八种控制图应用实例(minitab)
利用Minitab制作分阶段控制图(用于改善前后对比)
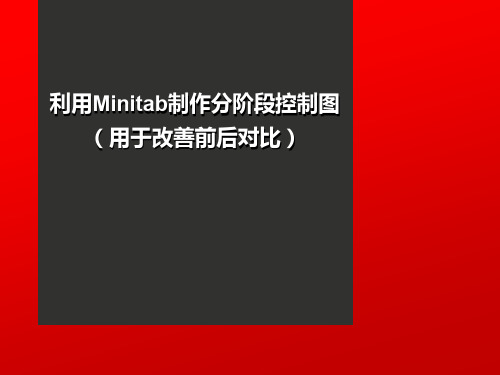
4 of 7
把我们存储的C5(对C5进行了标记为”数据“)列放入对话框中;
点击”单值控制图选项“,选择”阶段“把存储下标的列C4放入阶段对话框中,点击”确定“;
5 of 7
这个就是我们想要的控制图,能很直观的看到改善前后对比情况;
关闭!
基础数据
6 of 7
Thank you!
7 of 7
利用Minitab制作分阶段控制图
(用于改善前后对比)
关于改善前后对比的问题,如何才能更直观的体现出改善前后的差异,这里介绍利用控制图
实现的一个简单方法; 首先在做控制图之前,要先准备好改善前后的数据,改善前后的数据不要求一样多;
2 of 7
要做分阶段控制图,我们首先要把数据堆叠起来(Minitab善后的数据放入数据框;可以把堆叠后的数据放入一个新表
中,或者放入现有工作表中的指定列。
”当前工作表的列“:把数据放在哪一列; ”将下标存储在“:把改善前,改善后的标记存储在哪一列;
3 of 7
数据存储后,就可以做控制图了(控制图路径:统计--控制图--单值变量控制图--单值);
minitab的使用教材

minitab的使⽤教材第⼀节计量值控制图应⽤案例⼀、Xbar-R控制图应⽤案例某公司SPC⼩组对A产品注塑过程的⼀个关键尺⼨的分布离散过⼤的问题进⾏改进,在控制阶段,他们选⽤了X-R控制图对该尺⼨进⾏监控,应⽤流程如下:1.确定需要控制的过程:本例选定的需控制过程为A产品注塑成型过程。
2.确定需控制的项⽬:A产品的⼀个关键尺⼨规格为5.50+0.05mm3.定义测量系统:因为该过程采⽤3班⽣产,因此项⽬组确定的测量系统为3班各⼀位检验员,共⽤同⼀把卡尺,及各班⽣产的产品.4.量测系统分析:经⼩组分析认为该测量系统可接受5.消除明显过程偏差经过⼩组DMAI各阶段已将注塑成型过程的偏差降⾄最低6.确定抽样数及频率每⼩时⼀次,每次5PCS抽取样本数如下表:表17.计算控制界限:(1)计算X和RbarX=5.501 Rbar=0.031(2)计算X bar图控制界限:UCL=X+A2 R bar =5.501+0.58×0.031=5.519LCL=X-A2 R bar =5.5.01-0.58×0.03=5.483CL= X=5.501(3)计算R图控制界限:UCL=D4 R bar =2.11×0.031=0.065LCL= D3 R bar (⽆)CL=R bar =0.0318.根据作图:图,根据准则未发现异常.9.分析Rbar10分析X图:异常总结如下:bar(1)第6、10、11、26、超过控制界限(2)第3、7、27、28点排列呈⼀定的规律性,因为在这些点上,连续3个点中中⼼线⼀侧有2点超过2ó,即靠近控制界限的点太多。
11、计算过程能⼒:因为处于⾮受控状态,故⽆法计算过程能⼒。
