减轻C偏析的方法
控制高碳钢中心碳偏析的工艺实践
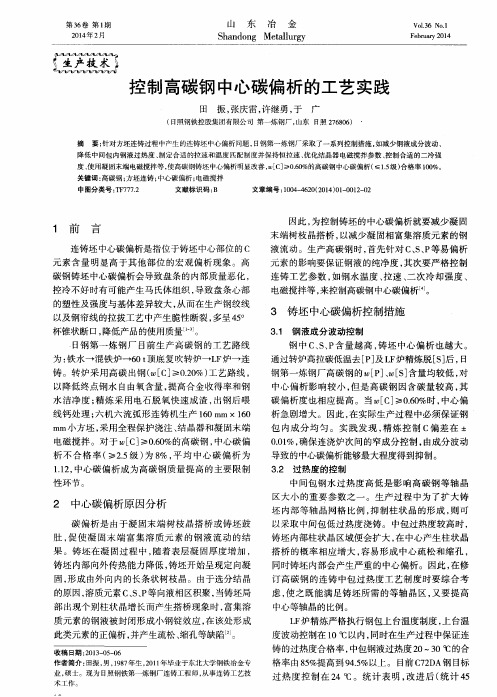
铸坯内部向外传热能力降低 , 铸坯开始呈现定向凝
固, 形 成 由外 向 内的长 条状树 枝 晶 。 由于选 分结 晶
同时铸坯 内部会产生严重的中心偏析 。因此 , 在修 订 高碳 钢 的连铸 中包 过 热度 工 艺 制度 时 要综 合 考 虑, 使之既能满足铸坯所需的等轴 晶区, 又要提高
性 环节 。
0 . 0 1 %, 确 保连 浇炉 次 间的窄成 分控 制 , 由成分 波 动
导致 的 中心碳偏析 能够最大程 度得到抑 制 。 3 . 2 过热 度的控 制
中间 包 钢水 过 热 度 高低 是 影 响 高碳 钢 等 轴 晶
区 大小 的重要 参 数 之 一 。生 产过 程 中为 了扩 大 铸 坯 内部 等 轴 晶 网格 比例 , 抑制 柱 状 晶 的形 成 , 则 可
控制高碳 钢 中心碳偏 析的工艺实践
田 振, 张庆雷 , 许 继勇 , 于 广
( 日照钢铁控股集 团有 限公司 第一炼钢厂 , 山东 日 照2 7 6 8 0 6 ) 摘 要 : 针对方坯连铸过程 中产生 的连铸坯 中心偏析 问题 , 1 3 钢第一炼钢厂采取 了一 系列控制措施 , 如减少钢液成分波动 、 降低 中间包 内钢液过热度 、 制 定合适的拉速和温度 匹配制度并保持恒拉速 、 优化结晶器 电磁搅拌参数 、 控制合适 的二冷强 度、 使用凝 固末端 电磁搅拌等 , 使高碳 钢铸坯 中心偏析明显改善 , w E C ] >0 / . 6 0 %的高碳钢中心碳偏析( ≤1 . 5 级) 合格率 1 0 0 %。 关键词 : 高碳钢 ; 方坯连铸 ; 中心碳偏析 ; 电磁搅拌
中图分 类号 : T F 7 7 7 . 2 文献标识码 : B 文章编号 : 1 0 0 4 — 4 6 2 0 ( 2 0 1 4 ) 0 1 — 0 0 1 2 — 0 2
一种铸坯中心偏析的控制方法

一种铸坯中心偏析的控制方法
一种铸坯中心偏析的控制方法是通过合理调整冶炼工艺参数和铸造工艺措施来降低铸坯中心偏析概率。
具体控制方法可包括:
1. 冶炼工艺参数控制:合理选择原料和调整炉温、冶炼时间等参数,以减少金属元素的不均匀分布,减少偏析的可能性。
2. 浇注温度控制:控制铸造过程中的浇注温度,避免过高或过低温度对金属流动性和凝固过程产生影响,减少偏析的发生。
3. 凝固速度控制:通过合理的铸造工艺措施调整凝固速度,如采用合适的冷却方式、增加冷却时间等,使得铸坯凝固过程均匀进行,减少偏析的发生。
4. 金属液体搅拌:在铸造过程中加入搅拌剂或采取机械搅拌设备,使金属液体充分搅拌,减少偏析的可能性。
5. 铸造材料选择:选择具有较低偏析倾向的铸造材料,如添加稳定元素、选用低偏析度的合金等,减少铸坯的中心偏析。
6. 控制浇注方式:合理控制浇注方式,如采用顶部浇注、底部浇注等方式,减少金属流动不均匀的可能,降低偏析的发生。
连铸工题库

一、判断题(正确的请在括号内打“√”,错误的请在括号内打“×”,每题2分,共120分)1.>CSP技术是由美国开发的。
( )答案:×2.>薄板坯连铸可用于中、小型钢厂。
( )答案:√3.>压缩铸造可以防止铸坯内裂。
( )答案:√4.>轻压下技术可以减少铸坯的中心偏析。
( )答案:√5.>轻压下的位置在铸坯已经全部凝固的位置。
( )答案:×6.>铸坯矫直时的表面温度,应避开脆性敏感区。
( )答案:√7.>铸坯厚度20mm~90mm,宽900mm~1600mm的连铸机叫薄板坯连铸机。
( ) 答案:×8.>铸坯的纵裂主要在二冷区产生。
( )答案:×9.>铸坯的液芯长度=(铸坯厚度×2/凝固系数)2×拉速。
( )答案:×10.>铸坯的低倍结构为激冷层、柱状晶和中心等轴晶。
( )答案:√11.>铸坯的表面缺陷主要决定于钢水在二冷段的凝固过程。
( )答案:×12.>中间包内采用塞棒,有利于浇铸初期和终了减缓旋涡的生成,提高钢水的收得率。
