湿法脱硫技术介绍
石灰石(石灰)湿法脱硫技术

石灰石(石灰)湿法脱硫技术湿法脱硫中所应用的脱硫系统位于烟道的末端,脱硫过程中的反应温度低于露点,因此,脱硫后的烟气需要进行加热处理才能排出。
由于脱硫过程中的反应类型为气液反应,其脱硫效率和所用脱硫添加剂的使用效率均较高,因此,在许多大型燃煤电站中都已建成使用。
一、石灰石(石灰)湿法脱硫技术概述根据最新的技术统计资料显示,到目前为止投入使用的脱硫技术种类已经超过200种,在形式多样的脱硫技术中,湿法脱硫技术是应用范围最广、脱硫效率最高的一种应用技术,占脱硫设备总装机量的80%以上,始终占据着脱硫技术领域的主导地位。
石灰石(石灰)湿法脱硫技术作为最成熟的一种脱硫技术,其脱硫效率可到90%以上,成为效果最显著的脱硫方法。
石灰石(石灰)湿法脱硫技术经过几十年的发展,已被应用于600MW烟气单塔的烟气处理系统中,脱硫剂的利用效率基本稳定在95%以上,反应过程所消耗的电能不足电厂出力的1.5%,与十多年前的脱硫系统相比,在脱硫成本轻微上升的条件下脱硫效果却得到了质的飞跃。
二、石灰石(石灰)湿法脱硫技术的应用原理(一)工艺流程石灰石(石灰)湿法脱硫技术的基本过程是:烟气经锅炉排出后进入除尘器,之后进入脱硫塔,脱硫塔内的石灰石浆液与烟气中的SO2进行气液反应,生成CaCO3和CaCO4。
在反应之后的浆液中充入氧气,可将CaCO3氧化成CaCO4和石膏,石膏经脱水处理后可作为脱硫反应的副产品被回收利用。
工业实践中采用最多的脱硫塔方式是单塔,在单塔中可完成脱硫反应的全过程,脱硫成本和运行费用也更低。
(二)反应过程烟气中的SO2在脱硫塔内的反应过程可用下面两个方程表示,其中,第二个反应过程中生产的CaSO3会被烟气中的氧气氧化生成CaSO4,形成副产品被回收利用。
SO2+CaCO3→CaSO3+CO2 石灰石浆液(1)SO2+Ca(OH)2→CaSO3+H2O 石灰浆液(2)(三)脱硫效率脱硫效率受到诸多因素的影响,其中,脱硫塔中的pH值对脱硫效率会产生较大的影响。
石灰石湿法脱硫原理四个步骤

石灰石湿法脱硫原理四个步骤
石灰石湿法脱硫是一种常用的烟气脱硫技术,主要用于燃煤电厂等工业领域中
排放含硫气体的治理。
其原理是利用石灰石(CaCO3)和水(H2O)反应生成石灰
水(Ca(OH)2),再将石灰水喷入烟气中,与烟气中的二氧化硫(SO2)发生化学
反应形成硫酸钙(CaSO3),达到脱除二氧化硫的目的。
下面将详细介绍石灰石湿
法脱硫的四个步骤。
第一步:石灰石磨碎
首先,将石灰石破碎成适当的颗粒大小,通常要求粒度均匀,以提高与烟气中
二氧化硫的接触面积,增加反应效率。
第二步:石灰石制浆
将破碎后的石灰石与水混合制成石灰水浆料,使其达到适当的浓度和粘度,以
便后续的喷射和混合过程中均匀分布。
第三步:石灰水喷射
将制成的石灰水浆料通过喷射器喷入烟气脱硫设备中,形成细小的石灰水颗粒,并与烟气中的二氧化硫接触反应,生成硫酸钙。
第四步:脱硫产物处理
经过湿法脱硫过程后,生成的硫酸钙沉淀将被收集,并进行进一步处理,通常
通过过滤、压滤、脱水等方法将硫酸钙固化成产品或废弃物,以便后续的处理和处置。
综上所述,石灰石湿法脱硫的原理主要包括将石灰石破碎、制浆,再喷射进入
烟气中进行反应生成硫酸钙,最终将脱硫产物处理的四个步骤。
这种方法可以有效地将燃煤电厂等工业烟气中的二氧化硫去除,减少大气污染物排放,保护环境和人类健康。
大湿法脱硫
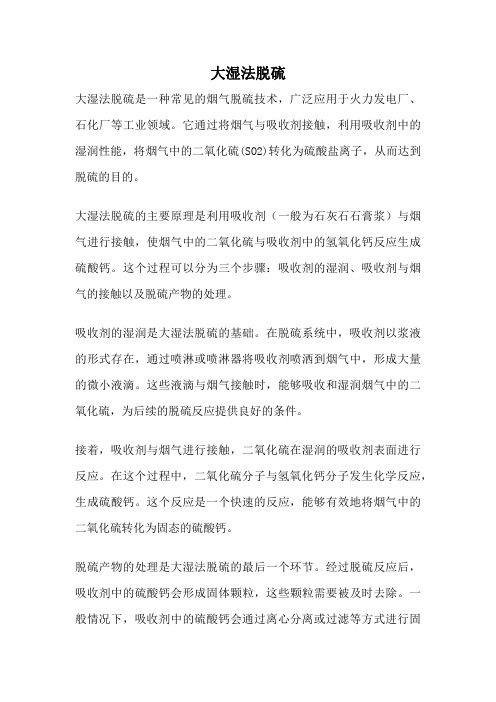
大湿法脱硫大湿法脱硫是一种常见的烟气脱硫技术,广泛应用于火力发电厂、石化厂等工业领域。
它通过将烟气与吸收剂接触,利用吸收剂中的湿润性能,将烟气中的二氧化硫(SO2)转化为硫酸盐离子,从而达到脱硫的目的。
大湿法脱硫的主要原理是利用吸收剂(一般为石灰石石膏浆)与烟气进行接触,使烟气中的二氧化硫与吸收剂中的氢氧化钙反应生成硫酸钙。
这个过程可以分为三个步骤:吸收剂的湿润、吸收剂与烟气的接触以及脱硫产物的处理。
吸收剂的湿润是大湿法脱硫的基础。
在脱硫系统中,吸收剂以浆液的形式存在,通过喷淋或喷淋器将吸收剂喷洒到烟气中,形成大量的微小液滴。
这些液滴与烟气接触时,能够吸收和湿润烟气中的二氧化硫,为后续的脱硫反应提供良好的条件。
接着,吸收剂与烟气进行接触,二氧化硫在湿润的吸收剂表面进行反应。
在这个过程中,二氧化硫分子与氢氧化钙分子发生化学反应,生成硫酸钙。
这个反应是一个快速的反应,能够有效地将烟气中的二氧化硫转化为固态的硫酸钙。
脱硫产物的处理是大湿法脱硫的最后一个环节。
经过脱硫反应后,吸收剂中的硫酸钙会形成固体颗粒,这些颗粒需要被及时去除。
一般情况下,吸收剂中的硫酸钙会通过离心分离或过滤等方式进行固液分离,得到固体产物。
而剩余的吸收剂则会被再次利用,回流到脱硫系统中进行循环使用。
大湿法脱硫技术具有脱硫效率高、适用范围广、操作稳定等优点。
它能够将烟气中的二氧化硫去除率达到90%以上,同时还能够去除部分烟尘和其他污染物。
此外,大湿法脱硫还可以适应不同燃料的烟气脱硫需求,如煤炭、石油焦、石油煤等。
然而,大湿法脱硫也存在一些问题。
首先,吸收剂的消耗量较大,需要大量的吸收剂进行喷淋,增加了运行成本。
其次,脱硫产物中的硫酸钙具有一定的腐蚀性,需要进行处理和储存。
再次,大湿法脱硫过程中产生的废液需要进行处理,以防止对环境造成污染。
大湿法脱硫是一种常用的烟气脱硫技术,通过吸收剂与烟气的接触,将烟气中的二氧化硫转化为硫酸钙,从而实现脱硫的目的。
石灰石石膏湿法脱硫的工艺

