如何选择刀具材料切削切削加工高温合金
数控刀具的选用范文

数控刀具的选用范文一、刀具材料的选择1.硬质合金刀具:硬质合金是一种高硬度、高强度的材料,具有耐磨、耐高温、耐压等优点。
它适用于高速切削、丝锥切削、铣削和钻孔等工艺。
硬质合金刀具的优势在于能够承受高速切削,并具有较高的切削速度和高度的负荷能力。
2.高速钢刀具:高速钢是一种具有良好的刚度和切削性能的材料,适用于一般加工工艺。
相比硬质合金刀具,高速钢刀具价格较低,具有优点是磨损不易产生细小裂纹。
同时,高速钢刀具可以根据加工工艺的要求进行刀具调整和刃口复磨,提高刀具使用寿命。
3.陶瓷刀具:陶瓷刀具因其具有优秀的刚性和高硬度而备受青睐,适用于高速切削、高温切削和非金属加工等工艺。
陶瓷刀具的耐磨性能好,刃口细粒度,可以提供更高的切削速度和更长的刀具寿命。
然而,陶瓷刀具比较脆弱,易于出现断裂情况,且价格较贵,使用成本较高。
二、刀具几何形状的选择1.刀具刃角:刃角是刀具刃部与工件表面之间的夹角。
刃角的选择要根据切削材料和加工工艺。
一般来说,刃角较小的刀具可以减小切削力,有利于提高加工精度和表面质量;刃角适中的刀具能够提高切削稳定性和刀具寿命;刃角较大的刀具适用于粗加工。
2.刀具刃部形状:根据加工要求,刀具的刃部可以有不同的形状,如平底、球头、锥度、T型等。
不同形状的刃部适合于不同的加工需求,如平底刀适用于开槽和粗加工,球头刀适用于表面加工和球面零件等。
三、刀具涂层的选择刀具的涂层对加工效果和刀具寿命有着重要影响。
常见的刀具涂层有TiN、TiCN、TiAlN等。
涂层可以提供刀具表面的硬度和耐磨性,减少摩擦和热量,从而提高切削速度和刀具寿命。
选择刀具涂层应根据加工材料、加工工艺和切削条件等因素进行综合考虑。
综上所述,数控刀具的选用需要根据加工材料、加工工艺和切削条件等因素进行综合分析和评估。
同时,合理的刀具选择还需要考虑生产成本、切削质量、加工效率和刀具寿命等因素,以达到最佳的加工效果和经济效益。
刀具及切削参数选择
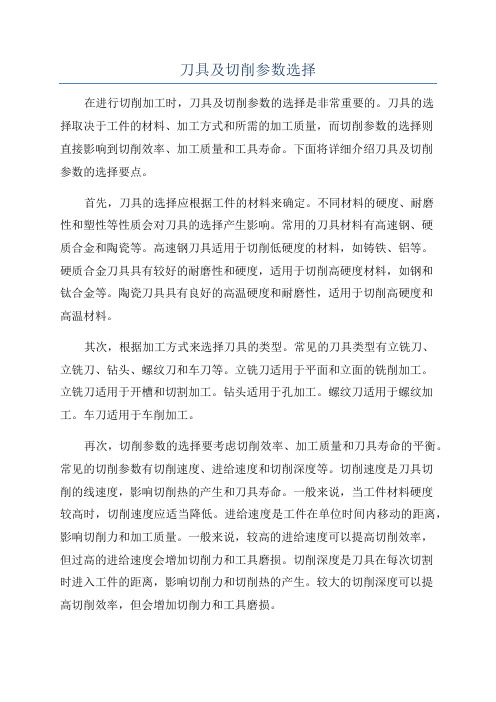
刀具及切削参数选择在进行切削加工时,刀具及切削参数的选择是非常重要的。
刀具的选择取决于工件的材料、加工方式和所需的加工质量,而切削参数的选择则直接影响到切削效率、加工质量和工具寿命。
下面将详细介绍刀具及切削参数的选择要点。
首先,刀具的选择应根据工件的材料来确定。
不同材料的硬度、耐磨性和塑性等性质会对刀具的选择产生影响。
常用的刀具材料有高速钢、硬质合金和陶瓷等。
高速钢刀具适用于切削低硬度的材料,如铸铁、铝等。
硬质合金刀具具有较好的耐磨性和硬度,适用于切削高硬度材料,如钢和钛合金等。
陶瓷刀具具有良好的高温硬度和耐磨性,适用于切削高硬度和高温材料。
其次,根据加工方式来选择刀具的类型。
常见的刀具类型有立铣刀、立铣刀、钻头、螺纹刀和车刀等。
立铣刀适用于平面和立面的铣削加工。
立铣刀适用于开槽和切割加工。
钻头适用于孔加工。
螺纹刀适用于螺纹加工。
车刀适用于车削加工。
再次,切削参数的选择要考虑切削效率、加工质量和刀具寿命的平衡。
常见的切削参数有切削速度、进给速度和切削深度等。
切削速度是刀具切削的线速度,影响切削热的产生和刀具寿命。
一般来说,当工件材料硬度较高时,切削速度应适当降低。
进给速度是工件在单位时间内移动的距离,影响切削力和加工质量。
一般来说,较高的进给速度可以提高切削效率,但过高的进给速度会增加切削力和工具磨损。
切削深度是刀具在每次切割时进入工件的距离,影响切削力和切削热的产生。
较大的切削深度可以提高切削效率,但会增加切削力和工具磨损。
此外,还应考虑冷却润滑剂的选择和使用。
合适的冷却润滑剂可以降低切削热的产生,减小工具磨损,提高加工质量。
综上所述,刀具及切削参数的选择需要考虑工件材料、加工方式和所需加工质量。
合理选择刀具类型和切削参数可以提高切削效率、加工质量和工具寿命。
在实际应用中,还需要根据具体情况进行调整和优化。
加工中心加工高温合金的方法

加工中心加工高温合金的方法
加工高温合金是一个具有挑战性的任务,需要采取一些特殊的方法和技术。
高温合金材料的加工性能与其化学成分、微观组织和加工参数等因素密切相关。
以下是加工中心加工高温合金的一些方法:
1. 选择合适的刀具材料和设计。
高温合金材料通常具有高硬度和高强度,因此需要使用硬度高、耐磨损的刀具材料。
同时,刀具的设计也应该考虑到高温合金材料的特性,例如大量的热量和高速的切削速度。
2. 控制切削速度和切削深度。
高温合金材料的加工速度和切削深度都应该合理设置,以确保加工效率和刀具寿命的平衡。
同时,需要避免过度热处理和热裂纹的发生。
3. 采用冷却液。
高温合金材料在加工过程中会产生大量的热量,因此需要采用冷却液进行冷却和润滑。
不同的高温合金材料需要采用不同的冷却液,以确保加工质量和刀具寿命。
4. 采用合适的加工技术。
高温合金材料可以采用不同的加工技术,例如立式铣削、横向铣削、车削和钻孔等。
这些技术可以根据不同的工件形状和加工要求进行选择。
总之,加工高温合金是一项艰巨的任务,需要掌握一些特殊的技术和方法。
只有正确地选择刀具材料和设计、控制切削速度和深度、采用冷却液以及选择合适的加工技术,才能够保证高温合金材料的加工质量和效率。
不同材质刀具切削参数

不同材质刀具切削参数在机械加工中,刀具的选择和切削参数的设置对于生产效率和产品质量具有重要影响。
