压力管道焊接工艺卡[优质文档]
工艺管道焊接方案及工艺工艺卡
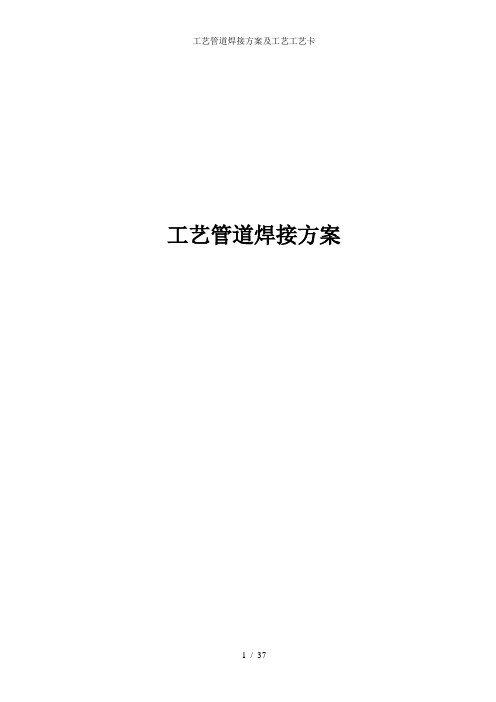
工艺管道焊接方案目录1、概述 (3)2、编制依据及验收规范 (3)3、施工准备 (3)4、焊接施工工序 (5)5、施工技术要求 (7)6、焊后热处理 (14)7、质量检查 (17)8、焊缝返修 (19)9、焊接质量保证体系 (20)10、安全施工技术要求 (23)11、工艺管道施工工作危害分析(JHA)记录 (25)12、管道焊接材料选用及工艺要求表 (28)13、管道焊接焊接工艺评定一览表 (28)14、工艺工艺卡 (29)1、概述1.1工程概况化工厂的工艺管道焊接,管道材质有碳钢、不锈钢及铬钼合金钢,该装置工艺管道全部采用工厂化预制加工,现场分段安装。
管道焊接的主要工程量见表1。
管道焊接工程量表12、编制依据及验收规范2.1《工业管道工程施工及验收规范》 GB50235-97 2.2《现场设备工业管道焊接施工及验收规范》 GB50236-98 2.3《石油化工剧毒、可燃介质管道工程施工及验收规范》及一号增补 SH3501-2002 2.4《石油化工工程铬钼耐热钢管道焊接技术规程》 SH/T3520-2004 2.5《石油化工铬镍奥氏体钢、铁镍合金和镍合金管道焊接规程》SH/T3523-1999 2.4《石油化工不锈钢复合钢焊接规程》 SH/T3527-1999 2.6《石油化工建设工程项目交工技术文件规定》 SH/T 3503—20072.7《工艺管道》 ASME B31.33、施工准备3.1人员准备3.1.1焊工担任管道焊接的焊工必须经过焊接基本知识和实际操作技能的培训,并取得相应的锅炉压力容器压力管道焊工考试合格证及经并经项目质量部考试合格,具备颁发的焊工上岗证,才能进入施工现场焊接作业;施焊前应参加焊接方案的技术交底,掌握本项目焊接工艺的技术要点、难点,严格遵守工艺纪律;相应的焊工合格项目见焊接工艺卡。
3.2焊接检验人员要求3.2.1从事焊接质量检验的人员应具有一定的实践经验和技术水平。
压力管道焊接工艺规程完整

压力管道焊接工艺规程1 合用范围本规程合用于工业管道或公用管道中材质为碳素钢、低合金钢、耐热钢、不锈钢和异种钢等压力管道的焊条电弧焊、钨极氩弧焊以及二氧化碳气体保护焊的焊接施工。
2 重要编制依据2.1 GB50236-2023《现场设备、工业管道焊接工程施工及验收规范》;2.2 GB/T20801-2023《压力管道规范-工业管道》;2.3 SH3501-2023《石油化工剧毒、可燃介质管道工程施工及验收规范》;2.4 GB50235-2023《工业金属管道工程施工及验收规范》;2.5 CJJ28-2023《城市供热管网工程施工及验收规范》;2.6 CJJ33-2023 《城乡燃气输配工程施工及验收规范》;2.7 GB/T5117-2023 《碳钢焊条》;2.8 GB/T5118-2023 《热强钢焊条》;2.9 GB/T983-2023 《不锈钢焊条》;2.10 YB/T5092-2023《焊接用不锈钢丝》;2.11 GB14957-1994《焊接用钢丝》;2.12 其他现行有关标准、规范、技术文献。
3 施工准备3.1 技术准备3.1.1 3.2 对材料的规定3.4 焊接人员3.4.2 3.5 施焊环境4.1 压力管道焊接施工流程图(见图1 )图1 焊 接 施 工 流 程 图 4.2 焊前准备及接头组对4.2.1 4.2.2 b )异种钢管子焊接时, 焊条或焊丝的选用一般应符合下列规定: 表1 常用钢号推荐选用的焊接材料焊前准备焊机性能确认 焊口组对质量评估正式施焊 焊接检查焊缝无损探伤结果评估焊后热解决硬度测试水压实验焊接坡口制备及清理 焊条烘干及焊丝清理焊缝外观检查是表2 不同钢号相焊推荐选用的焊接材料表3 常用钢号分类分组4.2.4 a)按SH3501-2023《石油化工剧毒、可燃介质管道工程施工及验收规范》分为SHA级的压力管道、中高合金钢及不锈钢管道的坡口应采用机械方法加工。
b)其他管道坡口宜采用机械方法加工, 当采用热加工方法时, 切割后必须去除影响焊接质量的表面层。
压力管道焊接作业指导书
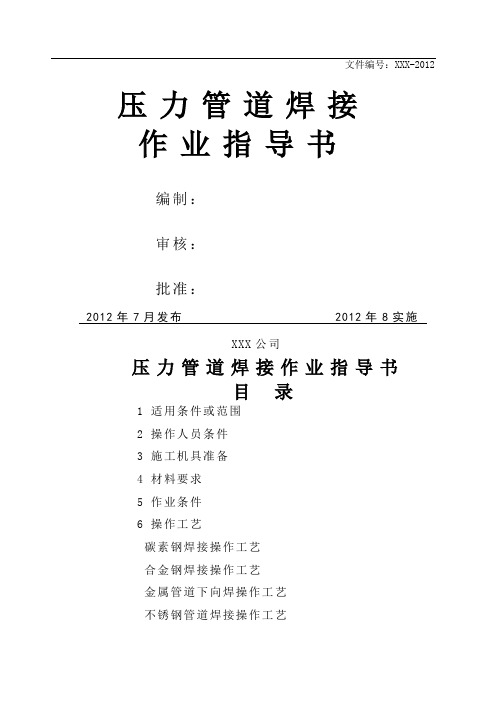
文件编号:XXX-2012压力管道焊接作业指导书编制:审核:批准:2012年7月发布2012年8实施XXX公司压力管道焊接作业指导书目录1 适用条件或范围2 操作人员条件3 施工机具准备4 材料要求5 作业条件6 操作工艺碳素钢焊接操作工艺合金钢焊接操作工艺金属管道下向焊操作工艺不锈钢管道焊接操作工艺有色金属焊接操作工艺钢塑复合管的焊接操作工艺7 焊接操作质量控制8 焊接安全操作注意事项9 支持性相关文件和资料1 适用条件或范围本作业指导书适用于本公司承接的各种压力容器、压力管道安装焊接;2 操作人员条件压力容器、压力管道安装焊工应受过操作技能、工作质量和施工安全的培训,并持有相应等级的焊工合格证,焊接热处理人员应经专业培训;3 施工机具准备施工机械设备:交流电弧焊机、直流电弧焊机、钨极氩弧焊机、二氧化碳气体保护焊机、埋弧自动焊机、内外对口器、电容焊机、手提砂轮坡口机、焊条烘干箱、焊条保温箱;工具和用具:焊枪、焊钳、焊炬、割炬、保温筒、錾子、扁铲、钢锉、钢锯、封头机架、内外对口器、加热板、电加热片、管材、管件固定机架以及面罩、护目镜、绝缘手套、绝缘鞋等焊接防护用具;量具:焊缝检验尺、角尺、钢板尺、钢卷尺、游标卡尺;检验和试验设备:X射线探伤机、光谱仪、测厚仪、超声波探伤仪、点温计、表面温度计、万用表、钳形电流表,各种力学性能试验机、电动试压泵;4材料要求4.1 