刻蚀设备与工艺介绍
刻蚀设备与工艺介绍
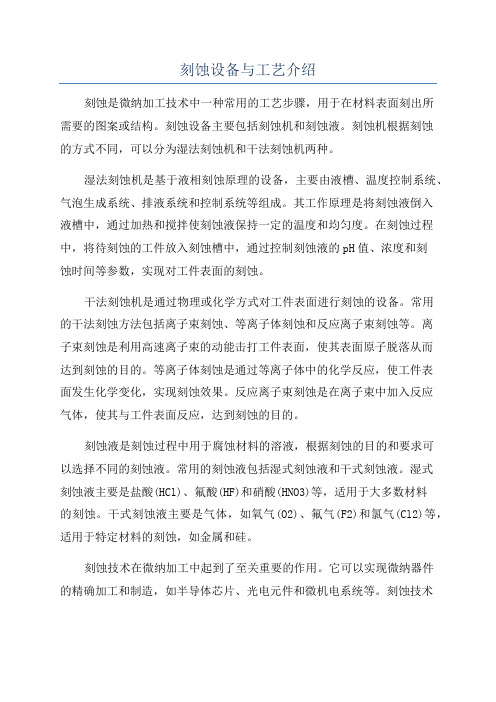
刻蚀设备与工艺介绍刻蚀是微纳加工技术中一种常用的工艺步骤,用于在材料表面刻出所需要的图案或结构。
刻蚀设备主要包括刻蚀机和刻蚀液。
刻蚀机根据刻蚀的方式不同,可以分为湿法刻蚀机和干法刻蚀机两种。
湿法刻蚀机是基于液相刻蚀原理的设备,主要由液槽、温度控制系统、气泡生成系统、排液系统和控制系统等组成。
其工作原理是将刻蚀液倒入液槽中,通过加热和搅拌使刻蚀液保持一定的温度和均匀度。
在刻蚀过程中,将待刻蚀的工件放入刻蚀槽中,通过控制刻蚀液的pH值、浓度和刻蚀时间等参数,实现对工件表面的刻蚀。
干法刻蚀机是通过物理或化学方式对工件表面进行刻蚀的设备。
常用的干法刻蚀方法包括离子束刻蚀、等离子体刻蚀和反应离子束刻蚀等。
离子束刻蚀是利用高速离子束的动能击打工件表面,使其表面原子脱落从而达到刻蚀的目的。
等离子体刻蚀是通过等离子体中的化学反应,使工件表面发生化学变化,实现刻蚀效果。
反应离子束刻蚀是在离子束中加入反应气体,使其与工件表面反应,达到刻蚀的目的。
刻蚀液是刻蚀过程中用于腐蚀材料的溶液,根据刻蚀的目的和要求可以选择不同的刻蚀液。
常用的刻蚀液包括湿式刻蚀液和干式刻蚀液。
湿式刻蚀液主要是盐酸(HCl)、氟酸(HF)和硝酸(HNO3)等,适用于大多数材料的刻蚀。
干式刻蚀液主要是气体,如氧气(O2)、氟气(F2)和氯气(Cl2)等,适用于特定材料的刻蚀,如金属和硅。
刻蚀技术在微纳加工中起到了至关重要的作用。
它可以实现微纳器件的精确加工和制造,如半导体芯片、光电元件和微机电系统等。
刻蚀技术的精度和效率对于微纳加工的成果和应用具有重要影响,因此需要不断改进和优化。
总结而言,刻蚀设备是微纳加工中一个重要的工艺步骤,包括湿法刻蚀机和干法刻蚀机两种。
刻蚀液根据刻蚀的需求可以选择不同的刻蚀液。
刻蚀技术在微纳加工中具有重要的应用价值,对于制造微纳器件起到了关键作用。
刻蚀机 腔体结构 工艺
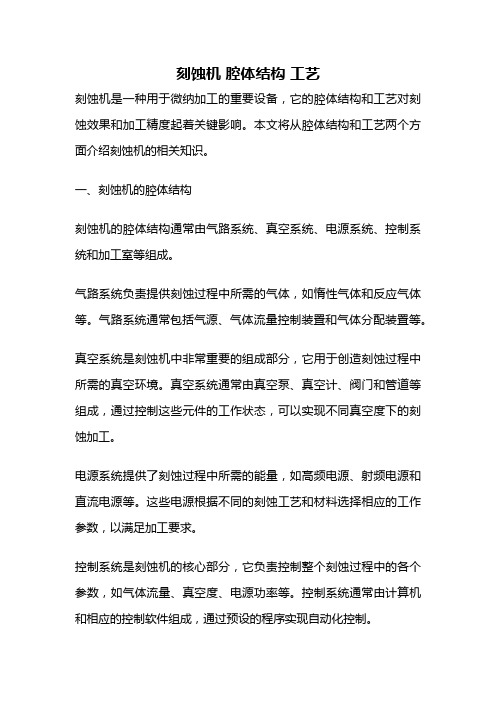
刻蚀机腔体结构工艺刻蚀机是一种用于微纳加工的重要设备,它的腔体结构和工艺对刻蚀效果和加工精度起着关键影响。
本文将从腔体结构和工艺两个方面介绍刻蚀机的相关知识。
一、刻蚀机的腔体结构刻蚀机的腔体结构通常由气路系统、真空系统、电源系统、控制系统和加工室等组成。
气路系统负责提供刻蚀过程中所需的气体,如惰性气体和反应气体等。
气路系统通常包括气源、气体流量控制装置和气体分配装置等。
真空系统是刻蚀机中非常重要的组成部分,它用于创造刻蚀过程中所需的真空环境。
真空系统通常由真空泵、真空计、阀门和管道等组成,通过控制这些元件的工作状态,可以实现不同真空度下的刻蚀加工。
电源系统提供了刻蚀过程中所需的能量,如高频电源、射频电源和直流电源等。
这些电源根据不同的刻蚀工艺和材料选择相应的工作参数,以满足加工要求。
控制系统是刻蚀机的核心部分,它负责控制整个刻蚀过程中的各个参数,如气体流量、真空度、电源功率等。
控制系统通常由计算机和相应的控制软件组成,通过预设的程序实现自动化控制。
加工室是刻蚀过程中的工作区域,通常由真空室和刻蚀室组成。
真空室用于创造刻蚀过程所需的真空环境,而刻蚀室则是实际进行刻蚀加工的地方。
刻蚀室内通常设有夹具、靶材和探针等,以保证加工的稳定性和精度。
二、刻蚀机的工艺刻蚀机的工艺是指刻蚀加工过程中所采用的方法和步骤。
刻蚀工艺的选择和优化直接影响到加工效果和加工质量。
首先是选择合适的刻蚀气体。
刻蚀气体通常分为惰性气体和反应气体两种。
惰性气体主要用于保护加工室和靶材,防止氧化或污染;而反应气体则是实际参与刻蚀反应的气体,它们可以与靶材表面发生化学反应,达到刻蚀的目的。
其次是确定刻蚀参数。
刻蚀参数包括刻蚀气体流量、刻蚀时间、刻蚀功率等。
这些参数的选择应根据具体的刻蚀要求和材料特性来确定,以确保刻蚀过程的稳定性和加工质量。
刻蚀机的工艺还包括刻蚀模式的选择。
常见的刻蚀模式有湿法刻蚀和干法刻蚀两种。
湿法刻蚀是在液体介质中进行的刻蚀,适用于一些化学反应比较剧烈的材料;而干法刻蚀则是在真空或气氛中进行的刻蚀,适用于一些对环境要求较高的材料。
刻蚀机设备和操作规程
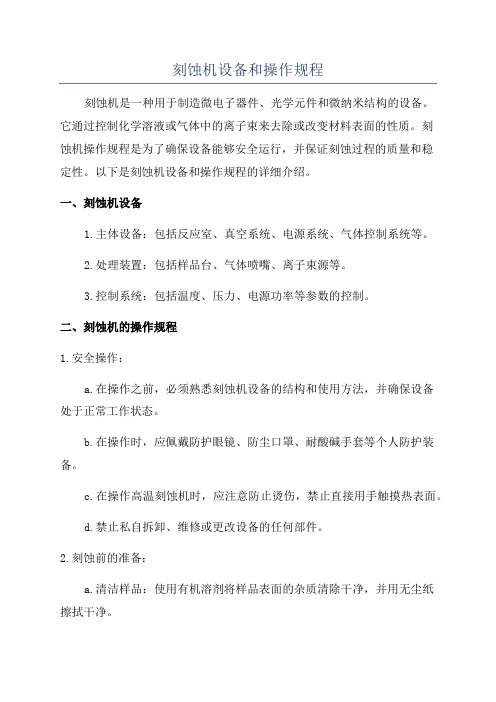
刻蚀机设备和操作规程刻蚀机是一种用于制造微电子器件、光学元件和微纳米结构的设备。
它通过控制化学溶液或气体中的离子束来去除或改变材料表面的性质。
刻蚀机操作规程是为了确保设备能够安全运行,并保证刻蚀过程的质量和稳定性。
以下是刻蚀机设备和操作规程的详细介绍。
一、刻蚀机设备1.主体设备:包括反应室、真空系统、电源系统、气体控制系统等。
2.处理装置:包括样品台、气体喷嘴、离子束源等。
3.控制系统:包括温度、压力、电源功率等参数的控制。
二、刻蚀机的操作规程1.安全操作:a.在操作之前,必须熟悉刻蚀机设备的结构和使用方法,并确保设备处于正常工作状态。
