生产管理之8大浪费 ppt课件
生产中八大浪费PPT课件
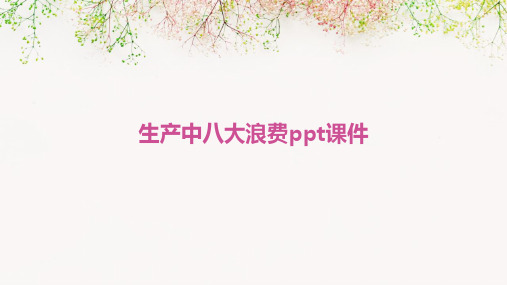
对员工反馈的信息进行及时处理和 跟进,确保问题得到解决和落实。
案例分析法
选择典型案例
经验借鉴
选择生产过程中具有代表性和普遍性 的浪费案例进行分析。
从案例中提炼出可供借鉴的经验和教 训,为减少类似浪费提供参考。
案例剖析
对选定的案例进行深入剖析,了解浪 费的具体情况和原因。
04
减少和消除策略
管理浪费
定义
管理浪费是指企业管理中不必要 的环节、流程或制度所造成的资 源、时间和成本的浪费。
危害
增加管理成本、降低管理效率; 影响企业决策效果和响应速度; 可能导致企业失去市场机会和竞 争优势。
解决方法
优化管理流程和组织结构,减少 不必要的管理环节和制度;实施 信息化和数字化管理手段,提高 管理效率和决策效果;加强员工 培训和管理素质提升,提高员工 对管理要求的认知和执行能力。
设备利用率提高
合理安排生产计划,充分利用设备产能,避免设备闲置和浪费。加强Βιβλιοθήκη 工培训和技能提升员工技能培训
01
针对员工岗位需求,制定个性化的培训计划,提高员工技能水
平和操作效率。
多能工培养
02
鼓励员工学习多种技能,培养多能工,提高员工适应性和灵活
性。
员工激励机制
03
建立合理的激励机制,激发员工积极性和创造力,促进员工持
生产中常见浪费现象
过度生产
生产超出实际需求或计划的产品,导致库存积压和 资金占用。
等待时间
设备或员工在等待下一道工序或资源时产生的空闲 时间。
运输浪费
不必要的物料搬运和运输,以及由此产生的时间和 资源消耗。
生产中常见浪费现象
01
02
生产现场管理的8大浪费

想要打败敌人必先了解敌人,对于车间现场管理来讲,浪费恐怕是最大的敌人。
因为浪费,企业付出了高额的生产成本还毫不知情;因为浪费,本来2个人能完成的工作偏偏需要5个人;因为浪费,企业付出大量的人力成本。
凡是不能创造价值的活动都称之为浪费,想要消除车间现场管理中的浪费,一定要认识这八项浪费现象。
所谓不良、返修的浪费,指的是由于制衣厂内出现不良品,需要进行处置的时间、人力、物力上的浪费,以及由此造成的相关损失。
这类浪费具体包括:材料的损失、不良品变成废品;设备、人员和工时的损失;额外的返修、QC、追加检查的损失;有时需要降价处理服装,或者由于耽误出货而导致工厂信誉的下降。
加工的浪费也叫过分加工的浪费,主要包含两层含义:第一是多余的缝制和过分精确的加工,例如实际缝制针脚过多造成资源浪费;第二是需要多余的作业时间和辅助设备,还要增加生产用电等能源的浪费,另外还增加了管理的工时。
动作的浪费现象在很多服装企业的生产线中都存在,常见的动作浪费主要有以下12种:两手空闲、单手空闲、作业动作突然停止、作业动作过大、左右手交换、步行过多、转身的角度太大,移动中变换“状态”、不明技巧、伸背动作、弯腰动作以及重复动作和不必要的动作等等,这些动作的浪费造成了时间和体力上的不必要消耗。
搬运是一种不产生附加价值的动作,而不产生价值的工作都属于浪费。
搬运的浪费具体表现为放置、堆积、移动、整列等动作浪费,由此而带来物品移动所需空间的浪费、时间的浪费和人力工具的占用等不良后果。
国内目前有不少服装企业管理者认为搬运是必要的,不是浪费。
因此,很多人对搬运浪费视而不见,更谈不上去消灭它。
也有一些服装企业利用传送带或机器搬运的方式来减少人工搬运,这种做法是花大钱来减少工人体力的消耗,实际上并没有排除搬运本身的浪费。
按照过去的管理理念,人们认为库存虽然是不好的东西,但却是必要的。
其实库存是没有必要的,甚至库存是万恶之源。
例如,有些服装企业生产线出现故障,造成停机、停线,但由于有库存而不至于断货,这样就将故障造成停机、停线的问题掩盖住了,耽误了故障的排除。
企业八大浪费培训ppt课件ppt
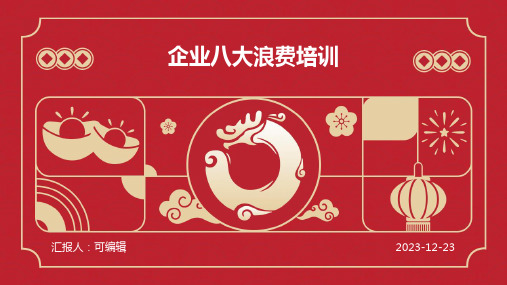
