第四章 粉末冶金原理成形前粉末的预处理
粉末冶金热处理

粉末冶金热处理一、前言粉末冶金热处理是一种重要的金属材料加工方法,它能够通过高温处理改善材料的性能,提高其机械性能、耐腐蚀性和耐磨损性等。
本文将从粉末冶金的基础知识开始,详细介绍粉末冶金热处理的原理、方法和应用。
二、粉末冶金基础知识1. 粉末冶金定义粉末冶金是一种制造零件的技术,它通过将金属或非金属材料制成微小颗粒,再利用压缩、烧结等工艺将这些颗粒化为块体或形成复合材料。
2. 粉末制备方法常用的粉末制备方法有机械法、化学法和物理法等。
其中机械法是最常用的方法之一,包括球磨法、振荡球磨法和高能球磨法等。
3. 粉末冶金加工工艺主要包括压制、烧结和后处理等过程。
其中压制是将粉末填充到模具中进行压缩成形;烧结则是将压制好的坯体进行高温处理,使其颗粒结合成为固体材料;后处理则是对烧结好的材料进行加工和表面处理。
三、粉末冶金热处理原理1. 热处理定义热处理是指通过加热和冷却等方式改变材料的组织结构和性能,以达到提高其机械性能、耐腐蚀性和耐磨损性等目的的过程。
2. 粉末冶金热处理原理粉末冶金材料在制备过程中由于颗粒之间存在空隙,因此其密度较低。
而经过高温热处理后,这些空隙会被填充,颗粒之间的结合力也会增强,从而提高了材料的密度和强度。
此外,热处理还可以改善材料的晶体结构和组织状态,增强其机械性能、耐腐蚀性和耐磨损性等。
四、粉末冶金热处理方法1. 真空烧结法真空烧结法是一种在真空环境下进行高温加工的方法。
由于真空环境下不存在氧化反应,因此可以避免材料表面被氧化和污染。
此外,真空烧结法还可以控制材料的晶体结构和组织状态,从而提高其机械性能和耐腐蚀性能。
2. 气氛烧结法气氛烧结法是一种在特定气氛下进行高温加工的方法。
常用的气氛有惰性气体、还原性气体和氧化性气体等。
这种方法可以控制材料的晶体结构和组织状态,从而改善其性能。
3. 热等静压法热等静压法是一种将粉末填充到模具中后,在高温高压下进行加工的方法。
这种方法可以使材料颗粒之间更加紧密地结合,从而提高其密度和强度。
粉末冶金原理-中文
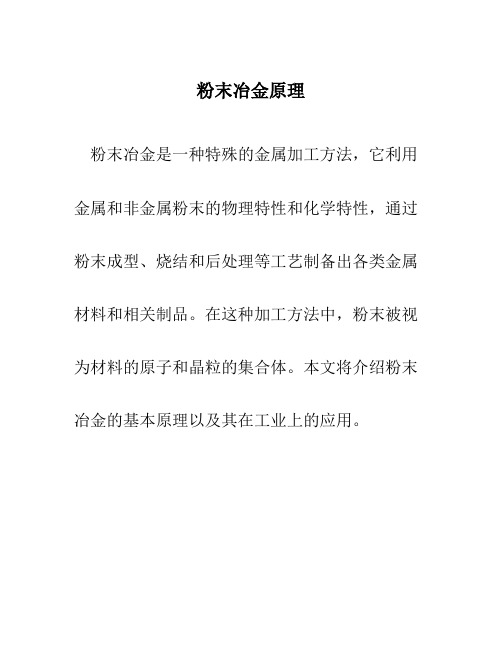
粉末冶金原理粉末冶金是一种特殊的金属加工方法,它利用金属和非金属粉末的物理特性和化学特性,通过粉末成型、烧结和后处理等工艺制备出各类金属材料和相关制品。
在这种加工方法中,粉末被视为材料的原子和晶粒的集合体。
本文将介绍粉末冶金的基本原理以及其在工业上的应用。
粉末冶金的基本原理1.原料选择:粉末冶金的首要任务是选择适当的原料。
原料可以是金属、合金或陶瓷等材料的粉末。
原料的选择应该考虑材料的化学成分、晶体结构、粒子形状和尺寸分布等因素。
2.粉末的制备:粉末的制备是粉末冶金的关键步骤之一。
常见的粉末制备方法包括研磨、机械合金化、溶液沉淀和气相反应等。
不同的制备方法可以获得不同尺寸和形状的粉末。
3.粉末的成型:成型是将粉末转变为所需形状的工艺。
常用的成型方法包括压制、挤出、注射成型和3D打印等。
通过成型,粉末可以被固化成具有一定强度和形状的零件。
4.烧结:烧结是粉末冶金过程中的关键步骤之一。
经过成型的粉末件放入高温环境中,粉末颗粒与颗粒之间发生扩散和结合,形成致密的材料。
烧结温度和时间会影响材料的致密性和力学性能。
5.后处理:烧结后的材料可能需要进行后处理。
常用的后处理方法包括热处理、表面处理和加工等。
通过后处理,可以改善材料的性能和功能。
粉末冶金的应用领域粉末冶金广泛应用于各个领域,包括汽车、航空航天、电子、能源、医疗和军工等。
1.汽车行业:粉末冶金技术在汽车行业中得到广泛应用。
例如,通过粉末冶金可以制备高强度和轻质的发动机零件和齿轮等关键部件,提高汽车的燃油效率和排放性能。
2.航空航天:航空航天行业对材料的要求非常高。
粉末冶金可以制备出具有优异的高温强度和耐腐蚀性能的钛合金和镍基合金等材料,用于制造航空发动机和航天器件。
3.电子:在电子行业中,粉末冶金可以制备具有高导电性和磁导率的材料,例如铜粉末用于制造电子线路板和电磁元件。
4.能源:粉末冶金在能源领域的应用主要集中在制备高温抗氧化和热电材料。
例如,通过粉末冶金可以制备铁素体不锈钢和铬基合金等材料,用于制造高温炉和热交换器等设备。
粉末冶金的原理
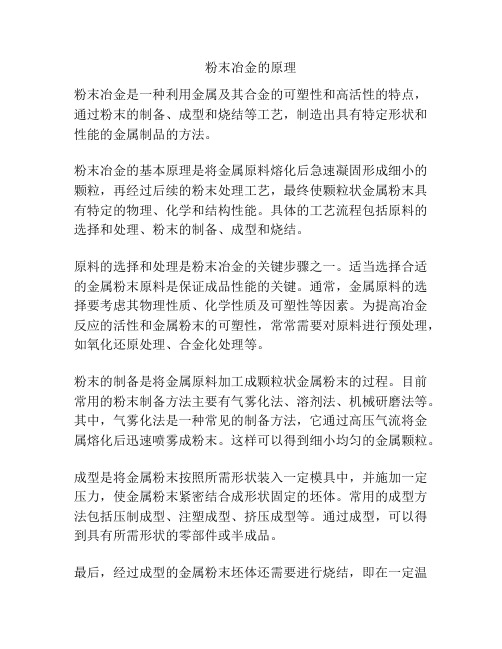
粉末冶金的原理粉末冶金是一种利用金属及其合金的可塑性和高活性的特点,通过粉末的制备、成型和烧结等工艺,制造出具有特定形状和性能的金属制品的方法。
粉末冶金的基本原理是将金属原料熔化后急速凝固形成细小的颗粒,再经过后续的粉末处理工艺,最终使颗粒状金属粉末具有特定的物理、化学和结构性能。
具体的工艺流程包括原料的选择和处理、粉末的制备、成型和烧结。
原料的选择和处理是粉末冶金的关键步骤之一。
适当选择合适的金属粉末原料是保证成品性能的关键。
通常,金属原料的选择要考虑其物理性质、化学性质及可塑性等因素。
