GCr15钢中网状碳化物在锻造及热处理过程中的形态变化_县晓明
GCr15轴承钢的热处理工艺设计

热处理工艺课程设计说明书课程名称:金属热处理工艺学设计题目:GCr15轴承钢的热处理工艺设计院系:机械工程学院班级:材料成型及控制工程 XXXX 学号: 0 9 1 1 0 1 1 00学生姓名: idealwang指导教师:黄老师热处理工艺课程设计任务书目录1 热处理工艺课程设计的目的 --------------------42 零件的技术要求及选材 ------------------------4 2.1工作条件和技术要求 -------------------------4 2.2材料的选择 ---------------------------------52.3化学成分及合金元素的作用 -------------------63 热处理工艺课程设计的内容及步骤 ---------------7 3.1相变点的确定 ----------------------------------7 3.2热处理工艺 ----------------------------------8 3.2.1工艺流程-------------------------8 3.2.2热处理工艺参数的制定-------------10 3.2.3处理工艺卡片填写---------------------12 3.2.4作过程中的注意事项 ------------------------------12 3.3家具的设计或者选用及零件的摆布------------------------13 3.4热处理设备的选择-----------------------16 3.5组织特点和性能的分析 ------------------------------16 4总结---------------------------------------------215 收获和体会 ---------------------------------236 参考文献 -----------------------------------237 附表 1 热处理工艺卡 -------------------------25§1 热处理工艺课程设计的目的热处理工艺课程设计是高等学校金属材料工程专业一次专业课设计练习,是热处理原理与工艺课程的最后一个教学环节。
控制大断面GCr15轴承钢网状碳化物析出的轧制方法[发明专利]
![控制大断面GCr15轴承钢网状碳化物析出的轧制方法[发明专利]](https://img.taocdn.com/s3/m/3e07ac39ba68a98271fe910ef12d2af90342a87e.png)
(19)中华人民共和国国家知识产权局(12)发明专利申请(10)申请公布号 (43)申请公布日 (21)申请号 201610750155.6(22)申请日 2016.08.29(71)申请人 湖北新冶钢有限公司地址 435001 湖北省黄石市黄石大道316号(72)发明人 李小龙 周敦世 周立新 程卫国 李德胜 徐尚呈 邹晖 黄国飘 (74)专利代理机构 北京五洲洋和知识产权代理事务所(普通合伙) 11387代理人 刘春成 荣红颖(51)Int.Cl.C21D 8/06(2006.01)(54)发明名称控制大断面GCr15轴承钢网状碳化物析出的轧制方法(57)摘要本发明公开了一种控制大断面GCr15轴承钢网状碳化物析出的轧制方法,该方法以GCr15连铸坯为原料,依次包括如下工序:加热、除鳞、粗轧、中轧、预精轧、第一次穿水冷却、棒材减定径机组精轧、第二次穿水冷却、冷床冷却,最终得到成品棒材。
采用该方法得到大断面GCr15轴承钢的网状碳化物级别由原来的≥3级降低至≤2级,不但提高了高碳铬轴承钢的综合机械性能,延长了轴承的使用寿命,而且降低了生产成本,提高了轴承钢市场竞争力。
权利要求书1页 说明书10页 附图2页CN 106086353 A 2016.11.09C N 106086353A1.一种控制大断面GCr15轴承钢网状碳化物析出的轧制方法,其特征在于,以GCr15连铸坯为原料,依次包括如下工序:加热、除鳞、粗轧、中轧、预精轧、第一次穿水冷却、棒材减定径机组精轧、第二次穿水冷却、冷床冷却,最终得到成品棒材。
2.根据权利要求1所述轧制方法,其特征在于,所述加热工序中,对所述连铸坯进行加热,均热温度为1200~1230℃;优选地,所述加热分为四段加热,依次为预热段、加热一段、加热二段和均热段,所述预热段的温度为600~700℃,所述加热一段的温度1000~1100℃,所述加热二段的温度1180~1230℃,所述均热段的温度1200~1230℃;进一步优选地,所述加热工序中的总加热时间为10~15h,均热时间为5~8h。
GCr15轴承钢组织控制毕业论文
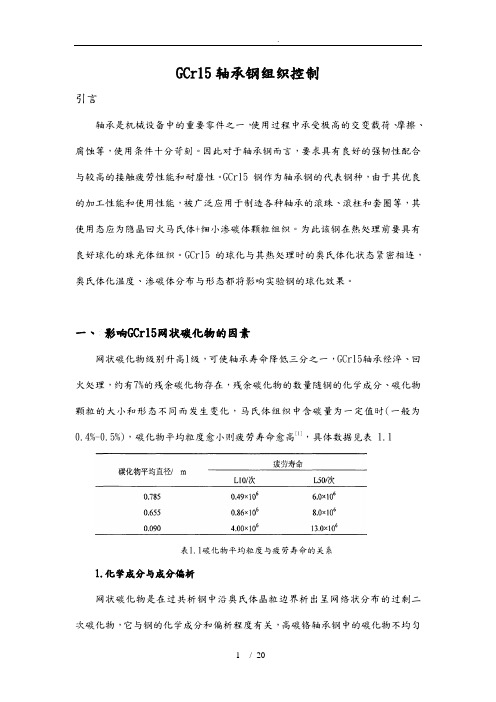
(奥氏体化温度1O50oC)
当GCr15钢奥氏体化温度为1050℃、二次碳化物全部固溶时,连续冷却转变图出现了二次碳化物开始析出曲线,即过冷奥氏体在发生珠光体或贝氏体转变之前,将首先沿奥氏体晶界析出网状碳化物。二次碳化物的析出主要取决于冷却速度,其析出的数量不仅与碳在奥氏体中的过饱和度有关,而且碳化物形成元素的扩散条件也具有一定影响。
(2)在不平衡条件下结晶(二元素在固相中不能充分扩散)
当温度沿t、t1、t2…变化时,液相成分沿a、al、a2…变化,固相则按凝固先后顺序存在着b、b1、b2…不同的化学成分。合金温度降到tp时还不会完全凝固,要一直冷到tk温度,合金才凝固完毕。图中c、cl、c2、…ck为从开始凝固起到某一结晶区间的结晶固相的平均成分。。k即为凝固结束时固相的平均成分。固相中存在着b、b1、b2…bp不同成分的差异,即合金的偏析。
表1.1碳化物平均粒度与疲劳寿命的关系
1.化学成分与成分偏析
网状碳化物是在过共析钢中沿奥氏体晶粒边界析出呈网络状分布的过剩二次碳化物,它与钢的化学成分和偏析程度有关,高碳铬轴承钢中的碳化物不均匀性实质上是钢液在冷却过程中宏观和微观偏析的结果。网状碳化物是过剩的二次碳化物,因此钢中含有碳化物形成元素的浓度愈高,过剩的二次碳化物数量就愈多,碳化物网状组织也就愈严重。钢液结晶时,由于选分结晶,最先凝固的部分溶质含量较低,溶质集聚于母液,浓度逐渐增加,因而最后凝固的部分溶质含量则很高。显然在最终凝固结构中溶质浓度分布是不均匀的,这种成分不均匀的现象称为偏析。如果分析晶粒的成分分布时,我们会发现钢锭或铸坯中心溶质浓度较高;而在一个晶粒的晶界处溶质的浓度较高。前者为宏观偏析,后者为显微偏析。
GCr15钢中网状碳化物在锻造及热处理过程中的形态变化

偏高 、 冷却 不 良产生 的锻 造 网。 可见 , 造 后 网状碳 化 物 超 标 主 要 存 在 形 成 锻 机理 不 同 的两 种 类 型 : 料 网和 锻 造 网。对 于 因 材
[ ] 樊东黎. 3 热处理技术 数据手 册 [ . 京 : M] 北 技术 工业
出版 社 ,0 0 20.
