精益生产线评审表(案例)
精益线评审表

2.1
3
2
物流管理: 库存控制应 使用物流 架,看板和 后拉系统; 持续下降单 量(目标2 个单量,以 针车每小时 产能计算即 为3小时)
2.2
4
2.3
4
现场作业观察生产线出现因工位器具原因造成的 1、现场观察现场物料是否有必要的、合理的器具用来转运和 停滞现象,每发现一处扣0.2分。 存放,2、是否有物料无序堆积、不方便操作者存取现象? 在制品期量标准或成品期量标准缺失,分别扣 0.5分。 现场检查在制品及成品数量与期量标准不相符, 且无外部他责原因,每发现一处扣0.3分。 在制品和成品统计数据不完整或每日动态未更 新,每发现一处扣0.1分。 超标在制品未有分析处理记录,每发现一处扣 0.2分。 未制定在制品消减计划,扣0.5 分。 在制品期量标准未实现同比降低,扣0.5分。 1、是否有针对或者覆盖本生产线在制品控制标准,并按照工 序、存放区域或者产品状态和属性进行合理划分? 2、抽查现场在制存放区(含在线的)是否按照在制标准执 行? 1、在制品日常监控方式或者记录有哪些?抽查连续相关记 录,确认是否能够每日更新? 2、现场即时清点或者检查前期记录,如有超标现象,是否有 分析处理记录? 1、是否有针对或者覆盖本生产线的在制压缩计划? 2、今年平均在制水平是否较以往统计有降低?
2
5.6
2
检查设备自主保全记录、故障现象记录,未填写 完整或动态未更新,每发现一处扣0.2分。 自主保全活动记录是否完整?抽选自主保全项目进行现场检 设备自主保全未按标准执行到位,每发现一处扣 查? 0.5分。
3.1
5Leabharlann 检查日计划完成情况,日均计划完成率未达到目 检查生产线日生产计划及完成情况(关注月度平均计划完成 标要求,每少一个百分点,扣0.5 分。 率)。
精益生产评价打分表

60 4.6.2 持续改善活动开展
4.6.3 基本的持续改善方法
5.1.1 系统应变能力提高
5.1.2 管理简单化
125 5.1.3 精益人才培养
5.1.4 公司形象提升
5.1.5 精益公司文化形成
5.2.1 员工及顾客满意率提
高
5.2.2 不良品率下降
175
5.2.3 人均生产率提高 5.2.4 生产周期缩短
25
25 25 25 25 25 25 1000
评价人员:
评价日期
得分
60
4.1.3 5S活动策划 4.1.4 5S活动展开
4.1.5 5S实施效果
4.1.6 全面推行5S活动
4.2.1 合理布局
4.2.2 多能工
4.2.3 均衡性生产
4.2.4 快速切换
160 4.2.5 看板管理
4.2.6 试听管理2.9 物流与搬运
50
5.2.5 库存量的降低
5.2.6 降低成本
5.2.7 利润提高
标准分 50
20 20 20 20 20 20 20 20 20 20 10 10 10 10 10 10 20 20 20 20 10 20 10 20 20 30 20 10 10 10 10 20 15 15 15 15 20 20 20 25 25 25 25 25
5.2 精益生产后取得 的有形成果
合计
50
1.1决策层对精益的重视
60 1.2精益长期推进的理念
1.3决策层的决心和目标
2.1精益生产的目标
80
2.2精益生产的核心 2,3精益生产的理论基础
2.4精益理论培训
3.1设立精益推进机构
3.2精益推进计划
XX鞋厂针车组精益生产执行力考核表
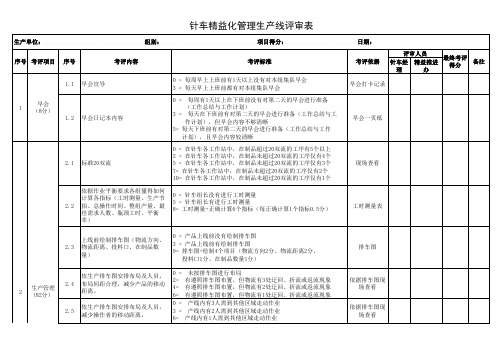
2.5
3 = 产线内有2人需到其他区域走动作业
减少操作者的移动距离。
6= 产线内有1人需到其他区域走动作业
排车图
依据排车图现 场查看
依据排车图现 场查看
生2产单生位产:管理 (82分)
序号 考评项目
组别:
项目得分:
日期:
序号 2.6 2.7
考评内容
针车组生产目视管理板
6S小组依据《6S评审标准》每2周 不定期进行现场巡查并进行评分
生管统计提供
3.1 精益生产课程培训
精益生产 3 培训
(10分) 3.2 精益生产课程培训课后作业
0= 参与精益生产课程培训,表现较差(经常请假、迟到或缺席) 3=参与精益生产课程培训,表现较好(偶尔请假、迟到) 5=参与精益生产课程培训,表现良好
培训签到表
0=精益生产培训课后作业经常未按时交作业,且没有将精益生产知
3 = 每天在下班前有对第二天的早会进行准备(工作总结与工 作计划),但早会内容不够清晰
5= 每天下班前有对第二天的早会进行准备(工作总结与工作 计划),且早会内容较清晰
2.1 标准20双流