b.在操作时,应佩戴防护眼镜、防尘口罩、耐酸碱手套等个人防护装备。
c.在操作高温刻蚀机时,应注意防止烫伤,禁止直接用手触摸热表面。
d.禁止私自拆卸、维修或更改设备的任何部件。
2.刻蚀前的准备:a.清洁样品:使用有机溶剂将样品表面的杂质清除干净,并用无尘纸擦拭干净。
b.放置样品:将需要刻蚀的样品放置在样品台上,并确保其稳定性。
c.设置参数:根据刻蚀材料和刻蚀深度的要求,设置刻蚀机的参数,如气体种类、气流速度、刻蚀时间等。
d.检查真空度:确保真空系统工作正常,并进行真空泄漏测试。
3.刻蚀操作:a.打开设备开关,开始抽真空。
b.打开气体进气阀门,将预定混合气体引入反应室。
c.设置离子束源的功率、倾角和扫描速度等参数。
d.按下启动按钮,开始刻蚀过程。
e.刻蚀过程结束后,将刻蚀样品取出,并进行后续处理。
4.刻蚀后的清洁:a.刻蚀后,将样品放入有机溶剂中清洗,去除刻蚀产物。
b.将清洗后的样品用纯净水冲洗,并用氮气将其风干。
5.定期维护:a.定期对设备进行维护,检查传动系统、真空系统和电源系统等。
b.柜后对设备进行清洁,清除积尘和杂质。
总结:刻蚀机设备和操作规程是确保刻蚀过程安全和高效的重要保证。
在进行刻蚀操作之前,必须进行充分的准备工作,包括清洁样品、设置参数等。
在刻蚀过程中,要严格遵守安全操作规程,并确保设备处于正常工作状态。
蚀刻技术及工艺分析..

定蚀刻液的再生与更新。
11
蚀刻常用介质
NaOH:是一种常见的重要强碱。固体又被称为烧
碱、火碱、片碱、苛性钠等,是一种白色固体,有 强烈的腐蚀性,在空气中易潮解,且与空气中CO2 二氧化碳起反应(因此要密封存放);除溶于水之 外,氢氧化钠还易溶于乙醇、甘油;但不溶于乙醚、 丙酮、液氨。其液体是一种无色,有涩味和滑腻感 的液体。
滚膜、烘干: A:滚膜机滚轮的压力; B:滚轮速度; C:滚膜膜厚; D:烘干程度; E:油墨的纯净度;
20
蚀刻特点
★ 改变了机械加工金属零件方式; ★ 可对大到传统行业设备使用的大面积微孔滤网, 小到眼睛几乎很难以分辨的细微零件进行加工;
★ 生产过程无外力冲击、不变形、平整度好;生 产周期短、应变快、不需模具的设计、制造;产 品无毛刺、无凸起、两面一样光、一样平;
★ 按图红加工平面凹凸型的金属材料制品,如:文 字、数字及复杂图型、图案。制造各种精密的,任 意形状的通孔零件。
12
来料前处理 烘干 涂膜 烘烤 曝光 显影 全检补漆 蚀刻 脱膜 全检包装
13
蚀刻工艺改进
蚀刻设备的改进, 主要体现:
1.在传送方式、喷淋方式, 目的是提高生产效率、 蚀刻速度和蚀刻均匀性。
2. 喷淋杆或喷嘴的移动为了使溶液能全面地喷淋 到板子表面每个部位, 并促使板面溶液加快流动, 是移 动喷淋杆或喷嘴。 目前的水平传送喷淋式蚀刻设备 的喷嘴与喷淋杆摆动的结构有多样不同。使得喷淋溶 液不固定于一个位置, 就让喷嘴摆动。摆动方式有的 是转动喷管摇摆喷嘴角度, 有的是平移喷管移动喷嘴 位置, 也有水平旋转喷管而使喷嘴旋转喷液。喷嘴摆 动方式不同, 目的是为提高蚀刻均匀性。
刻蚀设备与工艺介绍

刻蚀设备与工艺介绍刻蚀是一种重要的微纳加工技术,用于从薄膜或器件上去除材料以形成所需的图案和结构。
刻蚀可以用于制造各种微纳器件,如集成电路、光子学器件、传感器和微机电系统(MEMS)等。
在刻蚀过程中,通过控制刻蚀设备和工艺参数,可以实现所需的刻蚀深度、尺寸和形状。
刻蚀设备通常包括刻蚀机、刻蚀槽和辅助设备。
刻蚀机是刻蚀的核心设备,主要包括物理刻蚀机和化学刻蚀机。
物理刻蚀机主要通过物理方法,如离子轰击、物理挥发和物理溅射等,去除材料。
常见的物理刻蚀机有反应离子刻蚀(RIE)机、平行板刻蚀机和电子束刻蚀机等。
化学刻蚀机通过化学反应去除材料,常见的化学刻蚀机有浸没式刻蚀机和喷雾式刻蚀机等。
辅助设备包括真空系统、气体供给系统、温控系统和控制系统等,用于提供所需的刻蚀环境和参数控制。
刻蚀工艺是刻蚀的关键,它决定了刻蚀速率、选择比和表面质量等。
常见的刻蚀工艺包括湿刻蚀、干刻蚀和等离子体刻蚀等。
湿刻蚀是一种在液体介质下进行的刻蚀工艺,常用的刻蚀液有酸、碱和溶剂等。
湿刻蚀可以实现高选择性和较大的刻蚀深度,但其刻蚀速率较慢且难以控制。
干刻蚀是一种在气体介质中进行的刻蚀工艺,常用的气体有氧气、氮气和氟化物等。
干刻蚀速率较快且易于控制,但选择比较低且表面质量较差。
等离子体刻蚀是一种在等离子体条件下进行的刻蚀工艺,通过将气体电离产生等离子体,利用等离子体的化学反应和物理效应实现刻蚀。
等离子体刻蚀具有高选择性、较大的刻蚀速率和良好的表面质量,广泛应用于集成电路和光子学器件等领域。
刻蚀工艺的参数对刻蚀结果有重要影响,包括刻蚀气体、功率、压力、温度和刻蚀时间等。
不同的刻蚀工艺需要不同的参数组合,需要通过实验和优化来确定最佳参数。
刻蚀设备和工艺在微纳加工中起着至关重要的作用,它们决定了刻蚀的效率和质量。
随着微纳加工技术的不断发展,刻蚀设备和工艺将进一步提高,以适应更多元化的应用需求。
