首末件检验确认规范
压铸首末件及定时检验规范(含表格)
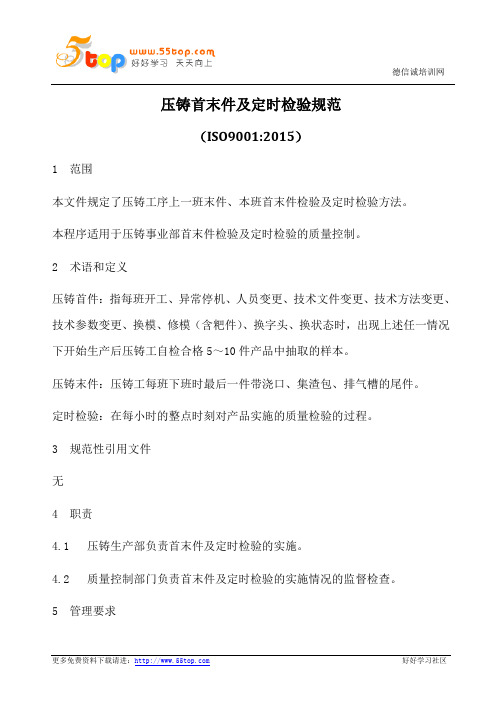
压铸首末件及定时检验规范(ISO9001:2015)1 范围本文件规定了压铸工序上一班末件、本班首末件检验及定时检验方法。
本程序适用于压铸事业部首末件检验及定时检验的质量控制。
2 术语和定义压铸首件:指每班开工、异常停机、人员变更、技术文件变更、技术方法变更、技术参数变更、换模、修模(含粑件)、换字头、换状态时,出现上述任一情况下开始生产后压铸工自检合格5~10件产品中抽取的样本。
压铸末件:压铸工每班下班时最后一件带浇口、集渣包、排气槽的尾件。
定时检验:在每小时的整点时刻对产品实施的质量检验的过程。
3 规范性引用文件无4 职责4.1 压铸生产部负责首末件及定时检验的实施。
4.2 质量控制部门负责首末件及定时检验的实施情况的监督检查。
5 管理要求5.1 压铸工序首末检验及定时检验5.1.1 首末件检验及定时检验标准:压铸工对照“压铸首件送检通知单”项目、检验作业指导书、修模通知等技术标准中的所有项目采取目测的方式进行自检,压铸班长、巡检对照检验作业指导书、修模通知等技术标准中的所有项目采取目测的方式进行互检、专检。
5.1.2 上一班的末件检验:压铸工对上一班的末件进行自检,自检合格后放在指定工作台上,由压铸班长、巡检分别进行互检、专检。
5.1.3 本班首件检验5.1.3.1 压铸工在开始生产压铸首件时,先去除首件浇冒口、飞皮,并对首件进行检验后,填写“压铸首件送检通知单”随首件交质量专检台,涉及换模、换字头、修模后的首件产品,压铸工应将修模前的样件和修模后的首件一同送质量专检台,并在“压铸首件送检检查记录”上登记。
5.1.3.2 压铸巡检按检验作业指导书、修模通知等要求对本班首件产品的尺寸及外观进行全面检查,涉及盖类字样位置检测的必须进行划线检查,并在“压铸首件送检检查记录”上进行记录。
5.1.3.3 有打磨要求的盖类产品在首件检验合格后,压铸巡检安排将上述产品交表面处理工序进行试打磨验证,表面处理工序应在30分钟内完成试打磨验证,打磨巡检确认效果并在“盖类产品打磨验证记录表”上记录。
首件检验管理规范
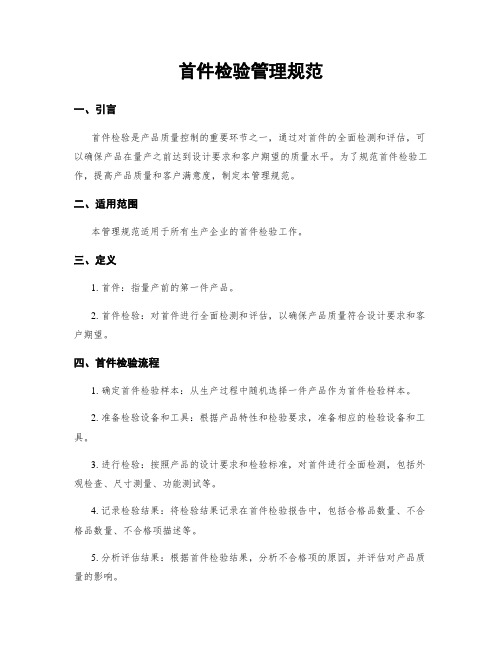
首件检验管理规范一、引言首件检验是产品质量控制的重要环节之一,通过对首件的全面检测和评估,可以确保产品在量产之前达到设计要求和客户期望的质量水平。
为了规范首件检验工作,提高产品质量和客户满意度,制定本管理规范。
二、适用范围本管理规范适用于所有生产企业的首件检验工作。
三、定义1. 首件:指量产前的第一件产品。
2. 首件检验:对首件进行全面检测和评估,以确保产品质量符合设计要求和客户期望。
四、首件检验流程1. 确定首件检验样本:从生产过程中随机选择一件产品作为首件检验样本。
2. 准备检验设备和工具:根据产品特性和检验要求,准备相应的检验设备和工具。
3. 进行检验:按照产品的设计要求和检验标准,对首件进行全面检测,包括外观检查、尺寸测量、功能测试等。
4. 记录检验结果:将检验结果记录在首件检验报告中,包括合格品数量、不合格品数量、不合格项描述等。
5. 分析评估结果:根据首件检验结果,分析不合格项的原因,并评估对产品质量的影响。
6. 提出改进措施:针对不合格项,制定相应的改进措施,防止类似问题再次发生。
7. 审核和批准:首件检验报告应经过相关部门的审核和批准,确保检验结果的准确性和可靠性。
8. 反馈和追踪:将首件检验结果反馈给生产部门,跟踪改进措施的执行情况,并进行后续的追踪检验。
五、责任和权限1. 生产部门负责组织和实施首件检验工作,保证首件检验的及时性和准确性。
2. 质量部门负责制定首件检验标准和检验方法,并对首件检验结果进行审核和批准。
3. 设计部门负责提供产品的设计要求和技术标准,以供首件检验参考。
4. 相关部门应积极配合首件检验工作,提供必要的支持和协助。
六、培训和考核1. 生产部门应对首件检验人员进行必要的培训,确保其具备相关的技术和知识。
2. 质量部门应定期对首件检验人员进行考核,评估其工作能力和水平。
七、记录和档案管理1. 首件检验报告应按照规定的格式进行记录,并进行适当的保存和管理。
2. 首件检验档案应按照规定的要求进行归档和保管,以备后续的查阅和审计。
首末检管理规定
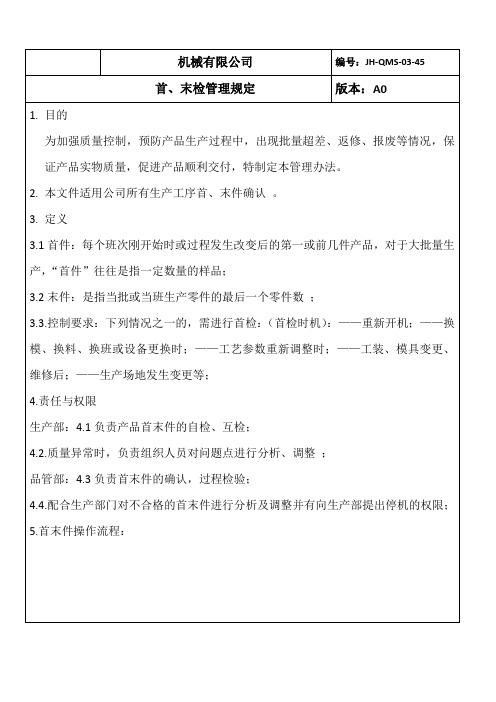
4.2.质量异常时,负责组织人员对问题点进行分析、调整 ;
品管部:4.3 负责首末件的确认,过程检验;
4.4.配合生产部门对不合格的首末件进行分析及调整并有向生产部提出停机的权限;
5.首末件操作流程:
流程图 产前准备
首件生产
NG
自检
OK NG
组长确认
机械有限公司
编号:JH-QMS-03-45
首件流程图
生产部
