中心偏析与中心疏松的形成与预防_邹冰梅
防止小方坯中心偏析的研发新成果

3 0
昆
钢
科
技
20 0 8年 1 第 4期 月
表 6 不 同原 料 加 热 到 6 ℃分 解 前 后 的数 据 0
l 2 3 4
水 分
%
P H
酚
%
水分
%
P H
酚
%
水分
%
P H
酚
%
水分
%
P H
5 结束 语
应用 3 的方 法进 行 生产 时 , C 解 后 的 3 对 O分
果 也不 同 。所 以 , 得 到 质量 好 , 稳 定 的粗 酚产 要 且
品. 在实 际生产 中还需 进一 步 改进操 作方 法。
防止 小方坯 中心偏 析的研发新成 果
虽然 大方 坯连 铸 现 已基 本 上 克 服 了一 度 曾影 响铸 坯质 量 的中心 疏松 及偏 析 这类 缺陷 , 小 方坯 但 连铸 中发 生 的类 似 问题 却 一直 未 能 得 到适 当 的解 决 。过去 的几年 , 多厂家 为提 高 自己小 方坯 连铸 许 机 浇 铸高 碳钢 及高 合 金 钢 的成 功 率 做 了大 量研 究 参 数 ( 如 浇铸 速 度, 例 浇注 方式 等 ) 上 述 具体 技 术 与
到要求 。 由于 实验 室 的操 作 条件 在 生 产 上不 容 易完 全 实现 .所 以在 实 际生 产上 分 解 效 果 没有 实验 室 的 效果 好 . 由于每 次 实验 的原 料 不 同 , 再 因此 分解 效
反 应 速度 。提 高分 解 效率 。使 酚 含量 尽快 达 到 要
求。
“ 钉 型 ” 分 的 形 成。 致 力 学 性 能不 一 致 , 微 成 导 造成
连铸板坯中心偏析的成因及预防措施调研
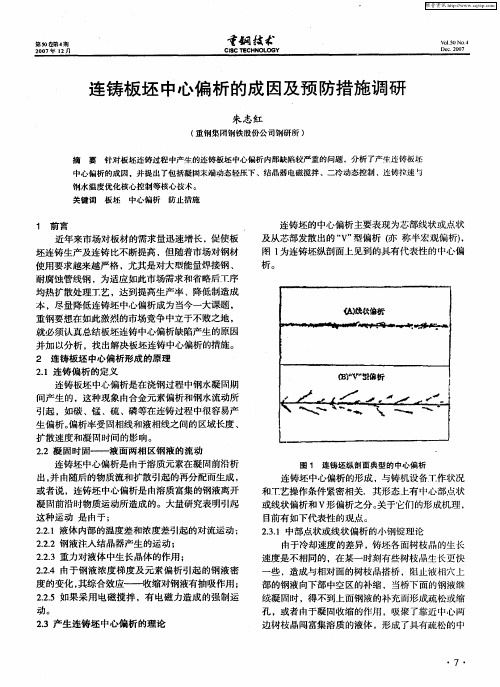
图 l 为连铸坯纵剖面上见到的具有代表性的中心偏 析。
本 ,尽量降低连铸坯中心偏析成为当今一大课题 , 重钢要想在如此激烈的市场竞争中立于不败之地 , 就必须认真总结板坯连铸中心偏析缺陷产生的原因 并加 以分析 ,找出解决板坯连铸中心偏析的措施。
2 连 铸板 坯 中心偏 析 形成 的原 理
关键 词 板坯 中心偏析 防止措 施
1 前 言
连铸 坯 的 中心偏 析 主要表 现 为芯 部线 状 或点 状 及从 芯部 发散 出的 “ ” V 型偏 析 ( 称 半宏 观偏 析) 亦 ,
近年来市场对板材的需求量迅速增长 , 促使板 坯连铸生产及连铸 比不断提高 .但随着市场对钢材 使用要求越来越严格 ,尤其是对大型能量焊接钢 、 耐腐蚀管线钢 ,为适应如此市场需求和省略后T序 均热扩散处理_艺 ,达到提高生产率 、降低制造成 丁
l蛙 鼍 蚜 ≈盘 砖 跫
焉
r ・
…。
l 兼筮 柱 状 岛 蜓 毙盎 § I
。 ‘
鬻
u 噬 l + 《 簧 强 蹴 “ 。
; . ‘
母 l 产 生埭
.;
:. 学 幻 - 憩 } . F : 土 钉
图 2 “ 钢 锭 ” 结构 形 成 过 程 示 意 图 小
图 1 连 铸 坯 纵 剖 面 典 型 的 中 心 偏 析
连铸坯中心偏析的形成 , 与铸机设备_作状况 T 和_艺操作条件紧密相关.其形态上有 中心部点状 T 或线状 偏 析 和 V形 偏析 之分 。 于它 们 的形 成机 理 , 关 目前有如下代表性的观点。 231中部 点状 或线 状 偏析 的小钢 锭理 论 .. 南于冷却速度 的差异 。 铸坯各面树枝品的生长 速度是 不相 同的 ,在某 一时 刻有 些树 枝 品生 长更 快 些 ,造成与相对面的树枝品搭桥 ,阻止液相穴上 部 的钢液 向下 部 中空 区的补 缩 ,当桥下 面 的钢液 继 续凝同时 ,得不到上面钢液的补充而形成疏松或缩 孔 ,或者 南于 凝 固收缩 的作 用 ,吸 聚 了靠近 中心 两 边{ 品闯富集 溶 质 的液体 。形成 了具 有疏 松 的 中 对枝
中心偏析与中心疏松的形成与预防

检查(如表 1),发现中心偏析一般为 B2.5 级,中 心疏松为 2 级左右。当铸坯轧制成材后,做两个断 面相互垂直的焊接试验时,在氧割或切口上出现局 部分层。根据该厂生产实际情况,为尽可能减少中 心偏析与中心疏松,生产高质量的铸坯,分析了中 心偏析与中心疏松缺陷的形成原因,提出了具体的 预防对策。
2005 年第 2 期
钢铁技术
·3·
二冷区喷嘴结构决定了冷却水的水流密度分 布、水滴速度和水滴直径。气-水喷嘴相对于压力 水喷嘴,具有喷水流量调节范围大、冷却强度大、 冷却均匀、不易堵塞等优点,但使用时消耗的动力 较大。各种喷嘴都存在一个能维持其良好雾化性能 的水量调节范围,因此,各二冷段喷嘴型号的选择 及数量的确定应保证喷嘴的实际工作水量变化范 围经常处于其正常的调节范围之内。
·2·
被“凝固晶桥”分开,晶桥下部钢液在凝固收缩时 得不到上部钢水补充而形成疏松或缩孔,并伴随中 心偏析。当凝固组织中柱状晶过于发达时,越容易 形成“凝固晶桥”,铸坯中也越容易产生中心偏析 和中心疏松。 2.2 钢液中易偏析溶质元素含量过高
中心偏析和中心疏松形成机理之二是钢液中 易偏析溶质元素析出与富集理论,即铸坯从表壳往 中心结晶过程中,钢液中的溶质元素在固液相界上 具有溶解平衡移动,C、S、P 等易偏析元素以柱状 晶粒析出,排到尚未凝固的金属液中,随结晶的继 续进行,这些易偏析元素被富集到铸坯中心或凝固 末端区域,由此产生中心偏析和中心疏松。 2.3 坯壳发生鼓肚
型钢龟裂影响因素及预防措施

型钢龟裂影响因素及预防措施袁月【摘要】以型钢表面龟裂为研究对象,通过对化学成分及连铸工艺、轧钢工艺的分析,阐述型钢表面产生龟裂缺陷形成的影响因素.并提出了炼钢工艺、连铸工艺及轧制工艺三方面的预防措施,确保连铸坯的质量,从而减少轧制后成品型钢表面龟裂缺陷.【期刊名称】《安徽冶金科技职业学院学报》【年(卷),期】2019(029)003【总页数】4页(P28-31)【关键词】龟裂;型钢;化学成分;预防措施【作者】袁月【作者单位】马钢股份公司长材事业部安徽马鞍山 243000【正文语种】中文【中图分类】TG335.4轧制过程中常见的缺陷有多种,龟裂是轧件常见缺陷中较为典型的一种。
龟裂是因裂纹在轧件上的宏观外形呈龟壳网络状态分布而得名,但是一种表面裂纹,深度较浅。
此种缺陷的产生都与钢坯的化学成分、铸坯条件及轧制过程控制有关。
本文以型钢表面龟裂为研究对象,探究其形成原因,并根据缘由提出相应的预防改进措施。
1 连铸坯与轧件裂纹形貌1.1 连铸坯裂纹形态及分类连铸坯裂纹常见位置分布及分类如图1所示。
1.2 轧件裂纹形态由图1.2可看出,龟裂裂纹出现频率较高的部位为角钢腿部、槽钢腹板表面。
图片均为成品角钢和槽钢,根据表面裂纹的深度,可以判断,在轧制过程中裂纹一直伴随存在。
图1 连铸坯裂纹位置及分类图2 角钢、槽钢龟裂形貌2 影响龟裂形成的因素2.1 化学成分研究表明,钢水的化学成分, 特别是当中的碳、硫、磷、锰等元素对铸坯及轧后成品的表面质量有显著的影响。
2.1.1 碳含量在碳钢中,碳含量对钢的热裂纹敏感性影响较大。
碳含量越高,轧制温度范围越窄,且钢的塑性越差。
含碳量过高,钢中会析出自由渗碳体和莱氏体,从而使钢的塑性下降,导致裂纹的产生。
2.1.2 硫含量硫元素对钢的热裂纹敏感性影响显著。
硫在钢中以FeS的形式存在,然而FeS和Fe易形成熔点较低(仅有985℃)的共晶体,当钢在1100~1200℃进行轧制时, 分布于晶界的低熔点共晶体固熔化而导致开裂,出现S的“热脆”现象。
高碳钢连铸方坯中心偏析