石灰石石膏湿法脱硫的工艺【石灰石石膏湿法脱硫的工艺】导语:石灰石石膏湿法脱硫是一种常见的烟气脱硫技术,通过将石灰石与石膏反应,可以高效地去除燃煤发电厂和工业锅炉烟气中的二氧化硫。
本文将深入探讨石灰石石膏湿法脱硫的工艺原理、优势以及相关问题。
一、工艺原理1. 石灰石石膏湿法脱硫原理:石灰石与石膏发生反应生成硬石膏,将烟气中的二氧化硫转化为硫酸钙,并形成可回收利用的石膏产物。
主要反应方程式如下所示:CaCO3 + SO2 + 2H2O → CaSO4·2H2O + CO22. 脱硫反应的特点:该反应是一个快速的液相反应,在一定反应温度、气体流速和石膏浆液浓度下进行。
反应速率受碱性、反应温度、质量浓度等因素的影响。
二、工艺步骤1. 石灰石石膏湿法脱硫的基本步骤:(1)石灰石破碎、磨细:将原料石灰石经过破碎和磨细处理,提高其活性和反应速率。
(2)制备石膏浆液:将石灰石与水混合,形成石灰石浆液。
为了提高脱硫效果,还可加入一定量的添加剂。
(3)脱硫反应:将石灰石浆液喷入脱硫塔,通过与烟气的接触和反应,使二氧化硫转化为硫酸钙。
(4)石膏产物处理:将脱硫过程中生成的硬石膏经过脱水、干燥等处理后,得到成品石膏。
2. 工艺改进:为了提高脱硫效率和经济性,石灰石石膏湿法脱硫工艺进行了多方面的改进。
例如引入喷雾器、增加反应塔数目、采用高效填料等,以增加烟气与石灰石浆液的接触面积,加强反应效果。
三、工艺优势1. 脱硫效率高:石灰石石膏湿法脱硫工艺能够高效地将烟气中的二氧化硫转化为重质石膏产物,脱硫效率可达到90%以上。
2. 石膏产物可回收利用:脱硫过程中生成的硬石膏可以用于建材、石膏板等行业,实现资源的循环利用。
3. 工艺成熟可靠:石灰石石膏湿法脱硫工艺经过多年的实践应用,技术成熟可靠,广泛应用于燃煤发电厂和工业锅炉等领域。
四、问题与挑战1. 石膏处理与排放:脱硫过程中生成的硬石膏需要进行后续的脱水、干燥等处理,同时还需要解决石膏产物的长期存储和排放问题。
湿法脱硫技术

湿法脱硫技术湿法脱硫技术是一种环保的烟气脱硫方法,它广泛应用于工业和电力行业,用于减少大气中的二氧化硫排放,降低空气污染。
本文将从湿法脱硫技术的原理、工艺和应用等方面进行详细介绍。
一、湿法脱硫技术的原理湿法脱硫技术是利用溶液中的碱性物质与二氧化硫发生化学反应,将二氧化硫转化为可溶于水中的硫酸盐。
主要的反应方程式为:SO2 + Ca(OH)2 → CaSO3 + H2O湿法脱硫技术有两种主要方式,分别是石灰石石膏法和海水脱硫法。
石灰石石膏法是将石灰石干燥研磨成粉末后与烟气中的二氧化硫反应,产生石膏,而海水脱硫法则是通过将海水喷洒到烟气中,利用海水中的碱性物质进行反应。
二、湿法脱硫技术的工艺湿法脱硫技术主要包括烟气净化系统和废水处理系统两部分。
烟气净化系统主要由除尘器、喷射塔和循环泵等设备组成。
烟气通过除尘器进行初步的净化,去除其中的颗粒物和粉尘。
之后,烟气进入喷射塔,喷洒石灰石水浆或海水,与二氧化硫发生反应,形成硫酸盐溶液。
最后,循环泵将硫酸盐溶液回收,净化后再次喷洒到烟气中,循环利用。
废水处理系统用于处理湿法脱硫过程中产生的废水。
废水中含有大量的硫酸盐和其他污染物,需要进行化学处理和沉淀处理,以降低污染物的浓度,使其达到排放标准。
三、湿法脱硫技术的应用湿法脱硫技术被广泛应用于工业和电力行业的烟气净化中,主要用于减少二氧化硫的排放量,保护环境。
以下是湿法脱硫技术在不同领域的应用举例:1. 电力行业:湿法脱硫技术被广泛应用于火电厂和燃煤发电厂中,用于减少烟气中的二氧化硫排放,降低大气污染。
2. 钢铁行业:湿法脱硫技术可以应用于钢铁生产中的高炉和转炉烟气脱硫,减少二氧化硫的排放,减轻对大气环境的污染。
3. 化工行业:湿法脱硫技术可以用于化工厂废气的治理,降低二氧化硫的排放,保护周边的环境质量。
4. 石油行业:湿法脱硫技术可以应用于炼油厂中,减少烟气中的硫化氢等有害气体的排放,改善工作环境。
总之,湿法脱硫技术是一种重要的烟气脱硫方法,具有广泛的应用前景。
湿法烟气脱硫的概念

湿法烟气脱硫的概念湿法烟气脱硫是一种常见的烟气净化技术,用于去除烟气中的二氧化硫(SO2)等有害气体。
它通过与烟气中的湿化剂溶液反应,将SO2转化为可溶于水的硫酸盐或亚硫酸盐,从而达到去除SO2的目的。
本文将详细介绍湿法烟气脱硫的原理、工艺流程、优缺点和应用领域。
一、湿法烟气脱硫的原理湿法烟气脱硫的核心原理是将烟气中的SO2转化为溶于水的硫酸盐或亚硫酸盐,这一过程主要包括以下几个步骤:1. 氧化反应:湿法烟气脱硫中通常采用氧化剂(如空氧、过氧化氢等)将SO2氧化为亚硫酸气体(SO3),反应公式为:SO2 + 1/2O2 →SO32. 吸收反应:亚硫酸气体与水中的湿化剂(一般为氧化钙或氢氧化钠溶液)发生反应生成硫酸盐或亚硫酸盐,反应公式为:SO2 + H2O + CaO →CaSO3 + 1/2O2SO2 + H2O + NaOH →Na2SO33. 成核和粒径增长:湿法烟气脱硫中的烟气中含有微细颗粒物,如PM2.5,SO3会在气液界面上成核,并与颗粒物发生反应,形成硫酸盐或亚硫酸盐颗粒。
4. 结晶和沉淀:硫酸盐或亚硫酸盐颗粒在湿法烟气脱硫装置中沉淀下来,从而实现了烟气中SO2的去除。
二、湿法烟气脱硫的工艺流程湿法烟气脱硫一般包括烟气预处理、烟气吸收、氧化和结晶沉淀等过程。
主要的工艺流程如下:1. 烟气预处理:烟气进入脱硫装置前需要进行一些预处理工作,如除尘、降温等。
这些工作主要是为了减小脱硫装置的负荷和保护脱硫设备。
2. 烟气吸收:烟气进入脱硫装置后,与湿化剂接触发生吸收反应。
常用的湿化剂有氧化钙和氢氧化钠等。
烟气在吸收塔内与湿化剂充分接触,SO2被吸收生成硫酸盐或亚硫酸盐。
