焦化煤气PDS法脱硫
PDS法煤气脱硫技术的应用情况

曹贵杰(河北迁安中化煤化工有限责任公司)我公司一期建成2座JN60-82型焦炉,年产焦炭110万吨,煤气发生量为5万m3/h,煤气净化采用PDS法脱硫工艺。
二期建设规模相同,并增加2套干熄焦装置,目前正在建设中。
1 PDS法煤气脱硫工艺的特点(1)工艺流程短,催化剂用量少,以焦炉煤气中的氨为碱源,原材料及动力消耗少,硫化氢、氰化氢的脱除效率高。
(2)脱硫塔采用科斯特填料,比表面积大,气液接触好,传质系数高,耐老化,抗腐蚀,设备维护费用低。
(3)脱硫塔前设有预冷塔,可保证进入脱硫塔煤气温度的稳定。
(4)采用耐腐蚀的铸铁泡罩蒸氨塔处理剩余氨水,氨汽直接导入脱硫塔前的煤气中,补充脱硫所需的氨源。
(5)终冷塔上段为碱液净化段,可进一步脱除煤气中的硫化氢,有效减轻了粗苯装置的腐蚀。
终冷塔净化段排出的碱液送蒸氨塔,以分解氨水中的固定铵盐,从而控制蒸氨废水中的氨氮含量,减轻污水处理装置的负担。
(6)为防止塔底沉积,预冷塔和脱硫塔底都设有排液管。
泡沫泵出口至泡沫槽设有回流管,可随时检查管道堵塞情况。
2 存在问题与改进措施经过1年的运行,我们对出现的问题进行了改进,取得了较好的效果。
(1)原设计脱硫塔煤气进口管的高度与脱硫液出口液封高度只相差200mm,致使脱硫液倒灌,后将脱硫塔出口液封高度降低了300mm,有效避免了脱硫液的倒灌现象。
(2)熔硫釜底部的三通球阀改为带蒸汽夹套的球阀,以防止堵塞。
(3)熔硫釜底放硫管由直角弯管改为倾斜的直管,并用蒸汽夹套保温。
(4)进入再生塔的压缩空气管与蒸汽(氮气)管加阀门连接,以便用蒸汽(氮气)清扫管道。
(5)更换泡沫泵,原设计选用扬程25m、流量25m3/h的泡沫泵,现改为扬程48m、流量3425m3/h 。
(6)为观察清液流出情况,熔硫釜清液管改加漏斗。
(7)在泡沫槽与泡沫泵进口之间加过滤器,防止再生塔防腐层脱落损坏泡沫泵。
3 操作制度(1) pH值。
煤气通过脱硫塔与脱硫液接触时,硫化氢从气相转入液相,进行一级离解、二级离解,最终发生离子反应。
我国焦炉煤气脱硫技术现状
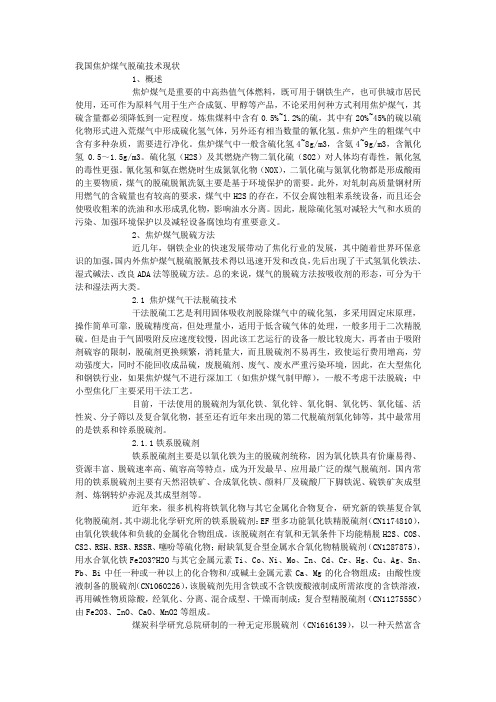
我国焦炉煤气脱硫技术现状1、概述焦炉煤气是重要的中高热值气体燃料,既可用于钢铁生产,也可供城市居民使用,还可作为原料气用于生产合成氨、甲醇等产品,不论采用何种方式利用焦炉煤气,其硫含量都必须降低到一定程度。
炼焦煤料中含有0.5%~l.2%的硫,其中有20%~45%的硫以硫化物形式进入荒煤气中形成硫化氢气体,另外还有相当数量的氰化氢。
焦炉产生的粗煤气中含有多种杂质,需要进行净化。
焦炉煤气中一般含硫化氢4~8g/m3,含氨4~9g/m3,含氰化氢0.5~1.5g/m3。
硫化氢(H2S)及其燃烧产物二氧化硫(SO2)对人体均有毒性,氰化氢的毒性更强。
氰化氢和氨在燃烧时生成氮氧化物(NOX),二氧化硫与氮氧化物都是形成酸雨的主要物质,煤气的脱硫脱氰洗氨主要是基于环境保护的需要。
此外,对轧制高质量钢材所用燃气的含硫量也有较高的要求,煤气中H2S的存在,不仅会腐蚀粗苯系统设备,而且还会使吸收粗苯的洗油和水形成乳化物,影响油水分离。
因此,脱除硫化氢对减轻大气和水质的污染、加强环境保护以及减轻设备腐蚀均有重要意义。
2、焦炉煤气脱硫方法近几年,钢铁企业的快速发展带动了焦化行业的发展,其中随着世界环保意识的加强,国内外焦炉煤气脱硫脱氰技术得以迅速开发和改良,先后出现了干式氢氧化铁法、湿式碱法、改良ADA法等脱硫方法。
总的来说,煤气的脱硫方法按吸收剂的形态,可分为干法和湿法两大类。
2.1 焦炉煤气干法脱硫技术干法脱硫工艺是利用固体吸收剂脱除煤气中的硫化氢,多采用固定床原理,操作简单可靠,脱硫精度高,但处理量小,适用于低含硫气体的处理,一般多用于二次精脱硫。
但是由于气固吸附反应速度较慢,因此该工艺运行的设备一般比较庞大,再者由于吸附剂硫容的限制,脱硫剂更换频繁,消耗量大,而且脱硫剂不易再生,致使运行费用增高,劳动强度大,同时不能回收成品硫,废脱硫剂、废气、废水严重污染环境,因此,在大型焦化和钢铁行业,如果焦炉煤气不进行深加工(如焦炉煤气制甲醇),一般不考虑干法脱硫;中小型焦化厂主要采用干法工艺。
pds法脱硫原理