12、Minitab在作X bar-R图中的运⽤:步骤如下:第⼀步:将表中的数据输⼊Minitab⼯作表中如下图:(图1-1)第⼆步:在minitab的下拉菜单中选择stat>control charts>Xbar-R,格⼯如下图(图1-2)第三步选中后出现的对话框出现如下信息:如(图1-3).(图1-3)第四步,点选TEST选项作测试选项选择:见(图1-4)(图1-4)各选项含义如下:超出3sigma的规格点;连续9点出现在中⼼线的⼀侧;连续14点交替上升或下降;中⼼线的⼀侧连续3个点中有2个超过2sigma;中⼼线的⼀侧连续5个点中有4个超出1sigma;连续15点位于1sigma规格内;连续8点超过1sigma规格;第五步:点击Options,输⼊sigma⽔平和控制图标题图1-5 第六步:点击“OK”⽣产我们所需的控制图:如下:图1-6第七步⼯作表输出结果如下:⼆、案例X bar-S控制图案例某公司最近接到⼀批机加⼯订单,因客户对产品的某个关键尺⼨“孔径A”要求极为严格,该公司决定⽤控制图平对该尺⼨的加⼯过程进⾏控制,为了对“孔径A”的分布状态有较为详细-S图对“孔径A”进⾏控制,控制流程如下:的了解,品质⼯程部⼯程师决定⽤Xbar1.确定需控制的过程及项⽬。
八种控制图应用实例(minitab)

八种控制图应用实例(minitab)1、试作均值极差控制图S a m p l eS a m p l e M e a n25232119171513119753140302010__X=29.86UCL=45.27LCL=14.46S a m p l eS a m p l e R a n g e252321191715131197531604530150_R=26.70UCL=56.47LCL=0Xbar-R Chart of C1S a m p l eS a m p l e M e a n25232119171513119753140302010__X=29.86UCL=45.27LCL=14.46S a m p l eS a m p l e S t D e v25232119171513119753120151050_S=10.79UCL=22.54LCL=0Xbar-S Chart of C13、试作移动极差控制图O b s e r v a t i o nI n d i v i d u a l V a l u e25232119171513119753168.067.567.066.566.0_X=67.036UCL=67.657LCL=66.416O b s e r v a t i o nM o v i n g R a n g e2523211917151311975310.80.60.40.20.0__MR=0.2333UCL=0.7624LCL=0111111I-MR Chart of C14、试作样本大小n 相等时的p 控制图SampleP r o p o r t i o n2523211917151311975310.300.250.200.150.100.050.00_P=0.1496UCL=0.3009LCL=0P Chart of C15、试作样本大小n 相等时的pn 控制图SampleS a m p l e C o u n t252321191715131197531108642__NP=3.76UCL=9.49LCL=0NP Chart of C66. 试作样本大小n 不相等时的p 控制图〔案例〕某电机厂生产洗衣机用小型电机,构成交验批的批量各不相等,现每隔1小时抽取一个样本,共25批,经检验将不合格品数及不合格品率记入数据表,试作分析用控制图。
Minitab控制图

控制图介绍
Minitab
Minitab
1.控制图的基本格式
• 控制图的基本格式如图所示。
质 量 特 性 数 据
●
● ● ● ● ● ● ●