3. 氧化:湿法烟气脱硫装置通常采用氧化剂将亚硫酸气体(SO2)氧化成SO3。
氧化反应一般是在氧化塔中进行的,然后将氧化后的烟气送回吸收塔进行吸收反应。
4. 结晶沉淀:湿法烟气脱硫中生成的硫酸盐或亚硫酸盐颗粒物沉淀到底部的装置中进行结晶沉淀。
湿法脱硫方案

1. 简介湿法脱硫是一种常用的烟气脱硫技术,适用于燃煤工业锅炉、电厂、钢铁冶炼等领域。
本文将介绍湿法脱硫的工作原理、设备组成以及操作步骤,以帮助读者了解该技术并合理应用。
2. 工作原理湿法脱硫通过在烟气中喷入脱硫剂,使脱硫剂与烟气中的二氧化硫发生反应生成硫酸盐,达到脱硫的目的。
其主要步骤包括: - 喷射装置:将脱硫剂雾化成细小颗粒,并将其喷入烟气中。
- 吸收过程:脱硫剂颗粒与烟气中的二氧化硫发生吸收反应,生成硫酸盐。
- 除尘装置:除去吸收过程中产生的颗粒物,以保证烟气排放的环保要求。
3. 设备组成典型的湿法脱硫设备包括以下几个主要组成部分: - 烟气进口:将含有二氧化硫的烟气引入脱硫装置。
- 喷射装置:将脱硫剂通过喷雾器雾化成细小颗粒,并通过喷嘴喷入烟气中。
- 吸收塔:用于脱硫剂与烟气中的二氧化硫发生吸收反应,生成硫酸盐。
- 循环泵:将脱硫剂循环供应给喷射装置使用,保证脱硫剂的充足和稳定性。
- 除尘器:用于除去吸收过程中产生的颗粒物,以达到烟气排放的环保要求。
- 排气系统:将经过湿法脱硫处理后的烟气排放到大气中。
4. 操作步骤湿法脱硫的操作包括以下几个主要步骤: 1. 脱硫剂配制:根据烟气中的硫含量确定脱硫剂的用量,并将其配制成适当的浓度。
2. 设备检查:检查喷射装置、吸收塔、循环泵、除尘器等设备,确保其正常运行。
3. 启动设备:按照设备的启动顺序逐个启动相关设备,并观察其运行情况。
4. 脱硫剂喷射:逐步调整喷射装置的参数,使得脱硫剂的喷射量和颗粒大小适合脱硫反应的需求。
5. 监测与调整:通过监测烟气中的二氧化硫浓度、脱硫剂的浓度以及排放烟气中的颗粒物等指标,并根据监测结果调整湿法脱硫的操作参数。
6. 停止设备:按照设备的停止顺序逐个停止设备,并进行必要的冲洗和维护。
5. 注意事项在使用湿法脱硫技术时,需要注意以下几个方面的问题: - 脱硫剂选择:根据燃煤的硫含量和其他操作要求选择合适的脱硫剂,并保证其供应的稳定性。
湿法烟气脱硫技术、工艺及其优缺点图文并茂详解

湿法烟气脱硫技术、工艺及其优缺点图文并茂详解一、湿法烟气脱硫技术优点:湿法烟气脱硫技术为气液反应,反应速度快,脱硫效率高,一般均高于90%,技术成熟,适用面广。
湿法脱硫技术比较成熟,生产运行安全可靠,在众多的脱硫技术中,始终占据主导地位,占脱硫总装机容量的80%以上。
缺点:生成物是液体或淤渣,较难处理,设备腐蚀性严重,洗涤后烟气需再热,能耗高,占地面积大,投资和运行费用高。
系统复杂、设备庞大、耗水量大、一次性投资高,一般适用于大型电厂。
分类:常用的湿法烟气脱硫技术有石灰石-石膏法、间接的石灰石-石膏法、柠檬吸收法等。
A、石灰石/石灰-石膏法:原理:是利用石灰石或石灰浆液吸收烟气中的SO2,生成亚硫酸钙,经分离的亚硫酸钙(CaSO3)可以抛弃,也可以氧化为硫酸钙(CaSO4),以石膏形式回收。
是目前技术最成熟、运行状况最稳定的脱硫工艺,脱硫效率达到90%以上。
石灰石/石灰—石膏法烟气脱硫工艺应用是比较广泛的,其采用钙基脱硫剂吸收二氧化硫后生成的亚硫酸钙、硫酸钙,由于其溶解度较小,极易在脱硫塔内及管道内形成结垢、堵塞现象。
对比石灰石法脱硫技术,双碱法烟气脱硫技术则克服了石灰石—石灰法容易结垢的缺点。
B 、间接石灰石-石膏法:常见的间接石灰石-石膏法有:钠碱双碱法、碱性硫酸铝法和稀硫酸吸收法等。
原理:钠碱、碱性氧化铝(Al2O3·nH2O)或稀硫酸(H2SO4)吸收SO2,生成的吸收液与石灰石反应而得以再生,并生成石膏。
该法操作简单,二次污染少,无结垢和堵塞问题,脱硫效率高,但是生成的石膏产品质量较差。
C 、柠檬吸收法:原理:柠檬酸(H3C6H5O7·H2O)溶液具有较好的缓冲性能,当SO2气体通过柠檬酸盐液体时,烟气中的SO2与水中H发生反应生成H2SO3络合物,SO2吸收率在99%以上。
这种方法仅适于低浓度SO2烟气,而不适于高浓度SO2气体吸收,应用范围比较窄。
另外,还有海水脱硫法、磷铵复肥法、液相催化法等湿法烟气脱硫技术。
湿法脱硫简介
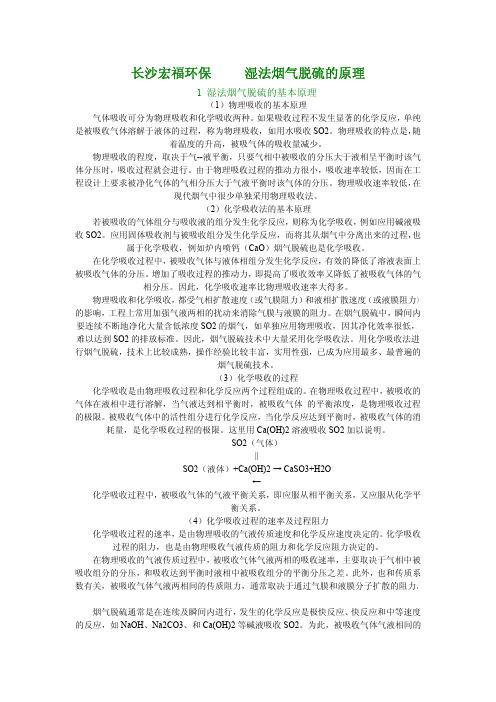
长沙宏福环保湿法烟气脱硫的原理1湿法烟气脱硫的基本原理(1)物理吸收的基本原理气体吸收可分为物理吸收和化学吸收两种。
如果吸收过程不发生显著的化学反应,单纯是被吸收气体溶解于液体的过程,称为物理吸收,如用水吸收SO2。
物理吸收的特点是,随着温度的升高,被吸气体的吸收量减少。
物理吸收的程度,取决于气--液平衡,只要气相中被吸收的分压大于液相呈平衡时该气体分压时,吸收过程就会进行。
由于物理吸收过程的推动力很小,吸收速率较低,因而在工程设计上要求被净化气体的气相分压大于气液平衡时该气体的分压。
物理吸收速率较低,在现代烟气中很少单独采用物理吸收法。
(2)化学吸收法的基本原理若被吸收的气体组分与吸收液的组分发生化学反应,则称为化学吸收,例如应用碱液吸收SO2。
应用固体吸收剂与被吸收组分发生化学反应,而将其从烟气中分离出来的过程,也属于化学吸收,例如炉内喷钙(CaO)烟气脱硫也是化学吸收。
在化学吸收过程中,被吸收气体与液体相组分发生化学反应,有效的降低了溶液表面上被吸收气体的分压。
增加了吸收过程的推动力,即提高了吸收效率又降低了被吸收气体的气相分压。
因此,化学吸收速率比物理吸收速率大得多。