DryEtch工艺及设备介绍

• Dry Strip 反应气体(SF6/NF3) :
SF6/NF3
CxHy (PR胶) + O2 -----> COx↑ + H2O↑
Active GI
Active GI
1.2 Dry Etch 工艺介绍
2.5 温控系统
Chiller (Heater Exchanger)
Pt Sensor (热电偶):温度测量
Chiller Chiller Hose Connector
2.5 温控系统
TC & BC:
Plasma Connection
Glass
---------
+++++++ --------
+++++++
• Ashing 反应气体(SF6/NF3) :
SF6/NF3
CxHy (PR胶) + O2 -----> COx↑ + H2O↑
Active GI
Active GI
1.2 Dry Etch 工艺介绍
• N+ Etch & Dry Strip
N+ Etch:针对TFT Channel 区域a-Si进行反应,生产挥发性气体的过程。 Dry Strip:针对N+ Etch后Glass表面PR胶进行反应,生成挥发性气体的过程。
• Ash/Act or Act/Ash
Active Etch:针对Pixel 区域a-Si进行反应,生产挥发性气体的过程。 Ashing:针对TFT Channel区域PR胶进行反应,生成挥发性气体的过程。
刻蚀工艺介绍

刻蚀前后对比照片
Metal刻蚀前后:
ITO刻蚀前后:
主要工艺参数
1 刻蚀液浓度 刻蚀液的浓度对刻蚀效果影响较大,所以 我们主要通过:来料检验、首片确认、定 期更换的方法来保证。 温度越高刻蚀效率越高,但是温度过高工 艺方面波动较大,只要通过设备自带温控 器和点检确认。 刻蚀流片的速度与刻蚀速率密切相关 喷淋流量的大小决定了基板表面药液置换 速度的快慢,流量控制可保证基板表面药 液浓度均匀。 过刻量即测蚀量,适当增加测试量可有效 控制刻蚀中的点状不良
辛小刚
刻蚀原理刻蚀不良原因分析
刻蚀原理介绍
刻蚀是用一定比例的酸液把玻璃上未受光刻胶保护的 Metal/ITO膜通过化学反应去除掉 膜通过化学反应去除掉, Metal/ITO膜通过化学反应去除掉,最终形成制程所需 要的图形。 要的图形。
刻蚀种类
目前我司的刻蚀种类主要分两种: 1、Metal刻蚀 刻蚀液主要成分:磷酸、硝酸、醋酸、水。 Metal:合金金属 2、ITO刻蚀 刻蚀液主要成分:盐酸、硝酸、水。 ITO:氧化铟锡(混合物)
刻蚀原理介绍主要工艺参数刻蚀液更换频率的管控刻蚀不良的产生原因单击此处编辑母版标题样式单击此处编辑母版标题样式刻蚀工艺介绍辛小刚刻蚀原理介绍刻蚀主要工艺参数刻蚀液更换频率的管控刻蚀不良原因分析刻蚀是用一定比例的酸液把玻璃上未受光刻胶保护的metalito膜通过化学反应去除掉最终形成制程所需要的图形
刻蚀工艺介绍
2
刻蚀温度
3
刻蚀速度
4
喷淋流量
5
过刻量
刻蚀液更换频率的管控
作业数量管控: 作业数量管控: 每天对生产数量及时记录,达到规定作业片数 及时更换。 作业时间管控: 作业时间管控: 由于药液的挥发,所以如果在规定更换时间未 达到相应的生产片数药液也需更换。 首片和抽检管控: 首片和抽检管控: 作业时需先进行首片确认,且在作业过程中每 批次进行抽检(时间间隔约25min)。
dse刻蚀设备原理
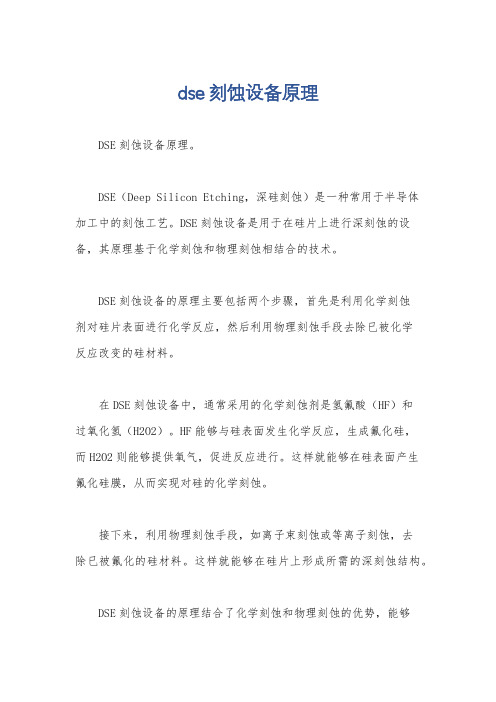
dse刻蚀设备原理
DSE刻蚀设备原理。
DSE(Deep Silicon Etching,深硅刻蚀)是一种常用于半导体
加工中的刻蚀工艺。
DSE刻蚀设备是用于在硅片上进行深刻蚀的设备,其原理基于化学刻蚀和物理刻蚀相结合的技术。
DSE刻蚀设备的原理主要包括两个步骤,首先是利用化学刻蚀
剂对硅片表面进行化学反应,然后利用物理刻蚀手段去除已被化学
反应改变的硅材料。
在DSE刻蚀设备中,通常采用的化学刻蚀剂是氢氟酸(HF)和
过氧化氢(H2O2)。
HF能够与硅表面发生化学反应,生成氟化硅,
而H2O2则能够提供氧气,促进反应进行。
这样就能够在硅表面产生
氟化硅膜,从而实现对硅的化学刻蚀。
接下来,利用物理刻蚀手段,如离子束刻蚀或等离子刻蚀,去
除已被氟化的硅材料。
这样就能够在硅片上形成所需的深刻蚀结构。
DSE刻蚀设备的原理结合了化学刻蚀和物理刻蚀的优势,能够
实现对硅材料的高效深刻蚀,广泛应用于半导体器件制造、MEMS (Micro-Electro-Mechanical Systems,微机电系统)制造等领域。
总的来说,DSE刻蚀设备的原理是利用化学刻蚀和物理刻蚀相
结合的技术,通过化学反应和物理去除的方式实现对硅材料的深刻蚀,为半导体加工和微纳加工提供了重要的工艺手段。
等离子体刻蚀工艺及设备

等离子体刻蚀工艺及设备
等离子体刻蚀工艺及设备是一种重要的微加工技术,广泛应用于半导体、光电子、MEMS等领域。
