F专用刀具设计
数控机床编程中进给功能指令F、主轴转速功能指令S、刀具功能指令T简介
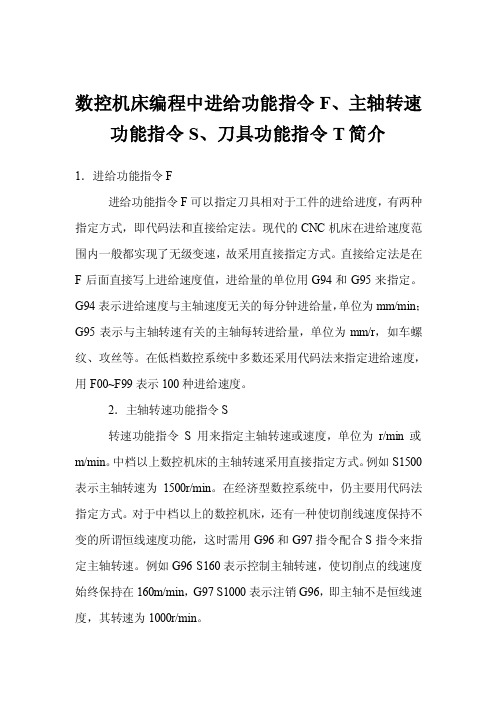
数控机床编程中进给功能指令F、主轴转速功能指令S、刀具功能指令T简介1.进给功能指令F进给功能指令F可以指定刀具相对于工件的进给进度,有两种指定方式,即代码法和直接给定法。
现代的CNC机床在进给速度范围内一般都实现了无级变速,故采用直接指定方式。
直接给定法是在F后面直接写上进给速度值,进给量的单位用G94和G95来指定。
G94表示进给速度与主轴速度无关的每分钟进给量,单位为mm/min;G95表示与主轴转速有关的主轴每转进给量,单位为mm/r,如车螺纹、攻丝等。
在低档数控系统中多数还采用代码法来指定进给速度,用F00~F99表示100种进给速度。
2.主轴转速功能指令S转速功能指令S用来指定主轴转速或速度,单位为r/min或m/min。
中档以上数控机床的主轴转速采用直接指定方式。
例如S1500表示主轴转速为1500r/min。
在经济型数控系统中,仍主要用代码法指定方式。
对于中档以上的数控机床,还有一种使切削线速度保持不变的所谓恒线速度功能,这时需用G96和G97指令配合S指令来指定主轴转速。
例如G96 S160表示控制主轴转速,使切削点的线速度始终保持在160m/min,G97 S1000表示注销G96,即主轴不是恒线速度,其转速为1000r/min。
应指出的是,当由G96转为G97时,应对S码赋值,否则将保留G96指令的最终值。
当由G97转为G96时,若没有S指令,则按前一G96所赋S值进行恒线速度控制。
3.刀具功能指令T刀具功能指令T后面跟若干位数字,主要用来选择刀具,也可用来选择刀具偏置。
例如,T12用作选刀时表示12号刀具;用作刀具补偿时,表示按照12号刀具事先设定的偏置值进行刀具补偿。
若用四位数字时,如T0101,前两位01表示刀具号,后两位01表示刀具补偿号。
金属切屑刀具设计——圆体成形车刀、棱体成形车刀、圆拉刀的设计
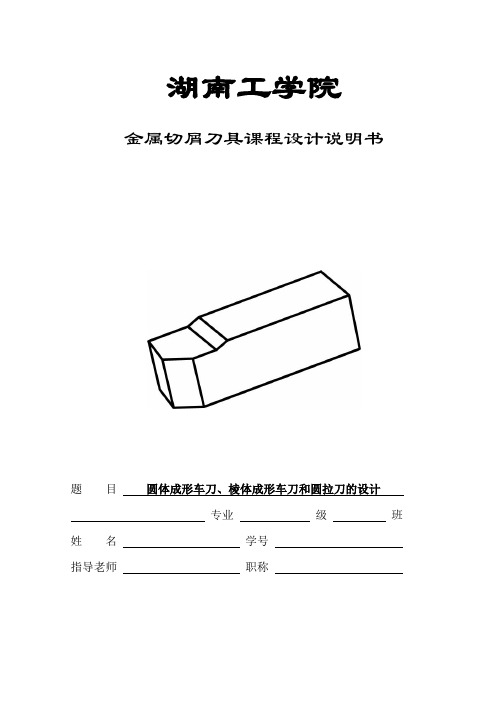
湖南工学院金属切屑刀具课程设计说明书题目圆体成形车刀、棱体成形车刀和圆拉刀的设计专业级班姓名学号指导老师职称圆体成形车刀设计设计说明及计算备注设计课题:工件如下图所示,材料为ζb=0.65GPa碳钢棒料,成形表面粗糙度为Ra3.2um,在C1336型单轴自动车床上加工。
要求设计圆体成形车刀。
设计步骤如下:1) 选择刀具材料查高速钢牌号及用途表,选用普通高速钢W18Cr4V制造。
2) 选择前角γf及后角αf根据材料的力学性能,查成形车刀的前角和后角表得:γf=10°,αf=12°。
3)画出刀具廓形(包括附加刃)计算图如下取k r=20°,a=2mm,b=1.5mm,c=5mm,d=1mm。
标出工作廓形各组成点1-12。
以0-0线(通过9-10段切削刃)为基准(以便于对刀),计算出1-12各点处的计算半径r jx(为避免尺寸偏差值对计算准确性的影响,故常采用计算尺寸、计算半径、计算长度和计算角度来计算):a、b、c、d ------ 成形车刀的附加刀刃;a ------ 为避免切削刃转角处过尖而设的附加刀刃宽度,常取为0.5—3mm;b ------ 为考虑工件端面的精加工和倒角而设的附加刀刃宽度,其数值应大于端面精加工余量和倒角宽度。
为使该段刀刃在主剖面内有一定后角,常做成偏角k r=15°--45°,b值取为1—3mm;如工件有倒角,k r值应等于倒角角度值,b值比倒角宽度大1—1.5mm;c ------ 为保证后续切断工序顺利进行而设的预切槽刀刃宽度,c值常取3—8mm;d ------ 为保证成形车刀刃延长到工件毛坯表面之外而设的附加刀刃宽度,常取d=0.5—2mm。
高速钢牌号及用途表出自金属切削刀具设计简明手册第113页附表5。
注:在本课程设计中本书后面简称刀具设计手册。
成形车刀前角和后角表见刀具设计手册第28页表2-4。
r jx=基本半径±(半径公差/2) r j1=22.64/2mm=11.32mmr j2=28/2mm=14mmr j4=25/2mm=12.5mm再以1点为基准点,计算出计算长度l jxl j2=10mml j3=20mml j4=27mml j5=35mm4) 计算切削刃总宽度Lc ,并校验Lc/d min 之值 Lc=lj5+a+b+c+d=35+2+1.5+5+1=44.5mm d min =2×rj1=2×11.32=22.64mm 则5.29655.164.225.44min <==mmmmd L c ,允许。
车刀图解

刀杆的形状、尺寸及选择
刀杆:45钢 截面形状:矩形、正方形、圆形。常用矩形。 矩形和方形刀杆的截面尺寸,一般按机床中心高选取。 刀头尺寸:刀头有效长度l、刀尖偏距m
刀槽的形状、 刀槽的形状、尺寸及选择
刀槽形状:通式、半封闭式、封闭式、切口式
2.2 机夹式车刀
