专用刀具设计
刀具设计说明书

BXH=16x25 L=150mm M=6(90°外圆车刀) 半封闭槽
r =30°, j
rc =-12°, hc =20.04mm
C coso
hc
(1 ~
2) cos(
c)
=
25
6 cos8 cos(8 (12
))
=20.04mm
YT15 45 钢
=18°, =8°, ‘=8°,
o
o
o
3 几何角度
表 3-8,表 3-9
kr=90°Kr’=8°, =0, s
断屑参数 4 前刀面形
式
5 过渡刃
6 刀片形式 车刀外形
7结 构 尺 寸
8 刀槽形式
表 3-11,表 3-12(估计 f=0.35mm/r)
a 表 3-13(估计 p =1~1.5mm)
表 3-3(d)
表 3-1,表 3-2,表 3-5
表 3-4
r sin
j
ln 2qn
=
2.5 2 2.5
=
1 2
r r r c =
o-
=18°-30°=-12°
j
r 0.8mm
圆弧卷削槽前刀面
rn 2.5mm,Cn 0.3mm
br1 =0.2mm,Wn 2.5mm,
圆弧刃
r 0.8mm
A315
刀具设计说明书
1.工序尺寸精度分析
半精车外圆φ 62.4mm,尺寸精度约为 IT9,表面粗糙度约为 3.2um m
2.刀具类型确定
焊接式 90°外圆车刀
3.刀具设计参数确定
序 号
项目
1 车刀类型
整体合金立铣刀的设计
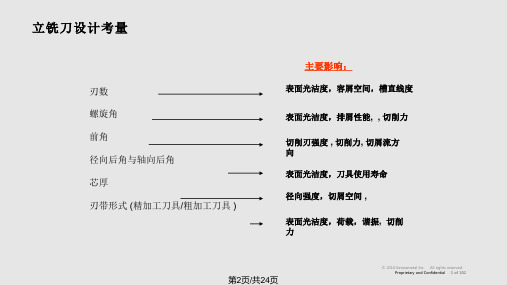
第3页/共24页
刀柄直径
立铣刀设计基本参数
侧视图
端视图
径向前角
主后角
轴向锲角 主后角
次后角
次后角
过中心刃
© 2010 Kennametal Inc. l All rights reserved. l Proprietary and Confidential l 3 of 102
凹角
锲角
第4页/共24页
切削面
次要后角
第10页/共24页
© 2010 Kennametal Inc. l All rights reserved. l Proprietary and Confidential l 9 of 102
前刀面设计
传统前刀面 (一个表面) 接触区大
切屑速度慢 接触区小
快速切屑 前刀面 (两个表面)
刀尖条件
刃数
容屑空间
2刃 过中心切削
3刃 过中心切削
4刃 过中心切削
6刃
8刃
过中心切削 过中心切削
表面光洁度
第5页/共24页
© 2010 Kennametal Inc. l All rights reserved. l Proprietary and Confidential l 4 of 102
齿距
© 2010 Kennametal Inc. l All rights reserved. l Proprietary and Confidential l 12 of 102
粗加工齿形
粗加工刀具
粗齿 铝,非铁材料
深槽铣 主轴荷载少
半精加工刀具
密齿 钢,铸铁 仿形,槽铣 耐磨损性能好
超密齿 不锈钢,钛,高温合金
第六章 成形车刀

改 变 零 件 廓 形
刃 上 磨 出 凹
• 3)将 Krx =O°的刃段磨出副偏角Krx′=2°~3°,可使摩 擦大为减少。同样不改变工件的廓形,普遍采用。 • 4)采用斜向进给成形车刀,以形成Krx> 7°,使 α ox≥ 2°~ 3°。 • 5)采用螺旋体成形车刀,将圆体成形车刀各段切削刃 的后面制成螺旋面,使Krx= 0°处的后面与加工表面形 成一定间隙,使α ox≥ 2°~ 3°。结构复杂,制造麻烦 ,较少采用。
• (3) 圆体成形车刀。它好似由长长的棱体车刀包在 一个圆柱面上而形成。刀体是一个磨出了排屑缺口 和前刀面,并且带安装孔的回转体。它允许重磨的 次数最多,制造也比棱体成形车刀容易,且可加工 零件上的内、外成形表面;但加工误差较大,加工 精度不如前两种成形车刀高。
●
按进给方向
车削时,切削刃沿工件表面的 切线方向切入工件。由于切削 刃相对于工件有较大的倾斜角, 所以切削刃是依次先后切入和 切出,始终只有一小段切削刃 在工作,从而减小了切削力; 但切削行程长,生产率低。适 于加工细长、刚性较差且廓形 深度差别小的外成形表面。
•2. 正交平面后角及其过小时的改善措施
• 成形车刀后面与工件过渡表面间 的摩擦程度取决于切削刃各点的 后角大小,因此要对切削刃上关 键点的后角进行验算。 • 为了简化,现以γ f= 0°、λ s=0° 的成形车刀为例来进行讨论。如 图6-4所示,切削刃上任一点在假 定工作平面内的后角为与该点主 剖面后角为间的关系为:
