大方坯轴承钢中心偏析的成因及预防措施
分析V形偏析的形成原因和防止办法
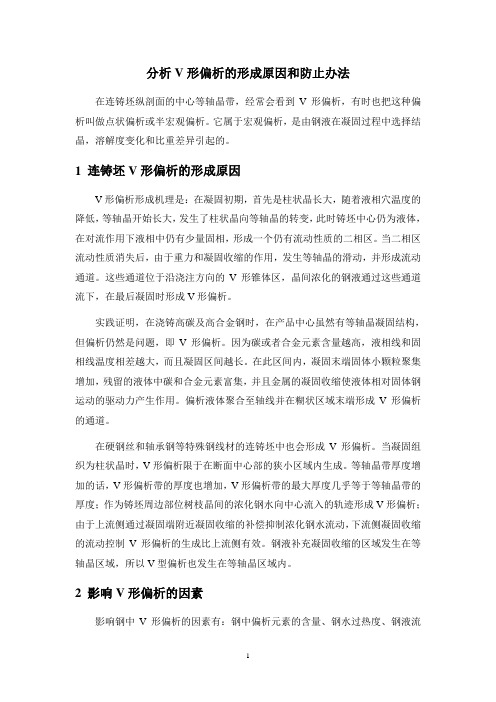
分析V形偏析的形成原因和防止办法在连铸坯纵剖面的中心等轴晶带,经常会看到V形偏析,有时也把这种偏析叫做点状偏析或半宏观偏析。
它属于宏观偏析,是由钢液在凝固过程中选择结晶,溶解度变化和比重差异引起的。
1 连铸坯V形偏析的形成原因V形偏析形成机理是:在凝固初期,首先是柱状晶长大,随着液相穴温度的降低,等轴晶开始长大,发生了柱状晶向等轴晶的转变,此时铸坯中心仍为液体,在对流作用下液相中仍有少量固相,形成一个仍有流动性质的二相区。
当二相区流动性质消失后,由于重力和凝固收缩的作用,发生等轴晶的滑动,并形成流动通道。
这些通道位于沿浇注方向的V形锥体区,晶间浓化的钢液通过这些通道流下,在最后凝固时形成V形偏析。
实践证明,在浇铸高碳及高合金钢时,在产品中心虽然有等轴晶凝固结构,但偏析仍然是问题,即V形偏析。
因为碳或者合金元素含量越高,液相线和固相线温度相差越大,而且凝固区间越长。
在此区间内,凝固末端固体小颗粒聚集增加,残留的液体中碳和合金元素富集,并且金属的凝固收缩使液体相对固体钢运动的驱动力产生作用。
偏析液体聚合至轴线并在糊状区域末端形成V形偏析的通道。
在硬钢丝和轴承钢等特殊钢线材的连铸坯中也会形成V形偏析。
当凝固组织为柱状晶时,V形偏析限于在断面中心部的狭小区域内生成。
等轴晶带厚度增加的话,V形偏析带的厚度也增加,V形偏析带的最大厚度几乎等于等轴晶带的厚度;作为铸坯周边部位树枝晶间的浓化钢水向中心流入的轨迹形成V形偏析;由于上流侧通过凝固端附近凝固收缩的补偿抑制浓化钢水流动,下流侧凝固收缩的流动控制V形偏析的生成比上流侧有效。
钢液补充凝固收缩的区域发生在等轴晶区域,所以V型偏析也发生在等轴晶区域内。
2 影响V形偏析的因素影响钢中V形偏析的因素有:钢中偏析元素的含量、钢水过热度、钢液流动、拉速、压下量、冷却及凝固等。
3 减少连铸坯V形偏析的措施(1) 众所周知,钢中偏析元素(C、P、S等)质量分数越高,偏析度也越高。
铸坯凝固结构对中心偏析影响的研究
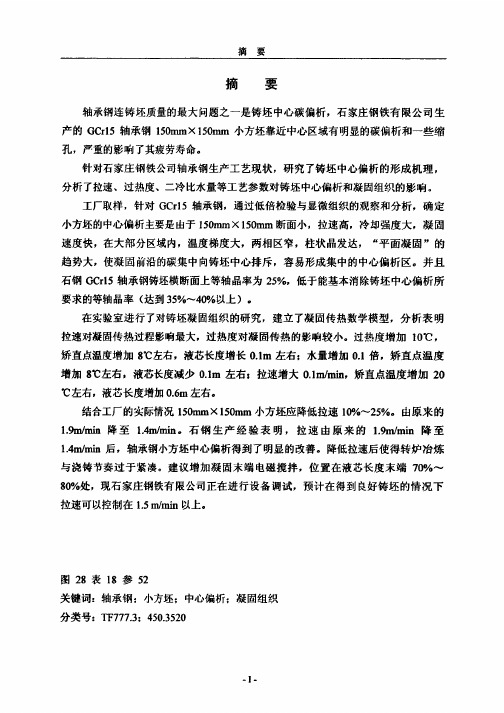
m c川s oc 阁 c bn g g o icnn uc 1g a h b i s e e i fe 扮 m m a S ean no tus ai b n a e n t d r e t O r i i o s n l k S n vi e g . t a T e fc o P c p 印 er s ba c t s e,u r 成 掀 朋d c lg h e贻t r s a 的l ,u s al p d s h l f o e r e s c sn e g 沐 e 叮 oi n
cnas g o h b n ea e.u aC ss t f r I ne ge etl g an a e a r1 Sc sI e i e , l 抓 h r re t S eS tn e r i C d h ’ O co w Pi n e u n g i , h 五ei re 巧ea t pr r g s re 幻卜 h nrwrcl l c sl ℃z g a 丘t n e ea e r g t,胃 p搜 aoe o u l r t n l r d m t U 胡 ar , ma y a r s ug w e f 斤 z t d g 以 y 】 o认r s n m的 s c r比货 “d Pr hr a e i e e 邝 “b o o ,t l g n nn c wp 吧 t ad i l te 四 e e t u rU , w cr u ec b t c t oc就 g lLs e crt ne f c tg i i Ps h e l 时 n e e f出i bl l mt c sl戏 ot ai bl h d o h nr e nie o d y a e h sn l t e f hi U ln 5思C L s os j 山 gr & 抚I o ti 声衅呱 w c i oet e 代 . i出 a o n . d 2 5 加 h l r 胡r 月 s w h 咖 Te li an 胜c 传oi t a e sd n h 曰 田 mt g o c o s”t fb eh b nt i a t h戒廿 ” ln m e 七s ft o d i i 叨 U s e oe d d e i d h be s.b 胡a a s w t t l re 此  ̄ s ae n Te l sh sl 州 i a i t e y o l n t i a g s i d吟 吨 几 优 比 dge 以 ,eee r f u ht n e Oo ℃Z e dg eo u r a o s r a i u c n 6en l , e e f sp h 吟 创 d勿 1℃, e p e fn l i s r g e e t 姆 0 e h t e e a e ti 。 gp i r b ℃ lu . r e t n 沁 t. l t pru osa 忱 i s t c a d s ,qic l g e a uomWar m t f rg n o n e y r h e s i do n h i e l . 比 1 韶 b o t e t t pr r sa t n S t r 犯 b a us 峋 d 解茂 目 y .i s e e a e ti eg I ie d b t℃月 山 . l , m l o r g 苗 幻n 山 y o m h e 理 f h c cr s rn . .u吨 r nr e 0 nm氏t l p a e s i t n O ht o m Pl a c e d勿 . 