25个必备精益生产工具
精益生产的十大工具

精益生产的十大工具精益生产的十大工具是精益生产方法中使用的工具和技术,旨在帮助企业提高生产效率、降低成本、提高质量。
精益生产是一套关于如何优化生产流程的方法论,其核心理念是通过消除浪费,实现更高效、更灵活的生产。
第一个工具是价值流图。
价值流图是将产品的生产流程可视化的工具,它可以帮助企业了解产品从原材料到最终交付的整个流程,从而找出生产中的浪费和瓶颈,并进行优化。
第二个工具是流程平衡。
流程平衡是通过平衡工作站之间的工作量,达到生产过程中的最佳效益。
通过优化工作站之间的工作分配,可以有效地降低等待时间,提高整体生产效率。
第三个工具是一体化生产系统。
一体化生产系统是通过整合产线上的各个工作站,实现生产过程的无缝衔接。
通过一体化生产系统,企业可以实现生产过程的整合和优化,提高生产效率。
第四个工具是短交付时间。
短交付时间是指将产品从订单到交付的时间尽量缩短。
通过缩短交付时间,可以提高客户满意度,同时也可以减少库存和浪费。
第五个工具是标准化工作。
标准化工作是指制定明确的工作标准和操作规范,确保每一项工作都能按照规定的要求进行。
通过标准化工作,可以提高产品质量和生产效率。
第六个工具是柔性生产。
柔性生产是指企业具备快速调整生产线的能力,以适应市场需求的变化。
通过柔性生产,企业可以更加灵活地应对市场变化,降低库存和生产成本。
第七个工具是持续改进。
持续改进是指企业不断地寻找改进的机会,并采取行动来实现持续的改变。
通过持续改进,企业可以不断提高生产效率和产品质量,保持竞争优势。
第八个工具是团队合作。
团队合作是指利用团队的力量,共同解决问题和实现目标。
通过团队合作,可以激发员工的创造力和合作精神,提高生产效率。
第九个工具是视觉管理。
视觉管理是指通过可视化的手段来传达信息和管理生产过程。
通过视觉管理,可以提高沟通效率,减少错误和浪费。
第十个工具是员工培训。
员工培训是指提供必要的培训和教育,使员工能够更好地理解和应用精益生产的方法。
精益生产工具有哪些?
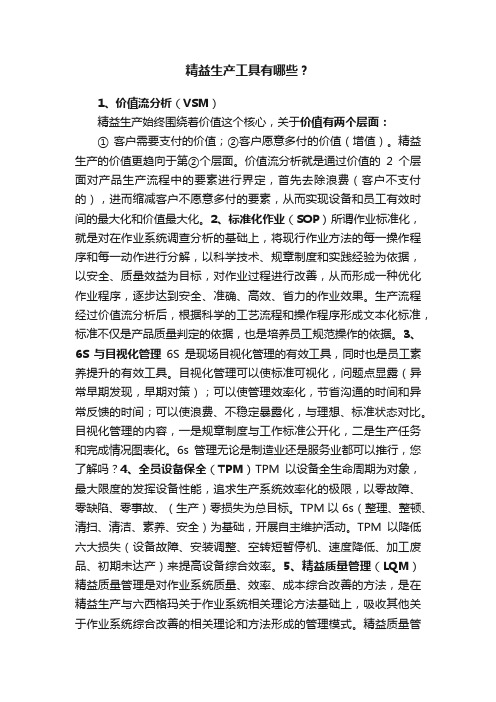
精益生产工具有哪些?1、价值流分析(VSM)精益生产始终围绕着价值这个核心,关于价值有两个层面:① 客户需要支付的价值;②客户愿意多付的价值(增值)。
精益生产的价值更趋向于第②个层面。
价值流分析就是通过价值的2个层面对产品生产流程中的要素进行界定,首先去除浪费(客户不支付的),进而缩减客户不愿意多付的要素,从而实现设备和员工有效时间的最大化和价值最大化。
2、标准化作业(SOP)所谓作业标准化,就是对在作业系统调查分析的基础上,将现行作业方法的每一操作程序和每一动作进行分解,以科学技术、规章制度和实践经验为依据,以安全、质量效益为目标,对作业过程进行改善,从而形成一种优化作业程序,逐步达到安全、准确、高效、省力的作业效果。
生产流程经过价值流分析后,根据科学的工艺流程和操作程序形成文本化标准,标准不仅是产品质量判定的依据,也是培养员工规范操作的依据。
3、6S与目视化管理6S是现场目视化管理的有效工具,同时也是员工素养提升的有效工具。
目视化管理可以使标准可视化,问题点显露(异常早期发现,早期对策);可以使管理效率化,节省沟通的时间和异常反馈的时间;可以使浪费、不稳定暴露化,与理想、标准状态对比。
目视化管理的内容,一是规章制度与工作标准公开化,二是生产任务和完成情况图表化。
6s管理无论是制造业还是服务业都可以推行,您了解吗?4、全员设备保全(TPM)TPM以设备全生命周期为对象,最大限度的发挥设备性能,追求生产系统效率化的极限,以零故障、零缺陷、零事故、(生产)零损失为总目标。
TPM以6s(整理、整顿、清扫、清洁、素养、安全)为基础,开展自主维护活动。
TPM以降低六大损失(设备故障、安装调整、空转短暂停机、速度降低、加工废品、初期未达产)来提高设备综合效率。
5、精益质量管理(LQM)精益质量管理是对作业系统质量、效率、成本综合改善的方法,是在精益生产与六西格玛关于作业系统相关理论方法基础上,吸收其他关于作业系统综合改善的相关理论和方法形成的管理模式。
精益生产管理的十大工具

精益生产管理的十大工具精益生产管理是一种通过优化生产过程,减少浪费和提高效率的方法。
在精益生产管理中,有许多工具和技术可用于帮助企业实现这些目标。
以下是精益生产管理的十大工具。
1. 价值流图:价值流图是一种可视化工具,用于展示产品或服务在整个价值流中的流动,包括所有的价值和非价值活动。
通过使用价值流图,企业可以识别出浪费和瓶颈,并制定改进计划。
2. 5S:5S是一个用于组织和维护工作场所的系统。
它包括整理、整顿、清扫、标准化和维持的步骤。
通过实施5S,企业可以改善工作环境,减少浪费和提高工作效率。
3. 高效供应链管理:高效供应链管理是通过优化供应链中的物流和信息流来降低成本和提高响应速度。
它包括减少库存、改善交付时间和优化供应链合作伙伴关系等方面。
4. 物料需求计划:物料需求计划是一种用于确定需要多少原材料和零部件的工具。
通过正确计划物料需求,企业可以避免库存积压和缺货的问题。
5. 单点作业:单点作业是一种通过减少从一台机器到另一台机器的传送时间来减少生产周期的方法。
这可以通过重新布局设备、改进工艺流程和优化工作站来实现。
6. 柔性生产:柔性生产是一种能够快速适应市场需求和变化的生产方式。
它包括灵活的工作组织、多功能的设备和高度培训的员工。
7. 持续改进:持续改进是一种通过不断寻找和消除浪费、改进工艺和提高质量来提升生产效率的方法。
它可以通过实施PDCA循环(计划、执行、检查、行动)和员工参与来实现。
8. 产能平衡:产能平衡是一种通过平衡生产线上的工作负荷来避免瓶颈和过度生产的方法。
这可以通过调整生产节奏、提高设备利用率和优化工艺来实现。
9. 供应商合作:供应商合作是一种与供应商建立长期合作关系,并与其共同努力改进质量、交付和成本的方法。
这可以通过共享信息、共同制定目标和进行持续改进活动来实现。
10. 质量管理工具:质量管理工具是一系列用于识别和解决质量问题的方法和技术。
其中包括流程图、因果图、直方图、散点图等。
精益生产培训之十大工具
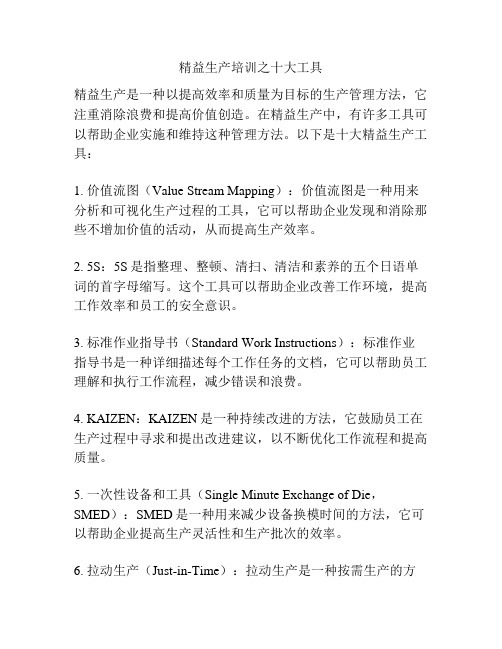
精益生产培训之十大工具精益生产是一种以提高效率和质量为目标的生产管理方法,它注重消除浪费和提高价值创造。
在精益生产中,有许多工具可以帮助企业实施和维持这种管理方法。
以下是十大精益生产工具:1. 价值流图(Value Stream Mapping):价值流图是一种用来分析和可视化生产过程的工具,它可以帮助企业发现和消除那些不增加价值的活动,从而提高生产效率。
2. 5S:5S是指整理、整顿、清扫、清洁和素养的五个日语单词的首字母缩写。
这个工具可以帮助企业改善工作环境,提高工作效率和员工的安全意识。
3. 标准作业指导书(Standard Work Instructions):标准作业指导书是一种详细描述每个工作任务的文档,它可以帮助员工理解和执行工作流程,减少错误和浪费。