UCL
● ●
CL LCL
子样号
• 中心线CL(Central Line)——用细实线表示; • 上控制界限UCL(Upper Cortrol Limit)——用虚线表示; • 下控制界限LCL(Lower Control Limit)——用虚线表示。
Minitab
2) 失控状态的判断
只要控制图上的点出现下列情况时,就可判断工序 为失控状态: • (a) 控制图上的点超出控制界限外或恰好在在界限上; • (b) 控制界限内的点排列方式有缺陷,呈现非随机排 列。
Minitab
控制图有缺陷的状态
• • (1)点越出控制界限。 (2) 点在控制界限附近,即在 2σ~3σ 之间。 ( 称为 警戒区间) a)连续3点中有2点在警戒区内(0.0053);
Minitab
控制图有缺陷的状态
(4)点有连续上升或下降趋向,如点数≥7,则判断 有系统性因素影响。
● ● ● ● ● ● ● ● ● ●
μ
-3σ
(5)点的波动呈现周期性变化,表明生产过程有系 统性因素发生。
Minitab
子集的变量控制图 X-bar R S X-bar-R X-bar-S
Minitab
• 检验 1 一个点距离中心线超过 3-sigma。检 验 1 评估变异模式是否稳定。 • 检验 1 提供出最强有力的缺乏控制证据。 • 如果过程中的较小偏移有意义,则可以使 用检验 2、5 和 6 对检验 1 进行补充,以便 生成敏感度更高的控制图
MSA测量系统分析之Minitab中文应用案例(步骤清晰实用)精选全文

应多数值在控 制限外
在控制限外表示过程实际 的变差大,同时表明测量 能力高。
均值
部件对比图:可显示在研究过程中所测量的并按部件排列的所有测量结果。测量结果用 点表示,平均值用带十字标的圆形符号表示。 判断:1.每个部件的多个测量值应紧靠在一起,表示测量的重复再现性的变差 小。
2.各平均值之间的差别应明显,这样可以清楚地看出各部件之间的差别。 例:图中的7#、10#重复测量的精确度较其他点要差,如果测量系统的R&R偏大时,可 以对7#、10#进行分析。
所有点落在管理界限内 ->良好
大部分点落在管理界限外 ->主变动原因:部品变动
->良好
->测量值随部品的变动 ->测量值随OP的变动
->对于部品10,OP有较大分歧;
M--测量系统分析: 离散型案例(名目型):gage名目.Mtw
背景:3名测定者对30部品反复2次TEST
检查者1需要再教育; 检查者3需要追加训练; (反复性)
(2).在量具信息与选项栏分别填入相关资料与信息。
填入相关 资料
注:其他选项若无要求,选择 默认项,不做改动。
一般为6 倍标准差
零件公差 规格
4.5、结果生成:数据表与图表
图表分析表
数据会话表
5.结果分析: (1)图表分析
变异分量条形图:展示了会话窗口中的计算结果,此图显示整个散布中R&R 占的比重是否充分小。 判断:量具R&R,重复(Repeat), 再现性(Reprod)越小越好。
A—假设测定:案例:2sample-t.MTW (2): 2-sample t(单样本)
① 正态性验证:
<统计-基本统计- 正态性检验 : >
MiNitab作控制图的方法
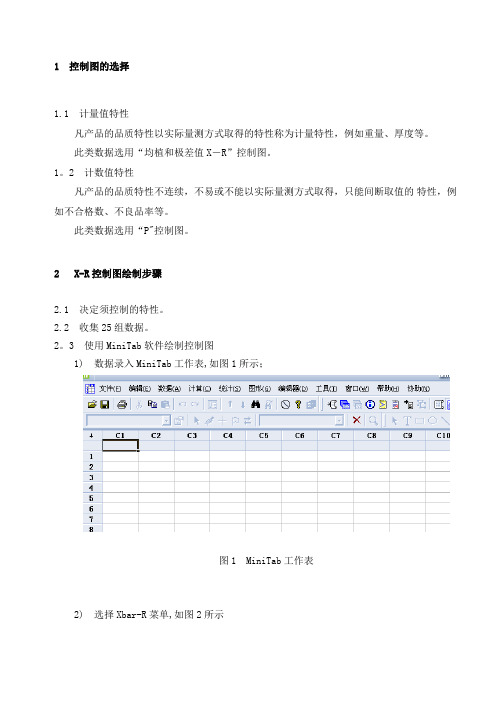
1 控制图的选择1.1 计量值特性凡产品的品质特性以实际量测方式取得的特性称为计量特性,例如重量、厚度等。
