机床换刀点调试步骤
数控设备的安装调试及验收步骤

数控设备的安装调试及验收步骤数控设备的安装、调试和验收是设备前期管理的重要环节。
当机床运到后,首先要进行安装、调试、并进行试运行,精度验收合格后才能交付使用。
多数数控机床都是分解为部件装箱运输,到位后再进行组装和重新调试。
一、数控设备的安装一般数控设备的安装可按以下步骤进行。
1. 开箱核查数控设备到位后,设备管理部门要及时组织设备管理人员、设备安装人员、以及各采购员等开箱检查,如果是进口设备,还须有进口商务代理海关商检人员等。
检验的主要内容是:1)装箱单;2)校对应有的随机操作、维修说明书、图样资料、合格证等技术文件;3)按合同规定,对照装箱单清点附件、备件、工具的数量、规格及完好状况;4)检查主机、数控柜、操作台等有无明显碰撞损伤、变形、受潮、锈蚀等,并填写“设备开箱验收登记卡”存档。
开箱验收如果发现货物损坏或遗漏,应及时与有关部门或外商联系解决。
尤其是进口设备,应注意索赔期限。
2. 安装前的准备工作认真阅读理解设备安装方面资料,了解生产厂家对机床基础的具体要求和组装要求,做好安装前的准备工作。
3. 部件组装机床组装前要把导轨和各滑动面、接触面的防绣涂料清洗干净,把机床各部件,如数控柜、电气柜、立柱、刀库、机械手等组装成整机。
组装时必须使用原来的定位销、定位块等定位元件,以便保证调整精度。
4. 油管、气管的连接根据机床说明书中的电气接线图和气、液压管路图,将有关电缆和管道按标记一一对号接好。
连接时特别要注意可靠的接触及密封,否则试机时,漏油、漏水,给试机带来麻烦。
油管、气管连接中要特别防止异物从接口中进入管路,造成整个液压、气压系统故障。
电缆和管路连接完毕后,做好各管线的固定,安装防护罩壳,保证整齐的外观。
5. 数控系统的连接1)外部电缆的连接主要指数控装置与MDI/CRT单元、强电控制柜、机床操作面板、进给伺服电动机和主轴电动机动力线、反馈信号线的连接等,这些连接必须符合随机提供的连接手册的规定。
数控车床刀具补偿及换刀程序编写

绝对编程:
G90 G28 X140.0 Z130.0 ; A--B--R
T0202 ;
换刀
G29 X60.0 Z180.0 ;
R--B--C
参考点
增量编程
G28 U40 W100 T0000 T0202 目标点 G29 U-80 W50
可以使按工件轮廓编程不受影响.
❖ 一、刀具补偿的概念
❖ 刀具补偿:是补偿实际加工时所用的刀具
与编程时使用的理想刀具或对刀时使用的 基准刀具之间的偏差值,保证加工零件符 合图纸要求的一种处理方法。
二、刀具补偿的种类
刀具补偿
刀具的几何补偿
(TXXXX实现)
几何位置补偿 磨损补偿
刀尖圆弧半径补偿
(G41、G42实现)
从图示可知,
➢ 若刀尖方位码设为0或9时,机床将以刀尖圆弧中心
为刀位点进行刀补计算处理;
➢ 当刀尖方位码设为1~8时,机床将以假想刀尖为刀
位点,根据相应的代码方位进行刀补计算处理。
5、刀具半径补偿指令 ❖格式:
G41 G00 X __ Z __ G42 G01
G40 G00 X__ Z __
❖说明:
3、刀径补偿的取消
❖刀具中心从与编 程轨迹偏离过度到 与编程轨迹重合的 过程.
刀径补偿的引入和取 消必须是不切削的空 行程上.
