离心风机结构形式
§6-4-1 离心式风机的结构
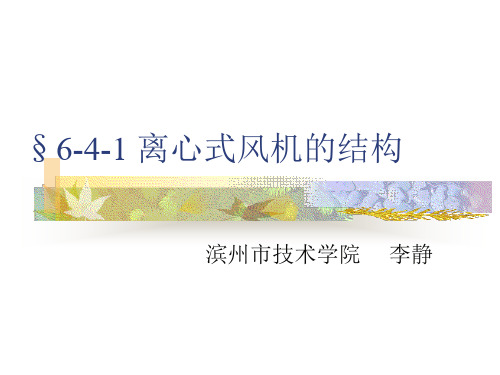
• • 图 (b):进气箱,通流截面是收敛的,进气室底端与进风口对
齐,可减少涡流。
2)进气箱进口横截面积Ai与 叶轮进口截面积A0之比不能 太小,太小会使风机压力和 效率显著下降。
一般 : Ai/ A0>1.5 最好: Ai/ A0=1.75~2.0
小。 • 蜗舌顶端与叶轮外径的间隙s,对噪声的影响较大。间隙s小,
噪声大;间隙s大,噪声减小。一般取s=(0.05~0.10)D2。 • 蜗舌顶端的圆弧r,对风机气动力性能无明显影响,但对噪声影
响较大。 圆弧半径r小,噪声会增大,一般取r=(0.03~0.06)D2。
小结:通过设备的机构特点对离心式风 机进行讲解,效果较好。
§6-4-1 离心式风机的结构
滨州市技术学院 李静
课型
新授课
课时
2
教学目标
知识目标:能试读离心式风机的结构纵剖图和实物图,说明他 们的结构及主要部件的作用。
技能目标:能试读主要部件图,说明它的结构、形式、特点和 基本原理。
德育目标:了解电厂中离心式风机的转子和静子部分的设备结 构。
教学重点 教学难点
教后记 对比离心式风机的结构学习本节内容,效果较好。 布置作业 P174 6-12 作业情况 完成较好,让学生通过图形和动漫来加深对离心式风机的认识。
离心式风机的结构
一、叶轮
• 结构:前盘、后盘、 叶片及轮毂等
• 平直前盘:制造工艺简单,但气流进口后分离损失较大,因而 风机效率较低。
• 弧形前盘:制造工艺较复杂,但气流进口后分离损失很小,效 率较高。
• 3)进气箱与风机出气口的相对位置,以α=90°为最佳,而以 α=180°为最差。
• 为了进行风机的调节,一般在进风口前或进气箱流道内装设进口 导流器。
外转子离心风机结构

外转子离心风机结构1.壳体:外转子离心风机的壳体通常采用优质的铁皮板制成,具有强度高、耐腐蚀等特点。
壳体内部包含了进气口、排气口等,起到保护转子和导叶的作用。
2.转子:转子是外转子离心风机的核心部件,它由蜗壳、叶轮、轴承等组成。
蜗壳位于转子的前端,用于引导气流,使其达到理想的流态。
叶轮是外转子离心风机的推进机构,通过高速旋转产生气流。
轴承则用于支撑转子的转动,保证其平稳运行。
3.导叶:导叶位于转子的后端,用于调整气流的方向和压力。
导叶通常由若干个可调节的导叶片组成,通过改变导叶片的角度,可以调整风机的性能参数,如流量、压力等。
导叶的调整通常由电动或手动控制系统完成。
4.进气口和排气口:进气口是外转子离心风机从外界吸气的通道,排气口则是将气流排出的通道。
进气口和排气口通常位于风机的侧面,通过进气和排气口的设计合理,可以提高风机的排气效率。
外转子离心风机的工作原理是:进气口处的气流通过导叶的引导,进入转子内部。
转子高速旋转,产生离心力,将气流推向叶轮部分,使气流加速,同时增加气流的压力。
气流随后经过导叶的调节,使得气流的方向和压力得以调整,最后从排气口排出。
外转子离心风机具有一些优点,首先是其高效率。
由于转子位于风机外部,转子的直径较大,叶轮的半径也相应增加,使得离心力得到更好的利用,提高了风机的压力和流量效率。
其次是体积小。
由于转子位于风机外部,减小了转子与壳体之间的间隙,使得风机的整体尺寸更小。