成形车刀设计的基本步骤
一、选用刀具材料(根据加工材料选择) 二、确定刀具几何角度(前角与后角) 三、确定刀具结构尺寸(主要是最大廓深,深度确定 以后可查阅相关手册) 四、确定工件组成点与组成点平均尺寸 五、计算刀具各点对应的廓形深度 六、个组成点廓形的深度公差 七、计算刀具斜线部分的倾角 八、求近似圆弧,作出刀具廓形图以及样板图。
机械制造装备设计第五章专用车刀设计
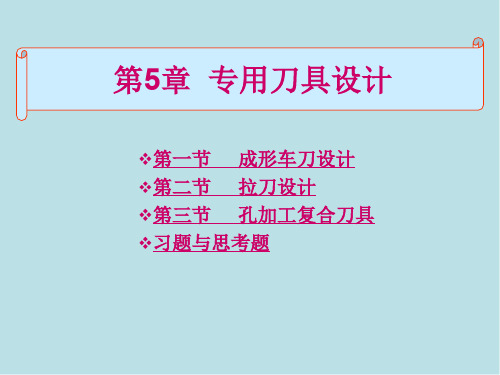
形1''、2''、3''、4''。
2)计算法
应首先画作出计算图,如图5- 6所示
求刀具前刀面上各组成点的尺
制造时,将它的前刀面作成距其中心
为h距离: h=Rsin( γ f+ α f)
安装时,再将刀具中心O2比工件中 心装高H距离,同时使切削刃上最外
点与工件轴线等高 :H=Rsin α f
在磨钝重磨时也应使h值不变 , h为半 径的磨刀检验圆,重磨时应保证前刀 面与这个圆相切
图5-3 成形车刀前角和后角的形成
图5-4 a :
当α f=0°,γ f=0°时成形车刀的截形 与工件的廓形才能完全相同,但后角α f=
0°的刀具是无法进行切削的 图5-4 b:
前角γ f≥0°、后角α f>0°时 ,成形车 刀的截形与工件廓形不相等。既刀具截形深 度P小于相应的工件廓形深度ap 为了使成形车刀能切出准确的工件形状,
图5-3 。
f f
成形车刀前角和后角是通过刀具 的正确制造和正确安装形成的
图5-3 a) :棱体成形车刀的前 角和后角
制造时,将前刀面和后刀面的夹角磨
成90°-( γ f+ α f) 角。安装
时,只要将刀体倾斜α f角,即能形 成所需的前角和后角
图5-3 b) :圆体成形车刀前角 和后角
钻铰复合刀具设计
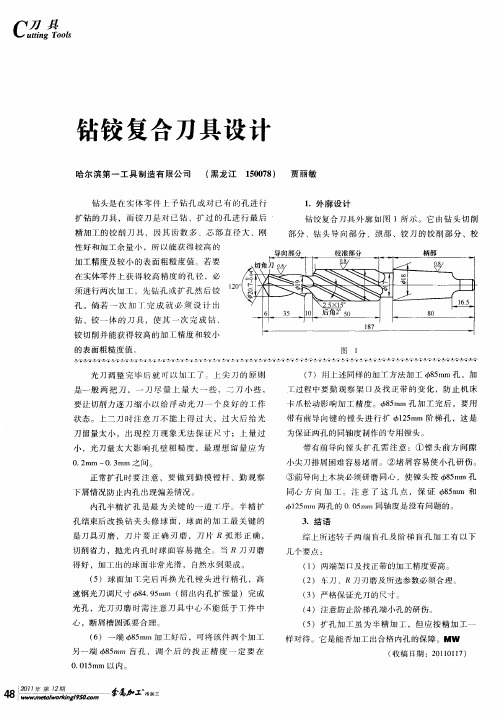
应用程序直接相连 ,从 而使 用 户可 以随 时随地 、 自由
灵 活地 与 他 人 共 享 设 计 并 开 展 协 作 。
参 釉 露
轰
内孔半精 扩 孑 是 最 为关 键 的一 道 T 序 。半 精 扩 L 孔结 束后 改换 钻 夹 头 修球 面 ,球 商 的加 工最 关 键 的 是刀具 刃 磨 ,刀 片 要 正 确 刃磨 ,刀 片 R 弧形 正 确 , 切 削省力 ,抛 光 内孔 时 球 面容 易 抛 全 。当 R刀 刃磨 得 好 ,加 工 出的球 面非常光 滑 , 自然水 到渠 成 。 ( )球 面加 完 后 再 换 光孔 镗 头 进行 精 孔 ,高 5 速 钢光刀 调尺 寸 6 4 9 r ( 出内孔 扩涨量 ) 完成 8.5 m 留 a 光 孔 ,光 刀刃 磨 时需 注意 刀 具 中 心不 能 低 于 丁件 中 心 ,断屑槽 圆弧要 合理 。 ( )一端 4 5 6 9 mm加 工好 后 ,可将该 件 调个加 工 8
( 稿 日期 :2 10 1 ) 收 0 117
4 8
参磊 岛 舡
C 盎。
准部 分 、颈 部 以及 柄部 组成 。
分 可 减 小 摩 擦 , 防 止 产 生 喇 叭 形 孔 和 孔 径 扩 大 等 毛 病。 铰 刀 前 角 为 5 、 后 角 为 l。 刃 宽 为 F = 。 0、
棱 边 与 孔 壁 的 摩 擦 。 倒 锥 量 是 每 10 0 mm 长 度 上 减 小 00 . 3~0 1rm, 大 直 径 钻 头 取 大 值 。 .2 a 钻头 沟 形 如 图 2 所 示 d ,一 d 的 倒 锥 量 为
5 .结 语
这种 钻铰 复 合 刀 具 ,可 大批 量 生 产 ,适 合 加 工 对孔 径要 求 极 高 的 零 部 件 产 品 ,能 降 低 劳 动 强 度 ,
刀具设计任务书

设计题目: 工件材料HT400,使用机床CA6140,加工后dm=200,Ra=3.2,需粗,半精车完成,加工余量自定,设计装S 刀片45°弯头外圆车刀。
一.设计可转位车刀1、选择刀片夹固结构考虑到加工是在CA6140普通机床上进行,属于连续切削,参照典型车刀夹固结构简图和特点,采用杠杆式刀片夹固结构。
2、选择刀片材料(硬质合金牌号)由原始条件结构给定:被加工工件材料为HT400,连续切削,完成粗车、半精车两道工序,按照硬质合金的选用原则,选取刀片材料(硬质合金牌号)为YG6。