应对措施与解决方案
3. 提高员工技能水平
加强员工技能培训和技能认证,提高员工的技能水平 和操作熟练度,确保员工能够按照标准操作规程进行 生产,减少因操作不当导致的加工浪费。
表现
设备空转、操作员等待、生产流程停 滞等。
产生原因与影响
产生原因
生产计划安排不合理、设备故障率高、物料供应不及时等。
影响
降低生产效率、增加生产成本、影响产品质量和客户满意度等。
应对措施与解决方案
应对措施
优化生产计划、加强设备维护保养、提高物料供应的及时性等。
解决方案
采用精益生产管理、引入自动化和智能化设备、建立快速响应机制等。
引入自动化和智能化设备
通过自动化和智能化设备来替代人工操作, 提高生产效率。
08 管理浪费
CHAPTER
定义与表现
定义
管理浪费是指企业在管理过程中出现的资源浪费现象,如决策失误、组织结构 不合理、流程繁琐等。
表现
管理浪费通常表现为工作效率低下、资源分配不均、信息传递不畅、决策缓慢 等问题。
产生原因与影响
原因
管理浪费的产生原因主要包括管理层决策能力不足、组织结构复杂、缺乏有效的 管理制度和流程等。
影响
管理浪费会导致企业资源浪费、效率低下、竞争力下降,甚至可能导致企业破产 倒闭。
应对措施与解决方案
应对措施
提高管理层决策能力、优化组织结构 、简化流程、建立有效的管理制度和 流程等。
解决方案
引入先进的管理理念和方法,加强内 部培训和人才培养,建立科学的管理 体系和流程,提高企业整体的管理水 平。
八大浪费识别ppt课件
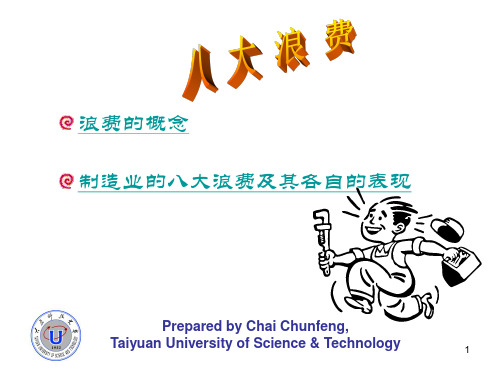
制造过多的Muda:后果
4、 它会产生搬运、堆积的浪费,并使得 先入先出作业变得困难。 5、 需要增加踏板、包装箱(周转箱)等 容器 6、 库存量变大,管理工时增加 7、 利息负担增加 8、 等待的浪费
30
制造过多的Muda:对策
• 要考虑到下一个流程或下一条生产线的正确生 产速度;而不要只尽所能,在本流程生产过多 的产品。
Prepared by Chai Chunfeng,
Taiyuan University of Science & Technology
4
隐性浪费/显性浪费
• 显性浪费 – 定义为可见的浪费 – 这些浪费很容易签 别
如:
– 在流程中引起不良 品的错误
– 等待时间浪費
• 隐性浪费 • 定义为看不见的浪費 • 这些浪費不易被签别 • 这些工作看起来非常有
3. 作业动作停止的浪费 9. 不了解作业技巧的浪
4. 作业动作太大的浪费
费
5. 拿的动作交替的浪费 10. 伸背动作的浪费
6. 步行的浪费
11. 弯腰动作的浪费
7. 转身角度太大的浪费 12. 重复动作的浪费
15
• 任何人体的动作,若 是没有直接产生附加 价值,就是没有生产 力。例如,人在走路 时,他并没有增加价 值。特别是,如提起 或持着一个重物,需 用到作业员身体一部 分的特别体力的动作, 应予以避免
对策:
•库存意识的改革 •U型设备配置 •均衡化生产 •生产流程调整顺畅 •看板管理的贯彻 •快速换线换模 •生产计划安排考虑库存 消化
注意:
•库存是万恶之源 •管理点数削减降低安全库存
25
•消除生产风险降低安全库存
欧美VS日本
八大浪费及改善技法(共27张PPT)
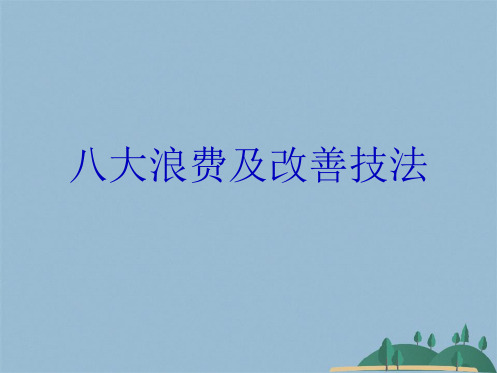
待机 运输
加工
• 通过作业观察,修改工序安排方法,重新安排作业
• 实现工序同期化,使各个工序直接连接上 (流水生产)
• 区分人工和设备作业,用机械来替代人工作业
(加工时间 加工工时)
• 必须得在实物挂上看板
库存
• 维持适当的看板数量
• 不把同一个产品放在一个场所
工作
• 修改设备布置及操作法,改善标准作业
八大浪费及改善技法
在我们周围的工作区域是否存在这些现象
堆积库存
过量走动
设备故障
过多运输
组织复杂!汇报繁琐!