结构比较复杂 常用的两种结构形式:上压式、侧压式 上压式 多用螺钉和压板从上向下施力压紧刀片,结构简 单,使用方便可靠。 侧压式 利用楔形块和螺钉从刀片侧面将刀片压紧,刀片 上无障碍,排屑顺畅。
h = R ⋅ sin(γ + α ) 重磨前刀面时,必须保持h不变。为便是控制, H = R ⋅ sin α 刀具两端面上刻有刃磨检验园。半径(mm) 式中:R — 圆体成形车刀最大外圆
c 1 f f 1 f
钢料:rf=5°~10°,抗拉强度高的取小值,反之取大值; 铸铁: rf=0°~10°,硬度高的取小值,反之取大值; 成形车刀的后角取决于其种类。圆体形车刀:αf=10º ~12º 棱体形车刀:αf=12º ~15º
成形车刀的类型
按外形和结构分: 平体成形车刀 切削刃为成形刃,其它与普通刀具结构相似 棱体成形车刀 外形棱柱体,刚性好,寿命长 圆体成形车刀 带有刀孔的回转体 按进给方向分:进向成形车刀、切向成形车刀
成形车刀的前角、后角
成形车刀切削刃形状复杂,有直线部分,也有曲线部分, 各段的主剖面方向互不相同,为简便起见,规定:成形车 刀的前角、后角均在假定工作平面内度量,并以切削刃上 最外一点(工件上半径最小处的点)的侧前角、侧后角作 为刀具的名义前角、后角。 前角、后角的形成 只刃磨前刀面,预先磨出一定的角度,再相对工件装 夹成一定位置,分别形成需要的前角、后角。
2.3 可转位车刀
利刀的形状和设计有哪些特点?
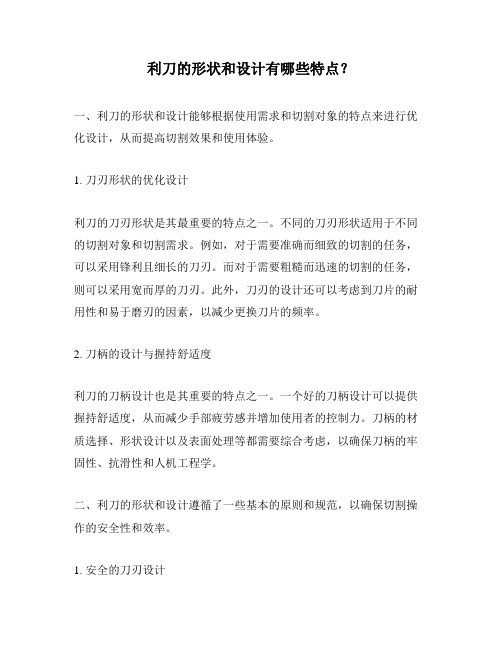
利刀的形状和设计有哪些特点?一、利刀的形状和设计能够根据使用需求和切割对象的特点来进行优化设计,从而提高切割效果和使用体验。
1. 刀刃形状的优化设计利刀的刀刃形状是其最重要的特点之一。
不同的刀刃形状适用于不同的切割对象和切割需求。
例如,对于需要准确而细致的切割的任务,可以采用锋利且细长的刀刃。
而对于需要粗糙而迅速的切割的任务,则可以采用宽而厚的刀刃。
此外,刀刃的设计还可以考虑到刀片的耐用性和易于磨刃的因素,以减少更换刀片的频率。
2. 刀柄的设计与握持舒适度利刀的刀柄设计也是其重要的特点之一。
一个好的刀柄设计可以提供握持舒适度,从而减少手部疲劳感并增加使用者的控制力。
刀柄的材质选择、形状设计以及表面处理等都需要综合考虑,以确保刀柄的牢固性、抗滑性和人机工程学。
二、利刀的形状和设计遵循了一些基本的原则和规范,以确保切割操作的安全性和效率。
1. 安全的刀刃设计利刀的刀刃设计需要遵循一些安全性原则,以避免在切割过程中出现危险。
例如,刀刃的形状不应该存在突出的尖锐部分,以防止意外划伤。
同时,易于控制的刀刃形状和设计也可以减少切割时的滑动和划伤危险。
2. 刀柄的防滑设计由于切割工作往往需要一定的力量,因此利刀的刀柄设计需要具备防滑的特性,以确保切割操作的稳定性。
采用防滑材质、设计凹槽或刻痕等方式,可以有效提高刀柄的防滑性能,使操作更加安全稳定。
三、利刀的形状和设计还与切割对象的特点有关。
1. 不同切割对象的特点不同的切割对象有不同的特点,例如硬度、尺寸、形状等。
因此,利刀的形状和设计需要根据切割对象的特点来进行优化。
例如,对于硬度较高的材料,需要采用耐磨性更强的刀刃材料和结构设计,以保证刀刃的寿命和切割效果。
2. 需求适应性设计利刀的形状和设计还可以根据不同切割需求的适应性进行优化。
例如,对于需要切割复杂曲线的任务,可以设计弯折可调的刀刃,以提供更灵活的操作和切割方式。
而对于需要连续切割的任务,则可以设计多刀片结构,以提高切割效率。
盾构机械刀盘及刀具设计与优化

盾构机械刀盘及刀具设计与优化随着城市地下空间的不断开发和利用,盾构机械在地铁、隧道等工程领域中得到了广泛应用。
盾构机械的刀盘及刀具是决定其施工质量和效率的重要因素之一。
本文将重点讨论盾构机械刀盘及刀具的设计与优化。
1. 刀盘设计1.1 刀盘结构设计刀盘是盾构机械的核心部件之一,其结构设计的合理性对盾构机械的工作效果有着重要的影响。
刀盘的结构设计应该考虑以下几个方面:1.1.1 刀盘刚度设计刀盘的刚度设计直接影响到刀具在施工过程中的稳定性和耐久性。
应该根据盾构机械的工作条件和土壤的物理特性,合理选择刀盘的材料和结构尺寸,确保刀盘具有足够的刚度。
1.1.2 刀盘模块化设计刀盘的模块化设计可以极大地提高刀具更换的效率,并且便于维护和保养。
刀盘的模块化设计应该考虑到刀具的安装和拆卸便捷性,同时也要保证刀具的工作性能。
1.1.3 刀盘防护设计刀盘的防护设计不仅能够保护刀具,在施工过程中还能够减少对环境的影响。
刀盘的防护设计应考虑到刀具的精度和平衡性,同时也要与盾构机械的其它部件协调配合。
1.2 刀盘传动系统设计刀盘传动系统是盾构机械的另一个重要部分,其设计的合理性对盾构机械的运行效果至关重要。
刀盘传动系统设计应该考虑以下几个方面:1.2.1 传动效率设计传动效率直接关系到盾构机械的工作效率。
刀盘传动系统的设计应该尽可能地提高传动效率,降低能量损耗。
1.2.2 齿轮设计齿轮是刀盘传动系统中常用的传动元件,其设计应考虑到负载分配、噪声控制等方面的需求。