此类数据选用“均植和极差值X-R”控制图。
1。
2 计数值特性凡产品的品质特性不连续,不易或不能以实际量测方式取得,只能间断取值的特性,例如不合格数、不良品率等。
此类数据选用“P"控制图。
2 X-R控制图绘制步骤2.1 决定须控制的特性。
2.2 收集25组数据。
2。
3 使用MiniTab软件绘制控制图1) 数据录入MiniTab工作表,如图1所示;图1 MiniTab工作表2) 选择Xbar-R菜单,如图2所示图2 Xbar-R菜单 3) 根据会话窗口输入相应数据,如图3所示图3 Xbar-R会话窗口 4)绘制X—R控制图,如图4所示S a m p l eS a m p l e M e a n5432126242220__X=22.221UCL=25.459LCL=18.984S a m p l eS a m p l e R a n g e543211612840_R=6.70UCL=13.42LCL=01Xbar-R Chart of C12图4 X-R 控制图2。
4 检查是否有超出控制界限的点,如图4中第5组数据。
2。
5 将超出控制界限的数据剔除并重复“2.4”。
3 生产现场X-R 控制图的使用3。
1 生产现场依据规定的抽样频率及抽样数,记录数据,所得数据录入MiniTab 工作表. 3.2 根据历史计算出的“均值"、“标准差”,绘制生产现场实时X —R 控制图。
历史统计值输入窗口如图5所示。
图5 控制参数输入窗口4 控制图判读原则及异常控制图的纠正/预防措施4.1 正常之控制图其各点的动态1) 多数的点集中在中心线附近。
2)少数的点落在控制界限附近(但未超出控制界限).3)各点的分布呈随机状态。
4。
2 异常控制图的判读1)任何超出控制限的点2) 连续7个点在中心线之上或之下3)连续7个点上升或下降4)任何其它明显的非随机图形,如2/3的描点应落在控制限1/3的中间区域,描点成规则形状。
MINITAB在制药企业产品质量回顾中的应用
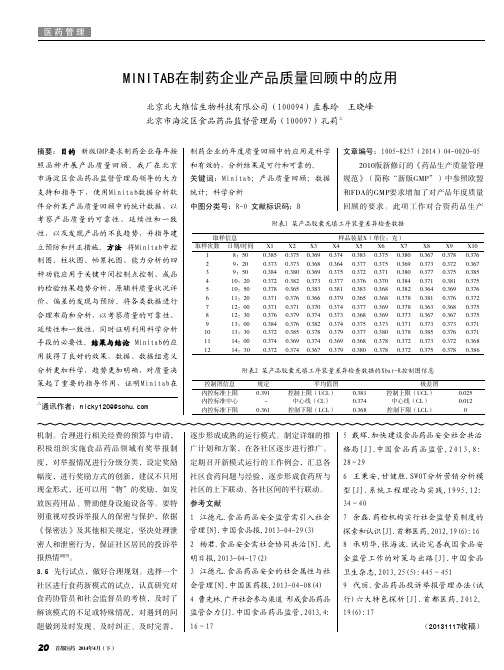
X8 0.367 0.373 0.377 0.371 0.364 0.381 0.363 0.367 0.373 0.385 0.373 0.375
X9 0.378 0.372 0.375 0.381 0.369 0.376 0.368 0.367 0.373 0.376 0.372 0.378
X10 0.376 0.367 0.385 0.375 0.376 0.372 0.375 0.375 0.371 0.371 0.368 0.386
逐步形成成熟的运行模式。制定详细的推 广计划和方案,在各社区逐步进行推广。 定期召开新模式运行的工作例会,汇总各 社区食药问题与经验,逐步形成食药所与 社区的上下联动、各社区间的平行联动。 参考文献 1 江德元.食品药品安全监管需引入社会 管理[N].中国食品报,2013-04-29(3) 2 杨君.食品安全需社会协同共治[N].光 明日报,2013-04-17(2) 3 江德元.食品药品安全的社会属性与社 会管理[N].中国医药报,2013-04-08(4) 4 曹先林.广开社会参与渠道 形成食品药品 监管合力[J].中国食品药品监管,2013,4: 16~17
水分(%)应≤14.5%批号 13.30 13.94 14.42 14.39 14.14 14.04 12.88 14.47 14.38 13.14 13.40 13.62 12.70 12.80 13.72 13.28 13.66 14.37 14.48