《 轴承) 0 2 №. } 1. 8 2
厚壁 锻件 锻造 时 中频 加热 到 110℃透烧 , 5 锻
造温 度偏 高是 晶粒 粗化 的主 要原 因。其 次 锻造 摩
擦 发热 , 促使 锻 件 温 度 、 热 出 现 反 弹 , 之 终 锻 蓄 加
4 结论
() 1 中频 热 切 下 料 加 热 温度 低 , 间 短 , 材 时 对
承 的 成 品 检 验 , 详 细 介 绍 了这 些 检 验 的 检 测 项 目 、 测 方 法 和 判 断 标 准 。 还 检
中 国 计 量 出版 社 出版 , 册 定 价 3 每 8元 , 寄 费 1 元 。 需 要 者 请 与 洛 阳 轴 邮 O
承 研 究所 有 限 公 司技 术 资料 发 行 室 陈 红 帆 联 系 。 电 话 :3 9—6 8 15 07 4 8 0 1
环 节冷 却 速 度不 足 造 成锻 件 在 A m —A l温 度 区 c r
间热量 散失 缓慢 、 过程 延 长 , 为二 次 封 闭 网状碳 成
料表 层组织 中珠 光体 、 网状 碳化 物 仅 有局 部 溶 解 、
破断 的作 用 , 不 足 以改 变 热 轧 材 原 始 组 织 中 网 但 状碳 化物 的分 布特 征 。
选用 3种 规格 、 炉号 的热 轧材 作 为对 比材 4个
料 , 加 工工 艺 以实 际生 产工 艺为 准 , 却 方 式及 热 冷
GCr15钢的特性、化学成分、热处理工艺及应用 2

GCr15钢的特性、化学成分、热处理工艺及应用⒈GCr15钢的特性GCr15钢是在T10A钢的基础上主要加入Cr元素而研制成的。
GCr15钢特性如下:⑴、GCr15钢中加入Cr元素主要是为了提高钢的淬透性,同时固溶于基体强化基体组织。
另外,Cr元素溶入Fe3C中形成复合(Fe、Cr)3C可提高其硬度,增加钢的硬度与耐磨性。
⑵、由于钢中加入单一的弱碳化物形成元素Cr,GCr15钢的力学性能、耐磨性、淬透性和淬火变形不如CrWMn钢。
⒉GCr15钢主要化学成分0.95%~1.05%C、0.25%~0.45%Mn、1.40%~1.65%Cr、0.15%~0.35%Si、≤0.025%P、≤0.025%S。
⒊GCr15钢的热处理工艺GCr15钢相变点为:AC1745℃、Accm900℃、Ar1700℃、Ms235℃。
GCr15钢的始锻温度为1050~1100℃,终锻温度为800~850℃,锻造后空冷至700℃,在砂中冷却或坑中冷却。
GCr15钢常见的热处理工艺热处理铜套工艺工艺参数硬度要求工艺特点不完全退火加热770~790℃,保温后随炉冷却至550℃以下出炉空冷187~229HBS Ac1745℃,Accm900℃,加热温度应Ac1~Accm在之间等温球化退火加热770~790℃,680~700℃等温后随炉冷却至550℃以下出炉空冷187~229HBS加热温度应在Ac1~Accm之间,等温温度应低于Ar1700℃线20℃,以获得粒状珠光体组织去应力退火加热600~700℃,保温,空冷187~229HBS消除残余应力,消除加工硬化正火加热930~950℃,保温,空冷302~388HBS加热温度高于Accm,消除偏析、带状组织、网状组织,细化晶粒淬火加热830~850℃,保温,油冷62~65HRC淬火加热温度在Ac1~Accm之间,Cr元素的溶解,提高淬透性,改善回火稳定性,同时也降低Ms点,有不少残留奥氏体存在下贝氏体等温淬火加830~850℃,240~300℃硝盐浴等温,后出浴空冷58~62HRC Ms202℃,等温淬火组织为下贝氏体+碳化物+少量马氏体+极少量残余奥氏体,淬火变形很小,强度高,韧性好回火加热150~190℃,保温2h,炉冷58~~62HRC强调硬度取下限,强调韧性取上限调质淬火:加热840~860℃,油冷;回火:加热660~680℃,保温后炉冷或空冷197~217HBS 高温淬火可以消除碳化物组织缺陷,高温回火得到细小的回火索氏体组织,为再淬火做组织准备,在改善韧性同时,提高强度。
GCr15轴承钢过热_带状组织_的分析_查敏

GCr15轴承钢过热“带状组织”的分析上海交通大学国家教委高温材料及高温测试开放实验室(上海 200030) 蔡 查 敏 张惠娟【摘要】 对GCr15轴承钢进行了不同淬火和回火热处理工艺试验。
发现当淬火加热温度过高时,淬火组织中将会呈现出一种明暗相间的过热“带状组织”,这是由于样品中不同区域高温下含铬碳化物溶解难易程度不同导致抗蚀性能差别而引起的。
它与轴承钢原始组织的碳化物带状组织有联系而又有区别。
关键词:轴承钢 感应热处理 过热 带状组织Analysis on the Overheated Zonal Structure of Bearing Steel GCr15Cai Xun,Zha Min,Zhang Huijua n(Sha ng hai J iao To ng U niv ersity,Public Labor ato ry o f State Educa tio n Co mmissio no f P.R.CHIN A for H igh T emperatur e M aterials a nd H igh T empera tur e Tests,Shanghai200030)【Abstract】 Differ ent har dening and tem pering tests o f bea ring steel wer e per for med.It is fo und that a brigh t-da rk zo na l str uc-ture can be o btained due to ov erhea ted opera tio nal temper atur e.The reaso n fo r th e zonal str uctur e is the diffe rence in the co rro-sio n resistance of va rio us zo nes o f th e sample as a result o f v ariable disso lution ra te o f chr omium car bide at the high austenitiz-ing tempe ratur e.It is co nce rned with the car bide banded str uctur e in the prio r sturcture o f bea ring steel.Key words:bea ring steel,induction heat tr eatment,o ve rheating,zonal structur e1 前言为提高硬度和耐磨性,GCr15轴承钢在加工成零件后均需进行淬火+回火热处理。