合理选择齿轮的材料和结构尺寸,可以提高刀盘传动系统的可靠性和耐久性。
1.2.3 传动稳定性设计传动稳定性是刀盘传动系统设计时需要充分考虑的因素,合理选择传动比、减小晃动等措施,可以提高刀盘传动系统的稳定性。
2. 刀具设计与优化2.1 刀具材料选择刀具材料的选择直接影响到刀具的硬度、韧性和耐磨性等性能。
应根据盾构机械工作的土壤条件和设计要求,选择适合的刀具材料,以确保刀具有良好的工作性能和寿命。
留磨滚刀的设计和应用

80
机械传动
2 S 为零位线和上偏差线间的距离, 1
2008 年
零;
单边法向齿厚
须放在补偿区。如果把
都放在留磨区中 , 会造成
上偏差, 是定值 ;
为主刀刃和上偏差线间的距离 , 留
热前滚齿无补偿区, 热后磨齿 余量过大, 且出磨齿台 阶, 这是目前国内外一些工厂留磨滚刀设计和使用中 广泛存在的误区 ; 类似的道理 , 如果把 都放在补偿 区中 , 会造成热后胀大量小于补偿量, 出现齿面磨不出 来的情况。 对于大直径中小模数的齿轮或齿圈 , 热处理后公 法线长度的胀大量会远大于滚刀的挖根量 , 这时滚齿 的公法线长度甚至会小于最终磨齿尺寸 , 留磨量完全 靠热后胀大补偿。滚齿刀具的设计和滚齿参数的选择 必须综合考虑以上因素。
1
留磨滚刀的基本形式和参数
为了留出磨齿余量 , 避免磨齿时磨到齿根造成应
为过渡刃切线的切点 , 这一点和 A 点的距离和过渡刃 压力角大小有关。 1. 2 留磨滚刀 3 个最重要参数 刀具齿顶高 h a0 , 刀具 齿顶圆角半 径 h a 0高 , 小 , 不利于弯曲强度 ; h a0 短,
F,
力集中及释放齿根压应力或产生拉应力 , 渗碳淬火磨 齿的渐开线硬齿面齿轮已广泛采用带有一定挖根量的 单圆 弧留 磨滚 刀, 也称 凸头 留磨 滚刀。 GB/ T13562001 ( idt ISO 53: 1998)
第 32 卷
第2期
留磨滚刀的设计和应用
79
文章编号 : 1004- 2539( 2008) 02- 0079- 03
留磨滚刀的设计和应用
( 宝钢集团苏州冶金机械厂 , 江苏 苏州 215151)
李钊刚
摘要
系统地讨论了渐开线硬齿面齿轮留磨滚刀的设计和应用 。指出留磨滚刀的挖根量应分为 3
专用机床的刀具进给机构和工作台转位机构设计

Байду номын сангаас
专用机床的定义和特点
总结词
专用机床广泛应用于汽车、航空、能源、电子、医疗器械等众多领域。
详细描述
专用机床因其高精度和高效率的特点,被广泛应用于汽车、航空、能源、电子、医疗器械等众多领域。在汽车行业中,专用机床用于加工发动机缸体、变速器齿轮等关键零部件;在航空领域,专用机床用于加工飞机结构件和发动机零件;在能源领域,专用机床用于加工核反应堆和风力发电设备的核心部件;在电子行业,专用机床用于加工微型电子元件和精密模具;在医疗器械领域,专用机床用于加工人工关节、牙科种植体等医疗器件。
01
利用有限元分析等方法,对机床的强度和刚度进行详细分析,确保满足使用要求。
02
对关键部件进行强度和刚度校核,确保其在各种工况下的安全性和可靠性。
专用机床的强度和刚度分析
专用机床的性能分析和优化
05
对专用机床的运动学特性进行分析,包括运动轨迹、速度和加速度等,以确定机床的动态性能和精度。
根据运动学分析结果,对机床的结构和布局进行优化,以提高其运动性能和加工精度。
专用机床的总体布局
选择合适的传动方式,如机械传动、液压传动或电气传动,以满足加工要求和提高机床性能。
根据机床总体布局,设计合理的支撑结构,确保机床的稳定性和刚度。
优化设计关键部件,如主轴箱、导轨、丝杠等,以提高机床的加工精度和使用寿命。
专用机床的结构设计
03
根据分析结果,对机床结构进行优化,提高其动态特性和热稳定性。
改进建议
根据性能优化结果,提出针对性的改进建议,包括材料选择、热处理工艺和装配精度等,以完善机床的整体性能。
THANKS
感谢观看
校核和优化设计
刀具说明书(完整版).docx

圆孔拉刀及矩形花键铣刀设计说明书前言 (1)绪论 (2)三刀具设计 (3)(一)矩形花键铣刀的设计 (3)1齿形设计计算 (3)2结构参数选择计算............................3矩形花键铣刀的技术条件 (5)4刀具的全部计算 (7)(二)圆孔拉刀的设计 (8)1选定刀具类型、材料的依据 (8)2刀具几何参数的选择设计 (9)15四总结五致谢 (16)六参考文献 (17)、八一、冃IJ 言大学三年的学习即将结束,在我们即将进入大四,踏入社会之前,通过课程设计来检查和考验我们在这几年中的所学,同时对于我们自身来说,这次课程设计很贴切地把一些实践性的东西引入我们的设计中和平时所学的理论知识相关联。
为我们无论是在将来的工作或者是继续学习的过程中打下一个坚实的基础。
我的课程设计课题目是矩形花键拉刀与矩形花键铣刀的设计。
在设计过程当中,我通过查阅有关资料和运用所学的专业或有关知识,比如零件图设计、金属切削原理、金属切削刀具、以及所学软件AUTOCA的运用,设计了零件的工艺、编制了零件的加工程序等。