该技术利用等离子体对材料进行刻蚀,能够实现高精度、高效率的微米级加工,对于制备微电子器件和微系统具有重要的意义。
等离子体刻蚀工艺的基本原理是利用高频电场在真空中产生等
离子体,将等离子体束聚焦到加工对象表面,利用化学反应或物理撞击的方式将表面材料剥离或刻蚀。
该技术具有非接触、无损伤、高精度等特点,能够加工出各种形状和尺寸的微结构。
等离子体刻蚀设备由真空系统、高频电源、气体供给系统、加工室、聚焦系统等组成。
真空系统用于维持反应室内气体压力低于1 Pa,高频电源产生高频电场,气体供给系统提供刻蚀气体,加工室是等离子体刻蚀的主要区域,聚焦系统用于聚焦等离子体束。
在等离子体刻蚀过程中,刻蚀气体的选择和气体流量对加工效果影响较大。
常用的刻蚀气体有CF4、SF6、Ar等,不同的刻蚀气体能够实现不同的加工效果。
气体流量的调节能够控制刻蚀速率和刻蚀质量,流量过大或过小都会对加工效果产生不良影响。
等离子体刻蚀工艺和设备的发展促进了微电子器件和微系统制
备的进一步发展,未来该技术还将在纳米加工、生物医学等领域展现出更广阔的应用前景。
- 1 -。
碳化硅刻蚀技术路线

碳化硅刻蚀技术路线
1. 刻蚀方法:
碳化硅刻蚀主要采用干法刻蚀技术,包括物理刻蚀和化学气相刻蚀。
物理刻蚀通常使用高能离子束或者等离子体进行刻蚀,而化学气相刻蚀则利用气相中的化学物质对碳化硅进行化学反应,从而实现刻蚀。
2. 刻蚀设备:
常见的碳化硅刻蚀设备包括反应离子束刻蚀机(RIE)、电子束物理气相沉积(EBPVD)和电子束物理气相沉积(EBPVD)等。
这些设备能够提供高能离子束或者特定的化学气相环境,从而实现对碳化硅的精确刻蚀。
3. 刻蚀参数:
在进行碳化硅刻蚀时,需要考虑到刻蚀速率、表面粗糙度、刻蚀选择性等参数。
这些参数需要通过实验和优化来确定,以实现对碳化硅的高效刻蚀。
4. 刻蚀工艺:
碳化硅刻蚀工艺通常包括清洗表面、预处理、刻蚀和后处理等步骤。
清洗表面可以去除杂质,预处理可以提高刻蚀效果,而后处理则可以修饰刻蚀表面特性。
5. 应用领域:
碳化硅刻蚀技术在功率器件、光电子器件、传感器等领域有着重要的应用。
通过精确控制刻蚀工艺,可以制备出具有高性能的碳化硅器件。
总的来说,碳化硅刻蚀技术路线涉及到刻蚀方法、刻蚀设备、刻蚀参数、刻蚀工艺和应用领域等多个方面。
通过对这些方面的深入了解和优化,可以实现对碳化硅材料的高效刻蚀,为碳化硅器件的制备提供技术支持。
刻蚀的工艺

刻蚀的工艺
刻蚀是一种常用的微纳加工工艺,通过将化学蚀刻剂作用于材料表面,使其在预定区域发生化学反应而被蚀刻掉,从而实现对材料的精确加工和形状控制。
刻蚀工艺广泛应用于半导体制造、光学元件制造、微纳米器件制造等领域。
刻蚀工艺通常分为湿法刻蚀和干法刻蚀两种。
1. 湿法刻蚀:湿法刻蚀是指将材料置入含有化学蚀刻剂的溶液中,通过溶液中的化学反应来蚀刻材料表面。
湿法刻蚀具有高蚀刻速率、高选择性和较低的成本等特点。
常见的湿法刻蚀包括酸性刻蚀、碱性刻蚀、氧化物刻蚀等。
2. 干法刻蚀:干法刻蚀是指将材料置入低压或大气压等特定环境中,通过气体或等离子体的物理作用或化学反应来蚀刻材料表面。
干法刻蚀通常具有更高的加工精度和更好的表面质量,但蚀刻速率较慢。
常见的干法刻蚀包括物理刻蚀(如离子束刻蚀、电子束刻蚀)和化学气相刻蚀等。
刻蚀工艺是一项复杂的加工技术,需要根据具体材料和加工要求选择合适的刻蚀工艺和工艺参数,以获得所需的形状和尺寸。
同时,刻蚀还要考虑蚀刻剂的选择、工艺控制、蚀刻均匀性等方面,以保证加工质量和一致性。
等离子体刻蚀工艺及设备
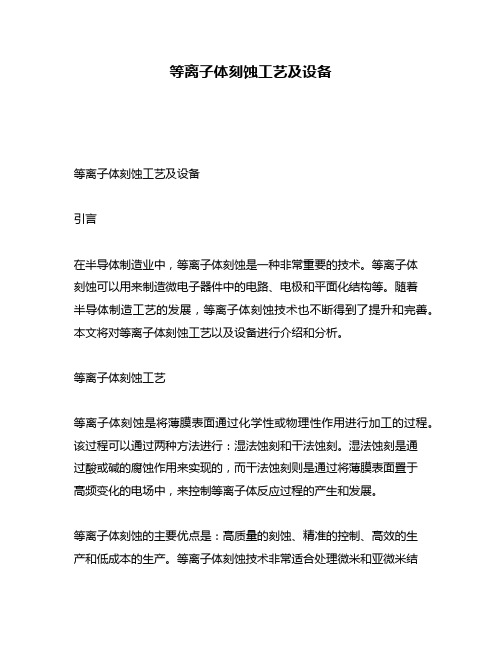
等离子体刻蚀工艺及设备等离子体刻蚀工艺及设备引言在半导体制造业中,等离子体刻蚀是一种非常重要的技术。
等离子体刻蚀可以用来制造微电子器件中的电路、电极和平面化结构等。
随着半导体制造工艺的发展,等离子体刻蚀技术也不断得到了提升和完善。
本文将对等离子体刻蚀工艺以及设备进行介绍和分析。
等离子体刻蚀工艺等离子体刻蚀是将薄膜表面通过化学性或物理性作用进行加工的过程。
该过程可以通过两种方法进行:湿法蚀刻和干法蚀刻。
湿法蚀刻是通过酸或碱的腐蚀作用来实现的,而干法蚀刻则是通过将薄膜表面置于高频变化的电场中,来控制等离子体反应过程的产生和发展。
等离子体刻蚀的主要优点是:高质量的刻蚀、精准的控制、高效的生产和低成本的生产。
等离子体刻蚀技术非常适合处理微米和亚微米结构,因为在这个范围内,湿法蚀刻不再适用。
与此同时,等离子体刻蚀技术还能够加工复杂的形状和不规则的表面结构。
在等离子体刻蚀工艺中,其主要步骤如下:1)清洗表面,去除杂质和沉积物。
2)制备遮蔽层,避免不必要的刻蚀。
3)使用化学反应喷淋射入反应气体,形成等离子体。
4)刻蚀薄膜,当荷电粒子和表面粒子相互作用时,会转移表面的能量,并产生表面化学反应,从而产生刻蚀和剥离效应。
5)进行清洗和脱层。
等离子体刻蚀设备等离子体刻蚀设备是通过对薄膜表面施加高频电压,而实现表面化学反应的装置。