焊接材料应符合设计文件的规定;焊接材料应符合现行国家焊接材料标准;4.2.1 焊条应符合以下标准碳钢焊条GB/T5117、低合金钢焊条GB/T5118、不锈钢焊条GB/T983、铝及铝合金焊条GB/T3669、铜及铜合金焊条GB/T3670;4.2.2 焊丝应符合以下标准气体保护电弧焊用碳钢、低合金钢焊丝GB/T8110、焊接用不锈钢丝YB/T5092、铝及铝合金钢丝GB/T10858、铜及铜合金焊丝GB/T9460;焊接材料应按相关标准的规定进行检验和验收;焊接材料必须具有制造厂的质量证明书;现场具有焊接材料储存场所及烘干、去污设施,并应建立保管、烘干、清洗、发放制度;氩气应符合现行国家标准氩GB/T4842的规定,且纯度不应低于%钨极宜采用铈钨极或钍钨极;二氧化碳气体的纯度不应低于%,含水量不应超过%,使用前应预热或干燥;当瓶内气体压力低于时,应停止使用;氧乙炔焊所采用的氧气纯度不应低于%,乙炔气应符合现行国家标准溶解乙炔GB6819的规定;5 作业条件施工项目部已配备专业焊接技术人员、焊接检验人员、无损探伤人员;焊接工装设备、检验实验手段能满足工程项目的技术要求;已进行相应的焊接工艺评定;施焊环境符合GB50236规定;6 操作工艺碳素钢焊接操作工艺6.1.1 本工艺适合于含碳量小于或等于%的碳素钢的现场手工电弧焊、氩弧焊、二氧化碳气体保护焊、埋弧焊及氧乙炔焊;6.1.2 焊缝的设置应避开应力集中区,便于焊接和热处理,并应符合下列规定:6.1.2.1 组对时,相邻两纵向焊缝间的距离应大于壁厚的3倍,且不应小于100mm;加热炉受热面管子的焊缝中心与管子弯曲起点,联箱外壁及支、吊架边缘的距离不应小于70mm;同一直管段上两个对接焊缝间的距离不应小于150mm;6.1.2.3 除焊接及成型管件的其他管子对接焊缝的中心到管子弯曲起点距离不应小于管子外径,且不应小于100mm;管子对接焊缝与支、吊架边缘之间的距离不应小于50mm;同一直管段上两对接焊缝中心面间的距离;当公称直径大于或等于150mm时不应小于150mm;公称直径小于150mm时不应小于管子外径;6.1.2.4 不宜在焊缝及其边缘上开孔,当不可避免时,应符合GB50236的规定;6.1.2.5 焊缝的坡口形式和尺寸应符合设计文件和焊接工艺文件的规定;当没有特别规定时,埋弧焊焊缝坡口形式及尺寸应符合埋弧焊的推荐坡口规定,其他焊缝坡口形式和尺寸应符合气焊、焊条电弧焊、气体保护焊和高能束焊的推荐坡口的规定;6.1.3 焊前准备6.1.3.1 焊件的切割和坡口加工宜采用机械方法,也可采用气割等热加工方法,在采用热切割方法加工坡口后,必须除去坡口表面的氧化皮,溶渣及影响接头质量的表面层,并应将凹凸不平处打磨平整;6.1.3.2 焊件组对前应将坡口及其内外侧表面不小于10mm范围内油、漆、垢、锈、毛刺及镀锌层清除干净,且不得有裂纹、夹层等缺陷;6.1.3.3 除设计规定需要进行冷拉伸或冷压缩的管道外,焊件不得进行强行组对;管子或管件对接焊缝进行组时,内壁应齐平,内壁错边量不宜超过管壁厚度的10%,且不应大于2mm;6.1.3.5 不等厚对接焊件组对时,薄件端面应位于厚件端面之内;当内壁错边量超过;条规定或外壁错边量大于3mm时,应对焊件按GB50236现场设备、工业管道焊接工程施工及验收规范进行加工;6.1.4 焊接工艺要求6.1.4.1 焊材选用,应按照母材的化学成分、力学性能、焊接接头的抗裂性,焊前预热、焊后的热处理、使用条件及施工条件等因素综合确定,且焊接工艺性能良好;6.1.4.2 定位焊接缝应符合下列规定:a.焊接定位焊缝时,应采用与根部焊接道相同的焊接材料和焊接工艺,并应由合格焊工施焊;b.定位焊缝的长度、厚度和间距,应能保证焊缝在正式焊接过程中不致开裂;c.在焊接根部焊道时,应对定位焊缝进行检查,当发现缺陷时应处理后方可施焊;d.与母材焊接的工卡具其材质宜与母材相同或同一类别号;拆除工卡具时不应损伤母材,拆除后应将残留焊疤打磨修理至与母材表面齐平;6.1.4.3 严禁在坡口之外的母材表面引弧和试验电流,并应防止电弧擦伤母材;6.1.4.4 焊接时应采取合理的施焊方法和施焊顺序;6.1.4.5 施焊过程中应保证起弧和收弧处的质量,收弧时应将弧坑填满;多层焊的层间接头应错开,管子施焊时,管内施焊时应防止穿堂风;6.1.4.6 除工艺或检验要求需分次焊接外,每条焊缝宜一次连续焊完,当因故中断焊接时,应根据工艺要求采取保温缓冷或后热等防止产生裂纹的措施,再次焊接前,应检查焊层表面确认无裂纹后,方可按原工艺要求继续施焊;6.1.4.7 需预拉伸或预压缩的管道焊缝,组对时所使用的工卡具在整个焊接及热处理完毕并经检验合格后方可拆除;6.1.5 焊前预热及焊后热处理6.1.5.1 碳素钢焊接时,一般不采用焊前预热及焊后热处理,只在下述情况时才进行预热及焊后热处理;6.1.5.2 当焊件温度低于0℃时,钢材的焊缝应在始焊处100mm范围内预热到15℃以上;6.1.5.3 对有应力腐蚀的焊缝,应进行焊后热处理;6.1.5.4 焊前预热的加热范围,应以焊缝中心为基准,每侧不应小于焊件厚度的3倍;焊后热处理的加热范围,每侧应不小于焊缝宽度的3倍,加热带以外部分应进行保温;6.1.5.5 