4. KAIZEN:KAIZEN是一种持续改进的方法,它鼓励员工在生产过程中寻求和提出改进建议,以不断优化工作流程和提高质量。
5. 一次性设备和工具(Single Minute Exchange of Die,SMED):SMED是一种用来减少设备换模时间的方法,它可以帮助企业提高生产灵活性和生产批次的效率。
6. 拉动生产(Just-in-Time):拉动生产是一种按需生产的方法,它可以帮助企业减少库存和生产浪费,并且能够更好地满足顾客需求。
7. 故障模式与影响分析(Failure Mode and Effects Analysis,FMEA):FMEA是一种用来分析和评估潜在故障模式和其影响的方法,它可以帮助企业识别潜在风险,并采取措施进行预防和改进。
8. 委托管理(Gemba Walk):委托管理是一种通过实地走访生产现场来了解问题和挑战的方法,它可以帮助管理层与现场员工保持沟通,并及时解决问题。
9. PDCA循环:PDCA循环是指计划、实施、检查和行动的四个步骤,它是一种持续改进的管理方法,可以帮助企业不断优化工作流程和提高绩效。
精益生产常用工具
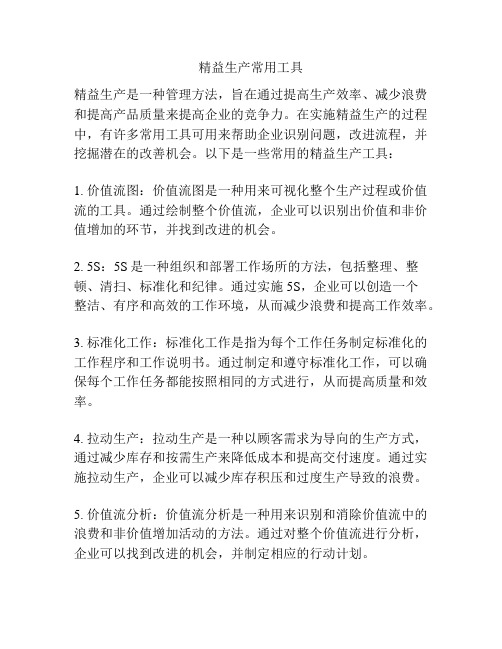
精益生产常用工具精益生产是一种管理方法,旨在通过提高生产效率、减少浪费和提高产品质量来提高企业的竞争力。
在实施精益生产的过程中,有许多常用工具可用来帮助企业识别问题,改进流程,并挖掘潜在的改善机会。
以下是一些常用的精益生产工具:1. 价值流图:价值流图是一种用来可视化整个生产过程或价值流的工具。
通过绘制整个价值流,企业可以识别出价值和非价值增加的环节,并找到改进的机会。
2. 5S:5S是一种组织和部署工作场所的方法,包括整理、整顿、清扫、标准化和纪律。
通过实施5S,企业可以创造一个整洁、有序和高效的工作环境,从而减少浪费和提高工作效率。
3. 标准化工作:标准化工作是指为每个工作任务制定标准化的工作程序和工作说明书。
通过制定和遵守标准化工作,可以确保每个工作任务都能按照相同的方式进行,从而提高质量和效率。
4. 拉动生产:拉动生产是一种以顾客需求为导向的生产方式,通过减少库存和按需生产来降低成本和提高交付速度。
通过实施拉动生产,企业可以减少库存积压和过度生产导致的浪费。
5. 价值流分析:价值流分析是一种用来识别和消除价值流中的浪费和非价值增加活动的方法。
通过对整个价值流进行分析,企业可以找到改进的机会,并制定相应的行动计划。
6. 周期时间分析:周期时间分析是一种用来测量和分析整个生产过程或价值流的时间的方法。
通过测量各个环节的时间,并分析其比例和关系,企业可以找到时间浪费和瓶颈,并采取相应的改进措施。
7. 柔性生产:柔性生产是一种以快速响应市场需求为导向的生产方式,通过灵活地调整生产线和生产能力,以适应需求的变化。
通过实施柔性生产,企业可以降低库存、提高交付速度和灵活性。
8. 产能平衡:产能平衡是指在不同工序间平衡产能,以避免过剩和瓶颈的发生,从而提高效率和质量。
通过进行产能平衡,企业可以合理安排生产能力,以满足顾客需求并避免资源浪费。
综上所述,以上提到的工具是精益生产中常用的工具,通过使用这些工具,企业可以识别问题,改进流程,并发现潜在的改善机会,从而提高生产效率和产品质量,降低成本,提高竞争力。
精益生产的十大工具

精益生产的十大工具1、准时化生产(JIT)准时生产方式是起源于日本丰田汽车公司,其基本思想是“只在需要的时候,按需要的量生产所需的产品”。
这种生产方式的核心是追求一种无库存的生产系统,或使库存达到最小的生产系统。
2、单件流JIT是精益生产的终极目标,它是通过不断消除浪费、降低库存、减少不良、缩短制造周期时间等具体要求来实现的。
单件流是帮助我们达到这一目标的关键手法之一。
3、看板管理(Kanban)看板是可以作为交流厂内生产管理信息的手段。
看板卡片包含相当多的信息并且可以反复使用。
常用的看板有两种:生产看板和运送看板。
4、零库存管理工厂的库存管理是供应链的一环,也是最基本的一环。
就制造业而言,加强库存管理,可缩短并逐步消除原材料、半成品、成品的滞留时间,减少无效作业和等待时间,防止缺货,提高客户对“质量、成本、交期”三大要素的满意度。
5、全面生产维护仃PM)以全员参与的方式,创建设计优良的设备系统,提高现有设备的利用率,实现安全性和高质量,防止故障发生,从而使企业达到降低成本和全面生产效率的提高。
6、运用价值流图来识别浪费生产过程中到处充斥着惊人的浪费现象,价值流图(ValueStreamMapping)是实施精益系统、消除过程浪费的基础与关键点。
7、生产线平衡设计由于流水线布局不合理导致生产工人无谓地移动,从而降低生产效率;由于动作安排不合理、工艺路线不合理,导致工人三番五次地拿起或放下工件。
8拉系统与补充拉系统所谓拉动生产是以看板管理为手段,采用“取料制”即后道工序根据“市场”需要进行生产,对本工序在制品短缺的量从前道工序取相同的在制品量,从而形成全过程的拉动控制系统,绝不多生产一件产品。
JIT需要以拉动生产为基础,而拉系统操作是精益生产的典型特征。
精益追求的零库存,主要通过拉系统的作业方式实现的。
9、降低设置时间(SetupReduction)为了使停线等待浪费减为最少,缩短设置时间的过程就是逐步去除和减少所有的非增值作业,并将其转变为非停线时间完成的过程。
精益生产十大工具
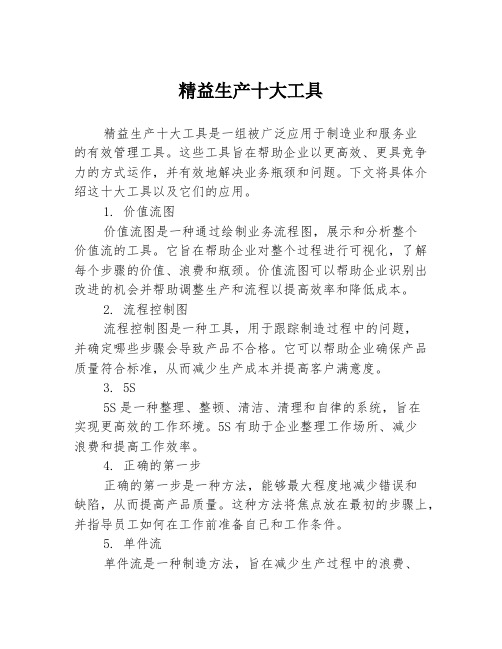
精益生产十大工具精益生产十大工具是一组被广泛应用于制造业和服务业的有效管理工具。
这些工具旨在帮助企业以更高效、更具竞争力的方式运作,并有效地解决业务瓶颈和问题。
下文将具体介绍这十大工具以及它们的应用。
1. 价值流图价值流图是一种通过绘制业务流程图,展示和分析整个价值流的工具。
它旨在帮助企业对整个过程进行可视化,了解每个步骤的价值、浪费和瓶颈。
价值流图可以帮助企业识别出改进的机会并帮助调整生产和流程以提高效率和降低成本。
2. 流程控制图流程控制图是一种工具,用于跟踪制造过程中的问题,并确定哪些步骤会导致产品不合格。
它可以帮助企业确保产品质量符合标准,从而减少生产成本并提高客户满意度。
3. 5S5S是一种整理、整顿、清洁、清理和自律的系统,旨在实现更高效的工作环境。
5S有助于企业整理工作场所、减少浪费和提高工作效率。
4. 正确的第一步正确的第一步是一种方法,能够最大程度地减少错误和缺陷,从而提高产品质量。
这种方法将焦点放在最初的步骤上,并指导员工如何在工作前准备自己和工作条件。
5. 单件流单件流是一种制造方法,旨在减少生产过程中的浪费、减少库存和减少制造时间。
它可以帮助企业以更高效的方式生产各种产品,并根据客户的需求提供服务。
6. 智能制造智能制造是一种制造技术,旨在将传统的制造过程与先进的计算机技术结合起来,以实现更高效、更可靠且更精确的生产。