会议!会议!会议! 2
无附加价值的工作
有附加价值的工作
何谓浪费:
不产生任何附加价值的
动作、方法、行为和计划
顾客不想付钱的所有行为 不能创造出附加价值的所有现 象和其结果 除净作业以外的所有行为都 是浪费
•人员过剩 动作、方法、行为和计划
加强教育培训与动作训练
Байду номын сангаас
定8. 期的•设设备备、模稼夹具动保养过剩
•生产速度快并不代表效率高
•生产浪费大 按物品的移动,详细观察现场。
设备配置不当或设备能力差
•设备余力并非一定是埋没成本
•业务订单预测有误
•生产能力过剩时,应尽量先考虑减
•生产计划与统计错误
少作业人员,但并非辞退人员,而
- 将现场和现物分别当作管理单位和管理对象,并直接观察现实情况,获取信息,从而做出判断
对作业进行反问 - 站在作业当中有浪费因素的观点,详细揭示作业工序
追究功能的必要性 - 进行调查追究其功能是否必要
浪费无处不在 - 假设除本质性功能外,到处都有浪费,揭示浪费因素
生产管理之8大浪费

■未注意部属的眼力与健康,造成不良品
■缺乏纪律,纵容粗心或不当的工作
■容许部属用不适当的材料(太好或太 差)
12
■未能追踪不良工作起何人,以致不能纠正 ■不能适才适用,特别是新人
■领料太多,多余料未退料
■领错材料,用错材料
■未能检查水、气、油等管路裂开破损, 导致遗漏
■未检查材料是否排列整齐,正确放置
生产管理中的8种浪费
1
1、时间的浪费
2
■缺乏适当的计划,使人员在换规格时产生
等待或者停工 ■班长未能彻底了解接受之命令与指示
■缺乏对全天工作内容的认识
■对班长的命令或指示不清楚 ■未能确实督导工具、材料、模具等应放
置于一定场所
■不应加班的工作,造成加班 3
■未检视每一工作是否供给合适的工具和资 源
■未研究部属个人的不同,以发挥他最大 的潜力
25
■评价一个人只重资格、种族、宗教、关 系、地域
■明知部属的的心理或者生理不适当,却 未加以调动
■生病的部属仍让他工作
■当可能且适当的时间,未能给予升迁
■未考虑影响薪资与工作条件的问题
■未训练一个后补者
26
4、欠缺对员工日常管理之数据
27
5、欠缺人员效率管理之数据
■未促使其他部属对新人表示关心、帮
助、友善的态度
23
■未尽可能的接近新人 ■没有告知新人,工厂生活情况与规划,
如安全,发薪日期,厕所位置,饮用 水,浴室等 ■未安排完整的训练计划
24
3、未使部属尽其所能
■未指导部属如何做好工作 ■未尽可能的说明工作,使其发生兴趣 ■未对部属的进步与个人生活表示关心 ■没有容纳部属错误的雅量 ■纵容部属派系存在或抱团
八大浪费培训PPT课件
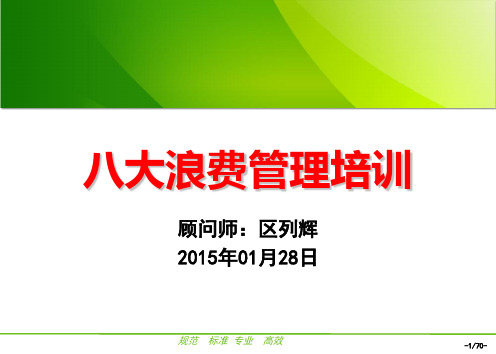
降低成
-6/70-
成本节减思想:降低成本
需求 < 供给
通过降低成本来降低销售价格
销售价格
利润 成本
规范 标准 专业 高效
-7/70-
竞争力提升 品质提升 制造成本降低 企业形象提升
改善 消除浪费 标准化
设 改善等
心、
动作改善、作业流程改善、物流改善、 备模夹治具改善、品质改善、管理
八大浪费、三无工程(无责任、无关
-29/70-
3.搬运的浪费
整个冲压过程包括取产品、冲压、 放置产品,其中取产品与摆放产 品占了50%的作业时间,并且这 些动作并不产生价值。
冲压完的产品要先放到周转车 上,再搬运到点焊工位点焊, 这些搬运过程都是浪费,为什 么不把冲压与焊接设备放在一 起呢?
