液体动压径向滑动轴承设计与分析
滑动轴承设计案例

13-9设计案例设计一机床用的液体动压润滑径向滑动轴承,载荷垂直向下,工作情况稳定,采用剖分式轴承。
已知工作载荷F=100000N,轴颈直径d=200mm,转速n=400r/min,在水平剖分面单侧供油。
解:一、选择轴承结构和材料选择正剖分式径向滑动轴承,由水平剖分面单侧供油,轴承包角β=180°,轴承材料按p≤[p],v≤[v],pv≤[pv]进行选取。
1)选择轴承宽径比通常宽径比在0.3~1.5范围内,根据机床常用的宽径比范围,取宽径比B/d=12)计算轴承宽度mmd d B B 2002001=⨯=⨯=)/(3)计算轴颈圆周速度sm dn/.194100060400200100060=⨯⨯⨯=⨯=ππν4)计算轴颈平均压力MPa dB F p 522020100000...=⨯==5)计算pv值MPapv/ms4195102⨯.=5.=.⋅6)选择轴瓦材料查常用金属轴承材料性能表,在保证p≤[p],v≤[v],pv≤[pv] 的条件下,选定轴承材料为ZCuSn10Pl1)初估润滑油粘度 二、承载能力计算s Pa n ⋅===--03601060400106067316731.)/()/('////η2)计算相应的运动粘度 取润滑油密度 3900mkg /=ρs mm m kg s Pa /.)/()(''26634010900036010=⨯=⨯⋅=ρηυ3)选定润滑油牌号参照表选定全损耗用油L-AN684)初选平均油温现选平均油温t m =50℃5)按t m =50℃查出L-AN68的运动粘度为 s mm /25040=υ6)换算出L-AN68于50℃时的运动粘度sPa ⋅≈⨯⨯==-0360104090065050.ρυη7)计算相对间隙 4/94/931/931/9(/60)(400/60)0.000841010n ψ≈=≈8)计算轴承量系数 221000000.00084 1.17220.036 4.190.2P F C vB ψη⨯===⨯⨯⨯9)求出轴承偏心率根据C P 及B/d 的值,查C P -表,偏心率 χ0.579χ=10)计算最小油膜厚度min 200(1)0.00084(10.579)35.36422d h m ψχμ=-=⨯⨯-=11)确定轴颈轴承孔表面粗糙十点高度 查得轴颈R Z1=0.0032mm ,轴承孔R Z2=0.0063mm12)计算许用油膜厚度 取安全系数S=2,则 []mR R S h Z Z μ190063000320221=+⨯=+=)..()([]min h h >满足要求。
液体动压润滑向心滑动轴承实验

3’
4’
5’
2’
F
3
45
6’
6
2 1’
1
7 7’
端泄影响系数
Pm
2’ 1’
3’ 4’
5’ 6’ 7’
12 3
4 5 67
七、实验报告要求
数据记录
压力表号 p1
p2
p3
p4
p5
p6
p7
p8 (轴向)
压力
江苏大学工业中心
七、实验报告要求
绘制油膜的轴向和周向压力分布曲线
3’
µl
=
0.001 m mm
5’
江苏大学工业中心
四、实验设备
动力装置 油压测试装置
加载装置
1-直流电动机 2-三角带 3-传感器 4-螺旋加载杆 5-弹簧片 6-测力计(百分表) 7-压力表(径向7只,轴向一只) 8-主轴瓦 9-主轴 10-主轴箱
江苏大学工业中心
五、实验步骤
实验条件:W=70kgf,n=500r/min。 1、打开电源。 2、将转速调至500r/min左右。 3、加载,外载荷为70Kg.f。 4、等待油压表稳定后读出P1-P8的数据,记录在表格中。
稳定后再进行数据记录。
江苏大学工业中心
分组实验
2’
F
3
4 5
6’
µP
MPa
= 0.01
mm
4’
8’
8’
2
1’ 1 20o
6 7’ 7
30o
30o
0
0
B/4
d
B/2
B
n
周向压力分布曲线
轴向压力分布曲线
江苏大学工业中心
七、实验报告要求
流体动压润滑径向滑动轴承计算举例

流体动压润滑径向滑动轴承计算举例
试设计一流体动压润滑径向滑动轴承。
其径向外载荷为 5000N ,轴颈转速为960r/min ,轴颈所允 许的最小直
径为20mm 。
解:
工作载荷HN 〕 ^000~
轴馬宽径叱引d
卷考值 [―TT ----- 1 轴颈直径贞mm]
歹且1 00 ▼ r 自定义'
轴转速
960
开赠i 计算
混合润滑计算
rt 十算结果显示
釉承压强(MPaJ 12.5000 釉頑速度〔“旳]1 0053 r 使用参考间隍计算
3)估算轴承间隙
卩间隙计算结果显示
直径间003
相对间隙
0.0015
计算间隙
4)选择材料
包角选择n iso
ZCuSn10P1
J
许用摄大压强〔忖pa] 许用摄丈速度丽畑 许用 pv®(Mpa x m/s ) 材料属性 15
10
15 踢音洞
材料适用场合
用于中速、重戟及受变载荷的轴承.用于中速、
承°
中载的轴 参考值
轴承平均压强12.500MPa 轴承平均速度
1. OOSm/s pv® 1
2.566M Pa.m/s
5)流体动压润滑计算结果
1) 选择轴承的内径
二
101
12.5663
0.00110
席自定文相对间隙
输入自定义相对间隙值: |0.0015
匚吝输入已知裁量
轴承相
(从
略)
6)根据计算结果需要重新设计,按“返回”按钮,即可以得到可行方案。
液体动力润滑径向滑动轴承设计计算

液体动力润滑径向滑动轴承设计计算流体动力润滑的楔效应承载机理已在第四章作过简要说明,本章将讨论流体动力润滑理论的基本方程(即雷诺方程)及其在液体动力润滑径向滑动轴承设计计算中的应用。
(一)流体动力润滑的基本方程流体动力润滑理论的基本方程是流体膜压力分布的微分方程。
它是从粘性流体动力学的基本方程出发,作了一些假设条件后得出的。
假设条件:流体为牛顿流体;流体膜中流体的流动是层流;忽略压力对流体粘度的影响;略去惯性力及重力的影响;认为流体不可压缩;流体膜中的压力沿膜厚方向不变。
图12-12中,两平板被润滑油隔开,设板A 沿x 轴方向以速度v 移动;另一板B 为静止。
再假定油在两平板间沿 z 轴方向没有流动(可视此运动副在z 轴方向的尺寸为无限大)。
现从层流运动的油膜中取一微单元体进行分析。
作用在此微单元体右面和左面的压力分别为p 及p p dx x ∂⎛⎞+⎜∂⎝⎠⎟,作用在单元体上、下两面的切应力分别为τ及dy y ττ⎛⎞∂+⎜⎟∂⎝⎠。