GCr15轧后控冷碳化物网状问题浅析

12
水冷至 500 ℃,空冷
珠光体 + 渗碳体 + 边缘部份淬火马氏体
3
12 12 水冷至 200 ℃,空冷
淬火马氏体
1. 5
13 12 水冷至 200 ℃,空冷
淬火马氏体
1. 5
选定表 1 中的第 9 、10 的实验方案 ,确定淬火后“返 红”温度为 700 ℃的空冷工艺 ,既可保证组织状态为
“珠光体 + 渗碳体”,又可保证碳化物网状级别 。 根据试验情况和现场控制情况 ,决定采用如下
要转变区域 ,冷却时应尽量控制在此区间 ,使得残余 奥氏体尽可能在珠光体区转变成珠光体 ,避免脆性 马氏体的形成 。
根据图 1 中 CCT 曲线看出 ,在 530 ℃~700 ℃之 间有效保温时间为 25 s~300 s ,即可以完成珠光体 的转变 ,故减少转变时间 ,加快转变速度 ,可以减少 碳化物网状的形成 ,对图中的温度控制和冷却转变 速度的摸索将结合组织和碳化物网状级别进行 。 2. 3 长城特钢试验生产工艺研究
·18 ·Vol. 9. No. 3. Sum. 40. SPECIAL STEEL TECHNOLOGY 第 9 卷第 3 期总第 40 期
表 1 不同冷却条件下的碳化物网状情况 Table 1 The carbide’s network results of
defficent cooling telogical process
关键词 GCr15 盘元 控制冷却 穿水温度 穿水速度 回火温度 碳化物网状
Analysis on Carbide’s Network f or GCr15 Bearing
Coil by Control the Rate of Cooling
GCr15轴承钢加热温度与碳化物的溶解扩散

上述试验说明, GC r15轴承钢加热到 1200 时, 碳化 物液析完全溶解, 但还存在碳化物的高浓度区, 这也说明 提高加热温度, 延长加热时间, 可以消除液析, 但成品钢 材上碳化物带状很难消除, 只能在一定程度上得到改善。
2 现场加热工艺改进及效果
根据轴承钢加热温度与碳化物溶解扩散试验研究 的结果, 对轧制前的加热工艺进行了改进。将改进前
碳化物液析属于三角晶系碳化物, 硬度极高, 它的 纹。在使用过程中, 处于表面层的液析碳化物容易剥
存在会使轴承零件在热处理过程中容易产生淬火裂
落成为磨损的起源, 显著降低轴承零件的耐磨性; 处于
作者简介: 刘 靖 ( 1965 08 ), 女, 副 教授, 博士, 主 要从 事轧 制过程组织 性能控制及复合板 轧制研究, 已发表论文 20余篇。 联 系 电 话: 010 62332572, 13520330657 E m ai:l liu jing @
轴承钢GCr15碳化物不均匀性金相分析与工艺建议

轴承钢GCrl5碳化物不均匀性金相分析与工艺建议李晟(科技质量部)摘要:通过金相分析,简要介绍了轴承钢GCrl5碳化物不均匀性的表现形式、分级判定、形成原因及应用危害;结合实际钢种CCT曲线及碳化物析出规律,探讨并提出了控制轴承钢GCrl5碳化物不均匀性适宜的工艺路径与措施。
关键词:轴承钢碳化物金相工艺Metallographic Research on Nonuniformity of Carbidein Bearing Steel GCrl5and Suggestions on Process ImprovementLI Sheng(Science&Technology and Quality Department)Abstract:Combining the metallographic analysis,this article briefly introduces the manifestation,grading judgment, causes and application hazards of carbide nonuniformity Bearing Steel GCrl5.By analyzing the CCT curves and the separation principles of carbide,appropriate process and measures for controlling nonuniformity of carbide in Bearing Steel GCrl5were also discussed and proposed.Keywords:Bearing Steel,Carbide,Metallography,Process—»-X-->—刖旨GCrl5是高碳饼轴承钢的代表钢种,它的综合性能良好,淬火和回火后具有高而均匀的硬度,良好的耐磨性和高的接触疲劳寿命,适宜于制造各种轴承套圈及滚动体。
【精品】滚动轴承用钢GCr15钢的热处理原理

第一章滚动轴承用钢GCr15钢的热处理原理一、滚动轴承用钢应具有的特性1、高的接触疲劳强度;2、高的耐磨性;(发生滑动摩擦的主要部位)1)、滚动体与滚道的接触面;2)、滚动体与保持架兜孔的接触面;3)、保持架引导与套圈引导档边的接触面;4)滚子的端面与套圈档边的接触面。
3、高的弹性极限;4、高的硬度;5、一定的韧性;6、好的尺寸稳定性;7、一定的防锈功能;8、良好的工艺性能。
二、GCr15钢的物理性能1、GCr15钢的临界点:Ac1:760℃Acm:900℃Ar3:707℃Ar1:6952、GCr15钢的Ms点:Ms点随着奥氏体固溶度的变化而变化,亦即随着奥氏体温度的升高而降低,GCr15钢在860℃温度Ms点为216~225℃。
三、铬轴承钢热处理基础1、基本概念1)、奥氏体:是碳及合金元素溶于r-Fe八面体间隙的间隙式固溶体。
特征:[1]、在钢的各种组织中,奥氏体的比容最小;[2]、奥氏体的塑性高,屈服强度低,容易塑性变形加工成型。
2)、珠光体:是过冷奥氏体共析分解的铁素体和碳化物的整合组织片状珠光体:是指在光学显微镜下能够明显看出F与Fe3C呈片状分布的组织状态。
根据片间距的大小分为普通片状珠光体、索氏体、屈氏体。
粒状珠光体:铁素体基体上分布着粒状Fe3C的组织。
GCr15的正常锻造后组织应为细珠光体类型组织及细小的网状碳化物组成,不允许有>3级的网状碳化物及明显线条状组织,不允许有粗针状马氏体和粗片状珠光体组织。
3)、马氏体:是碳在α-Fe中的过饱和固溶体。
马氏体分类:板条马氏体、片状马氏体、针状马氏体、隐晶马氏体。
GCr15钢淬火后得到的马氏体为隐晶马氏体或者细小结晶马氏体。
马氏体具有高的硬度、强度、耐磨性。
4)贝氏体:是过冷奥氏体在中温区域分解后所得的的产物,它一般是由铁素体和碳化物所组成的非层状组织。
