回转窑设计方案手册
回转窑设计方案手册

回转窑的设计一、窑型和长径比1.窑型所谓窑型是指筒体各段直径的变化。
按筒体形状有以下几种窑型:(1)直筒型:制造安装方便,物料在窑内移动速度较均匀一致,操作控制较易掌握,同时窑体砌造及维护较方便;(2)热端扩大型:加大单位时间内燃烧的燃料量及传热量,在原窑直径偏小的情况下,扩大热端将相应提高产量,适用于烧成温度高的物料;(3)冷端扩大型:便于安装热交换器,增大干燥受热面,加速料浆水分蒸发,降低热耗及细尘飞损,适用于处理蒸发量大、烘干困难的物料;(4)两端扩大型(哑铃型):中间的填充系数提高,使物料流动的机会减少,还可以节约部分钢材;还有单独扩大烧成带或分解带的“大肚窑”,这种窑型易挂窑皮,在干燥带及烧成带能力足够时,可以显著提高产量。
但这种窑型操作不便。
总之,不论扩大哪一带,必须保持预烧能力和烧结能力趋于平衡。
只有在生产窑上,经过生产实践和充分调查研究(包括必要的热工测定和计算),发现某一带确为热工上的薄弱环节,在这种特定条件下将该带扩大,才会得出较明显的效果。
目前国内外发展趋势仍以直筒型窑为主,而且尺寸向大型方面发展。
其他有色金属工业用回转窑(还原、挥发、硫化精矿焙烧、氯化焙烧、离析、烧结转化等)多采用较短的直筒窑。
2.长径比要得长径比有两种表示方法:一是筒体长度L与筒体公称直径D之比;另一是筒体长度L与窑的平均有效直径D均之比。
L/D便于计算,L/D均反映要的热工特点更加确切,为了区别起见,称L/D均为有效长径比。
窑的长径比是根据窑的用途、喂料方式及加热方法来确定的。
根据我国生产实践的不完全统计,各类窑的长径比示于表1中。
长径比太大,窑尾废气温度低,蒸发预热能力降低,对干燥不利;长径比太小,则窑尾温度高,热效率低。
同类窑的长径比与窑的规格有关,小窑取下限,大窑取上限。
表1各类窑的长径比窑的名称公称长径比有效长径比氧化铝熟料窑(喷入法)20~2522~27氧化铝焙烧窑20~2321.5~24碳素煅烧窑13.5~1917~24干法和半干法水泥窑11~15——湿法水泥窑30~42——单筒冷却机8~12——铅锌挥发窑14~1716.7~18.3铜离析窑——15~16氯化焙烧窑——12~17.7二、回转窑的生产率回转窑生产是一个综合热工过程,其生产率受多方面因素影响。
回转窑方案
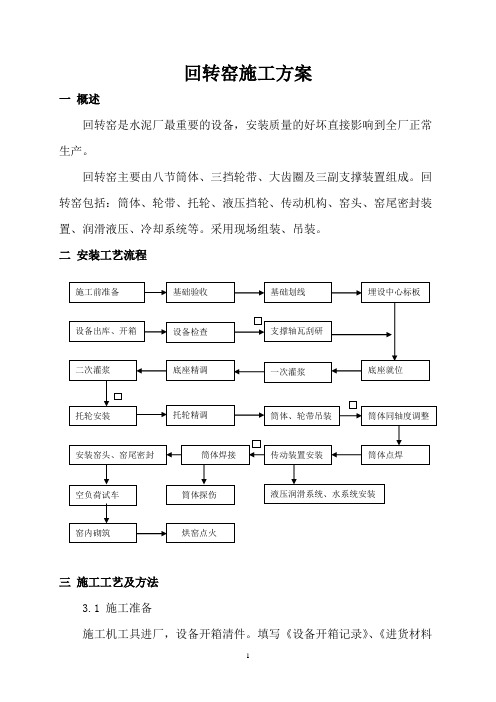
回转窑施工方案一概述回转窑是水泥厂最重要的设备,安装质量的好坏直接影响到全厂正常生产。
回转窑主要由八节筒体、三挡轮带、大齿圈及三副支撑装置组成。
回转窑包括:筒体、轮带、托轮、液压挡轮、传动机构、窑头、窑尾密封装置、润滑液压、冷却系统等。
采用现场组装、吊装。
二安装工艺流程三施工工艺及方法3.1 施工准备施工机工具进厂,设备开箱清件。
填写《设备开箱记录》、《进货材料验证记录》。
搭建临时设施,为施工作好准备。
3.2基础验收与划线设备安装前,混凝土基础应验收,验收合格后,方能进行安装。
提交的基础,必须达到下列要求:所有遗留的模板和露出混凝土外的钢筋,必须清除,并将设备安装现场及地脚孔内碎料、赃物及积水全部清理干净。
3.3埋设标板3.3.1中心标板在基础两端每条中心线上,便于安装找正的部位各埋设一块标板。
标板采用200×100×6-10mm的钢板制作。
用膨胀螺栓固定,钢板上用红油漆标出中心线。
3.3.2标高标板在每个窑墩的四角均埋设用作沉降标志的标高板。
采用φ15mm圆钢与80×80×10mm钢板焊接而且其圆顶顶呈半圆形。
埋设件必须埋设牢固,每个窑敦4个标高点在同一标高上,误差不大于0.5mm。
3.3.3在窑头、窑尾厂房内也各设置1个标高点,用于监测基础的沉降。
3.3.4划出回转窑的纵横中心线相邻两基础横向中心线间距允许偏差不大于±1.5mm。
首尾两基础横向中心线间距允许偏差不大于±6mm。
横向中心线的检查,采用对角线测量法,其目的不会产生平行四边形,减小误差,保证安装质量。
在放线时,钢卷尺应与弹簧秤配合使用,使钢盘尺受到相同张力,减少挠度的影响。
根据厂区标准水准点,测出基础上面基准点标高,作为安装设备的基准点,其偏差≤±1mm。
定期检查混凝土基础下沉情况。
在所有偏差均达到要求之后,所有预埋标板上打上样冲眼并作明显标记,成为永久性标记。
回转窑施工方案

回转窑主要施工方案设备及零件制作方案:考虑设备制作完毕后需要运输及现场安装等因素,施工场地制作主要是钢板卷制及部分筒体组对等。
筒体的圆周长应不超过两块钢板拼成,筒体的焊缝采取埋弧自动焊,筒体的对接焊缝外观应符合《焊接通用技术条件》的规定,对接焊缝应按GB11345-89标准进行10%的Ⅱ级探伤抽查,重点检查各纵、环焊缝的交叉点。
回转窑每台筒体制作总长100米,根据钢板尺寸分段加工制作,每段筒体未加支撑前椭圆度不大于5mm,长度差不超过2mm,两口周长差不大于3mm,相邻段周长差不超过5 mm。
冷却机每台筒体制作总长46米,根据钢板尺寸分段加工制作,每段筒体未加支撑前椭圆度不大于5mm,长度差不超过2mm,两口周长差不大于3mm,相邻段周长差不超过5 mm。
卷板时,调成慢速,尽量一次匀速卷成,中间注意测量并消除筒体自重影响,焊接完成,去掉搭接板磨平焊疤,再上卷板机,上滚筒压力逐圈减轻,同时筒体两侧支以转胎,滚动几个整圈以释放应力,并及时进行测量,对个别地方弧度不合适者,适度加以调整,务使无死弯或直边现象,用内弧样板测量,其最大间隙不大于 6MM 为宜。
卷板时,先压出合适曲率的板端,割除直板段,然后多次落辊,滚压成合适曲率的筒片;滚压过程中前后要有接应,以防折死板。