等离子体刻蚀设备的核心部分是电极板,其作用是控制等离子体的形状、大小和位置。
现在,主要使用的等离子体刻蚀设备有两种类型:平板式和并联板式。
平板式等离子体刻蚀设备由两个并排的电极板组成,这些电极板之间通过等离子体形成的空气间隙进行沟通。
这种在大型集成电路制造中使用的设备,可以进行长时间的蚀刻,产生大量的等离子体反应区。
并联板式等离子体刻蚀设备由多个平行的电极板组成,这些电极板之间的间隔可以通过移动电极板来调整。
并联板式等离子体刻蚀设备的优点在于能够进行精细的调整,从而获得更高的制造精度。
总结等离子体刻蚀是半导体制造业中不可或缺的技术之一。
刻蚀工艺介绍ppt
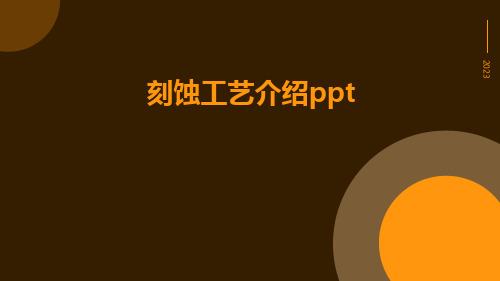
2023
刻蚀工艺介绍ppt
contents
目录
刻蚀工艺简介刻蚀工艺分类刻蚀工艺流程刻蚀工艺参数优化刻蚀设备及厂商刻蚀工艺发展方向
刻蚀工艺简介
01
刻蚀工艺是指利用化学或物理方法有选择性地去除材料表面上的部分物质,以达到制备特定形状和尺寸的目的。
刻蚀工艺包括干法刻蚀和湿法刻蚀两种,其中干法刻蚀主要利用等离子体或激光等高能粒子进行表面处理,而湿法刻蚀则主要利用化学试剂对材料表面进行腐蚀。
设备名称
溅射刻蚀机(Sputtering Etcher)
设备名称
等离子刻蚀机(Plasma Etcher)
功能描述
溅射刻蚀机利用高能粒子撞击靶材表面,使靶材表面的粒子撞击待刻蚀材料表面,从而实现刻蚀。
主要设备及功能描述
各厂商设备特点比较
厂商A
设备稳定性好,售后服务有保障,但价格较高。
厂商B
设备性价比高,但技术支持能力较弱。
03
利用氢氧化钠对硅、二氧化硅等材料进行刻蚀。氢氧化钠具有强碱性,能够与硅、二氧化硅等材料发生化学反应,将目标材料去除。
利用化学溶液对材料进行刻蚀。在湿法刻蚀过程中,目标材料与化学溶液发生化学反应,将目标材料去除。
湿法刻蚀
利用等离子体、激光或其他光源对材料进行刻蚀。在干法刻蚀过程中,中性粒子或离子与目标材料发生碰撞,通过物理作用将目标材料去除。
控制曝光能量
曝光
选择合适的显影液
选择合适的显影液,以将曝光后的光刻胶溶解去除,从而形成所需的图案。
控制显影时间和温度
控制显影液的使用时间和温度,以避免显影过度或不足,影响刻蚀的质量和精度。
显影
去除未曝光的光刻胶
通过化学试剂或物理方法将未曝光的光刻胶去除,以暴露出硅片表面需要刻蚀的区域。
刻蚀设备简介演示

利用射频电源产生的高频电场,将气体激发为等离子体,通过反应气体与材料 表面的化学反应来刻蚀表面。
激光刻蚀设备
激光诱导等离子刻蚀设备
通过高能激光束照射材料表面,产生等离子体,实现表面刻蚀。
激光烧蚀刻蚀设备
利用高功率激光束将材料表面烧蚀,实现物理刻蚀。
其他类型刻蚀设备
电化学刻蚀设备
刻蚀设备简介演示
汇报人: 2023-11-23
目录
• 刻蚀设备概述 • 刻蚀设备类型 • 刻蚀设备的关键部件 • 刻蚀设备的操作与维护 • 刻蚀技术的发展趋势与挑战 • 刻蚀设备的应用案例
01
刻蚀设备概述
Chapter
定义与分类
刻蚀设备定义
刻蚀设备是一种用于材料表面处 理的设备,通过物理或化学方法 实现材料表面的选择性去除。
将准备好的样品放入设备中的指定位 置,关闭腔体并启动真空系统。
开始刻蚀
满足安全条件后,启动刻蚀设备并 进行实时监测,记录刻蚀过程中的 数据。
刻蚀结束与清洗
当刻蚀达到预定时间或达到预定工 艺条件时,关闭设备并解除真空状 态,取出样品进行清洗。
常见问题及解决方案
检查工艺参数是否设置正确,如 气体流量、压力等参数是否稳定 ,同时确认样品表面是否平整、 无污染。
应,从而提高刻蚀效果。
组成部分
真空系统通常包括真空泵、真空 测量仪器和管路等部分,以确保
真空环境的稳定和准确控制。 Nhomakorabea控制系统
定义
控制系统是用于监控和控制刻蚀设备各部件的电 子系统。
功能
它确保设备在刻蚀过程中能够稳定运行,并对异 常情况进行监测和报警。
组成部分
控制系统通常包括传感器、控制器和执行器等部 分,以实现对设备各部件的精确控制和监测。
半导体刻蚀工艺简介

半导体刻蚀⼯艺简介此保护膜可保护多晶硅的侧壁,进⽽形成⾮等向性刻蚀。
使⽤Cl2等离⼦体对多晶硅的刻蚀速率⽐使⽤F原⼦团慢很多,为兼顾刻蚀速率与选择⽐,有⼈使⽤SF6⽓体中添加SiCl4或CHCl3。
SF6的⽐例越⾼,刻蚀速率越快;⽽SiCl4或CHCl3的⽐例越⾼,多晶硅/SiO2的刻蚀选择⽐越⾼,刻蚀越趋向⾮等向性刻蚀。
除了Cl和F的⽓体外,溴化氢(HBr)也是⼀种常⽤的⽓体,因为在⼩于0.5µm的制程中,栅极氧化层的厚度将⼩于10nm,⽤HBr等离⼦体时多晶硅/SiO2的刻蚀选择⽐⾼于以Cl为主的等离⼦体。
4.⾦属的⼲法刻蚀⾦属刻蚀主要是互连线及多层⾦属布线的刻蚀,⾦属刻蚀有以下⼏个要求:⾼刻蚀速率(⼤于1000nm/min);⾼选择⽐,对掩蔽层⼤于4:1,对层间介质⼤于20:1;⾼的刻蚀均匀性;关键尺⼨控制好;⽆等离⼦体损伤:残留污染物少;不会腐蚀⾦属。