不同的材料对切削条件有不同的需求,因此了解各种材料的特性并相应地调整切削参数是至关重要的。
本文将探讨几种常见金属材料的刀具切削参数。
一、不锈钢不锈钢具有良好的强度和耐腐蚀性,但相对较硬,切削时需要较高的切削力和适当的冷却。
一般建议使用硬度较高(如高速钢)的刀具,以避免过度磨损。
切削速度应保持在较低水平,进给量也应适当控制。
为了确保良好的冷却效果,通常会使用水基或油基切削液。
二、铝合金铝合金轻便且易于加工,但其易脆性和敏感性使得切削过程需要特别注意。
推荐使用硬质合金或涂层刀具,因为它们能够抵抗铝的氧化作用。
切削速度应控制在中等范围,进给量也需适度降低。
为防止粘刀现象,可以使用乳化油或极压切削油。
三、碳钢碳钢是常用的结构材料,其质地均匀、韧性好。
对于碳钢的切削,可以选择钨钻类刀具,由于其高硬度和高温性能良好,可以有效地进行切削。
切削速度可在中等偏高的范围内,进给量和背吃力矩应适中。
推荐使用润滑性能好的乳化油。
四、钛合金钛合金具有优异的抗腐蚀性和高强度,但也因此而变得异常敏感和脆弱。
钛合金的切削要求非常精确的控制,包括缓慢的切削速度、小直径的切入和切出路径以及充分冷却等。
通常建议使用金刚石涂层的高速钢刀具或者超细颗粒硬质合金涂层刀具,这样可以更好地适应钛合金的高温高压环境。
此外,还需根据实际情况选择合适的冷却剂来减少热变形和提高加工质量。
五、铜合金铜合金具有良好的导电性和导热性,适合于制造电气元件和其他相关产品。
然而,由于其软性,需要更小的切削力和更大的容屑空间。
一般来说,高速钢或硬质合金刀具都能满足这种材料的切割需求。
切削速度应在低速范围内,进给量也要适当减小。
同时,为了防止过热和粘刀现象,我们推荐使用水溶性切削液。
六、高强度钢高强度钢具有较高的硬度和强度,因此需要更高的切削力和更大的切削深度。
推荐使用硬度较高(如超细颗粒硬质合金)的刀具,并适当提高切削速度和进给量。
高温合金的种类与刀具选择
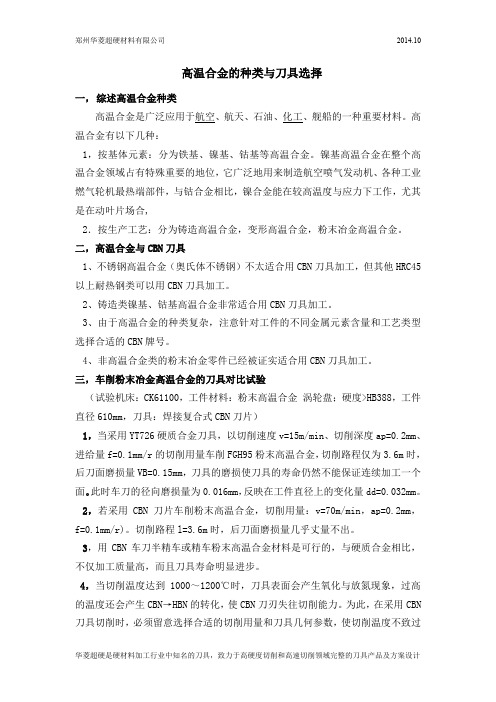
高温合金的种类与刀具选择一,综述高温合金种类高温合金是广泛应用于航空、航天、石油、化工、舰船的一种重要材料。
高温合金有以下几种:1,按基体元素:分为铁基、镍基、钴基等高温合金。
镍基高温合金在整个高温合金领域占有特殊重要的地位,它广泛地用来制造航空喷气发动机、各种工业燃气轮机最热端部件,与钴合金相比,镍合金能在较高温度与应力下工作,尤其是在动叶片场合,2.按生产工艺:分为铸造高温合金,变形高温合金,粉末冶金高温合金。
二,高温合金与CBN刀具1、不锈钢高温合金(奥氏体不锈钢)不太适合用CBN刀具加工,但其他HRC45以上耐热钢类可以用CBN刀具加工。
2、铸造类镍基、钴基高温合金非常适合用CBN刀具加工。
3、由于高温合金的种类复杂,注意针对工件的不同金属元素含量和工艺类型选择合适的CBN牌号。
4、非高温合金类的粉末冶金零件已经被证实适合用CBN刀具加工。
三,车削粉末冶金高温合金的刀具对比试验(试验机床:CK61100,工件材料:粉末高温合金涡轮盘;硬度>HB388,工件直径610mm,刀具:焊接复合式CBN刀片)1,当采用YT726硬质合金刀具,以切削速度v=15m/min、切削深度ap=0.2mm、进给量f=0.1mm/r的切削用量车削FGH95粉末高温合金,切削路程仅为3.6m时,后刀面磨损量VB=0.15mm,刀具的磨损使刀具的寿命仍然不能保证连续加工一个面。
此时车刀的径向磨损量为0.016mm,反映在工件直径上的变化量dd=0.032mm。
2,若采用CBN刀片车削粉末高温合金,切削用量:v=70m/min,ap=0.2mm,f=0.1mm/r)。
切削路程l=3.6m时,后刀面磨损量几乎丈量不出。
3,用CBN车刀半精车或精车粉末高温合金材料是可行的,与硬质合金相比,不仅加工质量高,而且刀具寿命明显进步。
4,当切削温度达到1000~1200℃时,刀具表面会产生氧化与放氮现象,过高的温度还会产生CBN→HBN的转化,使CBN刀刃失往切削能力。
高温合金的高速经济性车削技巧
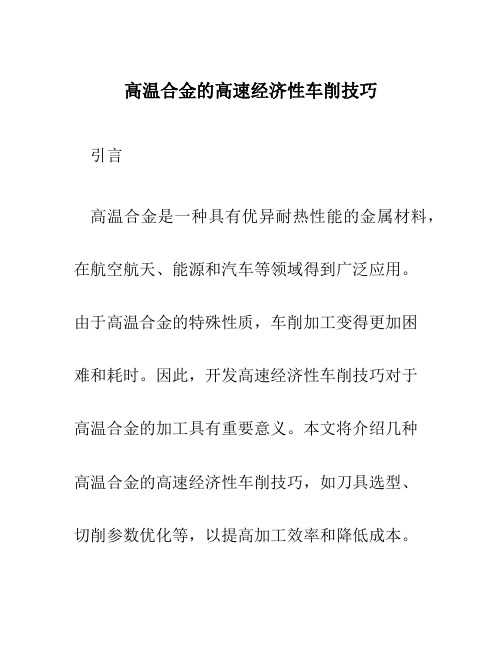
高温合金的高速经济性车削技巧引言高温合金是一种具有优异耐热性能的金属材料,在航空航天、能源和汽车等领域得到广泛应用。
由于高温合金的特殊性质,车削加工变得更加困难和耗时。
因此,开发高速经济性车削技巧对于高温合金的加工具有重要意义。
本文将介绍几种高温合金的高速经济性车削技巧,如刀具选型、切削参数优化等,以提高加工效率和降低成本。
选择合适的刀具高温合金的硬度和韧性较高,因此选择合适的刀具至关重要。
以下是几种常用的刀具材料及其适用情况:1.硬质合金刀具:适用于加工镍基高温合金和钴基高温合金,具有较高的耐磨性和热稳定性;2.陶瓷刀具:适用于加工钛基高温合金,具有良好的高温抗磨性能;3.CBN刀具:适用于加工铁基高温合金,具有较高的硬度和热稳定性。
在选择刀具时,还应考虑刀具的几何形状、刀具涂层和刀具刃口的特征。
合理选择刀具有助于提高车削效率和延长刀具寿命。
优化切削参数切削参数的优化可以提高车削效率和降低能耗。
以下是一些常用的切削参数优化的技巧:1.切削速度:高速切削能够缩短车削时间,但也会增加切削温度。