为提高冶金反应的活性和金属粉末的可塑性,常常需要对原料进行预处理,如氧化还原处理、合金化处理等。
粉末的制备是将金属原料加工成颗粒状金属粉末的过程。
目前常用的粉末制备方法主要有气雾化法、溶剂法、机械研磨法等。
其中,气雾化法是一种常见的制备方法,它通过高压气流将金属熔化后迅速喷雾成粉末。
这样可以得到细小均匀的金属颗粒。
成型是将金属粉末按照所需形状装入一定模具中,并施加一定压力,使金属粉末紧密结合成形状固定的坯体。
常用的成型方法包括压制成型、注塑成型、挤压成型等。
通过成型,可以得到具有所需形状的零部件或半成品。
最后,经过成型的金属粉末坯体还需要进行烧结,即在一定温度下对金属粉末进行加热处理,使其颗粒之间发生结晶和扩散,相互融合并形成坚固的金属材料。
烧结可以通过自发热烧结、辅助烧结等方法来实现。
烧结过程中,金属粉末之间的氧化物和杂质也会在高温下被还原和挥发。
通过以上的处理工艺,粉末冶金可以制备出具有复杂形状、高强度、良好磨损性能和耐磨性能的金属制品。
由于粉末冶金具有成本低、能耗少、无需后加工等优势,因此在汽车、航空航天、工具等领域得到广泛应用。
粉末冶金原理第四章

4.2 粉末退火
粉末的退火可使氧化物还原,降低碳 和其他杂质的含量,提高粉末的纯度, 同时还能消除粉末的加工硬化,稳定 粉末的晶体结构。用还原法、机械研 磨法、电解法、喷雾法以及羰基离解 法所制得的粉末通常都要退火处理。
4.3 团聚粉末的分散
图4-1 颗粒接触处液体 作用产生粉末团聚
4.3 团聚粉末的分散
4.5 粉末的充填
4.5.1 粉末充填的意义 4.5.2 改善粉末充填的技术
4.5.1 粉末充填的意义
图4-7 粉末的松装密度与颗粒形状的关系
4.5.2 改善粉末充填的技术
图4-9 由大小颗粒组成的混合粉的 成分与粉末松装密度的关系
4.5.2 改善粉末充填的技术
图4-10 颗粒粒径比对混合 粉末松装密度的影响
4.4.5 干燥粉末的混合
图4-4 粉末在螺旋混合器中的对流混合和叶片式混合机的剪切混合
4.4.5 干燥粉末的混合
图4-5 混料器 a)圆筒 b)立方体 c)双锥筒 d)V形筒
4.4.5 干燥粉末的混合
图4-6 工艺条件对混合速度的影响
4.4.6 混合粉末的密度计算
混合后的粉末应当注意以下几点:避 免振动已经干燥的粉末;装料时不要 让干燥的粉末自由落下,因为这样易 发生粒度偏析;对粉末-黏结剂的混合 物来说,尽量减少粉末间不必要的剪 切。
图4-2 粉末颗粒研磨后发生明显的解团聚,形状发生改变
4.4 粉末混合
4.4.1 4.4.2 4.4.3 4.4.4 4.4.5 4.4.6
粉末混合的意义 粉末形状、粒度和纯度调整 混合物的均匀性 粉末混合方法 干燥粉末的混合 混合粉末的密度计算
4.4.1 粉末混合的意义
如前所述,混合和合批是压制前两个 常用的预处理步骤,它们的共同点是 将粉末混合均匀。不同点是合批是指 将成分相同而粒度不同的粉末或不同 生产批次的粉末进行均匀混合,保持 产品的同一性;而混合是指将成分不 同的粉末均匀混合,得到新成分的材 料。通过合批可以达到控制粉末粒度 分布的目的。
粉末冶金成型原理

中小学生足球学习兴趣的提高策略分析随着体育教育的普及和足球运动的热度不断增加,越来越多的中小学生对足球运动产生了浓厚的兴趣。
如何提高中小学生对足球学习的兴趣,让他们在足球运动中得到快乐和成长,是每个足球教练和老师都需要思考和关注的问题。
本文将分析并总结一些有效的策略,帮助中小学生提高足球学习兴趣。
一、注重趣味性和互动性中小学生的足球学习应该是一种快乐的体验。
教练和老师们可以通过增加趣味性和互动性,激发学生对足球的兴趣。
可以利用小游戏和趣味赛事的形式,让学生在轻松愉快的氛围中学习和训练足球技能,增强学生的参与感和归属感。
还可以引入一些趣味性的训练器材和设备,如彩色训练球、趣味障碍训练道具等,让学生在训练中感受到乐趣。
二、激发学生的竞争欲望竞争是足球运动中不可缺少的元素,教练和老师们可以通过设置一些竞赛和比赛,激发学生的竞争欲望,让他们在比赛中感受到胜利的喜悦和失败的挫折,从而提高学生的学习兴趣和积极性。
还可以利用小组合作的形式进行比赛训练,培养学生的团队合作意识和集体荣誉感,增强学生的足球学习兴趣。
三、关注学生的个性化需求中小学生的个性差异较大,教练和老师们应该关注学生的个性化需求,根据学生的特长和兴趣,灵活调整训练内容和方式。
对于对足球技能有特长的学生,可以给予重点培养和引导,提供更高级的技战术训练;对于对足球漫技能较为薄弱但对足球运动很感兴趣的学生,可以通过一些外围活动和故事分享,激发他们学习足球的热情。
只有关注学生的个性化需求,才能真正激发学生的学习兴趣。
四、营造积极的学习氛围教练和老师们应该努力营造一个积极向上的足球学习氛围,让学生在积极的氛围中学习和成长。
可以通过举办足球文化节、足球运动会等活动,让学生感受到足球运动的魅力和魅力,增强他们对足球的热爱。
