关于回流焊工艺发展的讨论
《回流焊接技术地实用工艺要点和技术整合考虑》

《回流焊接技术的工艺要点和技术整合考虑》发表时间:2004-7-19 20:57:29 来源:美国KIC公司作者:薛竞成/技术兼管理顾问点击 156 次前言:焊接,是电子板组装作业中的重要工序,如果没有很好的掌握它,不但会出现许多“零时故障”还会直接影响焊点的寿命。
但是由于目前电子产品更新换代的速度非常快,除了小部分对使用寿命要求很严格的行业或产品制造商外,绝大部分的制造商都忽略了产品寿命的问题,相关的质量管理也往往处于被动状态(往往要等产品出现大量问题后才会想到去处理)。
焊接工艺就是因此被忽略的一个重要环节。
中国SMT工业已经有20多年的历史了,蓬勃发展也已经超过了10年。
可我们在焊接工艺上做得还不够理想。
拿处理焊接工艺的必须品测温仪为例,在7、8年前,还可以见到有些制造商没拥有和使用这种仪器,现在几乎都有了,可是还有很多用户没有对所有产品进行测温认证、调整温度设置;有的用户使用测温了,却没有掌握焊接工艺要点,又无法优化工艺。
这种现象,是会影响中国作为世界加工中心的技术发展。
本文希望通过对回流焊接原理和要点的解释,促使用户在本课题上做进一步的学习和研究,以达到更好的处理这门技术的目的。
在SMT技术应用中,可供使用的焊接技术不单是回流焊接,而回流焊接中也有诸如红外、热风、激光、白热光、热压等等技术。
由于篇幅和时间的原因,我只对最常用的热风回流焊接技术作解释。
另外,任何工艺结果,都是个综合性。
PCBA的组装质量,并不是单由焊接工艺决定的。
即使是如焊球之类看是焊接问题的,也都是由设计、材料、设备、和工艺(包括焊接前的各工艺工序)所合成的。
所以技术整合应用和管理才是保证良好组装质量的根本做法。
以影响SMT的工序之多(注一)以及决定质量因素种类之多,要充分的解释技术整合应用,我想即使用十数万字也是不够的。
所以本文在有限的篇幅中,只对焊接工艺做重点解释,对于其他相关的工艺、可制造性设计、材料质量、设备能力等等都假设做得到位。
回流焊技术应用及质量控制

印刷电路板回流焊技术应用、温度以及质量控制在回流工艺里最主要是控制好固化、回流的温度曲线亦即是固化、回流条件,正确的温度曲线将保证高品质的焊接锡点。
在回流炉里,其内部对于我们来说是一个黑箱,我们不清楚其内部发生的事情,这样为我制定工艺带来重重困难。
为克服这个困难,在SMT行业里普遍采用温度测试仪得出温度曲线,再参巧之进行更改工艺。
温度曲线是施加于电路装配上的温度对时间的函数,当在笛卡尔平面作图时,回流过程中在任何给定的时间上,代表PCB上一个特定点上的温度形成一条曲线.几个参数影响曲线的形状,其中最关键的是传送带速度和每个区的温度设定。
带速决定机板暴露在每个区所设定的温度下的持续时间,增加持续时间可以允许更多时间使电路装配接近该区的温度设定.每个区所花的持续时间总和决定总共的处理时间。
每个区的温度设定影响PCB的温度上升速度,高温在PCB与区的温度之间产生一个较大的温差。
增加区的设定温度允许机板更快地达到给定温度.因此,必须作出一个图形来决定PCB的温度曲线。
接下来是这个步骤的轮廓,用以产生和优化图形。
需要下列设备和辅助工具:温度曲线仪、热电偶、将热电偶附着于PCB的工具和锡膏参数表。
测温仪一般分为两类:实时测温仪,即时传送温度/时间数据和作出图形;而另一种测温仪采样储存数据,然后上载到计算机.将热电偶使用高温焊锡如银/锡合金,焊点尽量最小附着于PCB,或用少量的热化合物(也叫热导膏或热油脂)斑点覆盖住热电偶,再用高温胶带(如Kapton)粘住附着于PCB。
附着的位置也要选择,通常最好是将热电偶尖附着在PCB焊盘和相应的元件引脚或金属端之间.如图示(将热电偶尖附着在PCB焊盘和相应的元件引脚或金属端之间)锡膏特性参数表也是必要的,其应包含所希望的温度曲线持续时间、锡膏活性温度、合金熔点和所希望的回流最高温度。
理想的温度曲线理论上理想的曲线由四个部分或区间组成,前面三个区加热、最后一个区冷却。
炉的温区越多,越能使温度曲线的轮廓达到更准确和接近设定.(理论上理想的回流曲线由四个区组成,前面三个区加热、最后一个区冷却)预热区,用来将PCB的温度从周围环境温度提升到所须的活性温度。
回流焊无铅焊接的特点和对策

钎焊机理钎焊分为硬钎焊和软钎焊。
主要是根据钎料(以下称焊料)的熔化温度来区分的,一般把熔点在450℃以下的焊料叫作软焊料,使用软焊料进行的焊接就叫软钎焊;把熔点在450℃以上的焊料叫作硬焊料,使用硬焊料进行的焊接就叫硬钎焊。
在美国MIL SPEC军用标准中,是以800℉(429℃)的金属焊料的熔点作为区分硬钎焊和软钎焊的标准。
电子装联用锡焊是一种软钎焊,其焊料主要使用锡Sn、铅Pb、银Ag、铟In、铋Bi等金属,目前使用最广的是Sn-Pb和Sn-Pb-Ag 系列共晶焊料,熔点一般在185℃左右。
钎焊意味着固体金属表面被某种熔化合金浸润。
这种现象可用一定的物理定律来表示。
如果从热力学角度来考虑浸润过程,也有各种解释的观点。
有一种观点是用自由能来解释的。
⊿F=⊿U-T⊿S 在这里,F是自由能,U是内能,S是熵。
⊿F 与两种因素有关,即与内能和熵的改变有关。
一般S常常趋向于最大值,因此促使-T⊿S也变得更小。
实际上,当固体与液体接触时,如果自由能F减少,即⊿F是负值,则整个系统将发生反应或趋向于稳定状态。
由此可知,熵是浸润的促进因素,因为熵使⊿F的值变得更小。
⊿F的符号最终决定于⊿U的大小和符号,它控制着浸润是否能够发生。
为了产生浸润,焊料的原子必须与固体的原子接触,这就引起位能的变化,如果固体原子吸引焊料,热量被释放出来,⊿U是负值。
如果不考虑⊿U的大小和量值,那么,熵值的改变与表面能的改变有同样的意义,浸润同样是有保证的。
在基体金属和焊料之间产生反应,这就表明有良好的浸润性和粘附性。
如果固体金属不吸引焊料,⊿U是正值,这种情况下,取决于⊿U在特殊温度下的大小值,才能决定能否发生浸润。