高碳钢连铸方坯中心偏析薛正良李正邦张家雯摘要:综述了高碳钢连铸方坯中心偏析的成因和控制方法,分析了电磁搅拌和接近液相线温度的低过热度浇铸技术对消除或改善高碳钢连铸方坯中心偏析的作用和效果。
指出低过热度浇铸和二次水膜强化冷却是解决高碳钢连铸方坯中心偏析的有效途径,并可提高拉坯速度。
关键词:连铸坯中心偏析高碳钢低过热度Centerline Segregation in Continuous Cast High-Carbon SteelBilletXue Zhengliang Li Zhengbang Zhang Jiawen(Center Iron & Steel Research Institute)Abstract:The formation mechanism and control technology of centerline segregation in continuous cast high-carbon steel billets are reviewed in this paper.The effects of electromagnetic stirring and low surperheat casting at near liquidus temperature on eliminating or improving the centerline segregation in high-carbon steel billets are also analyzed.It is put forward that casting at near liquidus temperature and internsive secondary cooling are the effective way to solve the centerline segregation in continuous casthigh-carbon steel billets,which also can increase casting speed. Keywords:continuous cast billet centerline segregation high-carbon steel low superheat▲中心偏析是连铸坯中最常见的宏观缺陷,由于它不能通过后续的轧制或退火处理来消除,因而对材料的机械性能和加工性能产生有害的影响。
连铸过程电磁搅拌下钢液温度场的数值模拟

连铸过程电磁搅拌下钢液温度场的数值模拟夏莉;姚寿广【摘要】利用ANSYS5.6软件对连铸过程中线性电磁搅拌器作用下钢液内流场及温度场进行数值模拟,结果表明:电磁搅拌的作用加强了钢液内部换热,使得铸坯内温度梯度减小,过热度迅速消失,液相穴变宽、变浅.这为液相穴内生成大量晶核提供了条件,并且有利于晶核最终发展成致密的等轴晶组织.【期刊名称】《江苏科技大学学报(自然科学版)》【年(卷),期】2005(019)001【总页数】4页(P73-76)【关键词】连铸;电磁搅拌;流场;温度场;数值模拟【作者】夏莉;姚寿广【作者单位】江苏科技大学,机械与动力工程学院,江苏,镇江,212003;江苏科技大学,机械与动力工程学院,江苏,镇江,212003【正文语种】中文【中图分类】TG2490 引言在钢铁业界,随着对钢材产品加工性能、强度、抗疲劳性能以及韧性、耐腐蚀性等各方面性能指标的要求不断提高,生产高洁净度、高均匀性和具有超细组织的高品质钢材已成为钢铁生产者面临的新任务。
连铸电磁搅拌技术通过电磁感应产生的电磁力驱动钢液的流动,以改善钢液凝固过程中的传热和传质条件,从而有利于铸坯内等轴晶凝固组织的形成;同时在改善铸坯的表面质量及皮下质量,减轻中心偏析及中心疏松等内部缺陷方面也有显著的作用[1~3]。
凝固过程中温度场影响到了钢液的形核率与晶粒的生长形态,对温度场的控制有利于获得最佳的凝固组织,但以往对这方面所作的研究却很少。
本文针对连铸二冷区单侧线性搅拌作用下铸坯内温度场进行数值模拟,探讨搅拌对铸坯内温度场的影响及作用规律。
1 数学模型对于连铸板坯且忽略搅拌器端部绕线时,可将问题简化为二维模型。
1.1 电磁场基本方程描述电磁场的Maxwell方程组:( 1 )( 2 )·B=0( 3 )描述材料电磁特性的本构方程:B=μH( 4 )J=σ[E+v×B]( 5 )采用磁矢势法对搅拌器的谐波电磁场进行数值模拟。
大方坯轴承钢中心偏析的成因及预防措施

第44卷 第8期 2009年8月钢铁Iron and Steel Vol.44,No.8August 2009大方坯轴承钢中心偏析的成因及预防措施何庆文1,2, 王 宝1, 王福明1, 刘 青1(1.北京科技大学冶金与生态工程学院,北京100083; 2.莱芜钢铁股份有限公司特殊钢厂,山东莱芜271105)摘 要:对莱钢特钢厂连铸生产的大方坯轴承钢中心偏析的成因进行分析,研究了中间包钢水过热度等因素对中心偏析的影响,并对莱钢特钢厂的生产实践提出了预防措施。
改善连铸轴承钢的中心偏析的方法和途径有:降低和稳定过热度,合理选择拉速、二冷强度和电磁搅拌参数等。
关键词:轴承钢;方坯;中心偏析;预防措施中图分类号:TF762+.4,TF777.2 文献标识码:A 文章编号:04492749X (2009)0820039203C ause and Preventive Measure for CentralSegregation of B earing Steel B loomH E Qing 2wen 1,2, WAN G Bao 1, WAN G Fu 2ming 1, L IU Qing 1(1.Metallurgical and Ecological Engineering School ,University of Science and Technology Beijing ,Beijing 100083,China ; 2.Special Steel Plant ,Laiwu Iron &Steel Co.,Ltd.,Laiwu 271105,Shandong ,China )Abstract :The reasons of central segregation of 260mm ×300mm bearing steel bloom have been analyzed ,and the effects of superheat and other factors on central segregation have been investigated.Based on the analysis ,some countermeasures to prevent central segregation have been implemented according to the practice in Special Steel Plant of Laiwu Iron and Steel Co.,Ltd.Technologies which is used to induce the center segregation contain lowering and stabilizing superheat ,choosing reasonably casting speed ,intensity of secondary cooling water and the parameters of electromagnetic stirring and so on.K ey w ords :bearing steel ;bloom ;central segregation ;preventive measure作者简介:何庆文(19682),男,博士生,高级工程师; E 2m ail :lghqw @ ; 修订日期:2008212216 莱钢特钢厂轴承钢生产流程为:50t U HP 2EA F (铁水热装比大于50%)+50t L F +60t VD 真空脱气+3机3流大方坯全弧形合金钢连铸机+铸坯入坑缓冷、部分连铸坯直接热送轧制成材。
管线钢连铸坯中心偏析分析与探讨

