金属切削原理与刀具复习共60页
金属切削原理与刀具综合复习题

金属切削原理与刀具综合复习题一、填空题(每空1分,共分)1、切削运动是指在切削过程中刀具相对于工件的运动,可分为和。
2、车刀的切削部分组成包括:、、、、和。
3、确定刀具几何角度的参考坐标系有两大类:一类称为和另一类称为。
4、在刀具材料中,工具钢包括:、和。
5、金属切削过程的实质是金属在刀具的作用下产生_______、________和________的变形过程。
6、用作刀具的瓷材料,根据其化学成分可分为:和。
7、切屑的种类有多种多样,归纳起来有以下四类:、、和。
8、影响切削力的主要因素包括:、、和等。
9、刀具磨损的主要原因有:、、和。
10、切削液的作用包括四方面: 、、、。
11、按车刀结构的不同,可分为整体式、和车刀。
12、车刀由用于切削的________________和用于装夹的________________两部分组成。
13、刀具材料种类繁多当前使用的刀具材料分5类:_______________,________________,________________,________________和_____________。
一般机加工使用最多的是________________和________________。
14、根据一面两角法,________________和________________两角可以确定前刀面的方位,________________和________________两角可以确定后刀面的方位,________________和________________两角可以确定主切削刃的方位。
15、刀尖的修磨形式有________________、________________和________________。
16、刀具磨损有正常磨损和非正常磨损两类。
其中正常磨损形式包括________________、________________、______________和________________四种形式。
金属切削原理与刀具复习
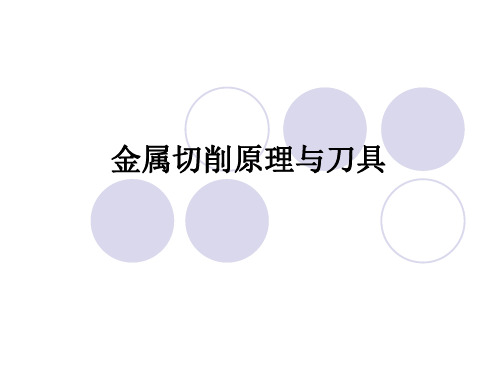
几何角度来表示,这样就必须将刀具置 于空间坐标平面参考系内。该参考系包 切削平面 Ps:切 削刃和切削速度方 括参考坐标平面和测量坐标平面(给出 向确定的面。 定义)。
基面 Pr和切削平面 Ps合称参考坐标平面
1.2.2刀具角度的坐标平面与参考系之重点 概念
1、参考平面:与刀具的安装基准、切削运动有关,包括基面和切削平面 (注意) 基面:选定点的基面,过改点且与速度垂直的平面。 切削平面:选定点的切削平面,是过改点且与过渡表面相切的平面 2、测量平面:主要考虑制造和测量的方便,选取的平面。 (如何推广定义?)
五、本课程要求
1.掌握基本知识; 2.掌握基本理论; 3.掌握基本技能;
六、学习的方法
《金属切削原理与刀具》是研究金属切削加工与生产的理论和应用的技术基础课程, 应用非常广泛。作为技术基础课程,具有基础性,应用性和先进性。 1、以课堂教学为主,辅以一定量的现场教学; 2、必要的实验项目是学习的关键; 3、以课外自学为辅,每星期有一个学时的辅导答疑。
2.工件表面
切削过程中,工件上有三个不断变化的表面。 待加工表面:工件上即将被切除的表面。 过渡表面:正被切削的表面。下一切削行程将被切除。 己加工表面: 切削后形成的新表面。
车削运动和加工表面 1-待加工表面 2-过渡表面 3-已加工表面