这时,增加T⊿S值的外部热能,能对浸润起诱发作用。
这种现象可以解释弱浸润。
在焊接加温时,表面可能被浸润,在冷却时,焊料趋于凝固。
在开始凝固的区域,⊿U是正值,其值比T⊿S大得多,当⊿F最终变为正值时,浸润现象就发生了。
SMT回流焊接工艺解析
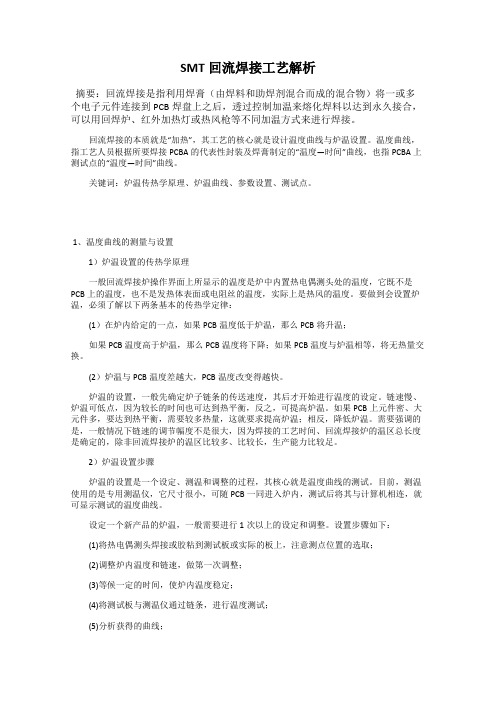
SMT回流焊接工艺解析摘要:回流焊接是指利用焊膏(由焊料和助焊剂混合而成的混合物)将一或多个电子元件连接到PCB焊盘上之后,透过控制加温来熔化焊料以达到永久接合,可以用回焊炉、红外加热灯或热风枪等不同加温方式来进行焊接。
回流焊接的本质就是“加热”,其工艺的核心就是设计温度曲线与炉温设置。
温度曲线,指工艺人员根据所要焊接PCBA的代表性封装及焊膏制定的“温度—时间”曲线,也指PCBA上测试点的“温度—时间”曲线。
关键词:炉温传热学原理、炉温曲线、参数设置、测试点。
1、温度曲线的测量与设置1)炉温设置的传热学原理一般回流焊接炉操作界面上所显示的温度是炉中内置热电偶测头处的温度,它既不是PCB上的温度,也不是发热体表面或电阻丝的温度,实际上是热风的温度。
要做到会设置炉温,必须了解以下两条基本的传热学定律:(1)在炉内给定的一点,如果PCB温度低于炉温,那么PCB将升温;如果PCB温度高于炉温,那么PCB温度将下降;如果PCB温度与炉温相等,将无热量交换。
(2)炉温与PCB温度差越大,PCB温度改变得越快。
炉温的设置,一般先确定炉子链条的传送速度,其后才开始进行温度的设定。
链速慢、炉温可低点,因为较长的时间也可达到热平衡,反之,可提高炉温。
如果PCB上元件密、大元件多,要达到热平衡,需要较多热量,这就要求提高炉温;相反,降低炉温。
需要强调的是,一般情况下链速的调节幅度不是很大,因为焊接的工艺时间、回流焊接炉的温区总长度是确定的,除非回流焊接炉的温区比较多、比较长,生产能力比较足。
2)炉温设置步骤炉温的设置是一个设定、测温和调整的过程,其核心就是温度曲线的测试。
目前,测温使用的是专用测温仪,它尺寸很小,可随PCB一同进入炉内,测试后将其与计算机相连,就可显示测试的温度曲线。
设定一个新产品的炉温,一般需要进行1次以上的设定和调整。
设置步骤如下:(1)将热电偶测头焊接或胶粘到测试板或实际的板上,注意测点位置的选取;(2)调整炉内温度和链速,做第一次调整;(3)等候一定的时间,使炉内温度稳定;(4)将测试板与测温仪通过链条,进行温度测试;(5)分析获得的曲线;(6)重复2)~5)的步骤,直到达到要求为止。
回流焊接的技术整合管理 第二部份:回流焊接技术的种类和原理

回流焊接的技术整合管理第二部份:回流焊接技术的种类和原理前言:在上期刊登的本系列的第一篇文章中我和读者们分享了‘技术整合’的概念。
本期我们进一步来看看回流技术的种类和原理。
了解各种回流技术能够让我们更好计划我们的工艺技术发展路标,让我们选择最适合的技术配搭,以及让我们了解故障模式的形成和焊接工艺的关系,对我们处理和预防问题的效率起着关键性的作用。
回流焊接的定义:在电子板组装焊接技术中存在两大类别。
一是‘单流’焊接工艺技术(Flow Soldering Process)。
另一就是‘回流’或‘再流’焊接工艺技术(Reflow Soldering Process)。
这两大类技术的主要差别在于焊接过程中的焊料(如SnPb)和形成焊点的热能是否分开或同时出现。
在单流焊接中,焊料和热能是同时加在焊点上的,例如手工锡丝焊接和波峰焊接就是属于这种分类。
而在回流焊接中,焊料(一般是锡膏或固态焊料)却是和热能(如回流炉子的热风)在不同的工序中加入的。
回流焊接技术的种类:从以上的定义中,我可以猜测得出,回流焊接技术就不只是我们经常见到使用锡膏印刷,而后热风回流炉子来焊接的一类工艺技术了。
事实上回流焊接工艺的种类比起单流焊接工艺种类的来得多。
而且各有其能力上的优点和相对的应用范围。
电子组装业界中有不少焊接工艺是属于回流类的,有些已经或即将成为历史,例如气相焊接工艺就是。
本篇将只介绍目前还在使用中的以下8种。
1.热板技术;2.热压技术;3.热风/热气技术;4.发热光(白光)技术;5.激光技术;6.红外线技术;7.电感发热技术;8.火炬技术。
工业界对焊接技术也有另外一种分类的做法,就是按照热的传递方式来分类。
也就是按‘传导’、‘辐射’和‘对流’传热模式来分类。
例如以上1和2类的热板和热压工艺都属于‘传导’加热工艺;第3类的热风属于‘对流’加热工艺;而第4到第6项则属于‘辐射’加热工艺。
至于那些不采用以上任何方法的,业界将其列为‘特别焊接技术’。
回流焊焊接关键工艺的研究

1 影 响 回流 焊 焊 接 质量 的主 要 因素
1 . 1 P C B焊盘 的设计 回流焊的焊接质量与 P C B焊盘设计 有直接的关系 如果 P C B焊 盘设计合 理 . 贴装时少 量的歪斜可 以在 回流焊时 . 由于熔 融焊锡表面 张力 的作用而得 到纠正 : 相反 . 如果 P C B焊 盘设计不合 理 , 即使 贴装 位置 十分准确 , 回流焊后反而会出现元件位 置偏移 、 桥连等焊接缺陷 。 1 . 2 焊膏质量及焊膏的正确使用 焊膏质量包括焊膏 中的金属微粉含量 、 金属粉末的含氧量 、 粘度 、 保形性等 : 焊 膏的使用方法要 正确 , 如从低 温柜取 出焊膏必 能直接使 用等 1 - 3 元器件引脚 、 印制电路板的焊盘质量 包括焊盘和引脚的氧化和污染 . 或印制板受潮等情况 1 . 4 焊膏的印刷质量 包括印刷位置正确与否 、 焊膏量 的多少 、 焊 锡量是否均匀 、 焊膏图 形是否清晰 . 有无粘连 、 印制板表面是否被焊膏粘污等 。
元 器件最终在回流炉的焊接 中完成连接 。 本 文针对 回流焊接工艺 中常见的焊接缺 陷。 分析 了对 回流焊焊接质量的影响 因素 . 并对其 中关键工艺
进 行 了研 究 。
【 关键词 】 S M T ; 回流焊; 锡 膏印刷 ; 温度 曲线 0 引 言