操作工对首件生产的产品进行检验,确认符 合技术要求和工序要求,填写《自检记录表》 并签名(尺寸需填写具体测量数值)
生产部
《自检记录表》
班组长确认操作工每个首件都有做检验,并 对操作工的首件检验结果做确认签字
生产部
《自检记录表》
OK OK
QC 确认
QC 对生产的《自检记录表》做确认,确认 车间有正常进行首件自检工作,并核对检验 结果后在《自检记录表》签字
版本:A0
说明
责任部门
相关记录
班、组长对操和工进行必须的岗前培训,准 备好生产所需的技术文件和工装治具,并确 认文件和治具正确性和适用后,派发给操作 工,作业前对人、机、料、法、环进行确认
生产部
《作业准备验证记录表》
经培训合格的员工允许上岗,并按照技术资 料和步骤,第个独立的作业单位首先生产第 一件产品
产,“首件”往往是指一定数量的样品;
3.2 末件:是指当批或当班生产零件的最后一个零件数 ;
3.3.控制要求:下列情况之一的,需进行首检:(首检时机):——重新开机;——换
模、换料、换班或设备更换时;——工艺参数重新调整时;——工装、模具变更、
维修后;——生产场地发生变更等;
4.责任与权限
生产部:4.1 负责产品首末件的自检、互检;
首中末件检验规范 (1)

首中末件检验规范(IATF16949-2016/ISO9001-2015)1.0目的和范围本办法规定了生产线首、中、末件的定义以及检查要求。
本办法适用于各车间/生产线的整个生产过程。
2.0定义本办法采用下列定义:2.1首件为以下情况下生产的第一件产品:(a)每班开始操作时;(b)设备调整时;(c)加工方法变化时;(d)加工条件变化时;(e)作业方法变化时;(f)更换模具时;(g)设备故障修理后再次运转时;(h)更换操作人员时。
(i)容量为每机台/3件。
(h)首检时间为接班后半小时内.2.2中件每班午休后生产的第一件产品。
正常生产时中检容量为每机台/3件,巡检时间为下午13:00。
2.3末件正常生产时的最后一件产品。
正常容量为每机台/3件2.4如发生(b)-(h)中任何一项变化,需重新按本定义对产品进行行首,中,末检查。
3.0职责3.1品质部对本办法负管理职责,并保证贯彻执行;3.2生产线班长、操作人员和检验员对正确执行本办法负责。
4.0实施办法4.1 首、中、末件检查文件编制4.1.1产品/过程开发工程师负责根据产品质量特性的重要性编写首、中、末件检查文件。
4.1.2首、中、末件检查文件由质量部检验员校对,质量工程师审核、品质部长批准后实施。
4. 2首、中、末件检查基准文件更改首、中、末件检查基准文件发生更改时,过程工程师填写更改单一式三份,经检验员校对,质量工程师审核,品质部长批准后实施更改,更改单由车间、品质部和管理员各保存一份。
4.3检查的实施4.3.1正常生产情况下每班应检查首、中、末件。
4.3.2在每半班发生2.1中(b)~(h)规定情况时,只检查首件、末件。
4.3.3操作工按照检查文件规定的项目对各工序产品/试件进行逐项检查,将检查的实际测量结果记录在三检表内。
4.3.4检查完毕后,针对有关键工序,例如注塑工序,应将产品/试件整齐地放在首、中、末件检查台上;其它工序,有检具的应放置在检具上,没有检具的可在适当位置放置,首件用黄色夹子,中件用白色夹子,末件用蓝色夹子标识,下料和包装工序可以整包标识,单独存放。
首中末件检验规范

首中末件检验办法1.目的和范围本办法规定了生产线首、中、末件的定义以及检查要求。
本办法适用于各车间/生产线的整个生产过程。
2.定义本办法采用下列定义:2.1首件为以下情况下生产的第一件产品:(a)每班开始操作时;(b)设备调整时;(c)加工方法变化时;(d)加工条件变化时;(e)作业方法变化时;(f)更换模具时;(g)设备故障修理后再次运转时;(h)更换操作人员时。
(i)容量为每机台/3件。
(h)首检时间为接班后半小时内.2.2中件每班午休后生产的第一件产品。
正常生产时中检容量为每机台/3件,巡检时间为下午13:00。
2.3末件正常生产时的最后一件产品。
正常容量为每机台/3件2.4如发生(b)-(h)中任何一项变化,需重新按本定义对产品进行行首,中,末检查。
3.职责3.1品质部对本办法负管理职责,并保证贯彻执行;3.2生产线班长、操作人员和检验员对正确执行本办法负责。
4.实施办法4.1 首、中、末件检查文件编制4.1.1产品/过程开发工程师负责根据产品质量特性的重要性编写首、中、末件检查文件。
4.1.2首、中、末件检查文件由质量部检验员校对,质量工程师审核、品质部长批准后实施。
4. 2首、中、末件检查基准文件更改首、中、末件检查基准文件发生更改时,过程工程师填写更改单一式三份,经检验员校对,质量工程师审核,品质部长批准后实施更改,更改单由车间、品质部和管理员各保存一份。
4.3检查的实施4.3.1正常生产情况下每班应检查首、中、末件。
4.3.2在每半班发生2.1中(b)~(h)规定情况时,只检查首件、末件。