管线钢连铸坯中心偏析分析与探讨近年来,随着石油、天然气等脆弱资源的不断消耗,地球环境的持续恶化以及人类活动的日益增加,越来越多的人开始重视环境保护,而管线钢的应用正是维护环境的必要手段之一。
它的承载能力大、耐腐蚀性强,且可以连铸出大小规格、各种不同形状的钢材,成为各行各业的首选材料。
然而,连铸的生产过程也会产生偏析现象,造成连铸外形和钢料物性的偏离,严重地影响着生产效率和质量。
因此,深入研究管线钢连铸坯中心偏析现象对于管线钢的生产有着重要意义。
管线钢连铸坯中心偏析是指在管线钢连铸过程中,将钢水放入带有内部凹槽的连铸坯后,出现不均匀的坯料径向流动和分布现象。
这一现象会使得管线钢的外形及其材料物性受到影响,甚至可能影响管线钢的安全运行。
所以,对管线钢连铸坯中心偏析现象的深入分析及探讨,有助于合理改善管线钢的生产工艺,减少生产成本,同时提高整体的质量控制。
在管线钢连铸坯中心偏析研究方面,研究者采用了实验测试、模拟计算和数据分析等方法。
例如,通过仿真分析和实验室研究,对坯料偏析现象的影响因素进行了研究,如:连铸坯的凹腔几何参数、加料位置、充型状态等。
以及坯料偏析现象发生的条件、规律和动力学过程。
进一步,模拟计算和数据分析技术还被用于分析不同熔炼技术、温度等因素与坯料偏析现象之间的关系,并且提出更好的熔炼技术进行优化,以减少或消除管线钢连铸坯中心偏析现象。
此外,在实际生产中,操作工艺参数也可以改善坯料偏析现象。
例如,在放料时减少管口宽度,可以减少坯料运动速度,而减小注入水量,可以降低坯料表面温度。
此外,可以采用椭圆形或弯折形注入管,以改变坯料运动趋势,减少坯料偏离中心线;还可以通过减少蒙皮厚度、改变放料管管口角度等方式减少偏析。
另外,增加护函的厚度,也可以改善坯料的流动和偏析现象。
根据研究结果,运用椭圆形或弯折形注入管、减少管口宽度、改变放料管管口角度等操作参数,可以改善管线钢连铸坯中心偏析现象。
而采用仿真分析和实验室研究,对坯料偏析现象的影响因素进行研究的数据分析,也可以解决偏析现象,进而提高管线钢的生产效率。
连铸板坯动态轻压下辊缝偏差研究
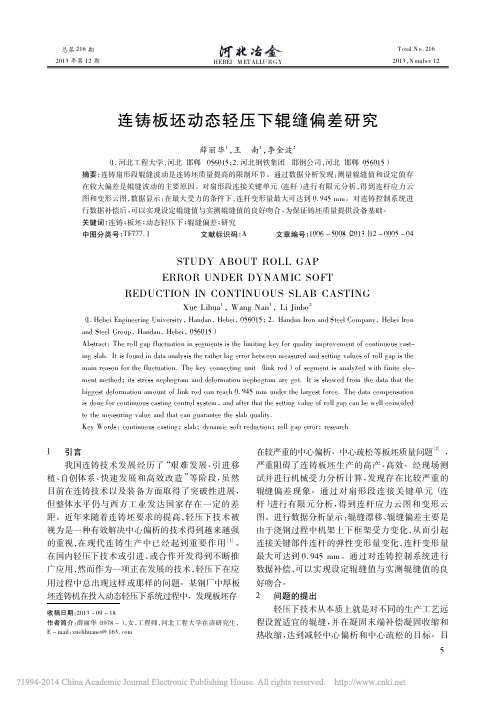
总第216期2013年第12期HEBEI M ET ALLU RGYT otal N o.2162013,N umber 12收稿日期:2013-09-18作者简介:薛丽华(1978-),女,工程师,河北工程大学在读研究生,E -mail :xuelihuanet@163.com连铸板坯动态轻压下辊缝偏差研究薛丽华1,王南1,李金波2(1.河北工程大学,河北邯郸056015;2.河北钢铁集团邯钢公司,河北邯郸056015)摘要:连铸扇形段辊缝波动是连铸坯质量提高的限制环节。
通过数据分析发现:测量辊缝值和设定值存在较大偏差是辊缝波动的主要原因。
对扇形段连接关键单元(连杆)进行有限元分析,得到连杆应力云图和变形云图,数据显示:在最大受力的条件下,连杆变形量最大可达到0.945mm 。
对连铸控制系统进行数据补偿后,可以实现设定辊缝值与实测辊缝值的良好吻合,为保证铸坯质量提供设备基础。
关键词:连铸;板坯;动态轻压下;辊缝偏差;研究中图分类号:TF777.1文献标识码:A文章编号:1006-5008(2013)12-0005-04STUDY ABOUT ROLL GAPERRORUNDERDYNAMIC SOFTREDUCTION IN CONTINUOUS SLAB CASTINGXue Lihua 1,Wang Nan 1,Li Jinbo 2(1.Hebei Engineering University ,Handan ,Hebei ,056015;2.Handan Iron and Steel Company ,Hebei Iron and Steel Group ,Handan ,Hebei ,056015)Abstract :The roll gap fluctuation in segments is the limiting key for quality improvement of continuous cast-ing slab.It is found in data analysis the rather big error between measured and setting values of roll gap is the main reason for the fluctuation.The key connecting unit (link rod )of segment is analyzed with finite ele-ment method ;its stress nephogram and deformation nephogram are got.It is showed from the data that the biggest deformation amount of link rod can reach 0.945mm under the largest force.The data compensation is done for continuous casting control system ,and after that the setting value of roll gap can be well coincided to the measuring value and that can guarantee the slab quality.Key Words :continuous casting ;slab ;dynamic soft reduction ;roll gap error ;research1引言我国连铸技术发展经历了“艰难发展、引进移植、自创体系、快速发展和高效改造”等阶段,虽然目前在连铸技术以及装备方面取得了突破性进展,但整体水平仍与西方工业发达国家存在一定的差距。
连铸坯中心偏析和疏松缺陷在轧制过程中的形态演化

连铸坯中心偏析和疏松缺陷在轧制过程中的
形态演化
嘿,朋友!咱今儿来聊聊连铸坯中心偏析和疏松缺陷在轧制过程中的形态演化这事儿。
您想想啊,这连铸坯就好比是一块还没雕琢好的璞玉,里面存在着中心偏析和疏松这样的小毛病。
那在轧制过程中,它们会发生啥样的变化呢?
先说这中心偏析,它就像是藏在蛋糕中心不均匀分布的水果粒儿。
在轧制的时候,受到强大的压力和热力作用,原本不均匀的成分分布会变得更加复杂。
原本集中在一处的元素,可能会被挤来挤去,导致材料的性能变得不稳定。
这难道不像是一场混乱的“分子搬家”吗?
再说说疏松缺陷,它就像是一块海绵里的空洞。
轧制的时候,这些空洞可不会乖乖待着,它们会被压缩、变形。
但要是处理不好,这些空洞可能还会相互连接,形成更大的缺陷,就像小水滴汇聚成了大水流一样,那可就麻烦啦!
您可能会问,这对最终的产品质量影响有多大呢?那可真是不容小觑!中心偏析可能会让钢材的强度和韧性大打折扣,疏松缺陷则可能让材料变得容易断裂。
这就好比一辆汽车,要是零部件质量不过关,跑在路上能让人放心吗?
那怎么解决这些问题呢?这就得从源头抓起,优化连铸工艺,控制好冷却速度和温度,尽量减少中心偏析和疏松缺陷的产生。
在轧制过程中,合理调整轧制参数,给这些缺陷来个“大改造”。
总之,连铸坯中心偏析和疏松缺陷在轧制过程中的形态演化可不是小事,咱们得重视起来,才能生产出高质量的产品,您说是不是这个理儿?。
宽厚板连铸坯中心偏析的产生原因及控制

关键词 : 低碳微合金钢 ; 板坯 ; 内部缺 陷
中 图分 类 号 :f 7 . T’ 7 1 7 文 献 标 识 码 : B 文 章 编 号 :09— 4 8 2 1 ) 1 0 1 10 5 3 (0 0 O — 0 5—0 3
Ca e nd Co t o n Ce t r Se r g to o ntnu u us sa n r lo n e g e a i n f r Co i o s Ca tng Bi e so i e a si l t fW d nd Thik Plt s l c ae
内部存 在 中心偏 析 、 中心疏 松 等质量 缺 陷 , 响 了产 影 品 的性 能 。
2 , 括 N 、 T、 、r 合 金 元 素 。该 钢 种典 % 包 bV、iMo C 等
型成分 范 围见表 1 。
奏 鱼塑堡壁丝鱼垒塑重量坌墼
C
。
S i
。
Mn
 ̄5 2
P
第3 6卷第 1 期
21 0 0年 o . 6, . F bur 2 1 e r ay, 0 0
S in e a d T c n lg fB o o t e ce c n e h o o y o a tu S e l
宽 厚板 连铸 坯 中心偏 析 的产 生 原 因及 控 制
S
b
Al I
。0 % ‘2
Al
 ̄2 00 02 l
-
(o 0 0 (o o 2。 0 5 .2 _l 00 .2 .
 ̄
~
 ̄
l4 l5
3 5
D05 .3
3 2
1 包 钢低 碳 微 合 金 钢 成 分及 工 艺 路 线 1 2
中心偏析原因_危害_评定及预防_上_
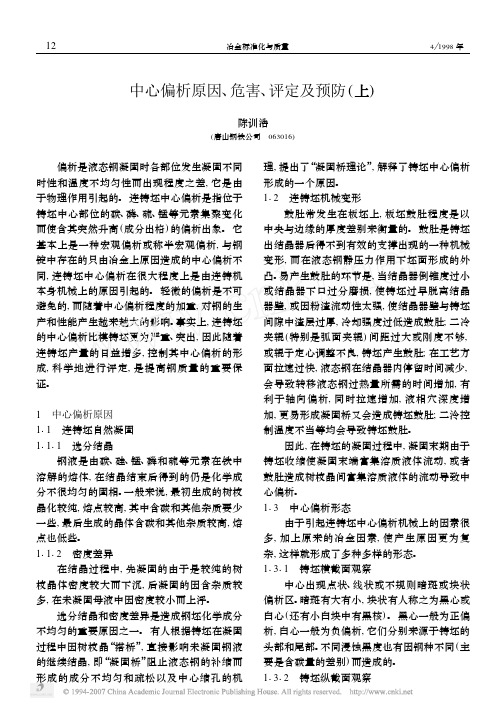
对后一个标准, 描述中心偏析的形貌特征 为: 铸坯硫印图的中心区域内有颜色深浅不一 的褐斑或集中的褐带, 褐带呈连续和不连续两 种。 原则依照该标准附录 A 提供的第一评级 图, 以偏析类型、偏析带厚度或偏析斑点大小评 定。评级图, 是 A、B、C3 类组成, A 类评级见表 1, B 类评级见表 2, C 类评级见表 3。 再在相应 产品标准的技术条件 (不少标准笼统称为偏析, 希望修订时给予明确, 以适应连铸坯的需要) 中, 查出规定的合格级别来判定产品是否合格。
若用有明显中心偏析的钢材做成钻头, 还 会形成对钻头极为不利的粗柱晶结构。 在使用 中裂纹沿晶界发展, 该结构导致崩牙。有资料说 明, 使用寿命可能缩短到正常的 1 20 至 1 7。 21212 使钢材出现各向异性
中心偏析在板坯的纵向和宽度方向上的分 布有很大变化, 中心偏析在宽度方向的分布与 冷状态下板厚有关, 这使钢中的化学成分出现 很不均匀状态, 导致力学性能各向异性, 特别是 由于M nS 在中心偏析带内聚集, 使成品钢板沿 厚度方向的力学性能变坏。 但是对于低硫钢来 说, 这种影响就不大了。 21213 降低钢材韧性
1 中心偏析原因 111 连铸坯自然凝固 11111 选分结晶
钢液是由碳、硅、锰、磷和硫等元素在铁中 溶解的熔体, 在结晶结束后得到的仍是化学成 分不很均匀的固相。一般来说, 最初生成的树枝 晶化较纯, 熔点较高, 其中含碳和其他杂质要少 一些, 最后生成的晶体含碳和其他杂质较高, 熔 点也低些。 11112 密度差异
含夹杂物和疏松缺陷的车轮材料疲劳性能对比研究