此外,外转子离心风机具有运行平稳、噪音低等优点。
综上所述,外转子离心风机是一种结构紧凑、高效率的离心风机。
通过其独特的壳体、转子、导叶、进气口、排气口等组成,它能够在工业、建筑等领域中起到高效、稳定的通风、送风作用。
离心式鼓风机的结构

离心式鼓风机的结构
离心式鼓风机主要由以下结构组成:
1.机壳。
离心式鼓风机的机壳由铸铁制作,或用钢板焊接而成。
机壳根据叶轮形式可做成水平剖分或蜗壳状。
2.转子组件。
离心式鼓风机的主要部件是转子,它是由叶轮、主轴、轴套、排气室、平衡盘、密封、联轴器等部件组成。
3.叶轮。
叶轮由轮盘、轮毂和叶片铆接、焊接或整体铸造而成。
其主要作用是使气体通过叶轮后提高压力和气流速度。
4.主轴。
主轴上装有风机的转动部件,其作用是传递转矩使叶轮旋转,一般离心式风机的轴伸出机壳外面。
此外,离心式多级鼓风机机壳内有回流室、隔板、扩压器等零件,气体由扩压器进入回流室,然后引入下一级叶轮,连续的把气体送入管道。
离心风机的结构

离心风机的结构离心风机是一种常见的风力设备,主要用于输送气体和增加气体的压力。
它的结构设计简单,但却非常有效。
下面将详细介绍离心风机的结构及工作原理。
1. 外壳:离心风机的外壳通常由金属或塑料制成,用于固定内部的零部件并保护风机免受外部环境的影响。
外壳的设计通常采用流线型,以减少气体在进出口处的阻力,提高风机的效率。
2. 叶轮:叶轮是离心风机中最重要的部件之一,它负责将气体加速并转移能量。
叶轮通常由金属制成,具有多个叶片,这些叶片的形状和角度经过精确设计,以确保气体能够顺利通过并获得最大的动能。
3. 驱动装置:离心风机的驱动装置通常包括电机和传动装置。
电机负责提供动力,传动装置则将电机的旋转运动传递给叶轮。
传动装置通常采用皮带、联轴器或直接连接的方式。
4. 进出口:离心风机的进出口是气体进出的通道,进口处的气体经过叶轮加速后,通过出口处排出。
进出口的设计也非常重要,它们的尺寸和形状需要根据具体的工作要求来确定,以确保风机能够正常运行。
5. 支撑结构:离心风机的支撑结构用于支撑整个设备,并将其固定在所需的位置。
支撑结构通常由金属或混凝土制成,具有足够的强度和稳定性,以确保风机在运行过程中不会发生倾斜或晃动。
离心风机的工作原理如下:当电机启动时,驱动装置将转动能量传递给叶轮,叶轮开始加速并将气体抛出。
由于叶轮的旋转运动产生了离心力,气体被迫沿着叶轮的外边缘加速运动,最终被排出风机。
这样就实现了气体的输送和增压。
总的来说,离心风机的结构简单而有效,通过合理设计和精密制造,能够实现高效的气体输送和增压。
在工业生产和生活中,离心风机被广泛应用于通风、空调、换气等领域,为人们创造了舒适的生活和工作环境。
离心风机结构形式
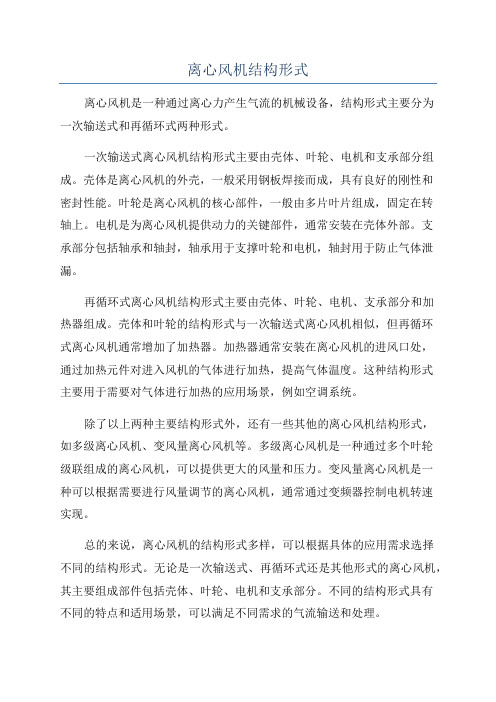
离心风机结构形式
离心风机是一种通过离心力产生气流的机械设备,结构形式主要分为
一次输送式和再循环式两种形式。
一次输送式离心风机结构形式主要由壳体、叶轮、电机和支承部分组成。
壳体是离心风机的外壳,一般采用钢板焊接而成,具有良好的刚性和
密封性能。
叶轮是离心风机的核心部件,一般由多片叶片组成,固定在转
轴上。
电机是为离心风机提供动力的关键部件,通常安装在壳体外部。
支
承部分包括轴承和轴封,轴承用于支撑叶轮和电机,轴封用于防止气体泄漏。