附表4 2012年偏差原因分类表
偏差原 因分类
我公司采用Minitab控制图功能时在该 软件“Xbar-R选项”中设置以上八个检验 模式,任何检验异常都应结合实际生产进
gb40912001将ucl和lcl之间等分为六个区标号为abccba两个a区b附表1某产品胶囊充填工序装量差异检查数据附表2某产品胶囊充填工序装量差异检查数据的xbarr控制图信息附表3某厂供货的原料水分检测数据附表42012年偏差原因分类表附图1某产品胶囊充填工序装量差异检查数据的xbarr控制图23211917151311039038037036样本037443ucl038123lcl036762039103612321191715131100240018001200060000样本r001179ucl002493lcl0某产品胶囊充填工序装量差异检查数据的xbarr控制图批号水分应145批号201201011330201201021394201201031442201202041439201203051414201204071404201205081288201205091447201206101438201206111314201207121340201208131362201209151270201209161280201210171372201210181328201211191366201212211437201212221448企业来说是熟练的但对大部分国内药品生产企业尤其是口服制剂企业的质量管理人员来说却相当陌生要想正确实施无疑是困难重重
MiNitab作控制图的方法
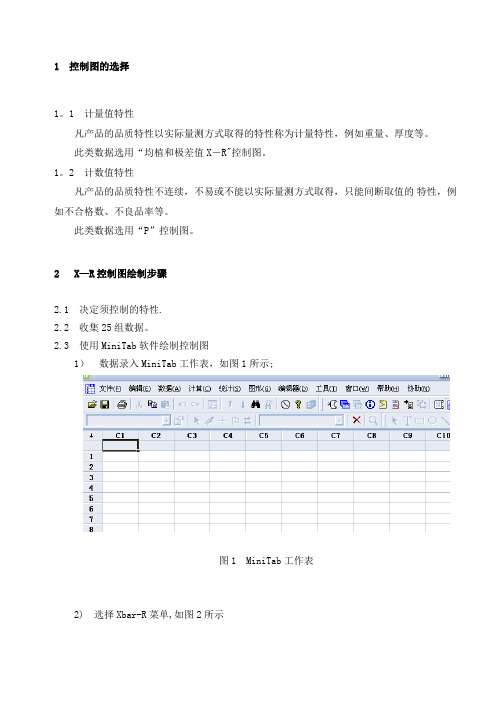
1 控制图的选择1。
1 计量值特性凡产品的品质特性以实际量测方式取得的特性称为计量特性,例如重量、厚度等。
此类数据选用“均植和极差值X-R"控制图。
1。
2 计数值特性凡产品的品质特性不连续,不易或不能以实际量测方式取得,只能间断取值的特性,例如不合格数、不良品率等。
此类数据选用“P”控制图。
2 X—R控制图绘制步骤2.1 决定须控制的特性.2.2 收集25组数据。
2.3 使用MiniTab软件绘制控制图1)数据录入MiniTab工作表,如图1所示;图1 MiniTab工作表2) 选择Xbar-R菜单,如图2所示图2 Xbar—R菜单 3)根据会话窗口输入相应数据,如图3所示图3 Xbar—R会话窗口 4)绘制X-R控制图,如图4所示S a m p l eS a m p l e M e a n5432126242220__X=22.221UCL=25.459LCL=18.984S a m p l eS a m p l e R a n g e543211612840_R=6.70UCL=13.42LCL=01Xbar-R Chart of C12图4 X —R 控制图2。
4 检查是否有超出控制界限的点,如图4中第5组数据。
2。
5 将超出控制界限的数据剔除并重复“2.4"。
3 生产现场X —R 控制图的使用3。
1 生产现场依据规定的抽样频率及抽样数,记录数据,所得数据录入MiniTab 工作表。
3.2 根据历史计算出的“均值"、“标准差”,绘制生产现场实时X-R 控制图。