智能制造的目标是提高质量、降低成本并增强企业的竞争力。
7. 按需制造按需制造是一种生产模式,在该模式下,生产和服务是根据客户需求实时产生的。
按需制造可以大大减少库存,避免过剩的库存和减少过时产品,从而提高效率和降低成本。
8. JidokaJidoka是一种制造方法,旨在通过自动化控制制造过程和机器上的检测,实现实时可视化生产过程。
Jidoka可帮助企业有效地识别和纠正制造过程中的错误,并最大限度地减少损失和产品缺陷。
9. KaizenKaizen是一种改进方法,旨在不断优化生产过程。
精益生产13个主要工具
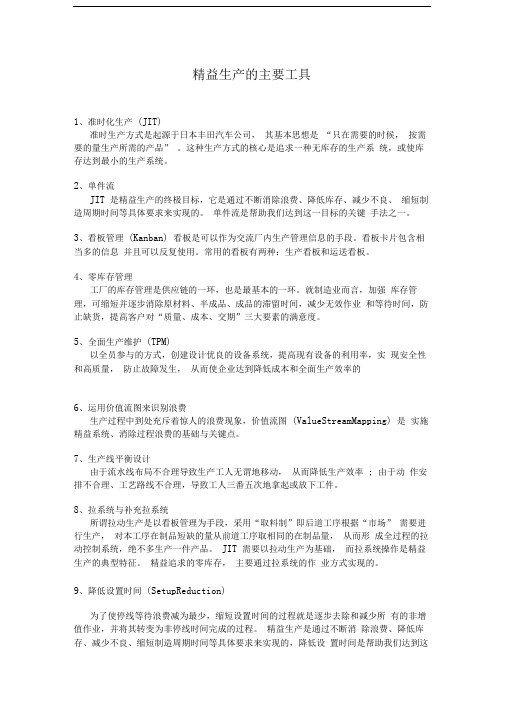
精益生产的主要工具1、准时化生产(JIT)准时生产方式是起源于日本丰田汽车公司,其基本思想是“只在需要的时候,按需要的量生产所需的产品” 。
这种生产方式的核心是追求一种无库存的生产系统,或使库存达到最小的生产系统。
2、单件流JIT 是精益生产的终极目标,它是通过不断消除浪费、降低库存、减少不良、缩短制造周期时间等具体要求来实现的。
单件流是帮助我们达到这一目标的关键手法之一。
3、看板管理(Kanban) 看板是可以作为交流厂内生产管理信息的手段。
看板卡片包含相当多的信息并且可以反复使用。
常用的看板有两种:生产看板和运送看板。
4、零库存管理工厂的库存管理是供应链的一环,也是最基本的一环。
就制造业而言,加强库存管理,可缩短并逐步消除原材料、半成品、成品的滞留时间,减少无效作业和等待时间,防止缺货,提高客户对“质量、成本、交期”三大要素的满意度。
5、全面生产维护(TPM)以全员参与的方式,创建设计优良的设备系统,提高现有设备的利用率,实现安全性和高质量,防止故障发生,从而使企业达到降低成本和全面生产效率的6、运用价值流图来识别浪费生产过程中到处充斥着惊人的浪费现象,价值流图(ValueStreamMapping) 是实施精益系统、消除过程浪费的基础与关键点。
7、生产线平衡设计由于流水线布局不合理导致生产工人无谓地移动,从而降低生产效率; 由于动作安排不合理、工艺路线不合理,导致工人三番五次地拿起或放下工件。
8、拉系统与补充拉系统所谓拉动生产是以看板管理为手段,采用“取料制”即后道工序根据“市场” 需要进行生产,对本工序在制品短缺的量从前道工序取相同的在制品量,从而形成全过程的拉动控制系统,绝不多生产一件产品。
JIT 需要以拉动生产为基础,而拉系统操作是精益生产的典型特征。
精益追求的零库存,主要通过拉系统的作业方式实现的。
9、降低设置时间(SetupReduction)为了使停线等待浪费减为最少,缩短设置时间的过程就是逐步去除和减少所有的非增值作业,并将其转变为非停线时间完成的过程。
精益生产的十大工具
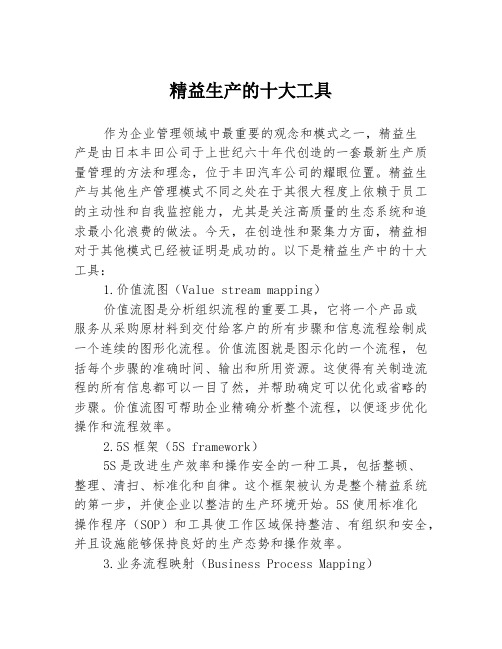
精益生产的十大工具作为企业管理领域中最重要的观念和模式之一,精益生产是由日本丰田公司于上世纪六十年代创造的一套最新生产质量管理的方法和理念,位于丰田汽车公司的耀眼位置。
精益生产与其他生产管理模式不同之处在于其很大程度上依赖于员工的主动性和自我监控能力,尤其是关注高质量的生态系统和追求最小化浪费的做法。
今天,在创造性和聚集力方面,精益相对于其他模式已经被证明是成功的。
以下是精益生产中的十大工具:1.价值流图(Value stream mapping)价值流图是分析组织流程的重要工具,它将一个产品或服务从采购原材料到交付给客户的所有步骤和信息流程绘制成一个连续的图形化流程。
价值流图就是图示化的一个流程,包括每个步骤的准确时间、输出和所用资源。
这使得有关制造流程的所有信息都可以一目了然,并帮助确定可以优化或省略的步骤。
价值流图可帮助企业精确分析整个流程,以便逐步优化操作和流程效率。
2.5S框架(5S framework)5S是改进生产效率和操作安全的一种工具,包括整顿、整理、清扫、标准化和自律。
这个框架被认为是整个精益系统的第一步,并使企业以整洁的生产环境开始。
5S使用标准化操作程序(SOP)和工具使工作区域保持整洁、有组织和安全,并且设施能够保持良好的生产态势和操作效率。
3.业务流程映射(Business Process Mapping)业务流程映射也被称为过程绘图,是企业中获得一些方案和改善的关键步骤。
此工具小组可以使用符号和图形描述企业中任何类型的业务流程和相关信息。
这可以揭示在过程中发生的问题、浪费、冗余和延迟,因此有助于消除不必要的步骤、改善流程的质量和效率。
4.一次流程变更(Single Piece Flow)这是一种最小化生产时间的原则,可以通过同一物品的生产技术一步步生产出多个物品。
使用一次流程变更工具,可以有效地降低制造成本,并使产品变得更加高效和可追溯,提高产品的核心竞争力。
5.生产平衡(Production Levelling)生产平衡是实现精益生产中的关键工具,可以帮助企业产生一个稳定的、平均的生产率水平。
精益生产管理十大工具

精益生产管理十大工具
1. 展开-收缩图:用于分析流程中的重复性工作和非必要步骤,并将不必要的步骤剔除。
2. 生产可视化:通过对生产情况进行实时可视化,能够更好地理解生产过程中存在的问题,以及如何纠正问题。
3. 价值流图:用于识别和分析流程中的不必要步骤,以便于合理安排人力、物力和资源。
4. 精益5S管理:通过建立整洁、易于清洁、安全和方便操作的工作环境,有效提高生产效率。
5. 六大白帽子:指的是6个基本的精益思想:标准化、流程改进、定期检查、及时应对、数据分析和精益文化。
6. 生产线平衡:用于识别和分析生产线上的瓶颈,保证生产过程中每一道工序都能够得到有效的利用。
7. 改善小组:建立一组小组来改善当前的生产过程,以提高效率,降低成本。
8. 标准化:建立标准的流程,以确保每一道工序都能够稳定、高效地完成。
9. 重复性分析:分析企业的生产过程中存在的重复性工作,以便确定可以剔除的不必要步骤。
10. 精益工厂:将精益管理思想贯彻到整个企业,改善整体的生产流程,以达到高效运营的目的。
精益生产13个主要工具

精益生产的主要工具1、准时化生产(JIT)准时生产方式是起源于日本丰田汽车公司,其基本思想是“只在需要的时候,按需要的量生产所需的产品”。
这种生产方式的核心是追求一种无库存的生产系统,或使库存达到最小的生产系统。
2、单件流JIT是精益生产的终极目标,它是通过不断消除浪费、降低库存、减少不良、缩短制造周期时间等具体要求来实现的。
单件流是帮助我们达到这一目标的关键手法之一。
3、看板管理(Kanban)看板是可以作为交流厂内生产管理信息的手段。
看板卡片包含相当多的信息并且可以反复使用。
常用的看板有两种:生产看板和运送看板。
4、零库存管理工厂的库存管理是供应链的一环,也是最基本的一环。
就制造业而言,加强库存管理,可缩短并逐步消除原材料、半成品、成品的滞留时间,减少无效作业和等待时间,防止缺货,提高客户对“质量、成本、交期”三大要素的满意度。