4)背吃刀量ap (切削深度)
工件上已加工表面与待加工表面间的垂直距离。单位:mm 。 在与主运动和进给运动方向所组成的平面的法线方向上度量。
第一章 基本定义
本章内容: 1、切削过程: 工件切削表面、切削用量 2、刀具:坐标、参考系、基本角度 事例
第一章 基本定义
1.1切削运动、工件表面与切削用量
补充:1、切削加工必备三个条件: (1)刀具和工件间要有形成零件结构要素所需的相对运动。这类相对运动由各 种切削机床的传动系统提供。 (2)刀具材料的性能能够满足切削加工的需要。刀具在切除工件上多余材料时, 工作部分将受到切削力、切削热、切削摩擦等的共同作用,目切削负荷很 重,工作条件恶劣,因此,刀具材料必须具有适应强迫切除多余材料这一 特定过程的性能,例如足够的强度和刚度、高温下的耐磨性等。 (3)刀具必须具有一定的空间儿何结构。零件多余材料被刀具从工件上切除的 本质,仍然是材料受力变形直至断裂破坏,只是完成这个过程的时间很短, 材料变形破坏的速度很快。为了完成这一过程时能够确保加工质量、尽量 减少动力消耗和延长刀具寿命,刀具切削部分的几何结构和表面状态必须 能适应切削过程的综合要求。
金属切削原理与刀具期末复习重点

第一章切削加工:利用刀具切除被加工零件多于材料的方法1. 切削用量:切削加工过程中切削速度,进给量和背吃刀量的总称 Vc=πdn/1000 d 为直径 n 为转速(1)切削速度Vc 指切削刃选定点相对工件主运动的瞬时速度 V f =nf V f 为进给速度(2)进给量f 为刀具在进给方向上相对工件的位移量 a p =(d w -d m )/2 d w 为待加工表面直径 d m 为已加工表面直径(3)背吃刀量a p 指垂直进给速度方向测量的切削层最大尺寸(4)切削时间T m 指切削时直接改变工件尺寸、形状等工艺过程所需的时间pL 为刀具行程长度 A 半径方向加工 2. 合成切削运动:主运动和进给运动合成的运动 余量合成切削速度:切削刃选定点相对工件合成切削运动的瞬时速度Ve=V c +V f3. 刀具的组成:三面两刃一尖(1)前面:切屑流过的表面(2)后面:与过渡表面相对的表面(3)副后面:与已加工表面相对的表面(4)主切削刃:前、后刀面汇交的边缘(5)副切削刃:除主切削刃以外的切削刃(6)刀尖:主、副切削刃汇交的一小段切削刃4. 刀具角度参考系(1)基面:过切削刃选定点平行或垂直刀具安装面的平面(2)主切削平面:过切削刃选定点与切削刃相切并垂直与基面的平面(3)正交平面:过切削刃选定点同时垂直于切削平面和基面的平面(4)假定进给平面:过切削刃选定点平行于假定进给方向并垂直与基面的平面5.刀具角度(1)前角:正交平面中测量前面与基面间的夹角(2)后角:正交平面中测量后面与切削平面间的夹角(3)副后角:正交平面中测量副后刀面与切削平面间的夹角(4)主偏角:基面中测量主切削平面与假定工作平面间夹角(5)副偏角:基面中测量副切削平面与假定工作平面间夹角(6)刃倾角:切削平面中测量切削刃与基面间夹角6.刀具工作角度的影响(1)刀柄逆(顺)时针转动,主偏角增大(减小),副偏角减小(增大)(2)切削刃选定点高(低)于工件中心,前角增大(减小),后角减小(增大)(3)进给运动方向不平行与工件旋转轴线,主偏角减小,副偏角增大(4)纵向进给,前角增大,后角减小7.