( )答案:√13.>中包内钢水液面之所以要保持一定的高度,是为了促使钢中非金属夹杂物的充分上浮和保证中包不下渣。
( )答案:√14.>小方坯铸机事故冷却水的水量应能保证铸机的一定压力供水15min以上。
( )答案:√15.>为保证结晶器的传热效果,其水缝中冷却水的流速应保持在3~5m/s为宜。
( )答案:×16.>所有的钢种都可以采取连铸浇注。
( )答案:×17.>所谓固相矫直是指铸坯进入矫直区业已全部凝固时进行的矫直。
( ) 答案:√18.>事故冷却水的水量应不小于正常水量的1/5。
( )答案:×19.>事故冷却水的冷却部位有结晶器冷却水和机械闭路水。
高碳钢连铸坯偏析问题的分析与探讨

2007年炉外精炼年会论文集211高碳钢连铸坯偏析问题的分析与探讨曾四宝1,2)李洪波1,2)包燕平1)刘建华1)韩丽娜1)1)北京科技大学冶金与生态工程学院; 2)济南钢铁集团石横特殊钢厂摘要本文针对石横特殊钢厂R9m连铸机生产SWRH82B、GCr15等高碳钢连铸坯的偏析问题,分析讨论了钢水过热度、拉速、二次冷却强度和组合式电磁搅拌对连铸坯碳偏析影响,并对中心碳偏析问题提出了改善措施。
关键词偏析;钢水过热度;二次冷却强度;拉速;电磁搅拌1 前言对高碳钢来说,由于碳含量较高造成导热性差、凝固区间大,连铸坯本身容易产生偏析、疏松和缩孔等缺陷。
当前轴承钢连铸坯的控制水平普遍要求碳中心偏析指数≤1.15;钢帘线钢对碳偏析有更严格的要求,一般碳中心偏析指数≤1.05,否则在拉丝和扭转过程中容易引起断裂。
最近十几年来,随着钢水二次精炼、保护浇注、二次冷却、电磁搅拌和轻压下等技术的发展,高碳钢连铸技术也相应得到发展。
实际上,影响高碳钢连铸坯偏析的因素很多,如钢液过热度、二冷参数、拉速及电磁搅拌方式等。
关于钢液过热度对偏析的影响,国内外冶金工作者进行过大量的研究,得出了明确的结论,即随着过热度的降低,连铸坯的偏析逐渐减轻。
但是关于电磁搅拌和二冷水量等对偏析的影响目前还有争议。
通过统计分析石横特殊钢厂2006年3~9月份的生产情况和工艺变化情况,探讨了高碳钢(如SWRH82B、GCr15)连铸坯碳偏析的产生原因以及公司进一步改善碳偏析的途径,为工艺和装备优化、改进提供依据。
2 连铸机基本参数流数:4流;铸机半径:R9000/17500mm;流间距:1250mm;结晶器长度:850mm;浇铸断面:150mm×150mm;最大拉速:2.8m/min;电磁搅拌方式:M + F—EMS;二次冷却方式:足辊水冷0段+气雾冷却1、2、3段;浇铸钢种:碳结钢20#、45#、40Cr、ML10~35,20CrMo、高碳钢70#、80#、72A、82B、GCr15焊条钢H08A、H08Mn2SiA等。
减少方坯中心偏析的冶金手段
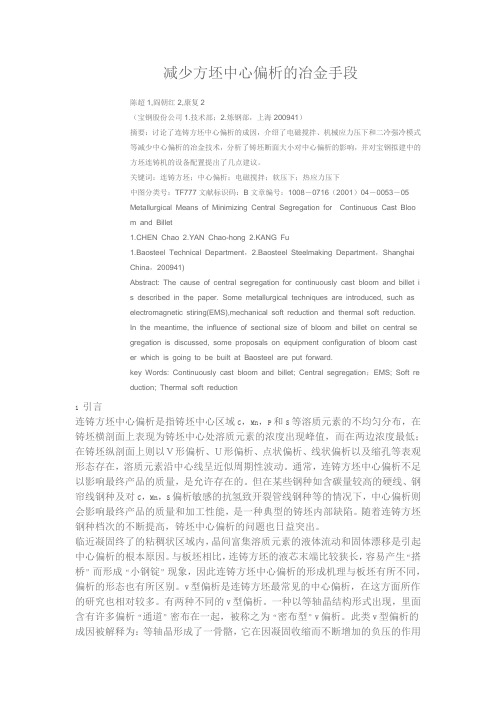
减少方坯中心偏析的冶金手段陈超1,阎朝红2,康复2(宝钢股份公司1.技术部;2.炼钢部,上海200941)摘要:讨论了连铸方坯中心偏析的成因,介绍了电磁搅拌、机械应力压下和二冷强冷模式等减少中心偏析的冶金技术,分析了铸坯断面大小对中心偏析的影响,并对宝钢拟建中的方坯连铸机的设备配置提出了几点建议。
关键词:连铸方坯;中心偏析;电磁搅拌;软压下;热应力压下中图分类号:TF777文献标识码:B文章编号:1008-0716(2001)04-0053-05Metallurgical Means of Minimizing Central Segregation for Continuous Cast Bloom and Billet1.CHEN Chao2.YAN Chao-hong 2.KANG Fu1.Baosteel Technical Department,2.Baosteel Steelmaking Department,ShanghaiChina,200941)Abstract: The cause of central segregation for