pds法脱硫原理
PDS法脱硫是一种通过溶液注入的方法来进行脱硫的技术,
具体原理如下:
1. 基本原理:PDS法脱硫是通过将一组特殊配方的氧化剂
(通常是二氧化硫和二氧化氮的混合物)溶解在水中,形成硫酸和硝酸的溶液。
当燃料燃烧产生的二氧化硫遇到这种溶液时,会发生反应生成硫酸,从而将二氧化硫转化为可溶性的硫酸盐。
2. 反应机理:PDS法脱硫的反应机理主要包括以下几个步骤: - SO2吸收:氧化剂溶液中的硫酸和硝酸会与燃烧过程中产
生的SO2发生反应,生成可溶性的硫酸盐(如硫酸钠)。
- 氧化反应:溶液中的氧化剂能够将SO2进一步氧化为硫酸。
- 反应生成物处理:生成的硫酸及其他反应生成物可以通过
各种方法进行处理和回收,用于实现硫酸或其他高价值产品的回收。
3. 设备构成:PDS法脱硫主要包括氧化剂储存和输送系统、
喷射系统、吸收塔、循环液处理系统和反应生成物处理系统等组成。
其中,喷射系统将氧化剂溶液以适量和适速喷入燃烧器中,吸收塔用于与烟气进行接触和反应,循环液处理系统用于处理反应产物和回收和再利用溶液。
总的来说,PDS法脱硫通过氧化剂溶液与燃烧过程中产生的
SO2进行反应,将SO2转化为可溶性的硫酸盐,以达到脱除
燃料中的硫化物的目的。
该方法具有脱硫效率高、适用范围广、
操作简单等优点,被广泛应用于工业燃煤锅炉、电厂和工业排放源的脱硫处理中。
PDS-600脱硫技术在焦炉煤气净化中的应用
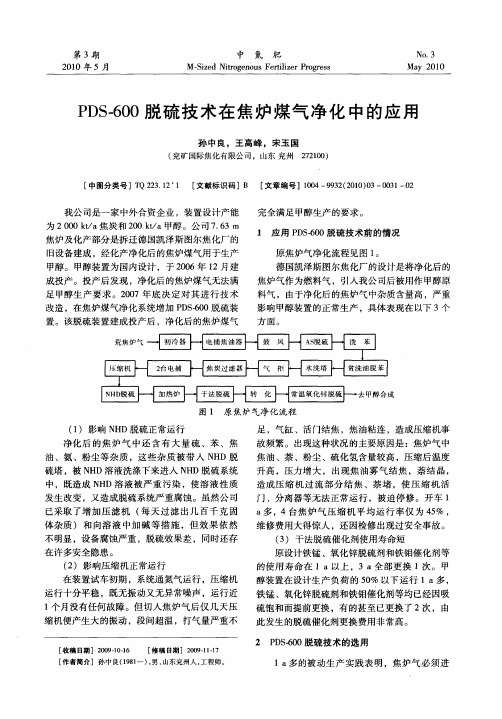
体杂质 )和 向溶液 中加 碱等措施 ,但效果依 然 不 明显 ,设备 腐蚀 严 重 ,脱硫 效果 差 ,同时还存
在许 多 安全 隐患 。
( ) 影 响压缩 机正 常运 行 2
在装 置试 车初 期 ,系 统通 氮气 运行 ,压 缩机
运行十分平稳 ,既无振动又无异常噪声 ,运行近 1 个月没有任何故障。但切人焦炉气后仅几天压
[ 修稿 日期 ]20 -11 0 91 —7
[ 作者简 介]孙 中良(9 1 ) 男 , 18 一 , 山东兖州人 , 工程师 。
1a多 的被 动生 产 实践 表 明 ,焦炉 气 必 须 进
・
3 2・
中 氮 肥
第 3期
行 深度 净化处 理才 能满 足 甲醇 生产 的需要 。我公 司技术 人员对 此进 行 了精 心 的研究 ,并对 国 内多
缩机 便产 生大 的振 动 ,段 间超 温 ,打气 量严 重不
铁锰 、氧化锌脱硫剂和铁钼催化剂等均已经 因吸 硫饱和而提前更换 ,有 的甚至 已更换 了 2 ,由 次
此发 生 的脱硫 催化 剂 更换 费用 非 常高 。
2 P Sl 0脱硫 技 术的 选用 D _0 5
[ 收稿 日期 ]2 0 — .6 0 91 1 0
( 菁钴 法 ) 的不足 ,采 用定 向合 成 技术 ,对具 酞 有 催化 活性 的物质 进行筛选 ,选 出更 具活性 的二 双 核酞菁 钴砜 十磺 酸铵 作 为催 化 剂 。P S60催 D -0
化 剂在脱 硫和 氧化 过程 中均 有催 化作 用 ,具 有用
入 口 H S质 量浓 度
空塔 气速 溶 液总碱 度 gL /)
10 / .0gm
出 口 H S质 量浓 度 ≤2 .0 m / 2 00 gm 07 / . 9m s 3 . ( ・ ) 0 3m / m h 1 3 L ( aC , 量 I5 6~ 2 N O 含 > 液体 喷淋 密度
焦化煤气PDS法脱硫工艺探讨

焦化煤气PDS法脱硫工艺探讨【摘要】未经净化的焦炉煤气中含有多种气体组分,尤其是含有焦油、萘、氰化氢(HCN)、硫化氢及多种结构复杂的有机硫。
不但污染空气,对人体也有较大毒害性。
探讨了PDS脱硫工艺的机理和流程,并作了必要的分析。
【关键词】焦化煤气;PDS脱硫1 PDS的结构特点PDS即为双核酞菁钴磺酸钠,其分子结构为(MPc—PcM)。
在工业脱硫装置上应用PDS法时,已证实对H多液相氧化反应具有极高的催化活性。
从量子化学理论上分析,PDS脱硫催化剂由于贯通于整个分子的大Π电子共扼体系与中心金属离子的可变价性能及酞菁环对中心金属离子不同价态的稳定作用相结合,构成了该脱硫剂特殊的催化性能。
磺化酞菁钴由邻苯二甲酸酐、尿素、氯化钴在钼酸铵催化下反应生成酞菁钴再磺化,亦可在三氯苯溶剂中反应后再磺化而得磺化酞菁钴。
分别产生8种不同构型的化合物。
这些不同的化合产物可与氧形成络合物,但稳定性有所不同:它们分别是:(1)双核酞菁钴六磺酸;(2)单核酞菁钴砜六磺酸;(3)酞菁钴—三磺酸双核酞菁钴砜五磺酸;(4)双核酞菁钴砜十磺酸。
钴原子结合氧原子能越多,说明络合物分子氧化硫离子的能力越强。
双核酞菁钴砜十磺酸铵分子中结合了8个氧,具有最强的催化能力。
所以,高活性乃至超活性的PDS,其有效成分是较多的双核酞菁钴砜十磺酸铵、酞菁钴—三磺酸双核酞菁钴砜五磺酸、双核酞菁钴砜六磺酸铵,而少含不与氧形成稳定络合物的单核酞菁钴砜六磺酸铵。
2 PDS催化脱硫机理研究表明,对同一金属离子来说,其双核酞菁化合物比单核酞菁化合物具有更高的活性。
在其催化反应中,催化剂与反应物系(HS-O2等)间的纵向电子转移是同等的,而催化剂分子的电子横向转移却有区别。
单核金属酞菁化合物间只能通过溶剂分子搭桥形成结构较松散的超分子体系,才能实现中心金属离子间的电子转移,而在双核金属酞菁化合物分子中却可以通过其遍布整个分子的大Π电子共轭体系有机地实现。
由此不难发现,PDS脱硫催化剂在催化液相H2S的氧化反应中之所以能快速反应,且表现出极高的催化活性,是由于双核金属酞菁化合物催化下的液相H2S多氧化反应过程为自由基反应。
焦炉煤气DDS脱硫技术(简装)
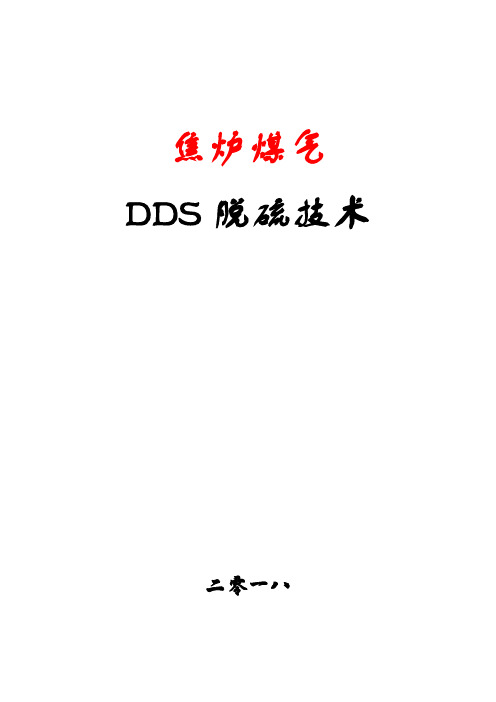
焦炉煤气DDS脱硫技术二零一八焦炉煤气DDS脱硫技术1、DDS脱硫技术简介1.1 概述DDS脱硫技术是“铁-碱溶液催化法煤气脱硫技术”的简称,是一种全新的湿法生物化学脱硫技术,用含DDS脱硫催化剂和亲硫耗氧性耐热耐碱菌及有关辅助材料的碱性溶液吸收煤气中的无机硫、有机硫、HCN和极少量的CO2,进行脱硫。
其脱硫原理和概念与传统的湿法脱硫技术有所不同。
1.2 DDS脱硫反应原理DDS脱硫剂是模仿人体正常血红蛋白的载氧性能研制出来的脱硫催化剂,它是含有铁的有机络合物的多聚合物。
DDS催化剂既能脱除无机硫又能脱除少量有机硫。
同时在吸收过程中会产生一些不溶性铁盐沉淀,好氧菌在DDS络合铁配体的协助下可以将这些不溶性铁盐瓦解,使之以活性铁离子的形式返回溶液中,保证溶液中各种形态铁离子的稳定存在。
DDS脱硫液在酚类物质与铁离子的共同催化下,用空气氧化再生,副产硫膏,再生DDS脱硫液循环使用。
其反应过程可归纳为:吸收反应、再生反应、生物降解反应。
1)吸收反应可以简单归结如下为五类反应:(1) H2S、CO2与碱及铁离子的反应。
(2) CS2、COS的水解反应。
(3) R-SH、 SH 与铁离子的反应。
(4) SO2与H2S的氧化还原反应。
(5) 少量铁离子在碱性溶液中的降解反应。
2)再生反应可以简单归结为如下三类反应:(1) NaHCO3与Na2CO3的转换过程(2) Fe3+氧化溶液中的S2-及HS-离子自身被还原为Fe2+,Fe2+再被空气中的氧及醌类物质氧化为Fe3+的反应。
(3) 醌氧化溶液中的S2-、HS-及Fe2+离子自身被还原为酚,酚再被氧化为醌的酚醌转换的过程。
3)生物降解过程的降解反应可以简单归结为如下三类反应:(1) 细菌与不溶性铁盐[Fe(OH)2、FeCO3、FeO、FeS]结合并返回到溶液中。
(2) 在DDS配体作用下瓦解不溶性铁,重新结合为DDS铁的形式。
(3) 载氧菌氧化溶液中的S2-及HS-离子。
PDS法焦炉煤气脱硫工艺分析