规范 标准 专业 高效
-30/70-
3.搬运的浪费
规范 标准 专业 高效
-35/70-
八大浪费
1.制造过多的浪费 2.等待的浪费 3.搬运的浪费 4.加工的浪费 5.库存的浪费 6.动作的浪费 7.不良的浪费 8.管理的浪费
规范 标准 专业 高效
-36/70-
SUCCESS
THANK YOU
2019/8/1
规范 标准 专业 高效
-37/70-
5.库存的浪费
制
移动
40%
造
所谓的附加值指的是通过加工或组装提 高产品的价值,其余的都是非附加值,就 浪费。
活
附加价值动作
15%
TOYOTA汽车公司
动
非效率的 ‘工作’ 40%
11 /72
定义 95%以上是浪费
规范 标准 专业 高效
-11/70-
八大浪费
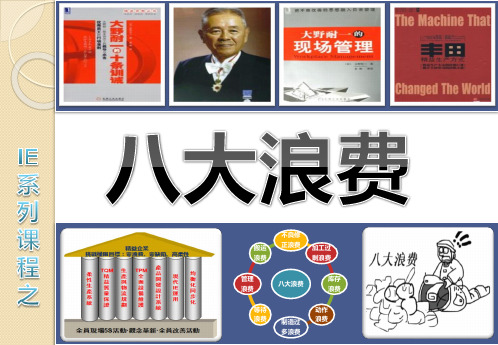
八大浪费
1
1 认识浪费
2 八大浪费详解
3 如何消除浪费
2
精益生产核心思想: 持续不断使浪费最小化、流动最大化的意识
精
适当的时间生 产必要数量的 市场急需产品
益 精 益 生 产
所有经营活动
都要有效有益,
•制订Check list发现并消 除;
设计不合理(Design):
•合理设计; •变成设计要素;
•设计验证与稽核;
•符合人体工效设计
32
7
动作浪费
1.员工需转身去取物料,包材,有 转身动作的浪费 2.长期作业员工易疲劳,不符合人 因工程
1.斜架供料,消除转身动作,降低疲劳 2.更符合人因工程,目视管理效果更好
(人員工作量不飽滿,設備稼動率低) 3.不均衡: 有時超負荷有時又不不飽和的狀態(差異狀態)。
4
浪費
不均衡
实质作业
・部件组装 ・喷涂 ・切削 ・冲压 ・焊接
作业
浪费
・等待 ・没有意义的搬运(临时放置) ・换手拿工具、部件 ・制造积压 ・部件的堆积 ・不合格品的修复
不产生附加价值的作业
・取部件、工具的行走 ・部件的开箱作业 ・部件的重新更换 ・按键按钮的操作 ・搬运作业
31
7
动作浪费
产生: 操作不经济(Handling): • 动作不精简;动作多余 设计不合理(Design): • 可同时完成但未同时; • 不必要但被增加; • 可同规格但不同; • 未考虑调整/转换/取放; • 物料需要翻找 改善方向: 操作不经济(Handling):
八大浪费

到底为什么要有库存量,最大的理由是“ 到底为什么要有库存量,最大的理由是“怕出问 ——出现故障怎么办 会不会因部分设备出问题, 出现故障怎么办? 题”——出现故障怎么办?会不会因部分设备出问题,而 影响整条生产线或工厂的生产呢? 影响整条生产线或工厂的生产呢?于是乎为了不使影响扩 库存便成了必要,众多的问题也被隐藏起来, 大,库存便成了必要,众多的问题也被隐藏起来,所有进 赚钱(发现问题、解决问题就是赚钱) 步、赚钱(发现问题、解决问题就是赚钱)的步调自然变 慢了。无怪乎精益生产方式称库存为万恶之源, 慢了。无怪乎精益生产方式称库存为万恶之源,绝对不允 许它存在,如果现在已经有了库存,也要行进一切办法, 许它存在,如果现在已经有了库存,也要行进一切办法, 将之降低,力争零库存。( 。(注 零库存的“ 将之降低,力争零库存。(注:零库存的“零”并非指数 学意义上的“完全没有”的意思,而是指把库存“ 学意义上的“完全没有”的意思,而是指把库存“尽量减 到最少的必要程度” 到最少的必要程度”。)
八大浪费之七:制造过多( 八大浪费之七:制造过多(早)的浪费
上面提到库存是万恶之源,而制造过多或提早完成, 上面提到库存是万恶之源,而制造过多或提早完成,则被视为最 大的浪费。 大的浪费。 精益生产方式所强调的是“适时生产” 也就是在必要的时候, 精益生产方式所强调的是“适时生产”,也就是在必要的时候, 做出必要的数量的必要的东西。此外都属于浪费。 做出必要的数量的必要的东西。此外都属于浪费。而所谓必要的东西 和必要的时候,就是指顾客已决定要买的数量与时间。 和必要的时候,就是指顾客已决定要买的数量与时间。假设客户只要 100个 而每个1 如果生产了150 150个 这售价却不会是150 150元 100个,而每个1元,如果生产了150个,这售价却不会是150元,因为 多余的50个并没有卖出去,仅是变成库存,因此利润也就无从产生, 50个并没有卖出去 多余的50个并没有卖出去,仅是变成库存,因此利润也就无从产生, 换句话说,多做了是浪费。 换句话说,多做了是浪费。 而制造过早同样也是浪费, 而制造过早同样也是浪费,但为什么有很多工厂会一而在地过多 与过早制造呢?最大的原因在于他们不明白这是一种浪费, 与过早制造呢?最大的原因在于他们不明白这是一种浪费,反而以为 多做能提高效率,提早做好能减少产能损失(不做白不做, 多做能提高效率,提早做好能减少产能损失(不做白不做,机器还不 是一样停着?),显然这是一种极大的误解。 ?),显然这是一种极大的误解 是一样停着?),显然这是一种极大的误解。
八大浪费培训课件ppt

4) 动作太大
10) 伸背动作
5) 左右手交换 11) 弯腰动作
6) 步行多
12) 重复/不必要的动作
一般来说作业者
有一半的时间是 “无效的” !