切削层:切削部分切过工件的一个单程所切除的工件材料层(1)切削层横截面积(2)切削厚度(3)切削宽度,主偏角减小,切削厚度减小,切削宽度增大切削方式(1)自由切削:只有一个主切削刃参与切削,非自由切削:主、副切削刃同时参与切削(2)正交切削:切削刃与切削速度方向垂直,非正交切削:切削刃不垂直切削速度方向第二章1、刀具材料性能:高硬度、高耐磨性、足够的强度与韧性、高耐热性、较好的工艺性与经济性2、刀具材料类型:工具钢(碳素工具钢、合金工具钢、高速钢),硬质合金,陶瓷(金属陶瓷、非金属陶瓷),超硬材料(立方氮化硼、金刚石),最常用的是高速钢与硬质合金3、高速钢、硬质合金、陶瓷、金刚石、立方氮化硼各有何性能特点,适用于何处?高速钢的特点:耐热温度低,切削速度低;强度高,工艺性最好。
《金属切削原理与刀具》知识点总结
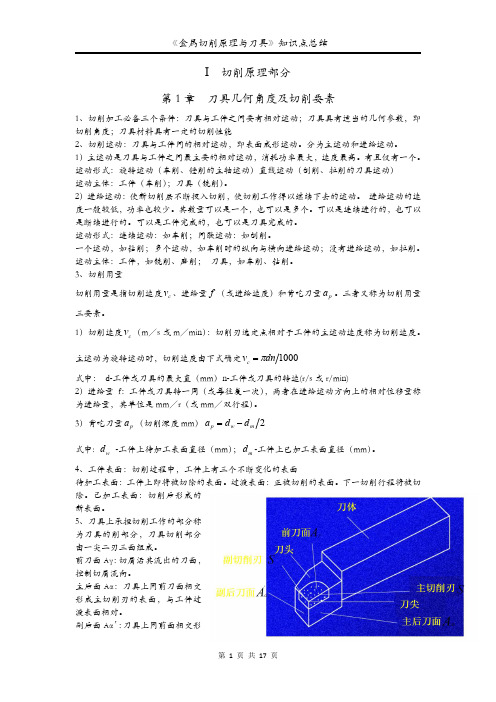
I 切削原理部分第1章刀具几何角度及切削要素1、切削加工必备三个条件:刀具与工件之间要有相对运动;刀具具有适当的几何参数,即切削角度;刀具材料具有一定的切削性能2、切削运动:刀具与工件间的相对运动,即表面成形运动。
分为主运动和进给运动。
1)主运动是刀具与工件之间最主要的相对运动,消耗功率最大,速度最高。
有且仅有一个。
运动形式:旋转运动(车削、镗削的主轴运动)直线运动(刨削、拉削的刀具运动)运动主体:工件(车削);刀具(铣削)。
2)进给运动:使新切削层不断投入切削,使切削工作得以继续下去的运动。
进给运动的速度一般较低,功率也较少。
其数量可以是一个,也可以是多个。
可以是连续进行的,也可以是断续进行的。
可以是工件完成的,也可以是刀具完成的。
运动形式:连续运动:如车削;间歇运动:如刨削。
一个运动,如钻削;多个运动,如车削时的纵向与横向进给运动;没有进给运动,如拉削。
运动主体:工件,如铣削、磨削;刀具,如车削、钻削。
3、切削用量切削用量是指切削速度c v 、进给量f (或进给速度)和背吃刀量p a 。
三者又称为切削用量三要素。
1)切削速度c v (m/s 或m/min):切削刃选定点相对于工件的主运动速度称为切削速度。
主运动为旋转运动时,切削速度由下式确定1000dn v c π=式中:d-工件或刀具的最大直(mm)n-工件或刀具的转速(r/s 或r/min)2)进给量f:工件或刀具转一周(或每往复一次),两者在进给运动方向上的相对位移量称为进给量,其单位是mm/r(或mm/双行程)。
3)背吃刀量p a (切削深度mm)2m w p d d a -=式中:w d -工件上待加工表面直径(mm);m d -工件上已加工表面直径(mm)。
4、工件表面:切削过程中,工件上有三个不断变化的表面待加工表面:工件上即将被切除的表面。
过渡表面:正被切削的表面。
下一切削行程将被切除。
己加工表面:切削后形成的新表面。
5、刀具上承担切削工作的部分称为刀具的削部分,刀具切削部分由一尖二刃三面组成。
0第一课 金属切削原理、刀具与机床 知识点复习
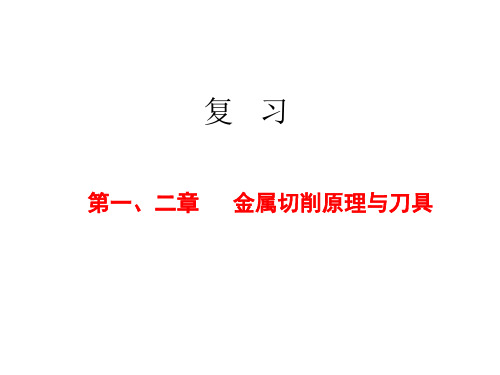
刃倾角的影响
车刀材料的影响
§5 切削热和切削温度
一、切削热的产生和传导
1、切削热的来源 切屑变形功、前后刀面的摩擦功
2、切削热的传出 切削、工件、刀具、周围介质等
二、切削温度的测量
1、切削温度:一般指前刀面与切屑接触区域的平均温度 2、切削温度的理论计算 3、测量方法 ➢ 热电偶法:自然热偶法和人工热偶法 ➢ 辐射温度计法:辐射热计法、红外线干板法、红外 线胶片法 ➢ 其他方法:热敏颜料法、热敏电阻法、量热计法、 金属组织观察法