①铝的刻蚀。
铝是半导体制备中最主要的导线材料,具有电阻低、易于淀积和刻蚀等优点。
铝刻蚀通常采⽤加⼊卤化物的氯基⽓体,最常⽤的是BCl3。
因为铝在常温下表⾯极易氧化⽣成氧化铝,氧化铝阻碍了刻蚀的正常进⾏,⽽BCl3可将⾃然氧化层还原、保证刻蚀的进⾏,⽽且BCl3还容易与氧⽓和⽔反应,可吸收反应腔内的⽔汽和氧⽓,从⽽降低氧化铝的⽣成速率。
1.4质量评价⼀、⼲法刻蚀的终点监测近⼏年发展起来的⼲法刻蚀⼯艺,为了提⾼刻蚀精度,深⼊研究刻蚀机理,实现刻蚀设备的⾃动化,需要解决⼯艺过程的监控问题,特别是精确控制刻蚀终点。
因为⼲法刻蚀的选择性不如湿法,终点监控不当极易造成过腐蚀,甚⾄破坏下层图形。
早期的监控⽅法是计时法。
假设被刻蚀材料的膜厚已知,先通过实验确定刻蚀速率,然后在⼯艺过程中,由计时确定终点。
但由于影响刻蚀速率的因素太多(如压⼒、温度、流量、⽓体配⽐等),刻蚀速率难于重复(如前所述,对铝的等离⼦体刻蚀更是如此),不能满⾜⼯艺要求。
表1-1⼏种等离⼦体刻蚀终点检测⽅法⼆、⼲法刻蚀的质量检测刻蚀⼯艺的最后⼀步是进⾏检查以确保刻蚀的质量,通常都是⽤⾃动检测系统进⾏的。
刻蚀工艺及设备

刻蚀工艺与设备培训
王瑗 纳米加工平台
2009.5
1
1
刻蚀的基本原理
2
IBE刻蚀原理及设备
3
RIE刻蚀原理及设备
4
ICP刻蚀原理及设备
5 工艺过程、检测及仪器
2
1
刻蚀的基本原理
刻蚀
用物理的、化学的或同时使用化学和物理的方 法,有选择地把没有被抗蚀剂掩蔽的那一部分 材料去除,从而得到和抗蚀剂完全一致的图形
¾ 若工作腔室处于真空,须先放气然后再放入刻蚀样品。 进入真空室系统的样品或零件,绝对要求外部干净,尤其防止将水 和易挥发性的固体或液体带入系统,放好样品后,即可开始抽真空 刻蚀过程中密切关注监控系统,程序运行中不稳定情况,记录所有 参数(功率,气体流量等)
35
5
工艺过程、检测及仪器
¾ 刻蚀后的检查 (1) 正面颜色是否异常及刮伤 (2) 有无缺角及Particle
• ICP Service模式权限很大,为避免误操作,仅限关闭真空装置时 操作
• 在手动模式下进行托盘定位时,一定要注射频源功率不宜设置过高,ICP小于2000W,RF小于500W
33
4
ICP刻蚀原理及设备
加工过程中参数调节
温度 刻蚀速率,化学反应
扩散
反应
表面扩散
17
3
RIE刻蚀原理及设备
18
3
RIE刻蚀原理及设备
TEGAL PLASMA ETCHER, MODEL 903e
适用于150mm单片晶片上的SiO2和Si3N4的刻蚀; 刻蚀温度能控制在20-35度之间
主机
射频源
显示器
19
3
RIE刻蚀原理及设备
刻蚀工艺介绍范文

刻蚀工艺介绍范文刻蚀工艺是一种在半导体器件制造过程中广泛使用的技术,它通过化学和物理的方法将材料从表面或者内部剥离,以实现器件的结构和功能的定义。
刻蚀工艺可分为湿法刻蚀和干法刻蚀两种,每种方法都有不同的适用场合和优势。
湿法刻蚀是最早应用于半导体工艺中的刻蚀方法之一、它使用酸或碱溶液作为刻蚀液,通过溶解和化学反应来去除材料。
湿法刻蚀的优点是刻蚀速率较快,可以进行立体和非立体的刻蚀,并且可以选择性地去除目标材料。
湿法刻蚀的缺点是刻蚀深度难以控制,刻蚀液的处理和废液的处置会带来环境污染问题。
干法刻蚀是利用气体的物理和化学反应来去除材料。
它主要包括离子束刻蚀、反应离子刻蚀和物理气相刻蚀等方法。
干法刻蚀的优点是刻蚀速率较慢,刻蚀深度易于控制,可实现较高的刻蚀选择性,并且不会产生液体废液,符合环保要求。
干法刻蚀的缺点是设备成本较高,需要较为复杂的真空系统和气体处理系统。
刻蚀工艺的应用非常广泛,特别是在集成电路制造过程中。
刻蚀工艺可以用于定义集成电路中的通孔、晶体管沟槽、金属线和栅极等结构。
刻蚀工艺的准确性和可重复性对于实现高性能和高可靠性的器件非常重要。
刻蚀工艺的优化对于降低器件制造成本、提高器件性能和扩大器件功能都具有重要意义。
刻蚀工艺的优化主要包括增加刻蚀速率、提高刻蚀选择性和改善表面质量等方面。
为了增加刻蚀速率,可以通过增加刻蚀液的浓度、温度和搅拌速度等方法来提高刻蚀效率。
而为了提高刻蚀选择性,可以选择合适的刻蚀液、合适的刻蚀条件和合适的掩膜材料来实现。
在改善表面质量方面,可以使用气体混合物或者添加一些表面活性剂来减少表面缺陷和粗糙度。
总之,刻蚀工艺是一项关键的半导体器件制造技术,它可用于定义器件的结构和功能。
刻蚀工艺通过化学和物理的方法将材料从表面或者内部剥离,以实现器件的结构和功能的定义。
湿法刻蚀和干法刻蚀是常用的刻蚀方法,各具特点和优势。
刻蚀工艺的优化在提高器件性能、降低制造成本和实现器件功能扩展方面具有重要意义。
半导体微细加工中的刻蚀设备及工艺