continuously cast bloom and billet is described in the paper. Some metallurgical techniques are introduced, such aselectromagnetic stiring(EMS),mechanical soft reduction and thermal soft reduction.In the meantime, the influence of sectional size of bloom and billet on central segregation is discussed, some proposals on equipment configuration of bloom caster which is going to be built at Baosteel are put forward.key Words: Continuously cast bloom and billet; Central segregation;EMS; Soft reduction; Thermal soft reduction1 引言连铸方坯中心偏析是指铸坯中心区域C,Mn,P和S等溶质元素的不均匀分布,在铸坯横剖面上表现为铸坯中心处溶质元素的浓度出现峰值,而在两边浓度最低;在铸坯纵剖面上则以V形偏析、U形偏析、点状偏析、线状偏析以及缩孔等表观形态存在,溶质元素沿中心线呈近似周期性波动。
碳化物偏析

碳化物偏析
碳化物偏析是一种金属材料中碳的偏析现象,通常发生在低合金钢、铸铁和不锈钢等材料中。
这种偏析现象会导致材料中碳含量不均匀,从而影响其力学性能和耐腐蚀性能。
碳化物偏析的原因主要是由于材料中的碳在加热过程中向表面
聚集,并在高温下与其他元素形成碳化物。
这些碳化物通常比材料中其他的碳化物更容易形成,并更容易沉淀在材料表面或颗粒界面上。
这就导致了材料表面或颗粒界面上的碳含量比材料中其他部分的碳
含量更高。
碳化物偏析的影响可以通过控制材料的加热和冷却过程来降低。
此外,添加适量的合金元素也可以减轻碳化物偏析的影响。
对于一些关键的应用场景,例如航空航天和核电站等,碳化物偏析是一个必须要考虑的因素。
因此,对于这些关键应用场景的材料,需要通过特殊的加工工艺和合金设计来减轻碳化物偏析的影响。
- 1 -。
消除晶内偏析的方法

消除晶内偏析的方法
1. 均匀化处理:将材料加热到高温,并保持一定时间,使原子或离子在晶体内充分扩散,从而减少偏析。
均匀化处理可以在材料制备过程中进行,也可以在后续的加工过程中进行。
2. 固溶处理:将材料加热到高温,并使其与一种或多种元素形成固溶体,从而减少偏析。
固溶处理可以改善材料的力学性能和耐腐蚀性。
3. 快速凝固:通过快速凝固技术,可以使原子或离子在结晶过程中来不及充分扩散,从而减少偏析。
快速凝固技术包括激光熔覆、电子束熔覆等。
4. 锻造和挤压:通过锻造和挤压等加工工艺,可以使材料中的晶界和晶粒发生变形和移动,从而减少偏析。
这种方法适用于晶界偏析较严重的材料。
5. 热处理:通过适当的热处理,可以调整材料的晶粒尺寸和晶界结构,从而减少偏析。
例如,正火处理可以细化晶粒,从而减少晶内偏析。
6. 合金化:通过添加合适的合金元素,可以改善材料的晶体结构和化学成分均匀性,从而减少偏析。
例如,添加微量的硼、锆等元素可以改善钢的晶内偏析。
需要根据具体情况选择合适的消除晶内偏析的方法。
在实际应用中,常常综合使用多种方法来达到更好的效果。
焊锡合金偏析定义及其消除方法
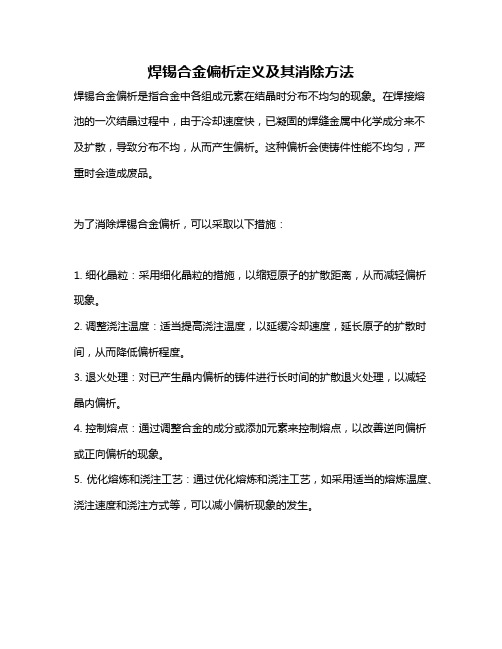
焊锡合金偏析定义及其消除方法
焊锡合金偏析是指合金中各组成元素在结晶时分布不均匀的现象。
在焊接熔池的一次结晶过程中,由于冷却速度快,已凝固的焊缝金属中化学成分来不及扩散,导致分布不均,从而产生偏析。
这种偏析会使铸件性能不均匀,严重时会造成废品。