(2)硬质合金 ➢ 突出性能:硬度、耐磨性、耐热性都很高;但抗弯 强度低,断裂韧性也较低
➢ 突出性能:硬度、耐磨性、耐热性都很高;但抗弯强度 低,断裂韧性也较低 ➢ 主要种类:
P类:YT5、YT15、YT30 K类:YG3、YG6、YG8 M类:YW1、YW2 ➢ 应用范围:
YG类→铸铁、有色金属、非金属材料 高强度钢、奥氏体钢、高温合金粗加工
§4 切削力与切削功率
一、切削力的来源、切削合力及其分解、切削功率
1、切削力的来源 ➢ 抗力
➢ 摩擦阻力
2、切削合力及分解
➢ 主切削力(切向力)
➢ 进给力(轴向力)
➢ 背向力
3、切削功率与电机功率
Pc
(Fzvc
Fxnw f 1000
) 103
Fzvc
103
PE
Pc
二、切削力的测量
1、切削力的理论计算 2、切削力的测量方法 ➢ 测定切削功率,计算切削力 ➢ 用测力仪测量切削力
六、切屑类型及其控制
1、带状切屑 ➢ 产生条件:加工塑性材料,切削速度较高,切削 厚度较小,刀具前角较大 ➢ 形态特征:内表面是光滑的,外表面是毛葺的
金属切削原理及刀具

金属切削原理及刀具§1切削运动和切削用量刀具从毛坯上切除多余金属,从而获得在行状上、尺寸精度上和表面质量都合乎预定要求的加工,称为金属切削加工。
在切削加工过程中,刀具与工件相互接触且存在着相互运动,这种相互运动的过程称为金属切削过程。
在切削过程中,将产生各种物理现象及其变化,这些都是金属加工原理所要研究的内容。
一.切削运动1)主运动切削时直接切除工件上的金属层,使之转变为切屑的运动,称为主运动。
通常,主运动的速度最高,消耗的功率最大。
主运动可以由工件完成,也可以由刀具完成。
车削时工件的旋转运动是主运动。
一种切削加工方法其主运动只有一个。
2)进给运动不断地将多余金属投入切削,以保证切削连续进行的运动,称为进给运动。
进给运动的速度较低,消耗的功率较小。
车削的时候,车刀的纵向移动和横向移动都属于进给运动。
一种切削加工方法其进给运动不限于一个。
在切削过程中,被切金属层不断地被切削而转变为切屑,从而加工出所需要地工件表面。
在工件表面形成的过程中,工件上有三个不断变化着的表面。
(1)已加工表面切削后在工件上形成的新表面。
(2)待加工表面即将被切除的表面。
(3)加工表面切削刃正在切削着的表面。
二.切削用量切削用量是衡量切削运动和切削力大小的参数。
它包括三个要素:切削速度、进给量、切削深度。
切削用量的大小,反映单位时间内的金属切除量。
它是衡量生产率的重要参数之一。
1.切削速度即主运动的线速度,即m/s。
其中,为工件待加工表面直径,n为工件转速;由于刀刃上各点相对于工件的旋转半径不同,因而刀刃上各点的切削速度也不相同。
计算时,应以最大速度为准。
2.进给量当主运动旋转一周时,刀具(或工件)沿进给方向上的位移量。
车削时,工件旋转一周,刀具沿进给方向的位移量。
显然,进给量的大小反映着进给速度的大小关系为:3.切削深度工件上已加工表面与待加工表面之间的垂直距离。
车削时,车削深度是待加工表面直径与已加工表面直径差的一半,即,其中,为工件已加工表面直径。
第二章金属切削原理与刀具详解

2、刀具角度的参考平面(静态)
1)基面Pr:过刀刃选定点⊥ 的平面。 2)切削平面Ps:包含 并与刀刃在选定点
相切的平面。 3)正交平面Po :过刀刃选定点⊥Pr,⊥Ps
的平面。
2、刀具角度的参考平面(静态)
3、刀具的标注角度
1)主偏角κr :主刀刃在基面上投影与走 刀方向的夹角。
2)刃倾角λs:主刀刃与基面在切削平面上 的夹角。
