60t电炉降低渣中氧化铁的工艺实践
60t电炉降低渣中氧化铁的工艺实践
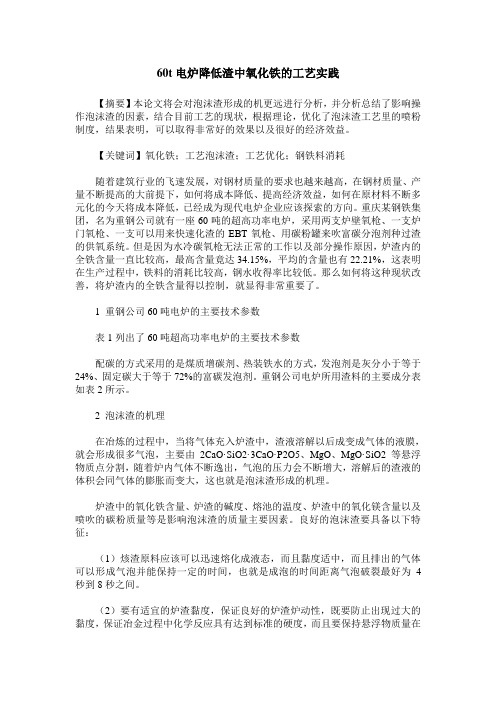
60t电炉降低渣中氧化铁的工艺实践【摘要】本论文将会对泡沫渣形成的机更远进行分析,并分析总结了影响操作泡沫渣的因素,结合目前工艺的现状,根据理论,优化了泡沫渣工艺里的喷粉制度,结果表明,可以取得非常好的效果以及很好的经济效益。
【关键词】氧化铁;工艺泡沫渣;工艺优化;钢铁料消耗随着建筑行业的飞速发展,对钢材质量的要求也越来越高,在钢材质量、产量不断提高的大前提下,如何将成本降低、提高经济效益,如何在原材料不断多元化的今天将成本降低,已经成为现代电炉企业应该探索的方向。
重庆某钢铁集团,名为重钢公司就有一座60吨的超高功率电炉,采用两支炉壁氧枪、一支炉门氧枪、一支可以用来快速化渣的EBT氧枪、用碳粉罐来吹富碳分泡剂种过渣的供氧系统。
但是因为水冷碳氧枪无法正常的工作以及部分操作原因,炉渣内的全铁含量一直比较高,最高含量竟达34.15%,平均的含量也有22.21%,这表明在生产过程中,铁料的消耗比较高,钢水收得率比较低。
那么如何将这种现状改善,将炉渣内的全铁含量得以控制,就显得非常重要了。
1 重钢公司60吨电炉的主要技术参数表1列出了60吨超高功率电炉的主要技术参数配碳的方式采用的是煤质增碳剂、热装铁水的方式,发泡剂是灰分小于等于24%、固定碳大于等于72%的富碳发泡剂。
重钢公司电炉所用渣料的主要成分表如表2所示。
2 泡沫渣的机理在冶炼的过程中,当将气体充入炉渣中,渣液溶解以后成变成气体的液膜,就会形成很多气泡,主要由2CaO·SiO2·3CaO·P2O5、MgO、MgO·SiO2等悬浮物质点分割,随着炉内气体不断逸出,气泡的压力会不断增大,溶解后的渣液的体积会同气体的膨胀而变大,这也就是泡沫渣形成的机理。
炉渣中的氧化铁含量、炉渣的碱度、熔池的温度、炉渣中的氧化镁含量以及喷吹的碳粉质量等是影响泡沫渣的质量主要因素。
良好的泡沫渣要具备以下特征:(1)烗渣原料应该可以迅速熔化成液态,而且黏度适中,而且排出的气体可以形成气泡并能保持一定的时间,也就是成泡的时间距离气泡破裂最好为4秒到8秒之间。
电弧炉冶炼电石渣脱氧操作工艺讲解

电弧炉冶炼电石渣脱氧操作工艺讲解第一步,装料。
将电石渣按照一定的配比加入到电弧炉中。
电石渣通常由硅酸盐和氧化铁组成,硅酸盐的主要成分是二氧化硅(SiO2),氧化铁的主要成分是三氧化二铁(Fe3O2)。
在装料过程中,需要严格控制电石渣的配比,以确保最终得到的电石渣可以充分脱氧。
第二步,冶炼。
通过电弧炉加热电石渣,将其熔化成液态。
电弧炉是一种利用电弧高温加热的设备,其特点是加热快、温度高、控制精度高。
冶炼过程中,需要控制电弧炉的加热温度和保持恒定的保温时间,以确保电石渣完全熔融。
第三步,脱氧。
在熔融的电石渣中添加还原剂,如焦炭、焦粉等。
脱氧的目的是将电石渣中的氧化物还原成金属,并将氧气捕捉在脱氧剂中形成氧化物。
脱氧反应可以通过以下方程式表示:
Fe3O2+4C=3Fe+4CO
SiO2+2C=Si+2CO
在脱氧过程中,需要控制还原剂的加入量和加入时机,以确保足够的还原剂与氧化物反应,并保持良好的混合。
同时,还需要控制脱氧反应的时间和温度,以确保反应充分进行。
总结:电弧炉冶炼电石渣脱氧是一种重要的冶金工艺,用于提高熔融金属的纯度。
操作工艺主要包括装料、冶炼和脱氧三个步骤。
通过严格控制电石渣的配比、加热温度和保温时间,以及控制还原剂的加入量、时机和反应时间,可以实现电石渣的充分脱氧,提高熔融金属的质量。
电弧炉冶炼白渣脱氧操作工艺讲解
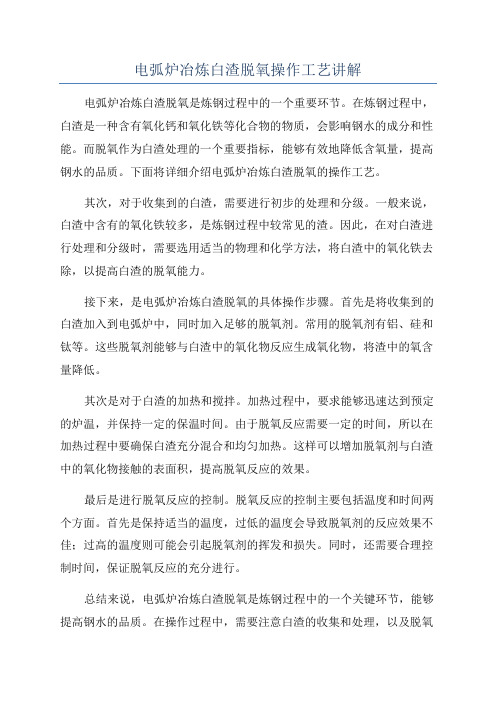
电弧炉冶炼白渣脱氧操作工艺讲解电弧炉冶炼白渣脱氧是炼钢过程中的一个重要环节。
在炼钢过程中,白渣是一种含有氧化钙和氧化铁等化合物的物质,会影响钢水的成分和性能。
而脱氧作为白渣处理的一个重要指标,能够有效地降低含氧量,提高钢水的品质。
下面将详细介绍电弧炉冶炼白渣脱氧的操作工艺。
其次,对于收集到的白渣,需要进行初步的处理和分级。
一般来说,白渣中含有的氧化铁较多,是炼钢过程中较常见的渣。
因此,在对白渣进行处理和分级时,需要选用适当的物理和化学方法,将白渣中的氧化铁去除,以提高白渣的脱氧能力。
接下来,是电弧炉冶炼白渣脱氧的具体操作步骤。