( 圳 深爱 半 导体 有 限公 司 ,广 东 深 圳 582 ) 深 109 摘 要 :与传 统 湿法 腐 蚀 比较 ,干 法 刻 蚀 具 有各 向异 性 、对 不 同材 料 选择 比 差 别较 大 、均 匀性 与 重 复 性好 、 易 于 实现 自动连 续生 产 等优 点 。 目前 ,刻 蚀技 术 已经 成 为 集成 电路 生产 中的 标 准技 术 ,干 法刻 蚀 设 备 亦成 为 关键 设备 。本 文对 半 导 体 生 产 中刻蚀 的原 理 、分 类 ,结 合 生 产 实际对
刻蚀工艺进行 了较 系统 的论述 ,并介 绍 了随着硅 片尺 寸的增 大,工艺线条进入 亚微 米级 时代 ,
相应 刻 蚀设 备 的发展 趋势 。
关键 词 :刻 蚀 设备 ;刻蚀 工 艺 ;半导 体 ;集 成 电路 ;亚微 米
中 图分类 号 :T 3 5 文献 标识 码 :A 文 章编 号 :17.7 6 (02 0 4 .4 N0 6 1 7 20 )1-0 10 4 1 Applc to a d v l p e f e c e ui m e t a ia i n n de e o m nt o t h q p n nd pr c s n e io o e s i s m c ndu t upe fne lne m a f c urng c or s r i i nu a 刻 蚀分 为湿 法 刻蚀 和 干法 刻蚀 两类 。湿法 刻 蚀
是将硅 片浸泡在 可与被刻蚀薄膜进 行反应 的溶 液 中,用化学方法除去不要部分的薄膜。早期制造业
以湿 法 为主 。 当半 导体 制造 业进 入 微米 、亚微 米 时
方面 ,要求高度 的各 向异性 以得到刻蚀 图形垂直
维普资讯
晶圆刻蚀设备的制作方法
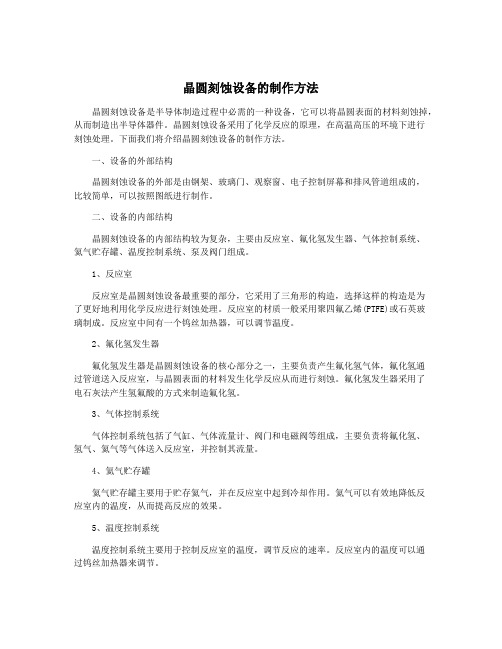
晶圆刻蚀设备的制作方法晶圆刻蚀设备是半导体制造过程中必需的一种设备,它可以将晶圆表面的材料刻蚀掉,从而制造出半导体器件。
晶圆刻蚀设备采用了化学反应的原理,在高温高压的环境下进行刻蚀处理。
下面我们将介绍晶圆刻蚀设备的制作方法。
一、设备的外部结构晶圆刻蚀设备的外部是由钢架、玻璃门、观察窗、电子控制屏幕和排风管道组成的,比较简单,可以按照图纸进行制作。
二、设备的内部结构晶圆刻蚀设备的内部结构较为复杂,主要由反应室、氟化氢发生器、气体控制系统、氦气贮存罐、温度控制系统、泵及阀门组成。
1、反应室反应室是晶圆刻蚀设备最重要的部分,它采用了三角形的构造,选择这样的构造是为了更好地利用化学反应进行刻蚀处理。
反应室的材质一般采用聚四氟乙烯(PTFE)或石英玻璃制成。
反应室中间有一个钨丝加热器,可以调节温度。
2、氟化氢发生器氟化氢发生器是晶圆刻蚀设备的核心部分之一,主要负责产生氟化氢气体,氟化氢通过管道送入反应室,与晶圆表面的材料发生化学反应从而进行刻蚀。
氟化氢发生器采用了电石灰法产生氢氟酸的方式来制造氟化氢。
3、气体控制系统气体控制系统包括了气缸、气体流量计、阀门和电磁阀等组成,主要负责将氟化氢、氢气、氦气等气体送入反应室,并控制其流量。
4、氦气贮存罐氦气贮存罐主要用于贮存氦气,并在反应室中起到冷却作用。
氦气可以有效地降低反应室内的温度,从而提高反应的效果。
5、温度控制系统温度控制系统主要用于控制反应室的温度,调节反应的速率。
反应室内的温度可以通过钨丝加热器来调节。
6、泵及阀门泵及阀门主要负责将残余的气体、液体和固体物质排出,从而避免对设备和操作者的危害。
以上就是晶圆刻蚀设备的制作方法,相信大家看完后对晶圆刻蚀设备的制作有了一定的了解。
三、设备的工作原理晶圆刻蚀设备的工作原理是将氟化氢和晶圆表面材料进行化学反应,从而使晶圆表面的材料被刻蚀掉。
氟化氢和晶圆表面的材料反应后,会生成气体或固体物质,这些物质需要通过泵和阀门流出反应室,以避免对设备和操作者的危害。
- 1、下载文档前请自行甄别文档内容的完整性,平台不提供额外的编辑、内容补充、找答案等附加服务。
- 2、"仅部分预览"的文档,不可在线预览部分如存在完整性等问题,可反馈申请退款(可完整预览的文档不适用该条件!)。
- 3、如文档侵犯您的权益,请联系客服反馈,我们会尽快为您处理(人工客服工作时间:9:00-18:30)。
保护好自己才能够更好的生产。当然,也没有必要因为危险就害怕, 在做好安全防护的前提下,我们的生产安全是有保障的,这个已在各 大型电池生产企业得到验证。
精选课件
2
二、电池生产工艺流程
硅片检验 丝网印刷
烧结
制绒 PECVD 分档测试
精选课件
SCHMID采用 滚轮带液 的原理进行刻蚀。
精选课件
13
刻蚀线
刻蚀线
一个程度有点重的微过刻的片子
对于直接RENA的片子,刻蚀后有时会有刻蚀 线——一条靠近边缘的淡淡的一条黑线。
正常情况下刻蚀线到边缘的距离控制在 1.5mm以下,最宽不得超过1.5mm。
精选课件
14
刻蚀线
•
刻蚀线一般是淡淡的一条黑线。
有时在边缘会有很显眼的很黑很黑
的线或黑区,这些东西就不是刻蚀
n+ Si
Front Grid AR-coating
Si - Wafer
PSG
p+ Si
Al
精选课件
21
酸碱槽的清洗原理
碱洗: NaOH或KOH中和掉硅片表面残余的酸,去除多孔硅。
酸洗 HF和HCl,中和掉硅片表面残余的碱,去除残存的氧化物 和重金属