再循环式离心风机结构形式主要由壳体、叶轮、电机、支承部分和加
热器组成。
壳体和叶轮的结构形式与一次输送式离心风机相似,但再循环
式离心风机通常增加了加热器。
加热器通常安装在离心风机的进风口处,
通过加热元件对进入风机的气体进行加热,提高气体温度。
这种结构形式
主要用于需要对气体进行加热的应用场景,例如空调系统。
除了以上两种主要结构形式外,还有一些其他的离心风机结构形式,
如多级离心风机、变风量离心风机等。
多级离心风机是一种通过多个叶轮
级联组成的离心风机,可以提供更大的风量和压力。
变风量离心风机是一
种可以根据需要进行风量调节的离心风机,通常通过变频器控制电机转速
实现。
总的来说,离心风机的结构形式多样,可以根据具体的应用需求选择
不同的结构形式。
无论是一次输送式、再循环式还是其他形式的离心风机,其主要组成部件包括壳体、叶轮、电机和支承部分。
不同的结构形式具有
不同的特点和适用场景,可以满足不同需求的气流输送和处理。
离心风机的结构

离心风机的结构
离心风机是一种广泛应用于通风、空调和工业生产中的设备。
它的主要作用是将空气或气体通过旋转叶轮产生的离心力推动到出口处,从而形成气流。
下面我们来了解一下离心风机的结构。
1.外壳:离心风机的外壳通常由钢板制成,它的主要作用是保护内部部件,并将进口端和出口端分开。
外壳上还会有进气口和排气口,以便引入或排出气体。
2.叶轮:离心风机的核心部件是叶轮,它通常由多个弯曲叶片组成。
当电机带动叶轮旋转时,空气或气体被吸入并被推向出口。
不同类型的离心风机使用不同形状和尺寸的叶轮。
3.驱动装置:驱动装置包括电机、皮带、联轴器等零件,其作用是将电能转化为机械能,并传递给叶轮使其旋转。
4.支撑架:支撑架用于固定整个离心风机装置,并支撑其重量。
支撑架通常由钢材或铝材制成,具有较高的强度和稳定性。
5.进气道:进气道是离心风机的一部分,其作用是将空气或气体引入叶轮。
进气道通常由圆形或方形管道组成。
6.出口:离心风机的出口通常由一个管道或一个喉咙组成。
当空气或气体通过叶轮推动到出口时,它们会被推向出口并形成一股强大的气流。
总之,离心风机是由外壳、叶轮、驱动装置、支撑架、进气道和出口
等部件组成。
这些部件协同工作,将电能转化为机械能,并将空气或
气体推向出口,从而实现通风、空调和工业生产等应用。
毕业设计毕业论文离心风机的设计

2. 离心式通风机的结构及原理2.1离心风机的基本组成主要由叶轮、机壳、进口集流器、导流片、联轴器、轴、电动机等部件组成。
旋转的叶轮和蜗壳式的外壳。
旋转叶轮的功能是使空气获得能量;蜗壳的功能是收集空气,并将空气的动压有效地转化为静压。
2.2离心风机的原理叶轮旋转产生的离心力使空气获得动能, 然后经蜗壳和蜗壳出口扩散段将部分动能转化为静压。
这样,风机出口的空气就是具有一定静压的风流。
1-进气室;2-进气口;3-叶轮;4-蜗壳;5-主轴;6-出气口;7-扩散器2.3离心风机的主要结构参数如图所示,离心风机的主要结构参数如下。
①叶轮外径, 常用D表示;②叶轮宽度, 常用b表示;③叶轮出口角,一般用β表示。
叶轮按叶片出口角的不同可分为三种:前向式──叶片弯曲方向与旋转方向相同, β> 90°(90°~ 160°);后向式──叶片弯曲方向与旋转方向相反, β< 90°(20°~ 70°);径向式──叶片出口沿径向安装,β= 90°。