4.3.3操作工按照检查文件规定的项目对各工序产品/试件进行逐项检查,将检查的实际测量结果记录在三检表内。
4.3.4检查完毕后,针对有关键工序,例如注塑工序,应将产品/试件整齐地放在首、中、末件检查台上;其它工序,有检具的应放置在检具上,没有检具的可在适当位置放置,首件用黄色夹子,中件用白色夹子,末件用蓝色夹子标识,下料和包装工序可以整包标识,单独存放。
班组零部件加工首、末件检验管理规定

1目的为了强化班组的质量管理,规范首件、末件检验,降低质量风险。
2适用范围本管理规定适用于生产线的首件检验和末件检验。
3职责3.1 技术质量室负责本规定的归口管理,对执行情况进行检查并按《班组产品质量评审考核办法》实施考核。
3.2 各相关部门应严格执行本规定。
4机加工工序首件检验要求4.1 首件检验指令的分类首件检验指令包括:首件自检、首件边做边检和首件停机送检等。
首件自检:即首件生产后仅要求操作工进行自检,合格后开始生产。
首件边做边检:即首件生产后送精测间或平台边生产边等待检测结果。
首件停机送检:即首件生产后送精测间或平台停机检测,检测合格后生产。
4.2 自检检测要求4.2.1普通加工工序:要求所有加工项目都要检测。
4.2.1.1同一把刀具钻、攻、粗镗具有相同检测内容的孔允许使用规定的检测手段检测该刀具加工的最后一个孔,其它孔目测。
4.2.1.2其它同一把刀具加工的具有相同检测内容的加工部位,首、尾加工部位必须检测,中间加工部位目测。
4.2.1.3具有不相同检测内容的加工部位,必须按4.3.1.1和4.3.1.2规定进行检测。
4.2.2精加工工序:同一把刀具钻、攻具有相同检测内容的孔允许按4.3.1.1和4.3.1.3要求检测,其它同一把刀具加工的所有内容都必须检测。
4.2.3有专用量具检测的项目必须使用相应的专用量具检测。
无专用量具检测的项目,通用量具可以检测的项目必须使用通用量具检测(高精度通用量具可以代用低精度通用量具,量程在测量范围内的游标卡尺、深度卡尺允许代用)。
无专用量具检测的项目,通用量具不可以检测的项目必须目测。
4.2.4首检工件在填写自检记录表时在“追溯号”旁标注“首”记号(自检记录表中有特殊规定的按自检记录表中的要求填写)。
末检件工件在填写自检记录表时在“追溯号”旁标注“末”记号。
4.2.5首件自检必须完成所有频次检内容。
4.3 送精测间检测要求4.3.1送检前工件必须进行自检并清理,送检时按照精测间要求进行登记,并注明“首件”、“专检”等能清楚表明检测目的的字样(允许简写)。
产品首件确认规范-B0

1.目的:预防出现批量和倾向性不良及人证产品一致不符合,确保生产顺利进行。
2.范围:适用于每批量产的第一件产品,包括从PCBA、装配到包装各生产阶段。
3.定义:首件指每批产品量产中生产部做出的第一件产品或转机型生产出的第一件产品。
4.责任:生产部负责首件产品的制作。
生产线拉长或PIE负责监督和主导首件产品制作的整体过程,并进行初次确认。
IPQC负责首件产品的再次确认,并进行开拉前准备工作的检查。
QE负责首件产品的最终确认,当资料不清或有疑问时,还需客户进行确认。
5.内容:5.1首件产品确认5.1.1生产部根据作业指导书准备好相应的工具、物料和人员,并按作业指导书作业,PIE跟进生产全过程。
5.1.2生产部完成第一台机后,将第一台机做为首件产品,并备上首件确认单,确保作业正确后,在制作一栏签名,并将首件产品和确认单交PlE进行确认。
5.1.3PIE参考工程资料或样机,进行物料、工艺、测试的确认,对新产品或有一定更新的产品,需请工程协助确认包装,确认好后在指定位置签名,然后交IPQC确认,如有异常,将异常状况填写于首件确认单的备注位置,交工程PE工程师进行分析与改善,依分析结果要求,退回生产重作。
5.1.4IPQC参考作业指导书及相关工程资料或样机,进行再次确认,确认好后签名,然后交QE或客户确认,如有异常需反馈PIE,并退回生产重作。
5.1.5QE需对首件产品作最终确认,结合工程资料、品质要求及客户要求进行确认,当资料不全或要求不明确时,可请客户协助确认,确认好后将首件产品及确认单还回到生产部。
如有异常需及时反馈到IE、IPQC、生产线。
5.2第一台机检查表作业过程5.2.1在首件产品确认的同时,由生产部发出“第一台机检查表”,填好相关生产机型、时间等项目,并进行自检,签名后交IE确认。
5..2.2PIE需对生产开拉前准备状况进行确认,并指导生产,将确认结果填入备注栏,再交IPQC确认。
5..2.3IPQC需对生产过程进行检查,并将检查结果填入“第一台机检查表”中,发现异文件编号产品首件确认规范文件版本QP-H-05B/0常需反馈到相应负责人,并提报工程部PE进行原因分析与制订改善对策;后依改善结果要求生产执行操作。
首中末件检验规范
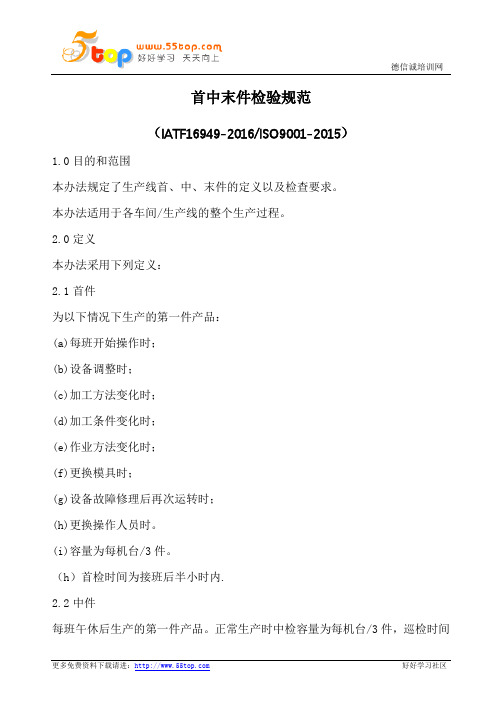