我利用此次课程设计的机会对以往所有所学知识加以梳理检验,同时又可以在设计当中查找自己所学的不足从而加以弥补,使我对专业知识得到进一步的了解和系统掌握。
由于本人水平有限,设计编写时间也比较仓促,在我们设计的过程中会遇到一些技术和专业知识其它方面的问题,再加上我们对知识掌握的程度,所以设计中我们的设计会有一些不尽如人意的地方,为了共同提高今后设计设计的质量,希望在考核和答辩的过程中得到各位指导老师的谅解与批评指正,不胜感激之至•、绪论2.1刀具的发展随着社会的发展,时代的进步,刀具在生产中的用途越来越广•刀具的发展在一定程度上决定着生产率,中国加入WTO后,各行各业面临的竞争越来越激烈,一个企业要有竞争力,其生产工具必须具有一定的先进性•中国作为一个农业大国,其在机械方面的发展空间相当大,而要生产不同种类的零件,不管其大小与复杂程度,都离不开刀具•目前,在金属切削技术领域中,我国和先进的工业国家之间还存在着不小的差距,但这种差距正在缩小。
金属切削刀具设计简明手册

金属切削刀具设计简明手册
金属切削刀具设计简明手册主要包含以下内容:
1. 刀具的种类和用途:介绍各种金属切削刀具的种类、特点和用途,如车刀、铣刀、钻头、丝锥等。
2. 刀具材料的选择:介绍刀具材料的种类、性能和适用范围,如高速钢、硬质合金、陶瓷等。
同时,还介绍了涂层刀具的基本知识和应用。
3. 刀具几何参数的设计:详细介绍了各种刀具的几何参数,如前角、后角、主偏角、副偏角等,以及这些参数对切削过程的影响和如何选择合适的参数。
4. 切削用量的选择:介绍了切削速度、进给量、切削深度等切削用量的选择原则和方法,以及如何根据不同的切削条件选择合适的切削用量。
5. 刀具的失效形式和预防措施:介绍了刀具在切削过程中可能出现的失效形式,如磨损、断裂、崩刃等,以及预防措施和刀具寿命的延长方法。
6. 切削液的选择和使用:介绍了切削液的种类、性能和适用范围,以及如何选择合适的切削液和正确地使用切削液。
7. 典型零件的加工工艺:以实际生产中常见的典型零件为例,介绍了从毛坯到成品的整个加工工艺过程,包括刀具的选择、切削用量的确定等。
8. 先进制造技术简介:简要介绍了现代制造技术的新发展,如数控加工、超精密加工、快速原型制造等,以及这些技术对金属切削刀具设计的影响。
以上内容可以帮助工程技术人员进行金属切削刀具的设计和选用,提高生产效率和加工质量。
刀片F计算公式
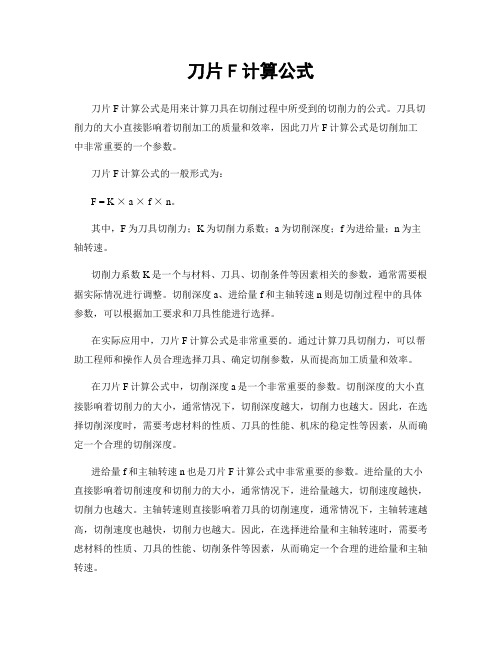
刀片F计算公式刀片F计算公式是用来计算刀具在切削过程中所受到的切削力的公式。
刀具切削力的大小直接影响着切削加工的质量和效率,因此刀片F计算公式是切削加工中非常重要的一个参数。
刀片F计算公式的一般形式为:F = K × a × f × n。
其中,F为刀具切削力;K为切削力系数;a为切削深度;f为进给量;n为主轴转速。
切削力系数K是一个与材料、刀具、切削条件等因素相关的参数,通常需要根据实际情况进行调整。
切削深度a、进给量f和主轴转速n则是切削过程中的具体参数,可以根据加工要求和刀具性能进行选择。
在实际应用中,刀片F计算公式是非常重要的。
通过计算刀具切削力,可以帮助工程师和操作人员合理选择刀具、确定切削参数,从而提高加工质量和效率。
在刀片F计算公式中,切削深度a是一个非常重要的参数。
切削深度的大小直接影响着切削力的大小,通常情况下,切削深度越大,切削力也越大。
因此,在选择切削深度时,需要考虑材料的性质、刀具的性能、机床的稳定性等因素,从而确定一个合理的切削深度。
进给量f和主轴转速n也是刀片F计算公式中非常重要的参数。
进给量的大小直接影响着切削速度和切削力的大小,通常情况下,进给量越大,切削速度越快,切削力也越大。
主轴转速则直接影响着刀具的切削速度,通常情况下,主轴转速越高,切削速度也越快,切削力也越大。
因此,在选择进给量和主轴转速时,需要考虑材料的性质、刀具的性能、切削条件等因素,从而确定一个合理的进给量和主轴转速。
在实际应用中,刀片F计算公式的准确性和合理性对于切削加工的质量和效率有着非常重要的影响。
通过合理选择切削参数,可以有效降低切削力,减少刀具磨损,提高加工质量和效率。
在实际应用中,刀片F计算公式还可以帮助工程师和操作人员进行切削力的预测和优化。
通过计算不同切削参数下的切削力,可以帮助工程师和操作人员选择最佳的切削参数,从而提高加工质量和效率。
总之,刀片F计算公式是切削加工中非常重要的一个参数。
超声波加工机床的刀具设计与材质选择
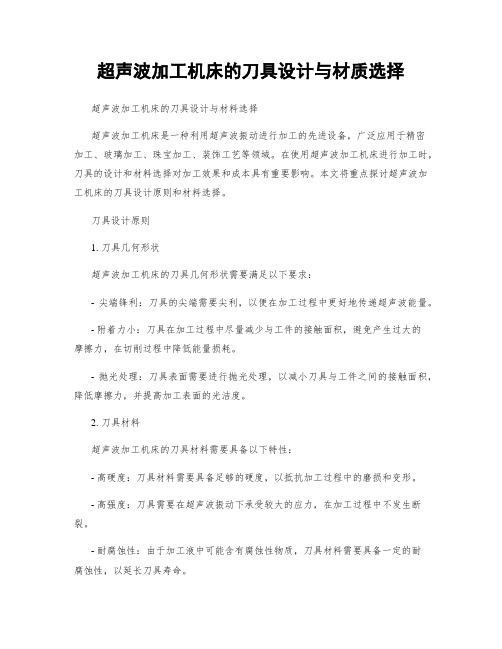
超声波加工机床的刀具设计与材质选择超声波加工机床的刀具设计与材料选择超声波加工机床是一种利用超声波振动进行加工的先进设备,广泛应用于精密加工、玻璃加工、珠宝加工、装饰工艺等领域。
在使用超声波加工机床进行加工时,刀具的设计和材料选择对加工效果和成本具有重要影响。