2.4离心风机的传动方式如图所示。
3. 离心式通风机的设计3.1 通风机设计的要求离心通风机在设计中根据给定的条件:容积流量,通风机全压,工作介质及以用其他要求,确定通风机的主要尺寸,例如,直径及直径比,转速n,进出口宽度和,进出口叶片角和,叶片数Z,以及叶片的绘型和扩压器设计,以保证通风机的性能。
对于通风机设计的要求是:(1)满足所需流量和压力的工况点应在最高效率点附近;(2)最高效率要高,效率曲线平坦;(3)压力曲线的稳定工作区间要宽;(4)结构简单,工艺性能好;(5)足够的强度,刚度,工作安全可靠;(6)噪音低;(7)调节性能好;(8)尺寸尽量小,重量经;(9)维护方便。
对于无因次数的选择应注意以下几点:(1)为保证最高的效率,应选择一个适当的值来设计。
(2)选择最大的值和低的圆周速度,以保证最低的噪音。
离心式风机的构造
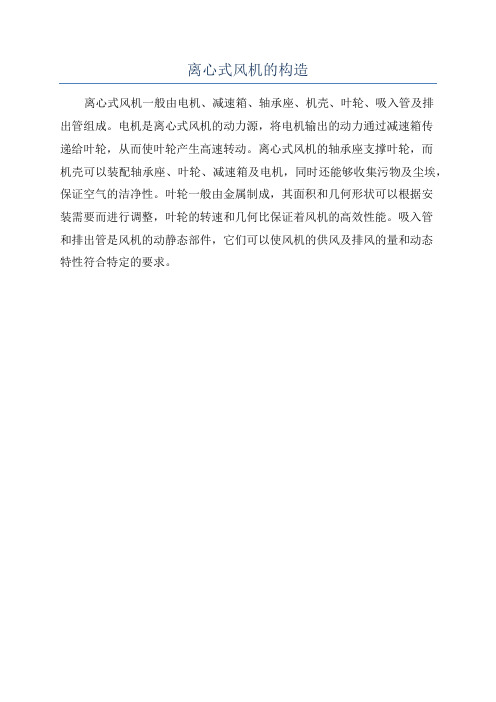
离心式风机的构造
离心式风机一般由电机、减速箱、轴承座、机壳、叶轮、吸入管及排
出管组成。
电机是离心式风机的动力源,将电机输出的动力通过减速箱传
递给叶轮,从而使叶轮产生高速转动。
离心式风机的轴承座支撑叶轮,而
机壳可以装配轴承座、叶轮、减速箱及电机,同时还能够收集污物及尘埃,保证空气的洁净性。
叶轮一般由金属制成,其面积和几何形状可以根据安
装需要而进行调整,叶轮的转速和几何比保证着风机的高效性能。
吸入管
和排出管是风机的动静态部件,它们可以使风机的供风及排风的量和动态
特性符合特定的要求。
第三章 离心泵与风机的主要部件与整体结构

平直前盘制造简单, 效率较低,而弧形前 盘气流进口后分离损 失较小,效率较高。
图3-36 前盘型式 (a)平直前盘;(b)锥形前盘;(c)弧形前盘
二、集流器 装置在叶轮前,它应使气流能均匀地充满叶轮的入口截 面,并且气流通过它时的阻力损失应该最小。
图3-37 集流器型式 (a)圆筒形;(b)圆锥形;(c)弧形; (d)锥筒形;(e)锥弧形
第三节 离心式风机的主要部件
一、叶轮
叶轮是离心风机传递能量 的主要部件,由前盘、后 盘、叶片及轮毂组成。 叶轮后弯式叶片有机翼型、 直板型及弯板型等三种; 机翼型效率最高。
图3-34 离心风机叶轮 1-前盘;2-后盘;3-叶片;4-轮毂
图3-35 后弯叶片形状 (a)机翼型;(b)直板型;(c)弯板型
由于泄漏原因叶轮两侧充有液体,液流压力不同,轴向力的 方向指向吸入口。
2、轴向力的平衡
(1)双吸式叶轮
单级泵可采用 双吸叶轮
(2)叶轮对称布置 多级泵采用对称排列的方式,叶轮 数为奇数时首级叶轮采用双吸式。
(3)平衡孔 单吸单级泵,可在叶轮后盖板上 开一圈小孔——平衡孔。 缺点:增加了泄漏,效率降低, 适用于单级泵或小型多级泵上。
第三章离心泵与风机的主要部件与整体结构第一节离心泵主要部件第二节离心泵整体结构第三节离心风机主要部件第四节离心风机整体结构第一节离心泵主要部件一叶轮1叶轮是将原动机输入的机械能传递给液体提高液体能量的核心部件
第三章 离心泵与风机的主要部件与整体结构
第一节 第二节 第三节 第四节 离心泵主要部件 离心泵整体结构 离心风机主要部件 离心风机整体结构
二、单级双吸泵
特点:S型泵,流量变大适 用于工厂、矿山、城市的 给水,亦可用作中、小型 火力发电厂循环水泵。