根据材料的热稳定性,选择合适的切削速度,避免刀具过热和材料过度烧结;2.进给速度:进给速度的选取要结合切削速度和刀具直径,以保证切削深度合理,避免过度负荷导致刀具断裂;3.切削深度:切削深度的控制要与切削速度和进给速度相匹配,避免过大切削深度引起刀具振动和工件变形;4.冷却润滑剂的使用:选择适当的冷却润滑剂可以有效降低切削温度,减少工件表面烧伤的风险。
使用合理的车削策略在高速经济性车削中,采用合理的车削策略可以最大程度地发挥刀具性能,提高车削效率。
1.粗车和半精车:采用大切削深度进行粗车和半精车,可以快速削除材料,提高加工速度;2.精车和半精车:采用较小的切削深度进行精车和半精车,以获得更高的加工精度和表面质量;3.断续进给和连续进给:对于易导致切削温度过高的材料,采用断续进给可以有效降低切削温度;4.干式和湿式车削:对于一些特殊材料,如钛合金,采用干式车削可以降低润滑剂的消耗和环境污染。
机床刀具的正确选择与使用方法
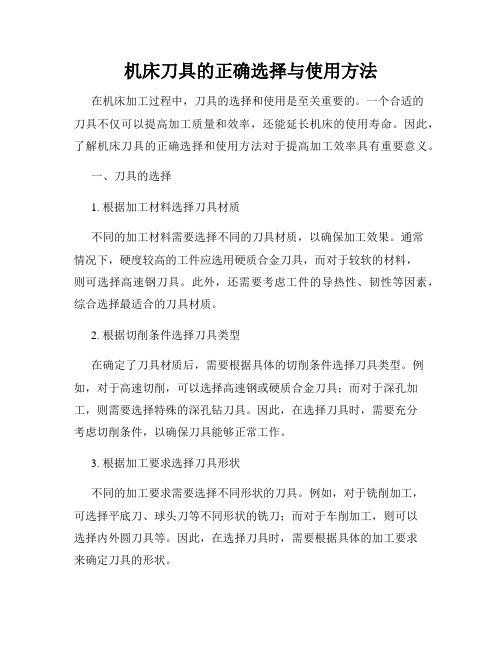
机床刀具的正确选择与使用方法在机床加工过程中,刀具的选择和使用是至关重要的。
一个合适的刀具不仅可以提高加工质量和效率,还能延长机床的使用寿命。
因此,了解机床刀具的正确选择和使用方法对于提高加工效率具有重要意义。
一、刀具的选择1. 根据加工材料选择刀具材质不同的加工材料需要选择不同的刀具材质,以确保加工效果。
通常情况下,硬度较高的工件应选用硬质合金刀具,而对于较软的材料,则可选择高速钢刀具。
此外,还需要考虑工件的导热性、韧性等因素,综合选择最适合的刀具材质。
2. 根据切削条件选择刀具类型在确定了刀具材质后,需要根据具体的切削条件选择刀具类型。
例如,对于高速切削,可以选择高速钢或硬质合金刀具;而对于深孔加工,则需要选择特殊的深孔钻刀具。
因此,在选择刀具时,需要充分考虑切削条件,以确保刀具能够正常工作。
3. 根据加工要求选择刀具形状不同的加工要求需要选择不同形状的刀具。
例如,对于铣削加工,可选择平底刀、球头刀等不同形状的铣刀;而对于车削加工,则可以选择内外圆刀具等。
因此,在选择刀具时,需要根据具体的加工要求来确定刀具的形状。
二、刀具的使用方法1. 切勿超负荷使用刀具刀具在工作时会受到一定的负荷,如果超负荷使用,容易导致刀具磨损过快甚至断裂。
因此,在使用刀具时,需要根据切削条件合理设置切削参数,避免超负荷使用刀具。
2. 定期检查刀具状态刀具在使用过程中会出现磨损,因此需要定期检查刀具状态。
一旦发现刀具磨损严重或者出现其他异常情况,应及时更换或修磨刀具,以确保刀具的正常使用。
3. 注意刀具的保养刀具在使用过程中需要定期进行清洁和保养,以延长刀具的使用寿命。
在清洁时,应使用专用清洁剂擦拭刀具表面,防止刀具受到腐蚀。
同时,在使用完毕后,应将刀具储存在干燥通风的环境中,避免受潮生锈。
总结:正确选择和使用机床刀具对于提高加工效率和质量具有重要意义。
通过根据加工材料选择刀具材质、根据切削条件选择刀具类型、根据加工要求选择刀具形状等方法,能够有效提高刀具的使用效率和寿命。
数控机床加工高温合金材料的最佳切削参数选择方法

数控机床加工高温合金材料的最佳切削参数选择方法高温合金材料由于其优异的机械性能和耐高温性能,广泛应用于航空航天、能源等领域。
然而,由于其具有较高的硬度和耐磨性,加工难度较大。
数控机床是目前加工高温合金材料的主要工具之一,但合适的切削参数选择对于获得优质的加工效果至关重要。
在选择数控机床加工高温合金材料的最佳切削参数之前,首先要了解高温合金材料的特性。
高温合金材料具有高强度、低热导率和高塑性等特点。
因此,在加工过程中需要考虑以下几个方面的因素:切削速度、进给速度、切削深度、切削力和切削温度。
首先,切削速度是指在单位时间内工件表面相对于刀具切削的线速度。
切削速度是影响切削效果的重要参数之一。
对于高温合金材料,由于其较高的硬度和热导率,较高的切削速度通常会导致刀具过早磨损和切削温度的升高。
因此,在选择切削速度时应综合考虑刀具材料、机床稳定性和切削效率等因素,选择一个合适的切削速度。
其次,进给速度是指刀具在单位时间内相对于工件的移动速度。
进给速度的选择应根据高温合金材料的硬度、机床的剛性以及刀具的耐磨性等因素综合考虑。
增加进给速度可以提高加工效率,但也会增加刀具的磨损。
因此,在选择进给速度时要找到一个平衡点,在保证加工效率的同时尽量减少刀具磨损。
第三,切削深度是指刀具在单位时间内相对于工件的切削厚度。
切削深度的选择应根据高温合金材料的硬度、刀具的耐磨性以及机床的剛性等因素综合考虑。
过大的切削深度会导致刀具过早磨损,而过小的切削深度则会降低加工效率。
因此,在选择切削深度时要找到一个合适的范围,在保证加工效率的同时尽量减少刀具磨损。
此外,切削力和切削温度也是影响高温合金材料加工的重要参数。
切削力直接影响机床的稳定性和切削刀具的寿命,而切削温度会影响切削表面的质量和切削效率。
因此,在选择切削参数时应尽量控制切削力和切削温度的大小,避免过大或过高。
综上所述,数控机床加工高温合金材料的最佳切削参数选择方法涉及切削速度、进给速度、切削深度、切削力和切削温度等关键参数的综合考虑。
切削加工高温合金的刀具材料

切削加工高温合金的刀具材料高温合金具有优良的高温强度、热稳定性及抗热疲劳性能,因此它广泛应用于航空航天、船舶、核工业、电站等行业,例如现代燃汽涡轮发动机的燃烧室、涡轮导向叶片与工作叶片、涡轮盘及涡轮转子结构件、航空发动机盘件、环形件等高温转动部件等等。
高温合金是最难加工的材料之一,如果45# 钢的加工性为100% ,则高温合金的相对加工性仅为5% ~20% ,其切削加工的特点有:①切削力大,是普通钢材的 2 ~ 4 倍。