公 i h ee t o t g e g e oe l l l 比i a s I e m ru f r hn r a i s t  ̄ d 2℃ l 记c l g e a uom on pi c y b 0 ,q 一 e t n ot 6 i o n h b .. u r e C b n h c acni n f a o t u i a s le dc t au10di o t ft , P l re hu b 二 ue m 苗 e t o i g tS h c r h l 雌 t o d 0 e ye d 1%2%O l m x5n刀 a n bl fml mmn 1耐mn t e ee e 0 . f 5 m l u c t i r . it 4 iA h x rn 5 0 0 sg l o i t e g / o . e Pl t c
轴承钢球用GCr15连铸钢坯中心碳偏析控制

径 :6 5m; 5 结 晶器 电 磁 搅 拌 ; 6 二 次 冷却 : 1 . ( ) () 气
据离 散度 大 。
0
雾 冷 却 系 统 ; 7 轻 压 下 装 置 ; 8 连 铸 坯 断 面 : 9 () () 30
m m X 0 m m ; 51
U
饕 S
2 GC l r 5钢 的 偏 析 分 析
的热传 递 , 少 了凝 固前沿 的温度梯 度 , 减 抑制 了柱状 晶 的定 向增 大 , 促进 了等轴 晶的生成 在凝 固末端采 用 轻 压下 , 可消 除 或减 少铸 坯 收缩 时产 生 的 内部空
化物带状 图片对 比见 图 1 。由图l可 以看 出 , 连铸钢 中 心区域存 在明显 的碳偏 析和聚集 的碳 化物带状 。
制过程拉长 , 形成 了钢材 中心区域 的带 状 . 降低了轴承 的寿命 。江阴兴澄特种钢铁有 限公 司( 以下简称“ 澄 兴
特钢” 采用连铸方式生产的GC 1 ) r 5钢, 通过低过热度浇 注、 二冷弱冷 、 结晶器电磁搅拌等工艺, 降低了GC l r 5钢
33 结晶器电 ・ 磁搅拌和凝固末端轻压下相结合
通过 电 磁搅 拌来 搅 动钢 液 , 打断 了凝 固前 沿 的 柱状 晶 , 之重新 与钢水混 合在一起 , 使 可作 为等轴 晶
理 论 、 质元 素析 出 与 富集 理 论 和连 铸坯 芯 部空 穴 溶 抽 吸理 论 三种模 型 , 而等轴 晶率 和鼓 肚 量是 影 响 中 心 偏析 的两 个重要 因素 , 随着 等轴 晶率 增 加 和鼓 肚 量 减少 , 中心偏 析会 大大改善 _ ] I 。为控 制 GC l 2 r 5钢 的 中 心碳 偏 析 , 澄 特 钢 对 3 0mm ×5 0mm 的 兴 9 l
轴承钢连铸
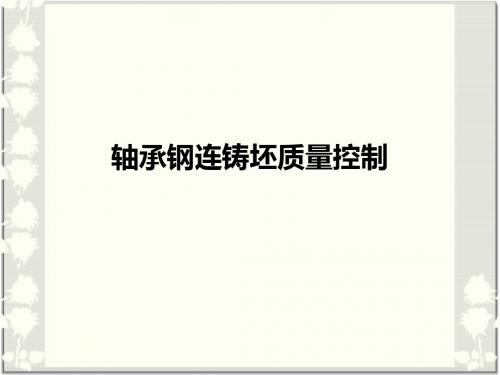
优化铸坯冷却系统
• 强化结晶器冷却系统, 提高结晶器冷却水流速度, 避免局部沸腾现象。采用合适的结晶器锥度, 减少 阻碍热传导的气隙, 增强传热效果。 • 根据二冷区内铸坯的表面温度、历史受水量、拉 坯速度及中间罐钢水过热度等因素对每流的冷却 强度进行动态控制,以达到最佳的冷却效果, 减少 铸坯表面裂纹、内部裂纹和翘曲现象, 提高其表面 质量和机械性能。
轴承钢连铸坯质量控制
轴承钢连铸坯的主要质量缺陷及其原因分析
• 轴承钢连铸主要质量问题是中心偏析、裂纹和夹 杂。 • 对于轴承钢等高碳钢铸坯,中心偏析区还有V形 偏析形成。这是因为在凝固末期,中心区液体的 温降速率大于周围液体,导致糊状区枝晶间拉应 力引起裂纹,周围的偏析液体渗人其中而形成V 形偏析。
• • • • • 采用低过热度洁净钢水浇注模式 优化铸坯冷却系统 降低铸坯的机械应力和应变率 结晶器液面控制 电磁搅拌和轻压下
采用低过热度洁净钢水浇注模式
• 强化钢水精炼, 使钢水成分、温度符合浇注要求, 有害元素和气体含量控制在最低水平。 • 采用保护浇注系统 • 采用双渣保护使钢水中夹杂物充分上浮, 中间包内 温度分布均匀, 实现各流稳定浇注。 • 选用合适性能的保护渣, 并均匀添加。 • 钢包、中间包加盖保温, 以减少热量散失,实现低 温浇注。
参考文献
[1]佘希芳,郑才翔,张晓东.改善轴承钢连铸坯质量的 主要技术措施,连铸.2000-06-15 [2]干勇,王忠英.国内特殊钢连铸生产技术的现状与 发展,特殊钢.2005-05.
降低铸坯的机械 减小机械应力。 采用多点或连续矫直, 降低铸坯表面和两相区的变 形率。
结晶器液面控制
• 采用结晶器液面控制系统, 配合小振幅、高频率的 振动, 使结晶器液面波动小, 以减小振痕, 避免卷渣 。
轴承钢偏析产生的原因
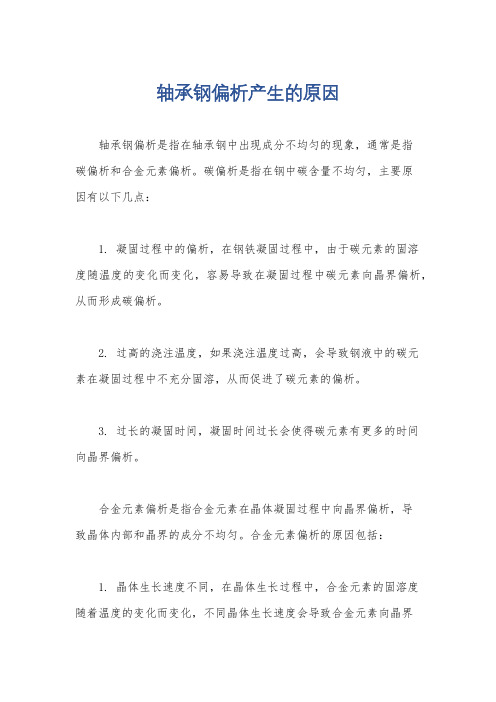
轴承钢偏析产生的原因
轴承钢偏析是指在轴承钢中出现成分不均匀的现象,通常是指
碳偏析和合金元素偏析。
碳偏析是指在钢中碳含量不均匀,主要原
因有以下几点:
1. 凝固过程中的偏析,在钢铁凝固过程中,由于碳元素的固溶
度随温度的变化而变化,容易导致在凝固过程中碳元素向晶界偏析,从而形成碳偏析。
2. 过高的浇注温度,如果浇注温度过高,会导致钢液中的碳元
素在凝固过程中不充分固溶,从而促进了碳元素的偏析。
3. 过长的凝固时间,凝固时间过长会使得碳元素有更多的时间
向晶界偏析。
合金元素偏析是指合金元素在晶体凝固过程中向晶界偏析,导
致晶体内部和晶界的成分不均匀。
合金元素偏析的原因包括:
1. 晶体生长速度不同,在晶体生长过程中,合金元素的固溶度