由于表面贴装组装件 密度高 、 电子产品体积小 、 重量轻 . 贴 片元件 的体积和重量只有传统插装元件 的 1 / 1 0左 右.一 般采用 表面贴装技 术后 。 电子产品体积缩小 4 0 %~ 6 0 %. 重量减轻 6 0 %~ 8 0 % 以上 因此 表 面贴装 技术 已越来越多地应用 到各个领域 。典 型的 S MT工艺分为 j 三 步: 在 印制 板上涂 覆焊膏——贴装元器 件—— 回流 焊接 . 每个步骤 都 必须严格控制 . 才能获得合格的产品质量 回流焊后产 品常见的质量缺陷有 : 桥连 、 锡珠、 立碑 、 P C B板翘 曲 、 印制板阻焊膜起泡 、 虚焊等。 对桥连 、 锡珠 、 立碑 和虚焊 缺陷, 在焊后 的 检查 中发现 , 还 可以修复 . 而 如果 出现 P C B板翘 曲 、 印制板起 泡的缺 陷. 就很可能造成 印制 板及 板上元器件 的报废 , 会造成很 大的经济和 时 间损 失 以下的细间距元器 件的印刷 . 必须采用不锈钢板 2 . 1 . 1 模板厚度 模板厚度如果 太薄 . 锡膏量少 , 焊点成 型不好 , 机械性 能不 良; 太 厚则易引起桥连 一般对于阻容元件和 1 . 2 7 a r m间距期间 . 采用 0 . 2 0 ~ 0 . 2 5 a r m厚度 的模板 印刷 : 对 于窄间距器件 . 采用 0 . 1 0 ~ 0 . 2 0厚度 的模 板 印刷 : 如0 . 6 4 a r m间距器件或更小 间距 器件 . 通常采用 0 . 2 0 am厚度 r 的金属模板 印刷 : 0 . 5 0 m m 间距 器件采用 0 . 1 5 mm厚度 的模板 印刷 : 对 于1 . 2 7 am和 0 r . 5 0 mm窄间距 器件混装 .可选 用 0 . 1 5 m m与 0 . 2 0 am之 r 间的模板 印刷 2 . 1 . 2 印刷 参 数 刮刀的速度 和压力决定 了焊膏所受 的剪切速率和剪切力大小。 刮 刀压力一定 的情况下 . 将印刷速度调慢 , 可保持焊膏 的黏度 基本不变 , 供 给焊膏 的时 间加长 , 焊膏量 增多 , 成 型较好 , 其值一 般 为 l O m m / s ~ 2 5 m m / s 另外如果模板与印刷板 之间存在接触 障碍 . 在 刮挤 时锡膏就 会被 挤出焊 盘或粘在模板底面 .在模板离开时就会产 生焊 膏塌陷 . 导 致 桥 连现 象 。一 般 模 板 与 P C B 的最 小 间 隙 ≤O . 2 0 am。 r 2 . 2 回流焊温度 曲线 : 回流焊 的 目的是将 印刷好 的锡膏熔融 . 将器件 的引脚 和印制板的 焊 盘连接起 来 . 最终完成 电气功能的导通 。 理想的 回流 焊温度曲线 由四个 部分或 区间组 成 .前面 三个 加热 区、 最后一个冷却 区 回流炉的温区越 多. 越 能使温度 曲线 的轮廓达到 更 准确 和接 近设定 大多数锡膏都能用 四个基本温区成功回流. .
阐述如何优化回流焊接工艺及质量缺陷

阐述如何优化回流焊接工艺及质量缺陷摘要:回流焊接工艺目前在国内社会应用相对广泛,但是,受回流焊接工艺传输速度快慢、温区温度变化差异、贴片机贴装精度等影响,常常会导致回流焊接产品出现质量问题,影响产品品质。
所以,做好回流焊接工艺及质量缺陷优化研究十分必要。
关键词:回流焊接工艺;锡珠;锡桥;优化引言:回流焊接工艺在实践应用操作中相对简单、焊接质量较高、焊接效率突出,更能实现成本节约,为自动化生产奠定了基础,所以,在社会中得到了广泛的使用。
回流焊接工艺作为目前表面贴装元器件焊接的关键工艺,做好工艺运用时产生的质量缺陷优化处理,方可提高回流焊接工艺应用价值。
(一)回流焊接工艺简析1.工艺流程回流焊还被唤作再流焊,通常是在贴片完成后的锡膏印刷电路板上实施回流焊接,主要过程为“利用回流焊机焊接贴装完成的电路板,采用回流加热的形式溶解焊锡膏,历经干燥-预热-融化-润湿-冷却步骤处理后,采用焊接方式焊接贴片元器件和印制板”,该技术流程又被唤作新型焊接技术。
2.工艺特点一是,能够控制回流焊点大小。
一般可通过控制焊盘设计尺寸、印刷焊膏量的方式控制焊点尺寸、形状等。
回流焊一般在操作的位置上放焊料即可,且用料量精准可控,无需在熔融的焊料中直接浸渍元器件,因此热冲击对元器件产生的影响较小。
二是,放焊膏时常选择钢网印刷形式,一般为了精简工艺流程、缩减生产成本,在实践中各焊接面通常仅印刷一次焊膏。
该特点要求所有装配面上的元器件则必须共用同一张钢网分配焊膏。
三是,焊料中的成分不会混入不纯物,保证焊料的组分。
可在同一基板上,波峰焊和回流焊可以混合使用。
[1](二)回流焊接质量缺陷与优化方法受回流焊接传输速度不快、温区间温度变化、贴片机贴装精度等因素影响,回流焊接工艺在实际操作中存在些许缺陷,诸如锡珠、锡桥等现象都比较常见。
1.锡珠锡珠和焊球相似,但是体积相对较小,锡珠的出现,主要是因为焊接前锡膏受各种因素影响超出焊盘,且焊接后单独出现在焊盘、引脚外侧,没有和锡膏彻底融合,以此形成的锡珠;锡珠一般在元器件两侧、细间距引脚间出现的几率较高,常会引发电路板短路等问题,锡珠质量缺陷见图一。
回流焊接工艺及常见质量缺陷的改进方法

图1回流焊接温度曲线图
预热区:从室温升高至120℃左右,升温时间60-80s,目的是对电路板上所有元器件进行预热,以达到第二温区的温度。
但是,在预热过程中升温速率应控制在适当的范围内,若升温速率太慢,锡膏中的水分不能尽快挥发,若升温速率太快,则电路板预热不够充分;因此升温区温度上升速率一般设置为1-2℃/s。
升温区:从120℃升高至210℃,升温时间90-120s,
2.1.1锡珠形成的原因
①回流焊机升温区温度设置不当,若预热时间短不充分,助焊剂活性较低不能去除焊盘和焊料颗粒表面的氧
[2]焊接时,升温区温度上升速度较快、时间较长,焊锡膏内部的助焊剂就会快速挥发出来,便会出现细间距引脚润湿不良,临界焊膏量减少,容易引起桥接现象。