首中末件检验规范(IATF16949-2016/ISO9001-2015)1.0目的和范围本办法规定了生产线首、中、末件的定义以及检查要求。
本办法适用于各车间/生产线的整个生产过程。
2.0定义本办法采用下列定义:2.1首件为以下情况下生产的第一件产品:(a)每班开始操作时;(b)设备调整时;(c)加工方法变化时;(d)加工条件变化时;(e)作业方法变化时;(f)更换模具时;(g)设备故障修理后再次运转时;(h)更换操作人员时。
(i)容量为每机台/3件。
(h)首检时间为接班后半小时内.2.2中件每班午休后生产的第一件产品。
正常生产时中检容量为每机台/3件,巡检时间为下午13:00。
2.3末件正常生产时的最后一件产品。
正常容量为每机台/3件2.4如发生(b)-(h)中任何一项变化,需重新按本定义对产品进行行首,中,末检查。
3.0职责3.1品质部对本办法负管理职责,并保证贯彻执行;3.2生产线班长、操作人员和检验员对正确执行本办法负责。
4.0实施办法4.1 首、中、末件检查文件编制4.1.1产品/过程开发工程师负责根据产品质量特性的重要性编写首、中、末件检查文件。
4.1.2首、中、末件检查文件由质量部检验员校对,质量工程师审核、品质部长批准后实施。
4. 2首、中、末件检查基准文件更改首、中、末件检查基准文件发生更改时,过程工程师填写更改单一式三份,经检验员校对,质量工程师审核,品质部长批准后实施更改,更改单由车间、品质部和管理员各保存一份。
4.3检查的实施4.3.1正常生产情况下每班应检查首、中、末件。
4.3.2在每半班发生2.1中(b)~(h)规定情况时,只检查首件、末件。
4.3.3操作工按照检查文件规定的项目对各工序产品/试件进行逐项检查,将检查的实际测量结果记录在三检表内。
4.3.4检查完毕后,针对有关键工序,例如注塑工序,应将产品/试件整齐地放在首、中、末件检查台上;其它工序,有检具的应放置在检具上,没有检具的可在适当位置放置,首件用黄色夹子,中件用白色夹子,末件用蓝色夹子标识,下料和包装工序可以整包标识,单独存放。
首件检验确认规范
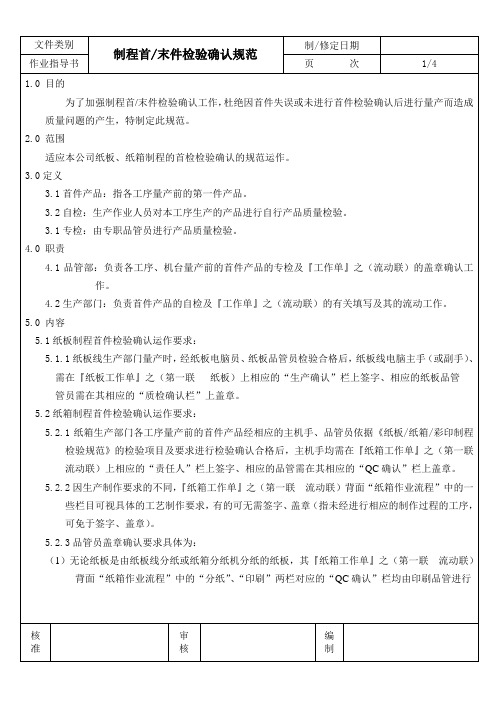
制程首/末件检验确认规范
制/修定日期
作业指导书
页次
1/4
1.0 目的
为了加强制程首/末件检验确认工作,杜绝因首件失误或未进行首件检验确认后进行量产而造成质量问题的产生,特制定此规范。
2.0范围
适应本公司纸板、纸箱制程的首检检验确认的规范运作。
3.0定义
3.1首件产品:指各工序量产前的第一件产品。
5.3.6为了确保(流动联)在流动时不产生丢失现象,该表单不连同产品一起流动,该表单经品管员首件检验确认盖章后,当面交给各工序的主机手,待相应的订单量产完成后在由主机手(机长)在该表单上填上相应的本工序损耗数后交给下道工的主机手,以此类推,直至流到生产部门的进仓员处办理进仓手续后收集交给生产部门主管处理。
3.2自检:生产作业人员对本工序生产的产品进行自行产品质量检验。
3.1专检:由专职品管员进行产品质量检验。
4.0职责
4.1品管部:负责各工序、机台量产前的首件产品的专检及『工作单』之(流动联)的盖章确认工作。
4.2生产部门:负责首件产品的自检及『工作单』之(流动联)的有关填写及其的流动工作。
5.0内容
(6)“打包”栏对应的“QC确认”栏,若属在纸箱大车间打包进仓,则由纸箱大车间成型品管员盖章确认;若在啤机大车间或啤机小车间打包进仓,则由啤机大车间及啤机小车间的品管员盖章确认。
5.3首件检验确认的其它有关要求:
5.3.1为了在生产过程中,『工作单』能真正体现指导生产,则由生产部门主机手(或机长)将『彩
5.1纸板制程首件检验确认运作要求:
5.1.1纸板线生产部门量产时,经纸板电脑员、纸板品管员检验合格后,纸板线电脑主手(或副手)、
需在『纸板工作单』之(第一联纸板)上相应的“生产确认”栏上签字、相应的纸板品管
首件检验规范
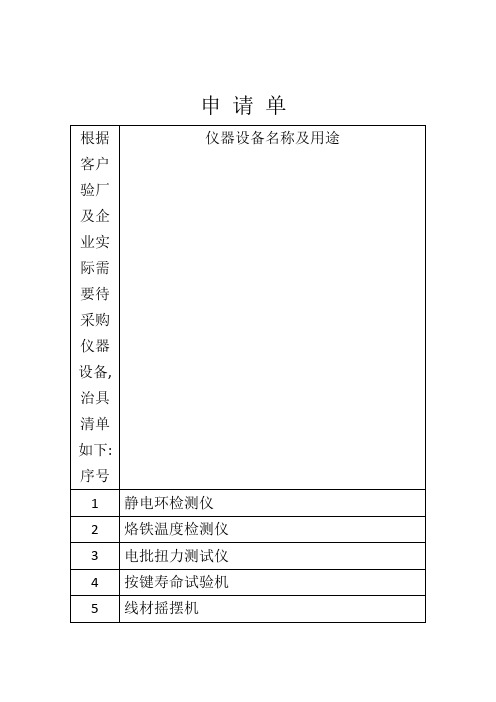
申请单制表:首件检查规范1.目旳为保证生产品质, 防止出现批量性旳产品不合格, 特制定本规范。
2.范围我司旳生产加工过程均应进行首件检查并依本制度进行。
3 职责3.1 品质部IPQC负责首件检查并填写首件检查汇报。
3.2 生产部负责首件旳自检及送检工作, 生产组长负责检查确实认4.术语4.1首件: 是指生产部加工生产旳产品, 经自我调试确认, 鉴定合乎规定后, 进行批量生产前旳第一个或三个产品(半成品、成品)。
只有在首件检查合格后才可以进行批量生产。
4.2首件检查:产品生产时进行旳检查、试验, 目旳是为了验证人、机、料、法、环、测这些影响原因在正常旳控制条件下。
5 规范内容5.1 首件检查旳时机:在每批产品投产时, 以及生产过程当中人员、机器设备、物料、工艺措施、环境条件、测试措施这六种原因有一种或一种以上发生明显变化时进行。