贝氏体分类:上贝氏体、下贝氏体上贝氏体:是一种两相组织,有铁素体和Fe3C所组成的,大致平行的铁素体板条自奥氏体晶界的一侧或两侧向奥氏体晶粒内部长大,Fe3C分布于铁素体板条之间。
GCr15轴承钢高温变形后控冷工艺的研究
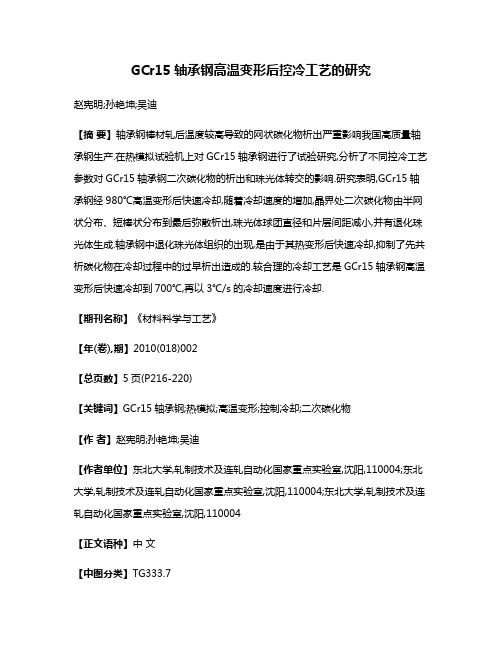
GCr15轴承钢高温变形后控冷工艺的研究赵宪明;孙艳坤;吴迪【摘要】轴承钢棒材轧后温度较高导致的网状碳化物析出严重影响我国高质量轴承钢生产.在热模拟试验机上对GCr15轴承钢进行了试验研究,分析了不同控冷工艺参数对GCr15轴承钢二次碳化物的析出和珠光体转交的影响.研究表明,GCr15轴承钢经980℃高温变形后快速冷却,随着冷却速度的增加,晶界处二次碳化物由半网状分布、短棒状分布到最后弥散析出,珠光体球团直径和片层间距减小,并有退化珠光体生成.轴承钢中退化珠光体组织的出现,是由于其热变形后快速冷却,抑制了先共析碳化物在冷却过程中的过早析出造成的.较合理的冷却工艺是GCr15轴承钢高温变形后快速冷却到700℃,再以3℃/s的冷却速度进行冷却.【期刊名称】《材料科学与工艺》【年(卷),期】2010(018)002【总页数】5页(P216-220)【关键词】GCr15轴承钢;热模拟;高温变形;控制冷却;二次碳化物【作者】赵宪明;孙艳坤;吴迪【作者单位】东北大学,轧制技术及连轧自动化国家重点实验室,沈阳,110004;东北大学,轧制技术及连轧自动化国家重点实验室,沈阳,110004;东北大学,轧制技术及连轧自动化国家重点实验室,沈阳,110004【正文语种】中文【中图分类】TG333.7轴承在机械产品和工程结构中应用十分广泛,轴承钢组织中碳化物的尺寸、形态和分布直接影响其接触疲劳强度和力学性能.GCr15轴承钢在轧后奥氏体状态下的冷却过程中,有二次碳化物析出,并在奥氏体晶界形成网状碳化物.如何降低网状碳化物级别,是热轧轴承钢急需解决的重大问题之一[1].钢材热变形后通过控制冷却可以改善其组织性能,细化奥氏体晶粒,抑制或延迟碳化物在冷却过程中的过早析出[2].近年来,在轴承钢生产领域,运用控轧控冷工艺解决网状碳化物严重析出问题已经开展了大量的工作,并取得一定的成果.轴承钢的轧后超快速冷却能够使碳化物微细、弥散析出[3].GCr15滚动轴承钢原始组织中碳化物的弥散均匀分布,直接提高其使用寿命 .本文以建立的CCT曲线为依据,对轴承钢热变形后不同冷却工艺进行模拟,分析了高温变形后冷却速度对轴承钢组织的影响,以期抑制轴承钢网状碳化物的析出,得到细小片层状珠光体组织.试验所用材料为由GCr15轴承钢棒材经过线切割制成Φ8 mm×15 mm圆棒,化学成分如表1所示.试验钢连续冷却转变曲线的测定和高温变形后快速冷却工艺模拟分别在Gleeble1500热模拟试验机和东北大学国家重点实验室自主研发的MMS-300多功能热力模拟试验机上进行,试样两端涂抹石墨粉以减少端部摩擦所造成的鼓肚效应.热模拟试验后将试样沿横向在靠近热电偶焊点处剖开,磨抛后采用4%硝酸酒精溶液腐蚀制成金相试样,组织观察在LEICA DMIRM多功能金相显微镜和FEI-Quanta 600扫描电镜上进行.对高温变形后不同冷速下的试样在1/2半径处进行布氏硬度试验.为了准确分析采用不同冷却速度对二次碳化物析出的影响,对热变形后不同冷却速度连续冷却到室温的试样进行淬-回火试验,经4%硝酸酒精溶液深腐蚀,挑选网状碳化物最严重区域,按照GB/T18254-2002进行网状评级.首先对GCr15钢进行CCT曲线的测定.将试样以10℃/s加热至奥氏体化温度1100℃,保温300 s后以10℃/s冷却至不同的变形温度,进行不同变形量单道次压缩变形,然后分别以不同连续冷却速度0.5、1、2、3、4、5、8、10、20、40、200℃/s冷却至室温.其中,变形温度(θ)和变形量(ε)分别为980℃和40%,变形速率为5/s,试验工艺如图1(a)所示.然后对其高温变形后快速冷却工艺进行模拟试验.将试样以10℃/s加热到1100℃,保温300 s后以10℃/s冷却至980℃,在980℃进行变形量为 40%的压缩变形,再以10℃/s的冷却速度冷却到700℃后,分别以不同冷却速度连续冷却到室温.具体试验工艺见图1(b).图2(a)为GCr15轴承钢980℃在40%变形条件下的CCT曲线.其中A、C、P分别代表奥氏体、碳化物和珠光体.对其高温变形后分别以1、3、5℃/s的冷却速度冷却室温,其冷却路径示意图见图2(b)中的粗线箭头.GCr15轴承钢高温变形后以10℃/s冷却到700℃,再分别以1、3、5℃/s冷却速度(v)冷却至室温的金相组织如图3所示.图3中,GCr15轴承钢高温变形后以10℃/s冷却到700℃,在接下来的冷却过程中,随着冷却速度的增加,晶界处二次碳化物析出减少.冷却速度为1℃/s时,呈网状连接的二次碳化物在晶界处仍隐约可见(图3(a));冷却速度增加到3℃/s时,晶界处仍有少量白色二次碳化物析出,但晶界处二次碳化物为短棒状,且网状结构已极大的减轻(图3(b));冷却速度达到5℃/s时由于冷却速度较快,在珠光体转变区域停留时间过短,残余奥氏体没有完全发生珠光体转变,室温组织如图3(c)所示,其中灰黑色基体组织为珠光体,灰白色块状组织为淬火马氏体和残留奥氏体组织,晶界处没有发现白色网状二次碳化物析出.图4为以不同冷却速度冷却到室温后对应的扫描电镜照片.图4中,GCr15钢高温变形后冷却速度为1℃/s时,扫描电镜下可以看到晶界处呈较为明显的网状分布的二次碳化物,而且,由于冷却速度相对较慢,珠光体球团直径和组织片层间距相对较大(图4(a));冷却速度为3℃/s时,不仅网状二次碳化物分布不再明显,而且,珠光体球团直径和片层间距相对减小(图4(b));冷却速度为5℃/s时,组织中已看不到网状二次碳化物,得到马氏体和珠光体的混晶组织(图4(c)).将上述的GCr15钢试样淬火-回火,其金相组织如图5所示.从图5可以看到,试验钢经淬-回火后深腐蚀,其组织为黑色回火马氏体及其上分布的白色二次碳化物.随着冷却速度变化,其基体上分布的白色碳化物数量和形状也发生变化.冷却速度1,3,5℃/s所对应的二次碳化物网状级别依次为4,2~3,1~2.热变形后以1℃/s连续冷却到室温,二次碳化物呈现不完整的网状分布,网状级别为4级;冷却速度为3℃/s时,由于冷却速度增加,二次碳化物析出量减少,网状趋势大大减弱,组织中二次碳化物已大部分呈断续的短棒状甚至点状,少部分由网状变为条状分布,评定级别应在2~3;冷却速度进一步增大达到5℃/s时,二次碳化物虽未完全弥散分布,但至多呈现点条状分布,完全看不到网状结构,网状级别在1~2级,达到标准.