例2:考虑刀尖半径补偿
D
C (24,-24)
O1111 N1 G92 X40.0 Z10.0 N2 T0101 N3 M03 S400 N4 G00 X40.0 Z5.0 N5 G00 X0.0 N6 G42 G01 Z0 F60 (加刀补) O N7 G03 X24.0 Z-24 R15 N8 G02 X26.0 Z-31.0 R5 N9 G40 G00 X30 (取消刀补) N10 G00 X45 Z5 N11 M30
第一章机床的安装调试和维护
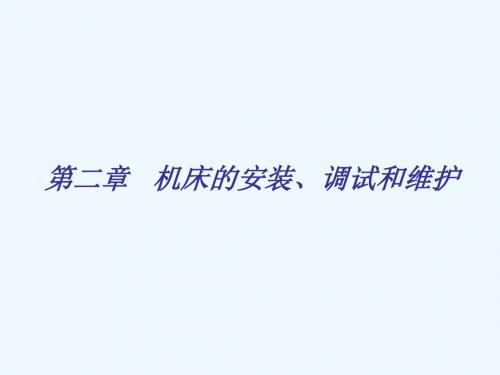
8、刀库不能往前换刀
气压过低;气阀损坏
检查、调整气源压力;换气阀;
第二章 机床的安装、调试和维护
二、数控机床的调试:
数控机床的调试包括:几何精度和加工精度的调整以及机床功能调试 1、机床精度调整 机床的几何精度一般在出厂前已经经过了调试和检验,特别是对于小 型机床,由于运输和安装过程中不需要进行部件的拆装,因此只要在安装 机床时能够保证床身的水平,机床的几何精度一般都能保证。床身的水平 可以通过调整垫铁和地脚螺栓来调整。 对于大、中型机床,由于要进行部件的拆装,因此在安装时不但要保 证床身的水平外,还要注意在组装部件时要保证组装的精度,才能保证机 床的几何精度。 2、机床功能调试: 调试前,先检查数控系统的参数和PLC的参数是否与随机手册中的参数 一致。然后试验各主要操作功能、安全措施、运行行程以及常用指令执行 情况等,如手动操作方式、点动方式、编辑方式(EDIT)、数据的输入方 式(MDI)、自动运行方式、软硬限位以及主轴挂档指令和各级转速指令是 否正确。最后检查机床辅助功能及附件的工作情况,如照明、冷却防护罩
0.01/300
14
主轴轴线和Y轴的垂直度
0.015/300
0.011/300
00上为0.012/300
a) 0.015 b) 0.01/300
第二章 机床的安装、调试和维 护
序号 16 检验项目 工作台面和X轴的平行度 允许误差
0.030
实际误差
第二章 机床的安装、调试和维护
数控功能:
(1)指令功能——指令的功能实现及准确性。
(2)操作功能——检验回原点、执行程序、进给倍率、急停等功能的准确性。 (3)CRT显示功能——检验位置、程序、各种菜单显示功能。
第二章 机床的安装、调试和维护
数控机床调试步骤要求

数控机床调试步骤要求〔一〕安装调试的前期准备工作:用户的准备事项,由售后效劳人员联系落实。
〔1〕立式加工中心1.机床的吊运与安装:包括机床的吊运、开箱、安装、粗调水平、防锈油的清洗。
其中安装可采用混凝土地基加地脚螺钉固定机床,或直接使用随机的调整垫铁加地脚螺钉固定机床。
2.根据机床型号的不同确定外接电源线的线径,以下为各种型号机床参考线径:2.1 CY-VMC650采用10平方毫米左右线径。
2.2 CY-VMC850采用16平方毫米左右线径。
2.3 CY-VMC1060/1270/1370采用25平方毫米左右线径。
2.4 CY-VMC1580/1690/1890采用35平方毫米左右线径。
2.5 所有机床必须可靠接地。
3.安装调试前用户需购置以下备件物品:3.1 空压机,要求排量在0.6立方米/分钟以上。
3.2 连接空压机至机床的PTV气管,外径为12毫米。
3.3 标准刀柄和拉钉:CY-VMC650/850/1060采用型号为BT-40刀柄和45°拉钉;CY-VMC1270/1370/1580采用型号为BT-50刀柄和45°拉钉。
3.4刀具的购置:根据用户加工零件的实际情况,来确定购置不同夹持方式的刀柄和刀具,比方:3.4.1铣平面用的盘铣刀柄和直径为Ф63、Ф80、Ф100不等的盘铣刀体及刀片。
3.4.2强力铣夹头刀柄,主要方便于夹持直径较大的外圆铣刀和球头铣刀,例如夹持Ф20毫米的球头铣刀。
3.4.3弹簧夹头刀柄,主要方便于夹持小直径外圆铣刀和球头铣刀,例如夹持Ф3~Ф16毫米的外圆铣刀。
常用的刀柄规格型号为Ф32型刀柄。
3.4.4一体式或别离式钻夹头刀柄,主要用于装夹直柄小直径钻头,常见刀柄规格型号为Ф3~Ф13毫米的钻夹头。
