行简单隔油,然后直接排放送到含油污水场。
2.7废气排放:本装置正常生产时排放的低压瓦斯,如初顶产品罐排放初顶气送到轻烃回收设施加以回收,常顶气和减顶气分别引到加热炉烧掉,因此本装置正常生产时,不向大气排放有污染性的废气。
塔和容器顶部油气的安全阀放空设有放空总管,引到装置外火炬烧掉;本装置的大气污染源主要是燃料在加热炉燃烧后排放的烟气,从烟气监测数据可知,其中不含SO2,NO X的排放量低于国家排放标准,对环境质量没有太大的影响。
2.8 本装置无废渣产生。
2.9噪声:经调查,该套装置的噪声污染主要来自加热炉火嘴、泵和风机的电机、空冷器风机。
加热炉火嘴在密闭的罩内操作,噪声低于85分贝。
常减压操作规程(DOC)
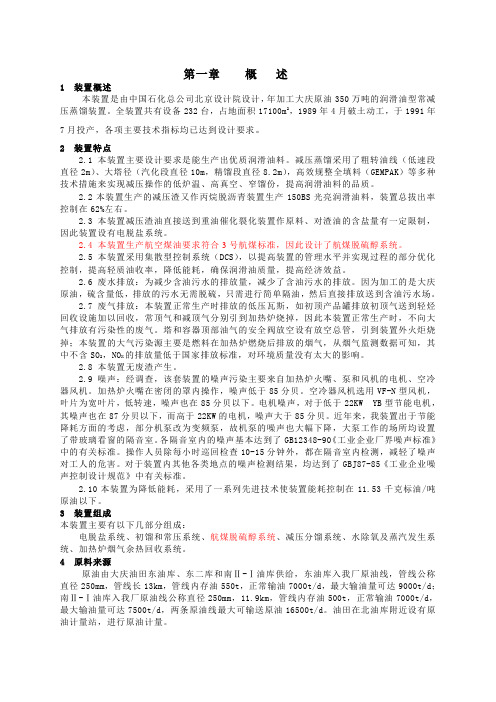
第一章概述1 装置概述本装置是由中国石化总公司北京设计院设计,年加工大庆原油350万吨的润滑油型常减压蒸馏装置。
全装置共有设备232台,占地面积17100m2,1989年4月破土动工,于1991年7月投产,各项主要技术指标均已达到设计要求。
2 装置特点2.1本装置主要设计要求是能生产出优质润滑油料。
减压蒸馏采用了粗转油线(低速段直径2m)、大塔径(汽化段直径10m,精馏段直径8.2m),高效规整全填料(GEMPAK)等多种技术措施来实现减压操作的低炉温、高真空、窄馏份,提高润滑油料的品质。
2.2本装置生产的减压渣又作丙烷脱沥青装置生产150BS光亮润滑油料,装置总拔出率控制在62%左右。
2.3本装置减压渣油直接送到重油催化裂化装置作原料、对渣油的含盐量有一定限制,因此装置设有电脱盐系统。
2.4 本装置生产航空煤油要求符合3号航煤标准,因此设计了航煤脱硫醇系统。
2.5本装置采用集散型控制系统(DCS),以提高装置的管理水平并实现过程的部分优化控制,提高轻质油收率,降低能耗,确保润滑油质量,提高经济效益。
2.6废水排放:为减少含油污水的排放量,减少了含油污水的排放。
因为加工的是大庆原油,硫含量低,排放的污水无需脱硫,只需进行简单隔油,然后直接排放送到含油污水场。
2.7废气排放:本装置正常生产时排放的低压瓦斯,如初顶产品罐排放初顶气送到轻烃回收设施加以回收,常顶气和减顶气分别引到加热炉烧掉,因此本装置正常生产时,不向大气排放有污染性的废气。
塔和容器顶部油气的安全阀放空设有放空总管,引到装置外火炬烧掉;本装置的大气污染源主要是燃料在加热炉燃烧后排放的烟气,从烟气监测数据可知,其中不含SO2,NO X的排放量低于国家排放标准,对环境质量没有太大的影响。
2.8 本装置无废渣产生。
2.9噪声:经调查,该套装置的噪声污染主要来自加热炉火嘴、泵和风机的电机、空冷器风机。
加热炉火嘴在密闭的罩内操作,噪声低于85分贝。
常减压装置操作规程

常减压装置操作规程第一章装置概述及主要设计依据本装置由闪蒸、常压蒸馏、减压蒸馏、电脱盐、、三注等部分组成。
主要产品为:汽油馏分、柴油、重柴油、减压馏分和燃料油。
一、本装置主要以下技术特点1、该装置采用二级交直流电脱盐、水技术,并采用在各级电脱盐罐前注破乳剂和注水等技术措施,以满足装置原料含盐、含水量、含硫、含酸的要求,电脱盐部分的主要技术特点为:(1)在电脱盐罐前设混合阀,以提高操作的灵活性并达到混合均匀的目的;(2)交流全阻抗防爆电脱盐专用变压器,以保护电脱盐设备安全平稳操作;(3)不停工冲洗,可定期排污;(4)采用组合式电极板;(5)设低液位开关,以保证装置操作安全;3、装置设置了闪蒸塔,以减少进常压炉的轻组分,并使原油含水在闪蒸塔汽化,避免对常压塔操作负荷的冲击。
4、在闪蒸塔、常压塔、减压塔顶采用注水、注中和缓蚀剂等防腐措施。