随着温度的变化而变化,不同晶体生长速度会导致合金元素向晶界
偏析。
2. 晶界活性差异,晶界通常是合金元素的偏析位点,晶界活性的差异会导致合金元素向晶界偏析。
除了以上原因外,还有一些其他因素可能会导致轴承钢偏析,例如原材料的质量、熔炼工艺、冷却速度等都可能对钢的偏析产生影响。
因此,为了减少轴承钢偏析的产生,需要在生产过程中严格控制原材料的质量、优化熔炼工艺、控制合金元素的含量和加强对凝固过程的监控等措施。
中心偏析与中心疏松的形成与预防

检查(如表 1),发现中心偏析一般为 B2.5 级,中 心疏松为 2 级左右。当铸坯轧制成材后,做两个断 面相互垂直的焊接试验时,在氧割或切口上出现局 部分层。根据该厂生产实际情况,为尽可能减少中 心偏析与中心疏松,生产高质量的铸坯,分析了中 心偏析与中心疏松缺陷的形成原因,提出了具体的 预防对策。
2005 年第 2 期
钢铁技术
·3·
二冷区喷嘴结构决定了冷却水的水流密度分 布、水滴速度和水滴直径。气-水喷嘴相对于压力 水喷嘴,具有喷水流量调节范围大、冷却强度大、 冷却均匀、不易堵塞等优点,但使用时消耗的动力 较大。各种喷嘴都存在一个能维持其良好雾化性能 的水量调节范围,因此,各二冷段喷嘴型号的选择 及数量的确定应保证喷嘴的实际工作水量变化范 围经常处于其正常的调节范围之内。
·2·
被“凝固晶桥”分开,晶桥下部钢液在凝固收缩时 得不到上部钢水补充而形成疏松或缩孔,并伴随中 心偏析。当凝固组织中柱状晶过于发达时,越容易 形成“凝固晶桥”,铸坯中也越容易产生中心偏析 和中心疏松。 2.2 钢液中易偏析溶质元素含量过高
中心偏析和中心疏松形成机理之二是钢液中 易偏析溶质元素析出与富集理论,即铸坯从表壳往 中心结晶过程中,钢液中的溶质元素在固液相界上 具有溶解平衡移动,C、S、P 等易偏析元素以柱状 晶粒析出,排到尚未凝固的金属液中,随结晶的继 续进行,这些易偏析元素被富集到铸坯中心或凝固 末端区域,由此产生中心偏析和中心疏松。 2.3 坯壳发生鼓肚
高碳钢连铸方坯中心偏析

高碳钢连铸方坯中心偏析薛正良李正邦张家雯摘要:综述了高碳钢连铸方坯中心偏析的成因和控制方法,分析了电磁搅拌和接近液相线温度的低过热度浇铸技术对消除或改善高碳钢连铸方坯中心偏析的作用和效果。
指出低过热度浇铸和二次水膜强化冷却是解决高碳钢连铸方坯中心偏析的有效途径,并可提高拉坯速度。
关键词:连铸坯中心偏析高碳钢低过热度Centerline Segregation in Continuous Cast High-Carbon SteelBilletXue Zhengliang Li Zhengbang Zhang Jiawen(Center Iron & Steel Research Institute)Abstract:The formation mechanism and control technology of centerline segregation in continuous cast high-carbon steel billets are reviewed in this paper.The effects of electromagnetic stirring and low surperheat casting at near liquidus temperature on eliminating or improving the centerline segregation in high-carbon steel billets are also analyzed.It is put forward that casting at near liquidus temperature and internsive secondary cooling are the effective way to solve the centerline segregation in continuous casthigh-carbon steel billets,which also can increase casting speed. Keywords:continuous cast billet centerline segregation high-carbon steel low superheat▲中心偏析是连铸坯中最常见的宏观缺陷,由于它不能通过后续的轧制或退火处理来消除,因而对材料的机械性能和加工性能产生有害的影响。
中心偏析原因_危害_评定及预防_上_
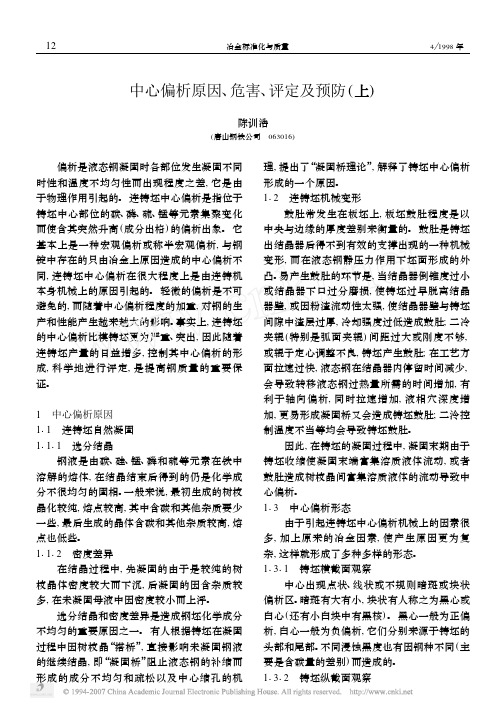
表 1 A 类中心偏析评级
评 定 原 则
级别
硫偏析带厚度, mm
形貌特征及测定方法
0. 5
> 0. 5
在铸坯宽度方向上, 硫
1. 0
0. 5~ 1. 5
偏析带呈连续状分布。厚度
1. 5
> 1. 5~ 2. 5
测定应选定在硫印图上偏
2. 0
> 2. 5~ 3. 0来自析带最严重位置, 其长度不
2. 5
2 中心偏析危害 211 中心偏析对钢成材的影响 21111 造成分层、断口不合格使钢报废
对含硫偏高的钢, 中心偏析带内往往有大 量硫化物聚集, 高熔点非金属夹杂物的变形程 度与基体大不样, 在轧制过程中造成钢的内部 裂纹, 大量的非金属夹杂物带使钢形成严重分 层。 对含锰偏高的结构钢, 容易呈现锰偏析, 在 铸态时出现树枝间锰的富集, 在轧态时出现富 锰的带状组织, 它经常使断口检查不合格。铸态 中存在锰偏析较磷偏析更不易消除, 即使热轧 后高温正火也不能消除锰偏析形成的带状组 织, 只能让钢报废。 21112 增加裂纹和疏松的敏感性