首先是将收集到的白渣加入到电弧炉中,同时加入足够的脱氧剂。
常用的脱氧剂有铝、硅和钛等。
这些脱氧剂能够与白渣中的氧化物反应生成氧化物,将渣中的氧含量降低。
其次是对于白渣的加热和搅拌。
加热过程中,要求能够迅速达到预定的炉温,并保持一定的保温时间。
由于脱氧反应需要一定的时间,所以在加热过程中要确保白渣充分混合和均匀加热。
这样可以增加脱氧剂与白渣中的氧化物接触的表面积,提高脱氧反应的效果。
最后是进行脱氧反应的控制。
脱氧反应的控制主要包括温度和时间两个方面。
首先是保持适当的温度,过低的温度会导致脱氧剂的反应效果不佳;过高的温度则可能会引起脱氧剂的挥发和损失。
同时,还需要合理控制时间,保证脱氧反应的充分进行。
总结来说,电弧炉冶炼白渣脱氧是炼钢过程中的一个关键环节,能够提高钢水的品质。
在操作过程中,需要注意白渣的收集和处理,以及脱氧剂的选择和加入。
同时要控制加热和搅拌的条件,以及脱氧反应的温度和时间。
通过合理的操作,可以有效地实现白渣的脱氧,提高钢水的质量。
电炉普通铁合金生产中废渣的深度处理技术研究
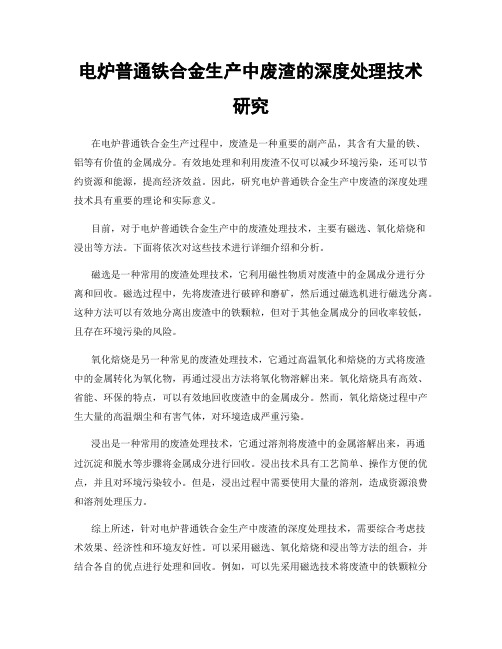
电炉普通铁合金生产中废渣的深度处理技术研究在电炉普通铁合金生产过程中,废渣是一种重要的副产品,其含有大量的铁、铝等有价值的金属成分。
有效地处理和利用废渣不仅可以减少环境污染,还可以节约资源和能源,提高经济效益。
因此,研究电炉普通铁合金生产中废渣的深度处理技术具有重要的理论和实际意义。
目前,对于电炉普通铁合金生产中的废渣处理技术,主要有磁选、氧化焙烧和浸出等方法。
下面将依次对这些技术进行详细介绍和分析。
磁选是一种常用的废渣处理技术,它利用磁性物质对废渣中的金属成分进行分离和回收。
磁选过程中,先将废渣进行破碎和磨矿,然后通过磁选机进行磁选分离。
这种方法可以有效地分离出废渣中的铁颗粒,但对于其他金属成分的回收率较低,且存在环境污染的风险。
氧化焙烧是另一种常见的废渣处理技术,它通过高温氧化和焙烧的方式将废渣中的金属转化为氧化物,再通过浸出方法将氧化物溶解出来。
氧化焙烧具有高效、省能、环保的特点,可以有效地回收废渣中的金属成分。
然而,氧化焙烧过程中产生大量的高温烟尘和有害气体,对环境造成严重污染。
浸出是一种常用的废渣处理技术,它通过溶剂将废渣中的金属溶解出来,再通过沉淀和脱水等步骤将金属成分进行回收。
浸出技术具有工艺简单、操作方便的优点,并且对环境污染较小。
但是,浸出过程中需要使用大量的溶剂,造成资源浪费和溶剂处理压力。
综上所述,针对电炉普通铁合金生产中废渣的深度处理技术,需要综合考虑技术效果、经济性和环境友好性。
可以采用磁选、氧化焙烧和浸出等方法的组合,并结合各自的优点进行处理和回收。
例如,可以先采用磁选技术将废渣中的铁颗粒分离出来,再使用氧化焙烧技术将金属转化为氧化物,最后通过浸出技术将氧化物溶解出来进行回收。
此外,还可以继续研究开发新的废渣处理技术,以提高废渣的处理效果和金属回收率。
例如,可以尝试利用生物技术或化学还原等方法将废渣中的金属成分溶解出来,或者开发新型的萃取剂和溶剂体系,实现高效、经济、环保的废渣处理和回收。
60t电炉降低渣中氧化铁的工艺实践
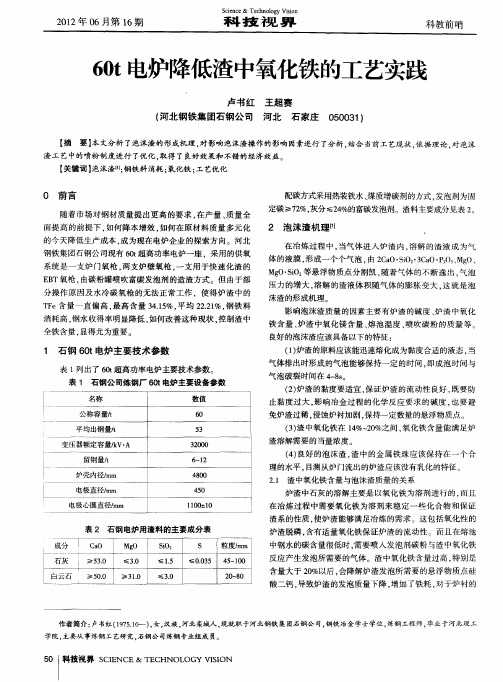
名称 公称容量/ t
平 均 出 钢 量/ t
气体排 出时形成 的气泡能够保持一定 的时 间 , 即成泡时 间与
气泡 破 裂 时 间 在 4 8 s
() 2 炉渣的黏度要适宜 , 保证炉渣 的流动性 良好 , 既要 防 止黏度过 大 , 响冶金过程 的化学 反应要求 的碱度 , 影 也要避 免炉渣过稀 , 侵蚀炉衬加剧 , 保持一定数量 的悬浮物质点。 ( ) 中氧化铁在 1%~ 0 3渣 4 2 %之间 , 氧化铁含量能满足 炉
2012年06月第16期sciencetechnologyvision科技视界科教前哨60t电炉降低渣中氧化铁的工艺实践卢书红河北钢铁集团石钢公司王超赛河北石家庄050031摘要l本文分析了泡沫渣的形成机理对影响泡沫渣操作的影响因素进行了分析结合当前工艺现状依据理论对泡沫渣工艺中的喷粉制度进行了优化
粒度/ mm
CO a
≥5 . 3 0 ≥5. 0 0
M
≤30 . ≥3 . 1 O
S02 i
≤1 . 5 ≤3O .