返回
工艺原理:
总反应方程式 2H2S + O2 → 2S + 2H2O 这方程式是整个脱硫的目的和整体过程,也是经常被大多数人忽略的一个反应方程 式,总方程式决定了总体思维模式。 3.2脱硫原理 对于无机硫: H2S+Na2CO3 → NaHS + NaHCO3 这是典型的复分解反应,也是酸碱中和反应,无须任何催化剂,即使加入催化剂, 也不能影响到反应平衡。 对于有机硫: RSH + Na2CO3 → RSNa + NaHCO3 虽然有机硫的平衡常数比无机硫小,但酸碱中和的推动力,能够使反应进行的深度 也很高。 3.3再生原理 对于无机硫: NaHS + 1/2 O2 → S + NaOH 对于有机硫: 2RSNa + 1/2 O2+ H2O → RSSR + 2NaOH
返回
工艺流程图:
返回
工艺分析:
PDS脱硫工艺是以酞菁钴磺酸盐系化合物的混合物为催化 剂的湿式氧化法脱硫工艺,其工艺过程与HPF工艺类同。 最初使用的PDS是双核酞菁钴六磺酸铵,后改进到二双核 酞菁钴砜+磺酸铵,其活性比原PDS提高一倍。PDS法硫 容量可大于0.5g/L,不发生堵塞,副产品盐类增长速度缓 慢,脱硫率大于97%,脱氰率大于95%,有机硫的脱除率 大于40%,PDS结合栲胶法可以达到更好的脱硫效果,该 工艺的缺点是产生大量废液不好处理,目前独立焦化厂使 用此工艺的较多。
PDS法焦炉煤气脱硫工艺分析
应化3141 张斌
关键词:焦炉煤气;PDS脱硫
人机化 含含 体硫氢 有有 也。及 焦多 未 有不多 油种 经 较但种 气 净 大污结 萘体 化 毒染构 氰组 的 害空复 化分 焦 性气杂 氢, 炉 。,的 ,尤 煤 对有 硫其 气 中
煤气站PDS湿式脱硫系统

煤气站 PDS+栲胶法湿式脱硫系统操 作规程一、概述: 1、任务:经一次加压机加压后的煤气进入脱硫塔下部与塔内喷淋而 下的脱硫液逆流接触, 煤气中 H2S 和 CO2 等酸性气体被吸收, 脱除 H2S 后的净煤气从塔顶经丝网除沫器分离夹带的液沫后, 送出脱硫工段供 用户使用。
2、原理: 经一次加压机加压后温度为 30~40℃的煤气依次进入 2 台并联 的脱硫塔底部,与塔顶喷淋的脱硫液逆向接触,脱除煤气中的大部分 H2S,其基本反应为: H2S(气)←→H2S(液) Na2CO3+2H2S → NaHS+NaHCO3 在 PDS 催化剂的作用下, 可脱除无机硫与有机硫, 同时促使 NaHCO3 进一步参加反应: NaHS+NaHCO3+(x-1)S ←→Na2Sx+CO2+H2O PDS 特有的催化氧化(再生)作用: Na2Sx+1/2O2+H2O ←→ 2NaOH+xS↓ NaHS+1/2O2 ←→ NaOH+S↓ 脱硫液吸收 H2S 的过程还伴随以下副反应: 2NaHS+2O2 → Na2S2O3+H2O2HCN+Na2CO3 → 2NaCN+CO2+H2O NaCN+S → NaCNS二、工艺流程: 一次加压机 捕滴器 脱硫塔 脱硫煤气低压主管富液池硫沫槽再生槽厢压机贫液槽软化水硫活化槽脱硫剂 蒸汽2.1煤气系统: 煤气系统:经加压机加压后的煤气进入脱硫塔下部与塔内喷淋而下的脱硫 液逆流接触, 煤气中 H2S 和 CO2 等酸性气体被吸收, 脱除 H2S 后的净煤气从 塔顶经丝网除沫器分离夹带的液沫后,送出脱硫工段供用户使用。
2.2溶液、空气系统: 溶液、空气系统:吸收 H2S 后富液从塔底出来,流入富液槽,用富液泵将 富液打入自吸空气喷射器,空气被自吸进入喷射器与富液一起喷入再生槽。
在再生槽内,溶液经空气氧化后得到再生。
再生后的空气及废气从塔顶放散, 再生后贫液在再生槽扩大部分与硫泡沫分层分离后, 经液位调节器调节位差, 自流入贫液槽,进入循环系统参与脱硫。
PDS脱硫技术在煤气净化中的应用

PDS脱硫技术在煤气净化中的应用我公司(原常州煤气厂)成建于1994年,拥有两座CM-2806型焦炉,年产焦炭25万吨。
脱硫工艺最初于1995年使用对苯二酚为催化剂,因生成的硫磺颗粒细不易提取,脱硫效率不高,于1997年又添加另一种催化剂OMC,使用两种混合催化剂改变了硫磺的粒度,脱硫效率有了大幅度提高,从而有利于工业的生产。
2003年我公司改用PDS法代替OMC法脱硫,经过三年多的生产实践表明,PDS法脱硫效果好,具有高效、节能、环保等优点,是国内中小焦化厂较佳的工艺选择。
1.脱硫工艺流程我公司原为OMC法脱硫,日处理煤气28万Nm3煤气。
主要设备为脱硫塔ø2612×32200mm三台,填料为轻瓷,再生塔ø2612×41780mm三台,其工艺流程简单、易操作,如图1所示。
鉴于目前公司焦炉不再供应城市煤气(2005年5月我公司不再供应城市煤气,改脱硫效率指标≥90%),故只开2#、3#脱硫系统,1#脱硫系统再生塔待修备用。
图1 PDS法脱硫工艺流程1—脱硫塔;2-液位调节器;3-再生塔;4-泡沫中间槽;5-反冲罐;6-戈尔过滤器;7-硫泡沫泵;8-地下槽;9-反应槽;10-循环泵来自鼓冷工段煤气进入脱硫塔,与塔顶喷淋下来的脱硫液逆向接触,煤气中的H2S、HCN被吸收后煤气从塔顶排出,富液自流到反应槽经循环泵去再生塔氧化再生,浮选出来的硫泡沫自流进入硫泡沫槽,再生的贫液经液面调节器流至脱硫塔顶循环使用。
硫泡沫由泡沫中间槽经硫泡沫泵送至戈尔过滤器,过滤后的清液流至反应槽,硫膏直接装袋。
过滤器反冲、放空的溶液进入泡沫中间槽,过滤挤干器后的溶液流入地下槽。
2.PDS脱硫工艺特点PDS法是东北师范大学近年来开发的一种新型双核酞箐钴磺酸盐脱硫催化剂,可同时高效、快速脱除高硫煤气中的H2S、HCN和有机硫,在相应的介质中,有机硫脱除率在50%以上。
脱硫过程中利用煤气自身的氨为碱源,在PDS的催化作用下,使煤气中的H2S转化为硫磺,HCN分解为NH3和CO2。
焦炉煤气脱硫技术路线