5、全面生产维护(TPM)以全员参与的方式,创建设计优良的设备系统,提高现有设备的利用率,实现安全性和高质量,防止故障发生,从而使企业达到降低成本和全面生产效率的提高。
6、运用价值流图来识别浪费生产过程中到处充斥着惊人的浪费现象,价值流图(ValueStreamMapping)是实施精益系统、消除过程浪费的基础与关键点。
7、生产线平衡设计由于流水线布局不合理导致生产工人无谓地移动,从而降低生产效率;由于动作安排不合理、工艺路线不合理,导致工人三番五次地拿起或放下工件。
8、拉系统与补充拉系统所谓拉动生产是以看板管理为手段,采用“取料制”即后道工序根据“市场”需要进行生产,对本工序在制品短缺的量从前道工序取相同的在制品量,从而形成全过程的拉动控制系统,绝不多生产一件产品。
JIT需要以拉动生产为基础,而拉系统操作是精益生产的典型特征。
精益追求的零库存,主要通过拉系统的作业方式实现的。
9、降低设置时间(SetupReduction)为了使停线等待浪费减为最少,缩短设置时间的过程就是逐步去除和减少所有的非增值作业,并将其转变为非停线时间完成的过程。
精益生产管理十大工具

精益生产管理十大工具在现代制造业中,精益生产管理是一种重要的管理思想,旨在提高生产效率、降低成本、提高产品质量。
为了实现这一目标,精益生产管理应用了各种工具和技术。
以下是精益生产管理中最常用的十大工具:价值流映射价值流映射是一种识别和消除生产过程中浪费的工具。
通过绘制价值流图,生产管理者可以清晰地看到价值创造的流程,并找出其中的浪费,进而采取措施进行改善。
小批量生产采用小批量生产可以减少库存、降低生产成本,并提高生产效率。
通过减少生产周期,企业可以更加灵活地响应市场需求。
标准化工作制定和遵守标准化工作流程可以确保生产过程稳定、高效。
员工们在遵循标准操作流程的情况下工作,有助于减少产生的错误和浪费。
5S整理法5S整理法是一种工厂管理方法,通过整顿、清扫、清洁、清理、素养的五个步骤,使工作环境整洁有序,提高工作效率。
建议箱建议箱是鼓励员工提出改进建议的工具。
通过员工的参与,可以发现生产过程中存在的问题和改进的机会,从而不断优化生产流程。
好的团队沟通有效的团队沟通是实现精益生产管理的重要前提。
通过团队沟通,可以加强团队协作,促进信息共享,提高生产效率。
周生产会议定期召开周生产会议可以及时跟踪生产进度,识别问题并制定解决方案。
通过会议记录和持续改进,可以提高生产计划的准确性。
一体化生产计划一体化生产计划是整合市场需求、生产能力、物流等因素的生产计划模式。
通过一体化计划,企业可以优化资源配置,提高生产效率。
质量控制质量控制是确保产品质量符合标准的一系列措施。
通过质量控制,可以降低次品率,提高产品质量,增强企业竞争力。
持续改进持续改进是精益生产管理的核心理念。
通过不断地发现问题、分析原因、提出改进建议并实施改进措施,企业可以不断提高生产效率和产品质量。
以上就是精益生产管理中最常用的十大工具。
通过合理应用这些工具,企业可以不断优化生产流程,提高生产效率,降低成本,实现持续增长。
精益生产十大工具

精益生产十大工具精益生产是一种旨在提高生产效率和减少浪费的管理方法。
它包含了许多工具和技术,旨在帮助组织更好地管理资源、提高产能和优化流程。
在这篇文章中,我将介绍精益生产的十大工具,以帮助读者更好地了解和应用这些工具。
1.5S法则:5S法则是一种用于组织工作环境和提高效率的方法。
它包括整理、整顿、清扫、标准化和自律五个步骤。
通过实施5S法则,组织可以改善工作环境,减少浪费和失误,并提高生产效率。
2.价值流图:价值流图是一种用于分析和改善生产流程的工具。
它可以帮助组织识别价值和非价值活动,并定位瓶颈和浪费。
通过分析价值流图,组织可以找到改进的机会,并优化流程以提高产出和客户满意度。
3.流程映射:流程映射是一种用于图形化表示和分析流程的工具。
它可以帮助组织识别和理解整个流程的各个步骤和关键决策点。
通过流程映射,组织可以更好地了解流程,并找出改进的机会。
4.持续改善:持续改善是精益生产的核心原则之一。
它强调从小改进开始,通过反复模拟和实验,逐步提高流程和产品的质量。
持续改进要求组织保持开放和灵活,不断追求更高的效率和产品质量。
5.单点故障:单点故障是指在生产过程中存在可能导致整个流程中断或崩溃的单一关键节点。
通过识别和消除单点故障,组织可以提高生产线的稳定性和可靠性,并降低因故障引起的停产和成本。
6.稳定性:稳定性是指生产流程的可靠性和一致性。
通过确保设备和工艺的稳定性,组织可以减少因工艺变异而导致的浪费和不良品,提高生产效率和质量。
7.柔性制造:柔性制造是指组织能够快速适应市场需求变化,并在不降低质量和效率的情况下生产不同类型的产品。
通过实施柔性制造,组织可以更好地利用资源、减少库存和满足客户需求。
8.精细化:精细化是指组织对生产过程中每一个环节和细节进行深入分析和控制。
通过精细化,组织可以更好地了解产品和生产线的性能,并找到改进的机会,以提高生产效率和质量。
9.标准化:标准化是指通过制定和执行标准,确保生产过程和产品的一致性和质量。
Top 25 Lean Tools- 精益生产25个工具

Top 25 Lean ToolsThe Big Idea – Lean has a very extensive collection of tools and concepts. Surveying the most important of these, understanding both what they are and how they can help is an excellent way to get started. Exploring LeanThere are a lot of great ideas to explore in lean. So where should you begin?One way to start is to survey the most important lean tools, with a brief description and short explanation of how each tool can improve your manufacturing operations.If a tool captures your interest or resonates with you in some way – explore it further to decide if it is something to pursue now…or later. Many of these tools can be successfully used in isolation, which makes it much easier to get started. On the other hand, the benefits will compound as more tools are used, as they