3、选择车刀合理角度根据刀具合理几何参数的选择原则,并考虑到可转位车刀:几何角度的形成特点,选取如下四个主要角度:(1) 前角=14° (2)后角=6° (3)主偏角=45° (4)刃倾角=-6° 后角0α的实际数值以及副后角和副偏角在计算刀槽角度时,经校验后确定。
4、选择切削用量根据切削用量的选择原则,查表确定切削用量为:粗车时:切削深度ap=3mm ,进给量:f=0.6mm/r ,切削速度v=110m/min 5、选择刀片型号和尺寸 (1)选择刀片有无中心固定孔由于刀片加固结构已选定为偏心式,因此应选用有中心固定孔的刀片。
(2) 选择刀片形状按照选定的主偏角=45°,选用正方形刀片。
(3) 选择刀片精度等级 选用U 级(4) 选择刀片内切圆直径d (或刀片边长L )根据已选定的ap 、kr 、s λ,可求出刀刃的实际参加工作长度se L 。
为:L se =sr pk a λcos sin=4.267mmL>1.5L se =sr pk a λcos sin =6.401mm因为是正方形,L>d>6.401(5)选择刀片厚度S根据ap ,f ,利用诺模图,得S ≥4.8.(6)选择刀尖圆弧半径r ε根据a p ,f, 利用诺模图,得连续切削r ε=1.2(7)选择刀片断屑槽型式和尺寸根据条件,选择A 型。
数控刀具产品设计方案模板
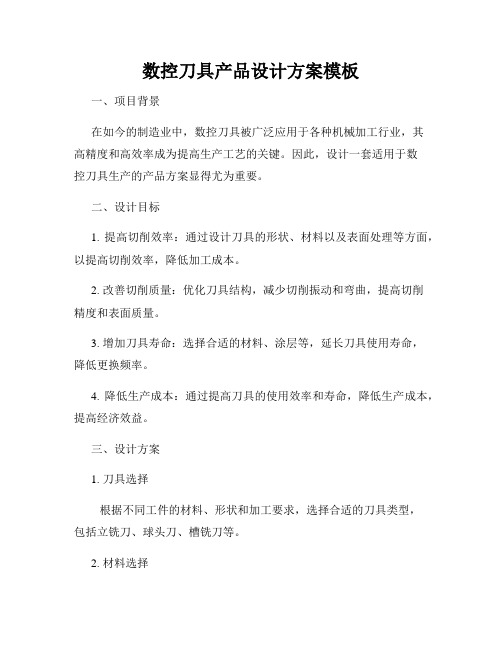
数控刀具产品设计方案模板一、项目背景在如今的制造业中,数控刀具被广泛应用于各种机械加工行业,其高精度和高效率成为提高生产工艺的关键。
因此,设计一套适用于数控刀具生产的产品方案显得尤为重要。
二、设计目标1. 提高切削效率:通过设计刀具的形状、材料以及表面处理等方面,以提高切削效率,降低加工成本。
2. 改善切削质量:优化刀具结构,减少切削振动和弯曲,提高切削精度和表面质量。
3. 增加刀具寿命:选择合适的材料、涂层等,延长刀具使用寿命,降低更换频率。
4. 降低生产成本:通过提高刀具的使用效率和寿命,降低生产成本,提高经济效益。
三、设计方案1. 刀具选择根据不同工件的材料、形状和加工要求,选择合适的刀具类型,包括立铣刀、球头刀、槽铣刀等。
2. 材料选择根据刀具使用环境和要求,选择耐磨、高硬度的刀具材料,如硬质合金、陶瓷材料等。
3. 刀具结构设计3.1 刀具形状设计:根据切削要求和工件形状,设计合适的刀具形状,包括刀具刃数、刃角、切削面等。
3.2 刀具尺寸设计:根据加工工件的尺寸要求,合理设计刀具的直径、长度等尺寸。
3.3 刀柄设计:设计刀柄的材料和结构,以提供足够的刚性和稳定性。
4. 表面处理通过涂层、热处理等方式,改善刀具的表面硬度和耐磨性,延长刀具的使用寿命。
5. 切削参数选择根据工件材料和形状,合理选择切削参数,包括切削速度、进给量、切削深度等,以达到最佳加工效果。
6. 刀具保养与更换制定刀具保养计划,包括定期润滑、磨损检查等,及时更换磨损严重的刀具,以确保加工质量和效率。
四、产品效益1. 提高生产效率:优化设计方案将提高切削效率和质量,缩短加工周期,提高生产效率。
2. 降低生产成本:延长刀具使用寿命,减少更换频率,降低生产成本。
3. 提升加工精度:通过改善刀具结构和选择合适的加工参数,提高加工工件的精度和表面质量。
4. 促进产品升级:通过引进新的刀具设计方案,推动数控刀具产品的升级改进,提高市场竞争力。
pcd刀具的设计原则

PCD刀具的设计原则一、合理选择PCD粒度PC D粒度的选择与刀具加工条件有关,如设计用于精加工或超精加工的刀具时,应选用强度高、韧性好、抗冲击性能好、细晶粒的P C D。
粗晶粒PC D刀具则可用于一般的粗加工。
PC D材料的粒度对于刀具的磨损和破损性能影响显著。
研究表明:P C D粒度号越大,刀具的抗磨损性能越强。
采用DeBeers 公司S YN DITE 002和S YN DITE025两种PC D材料的刀具加工S iC基复合材料时的刀具磨损试验结果表明,粒度为2μm的S YN DITE002PC D材料较易磨损。
二、合理选择PCD刀片厚度通常情况下,PC D复合片的层厚约为0.3~1.0mm,加上硬质合金层后的总厚度约为2~8mm。
较薄的PC D层厚有利于刀片的电火花加工。
DeBeers公司推出的0.3mm厚P CD复合片可降低磨削力,提高电火花的切割速度。
PC D复合片与刀体材料焊接时,硬质合金层的厚度不能太小,以避免因两种材料结合面间的应力差而引起分层。