筒节组对在定圆地板上进行,不加外力状态下达到规定圆度后,点固纵缝,临时支撑牢固再翻转进行焊接。
焊毕圆度精找,支撑加固。
筒节圆度的检查采用了在筒节外部挂线,测量外径检查圆度的方法。
具体做法是将筒节放置在临时托轮上,在该筒节的两端口各挂一个通过筒节圆心点的线坠,将筒节两端口圆周各自均分为8等分,利用均分出来的各点,在筒节外表面做出8条母线,将相应的两条母线处在水平位置时,在筒节两侧(母线位置上)挂两条平行于筒节的钢丝线,钢丝线距筒节圆心的距离应始终保持一致,此时可用钢板尺量出两条水平母线距钢丝线的各点的距离。
以此方法,不断地转动筒节,量出所有母线距钢丝线的距离。
回转窑说明书
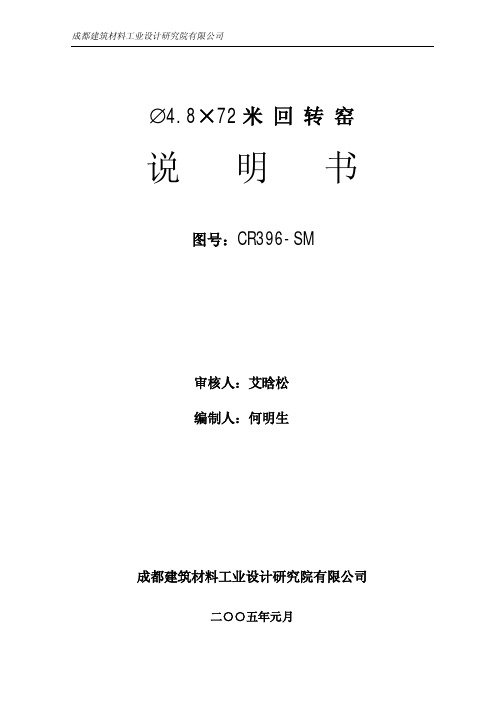
成都建筑材料工业设计研究院有限公司∅4.8×72米回转窑说明书图号:CR396-SM审核人:艾晗松编制人:何明生成都建筑材料工业设计研究院有限公司二○○五年元月目录一、技术性能 (2)二、结构概述 (2)三、安装要求 (4)(一)、核对基础及基础划线 (4)(二)、支承装置的安装 (5)(三)、筒体焊接和安装 (6)(四)、传动装置的安装 (8)(五)、其它部件的安装 (9)(六)、耐火砖砌筑要求 (9)四、操作维护及检修 (10)(一)、回转窑的试运转 (10)(二)、回转窑正常运转的维护 (11)(三)、停窑及检查 (16)(四)、回转窑的检修 (19)1一.技术性能回转窑筒体内径 4.8米回转窑筒体长度 72米回转窑筒体斜度 3.5%回转窑支承数 3档回转窑生产能力 5000吨水泥熟料/日回转窑转速主传动(正常)0.398~3.981转/分辅助传动(慢)0.19转/分传动电机:主传动辅助传动型号功率(千瓦) 转速(转/分) 型号功率(千瓦) 转速(转/分) ZSN4-400-22 630 1000 Y280S-4 75 1480减速机:主传动辅助传动型号速比型号速比ZSY630-31.5-Ⅴ30.73 ZSY315-31.5-Ⅱ30.52重量:回转窑总重(不包括筒体耐火砖和窑头耐火砖): 889 T大型起吊件重量:筒体大段节 24.35~65.65 T轮带 45.25~57.99 T支承装置 65.26~90.60 T大齿圈装置 31.81 T减速机 7.2 T二.结构概述φ4.8×72m回转窑由窑筒体部分、三档支承装置、传动装置、液压挡轮装置、窑头罩及密封装置、窑尾密封装置、主减速机油站、液压挡轮油站等组成。
筒体采用GB713的锅炉钢20g钢板卷制而成,全部采用自动焊焊接。
筒体壁厚一般为24毫米,轮带下为75、80、75毫米,过渡带为42、(55、42)、42毫米,从而能保证筒体有较好刚性。
φ4.8×72m回转窑维修手册(编写案例)概要

回转窑维修手册1目录第一章技术性能................................................... (3)1. 技术参数 (3)2.回转窑部件起吊重量...................................................... 4 第二章结构及工作原理概述 (5)1. 工作原理 (5)2.结构概述........................................................................ 5 第三章设备周期维修 (7)1. 筒体及轮带更换 (7)2. 大齿圈翻面维修 (19)3. 托轮瓦维修 (22)4. 液压挡轮维修 (25)5. 主减速机维修.................................................................. 29 第四章易损件表............................................................... 33 第五章回转窑托轮发热处理预案 (35)2本篇内容以南宁公司的天津院窑型为参照物。
第一章、技术性能1、技术参数筒体规格(内径 *长度 :¢4.8×72m斜度(正弦 :3.5%支承数: 3挡生产能力(配窑外预分解系统 : 5000t/d转速:主传动:0.41~4.1r/min辅助传动: 11.19r/h2、回转窑部件起吊重量:筒体总重量:328.25T ; 最大筒体段节重量:65.7T3筒体内衬总重量:668.726T第Ⅲ挡第Ⅱ挡第Ⅰ挡轮带:第Ⅰ挡:45T ; 第Ⅱ挡:57.6T ; 第Ⅲ挡:46.3T 窑头密封: 4.725T 窑尾密封: 9.832T大齿圈装置:齿数:188,模数 40,齿宽:550mm ,外径:¢7520mm 。
回转窑Φ4872m施工方案
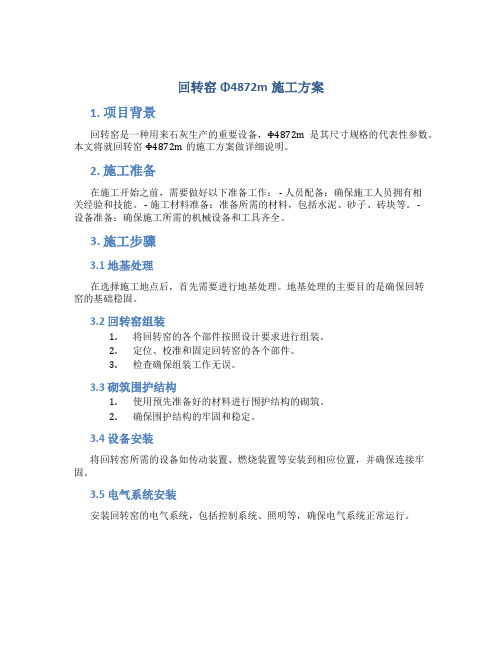
回转窑Φ4872m施工方案1. 项目背景回转窑是一种用来石灰生产的重要设备,Φ4872m是其尺寸规格的代表性参数。
本文将就回转窑Φ4872m的施工方案做详细说明。
2. 施工准备在施工开始之前,需要做好以下准备工作: - 人员配备:确保施工人员拥有相关经验和技能。
- 施工材料准备:准备所需的材料,包括水泥、砂子、砖块等。
-设备准备:确保施工所需的机械设备和工具齐全。
3. 施工步骤3.1 地基处理在选择施工地点后,首先需要进行地基处理。
地基处理的主要目的是确保回转窑的基础稳固。
3.2 回转窑组装1.将回转窑的各个部件按照设计要求进行组装。
2.定位、校准和固定回转窑的各个部件。
3.检查确保组装工作无误。
3.3 砌筑围护结构1.使用预先准备好的材料进行围护结构的砌筑。
2.确保围护结构的牢固和稳定。