焦炉煤气脱硫技术路线、现状及五种工艺对比焦炉煤气中的硫化物是一种有害物质,若不对其进行脱除,不仅会腐蚀生产设备,而且会带来环境污染,因此焦炉煤气在使用前必须进行脱硫处理。
本文对目前国内应用较多的焦炉煤气脱硫技术方案进行介绍,包括PDS法、HPF法、改良ADA法等。
通过对这些脱硫工艺在脱硫效果、碱源、成本等方面进行比较,发现PDS法和HPF法因其脱硫效率高、不需要外加碱源、生产流程简洁,被大多数企业所青睐,综合效益最佳。
引言煤在炼焦生产时一般72%~78%转化为焦炭,22%~28%转化为荒煤气,干煤中含有质量分数为0.5%~1.2%的硫,其中有20%~30%的硫转到荒煤气中,形成有机和无机硫化物。
而焦炉煤气中,硫化氢的含硫量占总含硫量的90%以上。
焦炉煤气中的硫化氢是一种有害物质,它会对化学产品回收设备和煤气输送管道产生腐蚀。
硫化氢含量高的焦炉煤气用于炼钢,会导致钢的质量下降; 用于合成氨生产,会导致催化剂中毒失效和管道设备等腐蚀;用于工业和民用燃料,其燃烧所排放废气中的硫化物会污染环境,对人体健康造成危害。
因此,焦炉煤气不论是用作工业原料还是城市燃气都需要对其进行脱硫净化。
煤气脱硫不仅可以改善煤气质量,减轻设备腐蚀,还可以提高经济效益。
本文对目前企业中常用的焦炉煤气脱硫方法进行分类介绍,主要对常用的一些湿式氧化脱硫法,包括PDS法、HPF法、改良ADA法等进行分析对比,说明各种工艺的优缺点。
1 焦炉煤气脱硫方法焦炉煤气脱硫工艺发展至今已经有50余种。
虽然工艺数量众多,但是根据反应的接触条件以及催化剂的种类的不同,总体上可以分为两大类: 一类是干法脱硫; 另一类是湿法脱硫。
1.1 干法脱硫干法脱硫是利用固体吸附剂,例如活性炭、氢氧化铁等脱除煤气中的硫化氢,使煤气中硫化氢的含量达到1~2mg/m3。
该工艺在脱硫反应中无液体存在,脱硫环境完全干燥。
一般适用于量不大的煤气脱硫或者精度要求较高的焦炉煤气二次脱硫( 即为在一次脱硫的基础上根据煤气的使用需要来进行第二次精脱硫)。
焦炉煤气脱硫净化的概述

焦炉煤气脱硫净化的概述摘要:在焦化厂生产中,焦炉煤气中所含的硫化氢及氰化氢是有害的杂质,它们腐蚀化产回收设备及煤气储存输送设施,还会污染厂区环境。
用此种煤气炼钢、轧钢加热,会降低钢材产品的质量,腐蚀加热设备;用作城市燃气,硫化氢及燃烧生产的二氧化硫、氰化氢及其燃烧生成的氮氧化物均有毒,会严重影响环境卫生。
所以焦炉煤气中的硫化氢和氰化氢应予清除,本文介绍了利用焦炉副产品焦炉煤气,经过湿法脱硫成为硫化氢含量较低的净化煤气的工艺及特点,为两台燃气发电机组提供合格(H2S≤0.7ppm)的煤气,同时为甲醇、锅炉发电、焦化分厂提供合格(H2S≤13ppm)的煤气,并对此工艺进行了评价,提出了建议。
关键词:焦炉煤气;湿法脱硫;硫化氢焦炉煤气脱硫方法分为:干法脱硫和湿法脱硫,干法脱硫是一种古老的煤气脱硫方法。
这种方法的工艺和设备简单,操作和维修比较容易。
但该法为间歇操作,占地面积大,脱硫剂的更换和再生工作的劳动强度较大,现代化的大型焦化厂已不再采用。
焦化净化煤气脱硫一般采用湿法脱硫:湿法脱硫又分为吸收法和氧化法,氧化法脱硫是对吸收法脱硫的改进和完善,是脱硫工艺更流畅,脱硫效果进一步提高。
脱硫工序包含循环水站、煤气预处理、气柜、罗茨风机、湿法脱硫、熔硫釜、脱油塔、精脱硫塔、VOC设施。
主要负责煤气的脱油脱萘、储存、提压和脱除无机硫,使湿法脱硫出口煤气中H2S≤13ppm后,一部分煤气送往压缩工序,另一部分煤气送甲醇、锅炉发电、焦化分厂生产使用。
同时熔硫釜产出硫磺模块。
压缩工序由三台往复式焦炉气压缩机及附属设备组成。
其任务是将湿法脱硫后的煤气通过四级压缩加压到4.15MPa,然后经脱油塔脱除含油下液、精脱硫塔脱除煤气中H2S,经外管送往燃气发电机组。
焦炉煤气经过提压后进入湿法脱硫塔,与脱硫贫液逆向接触,在PDS脱硫催化剂的作用下,利用碱性水溶液中的碱性化合物Na2CO3与硫化物H2S、COS等进行反应生成不稳定的中间硫化物,再利用空气和生成的中间硫化物反应生成单质硫和碱性物,将单质硫进行分离,使脱硫液再生,从而达到脱除H2S等硫化物并使脱硫液再生循环使用目的。
PDS脱硫工艺的应用与改造

燃 料 与 化 工 F e &C e cl rc se u l hmia Poess
6l
P 脱 硫 工 艺 的应 用 与 改 造 DS
孙益民 ( 山西 中煤 焦化 九鑫 公 司 ,晋 中 0 10 ) 3 3 7
氨法 一 D P S脱 硫 脱 氰 工 艺是 中冶 焦 耐 设计 的湿 法 氰 化 脱 硫 脱 氰 工 艺 。我 厂 煤 气 处 理 量 为 1 l x0 m / ,2套 5 14 / 3 h x 0m3 h的 P S法脱 硫 装 置并 联 操 作 , D
84 ̄8 8。 . .
究 后 ,将 熟 硫 工 艺 改 为 生硫 工 艺 ,增 加 2台 压 滤 机 ,硫 泡 沫在恒 温 状态 下进 行分 离得 到 硫膏 。 为 防 止 硫 膏 积 累 .从 脱 硫 泵 出 口引 出 1根 D 5 N 0管道 ,在扩 大 部 分增 加 l圈 喷淋 管 ,定 期 喷 洒 ,减少 硫 膏在再 生塔 扩大 部 分积 累 。 改造 后 ,节省 了熔 硫用 蒸 汽 .生 硫 工艺 的清 液
见 S为催 化 剂 ,利用 压 D 缩 空 气使 催化 剂发 生 液相催 化 氧化 反应再 生 .从 而 脱 除煤 气 中的 H S 目前 塔后 H S含 量 在 2 0 / z, 2 0 mg m
以下 。
预
脱
广 _] —L J _
上
14 蒸 氨 系统 改 造 .
原工 艺采 用熔 硫 釜生产 硫磺 ,环 境 恶劣 ,极 易
堵塞 管道 ,造 成脱 硫 系统无 法正 常运 行 。经分 析 研
在 进 预冷 塔 氨气 管路 上 引 出一 分 支 ,新 增加 1 台换 热 器 ,将氨 气冷 凝 为液态 氨 后补 入反 应槽 ,保 证 脱硫 液 中 的浓 度 大 于 8/ gL,此 时 ,最 佳 p H值 为
PDS法煤气脱硫工艺的影响因素