根据x 方向的平衡条件,得:整理后得根据牛顿流体摩擦定律,得,代入上式得 该式表示了压力沿x 轴方向的变化与速度沿y 轴方向的变化关系。
下面进一步介绍流体动力润滑理论的基本方程。
1.油层的速度分布将上式改写成(a)对y 积分后得(c)根据边界条件决定积分常数C1及C2:当y=0时,v= V;y=h(h为相应于所取单元体处的油膜厚度)时,v=0,则得:代入(c)式后,即得 (d)由上可见,v由两部分组成:式中前一项表示速度呈线性分布,这是直接由剪切流引起的;后一项表示速度呈抛物线分布,这是由油流沿x方向的变化所产生的压力流所引起的。
2、润滑油流量当无侧漏时,润滑油在单位时间内流经任意截面上单位宽度面积的流量为:将式(d)代入式(e)并积分后,得(f)设在 p=p max处的油膜厚度为h0(即时当润滑油连续流动时,各截面的流量相等,由此得 :整理后得该式为一维雷诺方程。
液体动压润滑径向轴承油膜压力和特性曲线

精品资料推荐液体动压润滑径向轴承油膜压力和特性曲线(二) HZS —I型试验台一.实验目的1. 观察滑动轴承液体动压油膜形成过程。
2. 掌握油膜压力、摩擦系数的测量方法。
3. 按油压分布曲线求轴承油膜的承载能力。
二.实验要求1. 绘制轴承周向油膜压力分布曲线及承载量曲线,求出实际承载量。
2. 绘制摩擦系f与轴承特性的关系曲线。
3. 绘制轴向油膜压力分布曲线三•液体动压润滑径向滑动轴承的工作原理当轴颈旋转将润滑油带入轴承摩擦表面,由于油的粘性作用,当达到足够高的旋转速度时,油就被带入轴和轴瓦配合面间的楔形间隙内而形成流体动压效应,即在承载区内的油层中产生压力。
当压力与外载荷平衡时,轴与轴瓦之间形成稳定的油膜。
这时轴的中心相对轴瓦的中心处于偏心位置,轴与轴瓦之间处于液体摩擦润滑状态。
因此这种轴承摩擦小,寿命长,具有一定吸震能力。
液体动压润滑油膜形成过程及油膜压力分布形状如图8-1所示。
滑动轴承的摩擦系数f是重要的设计参数之一,它的大小与润滑油的粘度(Pas)、轴的转速n (r/min)和轴承压力p (MPi)有关,令nP (7)式中:一轴承特性数观察滑动轴承形成液体动压润滑的过程,摩擦系数f随轴承特性数的变化如图8-2所示。
图中相应于f值最低点的轴承特性数c称为临界特性数,且c以右为液体摩擦润滑区,c以左为非液体摩擦润滑区,轴与轴瓦之间为边界润滑并有局部金属接触。
因此f值随减小而急剧增加。
不同的轴颈和轴瓦材料、加工情况、轴承相对间隙等,f—曲线不同,c也随之不同。
四.HZS-1型试验台结构和工作原理1•传动装置如图8-7所示,被试验的轴承2和轴1支承于滚动轴承3上,由调速电机6通过V带5 带动变速箱4,从而驱动轴1逆时针旋转并可获得不同的转速。
精品资料推荐(9)21 —轴2—试验轴承3—滚动轴承 4 —变速箱5 — V 带传动6—调速电机图8-7传动装置示意图2.加载装置该试验台采用静压加载装置,如图图8-8所示。
液体动压径向滑动轴承实验指导书

液体动压径向滑动轴承实验指导书一、实验内容与目的:1.观察径向滑动轴承的摩擦现象,加深对概念的理解; 2.测绘径向滑动轴承的摩擦特性曲线,掌握测绘方法;3.测绘径向滑动轴承油膜压力曲线,求油膜承载能力。
了解复杂问题的简化处理方法。
二、实验设备的结构与工作原理:本实验有二类(二种型号)设备,它们的结构示意图如图1和图2所示:它们包括以下向个部份:可以证明,抛物面与轴直径截面所围体积与以m P 值为高的长方体的体积之比32=KdB m 。
如果我们测量是精确的;那么我们计算结果摩擦状态指示装置的原理是用一个与轴和轴瓦相连的直流电路上的灯泡来指示的。
当轴当轴在很低的转速下转动时,轴将润滑油带入轴和轴瓦之间收敛性间隙内,但由于此时的油膜厚度很薄,轴与轴瓦之间部分微观不平的凸峰处仍在接触,当轴的转速达到一定值时,轴与轴瓦之间形成的压力油膜厚度完全分开两表面之间微观不平的凸峰,油膜守全将轴与轴瓦隔开,灯泡就不亮了。
这个指示装置还有一个作用就是当指示灯亮时不能加载,以免出现油温过高烧瓦等现三、实验方法与步骤:一)操作前检查:1.调速旋钮是否逆时针旋到底;2.将百分表调零;3.察看油标,检查润滑油油位是否到位;4.使加载系统处于未加载状态;二)实验操作(在做完以上准备工作后):1.观察润滑现象:接通电源,将调速旋钮右旋将使在一定转速(300转/分左右)下旋转,再回调至200转/分左右,然后再慢慢的调到转速为零。
注意观察各种摩擦状态。
2.摩擦系数测量:①接通电源,旋转调速旋钮使轴在一定转速(300转/分)下旋转。
②用加、减载荷方法记录在不同载荷情况下百分表读数;然后再在一固定载荷(HS-A型加到40kg;HZ型加三块砝码)下,用加、减转速方法记录百分表读数。
这样就得到摩擦系数各点值。
3.油膜承载压力测量:①调节调速旋钮,将轴转速达到各试验机的最高转速(500转/分以内);②加载使轴承受一定载荷(HS-A型100kg;HZ型六块砝码),待压力表值稳定后记录各块压力表的值。
液体动力润滑径向滑动轴承设计计算

液体动力润滑径向滑动轴承设计计算流体动力润滑的楔效应承载机理已在第四章作过简要说明,本章将讨论流体动力润滑理论的基本方程(即雷诺方程)及其在液体动力润滑径向滑动轴承设计计算中的应用。
(一)流体动力润滑的基本方程流体动力润滑理论的基本方程是流体膜压力分布的微分方程。
它是从粘性流体动力学的基本方程出发,作了一些假设条件后得出的。
假设条件:流体为牛顿流体;流体膜中流体的流动是层流;忽略压力对流体粘度的影响;略去惯性力及重力的影响;认为流体不可压缩;流体膜中的压力沿膜厚方向不变。
图12-12中,两平板被润滑油隔开,设板A 沿x 轴方向以速度v 移动;另一板B 为静止。
再假定油在两平板间沿 z 轴方向没有流动(可视此运动副在z 轴方向的尺寸为无限大)。
现从层流运动的油膜中取一微单元体进行分析。
作用在此微单元体右面和左面的压力分别为p 及p p dx x ∂⎛⎞+⎜∂⎝⎠⎟,作用在单元体上、下两面的切应力分别为τ及dy y ττ⎛⎞∂+⎜⎟∂⎝⎠。
根据x 方向的平衡条件,得:整理后得根据牛顿流体摩擦定律,得,代入上式得 该式表示了压力沿x 轴方向的变化与速度沿y 轴方向的变化关系。
下面进一步介绍流体动力润滑理论的基本方程。
1.油层的速度分布将上式改写成(a)对y 积分后得(c)根据边界条件决定积分常数C1及C2:当y=0时,v= V;y=h(h为相应于所取单元体处的油膜厚度)时,v=0,则得:代入(c)式后,即得 (d)由上可见,v由两部分组成:式中前一项表示速度呈线性分布,这是直接由剪切流引起的;后一项表示速度呈抛物线分布,这是由油流沿x方向的变化所产生的压力流所引起的。