3.4 设备安装将回转窑所需的设备如传动装置、燃烧装置等安装到相应位置,并确保连接牢固。
3.5 电气系统安装安装回转窑的电气系统,包括控制系统、照明等,确保电气系统正常运行。
4. 施工质量控制在整个施工过程中,需要进行严格的质量控制,确保施工质量符合设计要求。
主要包括对地基处理、回转窑组装、围护结构砌筑、设备安装和电气系统安装等方面进行检查和验收。
5. 施工安全措施在施工过程中,需要严格遵守施工安全规定,采取必要的安全措施,确保施工人员和设备的安全。
主要包括施工现场的安全防护、人员安全培训等。
6. 施工总结回转窑Φ4872m是一个较大型的设备,在施工过程中需要精心安排、严格控制质量,并确保施工安全。
只有如此,才能保证回转窑的正常运行和生产效率。
以上就是回转窑Φ4872m的施工方案,希望对相关人员能够有所帮助。
回转窑改进设计毕业设计

欢迎阅读引言风水冷却式回转窑,广泛用作水泥、镁砂和石灰石等块状和粉状材料的锻烧。
其特点是窑头处筒体采用可以喷入风水混合物的冷却筒和用集料包围窑头法兰以达到冷却筒体、防止筒体和法兰被烧坏的目的。
此风水冷却式回转窑具有结构简单合理、成本低、耐高温、寿命长等特点。
1回转体设计1.1回转体说明部分1.1.1由L/D=48/3=16.查《建材机械与设备》下册P67表18-5可知支点权取3.1.1.2支点位置的确定据《建材机械与设备》下册P67窑头悬伸段τ 1 /D≤1.5 τ 1 ≤1.5D≤1.5×3≤4.5m窑尾悬伸段τ 2 /D≈3 τ 2 ≈3D≈3×3≈9m烧成带τ 3 /D=4.5~5.5 τ 3 =(4.5~5.5)D=13.5~16.5m参照同规格、同类型的窑取τ 1 =3.5m τ 2 =7.5m τ 3 =18.5m1.1.3筒体钢板厚度的确定据《建材机械与设备》下册P65图18-54轮带下筒体厚δ1 =0.015D=0.045m过度段筒体厚δ2 =0.01D=0.03m烧成跨跨间筒体厚δ3 =0.007D=0.021m普通跨间筒体厚δ4 =0.006D=0.018m参照同规格、同类型的窑取δ1 =40mm δ2 =25mm δ3 =δ4 =22mm1.1.4筒体材质的选择采用A3 钢卷焊而成.1.1.5钢板宽度和长度的选择据《建材机械手册》第一卷P3-84表3-1-43.选四种不同宽度的钢板:B1 =2.5m B2 =2m B3 =1.5m B4 4=1m由筒体周长s=πD=3.14×3=9.42m,每节筒体用两块长5m的钢板卷焊而成.1.1.6钢板的排列如图:1.1.7垫板焊接在筒体上尺寸取宽B′=200mm,厚δ′=40mm,长1300mm或1100mm,垫板间距200~400mm.1.1.8筒体的结构筒体上没有挡砖圈,取样孔,档水圈,窑口护板,风冷套等各种附件.筒体为直筒式,在窑尾做成锥形收口,以防回料.2 筒体的计算2.1载荷的计算画载荷图,参考教材《建材机械与设备》下册P70例18-1 取大齿圈重P4=120KN,窑尾集中载荷P5=50KN.另 q1 =72.2KN/m,q2 =97.5KN/m,q3 =86KN/m,q4 =50.8KN/m,q5 =50.8KN/m2.2支点弯矩的计算①支点Ⅰ的弯矩可由摇头悬伸段求出:2 MⅠ=-q1 τ 1 (τ 1 /2+τ 2 )-?q2τ 22 =-72.2×3.0×(3.0/2+0.5)-97.5×0.5/2=-445.3(KN·m)②支点Ⅲ的弯矩可由窑尾悬伸段求出:2 -50×7.5=-1804(KN·m)MⅢ=-?q5 τ 25 -p5 τ 5 =-?×50.8×7.5③支点Ⅱ的弯矩由简化后的三弯矩方程式求出:MⅡ=(-6Bф1 -6Aф1 -τ3MⅠ-τ4MⅢ)/2(τ 3 +τ 4 )={-6×q3 /24×τ 33 -6×[P4 ×(18.5-3)×3×(18.5+3)÷6τ 4 ]-τ 3 MⅠ-τ 4 MⅢ}/2(τ3 +τ4 )={-?×86×18.53 -6[50.8/24×18.53 +120×15.5×3×21.5÷(6×18.5)]-18.5×(-445.3)-18.5×(-1804)}/2×(18.5+18.5)=-2452(KN·m)2.3支反力的计算①支点Ⅰ的反力RⅠ?0 =q1 τ 1 +q2 τ 2 =72.2×3+97.5×0.5=265.35(KN)RⅠ?Ⅰ可由τ 3 跨(Ⅰ-Ⅱ跨)求得,对静定基础上的Ⅱ点取矩。
回转窑手册

导读:回转窑作为煅烧活性石灰的窑炉,随着钢铁冶炼工艺发展的需要,经过长期的生产实践表明,它在满足钢铁冶炼需要的同时,亦在其它冶金行业中充分地体现出了它在大工业生产中的优越性和可持续发展的远景。
活性石灰产品,在钢铁企业特别是在转炉炼钢中被广泛的使用,用作造渣剂。
在缩短冶炼时间,提高产品质量,优化冶炼技术,提高经济效益等方面都发挥出了极其重要的作用。
随着回转窑操作技术和活性石灰煅烧工艺的发展和需要,如何更进一步地提高、完善和统一对回转窑操作知识的认识,达到理论与实践有机结合的目的,仍是活性石灰煅烧技术发展过程中不可忽视的课题。
坚持遵循理论理念,是提高回转窑操作水平的基本保证。
在生产实践中探索积累经验,是提高回转窑操作水平的有效手段。
在有关专家,工程技术人员的帮助下、在生产操作人员的配合下。
以贴近生产实际为主导,围绕回转窑的操作和活性石灰煅烧工艺,收集,整理汇编了《活性石灰回转窑操作手册》。
借此而达到提高操作技术水平,稳定生产运行,增强生产意识,完善生产管理,推进技术进步的目的。