焊前预热及焊后热处理中,焊件内外壁温度应均匀;6.1.5.6 焊前预热及焊后热处理时,测量和记录温度的部位和数量应合理,测温仪表应经计量检验合格;6.1.5.7 焊前的预热和后热处理温度应符合设计要求或焊接工艺文件的规定,当无规定时,碳素钢的焊前预热及焊后热处理温度宜符合表1的规定;碳素钢管材焊前预热及焊后热处理工艺条件表1合金钢焊接操作工艺6.2.1 适用范围:本工艺适用于低合金结构钢、低温钢、耐热钢、耐热耐蚀高合金等合金钢的手工电弧焊、氩弧焊、二氧化碳气体保护焊、埋弧焊及氧乙块焊;6.2.2 焊缝的设置应避开应力集中区,便于焊接和后热处理,并应符合、、、、的规定;6.2.3 焊前准备合金钢的焊接前的准备工作与6.1.3的要求相同;6.2.4 焊接工艺要求6.2.4.1 焊材选用应按照母材的化学成分、力学性能、焊接接头的抗裂性、焊前预热、焊后热处理、使用条件及施工条件等因素综合确定,且焊接工艺性能应良好;6.2.4.2 定位焊缝应符合的规定;6.2.4.3 严禁在坡口之外的母材表面引弧或试验电流,并应防止电弧擦伤母材;6.2.4.4 对含铬量大于或等于30%或合金元素总含量大于5%的焊件,氩弧焊打底焊接时,焊缝内侧应充氩气或其他保护气体,或采取其他防止内侧焊缝金属被氧化的措施;6.2.4.5 焊接时应采取合理的施焊方法和施焊顺序;6.2.4.6 施焊过程中应保证起弧和收弧的质量,收弧时应将弧坑填满,多层焊的层间接头应错开;管子施焊时,管内应防止穿堂风;6.2.4.7 除工艺或检验要求需分次焊接外,每条焊缝宜一次连续焊完,当因故中断焊接时,应根据工艺要求采取保温缓冷或后热等防止产生裂纹的措施,再次焊接前应检查焊层表面,确认无裂纹后,方可按原工艺要求继续施焊;6.2.4.8 低温钢、耐热耐蚀高合金钢接头焊接时,应符合下列规定:a.应在焊接作业指导书规定的范围内,在保证焊透和熔合良好的条件下,采用小电流、短电弧、快速焊接多层多道焊工艺,并应控制层间温度;b.对抗腐蚀性能要求高的双面焊缝,与腐蚀介质接触的焊层应最后施焊;c.低温钢焊接完毕,宜对焊缝进行表面焊道退火处理;6.2.5 焊前预热及焊后热处理;6.2.5.1 进行焊前预热及焊后热处理应根据钢材的淬硬性、焊件厚度、结构刚性、焊接方法及使用条件等因素综合确定;6.2.5.2 要求焊前预热的焊件,其层间温度应在规定的预热温度范围内;6.2.5.3 当焊件温度底于0℃时,所有钢材的焊缝应在始焊处100mm范围内预热到10℃以上;6.2.5.4 对有应力腐蚀的焊缝,应进行焊后热处理;6.2.5.5 调质钢焊缝的焊后热处理温度,应低于其回火温度;6.2.5.6 焊前预热的加热范围,应以焊缝中心为基准,每侧不应小于焊件厚度的3倍;焊后热处理的加热范围,每侧不应小于焊缝宽度的3倍,加热带以外部分应进行保温;6.2.5.7 焊前预热及焊后热处理中,焊件内外壁温度应均匀;6.2.5.8焊前预热及焊后热处理时,应测量和记录其温度,测温点的部位和数量应合理,测温仪表应经计量检定合格;6.2.5.9 对容易产生焊接延迟裂纹的钢材,焊后应及时进行焊后热处理,当不能及时进行焊后热处理时,应在焊后立即均匀加热到200~300℃,并进行保温缓冷,其加热范围应与焊后热处理要求相同;6.2.5.10 焊前预热及焊后热处理温度应符合设计或焊接工艺文件的规定,当无规定时,常用管材焊接的焊前预热及焊后热处理温度宜符合表2的规定;常用合金钢焊前预热及焊后热处理工艺条件表2焊后热处理的加热速率、热处理温度下的恒温时间及冷却速率应符合GB50236的规定;6.2.5.13 对热处理后进行返修的焊缝,返修后应重新进行热处理;金属管道全位置下向焊工艺6.3.1 本工艺适合于大直径低碳钢、低合金钢管道的全位置下向焊;6.3.2 用于下向焊的纤维素型焊条因药皮含有大量有机物,应妥善保管以防受潮;焊条一旦受潮应在70℃~80℃下烘烤~小时,烘烤温度最多不能超过100℃;烘烤次数不能超过2次;低氢型下向焊条则应按产品说明书要求严格烘干;6.3.3 焊前应将坡口两侧50mm范围内的油、锈、水等杂质清除干净;按设计要求或表3的规定进行焊口组对;下向焊管口组对尺寸表36.3.5 管径≥400mm的管道,采取二人对称焊法;管径≥700mm的管道;采取三人对称焊法;6.3.6 焊条运条角度可按表4选取表中12点、3点等指钟点位置;焊条运条角度表4,均匀快速向下运条,力争短时间内完成打底;6.3.8 热焊和填充焊须在打底焊道打磨和清理之后进行,各层焊道之间的间隔不应超过5分钟,否则应将层间温度加至预热温度,每层焊道的平焊接头处都要进行打磨,各层接头错开20~30mm,每层焊肉厚度掌握在~之间;6.3.9 盖面焊道应比坡口每边增宽~,运条可采用小锯齿摆动,当母材厚度≥12mm时,采用双焊道盖面成型;焊道层数按表5选取;不同壁厚的焊道层数表5同一焊缝的返修次数不能超过两次,返修时的预热温度比正式施焊的预热温度要高10°~20°,返修长度不小于50mm,采用多层多道焊,并采取缓冷措施;带裂纹性质缺陷的焊口一般从管线上切除;不锈钢管道焊接操作工艺6.4.1 本章节适用于各种不锈钢现场焊接管道的手工电弧焊、氩弧焊;6.4.2 焊缝的设置应避开应力集中区,便于焊接和热处理,并应符合,,,条的规定;6.4.3 