2.3.1立碑形成的原因
①贴片机贴装精度不够,贴装时元器件产生了偏移且大于允许值的15%,在回流焊接时由于锡膏熔化而造成表面的拉力不一样,拉力较大的一端拉着元器件沿其底部旋
图2锡珠质量缺陷示意图
图3锡桥质量缺陷示意图
图4立碑质量缺陷示意图
图1试板焊接坡口及拼装示意图
焊接及热处理工艺
采用水平熔化焊和水平对接的气体保护焊,保护气体80%Ar+20%CO2,保护气体流量15-20L/min。
选用两组不同的焊接参数作为对比试验,焊接线能量分别为22kJ/cm和27.6kJ/cm。
为了保证焊接接头的质量,焊接前要预热50℃,并严格控制焊接过程中夹层温度小150℃。
焊后热处理温度600-620℃[1]。
焊接坡口形式见。
回流焊无铅焊接的特点和对策

回流焊无铅焊接的特点和对策一、无铅焊接技术的现状无铅焊料合金成分的标准化目前还没有明确的规定。
IPC等大多数商业协会的意见:铅含量<0.1-0.2WT%(倾向<0.1%,并且不含任何其它有毒元素的合金称为无铅焊料合金。
1、无铅焊料合金无铅化的核心和首要任务是无铅焊料。
据统计全球范围内共研制出焊膏、焊丝、波峰焊棒材100多种无铅焊料,但真正公认能用的只有几种。
(1)目前最有可能替代Sn/Pb焊料的合金材料最有可能替代Sn/Pb焊料的无毒合金是Sn基合金。
以Sn为主,添加Ag、Cu、Zn、Bi、In、Sb等金属元素,构成二元、三元或多元合金,通过添加金属元素来改善合金性能,提高可焊性、可靠性。
主要有:Sn-Bi系焊料合金,Sn-Ag共晶合金,Sn-Ag-Cu三元合金,Sn-Cu系焊料合金,Sn-Zn系焊料合金(仅日本开发应用),Sn-Bi系焊料合金,Sn-In和Sn-Pb 系合金。
(2)目前应用最多的无铅焊料合金三元共晶形式的Sn95.8\Ag3.5\Cu0.7(美国)和三元近共晶形式的Sn96.5\Ag3.0\Cu0.5(日本)是目前应用最多的用于再流焊的无铅焊料。
其熔点为216-220℃左右。
由于Sn95.8\Ag3.5\Cu0.7无铅焊料美国已经有了专利权,另外由于Ag含量为3.0WT%的焊料没有专利权,价格较便宜,焊点质量较好,因此IPC推荐采用Ag含量为3.0WT%(重量百分比)的Sn-Ag-Cu焊料。
Sn-0.7Cu-Ni焊料合金用于波峰焊。
其熔点为227℃。
虽然Sn基无铅合金已经被较广泛应用,与Sn63\Pb37共晶焊料相比无铅合金焊料较仍然有以下问题:(A)熔点高34℃左右。
(B)表面张力大、润湿性差。
(C)价格高2、PCB焊盘表面镀层材料无铅焊接要求PCB焊盘表面镀层材料也要无铅化,PCB焊盘表面镀层的无铅化相对于元器件焊端表面的无铅化容易一些。
目前主要有用非铅金属或无铅焊料合金取代Pb-Sn热风整平(HASL)、化学镀Ni和浸镀金(ENIC)、Cu表面涂覆OSP、浸银(I-Ag)和浸锡(I-Sn)。
回流焊接技术的工艺要点和技术整合考虑
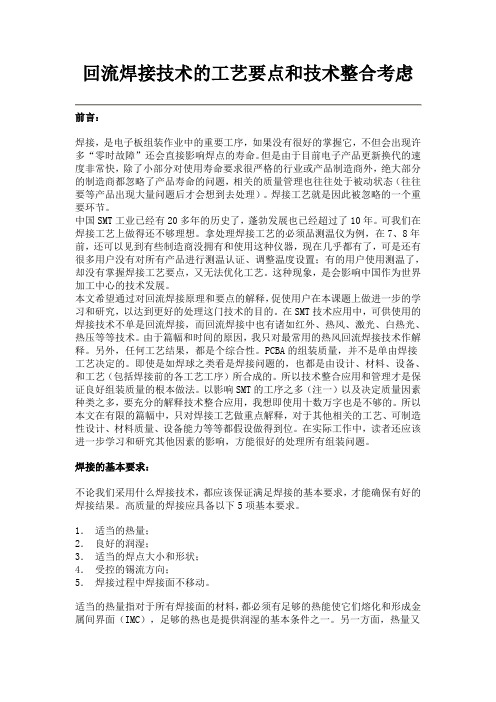
回流焊接技术的工艺要点和技术整合考虑前言:焊接,是电子板组装作业中的重要工序,如果没有很好的掌握它,不但会出现许多“零时故障”还会直接影响焊点的寿命。
但是由于目前电子产品更新换代的速度非常快,除了小部分对使用寿命要求很严格的行业或产品制造商外,绝大部分的制造商都忽略了产品寿命的问题,相关的质量管理也往往处于被动状态(往往要等产品出现大量问题后才会想到去处理)。
焊接工艺就是因此被忽略的一个重要环节。
中国SMT工业已经有20多年的历史了,蓬勃发展也已经超过了10年。
可我们在焊接工艺上做得还不够理想。
拿处理焊接工艺的必须品测温仪为例,在7、8年前,还可以见到有些制造商没拥有和使用这种仪器,现在几乎都有了,可是还有很多用户没有对所有产品进行测温认证、调整温度设置;有的用户使用测温了,却没有掌握焊接工艺要点,又无法优化工艺。
这种现象,是会影响中国作为世界加工中心的技术发展。
本文希望通过对回流焊接原理和要点的解释,促使用户在本课题上做进一步的学习和研究,以达到更好的处理这门技术的目的。
在SMT技术应用中,可供使用的焊接技术不单是回流焊接,而回流焊接中也有诸如红外、热风、激光、白热光、热压等等技术。
由于篇幅和时间的原因,我只对最常用的热风回流焊接技术作解释。
另外,任何工艺结果,都是个综合性。
PCBA的组装质量,并不是单由焊接工艺决定的。
即使是如焊球之类看是焊接问题的,也都是由设计、材料、设备、和工艺(包括焊接前的各工艺工序)所合成的。
所以技术整合应用和管理才是保证良好组装质量的根本做法。
以影响SMT的工序之多(注一)以及决定质量因素种类之多,要充分的解释技术整合应用,我想即使用十数万字也是不够的。
所以本文在有限的篇幅中,只对焊接工艺做重点解释,对于其他相关的工艺、可制造性设计、材料质量、设备能力等等都假设做得到位。
在实际工作中,读者还应该进一步学习和研究其他因素的影响,方能很好的处理所有组装问题。
焊接的基本要求:不论我们采用什么焊接技术,都应该保证满足焊接的基本要求,才能确保有好的焊接结果。
回流焊工艺技术论文总结

回流焊工艺技术论文总结回流焊工艺技术是一种目前较为常用的电子组装工艺,能够有效实现小尺寸、高密度和高质量的电子产品制造。
本文就回流焊工艺技术进行了研究和总结,具体包括工艺步骤、设备要求、工艺参数和质量控制等方面。
回流焊工艺技术一般包括以下几个步骤:首先是印刷焊膏,即将焊膏粘贴在PCB(Printed Circuit Board)上,以确保焊点的可靠性。
接着是贴装元件,即将所需的元件贴到PCB上的焊膏上,通常采用自动贴装机完成,提高了生产效率。
然后是预热阶段,通过预热使焊膏中的挥发物挥发掉,以避免焊接过程中引起不良。
接下来是焊接阶段,将PCB放入回流焊炉中进行焊接,通过加热使焊膏熔化,达到焊接的目的。
最后是冷却阶段,将焊接完的PCB冷却,以固化焊接点。
回流焊的设备要求包括回流焊炉、传送机构和温度控制系统等。