do support and reinforce each other.Quick Links> 5S > Andon > Bottleneck Analysis > Continuous Flow > Gemba (The Real Place)> Heijunka (Level Scheduling) > Hoshin Kanri (Policy Deployment) > Jidoka (Autonomation)> Just-In-Time (JIT) > Kaizen (Continuous Improvement) > Kanban (Pull System)> KPIs (Key Performance Indicators) > Muda (Waste) > Overall Equipment Effectiveness (OEE)> PDCA (Plan, Do, Check, Act) > Poka-Yoke (Error Proofing) > Root Cause Analysis> Single-Minute Exchange of Dies (SMED) > Six Big Losses > SMART Goals> Standardized Work > Takt Time > Total Productive Maintenance (TPM)> Value Stream Mapping > Visual Factory25 Essential Lean Tools5SWhat is 5S?Organize the work area:❖Sort (eliminate that which is not needed)❖Set In Order (organize remaining items)❖Shine (clean and inspect work area)❖Standardize (write standards for above)❖Sustain (regularly apply the standards)How does 5S help?Eliminates waste that results from a poorly organized work area (e.g. wasting time looking for a tool).AndonWhat is Andon?Visual feedback system for the plant floor that indicates production status, alerts when assistance is needed, and empowers operators to stop the production process.How does Andon help?Acts as a real-time communication tool for the plant floor that brings immediate attention to problems as they occur – so they can be instantly addressed.Bottleneck AnalysisWhat is Bottleneck Analysis?Identify which part of the manufacturing process limits the overall throughput and improve the performance of that part of the process.How does Bottleneck Analysis help?Improves throughput by strengthening the weakest link in the manufacturing process. Continuous FlowWhat is Continuous Flow?Manufacturing where work-in-process smoothly flows through production with minimal (or no) buffers between steps of the manufacturing process.How does Continuous Flow help?Eliminates many forms of waste (e.g. inventory, waiting time, and transport).Gemba (The Real Place)What is Gemba?A philosophy that reminds us to get out of our offices and spend time on the plant floor – the place where real action occurs.How does Gemba help?Promotes a deep and thorough understanding of real-world manufacturing issues – by first-hand observation and by talking with plant floor employees.Heijunka (Level Scheduling)What is Heijunka?A form of production scheduling that purposely manufactures in much smaller batches by sequencing (mixing) product variants within the same process.How does Heijunka help?Reduces lead times (since each product or variant is manufactured more frequently) and inventory (since batches are smaller).Hoshin Kanri (Policy Deployment)What is Hoshin Kanri?Align the goals of the company (Strategy), with the plans of middle management (Tactics) and the work performed on the plant floor (Action).How does Hoshin Kanri help?Ensures that progress towards strategic goals is consistent and thorough – eliminating the waste that comes from poor communication