焊接的坡口形式和尺寸应符合设计文件和焊接工艺文件的规定;当无规定时,焊缝坡口的形式和尺寸应符合GB50236附录C第条的规定;6.4.4 焊前准备6.4.4.1 不锈钢管子焊件的切割和坡口加工宜采用等离子弧热加工方法,热加工方法加工坡口后,必须清除坡口表面的氧化皮、熔渣及影响接头质量的表面层,且应将凸凹不平处打磨整齐;6.4.4.2 焊件组对前应将坡口及其内外侧表面不小于10mm范围内的油、漆、垢、毛刺等清除干净,且不得有裂纹夹层等缺陷;6.4.4.3 不锈钢焊件坡口两侧各100mm范围内,在施焊前应采取防止焊接飞溅物污染焊件表面的措施;6.4.4.4 管子或管件对接焊缝组对时,内壁应齐平,内壁错边量不宜超过管壁厚度的10%,且不应大于2mm;6.4.4.5 除设计规定需进行冷拉伸或冷压缩的管道外,焊件不得进行强行组对;6.4.4.6 不等厚对接焊件组对时,当内壁错边量超过条规定或外壁错边量大于3mm时,应对焊件按现场设备、工业管道焊接工程施工规范GB50236进行加工;下向焊条的焊接规范表66.4.5.1 焊条、焊丝的选用,应按照母材的化学成分、力学性能、使用条件及施工条件等因素综合确定,且焊接工艺性能应良好;6.4.5.2 严禁在坡口之外的母材表面引弧和试验电流,并应防止电弧擦伤母材;6.4.5.3 氩弧焊接时,焊缝内侧应充氩气保护,或采取其他防止内侧焊缝金属被氧化的措施;6.4.5.4 焊接时应采取合理的施焊方法和施焊顺序;6.4.5.5 奥氏体不锈钢、奥氏体不锈钢与非奥氏体异种钢接头焊接时应符合下列规定:a.应在焊接工艺文件规定的范围内,在保证焊透和熔合良好的条件下,采用小电流、短电弧、快速焊和多层多道焊工艺,并应控制层间温度;b.对抗腐蚀性能要求高的双面焊焊缝,与腐蚀介质接触的焊层应最后施焊;6.4.5.6 根据设计规定应对奥氏体不锈钢焊缝及其附近表面进行酸洗、纯化处理;有色金属管道焊接操作工艺6.5.1 铝及铝金属的焊接6.5.1.1 本节适应于工业纯铝及铝金属管道的手工钨极氩弧焊和熔化极氩弧焊;6.5.1.2 焊前准备a.焊丝选用应综合考虑母材的化学成分、力学性能和使用等因素,并应符合下列规定:1 纯铝焊接时,应选用纯度与母材相近的焊丝;2铝镁金属焊接时,应选用含镁量等于或略高于母材的焊丝;3铝锰金属焊接时,应选用与母材成分相近的焊丝或铝硅金属焊丝;4异种铝合金焊接时,应选用与抗拉强度较高一侧的母材相近的焊丝;5铝及铝合金焊接时,焊丝选用应符合GB50236附录D的规定,也可用母材切条作填充金属;b.焊件坡口制备应符合下列规定:1 坡口形式和尺寸应符合设计要求和焊接工艺文件的规定,当无规定时,应符合GB50236附录C的规定;2坡口加工应采用机械方法或等离子弧切割,切割后的坡口坡表面应进行清理,并应达到平整光滑、无毛刺和飞边;c.焊前清理应符合下列规定:1 施焊前应对焊件坡口、垫板及焊丝进行清理;清理方法如下:首先用丙酮或四氯化碳等有机溶剂去除表面油污,两侧坡口的清理范围不应小于50mm;清除油污后,坡口及其附近的表面可用锉削、刮削、铣削或用不锈钢丝刷清理至露出金属光泽,使用的钢丝刷应定期进行脱脂处理;2焊丝去除油污后,应采取化学方法去除氧化膜;可用5%~10%的NaOH溶液,在温度为70℃下浸泡30~60分钟,然后用温水洗净,并使之干燥;同时清理好的焊件和焊丝不得有水迹、碱迹或被沾污;d.焊件组对应符合下列规定:1 焊接定位焊缝时,采用与正式焊接相同的焊丝和焊接工艺,由合格焊工施焊;2 管道定位焊缝尺寸应符合表7规定;管道定位焊缝尺寸mm 表7膜应清理干净,并应将其两端修整成缓坡形;4 拆除定位板时,不应损伤母材,应将拆除后残留的焊疤打磨至与母材表面齐平;e、当焊缝背面需加永久性垫板时,垫板材质应符合设计规定;当无设计规定时,垫板材质应与母材相同,垫板上应开有容纳焊缝根部的沟槽;当焊缝背面需加临时垫板时,垫板应用对焊缝质量无不良影响的材质;f、管道的对接焊缝内壁应齐平,内壁错边量应符合下列规定:1当壁厚δ≤5mm时,内壁错边量不应大于;2当壁厚δ>5mm时,内壁错边量不应大于δ且不应大于2mm;g、不等厚对接焊件组对时,薄件端面应位于厚件端面之内;当表面错边量超过3mm或内壁错边量大于2mm时,应按第6.1.3.5条的规定,对焊件进行加工;6.5.1.3 焊接工艺要求a. 手工钨极氩弧焊采用交流电源,熔化极氩弧焊采用直流电源,焊丝接正极;b.焊接前焊件表面应保持干燥,无特殊要求时可不预热;c. 焊接前应在试板上试焊,当确认无气孔后再进行正式焊接;d. 宜采用大电流快速施焊法,焊丝的横向摆动不宜超过其直径的3倍;e. 引弧宜在引弧板上进行,纵向焊缝宜在熄弧板上熄弧;引弧板和熄弧板的材料应与母材相同;f. 手工钨极氩弧焊的焊丝端部不应离开氩气保护区,焊丝与焊缝表面的夹角15o,焊枪与焊缝表面的夹角为80o~90o;g. 多层焊时宜减少焊接层数,层间温度宜冷却至室温,且不应高于65℃;层间的氧化铝等杂物应采用机械方法清理干净;h. 对厚度大于5mm的立向焊缝,宜采用两人双面同步施焊工艺;i. 当钨极氩弧焊的钨极前端出现损耗或形状不规则时,应进行修正或更换钨极;当焊缝出现触钨现象时,应将钨极、焊丝、熔池处理干净后方可继续进行施焊;j.当熔化极氩弧焊发生导电嘴、喷嘴熔入焊缝时,应将该部位焊缝全部铲除,更换导电嘴和喷嘴后方可继续施焊;k.