新产品第一次试产、量产时旳首件产品。
每一批开始生产旳首件产品。
5MIE变更后旳首件产品。
中5.1.4制程中换料或工艺更改条件下生产之产品;5.1.5生产线持续中断生产4小时以上5.1.6工装、设备维护维修后旳首件产品;5.2 新产品首件检查生产部依工艺流程加工或调试并进行自检。
品质部PQC在生产部加工测试时, 应根据有关检查根据或样板, 从旁协助同步就外观等易于鉴定之特性予以确认。
生产部认定生产之产品合乎规定期, 将该首件交PQC深入检查。
PQC根据检查原则对首件进行全面旳检查, 如鉴定不合格, 应向生产部提出并规定改善, 直到鉴定合格为止。
PQC鉴定合格或鉴定不合格, 但属设计问题或生产部无法改善之问题时, 将首件产品送往开发部门, 交详细开发该产品之技术人员做检查。
中国品研发技术人员经检查后, 作出合格或不合格旳鉴定, 并填入《首件检查单》中。
研发部、品质部均鉴定合格后, 生产部方可正式量产。
研发部、品质部鉴定不合格时, 如属生产原因应对生产部改善、调试直到合格为止, 如属设计原因时, 应停止生产, 由研发部拟出对策加以改善后, 方可恢复生产, 并需重新作首件确认。
首件确认规范
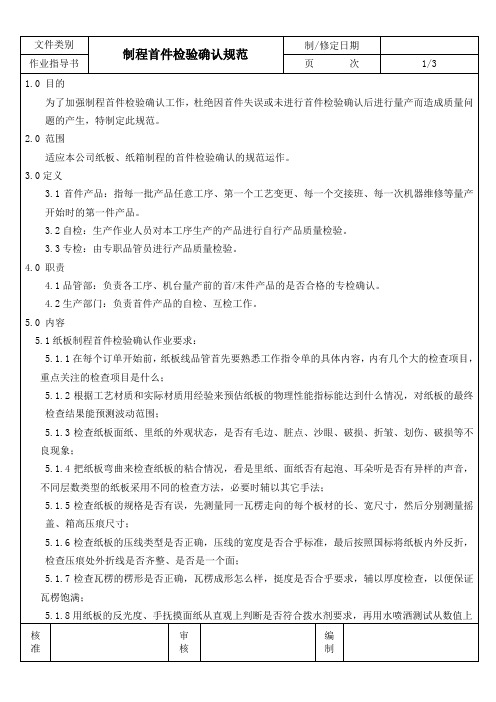
5.1.3检查纸板面纸、里纸的外观状态,是否有毛边、脏点、沙眼、破损、折皱、划伤、破损等不良现象;
5.1.4把纸板弯曲来检查纸板的粘合情况,看是里纸、面纸否有起泡、耳朵听是否有异样的声音,不同层数类型的纸板采用不同的检查方法时,应再做第二件直到首件产品检验合格后,才能投入批量生产;
5.4.4量产前的首件产品首先由工序主机手、班长进行自检→接着由相应工序的品管员进行专检。
5.4.5若没进行首检上机作业的,造成损失小于50元的考核机长50元/次,造成损失大于50元的按公司质量管理规范考核。
核
准
审
核
5.1.8用纸板的反光度、手抚摸面纸从直观上判断是否符合拨水剂要求,再用水喷洒测试从数值上
核
准
审
核
编制
文件类别
制程首件检验确认规范
制/修定日期
作业指导书
页次
2/3
来说明拨水剂浓度状态;
5.1.9以上各点都检查完之后,用水分测湿仪判断该纸板含水率,从而通知生产线调整,对产品增加或减少抽风时间;
5.1.10有特别要求的一定要通过仪器测试,用数值来确认纸板状态,及时对纸板做出处理;
5.3.3、检查成品规格尺寸(长、宽、高、内径、外径)是否在误差极限之内;
5.3.4、和样箱做比较,是否符合要求;
5.3.5、检查印刷图案文字、位置色相、印刷效果;
5.3.6、检查压痕线情况,纵压线成形是否漂亮,横压线是否有爆线现象等其它外观现象;
5.3.7、检查开槽成形、刀口光洁度情况;
5.3.8、检查箱钉首尾距、钉间钜、线偏差、钉子扣合状态、面子是否有打爆现象;
首末件检验管理规定

首末件检验管理规定首末件检验管理规定1.检验流程2.首末件检验是指对生产过程中的首件和末件产品进行严格的检验和测试,以确保产品质量符合相关标准和规范。
以下是首末件检验的流程和步骤:3. a. 制定检验计划:根据生产计划和产品要求,制定首末件检验的计划和方案。
4. b. 确定检验项目:明确需要检验的部位、尺寸、质量、外观等项目,并准备好相应的检验工具。
5. c. 进行抽样检查:按照规定的抽样方案,从生产批次中抽取首件和末件产品进行检查。
6. d. 执行检验:根据检验计划和项目,对首件和末件产品进行严格的质量检验和测试。
7. e. 记录检验结果:将检验过程中发现的问题和数据记录下来,并填写相应的检验报告。
8. f. 分析检验结果:对检验结果进行分析,评估产品质量状况,提出改进措施。
9.g. 储存检验记录:将检验报告和相关数据资料进行存档,以备后续查阅和处理。
10.责任与职责11.在首末件检验过程中,各个岗位和人员需要明确自己的责任和职责,以确保检验工作的顺利进行和质量问题的及时处理。
以下是相关岗位和人员的职责:12. a. 生产人员:负责按照生产计划进行生产,关注生产过程中的异常情况,并及时处理或上报。
13. b. 质检人员:负责制定首末件检验计划和方案,执行检验操作,分析检验结果,提出改进措施。
14. c. 技术人员:负责协助质检人员制定检验方案,提供技术支持和指导,解决检验过程中出现的技术问题。
15. d. 仓库管理人员:负责配合质检人员进行产品入库前的质量检查,确保产品数量和质量符合要求。
16. e. 上级管理人员:负责对首末件检验工作进行监督和考核,确保检验质量和效率得到保障。
17.首件检验标准18.首件检验是对生产过程中的首件产品进行严格的检查和测试,以确保后续产品的质量稳定和符合相关标准。
以下是首件检验的标准和要求:19. a. 外观完好:产品外观应无破损、划痕、变形等质量问题。
20. b. 尺寸符合:产品的尺寸应符合图纸和工艺要求,误差在允许范围内。