还可以邀请一些足球明星或资深教练来学校做客,与学生分享足球学习经验和技巧,激发学生的学习兴趣。
五、鼓励学生坚持训练和比赛足球学习是一个长期的过程,教练和老师们应该鼓励学生坚持训练和比赛,培养学生的毅力和耐心。
第4章-粉末的成形

13
4.2.3 压制过程
压制过程可分为四个阶段:
①粉末颗粒移动,孔隙减小,颗粒间相互挤紧; ②粉末挤紧,小颗粒填入大颗粒间隙中,颗粒开始
有变形; ③粉末颗粒表面的凹凸部分被压紧且啮合成牢固接
触状态; ④粉末颗粒加工硬化到了极限状态,进一步增高压
力,粉末颗粒被破坏和结晶细化。
讲解:XX
14
1、压坯密度不均匀及危害
V压m 11 Vm d
⑤ 孔隙度系数(孔隙相对容比)
V 孔 V 压 V m 1 1 1 1 d
V m V m
d d d1
讲解:XX
49
(二)巴尔申压制理论
在忽略加工硬化情况下,虎克定律也可用于塑性变形,对粉末 压制过程应用虎克定律,最终可得出
ln Pln P ma lx( 1 )
成形
无压成形
加压成形
松 装 烧 结
粉 浆 浇 注
模 压 成 形
热 压 成 形
等 静 压 成 形
轧 制 成 形
离 心 成 形
挤爆 压炸 成成 形形
讲解:XX
2
本章主要内容
• 粉末的预处理 • 普通模压法成形 • 压制理论 • 特殊成形方法
讲解:XX
3
§4.1 粉末的预处理
• 预处理包括:退火、筛分、混合、制粒、 加润滑剂等。
② 巴尔申方程用于硬粉末比软粉末效果好,尤其在压制开 始阶段效果较好,但没普遍意义(未考虑加工硬化、摩擦及 固体的滞弹性)。
③川北方程在压制压力不太大时,是个较好的经验方程。 ④ 所有方程在导出过程中都没有考虑压坯的形状尺寸、模 壁摩擦力,在实际应用中存在一定偏差。
讲解:XX
55
§4.7 特殊成形方法
粉末冶金知识讲义
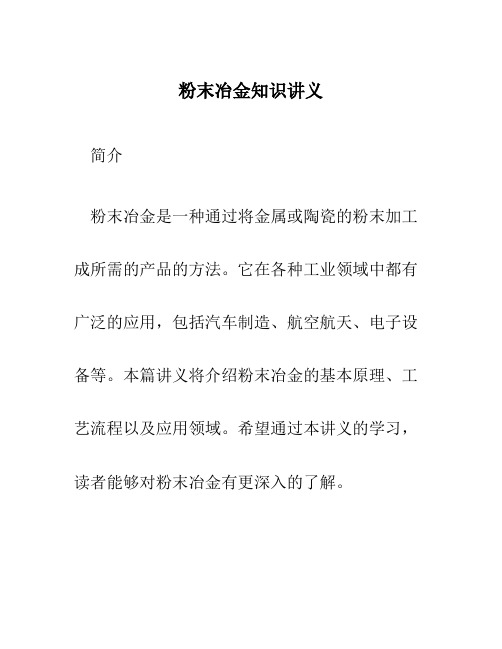
粉末冶金知识讲义简介粉末冶金是一种通过将金属或陶瓷的粉末加工成所需的产品的方法。
它在各种工业领域中都有广泛的应用,包括汽车制造、航空航天、电子设备等。
本篇讲义将介绍粉末冶金的基本原理、工艺流程以及应用领域。
希望通过本讲义的学习,读者能够对粉末冶金有更深入的了解。
粉末冶金的基本原理粉末冶金是利用金属或陶瓷的粉末制备材料的一种冶金方法。
它的基本原理是通过将粉末状的金属或陶瓷原料压制成形,在高温下进行烧结或热处理,使其形成致密的材料。
粉末冶金的主要原理包括:1.粉末制备:金属或陶瓷原料首先需要经过研磨和筛分等工艺步骤,制备成具有一定粒径和形状的粉末。
2.粉末成形:粉末通过压制工艺成形,常见的成形方法包括压制成型、注射成型和挤压成型等。
3.烧结或热处理:压制成形的粉末被置于高温下,经过烧结或热处理,使其形成致密的材料。
4.后续加工:经过烧结或热处理后的材料需要进行后续加工,例如机加工、表面处理等,以满足产品的具体要求。
粉末冶金的工艺流程粉末冶金的工艺流程包括粉末制备、成形、烧结或热处理以及后续加工等步骤。
具体工艺流程如下:粉末制备粉末制备是粉末冶金的第一步,它决定了最终材料的粒度和形状。
常见的粉末制备方法包括:•研磨:将金属块或陶瓷块通过研磨设备研磨成粉末状。
•气相沉积:通过将金属或陶瓷元素在高温下蒸发,然后在室温下与气体反应产生粉末。
•溶液法:通过将金属或陶瓷溶解在溶剂中,然后通过蒸发溶剂得到粉末。
成形成形是粉末冶金的第二步,它将粉末状的原料转化为所需的形状。
常见的成形方法包括:•压制成型:将粉末状原料放入模具中,通过压力将其固化成形。
•注射成型:将粉末与粘结剂混合后注射到模具中,通过固化将其成形。
•挤压成型:在高温下将粉末状原料通过挤压工艺转化为所需的形状。
烧结或热处理烧结或热处理是粉末冶金的关键步骤,它将成形后的粉末进行高温处理,使其结合成致密的材料。
常见的烧结或热处理方法包括:•烧结:将成形后的粉末置于高温下,使其颗粒之间发生结合,形成致密的材料。
粉末冶金的工艺流程-粉末的配制

粉末冶金成形前,要对粉末进行预处理及配制。预处理包括:退火、筛分、 制粒等。 退火
粉末的预先退火可使残留氧化物进一步还原、降低碳和其它杂质的含量,提 高粉末的纯度,消除粉末的加工硬化等。用还原法、机械研磨法、电解法、雾化 法以及羰基离解法所制得的粉末都要经退火处理。此外,为防止某些超细金属粉 末的自燃,需要将其表面钝化,也要作退火处理。经过退火后的粉末,压制性得 到改善,压坯的弹性后效相应减小。 筛分
将两种或两种以上不同成分的粉末均匀混合的过程。有时需将成分相同而粒 度不同的粉末进行混合,称为合批。混合质量不仅影响成形过程和压坯质量,而 且会严重影响烧结过程的进行和最终制品的质量。 混合有机械法和化学法两种方法
(1)机械法常用的混料机有球磨机、V 型混合器、锥形混合器、洒桶式混合 器、螺旋混合器等。机械法混料又可分为干混和湿混。铁基等制品生产中广泛采 用干混,制备硬质合金混合料则经常使用湿混。湿混时常用的液体介质为酒精、 汽油、丙酮等。为了保证湿混过程能顺利进行,对湿混介质的要求是:不与物料 发生化学反应,沸点低易挥发,无毒性,来源广泛,成本低等。湿混介质的加入Байду номын сангаас量必须适当,否则不利于研磨和高效率的混合。