为了消除焊锡合金偏析,可以采取以下措施:
1. 细化晶粒:采用细化晶粒的措施,以缩短原子的扩散距离,从而减轻偏析现象。
2. 调整浇注温度:适当提高浇注温度,以延缓冷却速度,延长原子的扩散时间,从而降低偏析程度。
3. 退火处理:对已产生晶内偏析的铸件进行长时间的扩散退火处理,以减轻晶内偏析。
4. 控制熔点:通过调整合金的成分或添加元素来控制熔点,以改善逆向偏析或正向偏析的现象。
5. 优化熔炼和浇注工艺:通过优化熔炼和浇注工艺,如采用适当的熔炼温度、浇注速度和浇注方式等,可以减小偏析现象的发生。
以上方法仅供参考,在实际操作中可能需要根据具体情况进行调整和优化。
如需更多信息,建议咨询专业技术人员或查阅相关技术手册。
焊锡合金偏析定义及其消除方法

焊锡合金偏析定义及其消除方法焊锡合金偏析是指在焊接过程中,焊锡合金中某些成分的浓度出现不均匀分布的现象。
这种不均匀分布可能导致焊接接头的力学性能下降以及可能产生缺陷,对焊接接头的可靠性和耐久性造成不利影响。
因此,了解焊锡合金偏析的定义和消除方法对于实现高质量焊接至关重要。
焊锡合金偏析通常分为两种类型,即向外偏析和向内偏析。
1. 向外偏析:向外偏析指的是在焊接过程中,焊锡合金中某些成分的浓度大于平均浓度。
这种情况下,偏高的成分可能会导致焊接接头变脆,降低了焊接接头的韧性和可靠性。
常见的向外偏析成分包括Sb(锑)和Cu(铜)等。
2. 向内偏析:向内偏析指的是在焊接过程中,焊锡合金中某些成分的浓度小于平均浓度。
这种情况下,偏低的成分可能导致焊接接头的力学强度下降,增加了焊接接头发生断裂或脆性破坏的风险。
常见的向内偏析成分包括Bi(铋)和Ag(银)等。
为了消除焊锡合金的偏析现象,可以采取以下措施:1. 控制焊接工艺参数:合理和稳定的焊接工艺参数对于防止焊锡合金偏析至关重要。
例如,控制焊接温度、焊接时间以及焊接热循环等,可以减少偏析的风险。
同时,确保焊接接头处于适当的温度范围内,避免过高的温度导致成分偏析。
2. 选用合适的焊锡合金:选择适合特定应用的焊锡合金对于减少偏析问题至关重要。
不同的焊锡合金组分会导致不同程度的偏析效应。
因此,在选择焊锡合金时,根据具体应用需求合理选择合金组分,并确保合金组分均匀分布以降低偏析风险。
3. 添加合适的助焊剂:助焊剂可以在焊接过程中帮助减少焊锡合金的偏析。
助焊剂中的活性剂可以调节焊接界面的物理化学性质,如表面张力和润湿性,从而改善焊接质量并减少偏析现象。
4. 合理设计焊接结构:焊接结构的设计也可以对焊锡合金偏析产生影响。
合理设计焊点和焊接接头的几何形状,可以减少应力集中和温度梯度,从而降低偏析的发生。
综上所述,焊锡合金偏析是焊接过程中面临的一个重要问题,其不仅会导致焊接接头质量下降,还可能引发接头断裂等安全隐患。
一种抑制大型钢锭宏观偏析的内冷方法

一种抑制大型钢锭宏观偏析的内冷方法简介:钢铁是现代工业中不可或缺的材料之一。
然而,由于钢材的生产过程中存在多种因素,如化学成分不均匀等,可能会导致钢锭宏观偏析。
本文将介绍一种抑制大型钢锭宏观偏析的内冷方法。
一、大型钢锭宏观偏析的危害在钢铁生产过程中,宏观偏析是一个常见的问题。
它可以影响到钢锭的性能和品质,甚至可能导致产品的失败。
大型钢锭宏观偏析是一种严重的宏观偏析现象,其偏析程度非常高,可以达到数十毫米级别。
这种宏观偏析一旦发生,将导致钢锭在铣削时增加浪费,使得成品率降低,生产成本增加。
二、内冷方法内冷方法是一种对抗宏观偏析的技术,它通过在钢锭中心使用注水方式来降低钢锭中心的温度,由此抑制钢锭的宏观偏析。
传统的内冷方法是在钢锭中心孔内注水,但这种方法的效果不佳,因为孔的直径太小,无法充分覆盖钢锭的中心区域。
而内冷方法则克服了这些缺点。
这种方法在钢锭中心区域安装一个水口,以使水在大范围内喷洒。
这种方法可以充分减缓钢锭的温升速度,并在全面降温过程中抑制宏观偏析的发生。
三、内冷方法的优点除了富有创新性和高效降温外,内冷方法还有其他很多优点。
首先,它可以降低钢锭的温度变化率,大大减少了钢锭宏观偏析的发生。