三、几何参数与结构设计PC D刀具的几何参数取决于工件状况、刀具材料与结构等具体加工条件。
由于P CD刀具常用于工件的精加工,切削厚度较小(有时甚至等于刀具的刃口半径),属于微量切削,因此其后角及后刀面对加工质量有明显影响,较小的后角、较高的后刀面质量对于提高P C D 刀具的加工质量可起到重要作用。
P C D复合片与刀杆的连接方式包括机械夹固、焊接、可转位等多种方式。
四、PCD复合片与刀杆连接方式的特点与应用连接方式-特点-应用范围机械夹固-由标准刀体及可做成各种集合角度的可换刀片组成,具有快换和便于重磨的优点-中小型机床整体焊接-结构紧凑、制作方便,可制成小尺寸刀具-专用刀具或难于机夹的刀具,用于小型机床机夹焊接-刀片焊接于刀头上,可使用标准刀杆,便于刃磨及调整刀头位置-自动机床、数控机床可转位-结构紧凑,夹紧可靠,不需重磨和焊接,可节省辅助时间,提高刀具寿命-普通通用机床五、PCD刀具的切削参数与失效机理PC D刀具切削参数对切削性能的影响①切削速度PC D刀具可在极高的主轴转速下进行切削加工,但切削速度的变化对加工质量的影响不容忽视。
成形铣刀设计汇总
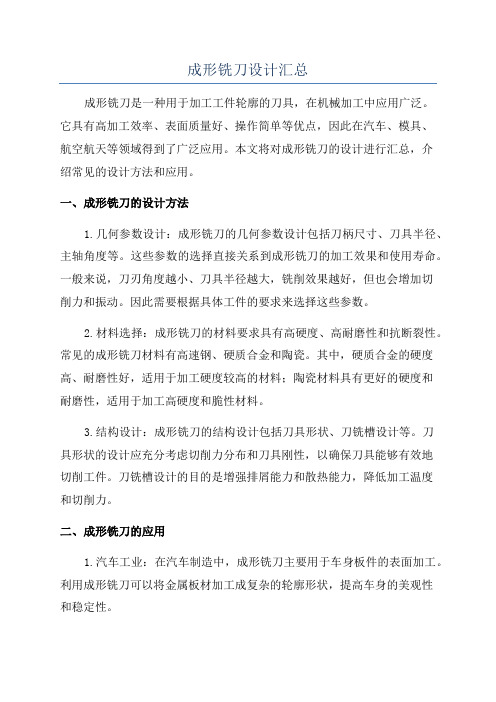
成形铣刀设计汇总成形铣刀是一种用于加工工件轮廓的刀具,在机械加工中应用广泛。
它具有高加工效率、表面质量好、操作简单等优点,因此在汽车、模具、航空航天等领域得到了广泛应用。
本文将对成形铣刀的设计进行汇总,介绍常见的设计方法和应用。
一、成形铣刀的设计方法1.几何参数设计:成形铣刀的几何参数设计包括刀柄尺寸、刀具半径、主轴角度等。
这些参数的选择直接关系到成形铣刀的加工效果和使用寿命。
一般来说,刀刃角度越小、刀具半径越大,铣削效果越好,但也会增加切削力和振动。
因此需要根据具体工件的要求来选择这些参数。
2.材料选择:成形铣刀的材料要求具有高硬度、高耐磨性和抗断裂性。
常见的成形铣刀材料有高速钢、硬质合金和陶瓷。
其中,硬质合金的硬度高、耐磨性好,适用于加工硬度较高的材料;陶瓷材料具有更好的硬度和耐磨性,适用于加工高硬度和脆性材料。
3.结构设计:成形铣刀的结构设计包括刀具形状、刀铣槽设计等。
刀具形状的设计应充分考虑切削力分布和刀具刚性,以确保刀具能够有效地切削工件。
刀铣槽设计的目的是增强排屑能力和散热能力,降低加工温度和切削力。
二、成形铣刀的应用1.汽车工业:在汽车制造中,成形铣刀主要用于车身板件的表面加工。
利用成形铣刀可以将金属板材加工成复杂的轮廓形状,提高车身的美观性和稳定性。
2.模具制造:在模具制造过程中,成形铣刀可以用于模具的粗加工和精加工。
粗加工时,成形铣刀以高速进行铣削,快速去除多余材料;精加工时,成形铣刀以低速进行铣削,得到更加精确的轮廓形状。
3.航空航天工业:在航空航天中,成形铣刀广泛应用于飞机结构件的制造。
成形铣刀可以用于加工各种材料的结构件,包括铝合金、钛合金和复合材料等。
4.电子工业:在电子工业中,成形铣刀可以用于加工电子元件的外壳。
利用成形铣刀可以将金属外壳加工成各种形状,以满足不同电子设备的外观要求。
总之,成形铣刀作为一种常见的刀具,在机械加工中扮演着重要的角色。
通过合理的设计和选择,成形铣刀能够有效地提高加工效率和加工质量,满足不同工件的加工要求。
刀具设计与检验指导书范本doc 10页
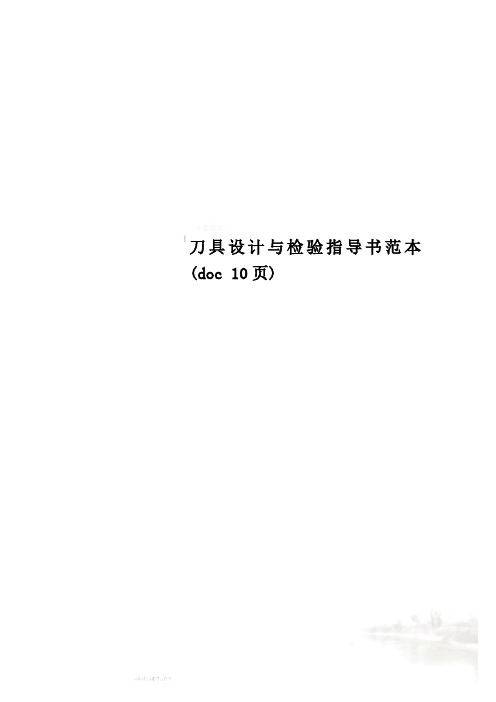
刀具设计与检验指导书范本(doc 10页)刀具設計與檢驗指導書一: 刀具的作用成形: 立軸機、四面刨、NC機、仿形機、刨花機、雙端作榫機…等鑽孔: 手搖鑽、水平雙端鑽、立式多軸鑽、水平多軸鑽…等拉槽: 刨花機、NC機、萬能鋸、立軸機、雙頭鋸…等開料: 帶鋸機、單片鋸、多片鋸…等裁切: 雙頭鋸、裁板機、橫切鋸、臺面鋸…等清底: NC機、刨花機…等修邊: 單片鋸、修邊機…等刨光: 手壓刨、雙面刨、單面刨、四面刨…等二: 刀具的種類(按使用機器分)立軸刀四面刨刀刨花刀仿形機刀NC刨花刀NC立軸刀NC刨刀萬能鋸刀鋸片鋸條鑽頭手提雕刻刨花刀刨刀方鑿指接刀鳩尾榫刀雙端作榫機刀三: 刀具詳解1: 立軸刀(代號: LPT或LPL/LPR) (注:分為平刀与形刀通常為4齒)要素 (1)平刀: 孔徑&外徑 (2)形刀:底徑、外徑、轉向備注: (1)立軸刀孔徑40MM(也有老機器30MM或25.4MM0、底徑通常做100MM,如有刀形比較大或成形死角時底徑按需縮小(2)通常立軸刀太于180MM的外徑是比較危險的(當切削外徑大于180時,可相對減小切削內徑,但內徑不能小于Φ70)(3)立軸刀一般為逆轉,如有成形端頭等一些特殊情況需正&逆2种轉向。