2、润滑油流量当无侧漏时,润滑油在单位时间内流经任意截面上单位宽度面积的流量为:将式(d)代入式(e)并积分后,得(f)设在 p=p max处的油膜厚度为h0(即时当润滑油连续流动时,各截面的流量相等,由此得 :整理后得该式为一维雷诺方程。
液体动力润滑径向滑动轴承的设计计算
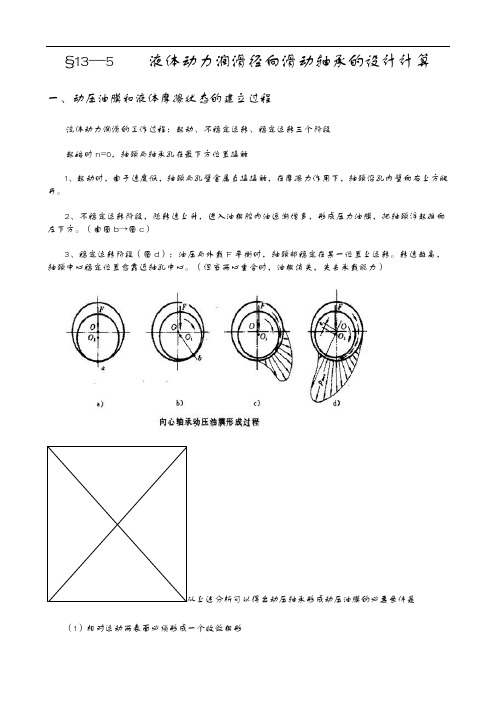
§13—5液体动力润滑径向滑动轴承的设计计算一、动压油膜和液体摩擦状态的建立过程流体动力润滑的工作过程:起动、不稳定运转、稳定运转三个阶段起始时n=0,轴颈与轴承孔在最下方位置接触1、起动时,由于速度低,轴颈与孔壁金属直接接触,在摩擦力作用下,轴颈沿孔内壁向右上方爬开。
2、不稳定运转阶段,随转速上升,进入油楔腔内油逐渐增多,形成压力油膜,把轴颈浮起推向左下方。
(由图b→图c)3、稳定运转阶段(图d):油压与外载F平衡时,轴颈部稳定在某一位置上运转。
转速越高,轴颈中心稳定位置愈靠近轴孔中心。
(但当两心重合时,油楔消失,失去承载能力)从上述分析可以得出动压轴承形成动压油膜的必要条件是(1)相对运动两表面必须形成一个收敛楔形(2)被油膜分开的两表面必须有一定的相对滑动速度v s,其运动方向必须使润滑从大口流进,小口流出。
(3)润滑油必须有一定的粘度,供油要充分。
v越大,η越大,油膜承载能力越高。
实际轴承的附加约束条件:压力pv值速度最小油膜厚度温升二、最小油膜厚度h min1、几何关系图13-13 径向滑动轴承的几何参数和油压分布O—轴颈中心,O1—轴承中心,起始位置F与OO1重合,轴颈半径-r,轴承孔半径R∴半径间隙:(13-6-1)半径间隙:(13-6)相对间隙:(13-7)偏心距:(13-8)偏心率:(13-9)以OO1为极轴,任意截面处相对于极轴位置为φ处对应油膜厚度为h,(13-10)h的推导:在中,根据余弦定律可得(13-11)略去高阶微量,再引入半径间隙,并两端开方得(13-12)三.流体动力润滑基本方程(雷诺方程)流体动力润滑基本方程(雷诺方程)是根据粘性流体动力学基本方程出发,作了一些假设条件后简化而得的。
假设条件是:1)忽略压力对润滑油粘度的影响;2)流体为粘性流体;3)流体不可压缩,并作层流;4)流体膜中压力沿膜厚方向是不变的;2)略去惯性力和重力的影响。
可以得出:∴(13-13)一维雷诺流体动力润滑方程上式对x取偏导数可得(13-14)若再考虑润滑油沿Z方向的流动,则(13-15)二维雷诺流体动力润滑方程式四、最小油膜厚度由中可看出油压的变化与润滑油的粘度、表面滑动速度和油膜厚度的变化有关,利用该式可求出油膜中各点的压力p,全部油膜压力之和即为油膜的承载能力。
流体动压润滑条件下滑动轴承的优化分析.

本科毕业设计题目流体动压润滑条件下滑动轴承的优化分析专业汽车服务工程作者姓名李洋洋学号2011206004单位机械与汽车工程学院指导教师杜娟2015年5月教务处编原创性声明本人郑重声明:所提交的学位论文是本人在导师指导下,独立进行研究取得的成果。
除文中已经引用的内容外,论文中不包含其他人已经发表或撰写过的研究成果,也不包含为获得聊城大学或其他教育机构的学位证书而使用过的材料。
对本文的研究作出重要贡献的个人和集体,均在文中以明确的方式表明。
本人承担本声明的相应责任。
学位论文作者签名:日期:指导教师签名:日期:摘要就当今的汽车而言,大约有80%的机械部件的损坏来自于磨损。
机械系统中摩擦能够得到相关的优化,更能够提高机械性能,延长其使用寿命。
然而传统发动机滑动轴承用非定常流体设计,对于发动机滑动轴承耐磨性能并没有真正的进行定性分析,缺乏一定的说服力。
本文首先介绍了滑动轴承的相关知识,然后对流体动压润滑进行详细说明并建立了流体动压润滑的计算模型,然后以发动机主轴承为例,分析轴承在不同转速下的最小油膜厚度、润滑油温升,发现转速过高时,油膜厚度过小且温升过高,导致滑动轴承不能处于良好的润滑状态,分析该现象的原因并提出相关改进方案:增粗轴颈、加宽轴承。
然后分别根据两种改进方案在不同转速下的最小油膜厚度、润滑油温升两个角度分析改进措施的优劣性。
关键词:流体动力润滑;转速;最小油膜厚度;温升AbstractIn terms of today's cars, and about 80% of the damage of the mechanical components from wear and tear. Mechanical friction in the system can get related optimization, more can improve the mechanical properties, extend its service life. However, the traditional engine bearing design with unsteady flow for engine bearing wear resistance and no real qualitative analysis, the lack of certain powers of persuasion.This paper first introduces the sliding bearing of the related knowledge, and elaborate on the hydrodynamic pressure lubrication and the calculation of hydrodynamic pressure lubrication model is established, and then to launch a main bearing as an example, analysis of the bearing under different rotational speed, the minimum oil film thickness, oil temperature rise, found at high speed, the temperature rise of the oil film thickness is too small and too high, lead to sliding bearing can't in good