第二章 金属切削原理 与刀具
第一节 金属切削与刀具的基本概念
金属切削过程与金属切削刀 具中有许多基本概念,熟练掌 握这些基本概念是讨论相关技 术问题的基础。
一、基本概念 1、加工表面
待加工表面:
工件上即将被切除的表面.
已加工表面:
工件上切削后新形成的表面。
加工表面(过渡表面):
工件上正在被切削的表面。
一、刀具材料应具备的性能
1)高的硬度和耐磨性 2)足够的强度和韧性 3)良好的热物理性能和耐热冲击性能 4)良好的工艺性 5)经济性
一、刀具材料应具备的性能
刀具材 料一般硬度 越高则韧性 较差;而硬度 越低则韧性 较好。
二、常用刀具材料
常用刀具材料主要有: 高速钢 硬质合金
1、高速钢
高速钢刀具一般为整体式或焊接式,热处 理后硬度一般为63~66HRC,耐热性为 500~650℃,制造工艺性好,在制造中、 低速切削刀具、形状复杂及成形刀具中高速 钢应用广泛。
第二节 刀具材料 刀具三要素: 1)刀具切削部分材料; 2)刀具切削部分几何形状; 3)刀具结构。
刀具切削部分的工作状态
刀具切削部分在工作时,受到切削力的作用和 冲击,有时会碎裂或折断。 刀具切削部分在工作时,受到工件和切屑的强 烈挤压、摩擦,会产生大量的切削热,使刀具切 削部分处于高温状态,影响刀具材料的切削性 能,在切除金属材料时,本身也会被磨损。
金属切削原理与刀具习
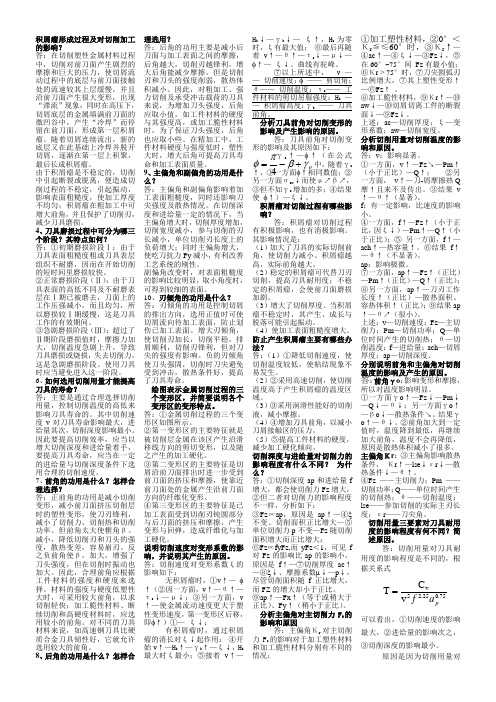
积屑瘤形成过程及对切削加工的影响?答:在切削塑性金属材料过程中,切削对前刀面产生剧烈的摩擦和巨大的压力,使切屑流动过程中的底层与前刀面接触处的流速较其上层缓慢,并且沿前刀面产生很大变形,出现“滞流”现象,同时在高压下,切屑底层的金属填满前刀面的微凹谷中,产生“冷焊”而停留在前刀面,形成第一层积屑瘤。
随着切屑连续流出,新的底层又在此基础上冷焊并脱开切屑,逐渐在第一层上积聚,最后长成积屑瘤。
由于积屑瘤是不稳定的,切削中引起断裂或脱离,便造成切削过程的不稳定,引起振动,影响表面粗糙度,使加工厚度不均匀;积屑瘤在粗加工中可增大前角,并且保护了切削刃,减少刀具磨损。
4、刀具磨损过程中可分为哪三个阶段?其特点如何?答:①初期磨损阶段Ⅰ:由于刀具表面粗糙度粗或刀具表层组织不耐磨,因而在开始切削的短时间里磨损较快。
②正常磨损阶段(Ⅱ):由于刀具表面的高低不同及不耐磨表层在Ⅰ期已被磨去,刀面上的工作压强减小,而且均匀,所以磨损较Ⅰ期缓慢,这是刀具工作的有效期间。
③急剧磨损阶段(Ⅲ):超过了Ⅱ期阶段磨损值时,摩擦力加大,切削温度急剧上升,导致刀具磨损或烧损,失去切削力,这是急剧磨损阶段。
使用刀具时应当避免进入这一阶段。
6、如何选用切削用量才能提高刀具的寿命?答:主要是通过合理选择切削用量,控制切削温度的高低来影响刀具寿命的。
其中切削速度v对刀具寿命影响最大,进给量其次,切削深度影响最小。
因此要提高切削效率,应当以增大切削深度和进给量着手,要提高刀具寿命,应当在一定的进给量与切削深度条件下选用合理的切削速度。
7、前角的功用是什么?怎样合理选择?答:正前角的功用是减小切削变形,减小前刀面挤压切削层时的塑性变形,使刀刃锋利,减小了切削力、切削热和切削功率。
但前角太大使楔角β。
减小,降低切削刃和刀头的强度,散热变差,容易崩刃。
反之负前角使β。
加大,增强了刀头强度,但在切削时振动也加大。
因此,合理前角应根据工件材料的强度和硬度来选择。
金属切削原理与刀具讲义