高温合金含有许多高熔点金属元素,构成组织结构致密的奥氏体固溶体,合金的塑性好,原子结构十分稳定,需要很大能量才能使原子脱离平衡位置,因而变形抗力大。
②切削温度高,最高可达1000 ℃左右。
高温合金导热系数小,仅为45# 钢的1/4 ~1/3 ,刀具与工件间摩擦强烈而导热性差,故切削温度高。
③加工硬化严重,表面硬度比基体硬度高50% ~100% 。
④塑性变形大,在室温下的延伸率可达30% ~50% 。
⑤刀具易磨损,常见的有扩散磨损、边界磨损、刀尖塑性变形、月牙洼磨损及积屑瘤。
由于这些特点,切削高温合金的刀具材料应具有高的强度、高的红硬性、良好的耐磨性和韧性、高的导热性和抗粘接能力等。
高速钢刀具材料是较早用于加工高温合金的刀具材料,现在由于加工效率等原因正被像硬质合金这样的刀具材料所替代。
但在一些成形刀具以及工艺系统刚性差的条件下,采用高速钢刀具材料加工高温合金仍是很好的选择。
另一方面,加工效率是一种综合的评判,高速钢刀具切削速度低,在某些特定条件下其损失的效率可以通过采用大的切削深度来弥补,因为高速钢刀具材料有更高的强度和韧性,且刃口可以更锋利,产生的切削热更低,加工硬化现象更轻。
用于加工高温合金的高速钢,常有钴高速钢、含钴超硬高速钢和粉末冶金高速钢等高性能高速钢。
在高速钢中加入适量的钴后,由于钴可促进奥氏体中碳化物的溶解作用,可以提高高速钢的热稳定性和二次硬度,高温硬度得到提高;同时钴还可促进高速钢回火时从马氏体中析出钨或钼的碳化物,增加弥散硬化效果,因而能提高高速钢的回火硬度,从而提高高速钢的耐磨性。
数控机床加工高温合金材料的最佳切削参数选择方法
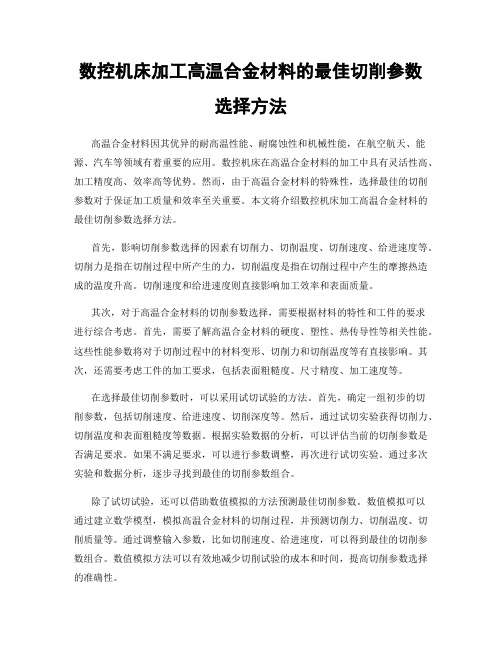
数控机床加工高温合金材料的最佳切削参数选择方法高温合金材料因其优异的耐高温性能、耐腐蚀性和机械性能,在航空航天、能源、汽车等领域有着重要的应用。
数控机床在高温合金材料的加工中具有灵活性高、加工精度高、效率高等优势。
然而,由于高温合金材料的特殊性,选择最佳的切削参数对于保证加工质量和效率至关重要。
本文将介绍数控机床加工高温合金材料的最佳切削参数选择方法。
首先,影响切削参数选择的因素有切削力、切削温度、切削速度、给进速度等。
切削力是指在切削过程中所产生的力,切削温度是指在切削过程中产生的摩擦热造成的温度升高。
切削速度和给进速度则直接影响加工效率和表面质量。
其次,对于高温合金材料的切削参数选择,需要根据材料的特性和工件的要求进行综合考虑。
首先,需要了解高温合金材料的硬度、塑性、热传导性等相关性能。
这些性能参数将对于切削过程中的材料变形、切削力和切削温度等有直接影响。
其次,还需要考虑工件的加工要求,包括表面粗糙度、尺寸精度、加工速度等。
在选择最佳切削参数时,可以采用试切试验的方法。
首先,确定一组初步的切削参数,包括切削速度、给进速度、切削深度等。
然后,通过试切实验获得切削力、切削温度和表面粗糙度等数据。
根据实验数据的分析,可以评估当前的切削参数是否满足要求。
如果不满足要求,可以进行参数调整,再次进行试切实验。
通过多次实验和数据分析,逐步寻找到最佳的切削参数组合。
除了试切试验,还可以借助数值模拟的方法预测最佳切削参数。
数值模拟可以通过建立数学模型,模拟高温合金材料的切削过程,并预测切削力、切削温度、切削质量等。
通过调整输入参数,比如切削速度、给进速度,可以得到最佳的切削参数组合。
数值模拟方法可以有效地减少切削试验的成本和时间,提高切削参数选择的准确性。
此外,可以借鉴以往的经验和文献资料。
在加工高温合金材料方面,已有许多研究者进行了大量的实验和分析工作。
他们通过试验和数据分析,总结了一些切削参数选择的经验和规律。
刀具材料的选用及新材料
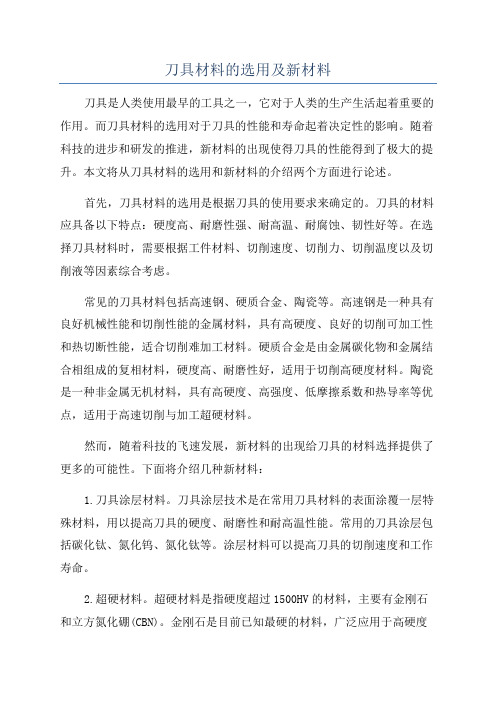
刀具材料的选用及新材料刀具是人类使用最早的工具之一,它对于人类的生产生活起着重要的作用。
而刀具材料的选用对于刀具的性能和寿命起着决定性的影响。
随着科技的进步和研发的推进,新材料的出现使得刀具的性能得到了极大的提升。
本文将从刀具材料的选用和新材料的介绍两个方面进行论述。
首先,刀具材料的选用是根据刀具的使用要求来确定的。
刀具的材料应具备以下特点:硬度高、耐磨性强、耐高温、耐腐蚀、韧性好等。
在选择刀具材料时,需要根据工件材料、切削速度、切削力、切削温度以及切削液等因素综合考虑。
常见的刀具材料包括高速钢、硬质合金、陶瓷等。
高速钢是一种具有良好机械性能和切削性能的金属材料,具有高硬度、良好的切削可加工性和热切断性能,适合切削难加工材料。
硬质合金是由金属碳化物和金属结合相组成的复相材料,硬度高、耐磨性好,适用于切削高硬度材料。
陶瓷是一种非金属无机材料,具有高硬度、高强度、低摩擦系数和热导率等优点,适用于高速切削与加工超硬材料。
然而,随着科技的飞速发展,新材料的出现给刀具的材料选择提供了更多的可能性。
下面将介绍几种新材料:1.刀具涂层材料。
刀具涂层技术是在常用刀具材料的表面涂覆一层特殊材料,用以提高刀具的硬度、耐磨性和耐高温性能。
常用的刀具涂层包括碳化钛、氮化钨、氮化钛等。
涂层材料可以提高刀具的切削速度和工作寿命。
2.超硬材料。
超硬材料是指硬度超过1500HV的材料,主要有金刚石和立方氮化硼(CBN)。
金刚石是目前已知最硬的材料,广泛应用于高硬度材料的切削。