手工钨极氩弧焊和熔化极氩弧焊的焊接工艺参数宜符合表8、表9、表10规定;手工钨极氩弧焊工艺参数表86.5.1.4焊件应采用下列防止变形措施:1 对易产生磁偏吹的焊缝,组对时使用工夹具应采用非磁性材料;2焊接顺序应对称进行,当从中心向外进行焊接时,具有大收缩量的焊缝宜先施焊,整条焊缝应连续焊完;3不等厚度对接焊件焊接时,应采取强拘束措施,防止对应于焊缝中心线的应力不均匀; 4焊件宜进行刚性固定或采取反变形方法,并应留有收缩余量;6.5.2 铜及铜合金的焊接;6.5.2.1 本节适用于紫铜管道的手工钨极氩弧焊及黄铜管道的氧乙炔焊接;6.5.2.2 焊前准备:a.紫铜焊接应选用含有脱氧元素,抗裂性好的焊丝;b.黄铜焊接应选用合锌量少、抗裂性好的焊丝;c.焊件坡口制备应符合下列规定:1 焊件坡口形式和尺寸应符合设计要求和焊接工艺文件的规定,当无规定时,宜符合GB50236规范附录C第条的规定;2紫铜及黄铜的切割和坡口加工应采用机械方法或等离子弧切割;d.焊件坡口及两侧小于20mm范围内的表面及焊丝,应采用丙酮或四氯化碳等有机溶剂去油污,并应采用机械方法或化学方法清除氧化膜等污物,使之呈现出金属光泽;当采用化学方法时,可用30%硝酸溶液浸蚀2~3mm,用水洗净并干燥;e.焊件的组对应符合下列规定:1 管道对接焊缝组对应内壁齐平,内壁错边量不应超过管壁厚度的10%,且不大于2mm;2 不等厚对接焊件组对时,当错边量大于3mm或管管道焊缝单面错边量大于2mm时,应按6.3.5条的规定对焊件进行加工;6.5.2.3 焊接工艺要求a.焊接定位焊缝时,应采用与正式焊接要求相同的焊接材料及焊接工艺,并应由合格焊工施焊;当发现定位焊缝有裂纹、气孔等缺陷时应清除重焊;b..铜管焊接位置宜采用转动焊,每条焊缝应一次性连续焊完,不得中断;c.紫铜钨极氩弧焊应符合下列规定:1 焊拉时应采用直流电源,母材接正极;2 焊前应检查坡口质量,不应有裂纹、分层、夹渣等缺陷,当发现缺陷时,应修磨或重新加工;3 焊前应将铜焊剂用无水酒清调成糊状涂敷在坡口或焊丝表面,应及时施焊;4 当焊件壁厚大于3mm时,焊前应对坡口两侧150mm范围内进行均匀预热,预热温度为350~550℃;5 当焊接过程中发生触钨时,应将钨极、焊接熔池处理干净后,方可继续施焊;6进行预热或多层焊时,应及时去除焊件表面及层间的氧化层,焊缝层间温度应控制在300~400℃;d.黄铜氧乙炔焊应符合下列规定:1 宜采用微氧化火焰和左焊法施焊;2 施焊前应对坡口两侧150mm范围内进行均匀预热,当板厚为5~15mm时,预热温度应为400~500℃,当板厚δ≥15mm时,预热温度应为500~550℃时;3 施焊前焊丝应加热,并蘸上焊剂;4 宜采用单层单道焊,当采用多层多道焊时,除底层采用细焊丝外,其他各层宜采用较粗焊丝,以减少焊接层数;各层表面熔渣应清除干净,接头应错开;5 异种黄铜焊接时,火焰应偏向熔点较高的母材侧,以确保两侧母材熔合良好;f.黄铜焊后热处理应符合下列规定:1 黄铜焊后进行热处理,热处理焊件前应采取防变形的措施;热处理加热范围以焊缝中心为基准,每侧不应小于焊缝宽度的3倍:2热处理温度应符合设计要求和焊接工艺文件规定,当夫规定时,可按下列常规的热处理温度进行:①消除焊接应力退火的热处理温度应为400~450℃;②软化退火的热处理温度应为500~600℃;3对热处理后进行返修的焊缝,返修后应重新进行热处理;钢塑复合管的焊接操作工艺6.6.1 用钢锯对管材下料,准确扣除封头环长度;6.6.2 对下好的管材待接端头进行封头;6.6.2.1 将锯好的管材固定在封头机架的固定块上,用车削机切削管材端面直至露出钢带的冲孔中心;6.6.2.2 将封头环在封头机架的滑动块上固定好并擦拭干净,同时将固定块上的管材端头也擦拭干净;6.6.2.3 将加热板架在封头机架上的固定块和滑动块中间,摇动滑动块手柄,使封头环和待接管材端头在加热板两侧按工艺要求加热;6.6.2.4 加热完毕后去处加热板并迅速摇动滑动块手柄并施加一定压力,使加热板两侧已经热熔的断面充分熔接在一起,并按工艺要求保持一段时间直至冷却;6.6.2.5 待熔接处充分冷却后,用钻床或简易铣刀切削封头环与管端熔接处,使其内壁及外沿光滑,并将封头环车削至3~6mm厚大管取上限,小管取下限;6.6.2.6 将封好的管材装入包装袋以保持封端清洁;6.6.2.7钢塑复合管封头工艺参数见表11;钢塑复合管封头工艺参数表116.6.3.1 清理干净管材及管件的端头;6.6.3.2 根据不同情况,可采用横式或纵式焊接,横式焊接的管材须保持水平、不摇动;纵式焊接须用管夹固定管材进行焊接;6.6.3.3 将封好头的钢塑复合管插入电热熔管件中,调节管件两端管材的位置并作适当的固定,将焊接电极插入管件两端的电极上,调节焊接参数,通电进行加热焊接,并保持管材、管件固定不动直至焊缝冷却;管材与管件焊接工艺参数表12。
焊接工艺评定及焊接工艺卡编写讲义

焊接工艺评定的一般要求
1母材 项目根据焊接工程需要委托本企业进行焊接工艺 2焊材 评定时,提供的母材,应符合设计文件和国家现 焊接工艺评定所用的焊条、焊丝、焊剂应具有出 3程序 行有关标准的规定,且有出厂质量证明书或复验 厂质量证明书。焊接用气体应符合现行有关标准 4签发报告 企业完成焊接工艺评定过程:拟定焊接工艺指导 报告。 。 的规定 书、试焊试件和制取试样、检验试件和试样、测 由企业焊接责任工程师审核,技术负责人签发。 定焊接接头是否具有所要求的使用性能、提出焊 用于压力容器产品的焊接工艺评定报告,并经所 接工艺评定报告。 在地技术监督部门确认。存入技术档案。