3.4.5带扁尾莫氏锥孔刀柄,主要用于装夹锥柄钻头。
常用的刀柄规格型号是3号和4号莫氏锥孔刀柄。
3.4.6不带扁尾莫氏锥孔刀柄,主要用于装夹锥柄外圆铣刀。
数控机床和安装及调试

(二)卧式数控车床几何精度检验
定位精度的检验
数控机床的定位精度是测量机床各坐标轴在数控系统控制下 所能达到的位置精度。
1、直线运动定位精度 这项检测一般在空载条件下进行,对所测的每个坐标轴在全
行程内,视机床规格,分每20mm、50mm或l00mm间距 正向和反向快速移动定位,在每个位置上测出实际移动距 离和理论移动距离之差。
几何精度检验,又称静态精度检Байду номын сангаас,是综合反映机床关键 零部件经组装后的综合几何形状误差。 数控机床的几何精度的检验工具和检验方法类似于普通机床, 但检测要求更高。
几何精度检测测试条件:
1、地基完全稳定、地脚螺栓处于压紧状态下进行。
2、机床各坐标轴往复运动多次,主轴按中等的转速运转 十多分钟后进行。在预热状态下进行。
1、外圆车削
试件长度取床身上最大车削直径的1/2,或最大车削长度 的1/3,最长为500mm,直径大于或等于长度的1/4。
精车后圆度小于0.007mm,
直径的一致性在200mm测量长度上小于0.03mm(机床加 工直径小于或等于800mm时)。
2、端面车削
试件外圆直径最小为最大加工直径的1/2。精车后检验其 平面度,300mm直径上为
数控系统的验收
CFTN为“1”表示正在执行M、S、T功能; CMTN为 "1"表示正在执行自动运行指令; CDWL为 "1"表示正在执行暂停; CINP为 "1"表示正在进行到位检测; COVZ"l"表示倍率为0%; CITL为"1"表示互锁信号接通; CSCT为 "1"表示等待主轴速度到达信号接通
太高。
5、回转工作台的定位精度
加工中心的刀库形式与自动换刀程序的调试
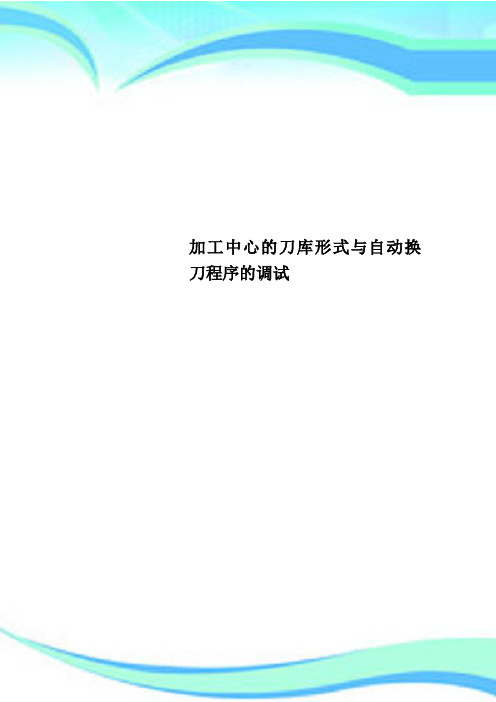
加工中心的刀库形式与自动换刀程序的调试————————————————————————————————作者:————————————————————————————————日期:ﻩ加工中心的刀库形式与自动换刀程序的调试一、实训目的( 1 )了解加工中心的各种刀库形式;( 2 )了解机械手换刀的基本动作组成;( 3 )掌握加工中心自动换刀程序的编写与调试运行;二、预习要求认真阅读加工中心组成、换刀装置、自动换刀程序的编写等章节内容。
三、实训理论基础1 .加工中心的刀库形式加工中心刀库的形式很多,结构各异。
常用的刀库有鼓轮式和链式刀库两种。
图 11-1鼓轮式刀库( a )径向取刀形式( b )轴向取刀形式 ( c )径向布置形式( d )角度布置形式鼓轮式刀库结构简单,紧凑,应用较多。
一般存放刀具不超过32 把。
见图 11-1。
径向取刀形式( a )多用于使用斗笠式刀库的立式加工中心和使用角度布置的机械手换刀装置的加工中心;形式( b )应用比较广泛,可用于立式和卧式加工中心,换刀可用机械手或直接主轴移动式换刀。
由于从布局设计方面的考虑,鼓轮式刀库一般都采用侧向安装的结构形式,若用于机械手平行布置的加工中心时,刀库中的刀袋(座)通常在换刀工作位可作90 o 翻转。
形式( c )多用于小型钻削中心;形式( d )一般用于专用加工中心。
链式刀库多为轴向取刀,适于要求刀库容量较大的加工中心。
见图11-2 。
图 11-2 链式刀库2 .自动换刀装置及其动作分解斗笠式刀库换刀装置我们已经在实训 4 中接触过,在此就不再赘述。
对于刀库侧向布置、机械手平行布置的加工中心,其换刀动作分解见图11-3。
换刀时,Txx指令的选刀动作和M6指令的换刀动作可分开使用。
图 11-3平行布置机械手的换刀过程图11-4 角度布置机械手的换刀过程对于刀库侧向布置、机械手角度布置的加工中心,其换刀动作分解见图 11-4 。
机械手换刀装置的自动换刀动作如下:(1)主轴端: 主轴箱回到最高处( Z 坐标零点),同时实现“主轴准停”。
FANUC刀库换刀——详解.