任何不产生价值的人员和设备的动作
15/32
精益生产专家
在日常生活中,随处都可以看到浪费 粮食的 现象。 也许你 并未意 识到自 己在浪 费,也 许你认 为浪费 这一点 点算不 了什么
在日常生活中,随处都可以看到浪费 粮食的 现象。 也许你 并未意 识到自 己在浪 费,也 许你认 为浪费 这一点 点算不 了什么
一、浪费定义
What
is
the
wastes?
什么是浪费: ◇在制造活动中,不增加价值的所有行为,是浪费; ◇尽管是增加价值的活动,所用的资源超过了
“绝对最少”的界限,也是浪费。
产生搬运、堆积的浪费,并使得先入先出的物流管 理变得困难。增加周转包装的需要,并造成质量问题。 ◆ 材料、人工、库存变大,周转资金增加,管理成本增加。
9/22 8/32
在日常生活中,随处都可以看到浪费 粮食的 现象。 也许你 并未意 识到自 己在浪 费,也 许你认 为浪费 这一点 点算不 了什么
2)库存的浪费(在制品WIP)
7/22 6/32
1)
在日常生活中,随处都可以看到浪费 粮食的 现象。 也许你 并未意 识到自 己在浪 费,也 许你认 为浪费 这一点 点算不 了什么
制造过多(早)的浪费
多做能提高效率,提早做好能减少 产能损失是一个很大的误解。
•生产多于下游客户所需 Making More Than Needed •生产快于下游客户所求 Making Faster Than Needed
8种浪费PPT课件
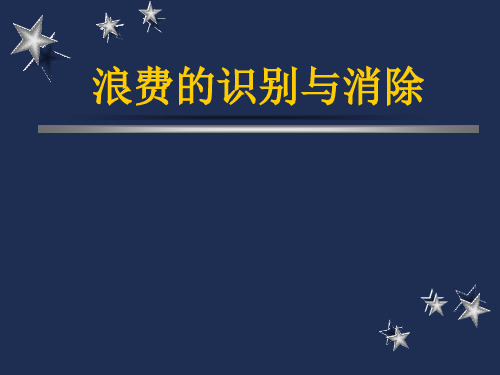
课程安排
– 浪费的3个原因 – 配套战略
• 人员支持性实践 • 降低变差 • 过程/员工控制 – 现场练习 – 过程检查
浪费的识别和消除
哲学
浪费的识别和消除是精益生产的 的核心
成功的实施要求所有的员工都受 到识别和消除他们工作中浪费的 培训
进先出” – Massive Rework Campaigns When
Problems Surface 出现问题时的大量返工作业 –Long Lead Time for Engineering Changes
工程更改导入期长 –Off Line Storage Area 线外储存空间
Waste of Inventory 存货造成的浪费
存货的浪费
定义:
Any Supply in Excess of Customer RequirementsNecessary to Produce Goods or Services Just in Time 任何超出客户要求的供应品,客户要求是指准时生产及提供服务所需。
存货的浪费
特点:
–Stagnated Material Flow 停滞的物料流 –FISH instead of FIFO“先进后出” 取代“先
纠正的浪费
定义: Repair of a Product or Service to Fulfill
Customer Requirements 维修产品或补偿服务以满足客户的要求
纠正的浪费
特点: • 维修和返工的空间 • 增加的检验 • 复杂的生产流程 • 有疑问的质量 • 影响装运/交付 • 客/供关系差 • 由于返工,报废,额外运费造成低效益 • 组织是被动反应(救火,赶工而不是预防导向)
班组成本控制之八大浪费
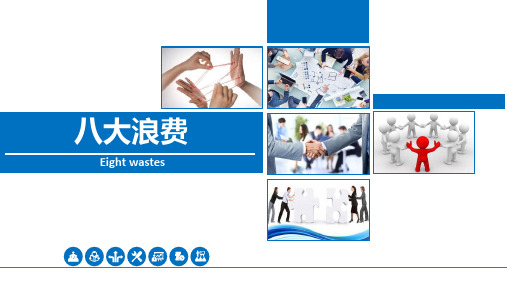
库存之“三不” 不大批量采购 不大批量生产 不大批量搬运
库存的浪费
库存浪费产生的原因: 集群式,大批量生产 供应商不稳定 呆滞物品未及时处理 视库存为当然,生产过剩 无计划/提早生产
对策: 一个流生产方式的设计 快速换模换线实施 供应商管控机制
异常物品处理流程标准制定 库存意识的改革
管理看板运用,产线管理导入
提早生产或生产了过多的、超过客户或下游工序所需要的量
这种浪费被视为 脱离了准时化生产(JIT)的原则,比需要的时候提前生产或生产数量超过了生产计划最必大要的的浪量费而!产生的库存。
由于过量生产掩盖了等待、动作、加工、搬运等浪费,又引起搬运工具、存放托盘增加等2次性浪费。
造成的浪费 ➢工序间积压在制品,交货期变长,过度占用空间 ➢工资提前支付 ➢产品积压造成不良发生 ➢提前用掉了费用(材料费、人工费)而且还增 加了产品的保管费用