0 = 在针车各工作站中,在制品超过20双流的工序有5个以上 2 = 在针车各工作站中,在制品未超过20双流的工序仅有4个 5 = 在针车各工作站中,在制品未超过20双流的工序仅有3个 7= 在针车各工作站中,在制品未超过20双流的工序仅有2个 10= 在针车各工作站中,在制品未超过20双流的工序仅有1个
评审人员
考评标准
考评依据 针车经 精益推进
理
办
0 = 每2小时未能依生产实际状况正确填写《生产目视管理板》
3= 每2小时能依生产实际状况正确填写《生产目视管理板》并未能 每2小时产量统
精益生产管理自评评价表单
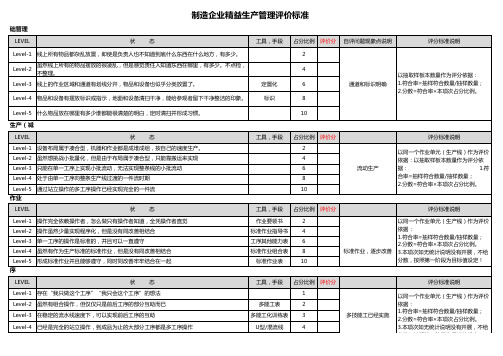
状
态
Level-1 作业完全依靠人,或是投入大量资金购入很多生产设备
Level-2 人手同机械共同作业
Level-3 虽然可以实现人机分离,但是人离开后机器会生产出不合格产品
Level-4 已经实现人离开后完全不会出现不合格品的自动化
1L5e、ve设l-5 完全的自动化,自动化设备相连形成不需要人工的流水作业,智能控制集成系统应用。 备维护
LEVEL
状
态
Level-1 工序到处堆放着前工序而来的硬塞入的零部件材料 Level-2 虽然是塞入式的生产,但有少数放置地点已经能标示出来 Level-3 放置地点形成定位定量,形成给后序定量送取的结构 Level-4 形成后工序定量送取的看板结构 1L1e、ve质l-5 不仅可以形成后工序定量送取的看板结构,还同改善活动相结合 量管控变
按灯
5
工具,手段 自动停止装置
占分比例 评价分 1 2 3 4 5
LEVEL
状
态
工具,手段 占分比例 评价分
Level-1 机械经常故障,红色级别事故全年都有
1
Level-2 机械故障完全依赖保全,事故时有发生
日常保全
2
Level-3 事后保全彻底,基本没有大的事故
定期保全
3
Level-4 预防保全彻底,基本没有红色级别的事故
预防保全计划
4
1L6e、ve员l-5 在公司内开展生产保全活动,机械没有故障,完全没有事故
5
工教育、
LEVEL
状
态
工具,手段 占分比例 评价分
Level-1 改善活动没有形成团队和组织,属于个人所想所做
1
有防差错
以同一个作业单元(生产线)作为评价 依据: 1.符合率=抽样符合数量/抽样数量; 2.分数=符合率×本项次占分比例。
精益生产线评审表(案例)

4.2
1
精益化管理生产线评审表
生产线名称: 序号 考评项目 考评内容 强化质量过程控制,有详尽的操作 及检验指导书,并同工艺文件一起 在各工序放置且有效执行。 加强工艺纪律,定期对操作者工艺 纪律执行情况进行检查,对发现问 题制定整改措施并有效实施。 强化产品在线检验,现场量检具齐 全且有效;按检验指导书要求开展 首、末件检验,自检、互检、专检 、巡检等检查工作。 做好质量数据(线内不良、后工序 不良、前十位质量问题等)收集、 统计和分析,对质量数据异常波动 实时分析,提出整改方案并有效实 施。月度质量指标达到控制目标要 求,运行趋势平稳、向好。 有效实施“质量门”管理,对生产 线质量控制点及在线检测进行全面 策划,完善“质量门”;明确“质 量门”操作标准和“守门人”管理 办法;每日检查“质量门”运行情 况进行,做好运行记录,确保指标 控制在特性值要求范围。 有明确的不合格品处置流程,严格 执行不合格品剔除、隔离、标识及 记录,防止不合格转入后生产线。 有效开展QC(质量控制)小组活 动,做好记录及评价,年度确保取 得1项以上公司级QC改进成果。 基本分 考评标准 检查人: 项目得分: 检查点 (请做好详细检查记录) 评审分值
3.2
1
3.3
1
现场检查当日生产情况,时节拍 差异率上下浮动超过10%,且未有 是否有时节拍差异率(达到10%以上)影响因素的记录表,并对 原因说明的,每出现一处扣0.2分 各影响因素如实记录? 。 检查生产线各工序标准作业指导 文件,每发现一处缺失的扣0.2分 1、是否对各工序的标准作业进行规定? 。 现场检查员工序作业有未按作业 2、抽选工序,按照作业指导文件检查操作的符合性。 指导标准操作的状况,每发现一 处扣0.2 分。 抽查月度工序标准作业稽查记 录,缺失或检查内容不完整的, 扣 1 分 异常统计表记录不完整或未动态 更新,扣0.5分。 生产线异常统计表未能有效体现 停工原因,扣0.5分。 生产线可动率未达到要求目标, 扣1分 抽查生产绩效指标完成情况,未 进行分析,制定改进、优化措施 的,每发现一处扣0.5分。 1、是否有工序标准作业检查计划或者周、月度检查的要求或规 定? 2、是否按照要求进行检查和记录?