加工中心机床圆盘式刀库发那科系统PMC的编程技术安庆长谷川数控机床有限公司 雷晓鹏北京发那科机电有限公司 胡 年自动换刀机构(ATC)是数控机床易发生故障的地方。
本文介绍PMC的编程思路和方法,供大家讨论。
此程序自2004年始已在数百台加工中心运用。
一、基本规则1、刀具在D0000到D0032登录。
D0000登录主轴刀具号,D0001到D0032登录刀套内刀具号,在此假定刀库容量为32把刀。
2、执行T码时,刀库中T码刀具旋转到换刀口位置,在刀库旋转过程中,程序自动加工运行不中断,称之为预选刀。
3、M6执行换刀过程,执行前,Z轴必须回第一参考点,即 G91 G28 Z0或 M19 G91 G28 Z0。
4、允许的大径刀(如面铣刀)直径不容许超过普通刀具(以下简称:小径刀)最大直径的二倍,否则大径刀之间随机交换会撞刀。
刀具重量不能超过刀库容许重量。
大径刀刀具号设定规则:大径刀的相临两侧刀套内必须为空,空刀套的刀具号自动设定为99(也可设定其他数字,PMC识别为空刀)。
D100内设定大径刀个数,小径刀刀具号必须大于大径刀个数乘2加1。
初始设定主轴刀具号D0000必须是小径刀刀具号。
5、大径刀具交换规则:小径刀可放进大径刀刀套内,大径刀不可放进小径刀刀套内。
主轴小径刀与刀库小径刀交换,一次性换刀;主轴大径刀与刀库大径刀交换,一次性换刀;主轴小径刀与刀库大径刀交换,一次性换刀,小径刀放进大径刀刀杯套内;主轴大径刀与刀库小径刀交换, 第一次将原大径刀刀套内的小径刀换到主轴上,第二次再进行小径刀之间的交换。
以上交换规则PMC自动识别换刀。
6、在刀库运行中发生停电等故障,具备中断点记忆和用按键操作恢复功能。
有完善的电机保护和报警操作提示。
7、以上自动刀具交换(ATC)动作本文介绍的都用PMC完成,读者也可用宏程序和PMC结合编程实现。
二、PMC程序框图三、详细介绍刀库盘旋转部分PMC程序和说明1、准备工作自动换刀部分反馈信号:R30.0=1 主轴抓刀反馈;R30.1=1 主轴松刀反馈,延迟0.2秒是消除信号反馈传感器安装误差,其它信号反馈延迟道理相同;R30.2=1 刀杯上(水平位置)信号反馈;R30.3=1 刀杯下(刀具垂直向下位置)信号反馈。
数控车床对刀点与换刀点的确定:

第二章 数控加工的工艺分析
2.2.6、对刀点与换刀点的确定: 、对刀点与换刀点的确定: 1.对刀点的确定 对刀点的确定 在使用对刀点确定加工原点时, 在使用对刀点确定加工原点时,就需要进行 对刀” “对刀”。 所谓对刀是指使“刀位点” 对刀点” 所谓对刀是指使“刀位点”与“对刀点”重 合的操作。 合的操作。每把刀具的半径与长度尺寸都是不同 刀具装在机床上后, 的,刀具装在机床上后,应在控制系统中设置刀 具的基本位置。 刀位点” 具的基本位置。“刀位点”是指刀具的定位基准 如下图所示, 点。如下图所示,圆柱铣刀的刀位点是刀具中心 线与刀具底面的交点; 线与刀具底面的交点;球头铣刀的刀位点是球头 的球心点或球头顶点; 的球心点或球头顶点;车刀的刀位点是刀尖或刀 尖圆弧中心;钻头的刀位点是钻头顶点。 尖圆弧中心;钻头的刀位点是钻头顶点。
第二章 数控加工的工艺分析
(a)
(b)
(a) 数控铣床坐标系; (b) 铣削加工零件
第二章 数控加工的工艺分析
第二章 数控加工的工艺分析