立方氮化硼硬度仅次于金刚石,具有良好的耐磨性和耐高温性能,适用于切削高硬度的热处理钢和铸铁。
3.纳米材料。
纳米材料是指颗粒尺寸在纳米级别的材料,具有与传统材料不同的性能。
纳米材料具有高硬度、高强度、高韧性、高热导率等特点,适用于高速切削和高温切削。
4.新型复合材料。
新型复合材料是将两种或两种以上的材料按一定比例复合而成的材料,具有诸多优点。
例如,碳纤维复合材料具有高强度、低密度、耐腐蚀等特点,适用于切削轻质材料。
刀具材质选用标准
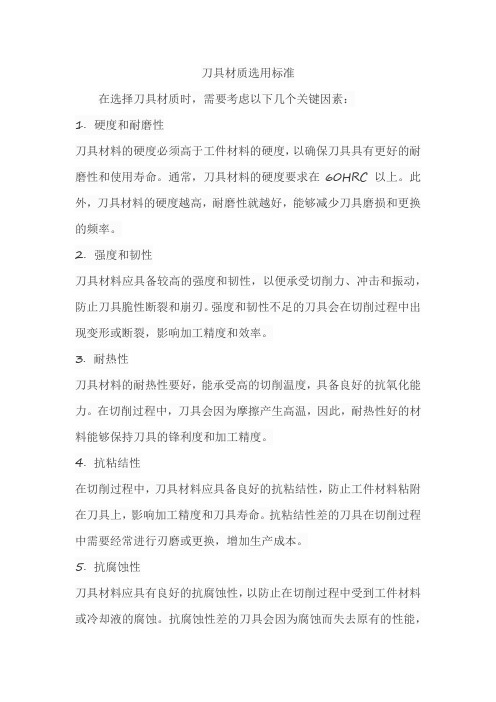
刀具材质选用标准
在选择刀具材质时,需要考虑以下几个关键因素:
1. 硬度和耐磨性
刀具材料的硬度必须高于工件材料的硬度,以确保刀具具有更好的耐磨性和使用寿命。
通常,刀具材料的硬度要求在60HRC以上。
此外,刀具材料的硬度越高,耐磨性就越好,能够减少刀具磨损和更换的频率。
2. 强度和韧性
刀具材料应具备较高的强度和韧性,以便承受切削力、冲击和振动,防止刀具脆性断裂和崩刃。
强度和韧性不足的刀具会在切削过程中出现变形或断裂,影响加工精度和效率。
3. 耐热性
刀具材料的耐热性要好,能承受高的切削温度,具备良好的抗氧化能力。
在切削过程中,刀具会因为摩擦产生高温,因此,耐热性好的材料能够保持刀具的锋利度和加工精度。
4. 抗粘结性
在切削过程中,刀具材料应具备良好的抗粘结性,防止工件材料粘附在刀具上,影响加工精度和刀具寿命。
抗粘结性差的刀具在切削过程中需要经常进行刃磨或更换,增加生产成本。
5. 抗腐蚀性
刀具材料应具有良好的抗腐蚀性,以防止在切削过程中受到工件材料或冷却液的腐蚀。
抗腐蚀性差的刀具会因为腐蚀而失去原有的性能,
需要频繁更换。
综上所述,选择合适的刀具材质需要考虑多个因素,包括硬度、强度和韧性、耐热性、抗粘结性和抗腐蚀性等。
根据不同的加工需求和工件材料,选择适合的刀具材质能够提高加工效率、降低生产成本、并确保加工质量。
数控机床加工高温合金的技巧与要点

数控机床加工高温合金的技巧与要点高温合金是一类具有优异耐高温性能的特种合金材料,广泛应用于航空、航天、能源等领域。
由于其高硬度、高强度、高韧性和高热膨胀系数等特点,高温合金的加工难度较大。
在数控机床加工高温合金时,需要掌握一些技巧与要点,以保证加工质量和效率。
本文将介绍数控机床加工高温合金的技巧与要点。
首先,选择适当的刀具材料和刀具参数是数控机床加工高温合金的重要要点。
由于高温合金具有较高的热硬化性和热软化性,刀具材料需要具备一定的耐磨性和耐热性。
普遍采用的刀具材料包括硬质合金、陶瓷和刚石涂层等。
此外,根据高温合金的性质和加工要求,合理选择刀具的几何参数,如前角、主偏角、切削速度和进给速度等,可以有效控制切削温度和延长刀具使用寿命。
其次,加工高温合金时,刀具的润滑与冷却是不可忽视的技巧。
由于高温合金加工过程中热量较大,容易产生大量的热应力和变形,因此,刀具的润滑与冷却是至关重要的。
采用适当的冷却液可以降低切削温度,减少刀具磨损和断裂数量。
同时,冷却液还可以起到排屑和清洁切削区域的作用。
在选用冷却液时,需考虑到其杂质、酸碱度和湿润性等特性,以确保加工质量。
此外,定期清洗和更换冷却液也是必要的,以保持其良好的工作状态。
另外,合理的切削参数和刀具路径设置也是数控机床加工高温合金的关键技巧之一。
根据高温合金的性质和加工要求,确定合适的切削速度、进给速度和切削深度等参数,可有效控制切削温度和提高生产效率。
同时,合理设置刀具路径可以避免过多的切削力集中在刀具上,降低切削振动和刀具的断裂风险。
在进行数控机床编程时,应仔细考虑刀具路径的选择和修整,以确保加工质量和效益。
此外,加工高温合金时,应注意刀具磨损和断裂的预防。
高温合金具有较高的硬度和韧性,容易导致刀具的磨损和断裂。
为预防刀具的磨损和断裂,可以采取以下措施:定期对刀具进行检查和测量,及时更换磨损过度的刀具;根据加工要求,采用合适的工艺和切削参数,减少刀具的磨损;加工过程中,及时清理切削区域的切屑和切削液,减少刀具的摩擦与损伤。
高温合金切削参数
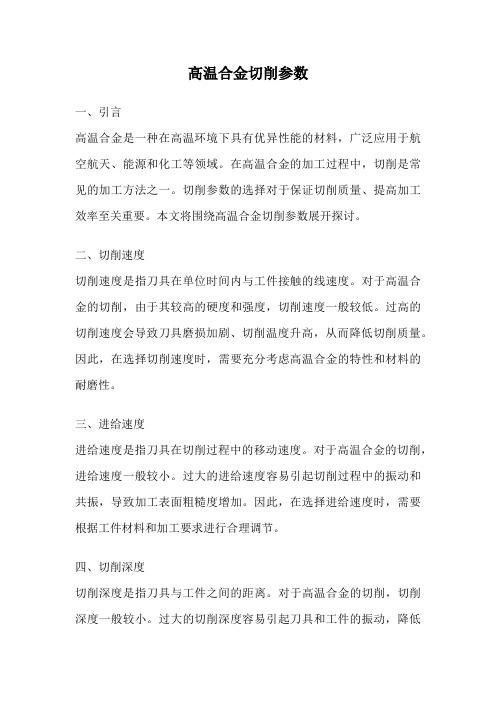
高温合金切削参数一、引言高温合金是一种在高温环境下具有优异性能的材料,广泛应用于航空航天、能源和化工等领域。
在高温合金的加工过程中,切削是常见的加工方法之一。
切削参数的选择对于保证切削质量、提高加工效率至关重要。
本文将围绕高温合金切削参数展开探讨。
二、切削速度切削速度是指刀具在单位时间内与工件接触的线速度。
对于高温合金的切削,由于其较高的硬度和强度,切削速度一般较低。
过高的切削速度会导致刀具磨损加剧、切削温度升高,从而降低切削质量。
因此,在选择切削速度时,需要充分考虑高温合金的特性和材料的耐磨性。
三、进给速度进给速度是指刀具在切削过程中的移动速度。
对于高温合金的切削,进给速度一般较小。
过大的进给速度容易引起切削过程中的振动和共振,导致加工表面粗糙度增加。
因此,在选择进给速度时,需要根据工件材料和加工要求进行合理调节。
四、切削深度切削深度是指刀具与工件之间的距离。
对于高温合金的切削,切削深度一般较小。
过大的切削深度容易引起刀具和工件的振动,降低加工质量。
因此,在选择切削深度时,需要根据工件的硬度和刀具的刚性进行合理调整。
五、切削润滑切削润滑是指在切削过程中使用润滑剂以减少切削摩擦和降低切削温度。