回流焊炉是整个工艺中最重要的设备,其主要作用是加热焊接区域,并通过传送机构使PCB通过回流焊炉。
温度控制系统则能够精确控制回流焊炉的加热温度和时间,以确保焊接质量。
针对回流焊工艺技术,关键的参数包括焊接温度、焊接时间和传送速度等。
焊接温度应根据焊膏的要求进行设置,一般在180-240度之间;焊接时间则取决于焊膏的熔点和PCB的传送速度,一般为1-3分钟;传送速度则应根据焊接工艺和焊接质量要求进行调整。
在回流焊工艺中,质量控制是非常重要的环节,主要体现在焊接质量和焊接返修等方面。
对于焊接质量的控制,可以通过焊接温度和焊接时间的控制,以及焊接工艺的优化来提高焊接质量。
而对于焊接返修,主要通过对焊接点的检测和测试,如焊接点外观、焊接点电阻和焊接点可靠性等指标进行评价和判断,以及对不良焊接点的修复等。
综上所述,回流焊工艺技术是目前较为常用的电子组装工艺之一,具有高效、高质量、高稳定性等优点。
通过合理的工艺步骤、设备要求、工艺参数和质量控制,可以实现对回流焊工艺的控制和优化,从而提高电子产品的质量和可靠性。
回流焊接技术的工艺要点和技术整合考虑
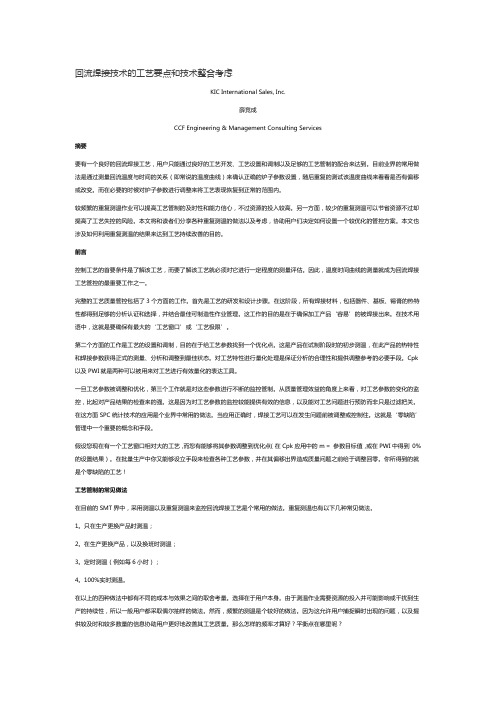
回流焊接技术的工艺要点和技术整合考虑KIC International Sales, Inc.薛竞成CCF Engineering & Management Consulting Services摘要要有一个良好的回流焊接工艺,用户只能通过良好的工艺开发、工艺设置和调制以及足够的工艺管制的配合来达到。
目前业界的常用做法是通过测量回流温度与时间的关系(即常说的温度曲线)来确认正确的炉子参数设置,随后重复的测试该温度曲线来看看是否有偏移或改变。
而在必要的时候对炉子参数进行调整来将工艺表现恢复到正常的范围内。
较频繁的重复测温作业可以提高工艺管制的及时性和能力信心,不过资源的投入较高。
另一方面,较少的重复测温可以节省资源不过却提高了工艺失控的风险。
本文将和读者们分享各种重复测温的做法以及考虑,协助用户们决定如何设置一个较优化的管控方案。
本文也涉及如何利用重复测温的结果来达到工艺持续改善的目的。
前言控制工艺的首要条件是了解该工艺,而要了解该工艺就必须对它进行一定程度的测量评估。
因此,温度时间曲线的测量就成为回流焊接工艺管控的最重要工作之一。
完整的工艺质量管控包括了3个方面的工作。
首先是工艺的研发和设计步骤。
在这阶段,所有焊接材料,包括器件、基板、锡膏的热特性都得到足够的分析认证和选择,并结合最佳可制造性作业管理。
这工作的目的是在于确保加工产品‘容易’的被焊接出来。
在技术用语中,这就是要确保有最大的‘工艺窗口’或‘工艺极限’。
第二个方面的工作是工艺的设置和调制,目的在于给工艺参数找到一个优化点。
这是产品在试制阶段时的初步测温,在此产品的热特性和焊接参数获得正式的测量、分析和调整到最佳状态。
对工艺特性进行量化处理是保证分析的合理性和提供调整参考的必要手段。
Cpk 以及PWI就是两种可以被用来对工艺进行有效量化的表达工具。
一旦工艺参数被调整和优化,第三个工作就是对这些参数进行不断的监控管制。
从质量管理效益的角度上来看,对工艺参数的变化的监控,比起对产品结果的检查来的强。
回流焊工艺技术和注意事项

回流焊工艺技术和注意事项远红外再流焊八十年代使用的远红外再流焊具有加热快、节能、运行平稳的特点,但由于印制板及各种元器件因材质、色泽不同而对辐射热吸收率有很大差异,造成电路上各种不同元器件以及不同部位温度不均匀,即局部温差。
例如集成电路的黑色塑料封装体上会因辐射吸收率高而过热,而其焊接部位银白色引线上反而温度低产生假焊。
另外,印制板上热辐射被阻挡的部位,例如在大(高)元器件阴影部位的焊接引脚或小元器件就会因加热不足而造成焊接不良。
1.2 全热风再流焊全热风再流焊是一种通过对流喷射管嘴或者耐热风机来迫使气流循环,从而实现被焊件加热的焊接方法。
该类设备在90年代开始兴起。
由于采用此种加热方式,印制板和元器件的温度接近给定的加热温区的气体温度,完全克服了红外再流焊的温差和遮蔽效应,故目前应用较广。
在全热风再流焊设备中,循环气体的对流速度至关重要。
为确保循环气体作用于印制板的任一区域,气流必须具有足够快的速度。
这在一定程度上易造成印制板的抖动和元器件的移位。
此外,采用此种加热方式就热交换方式而言,效率较差,耗电较多。
1.3 红外热风再流焊这类再流焊炉是在IR炉基础上加上热风使炉内温度更均匀,是目前较为理想的加热方式。
这类设备充分利用了红外线穿透力强的特点,热效率高,节电,同时有效克服了红外再流焊的温差和遮蔽效应,并弥补了热风再流焊对气体流速要求过快而造成的影响,因此这种IR+Hot的再流焊目前在国际上是使用得最普遍的。
随着组装密度的提高、精细间距组装技术的出现,还出现了氮气保护的再流焊炉。
在氮气保护条件下进行焊接可防止氧化,提高焊接润湿力,加快润湿速度,对未贴正的元件矫正力大,焊珠减少,更适合于免清洗工艺。
2 温度曲线的建立。
回流焊的分类及发展
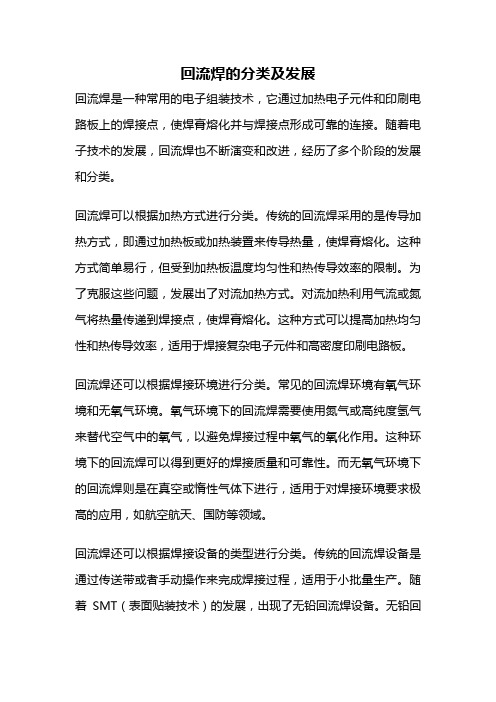
回流焊的分类及发展回流焊是一种常用的电子组装技术,它通过加热电子元件和印刷电路板上的焊接点,使焊膏熔化并与焊接点形成可靠的连接。
随着电子技术的发展,回流焊也不断演变和改进,经历了多个阶段的发展和分类。
回流焊可以根据加热方式进行分类。
传统的回流焊采用的是传导加热方式,即通过加热板或加热装置来传导热量,使焊膏熔化。
这种方式简单易行,但受到加热板温度均匀性和热传导效率的限制。
为了克服这些问题,发展出了对流加热方式。
对流加热利用气流或氮气将热量传递到焊接点,使焊膏熔化。
这种方式可以提高加热均匀性和热传导效率,适用于焊接复杂电子元件和高密度印刷电路板。
回流焊还可以根据焊接环境进行分类。
常见的回流焊环境有氧气环境和无氧气环境。