HF去除硅片表面氧化物 盐酸具有酸和络合剂的双重作用,氯离子能与 Pt2+、
应),四氟化硅又和水化合成氟硅酸进入溶液。
3.硫酸不参与反应,仅仅是增加氢离子浓度,加快反应,增加溶
液黏度(增大溶液与PSG薄层间的界面张力)和溶液密度。
精选课件
11
RENA刻蚀的机理
• 链的触发: 硝酸将硅氧化成二氧化硅,生成二氧化氮或一氧化氮 Si+4HNO3=SiO2+4NO2+2H2O (慢反应) Si+2HNO3=SiO2+2NO+2H2O (慢反应) • 链的扩展: 二氧化氮、一氧化氮与水反应,生成亚硝酸,亚硝酸很
线了,而是没有洗干净的酸,此时
需要在碱槽手动补碱来解决。如果
多次出现这种情况,必须检查碱洗
槽是否堵碱。
精选课件
15
RENA刻蚀的机理——溶液变绿
亚硝酸本身并不是特别稳定,它会慢慢分解。在时 刻时停的小批量生产时,溶液中的亚硝酸浓度的 平衡点不会超过一定的限度,刻蚀溶液会一直保 持无色。大批量生产时,亚硝酸浓度平衡点会有 所上升,亚硝酸浓度的略微增加,会导致有一个 有趣的现象——溶液颜色变成淡绿色和绿色。
HF
淋风
下 片
HF
刀
除刻蚀槽外,其它化学槽和水槽都是喷淋结构。去 PSG氢氟酸槽是喷淋结构,而且片子浸入到溶液内部。
精选课件
10
RENA刻蚀的机理
尽管很复杂,但刻蚀反应不外分成两步:
1. 硝酸/亚硝酸(HNO2)将硅氧化成二氧化硅(主要是亚硝酸
将硅氧化)。
2.二氧化硅和氢氟酸反应(快反应),生成四氟化硅和水(快反
快地将硅氧化成二氧化硅
2NO2+H2O=HNO2+HNO3 (快反应) Si+4HNO2=SiO2+4NO+2H2O (快反应)(第一步的主反应) 4HNO3+NO+H2O=6HNO2(快反应)
只要有少量的二氧化氮生成,就会和水反应变成亚硝酸。只要少量的 一氧化氮生成,就会和硝酸、水反应很快地生成亚硝酸。亚硝酸会很 快的将硅氧化,生成一氧化氮,一氧化氮又与硝酸、水反应。造成硅 的快速氧化,硝酸则最终被还原成氮氧化物。
只要刻蚀正常,溶液颜色变绿不会对片子效率产生 任何影响。刻蚀不合格片时可能会将一些杂质引 入刻蚀溶液,污染刻蚀溶液,但这与变绿无关。
精选课件
16
RENA刻蚀槽外观
精选课件
17
传说中的 裘千仞的“水上漂”,想拥有吗? 绝对给力!!!
精选课件
18
InOxSide
Edge isolation through back side emitter removal
精选课件
19
RENA刻蚀槽——轻功“水上漂”
精选课件
20
Edge Isolation Process
Saw damage etching + texturing
Diffusion
n+ Si
Edge isolation + Phosphor glass etching
AR-coating printing firing
精选课件
4
三、刻蚀工艺的作用
精选课件
5
三、RENA 机台外观
精选课件
6
三、SCCHMID SE机台外观
精选课件
8
RENA刻蚀专辑
精选课件
9
RENA Inoxide 大致构造
上 片
刻蚀槽 水
H2SO4/
喷
HNO3/
淋
水
碱洗槽
喷
KOH
淋
水吹
去PSG槽 喷 干
Au3+、Ag+、Cu2+、Cd2+、Hg2+等金属离子形成可溶于水的 络合物。
精选课件
22
SCHMID专辑
精选课件
23
SCHMID机台刻蚀的原理与RENA相同,所以
这里不再重复对化学反应的探讨,主要关注的是一 些不同点。
精选课件
24
RENA刻蚀槽采用“水上漂”的原理进行硅片背表 面和四周的刻蚀;
最终硅片背面(与刻蚀溶液接触)被氧化。
精选课件
12
RENA刻蚀的机理
第二步、二氧化硅的溶解
二氧化硅生成以后,很快与氢氟酸反应 SiO2+4HF=SiF4+2H2O;(四氟化硅是气体) SiF4+2HF=H2SiF6。
总反应 SiO2+6HF=H2SiF6+2H2O 最终刻蚀掉的硅以氟硅酸的形式进入溶液。
一、安全 二、电池工艺流程 三、刻蚀设备与工艺介绍
精选课件
1
一、安全
安全!!!
➢HF, HNO3,H2SO4, KOH,NaOH,HCl都是强腐蚀性的化学药 品,其中HF腐蚀更是强烈,它们的固体颗粒、溶液、蒸汽会伤害到人 的皮肤、眼睛、呼吸道,所以操作人员要按照规定穿戴防护服、防护 面具、防护眼镜、长袖胶皮手套,遵守安全操作规程。一旦有化学试 剂伤害了员工的身体,马上用纯水冲洗30分钟,送医院就医。
磷扩散 刻蚀
检验包装
3
三、刻蚀工艺的作用
硅片扩散后电池的边缘会有N型杂质与P型基底形成 PN结,以及扩散的过程中在电池表面形成了一层很厚的 磷硅玻璃层(PSG),因此需要周边刻蚀将边缘的PN结去 除,而磷硅玻璃则通过HF酸短时间浸泡来去除。
故扩散后要进行去周边及去PSG工序,原来这道工序 是分等离子刻蚀和HF酸洗设备两步进行的,现在我们的 设备可以一次进行,目前我们拥有两种刻蚀机台:RENA In-oxside,SCHMID 。