lubrication condition, analyses the reason of this phenomenon and put forward relevant improvement plan: enlargement of journal, widen the bearing. Then respectively according to the two kinds of improved scheme under different rotational speed, the minimum oil film thickness, oil temperature rise two Angle analysis of superiority and inferiority of some improvement measures.Keywords:hydrodynamic lubrication; Speed; Minimum oil film thickness; Temperature rise目录前言................................................................................................I I 1.轴承设计计算所涉及到的基础知识 .. (1)1.1 滑动轴承 (1)1.2牛顿粘性定律 (2)1.3.表面粗糙度 (3)1.3.1表面粗糙度定义 (3)1.3.2 表面粗糙度对零件的影响 (3)2.流体动压润滑 (4)2.1流体动压润滑基本理论 (4)2.2流体动力润滑的基本方程 (5)2.2.1油层速度的分布 (5)2.2.2润滑油流量 (6)3.发动机滑动轴承的流体润滑设计 (8)3.1建立弹性流体动压润滑的计算模型 (8)3.1.1建立动压润滑模型 (8)3.1.2相关参数选择 (8)3.2动压润滑设计 (9)3.2.1油膜承载能力的计算 (9)3.2.2最小油膜厚度的计算 (10)3.2.3轴承热平衡计算 (11)4.发动机主轴承流体润滑计算与结果分析 (12)4.1流体润滑计算 (12)4.2流体润滑计算结果分析 (15)5.发动机主轴承耐磨性改进方案 (16)5.1增大轴颈直径 (16)5.1.1最小油膜厚度分析改进方案 (16)5.1.2润滑油温升分析改进方案 (17)5.2增大轴承宽度 (17)5.2.1最小油膜厚度分析改进方案 (17)5.2.2润滑油温升分析改进方案 (18)结论 (19)参考文献 (20)致谢 (21)流体动压润滑条件下滑动轴承的耐磨性优化分析前言滑动轴承是机械系统中常见的装置之一,也是生产过程中不可或缺的原件。
液体摩擦动压向心滑动轴承的设计
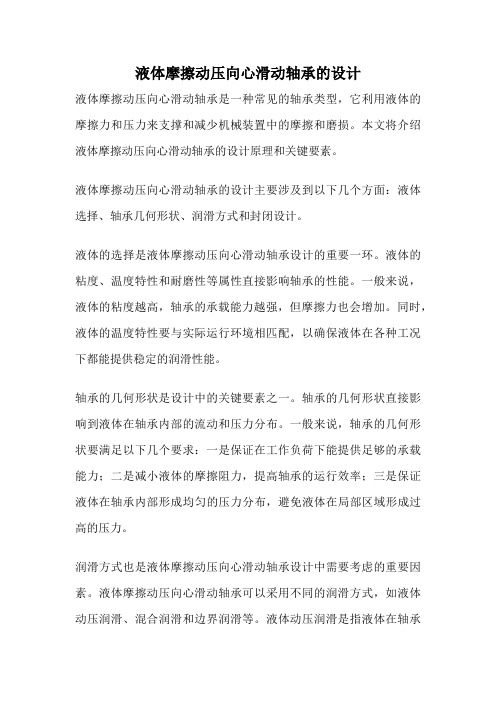
液体摩擦动压向心滑动轴承的设计液体摩擦动压向心滑动轴承是一种常见的轴承类型,它利用液体的摩擦力和压力来支撑和减少机械装置中的摩擦和磨损。
本文将介绍液体摩擦动压向心滑动轴承的设计原理和关键要素。
液体摩擦动压向心滑动轴承的设计主要涉及到以下几个方面:液体选择、轴承几何形状、润滑方式和封闭设计。
液体的选择是液体摩擦动压向心滑动轴承设计的重要一环。
液体的粘度、温度特性和耐磨性等属性直接影响轴承的性能。
一般来说,液体的粘度越高,轴承的承载能力越强,但摩擦力也会增加。
同时,液体的温度特性要与实际运行环境相匹配,以确保液体在各种工况下都能提供稳定的润滑性能。
轴承的几何形状是设计中的关键要素之一。
轴承的几何形状直接影响到液体在轴承内部的流动和压力分布。
一般来说,轴承的几何形状要满足以下几个要求:一是保证在工作负荷下能提供足够的承载能力;二是减小液体的摩擦阻力,提高轴承的运行效率;三是保证液体在轴承内部形成均匀的压力分布,避免液体在局部区域形成过高的压力。
润滑方式也是液体摩擦动压向心滑动轴承设计中需要考虑的重要因素。
液体摩擦动压向心滑动轴承可以采用不同的润滑方式,如液体动压润滑、混合润滑和边界润滑等。
液体动压润滑是指液体在轴承内形成动压膜,减小摩擦力和磨损;混合润滑是指液体和固体之间形成混合膜,提供更好的润滑效果;边界润滑是指液体无法形成润滑膜,但可以在摩擦表面上形成一层保护膜,减小摩擦和磨损。
封闭设计是液体摩擦动压向心滑动轴承设计中需要考虑的另一个重要因素。
封闭设计可以防止外界杂质进入轴承内部,同时防止液体的泄漏。
封闭设计通常包括密封圈和密封垫等部件,可以有效地提高轴承的使用寿命和可靠性。
液体摩擦动压向心滑动轴承的设计需要考虑液体选择、轴承几何形状、润滑方式和封闭设计等因素。
合理的设计可以提高轴承的承载能力、降低摩擦和磨损,并确保轴承的可靠性和使用寿命。
对于特定的应用场景,设计人员需要根据实际需求和工作环境选择适当的设计参数,以实现最佳的轴承性能。
液体动压滑动轴承实验

CQH-A液体动压滑动轴承实验台使用说明书本实验台用于液体动压滑动轴承实验,主要用它来观察滑动轴承的结构,测量其径向油膜压力分布和轴向油膜压力分布,测定其摩擦特征曲线和承载量。
该实验台结构简单、重量轻、体积小、外形美观大方,测量直观准确,运行稳定可靠。
一、实验台结构简介1. 该实验台主要结构见图1所示:图1 滑动轴承试验台结构图1. 操纵面板2. 电机3. V带4. 轴油压表接头5. 螺旋加载杆6. 百分表测力计装置7. 径向油压表(7只)8. 传感器支承板9. 主轴10. 主轴瓦11. 主轴箱2. 结构特点该实验台主轴9由两个高精度的单列向心球轴承支承。
直流电机2通过V带3驱动主轴9,主轴顺时针旋转,主轴上装有精密加工制造的主轴瓦10,由装在底座里的无级调速器实现主轴的无级变速,轴的转速由装在面板1上的左数码管直接读出。
主轴瓦外圆处被加载装置(未画)压住,旋转加载杆5即可对轴瓦加载,加载大小由负载传感器传出,由面板上右数码管显示。
主轴瓦上装有测力杆,通过测力计装置可由百分表6读出摩擦力值。
主轴瓦前端装有7只测径向压力的油压表7,油的进口在轴瓦长度的1/2处。
在轴瓦全长的1/4处装有一个轴向油压表的接头,需要时可用内六角扳手将堵油塞旋出,再装上备用的轴向油压表。
3. 实验中如需拆下主轴瓦观察,需按下列步骤进行:a. 旋出外加载传感器插头。
b. 用内六角扳手将传感器支承板8上的两个内六角螺钉卸下,拿出传感器支承板即可将主轴瓦卸下。