and inconsistent direction.Jidoka (Autonomation)What is Jidoka?Design equipment to partially automate the manufacturing process (partial automation is typically much less expensive than full automation) and to automatically stop when defects are detected.How does Jidoka help?After Jidoka, workers can frequently monitor multiple stations (reducing labor costs) and many quality issues can be detected immediately (improving quality).Just-In-Time (JIT)What is Just-In-Time?Pull parts through production based on customer demand instead of pushing parts through production based on projected demand. Relies on many lean tools, such as Continuous Flow, Heijunka, Kanban, Standardized Work and Takt Time.How does Just-In-Time help?Highly effective in reducing inventory levels. Improves cash flow and reduces space requirements.Kaizen (Continuous Improvement)What is Kaizen?A strategy where employees work together proactively to achieve regular, incremental improvements in the manufacturing process.How does Kaizen help?Combines the collective talents of a company to create an engine for continually eliminating waste from manufacturing processes.Kanban (Pull System)What is Kanban?A method of regulating the flow of goods both within the factory and with outside suppliers and customers. Based on automatic replenishment through signal cards that indicate when more goods are needed.How does Kanban help?Eliminates waste from inventory and overproduction. Can eliminate the need for physical inventories (instead relying on signal cards to indicate when more goods need to be ordered). KPIs (Key Performance Indicators)What are KPIs?Metrics designed to track and encourage progress towards critical goals of the organization. Strongly promoted KPIs can be extremely powerful drivers of behavior – so it is important to carefully select KPIs that will drive desired behavior.How do KPIs help?The best manufacturing KPIs:❖Are aligned with top-level strategic goals (thus helping to achieve those goals)❖Are effective at exposing and quantifying waste (OEE is a good example)❖Are readily influenced by plant floor employees (so they can drive results)Muda (Waste)What is Muda?Anything in the manufacturing process that does not add value from the customer’s perspective. How does Muda help?It doesn’t. Muda means ‘waste’. The elimination of muda (waste) is the primary focus of lean manufacturing.Overall Equipment Effectiveness (OEE)What is Overall Equipment Effectiveness?Framework for measuring productivity loss for a given manufacturing process. Three categories of loss are tracked:❖Availability (e.g. down time)❖Performance (e.g. slow cycles)❖Quality (e.g. rejects)How does Overall Equipment Effectiveness help?Provides a benchmark/baseline and a means to track progress in eliminating waste from a manufacturing process. 