> 3. 0~ 3. 5
小于中心偏析全长的 1 4,
3. 0
> 3. 5~ 4. 0
测 5 点取平均值
中心偏析原因、危害、评定及预防 (上)
15
级别
0. 5 1. 0 1. 5 2. 0 2. 5 3. 0
表 2 B 类中心偏析评级
评 定 原 则
硫偏析带厚度, mm
形貌特征及测定方法
> 1. 0
1. 0~ 2. 0
中心偏析和中心疏松明显的铸坯, 氢气可 被偏析和疏松捕集, 从而产生非扩散型氢偏析, 即使缓冷也不能减轻缺陷。在钢材中, 氢偏析会 引起裂纹, 即生成“中心偏析型”超声波缺陷, 使 其产生氢脆。 同时, 由于成分不均匀性, 使耐腐 蚀性能下降, 将会明显降低石油管线用钢的使 用性能。 21215 降低钢材疲劳性能
管坯中心偏析

管坯中心偏析
管坯中心偏析是指管坯在冷却过程中,由于内外表面的冷却速度不均匀,导致管坯中心部分的组织结构与外表面的组织结构不一致的现象。
管坯中心偏析的原因主要有以下几点:
1. 冷却速度不均匀:由于管坯在冷却过程中,内外表面的冷却速度不同,外表面的冷却速度较快,内部中心处的冷却速度相对较慢,导致其中心部分的组织结构与外表面不同。
2. 结晶核的分布不均匀:管坯在凝固过程中,结晶核的分布不均匀也会导致中心部分的组织结构与外表面不同。
如果结晶核分布不均匀,中心部分的晶粒尺寸会较大,而外表面的晶粒尺寸较小。
3. 冷却介质的性质:冷却介质的性质也会影响管坯中心偏析。
冷却介质的传热效果不同,会导致内外表面的冷却速度不均匀,进而引起中心部分的组织结构与外表面的差异。
管坯中心偏析对于管材性能的影响较大,中心部分的组织结构与外表面的差异会导致管材在力学性能、耐腐蚀性能等方面存在差异。
因此,制造过程中应采取措施,如优化冷却介质的性质、调整冷却速度等,以减少管坯中心偏析的发生,提高管材的质量。
方坯铸坯缺陷产生原因及预防措施
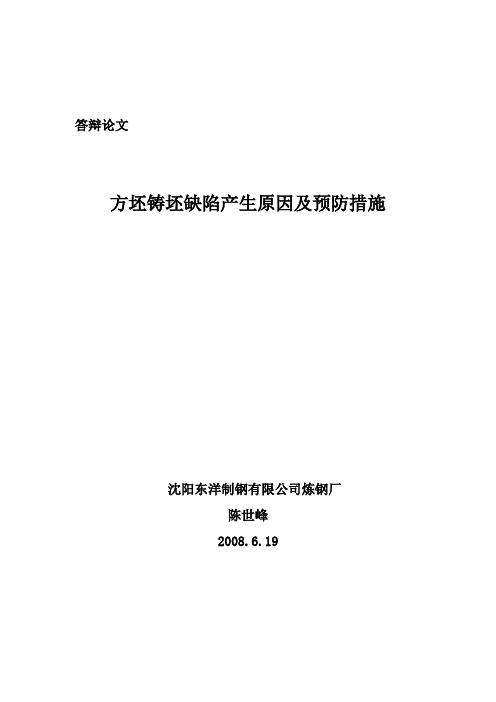
答辩论文方坯铸坯缺陷产生原因及预防措施沈阳东洋制钢有限公司炼钢厂陈世峰2008.6.19方坯铸坯缺陷产生原因及预防措施1.前言由于连铸坯质量问题多发于连铸,因此对连铸质量缺陷进行了分析,总结出发生原因,以减少连铸坯质量问题的发生。
2.铸坯主要有以下几种缺陷: 2.1卷渣2.1.1表面卷渣(见图1) 2.1.2内部卷渣(见图2)图1 图22.2裂纹2.2.1表面裂纹:头部表面裂纹(图3 )、尾部表面裂纹(见4) 。
图3 图42.2.2内部裂纹(见图5)图52.3气泡缺陷(见图6、见图7)Array Array图6 图73、缺陷产生原因及预防措施3.1卷渣产生原因及预防措施3.1.1表面卷渣产生原因及预防措施产生原因:(1)结晶器内形成渣条,当结晶器内钢液面波动量大于熔渣层厚度时、或挑渣条未挑净时、或在挑渣条过程中将渣条带入结晶器坯壳上时形成卷渣。
(2)在换包或等包降速过程中,由于操作不当造成中包液位较浅,导致中包内钢液形成涡流将中包渣卷进结晶器内,在上浮过程中被坯壳捕作形成卷渣。
(3)调整渣线高度超过液渣层厚度、或有渣条未挑净、等原因时造成颗粒渣被卷到坯壳上而形成卷渣。
(4)在开浇升速前液渣厚度未达到标准,造成颗粒渣或予熔层的保护渣直接与钢液接触,升速过程中在结晶器内造成钢液面发生波动,导致保护渣被卷入到坯壳上,形成卷渣。
(5)中包掉料或有杂物,开浇过程中被钢水冲到结晶器内,从而形成卷渣。
(6)中包内钢液面剧烈波动时,造成中包内覆盖剂被卷入中包钢液中,此时被卷入的覆盖剂受两个力作用:向上的钢水的浮力和向下的钢流股吸力作用,当向下的钢流股吸力大于向上钢水的上浮力时,卷入的覆盖剂就被卷入到结晶器内,在钢流流股的作用下,如被坯壳捕作而形成皮下卷渣,如被向下流股带入液相穴深处而形成内部卷渣。
(7)挑渣条用8#钢线(或细铁线),在钢线上结钢瘤或渣块,有钢瘤的8#线熔断到结晶器钢液内部,如被坯壳捕作到而形成皮下卷渣,如进入液相穴深处而形成内部卷渣。
轴承钢连铸坯偏析和致密度的分析
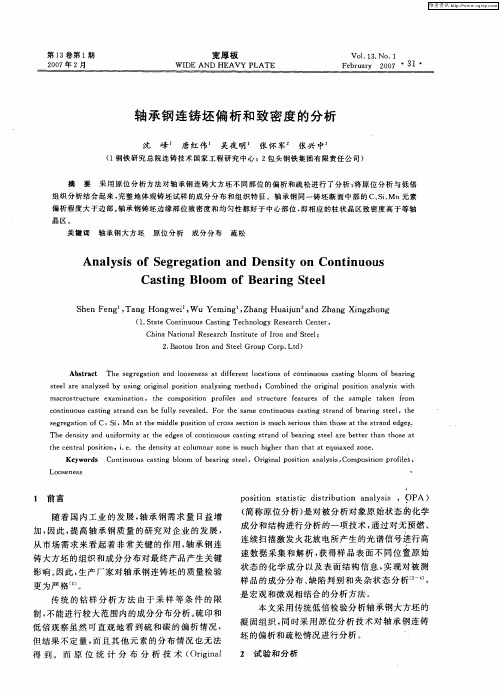
Ab t a t Th e r g t n a d l o e e s a i e e t l c to s o o tn o s c s i g b o m f b a i g s r c e s g e a i n o s n s t d f r n o a in fc n i u u a tn l o o e rn o f s e la e a a y e y u i g o i i a o i o n l zn t o ;Co i e h r i a o ii n a a y i wih t e r n l z d b sn rg n lp st n a a y i g me h d i mb n d t e o i n lp s t n l ss g o t ma r s r c u e x mi a in, t e o c o t u t r e a n to h c mp st n r fls n s r c u e e t r s f h s mp e a e f o o ii p o i a d t u t r fa u e o t e a l o e t k n r m
t e r lp s ton,i e t e d nst tc u na one i u h ghe ha ha te hec nt a o ii . . h e iy a ol m rz s m c hi rt n t ta quixe o a d z ne.