工厂精益制造改善评价表201302

整理整顿和清洁 状态
3
2
1
0
车间
基础管理
10 基础管理
作业纪律遵守状 态是否良好
11
改善意欲状态
12
看得到的管理体 制
13
工序有没有定量 标准,是否管理
14
有没有对生产计 划进行实绩管理
15
人均效率提升 (人均产出提 高)
16
现场的整理状态 良好。(作业环 生产管理 境)
A、制定了作业纪律并遵守。 B、作业纪律制定了,但只遵守了50%。 C、作业纪律制定好了,但只遵守很小一部分 。 D、作业纪律没有制定,而且作业开始前迟到 A、每人每月提出一件以上改善建议提案, 90%以上实施,效果显著。 B、建议提案每人每月1件以上,60%以上实 施,效果普通。 C、一部分人有改善意欲,偶尔建议提案。 D、觉得现在的方法是最好的,无改善余地。 A、全面实施并完全沉淀。 B、全面实施,但没有完全沉淀。 C、对看得见的管理有部分能理解,部分付诸 实施。 D、对看得见的管理完全不关心。 A、工序间的每个接点都设定,并切实在好的 位置标示出来。 B、工序间每个接点都设定,但标示不合适。 C、工序间每个接点只设定出来。 D、没有标准定量的概念而作业。 A、制定月度生产计划,有生产情况看板,持 续记录并管理生产实绩。 B、制定了生产计划,有生产情况看板但是没 有进行记录管理。 C、有每日生产计划,但没有看板也没有实绩 记录管理 D、对比生产计划实绩管理全无。 (本年人均实际产出-前年度人均产出) ----------------------------------- × 100% 前年度人均产出数 A、提高30%以上 B、20%以上 C、10%以上 D、10%以下 A、有过道标识、物品放置场所标识,管理状 态良好。 B、有过道标识,物品放置场所标识,但管理 状态不足。 C、有部分过道标识,物品放置场所标识,管 理状态不足。 D、完全没有过道标识、物品放置场所标识。
精益生产评价表
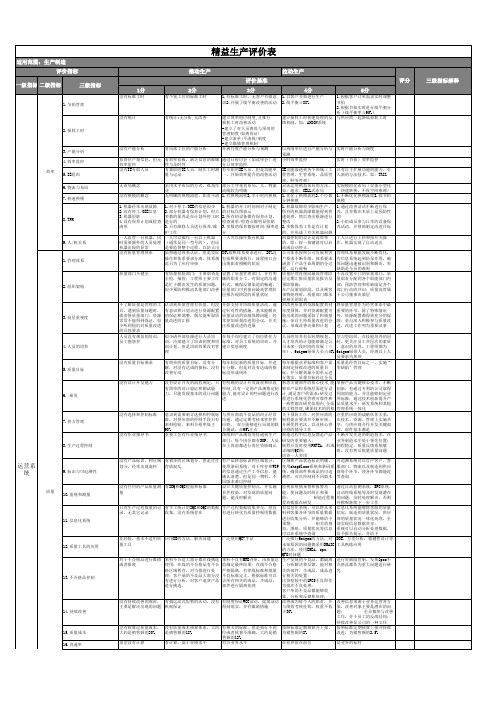
量与记录
一,开始效率提升的改善活动 程管理、生管系统、品质管 入新的方法技术。如:TRIZ
理、财务管理)
无布局概念
采用水平布局的方式,孤岛作 部分工序垂直布局,人、物流 灵活运用精益布局的方法。 实现模组化布局(设备小型化
业
动线较为明确
如:超市、CELL式布局
、快速转换,不收空间束缚)
没有换模的概念
部;预防管理和零缺陷是各个
很少预防和推动其他部门改善 质量部门可直接向最高管理阶 在产品策划阶段,以及顾客 部门行动的共识;质量高管属
层报告现阶段的质量状况
事物处理时,质量部门都承 于公司董事决策层
担相关的职责
不了解质量是管理的工 认识到质量管理有价值,但没 开始支持并协助质量活动,通 对改善质量的资源配置列到 将质量管理作为经营体系中最
进行挑选。
部件进行隔离处理
为批次不良处理;
客户单的不良品都能够收
集,分析和反馈和处理;
没有持续改善的规范, 有搞运动式短暂的活动,没有 有制度保证WCC活动,提案活动 改善成为每个人的职责,并 改善信息来源于业务运营各方
主要是解决出现的问题 机制保证
得到落实,并有激励措施
与绩效考核挂钩,权重不低 面,改善对象主要是潜在的问
质量 10.监视和测量
11.信息化系统
12.质量工具的应用
13.不合格品控制
14.持续改善
15.质量成本 16.直通率
精益生产评价表
推动生产
拉动生产
评价基准
评分
1分
2分
3分
4分
5分
没有标准工时
有个别工位的标准工时
1.有标准工时,无客户节拍意 1.以客户节拍进行生产
精益生产考核检查表
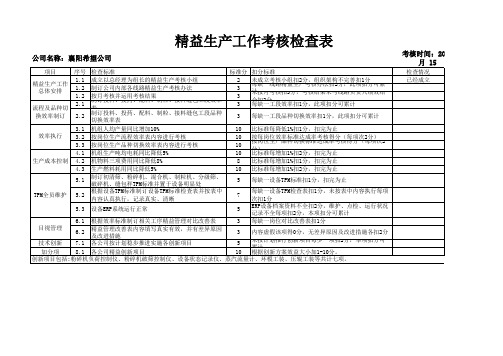
公司名称:襄阳希望公司
序号 1.1 精益生产工作 1.2 总体安排 1.2 2.1 流程及品种切 换效率制订 2.2 项目
考核时间:2009 年6
检查情况 已经成立
月 15
日
检查标准 标准分 扣分标准 成立以总经理为组长的精益生产考核小组 2 未成立考核小组扣2分,组织架构不完善扣1分 每缺一线路精益生产考核办法扣2分,此项扣分可累 制订公司内部各线路精益生产考核办法 3 计 未按月考核扣3分,考核结果未与线路负责人绩效结 按月考核并运用考核结果 3 合扣2分 制订投料、投药、配料、制粒、接料缝包工段效率 3 每缺一工段效率扣1分,此项扣分可累计 表 制订投料、投药、配料、制粒、接料缝包工段品种 3 每缺一工段品种切换效率扣1分,此项扣分可累计 切换效率表 3.1 机组人均产量同比增加10% 10 比标准每降低1%扣1分,扣完为止 效率执行 3.2 按岗位生产流程效率表内容进行考核 10 按每岗位效率标准达成率考核得分(每项次2分) 按岗位生产品种切换标准达成率考核得分(每项次2 3.3 按岗位生产品种切换效率表内容进行考核 10 分) 4.1 机组生产吨均电耗同比降低5% 10 比标准每增加1%扣2分,扣完为止 生产成本控制 4.2 机物料三项费用同比降低8% 8 比标准每增加1%扣1分,扣完为止 4.3 生产燃料耗用同比降低5% 10 比标准每增加1%扣2分,扣完为止 制订初清筛、粉碎机、混合机、制粒机、分级筛、 5.1 5 每缺一设备TPM标准扣1分,扣完为止 