零部件首、末件确认制度

常州市龙润机械有限公司文件编号版本号文件名称零部件首.末件管理办法修订版共2页第1页1 目的为加强质量控制,预防产品生过程中,出现批量超差、返修、报废等情况,保证产品实物质量,促进产品顺利交付,特制定本管理办法.2 范围本文件适用公司所有生产工序首末件确认;3 定义3.1.首件:每个班次刚开始时或过程发生改变后加工的第一或前几件产品,对于大批量生产,“首件”往往是指一定数量的样品。
3.2.末件:是指当批或当班生产零件的最后一个零件;3.3.控制要求:下列情况之一的,需进行首检:(首检时机) ----重新开机; ----换模、换料、换班或设备更换时; ----工艺参数重新调整时; ----工装、模具变更换维修后; ----生产场地发生变更;4 责任与权限制造部:4.1.负责产品首末件的自检,互检; 4.2.质量异常时,负责组织人员对问题点进行分析、调整; 品质部:4.3.负责首末件的确认,过程检验; 4.4.配合制造部门对不合格的首末件进行分析及调整并有向制造部提出停机的权限;5 首末件操作流程首件确认操作流程NGOKNGOKOK 责任部门行动措施生产制造/生产制造/品质检验生产制造1.生产班组长或作业员需依据检验指导书,对试生产出的产品进行自检2.在确认试生产件是合格后需通知当班检验人员对试生产件进行确认生产制造1.检验员在接到生产部门通知后,10分钟之内需对试生产件进行首检(检验5PCS,表单记录3PCS)2.当确认首件不合格时,检验员需立即通知生产班组长或工艺员对设备重新调整3.检验员需对不合格的试生产件进行隔离或做报废处理品质检验1.检验员确认首件合格后,检验结果填入<<首末件确认单>>,并在样件上贴上首件标签进行封样2..通知生产制造部门可以继续生产生产准备试生产作业员自检检验员首检通知班组长进行调整正式生产常州市龙润机械有限公司文件编号版本号文件名称零部件首.末件管理办法修订版共2页第2页末件确认操作流程OKOKNGOKOKNG OK 责任部门行动措施生产制造生产制造作业员需对当玉或当批次生产的末件进行自检生产制造1.当前班组长需对作业员自检的末件进行互检2.确认后若末件合格,需通知当班检验人员对末件进行确认品质检验1.检验员在接到生产部门通知后,10分钟之内需完成末检(检验5PCS,表单记录3PCS)2.当确认末件不合格时,检验员需立即通知生产班组长或工艺员,对问题进行分析与调整3.对当班生产的不合格产品需进行隔离,并开具<<不合格品处置单>>进行处理品质检验1.检验员确认末件合格后,检验结果需填入<<首末件确认单>>,并在样件上贴上标签进行封样2.对当斑生产合格的零件贴上合格标识并通知生产部门可流入到下道工序生产制造生产结束前作业员自检班组长确认检验员末检产品标识立即对当班生产产品进行确认流入下道工序立即对不良品进行隔离通知当班班组长立即调查原因并整改开具不合格评审单。
首末件检验规定

首末件检验规定河南赛尔车轮有限公司首末件检验程序编制:技术部审核:王海成批准:庞海强文件编号:JS-Y-03一、目的为确保生产产品和过程特性与生产技术要求保持一致,并防止大量不良之发生,特制定本程序。
二、范围凡制造部门生产产品首末件检验均遵照执行三、职责技术部编制产品首末件检验程序;质检部、生产车间共同完成首末件测量,做好记录,并负责标识和封存。
四、定义1、首件是每个班次刚开始时或过程发生改变(如人员的变动、换料及换工装、机床的调整、工装刀具的调换修磨等)后加工的第一或前几件产品。
对于大批量生产,“首件”是指一定数量的样品。
2、首件检验是对每个班次刚开始时或过程发生改变(如人员的变动、换料及换工装、机床的调整、工装刀具的调换修磨等)后加工的第一或前几件产品进行的检验。
一般要检验连续生产的3-5件产品,合格后方可继续加工后续产品。
3、末件是在工人完成整个产品生产后随机抽查几件产品。
4、末件检验是在工人完成整个产品生产后进行末件封样与首件进行对比从而判断模具或工装完好。
五、程序1、作业流程,见附件2、首件产出后,操作工及时通知或告知专职检验员检验,以首末件检查表项目逐一检查,并记录签字,若检验员发现并判定不合格,须停机处理或更换模具时,则由检验员、车间共同决定,并记录于首末件检查表,经整改再依据首末件检验程序,进行复检。
对检验合格的首件做标识即“首件”字样,具体可由质检部和车间共同确定认可的可追溯性标识。
3、末件产出后,操作工要对产品做“末件”标识,并送质检部由检验员检验,仍以首末件检查表项目逐一检查,并记录签字。
4、首件检查样品,须保留至末件检查合格以后,一起退回生产车间。
2011.7.16首末件检验流程生产通知首末件检验NO检验整改末件YES 首件YES NO复检入库继续生产。
首末件检验的8个关键步骤
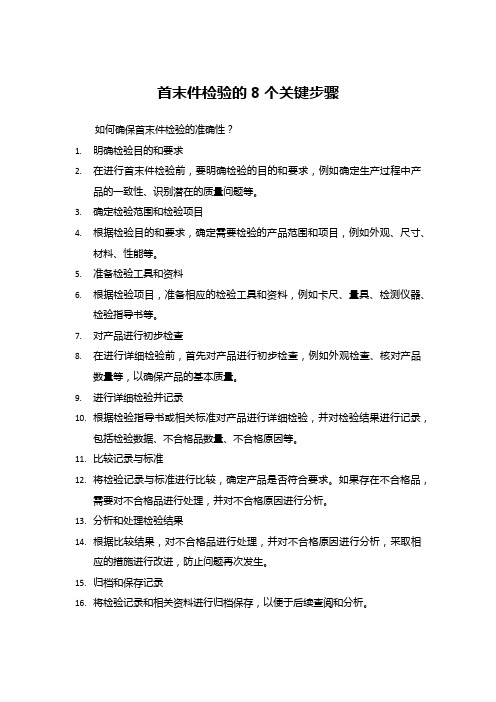
首末件检验的8个关键步骤
如何确保首末件检验的准确性?