本文将重点探讨超声波加工机床的刀具设计原则和材料选择。
刀具设计原则1. 刀具几何形状超声波加工机床的刀具几何形状需要满足以下要求:- 尖端锋利:刀具的尖端需要尖利,以便在加工过程中更好地传递超声波能量。
- 附着力小:刀具在加工过程中尽量减少与工件的接触面积,避免产生过大的摩擦力,在切削过程中降低能量损耗。
- 抛光处理:刀具表面需要进行抛光处理,以减小刀具与工件之间的接触面积,降低摩擦力,并提高加工表面的光洁度。
2. 刀具材料超声波加工机床的刀具材料需要具备以下特性:- 高硬度:刀具材料需要具备足够的硬度,以抵抗加工过程中的磨损和变形。
- 高强度:刀具需要在超声波振动下承受较大的应力,在加工过程中不发生断裂。
- 耐腐蚀性:由于加工液中可能含有腐蚀性物质,刀具材料需要具备一定的耐腐蚀性,以延长刀具寿命。
- 导声性能:刀具材料需要具备良好的导声性能,以便更好地传递超声波能量。
常用的刀具材料包括硬质合金(钨钢)、工具钢和陶瓷材料等。
硬质合金具有高硬度和较高的耐磨性,但耐腐蚀性和导声性能相对较差;工具钢具有较好的耐腐蚀性和导声性能,但硬度和耐磨性相对较低;陶瓷材料具有良好的导声性能和耐磨性,但脆性较高。
材料选择在选择超声波加工机床刀具的材料时,需要根据具体的加工要求和材料特性进行综合考虑。
1. 对于硬度较高的工件材料,如玻璃、石英等,可以选择使用硬质合金或工具钢作为刀具材料。
硬质合金的硬度较高,能够满足对硬度要求较高的加工工艺,并具有较好的耐磨性,适用于长时间的连续加工。
而工具钢则在一定硬度和耐磨性的同时,具备较好的导声性能和一定的韧性,适用于对刀具寿命有要求但对加工表面要求较高的情况。
非标刀具设计指导书

《机械制造技术》课程设计1.金属切削刀具设计的目的金属切削刀具课程设计是学生在学完《机械制造技术》课程的基础上进行的重要的实践性教学环节,其目的是使学生巩固和深化课堂理论教学内容,锻炼和培养学生综合运用所学知识和理论的能力,是对学生进行独立分析、解决问题能力的强化训练。
通过金属切削刀具课程设计,具体应使学生做到:(1) 掌握金属切削刀具的设计和计算的基本方法;(2) 学会运用各种设计资料、手册和国家标难;(3) 学会绘制符合标准要求的刀具工作图,能标注出必要的技术条件。
2.金属切削刀具设计的内容完成圆孔拉刀、矩形花键拉刀、铰刀三种刀具的设计和计算工作,绘制刀具工作图和必要的零件图以及编写一份正确、完整的设计说明书。
刀具工作图应包括制造及检验该刀具所需的全部图形、尺寸、公差、粗糙度要求及技术条件等;设计说明书应包括设计时所涉及的主要问题以及设计计算的全部过程;设计说明书中的计算必须准确无误,所使用的尺寸、数据和计量单位,均应符合有关标准和法定计量单位;使用A4纸打印,语言简练,文句通顺。
3.金属切削刀具设计的步骤设计步骤●准备工作1)认真研究设计任务书,分析设计题目的原始数据和工作条件,明确设计内容和要求。
2)通过观看录像,参观实物或模型等形式,熟悉各种类型和结构的刀具,主要是拉刀和铰刀部分,分析它们的优缺点以及各自使用的场合。
3)查阅相关设计资料,例如《复杂刀具设计手册》,并分组进行讨论,准备设计用具,拟定设计计划。
●拉刀的设计计算拉刀是一种高生产率的刀具,可以用来加工各种形状的通孔、直槽、螺旋槽以及直线或曲线外表面,广泛的用于大量和成批生产中。
拉刀的种类虽多,但结构组成都类似。
如普通圆孔拉刀的结构组成为:柄部,用以夹持拉刀和传递动力;颈部,起连接作用;过渡锥,将拉刀前导部引入工件;前导部,起引导作用,防止拉刀歪斜;切削齿,完成切削工作,由粗切齿和精切齿组成;校准齿,起修光和校准作用,并作为精切齿的后备齿;后导部,用于支承工件,防止刀齿切离前因工件下垂而损坏加工表面和刀齿;后托柄,承托拉刀。
圆形成形刀具设计方案

圆形成形刀具设计方案圆形成形刀具设计方案一、设计目标本设计方案的目标是设计一种圆形成形刀具,用于在金属加工过程中进行圆形成形操作,具有高精度、高效率、易使用等特点。
二、设计原理圆形成形刀具的设计原理是利用刀具的切削作用,将金属材料按照设计要求进行圆形成形。
三、设计要求1. 刀具的材料要求具有良好的切削性能和耐磨性能;2. 刀具的设计要求符合人体工程学,易于操作;3. 刀具的设计要具有高精度和高效率的特点。
四、设计方案1. 刀具材料选择:选用硬质合金材料,具有良好的切削性能和耐磨性能。
2. 刀具形状设计:刀具的形状采用圆形设计,便于进行圆形成形操作。
3. 刀具刃口设计:刀具的刃口采用尖锐的设计,以增加切削效果。
4. 刀具手柄设计:刀具的手柄采用人体工程学设计,符合人体手部力学特点,易于操作。
5. 刀具定位设计:刀具的定位设计采用精确的定位方案,以确保圆形成形操作的精度。
6. 刀具尺寸设计:刀具的尺寸设计要根据具体应用需求进行合理确定,保证切削效果和使用便捷性。
五、设计流程1. 确定设计目标;2. 确定设计原理;3. 分析设计要求;4. 选择合适的刀具材料;5. 进行刀具形状设计;6. 进行刀具刃口设计;7. 进行刀具手柄设计;8. 进行刀具定位设计;9. 进行刀具尺寸设计;10. 进行刀具制造和试用;11. 对刀具进行测试和改进。