二、主要技术参数实验轴瓦:内直径d=60mm有效长度B=125mm表面粗糙度∇7)材料ZCuSn5Pb5Zn5(即旧牌号ZQSn6-6-3)加载范围0~1000N(0~100kg⋅f)百分表精度0.01 量程0—10mm油压表精度 2.5% 量程0~0.6Mpa测力杆上测力点与轴承中心距离L=120mm测力计标定值k=0.098N/格电机功率:355W调速范围:2~400rpm实验台总量:52kg三、电气工作原理5 4 3图二1—主轴转速数码管:主轴转速传感器采集的实时数据。
液体动压滑动轴承实验报告

液体动压滑动轴承实验报告液体动压滑动轴承实验报告引言液体动压滑动轴承是一种常见的摩擦副,广泛应用于工业领域。
本实验旨在通过实际操作和数据分析,探究液体动压滑动轴承的工作原理和性能特点。
实验目的1. 了解液体动压滑动轴承的结构和工作原理。
2. 探究液体动压滑动轴承的摩擦特性和承载能力。
3. 分析液体动压滑动轴承的性能优势和应用范围。
实验装置和方法实验装置包括液体动压滑动轴承、电机、压力传感器、转速传感器和数据采集系统。
实验步骤如下:1. 将液体动压滑动轴承装配在电机轴上。
2. 连接压力传感器和转速传感器,并将其与数据采集系统连接。
3. 调整电机转速,记录不同转速下的轴承压力和摩擦力。
4. 根据实验数据,分析轴承的摩擦特性和承载能力。
实验结果与分析通过实验记录的数据,我们可以得到不同转速下的轴承压力和摩擦力。
根据数据分析,我们可以得出以下结论:1. 随着转速的增加,轴承压力逐渐增大。
这是因为液体动压滑动轴承的工作原理是通过液体的动压效应来支撑轴承负荷,转速增加会导致液体的动压效应增强,从而增大轴承压力。
2. 随着转速的增加,轴承摩擦力逐渐减小。
这是因为液体动压滑动轴承的摩擦力主要来自于液体的黏滞阻力,转速增加会导致液体黏滞阻力减小,从而减小轴承摩擦力。
实验结论根据实验结果和分析,我们可以得出以下结论:1. 液体动压滑动轴承具有较好的承载能力。
通过增加转速,可以增大轴承的承载能力,适用于高速旋转设备。
2. 液体动压滑动轴承具有较低的摩擦力。
由于液体的黏滞阻力较小,轴承运行时的摩擦损失较小,有利于提高设备的效率和使用寿命。
3. 液体动压滑动轴承适用于高温和高速环境。
由于液体动压轴承不需要润滑油脂,可以在高温和高速环境下稳定工作,适用于一些特殊工况。
实验总结通过本实验,我们深入了解了液体动压滑动轴承的工作原理和性能特点。
液体动压滑动轴承具有较好的承载能力和较低的摩擦力,适用于高速旋转设备和高温环境。
然而,在实际应用中,还需要考虑到成本、维护和安装等因素,综合评估选择最适合的轴承类型。
油液动压径向轴承设计及计算【开题报告】

毕业设计开题报告机械设计制造及自动化油液动压径向轴承设计及计算1、选题的背景、意义流体动压径向滑动轴承具有承载能力大、功耗小、耐冲击、抗振性好、运转精度高等突出的优点。
所以,在高速、低速以及高速精密的旋转机械中应用十分普遍,而且成为旋转机械的重要部件。
比如在汽轮机组、舰船主动力机组、石油钻井机械、轧机及各类大型机床中都有广泛的应用,而且成为这类机械的关键部件之一。
在这些机器中,径向滑动轴承的性能优劣直接影响或决定了整台机器的性能和效率。
比如在汽轮发电机组中,性能优良的滑动轴承可以减少停机检修的次数,烧瓦的可能性也低得多。
轴承基本参数(轴径的长径比、半径间隙、偏心距和轴承包角等)的变化,对轴承的静动态特性会产生很大的影响。
另外,实际工作中的滑动轴承,由于加工、安装误差等因数,其工况条件与理论分析时所考虑的理想工况有很大差距,这种情况下,轴承的一些性能参数会发生变化。
2、相关研究的最新成果及动态我国轴承行业发展到现在,已具备相当的生产规模和较高的技术、质量水平。
具有一定规模的轴承企业已发展到1 500余家,职工人数壮大到近80万人,轴承年产量从1 949年的1 3.8J5套增加到目前的20多亿套,轴承品种累计从1 00多个增加至7000多个,规格达28000多个。
近1 0年来国外轴承知名公司(如SKF、FAG、NSK、NBM 、 KOYO、T JM KEN、TORRlNGTON等)先后在我国投资办厂,对我国轴承设计技术水平的提高,生产工艺和生产管理的规范、生产装备水平的现代化、产品的质量和使用性能的提高等方面起到了很大的推动作用。
2OO亿元,年出口量逾7.7亿套,出口创汇约达7亿美元,世界排名第4,满足国内所需产品品种的70%以上,满足所需数量90%以上,出口量也以较高的比例递增。
在我国跨入世界轴承生产大国行列的同时,轴承工业依然存在低、散、差的问题普通微型、小型、中小型深但另一方面,我国轴承生产企业也面临来自国外知名轴承公司的激烈竞争和挑战,其结果必将加速我国轴承工业的产业结构和严品结构的调整步伐,真可谓机遇与挑战并存、生产与发展同在。
液体动压润滑径向轴承油膜压力和特性曲线
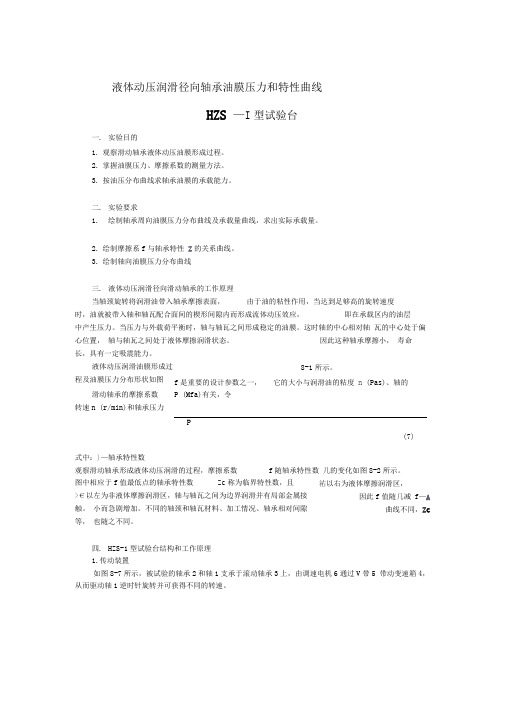
液体动压润滑径向轴承油膜压力和特性曲线HZS —I 型试验台一. 实验目的1. 观察滑动轴承液体动压油膜形成过程。
2. 掌握油膜压力、摩擦系数的测量方法。
3. 按油压分布曲线求轴承油膜的承载能力。
二. 实验要求1. 绘制轴承周向油膜压力分布曲线及承载量曲线,求出实际承载量。
2. 绘制摩擦系f 与轴承特性 Z 的关系曲线。
3. 绘制轴向油膜压力分布曲线三. 液体动压润滑径向滑动轴承的工作原理 当轴颈旋转将润滑油带入轴承摩擦表面,由于油的粘性作用,当达到足够高的旋转速度时,油就被带入轴和轴瓦配合面间的楔形间隙内而形成流体动压效应,即在承载区内的油层中产生压力。
当压力与外载荷平衡时,轴与轴瓦之间形成稳定的油膜。
这时轴的中心相对轴 瓦的中心处于偏心位置, 轴与轴瓦之间处于液体摩擦润滑状态。
因此这种轴承摩擦小, 寿命长,具有一定吸震能力。
液体动压润滑油膜形成过程及油膜压力分布形状如图 滑动轴承的摩擦系数 转速n (r/min)和轴承压力式中:)—轴承特性数观察滑动轴承形成液体动压润滑的过程,摩擦系数 f 随轴承特性数 几的变化如图8-2所示。
图中相应于f 值最低点的轴承特性数Z c 称为临界特性数,且>€以左为非液体摩擦润滑区,轴与轴瓦之间为边界润滑并有局部金属接触。
小而急剧增加。
不同的轴颈和轴瓦材料、加工情况、轴承相对间隙等, 也随之不同。
四. HZS-1型试验台结构和工作原理1.传动装置如图8-7所示,被试验的轴承2和轴1支承于滚动轴承3上,由调速电机6通过V 带5 带动变速箱4,从而驱动轴1逆时针旋转并可获得不同的转速。
8-1所示。