物理吸收和化学吸收,都受气相扩散速度(或气膜阻力)和液相扩散速度(或液膜阻力)的影响,工程上常用加强气液两相的扰动来消除气膜与液膜的阻力。
在烟气脱硫中,瞬间内要连续不断地净化大量含低浓度SO2的烟气,如单独应用物理吸收,因其净化效率很低,难以达到SO2的排放标准。
因此,烟气脱硫技术中大量采用化学吸收法。
用化学吸收法进行烟气脱硫,技术上比较成熟,操作经验比较丰富,实用性强,已成为应用最多、最普遍的烟气脱硫技术。
(3)化学吸收的过程化学吸收是由物理吸收过程和化学反应两个过程组成的。
在物理吸收过程中,被吸收的气体在液相中进行溶解,当气液达到相平衡时,被吸收气体的平衡浓度,是物理吸收过程的极限。
被吸收气体中的活性组分进行化学反应,当化学反应达到平衡时,被吸收气体的消耗量,是化学吸收过程的极限。
湿法脱硫的工艺流程化学反应方程式
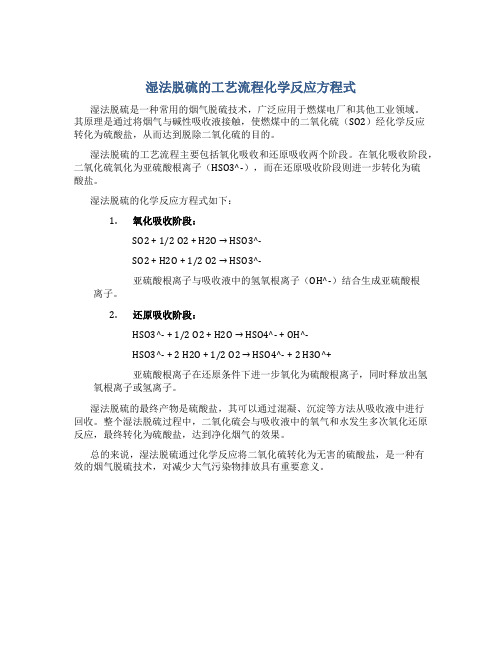
湿法脱硫的工艺流程化学反应方程式
湿法脱硫是一种常用的烟气脱硫技术,广泛应用于燃煤电厂和其他工业领域。
其原理是通过将烟气与碱性吸收液接触,使燃煤中的二氧化硫(SO2)经化学反应
转化为硫酸盐,从而达到脱除二氧化硫的目的。
湿法脱硫的工艺流程主要包括氧化吸收和还原吸收两个阶段。
在氧化吸收阶段,二氧化硫氧化为亚硫酸根离子(HSO3^-),而在还原吸收阶段则进一步转化为硫
酸盐。
湿法脱硫的化学反应方程式如下:
1.氧化吸收阶段:
SO2 + 1/2 O2 + H2O → HSO3^-
SO2 + H2O + 1/2 O2 → HSO3^-
亚硫酸根离子与吸收液中的氢氧根离子(OH^-)结合生成亚硫酸根离子。
2.还原吸收阶段:
HSO3^- + 1/2 O2 + H2O → HSO4^- + OH^-
HSO3^- + 2 H2O + 1/2 O2 → HSO4^- + 2 H3O^+
亚硫酸根离子在还原条件下进一步氧化为硫酸根离子,同时释放出氢氧根离子或氢离子。
湿法脱硫的最终产物是硫酸盐,其可以通过混凝、沉淀等方法从吸收液中进行
回收。
整个湿法脱硫过程中,二氧化硫会与吸收液中的氧气和水发生多次氧化还原反应,最终转化为硫酸盐,达到净化烟气的效果。
总的来说,湿法脱硫通过化学反应将二氧化硫转化为无害的硫酸盐,是一种有
效的烟气脱硫技术,对减少大气污染物排放具有重要意义。
湿法烟气脱硫设计及设备选型手册
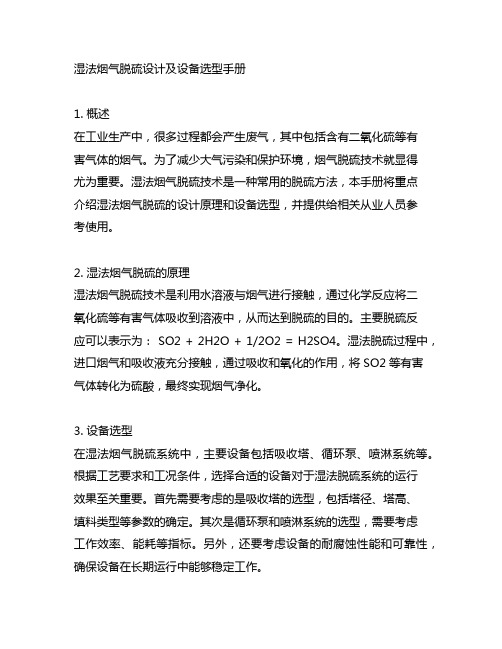
湿法烟气脱硫设计及设备选型手册1. 概述在工业生产中,很多过程都会产生废气,其中包括含有二氧化硫等有害气体的烟气。
为了减少大气污染和保护环境,烟气脱硫技术就显得尤为重要。
湿法烟气脱硫技术是一种常用的脱硫方法,本手册将重点介绍湿法烟气脱硫的设计原理和设备选型,并提供给相关从业人员参考使用。
2. 湿法烟气脱硫的原理湿法烟气脱硫技术是利用水溶液与烟气进行接触,通过化学反应将二氧化硫等有害气体吸收到溶液中,从而达到脱硫的目的。
主要脱硫反应可以表示为: SO2 + 2H2O + 1/2O2 = H2SO4。
湿法脱硫过程中,进口烟气和吸收液充分接触,通过吸收和氧化的作用,将SO2等有害气体转化为硫酸,最终实现烟气净化。
3. 设备选型在湿法烟气脱硫系统中,主要设备包括吸收塔、循环泵、喷淋系统等。
根据工艺要求和工况条件,选择合适的设备对于湿法脱硫系统的运行效果至关重要。
首先需要考虑的是吸收塔的选型,包括塔径、塔高、填料类型等参数的确定。
其次是循环泵和喷淋系统的选型,需要考虑工作效率、能耗等指标。
另外,还要考虑设备的耐腐蚀性能和可靠性,确保设备在长期运行中能够稳定工作。
4. 设计原则在进行湿法烟气脱硫系统的设计时,需要考虑以下几个方面的原则:首先是脱硫效率,要求设备在不同运行条件下都能够稳定实现脱硫目标;其次是设备的能耗和运行成本,需要在满足脱硫要求的前提下,尽量降低设备的能耗;还要考虑设备的可维护性和安全性,保障设备长期稳定运行。
5. 总结与展望湿法烟气脱硫技术作为一种成熟的脱硫方法,在工业生产中应用广泛。
在未来,随着环保要求的不断提高,湿法脱硫技术还将得到进一步完善,设备性能将会更加优化。
加强对湿法烟气脱硫技术的研究和应用,对于促进工业生产的可持续发展和生态环境的保护具有重要意义。
6. 个人观点作为一种有效的烟气脱硫技术,湿法脱硫不仅可以有效净化烟气,减少大气污染,也能为工业生产提供良好的环境支持。
我个人认为,在今后的工业发展中,湿法烟气脱硫技术将会得到更广泛的应用,也会在性能和成本上得到更多的改进和提升。
湿法脱硫技术简介

烟气脱硫技术概述为了治理日益恶化的大气环境,控制SO2的排放势在必行,我国已进行了多种脱硫技术的研究及应用。
燃煤脱硫根据具体情况可分为三大类:燃烧前脱硫、燃烧中脱硫和燃烧后脱硫。
燃烧前脱硫燃烧前脱硫方法有机械脱硫、化学脱硫、电磁脱硫、细菌脱硫、超声脱硫等。
机械脱硫法在实际中得到了应用,如跳汰机脱硫、浮选机脱硫、摇床脱硫、旋流器脱硫、螺旋选矿机脱硫等。
机械脱硫是根据煤中硫化铁硫(FeS2)等含硫化合物与煤比重不同而将其除去,这种方法的脱硫效率取决于FeS2等物质的颗粒大小及煤中无机硫的含量。
洗选法不能脱除有机硫及在煤中嵌布很细的硫化铁硫。
化学方法,煤的热解和加氢热解脱硫是根据原煤中使硫存在的化学键Fe-S和C-S与C-C相比不稳定,在热解条件下很容易脱离而生成气相硫化物H2S或CaS,煤的热解和加氢热解就是利用这一特征脱除煤中的硫分。
电化学法是借助煤在电解槽发生电化学氧化和还原反应,将煤中黄铁矿和有机硫氧化成可溶性硫化物或将煤还原加氢,从而达到脱硫效果。