• 单位焊接责任工程师审核,技术负责人批准, 单位焊接责任工程师审核,技术负责人批准,并且经过监检机构签章确认后存入技术 档案。 的规定。 档案。 的规定。 (五)焊接工艺评定技术档案应当保存至该工艺评定失效为止,焊接工艺评定试样应当 焊接工艺评定技术档案应当保存至该工艺评定失效为止, 五 焊接工艺评定技术档案应当保存至该工艺评定失效为止 保存5年 保存 年。
常用标准规范对焊接工艺评定报告的要求
压力管道焊接工艺规程完整

压力管道焊接工艺规程1 适用范围本规程适用于工业管道或公用管道中材质为碳素钢、低合金钢、耐热钢、不锈钢和异种钢等压力管道的焊条电弧焊、钨极氩弧焊以及二氧化碳气体保护焊的焊接施工。
2 主要编制依据2.1 GB50236-2011《现场设备、工业管道焊接工程施工及验收规范》;2.2 GB/T20801-2006《压力管道规范-工业管道》;2.3 SH3501-2011《石油化工剧毒、可燃介质管道工程施工及验收规范》;2.4 GB50235-2010《工业金属管道工程施工及验收规范》;2.5 CJJ28-2014《城市供热管网工程施工及验收规范》;2.6 CJJ33-2005 《城镇燃气输配工程施工及验收规范》;2.7 GB/T5117-2012 《碳钢焊条》;2.8 GB/T5118-2012 《热强钢焊条》;2.9 GB/T983-2012 《不锈钢焊条》;2.10 YB/T5092-2005《焊接用不锈钢丝》;2.11 GB14957-1994《焊接用钢丝》;2.12 其他现行有关标准、规范、技术文件。
3 施工准备3.1 技术准备3.1.1 压力管道焊接施工前,应依据设计文件及其引用的标准、规范,并依据我公司焊接工艺评定报告编制出焊接工艺技术文件(焊接工艺卡或作业指导书)。
如果属本公司首次焊接的钢种,则首先要制定焊接工艺评定指导书,然后对该种材料进行工艺评定试验,合格后做出焊接工艺评定报告。
3.1.2 编制的焊接工艺技术文件(焊接工艺卡或作业指导书)必须针对工程实际,详细写明管道的设计材质、选用的焊接方法、焊接材料、接头型式、具体的焊接施工工艺、焊缝的质量要求、检验要求及焊后热处理工艺(有要求时)等。
3.1.3 压力管道施焊前,根据焊接作业指导书应对焊工及相关人员进行技术交底,并做好技术交底记录。
3.1.4 对于高温、高压、剧毒、易燃、易爆的压力管道,在焊接施工前应画出焊口位置示意图,以便在焊接施工中进行质量监控。
压力管道焊接工艺指令卡
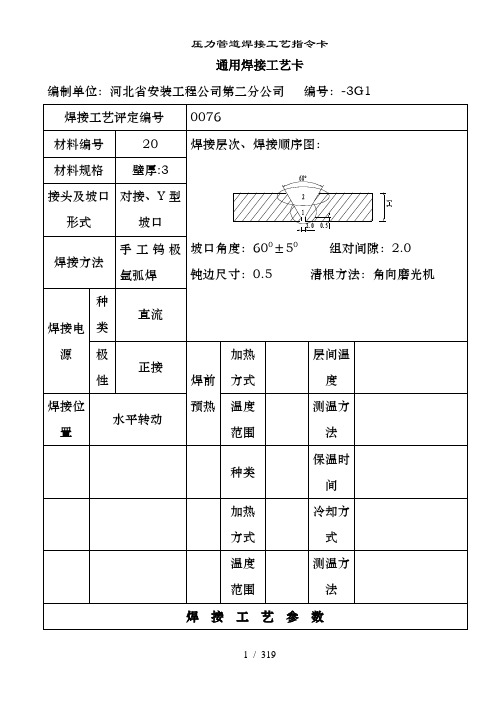
通用焊接工艺卡编制单位:河北省安装工程公司第二分公司编号:-3G1编制:日期:2006.10.9 审批:日期:2006.10.9通用焊接工艺卡编制单位:河北省安装工程公司第二分公司编号:-3G3编制: 日期:2006.10.9 审批:日期:2006.10.9通用焊接工艺卡编制单位:河北省安装工程公司第二分公司编号:-3G2编制:日期:2006.10.9 审批:日期:2006.10.9通用焊接工艺卡编制单位:河北省安装工程公司第二分公司编号:-4G1编制:日期:2006.10.9 审批:日期:2006.10.9通用焊接工艺卡编制单位:河北省安装工程公司第二分公司编号:-4G3编制:日期:2006.10.9 审批:日期:2006.10.9通用焊接工艺卡编制单位:河北省安装工程公司第二分公司编号:-4G2编制:日期:2006.10.9 审批:日期:2006.10.9通用焊接工艺卡编制单位:河北省安装工程公司第二分公司编号:-5G1编制:日期:2006.10.9 审批:日期:2006.10.9通用焊接工艺卡编制单位:河北省安装工程公司第二分公司编号:-5G3编制:日期:2006.10.9 审批:日期:2006.10.9通用焊接工艺卡编制单位:河北省安装工程公司第二分公司编号:-5G2编制:日期:2006.10.9 审批:日期:2006.10.9通用焊接工艺卡编制单位:河北省安装工程公司第二分公司编号:D9-10G1编制:日期:2006.5.10 审批:日期:2006.5.10通用焊接工艺卡编制单位:河北省安装工程公司第二分公司编号:D9-10G3编制:日期:2006.5.10 审批:日期:2006.5.10通用焊接工艺卡编制单位:河北省安装工程公司第二分公司编号:D9-10G2编制:日期:2006.5.10 审批:日期:2006.5.10通用焊接工艺卡编制单位:河北省安装工程公司第二分公司编号:5-7G2编制:日期:2006.5.10 审批:日期:2006.5.10通用焊接工艺卡编制单位:河北省安装工程公司第二分公司编号:-7G3编制:日期:2006.5.10 审批:日期:2006.5.10通用焊接工艺卡编制单位:河北省安装工程公司第二分公司编号:-7G1编制:日期:2006.5.10 审批:日期:2006.5.10通用焊接工艺卡编制单位:河北省安装工程公司第二分公司编号:-7G2编制:日期:2006.5.10 审批:日期:2006.5.10通用焊接工艺卡编制单位:河北省安装工程公司第二分公司编号:-8G1编制:日期:2007.5.10 审批:日期:2007.5.10通用焊接工艺卡编制单位:河北省安装工程公司第二分公司编号:-8G3编制:日期:2007.5.10 