对于高温合金的切削,切削润滑尤为重要。
适当的切削润滑可以有效降低切削温度,减少刀具磨损和工件表面质量的损伤。
常见的切削润滑方式包括干切削、液体冷却和切削液冷却等。
六、刀具材料刀具材料的选择对于高温合金的切削至关重要。
由于高温合金的硬度和强度较高,刀具材料需要具备较好的耐磨性和高温稳定性。
常见的刀具材料包括硬质合金、陶瓷和涂层刀具等。
在选择刀具材料时,需要综合考虑材料的硬度、热导率和化学稳定性等因素。
七、切削冷却切削冷却是指通过冷却剂对切削区域进行降温处理。
对于高温合金的切削,切削冷却尤为重要。
适当的切削冷却可以有效降低切削温度,减少刀具磨损和工件表面质量的损伤。
常见的切削冷却方式包括气体冷却、液体冷却和切削液冷却等。
高温合金4169加工技巧
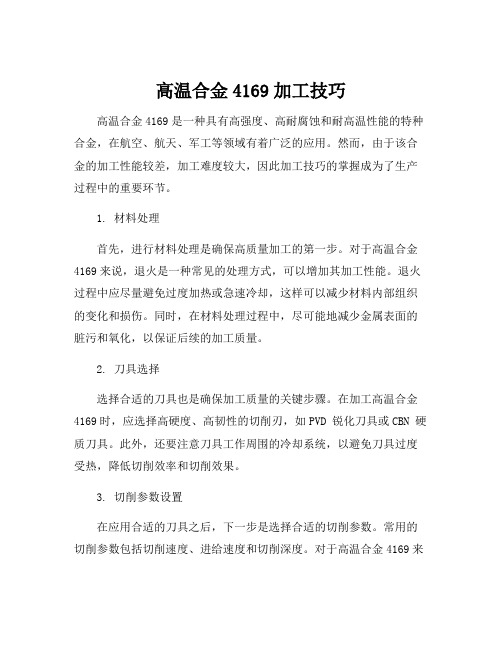
高温合金4169加工技巧高温合金4169是一种具有高强度、高耐腐蚀和耐高温性能的特种合金,在航空、航天、军工等领域有着广泛的应用。
然而,由于该合金的加工性能较差,加工难度较大,因此加工技巧的掌握成为了生产过程中的重要环节。
1. 材料处理首先,进行材料处理是确保高质量加工的第一步。
对于高温合金4169来说,退火是一种常见的处理方式,可以增加其加工性能。
退火过程中应尽量避免过度加热或急速冷却,这样可以减少材料内部组织的变化和损伤。
同时,在材料处理过程中,尽可能地减少金属表面的脏污和氧化,以保证后续的加工质量。
2. 刀具选择选择合适的刀具也是确保加工质量的关键步骤。
在加工高温合金4169时,应选择高硬度、高韧性的切削刃,如PVD 锐化刀具或CBN 硬质刀具。
此外,还要注意刀具工作周围的冷却系统,以避免刀具过度受热,降低切削效率和切削效果。
3. 切削参数设置在应用合适的刀具之后,下一步是选择合适的切削参数。
常用的切削参数包括切削速度、进给速度和切削深度。
对于高温合金4169来说,应该适当降低切削速度和进给速度,并减小切削深度,这样可以降低切削温度,减少切削压力和削屑损伤。
4. 工艺流程控制除了以上三点,还需要在整个加工过程中注意一些流程控制问题。
比如,控制每一次切削之后的均匀冷却时间,以避免材料的温度过高。
同时,对于较为复杂的零件,应该制定合理的工艺流程,对于不同的部位采用不同的工艺,以确保加工精度和加工效率。
总之,加工高温合金4169需要根据材料的性质和加工特点,选择合适的材料处理方法、刀具和切削参数,并注意流程控制问题。
只有这样,才能保证高质量加工和生产出优质的性能。
探讨不同材质的刀刃:如何选择合适的刀片

探讨不同材质的刀刃:如何选择合适的刀片刀片作为刀具的重要组成部分,对于切削、刻划等各种工作的效果至关重要。
不同材质的刀片具有各自的特点和应用场景,选择合适的刀片对于工作的顺利进行至关重要。
本文将分别探讨几种常见的刀片材质,并指导如何选择合适的刀片。
1. 高速钢刀片高速钢刀片是最常见的刀片材质之一,其主要成分是钼、钴、铬、钢等合金元素。
高速钢具有良好的耐热性和耐磨性,适用于高速切削情况下的工作。
它能够切削多种材料,包括铸铁、不锈钢、铝合金等。
高速钢刀片的价格相对较低,使用寿命较长,因此是大多数刀具的首选。
2. 硬质合金刀片硬质合金刀片是由钨钛碳等硬质合金颗粒通过粉末冶金工艺与钴等粘结相结合而成。
硬质合金刀片具有硬度高、耐磨性好的特点,尤其适合切削硬度高的材料,如碳化硬质合金、铸铁等。
硬质合金刀片的切削速度较高,但对切削液的要求相对较高,以降低刀片因温度升高而发生变形的风险。
3. 陶瓷刀片陶瓷刀片是由氧化锆或碳化硅等陶瓷材料制成。
陶瓷刀片具有极高的硬度和耐磨性,适用于高温和强腐蚀环境下的切削工作。
与其他材料相比,陶瓷刀片的切削性能更好,能够获得更高的切削速度和更好的表面质量。
然而,由于陶瓷刀片易受到冲击和弯曲,因此需要更小心地处理和使用。
4. 金刚石刀片金刚石刀片是由金刚石颗粒与金属粉末通过高温高压工艺制成。
金刚石刀片具有极高的硬度和耐磨性,能够切割各种硬度的材料,包括玻璃、陶瓷、石材等。
金刚石刀片在加工硬脆材料时表现出色,能够获得更高的切削速度和更好的切削质量。
然而,金刚石刀片的价格相对较高,且刀片之间的冷热差异容易导致刀片破裂。
在选择合适的刀片时,需要考虑以下几个因素:1. 材料特性:不同材料的硬度、耐磨性、热导率等特性不同,需要选择相应材质的刀片来适应切削工作。
例如,对于硬度高的材料,可以选择硬质合金或金刚石刀片;对于高温环境下的切削工作,陶瓷刀片是一个好的选择。
2. 切削条件:切削速度、切削力、切削液的选择等因素都会影响刀片的选择。
刀具材质选用标准
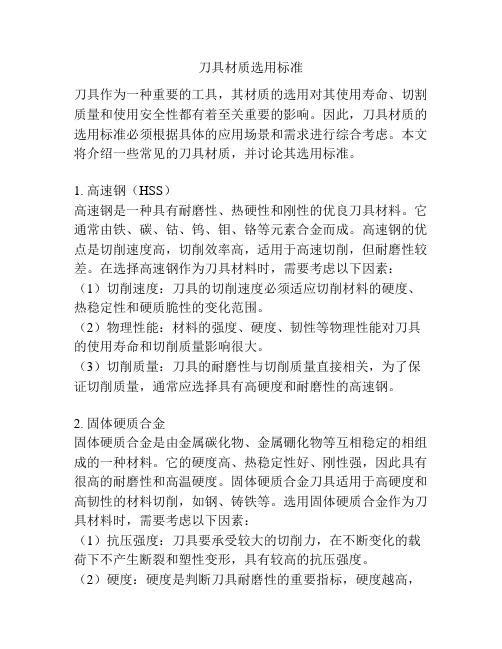
刀具材质选用标准刀具作为一种重要的工具,其材质的选用对其使用寿命、切割质量和使用安全性都有着至关重要的影响。
因此,刀具材质的选用标准必须根据具体的应用场景和需求进行综合考虑。
本文将介绍一些常见的刀具材质,并讨论其选用标准。
1. 高速钢(HSS)高速钢是一种具有耐磨性、热硬性和刚性的优良刀具材料。
它通常由铁、碳、钴、钨、钼、铬等元素合金而成。
高速钢的优点是切削速度高,切削效率高,适用于高速切削,但耐磨性较差。
在选择高速钢作为刀具材料时,需要考虑以下因素:(1)切削速度:刀具的切削速度必须适应切削材料的硬度、热稳定性和硬质脆性的变化范围。
(2)物理性能:材料的强度、硬度、韧性等物理性能对刀具的使用寿命和切削质量影响很大。