S
中钢水 的碳含量很低时 . 需要 喷入发泡剂碳粉与渣 中氧化铁
≤00 5 4 ~ 0 .3 5 l0 2—O 0 8
反应产生发泡所需要 的气体 。渣 中氧化铁含量过高 , 特别是 含量 大于 2 %以后 , 0 会降解炉渣发泡所需要 的悬浮物质点硅
E T氧枪 , B 由碳粉罐喷吹富碳发泡 剂的造渣 方式 。但 由于部
分操作 原 因及水 冷碳氧枪 的无 法正常工作 ,使得炉 渣 中的
M O・i: g SO 等悬浮物质点分 割凯 , 随着气体 的不断逸 出 , 气泡 压力的增大 , 溶解 的渣液 体积随气体 的膨胀变大 . 这就是泡
钢铁冶炼中炉渣中TiO2的去除方法
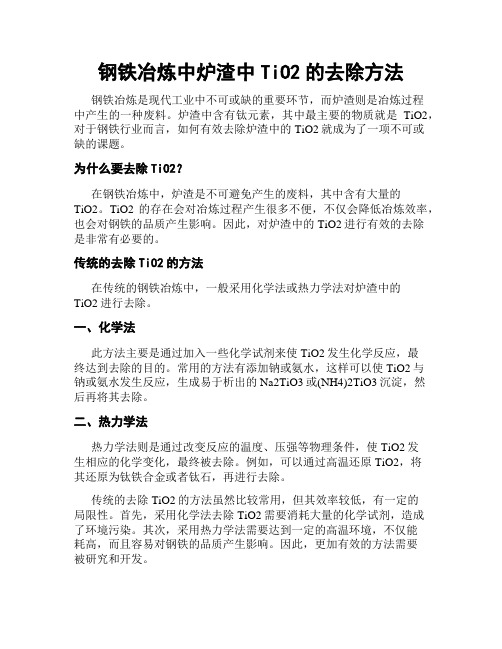
钢铁冶炼中炉渣中TiO2的去除方法钢铁冶炼是现代工业中不可或缺的重要环节,而炉渣则是冶炼过程中产生的一种废料。
炉渣中含有钛元素,其中最主要的物质就是TiO2,对于钢铁行业而言,如何有效去除炉渣中的TiO2就成为了一项不可或缺的课题。
为什么要去除TiO2?在钢铁冶炼中,炉渣是不可避免产生的废料,其中含有大量的TiO2。
TiO2的存在会对冶炼过程产生很多不便,不仅会降低冶炼效率,也会对钢铁的品质产生影响。
因此,对炉渣中的TiO2进行有效的去除是非常有必要的。
传统的去除TiO2的方法在传统的钢铁冶炼中,一般采用化学法或热力学法对炉渣中的TiO2进行去除。
一、化学法此方法主要是通过加入一些化学试剂来使TiO2发生化学反应,最终达到去除的目的。
常用的方法有添加钠或氨水,这样可以使TiO2与钠或氨水发生反应,生成易于析出的Na2TiO3或(NH4)2TiO3沉淀,然后再将其去除。
二、热力学法热力学法则是通过改变反应的温度、压强等物理条件,使TiO2发生相应的化学变化,最终被去除。
例如,可以通过高温还原TiO2,将其还原为钛铁合金或者钛石,再进行去除。
传统的去除TiO2的方法虽然比较常用,但其效率较低,有一定的局限性。
首先,采用化学法去除TiO2需要消耗大量的化学试剂,造成了环境污染。
其次,采用热力学法需要达到一定的高温环境,不仅能耗高,而且容易对钢铁的品质产生影响。
因此,更加有效的方法需要被研究和开发。
新兴的去除TiO2的方法随着科技的发展,钢铁冶炼中的工艺也得到不断的改进和创新,目前在去除炉渣中TiO2的方法也应运而生。
下面介绍一些新兴的方法。
一、氧化焙烧法氧化焙烧法是近年来比较流行的一种方法,其主要原理是通过氧化反应来使TiO2析出。
首先,将炉渣中的TiO2氧化成为TiO3,然后再通过TiO3与SiO2、CaO等材料发生反应,来生成钛酸盐类物质。
这种方法不仅去除效率高,而且对环境的污染也较少。
二、浸出法浸出法是一种比较简单的方法,其主要过程是将炉渣浸泡在一定的液体介质中,使其中的TiO2溶解到浸出液中。
氧化铁的粉碎工艺流程

氧化铁的粉碎工艺流程
氧化铁的粉碎工艺流程一般包括以下几个步骤:
1. 原料准备:选择合适的氧化铁原料,如铁矿石、废钢渣等,并进行破碎、磨矿等预处理。
2. 粉碎:原料经过预处理后,进入粉碎设备,如颚式破碎机、锤式破碎机等,进行粗碎和细碎,将颗粒尺寸减小到所需的粉碎度要求。
3. 筛分:将粉碎后的氧化铁料通过筛分设备,如振动筛、离心筛等,根据粒径大小分离出不同粒度的氧化铁粉末。
4. 磨细:对于需要更细碎的氧化铁颗粒,可以使用磨细设备,如球磨机、细磨机等,进一步提高粉末的细度。
5. 分级:通过气流分级设备,如气流分级机、离心分级机等,将粉碎后的氧化铁粉末按照粒径大小进行分级,得到所需的粉末粒度。
6. 包装和贮存:将粉碎好的氧化铁粉末进行包装,并存放在干燥、通风的仓库中,以防止潮湿和氧化。
需要注意的是,氧化铁的粉碎工艺流程可能会根据具体的生产要求和设备的不同
而有所差异。
以上只是一个基本的参考流程。
合理造好泡沫渣降低冶炼电耗先进操作法
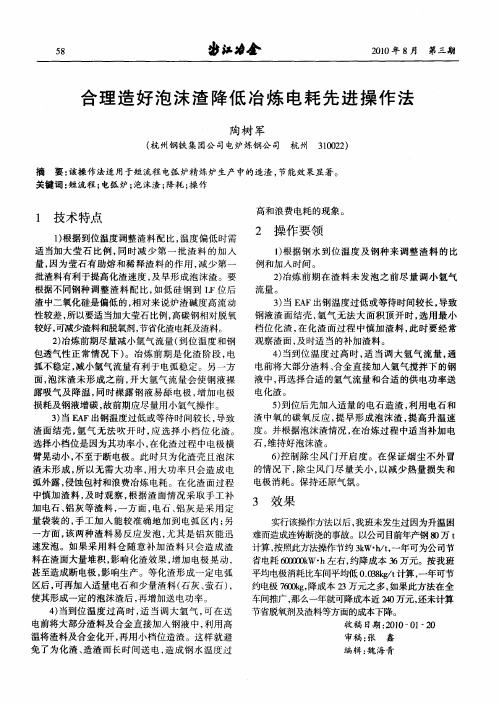
温将渣料及合金化开, 再用小档位造渣。这样就避
免 了为 化 渣 、 渣 而 长时 间送 电 , 成钢 水 温 度过 造 造
审稿 : 张 鑫
编辑 : 海青 魏
5 N位 后先 加入适量 的电石 造 渣 , 用 电石 和 ) 利 渣 中氧 的碳 氧反 应 , 早 形成 泡 沫渣 , 高 升 温速 提 提 度 。并 根 据泡沫 渣情况 , 冶炼过 程 中适 当补加 电 在 石 , 持好 泡沫渣 。 维