把颗粒大小不匀的原始粉末进行分级,使粉末能够按照粒度分成大小范围更 窄的若干等级。通常用标准筛网制成的筛子或振动筛来进行粉末的筛分。 制粒
将小颗粒的粉末制成大颗粒或团粒的工序,常用来改善粉末的流动性。在硬 质合金生产中,为了便于自动成形,使粉末能顺利充填模腔就必须先进行制粒。 能承担制粒任务的设备有滚筒制粒机、圆盘制粒机和振动筛等。 混合
此外,生产粉末冶金过滤材料时,在提高制品强度的同时,为了保证制品有 连通的孔隙,可加入充填剂。能起充填作用的物质有碳酸钠等,它们既可以防止 形成闭孔隙,还会加剧扩散过程,从而提高制品的强度。充填剂常常以盐的水溶 液方式加入。
粉末冶金原理

粉末冶金原理粉末冶金是一种利用金属粉末或者金属粉末与非金属粉末混合后,再经过压制和烧结等工艺制造金属零件的方法。
在粉末冶金工艺中,粉末的特性和原理起着至关重要的作用。
粉末冶金原理主要包括粉末的制备、成型、烧结和后处理等几个方面。
首先,粉末的制备是粉末冶金的第一步。
金属粉末的制备可以通过机械研磨、化学方法和物理方法等多种途径。
机械研磨是指将金属块或者金属棒经过研磨机械的加工,得到所需的金属粉末。
化学方法则是通过化学反应得到金属粉末,而物理方法则是通过物理手段如电解、喷雾等得到金属粉末。
在粉末冶金中,粉末的制备质量直接影响着最终制品的质量和性能。
其次,成型是指将金属粉末进行成型工艺,使其成为所需形状的工件。
成型方法包括压制成型、注射成型、挤压成型等多种方式。
压制成型是将金属粉末放入模具中,再经过压制机械的加工,使其成为所需形状的工件。
注射成型则是将金属粉末与粘结剂混合后,通过注射成型机械将其注射成型。
挤压成型是将金属粉末放入容器中,再通过挤压机械的作用,使其成为所需形状的工件。
成型工艺的精密度和成型质量对于最终产品的质量和性能至关重要。
接下来,烧结是粉末冶金中的关键工艺。
烧结是指将成型后的金属粉末在高温下进行加热处理,使其颗粒间发生结合,形成致密的金属材料。
烧结工艺的温度、压力和时间等参数对于最终产品的致密度、硬度和耐磨性等性能有着重要影响。
最后,后处理是指对烧结后的金属制品进行表面处理、热处理和精加工等工艺。
表面处理可以提高金属制品的耐腐蚀性和美观度,热处理可以改善金属制品的硬度和强度,精加工则可以提高金属制品的精度和表面质量。
总之,粉末冶金原理是一个复杂而又精密的工艺体系,涉及到材料科学、机械工程、化学工程等多个领域的知识。
通过对粉末的制备、成型、烧结和后处理等环节的深入研究和探索,可以不断提高粉末冶金工艺的精度和效率,为制造业的发展和进步提供更加可靠的技术支持。
粉末成形第四章
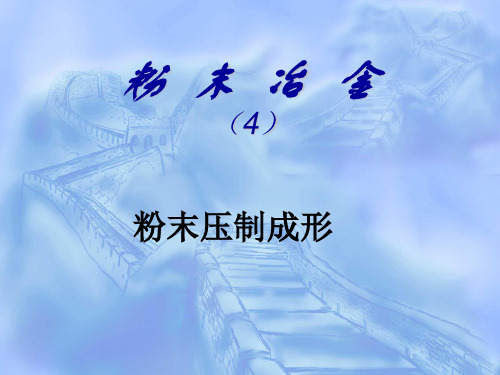
1
P
ξ—侧压力与正压力之比,即侧压系数;ν—泊松比
侧压系数ξ公式的假定
假定在弹性变形范围内有横向变形 没有考虑粉体的塑性变形 没有考虑到粉末特性及模壁及模壁变形 因此侧压力只能是一种估计数值
2)侧压力系数与压坯密度的关系
研究得出,粉末的侧压系数与密度的关系 有
P侧 P
最大
b 0.164 0.079 0.171 0.096 0.153 0.124 0.228 0.252
川北对十种粉末进行 压制得到的粉末体 积减少率与压力的 关系
3)黄培云压制理论方程
(d m d 0 )d m lg ln lg P lg M (d m d )d 0
dm—致密金属密度;d0—压坯原始密度;d—压坯 密度;P—压制压强;M—相当于压制模数;m—相 当于硬化指数 上述方程的适用方面: 黄培云方程:对软粉末或硬粉末适用效果较好 巴尔申方程:对硬粉末适用效果较好 川北公夫方程:在压制压力不太大时优越性显著
4、压制过程中力的分析
压制压力作用 在粉体后 P1—净压力;
P1使粉末产生位移,变形,克服粉末的 内摩擦力 P2克服粉末颗粒与模壁之间外摩擦力
P2 —压力损失
总 压
力
P = P1+ P2
4.1侧压力
侧压力—粉末体在压模内受压时,压坯会向周围膨 胀,模壁就会给压坯一个大小相等方向相反的作 用力。 或者压制过程中由垂直压力所引起的模壁施加于压 坯的侧面压力
0.03 0.03
0.02
0.23 0.3
0.1
0.3
0.25
退火气氛对粉末压制性能的影响
压力/MPa 200 400 压坯的孔隙度% H2 34.4 23.8 HCl 32.0 21.0 真空/Pa 4 2.5
粉末冶金工艺过程
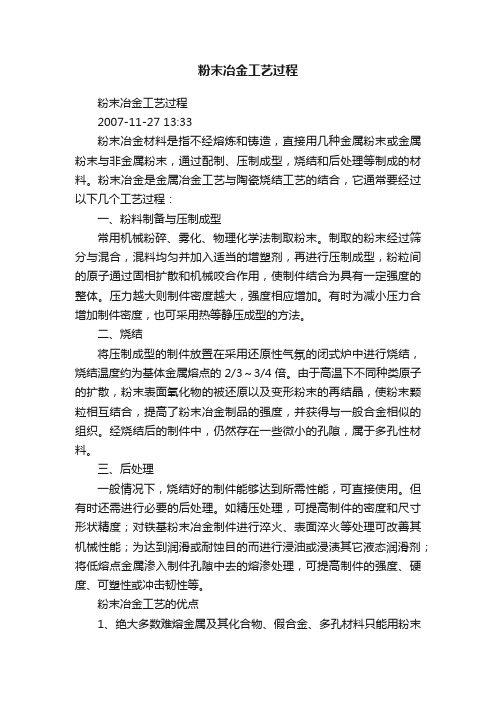
粉末冶金工艺过程粉末冶金工艺过程2007-11-27 13:33粉末冶金材料是指不经熔炼和铸造,直接用几种金属粉末或金属粉末与非金属粉末,通过配制、压制成型,烧结和后处理等制成的材料。