Th e st n n f r i t t e e g s o o tn o s c s i g s r n fb a i g s e la e b t e h n t o e a e d n i a d u io m t a h d e fc n i u u a tn t a d o e rn t e r e t r t a h s t y y
连铸方坯 中心偏析 标准
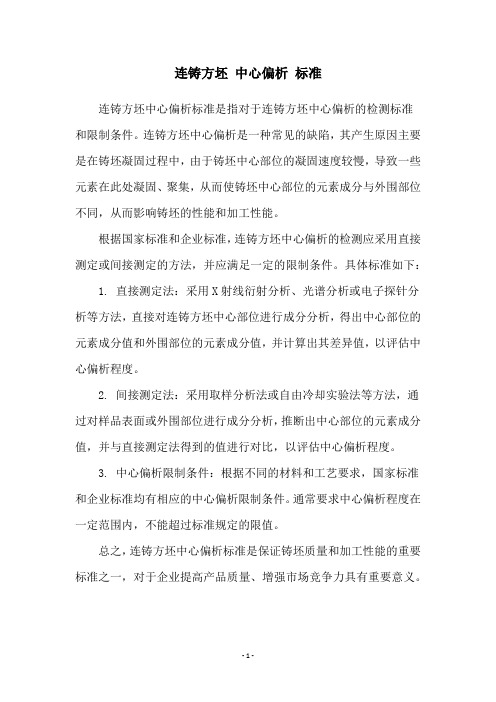
连铸方坯中心偏析标准
连铸方坯中心偏析标准是指对于连铸方坯中心偏析的检测标准
和限制条件。
连铸方坯中心偏析是一种常见的缺陷,其产生原因主要是在铸坯凝固过程中,由于铸坯中心部位的凝固速度较慢,导致一些元素在此处凝固、聚集,从而使铸坯中心部位的元素成分与外围部位不同,从而影响铸坯的性能和加工性能。
根据国家标准和企业标准,连铸方坯中心偏析的检测应采用直接测定或间接测定的方法,并应满足一定的限制条件。
具体标准如下: 1. 直接测定法:采用X射线衍射分析、光谱分析或电子探针分析等方法,直接对连铸方坯中心部位进行成分分析,得出中心部位的元素成分值和外围部位的元素成分值,并计算出其差异值,以评估中心偏析程度。
2. 间接测定法:采用取样分析法或自由冷却实验法等方法,通过对样品表面或外围部位进行成分分析,推断出中心部位的元素成分值,并与直接测定法得到的值进行对比,以评估中心偏析程度。
3. 中心偏析限制条件:根据不同的材料和工艺要求,国家标准和企业标准均有相应的中心偏析限制条件。
通常要求中心偏析程度在一定范围内,不能超过标准规定的限值。
总之,连铸方坯中心偏析标准是保证铸坯质量和加工性能的重要标准之一,对于企业提高产品质量、增强市场竞争力具有重要意义。
- 1 -。
轴承钢液析缺陷产生原因及预防措施
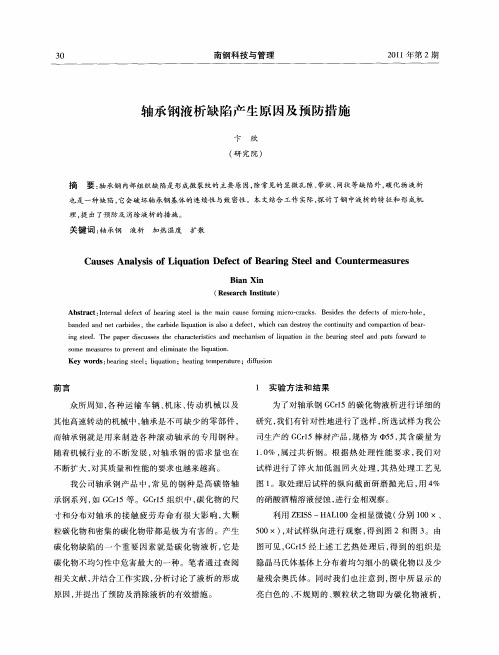
关键 词 : 轴承钢 液析 加热温度 扩散
Ca e us s Ana y i f Li ua i n De e to a i t e n unt r e s e l ss o q to f c fBe r ng S e la d Co e m a ur s
承钢钢坯 的加 热 温度应 该 尽量 提高 。但 是 , 这绝 对 不意味着加热温度愈高愈好 。从 防止显微 孔隙 的角
温。钢坯 在高温下保温时间愈 长 , 扩散效果 愈好 , 钢 中树枝状偏析程度也会愈低 。用 在高温长 时间保 温 后的钢坯生产 出来 的钢 材 , 化物 不均 匀性 必然很 碳 小 。尽管延长保 温 时间可 以增 加扩 散 的效果 , 降低 钢 中碳化物不 均匀性 , 过分 的延 长保 温时 间一 方 但 面是不经济 的, 另一方面可能造成粘钢 。 此外 , 控制钢坯 出炉速度 以及轧制节 奏 , 也能 有 效降低液析产生 的概率 。控制钢 坯 出炉 速度实 际上
相关文献 , 并结合工作实践 , 分析讨 论 了液 析 的形成
原 因, 并提 出了预防及消除液析 的有效措施 。
2 1 年第 2期 01
南钢 科技 与管 理
3 1
这种碳化 物很难 消 除。热 加 工时 , 破 碎成 不规 则 被 碎块 , 沿压延 方 向呈链 状或 条状 分布 。一 般认 为碳 化物液析属 于三角 晶系碳化物 , 其硬度 和脆 性极 高 ,
如果加热温度过 高 , 扩散 时 间过长 , 一方 面有可能 造 成钢材脱碳 超标 , 另一 方面 , 碳化 物即熔化 或消失 留
下孔洞甚至产生 内烧 , 孔洞如 果在 以后 的轧 制过程 中
大方坯轴承钢中心偏析的成因及预防措施
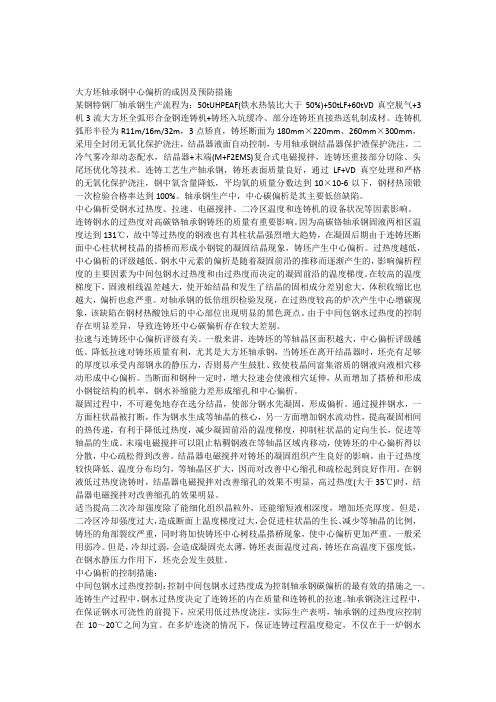
大方坯轴承钢中心偏析的成因及预防措施某钢特钢厂轴承钢生产流程为:50tUHPEAF(铁水热装比大于50%)+50tLF+60tVD真空脱气+3机3流大方坯全弧形合金钢连铸机+铸坯入坑缓冷、部分连铸坯直接热送轧制成材。
连铸机弧形半径为R11m/16m/32m,3点矫直,铸坯断面为180mm×220mm、260mm×300mm,采用全封闭无氧化保护浇注,结晶器液面自动控制,专用轴承钢结晶器保护渣保护浇注,二冷气雾冷却动态配水,结晶器+末端(M+F2EMS)复合式电磁搅拌,连铸坯重接部分切除、头尾坯优化等技术。
连铸工艺生产轴承钢,铸坯表面质量良好,通过LF+VD真空处理和严格的无氧化保护浇注,钢中氧含量降低,平均氧的质量分数达到10×10-6以下,钢材热顶锻一次检验合格率达到100%。
轴承钢生产中,中心碳偏析是其主要低倍缺陷。
中心偏析受钢水过热度、拉速、电磁搅拌、二冷区温度和连铸机的设备状况等因素影响。
连铸钢水的过热度对高碳铬轴承钢铸坯的质量有重要影响。
因为高碳铬轴承钢固液两相区温度达到131℃,故中等过热度的钢液也有其柱状晶强烈增大趋势,在凝固后期由于连铸坯断面中心柱状树枝晶的搭桥而形成小钢锭的凝固结晶现象,铸坯产生中心偏析。
过热度越低,中心偏析的评级越低。
钢水中元素的偏析是随着凝固前沿的推移而逐渐产生的,影响偏析程度的主要因素为中间包钢水过热度和由过热度而决定的凝固前沿的温度梯度。
在较高的温度梯度下,固液相线温差越大,使开始结晶和发生了结晶的固相成分差别愈大,体积收缩比也越大,偏析也愈严重。