燃 料 与 化 工 #$%& ’ ()%*+,-& ./0,%11%1
!"
!"# 法煤气脱硫工艺的影响因素
李万众 王先平 5 湘潭钢铁集团公司焦化厂 6 湘潭 !77733 8 我厂现有 ! 座焦炉,煤气发生量为 "9 3 : "9 " 万 * ; )。曾采用 <=< 法脱硫脱氰工艺t; 年改用 .=? 法。煤气脱硫装置设在 粗苯工段的煤气终冷洗萘塔后 6 进入脱硫塔底部的 煤气 温度为 43 : !3@ 6 与 塔顶喷 洒的 贫液逆 流接 触。脱硫塔底的富液经液封进入反应槽 6 用循环泵 抽出,经加热器后送入再生塔进行再生和浮选硫泡 沫。再生贫液经液位调节器返回脱硫塔。硫泡沫经 硫泡沫槽进入真空转鼓式过滤机,滤液回反应槽, 滤饼经熔硫釜处理 6 硫磺经中间槽放入冷却盘。 自 2334 年 A 月 以 来, 即 使 液 气 比 仅 39 37 : 39 7" 的条件下,脱硫效率也 B >3C ,脱硫液中副盐 浓度 D 2"3E ; F,且增长速度缓慢。现将控制脱硫工 艺影响因素的经验简述如下。 5 7 8 .=? 的中毒。市售 .=? 的主要成分是酞菁 钴磺酸盐,煤气中的焦油雾、萘及苯族烃等物质易 引起 .=? 中毒。当脱硫装置设在电捕焦油器后、 饱和器前时 6 硫泡沫呈现暗黄色,泡沫颗粒小,常 以悬浮硫的形式存在于脱硫液中,很难收集到硫泡 沫。当脱硫装置设在洗苯塔后时 6 循环洗油和贫油 的杂质易使 .=? 中毒 6 并会明显降低 .=? 的吸光 度。我厂为减少洗苯贫油的杂质量,将一台洗苯塔 作为捕雾器,取得了明显效果。 5 2 8 脱硫液中副盐的增长。原来 6 脱硫液中 G-2?2 H4 和 G-?(G 两项副盐的总浓度就超过 I33 E ; F,且增长非常快 6 致使 G-2 (H4 消耗居高不下。虽 然 6 这些副盐不会造成 .=? 的中毒,但随着碱度 的降低, JK 值下降较快,使脱硫效率明显降低。 另外 6 由于焦炉煤气中的 (H2 与 G-2 (H4 反应 生成 G-K(H4 。因 G-K(H4 的溶解度比 G-2 (H4 小得 多,当 JK L M : > 时 6 G-K(H4 就会晶体析出。当 脱硫塔中吸收的 (H2 与再生塔中解吸的 (H2 达到 平衡时,溶液中的 G-2 (H4 与 G-K(H4 当量比可达 到最佳值 5 7N 4 8 。在吸收过程中,虽然提高溶液的 碱度有利于 K2 ? 的吸收,但为控制副反应的速度和
PDS脱硫剂在煤气脱硫工艺中的应用效果
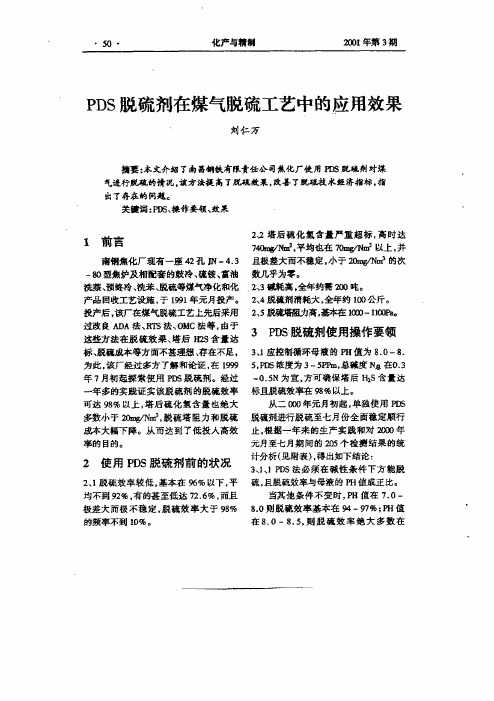
·50·化产与精制2001年第3期PDS脱硫剂在煤气脱硫工艺中的应用效果刘仁万籀要:本文介绍了南昌钢铁有限责任公司焦化厂使用PDS脱硫剂对珠气进行腻的情况,谊方法提高了脱硫效果,改善了脱琉技术经济描标,指出了存在的峨题。
关键词:PDS、操作要领、效果1前言南镪焦化厂现有一座42孔JN一4.3—80型焦炉及相配套的鼓冷、硫铵、富油洗萘、预终冷、洗苯、脱硫等煤气净化和化产品回收工艺设施。
于1991年元月投产。
投产后,该厂在煤气脱硫工艺E先I舌采用过改良ADA法、RTS法、OMC法等。
由于这些方法在脱碗毅果、塔后H2S含量达标、脱硫成本等方面不甚理想、存在不足,为此.该厂经过多方了解和论证,在1999年7月初起探索使用PDS脱硪剂。
经过一年多的实践证实该脱硫剂的脱硫效率可达98%以上,塔后硫化氢含量也绝大多数小于∞噬,N辞,脱硫塔阻力和脱硫成本大幅下降。
从而达到了低投入高效率的目的。
2使用PDS脱硫剂前的状况2、1脱硫效率较低,基本在96%以下,平均不到92%,有的甚至低达72.6%,而且极差大而极不稳定,脱硫效率大于98%的频率不到10%。
2,2塔后硫化氧含量严重超标,高时达74噙棚o,平均也在‰E俐甜以上.并且极差大而不稳定,小于20m跏?的次数几乎为零。
2、3碱耗高,全年约器200吨。
2,4脱硫剂消耗大,全年约100公斤。
2、5脱硫塔阻力高,基本在1000—1100Pa。
3PDS脱硫剂使用操作要领3,1应控制循环母液的PH值为8.0—8.5。
PDS浓度为3—5PPm,总碱度N总在0.3—0。
5N为宣,方可确保塔后}12s含量达标且脱硫效率在98%以上。
从二000年元月初起,单独使用PDS脱硫剂进行脱硫至七月份全面稳定顺行止,根据一年来的生产实践辊对2000年元月至七月期间的205个检测结果的统计分析(见附表),得出如下结论:3、1、1PDS法必须在碱性条件下方能脱硫,且脱硫效率与母藏的PH值成正比。
焦炉气制甲醇对PDS湿法脱硫的分析

炉 气 中 的硫 脱 除 干 净 , 到 ≤0 1mgm , 足 转 化 催 化 剂 和 甲 达 .4 / 满
2 P DS法 工 艺 流 程
来 自界 区外 的 焦 炉ห้องสมุดไป่ตู้气 ( :5 90 m / 、 Q 20 N h H S含 量 ≤30 0
m,N H N 含 量  ̄5 0 gN 首 先 进 入 焦 炉 气 压 缩 机 (0 ) e m 、C / 0m/m ) 86
Na s+ z 02+H E 一 DS2N 0 P a OH + s
最主要的毒物 , 首先会使 纯氧转化催化剂活性 降低 ( 转化催化 剂 主要活性成分为 N ) 转化炉 出 口气 中残余 甲烷含 量增 大 , 个 i, 整
装 置 的能 耗 因此 会 增 加 , 会 使 甲醇 合 成 催 化 剂 中毒 失 活 。 因 还 此 , 焦 炉 气 净 化 过 程 中 , 须 将 总 硫 脱 除 到 ≤0 1m / 为 此 在 必 .4 g m ,
K e o ds:c k v n g s;PDS;r g n r t n arv l yw r oeoe a e e e a i i oume o
硫 的各 种 化 合 物 是 烃 类 蒸 汽转 化 催 化 剂 和 甲醇 合 成 催 化 剂
12 .
硫 化 物 的 催 化 氧 化 再 生
Ab ta t s r c :Th rn i l n n l e c a t r fwe l e g s d s ph rz t n s ci n o 0 m i i n tn n H u i e e p cp e a d ifu n e f co s o tfu a e ul e ia i e to f2 l o o s i ab i i o l
焦炉煤气脱硫及硫回收工艺介绍及特点分析