注:順時針為正,逆時針為負2: 四面刨刀(代號:SPT/SPB/SPL/SPR)=立軸刀備注: (1)原則上立軸刀与四面刨刀是通用的但有一种八軸四面刨是用孔徑50MM刀(本廠不用)。
(2)四面刨刀分為上/下/左/右四面成形,四把刀轉向為上逆/下順/左順/右逆。
(3)四面刨刀的轉向是由立著的刀由上向上看,躺的刀由左向右看所得轉向確定。
(4)刀外徑不要超過180MM,最好160MM以下。
四面刨下刀外徑不要超過120MM 外徑(5)四面刨只能成形直形產品(6)排列順序:六軸四面刨: 下、內、外、上、上、下八軸四面刨: 下、內、外、內、外、上、上、下(4)刀片寬度一般情況下不能超過135,如有必要上下可挖槽Φ75*25mm(5)刀刃材料為3mm碳化鎢鋼,刀体材料為中碳鋼:(6)最大加工材料高度為120mm,最大加工材料寬度為205mm.(7)底刀規格同頂刀,轉向為順轉,若加工材料非上下兩面有刀形時,形刀一般為頂刀,底刀為平刀.(8)相鄰刀具即頂刀與側刀或底刀與側刀在工件上必需有1~2mm重迭部分.3: 仿形機刀=四面刨刀=立軸刀4: 萬能鋸刀(代號:JP)(1) 孔徑25.4MM,外徑220MM,齒數12T(特殊情況帶刮齒)(2) 主要用于開缺口&成形,5: 刨花刀(代號:LD)=NC刨花刀(代號:LD)普通刨花刀柄徑12&16MM,柄長45MM,2齒(特殊情況做4齒),外徑不要超過70MM。
薄壁槽圈加工的专用刀具与夹具设计
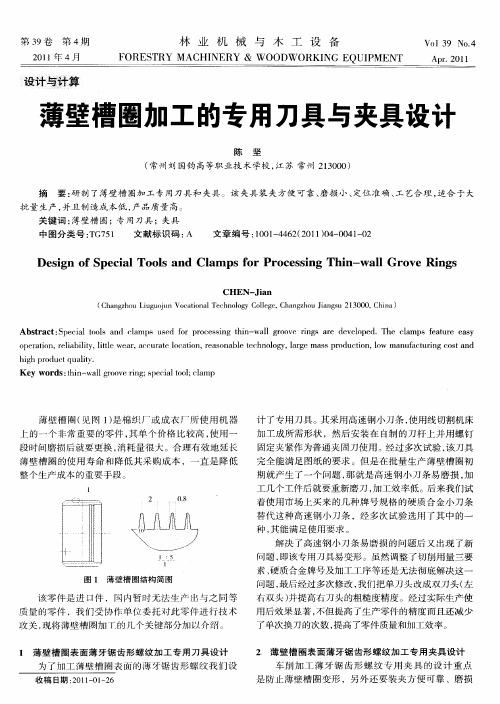
Absr c : p ca o l n lmp s d fr p o e sn h n wal r o e ig r e eo e t a t S e iltos a d ca s u e o r c s i g t i — l o v rn s a e d v lp d.Th lmp fau e e s g e ca s e tr a y
该零件是 进 口件 ,罔内暂时无法 生产 出与之 同等 质量 的零件 ,我们受 协作单 位委托 对此零件 进行技 术
攻关 , 现将 薄 壁槽 网加 丁 的 几 个 关 键 部 分 加 以介 绍 。
1 薄壁槽 图表面 薄牙锯 齿形螺纹加工专用刀具设计
为 了加 工 薄 壁 槽 圈 表 面 的 薄 牙锯 齿 形 螺 纹 我 们 设
计 了专用刀具 。其采 用高速钢小刀条 , 用线切割机床 使 加工成所 需形状 ,然后安装 在 自制 的刀杆上并用螺钉 固定夹紧作为普通夹 同刀使用 。经过多次试验 , 刀具 该 完全能满 足图纸 的要求 。但 是在批量生 产薄壁槽 圈初 期就产生 了一个 问题 , 那就是 高速钢小 刀条易磨损 , 加 工几个工件后就要重新磨刀 , 加工效率低 。 后来 我们试
段时 间磨损后就要更换 , 消耗量很 大。合理有效地延长 薄壁槽 圈的使用 寿命 和 降低 其采购成本 ,一直是 降低
刀具设计说明书

楔销式75度机夹不重磨车刀专业:机械设计制造及其自动化班级:机制三班姓名:刘丹丹学号:0908014345目录一选择刀片夹紧结构二、选择刀片材料三、选择车刀合理角度四、选择切削用量五、选择刀片的形状和尺寸六、确定刀垫的型号和尺寸七、计算刀槽角度八、计算铣制刀槽角度九、选择刀杆的材料和尺寸十、设计螺钉一选择刀片夹紧结构可转位车刀的典型刀片夹固结构有:偏心式、杠杆式、上压式、楔销式、拉垫式和杠销式等。
这里选择楔销式,结构比较简单,夹紧力大,夹紧可靠,刀尖位置精度高,操作方便,不阻碍切屑流动,便于观察切削区的工作情况。
缺点是夹紧力与切削力的方向相反。
二选择刀片材料硬质合金是由难熔金属碳化物(如WC、TiC℉、TaC、NbC等)和金属粘结剂经粉末冶金方法制成的。
硬质合金分为三类:YT,YG,YW。
YG类硬质合金主要用于加工铸铁和有色金属,YT类主要用于加工钢料,YW 类抗弯强度、疲劳强度和冲击韧度高,抗氧化能力和耐磨性也比较好,可用于加工铸铁及有色金属。
YT类硬质合金适于加工钢料。
加工钢料时,金属塑性变形大,摩擦很剧烈,切削温度很高。
YT类硬质合金具有较高的硬度和耐磨性,特别是较高的耐热性,抗粘结扩散能力和抗氧化能力也很好。