对轴承钢的低倍组织检验发现,在过热度较高的炉次产生中心增碳现象,该缺陷在钢材热酸蚀后的中心部位出现明显的黑色斑点。
由于中间包钢水过热度的控制存在明显差异,导致连铸坯中心碳偏析存在较大差别。
拉速与连铸坯中心偏析评级有关。
一般来讲,连铸坯的等轴晶区面积越大,中心偏析评级越低。
降低拉速对铸坯质量有利,尤其是大方坯轴承钢,当铸坯在离开结晶器时,坯壳有足够的厚度以承受内部钢水的静压力,否则易产生鼓肚、致使枝晶间富集溶质的钢液向液相穴移动形成中心偏析。
大型锻件的缺陷与对策

大型锻件的缺陷与对策:偏析钢中化学成分与杂质分布的不均匀现象,称为偏析。
一般将高于平均成分者,称为正偏析,低于平均成分者,称为负偏析。
尚有宏观偏析,如区域偏析与微观偏析,如枝晶偏析,晶间偏析之分。
大锻件中的偏析与钢锭偏析密切相关,而钢锭偏析程度又与钢种、锭型、冶炼质量及浇注条件等有关。
合金元素、杂质含量、钢中气体均加剧偏析的发展。
钢锭愈大,浇注温度愈高,浇注速度愈快,偏析程度愈严重。
(1)区域偏析它属于宏观偏析,是由钢液在凝固过程中选择结晶,溶解度变化和比重差异引起的。
如钢中气体在上浮过程中带动富集杂质的钢液上升的条状轨迹,形成须状∧形偏析。
顶部先结晶的晶体和高熔点的杂质下沉,仿佛结晶雨下落形成的轴心∨形偏析。
沉淀于锭底形成负偏析沉积锥。
最后凝固上部区域,碳、硫、磷等偏析元素富集,成为缺陷较多的正偏析区。
防止区域偏析的对策是:1)降低钢中硫、磷等偏析元素和气体的含量,如采用炉外精炼,真空碳脱氧(VCD)处理及锭底吹氩工艺。
2)采用多炉合浇、冒口补浇、振动浇注及发热绝热冒口,增强冒口补缩能力等措施。
3)严格控制注温与注速,采用短粗锭型,改善结晶条件。
在锻件横向低倍试片上,呈现与锭型轮廓相对应的框形特征,亦称框形偏析。
因锭中偏析带在变形时,沿分模面扩展而呈现为框形。
偏析带由小孔隙及富集元素构成,对锻件组织性能的均匀性有不良的影响。
电渣重熔以其纯净度高、结晶结构合理,成为生产重要大锻件钢坯的方法,但是如果在重熔过程中电流、电压不稳定,则会形成波纹状偏析。
当电流、电压增高时,钢液过热,结晶速度减缓,钢液中的溶质元素在结晶前沿偏聚形成富集带;当电流、电压减小时,熔质元素偏聚程度减小,这种周期性的变化,便形成了波纹状的偏析条带。
区域偏析在横向低倍酸浸试片上呈分散的深色斑点状,称之为点状偏析。
(2)枝晶偏析它属于微观偏析。
树枝状结晶与晶间微区成分的不均匀性,可能引起组织性能的不均匀分布。
采用扫描电镜(SEM)、波谱仪(WDS)、能谱仪(EDS)进行微区观察和成分分析可以检出并阐明原因,一般通过高温扩散加热,锻压合理变形与均匀化热处理可以消除或减轻其不良影响。
轴承故障及原因分析与防止措施

轴承故障及原因分析与防止措施运转时有异响1•滚动体或滚道剥落重皮,表面不平2. 轴承零件安装不当,轴承附件有松动和摩擦3. 缺乏润滑剂4. 轴承内有铁屑或污物1. 拆卸检查或更换2. 注意安装质量3. 按规定定时加润滑剂4. 拆卸、清洗或更换滚动体严重磨损1. 轴承承受了不当的轴向载荷2. 滚动体安装歪斜3. 润滑剂太稠4. 滚动体不滚动,产生滑动摩擦,以致磨伤5. 轴承温升过高导致滚动体损伤6. 机械振动或轴承安装不当,使滚动体挤碎7. 轴承制造精度不高,热处理不当,硬度低,滚动体被磨成多棱形1、2按要求保证安装质量3. 按规定使用润滑剂,或定期更换润滑剂4、5、6、7.注意使用中的维护滚道出现坑疤1. 金属剥落,锈蚀2. 缺少润滑剂3. 使用材料不当4. 轴承受冲击载荷5. 电流通过轴承,产生局部高温,金属熔化按轴承的工作性能正确选用轴承按规定定时加润滑剂严禁电气设备漏电,机器要有接地装置1.轴颈或轴承座孔配合面接触不良, 1.按要求保证安装滚道受力部位出现空隙,轴承受力大质量轴承内而不均匀,产生疲劳裂纹 2.按规程正确拆装外圈裂2.拆装不当,安装时受到敲打 3.及时更换磨损的纹 3.轴承间隙磨大造成冲击振动轴承4.轴承制造质量不良,内部有裂纹4.严格检查轴承的制造质量1.轴承受冲击力和交变载荷及滚动体按要求保证安装质表面接触应力反复变化hl2.内外圈安装歪斜,轴向配合台阶面正确使用轴承不垂直,轴弯曲,轴孔不同心注意不要将铁屑和3.轴承间隙调整过紧其他污物落入轴承轴承金4.轴承配合面之间落入铁屑或硬质脏内属剥落物正确选用轴承注意使用维护5. 轴颈或轴承座孔呈椭圆形,导致滚道局部负担过重6. 所选代用或换用轴承型号不符合规定滚动体1.安装间隙过小,挤压力过大合理调整间隙被压2.使用时受到剧烈冲击注意润滑剂的洁净碎,多 3.润滑剂中混入坚硬的铁屑等污物按规定时间更换或出现于 4.滚动体原来有裂纹或轴承使用时检修轴承推力球间过长轴承1•轴承清洗不干净,滚动体与滚道 1.注意清洗质量有砂粒或铁屑2.注意安装质量2.保持架变形,滚动体与轴承圈碰3.刮研轴径(或壳安装后触孔径),使其配合手转不3.轴承和轴(或壳孔)的配合过紧过盈适当减小;轴动(过盈量过大,轴承游隙减少)或轴承原始游隙太小,承原始游隙太小无法修理,必须更换1•轴承上下圈不平行按要求保证安装质轴承滚 2.回转速度过大道产生 3.滚动体在滚道上滑转按使用要求正确选刮痕 4.润滑剂不干净用轴承加强润滑管理。
铸坯中心偏析工艺影响因素分析及改进措施
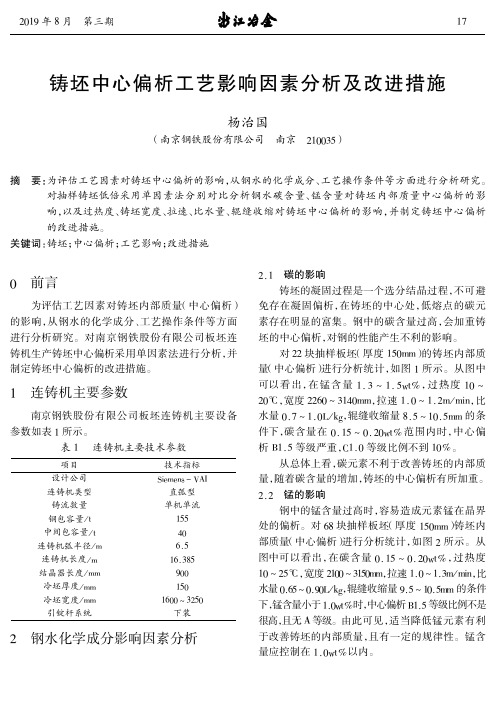
+!, - ".