离心式风机的工作原理

离心式风机的工作原理
离心式风机是一种常见的风机类型,其工作原理基于离心力产生的风力,用于产生气流或增强通风效果。
以下是离心式风机的工作原理:
1. 结构组成:离心式风机通常由驱动装置(如电动机)、叶轮、进风口、出风口和外壳等组成。
2. 进风过程:当电动机启动后,风机叶轮开始旋转。
外部空气通过进风口进入风机,形成进风流。
3. 叶轮运动:进风流穿过进风口后,叶轮将其吸入,然后通过旋转快速向外甩出。
叶轮的转动速度通常较高,产生的离心力将气体向外甩出。
4. 离心力:叶轮的离心力将气体从中心位置推向外部,形成强大的气体流。
这种离心力使得气体可以克服内部摩擦,并加速流动。
5. 出风流:离心式风机通过出风口排放已加速的气体流。
出风口通常位于风机的侧壁或顶部。
6. 调节风量:可以通过控制叶轮的转速或改变叶轮的叶片角度来调节风机的风量。
转速越高,风量越大。
7. 应用领域:离心式风机广泛应用于通风系统、空调系统、工业生产过程中的气体输送和循环等领域,以提供必要的气体流
动和风力。
总体而言,离心式风机利用驱动装置带动叶轮旋转,通过大量空气流经叶轮并受到离心力的作用,产生强大的气流以满足通风、排气或气体输送的需求。
第三章离心泵与风机主要部件与整体结构
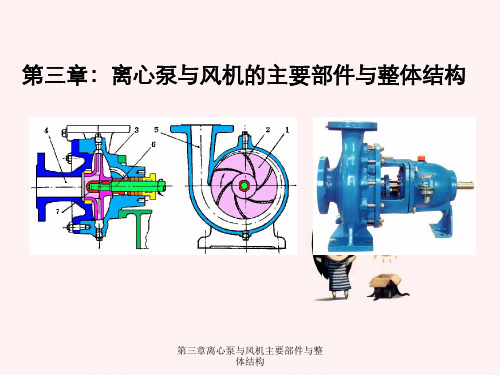
作用:将叶轮压出的高速液体汇集起来引向下一级叶 轮的入口(对末级导叶是引向压出管路),并将液体 的动能转化为压力能。(导叶与压出室的作用相同)
径向式导叶 流道式导叶
见教材 P35
偶数:正好对半布置 奇数:首级采用双吸式
第三章离心泵与风机主要部件与整体结 构
(2)平衡孔
(1)在叶轮后盖板上钻有数个小孔。 平衡压力
(2)并在与前盖板密封直径相同处装 有密封环。液体经过密封环间隙后, 压力下降,减少了作用在后盖板上的 力。
(3)在后盖板下部从泵壳处设连通管 与吸入侧相通,将叶轮背面的压力液 体引向吸入管。
3. 半螺旋形吸入室
单级双吸离心泵一般采 用半螺旋形吸入室结构。 使流体以正预旋进入叶轮, 改善流体在叶轮入口处的 流动,而且消除轴背面的 漩涡区。
优点:保证进口液流速度均匀。泵轴后无漩涡,阻力损 失较小。 缺点:有预旋,扬程有所下降。 半螺旋形吸入室大多应用在双吸式泵、多级中开式泵上
第三章离心泵与风机主要部件与整体结 构
第三章离心泵与风机主要部件与整体结 构
径向式导叶
正导叶 AB+BC
过渡区
反导叶
第三章离心泵与风机主要部件与整体结 构
流道式导叶
正、反导叶是连续的整体,形成单独的小流道,液流互不相混。 流阻比径向的小,但结构复杂。
第三章离心泵与风机主要部件与整体结 构
4.双层压出室、双压出室、倒置双涡室
优点:可以实现径向推力的平衡
2. 圆环形吸入室
在吸入室的起始段中,轴向 尺寸逐渐缩小,宽度逐渐增大, 整个面积还是缩小,使流体得 到一个加速。
离心风机内部结构
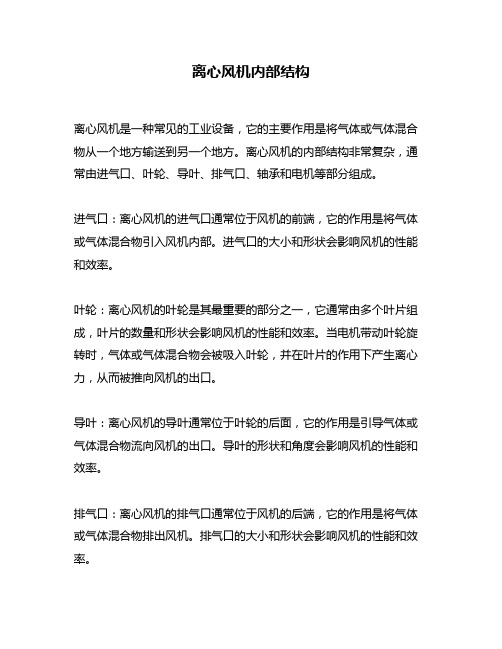
离心风机内部结构
离心风机是一种常见的工业设备,它的主要作用是将气体或气体混合物从一个地方输送到另一个地方。
离心风机的内部结构非常复杂,通常由进气口、叶轮、导叶、排气口、轴承和电机等部分组成。
进气口:离心风机的进气口通常位于风机的前端,它的作用是将气体或气体混合物引入风机内部。