历史统计值输入窗口如图5所示.图5 控制参数输入窗口4 控制图判读原则及异常控制图的纠正/预防措施4.1 正常之控制图其各点的动态1)多数的点集中在中心线附近。
2) 少数的点落在控制界限附近(但未超出控制界限)。
3)各点的分布呈随机状态。
4。
2 异常控制图的判读1) 任何超出控制限的点2)连续7个点在中心线之上或之下3) 连续7个点上升或下降4) 任何其它明显的非随机图形,如2/3的描点应落在控制限1/3的中间区域,描点成规则形状.4。
MiNitab作控制图的方法
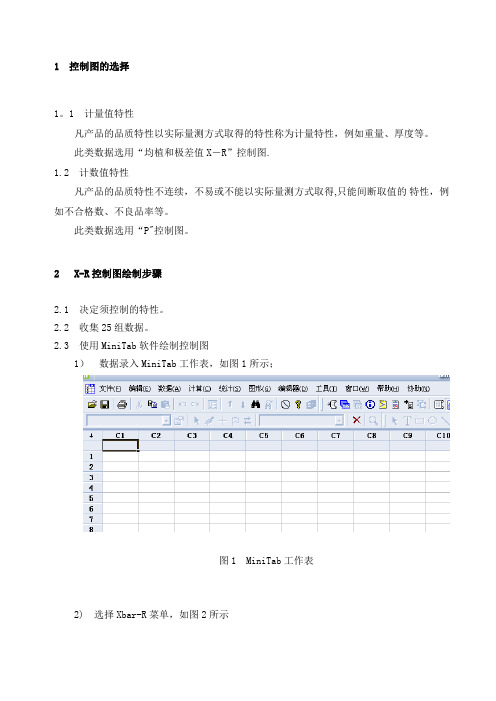
1 控制图的选择1。
1 计量值特性凡产品的品质特性以实际量测方式取得的特性称为计量特性,例如重量、厚度等。
此类数据选用“均植和极差值X-R”控制图.1.2 计数值特性凡产品的品质特性不连续,不易或不能以实际量测方式取得,只能间断取值的特性,例如不合格数、不良品率等。
此类数据选用“P"控制图。
2 X-R控制图绘制步骤2.1 决定须控制的特性。
2.2 收集25组数据。
2.3 使用MiniTab软件绘制控制图1)数据录入MiniTab工作表,如图1所示;图1 MiniTab工作表2) 选择Xbar-R菜单,如图2所示图2 Xbar-R菜单 3)根据会话窗口输入相应数据,如图3所示图3 Xbar—R会话窗口 4)绘制X-R控制图,如图4所示S a m p l eS a m p l e M e a n5432126242220__X=22.221UCL=25.459LCL=18.984S a m p l eS a m p l e R a n g e543211612840_R=6.70UCL=13.42LCL=01Xbar-R Chart of C12图4 X-R 控制图2。
4 检查是否有超出控制界限的点,如图4中第5组数据. 2。
5 将超出控制界限的数据剔除并重复“2。
4”。
3 生产现场X —R 控制图的使用3。
1 生产现场依据规定的抽样频率及抽样数,记录数据,所得数据录入MiniTab 工作表。
3。
2 根据历史计算出的“均值"、“标准差”,绘制生产现场实时X —R 控制图。
历史统计值输入窗口如图5所示。
图5 控制参数输入窗口4 控制图判读原则及异常控制图的纠正/预防措施4.1 正常之控制图其各点的动态1)多数的点集中在中心线附近.2)少数的点落在控制界限附近(但未超出控制界限)。
3)各点的分布呈随机状态。
4.2 异常控制图的判读1) 任何超出控制限的点2)连续7个点在中心线之上或之下3) 连续7个点上升或下降4)任何其它明显的非随机图形,如2/3的描点应落在控制限1/3的中间区域,描点成规则形状。
八种控制图应用实例(minitab)

1、试作均值极差控制图
2、试作均值极差控制图、中位数极差控制图和均值标准差控制图
3、试作移动极差控制图
4、试作样本大小n 相等时的p
控制图
5、试作样本大小n 相等时的pn
控制图
6. 试作样本大小n不相等时的p控制图
〔案例〕
某电机厂生产洗衣机用小型电机,构成交验批的批量各不相等,现每隔1
小时抽取一个样本,共25批,经检验将不合格品数及不合格品率记入数据
表,试作分析用控制图。
7. 试作C控制图
某电线生产过程中,每隔一定时间对100m导线进行检查,检查的结果如表所示,试作C控制图。
8. 试作U控制图
某电子产品检查的结果如表所示,试作U控制图。