(!) 量 $%!4 * $%"$&’( ,锰含量 !%$ * !%4&’( ,宽度 "4$$
/!0(.1 2 .3)
(") * #"$$66,拉 速 !%$ * !%#6 - 678,比 水 量 $%9 *
式中,+ 为液态金属凝固形核率;/ 为晶体生长 $%:1 - ;<,辊缝收缩量 =%4 * !$%466 的条件下,过热
大,己结晶形核的晶胞向前生长的速度越快,柱状 质量,过热度应控制在 ! * !$>范围内。
#’%6 年 2 月 第三期
铸坯中心偏析工艺影响因素分析及改进措施
%6
图 ! 过热度对中心偏析的影响
!"# 铸坯宽度的影响
缝收缩量 6"& ) %’"&((,从整体看,#%&’ ) #&&’((、
对 $$ 块抽样板坯(厚度 %&’(()铸坯内部质量 #&&’ ) #6&’((、!’’’ ) !!’’(( 期间,7%"’ 8 9%"& 级
从总体上看,碳元素不利于改善铸坯的内部质 量,随着碳含量的增加,铸坯的中心偏析有所加重。 !4! 锰的影响
钢中的锰含量过高时,容易造成元素锰在晶界 处的偏析。对 35 块抽样板坯(厚度 "%#)))铸坯内 部质量(中心偏析)进行分析统计,如图 ! 所示。从 图中可以看出,在碳含量 # 4 "% 7 # 4 !#819 ,过热度 "# 7 !%:,宽度 !"## 7 $"%#)),拉速 "4# 7 "4$)0 )’*,比 水量 #43% 7 #46#<0 =>,辊缝收缩量 64% 7 "#4%)) 的条件 下,锰含量小于 "4#819时,中心偏析 ?"4% 等级比例不是 很高,且无 . 等级。由此可见,适当降低锰元素有利 于改善铸坯的内部质量,且有一定的规律性。锰含 量应控制在 " 4 #819 以内。
减少方坯中心偏析的冶金手段
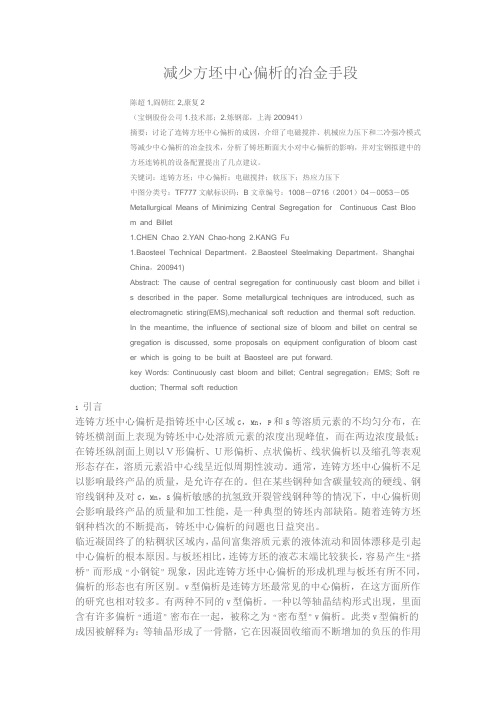
减少方坯中心偏析的冶金手段陈超1,阎朝红2,康复2(宝钢股份公司1.技术部;2.炼钢部,上海200941)摘要:讨论了连铸方坯中心偏析的成因,介绍了电磁搅拌、机械应力压下和二冷强冷模式等减少中心偏析的冶金技术,分析了铸坯断面大小对中心偏析的影响,并对宝钢拟建中的方坯连铸机的设备配置提出了几点建议。
关键词:连铸方坯;中心偏析;电磁搅拌;软压下;热应力压下中图分类号:TF777文献标识码:B文章编号:1008-0716(2001)04-0053-05Metallurgical Means of Minimizing Central Segregation for Continuous Cast Bloom and Billet1.CHEN Chao2.YAN Chao-hong 2.KANG Fu1.Baosteel Technical Department,2.Baosteel Steelmaking Department,ShanghaiChina,200941)Abstract: The cause of central segregation for continuously cast bloom and billet is described in the paper. Some metallurgical techniques are introduced, such aselectromagnetic stiring(EMS),mechanical soft reduction and thermal soft reduction.In the meantime, the influence of sectional size of bloom and billet on central segregation is discussed, some proposals on equipment configuration of bloom caster which is going to be built at Baosteel are put forward.key Words: Continuously cast bloom and billet; Central segregation;EMS; Soft reduction; Thermal soft reduction1 引言连铸方坯中心偏析是指铸坯中心区域C,Mn,P和S等溶质元素的不均匀分布,在铸坯横剖面上表现为铸坯中心处溶质元素的浓度出现峰值,而在两边浓度最低;在铸坯纵剖面上则以V形偏析、U形偏析、点状偏析、线状偏析以及缩孔等表观形态存在,溶质元素沿中心线呈近似周期性波动。
中心偏析原因危害评定及预防(下)
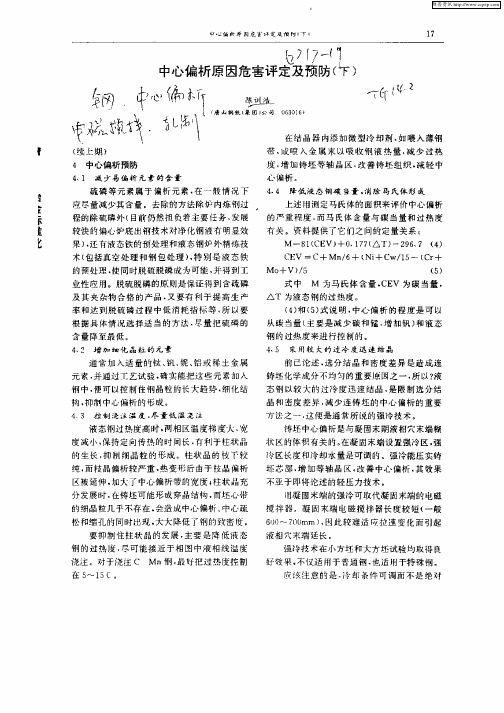
匕
C EV = C+ M n / 6 + ( Ni + Cw/ 1 5 一 ( Cr + Mo + V) / 5 ( 5 )
式中
M 为马 氏体 含量 . C E V 为碳 当 量 .