实现的方法或手段
行程距离缩短
改善效果或下一步
间距缩短至20mm,花费时间 变为2s,降低3s
动作的浪费
改善前
改善后
现状问题点描述
实现的方法或手段
冲床行程过大,模具冲压时间花费2s
行程距离缩短
改善效果或下一步
冲压行程缩短,花费时间变为 1.5s,降低0.5s
动作的浪费
改善前
换模与生产 时间长
工具不合理 仓库功能区块化
对策:
整流化按工序流程配置设备 不能连接的工序尽可能的靠近 按客户需求设计产能,少人化
一个流生产方式
库存管理三原则(库位、数量、 FIFO)的贯彻,物料车设计 仓库设置在生产线附近 (店铺规划)
搬运浪费
在实际作业中减少搬运浪费的对策
1、通过改善物品的放置位置来缩短搬运距离;(就近放置) 2、通过改善作业位置来消除搬运作业; 3、缩短工位(设备・工程)之间的距离来减少搬运浪费; 3、通过辅助治具来替代人员的搬运作业;
八大浪费培训教材课件
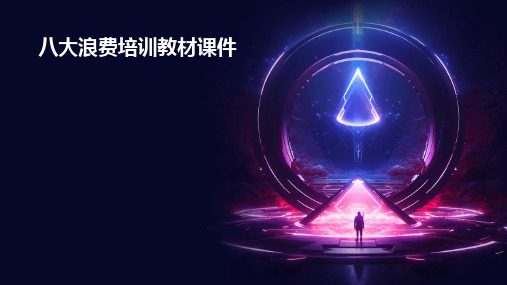
根据企业实际情况制定判定标准 ,明确哪些行为或现象属于八大 浪费,哪些不属于。判定标准应 具体、可操作,并具有约束力。
八大浪费的危害与影响
危害
八大浪费会导致企业资源浪费、效率 低下、成本增加、市场竞争力下降等 危害。
影响
八大浪费会影响企业的可持续发展, 降低员工的工作积极性和生产效率, 增加企业的经营风险。
企业缺乏明确的管理制度和流程,导致员工在工 作中无法遵循统一的标准和规范,造成管理上的 浪费。
决策失误
管理者在决策过程中缺乏充分的市场调研和数据 分析,导致决策失误,造成资源浪费和管理效率 低下。
人员素质不足
员工和管理者缺乏必要的专业知识和技能,无法 有效地完成工作任务,导致管理成本的增加和管 理效率的降低。
生产管理
生产计划安排不合理,导致半 成品或成品库存增加。
销售预测
对市场需求预测不准确,导致 库存积压或缺货。
表现形式
原材料库存
原材料、零部件等库存过多, 占用企业资金和仓储空间。
在制品库存
生产过程中的半成品、待加工 品等库存过多。
成品库存
已完成生产但未销售的成品库 存过多。
呆滞物料
长期未使用或无法再利用的物 料,形成无效库存。
无效搬运
搬运过程中存在无效操作,如手动 翻转、重新排列等。
改善方法
优化生产布局
合理规划生产线,使物料流动更加顺 畅。
减少过度生产
根据实际需求调整生产计划,减少库 存和搬运量。
采用合适的搬运方式
根据物料特性和数量选择合适的搬运 设备和技术,提高搬运效率。
引入自动化和智能化技术
通过引入自动化和智能化技术,减少 人工搬运和重复劳动,提高生产效率 。
精益生产---八大浪费共66页PPT资料
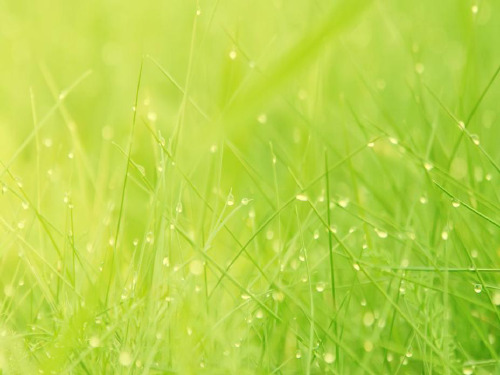
制造过多的浪费---对策
保证生产计划的准确性;
企划部门要对生产计划的排配、进度控制负 责
保证制程内品质稳定,实现了生产稳定高品 质,生产的流线化才有可能实现,才有可能
生产平准化
平衡各制程的产能
尽量减少制程及产品的迂回、曲折、往复和 停滞,以尽力减少制程内在制品
在产能规划时,在设备采购时,
26
库存的浪费---对策
•1.转变观念,认识到库存是企业的负担和罪 恶。 •2.系统改善,产线产能平衡改善,一个流生 产,看板管理的贯彻,快速换线,生产计划 安排考虑库存消化;
降低库存目标KPI订定;导入JIT;得库存管 理中的“三不”---不大批量生产、搬运、采购;
注意:
•库存是万恶之源 •管理点数削减降低安全库存 27 •消除生产风险降低安全库存
库存的浪费---表现
3、意识方面的损失 a.隐藏产能不平衡与过剩损失 b.隐藏机器故障损失 c.掩盖问题,使管理者感受不到问题的严重 性而失去改善的机会
24
库存的浪费---表现
25
库存的浪费---原因
•视库存为当然 •设备配置不当或设备能力差 •大批量生产,重视稼动 •物流混乱,呆滞物品未及时处理 •提早生产 •无计划生产 •客户需求信息未了解清楚
21
库存的现实意义
1、量产的必然产物
对市场需要品种少或者是行业价值链上游企业,批 量确实会带来低成本,但同时会带来库存。