粉末冶金是金属冶金工艺与陶瓷烧结工艺的结合,它通常要经过以下几个工艺过程:一、粉料制备与压制成型常用机械粉碎、雾化、物理化学法制取粉末。
制取的粉末经过筛分与混合,混料均匀并加入适当的增塑剂,再进行压制成型,粉粒间的原子通过固相扩散和机械咬合作用,使制件结合为具有一定强度的整体。
压力越大则制件密度越大,强度相应增加。
有时为减小压力合增加制件密度,也可采用热等静压成型的方法。
二、烧结将压制成型的制件放置在采用还原性气氛的闭式炉中进行烧结,烧结温度约为基体金属熔点的2/3~3/4倍。
由于高温下不同种类原子的扩散,粉末表面氧化物的被还原以及变形粉末的再结晶,使粉末颗粒相互结合,提高了粉末冶金制品的强度,并获得与一般合金相似的组织。
经烧结后的制件中,仍然存在一些微小的孔隙,属于多孔性材料。
三、后处理一般情况下,烧结好的制件能够达到所需性能,可直接使用。
但有时还需进行必要的后处理。
如精压处理,可提高制件的密度和尺寸形状精度;对铁基粉末冶金制件进行淬火、表面淬火等处理可改善其机械性能;为达到润滑或耐蚀目的而进行浸油或浸渍其它液态润滑剂;将低熔点金属渗入制件孔隙中去的熔渗处理,可提高制件的强度、硬度、可塑性或冲击韧性等。
粉末冶金工艺的优点1、绝大多数难熔金属及其化合物、假合金、多孔材料只能用粉末冶金方法来制造。
2、由于粉末冶金方法能压制成最终尺寸的压坯,而不需要或很少需要随后的机械加工,故能大大节约金属,降低产品成本。
用粉末冶金方法制造产品时,金属的损耗只有1-5%,而用一般熔铸方法生产时,金属的损耗可能会达到80%。
3、由于粉末冶金工艺在材料生产过程中并不熔化材料,也就不怕混入由坩埚和脱氧剂等带来的杂质,而烧结一般在真空和还原气氛中进行,不怕氧化,也不会给材料任何污染,故有可能制取高纯度的材料。
粉末冶金原理
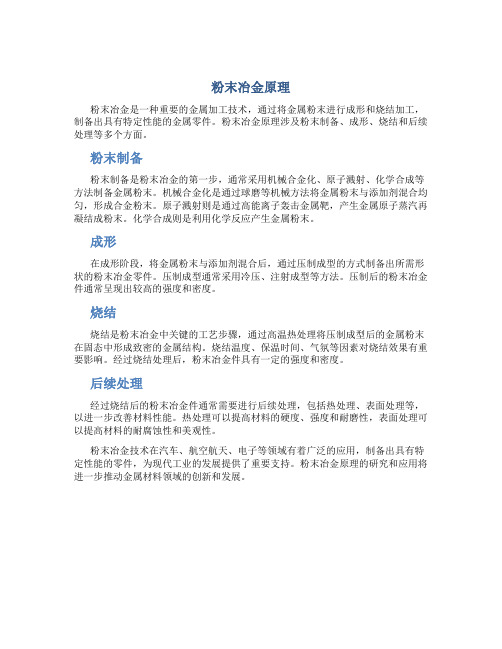
粉末冶金原理
粉末冶金是一种重要的金属加工技术,通过将金属粉末进行成形和烧结加工,制备出具有特定性能的金属零件。
粉末冶金原理涉及粉末制备、成形、烧结和后续处理等多个方面。
粉末制备
粉末制备是粉末冶金的第一步,通常采用机械合金化、原子溅射、化学合成等方法制备金属粉末。
机械合金化是通过球磨等机械方法将金属粉末与添加剂混合均匀,形成合金粉末。
原子溅射则是通过高能离子轰击金属靶,产生金属原子蒸汽再凝结成粉末。
化学合成则是利用化学反应产生金属粉末。
成形
在成形阶段,将金属粉末与添加剂混合后,通过压制成型的方式制备出所需形状的粉末冶金零件。
压制成型通常采用冷压、注射成型等方法。
压制后的粉末冶金件通常呈现出较高的强度和密度。
烧结
烧结是粉末冶金中关键的工艺步骤,通过高温热处理将压制成型后的金属粉末在固态中形成致密的金属结构。
烧结温度、保温时间、气氛等因素对烧结效果有重要影响。
经过烧结处理后,粉末冶金件具有一定的强度和密度。
后续处理
经过烧结后的粉末冶金件通常需要进行后续处理,包括热处理、表面处理等,以进一步改善材料性能。
热处理可以提高材料的硬度、强度和耐磨性,表面处理可以提高材料的耐腐蚀性和美观性。
粉末冶金技术在汽车、航空航天、电子等领域有着广泛的应用,制备出具有特定性能的零件,为现代工业的发展提供了重要支持。
粉末冶金原理的研究和应用将进一步推动金属材料领域的创新和发展。
粉末的预烧结名词解释

粉末的预烧结名词解释粉末冶金是一种重要的金属材料制备方法,该方法利用粉末作为原料,通过压制成型和烧结等工艺,制得形状复杂、性能优越的金属制品。
而预烧结是粉末冶金过程中的一个重要环节,它在最终烧结之前对粉末进行预处理,以提高材料的成型性、密度和力学性能。
预烧结是指将金属粉末在高温下经过一段时间的加热和冷却过程,在烧结之前先进行部分烧结的过程。
预烧结的主要目的是通过热处理改善粉末表面的一些性能,提高烧结过程中的烧结活性和成品的力学性能。
首先,预烧结可以去除粉末表面的氧化层。
在粉末制备的过程中,由于金属粉末容易与空气中的氧发生反应而形成氧化物,这些氧化物会对烧结过程产生一定的不利影响。
通过预烧结,可以在高温下使氧化物发生还原反应,将其还原为金属。
这样可以减少氧化物的含量,改善粉末的可烧结性,提高材料的致密性和力学性能。
其次,预烧结还能改善粉末的形状和流动性。
在粉末制备过程中,由于加工条件的限制或其他原因,粉末的颗粒形状往往不规则,流动性较差。
经过预烧结后,金属粉末颗粒会发生一定程度的形状改变和粒子聚合,使粉末表面变得更加平整光滑,颗粒之间的间隙减少,从而提高了粉末的成型性和流动性。
此外,预烧结还可以提高粉末的烧结活性。
在烧结过程中,金属粉末需要通过原子间的扩散来实现颗粒间的结合。
而经过预烧结后,金属颗粒表面的活化能得到降低,扩散速率增加,有利于烧结过程的进行。
这样可以缩短烧结时间,提高烧结的效率。
总的来说,预烧结是粉末冶金过程中的一项关键工艺,通过对金属粉末进行一定时间的高温处理,能够改善粉末的表面性能、成型性能和力学性能。