硬度测试表明,GCr15轴承钢980℃高温变形后分别以1℃/s冷却速度冷却,其布氏硬度最低,平均为HB354;以3℃/s冷却,其布氏硬度明显升高,平均为HB360;而以5℃/s冷却时,其布氏硬度最高,平均值达HB373.这是由于试样中晶界处二次碳化物随连续冷却速度增加依次从半网状、短棒状到弥散分布演化的结果.GCr15轴承钢属于过共析钢,由于碳含量较高,自奥氏体区连续冷却过程中,随着温度降低,将导致碳从过饱和奥氏体中析出,形成富铬的碳化物,即首先从奥氏体中析出先共析二次碳化物.通常,这种二次碳化物会优先在晶界上以仿晶界型网状形式排列形核长大[5].二次碳化物的析出主要取决于冷却速度,其析出的数量不仅与碳在奥氏体中的过饱和度有关,而且与碳化物形成元素在奥氏体中的扩散条件有关.轴承钢中C、Cr等元素的扩散受温度影响很大.这些元素沿奥氏体晶界的扩散速度远远大于晶内扩散速度(相差102~103倍),这也是二次碳化物多沿晶界析出,从而形成断续或者连续的网络状组织的原因.通过对CCT曲线分析可知,GCr15钢在热变形后的连续冷却过程中,二次碳化物析出主要温度区域为850~700℃,珠光体转变主要温度区域为750~500℃(图2).GCr15轴承钢在连续冷却过程中,当冷却速度缓慢时,由于晶界处缺陷多,C、Cr等碳化物形成元素在缓慢冷却过程中首先扩散到晶界处,在晶界处聚集长大、并置换铁形成Cr的合金碳化物,这些合金碳化物大量析出并连接成骨骼状紧密网状组织,形成网状碳化物.随着冷却速度增加,虽然仍然有C、Cr元素会向晶界处扩散并在晶界处聚集长大,但由于冷却速度增大,在二次碳化物析出区停留时间减小,C、Cr在高温区扩散时间减少,因此,晶界处析出的二次碳化物数量减少.试验钢高温变形后快速冷却至700℃以下,冷却速度足以快速通过二次碳化物析出温度区,然后减慢冷却,将使过冷奥氏体在珠光体转变温度区域完全发生珠光体转变.轴承钢晶界处二次碳化物随连续冷却速度增加而发生的形态变化,根据第二相强化理论,位错线以奥罗万模型绕过钢中的这种二次碳化物(第二相)质点,显然,随着相邻质点的间距减小,位错线的运动阻力增加,即质点的数量越多、越弥散,轴承钢的强度和硬度越高.当GCr15轴承钢试样以5℃/s冷却时,晶界处二次碳化物分布相对最为弥散(图5(c)),强度最高.由于硬度值是表征材料强度和韧性等一系列不同物理量组合的一种综合性能指标,因此,表现出了随冷却速度增加,试样中布氏硬度平均值增高的变化趋势.通常,过共析钢在发生珠光体转变前,会有先共析渗碳体的析出,即发生先共析转变.平衡状态下先共析碳化物的析出温度和成分范围表明,当过饱和奥氏体快速冷却到相变点以下的区域时,则会因同时对铁素体和渗碳体过饱和而直接进行珠光体转变[6].GCr15轴承钢高温变形后快速冷却至700℃以下,抑制了先共析碳化物的析出.由700℃至室温,以1℃/s冷却速度冷却,由于冷速相对较慢,钢在700℃以下相对较高的温度停留时间较长,发生先共析碳化物的析出,并在缓慢冷却过程中沿晶界处聚集长大并连接成网状形成网状碳化物,剩余奥氏体中含碳量则不断降低到共析点时才发生珠光体转变.由于碳化物在700℃以上的高温尚来不及析出,因此,碳化物网状结构并不十分明显.以3℃/s冷却时,由于冷速相对加快,过冷奥氏体在先共析碳化物析出区停留时间减少,虽然不能完全抑制先共析碳化物的网状析出,但先共析碳化物析出量明显减少,碳化物网状结构极大的减弱.以5℃/s冷却,由于冷速很快,阴影区浓度差值变大,则珠光体转变前先共析碳化物的析出及聚集长大非常困难,网状碳化物的析出被完全消除,GCr15钢由700℃被过冷到阴影区将同时析出铁素体和渗碳体,形成伪珠光体组织,达到了抑制网状碳化物析出的目的.上述网状碳化物析出的原理可以通过图2中的CCT曲线,在不同冷却速度条件下各相的析出过程得到合理的解释.GCr15轴承钢在980℃经40%的压缩变形,变形过程中所消耗的功,部分以形变储能形式存在,造成晶体点阵畸变和位错密度的增高,有利于C和Fe原子的晶体点阵重构,变形使能量升高,相变驱动力增大.同时,GCr15钢在700℃冷却速度加快,过冷度增大,亦使珠光体的相变驱动力增大.所以,珠光体的形核率增大.此外,变形在奥氏体中形成变形带,变形带可以起到分割奥氏体晶粒的作用,即奥氏体晶粒内部产生的变形带可以将奥氏体晶粒分割成几个小区域,因而增加了珠光体晶核的形核部位[7-8].变形对相变的加速作用还由于奥氏体晶界会发生应变集中,从而提高了晶界上珠光体晶核的形核率.因此,奥氏体向珠光体转变时珠光体晶核不仅可以在原奥氏体晶界上生成,而且可以在奥氏体晶粒内部生成,单位体积内晶界面积增大,达到了细化晶粒的目的,珠光体团尺寸变小.钢在700℃以不同冷却速度冷却,冷却速度增大,较低温度发生铁素体和渗碳体同时析出的伪共析反应.由于较大冷速使转变温度降低,碳原子扩散能力减小,不易进行较大距离迁移,渗碳体片和铁素体片逐渐变薄缩短.由于其长大速度减慢,珠光体团的轮廓也由块状逐渐变成扇形、团絮状等,珠光体球团直径和片层间距都更加细小,部分渗碳体片断开,呈短棒状或颗粒状.出现较为理想的退化珠光体组织.当然,冷却速度过大,虽然消除了网状碳化物,但在得到退化珠光体组织的同时,组织中同时也出现了马氏体,马氏体在使钢强化的同时损失了塑性,这是需要避免的.因此,GCr15轴承钢在700℃冷却时,应当严格控制其终冷温度,其冷却速度亦不易过大.高温变形后经过以3℃/s的较快冷却速度冷却,能够减小珠光体球团直径和珠光体片层间距,并基本消除网状碳化物,获得退化珠光体组织,因此,以3℃/s的冷却速度冷却应相对较为合适.GCr15轴承钢产品中存在大量碳化物.该钢高温变形后以10℃/s冷却到700℃以下,再以3℃/s冷却速度冷却,抑制了晶界处网状碳化物析出,热轧轴承钢基本能够得到细小的片层珠光体组织.1)GCr15轴承钢采用高温变形后以10℃/s冷却度速冷却至700℃以下,冷却速度足以快速通过二次碳化物析出温度区,能够有效地改善其组织形态,模拟试验取得了良好效果.2)GCr15轴承钢高温变形后快速冷却到700℃,再分别以不同冷却速度冷却.冷速较慢时,组织中仍含有网状碳化物;冷速过快,组织中淬火马氏体出现;当以3℃/s冷却速度冷却时,二次碳化物呈网状分布不再明显,而且,珠光体球团直径和组织片层间距相对减小,获得退化珠光体组织.因此,以3℃/s的冷却速度冷却相对较为合理.3)GCr15轴承钢中退化珠光体组织的出现,是由于其热变形后控制冷却,抑制了先共析碳化物在冷却过程中的过早析出,使其最终在基体组织中弥散析出,碳原子扩散能力低,无法进行较大距离迁移造成的.【相关文献】[1] WANG Y,YAN F G,WANG P.Finite element analysis of precision hard cutting using different cutting edge preparation[J].Applied Mechanics and Materials,2008,10-12:353-358.