破碎机、缝包秤TPM标准并置于设备明显处 根据设备TPM标准制订设备TPM标准检查表并按表中 每缺一设备TPM检查表扣1分,未按表中内容执行每项 TPM全员维护 5.2 7 内容认真执行,记录真实、清晰 次扣1分 ERP设备档案资料不全扣2分,维护、点检、运行状况 5.3 设备ERP系统运行正常 5 记录不全每项扣2分,本项扣分可累计 6.1 根据效率标准制订相关工序精益管理对比改善表 3 每缺一岗位对比改善表扣1分 目视管理 精益管理改善表内容填写真实有效,并有差异原因 6.2 3 内容虚假该项得0分,无差异原因及改进措施各扣2分 及改进措施 未按计划推行创新项目每少一项扣2分,本项扣分可 技术创新 7.1 各公司按计划稳步推进实施各创新项目 5 累计 加分项 8.1 各公司精益创新项目 10 根据创新方案效益大小加1-10分。 创新项目包括:粉碎机负荷控制仪、粉碎机破筛控制仪、设备状态记录仪、蒸汽流量计、环模工装、压辊工装等共计七项。
精益生产管理考核表格
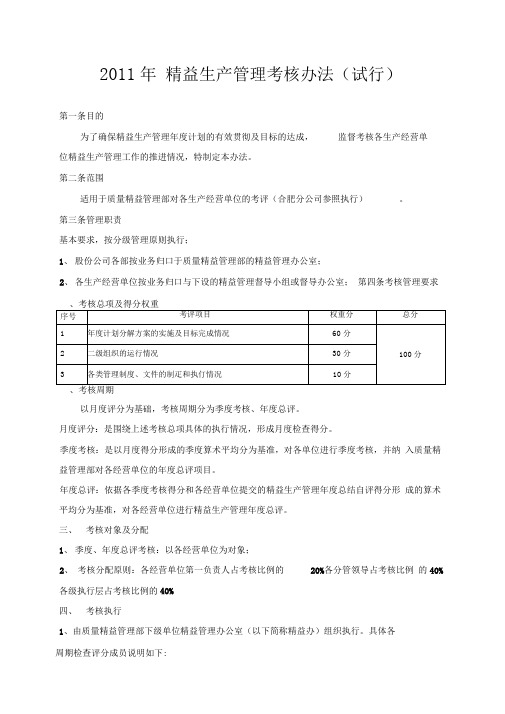
2011年精益生产管理考核办法(试行)第一条目的为了确保精益生产管理年度计划的有效贯彻及目标的达成,监督考核各生产经营单位精益生产管理工作的推进情况,特制定本办法。
第二条范围适用于质量精益管理部对各生产经营单位的考评(合肥分公司参照执行)。
第三条管理职责基本要求,按分级管理原则执行;1、股份公司各部按业务归口于质量精益管理部的精益管理办公室;2、各生产经营单位按业务归口与下设的精益管理督导小组或督导办公室;第四条考核管理要求以月度评分为基础,考核周期分为季度考核、年度总评。
月度评分:是围绕上述考核总项具体的执行情况,形成月度检查得分。
季度考核:是以月度得分形成的季度算术平均分为基准,对各单位进行季度考核,并纳入质量精益管理部对各经营单位的年度总评项目。
年度总评:依据各季度考核得分和各经营单位提交的精益生产管理年度总结自评得分形成的算术平均分为基准,对各经营单位进行精益生产管理年度总评。
三、考核对象及分配1、季度、年度总评考核:以各经营单位为对象;2、考核分配原则:各经营单位第一负责人占考核比例的20%各分管领导占考核比例的40%各级执行层占考核比例的40%四、考核执行1、由质量精益管理部下级单位精益管理办公室(以下简称精益办)组织执行。
具体各周期检查评分成员说明如下:2、季度考核及年度总评,经质量精益管理部审核,报公司总裁批准后执行,同时提交企业管理总部备案。
五、具体考评项目说明1、依据精益管理办公室制定的年度工作计划,要求各经营单位制定各自的年度分解计划、目标并贯彻实施,精益管理办公室将按各考核总项和周期对各经营单位进行评价打分。
2、各考核项目的考核评分周期均以月度为单位,以月度评价得分汇总形成季度算术平均分作为考核基准分,从而对各经营单位实施季度、年度考核。
3、为了便于考核实施,对各考核总项均设置了一定的目标分值,各考核总项的算术平均分乘以权重为最终得分。
具体考核标准、要求及分值见附表。
(一)年度计划分解方案的实施及目标完成情况(权重60分):1、年度计划分解方案指:6S管理、培训管理、TPM t理、改善管理、QC?舌动管理、提案管理。
精益项目评审表

评价标准1
评价标准2
评价标准3
评价标准4
评价标准5
评价标准6ຫໍສະໝຸດ 评价标准7精益项目评定标准:Lean Project Measurement Criteria
改善工具与方法的运用(36分) Application for impromvent tool and methodology
项目完成情况(8分) Project completion status
严重滞后于项目计划,几乎可以断定项目根本无法预期关闭, time Project has been delayed per plan, and can't close on
滞后计划一个月或以上,项目完成率<60%, Project has been delayed 1 month or more, achieved less 60% target 项目进展基本符合计划,项目完成率>80%, Project is almost met each milestone, and achieved more than 80% target
演示水平(满分8分) Presentation
时间偏差在3分钟之外,声音和语速运用一般,表达僵硬, Present time is exceed than 3 minutes of limited time, sound is flat 时间偏差在3分钟之内,声音和语速运用较好,较好阐述了报告内容 Present time is not exceed 3 minutes of limited time, sound and speed is attractive 时间控制得当,表达清晰生动,很好地阐述了报告内容, Good time control within the limited time, clear and concise present the project
优秀产线评比表Microsoft Excel 工作表