六、设计优势1. 刀具材料选用硬质合金,具有良好的切削性能和耐磨性能,增加刀具寿命;2. 刀具形状采用圆形设计,使刀具易于进行圆形成形操作;3. 刀具刃口采用尖锐的设计,增加切削效果;4. 刀具手柄采用人体工程学设计,易于操作;5. 刀具定位设计精确,确保切削精度;6. 刀具尺寸设计合理,保证切削效果和使用便捷性。
七、设计结果通过以上设计方案,可设计出一种圆形成形刀具,具有良好的切削性能、耐磨性能、高精度、高效率和易使用等特点,可广泛应用于金属加工领域。
刀具设计实施方案
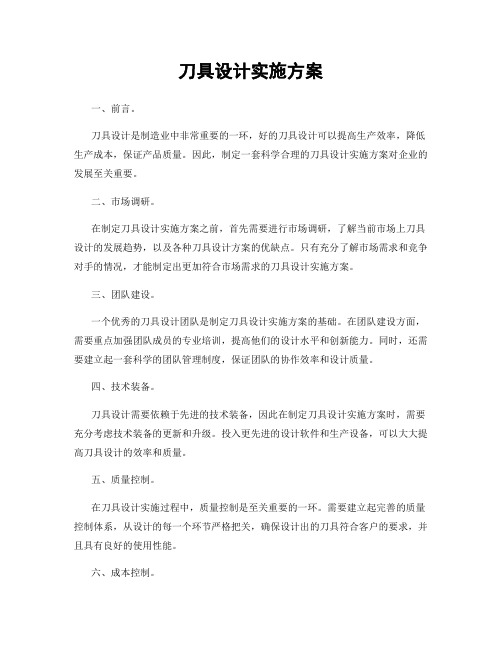
刀具设计实施方案一、前言。
刀具设计是制造业中非常重要的一环,好的刀具设计可以提高生产效率,降低生产成本,保证产品质量。
因此,制定一套科学合理的刀具设计实施方案对企业的发展至关重要。
二、市场调研。
在制定刀具设计实施方案之前,首先需要进行市场调研,了解当前市场上刀具设计的发展趋势,以及各种刀具设计方案的优缺点。
只有充分了解市场需求和竞争对手的情况,才能制定出更加符合市场需求的刀具设计实施方案。
三、团队建设。
一个优秀的刀具设计团队是制定刀具设计实施方案的基础。
在团队建设方面,需要重点加强团队成员的专业培训,提高他们的设计水平和创新能力。
同时,还需要建立起一套科学的团队管理制度,保证团队的协作效率和设计质量。
四、技术装备。
刀具设计需要依赖于先进的技术装备,因此在制定刀具设计实施方案时,需要充分考虑技术装备的更新和升级。
投入更先进的设计软件和生产设备,可以大大提高刀具设计的效率和质量。
五、质量控制。
在刀具设计实施过程中,质量控制是至关重要的一环。
需要建立起完善的质量控制体系,从设计的每一个环节严格把关,确保设计出的刀具符合客户的要求,并且具有良好的使用性能。
六、成本控制。
刀具设计实施方案的制定也需要考虑到成本控制的问题。
需要在提高设计质量的同时,尽量降低设计成本,提高企业的竞争力。
可以通过优化设计流程、提高设计效率等途径来降低设计成本。
七、市场推广。
制定完刀具设计实施方案后,还需要进行市场推广工作。
可以通过参加行业展会、举办技术交流会等方式,向客户展示公司的设计实力和创新能力,提升企业的知名度和美誉度。
八、总结。
刀具设计实施方案的制定是一个系统工程,需要全面考虑市场需求、团队建设、技术装备、质量控制、成本控制等多个方面的因素。
只有全面、科学的制定刀具设计实施方案,才能更好地推动企业的发展,提升企业的竞争力。
刀具设计减震原理及应用

刀具设计减震原理及应用刀具设计中的减震原理及应用涉及到刀具的结构、材料选择和使用环境等方面。
有效的减震设计可以减轻刀具振动对切削质量、刀具寿命和机床精度的不利影响,提高切削效率和加工质量。
下面将从刀具结构设计、材料选择和减震应用方面进行详细阐述。
刀具结构设计是减震设计的基础。
优秀的刀具结构设计可以减少切削振动,降低切削力和切削温度,提高切削稳定性和加工精度。
常见的刀具结构设计包括刀柄结构、刀片结构和切削辅助装置。
刀柄结构是刀具振动传递的关键部位之一。
在刀柄设计中,常采用独立刀柄和整体刀柄两种结构形式。
独立刀柄结构可以通过调整刀柄材料和形状来改变刀具的振动特性,减少刀具振动。
整体刀柄结构则可以提高刀具的刚度和稳定性,减弱切削振动。
此外,刀柄还可以采用中空结构,通过填充流体或填充刚性材料来减小切削振动。
刀片结构是刀具减震设计的另一个关键点。
刀片结构的合理设计可以降低切削振动和切削力,提高切削效率和切削质量。
常见的刀片结构设计包括面刀片、侧刀片和刀片吊形式。
面刀片结构适用于切削力较大的情况,它具有较大的刀片刚度和稳定性,可以减小切削振动。
侧刀片结构适用于切削力较小的情况,它具有较小的刀片刚度和稳定性,可以减轻切削振动。
刀片吊形式是通过刀片系统的吊装设计来实现减震效果,通过刀片的柔性悬挂减小切削振动。
切削辅助装置是减震设计的重要手段之一。
切削辅助装置可以采用振动切削刀具、自激振动切削刀具、振动刀具切削等方式来减小切削振动和提高加工精度。
振动切削刀具是通过引入激振器来实现刀具振动的方式,通过调节激振频率和振幅来减小切削振动。
自激振动切削刀具是通过刀片系统自身的刚度和阻尼来实现振动切削,通过调节刀片系统的阻尼比和频率来减小切削振动。
振动刀具切削是通过刀具振动产生波纹切削的方式来减小切削振动。
刀具材料的选择也是减震设计的重要因素之一。
材料的刚度和阻尼是减震设计的关键要素。
刚度高的材料可以提高刀具的刚度和稳定性,减小切削振动;阻尼大的材料可以吸收和消散切削振动的能量,减小切削振动。
刀具课程设计任务16

刀具课程设计任务16一、教学目标本课程的教学目标是让学生了解和掌握刀具的基本知识、使用方法和维护技巧。
通过本课程的学习,学生应能够:1.描述刀具的种类、结构和功能。
2.解释刀具的工作原理和材料。
3.演示正确使用和维护刀具的方法。