审批:日期:2007.5.10通用焊接工艺卡编制单位:河北省安装工程公司第二分公司编号:-8G2编制:日期:2007.5.10 审批:日期:2007.5.10通用焊接工艺卡编制单位:河北省安装工程公司第二分公司编号:-8G1编制:日期:2006.5.10 审批:日期:2006.5.10通用焊接工艺卡编制单位:河北省安装工程公司第二分公司编号:-8G3编制:日期:2006.5.10 审批:日期:2006.5.10通用焊接工艺卡编制单位:河北省安装工程公司第二分公司编号:-8G2编制:日期:2006.5.10 审批:日期:2006.5.10通用焊接工艺卡编制单位:河北省安装工程公司第二分公司编号:9-12G1编制:日期:2007.5.10 审批:日期:2007.5.10通用焊接工艺卡编制单位:河北省安装工程公司第二分公司编号:9-12G3编制:日期:2007.5.10 审批:日期:2007.5.10通用焊接工艺卡编制单位:河北省安装工程公司第二分公司编号:9-12G2编制:日期:2007.5.10 审批:日期:2007.5.10通用焊接工艺卡编制单位:河北省安装工程公司第二分公司编号:-10G1编制:日期:2006.5.10 审批:日期:2006.5.10通用焊接工艺卡编制单位:河北省安装工程公司第二分公司编号:-10G3编制:日期:2006.5.10 审批:日期:2006.5.10通用焊接工艺卡编制单位:河北省安装工程公司第二分公司编号:-10G2编制:日期:2006.5.10 审批:日期:2006.5.10通用焊接工艺卡编制单位:河北省安装工程公司第二分公司编号:-1-3G1编制:日期:2006.5.10 审批:日期:2006.5.10通用焊接工艺卡。
压力管道焊接作业指导书

压力管道焊接作业指导书TPMK standardization office【 TPMK5AB- TPMK08- TPMK2C- TPMK18】文件编号:XXX-2012压力管道焊接作业指导书编制:审核:批准:2012年7月发布 2012年8实施XXX公司压力管道焊接作业指导书目录1 适用条件或范围2 操作人员条件3 施工机具准备4 材料要求5 作业条件6 操作工艺6.1 碳素钢焊接操作工艺6.2 合金钢焊接操作工艺6.3 金属管道下向焊操作工艺6.4 不锈钢管道焊接操作工艺6.5 有色金属焊接操作工艺6.6 钢塑复合管的焊接操作工艺7 焊接操作质量控制8 焊接安全操作注意事项9 支持性相关文件和资料1 适用条件或范围本作业指导书适用于本公司承接的各种压力容器、压力管道安装焊接。
2 操作人员条件压力容器、压力管道安装焊工应受过操作技能、工作质量和施工安全的培训,并持有相应等级的焊工合格证,焊接热处理人员应经专业培训。
3 施工机具准备3.1 施工机械设备:交流电弧焊机、直流电弧焊机、钨极氩弧焊机、二氧化碳气体保护焊机、埋弧自动焊机、内外对口器、电容焊机、手提砂轮坡口机、焊条烘干箱、焊条保温箱。
3.2 工具和用具:焊枪、焊钳、焊炬、割炬、保温筒、錾子、扁铲、钢锉、钢锯、封头机架、内外对口器、加热板、电加热片、管材、管件固定机架以及面罩、护目镜、绝缘手套、绝缘鞋等焊接防护用具。
3.3 量具:焊缝检验尺、角尺、钢板尺、钢卷尺、游标卡尺。
3.4 检验和试验设备:X射线探伤机、光谱仪、测厚仪、超声波探伤仪、点温计、表面温度计、万用表、钳形电流表,各种力学性能试验机、电动试压泵。
4材料要求4.1 焊接材料应符合设计文件的规定。
4.2 焊接材料应符合现行国家焊接材料标准。
4.2.1 焊条应符合以下标准《碳钢焊条》GB/T5117、《低合金钢焊条》GB/T5118、《不锈钢焊条》GB/T983、《铝及铝合金焊条》GB/T3669、《铜及铜合金焊条》GB/T3670。
压力管道焊接工艺规程完整
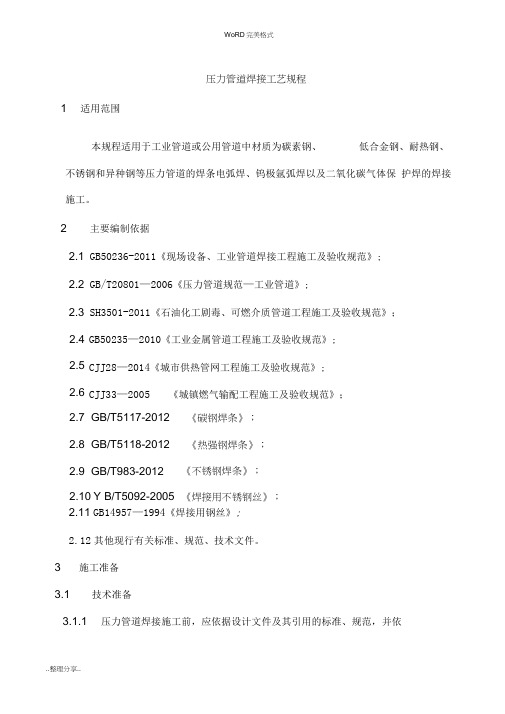
压力管道焊接工艺规程1 适用范围本规程适用于工业管道或公用管道中材质为碳素钢、低合金钢、耐热钢、不锈钢和异种钢等压力管道的焊条电弧焊、钨极氩弧焊以及二氧化碳气体保 护焊的焊接施工。
2主要编制依据2.1 GB50236-2011《现场设备、工业管道焊接工程施工及验收规范》; 2.2 GB/T20801—2006《压力管道规范—工业管道》;2.3 SH3501-2011《石油化工剧毒、可燃介质管道工程施工及验收规范》; GB50235—2010《工业金属管道工程施工及验收规范》; CJJ28—2014《城市供热管网工程施工及验收规范》; CJJ33—2005《城镇燃气输配工程施工及验收规范》;2.11 GB14957—1994《焊接用钢丝》; 2.12其他现行有关标准、规范、技术文件。
3 施工准备 3.1技术准备3.1.1 压力管道焊接施工前,应依据设计文件及其引用的标准、规范,并依2.4 2.5 2.6 2.7 GB/T5117-2012 《碳钢焊条》; 2.8 GB/T5118-2012《热强钢焊条》; 2.9 GB/T983-2012《不锈钢焊条》;2.10 Y B/T5092-2005 《焊接用不锈钢丝》;据我公司焊接工艺评定报告编制出焊接工艺技术文件(焊接工艺卡或作业指导书)。