日期项目12345678910111213141516171819202122232425262728效率32303028品质30281817纪律181716185S89891.14% 1.19% 1.39% 1.39%88847272效率283428303230品质283028302830纪律1618171818185S7879871.27% 1.11% 1.25% 1.15% 1.16% 1.18%799080878685000000000000000000000效率30品质15纪律185S81.41%71000000000000000000000效率30283032303234品质28282026301628试产试产试产停线停线试产S1线S2线S3线S4线总分S M T 9 月 份 A 班 优 秀 线 评 比 表达标率总分达标率总分达标率停线停线停线停线纪律181717181718185S 78878791.20% 1.23% 1.33% 1.20% 1.18% 1.37% 1.12%83817583857389000000000000000000000效率303428323430品质302828302528纪律1817181819185S8878781.16% 1.15% 1.23% 1.14% 1.18% 1.19%868781888584000000000000000000000效率343230323032品质302830302230纪律1818181817185S8879891.11% 1.16% 1.18% 1.12% 1.30% 1.12%90868589778900000000000000000000效率303228品质283028纪律1618185S7781.23% 1.15% 1.22%818782000000000000000000000停线停线停线停线S4线S5线S6线S7线总分达标率总分备注:效率35分,品质35分,纪律20分,5S10分,满分100分停线停线达标率总分达标率总分达标率日期项目12345678910111213141516171819202122232425262728效率33333032品质33323133纪律181818195S88781.09% 1.10% 1.16% 1.09%92918692效率31302930品质31323031纪律191917185S88771.12% 1.12% 1.20% 1.16%89898386效率30313030品质30312832纪律181817175S89991.16% 1.12% 1.19% 1.14%86898488效率33323132品质30262425S1线总分达标率总分达标率总分S2线S3线S4线S M T 9 月 份 B 班 优 秀 线 评 比 表达标率。
精益生产自评表
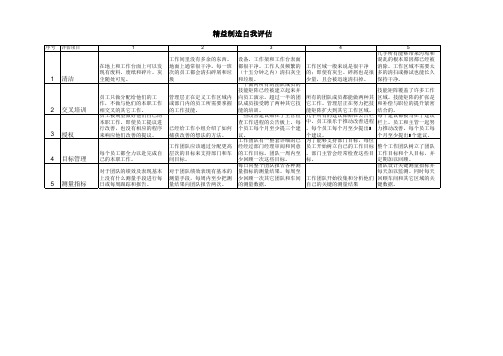
经常不能够按时完成生产任 务。通过现场协调生产的方 式来计划生产。 操作人员只负责完成工作, 质量检验则由质量检验员来 负责。 角色和职责或由个人自己定 或根据过去的工作实践来定 。 除非最近发生过事故,否则 没有人谈起安全或者坚持按 照安全工作的要求来进行工 作。
12 质量保证
正在努力协调好生产计划和 生产效率。每天讨论主要订 单的情况。 操作人员每天提供工作区域 内的质量信息。大部分的质 量问题都贴在了工作团队的 帕累托图上。
团队参加更广泛的策划工 作,基本上不需要管理支 持。每个月实施二十项改 进措施。 员工准时上班,充满热情 的工作并且愿意每个星期 至少加两次班。缺席率低 于1%,员工流动率低于 3%。 为了操作和维护的需要, 所有机器都已经标记上了 控制点、读出器和调整点 。 流程内库存从水平1中降低 了90%。各个操作员工之 间的工作量重新得到平 衡,差别控制在5%以内。
9
解决问题的 方法
10 流程控制
几乎没有大家都能够接受的 评定关键流程变量的标准。 许多流程都由个人主观来判 断。
已经正式开始系统的研究关 键流程的主要参数特性。
主要流程的所有的关键流程 变量都已经得到很好的理 解,而且大部分都已经被最 佳化。
精益制造自我评估
序号
评估项目 1 2 3 4 5
11 生产计划
工作团队能够清楚的知道所 有订单的情况。把生产能力 和工作任务联系起来考虑以 提高生产效率。 已经在工作区域内正式采用 错误防范措施。至少已经采 取了5个错误防范措施。团队 开始收集质量数据。 主管或团队领队分别和每一 位团队成员一起制定个人重 现性和再现性。 团队成员能够清楚的理解什 么是不安全的行为。工作人 员非常熟悉哪些不安全的行 为能够导致灾难或事故。 10%的换装时间已经降到了 个位数。办公区域已经得到 了换装时间为个位数的文件 。
安全精益生产管理风险评估表3.0版
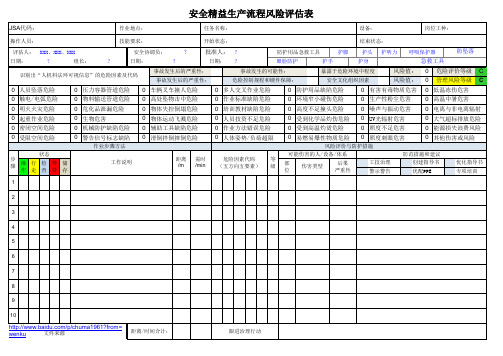
工作说明
距离 /m
需时 /min
危险因素代码 (五方向五要素)
等 级
风险评价与防护措施 可能伤害的人/设备/体系 部 位 伤害类型 后果 严重性 工技治理 警示警告
防范措施和建议 创建指导书 优配PPE 优化指导书 专项培训
/p/chuma1961?from= 文件来源 wenku
?