MiNitab作控制图的方法【范本模板】

1 控制图的选择1.1 计量值特性凡产品的品质特性以实际量测方式取得的特性称为计量特性,例如重量、厚度等。
此类数据选用“均植和极差值X-R”控制图。
1。
2 计数值特性凡产品的品质特性不连续,不易或不能以实际量测方式取得,只能间断取值的特性,例如不合格数、不良品率等。
此类数据选用“P”控制图.2 X—R控制图绘制步骤2.1 决定须控制的特性。
2。
2 收集25组数据.2.3 使用MiniTab软件绘制控制图1)数据录入MiniTab工作表,如图1所示;图1 MiniTab工作表2)选择Xbar—R菜单,如图2所示图2 Xbar-R菜单 3) 根据会话窗口输入相应数据,如图3所示图3 Xbar—R会话窗口4)绘制X-R控制图,如图4所示Sa m p l eS a m p l e M e a n5432126242220__X=22.221UCL=25.459LCL=18.984S a m p l eS a m p l e R a n g e543211612840_R=6.70UCL=13.42LCL=01Xbar-R Chart of C12图4 X —R 控制图2.4 检查是否有超出控制界限的点,如图4中第5组数据。
2.5 将超出控制界限的数据剔除并重复“2。
4”。
3 生产现场X —R 控制图的使用3。
1 生产现场依据规定的抽样频率及抽样数,记录数据,所得数据录入MiniTab 工作表。
3.2 根据历史计算出的“均值”、“标准差",绘制生产现场实时X-R 控制图。
历史统计值输入窗口如图5所示。
图5 控制参数输入窗口4 控制图判读原则及异常控制图的纠正/预防措施4.1 正常之控制图其各点的动态1)多数的点集中在中心线附近。
2)少数的点落在控制界限附近(但未超出控制界限)。
3)各点的分布呈随机状态。
4.2 异常控制图的判读1) 任何超出控制限的点2)连续7个点在中心线之上或之下3)连续7个点上升或下降4)任何其它明显的非随机图形,如2/3的描点应落在控制限1/3的中间区域,描点成规则形状.4.3 异常之控制图的纠正/预防措施1) 出现任何超出控制界限的点,都应提请相关单位进行原因分析,并采取纠正措施。
Minitab质量分析图表控制图

Xbar-S控制图-制作与分析
样本均值
血糖水平 的 Xbar-S 控制图
UCL=130.72 120
__
100
X =101.03
80
LCL=71.35
1
3
5
7
9
11
13
15
17
19
样本
50
UCL=50.67
40
30
_ S=28.77
20
10 LCL=6.88
极差R 控制图-制作与分析
样本极差
AB间距 的 R 控制图
18
16
UCL=15.98
14
12
10
8
_ R=7.56
6
4
2
0
LCL=0
1 3 5 7 9 11 13 15 17 19 21 23 25 样本
• 解释结果
➢ 这些点随机分布在各控制限制之间,表明这是稳定过程。此外,比较相同 数据在 R 控制图上的点与在 X 控制图上的点也很重要。比较Xbar控制 图,Xbar基本稳定,而且点的分布同R不相同,再次表明这是稳定过程。
标准差S控制图-制作与分析
• 假设您要显示 S 控制图,以便在一周的时间里监视三个班次中 故障数的变异性。由于在各班次中进行的测量次数有所不同,因 此数据中的子组大小不等。您要使用合并标准差估计 s。