2、保证整产零销的局部经济性
当设备快速换线困难(如重化工行业)时,选择整 产零销,会产生一定库存
3、市场剧烈增加时的缓冲
市场突然增加时如果有一定库存,会缓解企业生产 能力快速爬坡的压力,这是部分企业考虑安排库存的 原因。
八大浪费
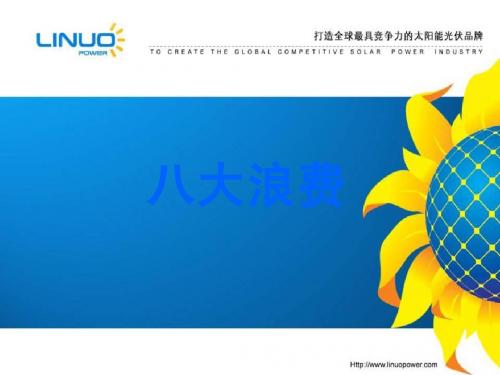
可用工时:22h
可用工时:22h
八大浪费
浪费的定义
何谓浪费:
不产生任何附加价值的动作、方法、行为和计划。
• • • • • • 盲目消耗、挥霍 没有发挥优势 未开发的区域 垃圾 无价值的剩余物 逐渐变弱
用不同的评判标准去判断一 个动作、行为、方法或计划时, 所得到的浪费程度都会不同。
八大浪费
浪费的识别和消除
四.动作浪费
动作浪费
(三) 浪费的产生:
操作不经济﹕动作不精简﹔动作多余 设计不合理﹕可同时完成但未同时﹔
不必要但被增加﹔
可同规格但不同﹔ 未考虑调整/转换/取放 物料需要翻找﹔
四.动作浪费
动作浪费
(四) 浪费的消除:
操作不经济﹕按经济原则设计并标准化﹔制订查 检表发现并消除﹔ 设计不合理﹕合理设计﹔变成设计要素﹔设计验 証与稽核﹔符合人体工效设计﹔
八大浪费
引子
产品包装过程
增值活动
直接为顾客创造价值的活动
设备加工过程
组 织 经 营 活 动
设备维护
必要非增值
多数发生于支援部门
计划变更
来料/制品/成品的检验
物料的浪费
不必要非增值
完全属于浪费
过多的搬运 冗长的会议
八大浪费
引子
不必要但非 增值活动 35%
增值活动 5%
必要但非增 值活动60%
顾客只愿意冲着那5%的增值掏腰包
精益生产的理念最早起源于日本丰田汽车公司的TPS
(Toyota Production System)。TPS的核心是追求消灭一切 “浪费”。 实现精益生产管理,最基本的一条就是消灭浪费。
浪费的识别和消除
八大浪费
- 1、下载文档前请自行甄别文档内容的完整性,平台不提供额外的编辑、内容补充、找答案等附加服务。
- 2、"仅部分预览"的文档,不可在线预览部分如存在完整性等问题,可反馈申请退款(可完整预览的文档不适用该条件!)。
- 3、如文档侵犯您的权益,请联系客服反馈,我们会尽快为您处理(人工客服工作时间:9:00-18:30)。
生产管理之8大浪费
三、材料与供应品 的浪费
生产管理之8大浪费
■督导不良,造成材料的浪费
■对新人指导不够
■指派新工作时未能充分指导
■任务单不清晰、难懂、开错、标准不明 确或新旧标准未能及时更正,造成浪费
■未对每一工序检查材料使用情形(标准 或者差异分析)
四、机器设备的浪费
生产管理之8大浪费
■缺乏工作计划,使所有可用的机器未 获得充分且适合的利用
■疏于检查机器,使其保持良好状态及避 免故障
■班长缺乏正确使用机器的知识,不了解 各种机器的能力
■未定期检查-绳、皮带、链条、输送 带、润滑系统
生产管理之8大浪费
■杀鸡焉用牛刀,小工作用大机器;
■在保养、修理、油漆工作上缺乏与保养 部门的协调
2、不能使新进员工充分发挥其生产力
■没有以亲切、帮助的态度接纳新进员工 ■对新进员工没有给予安全的工作指导
■未让新进员工了解全天的工作及其他内 容
■没有选择合适的老员工配合新进员工的 工作
■对学习速度慢的人没有耐心
■未促使其他部属对新人表示关心、帮 助、友善的态度生产管理之8大浪费
■未尽可能的接近新人 ■没有告知新人,工厂生活情况与规划,
如安全,发薪日期,厕所位置,饮用 水,浴室等 ■未安排完整的训练计划
生产管理之8大浪费
3、未使部属尽其所能
■未指导部属如何做好工作 ■未尽可能的说明工作,使其发生兴趣 ■未对部属的进步与个人生活表示关心 ■没有容纳部属错误的雅量 ■纵容部属派系存在或抱团
■未研究部属个人的不同,以发挥他最大 的潜力
生产管理之8大浪费
■工作人员缺乏必要的安全装配:手套、 安全帽、电焊护面、劳保鞋等
■管理人员未认清其安全责任和事故责任 ■不能激发与保持部属的安全意识以防止
故事 ■未与政府或保险公司之安全检查员配合
生产管理之8大浪费
七、缺乏合作的浪费
生产管理之8大浪费
■与其他管理人员或部门合作 ■未确实了解公司政策并向部属解释 ■不能聪明地处理谣言 ■推诿责任给其他班组长,部属或主管 ■未适当地讲部属的意见反映给主管 ■纵容不满的员工煽动反抗公司的做法