5、常压塔加热炉分别设空气预热器和氧含量检测、控制仪表,不凝汽引入加热炉燃烧,以节约能源并减少污染。
6、采用低速减压转油线,降低了转油线压降,以提高拔出率。
7、为了有效利用热能,对换热流程进行了优化设计,提高了换后温度,降低了能耗。
部分换热器管束采用了螺纹管和内插物等高效换热器,提高传热强度,减少设备台位,降低设备投资。
8、采用全填料干式减压蒸馏工艺,降低能耗,提高蜡油拔出率。
减压塔采用槽盘式分布器、辐射式进行分布器、无壁流规整填料等多项专利技术,可改善减压塔的操作状况、优化操作参数,提高产品质量。
9、减一中发生器蒸汽,供装置汽提用,较好地利用装置的过剩蒸汽,降低了装置能耗。
10、常压塔、常压汽提塔采用立式塔盘。
11、常顶油气与原油换热,提高低温位热量回收率。
12、采用浙大中控DCS软件进行流程模拟,优化操作条件。
二、装置能耗装置名称:60万吨/年常减压装置。
设计进料量:60万吨/年。
装置组成:电脱盐、常减压蒸馏、常减炉。
第二章工艺流程一、工艺流简述1、工艺流程说明约40℃的原油由设在罐区的原油泵(P-101/1.2)送入装置,原油进入装置后进入原油—常顶油气换热器(E-101/1.2)、然后分成两路换热网络,一路由原油—常一线换热器(E-102)、原油—常三线(二)换热器(E-103)、原油-常二线换热器(E-104/1.2)换热到122℃,在第二路原油经原油—减一线及减顶循换热器(E-105/1.2)、原油—减二线换热器(E-106/1.2)、原油—减三线换热器(E-107/1.2)换热到137℃,原油出换热网络I段后合并成一路原油升温至130℃进入电脱盐脱水系统,原油脱盐脱水系统采用二级交直流电脱盐工艺进行深度脱盐脱水。
电脱盐装置操作法

电脱盐装置操作法一、电脱盐罐变压器跳闸的原因及处理跳闸原因是因原油乳化和含水造成导电能力加强,电流增至一定程度而造成跳闸。
1、跳闸原因(1)脱盐罐油水界位过高,造成原油带水。
(2)混合强度过大,原油乳化严重,造成原油带水。
(3)原油较重,油水难以分离,造成原油带水。
(4)原油注水量突然升高,水量过大,造成原油带水。
(5)脱盐罐电器设备有故障。
2、处理措施(1)跳闸后首先要看界面、电流、温度等,判断出是什么原因,然后再采取相应的措施,争取尽快送上电。
(2)若是界面过高,先开切水副线,切水至正常位置后,脱盐罐送电,然后再检查造成界面超高的原因,联系解决。
(3)若界面正常,电流在跳闸前很高,当脱盐温度较高时,则应停掉注水,降低脱盐温度提高破乳剂注量;或降低原油处理量,以增加沉降时间,降低乳化油含水量,或减少混合强度。
(4)若原油带水或注水量突然升高则应停注水,脱盐罐加强切水,保持界面正常,才能使脱盐罐送上电。
(5)若原油乳化后严重送电困难,应降量,切除电脱盐,静置沉降,闭路送电正常后方可慢慢的把脱盐罐投入系统。
(6)若最后判断是罐内电器问题,根据性质再做相应处理(如停电、水冲、蒸罐,或进人检查等)。
二、电脱盐罐切水带油的原因1、脱盐罐切水带油一般是因为水面过低造成。
在加工重质原油时,往往会出现罐底乳化层,水位无法控制,甚至油水界面建立不起来。
此种情况下,水界面一建立,必将乳化层逼进电场,使脱盐罐无法正常工作。
水位建立不起来或油水界位极低,油水不分离或分立不好,就造成原油切水带油,如果切水控制阀或界面计失灵,使罐内实际界面过低,也会造成切水带油。
2、加工较重质原油,脱盐温度过低,也会造成油水分离不好,油水界位不清,水位无法控制。
3、混合强度过高,造成机械乳化,脱水困难而造成切水带油。
4、原油加工量过高,沉降分层时间不够,使油水界面不清,造成切水带油。
三、脱盐罐使用时的注意事项为了使脱盐罐能够正常运行,应注意以下事项:1、脱盐温度要控制在指标内,以使脱盐效果最佳。