➢ 1 打开文件“质量控制示例.MTW”。 ➢ 2 选择统计 > 控制图 > 子组的变量控制图 > S。
• 缺陷品控制图 ➢ 您可以将产品与标准进行比较,并将其归类为有缺陷产品或无缺陷产品。 例如,线长是否满足强度要求。缺陷品控制图有:
MiNitab作控制图的方法

1 控制图得选择1、1 计量值特性凡产品得品质特性以实际量测方式取得得特性称为计量特性,例如重量、厚度等.此类数据选用“均植与极差值X—R”控制图.1、2 计数值特性凡产品得品质特性不连续,不易或不能以实际量测方式取得,只能间断取值得特性,例如不合格数、不良品率等.此类数据选用“P”控制图。
2 X—R控制图绘制步骤2、1 决定须控制得特性。
2、2 收集25组数据。
2、3使用MiniTab软件绘制控制图1)数据录入MiniTab工作表,如图1所示;图1 MiniTab工作表2)选择Xbar-R菜单,如图2所示图2 Xb ar-R菜单3) 根据会话窗口输入相应数据,如图3所示图3 Xba r-R 会话窗口4) 绘制X -R 控制图,如图4所示S a m p l eS a m p l e M e a n5432126242220__X=22.221UCL=25.459LCL=18.984S a m p l eS a m p l e R a n g e543211612840_R=6.70UCL=13.42LCL=01Xbar-R Chart of C12图4 X—R 控制图2、4 检查就是否有超出控制界限得点,如图4中第5组数据。
2、5 将超出控制界限得数据剔除并重复“2、4”。
3 生产现场X-R 控制图得使用3、1生产现场依据规定得抽样频率及抽样数,记录数据,所得数据录入MiniTab工作表.3、2 根据历史计算出得“均值"、“标准差",绘制生产现场实时X—R控制图.历史统计值输入窗口如图5所示。
图5 控制参数输入窗口4 控制图判读原则及异常控制图得纠正/预防措施4、1 正常之控制图其各点得动态1) 多数得点集中在中心线附近。
2)少数得点落在控制界限附近(但未超出控制界限)。
3) 各点得分布呈随机状态.4、2 异常控制图得判读1)任何超出控制限得点2)连续7个点在中心线之上或之下3) 连续7个点上升或下降4) 任何其它明显得非随机图形,如2/3得描点应落在控制限1/3得中间区域,描点成规则形状。
- 1、下载文档前请自行甄别文档内容的完整性,平台不提供额外的编辑、内容补充、找答案等附加服务。
- 2、"仅部分预览"的文档,不可在线预览部分如存在完整性等问题,可反馈申请退款(可完整预览的文档不适用该条件!)。
- 3、如文档侵犯您的权益,请联系客服反馈,我们会尽快为您处理(人工客服工作时间:9:00-18:30)。
1、试作均值极差控制图
2、试作均值极差控制图、中位数极差控制图和均值标准差控制图
3、试作移动极差控制图
4、试作样本大小n相等时的p控制图
5、试作样本大小n相等时的pn控制图
6.
试作样本大小n 不相等时的p 控制图
〔案例〕
某电机厂生产洗衣机用小型电机,构成交验批的批量各不相等,现每隔1小时抽取一个样本,共25批,经检验将不合格品数及不合格品率记入数据表,试作分析用控制图。
7. 试作C控制图
某电线生产过程中,每隔一定时间对100m导线进行检查,检查的结果如表所示,试作C控制图。
实用文档
文案大全
8. 试作U 控制图
某电子产品检查的结果如表所示,试作U 控制图。