批准人: ?
日期: ?
防坠落 危险评价等级 管理风险等级 C C
急救工具 风险值: 风险值: 0 0
识别出“人机料法环可视信息”的危险因素及代码
暴露于危险环境中程度 安全文化组织因素
0 人员坠落危险 0 触电/电弧危险 0 明火火灾危险 0 起重作业危险 0 密闭空间危险 0 受限空间危险
状态
0 压力容器管道危险 0 物料输送管道危险 0 危化品泄漏危险 0 生物危害 0 机械防护缺陷危险 0 警告信号标志缺陷
距离/时间合计:
跟进治理行动
安全精益生产流程风险评估表
JSA代码:
操作人员: 评估人: 日期: XXX、XXX、XXX ? 组长: ? 作业地点: 技能要求: 安全协调员: 日期: ? 事故发生后的严重性: 事故发生后的严重性: 任务名称: 开始状态: 设备: 结束状态: 防护用品急救工具 眼脸防护 事故发生的可能性: 危险控制规程和硬件保障: 护手 护脚 护头 护身 护听力 呼吸保护器 岗位工种:
0 有害有毒物质危害 0 生产性粉尘危害 0 噪声与振动危害 0 UV光辐射危害 0 照度不足危害 0 照度刺眼危害
0 低温冻伤危害 0 高温中暑危害 0 电离与非电步 骤 操 行 检 等 储 作 走 查 待 存 1 2 3 4 5 6 7 8 9 10
作业步骤方法
精益现场评价表

3.按照N-TWI的基准,各栏没有漏记情况(包含作 业时间)(查看《标准作业书》是否有漏项,超过一项视为不合格) 基础技能训练场地 技能培训 ILU评价 作业要件一览表多 功能化 1.明确基本技能
业书》) (有《量检具,风枪等标准作
使作业时间最少化 排除差异
有表示作 1.与生产计划相应进行人员配置(编程充实度85% 1.与生产计划相应进行人员配置(编程充实度95%以上) 业充实度的作业配置图 以上)有表示作业充实度的相对应的作业配置图和实施倍率计算或生产 性提高
2.在有作业员休假时,明确代替其工作的人选(见《 2.规定标准的库存数(去现场看,有规定的标准库存)
5.进行防过失工作
对发生问题的地方彻 底进行解决,防过失 系统
1.使正常变得清楚明白(《点检表》中细节内容中是否清楚, 设备点检基准 1.设备启动前进行点检(现场有《点检卡》)
如:点检气压,压力多大标明,不能只写“目视”或是在现场看到在油杯上 划出上、下限的位置,油压表上划出上、下限的位置)
1.对异常进行发现(故障在减小)(《点检表》中记录是否有 1.规定发生异常时的处理方法(有无设备故障处理流程图)
发现异常,异常要注明原因)
1.留有发生异常时的相应记录并实施对策 2.进行目视管理
(看现场:有无特定的标识来表示,如空调上挂 绸布,空调开着绸布就飘起来,这样就知道此时空调是开着的)
防止灾害
2.生产和保养的分担明确(有《设备品质管理表 2.有设备的《点检基准书》及各设备的《点检表 》,表中区分了制造和保全两个部分的分担) 》,按照规定进行确认、记录 (查是否对点检表进行检 自我维护 保养 实施自我维护保养
动保护用具) 查,见《班长日计划》记录或作业观察中留有记录) 否有安全巡查的记录} 》,可以和工厂的3s诊断表并为一张表) 交别个部门做)
精益生产评估表

领 导 力
公司关注客户的需求(通过kpi 反 日映常)精益活动与公司的战略和 目 有标一直个接结相构关化的方法来选择和 跟 公踪司精为益其项精目益项目和活动保留 记 公录司通过多种方式传达其精益 活 定动期和召目开标精益回顾会议,回顾 精 管益理的团成队熟接度受过先进的精益技 术 工培作训团队已经接受了精益基础 和基本精益技术的培训 管理团队经常出现在办公室之 外和工作区域 管理层为员工提供必要的资源 和时间进行精益生产
支经理和主管被视为教练和导师 持对精益绩效指标进行定期跟踪
和 精报益告绩效和目标被共享和清晰 地 客展户示投诉和索赔显示在工作区 域 分析客户投诉的根本原因并确 定 与 与纠关主正键要措客供施户应达商成的合合作作协协议议已经 到 技位能矩阵用于管理和跟踪所有 工 管作理团层队通的过精奖益励技和能激励来授权 工 精作益团是队作参为与一精个益整生体产系统实现 的 定,期而进不行是精孤益立审的计技以术确保持续 改进
价 值 流
当前状态价值流图被标识为主 要 未产来品状(态或被产开品发族出)来,作为未 来 实精施益计活划动到的位指(包导括时间表、里 程 过碑程和所职有责者)被确定并意识到他 们 工的作责团任队理解他们在价值流中 的 过位程置图并和意价识值到流他图们对的所责有任的工 作 工团作队团都队是协可作用维的护和改进过程 图 价,值V流S图Ms用和于SI消PO除Cs浪费和简化 过 管程理层了解当前的瓶颈在哪 里 该,公以司及能如够何在清价除值它流们中有效地 管理其库存
得分 备注
0 Score: 0.0%
持 续 改 进
公司有改善团队或任何其他正 式 改的善改事进件团用队于解决问题并持续 改 改进善价/改值进流记录并公开显示 改善/改进小组定期开会,监督 改进进度 改善/改进团队目前正在进行优 先改进工作 建议和想法在整个操作过程中 被捕获并公开分享 该公司有一个开发和分享最佳 实 它践是的主内动部与论他坛人建立联系,寻 求 实共现同了问跨题类的似解过决程方的案CI横向扩 展 团的队机板会被用来划分问题的优先 级,分享对策和开放讨论
[实用生产表格]精益改善评分标准