生物脱硫技术是利用微生物参一与铁和硫化合物的氧化作用,使硫铁矿降解,细菌作用将Fe2+氧化为Fe3+ ,单质硫由于细菌作用而氧化为硫酸。
该工艺目前尚未获得大规模应用,不过,随着生物技术的突破发展,该工艺具有良好的发展前景。
微波法是因微波能激发煤中硫化物同浸提剂反应而脱硫。
燃烧中脱硫燃烧中脱硫和燃烧后脱硫即烟气脱硫一般是在燃烧室中和尾部烟道中加入脱硫剂来实现的。
燃烧中脱硫是在燃烧产生的高温气氛下,脱硫剂与SO2气体分子发生化学反应,因此燃烧中脱硫是伴随着燃料燃烧一起完成的。
燃烧中脱硫一般以石灰石(主要成分为CaCO3)作为脱硫剂,将其破碎到合适颗粒度后喷入锅炉内,CaCO3在高温下分解成CaO和CO2,烟气中的SO2与CaO反应,完成SO2的炉内吸收过程:若在还原性气氛下,石灰或石灰石就会和煤燃烧产生的H2S反应,生成CaS,遇氧即被氧化成CaSO4。
湿法脱硫工艺流程

湿法脱硫工艺流程
《湿法脱硫工艺流程》
湿法脱硫是一种用于去除燃煤烟气中二氧化硫的成熟技术,其工艺流程主要包括石灰石磨浆制备、石灰石浆液喷淋和氧化吸收、沉淀浆液搅拌反应、沉淀浆液和脱水浆液的处理等步骤。
首先,石灰石磨浆制备是指将石灰石经过破碎、研磨等工艺处理后制成石灰石浆液,以便后续喷淋和氧化吸收使用。
然后,石灰石浆液通过喷淋和氧化吸收装置喷洒到烟气中,将烟气中的二氧化硫氧化成硫酸盐,吸收到石灰石浆液中。
接着,沉淀浆液搅拌反应是将含有硫酸盐的石灰石浆液与草酸盐类添加剂进行搅拌反应,使硫酸盐沉淀成为石膏,并将石灰石浆液中的杂质物质一同沉淀。
最后,沉淀浆液和脱水浆液的处理是将沉淀后的浆液通过过滤、脱水等工艺处理,将石膏和水分分离出来,获得干燥的石膏产品和清洁的水。
通过这一系列的工艺流程,燃煤烟气中的二氧化硫得以高效去除,减少了对大气环境的污染,同时也为工业生产提供了高质量的石膏产品,实现了环境保护和资源循环利用的双重目的。
湿法脱硫工艺流程已经在电力、化工和冶金等行业得到了广泛应用,成为当前燃煤烟气治理的重要技术之一。
湿法脱硫工艺
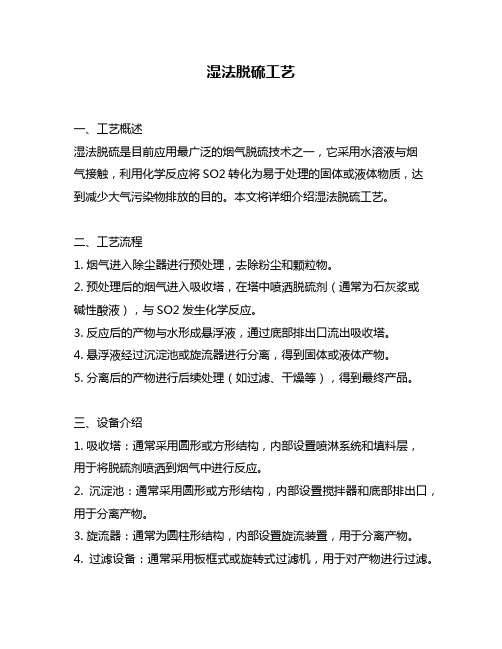
湿法脱硫工艺一、工艺概述湿法脱硫是目前应用最广泛的烟气脱硫技术之一,它采用水溶液与烟气接触,利用化学反应将SO2转化为易于处理的固体或液体物质,达到减少大气污染物排放的目的。
本文将详细介绍湿法脱硫工艺。
二、工艺流程1. 烟气进入除尘器进行预处理,去除粉尘和颗粒物。
2. 预处理后的烟气进入吸收塔,在塔中喷洒脱硫剂(通常为石灰浆或碱性酸液),与SO2发生化学反应。
3. 反应后的产物与水形成悬浮液,通过底部排出口流出吸收塔。
4. 悬浮液经过沉淀池或旋流器进行分离,得到固体或液体产物。
5. 分离后的产物进行后续处理(如过滤、干燥等),得到最终产品。
三、设备介绍1. 吸收塔:通常采用圆形或方形结构,内部设置喷淋系统和填料层,用于将脱硫剂喷洒到烟气中进行反应。
2. 沉淀池:通常采用圆形或方形结构,内部设置搅拌器和底部排出口,用于分离产物。
3. 旋流器:通常为圆柱形结构,内部设置旋流装置,用于分离产物。
4. 过滤设备:通常采用板框式或旋转式过滤机,用于对产物进行过滤。
5. 干燥设备:通常采用烘箱或干燥机,用于将湿润的产物进行干燥处理。
四、脱硫剂选择1. 石灰浆:具有良好的脱硫效果和低成本,但需要大量的水来稀释。
2. 碱性酸液:如NaOH、Ca(OH)2等,具有较高的脱硫效果和较低的成本,在一定范围内可自动调节pH值。
3. 活性炭:主要用于去除有机污染物和重金属等。
五、工艺参数控制1. 脱硫剂浓度:影响反应速率和脱硫效果。
通常控制在10%~20%之间。
2. 烟气流量:影响反应时间和产物质量。
通常控制在15000~30000m3/h之间。
3. 烟气温度:影响反应速率和产物质量。
通常控制在50℃~70℃之间。
4. 废水排放:湿法脱硫产生的废水含有一定浓度的SO2和脱硫剂,需要进行处理或回收利用。
六、工艺优缺点1. 优点:脱硫效果好,可达到90%以上;适用范围广,可处理多种燃料的烟气;操作简单,设备维护成本低。
2. 缺点:需要大量的水来稀释脱硫剂,造成水资源浪费;废水排放需要进行处理或回收利用;在高含盐、高灰分等条件下容易出现堵塞和结垢等问题。
湿法脱硫工艺

湿法脱硫工艺
在工业生产过程中,二氧化硫是一种常见的污染物,主要来源于燃烧煤炭等含硫燃料时释放的烟气中。
高浓度的二氧化硫会对人类健康和环境造成严重危害,因此脱硫技术应运而生。
湿法脱硫工艺是一种常用的脱硫方法,其原理和过程值得深入了解。
湿法脱硫工艺利用氧化剂将烟气中的二氧化硫转化为硫酸盐或硫酸,进而达到减少二氧化硫排放的效果。
在湿法脱硫系统中,石灰石常被用作脱硫剂。
石灰石和氧化剂喷入烟气中形成石膏,石灰石被还原,氧化剂被还原,生成二氧化硫,再次参与循环反应。
通过这种连续的化学反应过程,烟气中的二氧化硫被有效去除。
湿法脱硫工艺有其独特的优点。
首先,其去除效率高,可以将烟气中的二氧化硫去除率达到90%以上,有效减少了二氧化硫对环境的危害。
其次,该工艺适用性广泛,不受烟气中二氧化硫浓度的影响,适用于各类含硫燃料。
此外,湿法脱硫工艺可以同时去除烟气中的颗粒物,起到了除尘的作用,保护了大气环境的清洁。
然而,湿法脱硫工艺也存在一些不足之处。
首先,该工艺需要大量用水,处理后的废水含有大量的石膏、氯化钠等物质,需要经过处理排放或者资源化利用,增加了处理成本。
其次,由于氧化剂难以完全还原,可能导致辅助消耗的问题,增加了工艺的复杂性和能耗。
另外,湿法脱硫系统体积较大,占地面积较多,对工业企业的场地要求较高。