2.换刀点的确定 换刀点的确定 换刀点是为加工中心、 换刀点是为加工中心、数控车床等采用多刀 进行加工的机床而设置的, 进行加工的机床而设置的,因为这些机床在加工 过程中要自动换刀。对于手动换刀的数控铣床, 过程中要自动换刀。对于手动换刀的数控铣床, 也应确定相应的换刀位置。 也应确定相应的换刀位置。为防止换刀时碰伤零 刀具或夹具, 件、刀具或夹具,换刀点常常设置在被加工零件 的轮廓之外,并留有一定的安全量。 的轮廓之外,并留有一定的安全量。 2.2.7 刀具走刀路线的确定 走刀路线就是刀具在整个加工工序中的运动 轨迹,它不但包括了工步的内容, 轨迹,它不但包括了工步的内容,也反映出工步 顺序。走刀路线是编写程序的依据之一。 顺序。走刀路线是编写程序的依据之一。确定走 刀路线时应注意以下几点: 刀路线时应注意以下几点:
OKUMA OSP700自动换刀刀库故障诊断与维修
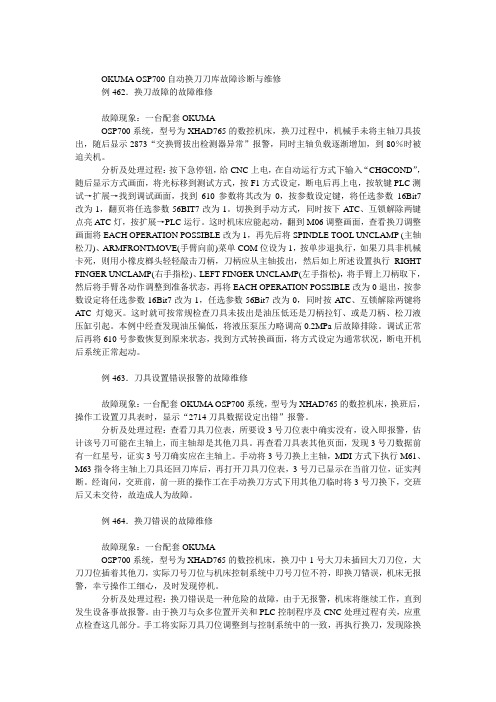
OKUMA OSP700自动换刀刀库故障诊断与维修例462.换刀故障的故障维修故障现象:一台配套OKUMAOSP700系统,型号为XHAD765的数控机床,换刀过程中,机械手未将主轴刀具拔出,随后显示2873“交换臂拔出检测器异常”报警,同时主轴负载逐渐增加,到80%时被迫关机。
分析及处理过程:按下急停钮,给CNC上电,在自动运行方式下输入“CHGCOND”,随后显示方式画面,将光标移到测试方式,按F1方式设定,断电后再上电,按软键PLC测试→扩展→找到调试画面,找到610参数将其改为0,按参数设定键,将任选参数16Bit7改为1,翻页将任选参数56BIT7改为1。
切换到手动方式,同时按下ATC、互锁解除两键点亮ATC灯,按扩展→PLC运行。
这时机床应能起动,翻到M06调整画面,查看换刀调整画面将EACH OPERA TION POSSIBLE改为1,再先后将SPINDLE TOOL UNCLAMP (主轴松刀)、ARMFRONTMOVE(手臂向前)菜单COM位设为1,按单步退执行,如果刀具非机械卡死,则用小橡皮榔头轻轻敲击刀柄,刀柄应从主轴拔出,然后如上所述设置执行RIGHT FINGER UNCLAMP(右手指松)、LEFT FINGER UNCLAMP(左手指松),将手臂上刀柄取下,然后将手臂各动作调整到准备状态,再将EACH OPERATION POSSIBLE改为0退出,按参数设定将任选参数16Bit7改为1,任选参数56Bit7改为0,同时按ATC、互锁解除两键将ATC灯熄灭。
这时就可按常规检查刀具未拔出是油压低还是刀柄拉钉、或是刀柄、松刀液压缸引起。
本例中经查发现油压偏低,将液压泵压力略调高0.2MPa后故障排除。
调试正常后再将610号参数恢复到原来状态,找到方式转换画面,将方式设定为通常状况,断电开机后系统正常起动。
例463.刀具设置错误报警的故障维修故障现象:一台配套OKUMA OSP700系统,型号为XHAD765的数控机床,换班后,操作工设置刀具表时,显示“2714刀具数据设定出错”报警。
数控机床整机调试与维护
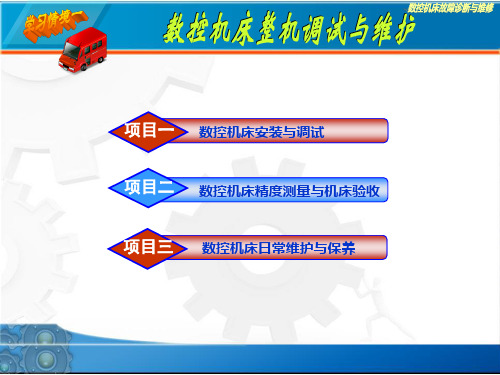
任务一 数控车床外观检查
三、伺服电动机的外观检查
对伺服电动机尤其是对带有 脉冲编码器的伺服电动机的外壳 应作认真检查,特别是后端盖处 。如发现有磕碰现象,应将电动 机后盖打开,取下脉冲编码器外壳 ,检查光码盘是否碎裂。
任务一 数控车床外观检查
四、接通数控柜电源;检查各输出电压
方法
(1)在接通电源之前,为了确保安全,可先将电动机动力线断开,这样 在系统工作时不会引起机床运动。但是应根据维修说明书的介绍对速度 控制单元作一些必要的设定,不致因断开电动机动力线而造成报警。
(3)
基础隔震
4.数控机床开箱和机床零部件的保管
1机床开箱
设备运抵现场后,将设备的包装箱 打开,以备检查和安装,这道工序称为 设备开箱。根据设备的大小和运输条件 ,有的是整体装箱,有的是分散(解体 )装箱,个别大型设备不装箱。设备开 箱时,应尽量做到不损伤设备和不 丢失附件;尽可能减少箱板(或 包装箱)的损失。