氧气环境下的回流焊需要使用氮气或高纯度氢气来替代空气中的氧气,以避免焊接过程中氧气的氧化作用。
这种环境下的回流焊可以得到更好的焊接质量和可靠性。
而无氧气环境下的回流焊则是在真空或惰性气体下进行,适用于对焊接环境要求极高的应用,如航空航天、国防等领域。
回流焊还可以根据焊接设备的类型进行分类。
传统的回流焊设备是通过传送带或者手动操作来完成焊接过程,适用于小批量生产。
随着SMT(表面贴装技术)的发展,出现了无铅回流焊设备。
无铅回流焊设备采用特殊的焊膏和工艺参数,以满足环保要求和提高焊接质量。
随着电子技术的不断进步和应用领域的不断扩大,回流焊也在不断发展。
未来的回流焊技术将更加注重能耗和环保,采用更加智能化的控制系统和先进的加热方式,以提高生产效率和焊接质量。
同时,随着电子元件的微型化和高密度集成,回流焊还将面临更大的挑战,需要更精密的焊接工艺和设备来满足需求。
回流焊经历了多个阶段的发展和分类,包括加热方式、焊接环境和设备类型等。
随着电子技术的不断发展,回流焊也在不断演变和改进,为电子组装提供了可靠和高效的焊接解决方案。
未来,回流焊将继续发展,以满足不断变化的电子行业需求。
回流焊接技术及工艺的研究
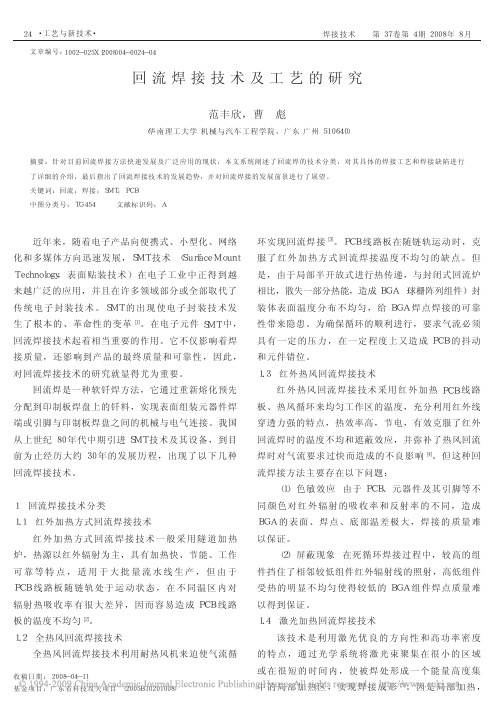
近年来,随着电子产品向便携式、小型化、网络化和多媒体方向迅速发展,SMT技术(SurfaceMountTechnology,表面贴装技术)在电子工业中正得到越来越广泛的应用,并且在许多领域部分或全部取代了传统电子封装技术。
SMT的出现使电子封装技术发生了根本的、革命性的变革[1]。
在电子元件SMT中,回流焊接技术起着相当重要的作用。
它不仅影响着焊接质量,还影响到产品的最终质量和可靠性,因此,对回流焊接技术的研究就显得尤为重要。
回流焊是一种软钎焊方法,它通过重新熔化预先分配到印制板焊盘上的钎料,实现表面组装元器件焊端或引脚与印制板焊盘之间的机械与电气连接。
我国从上世纪80年代中期引进SMT技术及其设备,到目前为止经历大约30年的发展历程,出现了以下几种回流焊接技术。
1回流焊接技术分类1.1红外加热方式回流焊接技术红外加热方式回流焊接技术一般采用隧道加热炉,热源以红外辐射为主,具有加热快、节能、工作可靠等特点,适用于大批量流水线生产,但由于PCB线路板随链轨处于运动状态,在不同温区内对辐射热吸收率有很大差异,因而容易造成PCB线路板的温度不均匀[2]。
1.2全热风回流焊接技术全热风回流焊接技术利用耐热风机来迫使气流循环实现回流焊接[3]。
PCB线路板在随链轨运动时,克服了红外加热方式回流焊接温度不均匀的缺点。
但是,由于局部半开放式进行热传递,与封闭式回流炉相比,散失一部分热能,造成BGA(球栅阵列组件)封装体表面温度分布不均匀,给BGA焊点焊接的可靠性带来隐患。
为确保循环的顺利进行,要求气流必须具有一定的压力,在一定程度上又造成PCB的抖动和元件错位。
1.3红外热风回流焊接技术红外热风回流焊接技术采用红外加热PCB线路板、热风循环来均匀工作区的温度,充分利用红外线穿透力强的特点,热效率高,节电,有效克服了红外回流焊时的温度不均和遮蔽效应,并弥补了热风回流焊时对气流要求过快而造成的不良影响[4]。
但这种回流焊接方法主要存在以下问题:(1)色敏效应由于PCB、元器件及其引脚等不同颜色对红外辐射的吸收率和反射率的不同,造成BGA的表面、焊点、底部温差极大,焊接的质量难以保证。
回流焊工艺分析
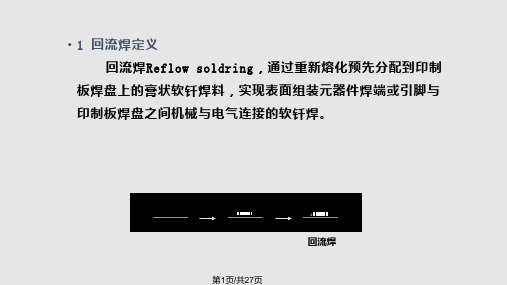
•
g 环境温度对炉温也有影响,特别是加热温区短、炉体宽度窄
的 回 流 焊 炉 , 在 炉 子 进 出 口第1处0页/要共2避7页免 对 流 风 。
• (7) 回流焊设备的质量
• 回流焊质量与设备有十分密切的关系。影响回流焊质量的主要参数: • a 温度控制精度应达到±0.1—0.2℃(温度传感器的灵敏度); • b 传输带横向温差要求±5℃以下,否则很难保证焊接质量; • c 传送带宽度要满足最大PCB尺寸要求; • d 加热区长度——加热区长度越长、加热区数量越多,越容易调整
高;助焊性能差;或焊膏使用不当: 度:如在有效期内使用;从冰箱取出焊
没有回温或使用回收与过期失效焊膏 膏,达到室温后才能打开容器盖;回收
的焊膏不能与新焊膏混装等。 第13页/共27页
(2) 润湿不良——又称不润湿或半润湿。元器件焊端、引脚 或印制板焊盘不沾锡或局部不沾锡。
润湿不良原因分析
预防对策
a 元器件焊端、引脚、印制 元器件先到先用,不要
• 1 回流焊定义 回流焊Reflow soldring,通过重新熔化预先分配到印制
板焊盘上的膏状软钎焊料,实现表面组装元器件焊端或引脚与 印制板焊盘之间机械与电气连接的软钎焊。
第1页/共27页
回流焊
2 回流焊原理
PCB 入口
110℃ 130℃ 155℃ 185℃ 240℃ 250℃ 90℃ 出口
有无BGA、CSP等特殊元器件进行设置。
第9页/共27页
•
d 还要根据设备的具体情况,例如加热区长度、加热源材料、
回流焊炉构造和热传导方式等因素进行设置。
•
热风炉和红外炉有很大区别,红外炉主要是辐射传导,其优点
是热效率高,温度陡度大,易控制温度曲线,双面焊时PCB上、下
回流炉回流焊接技术分析答辩稿
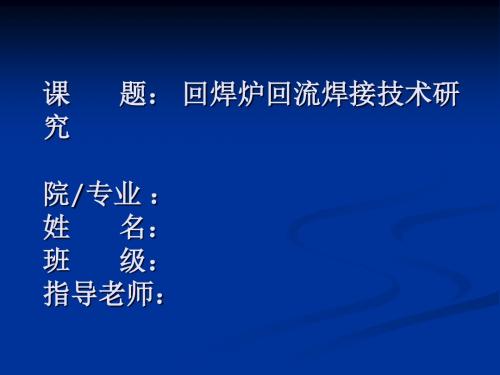
题: 回焊炉回流焊接技术研
院/专业 : 姓 名: 班 级: 指导老师:
第一章 课题背景
1.1 SMT回流焊接的目的和意义
1.2 回流焊接技术的发展 1.3 回流焊接技术目前存在的问题
1.1 回流焊接的目的和意义
目的:回流焊接将已置放在锡膏上所 有表面粘着元件的PC,经过预热活化 助焊剂,使零件焊接在印刷板上。 意义:最终使PCB经置件后的零件达到 稳定结合。
3.6环境因素影响
3.6.1 热风影响 3.6.2 链速的控制 3.6.3 风速和风量的影响
第四章 维护保养
4.1