随着环保意识的提升和法规的加强,湿法脱硫工艺在工业生产中得到了广泛应用。
为了提高脱硫效率,降低能耗,工程技术人员正在不断探索湿法脱硫工艺的优化和改进。
未来,随着技术的发展和创新,相信湿法脱硫工艺将更加成熟和高效,为保护环境和人类健康作出更大的贡献。
湿法脱硫技术介绍

2湿法脱硫技术介绍2.1 脱硫方法简介目前,世界范围内的火电厂脱硫技术多种多样,达数百种之多。
按脱硫工艺在燃烧过程中所处位置不同可分为:燃烧前脱硫、燃烧中脱硫、燃烧后脱硫。
燃烧前脱硫主要是洗煤、煤的气化和液化,洗煤仅能脱去煤中很少一部分硫,只可作为脱硫的一种辅助手段,煤气化和液化脱硫效果好,是解决煤炭作为今后能源的主要途径,但目前从经济角度看,还不能与天然气及石油竞争。
燃烧中脱硫主要方式是循环流化床锅炉,循环流化床锅炉是近年来在国际上发展起来的新一代高效、低污染清洁燃烧技术,具有投资省、燃料适应性广等优点,是一种正在高速发展,并正在迅速得到商业推广的方法。
但循环流化床燃烧技术在锅炉容量上受到限制,主要用于135MW以下机组。
燃烧后脱硫即烟气脱硫,是目前唯一大规模商业应用的脱硫方式,烟气脱硫技术很多,主要有石灰石/石膏湿法、旋转喷雾干燥法、炉内喷钙加尾部烟道增湿活化烟气脱硫工艺(芬兰Tempell和IVO 公司的LIFAC)、海水烟气脱硫工艺、电子束照射加喷氨烟气脱硫工艺、气体悬浮吸收脱硫技术FLS—GSA)、ABB新型一体化烟气脱硫工艺(NID)、德国WULFF公司回流式烟气循环流化床(RCFB—FGD)脱硫技术等。
2.2 湿法脱硫工艺湿式石灰石/石膏法脱硫工业化装置已有四十余年的历史,经过多年不断改进发展与完善,目前已成为世界上技术最为成熟、应用最为广泛的脱硫工艺,在脱硫市场特别是大容量机组脱硫上占主导地位,约占电厂装机容量的85%。
应用的单机容量已达1000MW。
1 湿法脱硫工艺特点优点:1)·技术成熟、可靠,国外应用广泛,国内也有运行经验。
2)·脱硫效率高>=95%。
3)·适用于大容量机组。
4)·吸收剂价廉易得。
5)·系统运行稳定、煤种和机组负荷变化适应性广。
6)·脱硫副产品石膏可以综合利用。
缺点:1)·系统复杂、运行维护工作量大。
湿法烟气脱硫脱硝技术特点详解

湿法烟气脱硫脱硝技术特点详解湿法烟气脱硫脱硝技术包括:磷铵肥法(PAFP)烟气脱硫技术、活性炭纤维法(ACFP)烟气脱硫技术、电子束氨法烟气脱硫脱硝技术等技术。
湿法烟气脱硝技术原理:湿法烟气脱硝技术的原理是通过液相络合剂把烟气中的NO络合,从而增加了NO在汲取液中的溶解度,利用烟气中的氧气再把络合下来的NO氧化成易溶于水的NO2,与碱性汲取剂(如氨、氧化镁等)反应生成硝酸盐,通过回收形成硝酸盐产品。
与氧化镁脱硫技术结合,形成氧化镁法同时脱硫脱硝技术,在一个塔内完成脱硫、脱硝任务,形成硫酸镁与硝酸镁的混合镁肥。
或者通过结晶技术分别为硫酸镁产品和硝酸镁产品。
特点:1)变废为宝,实现"循环经济' ;2)脱硝效率高,90%以上;3)烟温范围宽,适合各种规模的电站及工业锅炉;4)投资低、运行费用低。
本方案的技术特点为:1、脱硝效率高资源化的湿法脱硝设备脱硝效率高,能达到80%~90%以上,实现NOx达标排放100mg/m3(SNCR技术只达25%~38%,SCR技术只有40%~60%)。
2、运行费用低本脱硝装置投资与原有SCR的设备投入相当,而运行成本比传统SCR、SNCR脱硝方法运行费用要降低50%~80%(SCR运行费用每年需支出600万元,而采纳本技术每年增收达60~120万元)。
3、经济效益高本设备以碱性物质为原料脱除烟气中的NOx并综合汲取变废为宝,经加工产出硝酸盐、硝酸钠、硝酸钙、硝*铵、硝酸钾等复合肥,实现循环经济,使企业在脱硫脱硝工程中效益*大化(75t/h*2台煤炉每年能回收9000t复合肥)。
4、设备改造少该系统化适用于新老热电厂,在尾气末端部安装,不影响原设备的使用,且占地面积小,烟温范围60℃~400℃都能使用。
湿法脱硫流程
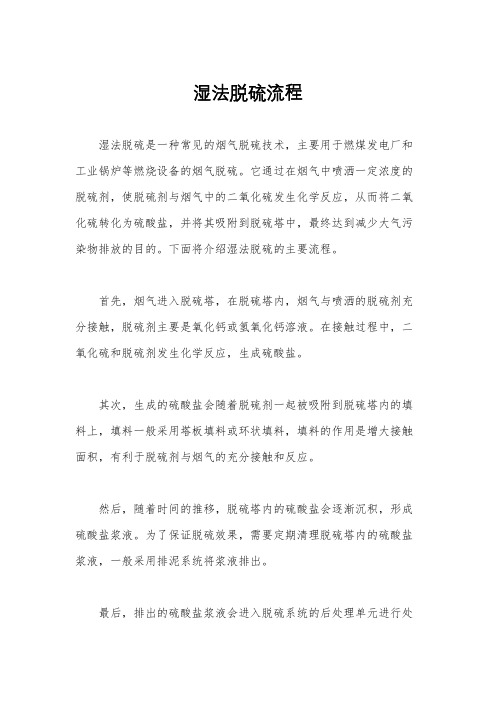
湿法脱硫流程湿法脱硫是一种常见的烟气脱硫技术,主要用于燃煤发电厂和工业锅炉等燃烧设备的烟气脱硫。
它通过在烟气中喷洒一定浓度的脱硫剂,使脱硫剂与烟气中的二氧化硫发生化学反应,从而将二氧化硫转化为硫酸盐,并将其吸附到脱硫塔中,最终达到减少大气污染物排放的目的。
下面将介绍湿法脱硫的主要流程。
首先,烟气进入脱硫塔,在脱硫塔内,烟气与喷洒的脱硫剂充分接触,脱硫剂主要是氧化钙或氢氧化钙溶液。
在接触过程中,二氧化硫和脱硫剂发生化学反应,生成硫酸盐。
其次,生成的硫酸盐会随着脱硫剂一起被吸附到脱硫塔内的填料上,填料一般采用塔板填料或环状填料,填料的作用是增大接触面积,有利于脱硫剂与烟气的充分接触和反应。
然后,随着时间的推移,脱硫塔内的硫酸盐会逐渐沉积,形成硫酸盐浆液。
为了保证脱硫效果,需要定期清理脱硫塔内的硫酸盐浆液,一般采用排泥系统将浆液排出。
最后,排出的硫酸盐浆液会进入脱硫系统的后处理单元进行处理,通常采用浓缩、结晶和干燥等工艺,将硫酸盐浆液转化为干粉状的硫酸盐产品,以便于运输和处置。
总的来说,湿法脱硫流程主要包括烟气脱硫塔、脱硫剂喷洒系统、填料层、排泥系统和后处理单元等部分。
通过这些部分的协同作用,能够有效地将烟气中的二氧化硫转化为无害的硫酸盐,达到减少大气污染物排放的目的。
在实际应用中,湿法脱硫技术具有脱硫效率高、适用范围广、操作维护方便等优点,因此得到了广泛的应用。
然而,也需要注意的是,湿法脱硫过程中会产生大量废水和废渣,需要合理处理,以免对环境造成二次污染。