进气口的大小和形状会影响风机的性能和效率。
叶轮:离心风机的叶轮是其最重要的部分之一,它通常由多个叶片组成,叶片的数量和形状会影响风机的性能和效率。
当电机带动叶轮旋转时,气体或气体混合物会被吸入叶轮,并在叶片的作用下产生离心力,从而被推向风机的出口。
导叶:离心风机的导叶通常位于叶轮的后面,它的作用是引导气体或气体混合物流向风机的出口。
导叶的形状和角度会影响风机的性能和效率。
排气口:离心风机的排气口通常位于风机的后端,它的作用是将气体或气体混合物排出风机。
排气口的大小和形状会影响风机的性能和效率。
轴承:离心风机的轴承通常位于叶轮和电机之间,它的作用是支撑叶轮并减少摩擦。
轴承的质量和性能会影响风机的寿命和效率。
电机:离心风机的电机通常位于轴承的后面,它的作用是带动叶轮旋转。
电机的功率和效率会影响风机的性能和效率。
总之,离心风机的内部结构非常复杂,各个部分之间相互作用,共同完成气体或气体混合物的输送任务。
在实际应用中,需要根据具体的要求选择合适的离心风机,并对其内部结构进行优化和调整,以达到最佳的性能和效率。
离心风机结构形式
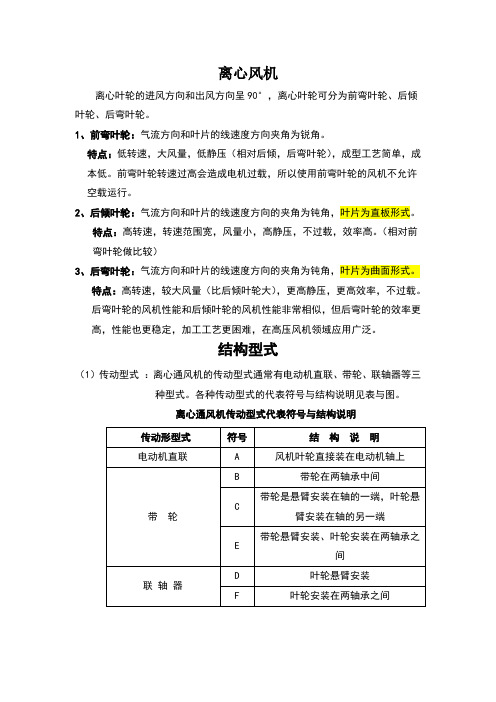
离心风机离心叶轮的进风方向和出风方向呈90°,离心叶轮可分为前弯叶轮、后倾叶轮、后弯叶轮。
1、前弯叶轮:气流方向和叶片的线速度方向夹角为锐角。
特点:低转速,大风量,低静压(相对后倾,后弯叶轮),成型工艺简单,成本低。
前弯叶轮转速过高会造成电机过载,所以使用前弯叶轮的风机不允许空载运行。
2、后倾叶轮:气流方向和叶片的线速度方向的夹角为钝角,叶片为直板形式。
特点:高转速,转速范围宽,风量小,高静压,不过载,效率高。
(相对前弯叶轮做比较)3、后弯叶轮:气流方向和叶片的线速度方向的夹角为钝角,叶片为曲面形式。
特点:高转速,较大风量(比后倾叶轮大),更高静压,更高效率,不过载。
后弯叶轮的风机性能和后倾叶轮的风机性能非常相似,但后弯叶轮的效率更高,性能也更稳定,加工工艺更困难,在高压风机领域应用广泛。
结构型式(1)传动型式:离心通风机的传动型式通常有电动机直联、带轮、联轴器等三种型式。
各种传动型式的代表符号与结构说明见表与图。
离心通风机传动型式代表符号与结构说明连接方式AMCA标准连接方式中国标准说明ARR1无ARR1安装形式:皮带传动,风机不带底座和皮带轮,电机由用户自己安装。
ARR3E型ARR3安装形式:皮带传动,轴承位于风机两侧。
例如:ICCARR4A型ARR4安装形式:直联传动,电机轴与风机叶轮直接连接。
例如:CFD/CBDARR8D型ARR8安装形式:直联传动,电机与风机轴通过连轴器传动。
ARR9C1型ARR9安装形式:皮带传动,电机位于电机支撑板侧面。
ARR10C3型ARR10安装形式:皮带传动,电机位于风机轴正下方。
例如:CUSARR12C2型ARR12安装形式:皮带传动,轴承位于叶轮同一侧,电机置于风机底座上。
例如:BCSD、BCSL直联传动优点:节省部件(皮带轮、轴、轴承、皮带等)易损部件少,可靠性高;缺点:转速固定,其转速就等于电机转速;皮带传动优点:转速可调,选择主动轮和从动轮的不同传动比,调节其转速,电机安装位置也比较灵活;缺点:易损部件多,需要及时维护;(2)离心通风机出气口安装位置按叶轮轮旋转方向,根据安装角的不同各规定8种基本位置(从原动机侧看)。