进板端保养 4.2 FLUX收集装置保养 4.3 炉内保养
第五章 总结
回流焊工艺是当前表面贴装技术中最重要的焊接工艺,它 已在包括手机,电脑,汽车电子,控制电路、通讯、LED 照明等许多行业得到了大规模的应用。越来越多的电子原 器件从通孔转换为表面贴装,回流焊在相当范围内取代波 峰焊已是焊接行业的明显趋势。 所以如何进一步提高回流焊接技术,规避电路板生产的问 题,需要SMT工程师和科研人员的努力。通过六个月的实 习,我了解了回流焊接技术在现代工业中的运用,同时在 回流焊接时各个时间段的作用。不同焊接方式的选择,对 电路板的影响,SMT工程师采用不同的方式进行改进。 在现在电子工业中,我觉得应该加强企业对回流焊接技术 的监察控制,确认回流焊接后电路板的质量,将回流焊基 本操作作为全员培训的内容。
1.2 SMT回流焊接技术的发展
1.2.1
红外线辐射回流焊接 1.2.2 全热风回流焊接 1.2.3 红外线加热风回流焊接 1.2.4 充氮(N2)回流焊
- 1、下载文档前请自行甄别文档内容的完整性,平台不提供额外的编辑、内容补充、找答案等附加服务。
- 2、"仅部分预览"的文档,不可在线预览部分如存在完整性等问题,可反馈申请退款(可完整预览的文档不适用该条件!)。
- 3、如文档侵犯您的权益,请联系客服反馈,我们会尽快为您处理(人工客服工作时间:9:00-18:30)。
关于回流焊工艺发展的讨论2003-6-18 9:00:31 文章作者:本站新闻管理员阅读818次双击鼠标自动滚屏,单击停止最近几年,SMT生产技术已发生了巨大的变化,其中:生产标准的改变,新型焊膏的利用、不同基材的出现,以及元器件本身材料和设计的革新都使得热处理工艺不断发展。
新型元器件的设计动力是来自于产品小型化的不断驱使。
这些新型元器件封装包括:BGA(球栅阵列)、COB(裸芯片)、CSP(微型封装)、MCM(多芯片模块),以及flip chip(倒装片)等。
产品小型化回流焊使得元器件越做越小,并使管脚数增加,使间距变小。
另外为减少成本,免清洗和低残留焊膏使用的更加广泛,与之相应的是氮气的使用也随之增加。
市场对手持式电子产品的不断需求始终是一个强大的驱动力,它使得封装工艺必须适应这些产品的技术要求。
因此更小、更密、更轻的组装技术,以及更短的产品周期、更多、更密的I/O引线,更强的可操控性----都把回流焊技术提到一个新的层次上来讨论。
同时也对热处理工艺的控制手段和设备提出了新的要求。
考虑到这些压力,我们提出了一个简单的设想图,其中的一些方案可以回答回流焊工艺今后会遇到的挑战。
氮气惰性保护使用惰性气体,一般采用氮气,这种方法在回流焊工艺中已被采用了相当长的一段时间,但它的价格还是一个问题。
因为惰性气体可以减少焊接过程中的氧化,因此,这种工艺可以使用活性较低的焊膏材料。
这一点对于低残留物焊膏和免清洗尤为重要。
另外,对于多次焊接工艺也相当关键。
比如:在双面板的焊接中,氮气保护对于带有OSPs的板子在多次回流工艺中有很大的优势,因为在N2的保护下,板上的铜质焊盘与线路的可焊性得到了很好的保护。
使用氮气的另一个好处是增加表面张力,它使得制造商在选择器件时有更大的余地(尤其是超细间距器件),并且增加焊点表面光洁度,使薄型材料不易褪色。
真正最大的好处是降低了成本。
氮气保护的费用取决于各种各样的因素,包括氮气在机器中使用的位置,氮气的利用率等。
当然,我们通常感觉氮气消耗是一种工艺过程中额外的费用,因此总是想方设法减少氮气的消耗。
目前焊膏的化学成份也在不断的改进提高,以便将来的工艺中不再使用氮气保护;或者至少在较高的O2浓度值下(比如:1000ppm对比目前为50ppm)取得良好的焊接效果,以便减少氮气的用量。
对于是否使用氮气的保护,我们必须综合考虑许多问题,包括:产量要求的质量等级,以及每一对应的氮气消耗费用。
使用氮气是有费用的问题,但是如果将它对提高产量与质量所带来的好处计算进来,那么它的费用是相对微不足道的。
如果焊接炉不是强制回流的那一种,并且气流是分层状态,那么氮气的消耗是比较容易控制的。
但是,目前大多数炉的工作方式都是大容量循环强制对流加热,炉体内的气流是在不停的流动,这给氮气的控制与消耗提出了一个新的难题。
一般,我们采取这几种方法降低氮气用量。
首先,必须减少炉体进口的尺寸,尤其是垂直方向上的开口尺寸,使用遮挡板、卷帘幕,或者利用一些其它的东西来堵住进出口的孔隙。
由遮挡板、卷帘幕向下形成的隔离区可以阻挡氮气的外泄,并且使外部的空气无法进入炉体内部,也有些回流炉是采用自动的滑动门来隔离空气。
另外一种方法是基于这样一个科学概念:被加热的氮气将漂浮于空气之上,并两种气体不会混合。
因此,回流炉的加热腔被设计成比进出口的位置高一些,因为氮气会自然的与空气分层,这样便可以用很少的氮气供给量来保持一个较纯的浓度。
双面加工双面板工艺越来越多的被采用,并且变得更加复杂。
这是因为它能给设计者提供更大、更灵活的设计空间。
双面板大大加强了PCB的实际利用率,因此降低了制造成本。
到目前为止,双面板经常采用的工艺是上面过回流炉,下面过波峰焊炉。
今天大家都逐渐倾向于双面都过回流炉是一种更佳的方法。
但工艺上仍有一些问题,比如:再次回流时,底部较大的元件或许会掉下来,或者底部的焊点会部分重新熔化,以至于影响到焊点的可靠性。
有几种方法已发展出来用以完成二次回流,其中之一将第一面的元件上胶固化,使它在翻面过二次回流时不会从板上掉下来,并且保持正确的位置。
另外一种方法是使用不同熔点的焊膏,其中第二次回流时使用的焊膏熔点较第一次的要低。
但是使用方法有一些严重的问题需要注意:第一个是造成了最后的成品在维修有一个“太低”的熔化温度;第二个是如果使用更高一级的回流温度又会造成对元器件和基板的热冲击。
对于大多数元件来说,二次回流时,焊点熔锡的表面张力是足已维持元件在底部的粘力,使元件牢牢的固定在基板上。
这里有一个元件重量与引脚(焊盘)张力的比例关系,它可以计算出元件在二次回流时能不能粘贴在基板底部而不会掉落,从而不用对每一个元器件都做实际的测试。