在加工钢料时,刀具磨损小,刀具耐用度较高,所以在加工40Cr材料工件时应选择YT类硬质合金作为刀具材料。
选取刀片材料为YT15。
三选择车刀的合理角度1.主偏角主偏角kr主偏角对可转位车刀的寿命影响较大。
一般来说,减小主偏角可提高刀具工作寿命。
但当工艺系统或被加工工件刚性不足时,减小主偏角会增大径向力,从而加大变形挠度,引起加工振动,降低加工精度和加工表面质量,同时影响刀具寿命,因此,应针对不同的加工条件选择不同的主偏角。
设计刀具时的主偏角推荐值见表1。
表1可转位车刀主偏角推荐值2.前角的选择加工塑性材料时(钢),应选用较大前角。
切削钢料时,切削变形很大,切屑与前刀面的接触面积较长,刀屑之间的压力和摩擦力都很大,为了减小切屑的变形和摩擦,宜选用较大的前角。
棱形成形车刀设计

棱形成形车刀设计:XXX学号:XXX班级:XXX导师:XXX前言成形车刀是加工回转体成形外表的专用工具,它的切削刃形状是根据工件的轮廓设计的。
用成形车刀加工,只要一次切削行程就能切出成形外表,操作简单,生产效率高,成形外表的精度与工人操作水平无关,主要取决于刀具切削刃的制造精度。
它可以保证被加工工件外表形状和尺寸精度的一致性和互换性,加工精度可达IT9—IT10,外表粗糙度Ra6.3—Ra3.2。
成形车刀的可重磨次数多,使用寿命长,但是刀具的设计和制造较复杂,本钱高,故主要用在小型零件的大批量生产中。
由于成形车刀的刀刃形状复杂,用硬质合金作为刀具材料时制造比拟困难,因此多用高速钢作为刀具的材料。
棱形成型车刀是成型车刀三种中的一种,棱柱体的刀头和刀杆分开制作,大大增加了沿前刀面的重磨次数,刀体刚性好,但比圆体成形车刀制造工艺复杂,刃磨次数少,且只能加工外成形外表。
棱体成形车刀的后刀面是成形棱形柱面,前刀面是平面。
后刀面与燕尾面K-K平行,而前刀面与K-K呈倾角90°-〔rf+af 〕。
在制造棱体成形车刀时,将前刀面与后刀面的夹角磨成90°-〔rf+af 〕。
切削时,将后刀面安装出af 角,这样就形成了前角rf 和后角af 。
棱体成形车刀是以燕尾作为定位基准,配装在刀夹的燕尾槽内。
刀具燕尾的后平面是夹固基准。
安装时,刀体竖立并倾斜角,刀夹下端的螺钉可将计算基准点的位置调整与工件中心等高后用螺栓夹紧,同时下端螺钉可以承受局部切削力,以增强刀具的刚性。
棱体成形车刀的刃磨比拟简单,只要在工具磨床上使用一简单的双向万能刃磨夹具,将刀具后刀面与砂轮外表的垂线装成〔rf+af〕的角度即可刃磨。
目录设计任务书 (4)设计方案 (5)一、机床的选择 (5)二、选择刀具材料 (5)三、选择刀具前角和后角 (5)四、棱形成型车刀的廓形设计 (6)五、用计算法求切削刃各点的廓形深度 (7)六、确定刀具各段切削刃的廓形宽度 (8)七、确定棱形成型车刀的构造尺寸 (8)八、刀具局部尺寸公差及形位公差 (8)九、绘制刀具和样板工作图 (9)十、UG效果图 (10)参考文献 (11)设计任务书条件:1.要加工的工件零件图如下所示。
用正交试验设计方法优化刀具设计

验 点有 如下两个 条件 : 1 任 一因素 的诸 水平做 相 同数 目的试 验 ; )
2 )任两个因素的水平组合做相同数 目的试验 。 这 就 使得 用 正 交 表 安 排 的 试 验 有很 好 的代 表 性 ,同 时 ,大 大 减 少 了 试验 次 数 。将 正 交试 验 法 应 用 在 刀具 设 计 中 , 既 可 以 避 免 一 些 无 谓 的 计
会 出现 为 了指 标 合格 ,某 参 数 只能 选 取 极 端 值 , 尽 管校 验 合 格 ,但选 定 的参 数 不一 定是 最 优 。 要
用正 交试 验优化 刀具设 计过 程 。
1 )试 验 目的
通过 正交 试 验 ,找 出在 满 足 拉 刀 强 度要 求 的 前提 下 ,刀 具 参数 的最 优 值 。使 刀 具 既 符合 工 作
性 能 要求 ,又节 约材料 ,降 低成 本 。 2 )确定 因素 、水 平和指 标
21 试验指 标和 因素 的选取 .
在 圆 孔 拉 刀 设 计 中 ,需 要 校 验 的 指 标 主 要
找到 最 优 的 参数 组 合 ,就 需要 多次 反 复 计 算和 试
验 ,在 有 多 因 素影 响 时 ,就 更难 确 定 合 理 的参 数
1 正交试验设计方法的优点
简 单 说 ,正 交试 验设 计 就 是 用 正 交 表确 定 试 验 方 案 ,并 对 结果 进 行 统 计分 析 。正 交 试验 的试
22 水 平的确定 .