目录前言第一部分、回转窑基础理论部分第一章、活性石灰一、石灰二、活性石灰三、活性石灰质量要求第二章、煅烧活性石灰的原料一、原料的选择二、理化指标第三章、燃料与燃料燃烧一、燃料二、热值三、燃料燃烧四、空气与燃烧五、热量换算第四章、传热第五章、活性石灰的煅烧设备一、回转窑二、竖式预热器三、竖式冷却器四、燃烧器五、排烟机六、收尘器第六章、活性石灰的煅烧一、活性石灰的煅烧机理二、活性石灰的煅烧过程第二部分、回转窑操作基础部分第七章、回转窑的点火操作一、点火前的检查二、点火前的准备三、点火操作第八章、烘窑与升温一、烘窑升温的目的二、烘窑升温曲线三、窑况四、烘窑五、升温第九章、回转窑的加料操作第十章、回转窑的生产操作第十一章、回转窑的火焰调整第十二章、回转窑与结圈活性石灰回转窑操作手册前言回转窑作为煅烧活性石灰的窑炉,随着钢铁冶炼工艺发展的需要,经过长期的生产实践表明,它在满足钢铁冶炼需要的同时,亦在其它冶金行业中充分地体现出了它在大工业生产中的优越性和可持续发展的远景。
水泥熟料回转窑设计说明书
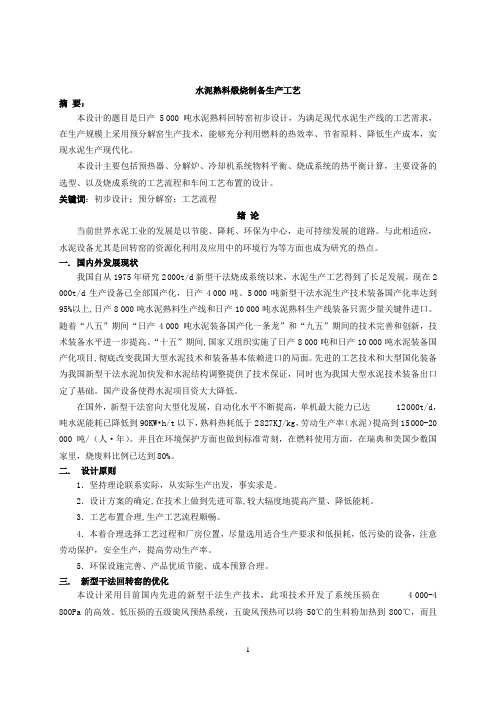
水泥熟料煅烧制备生产工艺摘要:本设计的题目是日产5000吨水泥熟料回转窑初步设计,为满足现代水泥生产线的工艺需求,在生产规模上采用预分解窑生产技术,能够充分利用燃料的热效率、节省原料、降低生产成本,实现水泥生产现代化。
本设计主要包括预热器、分解炉、冷却机系统物料平衡、烧成系统的热平衡计算,主要设备的选型、以及烧成系统的工艺流程和车间工艺布置的设计。
关键词:初步设计;预分解窑;工艺流程绪论当前世界水泥工业的发展是以节能、降耗、环保为中心,走可持续发展的道路。
与此相适应,水泥设备尤其是回转窑的资源化利用及应用中的环境行为等方面也成为研究的热点。
一. 国内外发展现状我国自从1975年研究2000t/d新型干法烧成系统以来,水泥生产工艺得到了长足发展,现在2 000t/d生产设备已全部国产化,日产4000吨、5000吨新型干法水泥生产技术装备国产化率达到95%以上,日产8000吨水泥熟料生产线和日产10000吨水泥熟料生产线装备只需少量关键件进口。
随着“八五”期间“日产4000 吨水泥装备国产化一条龙”和“九五”期间的技术完善和创新,技术装备水平进一步提高。
“十五”期间,国家又组织实施了日产8000吨和日产10000吨水泥装备国产化项目,彻底改变我国大型水泥技术和装备基本依赖进口的局面。
先进的工艺技术和大型国化装备为我国新型干法水泥加快发和水泥结构调整提供了技术保证,同时也为我国大型水泥技术装备出口定了基础。
国产设备使得水泥项目资大大降低。
在国外,新型干法窑向大型化发展,自动化水平不断提高,单机最大能力已达12000t/d,吨水泥能耗已降低到90KW•h/t以下,熟料热耗低于2827KJ/kg,劳动生产率(水泥)提高到15000-20 000吨/(人·年)。
并且在环境保护方面也做到标准苛刻,在燃料使用方面,在瑞典和美国少数国家里,烧废料比例已达到80%。
二. 设计原则1.坚持理论联系实际,从实际生产出发,事实求是。
t新型干法水泥生产线回转窑工艺设计说明书

5000t新型干法水泥生产线回转窑工艺设计原始资料一、物料化学成分(%)成分Loss SiO2 AI2O3 Fe2O3 CaO MgO SO3 其它合计干生料100熟料0 100煤灰0 100、煤的工业分析及元素分析(%温度:900C ;出窑熟料温度:1360r ;废气出预热器温度:330C ;出预热器飞灰温度:300E 窑尾气体温度:1100C。
2、入窑风量比(%。
一次风(K 1):二次风(K2):窑头漏风(K3)=10:85:5 。
3、燃料比(%。
回转窑(Ky):分解炉(Kf) =40:60 。
4、出预热器飞灰量。
kg熟料。
5、出预热器飞灰烧失量。
%6各处空气过剩系数。
窑尾,a y=分解炉出口a L=预热器出口a f=。
7、入窑生料采用提升机输送。
8、漏风。
预热器漏风量占理论空气的比例K4=;提升机带入空气量忽略;分解炉及窑尾漏风(包括分解炉一次空气量),占分解炉用燃料理论空气量的比例K6=9、袋收尘器和增湿塔综合收尘效率为%10、熟料形成热。
根据简易公式(6-20)计算。
11、系统表面散热损失。
460kJ/kg熟料。
12、生料水分。
%13、窑的设计产量。
5000t/d。
四、物料平衡与热量平衡计算基准:1kg熟料,温度:0C;范围:回转窑+分解炉+预热器系统根据确定的基准和范围,绘制物料平衡图(图1)、热量平衡图(图2)。
图1物料平衡图图2热量平衡图物料平衡计算收入项目(1)燃料总消耗量m (kg/kg)其中:窑头燃料量m yr = K y m r (kg/kg)分解炉燃料量m Fr = K F m r (kg/kg)(2)生料消耗量、入预热器物料量a.干生料理论消耗量100 m r A y a 10025.71 1 m rgSL二100 L s= 100 35'2—(kg/kgm式中:a—燃料灰分掺入量,取100%b.出电收尘飞损量及回灰量m Fh= m fh(1 -)=x (1 —二(kg/kg)m yh = m fh —m h= — = (kg/kg)图1物料平衡图图2热量平衡图c.考虑飞损后干生料实际消耗量100 35.2 儿、s100 35.82d.考虑飞损后生料实际消耗量100 _ v100m s=m s (kg/kg)100 W s__入100 0.2e.入预热器物料量入预热器物料量_ m + m k_ —+_—(kg/kg)(3)入窑系统空气量燃料燃烧理论空气量V' LK_ ++(S — O)= x + x + x —_ (Nn i/kg 煤)m‘Lk_ V' Lk x_x_ (kg/kg 煤)b.