△T 为液态 钢的过 热度 。 ( 4 ) 和( 5 ) 式说 明 , 中心 偏析 的 程 度是 可 以 从碳 当量 ( 主 要是 减 少 碳 和 锰 . 增加钒) 和 液 态 钢的 过热 度来进 行控 制的 。
上 述用 测定马 氏体 的面积 来评 价 中心 偏析 的严重 程 度 . 而 马 氏体 含量 与 碳 当 量 和过 热度 有 关 。资料提 供了 它们 之间的 定量 关系
M一8 1 ( CEV ) +0 、 I 7 7 ( △ T) 一2 : 9 6 、 7 ( 4 )
童
较快 的偏心炉 底 出钢技 术对净 化钢 液有 明显 效 果) , 还 有液 态铁的预 处理 和液 态钢炉 外 精炼 技 术( 包括 真空 处理 和钢 包 处理 ) t 特 别 是 液 态 铁 的预 处理 , 使 同时脱 硫脱磷 成 为可能 , 并 得到 工 业性 应 用 。脱硫 脱磷 的原 则是 保证 得到 含硫 磷 及 其 夹 杂物 合格 的 产 品 , 又要 有 利于 提 高 生 产 率 和达 到 脱硫 磷 过 程 中低 消耗 指 标 等 , 所 以要 根据 具体 情 况选 择适 当的 方 法 , 尽量 把 硫 磷 的 含量 降至最 低 。
维普资讯
中・ 0偏 析 原 因危 害评 定醍 预 防 ( 下
1 7
7 f 7 一 ( 中心偏 析 原 因危 害评 定 及预 防 ( 下)
童
咿鼻 { 1
- 1、下载文档前请自行甄别文档内容的完整性,平台不提供额外的编辑、内容补充、找答案等附加服务。
- 2、"仅部分预览"的文档,不可在线预览部分如存在完整性等问题,可反馈申请退款(可完整预览的文档不适用该条件!)。
- 3、如文档侵犯您的权益,请联系客服反馈,我们会尽快为您处理(人工客服工作时间:9:00-18:30)。
大方坯轴承钢中心偏析的成因及预防措施
某钢特钢厂轴承钢生产流程为:50tUHPEAF(铁水热装比大于50%)+50tLF+60tVD真空脱气+3机3流大方坯全弧形合金钢连铸机+铸坯入坑缓冷、部分连铸坯直接热送轧制成材。
连铸机弧形半径为R11m/16m/32m,3点矫直,铸坯断面为180mm×220mm、260mm×300mm,采用全封闭无氧化保护浇注,结晶器液面自动控制,专用轴承钢结晶器保护渣保护浇注,二冷气雾冷却动态配水,结晶器+末端(M+F2EMS)复合式电磁搅拌,连铸坯重接部分切除、头尾坯优化等技术。
连铸工艺生产轴承钢,铸坯表面质量良好,通过LF+VD真空处理和严格的无氧化保护浇注,钢中氧含量降低,平均氧的质量分数达到10×10-6以下,钢材热顶锻一次检验合格率达到100%。
轴承钢生产中,中心碳偏析是其主要低倍缺陷。
中心偏析受钢水过热度、拉速、电磁搅拌、二冷区温度和连铸机的设备状况等因素影响。
连铸钢水的过热度对高碳铬轴承钢铸坯的质量有重要影响。
因为高碳铬轴承钢固液两相区温度达到131℃,故中等过热度的钢液也有其柱状晶强烈增大趋势,在凝固后期由于连铸坯断面中心柱状树枝晶的搭桥而形成小钢锭的凝固结晶现象,铸坯产生中心偏析。
过热度越低,中心偏析的评级越低。
钢水中元素的偏析是随着凝固前沿的推移而逐渐产生的,影响偏析程度的主要因素为中间包钢水过热度和由过热度而决定的凝固前沿的温度梯度。
在较高的温度梯度下,固液相线温差越大,使开始结晶和发生了结晶的固相成分差别愈大,体积收缩比也越大,偏析也愈严重。
对轴承钢的低倍组织检验发现,在过热度较高的炉次产生中心增碳现象,该缺陷在钢材热酸蚀后的中心部位出现明显的黑色斑点。
由于中间包钢水过热度的控制存在明显差异,导致连铸坯中心碳偏析存在较大差别。
拉速与连铸坯中心偏析评级有关。
一般来讲,连铸坯的等轴晶区面积越大,中心偏析评级越低。
降低拉速对铸坯质量有利,尤其是大方坯轴承钢,当铸坯在离开结晶器时,坯壳有足够的厚度以承受内部钢水的静压力,否则易产生鼓肚、致使枝晶间富集溶质的钢液向液相穴移动形成中心偏析。
当断面和钢种一定时,增大拉速会使液相穴延伸,从而增加了搭桥和形成小钢锭结构的机率,钢水补缩能力差形成缩孔和中心偏析。
凝固过程中,不可避免地存在选分结晶,使部分钢水先凝固,形成偏析。
通过搅拌钢水,一方面柱状晶被打断,作为钢水生成等轴晶的核心,另一方面增加钢水流动性,提高凝固相间的热传递,有利于降低过热度,减少凝固前沿的温度梯度,抑制柱状晶的定向生长,促进等轴晶的生成。
末端电磁搅拌可以阻止粘稠钢液在等轴晶区域内移动,使铸坯的中心偏析得以分散,中心疏松得到改善。
结晶器电磁搅拌对铸坯的凝固组织产生良好的影响,由于过热度较快降低、温度分布均匀,等轴晶区扩大,因而对改善中心缩孔和疏松起到良好作用。
在钢液低过热度浇铸时,结晶器电磁搅拌对改善缩孔的效果不明显,高过热度(大于35℃)时,结晶器电磁搅拌对改善缩孔的效果明显。
适当提高二次冷却强度除了能细化组织晶粒外,还能缩短液相深度,增加坯壳厚度。
但是,二冷区冷却强度过大,造成断面上温度梯度过大,会促进柱状晶的生长、减少等轴晶的比例,铸坯的角部裂纹严重,同时将加快铸坯中心树枝晶搭桥现象,使中心偏析更加严重。
一般采用弱冷。
但是,冷却过弱,会造成凝固壳太薄,铸坯表面温度过高,铸坯在高温度下强度低,在钢水静压力作用下,坯壳会发生鼓肚。
中心偏析的控制措施:
中间包钢水过热度控制:控制中间包钢水过热度成为控制轴承钢碳偏析的最有效的措施之一。
连铸生产过程中,钢水过热度决定了连铸坯的内在质量和连铸机的拉速。
轴承钢浇注过程中,在保证钢水可浇性的前提下,应采用低过热度浇注,实际生产表明,轴承钢的过热度应控制在10~20℃之间为宜。
在多炉连浇的情况下,保证连铸过程温度稳定,不仅在于一炉钢水
的温度稳定,而且更重要的在于各连浇炉次之间的温度稳定,才能保证连铸过程的全程温度恒定,此稳定主要依靠生产过程中电炉、LF精炼炉、VD炉、连铸各工序间的相互协调和合理调度。
二冷工艺控制:轴承钢的裂纹敏感性强,高温导热系数小。
若加大二冷区冷却强度,会增大铸坯断面内的温度梯度,增加中心偏析和热裂倾向。
因此,采用弱的二冷配水工艺,且保证二冷配水均匀,以达到减少中心偏析和裂纹的目的。
稳定拉速:控制升降拉速幅度,做到升降平稳,提高浇铸稳定性。
保证合适的结晶器水口浸入深度,结晶器液面自控系统稳定,避免结晶器液面紊乱,保证结晶器液面稳定。
制定合适的温度拉速制度,通过降低钢水过热度、稳定拉坯速度,缩短并稳定液相穴长度,减轻因拉速不稳定造成连铸坯液相穴钢液补缩不充分。
生产中,轴承钢钢水过热度在10~20℃之间时,拉速控制在0.60~0.70m/min,对控制中心偏析效果明显。