焦炉煤气脱硫及硫回收工艺分析(冶金工业规划研究院)潘登摘要:简述了几种具有代表性的脱硫、脱氰工艺,分析了不同工艺特点。
介绍了常用的几种硫回收工艺,并总结了脱硫工艺组合硫回收工艺的原则和方法,为企业选择焦炉煤气净化工艺提供参考依据。
关键词:焦炉煤气,脱硫,硫回收,工艺分析一.前言炼焦煤在干馏过程中,煤中全硫的20~45%会转到荒煤气中,荒煤气中的硫以有机硫和无机硫两种形态存在,有机硫主要有二硫化碳、噻吩、硫醇等,煤气中95%以上的硫以H2S无机硫形态存在,由于荒煤气中的有机硫含量很少而且在煤气净化洗涤过程中大部分会被除去,因此焦炉煤气的脱硫主要是脱除煤气中的H2S,同时除去同为酸性的HCN。
据生产统计焦炉炼焦生产的荒煤气中H2S 含量为2~15g/m3,HCN含量为1~2.5 g/m3。
荒煤气中H2S在煤气处理和输送过程中,会腐蚀设备和管道危害生产安全,未经脱硫的煤气作为燃料燃烧时,会生成大量SO2,造成严重的大气污染,同时H2S含量较高的焦炉煤气用在冶炼,将严重影响钢材产品质量,制约高附加值优质钢材品种的开发。
出于生产安全,环保要求及煤气有效利用方面考虑,那种五、六十年代老焦化厂采用荒煤气→冷凝鼓风工段→硫铵工段→粗苯工段的无脱硫工段老三段模式与绿色环保的现代生产理念相悖,这样焦炉煤气脱硫已经成为煤气净化不可或缺的重要组成部分。
焦炉煤气脱硫,不但环保,而且还可以回收硫磺及硫酸等化学品,产生一定的经济效益。
在淘汰落后产能以及清洁生产政策下,对煤气脱硫的要求是越来越高,《焦化行业准入条件》已明确要求焦炉煤气必须脱硫,脱硫后煤气作为工业或其它用时H2S含量应不超过250 mg/Nm3,若用作城市煤气,H2S含量应不超过20mg/Nm3。
本文将对焦炉煤气常用脱硫工艺进行介绍,分析不同工艺的特点,同时对硫回收工艺作简要说明。
二.工艺概述近年来,焦炉煤气脱硫技术经不断发展与完善已日益成熟和广泛应用,脱硫产品以生产硫磺和硫酸工艺为主。
焦炉煤气脱硫工艺选择与方案设计

焦炉煤气脱硫工艺选择与方案设计摘要:随着工业化进程的不断加快,煤炭等化石能源的使用量也在不断增加,而煤炭的燃烧会产生大量的二氧化硫等有害气体,对环境和人类健康造成严重的影响。
因此,煤气脱硫技术的研究和应用变得越来越重要。
目前,焦炉煤气脱硫技术已经得到广泛应用,但是不同的脱硫工艺有着不同的优缺点,如何选择合适的脱硫工艺并设计出最优方案,成了研究的重点。
关键词:焦炉煤气;脱硫工艺;方案设计1焦炉煤气脱硫工艺对比分析目前,在实际应用中具有代表性的脱硫工艺包括 A.S 法煤气脱硫工艺、HPF 法脱硫工艺以及碳酸钠+PDS脱硫工艺。
(一)A.S 法煤气脱硫工艺A.S 法煤气脱硫工艺是一种常用的焦炉煤气脱硫技术,其主要原理是利用氨水与二氧化硫反应生成硫酸铵,从而达到脱硫的目的。
主要流程包括:氨水喷淋、反应吸收、过滤分离、再生吸收等步骤:将氨水喷淋到煤气中,与二氧化硫发生反应,生成硫酸铵;将含有硫酸铵的煤气进入吸收塔中,与吸收液进行反应吸收,使二氧化硫被吸收;将吸收液中的硫酸铵和水分离出来,得到含有硫酸铵的液体;将含有硫酸铵的液体进入再生塔中,通过加热和通入空气的方式,使硫酸铵分解为二氧化硫和氨水,再次用于煤气脱硫。
A.S 法煤气脱硫工艺能够将煤气中的二氧化硫脱除率达到90%以上,脱硫效率高。
该工艺适用于各种煤气,包括高温、高湿、高硫等煤气,具有很好的适应性。
且操作简单,设备投资和运行成本低,易于维护和管理。
同时不会产生二次污染,对环境友好,同时也能够回收利用氨水和硫酸铵,节约能源和资源。
(二)HPF 法脱硫工艺HPF法脱硫工艺是一种高效的焦炉煤气脱硫技术,其全称为高压喷雾吸收法该工艺主要通过高压喷雾将煤气中的SO2与水溶液中的氢氧化钠反应生成硫酸钠,从而达到脱硫的目的。
HPF法脱硫工艺的优点在于其脱硫效率高、操作简单、设备投资少、运行费用低等方面。
同时,该工艺对煤气中的其他污染物也具有一定的去除效果,如NOx、HC l等。
焦化煤气PDS法脱硫

煤气中的硫绝大部分以H2S的形式存在,而H2S随煤气燃烧后转化成SO2,空气中SO2含量超标会形成局域性酸雨,危害人们的生存环境,我国对燃烧发生炉煤气炉窑规定其SO2的最高排放浓度为900mg/m3;另一方面,SO2对诸如陶瓷、高岭土等行业的最终产品质量影响较大,鉴于以上因素,发生炉煤气中H2S的脱除程度业已成为其洁净度的一个重要指标。
1、煤气脱硫方法发生炉煤气中的硫来源于气化用煤,主要以H2S形式存在,气化用煤中的硫约有80%转化成H2S进入煤气,假如,气化用煤的含硫量为1%,气化后转入煤气中形成H2S大约2-3g/Nm3左右,而陶瓷、高岭土等行业对煤气含硫量要求为20-50mg/Nm3;假如煤气中的H2S燃烧后全部转化成SO2为2.6g/m3左右,比国家规定的SO2的最高排放浓度指标高出许多。
所以,无论从环保达标排放,还是从保证企业最终产品质量而言,煤气中这部分H2S都是必须要脱除的。
煤气的脱硫方法从总体上来分有两种:热煤气脱硫和冷煤气脱硫。
在我国,热煤气脱硫现在仍处于试验研究阶段,还有待于进一步完善,而冷煤气脱硫是比较成熟的技术,其脱硫方法也很多。
冷煤气脱硫大体上可分为干法脱硫和湿法脱硫两种方法,干法脱硫以氧化铁法和活性炭法应用较广,而湿法脱硫以砷碱法、ADA、改良ADA和栲胶法颇具代表性。
2、干法脱硫技术煤气干法脱硫技术应用较早,最早应用于煤气的干法脱硫技术是以沼铁矿为脱硫剂的氧化铁脱硫技术,之后,随着煤气脱硫活性炭的研究成功及其生产成本的相对降低,活性炭脱硫技术也开始被广泛应用。
2.1氧化铁脱硫技术最早使用的氧化铁脱硫剂为沼铁矿和人工氧化铁,为增加其孔隙率,脱硫剂以木屑为填充料,再喷洒适量的水和少量熟石灰,反复翻晒制成,其PH值一般为8-9左右,该种脱硫剂脱硫效率较低,必须塔外再生,再生困难,不久便被其他脱硫剂所取代。
现在TF型脱硫剂应用较广,该种脱硫剂脱硫效率较高,并可以进行塔内再生。
PDS湿法脱硫在焦炉煤气二级脱硫中的几种应用形式