入窑实际干空气量3 V/h= a y V' Lk n yr = a y Vl k K F m _ 1.05 xx_ (Nm /kg)n yk=x ^x (kg/kg)其中入窑一次空气量,二次空气量及漏风量01=«%= (Nm 3/kg)W _ k20_ (Nm 3/kg)V-Ok1_ K30 _ (Nm 3/kg)c.分解炉从冷却机抽空气量①出分解炉混合室过剩空气量V1_ ( a L— 1)V' Lk m_— 1) x = (Nm3/kg)②分解炉燃料燃烧空气量V2_ V'Lk m r _ V'Lk Km _x = (Nm 3/kg)③窑尾过剩空气量V3_ ( a y— 1)V' Lk m yr _ ( a y— 1)V' -Km _— 1) xx_ (Nm i/kg)④分解炉及窑尾漏入空气量3 V4 _ KVlkm _ K e VlKm _xx _ (Nm /kg)⑤分解炉冷却机抽空气量V F2k=V+V2 —V3—V4 _ +—— _ (Nm3/kg)m F2k_x V:2k = x (kg/kg)d. 气力提升泵喂料带入空气量(忽略)e. 漏入空气量预热器漏入空气量75= K 4V 1 Lk m r = (Nm 3/kg)窑尾系统混入空气总量V Lok2= V 4 + V 5 =+ = (Nm 3/kg) 全系统漏入空气量3V LOK = V L OK + V_OK2=X + =m °K =x V_OK =X = (kg/kg)支出项目(1) 熟料m sh =1kg (2) 出预热器废气量 a.生料中物理水含量W0.2mh= mx 100 = — x 100 =— (kg/kg)b.生料中化学水含量m is = =x — x = — (kg/kg)kS0.017 0.004m 「 0.804 =0.804c.生料分解放出CO 气体量:m wsVws = 0.8040.003 0.001叶0.8043(Nm /kg)3(Nm /kg)d.燃料燃烧生成理论烟气量V co2= 22.418224 x100 x60.10100m =(Nm i/kg)eM co2s M co2CO= CaO M CaO + MgO M44=x"56 +x44s CO2 L fhm co2=m gs〔0。
石灰回转窑技术规格书

第六章活性石灰回转窑技术规格书第一节概述1.1规模公司钒资源综合利用项目新建80万t/a活性石灰窑工程,包括一条800t/d的回转窑活性石灰生产线和三条600t/d的竖窑活性石灰生产线。
1.2原、燃料资源和成品石灰用途1.2.1石灰石所需石灰石原料均由业主自有的石灰石矿山提供,石灰石原料在矿山上破碎筛分并经过水洗后,其中:粒度在18~50mm的石灰石由汽车运输进厂后直接储存在石灰回转窑原料堆场内,以供1条800t/d活性石灰回转窑生产线使用;粒度在40~80mm的石灰石由汽车运输进厂,储存在石灰竖窑原料堆场内,以供3条600t/d活性石灰竖窑生产线使用。
石灰石性能指标表(%)注:石灰石粒度:18~50mm,其中大于50mm和小于18mm的总量不大于5%;水分含量:≤4%;1.2.2燃料采用高炉煤气、转炉煤气和焦炉煤气混合后的煤气作为热源物质,采用热值为3500kcal/Nm3煤气,压力为10Kpa,温度为常温。
典型煤气成份如下:1.2.3产品运输和用途①回转窑石灰经筛分后20~80mm的石灰由皮带运输至新区炼钢车间供炼钢转炉、精炼炉使用,年需要量约10万吨;供老区的石灰采用汽车运输,年需求量约10万吨。
小于20mm的石灰送入破碎线破碎成0~3mm石灰粉。
②0~3mm石灰粉一部分采用气力输送至烧结石灰料仓,供烧结用,年需求量约55.4万吨;一部分采用气力(或罐车)输送,供KR脱硫用,年需要量2.3万吨;供老区的石灰粉约2.3万吨,采用罐车运输。
1.3总图运输1.3.1地理位置项目所在地属亚热带湿润季风气候区,具有四季分明、气候温和、雨量充沛、云雾多、日照少、无霜期长等气候特点。
区内年平均气温17.8℃,极端最高气温38℃,极端最低气温-4℃;年平均无霜期297天。
年平均日照1010.1小时。
年平均降雨量994.7mm,降雨量按季节分布严重不均,70%以上降于夏、秋二季。
且夏季降水强度大,多大雨和暴雨。
机械毕业设计261750×12000回转窑设计说明书

┊┊┊┊┊┊┊┊┊┊┊┊┊装┊┊┊┊┊订┊┊┊┊┊线┊┊┊┊┊┊┊┊┊┊┊┊┊总论部分1. 现代磁性材料生产工艺的国内外发展现状及其发展趋势1.1磁性材料的分类磁性是物质的基本属性之一,在外磁场作用下,各种物质都呈现出不同的磁性。
磁性材料按其特性、结构和用途可分为软磁性材料、永磁性材料、磁记录材料、旋磁材料和非晶态软磁材料等。
软磁材料的磁性能的主要特点是磁导率高,矫顽力低。
属于软磁材料的品种有电工用纯铁、硅钢片、铁镍合金、软磁铁氧体和铁钴合金等,它们主要是作传递和转换能量的磁性零部件或器件。
永磁材料的磁性能的主要特点是矫顽力高,属于永磁材料的品种有铁镍钴、稀土钴、硬磁铁氧体等,它主要作用是在能够产生恒定磁通的磁路中,在一定空间内提供恒定的磁场作为磁场源。
1.2磁性材料的现状磁性材料作为一种重要的功能材料,广泛用于国民经济各个领域,在现今国民经济各个领域中扮演着一个重要的角色。
随着社会步伐的不断涌进,中国磁性材料又面临一次发展良机。
磁性材料作为电子行业的基础功能材料,永磁材料作为磁性材料的重要组成部分,在电子工业,电子信息产业、轿车工业、摩托车行业发挥着重要的作用,同时它还广泛用于医疗、矿山冶金、工业自动化控制、石油能源及民用工业。
永磁材料有永磁以及一切铁氧体瓷瓦、磁块、磁环、磁粉等,广泛用于各种微电机、扬声器、自动化装置、医疗机械、磁选设备以及一切需要恒定磁源的地方,用永磁代替电磁结构简单、使用可靠、节约能源、维护方便。