[2]刘宗昌.珠光体转变与退火[M].北京:化学工业出版社,2007.[3]王国栋,新一代TMCP的实践和工业应用举例[J].上海金属,2007,30:1-4.[4]郑逊昭,夏玉洲,陈文耀.GCr15轴承钢接触疲劳亚表面孔洞的形成[J].材料科学与工艺,1996,4 (3):29-33.[5]霍尼库姆R W K著.钢的显微组织和x`性能[M].北京:冶金工业出版社,1985.[6]胡光立,谢希文.钢的热处理[M].西安:西北工业大学出版社,2004.[7] UESUGI T.Recent development of bearing steel in japan transactions of the iron and steel[J].Institute of Japan,1988(11):893-899.[8]田村今男著.王国栋,刘振宇,熊尚武,译.高强度低合金钢的控制轧制与控制冷却[M].北京:冶金工业出版社,1992.。
控轧控冷改善GCr15钢网状碳化物

无法象新建的现代工业企业那样运用现存的成功和 成熟 的生 产技术去装备 一条相对 完美 的生产 线 , 只 而
能在原有工 艺装备上作 局部改进 , 克服各种各样 的困 难尽可 能使 自己的产 品能达 到用 户或 者说 市场 的基
Ha H nX n
( rd cinMa a e n e at n, ih a h n c e gS e il te o, t.P n a gGru , in y u Sc u n6 1 01 P o u t n g me t p r o D me tSc u nC a g h n p ca e l .L d, a g n o p Ja g o , ih a 2 7 ) S C
投入, 改善 1 1 m l Cl盘 圆碳 化物 网状 , 2~ 7 fG r5 提 高合 格率 。
1 改 进 方 案
通 过分 析 , 定 采取 控 制 轧制 与 控 制冷 却 相结 确
合, 即对 中轧 G r5 圆采 取 90℃左 右终 轧 , Cl盘 5 并用 强 制 冷 却 手段 控 制 轧后 冷 却 速度 以抑 制 网状 碳 化 物 的析 出 , 即采 用 高 压水 湍 流 搅 拌 急冷 至 80o左 0 C 右卷 取收 集 , 降低 网状级 别 。
Ke wo d : r 5 se l C r i en t o k T y r s GC l t e, a b d e w r , MCP F n l o l gtmp r u e , ia o i c n e e a r
引言
随着现代科 技和社会 的迅速 发展 , 承钢 的质 对轴 量和性能 提出 了更高 的要求 , 近几年攀 钢集 团江 以致 油长城特 殊钢有 限公 司生产 的 G r5 格率不 高 , Cl合 主 要表 现为碳 化物 网状 级别偏 高 。然而 作 为较老 的特 钢工业企业 , 轴承钢的生产工艺和技术装备较为稳 定。
GCr15SiMn轴承钢热处理工艺研究

GCr15SiMn轴承钢热处理工艺研究姓名:专业:机械制造及其自动化班级:学号:摘要:GCr15SiMn轴承钢广泛用于制作重型机床大型机械的大型轴承的钢球、滚子和套圈。
本文论述了不同锻后退火工艺、淬火工艺、回火工艺中组织转变和对该钢组织性能的影响,提出最佳热处理工艺。
关键词:GCr15SiMn、球化退火、淬火和回火、热处理。
前言:GCr15SiMn轴承钢是一种高碳铬轴承钢,提高了Si、Mn含量改善了淬透性和弹性极限,有回火脆性,白点敏感性强,焊接性能较差。
一、球化退火1、球化退火过程中的组织转变退火前的原始组织为热轧热锻或者正火组织,是片状碳化物与铁素体相间的珠光体。
将其加热至Ac1~Ac3之间并保温时,体心立方的铁素体转变为面心立方的奥氏体,部分片状碳化物溶解入奥氏体中,剩余的碳化物也逐渐由片状向粒状或球状转化。
加热温度越高,保温时间越长,则碳化物将全部溶入奥氏体中。
在随后的冷却过程中,如冷却速度足够缓慢或冷至770~800( GCr15SiMn)进行等温,则溶入的碳化物将以粒状在未溶碳化物或新位置析出,同时奥氏体转变为铁素体基体上分布着粒状碳化物和粒状珠光体,为球化退火的正常的组织。
冷速越大,析出的碳化物越细小,过缓的冷却速度产生粗大碳化物。
但冷却速度过快,且加热温度过高,保温时间不长,则溶入的碳化物将部分或全部以片状的形态析出,成为全部或含有部分片状碳化物分布于铁素体基体的混合珠光体。
二、淬火和回火1、淬火工艺过程中的组织转变把具有球化退火组织的工件加热到Ac1~Ac3之间进行保温时,铁素体基体转变成为奥氏体,粒状碳化物溶入奥氏体中并在奥氏体中扩散均匀化,同时奥氏体晶粒也不断长大,在随后的冷却过程中,如以足够快的冷却速度冷至Ms以下,奥氏体转变为马氏体,溶入奥氏体中的碳原子保留在马氏体中,随着工件温度的降低,越来越多的奥氏体转变为马氏体。
若在马氏体转变终止温度Mf以上某个温度保留冷却,未转变的奥氏体被保留下来成为残余奥氏体。
基于电渣重熔GCr15轴承钢中碳化物控制的研究

基于电渣重熔GCr15轴承钢中碳化物控制的研究基于电渣重熔GCr15轴承钢中碳化物控制的研究摘要:本文研究了基于电渣重熔的GCr15轴承钢中碳化物的控制方法与效果。
首先介绍了GCr15轴承钢的基本特性和应用,以及碳化物对钢材性能的影响。
随后详细阐述了电渣重熔工艺的特点和优势,并分析了该工艺对碳化物控制的影响因素。
根据实验结果,得出了减小碳化物的最佳电渣重熔工艺参数。
在此基础上,结合热处理工艺,对电渣重熔后的材料性能进行了综合研究,发现碳化物控制对钢材硬度、韧性、抗疲劳性能、耐磨性等方面均具有显著影响。
结果表明,基于电渣重熔的碳化物控制方法能够大幅提升轴承钢的综合性能,具有较高的应用潜力和推广价值。
关键词:轴承钢;碳化物;电渣重熔;控制方法;综合研究1. 引言轴承钢是一种具有高强度、高硬度、高精度和高耐磨性的特种钢材,广泛应用于各种机械设备中,其质量的好坏直接关系到机械设备的安全性、可靠性和寿命。
而钢材中的碳化物是影响钢材性能的重要因素之一,它不仅能提高钢材的硬度和耐磨性,还能影响钢材的抗拉伸强度、塑性和韧性等性能指标。
因此,如何控制钢材中碳化物的含量和组织成为轴承钢生产中的一项关键技术。
目前,常用的碳化物控制方法主要包括化学成分控制、热处理工艺控制和电渣重熔控制等。
其中,电渣重熔技术是一种通过高温和高集中度的能量输入,使钢材中的不均匀组织得以改善,同时对非金属夹杂物等有害杂质进行清除的有效方法。
因此,结合电渣重熔工艺进行碳化物控制具有较大的优势。
本文以电渣重熔GCr15轴承钢为研究对象,探讨了电渣重熔方法对碳化物控制的影响因素,以及在此基础上结合热处理工艺对材料性能的综合影响。