30g/in2是一个保守值,可以作为设计的标准。
另外一个方法是采用一种概念:即将冷的气体吹拂过基板底部,使底部的温度在二次回流时始终达不到熔点,但是由于基板上下面的温差可能会导致有潜在的应力产生。
虽然二次回流的工艺并不简单,但许多问题都在被不断解决掉,今后几年内,我们可以肯定的说,无论是在数量上还是在复杂程度上,高密度的双面板都将有一个长远的发展。
通孔通孔回流焊(也称插入式或带引针式回流焊)工艺在最近一段时期内应用得越来越广泛,因为它可以少过波峰焊这个工序,或者混装板(SMT与THT)也会用到它。
这样做最主要的好处是可以利用现有的SMT设备来组装通孔式的接插件,因为通孔式的接插件有较好的焊点机械强度。
在许多的产品中,表面贴装式的接插件不能提供足够的机械强度。
另外,在大面积的PCB上,由于平整度的关系,很难使表面贴装式的接插件的所有引脚都与焊盘有一个牢固的接触。
虽然好的工艺可以用来处理通孔回流焊,但仍有一些值得讨论的问题。
首先是通孔回流焊的焊膏用量特别大,因此在助焊剂挥发后形成的残留物也很多,会造成对机器的污染,所以助焊剂挥发管理系统有尤为重要。
另外一个问题是许多通孔元器件,尤其是接插件,并非设计成可以承受回流焊的高温。
基于红外回流炉(IR)的经验,如果用在通孔回流焊上是错误的。
因为它没有考虑到热传递效应对于大块元器件与几何形状复杂的元器件(比如有遮敞效应的元器件)的不同,现有混装经常使用SMD与THT元器件。
但对于强制热风回流炉来说,它有着极高的热传递效率,并不依靠红外辐射的高温。
因此在混装产品中,普遍使用强制热风回流工艺。
为了得到一个满意的焊接效果,问题的关键是要确保通孔回流焊基板各部份的焊膏量都恰到好处,以及注意那些不能承受温度变化与遮蔽效应的元器件,这个工艺发展的主要方向还是在工艺的完善与器件的改良上。
柔性基板为了处理表面安装柔性基板的焊接问题,一种专用的回流炉也被设计出来了,和一般回流炉最大的不同是在于它特殊的处理柔性基板的导轨。
但是,这种回流炉也必须同时满足已连续式的柔性PCB与分离式PCB的焊接需要。
在处理分离式PCB基板时,回流炉的工作连续性并不受前道工序的影响。
在卷式柔性基板的生产中,由于柔性基板是整条贯穿生产线,所以生产线上任何一处造成的停机都会使柔性基板带停止传递。
这样就会产生一个问题:停在炉内的柔性基板便会因高温而遭到破坏。
因此,这种特殊的炉必须允许这样情况发生:可以处理停在炉内的基板,并且在传送带恢复正常后立刻重新恢复正常的焊接操作。
无铅焊膏虽然近几年要求使用无铅焊膏的压力不象以前那样大,但人们依然关心焊膏中的含铅量与它对环境的影响,虽然电子业的铅污染只占所有铅污染量的百分之一以下,但有观察家还是认为有关禁止用含铅焊膏的法律在今后几年中将出台。
这样就只能努力去寻找一种可靠、经济的替代品。
许多代用品的熔点都比锡一铅合金高大约40°C。
这意味着回流炉需要工作在一个更高的温度环境中,这时使用氮气保护可以部份的消除高温所带来的PCB氧化与破坏的影响。
但是在实现无铅生产前,工业界是必须走一段痛苦的学习过程来解决将会面临的问题。
目前大多数炉的设计工作温度都在300°C以下,但无铅锡膏、非低熔点锡膏,在用于BGA、双面板、混装板的生产时,常需要更高的温度。
有一些工艺在回流区的温度需要350°C~400°C左右,因此必须改进炉的设计方案以迎合这种需求。
另一方面,进入高温炉的热敏感元件必须做改进,减少在进行高温操作时这些元件的受热量。
垂直烘炉市场对产品小型化的要求使倒焊片与DCA(芯片直接焊装)的应用越发的广泛。
倒焊片技术是将芯片倒装后用焊球将其与基板直接焊接,这样可以提高信号传输速度及减少尺寸。
另一种是底部填充工艺,这是将填充材料灌注入芯片与基板之间的空隙中,这是因为芯片与基板材料之间膨胀系数不一致,而填充材料则能保护焊点不受这种应力的影响。
还有是球状封顶以及围坝填充技术,这两种技术是用覆盖材料将已焊接的裸芯片加以封装的工艺。
几乎所有这几种封装材料都需要很长的固化时间,所以用在线式连续生产的固化炉是不实际的,平时大家经常使用“批次烘炉”,但垂直烘炉的技术也趋于完善,尤其在加热曲线比回流炉简单时,垂直烘炉完全能够胜任。
垂直烘炉使用一个垂直升降的传送系统作为“缓冲与累加器”,每一块PCB都必须通过这一道工序循环。
这样的结果就是得到了足够长的固化时间,而同时减少了占地面积。
在目前最先进的回流炉设计思想中,如何在增加产量的同时减少设备的维修量是一个关键的问题。
随着免洗焊膏与低残留焊膏的大量使用。
如何处理炉膏的助焊剂残留物这个问题也相应变得突出起来,因为这些焊膏内有大量的高沸点的溶剂来取代原来的松香,以获得理想的焊膏流变性。
目前焊膏供应商正在研究性能更加优越的焊膏,但由于质量与工艺认证是一个费工费时的过程,所以它们的应用经常相对滞后。
同时,助焊剂造成的污染也成为回流炉的一个重要课题。
从焊膏中挥发出来的物质重新凝结在机器冷却区表面形成污染物,这在充氮保护设备中表现得尤为突出,想要通过抽气口将挥发物抽走的方法在充氮炉中是不现实的。
因为抽气口会带走大量有用的氮气。
现在新型的助焊剂管理系统采用的方法是让气流在机内循环,经过一个凝结过滤装置,将助焊剂凝结在上面后除去,并将干净的气体(N2)放回炉内。
这套系统大大减少了助焊在冷却区及其它地方的残留量,并且使维修和除去污染物的工作可以在不停机的情况下进行。
从助焊剂管理系统出来的冷气流重新回到冷却区,对于焊点的冷却与降低PCB 出口温度都有额外的好处。
另一方面,回流的冷气体进入炉内的其它地方还可以表现出另外一些好处,例如:分隔不同加热区的温度,或者扩大上下加热区的温差。
但是不停机时间与费用是非常重要的,当公司的注意集中在运行费用上时,助焊剂管理系统就会显得非常重要。
回流炉如果使用周围的空气作为冷却介质,则可以采用大流量的方式冷却PCB,而且效率很高。
在充氮炉中,因为气流量受到严格控制,所以这是另一种情况。