![[实用生产表格]精益改善评分标准](https://img.taocdn.com/s3/m/2ea78c5eed630b1c59eeb5c5.png)
提案属于创新,没有模仿借鉴已有成果,具有较好的可 9-10分 行性和效果,提案具有较高的经济效益,可推广和借鉴
提案
1-3分
提案半天内可以完成,无技术难度,劳动强度和资源消 耗极少
4-6分
提案1-2天内可以完成,无技术难度,1-2人就可以实 施,资源消耗很少,各种资源不需要提前准备
备注
可行性
提案一周内可以完成,需要有经验的工作人员负责实 7-9分 施,需要3人~5人协作实施,资源消耗较大,各种资源
13-15分
出,能准确的说明改善提案的各项信息,清楚反应改善 前后的情况对比、改善原因及措施等信息,不需要指导
就可以根据提案申请表水平展开
1-2分 借鉴已有提案的改善思路和方法,水平展开的提案
3-5分
在借鉴已有提案的改善思路和方法的基础上,提案的改 善思路和方法有进一步的提高和改进
提案属于创新,没有模仿借鉴已有成果,具有一定的可 10 6-8分 行性和效果,具有一定无形和有形效果,无水平展开的
需要提前准备
15 提案半个月时间可以完成,需要技术人员指导,并安排
10-12分
有经验的工作人员负责实施,需要多工种、5人以上协 作实施,各种资源需提前作计划准备,且种类、数量很
多
提案一个月时间可以完成,需要技术人员提案制定实施
13-15分
措施,并指导实施,安排有经验的工作人员负责实施, 需要众多工作人员、多工种、多部门协作实施,消耗资
源需提案计划购买或定制,且种类、数量很多
1-5分 节约金额1万元/年以下
6-10分 节约金额1-3万元/年
有形成果
30
11-15分 节约金额3-5万元/年 16-20分 节约金额5-7万元/年
高效生产流程评价表

高效生产流程评价表本评价表旨在对生产流程进行评估,以确定其高效性及潜在优化点。
根据以下指标,评分范围为1到5,其中1表示最低,5表示最高。
请为每个指标选择最符合实际情况的评分。
1. 生产设备利用率- 设备是否得到充分利用?- 设备是否频繁出现故障或维修?- 是否存在设备空置时间较长的情况?评分: _______2. 产能与产量- 是否存在效率低下或闲置导致的产能浪费?- 实际产量是否满足计划产量?- 是否存在过程中的瓶颈点?评分: _______3. 工序排布与物料流动- 工序排布是否合理,便于物料流动?- 是否存在工序之间的物料等待时间过长?- 是否存在物料丢失或混淆的情况?评分: _______4. 人员效率与培训- 是否存在员工的生产效率较低?- 是否定期开展员工培训与技能提升?- 是否存在过多的人力浪费?评分: _______5. 质量控制- 是否存在生产过程中的品质问题?- 是否存在高成本的重工与报废?- 是否存在品质管理失控的情况?评分: _______6. 资源利用与环境保护- 是否存在不必要的资源浪费?- 是否有环境保护措施与管理制度?- 是否存在环境污染或废弃物处理不当?评分: _______7. 信息管理与沟通- 是否存在信息传递不畅或信息丢失的情况?- 是否有及时沟通与协调的机制?- 是否存在信息系统升级或改进的需求?评分: _______总分: _______请根据实际情况进行评分,并在总分处填写综合评分结果。
如有其他补充意见,请在下方提供。
谢谢!。
- 1、下载文档前请自行甄别文档内容的完整性,平台不提供额外的编辑、内容补充、找答案等附加服务。
- 2、"仅部分预览"的文档,不可在线预览部分如存在完整性等问题,可反馈申请退款(可完整预览的文档不适用该条件!)。
- 3、如文档侵犯您的权益,请联系客服反馈,我们会尽快为您处理(人工客服工作时间:9:00-18:30)。
查看生产线的现场物流流转是否存在折流、反流现象?
1.4
设备布局符合安全生产管理要求, 无明显安全缺陷。 优化人力资源配置,严格执行人力 资源配置管理办法,依据人力需求 公式进行动态人员核定,精简配 备,杜绝超员浪费。 线内、线外作业人员科学配备,有 序作业,生产线均衡率达到75%以上 。
1
现场检查生产线设备布置,发线评审表
生产线名称: 序号 考评项目 考评内容 基本分 考评标准 检查人: 项目得分: 检查点 (请做好详细检查记录) 评审分值
一、基本项目100分(10项):完成目标任务,得基本分;未完成,按考评标准评分。 1、是否有针对或者包含本生产线的设备布局图? 2、是否有针对或者包含本生产线的工艺流程图? 设备布局与工艺流程不相符扣1分 3、本生产线的设备布局与工艺流程相符性是否进行过评审论 。 证,有支持文件或者记录? 查阅《工序能力表》,存在明显 4、是否有针对或者包含本生产线的设备作业能力分析、测定的 的设备能力瓶颈扣1分。 相关记录或文件? 5、依据有关作业能力的明细查找是否存在明显的设备能力瓶颈 。 设备布局无有效论证或改善计 划,扣0.5分。 作业观察存 在不合理搬运、走动浪费且无改 善计划的有一处扣0.5分。 1、生产线投产前是否对设备布局进行过合理性论证,有何相关 文件或记录? 2、生产线投产后是否对设备布局进行过改善调整,有何改善方 案或论证材料? 3、现场观察是否存在因设备布局不合理导致的操作者非操作动 作的浪费现象,如果存在是否已经有改善计划?