6控 制 除尘 风 门开启 度 。在保 证 烟 尘 不外 冒 ) 的情 况下 , 除尘 风 门尽 量 关 小 , 以减 少 热量 损 失 和 电极消耗 。保持 还原气 氛 。
1 技术 特 点
1根据到位 温度调 整渣料 配 比, ) 温度 偏低 时需 适 当加大 莹 石 比例 , 时 减 少 第 一 批 渣 料 的加 人 同 量, 因为 莹石 有 助熔 和 稀 释渣 料 的作 用 , 少第 一 减 批渣料 有利于 提高化渣 速度 , 及早 形成 泡 沫渣 。要 根据 不 同钢 种 调整 渣 料 配 比, 如低 硅 钢 到 L F位 后 渣 中二 氧化 硅是偏低 的 , 相对来 说炉 渣 碱度 高流 动 性较 差 , 以要适 当加大莹 石 比例 , 所 高碳钢相对 脱氧 较好 , 可减少渣料和脱氧剂 , 节省化渣电耗及渣料 。 2 冶炼 前期尽 量减小 氩 气流量 ( ) 到位 温度 和钢 包透气性 正 常 情 况下 ) 。冶炼 前 期 是 化渣 阶段 , 电 弧不稳定 , 减小氩 气 流量有利 于电弧稳 定 。另一 方 面 , 沫渣 未 形成 之 前 , 大氩 气 流量 会 使钢 液 裸 泡 开 露 吸气 及 降温 , 同时 裸露 钢 液 易舔 电极 , 加 电极 增 损 耗及钢液 增碳 , 前期应 尽量用小 氩气操 作 。 故 3 当 E F出钢温度 过低或 等待 时间较长 , ) A 导致 渣 面结 壳 , 气 无 法 吹开 时 , 选 择 小 档 位 化 渣 。 氩 应 选择小档 位是 因为其 功率小 , 在化 渣过 程 中 电极 横 臂 晃动小 , 不至 于断 电极 。此 时只 为化 渣壳且 泡 沫 渣 未形 成 , 以无 需 大 功率 , 大 功率 只会 造 成 电 所 用 弧外 露 , 侵蚀 包衬 和浪费 冶炼 电耗 。在化 渣 面过 程 中慎加 渣料 , 时 观察 , 及 根据 渣 面情 况采 取 手 工 补 加 电石 、 灰 等渣 料 , 方 面 , 铝 一 电石 、 灰 是 采用 定 铝 量袋装 的 , 工 加入 能 较准 确 地 加到 电弧 区 内 ; 手 另 方 面 , 两 种 渣料 易 反应 发 泡 , 该 尤其 是 铝 灰能 迅 速发 泡 。如 果 采用 料 仓 随 意补 加 渣 料 只会 造 成 渣
利用碳粉降低终渣氧化铁技术的探讨

( 1 . 唐 山国丰钢铁 有限公 司,河北 唐山 0 6 3 3 0 0 ;2 . 唐 山科技职业技术学院 ,河北 唐 山 0 6 3 0 0 1 1) 【 摘 要】 采 用向渣 面加入碳 粉进行预脱 氧的技术 ,降低渣 中氧化铁 含量 ,有效地 降低 了终渣对 炉衬 的侵
蚀 ,有利 于溅渣护炉 ,可有效地 降低钢铁料 消耗 。
【 第一作者简介1张瑞松 ( 1 9 8 1 一 ),男,现在唐 山国丰钢铁有 限公司工作 ,助理工程师 。E - ma i 1 : Z h g r u i 。 #9 5 @1 6 3 . 。 m
3 项 目收 益 1 ) 经济效益。该工艺实施 后 ,有效 降低了钢铁料 、耐材
一
3 3 —
1 改善措 施
0. 0 7 O. O 8
0 . 09
,0. 09
6 ) 就 以上措 施对 现 场操 作人 员 进行 培训 ,保证 碳粉 降低终 渣w ( F e O) 技术 普及 和操作 的标准 化 。
2 项 目实 施 效 果
1 ) 提 高转 炉过 程 控 制 的稳 定性 ,为终 渣 碳粉 脱 氧提
60
5O 40 40 3O
30
强 的脱 氧 剂 碳 粉 ,使 其 与渣 中F e O 发 生反 应 ,大 幅度 降 低 渣 中W ( F e O)。钢 水 中的氧 会 向熔 渣 中扩 散 ,这 样在 出钢 脱 氧时能 降低 脱氧 剂和 合金 消耗 ,减 少钢 水 中夹杂物 的生 成 ,对提 高钢材 质 量至关 重要 。
3 ) 根据实际生产数据制定碳粉加入量 ( 参考见表1 ) 。
4 )自钢水 出至 总钢 水 量的4 / 5 时开 始可 以加 入碳 粉 ,
菜钢60tLF炉渣系工艺研究

】5 3 O . .
≤3 O
力不够强 , 不利于开发高端 H型钢产品。因此开展
渣系工艺研究 , 缩短成渣时间 , 合理分 配 L 不 同时 F 间段的精炼任务非常重要。本文主要介绍 了通过优
3 确定合理 的精炼渣 系
3 1 白泡 沫渣 的重 要性 .