4.分析刀具在实际应用中的优势和局限。
二、教学内容本课程的教学内容主要包括以下几个部分:1.刀具的基本概念:介绍刀具的定义、分类和应用领域。
2.刀具的结构与功能:讲解刀具的各个部分的作用和功能,以及它们对刀具性能的影响。
3.刀具的材料:介绍常用刀具材料的特点和适用范围。
4.刀具的使用与维护:教授正确使用刀具的方法,以及如何进行日常维护和保养。
5.刀具的应用案例:分析刀具在实际工作中的应用实例,探讨其优势和局限。
三、教学方法为了提高学生的学习兴趣和主动性,本课程将采用多种教学方法:1.讲授法:讲解刀具的基本概念、结构和材料等理论知识。
2.讨论法:学生讨论刀具的使用技巧和实际应用案例,促进学生思考和交流。
3.案例分析法:分析具体的刀具应用案例,让学生深入了解刀具在实际工作中的作用。
4.实验法:安排实验室实践环节,让学生亲自动手操作,掌握刀具的使用和维护方法。
四、教学资源为了支持教学内容和教学方法的实施,我们将准备以下教学资源:1.教材:选用权威、实用的刀具教材,为学生提供系统、全面的理论知识。
2.参考书:提供相关的刀具专业书籍,丰富学生的知识体系。
3.多媒体资料:制作精美的PPT、视频等教学课件,增强课堂的趣味性。
4.实验设备:准备充足的刀具实验设备,确保每个学生都能在实验环节亲身体验。
五、教学评估本课程的评估方式将包括以下几个方面:1.平时表现:通过观察学生在课堂上的参与程度、提问和回答问题的表现,评估其学习态度和积极性。
2.作业:布置适量的作业,评估学生对课程内容的理解和掌握程度。
3.考试:进行定期的考试,全面考察学生对刀具知识的掌握情况,包括理论知识和实际应用能力。
六、教学安排本课程的教学安排如下:1.教学进度:按照教材的章节顺序进行教学,确保每个章节都有足够的教学时间。
PDC刀具设计要素的选择原则

PDC刀具设计要素的选择原则I. 研究背景与目的A. PDC刀具的定义和应用B. 需求和问题的分析C. 研究目的II. PDC刀具设计要素概述A. 刀体设计B. 刀尖设计C. 刀片设计D. 组合设计III. PDC刀具设计要素选择的主要原则A. 刀体、刀尖和刀片的选择原则B. 单一要素的优缺点及其对刀具性能的影响C. 组合选择原则D. 常见方法IV. PDC刀具设计要素的分层次分析与决策A. 分层次分析方法B. 刀具设计要素的重要性分析C. 决策结果的评价V. 结论与展望A. 结论B. 展望VI. 参考文献I. 研究背景与目的A. PDC刀具的定义和应用PDC刀具是一种结合了超硬材料与金属材料的先进切削工具。
PDC全称“Poly-crystalline Diamond Compact”,即多晶金刚石复合材料。
它由金属材料基体与在其上涂层的超硬(金刚石)材料制成,通过多种切削工艺加工成具备优异切削能力的工具。
这种刀具具有强度高、硬度高、寿命长、使用成本相对较低、可靠性好等特点,广泛应用于机械制造领域,是高效、精度的重要保障。
B. 需求和问题的分析PDC刀具在生产制造过程中扮演着重要的角色,但其性能问题和使用成本问题也不容忽视。
目前,PDC刀具的性能问题主要包括其硬度差异导致的失效和断裂问题,以及使用成本较高等问题。
而解决这些问题的关键在于正确选择PDC刀具的设计要素,并合理组合,以提高刀具的性能、使用寿命和降低成本。
因此,本论文旨在探讨PDC刀具设计要素的选择原则,以帮助生产企业更好地选择、使用优秀的PDC刀具。
C. 研究目的本论文的主要目的是探究PDC刀具设计要素的选择原则,以提高刀具性能和使用效果。
具体地,研究要点包括:(1)PDC刀具设计要素的概述;(2)PDC刀具设计要素选择的主要原则;(3)PDC刀具设计要素的分层次分析和决策;(4)提高刀具设计与制造的技术和方法。
综上,本论文的目的是为帮助生产企业选择、使用高质量的PDC刀具,提高制造效率、减少生产成本,推进企业生产加工的发展,提高企业的竞争力。
- 1、下载文档前请自行甄别文档内容的完整性,平台不提供额外的编辑、内容补充、找答案等附加服务。
- 2、"仅部分预览"的文档,不可在线预览部分如存在完整性等问题,可反馈申请退款(可完整预览的文档不适用该条件!)。
- 3、如文档侵犯您的权益,请联系客服反馈,我们会尽快为您处理(人工客服工作时间:9:00-18:30)。
F2专用刀具设计思考题
1什么是孔加工复合刀具?
2孔加工复合刀具分类?举例说明.
3孔加工复合刀具设计要点?容屑及排屑如何考虑?
4组合机床上用孔加工复合刀具时切削用量如何选择?(切削速度按刀具的最大直径选择,进给量按刀具的最小直径选择。
) 5孔加工复合刀具的导向装置结构形式?
6备磨量?
F3
1拉削方式(拉削图形)有几种?各有什么优缺点?
2分层式拉削和分块式拉削的齿升量
3圆孔拉刀设计为什么常采用组合式结构?其中校准齿具有什么作用?(粗切齿采用分块式结构,精切齿采用成形式结构。
4粗切齿为什么需要设计有分屑槽?而精切齿的后角为什么取值较小?
5设计拉刀时,为什么要考虑容屑问题?(影响容屑系数的因素有哪些?)