通过实验和分析,得出了较为准确的碳化物控制方法和参数,并对该方法的应用前景进行了初步的评估。
2. GCr15轴承钢中碳化物的特点及其对钢材性能的影响GCr15轴承钢是一种高碳铬轴承钢,其主要化学成分为C:0.95~1.05、Si:0.15~0.35、Mn:0.20~0.40、Cr:1.40~1.65等。
GCr15轴承钢热处理过程中碳化物的析出与演变行为
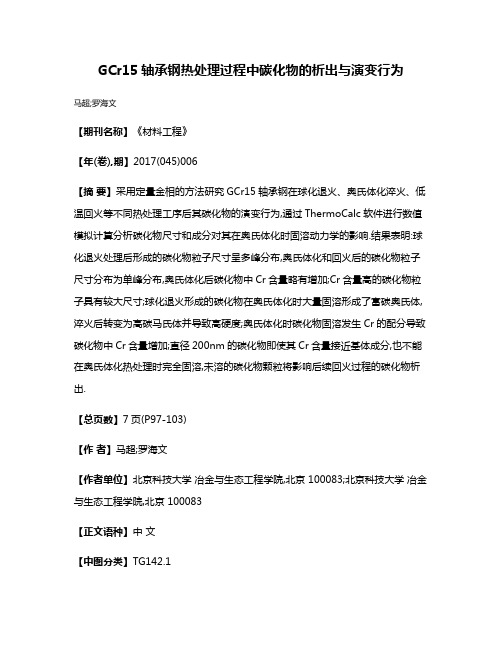
GCr15轴承钢热处理过程中碳化物的析出与演变行为马超;罗海文【期刊名称】《材料工程》【年(卷),期】2017(045)006【摘要】采用定量金相的方法研究GCr15轴承钢在球化退火、奥氏体化淬火、低温回火等不同热处理工序后其碳化物的演变行为,通过ThermoCalc软件进行数值模拟计算分析碳化物尺寸和成分对其在奥氏体化时固溶动力学的影响.结果表明:球化退火处理后形成的碳化物粒子尺寸呈多峰分布,奥氏体化和回火后的碳化物粒子尺寸分布为单峰分布,奥氏体化后碳化物中Cr含量略有增加;Cr含量高的碳化物粒子具有较大尺寸;球化退火形成的碳化物在奥氏体化时大量固溶形成了富碳奥氏体,淬火后转变为高碳马氏体并导致高硬度;奥氏体化时碳化物固溶发生Cr的配分导致碳化物中Cr含量增加;直径200nm的碳化物即使其Cr含量接近基体成分,也不能在奥氏体化热处理时完全固溶,未溶的碳化物颗粒将影响后续回火过程的碳化物析出.【总页数】7页(P97-103)【作者】马超;罗海文【作者单位】北京科技大学冶金与生态工程学院,北京 100083;北京科技大学冶金与生态工程学院,北京 100083【正文语种】中文【中图分类】TG142.1【相关文献】1.Fe-12.4Cr-0.13C合金高温时效过程中碳化物的析出行为研究 [J], 卢丽;朱娜琼;何燕霖;李麟2.终轧温度对GCr15轴承钢网状碳化物析出的影响 [J], 杨洪波;朱伏先;马宝国;刘相华3.Fe-15Mn-10Al-0.3C钢升温过程中κ-碳化物的析出行为研究 [J], 倪呈军;刘营凯;王白冰;祖武杰;史文4.45Cr9Si3气阀钢电渣锭、轧制及退火过程中碳化物析出行为 [J], 刘东风;郭靖;郭汉杰;杨文晟;段生朝5.K465合金在冷热循环过程中碳化物的析出行为 [J], 杨金侠;郑启;孙晓峰;张承忠;管恒荣;胡壮麒因版权原因,仅展示原文概要,查看原文内容请购买。
- 1、下载文档前请自行甄别文档内容的完整性,平台不提供额外的编辑、内容补充、找答案等附加服务。
- 2、"仅部分预览"的文档,不可在线预览部分如存在完整性等问题,可反馈申请退款(可完整预览的文档不适用该条件!)。
- 3、如文档侵犯您的权益,请联系客服反馈,我们会尽快为您处理(人工客服工作时间:9:00-18:30)。
县晓明,等: GCr15 钢中网状碳化物在锻造及热处理过程中的形态变化
ISSN1000 - 3762 轴承 2012 年8 期 CN41 - 1148 / TH Bearing 2012 ,No. 8
37 - 40
GCr15 钢中网状碳化物在锻造及热处理过程中 的形态变化
县晓明1 ,叶健熠2 ,折文革1
( 1. 甘肃海林中科科技股份有限公司,甘肃 天水 741018; 2. 洛阳轴研科技股份有限公司,河南 洛阳 471039)
局部溶解,原始封闭网状碳化物熔断后呈点、链状
·38·
《轴承》2012. №. 8
碳化物网络,如图 1 所示,心部仍保留有原材料的碳 化物网格特征,该现象同中频感应加热产生的集肤 效应及热量传导过程有关。在球化退火过程大颗 粒碳化物继续粗化,并形成 < 2 级的粗颗粒状网,如 图 2 所示。其原因在于: 原始网熔断形成点、链状碳 化物颗粒,粒度大于某一尺寸的区域,在球化退火 过程中反向析出长大的趋势大于溶解,导致粗大颗 粒的产生[2]。Φ601# 经热切下料→退火→淬火,局 部区域 > 3 级的碳化物网呈聚集、带状分布,保留有 成分偏析、碳化物极不均匀的特征,如图 3 所示。
为主,晶角处碳化物网较粗,500 倍下的组织形态 如图 8 所示,原始组织的晶粒度为 7 级。锻件经 中频加热( 1 153 ℃ ) →镦饼→辗扩→喷雾冷却后 组织形态发生显著变化: 二次网状碳化物沿奥氏 体晶界析 出,网 状 粗 细 不 均 的 特 征 突 出,晶 粒 粗 化,晶粒度达到 4 ~ 5 级,如图 9 所示。该试样经 等温球化退火,仍能观察到二次封闭网以点链、断 续链状的 形 态 沿 晶 界 残 存,如 图 10 所 示。淬 火 后,大于 3 级的网状碳化物仍保留断续链状的形 态,晶粒粗化特征依然清晰,如图 11 所示。
Φ601#
集中热切下料→空冷 →球化退火→淬火
观察不同规格的原 材料 经 球 化 退 火 后 的 网状碳化物
集中热切下料→空冷
观察原材料集中下 料后的网状碳化物
Φ602#
镦饼→穿孔→辗扩→ 喷雾冷却
观 察 原 材 料 经 锻、 辗、速冷后 的 网 状 碳 化 物
集中热切下料→中频 加热→镦饼→穿孔 → 辗 扩→喷雾冷却→球化退 火→淬火
通常消除材料中网状碳化物的正火加热温度 为 900 ~ 950 ℃ ,加热时间为 40 ~ 60 min[3]。集中 热切下料中频加热温度在 840 ℃ 左右,加热区间 为 Ac1 ~ Acm。由于加热时间短、切料后堆冷,热轧 材近表层原 始 珠 光 体 片 层、原 始 封 闭 网 状 碳 化 物 有溶断现象,但 Φ50 近表层、Φ601# 心部碳化物网 与切料前相 比 却 无 明 显 变 化,说 明 中 频 加 热 集 中 下料不足以改变热轧不退火材原始网状碳化物的 分布特征。 2. 2 薄壁锻件原始网状碳化物形态变化特征
Φ602# 热轧材碳化物呈封闭网格状,网较粗, 500 倍下的组织形态如图 4 所示,原始组织的晶粒 度为 7 ~ 8 级 。该 料 段 经 始 锻 加 热 ( 中 频 加 热 1 100 ℃ ) →镦饼→辗扩→喷雾冷却,因锻件壁厚 薄、冷却速度较快,二次碳化物沿晶界析出量明显 减少、网较 细,但 晶 粒 及 碳 化 物 网 格 尺 寸 明 显 变 大,500 倍下的组织形态如图 5 所示,锻件组织的 晶粒度为 5 ~ 6 级。
原材料的网状碳化物 锻造加热温度对材 料晶 粒 长 大 ( 碳 化 物 网) 的影响
球化退火后网状碳 化物分布特征
锻造加 热 温 度、冷 却 速度 对 网 状 碳 化 物 的 影响
2 热加工中网状碳化物的形态变化
2. 1 原始网状碳化物的形态变化 Φ50 热轧 材 热 切 下 料 后 近 表 层 原 始 组 织 出 现
机理不同的两种类型: 材料网和锻造网。对于因
公司科技处,1974: 241.
