硬质合金铰刀的设计及其切削实验研究
硬质合金与结构钢钎焊刀具切削试验及数据分析

钎 焊过 程 :① 焊接硬 质合 金工具 时均 匀加 热 刀杆 和刀头 保证 焊接质 量 ;② 钎焊 后冷 却 硬质 合金 片表面 产生 瞬时拉应 力 。采用 低 温 回火处 理能消 除部分 钎焊 应力 ,减小 裂纹 ;③ 焊后 清理 : 要对 焊 好 的硬质 合金 工件进 行焊 后清理 。3) 钎焊 的质量 检验 : 焊缝 检测方 法 : ① 刀 具经喷砂 处理 后 ,用 煤 油清洗 ,用 肉眼和 放大镜 观察 。有裂 纹 时 有 明显 黑 线 ;② 用 6 5 % 煤油 、3 0 % 的 变 压器 油及 5 % 的松 节油 调成 溶 液 ,加 入 少 量苏丹 红 ,将 检查 的刃具 放入 该溶 液中 浸泡 1 0 — 1 5 a r i n ,取 出 用 清水 洗 净 ,涂 上 高岭土 ,烘干 后检查 表面 ,如果 有裂 纹 , 溶液 的颜色将 在 白土显示 i _ l j 来, 肉眼可查 。 3 硬 质合 金与结 构钢 钎焊 刀具切 削试 验及数 据分 析 3 . 1 本次 试 验 中制造 的 3 把 刀具 的试 验方 法及试 验数据 进行 介绍 : N o . 1 刀 杆材 料 4 0 G r 1 0 ; 刀 头 材 料 X 3 0 9 . 8 ; 焊料 铜 H 6 2 ; 焊 缝扭 曲大 焊缝 分 布不均 匀 。 N o . 2刀 杆 材 料 4 0 G r 1 0 ; 刀 头 材 料 X 3 0 d ) 9 . 8 ; 焊料 银 焊条 ; 焊缝 扭 曲小焊 缝 分 布不 均匀 。 N o . 3 刀杆材料 4 0 G r 1 0 ; 刀 头 材 料 X 3 0 4 ) 9 . 8 ; 焊料 银 焊条 ; 焊缝 无扭 曲焊缝 分布均 匀 。 3 . 2 刀具 试验情 况 N o . 1 试验设备 X 5 2 K ; 加工材料 T 8 A ; 转速 9 5 0 转, 分 ;切 深 8 m m ; 加工 1 件 后 刀具 断裂 。 N o . 2 试验设备 X 5 2 K ; 加工 材 料 T 8 A ; 转速 9 5 0 转/ 分 ;切 深 8 a r m ; 加 工 3件后 刀具 断 裂。 N 0 3试验 设 备 X 5 2 K ; 加 工 材料 T 8 A ; 转速 9 5 0转 / 分 ;切 深 4 a r m; 加工 1 件 后
整体硬质合金刀具关键工步磨削工艺实验的研究

11500
茕
曩1000
5D0
磨莉次戢
(c)轴向磨削力
图414初步过程实验磨削力实验结果
由上图4.14可以看出,随着磨削次数的增加.磨削力逐渐增大,但增大的幅度很小。
对于砂轮线速度v。
=30m/s与v。
=60rals这两组参数,第一次的磨削力数值基本接近,但随着磨削次数的增加,v,f30m/s的磨削力基本保持不变,而vs=60m/s的磨削力却逐渐增大,从而v,=30m/s较v。
=60m/s具有更好的磨削稳定性。
4.242系统过程实验
由4.2.4.1中对初步过程实验的实验结果进行分析,选择v:=16m/s、vw=55mm/min、ah-2mm与h=30m/s、Vw=1lOmm/min、口^-2ram这两组磨削参数进行大量磨削实验,并对实验结果进行深入分析。
其实验结果如下。
(1)表面形貌
a)第l攻磨削后(b)第10次磨削后。
超细晶硬质合金刀具切削高温合金试验研究

车削GH2132过程中刀具磨损和刀具耐用度,为改善加工工艺 提供了参考数据。文献研究了切削GH2132时硬质合金中钻
GH2132高温合金进行了切削试验,对比了两种刀具在不同切削 速度条件下的切削力和刀-屑摩擦系数,测定了刀具后刀面的平
来稿日期:2020-05-22 基金项目:河北省科技计50项目(16211027);河北省教育厅高等学校科学技术研究项目(QN2016162) 作者简介:张好强,(1979-),男,河北衡水人,博士研究生,副教授,主要研究方向:绿色制造与先进加工技术;
侯锁霞,(1972-),女,河北衡水人,硕士研究生,副教授,主要研究方向:先进制造技术
第7期
张好强等:超细晶硬质合金刀具切削高温合金试验研究
149
均磨损宽度VB值,借助扫描电镜观察了刀具后刀面的磨损形貌, 同时对刀具的磨损机理进行了分析。
2试验部分
使用WC-Co类硬质合金刀片,牌号为YG8和YG8UF,刀片 型号为31303C,刀具形状,如图1所示。刀具材料表面形貌,如图 2所示。刀具几何参数,如表1所示。刀具材料的机械物理性能, 如表2所示。工件材料为高温合金GH2132,直径<p60mm,其化学 成分,如表3所示。在CK6140e数控车床上以外圆纵向车削方式 干切削,如图3所示。选定的切削用量,如表4所示。
60
65
70
75
切削速度(m/min)
(a)切削合力
1.0
1
1
u1
1
1
111
十-<
1
1
1
1j
厂
1
1
1
1
1
・
0.5 50
1
1
-------- 1------
精磨硬质合金数控刀片切削与磨损性能的实验研究

第27卷第4期2009年12月 河北建筑工程学院学报J OUR NAL O F HEBEI INSTITUTE OF AR C HITEC TUR E AN D C IVIL ENG INEER INGVol 27No 4Dec.2009收稿日期:20090820作者简介:女,1963年生,教授,张家口市,075024基金项目:河北省科技厅科学技术研究与发展计划项目(05212157)精磨硬质合金数控刀片切削与磨损性能的实验研究郭秀云 梁建明 王占英 刘春东 王少雷河北建筑工程学院摘 要 对YT 14三角形硬质合金数控刀片的切削与磨损性能进行了实验研究.在实验中,针对两种不同精度级的数控刀片进行了切削性能和磨损特性对比实验.实验表明:刀片精度级越高,其磨损速度越低.用高精度级刀片进行切削加工,不仅可以提高工件的加工表面质量,还可延长刀片的使用寿命,从而节省刀片的购置费用,具有可观的经济效益和社会效益.关键词 刀片;磨损;切削中图分类号 TH160 引 言数控机床在我国机械行业应用越来越普遍,数控刀具的制造与使用直接影响着数控机床效率的发挥.目前,在西方工业化国家中,硬质合金已占刀具材料的65%以上,硬质合金可转位刀片产量已达刀片总产量的70%~90%,所以研究硬质合金数控刀片的切削与磨损性能具有现实意义.国外硬质合金刀片产品分为精密级和普通级.精密级硬质合金刀片公差带很小,刀片必须经过精研,从而使刀片表面质量得到改善,但价格十分昂贵.从进口刀具产品外观质量上看,其外观、颜色和纹理明显优于国产刀具.在刀具产品使用性能上,进口刀具加工尺寸精度高、稳定性好、耐用度高、切除率高,刀具及其配件具有良好的互换性,一般装配后即可达到精度要求.在我国随着机械加工技术不断进步,硬质合金可转位刀具在机械行业的使用也越来越广泛.从目前使用情况来看,国产硬质合金可转位刀具的市场占有率低于进口刀具.由于国产硬质合金刀片的数量及品种均不能满足生产的需要,每年不得不花费美元去进口数控刀片.这样,从我国生产实际出发,应立足于国内数控刀片的生产,在产品外观上加以改进,相应增加一些表面处理工艺.国产硬质合金刀片精磨后,尺寸精度与国外的精密级刀片相近,刀片钝圆半径小,刀片表面质量也改善了,因此应用于精加工的场合,刀片的寿命长、可靠性好,而且价格便宜,极限切削深度也可取更小值.本实验分别对常规磨削与经精磨后的YT14三角形数控刀片进行了切削性能对比实验,观察并分析了刀片的磨损情况,探索了提高数控刀片的加工精度和延长刀片使用寿命的途径,为降低刀片的购置费用提供了理论依据和实验验证.1 实验装置本实验采用由无锡市荣盛合金工具有限公司生产的硬质合金切削刀片YT 14三角形可转位数控刀片.常规磨削的三角形数控刀片,表面粗糙度在Ra0 4~0 8甚至更高些.而需精磨的三角形数控刀片,将其固定在自行设计的专用夹具上,利用金刚石砂轮对各个刀面进行磨削.最后将各个加工面在金刚石研磨机上进行研磨,直至达到所需精度为Ra0 014~0 06.切削性能对比实验在沈阳机床厂生产的CAK3665di 型号数控机床进行.利用上海光学仪器五厂生产的型号为4XB 显微镜对三角形可转位数控刀片的主切削刃磨损量VBmax 进行观测.工件材料为45钢,直径为 40的棒料.2 实验条件及结果(1)当切削深度a p =1mm 、工件转速n w =500r/m in 、进给量f =0 2mm/r 时,经同等条件实验五次后,未经磨削与经精磨后的三角形数控刀片后刀面的最大磨损量VBmax (取平均值)与切削时间t 的实验数据见表1,VBmax 与t 的对应关系曲线见图1.表1 VBm ax 与t 的实验数据t(min)6 412 819 225 632 0VBmax(mm)未磨0 1060 1470 1750 1980 215已磨0 0750 1120 1520 183195图1 切削时间与磨损量的对应关系 图2 切削速度与磨损量的对应关系(2)当进给量f =0 2mm/r 、切削深度a p =1mm 、切削长度为640mm 时,经同等条件实验五次后,常规磨削与经精磨后的三角形数控刀片后刀面的最大磨损量VBm ax (取平均值)与切削速度V 的实验数据见表2,VBm ax 与V 的对应关系曲线见图2.表2 VBmax 与V 的实验数据V(m/min)62 8075 3687 92100 48113 04VBmax(mm)未磨0 1060 1330 1630 1970 227已磨0 0750 1110 1430 1630 187(3)当V =113 04m /min 、切削深度a p =1mm 、切削长度为640m m 时,经同等条件实验五次后,未经磨削与经精磨后的三角形数控刀片后刀面的最大磨损量VBmax (取平均值)与进给量f 的实验数据见表3,VBmax 与f 的对应关系曲线见图3.表3 VBm ax 与f 的实验数据f(mm/r)0 100 150 200 250 30VBmax(mm)未磨0 2200 2240 2270 2290 233已磨0 1820 1850 1870 1890 193(4)当V =113 04m/min 、进给量f =0 2mm/r 、切削长度为690mm 时,经同等条件实验五次后,未经磨削与经精磨后的三角形数控刀片后刀面的最大磨损量VBm ax (取平均值)分别与切削深度a p 的实验数据见表4,VBm ax 与ap 的对应关系曲线见图4.77第4期 郭秀云 梁建明 王占英等 精磨硬质合金数控刀片切削与磨损性能的实验研究表4 VBmax 与ap 的实验数据ap(mm)12345VBmax(mm)未磨0 2270 2280 2290 2300 230已磨0 1870 1880 1880 189189图3 进给量与磨损量的对应关系 图4 切削深度与磨损量的对应关系3 实验结果分析从图1~图4我们可以看到:(1)在整个切削过程中,当切削条件相同时,我们进行比较后刀面最大磨损量值.实验结果表明:未磨刀片的磨损量值大于经精磨后刀片的磨损量.(2)刀片在刚开始进行切削时,已磨刀片与未磨刀片的磨损量差值较大,随着切削时间的延长,此差值略有减小的趋势.(3)对刀片磨损量影响最大的是切削速度.在切削过程中,随着切削速度的提高,未磨和已磨刀片的磨损量均剧增,且未磨与已磨刀片磨损量差值处于0 020~0 041mm 的范围内.(4)进给量对未磨和已磨刀片的磨损量也有影响,仅次于切削速度.当改变进给量时,未磨和已磨刀片的磨损量处于0 038~0 040mm 的范围内.(5)切削深度的改变对未磨和已磨刀片的磨损量影响最小,二者的磨损量差值也基本保持稳定状态,处于0 040~0 041mm 之间.4 磨损量的经验公式利用角正回归法,对实验数据进行处理,可得后刀面磨损量的回归方程为:未磨为:VB max =0 00576a p0 1256f 0 7159V0 9866(mm);已磨为:VB max =0 00712a p 0 1523f 0 8976V 1 3116(mm);式中单位为:VB(mm );a p (m m);f(m m/r);V(m/min).5 结 论(1)由于已磨刀片表面精度高且结构密实,提高了表面硬度,能够减小刀片与切屑之间的摩擦系数,降低切削力,使刀片具有较好的耐磨性,促使刀片的抗磨损能力增强,从而其使用寿命也大大提高.(2)利用经精磨后的数控刀片进行切削加工,随切削参数的变化可不同程度地降低刀片的磨损速度,提高刀片的使用寿命.(3)在切削过程中,切削速度对刀片的切削性能及磨损速度影响最大;进给量次之;而切削深度影响最小.78河北建筑工程学院学报 第27卷(4)当改变进给量和切削深度时,已磨和未磨刀片的磨损量差值均略大于改变切削速度时二者的差值,所以大进给量和大切削深度的切削方式更能使刀片的使用寿命相对延长.(5)建议无论在粗加工或精加工时,尽量使用经精磨后的刀片进行切削加工.这样不仅提高了加工精度,而且还能延长刀片的使用寿命,从而节省刀片的购置费用.这一技术若广泛推广,将会产生良好的经济效益和社会效益.参 考 文 献[1]郭秀云.硬质合金磨削力的实验研究.硬质合金,1996,1[2]郭秀云.硬质合金材料磨削机理及磨削温度的实验研究.天津大学研究生毕业论文,1996,8[3]郭秀云.硬质合金磨削温度的实验研究.硬质合金,1997,2[4]于启勋.新型硬质合金 添加稀土元素的硬质合金.现代刀具材料系列讲座(七),2005,11,12[5]周泽华主编.金属切削原理.上海科学技术出版社,1984,12[6]陈章燕.平面、外圆磨削力计算公式的研究和应用.磨床与磨削,1992,4:27~31[7]郭秀云.磨削硬质合金材料去除机理的实验研究.硬质合金,1997,5[8]郭秀云.硬质合金磨削温度场的实验研究.硬质合金,1999,2[9]郭秀云.硬质合金刀片磨损性能的实验研究.新技术新工艺,2000,10The Experimental Study on Cutting and Wear Performance ofFine Grinding Cemented Carbide Numerical Control ToolsGuo Xiuy un ,Lian g Jia nm in g ,Wa ng Zha nyin g ,Liu Chun don g ,Wa ng Sha oleiH ebei Institute o f A rchitectur e and Civil Engineer ingAbstract T he cutting and w ear perform ance of YT 14triang le cemented carbide numerical contro lto ols w ill be studied ex perimentally in this paper.T he ex periment show s that the hig her the too l 's precisio n level is,the m ore slow ly it w ear s.H ig h precision leveled tools are used in the cutting process,w hich can not only im pro ve the surface cutting quantity,but also pr olong the tool's life time,then the purchasing expense of tools is saved and considerable economic and social benefits can be got.Key words tool;w ear;cutting79第4期 郭秀云 梁建明 王占英等 精磨硬质合金数控刀片切削与磨损性能的实验研究。
硬质合金铰刀及其标准化

硬质合金铰刀及其标准化硬质合金铰刀作为一种高效切削工具问世以来,已越来越广泛地被采用。
在ISO的硬质合金P, M和K类基础上,我国发展生产了碳化钨、碳化钻、碳化钛、碳化钽和钴等硬质合金材料,突破了高效铰削这一难关。
但是,对硬质合金铰刀如何正确设计、加工,特别是硬质合金铰刀各参数如何达到合理安排,使其标准化、优选化和系列化,并获得满意的经济效果,还是一个值得重视的课题。
1确定切削刃、校正刃、过渡刃刃带铰刀的要害部位之一就是刃带,不同的被加工材料,不同的工件铰削余量及不同的工件与铰刀的相对转速决定着不同的刃带宽度。
生产中使用的铰刀常出现以下情况:铰刀使用寿命短,刃带迅速磨损而报废;铰刀表面粗糙度差,导致被加工工件孔的表面粗糙度更差;工件经铰削加工后的孔变形,因而孔的圆度超差,往往造成产品报废。
分析现场使用后的硬质合金铰刀,发现所有报废的铰刀磨损量并不大,除靠近切削刃和过渡刃1~2mm处有磨损痕迹外,其余切削刃完好,因此得出结论:除了不断提高铰刀切削刃外圆的表面粗糙度要求外,还必须对硬质合金铰刀刃带宽度进行优化。
经过多次生产实践和试验,找出了铰刀刃带宽度的最佳尺寸范围,见表1。
表1碳钢用硬质合金铰刀刃带宽度推荐值(mm)表2硬质合金铰刀铰削不同硬度图一图二2掌握材料变形规律,合理确定硬质合金铰刀公差由于硬质合金铰刀与高速钢铰刀的切削状态不同,前者是切削加挤削,因此发热量大大超过了高速钢铰刀。
用硬质合金铰刀进行高速铰削时,最高发热量可达800℃,工件由热变冷时,工件内孔收缩量大,铰刀不立即取出还会有被咬死现象。
铰削中材料的硬度、单位切削力和铰削所产生的热量见表2。
不同的材料硬度和孔径,由于发热量变化,其变化规律如图1。
3正确制定企业标准,扩大硬质合金铰刀的使用范围从以上分析中可以看出,我们在制定硬质合金铰刀标准时不能硬套上级标准,在采用国际标准和国家标准普遍原则的前提下,还要注意制定企业内控标准。
针对不同特点制定的硬质合金铰刀公差原则已经被实践所证实,而且被广泛认可采纳。
解析硬质合金铰刀铰孔无规则收缩_龚小冬

# !" ! " " # 年 第 $% 期 ! ! !" " # $ % & ’ & ( )" $ * "" $ ’
冷加工
( 收稿日期:&))-)’&- )
( 广东! "#$%%% ) ! 李苏营
更大的进给速度以及防止断续切削时切削刃的破坏。 ( & ) 为了避免振动和切断面不平,将刀具磨成如图 % 所示的形状。这样在切削时,刀刃是逐渐切入工件的, 因此受力平稳、连续性好;同时由于刀刃的受力情况如 图 & 所示,沿工件的轴向分力 +% 与 +& 因大小相等方向 相反而相互抵消,因此不会出现普通切断刀易产生振动 的现象。
############################################ !" 解决的办法
针对主要原因,在铰刀加工工艺上采取措施: ( % ) 刀体材料选用 16370,使其焊刀片后仍保持一 定的硬度。 ( & ) 铰刀设计上尽量选用较薄的刀片,刀齿稍浅, 齿槽角度稍小,使齿背尽量加厚,且铰刀外径按孔的最 大极限尺寸设计。焊刀片时,铜焊尽量焊薄焊实在。 ( + ) 铰刀加工工艺在粗磨刀齿外圆时,留精磨量 )" %( 2 )" &,,,然后工具磨用死支片支撑前刀面,粗磨 后角为 %(* 2 %-* ,留圆柱刃带 )" (,, 左右 ( 每齿刃带 宽窄必须一致,否则容易产生跳动误差) 。刃带太窄不 便测量,刃带太宽又不易消除 “ 让刀” 。精磨外圆到最 后尺寸接近时千万不能急,多光整一会,就能避免 塌 陷,第三点是主要环节。 我们用前面所提到的前导向细长杆复合铰刀,试加 工几件,到生产线试用后,效果很好,孔的尺寸与铰刀 的外径完全吻合,孔的圆度和表面粗糙度质量都大幅提 高。我们将所有的硬质合金铰刀都按此加工,取得了同 样的效果。现在,我厂的硬质合金铰刀不再为尺寸和铰 孔质量而烦恼,节省了大量调刀时间、研磨工作和刀具 损耗,为工厂生产经营做出了不可磨灭的贡献。愿我们 的努力也能为我国的机械加工业进步有所帮助。
硬质合金铰刀制造公差值的设计
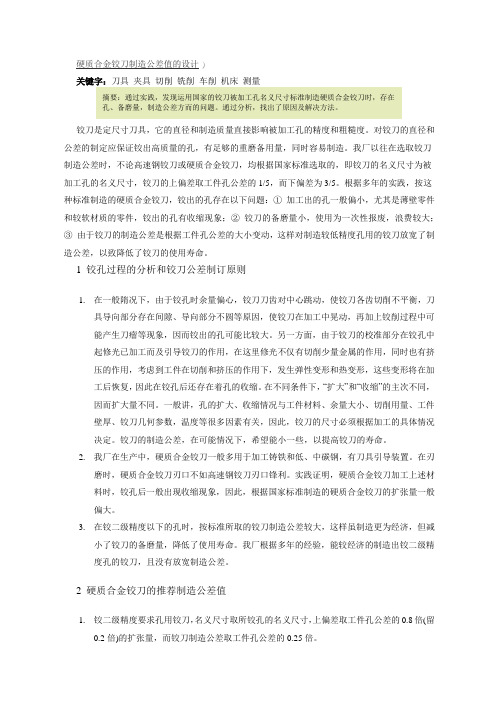
硬质合金铰刀制造公差值的设计)关键字:刀具夹具切削铣削车削机床测量摘要:通过实践,发现运用国家的铰刀被加工孔名义尺寸标准制造硬质合金铰刀时,存在孔、备磨量,制造公差方而的问题。
通过分析,找出了原因及解决方法。
铰刀是定尺寸刀具,它的直径和制造质量直接影响被加工孔的精度和粗糙度。
对铰刀的直径和公差的制定应保证铰出高质量的孔,有足够的重磨备用量,同时容易制造。
我厂以往在选取铰刀制造公差时,不论高速钢铰刀或硬质合金铰刀,均根据国家标准选取的,即铰刀的名义尺寸为被加工孔的名义尺寸,铰刀的上偏差取工件孔公差的1/5,而下偏差为3/5。
根据多年的实践,按这种标准制造的硬质合金铰刀,铰出的孔存在以下问题:①加工出的孔一般偏小,尤其是薄壁零件和较软材质的零件,铰出的孔有收缩现象;②铰刀的备磨量小,使用为一次性报废,浪费较大;③由于铰刀的制造公差是根据工件孔公差的大小变动,这样对制造较低精度孔用的铰刀放宽了制造公差,以致降低了铰刀的使用寿命。
1 铰孔过程的分析和铰刀公差制订原则1.在一般隋况下,由于铰孔时余量偏心,铰刀刀齿对中心跳动,使铰刀各齿切削不平衡,刀具导向部分存在间隙、导向部分不圆等原因,使铰刀在加工中晃动,再加上铰削过程中可能产生刀瘤等现象,因而铰出的孔可能比较大。
另一方面,由于铰刀的校准部分在铰孔中起修光已加工而及引导铰刀的作用,在这里修光不仅有切削少量金属的作用,同时也有挤压的作用,考虑到工件在切削和挤压的作用下,发生弹性变形和热变形,这些变形将在加工后恢复,因此在铰孔后还存在着孔的收缩。
在不同条件下,“扩大”和“收缩”的主次不同,因而扩大量不同。
一般讲,孔的扩大、收缩情况与工件材料、余量大小、切削用量、工件壁厚、铰刀几何参数,温度等很多因素有关,因此,铰刀的尺寸必须根据加工的具体情况决定。
铰刀的制造公差,在可能情况下,希望能小一些,以提高铰刀的寿命。
2.我厂在生产中,硬质合金铰刀一般多用于加工铸铁和低、中碳钢,有刀具引导装置。
硬质合金铰刀的设计及其切削实验研究

:
度
、
铰 刀 的 制 造 成 本 与 使 用 寿命
—
,
为铰 刀 设 计 的关键
,
。
( 2 )前角
(3
y
a
。
为 了 减 小切 屑 变 形 取
,
7
, ,
=
7
。 。
GB4 24 8
84
明确 规 定 以 IT 为孔 的 公 差 则 铰 刀 直 径 的
:
.
)后 角
。
刃带
b
。
。
铰 刀 属 精加
,
丁刀
具 为使其重
=
.
~
m
Y W2
15
1 3 3 5 x 10 k g/ m
.Leabharlann 3s,硬度
铰 刀 最 大直 径 :‰
=
=
19 5 13
.
0 0 0 2 = 19 5 1 l
. . .
m
m
HR A9 1 5
,
抗 弯强 度
。
19 0 0 M P
a
,
使用强度较高 能承受较大
,
、
铰刀 制造公差 孔公差 铰 刀 最 小直 径
d on
铰刀 公称直径 用 设计 引导 锥
,
切 削部分锥 角 西
m
,
。
角 大 小 主 要 影 响 被 加 工 孔 的表 面 粗
。
a r
为 提 高 铰 削 时 的 导 向作
25
a r m
,
糙 度 精 度 及 铰 削 时 的轴 向 力 的大 小 缸 过 大 会 使 切 削部
、
1x 4 5
。
硬质合金刀具在金属切削中的应用研究

硬质合金刀具在金属切削中的应用研究摘要:硬质合金刀具作为一种重要的刀具材料,在金属切削领域中具有广泛的应用。
本文通过分析硬质合金刀具的特性,探讨了其在金属切削中的应用研究现状及面临的挑战,并提出了未来的发展方向。
关键词:硬质合金刀具,金属切削,应用研究引言硬质合金刀具是根据研究人员对金属切削工艺发展的需要而设计的一种高性能切削工具。
它由金属粉末和添加剂经热处理而成,具有高硬度、高强度、耐磨损等优点,适用于对各种金属进行高效切削。
本文旨在通过对硬质合金刀具在金属切削中的应用研究进行系统的探讨,为相关行业的工程师和研究人员提供一定的参考和指导。
硬质合金刀具特性硬质合金刀具是由钴基或镍基合金粉末和一定比例的超硬颗粒(通常是碳化钨)以及其他辅助材料混合制备而成。
其具有以下特性:1. 高硬度:硬质合金刀具的硬度通常在80-95HRA之间,可以切削各种硬度的金属材料。
2. 高强度:硬质合金刀具具有较高的强度和刚性,可以在高速切削过程中保持较好的刚性,减少刀具变形和震动。
3. 耐磨损性:硬质合金刀具的超硬颗粒具有优异的耐磨损性,能够在长时间的切削过程中保持刀具的良好切削性能。
4. 耐热性:硬质合金刀具由于添加了合适的金属粉末,能够有效降低切削过程中的热膨胀和高温脆断现象。
硬质合金刀具在金属切削中的应用研究现状硬质合金刀具在金属切削领域中具有广泛的应用,已经取得了一系列显著的研究成果。
以下是一些典型的应用研究案例:1. 切削性能研究:许多研究人员针对硬质合金刀具的切削性能展开了深入的研究。
他们通过设计不同切削参数和刀具结构,评估了硬质合金刀具的切削力、切削温度、刀具磨损等指标,提出了切削性能优化的方法和策略。
2. 表面质量优化:硬质合金刀具在金属切削中的应用还涉及到对工件表面质量的要求。
一些研究人员通过控制切削参数和采用特殊的刀具结构,成功提高了金属加工的表面光洁度和粗糙度。
3. 刀具寿命评估:硬质合金刀具的使用寿命直接影响到加工成本和工艺效率。
铰刀的合适使用

铰刀的合理使用与改进本文以笔者在工厂中长期的使用经验与验证为依据,对标准铰刀结构上存在的问题提出了改进意见,同时还对铰刀如何合理使用的问题作了分析与介绍。
在机械加工中,孔加工约占加工总量的1/3。
而铰孔是普遍应用的一种精加工和半精加工孔的方法,加工孔径通常在Φ1~Φ100mm之间,尺寸精度一般可达H9~H7级(甚至H6级),加工表面粗糙度为Ra1.6~0.2μm。
铰孔用的刀具,目前生产上仍以标准的多齿铰刀为主。
我们知道,标准铰刀铰孔时通常会出现很多问题,例如误差度、直线度、排屑、让刀、振动现象、刀具使用寿命低、退刀时产生划痕等等,由于文章篇幅有限,在此不做详细列举。
改进铰刀的几何参数图1 铰削时切削厚度由于铰刀主要用于孔的精加工和半精加工,故应将切削层的厚度减薄,并且切削厚度愈小,切削刃参加工作部分长度相应增大,铰刀切入时的导向性好,刀具寿命也愈高。
由图1可知,铰削时的切削厚度:h D=f z sinκr=(f/z)sinκr上式中,fz为铰刀每齿进给量,单位mm/z;f为铰刀每转进给量,单位mm/r;z为铰刀齿数;κr为铰刀上的主偏角。
由此可见,为了提高铰孔质量和刀具的使用寿命,铰刀上的主偏角κr应取小值为宜。
试验也表明,κr角愈小,孔的表面粗糙度值Ra也愈小。
但通常认为手用铰刀应采用小的κr角,以使刀具工作时能保持良好的导向并减小轴向进给力,而机用铰刀的导向和轴向进给力均由机床和夹具来保证,为减少切屑变形,故使用较大的主偏角。
目前标准上(见技术标准出版社出版的“铣刀铰刀生产图册”)推荐的高速钢机用铰刀的主偏角为15°,手用铰刀的主偏角为1°;硬质合金铰刀的主偏角,切钢时推荐用15°,切削铸件为3°~5°。
但经生产验证,标准上推荐的主偏角数值,并不完全合适,作者在生产中将硬质合金机用铰刀的主偏角切钢件时也改为5°,无论是加工量与铰刀寿命均有明显提高。
机用铰刀设计

第三节机用铰刀设计一、高速钢机用铰刀设计(一)几何角度(见表3-21)表3-21 机用铰刀几何参数(二)铰刀直径与公差1、铰刀的直径基本尺寸d0等于被铰孔的基本尺寸Dω即:do=Dω(3-3-1)2、铰刀直径的制造公差G按GB4246-84规定等于被铰孔公差IT的0.35倍,即:图3—14铰刀公差和孔公差配置a)半圆形齿形 b)三角形齿形 c)五角形齿形图3—15铰刀公差和孔公差配置G=0.35IT (3-3-2)铰刀公差和孔公差的配合如图3-14。
3、用高速钢铰刀铰孔后,孔径一般发生扩张,按GB4246-84规定铰刀直径的上限尺寸d0max 等于孔的最大直径减0.15IT ,即:D omax =D ωmax -0.15IT (3-3-3) 铰刀直径的下限尺寸d0min 等于铰刀的最大直径d0max 减0.35IT ,即:D omax =D ωmax -0.35IT -0.15IT (3-3-4) 0.15IT 、0.35IT 的值应圆整到0.001mm 的整数倍。
铰刀直径与偏差见表3-22。
(三)齿数Z 及分布铰刀齿数Z 影响铰孔质量、刀齿强度和容屑空间并与工件材料、铰刀直径有关。
一般可按下式计算: )4~2(5.10+d Z = (3-3-5)加工韧性材料时Z 取小值;加工脆性材料时Z 取大值。
为了测量方便通常取偶数。
刀齿在圆周上分布为制造方便一般取等齿距分布。
Z 可按表3-23选取。
4、铰刀齿槽与尺寸当铰刀直径d 0<3mm 时铰刀齿槽形状可作成半圆形、三角形或五角形如图3—15所示。
当铰刀直径d 0≥3~20mm 时,铰刀齿槽通常作成直线齿背截形;当铰刀直径d 0>20mm 时,铰刀齿槽采用圆弧齿背截形,尺寸见表图3—17。
表3—17 铰刀齿槽形状与尺寸5、工作部分尺寸见表3-256.非工作部分结构尺寸见表3-26。
表3-26 莫氏锥柄机用高速钢铰刀非工作部分结构尺寸84。
圆锥柄为莫氏锥度,尺寸见表3-27。
金属切削原理与刀具 课题38 铰刀

铰刀的结构参数和几何参数
课题三十八 铰刀
二、齿数及齿槽形式 2.齿槽形式
铰刀的齿槽形式有直线形、圆弧形和折线形三种。
折线形:它常用于硬质合金铰刀,以保证硬质合金刀片有足够的刚性支承面 和刀齿强度。
铰刀的结构
铰刀的结构参数和几何参数
一、铰刀的结构
1.铰刀直径及其公差
课题三十八 铰刀
铰刀直径及其公差
Dw—孔的基本尺寸; d—铰刀公称直径; P—扩张量; Pa—收缩量; G—铰刀的制造公差; N—铰刀的磨损储备量
铰刀的结构参数和几何参数
一、铰刀的结构
1.铰刀直径及其公差
根据加工中孔径的变形性质不同,铰刀的直径确定方法如下:
(d)机用成套式铰刀
铰削特点
课题三十八 铰刀
铰削的加工余量一般小于0.1mm,铰刀的主偏角一般小于45°,因此,铰削时切削 厚度很小,仅为0.01~0.03mm。铰削过程除主切削刃正常的切削作用外,还对工件产 生挤刮作用,因此,它是一个复杂的切削和挤压摩擦过程。
一、铰削精度高
铰刀齿数较多,心部直径大,导向性及刚性好。铰削加工余量小,切削速度低,且 综合了切削和修光的作用,能获得较高的加工精度和表面质量。
为了便于测量直径,铰刀齿数一般取偶数。刀齿在圆周上一般为等齿距分布。在 某些情况下,为避免周期性切削载荷对孔表面的影响,也可选用不等齿距结构。
铰刀的结构参数和几何参数
二、齿数及齿槽形式 2.齿槽形式
铰刀的齿槽形式有直线形、圆弧形和折线形三种。
课题三十八 铰刀
直线形:它形状简单,齿槽可用单角铣刀一次铣出,制造容易,一般用于直 径d=1~20 mm的铰刀。
机用铰刀刀设计范文

机用铰刀刀设计范文铰刀(Milling Cutter)是机用刀具中的一种。
它主要用于铣削加工,并广泛应用于金属加工、机械制造、航空航天等行业。
铰刀的设计需考虑切削力、切削速度、刀具材料等多方面因素,以确保其能有效地完成加工任务。
首先,铰刀的设计需考虑切削力的大小和方向。
切削力是指在铰削过程中,刀具对工件施加的力的大小和方向。
由于铰削是切削力沿刀具刃口方向分布的一种切削方式,因此,铰刀的刃口设计需使切削力能够平稳地分散到刀具的各个部位,以避免刀具的变形或破裂。
其次,铰刀的设计还需考虑切削速度。
切削速度是指刀具与工件相对运动的速度。
在铣削加工中,切削速度是刀具切入工件后,与工件接触并切削的速度。
切削速度的设计需考虑到刀具与工件材料的硬度、切削液的冷却效果等因素,以确保切削速度适中,避免过高或过低对刀具和工件的损伤。
此外,铰刀的设计还需考虑刀具材料的选择。
刀具材料的选择直接关系到刀具的使用寿命和切削效果。
常见的刀具材料包括高速钢、硬质合金、陶瓷等。
高速钢是最常见的刀具材料,具有较好的耐磨性和刚性,适用于切削低硬度的材料。
硬质合金则具有更高的硬度和耐磨性,适用于切削高硬度的材料。
陶瓷由于其高硬度和高耐磨性,广泛应用于高速切削和高温切削等领域。
最后,铰刀的设计还需考虑其他因素,如刀具的形状和数量等。
刀具的形状包括直刃铰刀、斜齿铰刀、凹槽铰刀等。
不同形状的刀具适用于不同的加工任务。
此外,工件的形状和尺寸也会影响刀具的选择与设计。
对于大型工件,可能需要使用多个刀具进行联合铰削,以提高加工效率。
综上所述,机用铰刀的设计需考虑多方面因素,如切削力、切削速度、刀具材料、刀具形状和数量等。
只有合理地设计铰刀,才能确保其在加工过程中能够稳定、高效地完成加工任务。
- 1、下载文档前请自行甄别文档内容的完整性,平台不提供额外的编辑、内容补充、找答案等附加服务。
- 2、"仅部分预览"的文档,不可在线预览部分如存在完整性等问题,可反馈申请退款(可完整预览的文档不适用该条件!)。
- 3、如文档侵犯您的权益,请联系客服反馈,我们会尽快为您处理(人工客服工作时间:9:00-18:30)。
根据型芯的结构特点, 拟定了下列四套加工方案:
加工, 不需要用电火花清角, 重复 24 次便可完成加工, 既
( 1) 方案 1: 立式数控加工
节约加工时间, 又节约加工成本。
将型芯放在回转工作台上分度, 用加长刀具加工凹
经过对比讨论, 决定采用第四套加工方案。从车加工
!!!!!!!!!!!!!!!!!!!!!!!!!!!!!!!!!!!!!!!!!!!!!!!!!!!!!!!!!
孔的最大直径: 19.5+0.013=19.513mm 孔公差( IT6) =0.013mm
d0 2%
工作部分
B
A
B
Hale Waihona Puke A颈部柄部
kr C×45°引 导 锥
切削部分 A- A
圆柱部分
倒锥
校准部分
B- B b$1
$0
图 1 铰刀的结构
孔公差之 15%( 0.15 IT6) =0.002mm 铰刀最大直径: d0max=19.513- 0.002=19.511mm 铰刀制造公差=孔公差 35%( 0.35 IT6) =0.005mm 铰刀最小直径: d0min=d0max- 0.35IT6=19.511- 0.005=19.506mm 由于预加工孔较深, 为便于排屑取硬质合金铰刀齿 数为 3。为制造方便, 刀齿平均分布。 3 铰刀主要几何参数设计及刃形设计 ( 1) 主偏角 kr 对于一般铰刀, 可把主偏角 kr 看成是 切削部分锥角 !。kr 角大小主要影响被加工孔的表面粗 糙度、精度及铰削时的轴向力的大小。kr 过大会使切削部 分长度太短, 造成铰刀工作时定位精度低; kr 过小会使切 削宽度加大, 切削厚度变小, 铰削韧性材料时会产生较大 的切屑变形, 锥角 ! 已在前面设定。 ( 2) 前角 "o 为了减小切屑变形, 取 "o=7°。 ( 3) 后角 #o、刃 带 b$1 铰 刀 属 精 加 工 刀 具, 为 使 其 重 磨后径向尺寸变化不太大, 取后角 6°。刃磨后角时, 切削 部分应磨尖而不留刃带, 而校准部分应留刃带, 以保证良 好的导向及修光作用, 为提高加工表面质量及铰刀寿命, 取 b$1=0.3mm。 汽轮机联接孔直径 D=19.5mm, 长度 L=80mm。由于 孔长度大, 须对常规铰刀的刃形结构进行改良来完成此
考虑到汽轮机联接孔的加工难度主要体现在孔的深 度大, 必须选用耐高温性能好的刀具材料。由于硬质合金 具有很高的硬度、耐磨损、耐高温、线膨胀率小等一系列优 点, 因此被用作刀具的主要材料。硬质合金的牌号很多, YW2 型号硬质合金密度约为 13.15~13.35×103kg/m3, 硬度 HRA91.5, 抗弯强度 1900MPa, 使用强度较高, 能承受较大 的冲击负荷。而且具有很高的高温硬度、高温强度和较强 的抗氧化能力, 适于耐热钢、高锰钢、不锈钢及优质合金钢 等的加工。故选用 YW2 型号硬质合金材料制作铰刀。 2 铰刀的主要结构要素设计
图 2 直刃铰刀实体模型
图 3 螺旋刃铰刀实体模型
5 两种刃形铰刀铰削切屑形态的对比分析 为了研究两种铰刀的铰削效果, 进行了切屑的搜集。
从图 4 到图 7 中可以看出, 随着切削用量的改变, 切屑形 态有明显的变化。首先, 在固定进给量 f=0.1mm/r, 工件材 料为 A3 钢的实验中, 直刃铰刀在主轴转速 550r/min, 就 呈现为颜色变蓝的短螺卷切屑。颜色变蓝是因为加工过 程中没有使用冷却液, 产生的大量切削热使切屑和空气 中的氧气发生了化学反应, 其中, 影响最大的因素是切削 速度的改变。螺旋刃铰刀在切削主轴转速为 760r/min, 进 给量 为 64mm/min, 切 屑 形 态 虽 然 也 发 生 了 变 化 , 颜 色 有 些发蓝但还没有直刃刀具那么严重。在主轴转速较低的 情况下, 两种刃形铰刀的切屑形状都呈现为螺旋卷切屑。 说明铰刀工作状态良好, 加工过程中没有产生过热的现 象。在固定转速的实验中, 由于主轴转速选定 760r/min, 在不使用冷却液的情况下, 对铰削过程是一个比较高的
81 机械工程师 2008 年第 3 期
直刃铰刀
解决方案
S OLUTION 工艺 / 工装 / 模具 / 诊断 / 检测 / 维修 / 改造
工序的加工。为了有更多的优化选择余地, 进行了铰刀的 直刃和螺旋刃两种刃形设计, 以便为后面的对比实验研 究与优化设计打下基础。 4 硬质合金铰刀 I- DEAS 软件实体建模
选择一种合适加工方法, 并介绍洗衣机脱水桶模具型芯凹坑加工的全过程。
关键词: 数控加工; 分度槽; 型芯凹坑
中图分类号: TG659
文献标识码: B
文章编号: 1002- 2333( 2008) 03- 0083- 02
本文主要以数控加工中心加工洗衣机脱水桶模具型芯 坑, 由于凹坑最长达 330mm, 刀 具 直 径 不 能 太 小, 否 则 刚
[ 参考文献] [ 1] 李振加, 等.切屑折断过程与槽形 CAD 专家系统[ M] .北京: 机械
40
64
120
147
进给量 f/mm·min-1
图 7 工件材料为 40Cr 钢, 固定转速情况下的切屑形态
转速, 刀具切削速度很大。如图 5 所示, 直刃铰刀的切屑 大多呈现发蓝发红的氧化现象, 而在图 6 中可以看到, 高 速下直刃铰刀形成了很长的连续切屑, 这将严重影响工 件的加工精度和表面质量。在加工 40Cr 钢的实验中, 螺 旋刃铰刀的切屑形态一直保持卷曲状切屑, 说明它工作 状 态 良 好 。 只 有 当 在 主 轴 转 速 760r/min, 进 给 量 达 到 147mm/min 的时候才出现较短较碎的切屑。这证明了螺 旋刃铰刀的切削性能确实优于直刃铰刀。
削外形后, 型芯上 24 条带 不好, 故不采用。
出模斜度的凹坑及 24 条 3mm 宽、3mm 深的筋位, 成为整
( 4) 方案 4: 在型芯底部加工分度槽, 简易夹具实现卧
套模具加工的难点所在。
式数控加工
型芯结构如图 2 所示。
首先在型芯车加工时在端面多留 10mm 余量, 以备
500 170
80
6结语
工业出版社, 1996.
结合生产需要, 选取了刀具材料, 进行了直刃和 螺 旋 [ 2] Ning, Y.Investigation of chip formation in high speed end milling
刃 铰 刀 的 设 计 并 利 用 I- DEAS 软 件 对 铰 刀 进 行 实 体 建 模。通过观察对比切屑形态, 发现螺旋刃铰刀的切屑形态 最优, 说明螺旋刃铰刀的切削状态良好, 切削性能最好。
82 机械工程师 2008 年第 3 期
解决方案
工艺 / 工装 / 模具 / 诊断 / 检测 / 维修 / 改造 S OLUTION
洗衣机脱水桶模具型芯凹坑加工
周敏, 朱晓川 ( 广东中山职业技术学院, 广东 中山 528404)
摘 要: 讨论介绍洗衣机脱水桶模具型芯凹坑加工方法: 主要根据工厂的设备实际, 经过对不同加工方法的分析比较,
解决方案
工艺 / 工装 / 模具 / 诊断 / 检测 / 维修 / 改造 S OLUTION
硬质合金铰刀的设计及其切削实验研究
杨家 勇 1, 王秀 英 1, 赵 平 2, 李 斌 1 ( 1.哈尔滨西岗齿轮机械有限公司, 黑龙江 宾县 150400; 2.哈尔滨理工大学 机械动力学院, 哈尔滨 150080)
在加工汽轮机联接孔时以前使用标准铰刀, 在国家 标准 GB4245- 84 中, 推荐用通用高速钢 W18Cr4V。由于 它的碳化物不均匀性大, 颗粒度粗, 降低了铰刀的机械性 能, 使刀具耐用度降低, 另外 W18Cr4V 冶金质量差, 热塑 性差, 在加工条件恶劣的情况下, 例如在加工汽轮机联接 深 孔( L/D>4) 时 , 产 生 的 高 热量 使 刀 具 的 硬 度 下 降 , 加 工 过程中排屑困难, 堵塞的切屑刮伤了已加工表面, 且另使 铰刀破损甚至折断。为了解决这一问题, 在对加工条件和 标准铰刀结构进行分析的基础上, 进行了硬质合金铰刀 的设计与开发研究工作。 1 刀具材料选择
镶件结构, 通过线切割和 允许。
普通数控加工即可完成
( 3) 方案 3: 回转工作台卧工数控加工
加 工 , 难 度 较 小。( 2) 型 芯
采用 L 形支承架将回转工作台竖直固定, 再平放装
( !350×500) 可整体加工, 车 夹型芯, 分度进行加工。由于型芯 重 达 300kg, 受 力 情 况 图1
摘 要: 在加工汽轮机联接孔时,由于被加工孔较深,堵塞的切屑易刮伤已加工表面;且由于堵塞的切屑挤压使铰刀破损
折断,所以进行了硬质合金铰刀的设计, 并根据实验合理优选铰刀。
关键词: 硬质合金; 铰刀; 建模; 切屑
中图分类号: TG713.4
文献标识码: A
文章编号: 1002- 2333( 2008) 03- 0081- 03
R400
于分度槽的加工, 在型芯底部按 360°等分加工 12 条分度
R30
A
R2
槽( 总共 24 个凹坑) 和一条基准边, 基准边的深度应和型