第5期 收稿日期:2018-01-24作者简介:何秀风(1979—),女,硕士,工程师,从事化工工艺研究及设计工作。
PDS湿法脱硫在焦炉煤气二级脱硫中的几种应用形式何秀风(山西国控环球工程有限公司,山西太原 030024)摘要:针对目前很多企业需要增建二级脱硫系统的情况,本文简述了PDS脱硫的几种不同工艺,以及各工艺的优缺点,可供建设单位参考。
关键词:焦炉煤气;PDS;湿法脱硫中图分类号:X701.3 文献标识码:A 文章编号:1008-021X(2018)05-0145-01 随着《炼焦化学工业污染物排放标准》(GB16171-2012)的执行,尾气中的SO2排放量作为一个硬性指标成为各焦化厂争相达到的状态,而为了确保SO2的达标排放,作为热源的回炉煤气中的H2S含量也需严格控制。
目前,各焦化厂经过前期化产阶段的脱硫后,H2S含量大多在200mg/Nm3以上,甚至有些单位因为焦炉扩产或煤种变化,回炉煤气中的H2S含量达到1000mg/Nm3左右[1],对于这种情况,新上一套脱硫装置势在必行,而这种情况下的脱硫工艺大多采用PDS湿法脱硫工艺。
1 几种PDS精脱硫工艺形式PDS精脱硫工艺是指以PDS为催化剂的脱硫工艺,由东北师范大学开发[2],其中P是phthalocyanine(酞氰)的字头,D为dinucleus(双核)的字头,S为sulfonation(磺化)的字头,“PDS”的综合意思就是“双核磺化酞氰化合物”,这里指的是双核磺化酞氰钴[3]。
根据所选脱硫再生设备的不同,PDS精脱硫工艺又分为几种形式。
1.1 高塔再生工艺高塔再生工艺是从国外引进的技术,沿用至今,现在很多企业还在使用,其工艺流程如图1所示。
脱硫富液依靠再生泵送入再生塔的底部,与空压机送来的空气并流向上,进行氧化再生,再生后的脱硫贫液依靠位差直接流入脱硫塔中,与煤气接触进行反应。
图1 高塔再生工艺流程方框图高塔脱硫的优点是:再生稳定。
- 1、下载文档前请自行甄别文档内容的完整性,平台不提供额外的编辑、内容补充、找答案等附加服务。
- 2、"仅部分预览"的文档,不可在线预览部分如存在完整性等问题,可反馈申请退款(可完整预览的文档不适用该条件!)。
- 3、如文档侵犯您的权益,请联系客服反馈,我们会尽快为您处理(人工客服工作时间:9:00-18:30)。
煤气中的硫绝大部分以H2S的形式存在,而H2S随煤气燃烧后转化成SO2,空气中SO2含量超标会形成局域性酸雨,危害人们的生存环境,我国对燃烧发生炉煤气炉窑规定其SO2的最高排放浓度为900mg/m3;另一方面,SO2对诸如陶瓷、高岭土等行业的最终产品质量影响较大,鉴于以上因素,发生炉煤气中H2S的脱除程度业已成为其洁净度的一个重要指标。
1、煤气脱硫方法发生炉煤气中的硫来源于气化用煤,主要以H2S形式存在,气化用煤中的硫约有80%转化成H2S进入煤气,假如,气化用煤的含硫量为1%,气化后转入煤气中形成H2S大约2-3g/Nm3左右,而陶瓷、高岭土等行业对煤气含硫量要求为20-50mg/Nm3;假如煤气中的H2S燃烧后全部转化成SO2为2.6g/m3左右,比国家规定的SO2的最高排放浓度指标高出许多。
所以,无论从环保达标排放,还是从保证企业最终产品质量而言,煤气中这部分H2S都是必须要脱除的。
煤气的脱硫方法从总体上来分有两种:热煤气脱硫和冷煤气脱硫。
在我国,热煤气脱硫现在仍处于试验研究阶段,还有待于进一步完善,而冷煤气脱硫是比较成熟的技术,其脱硫方法也很多。
冷煤气脱硫大体上可分为干法脱硫和湿法脱硫两种方法,干法脱硫以氧化铁法和活性炭法应用较广,而湿法脱硫以砷碱法、ADA、改良ADA和栲胶法颇具代表性。
2、干法脱硫技术煤气干法脱硫技术应用较早,最早应用于煤气的干法脱硫技术是以沼铁矿为脱硫剂的氧化铁脱硫技术,之后,随着煤气脱硫活性炭的研究成功及其生产成本的相对降低,活性炭脱硫技术也开始被广泛应用。
2.1氧化铁脱硫技术最早使用的氧化铁脱硫剂为沼铁矿和人工氧化铁,为增加其孔隙率,脱硫剂以木屑为填充料,再喷洒适量的水和少量熟石灰,反复翻晒制成,其PH值一般为8-9左右,该种脱硫剂脱硫效率较低,必须塔外再生,再生困难,不久便被其他脱硫剂所取代。
现在TF型脱硫剂应用较广,该种脱硫剂脱硫效率较高,并可以进行塔内再生。
氧化铁脱硫和再生反应过程如下:(1)脱硫过程2Fe(OH)3+3H2SFe2S3+6H2OFe(OH)3+H2S2Fe(OH)2+S+2H2OFe(OH)2+H2SFeS+2H2O(2)再生过程2Fe2S2+3O2+6H2O4Fe(OH)3+6S4FeS+3O2+6H2O4Fe(OH)2+4S氧化铁脱硫剂再生是一个放热过程,如果再生过快,放热剧烈,脱硫剂容易起火燃烧,这种火灾现象曾在多个企业发生。
2.2活性炭脱硫技术活性炭脱硫主要是利用活性炭的催化和吸附作用,活性炭的催化活性很强,煤气中的H2S在活性炭的催化作用下,与煤气中少量的O2发生氧化反应,反应生成的单质S吸附于活性炭表面。
当活性炭脱硫剂吸附达到饱和时,脱硫效率明显下降,必须进行再生。
活性炭的再生根据所吸附的物质而定,S在常压下,190℃时开始熔化,440℃左右便升华变为气态,所以,一般利用450-500℃左右的过热蒸汽对活性炭脱硫剂进行再生,当脱硫剂温度提高到一定程度时,单质硫便从活性炭中析出,析出的硫流入硫回收池,水冷后形成固态硫。
活性炭脱硫的脱硫反应过程如下:2H2S+O2S+2H2O3、湿法脱硫技术湿法脱硫应用较早的方法是氨洗中和法,自从上世纪50年代初国外出现ADA法以来,我国也先后研制开发了改良型ADA法、MSQ法、KCS法以及栲胶法等脱硫技术。
与干法脱硫相比,湿法脱硫技术的应用相对要稍晚一些,最早湿法脱硫技术是在焦炉煤气和水煤气的净化方面首先应用,随着人们对发生炉煤气高净化度的要求,湿法脱硫技术才开始应用于发生炉煤气行业。
湿法脱硫技术应用于发生炉煤气净化与其在焦炉煤气和水煤气的净化方面的应用略有不同,脱硫设备、工艺和操作参数都略有调整。
湿法脱硫可以归纳分为物理吸收法、化学吸收法和氧化法三种。
物理吸收法是采用有机溶剂作为吸收剂,加压吸收H2S,再经减压将吸收的H2S 释放出来,吸收剂循环使用,该法以环丁矾法为代表;化学吸收法是以弱碱性溶剂为吸收剂,吸收过程伴随化学反应过程,吸收H2S后的吸收剂经增温、减压后得以再生,热砷碱法即属化学吸附法;氧化法是以碱性溶液为吸收剂,并加入载氧体为催化剂,吸收H2S,并将其氧化成单质硫,氧化法以改良ADA法和栲胶法为代表。