(2)
变压器的输入/ 输出电压检查。
开关电源的输入/输出 检查。测开关电源前 ,将开关电源的输出
线拆掉。
任务二 加工中心的调试
4.I/O检查
(1)PLC的输
入/输出检查。
(2)PLC的
输入/输出检查。
二、机电联调
任务二 加工中心的调试
方法
(1)先在JOG方式下,进行各坐标轴正反向点动操作,待动作正确 无误后,再在AUTO方式下试运行简单程序。
三、加工中心精度和功能调试的基本内容
1 精调床身
水平面精度
2 调整刀具交换装置与
检查附件或附属
5 装置的功能
4 检查、试验数
控功能
3
调整交换工作台
大中型数控机床安装调试和验收的详细步骤与方法
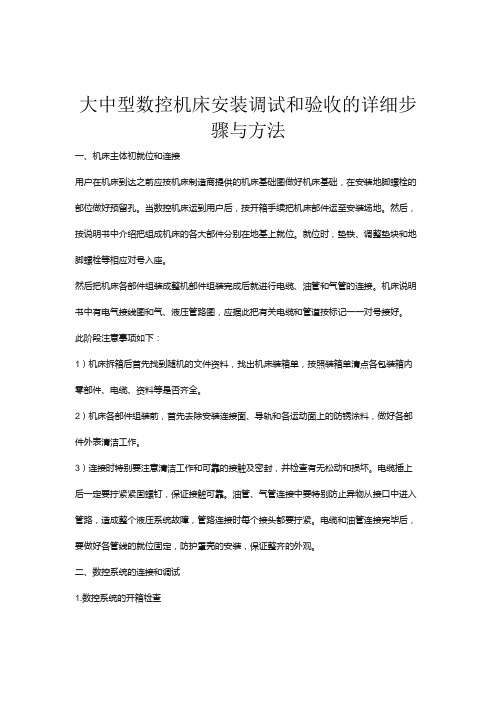
大中型数控机床安装调试和验收的详细步骤与方法一、机床主体初就位和连接用户在机床到达之前应按机床制造商提供的机床基础图做好机床基础,在安装地脚螺栓的部位做好预留孔。
当数控机床运到用户后,按开箱手续把机床部件运至安装场地。
然后,按说明书中介绍把组成机床的各大部件分别在地基上就位。
就位时,垫铁、调整垫块和地脚螺栓等相应对号入座。
然后把机床各部件组装成整机部件组装完成后就进行电缆、油管和气管的连接。
机床说明书中有电气接线图和气、液压管路图,应据此把有关电缆和管道按标记一一对号接好。
此阶段注意事项如下:1)机床拆箱后首先找到随机的文件资料,找出机床装箱单,按照装箱单清点各包装箱内零部件、电缆、资料等是否齐全。
2)机床各部件组装前,首先去除安装连接面、导轨和各运动面上的防锈涂料,做好各部件外表清洁工作。
3)连接时特别要注意清洁工作和可靠的接触及密封,并检查有无松动和损坏。
电缆插上后一定要拧紧紧固螺钉,保证接触可靠。
油管、气管连接中要特别防止异物从接口中进入管路,造成整个液压系统故障,管路连接时每个接头都要拧紧。
电缆和油管连接完毕后,要做好各管线的就位固定,防护罩壳的安装,保证整齐的外观。
二、数控系统的连接和调试1.数控系统的开箱检查无论是单个购入的数控系统还是与机床配套整机购入的数控系统,到货开箱后都应进行仔细检查。
检查包括系统本体和与之配套的进给速度控制单元和伺服电动机、主轴控制单元和主轴电动机。
2.外部电缆的连接外部电缆连接是指数控装置与外部MDI/CRT单元、强电柜、机床操作面板、进给伺服电动机动力线与反馈线、主轴电动机动力线与反馈信号线的连接及与手摇脉冲发生器等的连接。
应使这些符合随机提供的连接手册的规定。
最后还应进行地线连接。
3.数控系统电源线的连接应在切断数控柜电源开关的情况下连接数控柜电源变压器原边的输入电缆。
4.设定的确认数控系统内的印刷线路板上有许多用跨接线短路的设定点,需要对其适当设定以适应各种型号机床的不同要求。
数控机床调试步骤要求
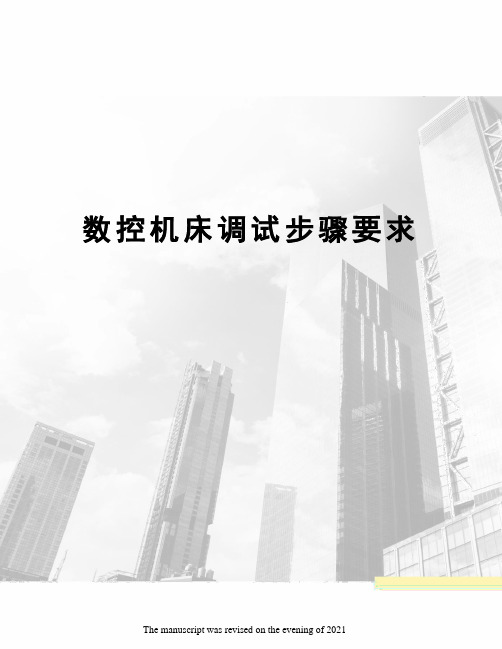
数控机床调试步骤要求 The manuscript was revised on the evening of 2021数控机床调试步骤要求(一)安装调试的前期准备工作:用户的准备事项,由售后服务人员联系落实。
(1)立式加工中心1.机床的吊运与安装:包括机床的吊运、开箱、安装、粗调水平、防锈油的清洗。
其中安装可采用混凝土地基加地脚螺钉固定机床,或直接使用随机的调整垫铁加地脚螺钉固定机床。
2.根据机床型号的不同确定外接电源线的线径,以下为各种型号机床参考线径:CY-VMC650采用10平方毫米左右线径。
CY-VMC850采用16平方毫米左右线径。