Journal of Mechanical Strength2023,45(4):820-825DOI :10.16579/j.issn.1001.9669.2023.04.009∗20211108收到初稿,20211214收到修改稿㊂∗∗王朝瀚,男,1996年生,安徽芜湖人,汉族,西南交通大学轨道交通运载系统全国重点实验室硕士研究生,主要研究方向为车轮与车轴材料的疲劳与断裂㊂∗∗∗鲁连涛(通信作者),男,1965年生,黑龙江佳木斯人,汉族,西南交通大学轨道交通运载系统全国重点实验室研究员,主要研究方向为材料与结构的疲劳与断裂㊂含夹杂物和疏松缺陷的车轮材料疲劳性能对比研究∗COMPARATIVE STUDY ON FATIGUE PROPERTIES OF WHEEL MATERIALS CONTAINING INCLUSIONS AND SHRINKAGE DEFECTS王朝瀚∗∗㊀徐㊀田㊀曾东方㊀鲁连涛∗∗∗(西南交通大学轨道交通运载系统全国重点实验室,成都㊀610031)WANG ZhaoHan ㊀XU Tian ㊀ZENG DongFang ㊀LU LianTao(State Key Laboratory of Rail Transit Vehicle System ,Southwest Jiaotong University ,Chengdu 610031,China )摘要㊀通过超声波探伤确定缺陷在CL65车轮轮辋中的位置,取出了含有缺陷的毛坯试样,并加工成疲劳试样㊂在岛津电液伺服疲劳试验机上进行疲劳试验,获得含缺陷试样的疲劳寿命,并分析了缺陷的形状㊁尺寸与化学成分㊂结果表明,疏松缺陷的主要成分为MnS,夹杂物缺陷的主要成分为硬质氧化物,含疏松缺陷试样的疲劳寿命高于含夹杂物缺陷试样㊂结合镶嵌应力理论建立有限元模型,分析了两种缺陷对车轮材料疲劳性能影响的差异㊂与夹杂物缺陷相比,疏松缺陷和基体界面上的镶嵌应力显著降低,缺陷周围应力集中程度小㊂因此,含MnS 疏松对车轮材料疲劳性能的危害程度明显小于氧化物夹杂㊂关键词㊀夹杂物缺陷㊀疏松缺陷㊀硫化锰㊀硬质氧化物㊀镶嵌应力中图分类号㊀TG142Abstract ㊀The location of the defect in the CL65wheel rims was determined by ultrasonic detection,and workblanksamples containing the defect were taken out and processed into fatigue samples.Through the fatigue test carried out on Shimadzu electro-hydraulic servo fatigue testing machine,the fatigue life of samples with defects was obtained.After the test,the shape,size and chemical composition of defects were analyzed.The results show that the main component of shrinkage defects is MnS and the main component of inclusion defects is hard oxides.The fatigue life of samples with shrinkage defects is longer than that of samples with inclusion defects.To analyze the difference between the influence of the two defects on the fatigue properties of wheel materials,the finite element models were established based on the tessellated stress pared with inclusion defects,the tessellated stress at the interface between shrinkage defects and the matrix is significantly reduced and the extent of stress concentration around defects is small.Therefore,the damage of shrinkage defects containing MnS on the fatigue propertiesof wheel materials is significantly less than that of oxide inclusions.Key words㊀Inclusion defects ;Porosity defects ;Manganese sulfide ;Hard oxides ;Tessellated stress Corresponding author :LU LianTao ,E-mail :luliantao @ ,Tel :+86-28-86466025,Fax :+86-28-86466025Manuscript received 20211108,in revised form 20211214.0㊀引言㊀㊀车轮钢在冶炼过程中不可避免地会引入缺陷,其中夹杂物和疏松是两种主要的缺陷形式㊂夹杂物和疏松是物理特征明显不同的两种缺陷,研究两种缺陷对车轮钢疲劳性能影响的差异,有助于合理区别处理这两种缺陷引起的车轮探伤报警㊂现有研究观察了钢材中疏松和夹杂物的形貌,分析了疏松和夹杂物形成的原因㊂其中夹杂物常见的成因有结晶器造成的卷渣夹杂和钢渣反应生成的内生夹杂,疏松的形成则受到钢液中气体和夹杂物的综合影响[1]㊂通常中心偏析与疏松伴随发生,由于中心偏析的存在,在产生疏松的区域容易形成MnS㊂P㊁S 等非金属元素含量的影响㊁钢水过热度和拉坯速度频繁变化等都会导致中心偏析和疏松的出现[2]㊂在研究疏松缺陷的影响时,李永奎等[3]发现,淬火热处理使得车轮材料疏松缺陷周围的周向残余应力过大,并在外载的叠加作用下,裂纹萌生并扩展㊂㊀第45卷第4期王朝瀚等:含夹杂物和疏松缺陷的车轮材料疲劳性能对比研究821㊀㊀ZENG等[4]在对车轮材料进行超声疲劳测试后发现,疲劳破坏萌生于内部含有MnS缺陷的鱼眼区域,并且在极端载荷下即使车轮材料踏面以下深部也可能由微观缺陷引发疲劳破坏㊂关于夹杂物缺陷的影响,由于夹杂物缺陷与材料基体的性能差异很大,破坏了基体的均匀性和连续性,因此在热处理和变形中容易引发应力集中,甚至成为裂纹源或促进裂纹扩展[5-7]㊂大量研究证明,车轮材料不可避免地会引入大量微观夹杂和少量宏观夹杂,微观夹杂可引起车轮踏面下的浅层剥离,宏观夹杂可引起车轮踏面以下深处辋裂[8][9]45-54[10-13]㊂米国发等[14]应用Goodier方程分析了夹杂物周围的应力状态,分析表明,氧化铝夹杂物尖角处的应力集中将造成夹杂物与基体脱开,或使夹杂物本身破裂从而形成空穴,在此处产生裂纹㊂魏华成等[15]则发现,当氧化物夹杂的尺寸和长宽比较大时夹杂物内部所受的应力状态较复杂,其将对车轮的使用寿命产生一定的影响㊂以往的研究分析了疏松缺陷和夹杂物缺陷对车轮材料性能的影响,但是目前关于疏松缺陷与夹杂物缺陷对车轮材料疲劳性能影响差异的机制尚不清楚㊂为了合理处理含不同缺陷的车轮,本文开展了含夹杂物和疏松缺陷车轮材料疲劳性能的对比研究㊂本研究通过超声波探伤确定缺陷在CL65车轮轮辋的位置,取出含有缺陷的毛坯试样,加工成疲劳试样,并进行疲劳试验,确定试样的缺陷种类和疲劳寿命㊂然后,结合镶嵌应力理论建立有限元模型,分析两种缺陷对车轮材料疲劳性能影响的差异㊂1㊀试验材料与试验方法1.1㊀取样㊀㊀使用超声波探伤设备对判废CL65车轮中缺陷的位置进行准确定位,发现缺陷集中于距离车轮踏面25~75mm,车轮端面20~60mm的区域内㊂通过机加工从车轮轮辋中取出含有缺陷的毛坯试样,并标注出缺陷在毛坯试样中的位置㊂1.2㊀热处理㊀㊀疏松缺陷和夹杂物缺陷在轮辋中的分布位置不同,导致两类缺陷周围材料的组织㊁力学性能等存在差异,为了在相同条件下对比两种材料的疲劳性能,本文对含疏松缺陷和夹杂物缺陷的毛坯试样进行热处理,使两种试样具有相同的组织和力学性能㊂由于毛坯试样的形状和尺寸不同,为了保证所有试样的热处理条件一致,将所有毛坯试样均加工成厚度10.5mm的含缺陷板状试样㊂参考实际车轮的热处理条件,含缺陷板状试样的热处理条件设定为875ħ,保温1.5h,空冷㊂热处理后,大部分试样的硬度介于280~300HV㊂1.3㊀表面处理㊀㊀虽然超声波探伤检测到的缺陷尺寸较大,但是如果直接对机加工后的试样进行疲劳试验,试样还是容易从表面发生疲劳破坏[9]45-54㊂为了增加试样从内部缺陷发生疲劳破坏的概率,对机加工后的试样进行微粒子喷丸表面强化处理㊂使用300目钢丸(平均直径约50μm),喷射压力为0.6MPa,喷射距离为150mm,覆盖率为200%㊂处理后的疲劳试样如图1所示㊂试样为平板结构,板厚约8mm,中间等截面段部分的长度约为15mm,宽度约为8mm㊂试样具体尺寸因缺陷位置和毛坯试样形状尺寸的差异而存在变化㊂缺陷位于试样中间的等截面段部位㊂图1㊀微粒子喷丸处理后的疲劳试样Fig.1㊀Fatigue specimen after the particle peening1.4㊀试验方法㊀㊀使用日本岛津电液伺服疲劳试验机进行试验,试验安装如图2所示㊂将疲劳试样安装在试验机上㊁下液压夹具之间,对试样施加应力比R=0.05的拉伸载荷,加载频率f为20Hz,加载波形为正弦波,试验初始最大应力设定为350MPa㊂若在350MPa的条件下施加100万周次的循环载荷后,试样未发生疲劳失效,则进行逐级升载试验㊂载荷间隔25MPa,作用次数50万次,直至试样断裂㊂图2㊀试样安装Fig.2㊀Installation of specimen2㊀试验结果2.1㊀缺陷分析㊀㊀如图3和图4所示,所有试样均发生源于内部缺㊀822㊀机㊀㊀械㊀㊀强㊀㊀度2023年㊀陷的疲劳失效㊂为了确定缺陷成分,用带有能谱仪(Energy Dispersive Spectroscopy,EDS)的扫描电镜对疲劳断口上的缺陷进行分析,结果如表1所示㊂表1中1~3号试样中缺陷富含Mn㊁S 等元素,缺陷种类为含MnS 的疏松缺陷,典型的扫描电子显微镜(Scanning Electron Microscope,SEM)图像及EDS 分析结果如图3所示㊂4~6号试样中的缺陷主要含有Al㊁O 等元素,缺陷种类为以Al 2O 3为主的氧化物夹杂,典型的SEM 图像及EDS 分析结果如图4所示㊂对比图3(b)和图4(b)可以看出,含MnS 的疏松缺陷表面光滑,且MnS 呈现片层状;氧化物夹杂表面则较为粗糙,表面分布着颗粒状的Al 2O 3㊂图3㊀含MnS 疏松缺陷试样Fig.3㊀Specimen containing MnS porositydefects图4㊀含氧化物夹杂缺陷试样Fig.4㊀Specimen containing oxide inclusion defects表1㊀疲劳试验观测结果Tab.1㊀Results of fatigue test试样编号No.缺陷尺寸Defect size /mm缺陷种类Defect type循环周次Cycle times 失效载荷Failure load /MPa10.820疏松Shrinkage 181045040020.464疏松Shrinkage 86155035030.428疏松Shrinkage186498040040.864氧化物夹杂Oxide inclusion 75500435050.766氧化物夹杂Oxide inclusion 64121235060.395氧化物夹杂Oxide inclusion897460350㊀㊀采用Murakami 的缺陷尺寸测定方法,将A (A 为裂纹在应力方向上的投影面积)作为缺陷的等效尺寸[16],测量结果见表1㊂疏松缺陷的等效尺寸介于0.42~0.82mm 之间,夹杂物缺陷的等效尺寸介于0.39~0.87mm 之间㊂可见,本文所观测的两类缺陷的尺寸基本相同㊂2.2㊀疲劳寿命㊀㊀如表1所示,在初始应力350MPa 的条件下,除了1号和3号试样外,其余试样的疲劳寿命均小于100万周次㊂1号和3号试样在350MPa 的条件下施加100万周次的疲劳载荷后,试样未发生疲劳失效㊂在逐级升载试验中,1号试样在375MPa 载荷作用下50万次,400MPa 载荷作用下约31万次后发生疲劳失效;3号试样在375MPa 载荷作用下50万次,400MPa 载荷作用下约36万次后发生疲劳失效㊂两件试样的总循环周次分别为1810450和1864980㊂因此,在缺陷尺寸差别不大的情况下,含疏松缺陷试样的疲劳强度高于含夹杂物缺陷试样㊂可见,疏松缺陷对车轮材料疲劳性能的危害小于夹杂物缺陷㊂㊀第45卷第4期王朝瀚等:含夹杂物和疏松缺陷的车轮材料疲劳性能对比研究823㊀㊀3㊀缺陷种类对疲劳性能的影响机制研究㊀㊀现有的研究发现,缺陷与材料基体之间刚度的差异会对裂纹的萌生与扩展产生干涉[17],并且裂纹萌生的概率会伴随缺陷与基体刚度差异的增大而上升[18]㊂缺陷与基体界面上的镶嵌应力也会在缺陷位置造成应力集中,降低材料疲劳强度[19]㊂本文建立了疲劳试验条件下含缺陷试样的有限元模型,从缺陷在刚度和镶嵌应力差异的角度,对比研究夹杂物和疏松缺陷对车轮材料疲劳性能的影响㊂3.1㊀有限元模型㊀㊀有限元模型考虑了两种材料缺陷:Al 2O 3夹杂物缺陷和含MnS 的疏松缺陷㊂为了研究两种缺陷在拉伸载荷作用下局部应力场的差异,本文分别在单轴拉伸试样的心部植入材料缺陷,并在计算中将缺陷理想化为球形,球体的直径统一为0.1mm㊂试样基体与缺陷的材料参数如表2所示㊂表2㊀试样基体与缺陷的材料参数Tab.2㊀Material parameters of matrix and defects材料Material 热膨胀系数Thermal expansioncoefficient αM /(10-6ħ-1)弹性模量Elastic modulus E M /GPa 泊松比Poissonᶄs ratioυMAl 2O 3夹杂物Al 2O 3inclusion 83900.25含MnS 的疏松Shrinkage containing MnS 181030.30基体Matrix14.82100.29因为缺陷的尺寸远小于试样,在单轴拉伸的加载条件下,缺陷周围的应力状态与试样外围的形状无关,所以将试样中间等截面段简化为棒状㊂又考虑到模型中边界条件和载荷的对称性,本文仅建立含缺陷的1/8对称单轴拉伸试样有限元模型,并在相应的对称面上施加对称约束,通过在试样的夹持端施加均匀的分布载荷实现拉伸加载,最终建立的有限元模型如图5所示㊂图5㊀含缺陷的单轴拉伸试样有限元模型Fig.5㊀Finite element model of uniaxial tensile specimen with defects3.2㊀镶嵌应力分布㊀㊀由于材料缺陷与基体间的热膨胀系数存在差异,在冷却过程中缺陷与基体之间会产生镶嵌应力,这是导致材料基体产生应力集中并萌生微裂纹的原因之一[20]978-983㊂因此,在本文有限元模型中考虑镶嵌应力对材料缺陷周围应力分布的影响㊂三维球形缺陷中的镶嵌应力通过温差法引入㊂温差法的实现原理为给缺陷和基体分别设定相应的热膨胀系数,随后通过在整个模型上施加温度载荷来引入热应变,则由该热应变引起的预应力可以看作是作用在缺陷和基体边界区域的镶嵌应力㊂取温度载荷为500ħ,即珠光体相变完成时温度与室温的温度差,由镶嵌应力计算公式得到硬质夹杂物表面的镶嵌应力为781MPa [20]982㊂施加温度载荷后硬质夹杂物表面的镶嵌应力分布如图6所示,与理论公式的计算结果一致㊂图6㊀硬质夹杂物表面的镶嵌应力分布云图Fig.6㊀Nephogram of tessellated stress distribution on thesurface of hard inclusions3.3㊀计算结果分析㊀㊀图7给出了当不考虑镶嵌应力时,在试验拉伸载荷(350MPa)作用下硬质夹杂物周围的轴向应力(S22)分布㊂由图7可知,在拉伸载荷作用下,夹杂物内部的应力分布是均匀的,而夹杂物与基体的界面处则存在明显的应力突变,这和夹杂物与基体之间的刚度不匹配有关㊂在远离夹杂物的区域,夹杂物对基体的影响将逐渐消除,基体的轴向应力值将逐渐趋近于试样的名义应力值㊂图7㊀硬质夹杂物局部轴向应力分布云图Fig.7㊀Nephogram of local axialstress distribution about hard inclusion由于图7中夹杂物与基体界面上的轴向应力存在明显的应力梯度,因此将图7中的AB 段圆弧作为应㊀824㊀机㊀㊀械㊀㊀强㊀㊀度2023年㊀力提取路径,得到不同缺陷界面上沿路径AB 的轴向应力分布如图8所示㊂由图8可知,由于硬质夹杂物与基体相比刚度偏大,而疏松与基体相比刚度偏小,因此硬质夹杂物和疏松沿界面的轴向应力分布存在明显的差异,且硬质夹杂物界面上的轴向应力的最大值要略大于疏松界面上轴向应力的最大值㊂图8㊀缺陷沿界面的轴向应力分布(无镶嵌应力)Fig.8㊀Axial stress distribution of defects along theinterface(without tessellated stress)图9给出了在考虑镶嵌应力之后,不同缺陷界面的轴向应力分布㊂由图9可知,硬质夹杂物界面上的轴向应力分布变化趋势更明显,最大值达到了587MPa㊂当单轴拉伸试样中存在疏松缺陷时,相比于硬质夹杂物,疏松与基体界面处的轴向应力最大值要明显低于硬质夹杂物的轴向应力最大值,这主要是由于疏松缺陷的热膨胀系数高于基体的热膨胀系数,在冷却过程中收缩程度大于基体,因此疏松缺陷周围不存在镶嵌应力㊂图9㊀缺陷沿界面的轴向应力分布(考虑镶嵌应力)Fig.9㊀Axial stress distribution of defects along theinterface(with tessellated stress)综上所述,缺陷刚度变化虽然会改变缺陷周围的轴向应力分布,但缺陷边界上的镶嵌应力对缺陷周围的应力水平变化的影响更大㊂与硬质夹杂物缺陷相比,疏松缺陷周围的镶嵌应力显著降低,轴向应力的最大值更小,因此疏松缺陷周围应力集中程度小,对车轮材料疲劳性能的危害程度较小㊂4㊀结论㊀㊀本文通过对从CL65车轮轮辋材料中加工出的试样进行疲劳试验,获得了试样的疲劳寿命和试样断口上的缺陷信息,并基于镶嵌应力理论建立有限元模型,分析了疏松缺陷和夹杂物缺陷对车轮材料疲劳性能的影响,得出结论:1)在缺陷尺寸相近的情况下,含疏松缺陷试样的疲劳寿命高于含夹杂物缺陷试样㊂2)缺陷刚度的差异改变了缺陷周围的轴向应力分布,但变化幅度明显要小于考虑镶嵌应力后的轴向应力分布,可见镶嵌应力是造成缺陷周围应力集中的重要因素㊂3)与夹杂物缺陷相比,疏松缺陷界面上的镶嵌应力显著降低,疏松缺陷周围应力集中程度小,因此疏松缺陷对车轮材料疲劳性能的危害程度小于夹杂物缺陷㊂参考文献(References )[1]㊀王㊀超,孙建设,张同方.轴承钢针孔状疏松成因分析及应对措施[J].山东冶金,2018,40(3):36-38.WANG Chao,SUN JianShe,ZHANG TongFang.Formation reasons and preventive measures of the pinhole general looseness in ball bearing steel[J].Shandong Metallurgy,2018,40(3):36-38(In Chinese).[2]㊀姚㊀桢,梁兆华,李全智,等.高碳钢连铸坯中心偏析的控制与改善[J].江西冶金,2011,31(1):1-4.YAO Zhen,LIANG ZhaoHua,LI QuanZhi,et al.Control and improvement of central segregation in high-carbon steel continuouscast billets [J ].Jiangxi Metallurgy,2011,31(1):1-4(In Chinese).[3]㊀李永奎,陈俊丹,陆善平.42CrMo 钢车轮锻件在淬火过程中的残余应力研究[J].金属学报,2014,50(1):121-128.LI YongKui,CHEN JunDan,LU ShanPing.Residual stress in the wheel of 42CrMo steel during quenching [J ].Acta MetallurgicaSinica,2014,50(1):121-128(In Chinese).[4]㊀ZENG D F,LU L T,ZHANG J W,et al.Effect of micro-inclusionson subsurface-initiated rolling contact fatigue of a railway wheel[J].Proceedings of the Institution of Mechanical Engineers,2016,230(2):544-553.[5]㊀ZHANG J,YANG J,JIANG T T,et al.On the mechanistic basis offatigue crack nucleation in Ni superalloy containing inclusions usinghigh resolution electron backscatter diffraction[J].Acta Materialia,2015(97):367-379.[6]㊀ZHANG T T,JIANG J,SHOLLOCK B A,et al.Slip localizationand fatigue crack nucleation near a non-metallic inclusion in polycrystalline nickel-based superalloy [J].Materials Science andEngineering A,2015(641):328-339.[7]㊀TAN J B,WU X Q,HAN E H,et al.Role of TiN inclusion oncorrosion fatigue behavior of Alloy 690steam generator tubes in borated and lithiated high temperature water[J].Corrosion Science,㊀第45卷第4期王朝瀚等:含夹杂物和疏松缺陷的车轮材料疲劳性能对比研究825㊀㊀2014,88:349-359.[8]㊀李雅洁,陈换过,蔡㊀丽,等.速度对含夹杂物动车车轮轮辋疲劳寿命影响的研究[J].机械强度,2019,41(3):707-712.LI YaJie,CHEN HuanGuo,CAI Li,et al.Study on the effect ofvelocity on the fatigue life of wheels rim containing inclusions[J].Journal of Mechanical Strength,2019,41(3):707-712(InChinese).[9]㊀EKBERG A,MARAIS J.Effects of imperfections on fatigue initiationin railway wheels[J].Proceedings of the Institution of MechanicalEngineers,Part F:Journal of Rail and Rapid Transit,2000,214(1):45-54.[10]㊀BERETTA S,DONZELLA G,ROBERTI R,et al.Contact fatiguepropagation of deep defects in railway wheels[C]ʊEuropeanConference on Fracture,2000.[11]㊀KABO E,EKBERG A.Fatigue initiation in railway wheels-Anumerical study of the influence[J].Wear,2002,253(1):26-34.[12]㊀KABO E,EKBERG A.Material defects in rolling contact fatigue ofrailway wheels-The influence of defect size[J].Wear,2005,258(7):1194-1200.[13]㊀EKBERG A,KABO E,NIELSEN J,et al.Subsurface initiatedrolling contact fatigue of railway wheels as generated by railcorrugation[J].International Journal of Solids and Structures,2007,44(24):7975-7987.[14]㊀米国发,刘彦磊,张㊀斌,等.夹杂物对轮辋裂纹萌生的影响[J].铁道学报,2010,32(4):108-113.MI GuoFa,LIU YanLei,ZHANG Bin,et al.Influence of inclusionon crack initiation in wheel-rim[J].Journal of the China RailwaySociety,2010,32(4):108-113(In Chinese).[15]㊀魏华成,张晓峰,李树林,等.KKD车轮热处理过程中车轮整体及夹杂物周围的残余应力分析[J].山西冶金,2019(5):48-49.WEI HuaCheng,ZHANG XiaoFeng,LI ShuLin,et al.Residualstress analysis of KKD wheel during heat treatment[J].ShanxiMetallurgy,2019(5):48-49(In Chinese).[16]㊀MURAKAMI Y.Metal fatigue:Effects of small defects andnonmetallic inclusion[M].Elsevier Science,2002:37-47. [17]㊀古㊀斌,郭宇立,李㊀群.基于构型力断裂准则的裂纹与夹杂干涉问题[J].力学学报,2017,45(6):1312-1321.GU Bin,GUO YuLi,LI Qun.Crack interacting with an individualinclusion by the fracture criterion of configurational force[J].Chinese Journal of Theoretical and Applied Mechanics,2017,45(6):1312-1321(In Chinese).[18]㊀ZHU M L,XUAN F Z.Fatigue crack initiation potential from defectsin terms of local stress analysis[J].Chinese Journal of MechanicalEngineering,2014,27(3):496-503.[19]㊀GU C,BAO Y P,GAN P,et al.Effect of main inclusions on crackinitiation in bearing steel in the very high cycle fatigue regime[J].International Journal of Minerals,Metallurgy and Materials,2018,25(6):623-629.[20]㊀马㊀跃,潘㊀涛,江㊀波,等.S含量对高速车轮钢断裂韧性的影响研究[J].金属学报,2011,47(8):978-983.MA Yue,PAN Tao,JIANG Bo,et al.Study of the effect of sulfurcontents on fracture toughness of railway wheel steels for high speedtrain[J].Acta Metallurgica Sinica,2011,47(8):978-983(InChinese).。
高强船板中心偏析产生的原因分析及预防措施