100% OEE means perfect production (manufacturing only good parts, as fast as possible, with no down time).PDCA (Plan, Do, Check, Act)What is PDCA?An iterative methodology for implementing improvements:❖Plan (establish plan and expected results)❖Do (implement plan)❖Check (verify expected results achieved)❖Act (review and assess; do it again)How does PDCA help?Applies a scientific approach to making improvements:❖Plan (develop a hypothesis)❖Do (run experiment)❖Check (evaluate results)❖Act (refine your experiment; try again)Poka-Yoke (Error Proofing)What is Poka-Yoke?Design error detection and prevention into production processes with the goal of achieving zero defects.How does Poka-Yoke help?It is difficult (and expensive) to find all defects through inspection, and correcting defects typically gets significantly more expensive at each stage of production.Root Cause AnalysisWhat is Root Cause Analysis?A problem solving methodology that focuses on resolving the underlying problem instead of applying quick fixes that only treat immediate symptoms of the problem. A common approach is to ask why five times –each time moving a step closer to discovering the true underlying problem.How does Root Cause Analysis help?Helps to ensure that a problem is truly eliminated by applying corrective action to the “root cause” of the problem.Single-Minute Exchange of Dies (SMED)What is Single-Minute Exchange of Dies?Reduce setup (changeover) time to less than 10 minutes. Techniques include:❖Convert setup steps to be external (performed while the process is running)❖Simplify internal setup (e.g. replace bolts with knobs and levers)❖Eliminate non-essential operations❖Create Standardized Work instructionsHow does Single-Minute Exchange of Dies help?Enables manufacturing in smaller lots, reduces inventory, and improves customer responsiveness. Six Big LossesWhat is Six Big Losses?Six categories of productivity loss that are almost universally experienced in manufacturing: ❖Breakdowns❖Setup/Adjustments❖Small Stops❖Reduced Speed❖Startup Rejects❖Production RejectsHow does Six Big Losses help?Provides a framework for attacking the most common causes of waste in manufacturing. SMART GoalsWhat are SMART Goals?Goals that are: Specific, Measurable, Attainable, Relevant, and Time-Specific.How do SMART Goals help?Helps to ensure that goals are effective.Standardized WorkWhat is Standardized Work?Documented procedures for manufacturing that capture best practices (including the time to complete each task). Must be “living” documentation that is easy to change.How does Standardized Work help?Eliminates waste by consistently applying best practices. Forms a baseline for future improvement activities.Takt TimeWhat is Takt Time?The pace of production (e.g. manufacturing one piece every 34 seconds) that aligns production with customer demand. Calculated as Planned Production Time / Customer Demand.How does Takt Time help?Provides a simple, consistent and intuitive method of pacing production. Is easily extended to provide an efficiency goal for the plant floor (Actual Pieces / Target Pieces).Total Productive Maintenance (TPM)What is Total Productive Maintenance?A holistic approach to maintenance that focuses on proactive and preventative maintenance to maximize the operational time of equipment. TPM blurs the distinction between maintenance and production by placing a strong emphasis on empowering operators to help maintain their equipment.How does Total Productive Maintenance help?Creates a shared responsibility for equipment that encourages greater involvement by plant floor workers. In the right environment this can be very effective in improving productivity (increasing up time, reducing cycle times, and eliminating defects).Value Stream MappingWhat is Value Stream Mapping?A tool used to visually map the flow of production. Shows the current and future state of processes in a way that highlights opportunities for improvement.How does Value Stream Mapping help?Exposes waste in the current processes and provides a roadmap for improvement through the future state.Visual FactoryWhat is Visual Factory?Visual indicators, displays and controls used throughout manufacturing plants to improve communication of information.How does Visual Factory help?Makes the state and condition of manufacturing processes easily accessible and very clear – to everyone.。
精益生产工具

精益生产工具精益生产是一种管理和生产方法,旨在通过最大化价值、降低浪费和提高效率来改进生产过程。
在精益生产中,有许多工具和技术可以帮助企业实现这些目标。
在本文中,我们将介绍一些常用的精益生产工具,并解释它们如何在实践中应用。
1. 价值流图价值流图是一种流程图,用于表示产品或服务的价值流动路径。
它标识了价值创造和浪费的点,并帮助识别改进的机会。
通过绘制和分析价值流图,企业可以更好地了解生产过程中的瓶颈、延误和浪费,并采取相应的改善措施。
2. 5S5S 是一种组织和管理方法,旨在创造整洁、有序和高效的工作环境。
它包括以下五个步骤:整理(Sort)、整顿(Set in order)、清洁(Shine)、标准化(Standardize)和维护(Sustain)。
通过实施5S,企业可以提高生产环境的可视性、安全性和效率。
3. 单片流单片流是一种生产方法,通过一次只生产一个产品,以最大程度地减少库存和等待时间。
单片流可以避免生产过剩,并提高产品交付的速度和质量。
它需要高度的协调和协作,但可以显著提高生产效率。
4. 精益生产零库存精益生产零库存是一种管理方法,旨在通过减少库存来降低成本和浪费。
它要求企业根据实际需求进行生产,并且只在必要时才从供应链中获取所需的原材料和零部件。
这种方法可以减少库存积压、降低仓储成本,并提高生产效率。
5. 业绩看板业绩看板是一种用于跟踪和可视化生产绩效的工具。
通过在工作区展示指标和数据,业绩看板可以帮助员工了解工作进展、问题和改进机会。
它还可以促进团队沟通和合作,激励员工参与精益生产活动。
6. 持续改进持续改进是精益生产的核心原则之一。
它鼓励企业不断寻求改进的机会,并通过小步骤和小改变来逐渐实现进步。
持续改进可以通过定期的团队会议、员工建议和问题解决活动来实施,以保持精益生产的持久性和稳定性。
总结:精益生产工具是实现精益生产方法的关键要素。
它们可以帮助企业发现并消除生产过程中的浪费和瓶颈,提高效率和质量。
精益生产13个主要工具

精益生产的主要工具1、准时化生产(JIT)准时生产方式是起源于日本丰田汽车公司,其基本思想是“只在需要的时候,按需要的量生产所需的产品”。
这种生产方式的核心是追求一种无库存的生产系统,或使库存达到最小的生产系统。
2、单件流JIT是精益生产的终极目标,它是通过不断消除浪费、降低库存、减少不良、缩短制造周期时间等具体要求来实现的。
单件流是帮助我们达到这一目标的关键手法之一。
3、看板管理(Kanban)看板是可以作为交流厂内生产管理信息的手段。
看板卡片包含相当多的信息并且可以反复使用。
常用的看板有两种:生产看板和运送看板。
4、零库存管理工厂的库存管理是供应链的一环,也是最基本的一环。
就制造业而言,加强库存管理,可缩短并逐步消除原材料、半成品、成品的滞留时间,减少无效作业和等待时间,防止缺货,提高客户对“质量、成本、交期”三大要素的满意度。
5、全面生产维护(TPM)以全员参与的方式,创建设计优良的设备系统,提高现有设备的利用率,实现安全性和高质量,防止故障发生,从而使企业达到降低成本和全面生产效率的提高。
6、运用价值流图来识别浪费生产过程中到处充斥着惊人的浪费现象,价值流图(ValueStreamMapping)是实施精益系统、消除过程浪费的基础与关键点。
7、生产线平衡设计由于流水线布局不合理导致生产工人无谓地移动,从而降低生产效率;由于动作安排不合理、工艺路线不合理,导致工人三番五次地拿起或放下工件。
8、拉系统与补充拉系统所谓拉动生产是以看板管理为手段,采用“取料制”即后道工序根据“市场”需要进行生产,对本工序在制品短缺的量从前道工序取相同的在制品量,从而形成全过程的拉动控制系统,绝不多生产一件产品。
JIT需要以拉动生产为基础,而拉系统操作是精益生产的典型特征。
精益追求的零库存,主要通过拉系统的作业方式实现的。
9、降低设置时间(SetupReduction)为了使停线等待浪费减为最少,缩短设置时间的过程就是逐步去除和减少所有的非增值作业,并将其转变为非停线时间完成的过程。