化L F精炼渣 系 目标 , 制定二次快速造 白泡沫渣操 作标准 , 确定合理渣量等以提高精炼渣的综合冶金性 能, 充分吸附夹杂物 , 进一步净化钢水。
0 前言
炼钢厂 4 转炉_4 L - F炉_ 4连铸 机主要 配套 _ 中 型 H 型 钢 生 产 线 , 要 生 产 Q 4C Q 4D 主 35 、 35 、 Q 4E 35 L等一系列抗低温 冲击优质 H型钢。4 转炉 冶炼及 4连铸 机浇注周期较 短 ( 平均 2 i) L 5mn ,F 精炼时间紧迫 。生产中常因工序衔接紧张,F快速 L 造 白渣 困难 , 夹杂物上浮时间难以保证 , 质量控制能
沫渣埋弧操作可提高热效率, 减少耐火材料侵蚀。 3 2 合理 目标 渣 系选择 . 炉渣的精炼能力决定于炉渣的化学性质和物理 性质 , 为确保渣尽快形成, 具有 良好 的流动性 、 发泡 埋弧作用 、 脱硫及吸附夹杂物的能力 , 要综合考虑各 组分对造渣的影响。 1 炉渣硫容量 从脱硫角度考虑 , ) 可选择的精 炼渣 系主 要有 C O—C F 渣 系 、 a a a2 C O—C F 一A2 3 a2 10 渣系、 a A2 3 S 2 C O— I 一 i 渣系 , C O—CF 渣系 0 O 而 a a2 具有最高的脱硫能力 。单从脱硫角度考虑, a CF 含 量 4 %左右为最佳组成 , 0 此时硫 的分配 比约为 10 7 10 但含 c F 量越 高, 8, a2 钢包 耐材侵蚀速度越快。
炼钢车间2×60T转炉三次除尘技术方案

秦皇岛宏兴钢铁有限公司炼钢车间2×60T转炉三次除尘工程技术方案张家口市宣化天洁环保科技有限公司2016年5月1.序言秦皇岛宏兴钢铁有限公司技改炼钢车间三次除尘工程尘源点包括2×60t转炉两座加料跨配顶吸罩,600T混铁炉一座配顶吸罩,散装料上料系统一套配集中除尘。
我公司根据秦皇岛宏兴钢铁有限公司提供的资料,编制了本方案,其目的在于为该除尘提供成套的、优化的、建设性的解决方案,确保符合国家环保要求,达标排放的前提下降低投资及运行成本。
2.尘源点概述2.1需治理的扬尘点本方案治理的尘源点配套除尘罩范围如下:1)、2×60T转炉加料跨顶吸罩;2)、600T混铁炉兑铁口、出铁口工位除尘罩;3)、散装料地坑料仓卸料口除尘罩;4)、散装料皮带机机头、机尾除尘罩;5)、转运站皮带机头除尘罩、振动筛除尘罩;6)、通廊皮带机头、皮带机尾除尘罩;7)、高跨散装料仓皮带布料口除尘罩。
3.设计原则及依据3.1设计原则●达标排放,保证除尘效果;●不影响冶炼操作工艺;●最大限度地降低运行费用及一次投资;●利于维护管理,长期、有效、稳定地运行。
3.2 设计依据●国家有关环保要求及环境指标:(获县以上环保部门的验收)排放浓度≤15mg/Nm³岗位粉尘浓度≤10mg/Nm³(扣除背景值)三次除尘捕集率≥95%(屋顶不冒黄烟),混铁炉捕捉率≥60%除尘效率≥99%。
●国家有关设计规范4.除尘工艺流程及设计说明4.1除尘工艺流程本套系统采用低阻、大流量系统工艺原则,其目的在于以最低的系统阻力,控制系统管道流速(18~20m/s),通过选取管道经济流速,尽量降低系统阻力损失从而能明显降低长期电耗。
换言之,追求的是在相同电机的情况下,最大限度地取得处理风量,提高捕集率。
在相同风量满足捕集效果的前提下,尽可能少地消耗电能,降低运行费,并合理组织烟气,使系统长期、可靠、稳定地运行在既不烧滤袋又不易于结露的中温状态。
改进用氧制度,降低渣中的氧化铁

H i n j n Mea ug el gi g o a tl ry l
D c mb r 2 e e e 01 l
改进 用 氧 制 度 , 降低 渣 中 的 氧 化 铁
李恺 军
( 东北 特钢 集 团北满 特殊钢 有 限责任 公 司 ,黑龙江
摘
齐齐 哈尔 1 14 ) 6 0 1
1 初炼钢水渣 中氧化铁的变化 规律
1 1 二次料 、 . 三次 料及 加氧 化铁 皮试验
施, 使渣 中 W FO 平均降到 2 .% , (e ) 54 每炉减少纯
铁 氧化 损失 14 t .4。
二 次料 、 三次 料及 加氧 化铁皮 试验 , 见表 l 。
表 1 二 次 料 、 次 料 及 加 氧 化 铁 皮 对 渣 中氧 化 铁 质 量 分 数 的 影 响 三
nace .
Ke W o d : x g n s se ;F O c n e to lg y r s O y e y tm e o t n fsa ;De u f r t n s e d s l ai p e u o
ห้องสมุดไป่ตู้
我 们针 对 一炼 初 炼 炉 三 次 料 渣 中 W( e 平 FO) 均 高达 5 . % 的 问题 , 展 了“ 进用 氧制 度 , 39 开 改 降 低渣 中 伽( e ”的工 作 ”, 出 了具 体 的改 进 措 FO) 提
第一种操 作方法 : 熔化期 大氧量深 吹供氧 , 炉料熔 化 8 %开始 全程泡沫渣 , 0 熔化期 脱磷完
成, 氧化期至 出钢渣钢界面吹氧 , 以造泡沫渣为 主 , 全程大 量喷吹 ( 人l 或 丁加入 ) 粉 ( 碳 或煤
4 . 52 4 . 46 4 . 61 4. 试验 1 53
电炉普通铁合金生产中废渣氧化性的探究

电炉普通铁合金生产中废渣氧化性的探究在电炉普通铁合金生产过程中,废渣产生是不可避免的一个环节。
废渣主要由炉料中的杂质和非金属物质组成,其氧化性对炉料的质量和生产效率有着重要影响。
本文将对电炉普通铁合金生产中废渣的氧化性进行探究。