1.明确检验目的和要求
2.在进行首末件检验前,要明确检验的目的和要求,例如确定生产过程中产
品的一致性、识别潜在的质量问题等。
3.确定检验范围和检验项目
4.根据检验目的和要求,确定需要检验的产品范围和项目,例如外观、尺寸、
材料、性能等。
5.准备检验工具和资料
6.根据检验项目,准备相应的检验工具和资料,例如卡尺、量具、检测仪器、
检验指导书等。
7.对产品进行初步检查
8.在进行详细检验前,首先对产品进行初步检查,例如外观检查、核对产品
数量等,以确保产品的基本质量。
9.进行详细检验并记录
10.根据检验指导书或相关标准对产品进行详细检验,并对检验结果进行记录,
包括检验数据、不合格品数量、不合格原因等。
11.比较记录与标准
12.将检验记录与标准进行比较,确定产品是否符合要求。
如果存在不合格品,
需要对不合格品进行处理,并对不合格原因进行分析。
13.分析和处理检验结果
14.根据比较结果,对不合格品进行处理,并对不合格原因进行分析,采取相
应的措施进行改进,防止问题再次发生。
15.归档和保存记录
16.将检验记录和相关资料进行归档保存,以便于后续查阅和分析。
总之,要确保首末件检验的准确性,需要明确检验目的和要求,确定合理的检验范围和项目,准备必要的检验工具和资料,对产品进行初步检查,进行详细检验并记录,比较记录与标准,分析和处理检验结果,并将检验记录和相关资料进行归档保存。
这些措施将有助于提高首末件检验的准确性和可靠性,从而为企业的质量控制提供有力支持。
首末件检验流程:确保工艺正确、零部件正确、质量稳定
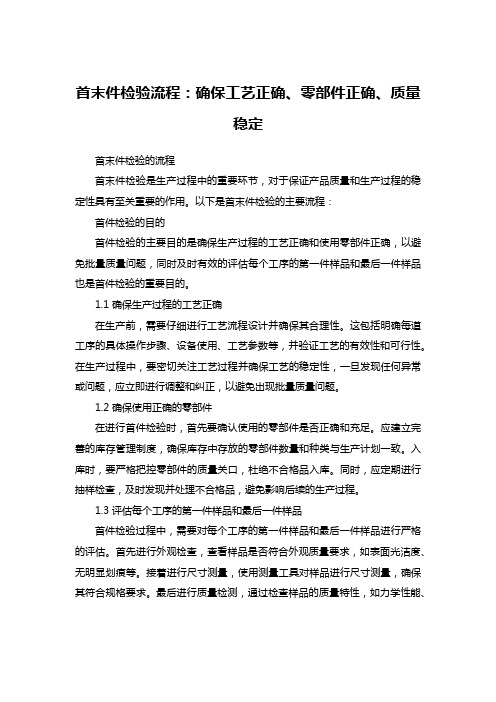
首末件检验流程:确保工艺正确、零部件正确、质量稳定首末件检验的流程首末件检验是生产过程中的重要环节,对于保证产品质量和生产过程的稳定性具有至关重要的作用。
以下是首末件检验的主要流程:首件检验的目的首件检验的主要目的是确保生产过程的工艺正确和使用零部件正确,以避免批量质量问题,同时及时有效的评估每个工序的第一件样品和最后一件样品也是首件检验的重要目的。
1.1 确保生产过程的工艺正确在生产前,需要仔细进行工艺流程设计并确保其合理性。
这包括明确每道工序的具体操作步骤、设备使用、工艺参数等,并验证工艺的有效性和可行性。
在生产过程中,要密切关注工艺过程并确保工艺的稳定性,一旦发现任何异常或问题,应立即进行调整和纠正,以避免出现批量质量问题。
1.2 确保使用正确的零部件在进行首件检验时,首先要确认使用的零部件是否正确和充足。
应建立完善的库存管理制度,确保库存中存放的零部件数量和种类与生产计划一致。
入库时,要严格把控零部件的质量关口,杜绝不合格品入库。
同时,应定期进行抽样检查,及时发现并处理不合格品,避免影响后续的生产过程。
1.3 评估每个工序的第一件样品和最后一件样品首件检验过程中,需要对每个工序的第一件样品和最后一件样品进行严格的评估。
首先进行外观检查,查看样品是否符合外观质量要求,如表面光洁度、无明显划痕等。
接着进行尺寸测量,使用测量工具对样品进行尺寸测量,确保其符合规格要求。
最后进行质量检测,通过检查样品的质量特性,如力学性能、化学成分等,确保其符合质量要求。
在最后一件样品检验完成后,与首件样品进行对比,评估整个批次的质量稳定性。
总结首末件检验是生产过程中不可或缺的环节,通过对其流程的详细了解,我们可以更好地把握生产过程中的关键质量控制点。
首件检验不仅可以帮助我们及时发现和纠正生产过程中的问题,还能确保生产过程的稳定性和产品质量的可靠性。
因此,在实际生产过程中,应充分重视首末件检验,并严格按照相关流程进行操作。
首件尾件确认作业规范

6.0相关文件
序号
文件名称
文件编号
6.1
《不合格品管理程序》
QEP-品-010
7.0相关表单
序号
表单名称
表单编号
文件/记录保存部门
文件/记录
保存期限
7.1
【前工序首件记录表】
QER-品-001
品管部
3年
7.2
【固晶首件检验记录表】
QER-品-003
品管部
3年
7.3
【焊线首件检验记录表】
QER-品-006
品管部
3年
7.4
【压盖首检检验记录表】
QER-品-015
品管部
3年
7.5
【印码首件检验记录表】
QER-品-016
品管部
3年
7.6
【贴片首件检验记录表】
QER-品-019
品管部
文件制(修)订履历
版本
工程变更通知号
制(修)订内容
生效日期
制(修)订
核准
A
首次发行
2019.09.26
Lh
L H