答案
F2
1.孔加工复合刀具是由两把或两把以上单个孔加工刀具结合在一个刀体上形成的专用刀具。
2举例;
同类:复合钻,复合扩孔钻,复合铰,镗,丝锥
不同类:钻-扩复合刀具,钻-扩-胶复合刀具,钻-攻复合刀具
3孔加工复合刀具设计要点
合理选择刀具材料
,合理选择结构形式,
重视容屑及排屑问题
,应保证良好的导向,
正确确定刀具总长度
4孔加工复合刀具切削用量的选择
1)进给量按复合刀具中的最小直径的单个刀具选择。
(2)切削速度按复合刀具中的最大直径的单个刀具选择。
(3)各刀具有相同的每秒进给量。
(4)选择切削用量时,要考虑各单个刀具的特点。
5导向装置结构形式有多种,
一般可分为固定式及旋转式两大类。
旋转式导向装置-与一般轴承无原则区别
合理选择结构形式
1)从保证刀具足够的强度和刚度来选择结构形式
2)从保证工件加工精度及表面质量来选择结构形式
3)从保证合理的使用寿命来选择结构形式
4)从保证刃磨方便来选择结构形式
重视容屑及排屑问题
容屑空间不够或排屑不畅通,则会造成前、后刀齿切下的切屑互相干扰和阻塞,致使刀齿崩裂甚至刀具折断
1)加大容屑空间
2)排屑应畅通
F3
1圆孔拉刀为什么采用组合式机构?
综合式(组合式)拉削方式,将拉刀的粗切齿采用分块式(轮切式)结构,精切齿采用成形式结构。
因此,缩短了拉刀的长度,保持较高的生产率,获得较好的工件加工精度和表面质量。
我国生产的圆孔拉刀较多地采取这种结构。
其余的见笔记
2分块式拉削方式每个刀齿参加工作的切削刃的长度(即切削宽度)较短,在保持相同的拉削力的情况下,允许较大的齿升量(切削厚度) ,在拉削余量一定时,分块式拉刀所需的刀齿总数要少很多,故拉刀长度大大缩短。
3圆孔拉刀为什么采用组合式机构?
校准齿的作用?
校准齿: 拉刀最后面的几个刀齿,它们直径都相同(与最后一个精切齿直径相等),不承担切削工作,仅起修光、校准作用。
4为什么需要设计分屑槽?
分屑槽的作用是将较宽的切屑分割成窄切屑,以便于切屑卷曲、容纳和清除
后角为什么取小值?
如后角取得大,刀齿直径就会减小得很快,拉刀使用寿命会显著缩短:因此,(内)拉刀切削齿后角都选得较小
5容屑槽
在拉削过程中,切下的切屑须全部容纳在容屑槽中,因此,容屑槽的形状和尺少应能保证较宽敞地容纳切屑,并尽量使切屑紧密卷曲。
为保证容屑空间和拉刀强度,在一定齿距下,可以选用浅槽或基本槽或深槽,以适应不同的要求。
F专用刀具设计主要知识点
1孔复合刀具的类型、应用及特点(总结)
2孔复合刀具的设计要点(题目)
3拉刀的类型、应用、结构特点(总结)
4拉刀切削部分的几何角度、结构参数(总结)
5拉削方式、特点及应用(总结)
1拉刀的(拉削)特点
1生产率高
2)拉削后工件精度与表面质量高
3)拉刀耐用度高.拉削速度低,切削温度低,每个刀齿实际参加切削的时间短
4)拉削加工应用范围广
5)拉削运动简单 .拉削加工只需要一个直线主运动,
由于拉刀结构比一般刀具复杂,制造成本高。
因此多用于成批大量生产
2拉刀切削部分结构要素
(1)几何角度
1)前角γ0:前刀面与基面的夹角,在正交平面内测量。
2)后角α0:后刀面与切削平面的夹角,在正交平面内测量。
3)主偏角kr:主切削刃在基面中的投影与进给方向(齿升量测量方向)的夹角,在基面内测量。
除成形拉刀外,各种拉刀的主偏角多为90°。
4)副偏角kr’:副切削刃在基面中的投影与已加工表面的夹角,在基面内测量
(2)结构参数
1)齿升量fz: 拉刀前后相邻两刀齿(或齿组)高度之差。
2)齿距p: 相邻刀齿间的轴向距离。
3)容屑槽深度h: 从顶刃到容屑槽槽底的距离。
4)齿厚g: 从切削刃到齿背棱线的轴向距离。
5)齿背角θ: 齿背与切削平面的夹角。
6)刃带宽度ba: 沿拉刀轴向测量的刀齿刃带尺寸。
3拉削方式及其特点
拉削方式可分为:分层式、分块式(轮切式)及组合式(综合式)
a分层式拉削
分层式拉削又分为成形式及渐成式两种。
(1)成形式
(2)每个刀齿的刀刃形状与被加工表面最终要求的形状相似,尺寸不同,切削齿的高度向后递增,工件上的拉削余量被一层一层地切去,由最后一个切削齿切出所要求的尺寸,经校准齿修光达到顶定的尺寸精度及表面粗糙度。
①成形式拉削的优点:
能获得较好的工件加工表面精度;加工平面和圆孔时,其拉刀齿齿形简单,制造容易。
②成形式拉削的缺点:a分屑槽与切削刃交界处呈尖角,散热条件差,刀齿磨损较快
b分屑槽使切屑表面形成一条加强筋,卷屑困难,需加大容屑空间。
由此刀齿切除的切屑很薄,需较多的刀齿才能切完余量。
成形式拉刀较长,耗费刀材,拉削生产率较低。
由于切削刃工作长度(切削宽度)大,则允许的齿升量(切削厚度)很小,在拉削余量一定时,需要较多的刀齿数,因此拉刀比较长。
(2)渐成式
刀齿的刀刃形状与加工最终表面形状不同,被加工工件表面的形状和尺寸由各刀齿的副切削刃所形成。
渐成式拉刀的制造比成形式简单
缺点在工件已加工表面上可能出现副切削刃的交接痕迹,使工件的加工表面质量稍差。
2.分块式拉削方式
分块式拉削工件上的每一层金属由一组尺寸基本相同的刀齿切去,每个刀齿仅切去一层金属的一部分。
优点:每个刀齿参加工作的切削刃的长度(即切削宽度)较短,在保持相同的拉削力的情况下,允许较大的齿升量(切削厚度),在拉削余量一定时,分块式拉刀所需的刀齿总数要少很多,故拉刀长度大大缩短。
缺点:因拉削厚度大,故拉削后的工件表面质量稍差。