首先,我们需要了解电炉普通铁合金生产的基本流程。
该生产过程通常分为炉料准备、炉料加入电炉、冶炼和废渣处理四个步骤。
在炉料准备过程中,需要选择适当的炉料组成,以确保最终合金的质量。
在炉料加入电炉时,需要掌握合适的加料时间和速度,以提高炉料的均匀性。
冶炼过程是将炉料加热至高温,并与还原剂进行反应,使得金属熔化并析出。
废渣处理阶段则是对冶炼过程中产生的废渣进行处理和清除。
废渣的氧化性对整个生产过程有着重要的影响。
首先,废渣的氧化性会影响金属的熔化和析出速度。
氧化性较高的废渣会促使金属更快地熔化,提高炉料的反应速度。
另外,废渣的氧化性还与废渣的溶解能力和流动性有关。
氧化性较高的废渣一般具有较高的溶解能力和流动性,有利于废渣的排出和处理。
因此,在电炉普通铁合金生产中,合适的废渣氧化性对于提高生产效率和质量是至关重要的。
那么,在电炉普通铁合金生产中,我们如何探究废渣的氧化性呢?一种常用的方法是利用实验室实验。
在实验室中,可以通过调整炉料成分、温度和氧化剂添加量等参数,进行一系列的实验研究。
首先,可以选择不同配比的炉料,探究不同成分对废渣氧化性的影响。
例如,通过调整炉料中的硅含量,可以研究硅对废渣氧化性的影响。
实验中,可以将不同硅含量的炉料加入电炉中进行冶炼,然后分析废渣的组成和性质,从而得出不同硅含量对废渣氧化性的影响。
另外,可以通过控制温度的方法来研究废渣的氧化性。
温度是影响化学反应速率和程度的重要因素之一。
通过在不同温度下进行实验,可以研究温度对废渣的氧化性的影响。
例如,可以在一定时间内,分别将炉料加热至不同温度进行冶炼,然后分析废渣的氧化程度和成分,以了解温度对废渣氧化性的影响。
电炉普通铁合金冶炼中降渣气的利用技术研究

电炉普通铁合金冶炼中降渣气的利用技术研究摘要:随着工业发展和资源紧缺,降低能源消耗和实现有效利用已成为全球炼钢行业的重要课题之一。
本文以电炉普通铁合金冶炼过程中产生的降渣气为研究对象,探讨了其利用技术。
本文首先介绍了电炉普通铁合金冶炼的基本原理和工艺流程,然后重点阐述了降渣气的含量和组成分析。
接下来,本文综述了目前常用的降渣气利用技术,包括煤气化、热风炉和燃气轮机等。
最后,本文提出了未来的研究方向和发展趋势,希望为电炉普通铁合金冶炼中降渣气的利用提供参考。
1. 引言电炉普通铁合金冶炼是一种重要的钢铁冶炼方式,其具有产量大、工艺灵活等优点。
然而,在冶炼过程中会产生大量的降渣气,不仅浪费了能源资源,还对环境造成污染。
因此,降渣气的利用技术研究具有重要的理论和实践意义。
2. 电炉普通铁合金冶炼的基本原理和工艺流程电炉普通铁合金冶炼是利用电焦炉加热冶炼矿石的过程,通过高温熔化的电炉将矿石中的金属还原为合金。
其基本原理是利用电棒产生的电能使炉料加热到足够高的温度,以实现金属的还原。
电炉普通铁合金冶炼的工艺流程包括料仓装料、预热、熔炼、卸渣等环节。
在熔炼过程中,炉料中的杂质会和金属发生化学反应生成气体,形成降渣气。
3. 降渣气的含量和组成分析降渣气的含量和组成对于其利用技术的研究具有重要的意义。
通过对电炉普通铁合金冶炼过程中产生的降渣气进行采样和分析,可以获得其含量和组成信息。
降渣气的含量主要取决于炉料的成分和冶炼工艺的控制。
常见的降渣气组成包括一氧化碳(CO)、二氧化碳(CO2)、氢气(H2)、一氧化氮(NO)等。
这些气体的含量和比例会影响降渣气的利用效果和经济效益。
4. 降渣气的利用技术综述目前,常用的降渣气利用技术主要包括煤气化、热风炉和燃气轮机等。
煤气化是一种常见的降渣气利用技术,其通过将降渣气经过气化反应后得到合成气,进一步用于燃烧、发电或化学合成。
煤气化技术具有高效能源转化率和多产物利用的优点,但也存在设备复杂、气体净化难度大的问题。
电炉普通铁合金生产中废渣焙烧技术的优化
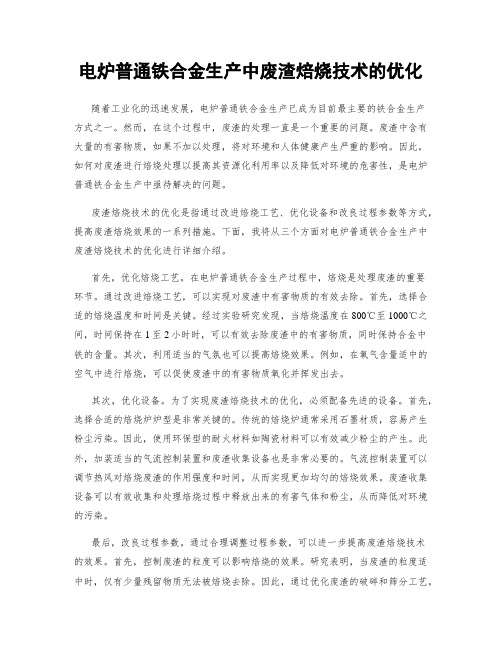
电炉普通铁合金生产中废渣焙烧技术的优化随着工业化的迅速发展,电炉普通铁合金生产已成为目前最主要的铁合金生产方式之一。
然而,在这个过程中,废渣的处理一直是一个重要的问题。
废渣中含有大量的有害物质,如果不加以处理,将对环境和人体健康产生严重的影响。
因此,如何对废渣进行焙烧处理以提高其资源化利用率以及降低对环境的危害性,是电炉普通铁合金生产中亟待解决的问题。
废渣焙烧技术的优化是指通过改进焙烧工艺、优化设备和改良过程参数等方式,提高废渣焙烧效果的一系列措施。
下面,我将从三个方面对电炉普通铁合金生产中废渣焙烧技术的优化进行详细介绍。
首先,优化焙烧工艺。
在电炉普通铁合金生产过程中,焙烧是处理废渣的重要环节。
通过改进焙烧工艺,可以实现对废渣中有害物质的有效去除。
首先,选择合适的焙烧温度和时间是关键。
经过实验研究发现,当焙烧温度在800℃至1000℃之间,时间保持在1至2小时时,可以有效去除废渣中的有害物质,同时保持合金中铁的含量。
其次,利用适当的气氛也可以提高焙烧效果。
例如,在氧气含量适中的空气中进行焙烧,可以促使废渣中的有害物质氧化并挥发出去。
其次,优化设备。
为了实现废渣焙烧技术的优化,必须配备先进的设备。
首先,选择合适的焙烧炉炉型是非常关键的。
传统的焙烧炉通常采用石墨材质,容易产生粉尘污染。
因此,使用环保型的耐火材料如陶瓷材料可以有效减少粉尘的产生。
此外,加装适当的气流控制装置和废渣收集设备也是非常必要的。
气流控制装置可以调节热风对焙烧废渣的作用强度和时间,从而实现更加均匀的焙烧效果。
废渣收集设备可以有效收集和处理焙烧过程中释放出来的有害气体和粉尘,从而降低对环境的污染。