还有方形、圆形、圆柱、片状、条形、扇形、瓦形、环形等多种形状的永磁材料,可广泛用于耳机、听筒、微形发声器件、磁性纽扣、磁性门吸、玩具、马达、磁疗保健、电脑设备、电子零件等不同领域。
另外,采矿业、航天航空、高保真音响、电机等也是词性材料涉猎的对象。
由此可见,磁性材料对我们的生活各方面将越来越重要。
1.3.铁氧体磁性材料铁氧体磁性材料概述铁氧体磁性材料是近三十多年迅速发展起来的一种新型的非金属磁性材料。
焙烧回转窑技术方案
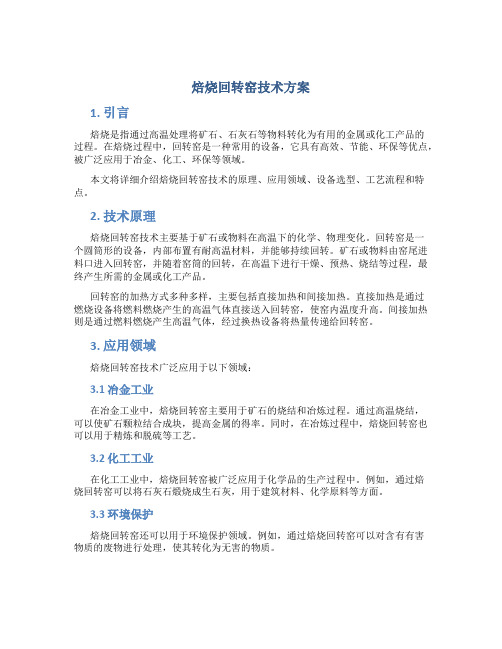
焙烧回转窑技术方案1. 引言焙烧是指通过高温处理将矿石、石灰石等物料转化为有用的金属或化工产品的过程。
在焙烧过程中,回转窑是一种常用的设备,它具有高效、节能、环保等优点,被广泛应用于冶金、化工、环保等领域。
本文将详细介绍焙烧回转窑技术的原理、应用领域、设备选型、工艺流程和特点。
2. 技术原理焙烧回转窑技术主要基于矿石或物料在高温下的化学、物理变化。
回转窑是一个圆筒形的设备,内部布置有耐高温材料,并能够持续回转。
矿石或物料由窑尾进料口进入回转窑,并随着窑筒的回转,在高温下进行干燥、预热、烧结等过程,最终产生所需的金属或化工产品。
回转窑的加热方式多种多样,主要包括直接加热和间接加热。
直接加热是通过燃烧设备将燃料燃烧产生的高温气体直接送入回转窑,使窑内温度升高。
间接加热则是通过燃料燃烧产生高温气体,经过换热设备将热量传递给回转窑。
3. 应用领域焙烧回转窑技术广泛应用于以下领域:3.1 冶金工业在冶金工业中,焙烧回转窑主要用于矿石的烧结和冶炼过程。
通过高温烧结,可以使矿石颗粒结合成块,提高金属的得率。
同时,在冶炼过程中,焙烧回转窑也可以用于精炼和脱硫等工艺。
3.2 化工工业在化工工业中,焙烧回转窑被广泛应用于化学品的生产过程中。
例如,通过焙烧回转窑可以将石灰石煅烧成生石灰,用于建筑材料、化学原料等方面。
3.3 环境保护焙烧回转窑还可以用于环境保护领域。
例如,通过焙烧回转窑可以对含有有害物质的废物进行处理,使其转化为无害的物质。
4. 设备选型在选型焙烧回转窑设备时,需要考虑以下因素:4.1 物料性质不同的物料具有不同的燃烧特性和热量传递特性,因此在选型设备时需要详细了解物料的物化性质。
4.2 产能要求根据焙烧生产线的产能要求,确定回转窑的尺寸和设计参数。
4.3 燃料种类和供应方式根据可用的燃料种类和供应方式,选择适合的回转窑加热方式。
5. 工艺流程焙烧回转窑的工艺流程一般包括以下几个步骤:5.1 进料与预热物料从窑尾进料口进入回转窑,同时在高温下进行干燥和预热,使其达到适合的烧结温度。
回转窑设计使用说明书
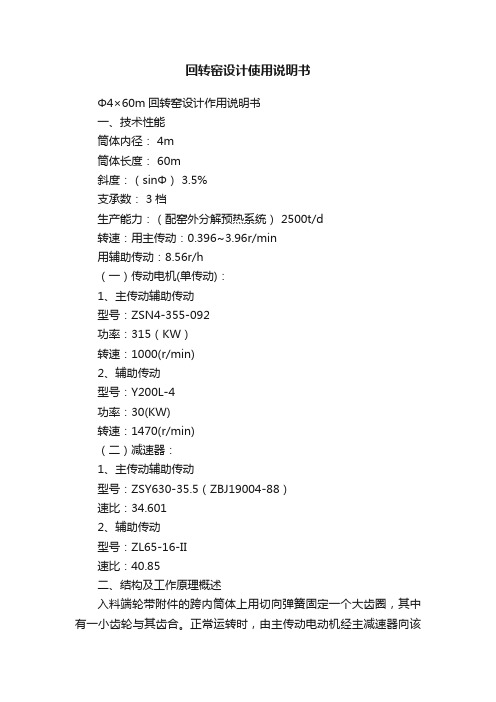
回转窑设计使用说明书Φ4×60m回转窑设计作用说明书一、技术性能筒体内径: 4m筒体长度: 60m斜度:(sinΦ) 3.5%支承数: 3档生产能力:(配窑外分解预热系统) 2500t/d转速:用主传动:0.396~3.96r/min用辅助传动:8.56r/h(一)传动电机(单传动):1、主传动辅助传动型号:ZSN4-355-092功率:315(KW)转速:1000(r/min)2、辅助传动型号:Y200L-4功率:30(KW)转速:1470(r/min)(二)减速器:1、主传动辅助传动型号:ZSY630-35.5(ZBJ19004-88)速比:34.6012、辅助传动型号:ZL65-16-II速比:40.85二、结构及工作原理概述入料端轮带附件的跨内筒体上用切向弹簧固定一个大齿圈,其中有一小齿轮与其齿合。
正常运转时,由主传动电动机经主减速器向该开式齿轮装置传递动力,驱动回转窑。
物料从窑尾(筒体的高端)进入窑内煅烧。
由于筒体的倾斜和缓慢的回转窑作用,物料既沿圆周方向滚动又沿轴向(从高端向低端)移动,继续完成分解和烧成的工艺过程,最后,生成熟料经窑头罩进入冷却机冷却。
燃料由窑头喷入窑内,燃烧产生的废气与物料进行热交换后,由窑尾导出,本设计不含燃料的燃烧器。
该窑在结构方面有以下主要特点:1、筒体采用保证五项机械性能(σs、σb &%、αk和冷弯实验)的镇静钢Q235-C钢板卷制,通常采用制动焊接。
筒体壁厚:一般为22mm,烧成带为25mm,轮带下为60mm、由轮带下到跨间有32mm、28mm厚的过渡段节,从而使筒体的设计更为合理,既保证横截面的钢性又改善了支承装置的受力状态。
在筒体进、出料端都装有耐高温、耐磨损的窑口护板。
其中窑头护板与冷风套组成环行分格的套筒空间,从喇叭口向筒体吹冷风冷却窑头护板的非工作面,以有利该部分的长期安全工作,当窑正常运转时,轮带能适度套在筒体上,以减少筒体径向变形。
回转窑筒体余热利用设计方案

回转窑筒体表面余热利用装置结构预设与运用一水泥回转窑筒体余热利用的研究现状山东泰安鲁润水泥制造有限公司利用了3.2× 52m回转窑筒体表面余热设计生产的热水生产装置代表了国内对回转窑表面余热利用的现状,该装置是利用水泥熟料烧成过程中回转窑筒体表面散热所产生的热量通过对流、辐射及传导等热作用由集热器吸收,从而产生可供职工浴室及生活用热水的一种热交换装置。
它主要包括集热器、进水管道、供水管道及储水箱4大部分。
自来水由水塔经进水管道至集热器加热后再通过集热器安装高度形成的高度差由供水管道输送至浴室、生活热水储水箱,然后进行使用。
该装置存在的不足之处:1、集热器安装在窑体上圆弧面,虽然有利于增强换热效果,但安装、维护不方便;集热器只能安装在放热带的右侧,窑体温度不高,同时回转窑表面温度最高的烧成带没有利用,余热利用率不高。