其次,钢锭的浪费量减少,这将节省大量的生产成本。
最后,内冷方法能够保持除过氧化氢之外的有害气体的生成和发生,保证了整个工艺的可靠性和安全性。
四、结论大型钢锭宏观偏析一直是钢铁制造中的一个难点,因为这种宏观偏析很难被抑制。
然而,内冷方法针对该问题提供了一个创新的解决方案。
这种方法简单、安全、高效,并可以节省大量的费用。
它已经被证明是一种行之有效的方法,可以应用于大型钢锭的制备,并带来巨大的经济效益。
减轻C偏析的方法

减轻碳偏析的方法高碳钢用于制作高强度的预应力钢丝和钢绞线,广泛应用于公路、铁路桥梁、海港码头、电站、大坝、工业民用建筑等领域,是一种高附加值产品,近年来,其需求量逐年攀升,所以高碳钢具有广泛的市场前景,而高碳钢在后续连续拉拔成单丝的过程中,压缩比可高达84%,这就要求原始的盘条成分化学均匀,钢的纯净度高,金属夹杂物含量低且无大型夹杂,连铸坯中心偏析和中心缩孔小,线材的表面质量好,不能有折叠、耳子等缺陷,组织性能均匀稳定等。
应该控制连钢、精炼、连铸、轧制、拉拔等各个生产环节,综合优化工艺,减轻偏析。
1.0炼钢生产工艺为:铁水预处理→转炉冶炼→LF炉精炼→喂丝→软吹→保护浇铸,炼钢过程主要控制连铸坯中心偏析、中心缩孔及夹杂物,从以下下面几个环节控制。
精炼部分:(1)成分控制,在铸坯结晶过程中,钢液中的溶质元素在固液相界上的溶解并未平衡移动,C、S、P等易偏析元素以柱状晶粒析出,排到尚未凝固的钢液中,随着结晶过程的进行,这些易偏析元素被富集到铸坯中心或者凝固末端区域,从而产生铸坯中心偏析。
由于出钢过程增碳量大,为达到LF精炼成分的目的,对钢中硅、锰成分分别用硅铁和锰铁调整,用含碳合金球或碳芯线微调碳成分。
硅是促进石墨化作用最强的合金元素,硅促进石墨化的能力,是镍的3倍,是铜的5倍。
无论在液态或者固态的钢中,硅与铁结合的作用都比碳强。
钢水中含有硅,就会使碳的溶解度降低。
因此含硅量越高,碳含量相应的越低,就会有更多的碳被排挤出来。
碳含量降低,铸坯碳偏析就会得到明显的改善。
(2)温度控制,由于高碳钢液相线温度低,因而其过程温度低,但是温度过低会造成化渣困难,所以要求LF炉第一次升温温度不能过低。
(3)夹杂物控制,为改变夹杂物的形态和分布,在钢水离开LF站之前,利用含钙包芯线对钢水进行钙处理,钙处理后,为保证夹杂物充分上浮,必须对钢包液进行较长时间的软吹氩,软吹氩时间要求不少于8min。
连铸部分:(1)浇注温度,浇注温度高,铸坯易产生柱状晶或者穿晶组织,造成中心疏松、缩孔和偏析加剧。
改善弹簧钢小方坯中心碳偏析的实践

改善弹簧钢小方坯中心碳偏析的实践孙光涛;桂仲林;王向红【摘要】结合中天钢铁第三炼钢厂3#连铸机的生产实际,分析二冷比水量和结晶器电磁搅拌电流强度对60Si2MnA弹簧钢160 mm×160 mm方坯中心碳偏析的影响,结果表明:二冷比水量增加,中心碳偏析指数先降低后增加;结晶器电磁搅拌强度增加,铸坯中心碳偏析指数降低.比水量为1.0 L/kg、结晶器电磁搅拌强度为300 A/3 Hz时,中心碳偏析指数达到最小值1.04,且铸坯的中心偏析指数波动更小.【期刊名称】《山东冶金》【年(卷),期】2017(039)003【总页数】2页(P16-17)【关键词】弹簧钢;60Si2MnA钢;小方坯;中心碳偏析;结晶器电磁搅拌;二冷比水量【作者】孙光涛;桂仲林;王向红【作者单位】中天钢铁第三炼钢厂,江苏常州213011;中天钢铁第三炼钢厂,江苏常州213011;中天钢铁第三炼钢厂,江苏常州213011【正文语种】中文【中图分类】TF777.360Si2MnA钢是应用于汽车悬架弹簧的高档弹簧用钢,悬架弹簧在汽车行驶过程中,承受高频往复压缩运动,工作环境恶劣,对所用弹簧钢质量要求很高。
由于60Si2MnA钢碳含量高,具有液相和固相间的温度区间较大、糊状区宽的特点,在小方坯连铸过程中铸坯中心易形成严重的碳偏析,且在后期的加热、轧制过程中难以消除,会对热轧盘条的机械性能产生不利影响,导致线材在拉拔过程中产生杯锥状断裂[1]。