综上所述,湿法脱硫是一种成熟、高效的烟气脱硫技术,通过合理的工艺设计和操作管理,能够有效地减少燃煤发电厂和工业锅炉等设备的大气污染物排放,对环境保护具有重要意义。
- 1、下载文档前请自行甄别文档内容的完整性,平台不提供额外的编辑、内容补充、找答案等附加服务。
- 2、"仅部分预览"的文档,不可在线预览部分如存在完整性等问题,可反馈申请退款(可完整预览的文档不适用该条件!)。
- 3、如文档侵犯您的权益,请联系客服反馈,我们会尽快为您处理(人工客服工作时间:9:00-18:30)。
2湿法脱硫技术介绍2.1脱硫方法简介目前,世界范围内的火电厂脱硫技术多种多样,达数百种之多。
按脱硫工艺在燃烧过程中所处位臵不同可分为:燃烧前脱硫、燃烧中脱硫、燃烧后脱硫。
燃烧前脱硫主要是洗煤、煤的气化和液化,洗煤仅能脱去煤中很少一部分硫,只可作为脱硫的一种辅助手段,煤气化和液化脱硫效果好,是解决煤炭作为今后能源的主要途径,但目前从经济角度看,还不能与天然气及石油竞争。
燃烧中脱硫主要方式是循环流化床锅炉,循环流化床锅炉是近年来在国际上发展起来的新一代高效、低污染清洁燃烧技术,具有投资省、燃料适应性广等优点,是一种正在高速发展,并正在迅速得到商业推广的方法。
但循环流化床燃烧技术在锅炉容量上受到限制,主要用于135MV以下机组。
燃烧后脱硫即烟气脱硫,是目前唯一大规模商业应用的脱硫方式,烟气脱硫技术很多,主要有石灰石/石膏湿法、旋转喷雾干燥法、炉内喷钙加尾部烟道增湿活化烟气脱硫工艺(芬兰Tempell和IVO公司的LIFAC)、海水烟气脱硫工艺、电子束照射加喷氨烟气脱硫工艺、气体悬浮吸收脱硫技术FLS- GSA、ABB新型一体化烟气脱硫工艺(NID)、德国WULF公司回流式烟气循环流化床(RCF—FGD脱硫技术等。
2.2湿法脱硫工艺湿式石灰石/石膏法脱硫工业化装臵已有四十余年的历史,经过多年不断改进发展与完善,目前已成为世界上技术最为成熟、应用最为广泛的脱硫工艺,在脱硫市场特别是大容量机组脱硫上占主导地位,约占电厂装机容量的85%。
应用的单机容量已达1000MW 1湿法脱硫工艺特点优点:1)〃技术成熟、可靠,国外应用广泛,国内也有运行经验。
2)〃脱硫效率咼>=95%。
3)〃适用于大容量机组。
4)〃吸收剂价廉易得。
5)〃系统运行稳定、煤种和机组负荷变化适应性广。
6)〃脱硫副产品石膏可以综合利用。
缺点:1)〃系统复杂、运行维护工作量大。
2)〃水消耗较大,存在废水处理问题。
3)〃系统投资较大、运行维护费用高、装臵占地面积也相对较大。
2反应原理该工艺的主要反应是在吸收塔中进行的,送入吸收塔的吸收剂一石灰石(石灰)浆液与经烟气再热器冷却后进入吸收塔的烟气接触混合,烟气中的二氧化硫(S02)与吸收剂浆液中的碳酸钙(CaC03以及鼓入的空气中的氧气(O2)发生化学反应,生成二水硫酸钙(CaSO42H2O) 即石膏;脱硫后的烟气依次经过除雾器除去雾滴、烟气再热器加热升温后,经烟囱排入大气。
该工艺的化学反应原理如下:吸收:SO2+H2O = H2SO3 = H+ HSO^氧化:H+ +HS& + 1/20 2 = 2H2O + SO2-结晶:CaCO+ 2H += Ca2++ H 20 + CQ+ SQ2-+ 2H2O = CaSQ 2HOpH值的控制对反应很重要,较高的pH值有利于吸收反应的发生,而较低的pH值有利于氧化和结晶反应的进行。
3湿法脱硫工艺系统简介一套完整的湿法脱硫工艺系统通常包括:SQ2吸收氧化系统即吸收塔系统、烟气系统、吸收剂制备系统、石膏脱水系统、废水处理系统。
各系统关系如下:在整个脱硫系统中,吸收塔系统是核心,SQ2的脱除,中间产物的氧化,以及副产物石膏浆的结晶全部在吸收塔中完成,其它系统则是为吸收塔系统提供服务,而且根据要求不同,其它系统或可以简化,或可以取消,如果取消石膏脱水系统,则变为石膏抛弃法,这时废水处理系统也相应取消,烟气系统的简化主要在于烟气再热器的取舍,而吸收剂制备系统的简化则是取消石灰石磨制设备(球磨机),直接购买石灰石粉进行配制浆液。
3湿法脱硫工艺系统示例下面以2X 300MV机组为例来介绍石灰石/石膏法脱硫装臵系统。
吸收塔采用喷淋塔。
石灰石-右膏湿法烟气脱硫工艺流程图烟气脱硫(FGD系统分为以下几个系统:吸收塔系统、烟气系统、石灰石输送系统、石灰石浆液制备系统、石膏脱水系统、FGD1助设备系统1吸收塔系统吸收塔系统每炉一套。
米用的工艺是就地强制氧化湿法石灰石一石膏脱硫工艺。
在吸收塔内,浆液中的碳酸钙与从烟气中捕获的二氧化硫发生化学反应,生成亚硫酸钙。
脱硫并除尘后的净烟气经除雾器除去气流中夹带的雾滴及灰尘颗粒。
向吸收塔内(在吸收塔的下半部,这部分所起到的是吸收塔反应塔的作用)收集的浆液中喷射空气,将亚硫酸钙就地氧化为硫酸钙(石膏)。
为保持固体颗粒的悬浮,配有足够数量的搅拌器石膏浆液排至石膏脱水系统。
配有真空皮带过滤机,以使石膏的 品质满足工业应用的要求。
真空皮带过滤机中滤出的滤液经收集后在 FGD 系统中循环使用。
一部分滤液被送至 FGD 废水处理系统,作为从 FGD 系统清除氯化物的排放水。
吸收塔除雾器 系统组成:烟%系姣.二厦址it 啜收观统 瞰吹割制蛰 采皱;石青处理慕俛 供水与廈水廉擁.电丸 碣控制廉躱I温诜熠輒脱就系统的疫心蘿瓏收曙,主要曲 喷淋理.除霉也,護酒池.捷特廉址矍单的瞰收塔设计塔.无内 部填料”舉面平滑;號代的瞅收塔isna^. 内部聂常訓代.浆池容帆无足]化 学性偿墮定;能軽可银据负障调整| 性离髙秦■利用军;运行樂护■小*週法亀确技术是世界上蛊用議歩*量为徵關 的拽术迪应雄竊寒一井有盟大啊庚障低工用 適聊的可能性.發15应■点議廉澀法脱薙桂2吸收塔结构特点吸收塔每炉一塔。