为 了便 于衡 量 各 因素 对 试 验 指 标 的 影 响 ,选 取 设 计 手 册 提 供 的 经 验 值 范 围 的 中 问 值 为 基 本
以 及 是 否 容 易 达 到 合 格 标 准 ,现 选 取 容 屑 条 件
- 1、下载文档前请自行甄别文档内容的完整性,平台不提供额外的编辑、内容补充、找答案等附加服务。
- 2、"仅部分预览"的文档,不可在线预览部分如存在完整性等问题,可反馈申请退款(可完整预览的文档不适用该条件!)。
- 3、如文档侵犯您的权益,请联系客服反馈,我们会尽快为您处理(人工客服工作时间:9:00-18:30)。
机床的刀架 相联接。
机床的刀 架相联接。
6.1.2 成形车刀的前角和后角 成形车刀的前角和后角是通过刀具的正确制造和安装形成的。 1、棱体成形车刀的前角和后角 制造时,将前刀面和后刀面的夹角磨成 90º-(γαf)角。
c—为保证后续切断工序顺利进行而设的预切槽刀刃宽度),c值常取为3~8(5—6—7—11段); d—为保证成形车刀刀刃处到工件毛坯表面之外而设的附加刀刃宽度(),常取0.5~2(11—12段)。
6.1.4 成形车刀设计要点
实际生产中,有时也可取图 示 的 附 加 刀 刃 形 式 , a′ 、 c′ 、 b′ 数 值 视 具 体 情 况 而 定 ( 其 中 a′>3)。
燕尾测量尺寸M值应与切削刃总宽度和测量滚柱直径相适应(表5—1)。 此外,为了方便调整棱体成形车刀的高度,增加成形车刀切削时的刚度,在刀体底部做有螺孔 以旋入螺钉,螺孔常取M6。 棱体成形车刀的结构尺寸见(表5—1)。
6.1.4 成形车刀设计要点
(2)圆体成形车刀
主要结构尺寸有: 刀体总宽度、 刀体外径d0、 内孔直径d 夹固部分尺寸等。
专用刀具设计
6.1 成形车刀设计
需要根据工件的廓形进行专门设计和制造。 主要用在卧式车床、转塔车床、自动车床上加工内、外回转成形表面。 加工表面的形状、尺寸精度主要取决于刀具的设计和制造精度,加工精度一般能达到08, 表面粗糙度≤6.3~3.2μm。 优点: 生产率高,加工表面形状、尺寸一致性高,互换性好以及刀具的重磨次数多,使 用寿命长和操作简便等。 不足:成形车刀的设计和制造比较麻烦,成本高。 多在成批、大量生产中使用。
1)刀体总宽度L0 L0
6.1.4 成形车刀设计要点
—成形车刀切削刃总宽度(); l —工件廓形宽度(); a、b、c、d—成形车刀的附加刀刃;
6.1.4 成形车刀设计要点 a—为避免切削刃转角处过尖而设的附 加刀刃宽度(),常取为0.5~3(9—10段); b—为考虑工件端面的精加工和倒角而 设的附加刀刃宽度(),其数值应大于端面精 加工余量和倒角宽度。
6.1.4 成形车刀设计要点
1)刀体总宽度 L0十 —切削刃总宽度(); —除切削刃外其它部分宽度()。
6.1.4 成形车刀设计要点
2)刀体外径和内孔直径
确定外径时,要考虑工件的最大廓形深度、排屑、刀体强度及刚度等,取值大小要受机床横刀架 中心高及刀夹空间的限制。
一般可按下式计算,再取相近标准值,即
为了便于制造与测量,H和h的尺寸一般圆整成 0.5倍数。
6.1. 3 成形车刀的截形设计 ▼工件的(轴剖面)轮廓形状 工件的廓形是规定在通过其轴线的平面内测量的; ▼已确定的刀具相关参数求解成形车刀的截形。 成形车刀的截形是规定在与后刀面垂直的剖面N—N内测量的。 对于圆体成形车刀,N—N剖面也就是刀体的轴剖面。
6.1.4 成形车刀设计要点
当/大于许用值或>80(为经验值)时,可采取下列措施: ①将工件廓形分段,改用两把或数把成形车刀切削加工。 ②改用切向进给成形车刀。 ③如已确定用径向进给,可在工件非切削部分增设辅助支承——滚轮托架,以增加工艺系统 刚度。
6.1.4 成形车刀设计要点 2)刀体高度H 刀体高度H与机床横刀架距主轴中心高度有关。
当 γf≥0º,αf>0º时, 成形车刀的截形与 工件廓形不相等。。
6.1. 3 成形车刀的截形设计
算。
刀具截形深度P<相应的工件廓形深度; 刀具截形宽度=工件廓形宽度相等。 为了使成形车刀能切出准确的工件形状,设计成形车刀时,必须对刀具的截形进行修正计
2、截形修正计算方法
6.1. 3 成形车刀的截形设计
D0≥2()
D0 具廓形最大直径(); 工件最大廓形深度();
e——保证足够的容屑空间所需要的距离(1)。可根据切削厚度及切屑的卷曲程度选取,一般取为 3—12。加工脆性材料时取小值,反之取大值;
刀体壁厚()。根据刀体强度要求选取,一般约为5~8; d——内孔直径()。其值应保证心轴和刀体有足够的强度和刚度,可依切削用量及切削力大小取为 (0.25—0.45),计算后再取相近标准值10(12)、16(19)、20、22、27等(带括号者为非优选系列尺 寸)。
6.1. 3 成形车刀的截形设计
将x分别用2、3、4代人上式,即可求出前刀面上各组成点的相应尺寸C2、C3、 (C4)。
②求刀具各组成点的截形深度 棱形成形车刀
6.1. 3 成形车刀的截形设计 圆体成形车刀
6.1. 3 成形车刀的截形设计
6.1. 3 成形车刀的截形设计