离心风机技术协议
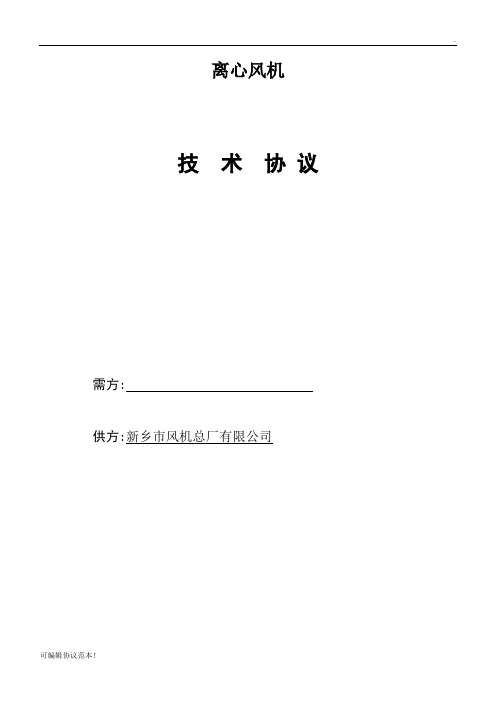
离心风机技术协议需方: 供方:新乡市风机总厂有限公司一、离心风机技术参数:3、离心式通风机G4-68 10D技术参数二、风机结构说明:风机采用单吸入单悬臂结构。
传动方式:电机+风机。
风机主要由叶轮、机壳、进风口及传动部分组成。
1、转子(叶轮、主轴):1.1、叶轮:叶轮加工工艺流程叶轮由轴盘、前盘、叶片、后盘组成。
轴盘:材质采用HT250/QT500按图纸加工,保证后盘止口外径、止口高度、轴孔直径、空深尺寸及键槽高度、深度尺寸。
前盘:1、下料:等离子气割下料1/3前盘(等离子机)。
2、拼接:锥形或弧形前盘按下料工件拼接一起满焊(二保焊)。
3、成型:用前盘压模在压力机上压型(压力机)。
4、检验:用前盘型线样板检验前盘成型弧度至合格。
叶片:1、下料:按叶片下料样板划线后剪板下料(剪板机)。
2、成型:叶片压模,压型(压力机)。
3、检验:用叶片样板检验叶片型线是否相符至合格。
后盘:1、下料:等离子气割下料(等离子机)。
2、车:车加工轴盘止口孔(车床)。
叶轮加工工艺过程1、配钻:与叶轮轴盘铆钉孔配钻后盘孔(钻床)。
2、铆接:轴盘与后盘铆接(铆钉机)。
3、对焊叶片:后盘在叶轮对焊胎上点焊叶片(手工焊)。
4、对焊前盘:在压力机上把前盘点焊在叶片上保证前盘与轴盘同心(压力机、同心控制仪)。
5、焊接:把所有焊缝按要求焊接(二保焊)。
6、整形:消除焊接变形,保证叶轮前、后盘跳动值,后盘平面度(叶轮整形胎)。
7、车加工:车加工叶轮8、平衡:在平衡机上做动平衡(动平衡机)。
9、着漆:先着两道底漆,再着一道面漆。
2机壳加工工艺机壳包括前、后侧板、蜗板、后盖板、出风口角钢。
前、后侧板:2.1、编程:按产品下料尺寸进行排料编程。
2.2、下料:按线等离子下料(等离子机)。
蜗板:1、下料:按机壳图纸尺寸在剪板机上下料,分蜗舌部分和蜗板部分。
2、蜗板成型:在蜗舌压模机上成型蜗舌。
3、拼接:将蜗舌部分与蜗板部分焊在一起。
4、卷弧:在卷园机上把蜗板卷出渐开线。
通风机的结构及原理

通风机的结构及原理主要由叶轮、机壳、进口集流器、导流片、电动机等部件组成。
1.离心式通风机离心式通风机具有很大的风量范围和风压范围, 在通风工程中被广泛应用。
如图7-1-2、7-1-3所示,空气从轴向流入, 径向流出。
(1)离心风机的基本组成旋转的叶轮和蜗壳式的外壳。
旋转叶轮的功能是使空气获得能量;蜗壳的功能是收集空气,并将空气的动压有效地转化为静压。
图7-1-2 离心风机结构图1-进气室;2-进气口;3-叶轮;4-蜗壳;5-主轴;6-出气口;7-扩散器图7-1-3 离心风机结构简图(2)离心风机的原理叶轮旋转产生的离心力使空气获得动能, 然后经蜗壳和蜗壳出口扩散段将部分动能转化为静压。
这样,风机出口的空气就是具有一定静压的风流。
离心风机的工作原理(3)离心风机的主要结构参数如图7-1-4所示,离心风机的主要结构参数如下。
①叶轮外径, 常用D表示;②叶轮宽度, 常用b表示;③叶轮出口角,一般用β表示。
叶轮按叶片出口角的不同可分为三种(如图7-1-5):前向式──叶片弯曲方向与旋转方向相同, β> 90°(90°~160°);后向式──叶片弯曲方向与旋转方向相反, β< 90°(20°~70°);径向式──叶片出口沿径向安装,β= 90°。