生产管理之8大浪费
■班长不能适当的安排自己的时间
生产管理之8大浪费
二、创意的浪费
生产管理之8大浪费
■未能倾听员工的建议 ■未能鼓励员工多提建议
■在各种问题上不能广听部署的意见
■不能够广泛的研讯本身工作与业务之有 关方法
■未询问新进员工过去工作经验,以获取 有益的意见
生产管理之8大浪费
■未充分向 其他部门请教 ■未考虑或指定适当人员处理所有有用的
生产管理中的8种浪费
生产管理之8大浪费
1、时间的浪费
生产管理之8大浪费
■缺乏适当的计划,使人员在换规格时产生
等待或者停工 ■班长未能彻底了解接受之命令与指示
■缺乏对全天工作内容的认识
■对班长的命令或指示不清楚 ■未能确实督导工具、材料、模具等应放
置于一定场所
■不应加班的工作,造成加班 生产管理之8大浪费
生产管理之8大浪费
■评价一个人只重资格、种族、宗教、关 系、地域
■明知部属的的心理或者生理不适当,却 未加以调动
■生病的部属仍让他工作
■当可能且适当的时间,未能给予升迁
■未考虑影响薪资与工作条件的问题
■未训练一个后补生产者管理之8大浪费
4、欠缺对员工日常管理之数据
生产管理之8大浪费
5、欠缺人员效率管理之数据
生产管理之8大浪费
六、意外事故的浪费
生产管理之8大浪费
■未认识到预防意外事故是工作的一部分 ■未对全体部属彻底说明安全事务
■未给机器装上安全防护,并确保有效
■纵容在工作场所滥用安全防护
■为彻底了解意外事故的间接成本
■未在适当处所上危险记号,并保持干净 与易读
生产管理之8大浪费
■物料放置不善 ■不了解构成意外危险的成因 ■未保存事故记录,并未加分析与运用 ■未建立良好的安全范例 ■为能持久地执行安全规则 ■没有定期与切实检查安全
生产管理之8大浪费
■该报废的机器仍加以修理,比买新 机花了更多费用
■可以修理的机器却报废 ■没有效率管理之数据(机器效率)
生产管理之8大浪费
五、人力的浪费
生产管理之8大浪费
1、无法控制有能力部属之人事变动
■未评估员工员工变动之直接与间接成本 ■“管”得太多 ■对纪律要求太松 ■能做到的“承诺”,却未遵守。
■闲置机器未加保养、任受潮湿、脏污、 灰尘、锈等侵蚀
■缺乏定期清洁,机器不洁
■应修理之处未立即修理
■所有转动零件未检查是否有适当的润滑 生产管理之8大浪费
■机器没有适当的操作说明书 ■缺乏良好的纪律以避免机器设备的滥用 ■纵容部属“不当方法”,修理机器 ■领班不知机器与设备的最新型式 ■滥用小机器作笨重工作 ■未促使部属注意机器的价值与情况
■领料太多,多余料未退料
■领错材料,用错材料
■未能检查水、气、油等管路裂开破损, 导致遗漏
■未检查材料是否排列整齐,正确放置
生产管理之8大浪费
■纵容员工公物私用 ■让不良材料当良品流入制程
■缺乏有效系统防止材料外流,避免损失 或被偷
■可再用的材料当废料处理
■产生不良未立即停止生产。
■纵容或滥用造成浪费:扫把,文具,油 布,灯泡,水管生产等管理之8大浪费
■未检视每一工作是否供给合适的工具和资 源
■放任员工故意逃避它们能作的工作 ■需要的人员不足
■保有太多冗员
■拙于填写报告及各种申请表
■纵容员工养成聊天,擅离工作岗位、浪 费时间之坏习惯
生产管理之8大浪费
■疏于查问与改正员工临时旷职及请假原因
■未要求员工准时开始工作,松于监督 ■拖延决策 ■班长本身不必要的请假与迟到或不守时 ■迟交报告 ■工作中不不要的谈话与查问 ■设备等需要修理时未立即查出原因
■机器故障或未调好 生产管理之8大浪费
■未能让部属了解材料或供应品的价值 ■命令或指示不清 ■纵容不良物料搬运 ■未注意部属的眼力与健康,造成不良品
■缺乏纪律,纵容粗心或不当的工作
■容许部属用不适当的材料(太好或太
差)
生产管理之8大浪费
■未能追踪不良工作起何人,以致不能纠正 ■不能适才适用,特别是新人
■许下不能做到的“承诺”
■无充分理由而解雇人。强留部属在他极端不喜欢的工作上 ■对待部属不公正 ■部属发生争吵时偏袒一方 ■对一个部属批评其他部属(指桑骂槐)
■不能像下属正确说明公司的目标与政策
■未能查出自愿离职的理由 ■在员工调薪上,生产班管理长之8大未浪费参与