利用结晶器电磁搅拌和提高二冷比水量等方式是目前改善小方坯铸坯中心碳偏析的重要手段[2]。
目前中天钢铁生产的160 mm×160 mm的60Si2MnA弹簧钢方坯中心碳偏析控制1.08~1.17,用户在拉拔过程中出现了杯锥状断裂。
针对此情况,通过现场试验分析了结晶器电磁搅拌工艺参数及二冷比水量对铸坯中心碳偏析的影响,确定了最佳工艺参数,改善了弹簧钢小方坯心部质量。
中天钢铁第三炼钢厂生产60Si2MnA弹簧钢线材工艺流程:KR→120 t转炉→LF 精炼→RH真空处理→CCM连铸→线材轧制。
“偏析”现象的分析及解决
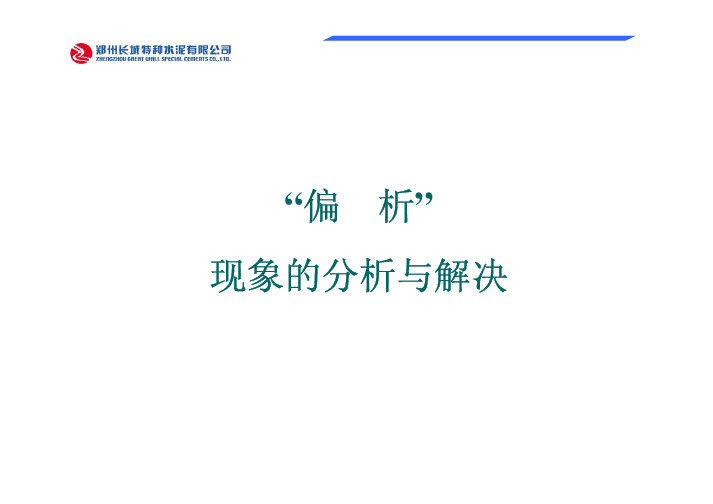
氧化铝类型对浇注料机理的影响
5 4.5ቤተ መጻሕፍቲ ባይዱ4 3.5 D 50 [micron] 3 2.5 2 1.5
烧结氧化铝粉 Ball size =Na20 >200 <2600ppm
AM21 AM22
活性氧化铝粉 较容易导致偏析和促使这种现象的发生
A170 RA810 A172
1 0.5 0 0 0.5 1 1.5 2 2.5 3
Binder phase %
170 140
71,4 11,4 17,2 100
无偏析现象
45
0,01% BA 0,01% BA + 0,01% BA + 0,005% BA 0,005 LiC 0,01 LiC + 0,025 LiC
过多的缓凝剂导致偏析效应可以通过加入碳酸锂来调整
•
举例说明由于添加剂而导致偏析效应
• 因为添加剂加入量或效果而要求多加水,近而导致偏析效应
•
过多缓凝剂加入量导致偏析效应
•
为了迎合合适的工作时间加入某种缓凝剂导致偏析效应 Æ Modify behaviour with addition of pH stablising additive
分散体系试验 :水的影响
Binder phase %
165
130
11
12
13
14
15
% Water addition (%)
在水加入量过多的情况下可以通过引入碳酸锂来调整 (0,0015-0,005%)
Using cyclindrical flow cone of 30mm x 50mm
分散体系试验 :缓凝剂的影响
浇注料工作时间 (mins)
- 1、下载文档前请自行甄别文档内容的完整性,平台不提供额外的编辑、内容补充、找答案等附加服务。
- 2、"仅部分预览"的文档,不可在线预览部分如存在完整性等问题,可反馈申请退款(可完整预览的文档不适用该条件!)。
- 3、如文档侵犯您的权益,请联系客服反馈,我们会尽快为您处理(人工客服工作时间:9:00-18:30)。
减轻碳偏析的方法
高碳钢用于制作高强度的预应力钢丝和钢绞线,广泛应用于公路、铁路桥梁、海港码头、电站、大坝、工业民用建筑等领域,是一种高附加值产品,近年来,其需求量逐年攀升,所以高碳钢具有广泛的市场前景,而高碳钢在后续连续拉拔成单丝的过程中,压缩比可高达84%,这就要求原始的盘条成分化学均匀,钢的纯净度高,金属夹杂物含量低且无大型夹杂,连铸坯中心偏析和中心缩孔小,线材的表面质量好,不能有折叠、耳子等缺陷,组织性能均匀稳定等。
应该控制连钢、精炼、连铸、轧制、拉拔等各个生产环节,综合优化工艺,减轻偏析。
1.0炼钢
生产工艺为:铁水预处理→转炉冶炼→LF炉精炼→喂丝→软吹→保护浇铸,炼钢过程主要控制连铸坯中心偏析、中心缩孔及夹杂物,从以下下面几个环节控制。
精炼部分:
(1)成分控制,在铸坯结晶过程中,钢液中的溶质元素在固液相界上的溶解并未平衡移动,C、S、P等易偏析元素以柱状晶粒析出,排到尚未凝固的钢液中,随着结晶过程的进行,这些易偏析元素被富集到铸坯中心或者凝固末端区域,从而产生铸坯中心偏析。
由于出钢过程增碳量大,为达到LF精炼成分的目的,对钢中硅、
锰成分分别用硅铁和锰铁调整,用含碳合金球或碳芯线微调碳成分。
硅是促进石墨化作用最强的合金元素,硅促进石墨化的能力,是镍的3倍,是铜的5倍。
无论在液态或者固态的钢中,硅与铁结合的作用都比碳强。