过 热度 、 恒定拉速 、 优化二冷配水 、 加大凝 固末端辊缝 收缩 量等措施 , 改善铸坯 内部 质量 , 取得 了 良好 效
果 , 强 船 板 断 口分 层 改 判 率 由原 来 的 3 0 % 下 降为 10 % 。 高 .9 .9 关键 词 : 中心 偏 析 ; 口分 层 ; 注 速 度 ; 次 冷 却 ; 缝 断 浇 二 辊
图 1 断 口分 层 图
2 0 年 邯 钢 公 司 三 炼 钢 厂 生 产 高 强 船 板 09 197 2t因质 量缺 陷改 判 69 7t其 中断 口分层 改 2 0 , 8 , 判 39 2t分 层改 判率 为 3 0 % 。 轧后 质 量 缺 陷分 6 , .5
中 图分 类 号 : G 3 . T 35 5 文 献 标 识 码 : B 文 章 编 号 :06— 0 8 2 1 )4—0 2 10 5 0 (0 1 0 0 4—0 4
REA S ON ANALYS S AND RECAUTI I P ONS FOR CENTRAL EGREGATI S ON OF GH — S HI TRENGTH HI S S P TEEL
05 01 6 5;2. Con iuo s tn u Ca tn a li il Ha a r n n S e lCo pa si g nd Ro l ng M l , nd n Io a d t e m ny, He e Io a e l b i r n nd Ste
( 、 北 钢铁 集 团 邯 钢 公 司 三 炼 钢 厂 , 北 邯 郸 0 6 1 ; 、 北 钢 铁 集 团 邯 钢 公 司 连 铸 连 轧 厂 , 北 1河 河 505 2河 河
邯郸 061 ) 50 5 摘 要 : 工 艺 及 设 备 两 个 方 面 分 析 中 心 偏 析 产 生 的 原 因 , 合 生 产 现 场 存 在 的 主 要 问 题 , 取 控 制 钢 水 从 结 采
高强钢连铸板坯中心偏析的分析及改善措施