f 是重要的设计参数之一,它的大小与润滑油的粘度 n (Pas)、轴的P (Mfa)有关,令P(7)祐以右为液体摩擦润滑区,因此f 值随几减 f —A曲线不同,Z c1 2 3 41 —测力计2—测力杆3—卡板4—加载板 5 —轴6—轴承7 —平衡重块图8-8加载及摩擦力矩测量装 置Go —初始载荷(包括压力表、平衡重及轴瓦的自重) Go = 8 kgf 。
液体动压滑动轴承实验指导书

实验四 液体动压滑动轴承实验指导书一、实验目的1、了解实验台的构造和工作原理,通过实验进一步了解动压润滑的形成,加深对动压原理的认识。
2、学习动压轴承油膜压力分布的测定方法,绘制油膜压力径向和轴向分布图,验证理论分布曲线。
3、掌握动压轴承摩擦特征曲线的测定方法,绘制f —n 曲线,加深对润滑状态与各参数间关系的理解。
二、实验原理及装置1.概述此项实验是径向加载的液体动压滑动轴承实验。
其目的是测量轴承与转轴间隙中的油膜在圆周方向的压力分布值(见图1),并验证径向油膜压力最大值批P MAX 不在外载荷F R 的垂线位置,而是在最小油膜厚度附近,即0=∂∂XP 处。
该实验还可以测试下列几项内容。
(1)测量轴承与转轴间隙中的油膜在轴线方向的压力分布值,并验证轴向压力分布曲线呈抛物线分布,即轴向油膜最大压力值在轴承宽度的中间位置(见图2)。
图1 周向油膜压力分布曲线 图2轴向油膜压力分布曲线(2)测量径向液体动压滑动轴承在不同转速、不同载荷、不同粘度润滑油情况下的摩擦系数f 值,根据取得的一系列f 值,可以做出滑动轴承的摩擦特性曲线,进而分析液体动压的形成过程,并找出非液体摩擦到液体摩擦的临界点,以便确定一定载荷、一定粘度润滑油情况下形成液体动压的最低转速,或一定转速、一定粘度润滑油情况下保证液体动压状态的最大载荷(见图3)。
图3 轴承摩擦特性曲线2.实验装置及原理本实验使用湖南长庆科教仪器有限公司生产的HS-B型液体动压轴承实验台如图4所示,它由传动装置、加载装置、摩擦系数测量装置、油膜压力测量装置和被试验轴承等组成。
图4 滑动轴承试验台1.操纵面板2.电机3.三角带4.轴向油压传感器接头5.外加载荷传感器6.螺旋加载杆7.摩擦力传感器测力装置8.径向油压传感器(7只)9.传感器支撑板10.主轴11.主轴瓦12.主轴箱1)传动装置由直流电机2通过三角带3带动主轴顺时针旋转,由无级调速器实现无级调速。
本实验台主轴的转速范围为3~375rpm,主轴的转速由装在面板1上的数码管直接读出。
动压径向滑动轴承设计中 将宽径比增大则最小油膜厚度
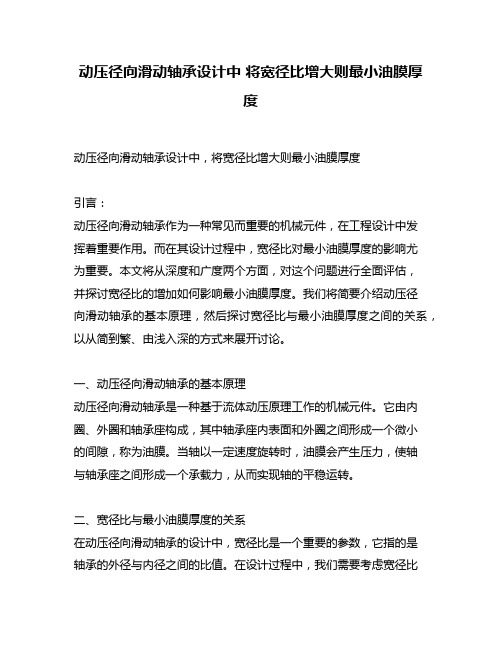
动压径向滑动轴承设计中将宽径比增大则最小油膜厚度动压径向滑动轴承设计中,将宽径比增大则最小油膜厚度引言:动压径向滑动轴承作为一种常见而重要的机械元件,在工程设计中发挥着重要作用。
而在其设计过程中,宽径比对最小油膜厚度的影响尤为重要。
本文将从深度和广度两个方面,对这个问题进行全面评估,并探讨宽径比的增加如何影响最小油膜厚度。
我们将简要介绍动压径向滑动轴承的基本原理,然后探讨宽径比与最小油膜厚度之间的关系,以从简到繁、由浅入深的方式来展开讨论。
一、动压径向滑动轴承的基本原理动压径向滑动轴承是一种基于流体动压原理工作的机械元件。
它由内圈、外圈和轴承座构成,其中轴承座内表面和外圈之间形成一个微小的间隙,称为油膜。
当轴以一定速度旋转时,油膜会产生压力,使轴与轴承座之间形成一个承载力,从而实现轴的平稳运转。
二、宽径比与最小油膜厚度的关系在动压径向滑动轴承的设计中,宽径比是一个重要的参数,它指的是轴承的外径与内径之间的比值。
在设计过程中,我们需要考虑宽径比对最小油膜厚度的影响。
通常情况下,增大宽径比会使最小油膜厚度减小。
这是因为相同转速下,增大宽径比会导致流经油膜的流量增加,从而增大单位面积上的速度梯度。
根据流体动力学的原理,速度梯度增大会引起油膜的压力降低,进而导致油膜厚度减小。
然而,当宽径比增加到一定程度时,最小油膜厚度会出现一个临界点。
在这个临界点之后,最小油膜厚度反而会开始增加。
这是因为过大的宽径比会导致流经油膜的流量增加过多,使得油膜压力不再降低,甚至到达饱和状态。
此时,增大宽径比会导致油膜的压力增加,从而使最小油膜厚度增加。
在动压径向滑动轴承的设计中,需要根据具体的工况和性能要求,合理选择宽径比,以达到最佳的最小油膜厚度。
三、增大宽径比对轴承性能的影响除了对最小油膜厚度的影响外,增大宽径比还会对动压径向滑动轴承的其他性能产生一定的影响。
增大宽径比能够提高轴承的刚度。
由于宽径比的增加会使油膜厚度减小,从而使轴承的刚度增加,提高了轴向的刚度。
液体动压径向滑动轴承设计与分析

液体动压径向滑动轴承设计与分析摘要动压式滑动轴承是轴承中的一个重要类别,对其进行分析研究在实际中具有重要意义。
液体动压径向滑动是其中的重要一类,本文以径向滑动轴承为研究对象,以雷诺方程的建立及求解过程为理论基础,对滑动轴承在处于液体动压的工况情况进行理论分析。
本课题的目的就是旨在结合滑动轴承的工作特点和性能,合理的优化轴承的结构形式,对轴承的各性能进行优化设计。
通过图纸对轴承结构进行分析优化,利用相关公式对性能进行计算与分析,对整个轴承进行优化设计。
关键字:滑动轴承;雷诺方程目录第一章1绪论 (4)1.1本课题的选定 (5)1.2滑动轴承制造和生产技术的发展现状 (5)1.3本课题研究的主要内容及基本工作思路 (6)(一)主要内容 (6)(二)本课题基本工作思路 (6)第二章2液体动压径向滑动轴承的总体设计方案 (6)2.1滑动轴承 (6)(一)滑动轴承的主要类型和结构 (6)2.2液体动压润滑的基本原理和基本关系 (8)(一)液体动压油膜的形成理论 (8)(二)液体动压润滑的基本方程 (8)(三)油楔承载机理 (11)2.3液体动压径向滑动轴承基本原理 (11)(一)径向滑动轴承液体动压润滑的建立过程 (11)(二)径向滑动轴承的几何关系和承载能力 (12)(三)径向滑动轴承的参数选择 (16)(四)径向滑动轴承的供油结构 (18)第三章3液体动压径向滑动轴承的实例计算 (20)3.1主要技术指标 (20)3.2选择轴承材料和结构 (20)3.3润滑剂和润滑方法的选择 (21)3.4性能计算 (21)(一)承载能力计算 (21)(二)层流校核 (22)(三)功耗计算 (22)(四)热平衡计算 (23)(五)安全度计算 (23)第四章4三维建模4.1三维建模依据 (23)4.2三维建模的基本图形 (24)4.3三维建模的步骤 (24)总结 (25)参考文献 (25)致谢 (27)附件外文翻译文献第一章1绪论滑动轴承在机械制造、大型电站、钢铁联合企业以及化工联合企业等机械设备中得到广泛应用,如何提高其寿命和工作可靠性越来越成为人类普遍关注的问题。