(3)切削质量:刀具的耐磨性与切削质量直接相关,为了保证切削质量,通常应选择具有高硬度和耐磨性的高速钢。
2. 固体硬质合金固体硬质合金是由金属碳化物、金属硼化物等互相稳定的相组成的一种材料。
它的硬度高、热稳定性好、刚性强,因此具有很高的耐磨性和高温硬度。
固体硬质合金刀具适用于高硬度和高韧性的材料切削,如钢、铸铁等。
选用固体硬质合金作为刀具材料时,需要考虑以下因素:(1)抗压强度:刀具要承受较大的切削力,在不断变化的载荷下不产生断裂和塑性变形,具有较高的抗压强度。
(2)硬度:硬度是判断刀具耐磨性的重要指标,硬度越高,耐磨性越好。
(3)韧性:韧性是判断刀具抗冲击性能的指标,适当的韧性可以增加刀具的使用寿命和安全性。
3. 陶瓷陶瓷刀具具有优异的硬度、耐磨性和化学稳定性,在高温下也能保持较好的硬度和强度。
陶瓷刀具适用于高硬度和脆性的材料切削,如陶瓷、玻璃等。
选用陶瓷作为刀具材料时,需要考虑以下因素:(1)抗断裂性:陶瓷材料的断裂强度相对较低,容易产生裂纹,导致刀具断裂。
因此,陶瓷刀具需要具备一定的抗断裂性能。
(2)耐磨性:陶瓷刀具的耐磨性能是非常重要的,目前,研究人员通过增加陶瓷的晶界相、改变陶瓷的组织结构等方式来提高陶瓷刀具的耐磨性。
冲床加工中的刀具材料选择与刀具寿命

冲床加工中的刀具材料选择与刀具寿命冲床加工是一种非常常见的金属加工方式,广泛应用于汽车零部件、家电制造、电子产品等行业。
在冲床加工中,刀具材料的选择和刀具寿命是至关重要的因素,直接影响着加工效率和产品质量。
本文将探讨冲床加工中的刀具材料选择和刀具寿命相关的问题。
一、冲床加工中的刀具材料选择1. 高速钢高速钢是一种常用的冲床刀具材料。
它具有良好的切削性能和耐磨性,适用于加工低碳钢、不锈钢、铜、铝等材料。
高速钢刀具的价格相对较低,易于加工和磨削,而且具有较高的耐热性和耐冲击性。
因此,在一些性能要求不太高的冲压加工中,可以选择高速钢刀具。
2. 硬质合金硬质合金是一种耐磨材料,由钨钴碳化物和粉末冶金技术制成。
它的硬度很高,耐磨性好,适用于加工高硬度和高强度的材料,如不锈钢、合金钢等。
硬质合金刀具的寿命相对较长,能够承受较高的冲击负荷,因此在要求高精度和长寿命的冲压加工中广泛应用。
3. 陶瓷陶瓷刀具主要由氧化铝等陶瓷材料制成,具有极高的硬度和耐磨性。
由于其导热性能较差,适用于加工高温合金和硬度非常高的材料。
陶瓷刀具的寿命可达到很高,但由于其易碎性,需要在使用过程中加强保护,并采取适当的安全措施。
二、刀具寿命的影响因素1. 刀具材料不同材料的刀具具有不同的硬度、耐磨性和耐冲击性,直接影响其寿命。
选择适合加工材料的刀具材料是提高刀具寿命的关键。
2. 工作环境工作环境因素也对刀具寿命有明显影响。
例如,如果切削材料中有大量磨料颗粒,会加速刀具磨损;如果切削润滑条件不良,也会对刀具寿命造成不利影响。
3. 刀具几何形状刀具几何形状的设计对刀具寿命也有重要影响。
合理选择刀具的刃角、刀尖强度等参数,能够减小切削力和热量产生,降低刀具磨损速度,提高刀具的寿命。
4. 切削速度与进给量切削速度和进给量的选择对刀具寿命也有较大影响。
一般来说,较高的切削速度会加速刀具磨损,而过大或过小的进给量都会对刀具产生不利影响。
因此,在加工过程中,需要根据具体情况选择适当的切削速度和进给量,以达到最佳的加工效果。
刀具材料与工件材料

刀具材料与工件材料在选择刀具材料时,以下几个因素需要考虑:1.强度和硬度:刀具材料需要具备足够的强度和硬度,以抵抗切削力和磨损。
一般来说,工具钢或高速钢是常用的刀具材料,具备较高的硬度。
2.切削温度:刀具在切削过程中会产生高温,刀具材料需要能够耐受高温并保持稳定的性能。
一些特殊的高温合金,如硬质合金和陶瓷材料,常常被用作切削工具。
3.导热性:刀具材料需要具备良好的导热性,以帮助快速散热并降低温度。
高导热性材料,如高速钢和硬质合金,常常被用于制造刀具。
在选择工件材料时,以下几个因素需要考虑:1.材料的物理性质:工件材料的物理性质,如硬度、强度、韧性和导热性,会影响切削过程中的加工难度和切削力。
一般来说,较软的金属(如铝)比较容易加工,而较硬的金属(如钛)则需要使用更坚硬的刀具材料。
2.工件材料的热状况:切削过程中会产生大量的热量,工件材料的热状况会影响加工的稳定性和表面质量。
一些难加工的材料,如耐热合金,可能需要采取特殊的冷却措施或选择更适合的刀具材料。
3.工件材料的表面质量:工件材料的表面质量会受到切削工具和切削参数的影响。
对于需要高表面质量的工件,需要选择具有较高精度和光洁度的刀具,并合理选择切削速度和进给速度。
在实际应用中,刀具材料和工件材料的选择需要综合考虑以上因素,并进行实际的试验和验证。
材料技术的不断发展也为刀具材料和工件材料的选择提供了更多的可能性,例如,刀具涂层技术和新型工件材料的开发等。
总之,刀具材料和工件材料的选择对于提高加工效率和产品质量至关重要。
刀具材料需要具备足够的强度、硬度和耐热性,而工件材料需要考虑物理性质、热状况和表面质量等因素。
合理选择刀具材料和工件材料,可以提高加工效率,降低生产成本,并获得更好的产品质量。
- 1、下载文档前请自行甄别文档内容的完整性,平台不提供额外的编辑、内容补充、找答案等附加服务。
- 2、"仅部分预览"的文档,不可在线预览部分如存在完整性等问题,可反馈申请退款(可完整预览的文档不适用该条件!)。