高强钢连铸板坯中心偏析的分析及改善措施摘要:高强度钢一般含有高碳含量和锰质量分数。
连铸坯在凝固过程中容易形成碳、锰等元素的枝晶偏析,导致中厚板中心出现严重的带状组织缺陷。
带钢结构对钢板的力学性能、成形性和断裂性能有着重要的影响。
对于冷轧钢板,带钢结构的存在会使材料表现出很强的各向异性能,导致材料在深加工过程中发生不均匀变形,即沿板宽方向的纵向纤维拉伸不一致,导致二次变形。
即使是在应力集中时裂纹的萌生也会影响最终产品的性能。
如何减少和消除连铸坯在凝固过程中产生的偏析,是连铸生产亟待解决的问题。
基于此,本文对高强钢连铸板坯中心偏析的分析及改善措施进行分析。
关键词:连铸坯;中心偏析;改善措施1连铸坯中心偏析的成因导致连铸坯出现中心偏析的原因主要包括两个方面,一方面是枝晶搭桥形成了小钢锭,另一方面是发生了铸坯鼓肚的问题。
在连铸坯凝固过程中,液芯末端会存在一个固液两相混合组成的糊状区。
凝固过程中,钢液会收缩向坯壳和拉坯方向,最终形成小孔。
位于弯月面的钢液受到地心引力会注入到收缩形成的孔洞当中,通过这种方式可以有效防止疏松和偏析问题的出现。
上述为理想状态,但是在实际铸造过程中,由于出现了小钢锭,钢液难以及时形成収缩孔或者难以注入收缩控制红,最终导致偏析问题出现在铸坯中心部位。
通过偏析问题出现的过程分析可知,拉坯方向液芯中心线附近的钢液会在钢液凝固过程中出现一定的变化,前沿温度梯度不同是造成凝固波动的主要原因。
2板坯中心偏析的形成机制及控制措施对板坯偏析的形成机理进行了大量的研究。
可以看出,板坯的中心偏析是由凝固过程中溶质元素的分离和结晶和凝固结束附近富集的偏析元素的液流引起的。
凝固结束时的钢液流动是由壳体的鼓包和凝固过程中钢液的体积收缩引起的。
板坯的中心偏析与钢成分、热性能、几何形状、工艺参数和设备条件密切相关。
不同冷却条件下坯料枝晶间的应力对坯料的中心偏析也有重要影响。
因此,根据不同的情况,我们需要分析中心偏析的原因。
针布钢72NbV拉丝笔尖状断裂的研究分析