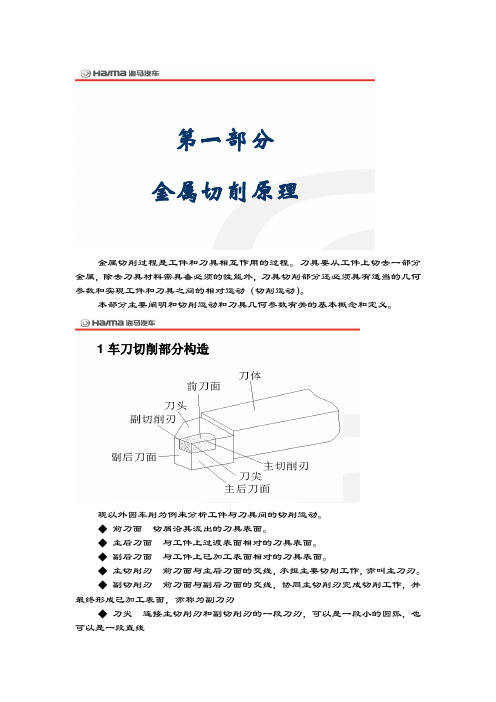
金属切削原理第一部分金属切削过程是工件和刀具相互作用的过程。
刀具要从工件上切去一部分金属,除去刀具材料需具备必须的性能外,刀具切削部分还必须具有适当的几何参数和实现工件和刀具之间的相对运动(切削运动)。
本部分主要阐明和切削运动和刀具几何参数有关的基本概念和定义。
1车刀切削部分构造现以外圆车削为例来分析工件与刀具间的切削运动。
◆ 前刀面 切屑沿其流出的刀具表面。
◆ 主后刀面 与工件上过渡表面相对的刀具表面。
◆ 副后刀面 与工件上已加工表面相对的刀具表面。
◆ 主切削刃 前刀面与主后刀面的交线,承担主要切削工作,亦叫主刀刃。
◆ 副切削刃 前刀面与副后刀面的交线,协同主切削刃完成切削工作,并最终形成已加工表面,亦称为副刀刃◆ 刀尖 连接主切削刃和副切削刃的一段刀刃,可以是一段小的圆弧,也可以是一段直线1、切削运动①主运动:主运动是从工件上切除金属所必须的运动。
只有一个、速度最高、消耗功率最大。
②进给运动:进给运动是使金属层不断投入切削过程,获得所需工件表面的运动。
不止一个、速度较小、消耗功率较小。
③合成运动:合成运动是上述主运动与进给运动的合成。
2、工件上的加工表面①待加工表面:工件上即将被切去的表面,随切削过程连续逐渐变小,直至全部切去。
②已加工表面:工件上已经切去了多余金属而形成的新表面,随切削继续而扩大。
③过渡表面,也叫切削表面:切削刃在切削中的表面,并在切削中不断改变,总是位于待加工表面和已加工表面之间。
➢前角γo:在正交平面内测量的前刀面和基面间的夹角。
前刀面在基面之下时前角为正值,前刀面在基面之上时前角为负值。
➢后角αo:在正交平面内测量的主后刀面与切削平面的夹角,一般为正值。
➢主偏角κr:在基面内测量的主切削刃在基面上的投影与进给运动方向的夹角。
➢副偏角κr’:在基面内测量的副切削刃在基面上的投影与进给运动反方向的夹角。
➢刃倾角λs:在切削平面内测量的主切削刃与基面之间的夹角。
无论用于何种加工,刀具都有三个主要角度:前角、切入角和后角。
金属切削原理与刀具复习题
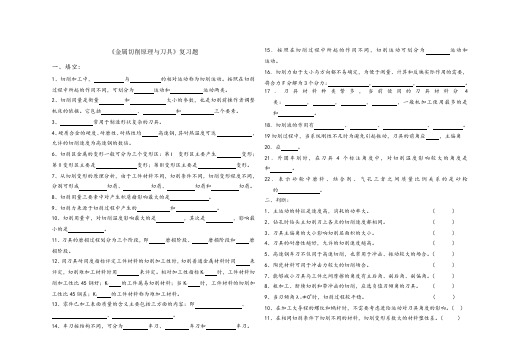
《金属切削原理与刀具》复习题一、填空:1、切削加工中,与的相对运动称为切削运动。
按照在切削过程中所起的作用不同,可划分为运动和运动两类。
2、切削用量是衡量和大小的参数,也是切削前操作者调整机床的依据。
它包括、和三个要素。
3、常用于制造形状复杂的刀具。
4、硬质合金的硬度、耐磨性、耐热性均高速钢,其耐热温度可达,允许的切削速度为高速钢的数倍。
6、切削区金属的变形一般可分为三个变形区:第І变形区主要产生变形;第Ⅱ变形区主要是变形;第Ⅲ变形区主要是变形。
7、从切削变形的原理分析,由于工件材料不同,切削条件不同,切削变形程度不同,分别可形成切屑、切屑、切屑和切屑。
8、切削用量三要素中对产生积屑瘤影响最大的是。
9、切削力来源于切削过程中产生的和。
10、切削用量中,对切削温度影响最大的是,其次是,影响最小的是。
11、刀具的磨损过程划分为三个阶段,即磨损阶段、磨损阶段和磨损阶段。
12、用刀具耐用度指标评定工件材料的切削加工性时,切削普通金属材料时用来评定,切削难加工材料时用来评定。
相对加工性指标Kr时,工件材料切削加工性比45钢好;Kr 的工件属易切削材料;当Kr时,工件材料的切削加工性比45钢差;Kr的工件材料称为难加工材料。
13、零件已加工表面质量的含义主要包括三方面的内容:即、、。