2、采用水塔间歇式供水,保证出水温度在100℃。
如果出水过多,集热器中水量过少,换热仍在不断进行,势必造成大量蒸汽产生,虽然集热器上部设计了排气孔,但会造成集热器的热变形加剧。
3、该设备虽然设计了电阻式温度计对内部水温进行检测,但没有建立自动调温系统,必须有专人值守,定期开关进水阀和检测水温。
4、间歇式供水并不能保证24小时的热水供应,使用效果有限。
二水泥回转窑筒体余热利用的性能设计有效利用窑外表面的散热量可有两条有效途径。
一是增大换热器与窑外表面的换热面积。
二是增加窑外表面与换热器表面的温度差。
该装置的设计还要具体考虑以下因素:(1)热交换位置的选择要合理回转窑筒体较长,在水泥熟料的煅烧过程中,各段温度差别较大。
烧成段的筒体温度最高平均在300~350℃,长度约占回转窑筒体长度的1/8~1/9左右。
分解带与放热反应带筒体表面温度平均在280~300℃,长度约占回转窑筒体长度的1/2左右。
干燥带和预热带筒体表面温度最低,平均在240~260℃,其长度约占回转窑筒体长度的1/5左右。
回转窑设计方案手册

回转窑的设计一、窑型和长径比1. 窑型所谓窑型是指筒体各段直径的变化。
按筒体形状有以下几种窑型:(1) 直筒型:制造安装方便,物料在窑内移动速度较均匀一致,操作控制较易掌握,同时窑体砌造及维护较方便;(2) 热端扩大型:加大单位时间内燃烧的燃料量及传热量,在原窑直径偏小的情况下,扩大热端将相应提高产量,适用于烧成温度高的物料;(3) 冷端扩大型:便于安装热交换器,增大干燥受热面,加速料浆水分蒸发,降低热耗及细尘飞损,适用于处理蒸发量大、烘干困难的物料;(4) 两端扩大型(哑铃型):中间的填充系数提高,使物料流动的机会减少,还可以节约部分钢材;还有单独扩大烧成带或分解带的“大肚窑” ,这种窑型易挂窑皮,在干燥带及烧成带能力足够时,可以显著提高产量。
但这种窑型操作不便。
总之,不论扩大哪一带,必须保持预烧能力和烧结能力趋于平衡。
只有在生产窑上,经过生产实践和充分调查研究(包括必要的热工测定和计算),发现某一带确为热工上的薄弱环节,在这种特定条件下将该带扩大,才会得出较明显的效果。
目前国内外发展趋势仍以直筒型窑为主,而且尺寸向大型方面发展。
其他有色金属工业用回转窑(还原、挥发、硫化精矿焙烧、氯化焙烧、离析、烧结转化等)多采用较短的直筒窑。
2. 长径比要得长径比有两种表示方法:一是筒体长度L与筒体公称直径D之比;另一是筒体长度L与窑的平均有效直径D均之比。
L/D便于计算,L/D均反映要的热工特点更加确切,为了区别起见,称L/D均为有效长径比。
窑的长径比是根据窑的用途、喂料方式及加热方法来确定的。
根据我国生产实践的不完全统计,各类窑的长径比示于表1中。
长径比太大,窑尾废气温度低,蒸发预热能力降低,对干燥不利;长径比太小,则窑尾温度高,热效率低。
同类窑的长径比与窑的规格有关,小窑取下限,大窑取上限。
二、回转窑的生产率回转窑生产是一个综合热工过程,其生产率受多方面因素影响。
分析其内在规律性,可以建立以下几个方面的数量关系。
回转窑方案

3200T/D水泥生产线机电设备安装工程①4.3 X6 6m回转窑安装工程施工方案编制:年月日审核:年月日批准:年月日X X X安装项目部零零七年七月空负荷试车G _安装窑头、窑尾密封筒体焊接r筒体探伤三次灌浆窑内砌筑—烘窑点火液压润滑系统、水 系统安装回转窑是水泥厂最重要的设备,安装质量的好坏直接影响到全厂正常生产, 为确保安装质量,特根据我公司多年安装回转窑的经验,编制以下施工方案。
本工程水泥熟料生产线回转窑直径© 4.3m ,长66 m ,重量约为600吨,生 产方法采用窑外分解形式。
筒体支承数 3个。
回转窑筒体分为7段,现场组装、 吊装。
回转窑包括:筒体、轮带、托轮、液压挡轮、传动机构、窑头、窑尾密封 装臵、润滑液压、冷却系统。
二、安装工艺流程:筒体、轮带吊装底座及托轮精调二次灌浆1rG筒体同轴度调整 G . 筒体点焊----- fc- 窑头罩就位传动装置安装关键工序:G 代表关键工序三、安装工艺及方法1. 施工准备熟悉施工图纸,进行图纸会审,熟悉施工环境,根据现场实际情况编制详细 的施工方案,进行技术交底;施工机工具进厂,设备开箱清件。
填写《设备开箱 记录》、《进货材料设备验证记录》。
2. 基础验收与划线设备安装前,混凝土基础应会同土建、监理、业主单位共同验收,验收合格基础外行尺寸:土 30mm 地脚螺栓孔深度:0〜20mm 基础上平面标咼: 0 — -20mm地脚螺栓孔垂直度:5/1000 中心线间距离:土1mm 地脚螺栓孔相互中心位臵:土 10mm 基础坐标位臵:土20mm 基准点标高对车间零点标高:土 3mm在基础两端每条中心线上,便于安装找正的部位各埋设一块标板。
标板采用膨胀螺栓后,方能进行安装。
验收范围:土建单位提供的中心线、标高点、基础外形尺寸、标高尺寸、基 础孔几何尺寸及相互位臵。
提交的基础,必须达到下列要求:所有遗留的模板和露出混凝土外的钢筋, 必须清除,并将设备安装现场及地 脚孔内碎料、赃物及积水全部清理干净并划好墨线。
- 1、下载文档前请自行甄别文档内容的完整性,平台不提供额外的编辑、内容补充、找答案等附加服务。
- 2、"仅部分预览"的文档,不可在线预览部分如存在完整性等问题,可反馈申请退款(可完整预览的文档不适用该条件!)。
- 3、如文档侵犯您的权益,请联系客服反馈,我们会尽快为您处理(人工客服工作时间:9:00-18:30)。
表 1 各类窑的长径比
窑的名称
公称长径比
有效长径比
氧化铝熟料窑 (喷入法 )
20~25
22~27
氧化铝焙烧窑
20~23