钢水中含有硅,就会使碳的溶解度降低。
因此含硅量越高,碳含量相应的越低,就会有更多的碳被排挤出来。
碳含量降低,铸坯碳偏析就会得到明显的改善。
(2)温度控制,由于高碳钢液相线温度低,因而其过程温度低,但是温度过低会造成化渣困难,所以要求LF炉第一次升温温度不能过低。
(3)夹杂物控制,为改变夹杂物的形态和分布,在钢水离开LF站之前,利用含钙包芯线对钢水进行钙处理,钙处理后,为保证夹杂物充分上浮,必须对钢包液进行较长时间的软吹氩,软吹氩时间要求不少于8min。
连铸部分:
(1)浇注温度,浇注温度高,铸坯易产生柱状晶或者穿晶组织,造成中心疏松、缩孔和偏析加剧。
浇铸温度高还会使得液芯变长,导致
铸坯坯壳发生鼓肚现象,在铸坯中心产生具有负压抽吸作用的空穴,使凝固末端富集溶质元素的钢液被吸入铸坯中心。
也是导致铸坯产生中心偏析的一个重要的原因。
而浇铸温度过低易造成中包水口冻结,迫使浇铸中断,不利于钢中夹杂物的上浮。
并可能恶化铸坯表面质量,因此,要严格控制浇注温度。
钢包、中间包永久层里加装保温材料,减少钢包、中间包钢水降温,稳定浇铸过程钢水温度。
中间包钢水面采用双覆盖渣,底层为碱性保护渣,起保护和净化钢水的作用,上层加炭化稻壳,起保温作用。
控制钢水过热度20~30℃为宜。
(2)拉速制度,拉速过高,铸坯在结晶器内停留时间变短,延长了钢水的凝固时间,使铸坯液芯变长,推迟了等轴晶的形核和长大,扩大了柱状晶区,促使柱状晶搭桥,增加了小钢锭结构形成的机会,还会发生铸坯鼓肚,加重了中心偏析和缩孔,而拉速过低可能使钢水回炉量过高而影响生产效率和产量,因此要从生产效率和拉速平衡的角度考虑,既不影响产量,又能保证连铸坯的质量。
此外拉速的稳定有利于连铸坯的内部质量和表面质量。
浇铸过程中拉速的变化会导致连
铸坯凝固结构的不均匀,增加保护渣卷入的几率。
(3)连铸冷却工艺,二次冷却条件直接影响铸坯质量的好坏,固液界面上的冷却条件严重影响固液两相区微观组织的生长,若二次冷却太弱,铸坯表面温度就会过高,铸坯液芯加长,抑制柱状晶生长,增加等轴晶区,坯壳抵抗因钢水静压力引起的鼓肚变形能力减弱,从而促进中心偏析的形成和扩展。
而二次冷却太强,使钢液中的元素没有足够的时间进行选分结晶,因此有利于偏析的改善,但是会加重中心缩孔。
比水量与铸坯组织枝晶间距的关系如下图,由图可看出,随着比水量的增加,冷却速率增大,一次枝晶间距和二次枝晶间距减少。
这主要是由于当二次冷却强度增大时,钢液凝固速度增加,溶质原速度析出和扩散减小,树枝晶组织细小致密化。
阻碍了枝晶间溶质向中心富集,减小中心偏析。
在相同比水量的情况下,随着铸坯厚度的增加,冷却速率逐步减小,但是到铸坯中心位置,不同比水量的冷却速率基本相同。
根据公式计算出结晶器坯壳厚度:
H=K*(L/V)1/2
式中:K—凝固系数,取值27;
L—结晶器有效长度,900mm;
V—拉速,1.9m/min;
计算结晶器坯壳厚度为18.6mm,实际状态下,有涉及冷却效率的问题,铸坯尚有75%的厚度为液相或固相混合相。
采用强冷缩小二
次枝晶间距的效果有限,所以将强冷区域延长,最大程度的利用了强冷的冷却效率,有效缩短了二次枝晶间距,对抑制高碳钢的中心偏析起到了明显的改善作用。
(4)电磁搅拌工艺,连铸使用电磁搅拌技术,能减少铸坯皮下气泡,非金属夹杂物缺陷的产生,改善铸坯铸坯表面质量,增加微细等轴晶,减轻中心偏析,缩孔和疏松,防止结晶器内的不均匀凝固。
根据搅拌位置不同,电磁搅拌分为结晶器电磁搅拌(MEMS)、二冷电磁搅拌(SEMS)以及凝固末端电磁搅拌(FEMS)。
实践表明,高碳钢必须采用M+S+F三段搅拌才能使铸坯中心偏析和疏松得到显著改善。
(5)保护浇铸,全程保护浇铸,钢包到中间包采用长水口加密封环,中间包加覆盖剂,中间包到结晶器之间采用浸入式水口,结晶器采用高碳钢专用保护渣。
(6)轻压下技术,炼轧厂铸机无轻压下设备,不具备轻压下功能,可以借助拉矫辊实施,用拉矫辊实施轻压下,有两个问题必须首先研究解决。