分发部门及份数
部门
份数
部门
份数
1.0目的
为了防止产品出现批量性的不合格,特制定首件、尾件确认相关的作业流程要求。
2.0范围
适用于生产之所有系列产品。
3.0定义
3.1首件检验:产品批量生产前或正常生产过程换班次或出现异常后生产的第一件或前几件产品的检验。
3年
7.7
【贴膜首件检验记录表】
首尾件检验管理规定xxxxxxxxx
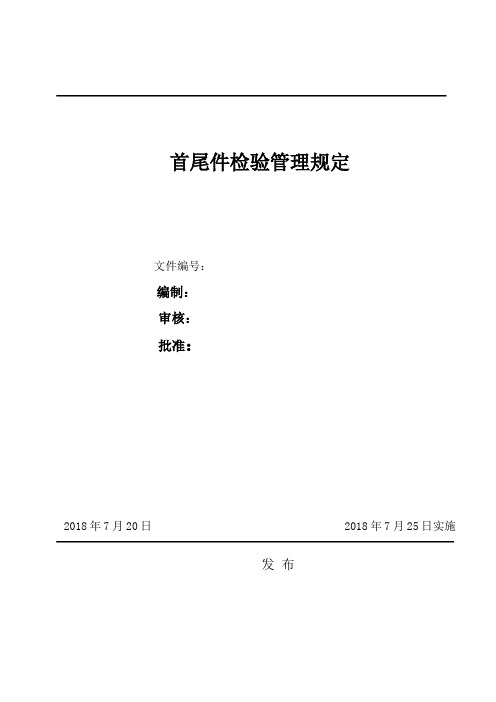
首尾件检验管理规定文件编号:编制:审核:批准:2018年7月20日 2018年7月25日实施发布1 目的保证工序要素满足产品质量要求,防止出现批量不合格产品。
2 适用范围适用于组装温控器产品的压片、铆接、旋铆、复口等加工阶段。
3 职责3.1品管部巡检员负责对操作者首尾件进行检验并对操作者的的自检、互检和专检工作进行监督、检查。
3.2技术部负责对检验设备、检验工装的检修和监督管理。
3.3生产车间操作者负责首尾件自检工作,巡检员对操作者首尾件自检结果进行专检确认;并组织对不合格首尾件的工艺分析。
生产车间负责对设备、工装的使用维护和日常保养。
4工作程序4.1 首尾件检验生产单位应组织操作员对首(尾)件进行自检和专检,品管部巡检员对首(尾)件进行进行确认并记录。
4.1.1首件检验或检验时机a)首件检验是对所有新产品投入、新设备投入、设备维修均要求进行首件检验和尾件检验(生产开始或工序要素发生变化时)的首件(或几件)产品实施自检和专检控制,防止产生批量废品。
b)首件检验时机出现下列情形之一,应进行首件检验:1)每班开工前。
2)工序操作者交替变化时;3)每批原材料、半成品投入时;4)工艺技术规范发生变更时;5)设备及工装调整后;6) 新产品投入、新设备投入、设备维修等后的生产,须经过首件确认。
4.1.2尾件检验和检验时机尾件检验是对工序每批生产完工后的最后一件(或几件)产品的检验,以便及时发现和消除工序要素中的异常现象,侧重于对工装合格状态的验证,保证下一轮生产产品质量的符合性。
4.1.3首尾件检验控制a)工序批生产中,操作者应按照工艺文件对加工的首件和尾件进行自检;自检合格,通知巡检员核查确认。
b)巡检员需对操作者首尾件自检结果进行确认,分别在“首件检验记录表”和“尾件检验记录表”上记录结果,并签名确认。
c)首件不合格,允许车间组长进行调整加工后再送验,但三次不合格,需停止加工,生产单位应及时提请首件不合格评审,由技术部和品管部共同组织施工员、工艺员、检验人员、操作者进行原因分析,采取措施予以解决。
首巡末件检验制度

首件、末件检验制度为了提高产品合格率,有效监控每一个批次产品状态。
保证产品各个工序的质量稳定性,特此增加首件、巡检、末件保存制度,检验的产品暂存在首件盒内,直到该批次产品生产结束,检验产品才可以流入下序生产。
一、首末件检验要求,状态处理。
1、如果首件不合格,请操着停止生产,班长级相关人员及时整改,合格后开始生产。
2、如果首件合格,巡检、末件不合格,该批次该工序产品第一时间隔离、挑选、返工。
3、如果首件合格,巡检、末件合格,可流入下工序生产。
4、首件由操作者(架模工)交到检验台,有检验员检查、确认签字、盖章后,操作工人保存在首件盒子内,到该工序生产结束。
5、检验员在生产过程中随机对该产品进行巡检,巡检产品可保存在首件盒子内。
6、操作工人在生产结束时、最后一、二件必须保存在首件盒子内,检验员对末件进行检查。
末件必须是最后一两件,不可中途在产品中挑选。
7、首件请放在机床台面空置区域,便于检验查看。
8、机床台面请不要放置工具、不相关产品,产品冲压后请不要放在工作台面,及时放置到框子内。
二、首末件判断产品责任制度。
1、首件检验不合格,检验员要求操作者停止生产,操作者通知架模工、班组长整改合格,后生产。
如果没有整改合格就生产,主要责任在操作者、班组长、架模工承担。
可放行的质量问题,必须走“不合格品报告”程序,不得私自口头放行。
2、巡检不合格,检验员通知操作停止生产,并隔离产品;走“不合格品处理程序”,如果对模具进行修模、重新架模,必选重新按照首件检验执行。
没有走不合格程序检验员责任,走了程序没有处理,班组长责任。
3、首件不合格、巡检合格,末件检验不合格,检验员通知操作停止生产,并隔离产品;走“不合格品处理程序”,没有走不合格程序检验员责任,走了程序没有处理,班组长责任。
如果对模具进行修模、重新架模,必选重新按照首件检验执行。
没有重新首件的操作者、架模工责任。
检验员职责区域划分。