① 低过热度 浇注 , 低 过 热度 浇注 时 能生 成 等轴
晶网格 , 有效阻止柱状 晶生长 。 ② 电磁搅 拌 , 电磁搅拌可 以打断柱 状 晶, 为 等轴 晶 的形成提供核心 , 减少凝 固时的温度 梯度 , 从 而抑
f r a c t u r e e f f e c t i v e l y .
Ke y wor d s: 7 2Nb V ,c a r d wi r e;wi r e d r a wi n g;p e n - t i p s ha pe d f r a c t u r e; mi c r o — h a r dn e s s;mi c r o s t r uc t u r e
段对针布钢 7 2 N b V拉 丝 笔 尖 断 裂 试 样 的研 究 表 明 :
1 ) 针布 钢 7 2 N b V在轧 后外 观 正 常情 况 下 出现 拉丝笔尖状 断裂 现象 , 原 因是轧 后冷却 速 度较快 以 及 中心元素偏析 , 心部生成 M相 , 造成力学性能不均 匀, 在承受拉伸应力 时相界 面容易产 生微裂纹 , 随应 力持续 , 裂纹扩展 , 最终演变 为钢材表 面金属 塑性 断 裂, 中心金属脆性断 裂。
制 了柱 状 晶 的 生 长 。
替代 小 方 坯 轧 制 , 调整 轧制工 艺, 应 能 有 效 防 止 7 2 N b V钢拉丝 时笔 尖状断裂。
参 考 文献 :
[ 1 ] 马福 昌 , 刘永龙 , 宋瑞 甫等. N b , V, r r i 微 合金元 素
对 连 铸 坯 表 面 质量 的 影 响 . 宽厚板 , 2 0 0 3 ( 4 ) : 1 4 .
消除连铸板坯中心偏析技术

消除连铸板坯中心偏析技术
Hatt.,M;先越蓉
【期刊名称】《重钢技术》
【年(卷),期】1990(031)003
【总页数】7页(P20-25,33)
【作者】Hatt.,M;先越蓉
【作者单位】不详;不详
【正文语种】中文
【中图分类】TF777.1
【相关文献】
1.消除连铸板坯中心偏析与中心疏松的研究 [J], 宋世雄;任晨辉;查显文
2.消除连铸板坯偏析技术的开发 [J], Hatto.,M;杜游
3.梅钢精冲钢连铸板坯中心偏析控制技术与应用 [J], 于小春;倪修华
4.用轻压下技术改善连铸板坯中心偏析 [J], L.K.Chiang;苏平旺
5.应用轻压下浇铸技术改善连铸板坯的中心偏析 [J], T.Masaoka;王淑怀
因版权原因,仅展示原文概要,查看原文内容请购买。
77MnCr钢丝笔尖状断口形态的分析