目前,在发生炉煤气的湿法脱硫技术中,应用较为广泛的是栲胶脱硫法。
它是以纯碱作为吸收剂,以栲胶为载氧体,以NaVO2为氧化剂。
其脱硫及再生反应过程如下:(1)吸收:在吸收塔内原料气与脱硫液逆流接触硫化氢与溶液中碱作用被吸收:H2S+Na2CO2=NaHS+NaHCO2(2)析硫:在反应槽内硫氢根被高价金属离子氧化生成单质硫:NaHS+NaHCO2+2NaVO2======S↓+Na2V2O2+Na2CO2+H2O(3)再生氧化在喷射再生槽内空气将酚态物氧化为醌态:2HQ+1/2O2====2Q+H2O以上过程按顺序连续进行从而完成气体脱硫净化。
另有资料和实验证实,在酚被氧化为醌的同时有双氧水生成,故再生氧化也可按下式表达:2HQ+O2====2Q+H2O2生成双氧水H2O2+V+4====V+5+H2OHS_+V+5====S0↓+V+4图3湿法栲胶脱硫和再生工艺流程(1)气体流程:降温、除尘、除焦油的冷煤气由煤气加压机升压至1800~2000mm水柱,进入脱硫塔底部,自下而上与塔内喷淋的脱硫液逆流接触,将煤气中的H2S 脱除至50mg/Nm3以下,脱硫后的煤气从脱硫塔顶部引出,经捕滴器脱除水份后,送至用户。
(2)溶液流程:从脱硫塔顶喷淋下来的溶液,吸收硫化氢后,称为富液,经脱硫塔液封槽引出至富液槽。
在富液槽内未被氧化的硫氢化钠被进一步氧化,并析出单质硫,此时,溶液中吸收的硫以单质悬浮状态存在。
出富液槽的溶液用再生泵加压后,打入再生槽顶部,经喷射器进入喷射再生槽,同时吸入足够的空气,以达到氧化栲胶和浮选硫膏之目的。
再生好的溶液称为贫液,贫液经液位调节器进入贫液槽,出贫液槽的贫液用脱硫泵打入脱硫塔顶部,经喷头在塔内喷淋,溶液循环使用。
再生槽浮选出的单质硫呈泡沫悬浮于液面上,溢流至硫泡沫槽内,上部清液回贫液槽循环使用,沉淀出的硫膏入熔硫釜生成副产品硫磺。
4、干法脱硫与湿法脱硫技术综合比较4.1干法脱硫的优缺点4.1.1干法脱硫的优点在选用反应活性好硫容高的脱硫剂的前提下,干法脱硫脱硫效率高,比较适宜处理含H2S较低的煤气,因为,煤气中H2S过高会造成脱硫剂很快失效。
4.1.2干法脱硫的缺点(1)干式氧化铁法脱硫设备笨重,脱硫剂再生大多为间歇再生,每次再生完毕,必须用蒸汽将塔内的残余空气吹净,煤气分析合格后,方能倒塔送气,否则会引起爆炸;另外,更换脱硫剂时,操作劳动强度大,操作不当很容易起火燃烧,较为危险。
(2)干式活性法脱硫脱硫剂再生使用的过热蒸汽不易获得,而且再生效果很难达到要求,多数厂家干脆就不再生,而是取出后更换新的活性炭。
干式脱硫,由于硫的吸附,会增加脱硫剂床层的阻力,即而引起煤气压力波动,不利于窑前煤气的正常燃烧;另外,采用干式脱硫,脱硫效率随着脱硫剂应用时间增加而不断降低,不利于控制最终产品质量;而且,由于干法脱硫大多属于间歇再生,为了不影响企业连续生产,必须设置备用脱硫塔,造成设备闲置浪费。
4.2湿式栲胶法脱硫优缺点4.2.1湿式栲胶法脱硫优点湿式栲胶法脱硫整个脱硫和再生过程为连续在线过程,脱硫与再生同时进行,不需要设置备用脱硫塔;煤气脱硫净化程度可以根据企业需要,通过调整溶液配比调整,适时加以控制,净化后煤气中H2S含量稳定。
4.2.2湿式栲胶法脱硫缺点设备较多,工艺操作也较复杂,设备投资较大4.3运行成本比较从煤气站脱硫系统运行费用来看,活性炭脱硫和氧化铁法脱硫较湿法栲胶脱硫要略低一些,但考虑干法脱硫需要再生的费用,则干法脱硫和湿法栲胶脱硫方法比较,其运行成本相差不大。
最近,我公司研制成功了一种新型湿法脱硫剂,可以替代价格较贵的栲胶和矾,使湿法脱硫成本大大降低,其运行成本已经低于干法脱硫。
5、干法脱硫与湿法脱硫技术结合应用对于一些对煤气中的H2S比较敏感的行业,可以结合干法脱硫与湿法脱硫技术的优点,将两种脱硫方法结合起来应用,利用湿法脱硫先将煤气中的大部分H2S脱除,然后,再利用干法脱硫对煤气中的H2S进行精脱,从而,达到较高的脱硫净度。
这样既利用了湿法脱硫可以在线调整的优点,又利用了干法脱硫脱硫效率高的优点,并克服了由于干法脱硫脱硫剂硫容因素造成的脱硫剂失效过快的问题。
PDS湿法脱硫工艺的分析与控制王玉艳佟斌(唐钢炼焦制气厂,唐山063039)唐钢炼焦制气厂为减少SO2的排放,对脱硫系统进行了全面改造,新建1套PDS法焦炉煤气脱硫装置。
该项目于2008年12月建成投产,新脱硫系统煤气处理能力为7万m3/h,脱硫液为碳酸钠溶液,同时添加PDS催化剂。
生产实践表明,该系统脱硫效果良好。
1 PDS法脱硫的原理及工艺流程来自粗苯的温度为30~35℃的煤气依次进入2台串联的脱硫塔底部,与塔顶喷淋的脱硫液逆向接触,脱除煤气中的大部分H2S,其基本反应为:H2S(气)←→H2S(液)Na2CO3+2H2S →NaHS+NaHCO3在PDS催化剂的作用下,可脱除无机硫与有机硫,同时促使NaHCO3进一步参加反应:NaHS+NaHCO3+(x-1)S ←→Na2S x+CO2+H2ONa2S x+1/2O2+H2O ←→2NaOH+xS↓NaHS+1/2O2←→NaOH+xS↓脱硫液吸收H2S的过程还伴随以下副反应:2NaHS+2O2 →Na2S2O3+H2O2HCN+Na2CO3 →2NaCN+CO2+H2ONaCN+S→NaCNS从2台脱硫塔底排出的脱硫液经液封槽进入溶液循环槽,用循环泵将脱硫液分别送入2台再生塔底部,与再生塔底部鼓入的压缩空气接触使脱硫液再生。
再生后的脱硫液从塔上部经液位调节器流回脱硫塔循环使用,浮于再生塔顶部扩大部分的硫泡沫靠液位差自流入硫泡沫槽,用泵将硫泡沫连续送往离心机,离心后的硫膏外运,离心液经过低位槽返回脱硫系统,工艺流程见图1。
图1 PDS法煤气脱硫工艺流程2 脱硫影响因素分析与控制PDS碱法脱硫包括气体进入液体的扩散过程,也包括化学反应过程。
影响扩散的因素有温度、液气比、传质面积、脱硫液浓度等;影响化学反应的因素包括脱硫液组成、温度、化学反应种类、反应进行程度等。
为保证脱硫系统的正常生产,在脱硫过程中必须控制好以下工艺条件。
1) 煤气及脱硫液的温度控制。
因为脱硫塔内的吸收反应是放热反应,因此当脱硫液温度较高时,加速副盐的成长,脱硫效率会随吸收液温度的升高而下降。
我厂的实践表明,脱硫液温度每升高2~3℃,脱硫效率下降4%~5%。
但脱硫液的温度过低会影响再生效果。
因此,我厂将煤气温度保持在30~35℃,脱硫液温度控制在35~40℃,使脱硫液温度高于煤气温度3~5℃,系统中多余的水分被煤气带走,以保证系统的水平衡。