液体动力滑动轴承的设计计算

最小油膜厚度 : hmin= R- (r +e)
定义: 直径间隙:Δ= D- d 半径间隙:δ= R- r = Δ/ 2 相对间隙:ψ = δ / r = Δ / d χ = e / δ 为偏心率 最小油膜厚度: hmin =δ-e = rψ(1-χ)
F
d φ a
e
o
o1
潘存云教授研制
注:偏心率χ 的大小反映了轴承的承载能力。 当载荷很小或转速很高时, χ≈0,此时轴、孔中心接 近重合,油楔消失, hmin≈δ; 当载荷很大或转速很小时, χ≈1,此时轴颈与轴瓦接 7 触,hmin≈0 ,油膜被破坏;
保证润滑油从大截面流进,从小截面出来。
2
二、流体动力润滑基本方程的建立
为了得到简化形式的流体动力平 衡方程(Navier-Stokes方程),作 如下假设: ▲ 流体满足牛顿定律,即 A
z
V
x
潘存云教授研制
du τ =η dy
;
B y
▲ 流体的流动是层流;
实际上粘度随压力的增高而增加;
即层与层之间没有 物质和能量的交换;
10
3、最小油膜厚度hmin 动力润滑轴承的设计应保证:hmin≥[h] 其中: [h]=S(Rz1+Rz2)
Rz1、Rz2—— 分别为轴颈和轴承孔表面粗糙度十点高度。
S—— 安全系数,常取S≥2。
考虑表面几何形状误差和轴颈挠曲变形等 11
4、轴承的热平衡计算 热平衡方程:产生的热量=散失的热量 Q=Q1+Q2 其中,摩擦热: Q=fρ v W 润滑油带走的热:Q1 = qρ c(to-ti) 轴承散发的热: Q2 =α 3π dB (to-ti) 式中: q ----润滑油流量m3/s; ρ ----滑油密度kg/m3; c ----润滑油的比热容,J/(kg. ℃ );
- 1、下载文档前请自行甄别文档内容的完整性,平台不提供额外的编辑、内容补充、找答案等附加服务。
- 2、"仅部分预览"的文档,不可在线预览部分如存在完整性等问题,可反馈申请退款(可完整预览的文档不适用该条件!)。
- 3、如文档侵犯您的权益,请联系客服反馈,我们会尽快为您处理(人工客服工作时间:9:00-18:30)。
液体动压径向滑动轴承设计与分析摘要动压式滑动轴承是轴承中的一个重要类别,对其进行分析研究在实际中具有重要意义。
液体动压径向滑动是其中的重要一类,本文以径向滑动轴承为研究对象,以雷诺方程的建立及求解过程为理论基础,对滑动轴承在处于液体动压的工况情况进行理论分析。
本课题的目的就是旨在结合滑动轴承的工作特点和性能,合理的优化轴承的结构形式,对轴承的各性能进行优化设计。
通过图纸对轴承结构进行分析优化,利用相关公式对性能进行计算与分析,对整个轴承进行优化设计。
关键字:滑动轴承;雷诺方程目录第一章1绪论 (4)1.1本课题的选定 (5)1.2滑动轴承制造和生产技术的发展现状 (5)1.3本课题研究的主要内容及基本工作思路 (6)(一)主要内容 (6)(二)本课题基本工作思路 (6)第二章2液体动压径向滑动轴承的总体设计方案 (6)2.1滑动轴承 (6)(一)滑动轴承的主要类型和结构 (6)2.2液体动压润滑的基本原理和基本关系 (8)(一)液体动压油膜的形成理论 (8)(二)液体动压润滑的基本方程 (8)(三)油楔承载机理 (11)2.3液体动压径向滑动轴承基本原理 (11)(一)径向滑动轴承液体动压润滑的建立过程 (11)(二)径向滑动轴承的几何关系和承载能力 (12)(三)径向滑动轴承的参数选择 (16)(四)径向滑动轴承的供油结构 (18)第三章3液体动压径向滑动轴承的实例计算 (20)3.1主要技术指标 (20)3.2选择轴承材料和结构 (20)3.3润滑剂和润滑方法的选择 (21)3.4性能计算 (21)(一)承载能力计算 (21)(二)层流校核 (22)(三)功耗计算 (22)(四)热平衡计算 (23)(五)安全度计算 (23)第四章4三维建模4.1三维建模依据 (23)4.2三维建模的基本图形 (24)4.3三维建模的步骤 (24)总结 (25)参考文献 (25)致谢 (27)附件外文翻译文献第一章1绪论滑动轴承在机械制造、大型电站、钢铁联合企业以及化工联合企业等机械设备中得到广泛应用,如何提高其寿命和工作可靠性越来越成为人类普遍关注的问题。
这里存在着两方面的工作:一是不断研究新的轴承材料及结构,以适应轴承的工作特点及其负荷指标不断提高的要求;二是深入地研究发生在轴承内部的各种工作状态,从而在设计中采取相应的措施,保证轴承在最理想的条件下运作。
这就涉及研究研究诸如流体动压润滑轴承中的润滑油膜的压力分布、最小油膜厚度、润滑膜的刚度等若干方面的问题。
轴承是轴系中的重要部件,其功用一是支承轴及轴上零件并保证轴的旋转精度,二是减小转动轴与其固定支承之间的摩擦与磨损。
因此,轴承既要有小的摩擦阻力,又要有一定的强度。
轴承分为两大类:滚动轴承和滑动轴承。
滚动轴承有很多优点,例如:已实现系列化、标准化、商品化,使用维护简单,互换性好等,故各工业部门应用广泛。
滑动轴承在一般情况下摩擦损耗较大,使用维护较复杂,因而应用较少。
因此,在滚动轴承和滑动轴承都能满足使用要求时,宜先选用滚动轴承。
尽管如此,但是在高速、高精度、重载、结构上要求剖分等场合下,滑动轴承就显示出它的优异性能。
因而在汽轮机、离心式压缩机、内燃机、大型电机中多采用滑动轴承。
此外,在低速而带有冲击的机器中,如水泥搅拌机、滚筒清砂机、破碎机等也常采用滑动轴承。
两者相比,普通滑动轴承又具有比滚动轴承使用寿命长、运转平稳,对冲击和振动敏感性小等优点。
这些优点使滑动轴承成功地应用于机床主轴轴承,大型汽轮机轴承,内燃机曲轴轴承。
轧钢机轴承以及简单机械的轴承。
随着工业的现代化进程,大量机械设备的速度和功率日益提高,工况日趋复杂,而轴承作为机械设备的关键部件对其各方面的性能要求也越来越高。
滑动轴承油膜中的滑油流动过程完全符合流体动力学的普遍规律,在 1886 年Reynolds 运用流体动力学的定律,分析润滑剂在间隙中的流动,从而求得了表示轴承中压力分布的基本微分方程即雷诺方程,它成为今天滑动轴承理论计算的基础。
但用传统数学方法对雷诺方程进行求解,只有在一些特定情况下刁‘能获得精确的解析解。