1、现场观察是否存在因生产线设备布置不合理导致的额外吊装 、转运装配的增加?或者人员越线/穿线走动? 2、现场观察是否有设备自身必要防护的缺失现象?或者存在安 全隐患的部位是否有必要的安全警示标志?
1.5
2
未按产量高低及员工技能熟练度 1、人员配置标准及测算公式(包括根据产量、节拍的分级依 进行人力需求动态核算,扣1分。 据)? 生产线配置人员超过核定人数, 2、人员配备(总数或者各工序人数)是否按此标准执行的? 扣1分。 生产线无人机操作分析记录,扣1 1、有无生产线各工序实际节拍分析,包括(操作时间、辅助时 分。生产线均衡率低于75%,扣1 间、等待时间、设备自动加工时间)? 分。 2、生产线平衡率测算依据,统计和计算结果如何?
1
《作业场所平面定置图》或各类 定置标识设计未能直观反映现场 环境信息,扣 1 分。 《周检查记录表》、《月度检查 记录表》记录内容不完整、未动 态更新,每发现一处扣0.2分。 现场6S问题点未制定整改计划或 未完成整改,分别扣0.5分。 现场作业区域划分、产品摆放、 产品标识及物料存放,存在不符 合管理要求状况,每发现一处扣 0.5 分。 检查存在跑、冒、滴、漏等现 象,每发现一处扣0.2分。 危险化学品包装物未及时退库, 扣0.5 分。 目视化检查现场环境保护措施, 发现一处不合格,扣0.2分 无管理标准优化、改进的相关记 录,扣1 分。
1.7
1
作业观察发现操作者存在明显的 动作浪费,有一处扣0.5分。
现场观察作业人员在正常作业过程中,是否存在动作浪费(不 包括非正常的作业移动)?
2.1
2
《6S管理办法》缺失,扣1分。 《6S评审标准》缺失,扣1分。
1、是否有《6S管理办法》或者同效内容的文件? 2、是否有《6S评审标准》或者同效的评审标准及细则?
2.2
依据现场实际,建立6S管理推进体 系,有6S管理工作计划并按进度开 展。
1
未建立日常推进体系,扣0.2分。 1、是否明确规定6S管理推进机构、责任人及检查主体? 6S管理工作计划缺失,扣0.3分。 2、是否有月度的6S工作计划及工作记录? 随机抽取月度计划,未按进度完 3、是否抽查的记录能够证明各项工作计划均已完成? 成,扣0.5 分 1、是否有针对或者覆盖本生产线的现场6S定置图及定置标准规 定?(标准内容应涵盖2.5条要求) 2、生产线现场是否按定置要求执行,并配有必要的目视化标 识? 1、是否有针对、涵盖本生产线的6S检查记录(包括周检查、月 度检查项目)及月度检查分值? 2、针对检查的发现的缺陷是否提出整改要求并且现场按要求及 时完成?
1.1
按照精益化管理原理,优化设备布 局,设备布局与工艺流程相符,设 备作业能力合理配备。
2
1.2
设备布局有完整论证方案或改善计 划,布局间距合理,减少产品和操 作者的移动距离。
1
1
设备布 局及人 力资源 配置优 化
1.3
设备之间物料流转顺畅,物流无交 叉、迂回、折流、返流等状况。
1
现场物流流转存在折流、返流现 象,有一处扣 0.5 分。
2.3
根据6S管理需要,合理进行作业现 场定置图设计和信息媒介物设计。 严格6S执行检查,依据《6S评审标 准》每日进行现场巡查,每周不定 岗位抽查,每月综合检查,查找现 场问题点并制定整改计划,确保整 改完成率达到100%。 现场6S管理活动有效开展,作业区 域合理划分;工具、材料、半成品 、成品等各类物资三定管理(定物 、定置、定量);产品标识及状态 标识明晰;现场整齐、清洁、安全 、有序。 现场环境保护措施有效运行,生产 过程中不存在跑冒滴漏现象,危险 化学品包装物及时退库,安全处理 和防护措施有效。 6S管理标准优化、改进,并有效实 施。
1.6
2
精益化管理生产线评审表
生产线名称: 序号 考评项目 考评内容 员工作业符合“动作经济”原则, 站立走动作业,减少弯腰、伸展、 停顿等动作浪费。 有明确的《6S管理办法》、《6S评 审标准》等现场管理制度及标准。 基本分 考评标准 检查人: 项目得分: 检查点 (请做好详细检查记录) 评审分值
2
6S及现 场环境 管理
2.4
2
2.5
2
同2.3,将2.3明确。
2.6
1
1、是否有明确针对或者覆盖本生产线的生产现场环境保护要 求,是否存在跑、冒、滴、漏等影响现场环境的现象? 2、现场危险化学品是否按要求妥善管理? 3、目视化检查现场环境的保护措施是否有效? 1、是否有过6S管理标准的优化和改进记录? 2、优化、改进后的管理标准是否得到有效实施?