21.5~24
碳素煅烧窑
13.5~19
17~24
干法和半干法水泥窑
11~15
——
湿法水泥窑
30~42
——
单筒冷却机
8~12
——
铅锌挥发窑
14~17
16.7~18.3
铜离析窑
——
15~16
D 均—— 窑的平均有效内径,米;
ψ—— 物料在窑内的平均填充系数,一般为
0.04~0.12 。各类窑的填充系数见表 2。
γ料—— 物料堆比重,吨 /米;某些物料的堆比重见表 3;
ω 料 —— 物料轴向移动速度,米 /小时;其值取决于窑运转情况,可按式 (12) 、式 (13)
及式 (14)计算或测定。 表 2 各类窑的平均填充系数
Qi —— 窑内某一工作带中对物料的传热量,千卡 /小时;
q 料 —— 物料必须在窑内吸收的总有效热量,千卡 /吨;
[q 料]i —— 物料在某一工作带内必须吸收的有效热量,千卡 所谓有效热量指的是不考虑非生产性消耗和热损失的热量。
η ——窑的热效率,一般为 55~65% ;
q 料 —— 每吨产品必须消耗的有效热,千卡 / 吨。
q 料 =( G 干料 +A)(q 吸 +C×t 高 +600w/100-w) ×103 千卡 /吨 式中: G 干料 —— 每公斤产品理论消耗干生料量 (不包括水分 ) ,公斤 / 公斤;
A —— 每公斤产品不可返回的飞尘损失,公斤 /公斤
窑名称
平均填充系数 ψ
铜离析窑
0.06~0.08
铅锌挥发窑
0.04~0.08
氧化焙烧窑
0.04~0.07
氯化焙烧窑
0.04~0.07
氧化铝熟料窑
0.06~0.08
氧化铝焙烧窑
0.06~0.08
表 3 某些物料的堆比重
物料名称 锌浸出渣 锌浸出残渣与 50% 焦粉混合料 铅鼓风炉水碎渣与 50% 焦粉混合料 氯化铜矿 锌沸腾焙烧细尘 硫化镍精矿 硫化镍焙砂 氧化铝和干氢氧化铝 碱石灰铝土矿干生料 碱石灰铝土矿熟料
q 吸 —— 每公斤产品吸热反应吸热量 (除去放热反应放热量) ,千卡 /公斤;
C ×t 高 —— 将物料加热到最高温度 (烧成带 ) 所需物理热,千卡 /公斤; W—— 湿生料中所含水分, % 。
5. 按窑内传热能力 : G=∑ Q÷q料 或 G=Qi [q ÷料 ]i 千卡 /小时 (5) 式中: ∑Q—— 窑内各带对物料的总给热量,千卡 / 小时;
堆比重 1.6~1.65 1.2~1.3 1.4~1.5 1.16 1.80 1.6~1.8 1.2~2.0 1.0 1.2 1.3~1.4
2. 按物料反应时间 有些工艺过程要求物料有一定的高温持续时间,以完成物理化学反应。若通过实验或
生产实践得知物料必须在窑内停留的时间, 则 :G=0.785×L/ τ×均D 2×ψ×料γ 吨 /小时 (2) 式中: L—— 窑长 ( 或某带长度 ) ,米; τ ——物料在窑内(或某带)停留时间,小时; 其他符号同前。 3. 按正常排烟能力
总之,不论扩大哪一带,必须保持预烧能力和烧结能力趋于平衡。只有在生产窑上,经 过生产实践和充分调查研究 (包括必要的热工测定和计算 ),发现某一带确为热工上的薄弱环 节,在这种特定条件下将该带扩大,才会得出较明显的效果。
目前国内外发展趋势仍以直筒型窑为主,而且尺寸向大型方面发展。其他有色金属工业 用回转窑 (还原、 挥发、 硫化精矿焙烧、 氯化焙烧、 离析、 烧结转化等 )多采用较短的直筒窑。
回转窑的设计
一、窑型和长径比
1. 窑 型 所谓窑型是指筒体各段直径的变化。按筒体形状有以下几种窑型:
(1) 直筒型:制造安装方便,物料在窑内移动速度较均匀一致,操作控制较易掌握,同时窑 体砌造及维护较方便;
(2) 热端扩大型:加大单位时间内燃烧的燃料量及传热量,在原窑直径偏小的情况下,扩大 热端将相应提高产量,适用于烧成温度高的物料;
(3) 冷端扩大型:便于安装热交换器,增大干燥受热面,加速料浆水分蒸发,降低热耗及细 尘飞损,适用于处理蒸发量大、烘干困难的物料;
(4) 两端扩大型 (哑铃型 ):中间的填充系数提高,使物料流动的机会减少,还可以节约部分 钢材;还有单独扩大烧成带或分解带的 “大肚窑 ” ,这种窑型易挂窑皮,在干燥带及烧成带 能力足够时,可以显著提高产量。但这种窑型操作不便。
2. 长径比 要得长径比有两种表示方法: 一是筒体长度 L 与筒体公称直径 D 之比; 另一是筒体长
度 L 与窑的平均有效直径 D 均之比。 L/D 便于计算, L/D 均反映要的热工特点更加确切, 为了区别起见,称 L/D 均为有效长径比。 窑的长径比是根据窑的用途、喂料方式及加热方 法来确定的。 根据我国生产实践的不 完全统计, 各类窑的长径比示于表 1 中。长径比太大, 窑尾废气温度低, 蒸发预热能力降低, 对干燥不利; 长径比太小, 则窑尾温度高, 热效率低。 同类窑的长径比与窑的规格有关,小窑取下限,大窑取上限。
氯化焙烧窑
——
12~17.7
二、回转窑的生产率 回转窑生产是一个综合热工过程,其生产率受多方面因素影响。分析其内在规律性,
可以建立以下几个方面的数量 关系。
1 / 10
1. 按窑内物料流通能力: G=0.785D 均 2×ψ×料ω×γ料 吨 /小时 (1) 式中:
G —— 单位生产率,吨 /小时;2 / 10 ψ干 —— 干燥带物料填充系数;
D 均干 —— 干燥带平均有效内径,米。
4. 按供热能力
G=K B×Q 低×η×/料q 吨 /小时 (4) 式中: B—— 燃料消耗量,公斤 /小时或标米 3/小时;
Q 低 —— 燃料低发热量,千卡 /公斤或千卡 / 标米 3;
K —— 系数,对铝厂用窑预热二次空气时, K=1.1~1.15 ;不预热时, K = 1.0 ;