由于这种困难很长一段时间滑动轴承还是按照 pv常数:轴承的平均压强,v:轴承两配合部分的相对滑动速度,常数:轴承副材料所确定经验数这种老方法双曲线法确定尺寸参数。
对于一些简单的、几何形状相似或结构相同的滑动轴承用这种计算方法并结合轴承生产中积累的经验来确定轴承尺寸一直还是成功的。
但随着新型或特殊结构的滑动轴承出现以及设计中对轴承可靠性要求的不断提高,这些经验数据就不再适合了。
最近二十几年以来随着计算机的技术发展其计算速度及计算能力迅速增长,许多传统数学方法难以求解的问题用计算机求解往往能够得到很好的结果,求解雷诺方程也就成为可能。
1.1本课题的选定随着科技的进一步发展,机械零件的规模越来越大,越来越完整,人们的需求越大,对物质的需求和要求也越来越高。
轴承作为一个机械零件,起着至关重要的作用。
用于支撑旋转零件(转轴、心轴)的装置通称为轴承。
条件不同,轴承的分类也不同:按其承载方向的不同,轴承可分为:径向轴承和推力轴承;按轴承工作时的摩擦性质不同,轴承可分为:滑动轴承和滚动轴承。
滑动轴承,根据其相对运动的两表面间油膜形成原理的不同,还可分为流体动力润滑轴承(简称动压轴承)和流体静力润滑轴承(简称静压轴承)。
和滚动轴承相比,滑动轴承具有承载能力高、抗压性好,工作平稳可靠,噪声小,寿命长等优点,它广泛用于内燃机、轧钢机、大型电机及仪表、雷达、天文望远镜等方面。
在动压轴承中,随着工作条件和润滑性能的变化,其滑动表面间的摩擦状态亦有所不同。
通常将其分为如下三种状态:不完全摩擦,边界摩擦和干摩擦。
完全液体摩擦是滑动轴承工作的最理想状况。
对那些重要且高速旋转的机器,应确保轴承在完全液体摩擦状态下工作,这类轴承常称为液体摩擦滑动轴承。
因此我这次的设计选择液体摩擦。
轴承上的反作用力与轴心线垂直的轴承称为径向轴承;轴承上的反作用力与轴心线方向一致的轴承称为推力轴承。
推力滑动轴承只能承受轴向载荷,与径向轴承联合才可同时承受轴向和径向载荷。
综上所述,我选择的设计是:液体动压滑动轴承的设计。
1.2滑动轴承制造和生产的技术的发展现状滑动轴承作为回转轴支承元件在机械领域的应用十分广泛。
与滚动轴承相比,滑动轴承工作平稳、可靠、噪音较低。
如果能够保证充分的液体润滑,使得滑动表面被润滑油分开而不发生直接接触,则还可以大大减少摩擦损失和表面磨损,甚至消除磨损。
另外,润滑油膜同时还具有一定的吸振能力川,这对提高轴承运转的稳定性和运转精度都是十分有益的。
滑动轴承的种类繁多,按轴承受力方向可分为径向滑动轴承、止推滑动轴承、径向止推滑动轴承按轴承所用的润滑剂来分可分为液体润滑滑动轴承、气体润滑滑动轴承、脂润滑滑动轴承和固体润滑滑动轴承,其中液体润滑滑动轴承又可分为油润滑滑动轴承、水润滑滑动轴承及磁流体润滑滑动轴承按轴承轴瓦材料来分又可分为金属滑动轴承、非金属滑动轴承和多孔质滑动轴承等等。
流体润滑滑动轴承又可分为流体动压润滑滑动轴承、流体静压润滑滑动轴承和流体动静压混合滑动轴承 121。
流体动压润滑滑动轴承有着长久的历史,它的应用研究己超过 10 年,其应用范围也是上述各种滑动轴承中最广泛的。
流体动压润滑,就是依靠被润滑的一对固体摩擦面间的相对运动,使介于固体摩擦面间的流体润滑膜内产生压力,以承受外载荷而免除固体相互接触,从而起到减少摩擦阻力和保护固体摩擦表面的作用。
自从 B.Tower 在其著名实验中发现了动压现象,继由0.Renyolds 分析了动压润滑的机理并导出了描述润滑膜压力分布的微分方程,即著名的雷诺方程,遂奠定了流体动力润滑理论的原始基础。
此外,流体动力润滑理论中还有其它的一些方程,如:流动的连续性方程、润滑剂的状态方程粘度和密度方程、表面的弹性方程、以及能量方程等。
当然应用最广的还是雷诺方程及其在各种具体条件下的变形形式,以及它们的求解。
由于这些理论的建立使得滑动轴承的研究取得了很多成果,促进了其在实际中的应用。
1.3本课题研究的主要内容及基本工作思路(一)主要内容根据所给技术指标对某型汽轮机液体动压径向滑动轴承进行设计计算以及性能分析。
(二)本课题的基本工作思路1.在液体动压径向滑动轴承的基本原理和雷诺方程的基础上设计滑动轴承。
2.计算内容包括:几何参数,安全度等方面3.关键理论和技术:流体动力的基本方程摩擦定律雷诺方程第二章2液体动压径向滑动轴承的总体设计方案2.1滑动轴承《机械设计》是一门培养学生机械设计能力的技术基础课。
在机械类各专业的教学计划中,它是主要课程。
机械设计课程在教学内容方面着重基本知识、基本理论和基本方法的掌握,在培养实践能力方面着重设计构思和设计技能的基本训练,使学生对实际工程具有分析、解决问题的能力,在设计中具有创新思维。
滑动轴承章节在整个课程的学习中又占到了很重要的部分。
滑动轴承的承载能力大,回转精度高,表面能形成润滑膜将运动副分开,减少了磨损,滑动摩擦力也可大大降低,并且润滑膜具有抗冲击作用,因此,在工程上获得广泛的应用。
2.1.1滑动轴承的主要类型和结构按受载荷方向不同,滑动轴承可分为径向滑动轴承和止推滑动轴承。
1径向滑动轴承径向滑动轴承用于承受径向载荷。
图2—1所示为整体式径向滑动轴承,图 2 -2所示为剖分式径向滑动轴承。
剖分式径向滑动轴承装拆方便,轴瓦磨损后可方便更换及调整间隙,因而应用广泛。
图2-1整体式滑动轴承图2-2剖分式滑动轴承2.止推滑动轴承止推滑动轴承用来承受轴向载荷。
按轴颈支承面的形式不同,分为实心式、空心式、环形式三种。
当轴旋转时,实心止推轴颈由于端面上不同半径处的线速度不相等,因而使端面中心部的磨损很小,而边缘的磨损却很大,结果造成轴颈端面中心处应力集中。
实际结构中多数采用空心轴颈,可使其端面上压力的分布明显改善,并有利于储存润滑油。
2.2液体动压润滑的基本原理和基本关系(一)液体动压油膜形成的原理图2-3动压油膜形成原理图液体动压油膜形成原理是利用摩擦副表面的相对运动,将液体带进摩擦表面之间,形成压力油膜,将摩擦表面隔开,如图 2-3 所示。
两个互相倾斜的平板,在它们之间充满具有一定粘度的液体。
当 AB 以速度 V 向左移动,而 CD 保持静止时,液体在此楔形间隙中作层流流动。
当各流层的速度分布规律为直线时,由于进口间隙大于出口间隙,则进口流量必大于出口流量但液体是不可压缩的,因此,在楔形间隙内形成油压,迫使大口的进油速度减小,小口的出油速度增大,从而使流经各截面的液体流量相等。
同时,楔形油膜产生的内压将与外载荷相平衡。
(二)液体动压润滑的基本方程雷诺方程是液体动压润滑基本方程,是研究流体动力润滑的基础。