①拉矫机夹棍和液压系统的能力是否满足轻压下的要求;②不同拉速下铸坯凝固末端的位置及轻压下的最佳位置。
2.0轧制
高碳钢轧制流程:加热炉→粗、中、预精轧、精轧机→水冷→吐丝机→斯太摩尔风冷线→集卷→打捆→成品入库,轧制过程主要控制线材表面质量,索氏体化率及渗碳组织,从以下方面控制:
(1)加热炉,控制加热炉内气氛,采用低加热,尽可能减少坯料在炉内高温段停留时间,以防止表面脱碳,为了保证铸坯中心碳的充分扩散,在不增加盘条表面脱碳、氧化铁皮的前提下,适当延长铸坯在炉内的时间,一般选择铸坯加热时间不小于150min,铸坯出炉(均热段)温度为960℃~1050℃。
(2)粗、中、预精轧和精轧机,采用低温开轧,获得小的奥氏体晶粒,高碳钢变形抗力大,粗、中、预轧机应均匀分配压下量,避免单机架压下过大,保证合理的活套量及连轧常数。
终轧温度是影响产品性能的主要因素之一,提高终轧温度,钢的抗拉强度呈上升趋势,这是由于终轧温度提高,有利于高碳钢中碳化物的溶解,增加了奥氏体的稳定性。
但是终轧温度越高,奥氏体晶粒长大趋势越严重,引起钢的断面收缩率下降,塑性降低,奥氏体晶粒大小直接影响到相变后的组织和晶粒尺寸,因此保证适宜的终轧温度,可使产品获得满足使用要求的组织和强度均一性,实验表明,终轧温度为950℃,钢的强度、塑性匹配较好,另外,为了避免轧件表面出现划伤和折叠,全线应该采用无扭转轧制。
(3)吐丝机,轧后冷却过程中,吐丝机温度的控制对线材性能的影响非常重要,在对高碳钢的控制冷却过程中,希望抑制铁素体的析出,
得到单一的片层间距适宜的珠光体组织,为此,通过加大相变前的冷却来抑制先共析铁素体的析出,一般设定吐丝温度为850℃~870℃。
(5)轧后控冷技术,轧后冷却制度直接影响到产品的最终性能。
线材作为深加工的原料,要求减少盘条二次氧化铁皮的生成量,在生产中,线材轧后控冷技术包括2部分:精轧机到吐丝机间的喷水冷却,吐丝机与集卷站间的散卷吹风冷却,根据过冷奥氏体等温转变动力学原理,共析钢过冷奥氏体600℃左右时分解的产物为索氏体,具有强度和塑性的最佳配合,此时形成的索氏体组织,其综合性能最好,高速线材轧后轧后控制冷却的主要目的是控制过冷度和冷却速度,以获得较高的索氏体化率,冷却过程中还应注意尽量减少线材边部至中心索氏体化率的差异,杜绝出现渗碳体和马氏体组织。
以高碳钢82B为例,82B钢的连续冷却转变曲线(CCT),如上图所示,由图可以看出82B在冷却过程中,过冷奥氏体转变为珠光体的温度区间为A~550℃,在该区间内转变温度越低,过冷度越大,珠光体片层间距越薄,索氏体具有较高的强度和较好的塑性,因此生产
82B时要求散卷冷却运输线采用大风量,快速冷却的方式,这样可以控制铁素体的析出量,增大过冷度,提高索氏体转变率。
另外线材在相变区滞留的时间越长,索氏体转变越充分,索氏体化率越高,研究表明,线材从吐丝机到相变前的冷却速度控制在小于15℃/s,相变过程中的冷却速度控制在2~5℃/s,可以获得良好的综合性能。
时效处理和拉拔
目前生产高碳钢钢绞线采用的工艺为:盘条→酸洗→磷化→冷拉拔→控制→稳定化处理→成品,拉拔过程主要控制内应力、断丝率等,从下面两个环节控制。
(1)时效处理:高速线材轧机生产时,82B盘条经风冷和水冷后的温度在几秒钟内从1000℃迅速降到600℃,使得盘条表面和心部产生很大的内应力,如果内应力没有释放完便进行拉拔,就会使其脆断几率明显增大,目前采用自然时效方式来释放内应力,时效时间一般不小于20天。
(2)拉拔过程:为了降低盘条拉拔断丝率,提高成材率,用户在拉拔过程中应注意:合理设计变形道次和每道次减径率,避免某道次超拉而引起拉拔断裂;在拉拔前仔细检查模子的损坏程度,选择优良的拉丝模并调整拉丝模与拉拔中心线的位置,避免模具损坏而导致的钢丝表面划伤和盘条在捻制过程中的断痕;防止过酸洗,钢丝制造过程中的多次酸洗或酸洗后清洗不净是高碳钢氢脆的主要原因,钢丝的早期断裂是由第二类氢脆引起的;加强润滑,避免刮伤钢丝表面的磷化膜,在拉拔过程中不时的挪动拉丝粉,防止拉丝粉结成块状,影响润
滑,增加断丝率。