图7-1-4 离心风机叶轮图7-1-5 离心风机叶片出口角(4)离心风机的传动方式如图7-1-6所示。
图7-1-6 离心风机的传动方式2.轴流式通风机如图图7-1-7所示,空气从轴向流入, 轴向流出。
在地下工程施工通风中得到广泛应用。
(1)轴流风机的基本组成集风器, 叶轮, 导叶和扩散筒。
集风器的作用是减少入口风流的阻力损失;叶轮的作用是, 叶轮旋转时叶片冲击空气, 使空气获得一定的速度和风压;导叶的作用扭转从叶轮流出的旋转气流, 使一部分偏转气流动能变为静压能, 同时可减少因气流旋转而引起的阻力损失;扩散筒的作用是将一部分轴向气流动能转变为静压能。
- 1、下载文档前请自行甄别文档内容的完整性,平台不提供额外的编辑、内容补充、找答案等附加服务。
- 2、"仅部分预览"的文档,不可在线预览部分如存在完整性等问题,可反馈申请退款(可完整预览的文档不适用该条件!)。
- 3、如文档侵犯您的权益,请联系客服反馈,我们会尽快为您处理(人工客服工作时间:9:00-18:30)。
离心风机
离心叶轮的进风方向与出风方向呈90°,离心叶轮可分为前弯叶轮、后倾叶轮、后弯叶轮。
1、前弯叶轮:气流方向与叶片的线速度方向夹角为锐角。
特点:低转速,大风量,低静压(相对后倾,后弯叶轮),成型工艺简单,成本低。
前弯叶轮转速过高会造成电机过载,所以使用前弯叶轮的风机不允许空载运行。
2、后倾叶轮:气流方向与叶片的线速度方向的夹角为钝角,叶片为直板形式。
特点:高转速,转速范围宽,风量小,高静压,不过载,效率高。
(相对前弯叶轮做比较)
3、后弯叶轮:气流方向与叶片的线速度方向的夹角为钝角,叶片为曲面形式。
特点:高转速,较大风量(比后倾叶轮大),更高静压,更高效率,不过载。
后弯叶轮的风机性能与后倾叶轮的风机性能非常相似,但后弯叶轮的效率更高,性能也更稳定,加工工艺更困难,在高压风机领域应用广泛。
结构型式
(1)传动型式 :离心通风机的传动型式通常有电动机直联、带轮、联轴器等三种
型式。
各种传动型式的代表符号与结构说明见表与图。
离心通风机传动型式代表符号与结构说明
连接方式AMCA标准连接方式
中国标准
说明
ARR1 无ARR1安装形式:皮带传动,风机不带底座与皮带轮,电机由用户自己安装。
ARR3 E型ARR3安装形式:皮带传动,轴承位于风机两侧。
例
如:ICC
ARR4 A型ARR4安装形式:直联传动,电机轴与风机叶轮直接
连接。
例如:CFD/CBD
ARR8 D型ARR8安装形式:直联传动,电机与风机轴通过连轴
器传动。
ARR9 C1型ARR9安装形式:皮带传动,电机位于电机支撑板侧
面。
ARR10 C3型ARR10安装形式:皮带传动,电机位于风机轴正下
方。
例如:CUS
ARR12 C2型ARR12安装形式:皮带传动,轴承位于叶轮同一侧,电机置于风机底座上。
例如:BCSD、BCSL
直联传动优点:节省部件(皮带轮、轴、轴承、皮带等)易损部件少,可靠性高; 缺点:转速固定,其转速就等于电机转速;
皮带传动优点:转速可调,选择主动轮与从动轮的不同传动比,调节其转速,电机安装位置也比较灵活;
缺点:易损部件多,需要及时维护;
(2)离心通风机出气口安装位置按叶轮轮旋转方向,根据安装角的不同各规定8种基本位置(从原动机侧瞧)。