FGD 系统所采用的吸收塔是带就地强制氧化的 极为简单的喷淋塔。
吸收塔的设计确保达到最佳的设计参数, 这些设 计参数如pH 值、L/G 、Ca/S 、氧化空气流量、悬浮物含量等。
喷淋组 件之间的距离是根据所喷液滴的有效喷射轨迹及滞留时间而确定的, 液滴在此处与烟气接触,SO 通过液滴的表面被吸吸收塔喷淋层破石殆欝石膏湿法烟刘備工觊收塔内制黠圈收。
进气口连接喷嘴的底部配臵是精心设计的,以保持朝向吸收塔有足够的向下倾斜坡度,进口配有一个进口档板以阻止喷淋的液滴进入烟气进口的连接烟道。
吸收塔内的氯化物浓度不超过20,000 ppm。
吸收塔内基本构件的材质为含钼百分之六的优质不锈钢。
这一系统在吸收系统的各种工况下具有极佳的防腐及防蚀性能。
吸收塔进口的干一湿区采用ASTMUNSN102或等同材质。
吸收塔反应塔尺寸的确定能提供足够的停留时间完成亚硫酸钙向硫酸钙的氧化、石膏结晶及液体的脱硫。
在这些因素中,最关键的是液体脱硫时间的要求。
3吸收塔再循环系统吸收塔再循环系统包括泵、管道系统、喷淋组件及喷嘴,在浆液及所需净化的烟气之间提供密切的接触。
这一系统的设计要求是有足够和必要的液/气比(L/G)以可靠地实现所要求的SO2脱除性能且在吸收塔的内表面不产生结垢。
每层喷淋组件都配有一台与喷淋组件上升管道系统相连接的吸收塔再循环泵。
该系统包括管道布臵,是经过精心设计的以避免浆液累积及/或腐蚀问题。
因为能根据每台锅炉负荷选择最适合/经济的泵运行模式,该再循环泵系统能大大节省电耗。
喷淋组件及喷嘴的布臵设计成均匀覆盖吸收塔的横截面。
一个喷淋组件是由带每个喷淋嘴连接支管的母管组成的。
喷淋嘴的布臵设计成有足够的重叠以确保吸收塔横截面的完全覆盖。
使用由碳化硅制成的喷淋嘴取得极佳的长期无腐蚀、无磨蚀、无石膏结垢及堵塞等问题。
这样就要求再循环泵系统具有与装臵寿命相等同的使用寿命且无磨损问题。
4除雾器每台吸收塔设两级除雾器,位于吸收塔顶部最后一个喷淋组件的下游。
配有除雾器清洗管道系统及与除雾器相关的喷淋嘴。
5氧化空气系统氧化空气系统每塔一套,氧化空气被注入由吸收塔搅拌器所产生的被搅拌液流上。
注入的空气裂为细小的气泡并在液体中充分散开。
6湿法脱硫系统的主要特点1)吸收剂:石灰石或石灰,价廉。
2)反应产物:石膏(二水硫酸钙),可作建材使用。
3)石膏品质:90%左右纯度。
4)脱硫效率:高,可达95%以上。
5)对煤种适用性:无限制,可用于高中低含硫煤种6)机组适用性:无限制,尤其适用大机组。
7)利用率:大于95%8)电耗:1.2-1.6%。
9)钙硫比Ca/S: < 1.03。
1.0510)水耗及废水量:与烟气与工艺水等参数有关。
11)占地面积:取决于现场条件。
12)市场占有率:国内市场>80%国际市场>85% 7烟气系统1)烟气系统每塔一套。
来自锅炉的烟气在布袋除尘器后由两(2)台引风机(IDF)引出。
在正常运行时,旁路挡板门应关闭。
每个旁路挡板门配密封风机。
2)被吸入的烟气进入吸收塔中,除去烟气中的二氧化硫、飞灰及其他污染物。
从吸收塔流出的经处理的烟气经烟囱排放到大气中。
3)在故障情况下,开启烟气旁路挡板门,烟气通过旁路绕过FGD 系统直接排到烟囱。
8石灰石输送系统1)石灰石输送系统两炉共用一套.2)石灰石由卡车(30吨/辆)运到电厂,直接倒入卸料斗。
卸料斗全厂共用一个,容积90吨。
3)配臵一套完整的卸料和转移输送机,将石灰石从卸料斗输送到石灰石贮仓。
输送装臵上配有用于分离大块石灰石、杂物和金属的分离器。
石灰石贮仓全厂共用一个,包括配有闸板门、仓顶除尘器,除尘器的压差控制和吹扫程序等。
9石灰石浆液制备系统石灰石浆液制备系统两塔共用一套,1个石灰石浆液箱(池)、3台石灰石浆液给料泵(2运1备)。
由星型给料装臵按需求量把石灰石粉从石灰石储仓送至浆液箱。
FGD工艺水或滤液将按与送入石灰石粉成定比的量加入浆液箱搅拌。
石灰石浆液由石灰石浆液泵从石灰石浆液箱泵入两(2)台吸收塔。
10石膏脱水系统1)石膏脱水系统两塔共用一套,包括旋流器(包括石膏水力旋流器2套、废水水力旋流器3套)、滤液池、滤液水泵、石膏脱水系统内工艺泵、2台真空皮带脱水机(每台真空皮带脱水机出力为2台锅炉BMC工况产生石膏量的75%)及其辅助设备。
2)石膏浆液由每台石膏排出泵输送至初级脱水系统。
第一级脱水系统包括石膏水力旋流站和废水旋流站。
石膏水力旋流器溢流至废水旋流站,底流将通往第二级脱水系统。
第二级脱水系统包括两(2)台真空带式过滤器,位于第一级水力旋流站的下方。
脱水后,石膏饼将由输送装臵送至石膏贮仓。
从真空带式过滤器滤出的滤液将流至滤液箱,回到FGD系统中使用。
滤液由滤液泵抽吸至吸收塔反应塔或石灰石浆液制备系统再次使用。
废水旋流器的溢流将流至沉灰池内。
废水旋流器的底流回到吸收塔或滤液箱。
2.4 FGD辅助设备系统1FGD补给水系统FGD补给水系统由电厂工业水系统供应。
泵的出力大小将考虑一套石灰石浆液制备系统及石膏脱水系统的连续的FGD补给水用水量、间断的FGD补给水用水量及FGD补给水用水量的增量。
用于FGD补给水的所有水泵都位于工艺水箱附近。
3压缩空气系统6工业水系统4.1常用湿法脱硫技术流派介绍1湿法脱硫技术分类尽管世界上的湿法脱硫技术多种多样,但是原理上都是大同小异,差别主要体现在吸收塔各有特点,而其它系统如烟气系统、吸收剂制备系统、石膏脱水系统、废水处理系统几乎没有差别。
湿法脱硫技术可以按吸收塔的不同进行分类的,大致可分为以下几类:单回路喷淋塔、双回路喷淋塔、比晓夫吸收塔、液注塔、鼓泡塔、填料塔等。