锻造温度过高、冷却不足产生的二次碳化物超标, [5] 况作田. 热轧轴承钢球坯网状碳化物达标的工艺探
应从规范锻造工艺,控制加热温度、改善冷却条件 着手加以防范; 而对于因热轧不退火材成分偏析、 碳化物不均 匀 所 导 致 的 网 状 超 标,应 从 加 强 材 料
1 试验条件及方法
选用 3 种规格、4 个炉号的热轧材作为对比材 料,热加工工艺以实际生产工艺为准,冷却方式及 试验分组情况见表 1。表中 Φ601#,Φ602#为不同冶 炼厂家、不同炉号的热轧不退火材,集中热切下料 的中频温度为 840 ℃ ,生产线始锻中频加热温度 为 1 100 ~ 1 150 ℃ 。网状碳化物级别参照 JB / T 1255 —2001《高 碳 铬 轴 承 钢 滚 动 轴 承 零 件 热 处 理 技术条 件》进 行 评 定,晶 粒 度 参 照 GB / T 6394— 2002《金属 平 均 晶 粒 度 测 定 方 法 》评 定 。 金 相 图 片未作说明的 均 为 4% 硝 酸 酒 精 深 腐 蚀,500 倍 下观察。
在成分偏析、碳 化 物 均 匀 性 较 差 且 存 在 碳 化 物 网 格的热轧材,由于锻造时中频加热升温速度快、保 温时间短,难 以 达 到 扩 散 退 火 的 效 果。 因 而 锻 件 球化退火、淬 火 后,在 成 分 偏 析 区 域 的 纵 截 面 上, 碳化物仍呈现为材料网( 封闭的带上网或带、网混 合特征) ,其网格尺寸、形态也有别于因锻造温度 偏高、冷却不良产生的锻造网。
环节冷却速度不足造成锻件在 Acm ~ Ar1 温度区 料表层组织中珠光体、网状碳化物仅有局部溶解、
间热量散失缓慢、过程延长,成为二次封闭网状碳 破断的作用,但不足以改变热轧材原始组织中网
化物沿奥氏体( A) 晶界析出、网壁增厚的主要因 状碳化物的分布特征。
素。球化退 火、淬 火 后 网 状 超 标,说 明 球 化 退 火、
图 10 球化退火后横截面封闭网状碳化物的形态 图 11 淬火后横截面网状碳化物形态特征
·40·
《轴承》2012. №. 8
厚壁锻件锻造时中频加热到 1 150 ℃ 透烧,锻 造温度偏高是晶粒粗化的主要原因。其次锻造摩
4 结论
擦发热,促使 锻 件 温 度、蓄 热 出 现 反 弹,加 之 终 锻
( 1) 中频热切下料加热温度低,时间短,对材
·39·
所示。网状碳化物与带状相伴而生的不均匀现象 与原材料成分偏析及扩散退火不充分或缺省扩散 退火有关且具有遗传特性。这 种 网、带 相 杂 的 碳 化物多以共晶型( Fe,Cr) 3 C 为主[4],这种存在严 重成分偏析、碳化物不均的热 轧 不 退 火 材,在 燃 气炉中加热到( 1 100 ± 50 ) ℃ ,保温 0. 5 ~ 1. 0 h 才能得到有效改善[5]。显然对 采 用 中 频 感 应 加 热的锻造方式而言,高温加热、长 时 间 保 温 来 改 善原材料成分偏析及碳化物分布不均匀的方法 不太现实。
关键词: GCr15 钢; 网状碳化物; 锻造温度; 晶粒度; 成分偏析
中图分类号: TH133. 33; TG115. 21
文献标志码: B
文章编号: 1000 - 3762( 2012) 08 - 0037 - 04
高碳铬轴承钢 GCr15 热 轧 棒 材 锻 造 轴 承 套 圈,经球化退火和淬、回火后常 因 网 状 碳 化 物 超 标而判不合格( JB / T 1255—2001 标准要求的 网 状碳化物合格级别为≤2. 5 级) 。对 GCr15 轴承 零件网状碳化物超标原因的解释和分析多集中 于 锻 造 过 程 中 始 锻 、终 锻 温 度 过 高 ,冷 却 缓 慢 ,网 状碳化物析出严重[1],而对原材料成 分 偏 析、碳 化物不均匀而产生的网状残留以及快速热切下 料所导致的粗点、链状碳化物 残 留 则 分 析 不 多。 本例通过 GCr15 热轧不退火材中网状碳 化 物 在 热切下料、锻造、球化退火及淬 火 过 程 中 的 形 态 变化分析探讨轴承零件中网状碳化物超标的原 因,并提出相应的控制措施。
图 1 Φ50 热轧材热切下料后纵截面表层组织形态
图 2 Φ50 热轧材经球化退火、淬火后纵截面网状 碳化物形态
图 4 Φ602# 原始热轧态横截面组织形态
图 3 Φ601# 热切下料、球化退火、淬火后纵截面 局部网状碳化物形态( 250 × )
图 5 Φ602# 锻件中频加热、镦饼、辗扩及速冷后 的横截面组织状态
摘要: GCr15 热轧不退火材经中频感应加热下料,锻造为轴承套圈,经喷雾冷却、球化退火及淬火后,检验网状
碳化物,结果表明,由于中频热切下料加热温度低,时间短,不足以改变热轧材原始组织的分布特征。高温锻造
后所形成的网状碳化物与热轧不退火材成分偏析、碳化物不均匀所导致的网状碳化物相比,往往存在网孔尺
寸、网壁厚度及分布形态上的明显差异,这些差异可作为判别轴承网状碳化物超标的原因和依据。
( 3) 因材料成分偏析、碳化物均匀性较差所致
封闭网状 碳 化 物 为 主,晶 粒 度 一 般 在 8 级 左 右。 的锻件网状碳化物,淬火后多以封闭的带上网或
热切下料对材料表层原始珠光体、网状碳化物溶 带、网混合的形态存在。
解及破断作用明显,但对热轧材心部的原始组织、
( 4) 网状碳化物网格大小、粗细及分布形态的
晶粒度及网状碳化物影响甚微。
差异,可作为 判 断 网 状 碳 化 物 超 标 原 因 及 采 取 相
热轧材经高温锻造加热,原始网格将发生溶 应措施的依据。
解和组织重 构,晶 粒 粗 化 成 为 锻 件 组 织 的 明 显 特
征; 终锻温度、冷却速度成为影响网状碳化物沿奥 参考文献: