Ranger305D_CN林肯电焊机说明书
林肯电气熔炼机器人305G操作手册说明书

Ranger 305 GOPERATOR’S MANUALIM674August, 2001Copyright © 2001 Lincoln Global Inc.This manual covers equipment which is nolonger in production by The Lincoln Electric Co. Speci cations and availability of optional features may have changed.Mar ‘95Mar ‘95Mar. ‘93for selecting a QUALITY product by Lincoln Electric. We want you to take pride in operating this Lincoln Electric C ompany product ••• as much pride as we have in bringing this product to you!Read this Operators Manual completely before attempting to use this equipment. Save this manual and keep it handy for quick reference. Pay particular attention to the safety instructions we have provided for your protection.The level of seriousness to be applied to each is explained below:vvTECHNICAL SPECIFICATIONS - Ranger 305G (K1726-1)TIG WeldingThe TOUCH START TIG setting of the MODE switch is for DC TIG (Tungsten Inert Gas) welding. To initiate a weld, the C ONTROL dial is first set to the desired current and the tungsten is touched to the work. During the time the tungsten is touching the work there is very little voltage or current and, in general, no tungsten contamination. Then, the tungsten is gen-tly lifted off the work in a rocking motion, which estab-lishes the arc.The ARC CONTROL is not active in the TIG mode.The RANGER 305G can be used in a wide variety of DC TIG welding applications. In general the ‘Touch Start’ feature allows contamination free starting with-out the use of a Hi-frequency unit. If desired, the K930-2 TIG Module can be used with the RANGER 305G. The settings are for reference.RANGER 305G settings when using the K930-2 TIG Module with an Amptrol or Arc Start Switch:•Set the MODE Switch to the TOUC H START TIG setting.• Set the "IDLER" Switch to the "AUTO" position.• Set the "WELDING TERMINALS" switch to the "REMOTELY C ONTROLLED" position. This will keep the "Solid State" contactor open and providea "cold" electrode until the Amptrol or Arc StartSwitch is pressed.When using the TIG Module, the OUTPUT control on the RANGER 305G is used to set the maximum range of the CURRENT CONTROL on the TIG Module or an Amptrol if connected to the TIG Module.WIRE WELDING-CVConnect a wire feeder to the RANGER 305G accord-ing to the instructions in INSTALLATION INSTRUC-TIONS Section.The RANGER 305G in the CV-WIRE mode, permits it to be used with a broad range of flux cored wire (Innershield and Outershield) electrodes and solid wires for MIG welding (gas metal arc welding). Welding can be finely tuned using the ARC C ON-TROL. Turning the ARC C ONTROL clockwise from –10 (soft) to +10 (crisp) changes the arc from soft and washed-in to crisp and narrow. It acts as an induc-tance control. The proper setting depends on the pro-cedure and operator preference. Start with the dial set at 0.Some recommended Innershield electrodes are: NR-311, NS-3M, NR-207, NR-203 Ni 1%, NR-204-H. Recommended Outershield electrodes are: 0S-70, 0S-71M.Some recommended solid wires for MIG welding are: .035 (0.9 mm), and .045 (1.1 mm), L-50 and L-56, .035 (0.9 mm) and .045 (1.1 mm) Blue Max MIG 308 LS.For any electrodes, including the above recommenda-tions, the procedures should be kept within the rating of the machine.(1)When used with argon gas. The current ranges shown must be reduced when using argon/helium or pure helium shielding gases.(2) Tungsten electrodes are classified as follows by the American Welding Society (AWS):Pure EWP1% Thoriated EWTh-12% Thoriated EWTh-2Though not yet recognized by the AWS, Ceriated Tungsten is now widely accepted as a substitute for 2% Thoriated Tungsten in AC and DC applications.(3) DCEP is not commonly used in these sizes.(4) TIG torch nozzle "sizes" are in multiples of 1/16ths of an inch:# 4 = 1/4 in.(6 mm)# 5 = 5/16 in.(8 mm)# 6 = 3/8 in.(10 mm)# 7 = 7/16 in.(11 mm)# 8 = _ in.(12.5 mm)#10 = 5/8 in.(16 mm)(5) TIG torch nozzles are typically made from alumina ceramic. Special applications may require lava nozzles, which are less prone to breakage, but cannot withstand high temperaturesand high duty cycles.RANGER 305G Extension Cord Length Recommendations(Use the shortest length extension cord possible sized per the following table.)Current (Amps)1520152038VoltageVolts120120240240240Load(Watts)180024003600480090003060(9)(18)40307560(12)(9)(23)(18)755015010050(23)(15)(46)(30)(15)1258822517590(38)(27)(69)(53)(27)175138350275150(53)(42)(107)(84)(46)300225600450225(91)(69)(183)(137)(69)Maximum Allowable Cord Length in ft. (m) for Conductor SizeConductor size is based on manimum 2.0% voltage drop.14 AWG12 AWG10 AWG8 AWG 6 AWG 4 AWGOPTIONS/ACCESSORIES AND COM-PATIBLE LINCOLN EQUIPMENTK957-1 HEAVY DUTY, TWO WHEEL TRAIL ER FOR SMALL WELDERSFor road, off-road and in-plant and yard towing. (For highway use, consult applicable federal, state and local laws regarding requirements for brakes, lights, fenders, etc.).K1737-1 FOUR WHEEL ALL-TERRAIN UNDERCAR-RIAGE For moving by hand.K1770-1 UNDERCARRIAGE (FACTORY)For moving by hand on a smooth surface. One or two gas cylinders can be mounted on the rear of the undercarriage with the installation of K1745-1 Cylinder Holder(s).K1739-1 CABLE CARRIER KITFor use on K1737-1 and K1770-1 Undercarriages.K1745-1 SINGLE GAS CYLINDER HOLDERFor use on K1770-1 Undercarriage. One or two may be installed on an undercarriage.K1788-1 ROLL CAGE - Gives added damage protection. K886-2 CANVAS COVER - Protects machine when not in use. S24647 SPARK ARRESTORMounts inside exhaust pipe.K702 ACCESSORY KITAccessory set includes 35 ft. (10.7 meters) 2 AWG electrode cable, 30 ft. (9.1 meters) 2 AWG work cable, headshield with No. 12 filter, GC300 work clamp and Cooltong 300 electrode holder. Cables are rated at 250 amps, 40% duty cycle.K85728 ft (8.5m) or K857-1 100 ft. (30.4m) REMOTE CONTROLPortable control provides same dial range as the output control on the welder. Has a convenient 6 pin plug for easy connection to the welder.K1690-1 GFCI RECEPTACLE KITIncludes one UL approved 120V ground fault circuit interrupter duplex type receptacle with cover and installation instructions. Replaces the factory installed 120V duplex receptacle.Each receptacle of the GFCI Duplex is rated at 20 Amps, the maximum total current from the GFC I Duplex is limited to the 20 Amps.Two kits are required.K802-N POWER PLUG KITProvides four 120 volt plugs rated at 20 amps each and one dual voltage, full KVA plug rated at 120/240 volts, 50 amps.K802-R POWER PLUG KITProvides four 120 volt plugs rated at 15 amps each and one dual voltage, full KVA plug rated at 120/240 volts, 50 amps.T12153-9 50 AMP, 120/240 V POWER PLUGK1816-1 FULL KVA ADAPTER KITPlugs into the 120/240V NEMA 14-50R receptacle on the casefront (which accepts 4-prong plugs) and converts it to a NEMA 6-50R receptacle, (which accepts 3-prong plugs.)ENGINE MAINTENANCE COMPONENTSDrain the oil while the engine is warm to assure rapidand complete draining.• Remove the oil filler cap and dipstick. Remove theyellow cap from the oil drain valve and attach theflexible drain tube supplied with the machine. Pushin and twist the drain valve counterclockwise. Pullthe valve out and drain the oil into a suitablecontainer.• C lose the drain valve by pushing in and twistingclockwise. Replace the yellow cap.• Refill to the upper limit mark on the dipstick with therecommended oil. Tighten the oil filler cap securely. Engine Oil Refill CapacitiesWithout oil filter replacement:• 1.7 US qt. (1.4 Imp qt., 1.6 liter)-KohlerWith oil filter replacement:• 2.0 US qt. (1.7 Imp qt., 1.9 liter)-KohlerUse 4-stroke motor oil that meets or exceeds therequirements for API service classification SG or SH.Always check the API SERVICE label on the oil con-tainer to be sure it includes the letters SG or SH.SAE 10W-30 is recommended for general, all-temper-ature use, -5 F to 104 F (-20 C to 40 C). For the Onanengine, it is recommended that SAE 30 oil be usedabove 82 F (27 C).See Engine Owner’s Manual for more specific infor-mation on oil viscosity recommendations.Wash your hands with soap and water after handlingused oil.Please dispose of used motor oil in a manner that iscompatible with the environment. We suggest youtake it in a sealed container to your local service sta-tion or recycling center for reclamation. Do not throwit in the trash, pour it on the ground or down a drain. Oil Filter Change• Drain the engine oil.• Remove the oil filter, and drain the oil into a suitablecontainer. Discard the used oil filter.•Clean the filter mounting base, and coat the gasketof the new oil filter with clean engine oil.•Screw on the new oil filter by hand, until the gasketcontacts the filter mounting base, then use an oil fil-ter socket tool to tighten the filter an additional 1/2 to7/8 turn.This Troubleshooting Guide is provided to help you locate and repair possible machine malfunctions.Simply follow the three-step procedure listed below.Step 1.LOCATE PROBLEM (SYMPTOM).Look under the column labeled “PROBLEM (SYMP-TOMS)”. This column describes possible symptoms that the machine may exhibit. Find the listing that best describes the symptom that the machine is exhibiting.Step 2.POSSIBLE CAUSE.The second column labeled “POSSIBLE CAUSE” liststhe obvious external possibilities that may contribute to the machine symptom.Step 3.RECOMMENDED COURSE OF ACTIONThis column provides a course of action for the Possible C ause, generally it states to contact your local Lincoln Authorized Field Service Facility.If you do not understand or are unable to perform the Recommended C ourse of Action safely, contact your local Lincoln Authorized Field Service Facility.HOW TO USE TROUBLESHOOTING GUIDEService and Repair should only be performed by Lincoln Electric Factory Trained Personnel.Unauthorized repairs performed on this equipment may result in danger to the technician and machine operator and will invalidate your factory warranty. For your safety and to avoid Electrical Shock, please observe all safety notes and precautions detailed throughout this manual.__________________________________________________________________________JapaneseChineseKoreanArabicREAD AND UNDERSTAND THE MANUFACTURER’S INSTRUCTION FOR THIS EQUIPMENT AND THE CONSUMABLES TO BE USED AND FOLLOW YOUR EMPLOYER’S SAFETY PRACTICES.SE RECOMIENDA LEER Y ENTENDER LAS INSTRUCCIONES DEL FABRICANTE PARA EL USO DE ESTE EQUIPO Y LOS CONSUMIBLES QUE VA A UTILIZAR, SIGA LAS MEDIDAS DE SEGURIDAD DE SU SUPERVISOR.LISEZ ET COMPRENEZ LES INSTRUCTIONS DU FABRICANT EN CE QUI REGARDE CET EQUIPMENT ET LES PRODUITS A ETRE EMPLOYES ET SUIVEZ LES PROCEDURES DE SECURITE DE VOTRE EMPLOYEUR.LESEN SIE UND BEFOLGEN SIE DIE BETRIEBSANLEITUNG DER ANLAGE UND DEN ELEKTRODENEINSATZ DES HER-STELLERS. DIE UNFALLVERHÜTUNGSVORSCHRIFTEN DES ARBEITGEBERS SIND EBENFALLS ZU BEACHTEN.JapaneseChineseKoreanArabicLEIA E COMPREENDA AS INSTRUÇÕES DO FABRICANTE PARA ESTE EQUIPAMENTO E AS PARTES DE USO, E SIGA AS PRÁTICAS DE SEGURANÇA DO EMPREGADOR.。
林肯焊机说明书
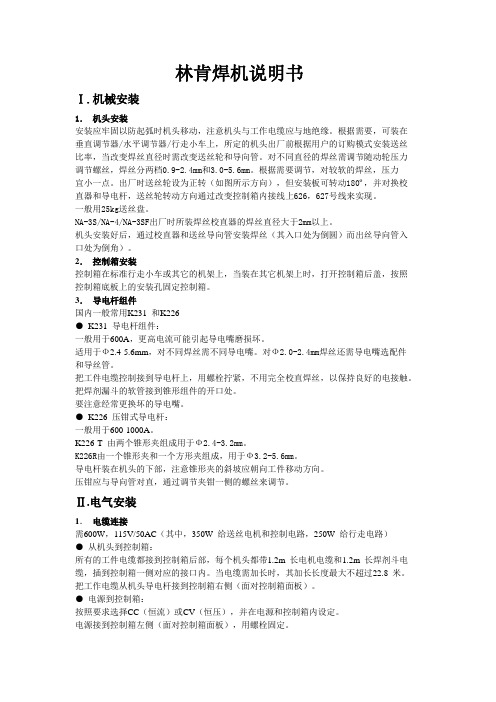
林肯焊机说明书Ⅰ.机械安装1.机头安装安装应牢固以防起弧时机头移动,注意机头与工作电缆应与地绝缘。
根据需要,可装在垂直调节器/水平调节器/行走小车上,所定的机头出厂前根据用户的订购模式安装送丝比率,当改变焊丝直径时需改变送丝轮和导向管。
对不同直径的焊丝需调节随动轮压力调节螺丝,焊丝分两档0.9-2.4mm和3.0-5.6mm。
根据需要调节,对较软的焊丝,压力宜小一点。
出厂时送丝轮设为正转(如图所示方向),但安装板可转动180º,并对换校直器和导电杆,送丝轮转动方向通过改变控制箱内接线上626,627号线来实现。
一般用25kg送丝盘。
NA-3S/NA-4/NA-3SF出厂时所装焊丝校直器的焊丝直径大于2mm以上。
机头安装好后,通过校直器和送丝导向管安装焊丝(其入口处为倒圆)而出丝导向管入口处为倒角)。
2.控制箱安装控制箱在标准行走小车或其它的机架上,当装在其它机架上时,打开控制箱后盖,按照控制箱底板上的安装孔固定控制箱。
3.导电杆组件国内一般常用K231 和K226●K231 导电杆组件:一般用于600A,更高电流可能引起导电嘴磨损坏。
适用于Ф2.4-5.6mm,对不同焊丝需不同导电嘴。
对Ф2.0-2.4mm焊丝还需导电嘴选配件和导丝管。
把工件电缆控制接到导电杆上,用螺栓拧紧,不用完全校直焊丝,以保持良好的电接触。
把焊剂漏斗的软管接到锥形组件的开口处。
要注意经常更换坏的导电嘴。
●K226 压钳式导电杆:一般用于600-1000A。
K226-T 由两个锥形夹组成用于Ф2.4-3.2mm。
K226R由一个锥形夹和一个方形夹组成,用于Ф3.2-5.6mm。
导电杆装在机头的下部,注意锥形夹的斜坡应朝向工件移动方向。
压钳应与导向管对直,通过调节夹钳一侧的螺丝来调节。
Ⅱ.电气安装1.电缆连接需600W,115V/50AC(其中,350W 给送丝电机和控制电路,250W 给行走电路)●从机头到控制箱:所有的工件电缆都接到控制箱后部,每个机头都带1.2m 长电机电缆和1.2m 长焊剂斗电缆,插到控制箱一侧对应的接口内。
林肯V350-PRO焊机产品说明书

E5.91PC Page 2 of 2 4/00
V350-PRO’s LED’s are bright and easy to read.
V350-PRO has easier set-ups.
Yes 5 modes
Similar.
V350-PRO has custom pipe welding output.
Arc control
Yes
Yes
Yes
Vt range.
V350-PRO has input voltage flexibility to go anywhere.
at 350 Amp output V350-PRO gives
50/25 Amps
power cost savings.
No. Handles on top. Machine hits knees when carrying
17 x 12.5 x 24
Weight
77 lbs.
76 lbs.
Thermal 400 GMS
Yes
Yes, Lift-Start™
Yes
No
Yes
Plastic overhang, no door protection Exposed on front
INVERTEC® V350-PRO
Designed Smart. Built Tough.
Feature
Output 3 Phase
Lincoln Invertec V350-PRO
350 Amps, 34 Volts 60% Duty Cycle
林肯电焊机操作手册说明书
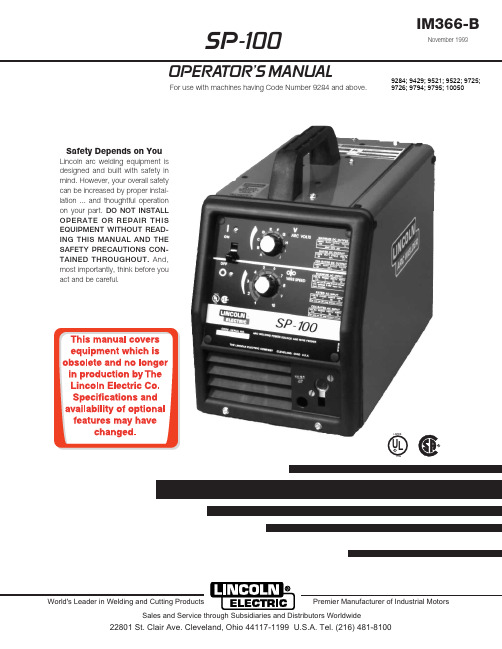
SP-100OPERA TOR'S MANUALFor use with machines having Code Number 9284 and above .Sales and Service through Subsidiaries and Distributors WorldwideWorld's Leader in Welding and Cutting Products Premier Manufacturer of Industrial MotorsIM366-BNovember 1993Safety Depends on YouLincoln arc welding equipment is designed and built wit h safet y in mind. However, your overall safety can be increased by proper instal-lat ion ... and t hought ful operat ion on your part.DO NOT INSTALL OPERATE OR REPAIR THIS EQUIPMENT WITHOUT READ-ING THIS MANUAL AND THE SAFETY PRECAUTIONS CON-TAINED THROUGHOUT.And,most importantly, think before you act and be careful.9284; 9429; 9521; 9522; 9725;9726; 9794; 9795; 10050Thank Youfor selecting a QUALITY product by Lincoln Electric.We want you to take pride in operating this Lincoln Electric C ompany product ••• as much pride as we have in bringing this product to you!Read this Operators Manual completely before attempting to use this equipment. Save this manual and keep it handy for quick reference. Pay particular attention to the safety instructions we have provided for your protection. The level of seriousness to be applied to each is explained below:PRODUCT DESCRIPTIONThe SP-100, Type K462, is a complete semiautomatic constant voltage DC arc welding machine. Included is a solid state controlled, single phase constant voltage transformer/ rectifier power source and a wire feeder for feeding .023 – .030" (0.6 – 0.8 mm) solid steel electrode and .035" (0.9 mm) cored electrode.The SP-100 is ideally suited for individuals having access to 115 volt AC input power, and wanting the ease of use, quality and dependability of both gas metal arc welding or GMAW (also known as MIG welding) and the Innershield®electrode process (self-shielded flux-cored or FC AW). A convenient chart is mounted inside the wire feed section door for setting welding procedures for 24 gauge through 12 gauge (0.6 – 2.5 mm) mild steel (Chart also may be found in this manual). The SP-100 is a rugged and reliable machine that has been designed for dependable ser-vice and long life.RECOMMENDED PROCESSES AND EQUIPMENTThe SP-100 can be used for welding mild steel using the GMAW, single pass, process which requires a supply of shielding gas or it can be used for the self-shielded, Innershield electrode process.The recommended gas and electrode for GMAW is welding grade CO2gas and .025" (0.6 mm) diameter Lincoln L-56 mild-steel welding wire [supplied on 12 1/2 lb (6 kg) spools]. For 14 gauge (2.0 mm) and thin-ner, CO2gas is recommended because it gives equal or better performance than a blended gas at a lower cost. A mixed gas consisting of 75 to 80% Argon and 20 to 25% CO2is recommended for welding on heav-ier gauge [12 gauge (2.5 mm) for example] steel.The recommended electrode for the self-shielded process is .035" (0.9 mm) diameter Lincoln Innershield NR-211-MP on 10 lb (4.5 kg) spools. This electrode can be used for all position welding of 20 gauge through 5/16" (1.0 – 8.0 mm) thick steel [multi-ple passes are required for 1/4" and 5/16" (6.0 and 8.0 mm)].OPTIONAL ACCESSORIES1.K463 CO2G as Regulator and Hose Kit—Includes a preset, nonadjustable pressure and flow regulator for use on C O2cylinders. Also included is a 10 foot (3.0 m) gas hose which con-nects to the rear of the SP-100.2.K499 Ar-Mixed Gas Regulator and Hose Kit—Includes a preset, nonadjustable pressure and flow regulator for use on argon-mixed gas cylin-ders. Also included is a 10 foot (3.0 m) gas hose which connects to the rear of the SP-100.3..035 (0.9 mm) Innershield®Welding Kit —Includes a contact tip, a gasless nozzle and a cable liner to permit the SP-100 gun and cable to use a .035" (0.9 mm) diameter flux-cored elec-trode. Also included is a spool of .035 (0.9 mm) Innershield®NR-211-MP.Two kits are available:K549-1 kit is for use with the Magnum™100L gun (with red trigger).K464 kit is for use with the original Lincoln Electric®gun (with black trigger).4.M15448-1 Reversible Drive Roll with doubleknurled grooves for .035 cored electrode.5.K467 Input Line Cord — Same as line cord sup-plied with the SP-100 but has a NEMA type 5-20P plug for use on 25 amp branch circuits.To install optional features refer to instructions included with the kit, and/or in this manual.INSTALLATIONDESCRIPTION OF CONTROLSBecome familiar with the SP-100 controls and compo-nents before attempting to weld. Refer to illustrations and lettered items below for brief descriptions.A.Wire speed — Controls the wire speed from 50 –400 in./min (1.3 – 10 m/min). The control can be preset on the dial to the setting specified on the SP-100 Application Chart located on the inside of the wire feed section door. Wire speed is not affected when changes are made in the voltage control. The control is marked (“olo”)B.Power ON/OFF switch — When the power is on,the fan motor will run and air will be exhausted out the louvers in the front of the machine. The welding output and wire feeder remain off until the gun trigger is pressed.C.Voltage control — A continuous control that givesfull range adjustment of power source output volt-age. Can be adjusted while welding.D.Thumbscrew — secures gun and cable assembly.E.Positive (+) and negative (–) output terminals.F.Shielding gas hose (factory installed, not shown)— routed from gas solenoid inside rear of machine to gun connector block.G.Gun trigger lead connectors.H.Circuit breaker — Protects machine from damageif maximum output is exceeded. Button will extend out when tripped. (Manual reset.)I.Wire spool spindle.J.Gas solenoid inlet fitting.K.Power cord.L.Spring loaded pressure arm — adjusts pressureof idle roll on wire.M.Wire feed gearbox and gun connector block.N.Wire feed section door — With application chartfor machine setting procedures.O.Gun cable and control lead access hole.P.Work cable access hole.LOCATIONLocate the welder in a dry location where there is free circulation of clean air into the louvers in the back and out the front. A location that minimizes the amount of smoke and dirt drawn into the rear louvers reduces the chance of dirt accumulation that can block air pas-sages and cause overheating.WORK CABLE AND CLAMP INSTALLATIONWork Clamp InstallationAttach the work clamp to the work cable per the fol-lowing:1.Unplug the machine or turn the power switch to the “Off” position.2.Insert the work cable terminal lug with the larger hole through the strain relief hole in the work clamp as shown below.3.Fasten securely with the bolt and nut provided.Work cableWork clampWork Cable Installation1.Open the wire feed section door on the right side ofthe SP-100.2.Pass the end of the work cable that has the termi-nal lug with the smaller hole through the hole (holeD) next to the louvers in the case front.3.Route the cable under and around the back of thewire feed unit.ing wing nut provided, connect the terminal lugto the negative (–) output terminal located above the wire feed unit; item M (make certain that both wing nuts are tight).NOTE: This connection gives the correct electrode polarity for the GMAW process. If using Innershield, see Output Polarity C onnection Section below for negative electrode polarity connection. OUTPUT POLARITY CONNECTIONThe SP-100, as shipped, is connected for positiveelectrode polarity.To connect for negative electrode polarity (required for the Innershield process), connect the short cable attached to the gun connector block to the negative (–) output terminal and the work cable to the positive (+) terminal using the provided wing nuts (make cer-tain that both wing nuts are tight).GUN INSTALLATIONAs shipped from the factory, the SP-100 gun is ready to feed .023, .024 or .025" (0.6 mm) wire. If .030" (0.8 mm) wire is to be used, install the .030" (0.8 mm) con-tact tip. .023 – .025" contact tip is stenciled .025 and/or 0.6 mm and .030" contact tip is stenciled .030 and/or 0.8 mm. See Maintenance Section for instruc-tions to change contact tip.If .035" (0.9 mm) Innershield flux cored wire is to be used, see Maintenance Section for instructions to change contact tip, cable liner, and gas nozzle.C onnect the gun cable to the SP-100 per the follow-ing:1.Unplug the machine or turn power switch to the off“O” position.2.Pass the insulated terminals of the gun trigger con-trol leads, one at a time, through the rectangular “keyhole” opening (item F) in the case front. The leads are to be routed under the wire feed unit and through the cable hanger on the inner panel.3.Insert the connector on the gun conductor cablethrough the large hole in the SP-100 case front.Make sure the connector is all the way in the metal connector block to obtain proper gas flow. Rotate the connector so control leads are on the underside and tighten the thumbscrew in the connector block.4.Connect the insulated control lead terminals to thetwo insulated 1/4" (6.4 mm) tab connector bushings located above the “Gun Trigger C onnection” decal in the wire feed section. Either lead can go to either connector. Form the leads so that they are as close as possible to the inside panel.WIRE FEED DRIVE ROLLThe SP-100 drive roll has two grooves; one for .023 –.025" (0.6 mm) solid steel electrode and the other for .030" (0.8 mm) solid and .035" (0.9 mm) flux-cored steel electrode. As shipped, the drive roll is installed in the .023/.025" (0.6 mm) position (as indicated by the stenciling on the exposed side of the drive roll).Replace the washer and retaining screw.connectors{Brass connectorIdle roll armRetaining ScrewWELDING WIRE LOADINGThe machine power switch should be turned to the OFF (“O”) position before working inside the wirefeed enclosure.------------------------------------------------------------------------The machine is shipped from the factory ready to feed 8" (200 mm) diameter spools [2.2" (56 mm) max. width]. These spools fit on a 2" (50 mm) diameter spindle that has a built-in, adjustable* friction brake to prevent overrun of the spool and excess slack in theWARNINGK499 Argon-Mixed Gas Regulator and Hose Kit Install the pressure-flow regulator and gauge to a cylinder according to the instructions in Section 1.10.C onnect one end of the 10 foot (3.0 m) hose to the SP-100 gas inlet fitting and the other end to the regu-lator fitting.The K499 argon-mixed gas pressure-flow regulator is preset by the manufacturer to deliver a nominal flow of 30 cubic feet per hour (14 1/min) of argon or argon-mixed gas. This setting cannot be changed..035" (0.9 mm) Innershield Welding KitIncludes a contact tip, gasless nozzle, and a cable liner to permit the SP-100 gun and cable to use .035 (0.9 mm) diameter flux-cored electrode. Also included is a spool of .035 (0.9 mm) Innershield®NR-211-MP. The K549-1 Kit is for use with the Magnum™100L gun (with red trigger). The fitting on the end of the liner is stenciled with the maximum rated wire size (.045"/1.2 mm).The K464 Kit is for use with the earlier “Lincoln Electric®” gun (with black trigger). The end of the brass fitting on the end of the liner for .035 (0.9 mm) wire is color coded green. The .023-.030 (0.6-0.8 mm) factory installed liner is color coded orange.See Maintenance and Troubleshooting Section for instructions on installing liner and contact tip in gun.K467 Input Line CordSame as line cord supplied with the SP-100 but has a NEMA type 5-20P plug for use on a 25 amp branch circuit with a nominal voltage rating of 115 volts to 125 volts, 60 hertz. Install per the following:1.Turn the SP-100 Power Switch to OFF (“O”).2.If connected, remove the line cord plug from powersupply receptacle.3.Remove the two screws that hold the line cordreceptacle in the SP-100 flanged inlet connector and disconnect the line cord from the SP-100.4.C onnect the S18410 input line cord receptacle tothe SP-100 and replace the retaining screws.OPERATING INSTRUCTIONS1.Decrease stickout2.Increase WFS (wire feed speed) (“oIo”)3.Decrease voltage (“V”)4.Increase speed5.Decrease drag angle6.Check for correct gas, if usedIf Arc Blow Occurs (in order of importance) (NOTE: Try different ground connection locations before adjusting procedures)1.Decrease drag angle2.Increase stickout3.Decrease voltage (“V”)4.Decrease WFS (wire feed speed) (“oIo”) andvoltage (“V”)5.Decrease travel speedTo Eliminate Stubbing (in order of importance)1.Increase voltage (“V”)2.Decrease WFS (wire feed speed) (“oIo”)3.Decrease stickout4.Increase drag angleStubbing occurs when the electrode drives through the molten puddle and hits the bottom plate tending to push the gun up.PROPER GUN HANDLINGMost feeding problems are caused by improper han-dling of the gun cable or electrodes.1.Do not kink or pull the gun cable around sharp cor-ners.2.Keep the gun cable straight as practical when weld-ing.3.Do not allow dolly wheels or trucks to run over thecables.4.Keep the cable clean per maintenance instructionsin this Operation Manual.5.Innershield electrode has proper surface lubrica-tion. Use only clean, rust-free electrode.6.Replace the contact tip when it becomes worn orthe end is fused or deformed.Low or no gas flow Cylinder valve closed Open cylinder valveGas flow not set correctly Set proper flow rateCylinder out of gas Get new cylinder of gasLeak in gas line Inspect and replaceClog or Leak in gun Check for obstruction or defective sealsArc unstable Wrong welding polarity Check polarity - Refer to proper sectionErratic or Intermittent Wrong size, worn and/or Replace tip - remove any spatter on end of tip Arc - Poor Starting melted contact tip"Hunting" ArcWorn work cable or poor connections Inspect - repair or replace as necessaryLoose electrode connections Be sure electrode lead is tight, gun cable tight inwire feeder contact block, gun nozzle and guntip tightM 16576S P 100 W I R I N G D I A G R A MNow Available...12th Edition The Procedure Handbook of Arc WeldingWith over 500,000 copies of previous editions publishedsince 1933, the Procedure Handbook is considered by many tobe the “Bible” of the arc welding industry.This printing will go fast so don’t delay. Place yourorder now using the coupon below.The hardbound book contains over 750 pages of weldinginformation, techniques and procedures. Much of this materialhas never been included in any other book.A must for all welders, supervisors, engineers anddesigners. Many welding instructors will want to use the bookas a reference for all students by taking advantage of the lowquantity discount prices which include shipping by4th class parcel post.$15.00postage paid U.S.A. Mainland How To Read Shop Drawings The book contains the latest information and application data on the American Welding Society Standard Welding Symbols. Detailed discussion tells how engineers and draftsmen use the “short-cut” language of symbols to pass on assembly and welding information to shop personnel.Practical exercises and examples develop the reader’s abilityto visualize mechanically drawn objects as they will appearin their assembled form.187 pages with more than 100 illustrations. Size 8-1/2” x 11”Durable, cloth-covered board binding.$4.50postage paid U.S.A. Mainland New Lessons in Arc Welding Lessons, simply written, cover manipulatory techniques;machine and electrode characteristics; related subjects,such as distortion; and supplemental information on arc welding applications, speeds and costs. Practice materials,exercises, questions and answers are suggested for each lesson.528 pages, well illustrated, 6” x 9” size, bound in simulated,gold embossed leather.$5.00postage paid U.S.A. Mainland Need Welding Training?The Lincoln Electric Company operates the oldest andmost respected Arc Welding School in the United States at itscorporate headquarters in Cleveland, Ohio. Over 100,000stu-dents have graduated. Tuition is low and the training is“hands on”For details write: Lincoln Welding School 22801 St. Clair Ave.Cleveland, Ohio 44117-1199.and ask for bulletin ED-80 or call 216-383-2259 and ask for the Welding School Registrar.Lincoln Welding School BASIC COURSE$700.005 weeks of fundamentals There is a 10%discount on all orders of $50.00 or more for shipment at one time to one location.Orders of $50 or less before discount or orders outside of North America must be prepaid with charge, check or money order in U.S. Funds Only.Prices include shipment by 4th Class Book Rate for U.S.A. Mainland Only.Please allow up to 4 weeks for delivery.UPS Shipping for North America Only.All prepaid orders that request UPS shipment please add:$5.00For order value up to $49.99$10.00For order value between $50.00 & $99.99$15.00For order value between $100.00 & $149.00For North America invoiced orders over $50.00 & credit card orders, if UPS is requested, it will be invoiced or charged to you at cost.Outside U.S.A. Mainland order must be prepaid in U.S. Funds. Please add $2.00 per book for surface mail or $15.00 per book for air parcel post shipment.METHOD OF PAYMENT:(Sorry, No C.O.D. Orders)CHECK ONE:Name:_______________________________________________Please Invoice (only if order is over $50.00)Address:_______________________________________________Check or Money Order Enclosed, U.S. Funds only_______________________________________________Credit Card - Telephone:_______________________________________________Signature as it appears on Charge Card:Account No.Exp Date |_|_||_|_|______________________Month Year USE THIS FORM TO ORDER:Order from:BOOK DIVISION, The Lincoln Electric Company, 22801 St. Clair Avenue, Cleveland, Ohio 44117-1199BOOKS OR FREE INFORMATIVE CATALOGSTelephone: 216-383-2211 or, for fastest service, FAX this completed form to: 216-361-5901.Lincoln Welding School Titles:Price Code Quantity Cost (ED-80)New Lessons in Arc Welding $5.00L Seminar Information Procedure Handbook “Twelfth Edition”$15.00PH (ED-45)How to Read Shop Drawings $4.50H Educational Video Information Incentive Management $5.00IM (ED-93)A New Approach to Industrial Economics $5.00NA James F. Lincoln Arc WeldingThe American Century of John C. Lincoln $5.00AC Foundation Book Information Welding Preheat Calculator $3.00WC-8(JFLF-515)Pipe Welding Charts $4.50ED-89SUB TOTALAdditional Shipping Costs if anyTOTAL COSTJapaneseChineseKoreanArabicREAD AND UNDERSTAND THE MANUFACTURER’S INSTRUCTION FOR THIS EQUIPMENT AND THE CONSUMABLES TO BE USED AND FOLLOW YOUR EMPLOYER’S SAFETY PRACTICES.SE RECOMIENDA LEER Y ENTENDER LAS INSTRUCCIONES DEL FABRICANTE PARA EL USO DE ESTE EQUIPO Y LOS CONSUMIBLES QUE VA A UTILIZAR, SIGA LAS MEDIDAS DE SEGURIDAD DE SU SUPERVISOR.LISEZ ET COMPRENEZ LES INSTRUCTIONS DU FABRICANT EN CE QUI REGARDE CET EQUIPMENT ET LES PRODUITS A ETRE EMPLOYES ET SUIVEZ LES PROCEDURES DE SECURITE DE VOTRE EMPLOYEUR.LESEN SIE UND BEFOLGEN SIE DIE BETRIEBSANLEITUNG DER ANLAGE UND DEN ELEKTRODENEINSATZ DES HER-STELLERS. DIE UNFALLVERHÜTUNGSVORSCHRIFTEN DES ARBEITGEBERS SIND EBENFALLS ZU BEACHTEN.JapaneseChineseKoreanArabicLEIA E COMPREENDA AS INSTRUÇÕES DO FABRICANTE PARA ESTE EQUIPAMENTO E AS PARTES DE USO, E SIGA AS PRÁTICAS DE SEGURANÇA DO EMPREGADOR.(such as loss of business, etc.) caused by the defect or Sales and Service through Subsidiaries and Distributors Worldwide22801 St. Clair Ave. Cleveland, Ohio 44117-1199 U.S.A. Tel. (216) 481-8100Premier Manufacturer of Industrial Motorsd。
林肯电焊机说明书

MAGNUM® PRO ROBOTIC GUNS DESIGNED FOR LONG LIFE.Thru-ArmExternal DressPublication E12.03 | Issue Date 07/24/20• Patented HexConnect ™ Gun Bushing- Delivers superior mechanical and electrical connectionresulting in longer expendable life. - Resists twisting and provides more points of contactfor current flow.• Fixed Electrical Connection- Robust design resists fatigue - Lasted over 1 milliontortuous flex cycles in extreme lab testing. - Competitive rotating designs can cause micro-arcingresulting in arc instability and potential shorter gun life.Tough Teflon ® Insulation• Single Tool Center Point (TCP) - No need to re-programwhen switching between the Magnum ® PRO 350 and 550 amp expendables.• Contact Tip Technology - Copper Plus ™ - more copper for better heat dissipation.- Anti-Seize ™ thread design on contact tips and diffuser.• Aluminum- Aircraft grade aluminum outer tube extends service.• Copper- High quality copper inner tube enhances electrical conductivity.Contact Tip for up to 550 AMagnum ®PRO 550 A ExpendablesGun Tube Insulator 550 A(1) 550 only350 A and 550 A Magnum ® PRO Expendable Parts are interchangeable. Interchanging will require gun tube insulator and gas diffuser changes. Customersmay choose to change expendable parts to standardize stocking parts or to make the gun more compact for tight spaces.(2)(2)Gas Diffuser for up to 550 A Slip-onGas Diffuser for up to 550 AThread-on (2) Jump liners and wire guides are only used on Thru-arm torches with wire brake.Gas Nozzlefor 550Thread-on 1/8 in. (3.2 mm) RecessedBottleneck Gas Nozzle for 550Thread-on 1/8 in. (3.2 mm)RecessedGENERAL OPTIONSRobotic Gun Tube Straightener Used in the event of a robot crash to check and correct robotic gun tube alignment. OrderK3193-1(Compatible with all standard KP3056-XX and KP3057-XX gun tubes)K3193-2(Compatible with all standard KP3354-XX and KP3355-XX gun tubes)EXTERNAL DRESS OPTIONS External Dress Torch Mounting KitsDesigned to mount the External Dress torch in the proper orientation for the application and fixturing presented to the robot. Consult Automation Division for correct mounting kit selection assistance. OrderKP2769-2222 Degree – Lincoln Electric Tool Center Point (TCP)KP2769-4545 Degree – Lincoln Electric Tool Center Point (TCP)KP2769-180180 Degree – Lincoln Electric Tool Center Point (TCP)KP3054-2222 Degree – Tregaskiss ® TCP, FANUC ® Solid Mount KP3055-2222 Degree – Tregaskiss ® TCP, Tregaskiss ® Clutch Mount KP3499-2222 Degree - Lincoln Electric Tool Center Point (TCP)for ABB and KUKA Robot Arms KP3499-4545 Degree - Lincoln Electric Tool Center Point (TCP)for ABB and KUKA Robot Arms KP3499-180180 Degree - Lincoln Electric Tool Center Point (TCP)for ABB and KUKA Robot ArmsExternal Dress Break-Away Disks Replaceable mounting interface disk designed to protect the robot arm by absorbing the effects of any damage in the event of a robot work envelope collision. OrderKP3194-1External Dress Break-Away Disk (Fanuc iB)KP3194-2External Dress Break-Away Disk (Fanuc 50 iC)KP3194-3External Dress Break-Away Disk (Fanuc iC)KP3194-4External Dress Break-Away Disk(ABB2600)KP3194-5External Dress Break-Away Disk(KR6, KR8, KR10)THRU-ARM OPTIONSThru-Arm Break-Away Disks Replaceable mounting interface disk designed to protect the robot arm by absorbing the effects of any damage in the event of a robot work envelope collision.See specification chart below for correct part number rWire Brake PlugPlug when removing wire brake from K4307-2 Order K3563-1Nose Cone Assemblies See specification chart below for correct part numberTorch HousingsSee specification chart below for correct part numberAir Blast KitBlows spatter from the nozzle orifice. Includes 20 ft (6.1 m) hose and fitting. Order K3352-1Thru-Arm Replacement Cable AssembliesSee specification chart below for correct part numberK466-10(1) K1500-3 Gun Receiver Bushing is required for Power Feed 10 series, LF series and LN-25 PRO wire feeders.(2)Terms are tradmarks of Illinois Tool Works.[3]Included with External Dress Torch [4]Included with Thru-Arm Torch(3)(3) Note that external dress guns include a 22 degree Lincoln Electric TCP gooseneck,liner and consumables. Mounting kit is not included.®®®®®®The Lincoln Electric Company22801 St. Clair Avenue • Cleveland, OH • 44117-1199 • U.S.A.C USTO ME R ASSI STA NC E PO LICYThe business of The Lincoln Electric Company ® is manufacturing and selling high quality welding equipment, consumables, and cutting equipment. Our challenge is to meet the needs of our customers and to exceed their expectations. On occasion, purchasers may ask Lincoln Electric for information or advice about their use of our products. Our employees respond to inquiries to the best of their ability based on information provided to them by the customers and the knowledge they may have concerning the application. Our employees, however, are not in a position to verify the information provided or to evaluate the engineering requirements for the particular weldment. Accordingly, Lincoln Electric does not warrant or guarantee or assume any liability with respect to such information or advice. Moreover, the provision of such information or advice does not create, expand, or alter any warranty on our products. Any express or implied warranty that might arise from the information or advice, including any implied warranty of merchantability or any warranty of fitness for any customers’ particular purpose is specifically disclaimed.Lincoln Electric is a responsive manufacturer, but the selection and use of specific products sold by Lincoln Electric is solely within the control of, and remains the sole responsibility of the customer. Many variables beyond the control of Lincoln Electric affect the results obtained in applying these types of fabrication methods and service requirements.Subject to Change – This information is accurate to the best of our knowledge at the time of printing. Please refer to for any updated information.For best welding results with Lincoln Electric equipment, always use Lincoln Electric consumables. Visit for more detail.All trademarks and registered trademarks are the property of their respective owners.。
林肯电气Bester热带车道500S电焊机操作指南说明书

IM304109/2016REV03HOT ROD 500S OPERATOR’S MANUALENGLISHLincoln Electric Bester Sp. z o.o.ul. Jana III Sobieskiego 19A, 58-263 Bielawa, Polandwww.lincolnelectric.euDeclaration of conformityLincoln Electric Bester Sp. z o.o.Declares that the welding machine:K14089-2 HOT ROD 500S 220/380/440Vconforms to the following directives:2014/35/EU , 2014/30/EUand has been designed in compliance with thefollowing standards:EN 60974-1:2012; EN 60974-10:201420.04.2016Piotr SpytekOperations DirectorLincoln Electric Bester Sp. z o.o., ul. Jana III Sobieskiego 19A, 58-263 Bielawa, Poland12/0512/05 THANKS! For having chosen the QUALITY of the Lincoln Electric products.∙Please Examine Package and Equipment for Damage. Claims for material damaged in shipment must be notified immediately to the dealer.∙For future reference record in the table below your equipment identification information. Model Name, Code & Serial Number can be found on the machine rating plate.Model Name: ………………………………………………………………………………………………………………………………………….Code & Serial Number: ………………………………………………………………….. …………………………………………………………………..Date & Where Purchased …………………………………………………………………. …………………………………………………………………..ENGLISH INDEXSafety (1)Installation and Operator Instructions (2)Electromagnetic Compatibility (EMC) (6)Technical Specifications (7)WEEE (8)Spare Parts (8)Electrical Schematic (8)Accessories (8)Safety11/04WARNINGThis equipment must be used by qualified personnel. Be sure that all installation, operation, maintenance and repair procedures are performed only by qualified person. Read and understand this manual before operating this equipment. Failure to follow the instructions in this manual could cause serious personal injury, loss of life, or damage to this equipment. Read and understand the following explanations of the warning symbols. Lincoln Electric is not responsible for damages caused by improper installation, improper care or abnormal operation.The manufacturer reserves the right to make changes and/or improvements in design without upgrade at the same time the operator’s manual.Installation and Operator InstructionsRead this entire section before installation or operation of the machine.Location and EnvironmentThe HOT ROD 500S welders can be stacked three high when the following precautions are observed: ∙ Be sure the bottom machine is on a firm, levelsurface suitable for the total weight (610kg) of the stacked machines.∙ Stack the machine with the fronts flush.∙ Be certain the pins on the top font corners of thelower machines fit through the holes in the base rails of the upper machines.This machine will operate in harsh environments. However, it is important that simple preventativemeasures are followed to assure long life and reliable operation:∙ Do not place or operate this machine on a surfacewith an incline greater than 15° from horizontal. ∙ Do not use this machine for pipe thawing.∙ This machine must be located where there is freecirculation of clean air without restrictions for air movement to and from the air vents. Do not cover the machine with paper, cloth or rags when switched on.∙ Dirt and dust that can be drawn into the machineshould be kept to a minimum.∙ This machine has a protection rating of IP23. Keep itdry when possible and do not place it on wet groundor in puddles.∙ Locate the machine away from radio controlledmachinery. Normal operation may adversely affect the operation of nearby radio controlled machinery, which may result in injury or equipment damage. Read the section on electromagnetic compatibility in this manual.∙ Do not operate in areas with an ambient temperaturegreater than 55°C.Duty cycle and OverheatingThe duty cycle of a welding machine is the percentage of time in a 10 minute cycle at which the welder can operate the machine at rated welding current.Example: 60% duty cycle:Welding for 6 minutesBreak for 4 minutesExcessive extension of the duty cycle will cause the thermal protection circuit to activate.The machine is protected from overheating by a temperature sensor.When the machine is overheated the output of themachine will turn "OFF", and the Thermal Indicator Light will turn "ON". When the machine has cooled to a safe temperature the Thermal Indicator Light will go out and the machine may resume normal operation.Minutes or decrease duty cycleInput Supply ConnectionCheck the input voltage, phase, and frequency supplied to this machine before turning it on. Verify theconnection of grounding wires from the machine to the input source. The allowable input voltages are 3x220V 50/60Hz, 3x380V 50/60Hz and 3x440V 50/60Hz(3x440V: factory default). For more information about input supply refer to the technical specification section of this manual and to the rating plate of the machine.If it is necessary to change the input voltage:∙ The input cable must be disconnected from themains supply and the machine switched OFF.Cable length Up to 10 m 10 – 50 m 50 – 75 m Cable size 70 mm 2 95 mm 2120 mm 2control is used to set the level of the increased current and arc start current is made easy. electrode and the workpiece. welding it continues to display the average welding current and voltage for 5 seconds.8. Welding Current Knob Control:Potentiometer used to set the output current on the range 50A - 625A (alsoduring welding).9. Local/Remote Switch: Remote Control Unit K10095-1-15M and K870 can be used with this machine. Itchanges control of the Output Current from themachine Welding Current [8] to the K10095-1-15M or K870 and vice versa.10. Remote Control Connector: If a remotecontrol is used, it will be connected to the remote connector (see "Accessories"chapter).11. Negative Output Terminal: Negative14applicable standards. This connection shall be performed only by a qualified person.Welding SMAW (MMA) ProcessHOT ROD 500S does not include the electrode holder with lead necessary and the work lead for SMAWwelding, but the one can be purchased separately (see "Accessories" chapter).For starting welding process with SMAW process you should:∙ First turn the machine off.∙ Determine the electrode polarity for the electrode tobe used. Consult the electrode data for this information.∙ Depending on the polarity of using electrode,connect the work lead and the electrode holder with lead to output socket [11] or [12] and lock them. See the Table 1.Table 1.Output socketP O L A R I T YD C (+) The electrode holderwith lead to SMAW[12] Work lead [11] D C (-) The electrode holder with lead to SMAW[11] Work lead[12]IOff CONTROL DIALS Hot Start OUTPUT CURRENT CONTROL RANGE SWITCH LOW Output Current Control Dial Range LowHIGH Output Current Control Dial Range HighOUTPUT CURRENT CONTROL "MACHINE-REMOTE" SWITCHRemote Output Current ControlMachine Output Current ControlRATING PLATEThree Phase PowerTransformer RectifierRectifier DC OutputConstant Current Characteristic Shielded Metal Arc Welding Line ConnectionHIGH TEMPERATURE WARNING LIGHTHigh Temperature LimitWARNINGWarning IdentificationGROUNDSignifying the Earth (Ground) ConnectionMaintenanceWARNINGFor any repair operations, modifications ormaintenances, it is recommended to contact the nearest Technical Service Center or Lincoln Electric. Repairs and modifications performed by unauthorized service or personnel will cause, that the manufacturer’s warranty will become null and void.Any noticeable damage should be reported immediately and repaired.Routine maintenance (everyday)∙ Check condition of insulation and connections of thework leads and insulation of power lead. If any insulation damage exists replace the lead immediately.∙ Check the welding gun condition: replace it, ifnecessary.∙ Check condition and operation of the cooling fan.Keep clean its airflow slots.Periodic maintenance (every 200 working hours but at list once every year)Perform the routine maintenance and, in addition: ∙ Keep the machine clean. Using a dry (and lowpressure) airflow, remove the dust from the external case and from the cabinet inside.∙ If it is required, clean and tighten all weld terminals.The frequency of the maintenance operations may vary in accordance with the working environment where the machine is placed.Electromagnetic Compatibility (EMC)11/04 This machine has been designed in accordance with all relevant directives and standards. However, it may still generate electromagnetic disturbances that can affect other systems like telecommunications (telephone, radio, and television) or other safety systems. These disturbances can cause safety problems in the affected systems. Read and understand this section to eliminate or reduce the amount of electromagnetic disturbance generated by this machine.Before installing the machine, the operator must check the work area for any devices that may malfunction because of electromagnetic disturbances. Consider the following.∙Input and output cables, control cables, and telephone cables that are in or adjacent to the work area and the machine.∙Radio and/or television transmitters and receivers. Computers or computer controlled equipment.∙Safety and control equipment for industrial processes. Equipment for calibration and measurement.∙Personal medical devices like pacemakers and hearing aids.∙Check the electromagnetic immunity for equipment operating in or near the work area. The operator must be sure that all equipment in the area is compatible. This may require additional protection measures.∙The dimensions of the work area to consider will depend on the construction of the area and other activities that are taking place.Consider the following guidelines to reduce electromagnetic emissions from the machine.∙Connect the machine to the input supply according to this manual. If disturbances occur if may be necessary to take additional precautions such as filtering the input supply.∙The output cables should be kept as short as possible and should be positioned together. If possible connect the work piece to ground in order to reduce the electromagnetic emissions. The operator must check that connecting the work piece to ground does not cause problems or unsafe operating conditions for personnel and equipment.∙Shielding of cables in the work area can reduce electromagnetic emissions. This may be necessary for special applications.due to conducted as well as radio-frequency disturbances.Technical SpecificationsNAME INDEXHOT ROD 500S K14089-2INPUTInput Voltage U1EMC Group / Class FrequencyHOT ROD220/380/440V / 3~ II / A 50 / 60 Hz 500SInput Power at Rated Cycle InputAmperesI1max cosφHOT ROD43 kVA @ 35 Duty Cycle (40°C) 220V 3~ 114A0,89500S 380V 3~ 65,5A440V 3~ 57ARATED OUTPUTDuty Cycle 40°C / 55°C(based on a 10 min. period)Output Current Output VoltageHOT ROD 35% / 25% 600A 44 V 500S 60% / 35% 500A 40 V100% / 60% 375A 35 VOUTPUT RANGEWelding Current Range Peak Open Circuit VoltageHOT ROD50A - 625A 65,5 V500SRECOMMENDED INPUT CABLE AND FUSE SIZESFuse or Circuit Breaker Size Power Lead220V~ 380V~ 440V~HOT RODD 125 A D 63 A D 63 A 4 Conductor, 16mm2500SDIMENSIONWeight Height Width Length HOT ROD203 kg 795 mm 566 mm 813 mm 500SProtection Rating Operating Humidity(t=20°C)Operating Temperature StorageTemperatureIP23 ≤ 90 % from -10 ºC to +55 ºC from -25 ºC to +55 ºCEnglish 8 English WEEE07/06Spare Parts12/05Part list reading instructions∙ Do not use this part list for a machine if its code number is not listed. Contact the Lincoln Electric Service Department for any code number not listed.∙ Use the illustration of assembly page and the table below to determine where the part is located for your particular code machine.∙ Use only the parts marked "●" in the column under the heading number called for in the assembly page (# indicate a change in this printing).First, read the Part List reading instructions above then refer to the "Spare Part" manual supplied with the machine, which contains a picture-descriptive part number cross-reference).Electrical SchematicRefer to the "Spare Parts" manual supplied with the machine.AccessoriesK10376Adapter M14/DINSe (F) (to connect the welding cables). *E/H-400A-70-5M The electrode holder with lead - 5m.*GRD-600A-95-5M Work Lead with the Work Clamp - 5m.FL060583010 FLAIR 600 Gouging torch with mounted monocable - 2,5m.* N/B-600A-95-5M 5m-extension cable for gouging torch. K14090-1 AV Meter KitK10095-1-15M Hand Amptrol.K870 Foot Amptrol.K1039815m-extension cable for remote ctrl box.* Co-operates with K10376 E n g l i s hDo not dispose of electrical equipment together with normal waste!In observance of European Directive 2012/19/EC on Waste Electrical and Electronic Equipment(WEEE) and its implementation in accordance with national law, electrical equipment that has reached the end of its life must be collected separately and returned to an environmentally compatible recycling facility. As the owner of the equipment, you should get information on approved collection systems from our local representative.By applying this European Directive you will protect the environment and human health!。
林肯电子公司的高压电焊机说明书
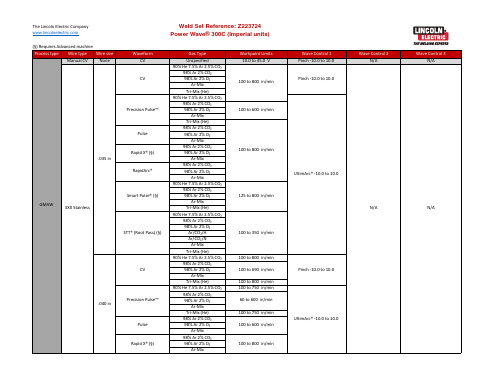
Ar-Mix Tri-Mix (He) 90% He 7.5% Ar 2.5% CO₂ 98% Ar 2% CO₂ 98% Ar 2% O₂
100 to 625 in/min
75 to 500 in/min
75 to 495 in/min
75 to 780 in/min
75 to 760 in/min
100 to 510 in/min
90 to 225 in/min
Wave Control 1 Pinch -10.0 to 10.0 UltimArc® -10.0 to 10.0 Pinch -10.0 to 10.0 UltimArc® -10.0 to 10.0 UltimArc® -10.0 to 10.0 Pinch -10.0 to 10.0 UltimArc® -10.0 to 10.0 Pinch -10.0 to 10.0 UltimArc® -10.0 to 10.0 Pinch -10.0 to 10.0 UltimArc® -10.0 to 10.0 UltimArc® -10.0 to 10.0
100 to 600 in/min
100 to 645 in/min 100 to 625 in/min 100 to 645 in/min 90 to 250 in/min 125 to 700 in/min 150 to 750 in/min 125 to 800 in/min
Wave Control 1 UltimArc® -10.0 to 10.0
305G林肯汽油自发电电焊机

305G林肯汽油自发电电焊机操作规程一、设备结构及特点1.1设备结构1.2 焊机性能参数1.3 发动机性能参数1.4设备的特点:1、采用无刷发电机,维护保养简单。
2、焊接特点优异,可适合各种焊接需要。
3、采用钥匙启动或停机,高,低速运行也由开关控制。
4、装有怠速装置,节约能源。
怠速装置能在焊接作业或使用电源中稍适休息时自动调低发动机转速,达到节约能源,降低噪音的效果。
怠速装置不论对焊接作业还是交流电源都起作用,只要把IDLE 开关放在“ON”上即可。
三、操作方法3.1 启动前的检查:3.1.1、检查机油:发动前必须检查机油,机油位置应在上限FULL和下限ADD之间,检查时油标要完全插入,机油过多会造成发动机破损,必须十分注意。
运行中不得拔出油标尺,机油会喷出来,十分危险。
请使用API类SC级以上的机油,推荐使用SAE10W30全季节机油。
低质机油会影响发动机寿命。
不同品牌的机油不得混合使用。
3.1.2、检查燃料:请再启动前检查并加满燃料。
请用汽车用无铅汽油。
低质汽油会影响出力或造成故障。
3.1.3、检查电瓶:请每天检查电瓶液,定期清除电瓶端子的腐蚀情况。
电瓶液溅在身上或衣服上要立即冲洗。
3.1.4、检查线路:经常检查线路接头部有无松脱,断线,绝缘破损,以便及时处置。
以上检查完成后,启动机器,再注意一下有无漏油处。
3.2操作方法:1、将交流电开关设为OFF状态,使设备在无负荷状态下启动。
怠速开关拨至自动,焊接作业时,只要焊条接触母材,发动机瞬间即可升至额定转数。
当焊接中断7秒钟之后,发动机自动进入低速运转。
2、设备开关拨至START。
检查燃油油位及仪表是否指示正常。
3、拉开风门环。
4、按动启动按钮,设备启动后松手。
5、关闭风门环,怠速状态下暖机5分钟。
6、根据实际情况通过旋钮选择适合的焊接电流方式与电流大小,进行焊接。
7、工作中注意焊机是否有异常振动、声音或气味,电缆连接处是否有过热现象。
8、焊接作业完成后,设备开关拨至STOP,设备停止。
Lincoln 电焊机和切割设备产品说明书

TELESCOPIC EXTRACTION ARML TA 2.0-CW™IM10108July,2011Safety Depends on YouLincoln arc welding and cutting equipment is designed and built with safety in mind. However,your overall safety can be increased by proper installation ... and thoughtful operation on your part.DO NOT INSTAL L ,OPERATE OR REPAIR THIS EQUIPMENT WITHOUT READ-ING THIS MANUAL AND THE SAFETY PRECAUTIONS CON-TAINED THROUGHOUT.And,most importantly, think beforeyou act and be careful.Copyright © Lincoln Global Inc.SECTION A:WARNINGSC ALIFORNIA PROPOSITION 65 WARNINGSWARNING: This product, when used for welding or cutting, produces fumes or gases which contain chemicals known to the State of California to cause birth defects and, in some cases, cancer. (California Health & Safety Code § 25249.5 et seq.)ARC WELDING CAN BE HAZARDOUS. PROTECTYOURSELF AND OTHERS FROM POSSIBLE SERIOUS INJURY OR DEATH. KEEP CHILDREN AWAY.PACEMAKER WEARERS SHOULD CONSULT WITH THEIR DOCTOR BEFORE OPERATING.Read and understand the following safety highlights. For additional safety information, it is strongly recommended that you purchase a copy of “Safety in Welding & Cutting - ANSI Standard Z49.1” from the American Welding Society, P.O. Box 351040, Miami, Florida 33135 or CSA Standard W117.2-1974. A Free copy of “Arc Welding Safety” booklet E205 is available from the Lincoln Electric Company, 22801 St. Clair Avenue, Cleveland, Ohio 44117-1199.BE SURE THAT ALL INSTALLATION, OPERATION,MAINTENANCE AND REPAIR PROCEDURES ARE PERFORMED ONLY BY QUALIFIED INDIVIDUALS.FOR ENGINE POWERED EQUIPMENT.1.a.Turn the engine off before troubleshootingand maintenance work unless themaintenance work requires it to be running.1.b.Operate engines in open, well-ventilated areas or vent the engineexhaust fumes outdoors.with hot engine parts and igniting. Do not spill fuel when filling tank. If fuel is spilled, wipe it up and do not start engine until fumes have been eliminated.1.d. Keep all equipment safety guards, coversand devices in position and in good repair.Keep hands, hair, clothing and tools away from V-belts, gears, fans and all other moving parts when starting, operating or repairing equipment.1.e.In some cases it may be necessary to remove safety guards toperform required maintenance. Remove guards only when necessary and replace them when the maintenance requiring their removal is complete. Always use the greatest care when working near moving parts. 1.f. Do not put your hands near the engine fan. Do not attempt tooverride the governor or idler by pushing on the throttle control rods while the engine is running. 1.g.To prevent accidentally starting gasoline engines while turningthe engine or welding generator during maintenance work,disconnect the spark plug wires, distributor cap or magneto wire as appropriate. 1.h.To avoid scalding, do not remove the radiatorpressure cap when the engine is hot.ELECTRIC ANDMAGNETIC FIELDS MAY BE DANGEROUS2.a.Electric current flowing through any conductorcauses localized Electric and Magnetic Fields (EMF).Welding current creates EMF fields around welding cables and welding machines 2.b.EMF fields may interfere with some pacemakers, andwelders having a pacemaker should consult their physician before welding. 2.c.Exposure to EMF fields in welding may have other health effectswhich are now not known. 2.d.All welders should use the following procedures in order tominimize exposure to EMF fields from the welding circuit:2.d.1.Route the electrode and work cables together - Securethem with tape when possible.2.d.2.Never coil the electrode lead around your body.2.d.3.Do not place your body between the electrode and workcables. If the electrode cable is on your right side, the work cable should also be on your right side.2.d.4.Connect the work cable to the workpiece as close as pos-sible to the area being welded.2.d.5.Do not work next to welding power source.SAFETYD (CFM)040080012001600A (Pa)40080012001600B (m 3/h)2000STATIC PRESSURESTATIC PRESSURE AIRFLOWAIRFLOWTOP VIEWFRONT VIEWFIGURE A.1 - STATIC PRESSUREFIGURE A.2 - REACHCOMPONENTSThe product consists of the following main compo-nents and elements:A. Wall mounting bracket B. Counterweight casing C. Rotatable hoodD. Hose 65 in. (1650 mm)E. TubeF. Hose 20 in. (500 mm)G. Rotating hingeH. RopeI. CounterweightJ. Rubber gaskets (4)K.Extension arm *Hardware (not shown)READ ENTIRE INSTALLATION SECTION BEFORE STARTING INSTALLATION.SAFETY PRECAUTIONSINSTALLATION• The installation of this product is exclusivelyreserved to well authorized, trained and qualified engineers.•During installation, always use Personal Protective Equipment (PPE) to avoid injury. This also applies for persons who enter the work area during installa-tion.• Use sufficient climbing gear and safety guards when working on a higher level than 78.74 inches (2meters) (local restrictions may apply).• Never install the product in front of entrances and exits which must be used for emergency services.• Mind any gas and water pipes and electric cables.• Make sure the wall, ceiling or support system are strong enough to carry the product.• Ensure the workspace is well illuminated.• Use common sense. Stay alert and keep your atten-tion to your work. Do not install the product when you are under the influence of drugs, alcohol or medi-cine.• Make sure that the workshop, in the vicinity of the product, contains sufficient approved fire extinguish-ers.• Air containing particles such as chromium, nickel,beryllium, cadmium, lead etc., which is a health haz-ard, should never be recycled. This air must always be brought outside the working area.USE• Inspect the product and check it for damage. Verify the functioning of the safety features.• During use, always use Personal ProtectiveEquipment (PPE) to avoid injury. This also applies for persons who enter the work area.• Check the working environment. Do not allow unau-thorized persons to enter the working environment.• Protect the product against water and humidity.• Make sure the room is always sufficiently ventilated;this applies especially to confined spaces.INSTALLATION HEIGHTThe recommended installation height of the wall mounting bracket is 11.5 ft. (3500 mm). If the subject work bench is lower than the standard height of 3.0 ft.(900 mm), it is advisable to install the wall mounting bracket at a height of 9.8-10.6 ft. (3000-3250 mm).See Figure A.3.TOOLS AND REQUIREMENTSThe following tools are needed to install and maintain the extraction arm.• 17mm wrench • 13mm wrench • 10mm wrench (2)UNPACKINGCheck that the product is complete. See Components in this section.If parts are missing or damaged, contact your supplier.MOUNTINGThe package contains no mounting hardware for the wall mounting brackets since the required mounting hardware depends on the wall type. Wall mounting brackets can be mounted on:• A thin brick or concrete wall (min. thickness of 4inches/100 mm), using four threaded rods M10.• A thick brick or concrete wall, using four cotter bolts M10x120x60.• Steel profile (e.g. H-profile), using four threaded rods M10.USE CAUTION WHEN MOUNTING• Check that the wall composition is strong enough before mounting the wall brackets.• Before drilling,verify locations of existing gas,water and electrical conduits.B• Mount the wall mounting bracket to the wall.NOTE:For this purpose, two square tubes(30x30x3mm) need to be mounted to prevent bending.NOTE:For central extraction systems, a tapered fanflange is required.ATTACHING THE COUNTERWEIGHT CASING• Slide the counterweight casing (C) over the counter-weight.• Using a 13mm wrench, fasten the casing to the wall mounting bracket (A) using 2 bolts M8x10 and 2 lock washers M8 (B).• Securely tighten bolts.ATTACHING THE ROPE• Pull the arm to the longest position.• Guide the rope through the rotating hinge (D) and over the pulley (C), the counterweight pulley (B) and the other small pulley (A).• Keep the counterweight in the highest position,which means just below the small pulleys. Securely fasten the rope to the counterweight by tying a knot (E). The rope should be threaded through the hole in the counterweight pulley. The knot must be large enough so the rope cannot slip back through thehole.• Tying the counterweight too low will affect thereach of the extraction arm.BCAATTACHING THE HOSE AND EXTRAC-TION HOODTo mount the 65 in. (1650 mm) hose and the extrac-tion hood, proceed as follows:• Make sure the extraction arm is fully extended.• Place a rubber gasket over the tube and fold back 2/3.• Place the flexible hose 65 in. (1650 mm) over the tube. To secure the hose, at least one metal ring of the hose should be applied over ridges of the tube.• Fold back the gasket and place it over the hose.MOUNTING OF THE EXTRACTION HOOD• Place a gasket over the extraction hood and fold back 2/3.• Mount the extraction hood to the extraction arm using a bolt M6x40, a nut M6 and 2 washers M6.Tighten using two 10mm wrenches.• Place the flexible hose over the extraction hood. To secure the hose, at least one metal ring of the hose should be applied over the ridges of the hood.• Fold back the rubber gasket and place it over the hose.ATTACHING THE HOSE TO THE ROTATING HINGEThe rotating hinge and the tube are both provided with a rubber gaskets. To attach the shorter flexible hose proceed as follows:• Remove the banding straps from the flexible hose.• Fold back 2/3 of both rubber gaskets. (A+D).• Place the flexible hose (C) over the collar (B) and the tube (E). To secure the hose, at least one metal ring of the hose should be applied over the ridges of the collar. The same goes for the tube.• Fold back the gaskets and place them over the hose. Make sure the upper gasket overlaps the alu-minum rotating hinge approximately 0.4 in. (10 mm).GENERAL DESCRIPTIONThe LTA 2.0-CW™ is a wall-mounted telescopic extraction arm with a rotatable hood. Located in the hood is a throttle valve that can be fully opened, par-tially opened or completely closed to control airflow.The arm features a focus extraction spoiler which directs the air into the hood. The extraction arm is based on a telescopic tube, allowing it to be extended to give a 8.2 ft (2.5 m) working radius and com-pressed to 5 ft (1.5 m). The arm is fitted with a spring balance which enables it to be moved from a vertical to a horizontal position in one easy movement. If mounted on a column, the arm can be turned 300°due to the rotating hinge. The LTA 2.0-CW™ is often used in welding booths.MANUAL OPERATIONThe extracted welding fume enters the extraction arm via the rotatable hood. The arm discharges the pollut-ed air to a filter unit or directly to the atmosphere. The hood of the arm is fitted with a throttle valve, which can be controlled using the rotary knob(s). The throttle valve is mostly used when several extraction arms are integrated in a line installation; in such configurations closing the throttle valve prevents the loss of costly heated air.NOTE:If an automatic damper system is part of theassembly, keep the manual damper open at all times.ELECTRIC SHOCK CAN KILLThe manufacturer does not accept any liability for damage to the product or personal injury caused by ignoring the safety instructions in this manual,or by negligence during installation, use, mainte-nance, and repair of the product mentioned on the cover of this document and any correspond-ing accessories. Specific working conditions or used accessories may require additional safety instructions. Immediately contact your supplier if you detect a potential danger when using the product.The user of the product is always fully responsi-ble for observing the local safety instructions and regulations. Observe all applicable safety instruc-tions and regulations.USER MANUAL• Everyone working on or with the product, must be familiar with the contents of this manual and must strictly observe the instructions therein. The man-agement should instruct the personnel in accor-dance with the manual and observe all instructions and directions given.• Never change the order of the steps to perform.• Always keep the manual with the product.USERS• The use of this product is exclusively reserved to well authorized, trained and qualified users.Temporary personnel and personnel in training can only use the product under supervision and respon-sibility of skilled engineers.• Use common sense. Stay alert and keep your atten-tion on your work. Do not use the product when you are under the influence of drugs, alcohol or medi-cine.• The product is not to be used by children or persons with reduced physical, sensory or mental capabili-ties, or lack of experience and knowledge.INTENDED USEThis product has been designed exclusively for extracting gases and particles which are released during the most common welding processes. Using this product for other purposes is considered contrary to its intended use. The manufacturer accepts no lia-bility for any damage or injury resulting from suchuse. The product has been built in accordance with state-of-the art standards and recognized safety regu-lations. Only use this product when in technically per-fect condition in accordance with its intended use and the instructions explained in the user manual.PRODUCT COMBINATIONSIf the product is used in combination with other prod-ucts or machines, the safety instructions in the docu-mentation of these products also apply.CONTROLSThe LTA 2.0-CW™ is provided with a handle for easy positioning and a throttle valve for adjustment of the airflow. All movement of the arm is controlled from the hood.A. Rotary knobs for adjustment of throttle valve.B. Handle for positioning of the extraction arm and• Using the handle (B), position the hood of the extrac-tion arm in the desired position at approximately 6-20 inches (15-50 cm) from the source of fume.NOTE:Retraction movement must happen slowly to allow counterweight to descend.• Open the throttle valve (A).• Turn on the connected extraction fan; refer to the corresponding manual.• S tart welding.• If desired, adjust the airflow by turning the rotary knob of the throttle valve (A).NOTE:If an automatic damper system is part of the assembly, keep the manual damper open atall times.• Turn off the connected extraction fan approx. 20 sec-onds after finishing welding; refer to the correspond-ing manual.SERVICE, MAINTENANCE AND REPAIRS• Observe the maintenance intervals given in this manual. Overdue maintenance can lead to high costs for repair and can render the guarantee null and void.• During service, maintenance and repair jobs, always use Personal Protective Equipment (PPE) to avoid injury. This also applies for persons who enter the work area.• Always use tools, materials, lubricants and service techniques which have been approved by the manu-facturer. Never use worn tools and do not leave any tools in or on the product.• Safety features which have been removed for ser-vice, maintenance or repairs, must be put back immediately after finishing these jobs and it must be checked that they will still function properly.• Use sufficient climbing gear and safety guards when working higher than 2 meters (local restrictions may apply).• Ensure the workspace is well illuminated.The product has been designed to function without problems for a long time with a minimum amount of maintenance. In order to guarantee this, some simple regular maintenance and cleaning activities are required which are described in this chapter. If you observe the necessary caution and carry out the maintenance at regular intervals, any problems occur-ring will be detected and corrected before they lead to a total breakdown. The indicated maintenance inter-vals can vary depending on the specific working and ambient conditions. Therefore it is recommended to thoroughly inspect the complete product once every year beside the indicated periodic maintenance. For this purpose contact your supplier. See Table D.1.DISPOSALAfter life of the product, dispose of it in accordance with federal, state and local regulations.COMPONENT Outside Arm Flexible Hoses Inside Arm Arm MovementRotatable ArmACTIONCheck and clean with a non-aggressive detergent.Check for cracks or damages. Replace if necessary.Check and clean thoroughly.Check horizontal, vertical and diagonal armmovement. If necessary, adjust the spring and friction.See Figure F.2.Check the function of the hood hinge. If necessary, adjust the friction. See Figure F.1.Check the function of the throttle valve. See Figure B.1.FREQUENCYEvery 3 mo.XEvery 6 mo.X X X X XTABLE D.1 - PERIODIC MAINTENANCETABLE D.1 - MAJOR COMPONENTSThis Troubleshooting Guide is provided to help you locate and repair possible machine malfunctions.Simply follow the three-step procedure listed below.Step 1.LOCATE PROBLEM (SYMPTOM).Look under the column labeled “PROBLEM (SYMP-TOMS)”. This column describes possible symptoms that the machine may exhibit. Find the listing that best describes the symptom that the machine is exhibiting.Step 2.POSSIBLE CAUSE.The second column labeled “POSSIBLE CAUSE” liststhe obvious external possibilities that may contribute to the symptom.Step 3.RECOMMENDED COURSE OF ACTIONThis column provides a course of action for the Possible Cause.If you do not understand or are unable to perform the Recommended Course of Action safely, contact the Lincoln Electric Automation Division at 888.935.3878HOW TO USE TROUBLESHOOTING GUIDEService and Repair should only be performed by Lincoln Electric Factory Trained Personnel.Unauthorized repairs performed on this equipment may result in danger to the technician and machine operator and will invalidate your factory warranty. For your safety and to avoid Electrical Shock, please observe all safety notes and precautions detailed throughout this manual.__________________________________________________________________________FIGURE F.1 - HOOD ADJUSTMENTFIGURE F.2 - ARM ADJUSTMENTJapaneseChineseKoreanArabicREAD AND UNDERSTAND THE MANUFACTURER’S INSTRUCTION FOR THIS EQUIPMENT AND THE CONSUMABLES TO BE USED AND FOLLOW YOUR EMPLOYER’S SAFETY PRACTICES.SE RECOMIENDA LEER Y ENTENDER LAS INSTRUCCIONES DEL FABRICANTE PARA EL USO DE ESTE EQUIPO Y LOS CONSUMIBLES QUE VA A UTILIZAR, SIGA LAS MEDIDAS DE SEGURIDAD DE SU SUPERVISOR.LISEZ ET COMPRENEZ LES INSTRUCTIONS DU FABRICANT EN CE QUI REGARDE CET EQUIPMENT ET LES PRODUITS A ETRE EMPLOYES ET SUIVEZ LES PROCEDURES DE SECURITE DE VOTRE EMPLOYEUR.LESEN SIE UND BEFOLGEN SIE DIE BETRIEBSANLEITUNG DER ANLAGE UND DEN ELEKTRO-DENEINSATZ DES HERSTELLERS. DIE UNFALLVERHÜTUNGSVORSCHRIFTEN DES ARBEITGEBERS SIND EBENFALLS ZU BEACHTEN.JapaneseChineseKoreanArabicLEIA E COMPREENDA AS INSTRUÇÕES DO FABRICANTE PARA ESTE EQUIPAMENTO E AS PARTES DE USO, E SIGA AS PRÁTICAS DE SEGURANÇA DO EMPREGADOR.• Sales and Service through Subsidiaries and Distributors Worldwide •Cleveland, Ohio 44117-1199 U.S.A. TEL: 888.935.3878 FAX: 216.383.8823。
林肯 Ranger 405 D 引擎驱动多功能焊接机说明书

Fuel Gauge Key Start Idler SwitchCharger Light Hourmeter DigitalVolt/Amp Meter SelectionThe LN25 is capable of welding with eitherRANGER 405 DWELDING OUTPUTLincoln Electric (UK) Ltd Mansfield Road, Aston Sheffield S26 2BS Telephone 0114 287 2401Fax 0114 287 2582GB062.03/02RANGER 405 D DISTRIBUTED BYMax Dimensions Part Number Current Range Duty Cycle OCV Weight L x W x H (mm)KA1453-3CC 30-405 amps 370A, 34V @ 60%CC 62V 550kg1665 x 733 x 970CV up to 405 amps300A, 32V @ 100%CV 49VAUXILIARY POWERRated Voltages Rated OutputWire Feeder 1 Phase/3 Phase ReceptaclesResidual Current DeviceSupply 220-240/1/50/6010 kVA 3 x 240V , 15A 4 pole, 25A 42V AC @ 10A 400-415/3/50/6015 kVA 1 x 415V , 20A (30mA trip current)115V AC @ 5A110/1/50/605 kVA1 x 115V , 20A(All circuit breaker protected)ENGINE SPECIFICATIONACCESSORIES:Make/Model Kubota/D1105Lubrication Forced feed,full flow oil filterCooling SystemPressurised (0.9kg/cm 2)Radiator.Pump forced circulation,(50% Ethylene Glycol - 50% water)and an overflow reservoir bottleFuel SystemIndirect Injection, 2x fuel filters,lift pump, automatic bypass valve for easy bleedingFuel Tank Capacity 45 litresAir Cleaner Heavy duty,2 stage dry cartridge typeMuffler Low noise mounted with machine casingOperating SpeedSound Levels (approx.)High Idle Low Idle Full LoadSpeed 3150rpm 1550rpm 3000rpm@7m 69dBA 66dBA 70dBA@1m 78dBA 68dBA 78dBAOrdering Information K10373-1K10374-1K10095-3-15M K903-1D4512-B K930-2K449-1Ordering Information Two-wheeled site undercarriage Factory-mounted undercarriage for highway towing, without brake Remote Output Control with 15m lead Spark arrestor Chalwyn Valve TIG ModuleLN25 Wire Feed UnitType 3 Cyl,Watercooled,4 cycle, dieselDisplacement1124ccPower(SEA J1349 net intermittent)18.6KW @ 3000rpmElectrical System 12V Battery & starter, key start & stop, glow plugs,alternator battery charger(internal regulator)Governor Type Centrifugal (Flywheel high speed mechanical)。
林肯电子公司焊接设备说明书
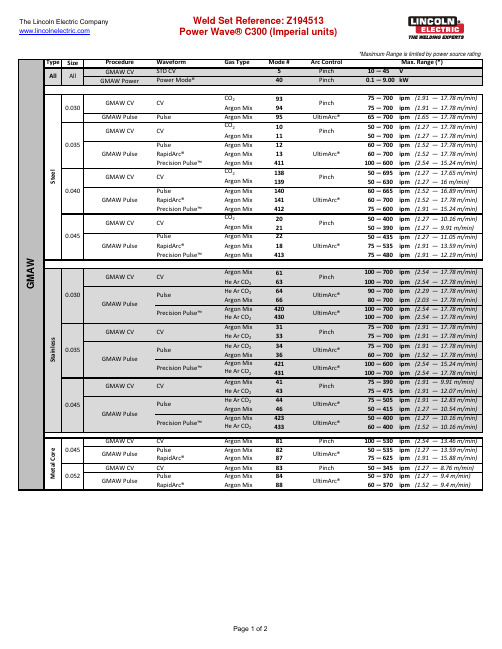
0.030
0.035
0.045 0.045 0.052
Procedure GMAW CV GMAW Power
Waveform STD CV Power Mode®
GMAW CV GMAW Pulse
GMAW CV GMAW Pulse
GMAW CV GMAW Pulse
The Lincoln Electric Company
Weld Set Reference: Z194513 Power Wave® C300 (Imperial units)
GMAW
Metal Core
Stainll All
Gas Type
CO2 Argon Mix Argon Mix CO2 Argon Mix Argon Mix Argon Mix Argon Mix CO2 Argon Mix Argon Mix Argon Mix Argon Mix CO2 Argon Mix Argon Mix Argon Mix Argon Mix
ipm (2.54 ― 17.78 m/min) ipm (2.54 ― 17.78 m/min) ipm (2.29 ― 17.78 m/min) ipm (2.03 ― 17.78 m/min) ipm (2.54 ― 17.78 m/min) ipm (2.54 ― 17.78 m/min)
ipm (1.91 ― 17.78 m/min) ipm (1.91 ― 17.78 m/min) ipm (1.91 ― 17.78 m/min) ipm (1.52 ― 17.78 m/min) ipm (2.54 ― 15.24 m/min) ipm (2.54 ― 17.78 m/min) ipm (1.91 ― 9.91 m/min) ipm (1.91 ― 12.07 m/min) ipm (1.91 ― 12.83 m/min) ipm (1.27 ― 10.54 m/min) ipm (1.27 ― 10.16 m/min) ipm (1.52 ― 10.16 m/min)
林肯电气Invertec V350-PIPE氧化铜焊接机操作手册说明书
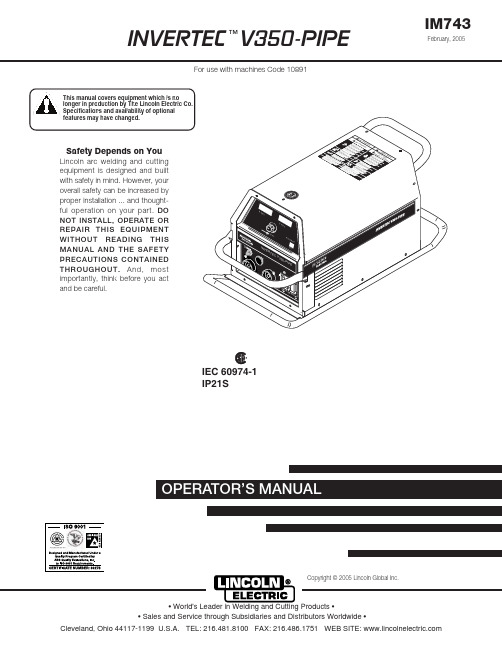
INVERTEC V350-PIPEOPERATOR’S MANUALFor use with machines Code 10891IM743February, 2005™••Copyright © 2005 Lincoln Global Inc.This manual covers equipment which is nolonger in production by The Lincoln Electric Co. Speci cations and availability of optional features may have changed.Mar‘95vvfor selecting a QUALITY product by Lincoln Electric. We want you to take pride in operating this Lincoln Electric Company product ••• as much pride as we have in bringing this product to you!PARALLEL OPERATIONThe V350-PIPE are operable in parallel in CC mode. For best results, the currents of each machine should be reasonably well shared. As an example, with two machines set up in parallel for a 400 amp procedure, each machine should be set to deliver approximately 200 amps, not 300 amps from one and 100 amps from the other. This will minimize nuisance shutdown conditions. In general, more than two machines in parallel will not be effective due to the voltage require-ments of procedures in that power range.To set machine outputs, start with output control pots and arc control pots in identical positions. Use the output control pots to balance the currents and main-tain the desired voltage or current. The arc control pots should be kept identical on the two machines.5. THERMAL• This status light indicates when the power source has been driven into thermal overload. If the output terminals were "ON", the "ON" light will blink indicating that the out-put will be turned back on once the unit cools down to an acceptable temperature level. If the unit was operating in the "REMOTE" mode, the trigger will need to be opened before or after the thermal has cleared and closed after the machine has cooled down to an acceptable tempera-ture to establish output.6. CONTROL-REMOTE / LOCAL• Two status lights indicate the location of output control as pre-determined by the power sources auto-configure sys-tem.• The LOCAL display will be lit when control is at the power source.• The REMOTE display will be lit when a remote pot/control is detected.These Output Control configurations can be overridden (switched) with the CONTROL push button. When changed, the unit will power up in the configuration it was in when it was last powered down.HIDDEN MIDDLE CONTROL PANEL–PROCESS SET UP PANEL7. WELD MODE SELECT(See Figure 1.B)The Mode Control button selects from the following welding modes. CC-STICK SOFT: The Stick Soft process features continuous control ranging from 5 to 425 amps. This mode was intended for most SMAW applications, and Arc Gouging.•Arc Gouging: Setting the output of the Stick Soft mode to 425 amps will enable the arc-gouging mode. The actual output current will depend on the size of carbon used. The recommended maximum size carbon is 5/16".• The Hot Start control regulates the starting current at arc initiation. Hot Start can be adjusted from min-imum (0), with no additional current added at arc start, to maximum (10), with double the preset cur-rent or 425 amps (max of machine) added for the first second after arc initiation.•The Arc Control regulates the Arc Force to adjust the short circuit current. The minimum setting (-10) will produce a "soft" arc and will produce minimal spatter. The maximum setting (+10) will produce a "crisp" arc and will minimize electrode sticking.CC-STICK CRISP:The Stick Crisp mode features continuous control from 60 to 250 amps. This mode was intended primarily for pipe welding applications.• The Hot Start control regulates the starting current at arc initiation. Hot Start can adjust starting current up or down by 25% of the preset value. The recom-mended setting for Hot Start is 5 where the initial current is equal to the preset current.• The Arc Control regulates the Arc Force to adjust the short circuit current. The minimum setting (-10) will produce a "soft" arc and will produce minimal spat-ter. The maximum setting (+10) will produce a "crisp" arc and will minimize electrode sticking.OPTIONS / ACCESSORIES• Undercarriage – K1764-1• Valet Style Undercarriage – K1838-1K857Remote Output ControlK814 Arc Start SwitchK812 Hand Operated AmptrolK870Foot Operated AmptrolNote: All of the above remote controls connect directly to the 6-pin MS-style connector on the front of the V350-PIPE or with either a K864 or K876 adapter and connect it to either of the14 pin wire feeder MS-style connectors on the rear of the V350-PIPE. (See Diagram in Section F-1)K316L-2LN-23PK428, K446, K449LN-25K617 (-1 or -2) K618 (-1 or -2)LN-742K440 (-1), K567-1LN-7 GMAK1559-1, K1564-1LN-10K1499-1, K1521-1DH-10This Troubleshooting Guide is provided to help you locate and repair possible machine malfunctions.Simply follow the three-step procedure listed below.Step 1.LOCATE PROBLEM (SYMPTOM).Look under the column labeled “PROBLEM (SYMP-TOMS)”. This column describes possible symptoms that the machine may exhibit. Find the listing that best describes the symptom that the machine isexhibiting.Step 2.POSSIBLE CAUSE.The second column labeled “POSSIBLE CAUSE ” lists the obvious external possibilities that may contribute to the machine symptom.Step 3.RECOMMENDED COURSE OF ACTIONThis column provides a course of action for the Possible Cause, generally it states to contact your local Lincoln Authorized Field Service Facility.If you do not understand or are unable to perform the Recommended Course of Action safely, contact your local Lincoln Authorized Field Service Facility.HOW TO USE TROUBLESHOOTING GUIDEService and Repair should only be performed by Lincoln Electric Factory Trained Personnel.Unauthorized repairs performed on this equipment may result in danger to the technician and machine operator and will invalidate your factory warranty. For your safety and to avoid Electrical Shock, please observe all safety notes and precautions detailed throughout this manual.__________________________________________________________________________JapaneseChineseKoreanArabicREAD AND UNDERSTAND THE MANUFACTURER’S INSTRUCTION FOR THIS EQUIPMENT AND THE CONSUMABLES TO BE USED AND FOLLOW YOUR EMPLOYER’S SAFETY PRACTICES.SE RECOMIENDA LEER Y ENTENDER LAS INSTRUCCIONES DEL FABRICANTE PARA EL USO DE ESTE EQUIPO Y LOS CONSUMIBLES QUE VA A UTILIZAR, SIGA LAS MEDIDAS DE SEGURIDAD DE SU SUPERVISOR.LISEZ ET COMPRENEZ LES INSTRUCTIONS DU FABRICANT EN CE QUI REGARDE CET EQUIPMENT ET LES PRODUITS A ETRE EMPLOYES ET SUIVEZ LES PROCEDURES DE SECURITE DE VOTRE EMPLOYEUR.LESEN SIE UND BEFOLGEN SIE DIE BETRIEBSANLEITUNG DER ANLAGE UND DEN ELEKTRODENEINSATZ DES HER-STELLERS. DIE UNFALLVERHÜTUNGSVORSCHRIFTEN DES ARBEITGEBERS SIND EBENFALLS ZU BEACHTEN.JapaneseChineseKoreanArabicLEIA E COMPREENDA AS INSTRUÇÕES DO FABRICANTE PARA ESTE EQUIPAMENTO E AS PARTES DE USO, E SIGA AS PRÁTICAS DE SEGURANÇA DO EMPREGADOR.。
林肯电气 电弧焊机操作手册 Power Wave
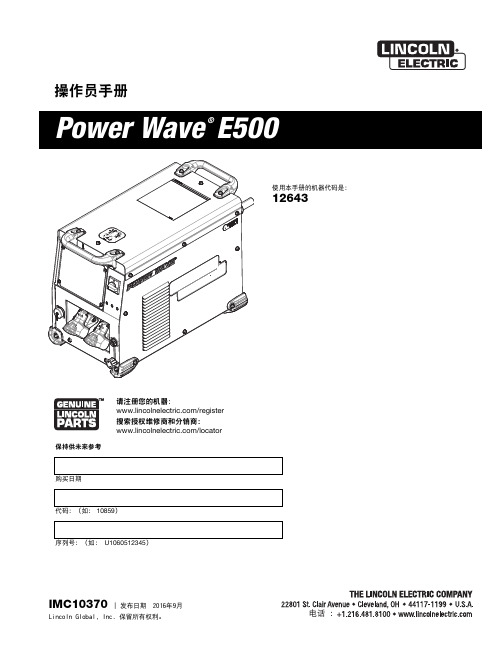
操作员手册请注册您的机器:/register 搜索授权维修商和分销商: /locatorIM C 10370 | 发布日期 2016年9月Lincoln Global, Inc. 保留所有权利。
使用本手册的机器代码是:12643!˖保持供未来参考购买日期代码:(如:10859)序列号:(如: U1060512345)目录产品描述 (3)设备局限 (3)设计特点 (3)安装 .......................................................................A部分技术规格 .........................................................................A-1机器接地 .........................................................................A-2位置与冷却通风 ....................................................................A-2高频保护 .........................................................................A-2升举.........................................................................A-2堆垛 .........................................................................A-2倾斜.........................................................................A-2环境局限性.........................................................................A-2箱前控制 .........................................................................A-3箱后控制 .........................................................................A-4电弧焊的推荐焊条和作业电缆尺寸 .....................................................A-7控制电缆与电压传感连接.............................................................A-8TYPICA;集成系统(单ARM)...........................................................A-9操作 .......................................................................B部分通电顺序 .........................................................................B-1负载周期.........................................................................B-2常见焊接工艺.......................................................................B-3配件 .......................................................................C部分维护 .......................................................................D部分目视检查 .........................................................................D-1例行维护 .........................................................................D-1定期维护 .........................................................................D-1故障排除 .......................................................................E部分如何使用故障排除指南...............................................................E-1用状态灯解决系统问题...............................................................E-2POWER WAVE的错误代码 ..............................................................E-3图 ...........................................................................F部分零部件清单可能会在未给出通知的情况下修改或升级内容/详情。
林肯全球自动焊接系统NA-5 焊接机说明书
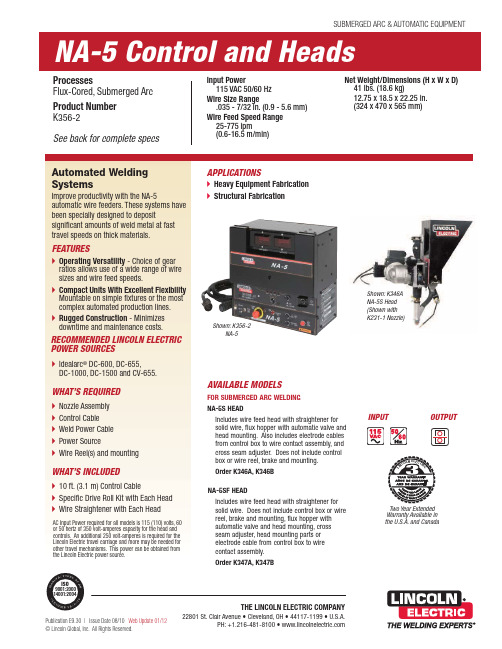
Publication E9.30 | Issue D a te 08/10 Web Update 01/12© Lincoln Global, Inc. All Rights Reserved.SUBMERGED ARC & AUTOMATIC EQUIPMENTProcessesFlux-Cored, Submerged Arc Product Number K356-2See back for complete specs Input Power115 VAC 50/60 Hz Wire Size Range.035 - 7/32 in. (0.9 - 5.6 mm)Wire Feed Speed Range 25-775 ipm(0.6-16.5 m/min)Net Weight/Dimensions (H x W x D)41 lbs. (18.6 kg)12.75 x 18.5 x 22.25 in.(324 x 470 x 565 mm)PH: +1.216-481-8100 • Shown: K356-2NA-5[ 2]|NA-51.Control Power Switch –Turns wire feeder input power on and off. Also serves as an emergency stop switch.2.Pilot Light –Shows when the electrode is "hot".3.Inch Pushbuttons –Feed electrode up and down when not welding.4.Start and Stop Pushbuttons –Control welding cycles.5.Meter Value Pushbutton –Monitor either the preset values or the actual values.6.Timer Control –For burnback and/or wire react time.7.Crater Module (optional) –Controls procedure for anadjustable period of time to regulate bead size or fill craters at the end of the weld.8.Weld Timer (optional) –Eliminates the need to press stop pushbutton.9.Lockable Cover –Lockout procedure controls when necessary.10.Digital Display –Monitor wire feed speed and voltage on separate meters.11.Start Module (optional) –Controls penetration, bead size, or other factors for an adjustable time at the start of the weld.12.WFS and Voltage Preset Controls –Preset wire feed speed and voltage prior to and during welding. These controlseliminate returning to the power source for routine procedure changes.13.Travel Switch –Controls the travel mechanism for automatic starting and stopping when welding, travel without welding during setup and travel off.12345678910111213K299 Reel and Mounting – Order separately.NA-5 Control K356-2DC Power Source –Constant Voltage type with on-off control of power source output.4 ft. (1.2 m) Motor Cord –Included with K346.4 ft. (1.2 m) Electrode CablesContact Nozzle (optional)K335-26 Extension – Motor, flux hopper and electrode cables. Optional when more than 4 ft. (1.2 m) is required.Work Cable – Two or more 4/0NA-5S and NA-5SFFor Submerged Arc WeldingTwo 4/0 electrode cables and the multi-conductor control cable.Flux Hopper –Included with K346.Solid Wire Straightener Head4 ft. (1.2 m) Flux Hopper Cord –Included with K346.REQUIRED EQUIPMENTSolenoid AssemblyValve to automatically control water flow when using cooling attachment on K148 contact assemblies. Can also be used to control gas. Order K223Starting or Crater Module Permits additional settings of wire feed speed and voltage for an adjustable period of time (10 seconds max). Can be used for either a starting procedure or a crater fill procedure. If both are required, two assemblies must be ordered.Order K334Remote Interface ModulePermits remote operation of theNA-5 Inch Up, Inch Down, Start andStop Functions by either of thefollowing user-supplied externalsignals and provides electricalisolation of the NA-5 control circuitryfrom these signals:- SwitchesMomentary closure of contactsrated for 24 volts,5 milliamperes, DC.-24 Volt SignalsMomentary application of 24volt ±10% AC or DC signalcapable of 5 milliamperessteady state. (.15 amp peakcapacitive in rush) per input.This module can be used withall codes of NA-5 Controls andreplaces the earlier K336Remote Pushbutton InterfaceModule, which provided for onlyexternal switch closure signals.Order K336Weld Timer ModulePermits setting of weld time for anadjustable period of time. Eliminatesneed to press stop pushbutton. Thetimer unit is adjustable from 0.00 -9.99 seconds.Order K337-10Control To Head ExtensionCable AssemblyThe standard head is equipped withcables which permit the head to bemounted up to four feet from thecontrols. "F" models, however, donot include electrode cables. Whenthe head is mounted further awayfrom the control, extension cableassemblies must be purchased. Forthe NA-5S head: Includes motor,tachometer, and flux valve leadextensions with polarized plugs andelectrode. 26 ft. length.Order K335-26Recommended for the NA-5N, andSF heads. It is the same as the K335without the flux valve lead extension.Available in 46 ft. lengths.Order K338-46Mounting KitFor use if the NA-5 control box is tobe mounted on the carriage.Order T14469SINGLE ELECTRODESubmerged Arc Contact NozzleAssembly for 3/32 in. (2.4 mm),1/8 in. (3.2 mm) and 5/32 in.(4.0 mm) electrodes.For 5/64 in. (2.0 mm), 3/16 in.(4.8 mm) or 7/32 in. (5.6 mm) sizes,order additional appropriate KP1962tips. Outer flux cone gives full fluxcoverage with minimumconsumption.(Rated up to 650 amps.)Order K231-1K231 nozzle tipsDesigned for long life.OrderKP1962-1B1for 1/8 in. (3.2mm) wireKP1962-2B1for 3/16 in. (4.8 mm) wireKP1962-3B1for 3/32 in. (2.4 mm) wireKP1962-4B1for 5/32 in. (4.0 mm) wireKP1962-5B1for 7/32 in. (5.6 mm) wireKP2082-2B1for 5/64 in. (2.0 mm) wireNarrow Gap Deep Grove NozzleFor single arc 3/32 in. (2.4 mm)diameter wire welding on thickwalled steel plate with nearlyparallel-sided, narrow gap jointpreparations.Order K386Contact Jaw AssemblySingle arc contact jawassembly for 1/8-7/32 in.(3.2-5.6 mm) diameter wire. Ruggedcontact jaws for maximum life atcurrents over 600 amps.Order K226RTWINARC®Tiny Twinarc®Wire StraightenerStraightens wire diameters .045 thru3/32 in. (1.2 thru 2.4 mm).Particularly valuable on longerelectrical stickout procedures.Order K281Tiny Twinarc®Feeds two 1/16, 5/64, or 3/32 in.(1.6, 2.0, or 2.4 mm) electrodes forhigh speed submerged arc welds onthin gauge (1.89 mm) to heavy plate.Includes contact nozzle, wire guides,drive rolls and guides, and a secondwire reel and mounting bracket.Order K129-1/16K129-5/64K129-3/32Large Wire Twinarc®Contact AssembliesFeeds two 5/64 in. (2.0 mm),3/32 in. (2.4 mm) or 1/8 in. (3.2 mm)wires for submerged arc weldingon "Fast-Fill" joints or hardfacingbeads.Order K225GENERAL OPTIONSConcentric FluxCone AssemblyFor use with K148B, Positive ContactNozzle Assembly. Gives concentricflux coverage around the electrode.Order K285Positive Contact AssemblyFor single arc welding at highcurrents (optional T12928 watercooling attachment recommendedwhen welding over 600 amps).Order K148A(for 3/32 to 1/8 in. wire)Order K148B(for 5/32 to 3/16 in. wire)ESO (Extended Stick-Out)ExtensionLinc-Fill long stickoutextension for K148A Single ArcPositive Contact Nozzle Assembly.Required for long stickout technique.Order K149-5/325 in. Nozzle ExtensionExtends the wire for subarc nozzlesby 5 inches [up to 1/4 in. (6.4 mm)diameter wire].Order KP2721-1Horizontal Head AdjusterProvides crank adjustment of headposition. Has 2 in. (51 mm)horizontal travel.Order K96Vertical Lift AdjusterProvides 4 in. (102 mm) hand crankadjustment of vertical head position.It also includes up to 3-3/4 in.(95.2 mm) in-and-out horizontaladjustment with stops that can bepreset for simple repetition of thesame adjustment.Order K29SpreadArc OscillatorOscillates head across the line oftravel. Calibrated dwell time andoscillation speed controls permit theSpreadArc to cover large areasquickly with smooth beads ofminimum admixture.Order K278-1TC-3 Self-PropelledTravel CarriageThe TC-3 travel carriage allows themounting of up to two feed heads/controllers and wire reels to a beamfor basic hard automationinstallations.Order K325 HCS(for 5-75 ipm)NA-5| [ 3]Automatic Flux Hopper Assembly Flux Hopper for MAXsa ™29 Heads (included standard on the MAXsa ™22 Heads). Order K219Wire Reel Assembly for 50-60 lb. CoilsAccommodates 50 lb. (22.7 kg) or 60 lb. (27.2 kg) coils of wire on automatic wire feeders. The unit includes a wire reel mountingspindle and braking system. Cannot be used with K2462-1.Order K299Tandem ReelsTwo Wire Reel Mounting for TC-3. Order K390Tandem Arc FrameworkProvides mountings with desired positioning adjustments for two standard Automatic Wire Feed Heads. Includes insulation and hardware to permit direct mounting to a high capacity TC-3 Carriage, or to the user's gantry or fixture for either direction of travel.Order K387Flux HopperTandem Arc Flux Hopper for K387 mountings. Order K389Wire Straightener (Subarc) up to 7/32 in. (5.6 mm)Includes a three roll wire straightener with adjustable pressure. (1 included with each tractor and MAXsa ™Feed Head.) Order K1733-5(1)For the K347 Head, order the K338 extension.(2)For gear ratios shown.C U S T O M E R A S S I S T A N C E P O L I C YThe business of The Lincoln Electric Company is manufacturing and selling high quality welding equipment, consumables, and cutting equipment. Our challenge is to meet the needs of our customers and to exceed their expectations. Onoccasion, purchasers may ask Lincoln Electric for information or advice about their use of our products. Our employees respond to inquiries to the best of their ability based on information provided to them by the customers and the knowledge they may have concerning the application. Our employees, however, are not in a position to verify the information provided or to evaluate the engineering requirements for the particular weldment. Accordingly, Lincoln Electric does not warrant or guarantee or assume any liability with respect to such information or advice. Moreover, the provision of such information or advice does not create, expand, or alter any warranty on our products. Any express or implied warranty that might arise from the information or advice, including any implied warranty of merchantability or any warranty of fitness for any customers’ particular purpose is specifically disclaimed.Lincoln Electric is a responsive manufacturer, but the selection and use of specific products sold by Lincoln Electric is solely within the control of, and remains the sole responsibility of the customer. Many variables beyond the control of Lincoln Electric affect the results obtained in applying these types of fabrication methods and service requirements.Subject to Change – This information is accurate to the best of our knowledge at the time of printing. Please refer to for any updated information.For best welding results with Lincoln Electric equipment, always use Lincoln Electric consumables. Visit for more details.。
电焊机说明书

电焊机说明书电焊机说明书1. 引言本文档是针对电焊机的使用说明书,旨在帮助用户正确、安全地操作电焊机。
在使用电焊机之前,请仔细阅读本说明书,并按照相关操作指导进行操作。
2. 产品概述电焊机是一种用于焊接金属的设备。
它采用电力作为能源,通过将电能转化为热能,使金属部件产生高温,从而实现金属的熔化和连接。
电焊机广泛应用于建筑、制造业等领域。
3. 安全注意事项在使用电焊机时,请务必遵守以下安全注意事项:1. 在使用电焊机之前,请仔细阅读并理解本说明书中的所有内容。
2. 了解并遵守当地的安全法规和规定。
3. 在使用电焊机之前,请确保自己已经接受过相关的培训,并具备相应的焊接技能。
4. 使用电焊机时,请佩戴适当的个人防护装备,包括焊接面罩、手套和护目镜等。
5. 在操作电焊机时,请确保工作区域周围没有易燃物,以防止火灾的发生。
6. 在操作电焊机时,请注意周围的安全,确保没有其他人员接近工作区域。
7. 使用电焊机时,请确保设备的电源线路正常,接地良好。
8. 如果发现电焊机有异常情况(例如烧焊机、异常喷火等),请立即停止使用,拔掉电源插头,并联系专业维修人员进行修理。
9. 在使用电焊机时,请保持专注,避免分心和疲劳操作。
4. 使用步骤步骤一:准备工作在开始使用电焊机之前,需要进行以下准备工作:1. 确保电焊机的电源线插头与电源插座相匹配,并确保连接稳固。
2. 检查焊接电缆和焊枪的连接是否牢固。
3. 确保工作区域通风良好,以免产生有害气体。
步骤二:调整参数1. 打开电焊机的电源开关。
2. 根据所需焊接工艺和焊接材料的要求,调整电流值和电极直径。
3. 确保调整的参数在安全范围内,并根据需要做出适当的调整。
步骤三:开始焊接1. 将焊枪对准焊接位置,并同时按下焊接开关和踏板(如果有的话)。
2. 保持稳定的焊接速度和焊接角度,确保焊接均匀。
3. 注意控制焊接时间,避免过度烧焊。
步骤四:结束焊接1. 在完成焊接后,松开焊接开关和踏板。
林肯 Ranger 305D 引擎驱动焊接机说明书

Advantage LincolnThe Ranger 305D is a powerful stick, TIG, and wire welding engine driven welder that is ready for all day, everyday performance on construction, maintenance or pipe applica-tions. Rugged and dependable, the Ranger 305D is built through the entire day. Lincoln’s Ranger 305D ... it’s ready for a workout.Ranger ®305D•Diesel Engine-Driven Welder-A powerful 300 amp DC CC/CV diesel engine-driven welder. All rated outputs at 100% duty cycle 104°F (40°C).•Multi-Process Welding-Excellent DC multi-process welding for general purpose stick, downhill pipe (stick), TIG, cored-wire, MIG (CO 2and blended gas) and arc gouging.•Digital Weld Meters-Digital weld meters for amps and volts makes it easy to precisely pre-set your procedures and monitor actual welding output.•-arc, low spatter and excellent bead appearance.•Plenty of AC Generator Power-A portable powerhouse – delivers 10,000 watts peak (9,500 watts continuous) of 120V/240V AC generator power. Enough power to run lights, tools, and weld at the same time!•Skewed Rotor Design-Skewed rotor design provides AC power waveshape suitable for operating Lincoln Pro-Cut ® plasma cutters and inverter power sources. Lincoln was first in the welding industry with this feature.•One-Pak ™Package-Convenient way to order a welding system. See inside.•Three-Year Warranty-Three-year Lincoln warranty on welder (engine is warranted separately by the engine manufacturer).300 Amp DC Diesel Engine Driven WelderStick, TIG, MIG, Flux-Cored, GougingProcessesOutputInputPERFORMANCEWelding Performance•Provides superior DC arc welding performance for stick, TIG, cored-wire, MIG and arc gouging.••CC-Stick mode is optimized for general purpose stick using E7018 low hydrogen electrode.•Downhill Pipe welding mode excellent for cellulosic electrodes,such as Fleetweld ® 5P +.Fast travel speeds, especially on fillpasses. Arc control adjustment for a softer, buttery arc, or a more forceful, digging arc.•Arc force control provides a soft or more forceful digging arc in CC-stick or downhill pipe mode and inductance/pinch control in CV wire mode.•Built-in “hot” start for easier starts and restrikes minimizing the electrode “sticking” to the work.•Arc gouging with up to 3/16” carbons.•Touch-Start DC TIG ™ – lift tungsten to start the arc.AC Generator Performance•Two 120V 20A GFCI (ground fault circuit interrupter) duplex receptacles with weather resistant covers. Circuit breaker protection for, among tools, up to 9” grinder.•Up to 40 amps at 240V from the 120V/240V receptacle with weather resistant covers. Circuit breaker protection.•Maximum generator power (while not welding) is available at any weld dial setting.•Skewed rotor design provides AC power waveshape suitable for operating Lincoln Pro-Cut ® plasma cutters and inverter power sources.FEATURES•Simple Controls - Keep training time to a minimum with thestraightforward control panel of the Ranger 305D. The flip-down control panel door keeps less frequently used controls out of the way.• Single, full-range output control dial. No confusion with taps and controls!• 4 welding modes: CC-Stick, Downhill Pipe, CV-Wire, and T ouch-Start TIG™.• Dual digital output meters for presetting weld amps for stick, TIG or downhill pipe modes, or voltage for CV wire mode. Also displays actual outputs while welding. Memory feature holds output read-ings for 7 seconds after welding stops for viewing by the operator.• Output at welding terminals controlled by electronic contactor. Can be switched to "On", or to "Remotely Controlled". •Remote is auto-activated when plugged into a 6-pin connector.• Compatible with many Lincoln wire feeders including the LN-15, LN-25, LN-23P , LF-72, LF-74, LN-7, LN-7 GMA, LN-742, LN-8, and Cobramatic™ wire feeders, Magnum SG and Prince Spool Guns.•Wire feed voltmeter switch matches polarity of wire feeder volt meter to polarity of electrode.• T op-of-the-line water-cooled Kubota ®18.8HP D722 diesel engine.•Fully enclosed case for equipment protection and low noise. Lower noise than partially-enclosed welders of comparable size. Y ou can hear the difference! Noise at rated load:– 104.2 dB sound power (Lwa)– 80.6 dBA sound level at 23 ft. (7m)•Glow plugs for rapid starting down to 5°F (-15°C).•Electric fuel pump and automatic air-bleed system virtually eliminates manual air bleeding if fuel tank is run dry. Activated when glow plug button is pressed.QUALITY AND RELIABILITY•Printed circuit boards are environmentally-shielded using Lincoln's engineered potting and protective frame trays.•Oil dip stick, filters, spark plugs, etc. are easily accessed with left, right and top engine doors. Left and right doors are removable.•Adjust exhaust direction with top-mounted 360º rotatableexhaust muffler. Muffler made from aluminized steel for long life.•Attractive red and black powder paint finish offers increased durability with added protection from rust and corrosion.• Longer engine life, reduced noise emissions and greater fuel economy with automatic engine idler.•Conveniently located engine maintenance label under top engine door.•Engine hour meter for scheduled maintenance.• Circuit breaker protection on the battery ignition system provides added component protection.• Reliable start-up with Group 58 battery with 550 cold cranking amps.•Automatic engine shutdown protection for low oil pressure or high engine temperature. Indicator light on control panel.•Dependability and long life aided by all-copper windings in rotor and stator with high quality insulation.• Approved by Canadian Standards Association (CSA).•Manufactured under a quality system certified to ISO 9001 requirements and ISO 14001 environmental standards.• Three year Lincoln warranty. (Engine is warranted separately by the manufacturer.)FEATURES CONT.•Engine closed breather system keeps engine compartment clean! Eliminates oil mist from collecting inside enginecompartment, especially on radiator surfaces, which wouldlower engine cooling efficiency. Also prevents oil drips to a truck bed or the ground from an open breather discharge.• 12 gallon fuel capacity allows you to run an extended day. 20% longer than the nearest competitor!• Electric fuel gauge located on control panel makes it easy to check the fuel level during operation and refueling. Helps you eliminate running low on fuel during critical jobs.• Large top fuel filler neck is easily accessed for refueling.• Electric start. Engine battery charging system light to indicate abnormal charging.• Oil drain valve (no tools required) with removable extension tube.• Convenient truck or trailer mounting with front and rear holes in base.27453Printed circuit boards areenvironmentally-shielded using Lincoln's engineered potting and protective frame trays.(1) DC constant voltage capability provides convenience and added safety when welding in electrically hazardous conditions.(2)When welding, available auxiliary power will be reduced. Output voltage is within +\- 10% at all loads up to rated capacity.(3)120V will operate either 60 Hz or 50/60 Hz power tools, lights, etc.(4)Circuits cannot be wired in parallel to operate the same device.(5)Height is to top of exhaust elbow. Enclosure height is 30" (762 mm).(6) Kubota warranty is 2 years/2,000 hours for machines shipped within the U.S., Canada, Pacific Ocean region and Western Europe.Warranty is 1 year/1,000 hours for Asia, Africa and Middle East.SYSTEM SELECTIONOne-Pak™ Welding PackageOrder a Lincoln One-Pak™ and get everythingyou need to complete a welding package - allwith one order number.(Package is not assembled.)Each UNASSEMBLED Package Contains:•Ranger 305D (K1727-2)•Accessory Kit (K704)•LN-25 Wire Feeder (K449)•Gun and Cable (K126-2)•Drive Roll Kit (KP653-3/32)•.072” NR-232 25 Lb. Spool (ED030644)Order:K2352-1K449 LN-25 Wire FeederK126-2 Gun and Cable.072” NR-232 25 Lb. SpoolKP653-3/32 Drive Roll KitK704 Accessory KitRanger 305DGENERAL OPTIONSPower Plug KitProvides four 120V plugs rated at 20 amps each, and one dual voltage, full KVA plug rated at 120/240V , 50 amps. 120V plug may not be compatible with common household receptacles.Order K802NPower Plug KitProvides four 120V plugs rated at 15 amps each, and one dual voltage, full KVA plug rated at 120/240V , 50 amps. 120V plug is compatible with common household receptacles.Order K802RFull-KVA Power PlugOne dual voltage plug rated at120/240V , 50 amps. NEMA 14-50P .Order T12153-9Spark Arrester KitAttaches between muffler and exhaust elbow. Virtually eliminates spark emissions.Order K1898-1Roll CageImproves damage protection and includes built-in cable rack.Attaches to K957-1 trailer.Order K1789-1Cold Weather Operation Kit For extreme cold conditionswhere engine glow plug starting is not sufficient. Includes oil pan heater, engine water heater and radiator grill tarp.Order K2174-1Small Two Wheel Welder Trailer For heavy-duty road, off-road, plant and yard use. Includes wheeled jack, safety chains, 12” wheels,and large rear bumper. Stiff 3/16”steel frame is prime painted using the e-coat process and finished with powder coating technology for superior rust and corrosion resist-ance. Low sway suspension gives outstanding stability with manage-able tongue weight. E-Z Lube™Axle-pack wheel bearings with a grease gun. Compact and maneu-verable, with 47” max. width for narrow aisles and doors.Order:K957-1TrailerK958-12” Ball HitchK958-2 Lunette Eye Hitch K959-2 Fender & Light Kit K965-1 Cable RackSTICK OPTIONSAccessory KitIncludes 35 ft. (10.7m) #2/0 elec-trode cable, 30 ft. (9.1m) #2/0work cable, headshield, work-clamp and electrode holder. 400amp capacity. Order K704Accessory KitFor Stick welding. Includes 20 ft.(6.1m) #6 electrode cable with lug,15 ft. (4.6m) #6 work cable with lugs, headshield, filter plate, work clamp, electrode holder and sam-ple pack of mild steel electrode.150 amp capacity.Order K875Remote Control KitConsists of a control box with choice of two cable lengths.Permits remote adjustment of output.Order K857for 25 ft. (7.6m)K857-1for 100 ft. (30.5m)TIG OPTIONSPro-Torch ®PTA-26V TIG Torch Air-cooled 200 amp torchequipped with valve for gas flow control. 25 ft. (7.6m) length. Order K1783-9Foot Amptrol®Varies current while welding for making critical TIG welds and crater filling. Depress pedal to increase current. Depressingpedal fully achieves maximum set current. Fully raising the pedal fin-ishes the weld and starts the afterflow cycle. Includes 25 ft.(7.6m) control cable.Order K870Hand AmptrolProvides 25 ft. (7.6m) of remote current control for TIG welding. (6pin plug connection). Velcro straps secure torch.Order K963-3 (one size fits all Pro-Torch TIG torches).Magnum Parts Kit for PTA-26V TIG TorchMagnum Parts Kit provides all the torch accessories you need to start welding. Parts kit provides collets, collet bodies, a back cap,alumina nozzles and tungstens in a variety of sizes, all packaged in an easy to carry reclosable pack.Order KP509120V120VTIG OPTIONS CONT.Precision TIG 185 Ready-Pak For AC TIG welding with square wave performance use the AC generator of the engine-driven welder to supply the power. Easy setup. Includes torch, foot amp-trol, gas regulator and hose.Requires the K1816-1 Full KVA Adapter Kit.Order K2347-1Invertec V205-T AC/DC One-Pak™ PackageFor AC TIG welding with square wave performance use the AC generator of the engine-driven welder to supply the power. Easy setup. Includes torch, parts kit,regulator and hose kit, Twist-Mate™ torch adapter, work cable with Twist-Mate end, and foot Amptrol®. Requires the K1816-1Full-KVA Adapter Kit.Order K2350-1Full-KVA Adapter KItProvides convenient connection of Lincoln Electric equipment with NEMA 6-50R plug to LIncoln engine-driven welders having a Full-KVA receptacle.Order K1816-1WIRE FEEDERSLN-25 Wire FeederPortable CC/CV unit for flux-cored and MIG welding. Includes gas solenoid & internal contactor. For spools up to 44 lbs. (19.9 kg).Order K449LN-15 Across-The-Arc Wire FeederPortable CC/CV unit for flux-cored and MIG welding. Includes gas solenoid, adjustable flow meter and internal contactor. For 10-15 lb. (4.5-6.8 kg) spools.Order K1870-1Remote Voltage Control (LN-25)Provides 25 ft. (7.6m) of remote output control and output jumper (2 and 4) for machines having 6-pin MS-type connector.Order K444-1Magnum® 350 Innershield Gun (for LN-25)For self-shielded wire with 15 ft.(4.5m) cable. For .062-3/32” (1.6-2.4mm) wire.Order K126-2WIRE FEEDERS CONT.Drive Roll and Guide Tube Kit (for LN-25)For .068-3/32” (1.8-2.4mm) cored or solid steel wire.Order KP653-3/32Drive Roll and and Wire Guide Kit (for LN-15)For 1/16” (1.6mm) cored wire. Order KP1697-1/16CGun Receiver Bushing(For LN-15)For use with K126-2 Magnum 350Innershield Gun. Order K1500-1Magnum® 300 MIG GunFor .035-.045” (0.9-1.2mm) gas-shielded wire with 15 ft. (4.5m)cable.LN-25Order K1802-1(includes Connector Kit)LN-15Order:K470-2 Magnum 300 MIG Gun K466-10 Connector Kit Drive Roll and Guide Tube Kit (for LN-25)For .035-.040” (0.9-1.0mm) solid steel wire Order KP653-035SDrive Roll and Wire Guide Kit (for LN-15)For .035 (0.9mm) solid steel wire. Order KP1696-035SLN-23P Wire FeederPortable CV unit for Innershield pipe welding. Control cable operates contactor inside Wire Feed Module for “cold” electrode.Includes drive rolls and guide tubes. Requires LN-23P Adapter Kit (K350-1) and Gun and Cable Assembly.Order K316L-1LN-23P Adapter KitRequired to adapt LN-23P to any Lincoln power source. Makes 14pin connection at power source.Order K350-1Magnum® 250 Innershield Gun (for LN-23P)For lighter weight and easier handling. Rated 250 amps, 60%duty cycle. For .068 - 5/64” (1.7 -2.0 mm) Innershield wire andincludes reduced speed switch. For pipe welding, a KP1909-1 62°gun tube is recommended.Order K355-10。