14、车刀按结构不同,可分为车刀、车刀和车刀。
15.按照在切削过程中所起的作用不同,切削运动可划分为运动和运动。
16.切削力由于大小与方向都不易确定,为便于测量、计算和反映实际作用的需要,将合力F分解为3个分力:,,。
17.刀具材料种类繁多,当前使用的刀具材料分4类:,,,,一般机加工使用最多的是和。
18.切削液的作用有、、、。
19切削过程中,当系统刚性不足时为避免引起振动,刀具的前角应,主偏角20.应。
21.外圆车削时,在刀具4个标注角度中,对切削温度影响较大的角度是和。
22.表示砂轮中磨料、结合剂、气孔三者之间质量比例关系的是砂轮的。
金属切削原理与刀具
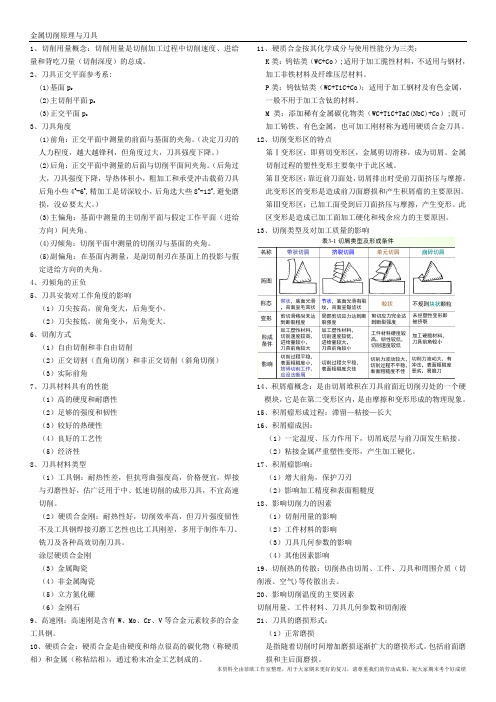
1、切削用量概念:切削用量是切削加工过程中切削速度、进给量和背吃刀量(切削深度)的总成。
2、刀具正交平面参考系:(1)基面p r(2)主切削平面p s(3)正交平面p o3、刀具角度(1)前角:正交平面中测量的前面与基面的夹角。
(决定刀刃的人力程度,越大越锋利,但角度过大,刀具强度下降。
)(2)后角:正交平面中测量的后面与切削平面间夹角。
(后角过大,刀具强度下降,导热体积小,粗加工和承受冲击载荷刀具后角小些4o-6o,精加工是切深较小,后角选大些8o-12o,避免磨损,没必要太大。
)(3)主偏角:基面中测量的主切削平面与假定工作平面(进给方向)间夹角。
(4)刃倾角:切削平面中测量的切削刃与基面的夹角。
(5)副偏角:在基面内测量,是副切削刃在基面上的投影与假定进给方向的夹角。
4、刃倾角的正负5、刀具安装对工作角度的影响(1)刀尖按高,前角变大,后角变小。
(2)刀尖按低,前角变小,后角变大。
6、切削方式(1)自由切削和非自由切削(2)正交切割(直角切削)和非正交切削(斜角切削)(3)实际前角7、刀具材料具有的性能(1)高的硬度和耐磨性(2)足够的强度和韧性(3)较好的热硬性(4)良好的工艺性(5)经济性8、刀具材料类型(1)工具钢:耐热性差,但抗弯曲强度高,价格便宜,焊接与刃磨性好,估广泛用于中、低速切削的成形刀具,不宜高速切削。
(2)硬质合金刚:耐热性好,切削效率高,但刀片强度韧性不及工具钢焊接刃磨工艺性也比工具刚差,多用于制作车刀、铣刀及各种高效切削刀具。
涂层硬质合金刚(3)金属陶瓷(4)非金属陶瓷(5)立方氮化硼(6)金刚石9、高速刚:高速刚是含有W、Mo、Cr、V等合金元素较多的合金工具钢。
10、硬质合金:硬质合金是由硬度和熔点很高的碳化物(称硬质相)和金属(称粘结相),通过粉末冶金工艺制成的。
11、硬质合金按其化学成分与使用性能分为三类:K类:钨钴类(WC+Co);适用于加工脆性材料,不适用与钢材,加工非铁材料及纤维压层材料。
金属切削原理知识与刀具含习题答案
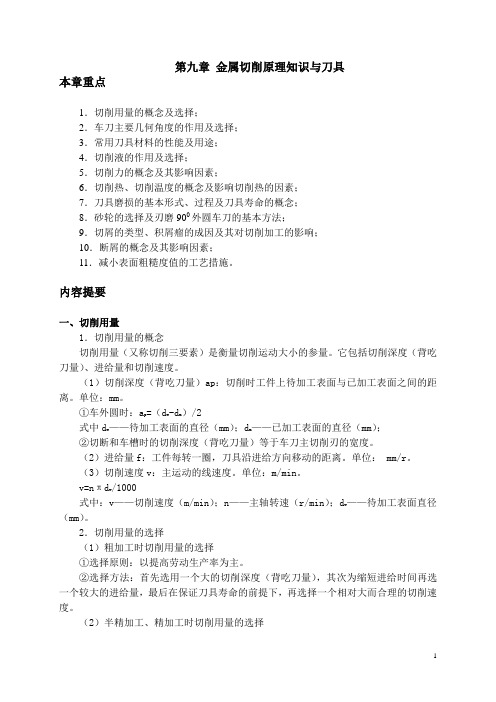
第九章金属切削原理知识与刀具本章重点1.切削用量的概念及选择;2.车刀主要几何角度的作用及选择;3.常用刀具材料的性能及用途;4.切削液的作用及选择;5.切削力的概念及其影响因素;6.切削热、切削温度的概念及影响切削热的因素;7.刀具磨损的基本形式、过程及刀具寿命的概念;8.砂轮的选择及刃磨900外圆车刀的基本方法;9.切屑的类型、积屑瘤的成因及其对切削加工的影响;10.断屑的概念及其影响因素;11.减小表面粗糙度值的工艺措施。
内容提要一、切削用量1.切削用量的概念切削用量(又称切削三要素)是衡量切削运动大小的参量。