CY-VMC1060/1270/1370采用25平方毫米左右线径。
CY-VMC1580/1690/1890采用35平方毫米左右线径。
所有机床必须可靠接地。
3.安装调试前用户需购买以下备件物品:空压机,要求排量在立方米/分钟以上。
连接空压机至机床的PTV气管,外径为12毫米。
标准刀柄和拉钉:CY-VMC650/850/1060采用型号为BT-40刀柄和45°拉钉;CY-VMC1270/1370/1580采用型号为BT-50刀柄和45°拉钉。
刀具的购买:根据用户加工零件的实际情况,来确定购买不同夹持方式的刀柄和刀具,比如:铣平面用的盘铣刀柄和直径为Ф63、Ф80、Ф100不等的盘铣刀体及刀片。
强力铣夹头刀柄,主要方便于夹持直径较大的外圆铣刀和球头铣刀,例如夹持Ф20毫米的球头铣刀。
弹簧夹头刀柄,主要方便于夹持小直径外圆铣刀和球头铣刀,例如夹持Ф3~Ф16毫米的外圆铣刀。
常用的刀柄规格型号为Ф32型刀柄。
一体式或分离式钻夹头刀柄,主要用于装夹直柄小直径钻头,常见刀柄规格型号为Ф3~Ф13毫米的钻夹头。
带扁尾莫氏锥孔刀柄,主要用于装夹锥柄钻头。
常用的刀柄规格型号是3号和4号莫氏锥孔刀柄。
不带扁尾莫氏锥孔刀柄,主要用于装夹锥柄外圆铣刀。
常用的刀柄规格型号是3号和4号莫氏锥孔刀柄。
车床和铣床常用操作步骤-

数控铣床1、打开“on”机床——开气泵(0.6Mpa以上)2、开机后,旋钮“ZRN原点复归”档,在主界面上按“+Z”,等刀具回到零位,再选择“+X”“+Y”,使工作台回到原位。
3、旋钮“MDI”,选择显示屏“手动mst”——直接在主轴转速栏输入“ 1200”——input————按主界面“主轴正转”或“主轴反转”启动主轴运动,用手轮可以控制轴沿x、y、z轴移动,上为+z,左为+x,前为+y。
100档:转1圈移动1cm;10档:转1圈移动1mm;1档:转1圈移动0.1mm。
4、快速对刀:按旋钮“MPG手轮”,按钮“set up”,选择W测定——宽度测量,移动x轴,左边碰一下,——按下取得临界值,再次移动x轴,然后右边碰一下,——取得临界值——选择坐标系(G54)——写入坐标系,自动对刀x轴中点。
Y轴同样。
Z轴直接把刀移到工件表面刚接触处,按两次取得临界值,然后写入坐标系。
5、选择刀号:旋钮“EDIT编辑”,按界面“monitor”打开程序——按input,输入语句,如果要换刀,输入M06 T06,第6把刀。
换刀:旋钮“MPG手轮”——把刀装入主轴,按下主轴上绿色按钮。
刀号在红色显示框中,刀库号——主轴刀号,当到装入时,记住此时的“主轴刀号”,不管刀库怎么变,都可以通过M06 T**指定找到它。
,6、单句程序执行:旋钮“AUTO自动”,按界面“SBK单段执行”,按“程序启动”绿色按钮执行程序。
7、新建程序:旋钮“edit”——按钮Edit——显示屏上打开或者新建——直接输入程序名,注意:9000以上的名字不能新建,为保护区域。
8、设置安全平面,在坐标系下——EXT中——可在Z轴输入一个正值(如200),让整个程序提高一个200mm高度运行。
9、显示屏上选择轨迹——跟踪——程序启动时可以观察轨迹。
10、程序,G90 绝对坐标(默认对刀的0点为原点坐标),G91相对坐标,相对上一条指令的位置坐标11、catia中的程序选择fanuc0系统导出,如果有多个加工流程,需要选择all program,把所有程序存入一个代码中,在存入数控铣床前,需要对程序进行简单的处理:1)程序的第一句改成,N1 G0 G90 ,然后把前面的所有语句删除,保留程序编号。
数控机床手动换刀控制线路的安装与调试

项目三任务三视 频1:数控机床 手动换刀操作演 示
项目三任务三视 频2:数控机床 自动换刀操作演 示