(3)双曲线误差
6.1. 3 成形车刀的截形设计 加工圆锥表面时会产生双曲线误差
(3)双曲线误差
6.1. 3 成形车刀的截形设计
(3)双曲线误差
6.1. 3 成形车刀的截形设计
6.1. 3 成形车刀的截形设计
1、确定刀体结构尺寸
(1)棱体成形车刀
棱体成形车刀的装夹 部分多采用燕尾结构, 这种结构装夹稳固可靠, 能承受较大切削力。
6.1.4 成形车刀设计要点
燕尾结构的主要尺寸有:刀体总宽度L0、刀体高度H、刀体厚度B以及燕尾尺寸M等。
6.1.2 成形车刀的前角和后角
当γf>0时,切削刃上只有基点1 与工件中心等高,而刃上其他各点都 低于工件中心。
因此,切削刃上各点的切削平 面和基面位置不同,因而刃上各点的 前角和后角也都不相同,离基点愈远 (径向)的点的前角愈小,后角愈大。
在自动车床上使用圆体成形车刀,其前、后角通 常根据机床刀架的尺寸及刀具的安装尺寸H和重磨尺寸 A而定。
6.1.1车刀的类型与装夹
1、成形车刀的类型
☆平体成形车刀 一般用于单件、小批生产,加工简单成形 表面。
☆ 棱体成形车刀 刀体为棱柱体,沿前刀面可重磨次数比平体成形车刀多,刀 体刚性高;但制造成本较高,且只能加工外成形表面。
☆ 圆体成形车刀 刀体是一个磨出排屑缺口和前刀面并带安装孔的回转体。它 允许的重磨次数最多,制造也比棱体刀容易,且可加工内、外成 形表面;但加工精度不如棱体成形车刀高。
在确定切削刃总宽度时,还 应考虑机床功率及工艺系统刚度。
6.1.4 成形车刀设计要点
因为径向成形车刀切削刃同时参加切削,径向切削分力很大,易引起振动。一般应限制切 削刃总宽度与工件最小值径的比值,使/不超过下列数值即可:
粗加工2—3,半精加工1.8~2.5,精加工1.5~2。 工件直径较小时取小值,反之取大值。
1、截形设计的必要性
成形车刀磨钝后需要重磨,一般只磨前刀面。 要保证重磨后切削刃的形状不发生变化,需要保证在不同位置的法平面内,成形车刀的后 刀面截形完全一致。
6.1. 3 成形车刀的截形设计
由图可知,只有当γ0º,α0º时,成形车刀的截形与工件的廓形才能完全相同。 但后角α0º的刀具是无法进行切削的。
(1)确定工件成形表面的组成点和基点 一般只选择工件廓形上的转折点及其他特殊点进行计算。
直线段廓形,可取两端点作为组成点; 曲线段廓形,选两端点和曲线部分中间点作为组成点。
以工件廓形半径最小点作为计算基准点(基点)1,然后依次对各组成点编号,并在工件廓 形图上标出各组成点的轴向尺寸和径向尺寸。
在标注尺寸时,须注意有公差要求的径向尺寸应取其平均尺寸作为计算尺寸。
根据刀具截形宽度与工件 廓形宽度相等,即可画出成形车 刀截形。
6.1. 3 成形车刀的截形设计
用作图法求圆体成形车刀的截形。
在工件主视图上,先通过 (与工件中心等高度的)基点1, 向下作一与水平线倾斜成γf 角的前刀面线、向上作一与水 平线倾斜角成αf角的上斜线, 然后以基点1为圆心,以R为半 径作弧与上斜线相交,即为圆 体刀的圆心O2。
安装时,只要将刀体倾斜αf角,即能形成所需的前角和 后角。
2、圆体成形车刀前角和后角
制造时,将它的前 刀面作成距其中心为h距 离。
6.1.2 成形车刀的前角和后角 安装时,再将刀具中心O2比工件中心装高H距 离,形成所需的前角和后角。 h和H之值可由下列公式计算:
在制造时和磨钝重磨时也应使h值不变。 通常在刀具端面上刻一个以02为中心,h 为半径的磨刀检验圆,重磨时应保证前刀面与这 个圆相切。
6.1. 3 成形车刀的截形设计
用作图法求棱体成形车刀的截形。
如图所示,先按放大 比例,按计算尺寸画出工件 的主、俯视图,选定组成点 2,3,4。
在主视图上,从基点1 作刀具前刀面和后刀面二条 直线,分别与水平线及垂直 线交成γf角和αf角。
6.1. 3 成形车刀的截形设计
前刀面与工件上r2、r3(r4) 各圆的交点为2′、3′(4′), 过这些点引平行于后刀面的直线, 则它们和基点处后刀面的垂直距 离P2、P3(P4)就是所要求的棱体 刀成形车刀各组成点的截形深度。
6.1.4 成形车刀设计要点 3)刀体夹固部分尺寸 圆体成形车刀常采用内孔与端面定位,螺栓夹固结构。
6.1.4 成形车刀设计要点
沉头孔用于容纳螺栓头部。 刀体端面的凸台齿纹一方面是为防止切削时,刀具与刀夹体间发生相对转动,另一方面还可 用它粗调刀具高度。 为简化制造,也可制做可换端面齿环,用销子与圆刀体相连。 端面齿纹和端面销孔结构尺寸参见表5—2和表5—3。
30 mm 0 0.2
(30-0.2/2)29.9。
当工件上的径向尺寸未注公差时,允许该尺寸直接作为计算尺寸。
6.1. 3 成形车刀的截形设计 (2)求解刀具截形组成点的方法
成形车刀的截形设计实际上就是根据工件廓形各组成点求出刀具截形的相应组成点。
作图法:比较简单、直观,作图误差大,精确度低; 公式计算法:精确度高,计算工作量大; 查表法:根据计算结果预先列成表格,设计时只要根据已知条件查表或通过简单运算即可得到 设计结果,设计精度也比较高,且简便、迅速。 所以,在实际生产中常用计算法和查表法进行设计,用作图法辅以校验。