最后,改良过程参数。
通过合理调整过程参数,可以进一步提高废渣焙烧技术的效果。
首先,控制废渣的粒度可以影响焙烧的效果。
研究表明,当废渣的粒度适中时,仅有少量残留物质无法被焙烧去除。
因此,通过优化废渣的破碎和筛分工艺,可以得到更加均匀的粒度分布,提高焙烧效果。
完善电炉冶炼工艺降低冶炼成本
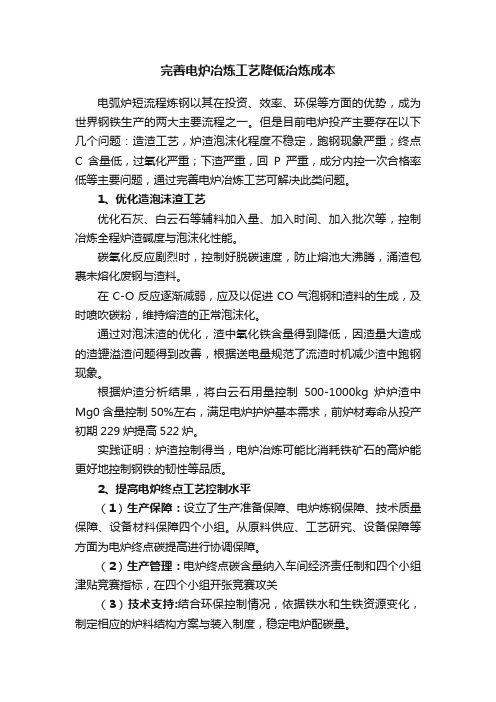
完善电炉冶炼工艺降低冶炼成本电弧炉短流程炼钢以其在投资、效率、环保等方面的优势,成为世界钢铁生产的两大主要流程之一。
但是目前电炉投产主要存在以下几个问题:造渣工艺,炉渣泡沫化程度不稳定,跑钢现象严重;终点C含量低,过氧化严重;下渣严重,回P严重,成分内控一次合格率低等主要问题,通过完善电炉冶炼工艺可解决此类问题。
1、优化造泡沫渣工艺优化石灰、白云石等辅料加入量、加入时间、加入批次等,控制冶炼全程炉渣碱度与泡沫化性能。
碳氧化反应剧烈时,控制好脱碳速度,防止熔池大沸腾,涌渣包裹未熔化废钢与渣料。
在C-O反应逐渐减弱,应及以促进CO气泡钢和渣料的生成,及时喷吹碳粉,维持熔渣的正常泡沫化。
通过对泡沫渣的优化,渣中氧化铁含量得到降低,因渣量大造成的渣罐溢渣问题得到改善,根据送电量规范了流渣时机减少渣中跑钢现象。
根据炉渣分析结果,将白云石用量控制500-1000kg炉炉渣中Mg0含量控制50%左右,满足电炉护炉基本需求,前炉材寿命从投产初期229炉提高522炉。
实践证明:炉渣控制得当,电炉冶炼可能比消耗铁矿石的高炉能更好地控制钢铁的韧性等品质。
2、提高电炉终点工艺控制水平(1)生产保障:设立了生产准备保障、电炉炼钢保障、技术质量保障、设备材料保障四个小组。
从原料供应、工艺研究、设备保障等方面为电炉终点碳提高进行协调保障。
(2)生产管理:电炉终点碳含量纳入车间经济责任制和四个小组津贴竞赛指标,在四个小组开张竞赛攻关(3)技术支持:结合环保控制情况,依据铁水和生铁资源变化,制定相应的炉料结构方案与装入制度,稳定电炉配碳量。
(4)操作工艺:完善了不同炉料装入结构时的送电制度、氧燃就比模式、(4)吹炼模式:确定了吹氧量与配碳量之间的规律;根据炉衬侵蚀情况,调整氧枪使用。
(5)炉型维护:利用更换出钢口对电炉炉型进行进一步维护,保证熔池均匀,提高操作稳定性。
3、多功能炉壁碳氧喷枪技术电炉采用当代最先进的多功能炉壁碳氧喷枪技术,以最简便、最有效的方式向电炉炼钢提供化学能,实现强化供氧、消除EBT冷区,有效缩短冶炼周期、降低电耗、提高金属收得率,达到降低生产成本和提高生产率的目的。
电炉炼钢操作方法及冶炼工艺

• 熔末升温期
电弧开始暴露给炉壁至炉料全部熔化为熔末 升温期。
此阶段因炉壁暴露,尤其是炉壁热点区的暴 露受到电弧的强烈辐射。
应注意保护炉壁,即提前造好泡沫渣进行埋 弧操作,否则应采取低电压、大电流供电。
各阶段熔化与供电情况见下表。 典型的供电曲线如下图。
炉料熔化过程与操作
熔化过程 点弧期
电极位置 送电 → d极
)氧化期的温度控制
氧化期的温度控制要兼顾脱磷与脱碳二者的 需要,并优先去磷。在氧化前期应适当控制升温 速度,待磷达到要求后再放手提温。
一般要求氧化末期的温度略高于出钢温度 20~30℃,以弥补扒渣、造新渣以及加合金造成 的钢液降温,见图。
降低钢中的碳,利用碳-氧反应(C+O2 →CO) 这个手段,来达到以下目的; 搅动熔池,加速反应,均匀成分、温度; 去除钢中气体与夹杂。
实际上,电炉就是通过高配碳,利用吹氧脱 碳这一手段,来达到加速反应,均匀成分、温度, 去除气体和夹杂的目的。
脱碳反应与脱碳条件:
[C]+[O] =CO↑ , △HCO=-0.24kcal=-22kJ<0 分析:该反应是在钢中进行,是放热反应。
提高变压器输入功率,加快废钢熔化速度 ; 废钢预热,利用电炉冶炼过程产生的高温废气 进行废钢预热等。
四、氧化期
氧化期是氧化法冶炼的主要过程,能够去除钢中的磷、 气体和夹杂物。
当废钢料完全熔化,并达到氧化温度,磷脱除70%~ 80%以上进入氧化期。为保证冶金反应的进行,氧化开始温 度高于钢液熔点50~80℃。 (1)氧化期的主要任务
第五章 电炉炼钢冶炼工艺
第一节 电炉冶炼操作方法 第二节 冶炼工艺
第一节 电炉冶炼操作方法
操作方法一般是按造渣工艺特点来划分的,有单渣 氧化法、单渣还原法、双渣还原法与双渣氧化法,目前普 遍采用后两种。
- 1、下载文档前请自行甄别文档内容的完整性,平台不提供额外的编辑、内容补充、找答案等附加服务。
- 2、"仅部分预览"的文档,不可在线预览部分如存在完整性等问题,可反馈申请退款(可完整预览的文档不适用该条件!)。
- 3、如文档侵犯您的权益,请联系客服反馈,我们会尽快为您处理(人工客服工作时间:9:00-18:30)。
60t电炉降低渣中氧化铁的工艺实践
【摘要】本论文将会对泡沫渣形成的机更远进行分析,并分析总结了影响操作泡沫渣的因素,结合目前工艺的现状,根据理论,优化了泡沫渣工艺里的喷粉制度,结果表明,可以取得非常好的效果以及很好的经济效益。
【关键词】氧化铁;工艺泡沫渣;工艺优化;钢铁料消耗
随着建筑行业的飞速发展,对钢材质量的要求也越来越高,在钢材质量、产量不断提高的大前提下,如何将成本降低、提高经济效益,如何在原材料不断多元化的今天将成本降低,已经成为现代电炉企业应该探索的方向。
重庆某钢铁集团,名为重钢公司就有一座60吨的超高功率电炉,采用两支炉壁氧枪、一支炉门氧枪、一支可以用来快速化渣的EBT氧枪、用碳粉罐来吹富碳分泡剂种过渣的供氧系统。