- 3、如文档侵犯您的权益,请联系客服反馈,我们会尽快为您处理(人工客服工作时间:9:00-18:30)。
如何选择刀具材料切削切削加工高温合金
一、高温合金的含义及性能
1、高温合金的含义:是指以铁、镍、钴为基,能够在600℃以上的高温及
一定应力作用下长期工作的一类金属材料,又被称为超合金,热强合金。
2、高温合金的特点:具有较高的高温强度,良好的抗氧化能和抗腐蚀性能,良好的疲劳性能、抗断裂韧性等综合性能。
高温合金是单一奥氏体组织,可以
在各种温度下具有良好的组织稳定性和使用可靠性。
由于高温合金的特点,已成为制造航空航天发动机热端部件的关键材料,
是航空航天材料的重要成员,也可以广泛应用在石油化工、电力、冶金等领域。
二、高温合金的发展历程
760℃高温材料发展过程从20世纪30年代后期起,为了满足新型发动机的需要,在第二次世界大战期间,高温合金的研究进入了蓬勃发展时期。
40年代初,英国首先在80镍-20钴合金中加入少量铝和钛,研制成第一种具有较高高
温强度的镍基合金。
同一时期,美国为了适应航空活塞式发动机用涡轮增压器
发展的需要,开始采用钴基合金制作叶片。
此外,美国还研制出用以制作喷气发动机的燃烧室的镍基合金。
以后,冶
金学家为了进一步提高合金的高温强度,在镍基合金中加入钨、钼、钴等元素,增加铝、钛含量,研制出一系列牌号的合金,但由于钴资源缺乏,钴基高温合
金发展受到限制。
40年代,铁基高温合金也得到了发展,50年代出现A-286和Incoloy901
等牌号,但因高温稳定性较差,从60年代以来发展较慢。
苏联于1950年前后
开始生产镍基高温合金,后来生产变形高温合金和铸造高温合金。
中国从1956
年开始试制高温合金,逐渐形成变形高温合金和铸造高温合金。
70年代美国还
采用新的生产工艺制造出定向结晶叶片和粉末冶金涡轮盘,以适应航空发动机
涡轮进口温度不断提高的需要。
三、高温合金的分类
(1)按基体元素来分:铁基高温合金、镍基高温合金和钴基高温合金。
其
中铁基高温合金适合的温度在600~800℃,镍基高温合金适用于650~1000℃范
围内的温度;钴基高温合金适合730~1100℃,但由于钴是一种重要的战略资源,致使钴基合金的发展受到限制。
目前镍基高温合金应用较广泛。
(2)按强化方式:固溶强化型,沉淀强化型,氧化物弥散强化型以及纤维
强化型等。
(3)按制备工艺:变形高温合金,铸造高温合金以及粉末冶金高温合金。
四、高温合金的加工难点及方法
1、切削加工高温合金的难点:(1)耐高温性能直接提高了加工难度;(2)在加工时重切削力以及产生的高温的共同作用下,刀具容易产生碎片或变形,
或者导致刀具断裂;(3)大多数高温合金都会迅速产生加工硬化现象,从而影响工件的表面精度。
2、高温合金的加工方法:(1)尽量在工件硬化前加工合金;(2)使用锋利的锐角切刃的刀具;(3)使用强度高的几何外形的刀具;(4)采取提高钢
度措施的刀具。
目前。
可切削加工高温合金的刀具材料有硬质合金刀具,涂层刀具,陶瓷
刀具,立方氮化硼刀具,由于其硬质合金刀具和涂层硬质合金刀具的硬度低,
抗变形能力差,适合加工硬度较低的高温合金。
陶瓷刀具可以切削加工高温合金,但只适合精加工工序。
但陶瓷刀具更易
于产生缺口和碎片,尤其是在加工表面带有砂垢的铸件时,更容易产生这种现象。
在切削加工高温合金等高硬度合金材料时,常采用立方氮化硼刀具。
立方
氮化硼刀具是目前加工黑色金属材料最佳的刀具材料。
虽说立方氮化硼刀具的
价格较高,但切削加工高温合金确实相较于硬质合金刀具、涂层刀具和陶瓷刀
具效果要好。
五、切削加工高温合金的立方氮化硼刀具
目前,国内切削加工高温合金的立方氮化硼刀具主要是以华菱超硬为代表
的非金属粘合剂立方氮化硼刀具。
华菱超硬针对高温合金的难加工问题及传统
刀具切削加工高温合金零件出现的问题,研制出高效切削加工高温合金的立方
氮化硼刀具BN-K11牌号和BN-S200牌号,均属于精加工牌号,其中立方氮化硼刀具BN-K11牌号吃刀深度控制在0.3mm以内为好。
下面简单介绍一下华菱超硬立方氮化硼刀具切削加工高温合金零件的案例。
六、华菱超硬立方氮化硼刀具切削加工高温合金的案例
1、华菱超硬立方氮化硼刀具BN-K11牌号加工医疗器械的案例
加工零件:髋关节支承盖
加工材料:钴基合金;
硬度:HRC35;
加工工序:精加工工序;
刀具牌号:BN-K11牌号;
切削参数:ap=0.15mm;
Fr=0.10mm/r;
Vc=210m/min.
加工方式:干式切削
加工效果:与某欧系品牌PCBN刀片相比(如下图):不仅切削速度高于某欧系品牌PCBN刀片,而且刀具寿命也高于某欧系品牌PCBN刀片。
(2)华菱超硬立方氮化硼刀具BN-S200牌号加工镍基高温合金案例
加工对象材料:镍基合金 Inconel 718 ;
加工镍基合金硬度:HRC45-HRC47(沉淀硬化态镍基合金);
刀具材质牌号:BN-S200牌号圆形CBN刀片RNGN120400;
加工工序: 精加工;
切削速度: 350 m/min;
进给量: 每转0.15 mm/rev(此参数下镍基合金精加工后表面粗糙度Ra0.3-Ra0.4);
切削深度(单边背吃刀量): 0.5 mm;
七、总结
随着现代技术的不断发展,越来越多的难加工材料出现,为了获得好的加工效率,机械加工商一直在寻找可高效加工难加工工件的刀具材料,这对刀具行业来说,只要研制出高质量高效率的刀具材料或刀具牌号,就可占据刀具市场,而且推动中国机械制造业的发展。