预烧结的主要作用包括去除氧化物、改善粉末的形状和流动性,以及提高粉末的烧结活性。
通过合理控制预烧结的温度、时间和气氛等参数,可以实现对粉末性能的调控和优化,为后续烧结工艺提供良好的基础。
粉末冶金技术在诸多领域中得到广泛应用,如汽车制造、航空航天、机械制造等。
预烧结技术的研究和应用,能够提高金属材料的综合性能,拓展材料的应用范围,推动工程材料的进步和创新。
粉末冶金原理

粉末冶金原理
粉末冶金是一种通过粉末冶金工艺制备金属、合金、陶瓷和复合材料的方法。
它是一种高效的材料制备技术,具有原料利用率高、产品尺寸精度高、材料组织均匀等优点,因此在航空航天、汽车、电子、机械等领域得到广泛应用。
粉末冶金的基本原理是将金属粉末或合金粉末按一定的成型方法制备成所需形
状的坯料,然后通过烧结或热压等方法将其致密化,最终得到所需的产品。
这种方法可以制备复杂形状的产品,且可以调控产品的性能,因此在一些特殊领域有着独特的优势。
粉末冶金的工艺包括粉末制备、成型和烧结等步骤。
首先是粉末的制备,通常
采用机械球磨、化学法、电化学法等方法制备金属或合金粉末。
然后是成型,通过压制、注射成型等手段将粉末压制成所需形状的坯料。
最后是烧结,将压制好的坯料在一定的温度下进行热处理,使粉末颗粒之间发生扩散与结合,最终形成致密的产品。
粉末冶金的优点之一是可以制备高性能的材料。
由于粉末冶金可以制备复杂形
状的产品,因此可以设计出更加符合工程需求的材料,提高材料的使用性能。
另外,由于粉末冶金可以控制材料的成分和微观结构,因此可以调控材料的力学性能、导热性能、磁性能等,满足不同领域的需求。
除此之外,粉末冶金还可以实现材料的资源化利用。
由于粉末冶金可以利用废料、废料料等再生资源进行材料制备,因此可以减少对原材料的依赖,实现资源的再利用,降低生产成本,减少对环境的影响。
总的来说,粉末冶金是一种高效的材料制备技术,具有制备高性能材料、实现
资源化利用等优点,因此在现代工业中得到了广泛的应用。
随着科技的发展,相信粉末冶金技术会不断完善,为人类社会的发展做出更大的贡献。
粉末冶金步骤

粉末冶金步骤
粉末冶金是一种利用粉末材料制造金属零件的技术,它可以制造出具
有良好外观、精确尺寸和质量的零件。
粉末冶金的步骤主要包括:
1.粉末准备:首先,需要准备粉末材料,根据要求的零件材料,选择
合适的粉末材料,并将其经过粉碎、筛选、混合等处理,以达到要求
的粉末质量。
2.粉末成型:粉末成型是粉末冶金的关键步骤,它可以采用压制、挤压、热压等方法,将粉末材料压制成所需的零件形状。
3.烧结:烧结是将粉末成型的零件经过高温烧结,使粉末材料熔融,
形成紧密的金属结构,从而达到粉末冶金的目的。
4.热处理:热处理是指将烧结后的零件经过适当的温度和时间,使其
结构发生变化,从而改善零件的性能。
5.表面处理:表面处理是指将热处理后的零件经过表面处理,使其表
面光洁,抗腐蚀性能更好,从而满足使用要求。
6.检测:最后,需要对粉末冶金的零件进行检测,以确保零件的质量,确保零件的尺寸、形状、表面质量等满足要求。
粉末冶金是一种复杂的技术,需要经过多个步骤,才能制造出具有良
好外观、精确尺寸和质量的零件。
正确的步骤和技术操作,可以有效
提高粉末冶金的效率,提高零件的质量,从而满足客户的要求。
粉末冶金原理-粉末成形-第一讲
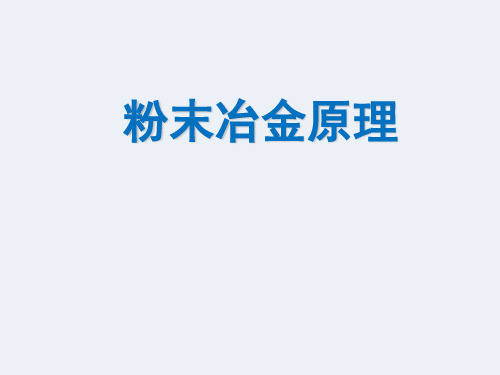
4.2粉体压制成形原理与技术
粉体压制成形-位移和变形
粉末的位移
粉末位移的形式
a)粉末颗粒的接近 b)粉末颗粒的分离 c)粉末颗粒的滑动 d)粉末颗粒的转动 e)粉末颗粒因粉碎而产生的移动
粉末在松装堆集时,由于表面不规则,彼此之间有摩擦, 颗粒相互搭架而形成拱桥孔洞的现象,称为拱桥效应。
施加压力时,拱桥效应遭到破坏,粉末颗粒彼此填充孔
压力停止后,压坯出现膨胀现象 (弹性后效)
压制示意图 1—阴模 2—上模冲 3—下模冲 4—粉末20
4.2粉体压制成形原理与技术
粉体压制成形-位移和变形
压制过程中,粉末之 间的孔隙度大大降低, 彼此的接触面积显著 增大; 粉末在压模内经受压 力作用后变得较密实 而具有一定的形状和 强度。
金属粉末压制过程中的简化阶段
可以实现原子级混合; W-Cu-Ni包覆粉末的制造工艺: W粉+Ni(NO3)2溶液→混合→热解还原(700-750℃) →W-Ni包覆粉 +CuCl2 溶 液 → 混 合 → 热 解 还 原 ( 400-450℃ ) →W-Cu-Ni包覆粉末
9
4.1成形前粉末的预处理
混合物的均匀性
大范围的分散、部分均匀化的团聚结构、理想的均匀 分散结构。
压制时粉末的变形
24
4.2粉体压制成形原理与技术
粉体压制成形-位移和变形
粉末的变形 随着压力的增加,产生新的颗粒接触,堆积更加致
密,孔隙度减少。
压坯孔隙度、颗粒接触点数以及接触点处面积与压制压力的关系
25
4.2粉体压制成形原理与技术
粉体压制成形-位移和变形
粉末的变形 压力低的时候,塑性变形