但是因为水冷碳氧枪无法正常的工作以及部分操作原因,炉渣内的全铁含量一直比较高,最高含量竟达34.15%,平均的含量也有22.21%,这表明在生产过程中,铁料的消耗比较高,钢水收得率比较低。
那么如何将这种现状改善,将炉渣内的全铁含量得以控制,就显得非常重要了。
1 重钢公司60吨电炉的主要技术参数
表1列出了60吨超高功率电炉的主要技术参数
配碳的方式采用的是煤质增碳剂、热装铁水的方式,发泡剂是灰分小于等于24%、固定碳大于等于72%的富碳发泡剂。
重钢公司电炉所用渣料的主要成分表如表2所示。
2 泡沫渣的机理
在冶炼的过程中,当将气体充入炉渣中,渣液溶解以后成变成气体的液膜,就会形成很多气泡,主要由2CaO·SiO2·3CaO·P2O5、MgO、MgO·SiO2等悬浮物质点分割,随着炉内气体不断逸出,气泡的压力会不断增大,溶解后的渣液的体积会同气体的膨胀而变大,这也就是泡沫渣形成的机理。
炉渣中的氧化铁含量、炉渣的碱度、熔池的温度、炉渣中的氧化镁含量以及喷吹的碳粉质量等是影响泡沫渣的质量主要因素。
良好的泡沫渣要具备以下特征:
(1)烗渣原料应该可以迅速熔化成液态,而且黏度适中,而且排出的气体可以形成气泡并能保持一定的时间,也就是成泡的时间距离气泡破裂最好为4秒到8秒之间。
(2)要有适宜的炉渣黏度,保证良好的炉渣炉动性,既要防止出现过大的黏度,保证冶金过程中化学反应具有达到标准的硬度,而且要保持悬浮物质量在
一定的数量,也要防止炉渣过稀,因为过稀的炉渣会加剧侵蚀炉衬。
(3)渣内的氧化铁应该保持在14%到20%之间,因为适宜的氧化铁含量可以满足炉渣溶解所需要的浓度。
(4)满足标准的泡沫渣,其渣中的铁珠最好保持在合理的水平,从炉内流出的炉渣可以看出呈现没有乳化特征。
2.1 炉渣中氧化铁的含量和泡沫渣的质量之间的关系
炉渣中的石灰通过氧化铁溶剂进行溶解,而且在冶炼的过程中氧化铁可以维持一些化合物的稳定,同时可以保证渣系性质,从而使炉渣可以满足冶炼要求。
这包括氧化性炉渣脱磷,适量的氧化铁可以保证炉渣流动性。
而且熔池中钢水含碳量很低时,应该将发泡剂碳粉喷入炉中,让其与炉渣里的氧化铁发生反应从而产生需要的气体。
如果炉中有过高的氧化铁,尤其是其含量大于20%时,就会将悬浮物质点硅酸二钙降解,从而使炉内的发泡质量降低,钢铁的耗费增加了,对炉衬的侵蚀作用也特别明显。
大量的实践表明,如果渣中的氧化铁保持在20%到40%之间,泡沫化的过程可以顺利地进行,如果氧化铁的含量在20%到40%之间,此时炉内就会出现水渣,如果炉内的氧化铁含量较低,在7%以内,炉渣有可能会出现炉渣黏度太大或是出现乳化的现象,从而不利于炉门流渣操作以及钢渣之间的物理和化学反应。
2.2 吹氧量对炉内泡渣的质量所造成的影响
一般的条件下,在氧化钙的含量相同,熔池里出现脱碳反应的情况下,如果吹氧量越多,脱碳时产生的气体也就越多,渣里所含的氧化铁也会增加,泡沫渣高度也就越大。
如果熔池中的碳含量比较低,吹氧量越多,氧化铁的含量也就越高,这样泡沫渣也就越不稳定。
2.3 喷吹碳粉对炉内泡沫渣质量所造成的影响
喷吹碳粉具有以下两个主要作用:一是可以降低渣所含的氧化铁,将泡沫渣的黏度提高,从而将泡沫渣的质量提高;二是喷吹的碳粉可以与氧化铁发生化学反应生成一氧化碳气体,从而为炉渣的发泡提供气源。
3 工艺的优化
3.1 进行优化工艺前的冶炼效果
因为渣中的氧化铁对设备和工艺具有影响,所以本论文将讨论如果降低氧化铁的含量。
通过总结历史数据,统计了1月份到5月份的数据。
具体的部分数据如下表所示。
从表3的数据可以看出,全铁的含量最高可达31.38%,平均的含量就达
23.14%,每炉的发泡剂用量固定的平均量为100千克,渣中的全铁含量总体较高,氧化铁的含量过高,会使炉渣的密度增加,从而使铁料增加,影响了脱碳的反应速度。
此外,铁的含量过高也是溶解氧含量过高的表现,容易出现其他的夹杂物。
而且,渣中的铁与碳粉发生还原反应,这是吸热反应,容易浪费电能,增加损失。
3.2 优化工艺
如表4所示
根据优化工艺以后的数据,可以采取具体的优化措施,如下所列:
(1)造渣操作要与供电制度以就脱碳反应相结合,合理的将供供电强度以及供氧控制,将喷吹碳粉流量调整。
(2)在冶炼的前期,要以脱磷、造氧化炸为主,控制吹氧的流量和角度。
等到炉渣泡沫化充分以后,再进行脱碳反应。
根据炉渣的情况以及脱碳的速度控制喷吹发泡剂的操作。
(3)如果碳含量在0.2%到0.5%之间,就要降低枪位,大量地喷吹碳粉,从而可以将渣中的氧化铁含量降低,也可以将剧烈沸腾机率降低。
(4)根据终点情况以及炉渣的情况调整碳粉喷吹操作,适时地流渣,并补造新渣,从而保证泡沫渣的高度。
(5)在冶炼的最后,在终点喷吹富碳发泡剂,如果终碳较低就喷吹两分钟左右,如果终碳较高就喷吹一分钟左右。
对稠化终渣以及调整渣系能够起到非常好的效果,从而调整了渣中的氧化铁的含量,将生产工艺的铁耗降低。
4 结论
通过对喷粉量的分阶段控制,优化了供电曲线和吹氧的强度,从而保证了泡沫渣的黏度和高度。
在冶炼的中期适量的放渣,前及时补造新渣,从而可以保证钢渣流动性。
并且,在出钢前喷粉可以降低渣中全铁的含量,从而将铁耗降低,这样渣中全铁的含量可以控制在20%左右;在出钢前喷粉也可以稠化终渣,从而控制住了出钢的下渣,这样可以保证钢水质量。
参考文献:
[1]俞海明,秦军.现代电炉炼钢操作[M].北京:冶金工业出版社,2009.
[2]王振宙,朱荣,等.电弧炉炉壁吹氧对渣线MgO-C砖的侵蚀分析[J].冶金能源,2008(1).。