它包括切削深度(背吃刀量)、进给量和切削速度。
(1)切削深度(背吃刀量)ap:切削时工件上待加工表面与已加工表面之间的距离。
单位:mm。
①车外圆时:ap =(dw-dm)/2式中dw ——待加工表面的直径(mm);dm——已加工表面的直径(mm);②切断和车槽时的切削深度(背吃刀量)等于车刀主切削刃的宽度。
(2)进给量f:工件每转一圈,刀具沿进给方向移动的距离。
单位: mm/r。
(3)切削速度v:主运动的线速度。
单位:m/min。
v=nπdw/1000式中:v——切削速度(m/min);n——主轴转速(r/min);dw——待加工表面直径(mm)。
2.切削用量的选择(1)粗加工时切削用量的选择①选择原则:以提高劳动生产率为主。
②选择方法:首先选用一个大的切削深度(背吃刀量),其次为缩短进给时间再选一个较大的进给量,最后在保证刀具寿命的前提下,再选择一个相对大而合理的切削速度。
(2)半精加工、精加工时切削用量的选择①选择原则:以保证加工精度为主。
②选择方法:切削余量原则一次进给完成,也可分多次,但最后一次进给的余量不得小于0.1mm;进给量应选小一些;切削速度应根据刀具材料选择,高速钢刀具一般小于5m/min,硬质合金可大于80 m/min。
二、刀具的几何角度1.切削运动——切削时刀具与工件之间的相对运动,包括主运动和进给运动。
第1章 金属切削原理及刀具 学习指导
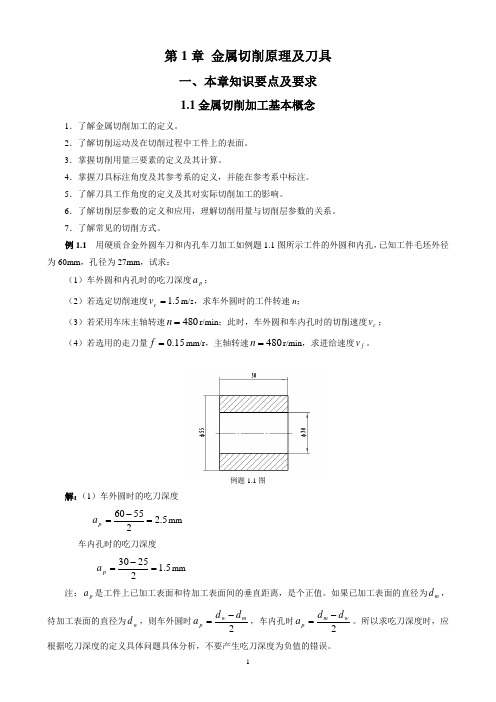
第1章 金属切削原理及刀具一、本章知识要点及要求1.1金属切削加工基本概念1.了解金属切削加工的定义。
2.了解切削运动及在切削过程中工件上的表面。
3.掌握切削用量三要素的定义及其计算。
4.掌握刀具标注角度及其参考系的定义,并能在参考系中标注。
5.了解刀具工作角度的定义及其对实际切削加工的影响。
6.了解切削层参数的定义和应用,理解切削用量与切削层参数的关系。
7.了解常见的切削方式。
例1.1 用硬质合金外圆车刀和内孔车刀加工如例题1.1图所示工件的外圆和内孔,已知工件毛坯外径为60mm ,孔径为27mm ,试求:(1)车外圆和内孔时的吃刀深度p a ;(2)若选定切削速度5.1=c v m/s ,求车外圆时的工件转速n ;(3)若采用车床主轴转速480=n r/min ;此时,车外圆和车内孔时的切削速度c v ;(4)若选用的走刀量15.0=f mm/r ,主轴转速480=n r/min ,求进给速度f v 。
例题1.1图解:(1)车外圆时的吃刀深度5.225560=-=p a mm 车内孔时的吃刀深度 5.122530=-=p a mm 注:p a 是工件上已加工表面和待加工表面间的垂直距离,是个正值。
如果已加工表面的直径为m d ,待加工表面的直径为w d ,则车外圆时2m w p d d a -=,车内孔时2w m p d d a -=。
所以求吃刀深度时,应根据吃刀深度的定义具体问题具体分析,不要产生吃刀深度为负值的错误。
(2)根据 1000dnv c π= ,则7.4776014.35.110001000=⨯⨯==d v n c πr/min 注:当转速一定时,切削刃上各点的切削速度是不同的。
考虑到切削速度对刀具磨损和已加工质量有影响,在计算时,应取最大的切削速度。
所以在切削速度的计算公式中,d 的取值应根据不同的加工情况确定。
例如外圆车削时,d 取待加工表面直径,内孔车削时,d 取已加工表面的直径。