31
粉末冶金原理-粉末成形-第二讲
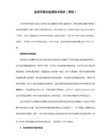
16
4.2粉体压制成形原理与技术
压制压力与压坯密度关系的解析
• 黄培云压制理论:考虑粉末的非线性弹滞体的特征和压形 时大幅度变化
lg ln
m m
0 0
n lg
p lg M
:压坯密度;0:压坯原始密度 m:致密金属的密度;
n:硬化指数的倒数; M:压制模量。
不规则粉末在压制过程中的接触面积比规则形状粉末大,压 坯强度高,成形性好。 粉末松装密度的影响
松装密度小,模具的高度及模冲的长度必须大,压制高密度 压坯时,密度分布容易不均匀。
26
4.2粉体压制成形原理与技术
压坯密度的分布分析 影响压制过程的因素
• 粉末的性能 材料及粉末组成的影响
粉末的强度越高,压制成 形越难。
面,边缘的应力比中心 部位的大; 远离模冲的底部,中心 部位的应力比边缘应力 大。
3
4.2粉体压制成形原理与技术
侧压力和模壁摩擦力
侧压力与正压力关系:
P侧
=
P=
1
P
测压系数 :单位侧压力与单位压制压力的比值
测压系数
=
P侧 P压
=最大
最大 为达到理论密度的测压系数;
• 常用的压坯强度与压坯相对密度的关系
C 0 m
C为常数;m 6
18
4.2粉体压制成形原理与技术
压制压力对压坯强度的影响
• 压坯强度的提高依赖于压坯密度的提高,压坯密度的提高又 需要高的压制压力。如何建立压坯强度与压制压力的关系?
• 途径一:通过压坯强度与压坯密度的关系、压坯密度与压制 压力的关系建立模型(解析的)。
• 第Ⅲ阶段:压力继续增大超过某一 定值后,随着压力的升高,压坯的 相对密度继续增加。(粉末颗粒开 始变形,位移和变形都起作用)
- 1、下载文档前请自行甄别文档内容的完整性,平台不提供额外的编辑、内容补充、找答案等附加服务。
- 2、"仅部分预览"的文档,不可在线预览部分如存在完整性等问题,可反馈申请退款(可完整预览的文档不适用该条件!)。
- 3、如文档侵犯您的权益,请联系客服反馈,我们会尽快为您处理(人工客服工作时间:9:00-18:30)。
成形剂及其分解产物不与粉末发生反应
分解温度范围较宽 分解产物不污染环境
润滑剂 ↓粉末颗粒与模壁间的摩擦
摩擦力导致
压坯密度分布不均匀 影响被压制工件的表面质量 降低模具的使用寿命
粉末压制用的润滑剂
硬脂酸
硬脂酸锌 工业润滑蜡
PEG
(二硫化钼、石墨粉、硫磺粉也可起润滑作用)
难以通过压制所产生的变形而赋予粉末坯体足够的 强度
添加成形剂提高生坯强度,利于成形
2)流动性差的粉末 粘结剂作用
细粉或轻质粉末
适当增大粉末粒度,减小颗粒间的摩擦力
改善粉末流动性,提高压制性能
橡胶、硬脂酸、石蜡、SBS 、PEG、PVA等
选择准则
能赋予待成形坯体以足够的强度
易于排除
末压制性能
用还原法、机械研磨法、电解法、喷雾法以及
羰基离解法所制取的粉末通常都要进行退火处理。
粉末钝化
使细粉末适度变粗,或形成氧化薄膜,防止粉末 自燃
退火温度
高于回复-再结晶温度,(0.5-0.6)Tm 电解铜粉的退火温度约为300℃,电解铁粉或电解 镍粉约为700 ℃,不能超过900 ℃
退火气氛 还原性气氛(CO,H2),惰性气氛,真空
在要求清除杂质和氧化物,即进一步提高粉末化学纯度时,要采用 还原性气氛(氮、分解氨、转化天然气或煤气等)或真空退火; 消除粉末的加工硬化或者使细粉末粗化防止自燃时,就可以采用惰
性气体作为退火气氛。
2、合批与混合 blending
混合
and
mixing
不同成分的粉末借助于外力作用实现颗粒组份间分 布均匀的过程 合批 同类粉末或粉末混合物的混合 消除因粉末在运输过程中产生的偏析或在粉末生产 过程中不同批号粉末之间的性能差异 获得性能均匀的粉末料
喷雾干燥制粒全过程是在密封系统中形成的,共分为四个阶段:①料浆的雾 化;②液滴群与加热介质想接触;③液滴群干燥;④料粒与加热介质分离。
5、 成形剂(binder)和润滑剂(lubricant) 成形剂 (非增塑成形):为了提高压坏强度或为了 防止粉末混合料偏析而添加的物质,有时也叫 粘结剂,在烧结前或烧结时将该物质除掉 场合 1)硬质粉末:如硬质合金,陶瓷等 粉末变形抗力很高
机械法混合与化学法混合
机械混合方式
干混法:铁基及其它粉末冶金零件的生产
湿混法:硬质合金或含易氧化组份合金的生产
WC与Co粉之间除产生一般的混合均匀效果
发生显著的细化效果
一般采用工业酒精作为研磨介质
湿磨的主要优点
有利于环境保护
无粉尘飞扬和减轻噪音 提高破碎效率,有利于粉末颗粒的细化 保护粉末不氧化 不足 操作工序增加 粉料干燥增加能耗
细小颗粒或硬质粉末 为了成形添加成形剂 改善流动性添加粘结剂 进行自动压制或压制形状较复杂的大型 P/M制品 粉末结块 原理 借助于聚合物的粘结作用将若干细小颗粒 形成团粒
减小团粒间的摩擦力 大幅度降低颗粒运动时的摩擦面积 增大运动单元的动力(重量)
制粒方法