03 数控机床手动换刀控制线路的安装与调试 3.认识新功能指令
(1)前沿检测DIFU(SUB57) 读取输入信号的前沿,扫到1后,输出即为“1”,见图3-3-4所示。
图3-3-4 前沿检测DIFU(SUB57)指令
(前沿号)1~256,指定进行前沿检测的作业区号,其它前沿/后沿检测和号重复时, 就不能进行正确检测,使用示例见图3-3-5所示:
图3-3-5 前沿检测DIFU(SUB57)示例
03 数控机床手动换刀控制线路的安装与调试 3.认识新功能指令
(2)后沿检测DIFD(SUB58) 读取输入信号的后沿,扫到1后,输出即为“1”,见图3-3-6所示。
完成数控机床四工位刀架手动控制线路的安装与调试。
图3-3-12 刀架主电路及控制电路
图3-3-13 刀架电路PMC输入输出电路
03 数控机床手动换刀控制线路的安装与调试
【任务时实施】
1.安装与调试线路 2.编写与调试PMC程序 (1)I/O分配表
序号 PMC地址
1
X0.2
2
X3.0
3
X3.1
4
X3.2
1)无源接近开关 2)涡流式接近开关 3)电容式接近开关 4)霍尔接近开关 5)光电式接近开关 6)热释电式接近开关 7)其它型式的接近开关
图3-3-1 接近开关实物图
03 数控机床手动换刀控制线路的安装与调试 【任务准备】 1.认识接近开关
(2)三线制接近开关的接线 依据接近开关的线数,有两线制与三线制。两线制接近开关与行程开关一样
1.自动换刀方式下的数据处理过程 数控车床在进行自动换刀时,动作与手动换刀时基本相同,但控制流程却相差 很大,其数据处理流程如图3-3-16所示。
GSK980TC3简易调试手册(第二版)

GSK980TC3机床调试简易说明一、修改各类型参数步骤二、机床调试步骤常用参数快捷调试常用参数界面将系统的参数进行功能的分类,选择对应的模块,进入参数界面,将相应的参数修改。
参数修改步骤:(1) CNC设置界面,打开参数开关。
(2) 输入机床厂家密码(原始密码:111111)A :机床上电后,查看并消除系统各类报警:1、急停报警:系统急停信号为常闭触点,当急停信号状态为0时将出现急停报警。
在诊断(X 信号)界面查看信号X9.4(外部急停报警)状态;当K6.3=1(使用外接手轮急停),同时要查看信号X11.0(外接手轮急停)状态。
当上述某一信号状态为0时,要检查对应的急停开关是否被按下,对应信号的回路接线是否正确。
假如外接手轮脉冲发生器没有急停开关,可以将K6.3(是否使用外接手轮急停)设置为0。
系统如无需安装急停开关,可将急停信号短接到系统+24V ,或者将位参数N0:61#5(是否忽略急停报警)设置为1。
注意:位参数N0:61#5(是否忽略急停报警)设置为1时,外部急停和外接手轮急停报警都无效。
2、硬限位报警:系统硬限位信号为常闭触点,当信号状态为0时将出现硬限位报警。
根据报警信息,在诊断(X信号)界面查看相应报警轴信号。
X0.0至X0.3为各轴硬限位信号。
若各轴仅使用一个限位开关,则需将PLC参数K6.0修改为1。
配绝对式电机,无硬限位开关时,将位参数N0:61#6(是否忽略硬限位报警)设置为1。
3、驱动器报警通电时,系统若显示X轴、Z轴或主轴驱动单元报警,应先检查对应的驱动单元是否显示报警。
若显示报警,可以根据显示的报警号对应驱动单元说明书找出报警原因,然后进行排除,消除报警。
若驱动器不显示报警,首先确认驱动单元连线是否正确,若连线正确,则系统的报警参数所设定的电平与驱动单元的报警电平不匹配,可以修改位参数NO:19#0 ~ NO:19#4(进给轴报警电平)或者NO:19#5~ NO:19#6(主轴报警电平)。