77MnCr钢丝笔尖状断口形态的分析田庆荣;刘莹【摘要】某预应力钢丝生产厂在使用Φ12.5 mm的77MnCr盘条生产Φ7.0 mm 的螺旋肋预应力钢丝时,常在拉拔过程中发生断线的现象.针对该问题,利用光学显微镜、扫描电镜和能谱仪对77MnCr盘条在冷拉拔过程中产生笔尖状断口的断裂试样进行了系统检测和分析.检验结果表明,试样中心部位存在的“V”形裂纹是造成盘条在拉拔过程中产生断裂的裂纹源.经分析得出V形裂纹的形成与盘条心部存在的网状渗碳体有关,而网状渗碳体的产生与连铸坯中心偏析,尤其是碳偏析和盘条轧制过程中的冷却速度有着十分紧密的关系.【期刊名称】《天津冶金》【年(卷),期】2012(000)004【总页数】3页(P47-49)【关键词】77MnCr盘条;笔尖状断口;网状渗碳体;中心碳偏析【作者】田庆荣;刘莹【作者单位】天津钢铁集团有限公司技术中心,天津 300301;天津钢铁集团有限公司技术中心,天津 300301【正文语种】中文某预应力钢丝生产厂在使用Φ12.5mm的77Mn-Cr盘条生产Φ7.0mm的螺旋肋预应力钢丝时,常在拉拔过程中发生断线的现象,降低了生产节奏,给厂家的生产和经济效益带来很大的影响。
根据检查发现,在产生拉拔断线的断口形态中以笔尖状断口形貌最为普遍。
因此我们对发生断裂的钢丝过程线进行系统分析,找出笔尖转断口形态的形成机理,为提高产品质量提供改进措施。
产生拉拔断裂的钢丝断口形貌为笔尖状形态,即断口的一端为锥体,像一个笔尖,另一端为锥孔呈凹陷状(如图1所示)。
笔尖的尖头位置基本上是处于钢丝的中心部位。
这种断口没明显的有放射区,整个锥面都属于剪切唇。
取拉拔断裂试样进行化学成分检验,检验结果示该试样的碳含量为0.81%,已经超过了共析点成分,达到了过共析钢的成分范围。
其他元素的含量分别为Si:0.23%,Mn:0.68%,Cr:0.30%,P:0.015%,S:0.016%。
把笔尖状断口试样沿纵向截面剖开,经磨抛后在试样中心部位可以看到一串的V形裂纹,如图2(a)所示。
- 1、下载文档前请自行甄别文档内容的完整性,平台不提供额外的编辑、内容补充、找答案等附加服务。
- 2、"仅部分预览"的文档,不可在线预览部分如存在完整性等问题,可反馈申请退款(可完整预览的文档不适用该条件!)。
- 3、如文档侵犯您的权益,请联系客服反馈,我们会尽快为您处理(人工客服工作时间:9:00-18:30)。
备注
0 角部皮下气泡 5 个
0
1.5
1.5 有 4 mm×8 mm 缩孔
1.5
0 有皮下气泡 2 级
0 有皮下气泡 1 级
0
0
0
0
0
0
2 中心偏析与中心疏松形成原因 中心偏析是指钢液在凝固过程中,溶质元素在
固液相中进行再分配时,表现为铸坯中元素分布不 均匀,铸坯中心部位的 C、S、P 等元素含量明显高 于其它部位。在铸坯厚度中心凝固末端区域常表现 为“V”偏析。中心疏松是指钢液在凝固末期,在 铸坯厚度中心的枝晶间产生微小空隙。导致中心偏
轻压下技术,就是通过在连铸坯液芯末端附近 施加均匀外力,使铸坯产生一定的压缩量,以补偿 铸坯的凝固收缩量[5]。采用轻压下技术可消除或减 少铸坯收缩形成的内部空隙,防止晶间富集溶质元 素的钢液向铸坯中心横向流动;同时轻压下所产生 的挤压作用还可以促使液芯中富集溶质元素的钢 液沿拉坯方向反向流动,使溶质元素在钢液中重新 分配,从而使铸坯的凝固组织更加均匀致密,起到 改善中心偏析和减少中心疏松的作用[6]。
析和中心疏松产生的原因很多,且这两种缺陷往往 相伴而生。 2.1 铸坯凝固组织中柱状晶过于发达
中心偏析和中心疏松形成机理之一是“凝固 晶桥”理论,即铸坯凝固过程中,铸坯传热的不稳 定性导致柱状晶生长速度快慢不一,优先生长的柱 状晶在铸坯中心相遇形成“搭桥”,液相穴内钢液
2005 年第 2 期
钢铁技术
拉坯速度也是影响柱状晶生长的重要因素。拉 坯速度大,铸坯在结晶器内停留时间短,铸坯液芯 延长,这不但推迟了等轴晶的形核和长大,扩大了 柱状晶区,而且发生铸坯鼓肚的危险系数也增大。 因此,在不影响产量的前提下,拉坯速度不宜过大。 在生产实践中,需根据不同钢种在不同的操作模式 (如开始浇注、快速更换中间罐、快速更换浸入式 水口、更换结晶器保护渣、异钢种连浇时拉坯终了 到拉坯开始过程、终止浇注等)下制定相应的控制 标准。具体标准的设定可在生产中慢慢积累经验, 也可以参照有成功生产经验的钢厂数据来设定。 3.4 优化二次冷却技术
中心偏 析(级) B2.5 B2.5
B3 B3 B>3 B0.5 B1.5 B1 B1 B0.5 B1.0 B0.5 B1.0
中心疏 松(级)
1.5 1.5 1.5 ﹤3 1.5 2 3
2 2 1 0.5 1 1
中间裂 纹(级)
0.5 0.5
1 1.5 0.5 0 0 0 0 0 0 ﹥3 2.5
角部裂 纹(级)
连铸生产中的电磁搅拌技术,就是把按一定规 律排列的线圈安装在连铸机某一部位,电磁力。该电磁力推动铸坯坯壳内未凝固的钢液 沿一定方向循环运动,破坏了钢液凝固组织中已形 成的粗大的柱状晶,使晶粒细化;阻碍了柱状晶的 进一步形成,增加了等轴晶率;改善了铸坯中心部 位碳成分和硫化物等夹杂物分布不均的特点,增加 了夹杂物相互碰撞和聚合的机会,使夹杂物尺寸增 大易于上浮,以减缓中心偏析和中心疏松的产生。
0 0 0 0 0 0 0 0 0 0 0.5 0.5 0
三角区裂 氧化铝夹 针孔状气 纹(级) 杂(级) 泡(级)
1
0
0
0.5
0
0
1
0
0
0.5
0
0
0.5
0
0
﹥1.5
0
0
0.5
0
0
1
0
0
1
0
0
1
0
0
1
0
0
0.5
0
0
1
0
0
蜂窝气 泡(级)
0 0 0 0 0 0 0 0 0 0 0 0 0
硅酸盐 夹杂(级)
铸坯规格 (mm) 250×1550 250×1550 250×1550 250×1550 250×1550 250×1550 250×1550 250×1550 250×1550 250×1550 250×1550 250×1550 250×1550
表 1 某钢铁(集团)公司炼钢厂铸坯低倍检验报告
中心偏析形成机理之三是空穴抽吸理论,即铸 坯在凝固过程中若发生坯壳鼓胀,在铸坯中心就会 产生空穴,这些空穴具有负压抽吸作用,使富集了 溶质元素的钢液被吸入铸坯中心而导致中心偏析; 在凝固末期由于液体向固体转变发生体积收缩而 产生一定空穴,也使凝固末端富集溶质元素的钢液 被吸入铸坯中心,导致产生中心偏析。因此,铸坯 鼓肚量越大,中心偏析就会越严重。
连铸生产是一个连续动态的过程,因钢水温 度、铸坯厚度、钢种、拉坯速度和喷水条件等因素 不断变化,铸坯液芯的凝固位置也不断变化。静态 轻压下技术要求铸坯凝固终点位置基本保持不变, 需预先设定好轻压下区域,并调整好相应扇形段辊 缝。为发挥轻压下的最佳效果,找准凝固点,轻压 下技术的应用从静态发展到了动态。动态轻压下可 根据拉坯速度变化、铸坯凝固终点的位置变化,对 轻压下位置和压下量进行动态控制。VAI 开发的动 态轻压下系统由三个核心部分组成[7, 8]:带有远程 控制装置、4 个位置调整液压缸的 SMART 扇形段, 可在支撑框架上自动定位,驱动辊的升降由一个传 动液压缸实现,夹紧由配有内装式位置变送器的 4 个位置液压缸完成。对 SMART 扇形段进行计算机远 程控制的锥度自动调整 ASTC 系统,可根据不同钢 种自动选择目标辊缝,自动调整开浇和出尾坯状态 各扇形段的辊缝设定值;动态计算模型 DYNACS 系 统,能根据实际水流量、拉坯速度、钢种和过热度, 准确控制和确定铸坯的凝固点。VAI 的动态轻压下 技术已经在梅钢、武钢、芬兰的 Rautaruukki 和 AvestaPolarit 钢厂、意大利的 ILVA 钢厂、韩国的 POSCO 公司、奥地利的 Voestalpinestahl 钢公司以 及美国的 Bethlehem Steel 钢公司成功投入使用, 并且效果不错。
在板坯连铸机上采用电磁搅拌技术,要使其充 分发挥搅拌作用,显著降低中心偏析和中心疏松, 需准确计算电磁搅拌装置的具体安装位置和铸坯 中心的电磁推力大小。有研究表明[4],电磁搅拌装
置安装在钢水未凝固率为 25%~40%范围内较合 适,此时等轴晶率高;电磁推力控制在 65 mmFe~ 147 mmFe 范围内,搅拌效果较理想。 3.6 采用轻压下技术
3 中心偏析与中心疏松预防对策 由中心偏析与中心疏松形成原因分析,若能采
取措施促进铸坯中心凝固组织等轴晶化,减少钢液 中易偏析元素含量,控制铸坯鼓肚量,就可以减缓 中心偏析和中心疏松的产生。 3.1 提高钢水纯净度
钢中含碳量与凝固组织关系密切,影响柱状晶 和等轴晶的生长比率,必然对铸坯中心偏析和中心 疏松的产生起决定性作用。有研究表明[1],在其它 条件相同的情况下对含碳量分别为 0.3%、0.1%和 0.6%的三种钢进行浇注,发现其柱状晶长度、中 心偏析宽度和中心疏松空穴按含碳为 0.3%、0.1 %和 0.6%的顺序依次增加。因此,必须提高转炉 生产中碳的命中率,准确控制钢液中的碳含量。
板坯连铸机,设计铸坯规格为厚 200 mm、220 mm、 250 mm,宽 1400 mm~1800 mm。试运行期间生产了 断面为 250 mm×1550 mm 的 Q235、Q345 钢板坯, 低倍组织检验结果中心偏析和中心疏松较严重。我 们摘录了 13 个炉批号的低倍检验报告,进行对比
检查(如表 1),发现中心偏析一般为 B2.5 级,中 心疏松为 2 级左右。当铸坯轧制成材后,做两个断 面相互垂直的焊接试验时,在氧割或切口上出现局 部分层。根据该厂生产实际情况,为尽可能减少中 心偏析与中心疏松,生产高质量的铸坯,分析了中 心偏析与中心疏松缺陷的形成原因,提出了具体的 预防对策。
炉批号
451-520 451-505 451-611 451-614 441-262 451-481 451-482 441-265 451-484 441-415 441-418 451-766 441-440
钢钟
Q345 Q345 Q345 Q345 Q345 Q235 Q235 Q345 Q235 Q235 Q235 Q235 Q235
钢液中 S、P 等是易偏析元素,它们在钢液中 的含量和分布形态影响铸坯的中心偏析和中心疏 松。通过冶炼洁净钢,如采用铁水预处理或钢包脱 硫等技术,降低钢液中 S、P 等易偏析元素含量, 提高钢水纯净度,可有效防止中心偏析和中心疏松
的产生。 3.2 控制铸坯鼓肚量
控制铸坯鼓肚量,可以有效减缓中心偏析产 生。铸坯鼓肚量的大小主要与二冷区辊间距、坯壳 厚度、钢水静压力等有关。辊间距越小,坯壳越厚, 钢水静压力越小,鼓肚量就越小。因此,在设计连 铸机时,尽可能设计采用小辊径密排辊列布置,缩 小辊间距;采用刚性多节辊,防止支承辊变形;连 铸机不宜过高,以便于降低液相穴高度,减小钢水 静压力;在生产中对二冷区夹辊需严格对弧。 3.3 控制浇注温度和拉坯速度
二次冷却技术对铸坯的表面质量和内部质量 有重要影响,中心偏析和中心疏松等缺陷的形成与 之有紧密的联系。二次冷却技术包括二冷区分段、 二冷区喷嘴选择及配置、喷水条件(如流量、压力) 的确定等。
二冷区分段应根据连铸机的辊列排布,沿拉坯 方向从上到下按各冷却段长度逐渐增加的原则划 分,一般板坯连铸机为 7~9 个冷却段。
浇注温度是影响柱状晶生长的重要因素。浇注 温度高,铸坯柱状晶发达;浇注温度低,铸坯等轴 晶发达。因此,在不引起水口冻结的情况下,应尽 可能采用低过热度浇注。在生产操作中,可根据各 厂经验,对不同钢钟制定相应的钢水罐和中间罐目 标过热度基准。国内某厂的经验是:在生产低碳钢 ([C]≤0.08%)时,钢水罐和中间罐内钢水目标 过热度最好分别控制在 60℃、30℃之内;生产包晶 钢和中碳钢(≤0.08%[C]≤0.30%)时,钢水罐 和中间罐内钢水目标过热度最好分别控制在 55℃、 25℃之内。
2005 年第 2 期 ·炼钢·
钢铁技术
·1·
中心偏析与中心疏松的形成与预防