擦筛制粒 喷雾干燥 挤压制粒 旋转盘制粒
即强化颗粒的对流与剪切作用
偏析(segregation)现象
反混合现象
涉及相容性问题—“物以类聚”
由颗粒之间密度差异引起 粒度差异 颗粒形状差异
球形颗粒与针状颗粒具有最小的偏析趋势
混合均匀程度和效率取决于 粉末颗粒的尺寸及其组成 颗粒形状 待处理粉末组元间比重差异 混合设备的类型 对于给定的粉末和混合设 混合工艺 备,最佳混合工艺一般 装料量 采用实验加以确定 球料比 转速 研磨体的尺寸及其搭配
常用润滑剂
常用润滑剂的添加量为0.5%~1.5%(质量分数)。对于金 属粉末,经常采用Al、Zn、Li、Mg和Ca的硬脂酸盐作为润 滑剂。硬脂酸分子链包括12~22个碳原子,这些碳链表面活 性好,而且熔化温度相对较低,硬脂酸盐通常是雾化法制 备的球形颗粒,粒度通常在10~30μm之间 。
润滑剂 硬脂酸锌 氧化物 质量分数 /% 14 软化温度 /℃ 100~120 熔化温度 密度 /℃ /(g*m-3 ) 130 1.09
2、粉末润滑 粉末润滑指润滑剂与金属粉末混合,其优点是润滑剂不 仅在模壁上,而且也在粉末颗粒之间。 粉末润滑的条件: a.将润滑剂磨成细粉 b.润滑剂的量取决与坯块形状 c.润滑时间:20~40min 优点:减少压制压力,改善坯块密度分布,提高坯块密 度; 缺点:润滑剂在烧结过程中分解产生的气体从炉子的预 热带逸出,使烧结时的保护气氛流速加快,使炉子的 管理变得复杂。 理论上模壁润滑更好,但是它不容易与自动压制 设备配合,因此,通常把润滑剂与金属粉末混合作为 压制前的最后一道工序。
消除元素粉末组元(特别是轻重组元)间的偏析
3、筛分
筛分的目的在于把颗粒大小不同的原始粉末进行分级。
通常用标准筛网或振动筛进行筛分, 而对于钨钼等难熔金属的细粉或者超细粉则使用空气分 级的方法。
4 制粒 pelletizing or granulating
定义:制粒是将小颗粒的粉末制成大颗粒或团粒的工序 目的:常用于改善粉末的流动性。 粉末制粒后,其颗粒直径比原始粉末粒径大, 每个颗粒周围可接触到的颗粒数目减少,故其 粘附性,凝聚性与相互磨擦力大为减弱,从而 改善与提高颗粒料的流动性。 作用: 制粒后粉末流动性好,粉末能顺利充填型腔,且便于压制, 能加少压模的损耗,延长模具寿命。同时还能提高制品的 尺寸和重量精度。 制粒工艺后细粉减少,颗粒不易碎裂,便于保管运输,使粉 尘飞扬和污染减少。
润滑方式
粉末内润滑internal lubrication
润滑剂直接加入粉末中
铁基粉末 润滑剂含量提高0.1% 坯件的无孔隙密度下降0.05g/cm3
模壁润滑die wall lubrication
静电喷涂
溶液涂敷
1、模壁润滑
在刚性模具中压制时,在模壁和模冲上涂润滑剂, 目的是使压制的坯块与模具容易分离,但由于粉末 体表面是粗造的,易刺穿涂在模壁上的润滑膜产生 摩擦,增加压制力,损坏模具。 对润滑剂的要求:既要附着到金属表面上,还要不渗 入到金属中。 润滑剂:硬脂酸、人造蜡、硬脂酸锌、硬脂酸
在滑动与离心状态,颗粒之间很少发生相 对运动,混合效果最差 而对于组元之间比重差异大的混合物体系 剧烈的抛落容易造成组元间的成分偏析,应 予避免
混合机理
严格意义上的扩散过程并不存在 实际上为微区内的颗粒对流
粉末颗粒混合通过对流与剪切作用实现
添加适当数量的研磨体可强化混合效果
球磨介质损耗
成本提高
混合机理简介
粉末床的运动行为
(a)粉末体整体滑动
(b)粉体局部坍塌
(c) 粉末整体滚动
(d)小瀑布状抛落
(e)大瀑布状抛落
(f)离心状
取决于 圆筒形混合器的转速 筒体的直径 二者对粉末床运动行为的影响可用Froude准 数描述 Fr=(ω2R)/g (惯性离心力/重力) 材料的物性(颗粒尺寸,颗粒形状等,主要影响粉 末的静态响应角,与颗粒间摩擦力大小有关) 装料量 筒壁的粗糙程度
第四章 成形前粉末的预处理
粉末原料由于最终产品性能的需要或者改善成形 过程的要求,在成形前都要经过一些预处理。
预处理包括:粉末退火、筛分、混合、制粒、加 润滑剂、成型剂等等。
1、还原退火 reducing and annealing
作用 还原氧化物、降低碳和其它杂质的含量,提高纯度
消除粉末加工硬化,稳定粉末的
CaO Li2O
9 5
115~120 195~200
160 220
1.03 1.01
静电喷涂模壁润滑系统
粉末润滑与模壁润滑零件表面质量差异
双锥形混料机
V形混料机
多维混料机
化学法混合
金属或金属化合物粉末与添加金属的盐 溶液均匀混合,或者是各组元全都以某种盐 的溶液形式混合,经沉淀、干燥、还原等处 理方法而得到均匀分布的混合粉末
化学法混合
混合较前者更为均匀,可以实现原子级混合 W-Cu-Ni包覆粉末的制造工艺 W粉+Ni(NO3)2溶液→混合→热解还原(700750℃) →W-Ni包覆粉 + CuCl2溶液→混合→热解还原( 400-450℃) →W-Cu-Ni包覆粉末 存在环保问题