如果属本公司首次焊接的钢种,则首先要制定焊接工艺评定指导书, 然后对该种材料进行工艺评定试验,合格后做出焊接工艺评定报告.3.1.2 编制的焊接工艺技术文件(焊接工艺卡或作业指导书)必须针对工程实际,详细写明管道的设计材质、选用的焊接方法、焊接材料、接头型式、具体的焊接施工工艺、焊缝的质量要求、检验要求及焊后热处理工艺(有要求时)等.3.1.3 压力管道施焊前,根据焊接作业指导书应对焊工及相关人员进行技术交底,并做好技术交底记录。
3.1.4 对于咼温、咼压、剧毒、易燃、易爆的压力管道,在焊接施工前应画出焊口位置示意图,以便在焊接施工中进行质量监控.3.2 对材料的要求3.2.1 被焊管子(件)必须具有质量证明书,且其质量符合国家现行标准(或部颁标准)的要求;进口材料应符合该国家标准或合同规定的技术条件。
压力管道焊接工艺规范标准设计
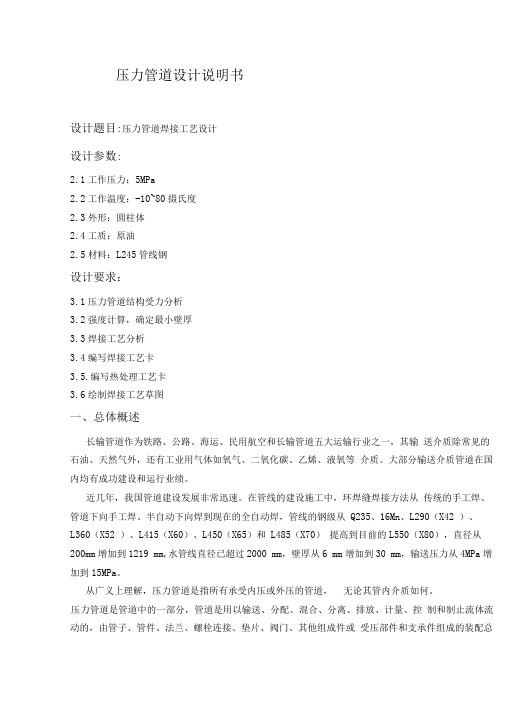
压力管道设计说明书设计题目:压力管道焊接工艺设计设计参数:2.1工作压力:5MPa2.2工作温度:-10~80摄氏度2.3外形:圆柱体2.4工质:原油2.5材料:L245管线钢设计要求:3.1压力管道结构受力分析3.2强度计算,确定最小壁厚3.3焊接工艺分析3.4编写焊接工艺卡3.5.编写热处理工艺卡3.6绘制焊接工艺草图一、总体概述长输管道作为铁路、公路、海运、民用航空和长输管道五大运输行业之一,其输送介质除常见的石油、天然气外,还有工业用气体如氧气、二氧化碳、乙烯、液氧等介质。
大部分输送介质管道在国内均有成功建设和运行业绩。
近几年,我国管道建设发展非常迅速。
在管线的建设施工中,环焊缝焊接方法从传统的手工焊、管道下向手工焊、半自动下向焊到现在的全自动焊,管线的钢级从Q235、16Mn、L290(X42 )、L360(X52 )、L415(X60)、L450(X65)和L485(X70)提高到目前的L550(X80),直径从200mm增加到1219 mm,水管线直径已超过2000 mm,壁厚从6 mm增加到30 mm,输送压力从4MPa增加到15MPa。
从广义上理解,压力管道是指所有承受内压或外压的管道,无论其管内介质如何。
压力管道是管道中的一部分,管道是用以输送、分配、混合、分离、排放、计量、控制和制止流体流动的,由管子、管件、法兰、螺栓连接、垫片、阀门、其他组成件或受压部件和支承件组成的装配总成。
压力管道具有以下特点:(1)、压力管道是一个系统,相互关联相互影响,牵一发而动全身。
(2)、压力管道长径比很大,极易失稳,受力情况比压力容器更复杂。
压力管道内流体流动状态复杂,缓冲余地小,工作条件变化频率比压力容器高(如高温、高压、低温、低压、位移变形、风、雪、地震等都有可能影响压力管道受力情况)。
(3))管道组成件和管道支承件的种类繁多,各种材料各有特点和具体技术要求,材料选用复杂。
(4)、管道上的可能泄漏点多于压力容器,仅一个阀门通常就有五处。
压力管道焊接法兰工艺规程(含卡箍连接)

压力管道与法兰焊接工艺规程1.总则;为加强的焊接质量,防止法兰变型,管道漏油。
给公司造成经济损失,管道的焊接必须采用手工电弧焊。
2.焊前准备2.1坡口加工后应进行外观检查,其表面不得与裂纹、夹层等缺陷。
2.2焊接接头组对前,应用手工或机械方法清理内外表面,在坡口两侧20mm范围不得有油漆、毛刺、锈斑、氧化皮及其他对焊接过程有害的杂物。
3.焊接管道对接头焊接形式见图1管道与对焊法兰如图a,钢管与法兰颈部对焊管道与平焊法兰如图3.0.2,钢管外径插入法兰内径焊接3.1定位焊应与正式焊接工艺相同,其焊缝长度宜为10~15mm,高宜为2~4mm,且不超过壁厚的2/3.3.2不得在焊件表面引弧或试验电流,焊件表面不得有电弧擦伤等缺陷。
3.3定位焊的焊缝不得有裂纹及其它缺陷,若发现缺陷应及时清除,定位焊焊道的两端应修磨成缓坡形。
3.4在保证焊透及熔合良好的条件下,应选用小的焊接参数,采用短弧、多层多焊道,层间温度控制在60℃以下。
3.5有耐腐蚀性要求的双面焊焊缝,与介质接触的一侧应最后焊接。
3.6采用手工电弧焊打底但施焊者必须具备相应焊工合格项目,其焊接工艺参数见下表:3.7在焊接中应确保起弧与收弧的质量,收弧时应将弧坑填满,多层焊的层间接头应相互错开。
3.8为防止焊接法兰盘的变型,法兰盘和管道打底焊接时应分为三段焊接应小电流焊接。
第二遍时电流可适应调大,电流参数见上表。
3.9焊接完毕后,应及时将焊缝表面的熔渣及附近的飞溅物清理干净,并检查焊口质量。
4.要求质检检收4.1焊口要求外观平整。
4.2法兰盘焊完后不得变型超过0.15-0.30mm。
不合格作废,根据法兰和管道粗细进行处理【主任和操作员】焊接电流的选择主要根据焊条直径选择电流,焊接电流选择注:立、仰、横焊电流应比平焊小10%左右。
焊角焊缝时,电流要稍大些。
打底焊时,特别是焊接单面焊双面成形焊道时,使用的焊接电流要小;填充焊时,通常用较大的焊接电流;盖面焊时,为防止咬边和获得较美观的焊缝,使用的电流稍小些。
压力工艺管道焊接作业指导书

压力管道安装焊接作业指导书一、焊工安全操作规程1、电焊、气焊工均为特程作业,身体检查合格,并经专业安全技术学习,训练和考试合格,颁发“特种作业操作证”后方能独立操作。
2、焊接场地,禁止放易燃易爆物品。
应备有消防器材,保证足够的照明和良好的通风。
3、操作场地10米内,不应储存油类或其它易燃易爆物品,(包括有易燃易爆气体的器皿管线)。
临时工地若有此类物品,而又必须在此操作时,应通知消防部门和安技意部门到现场检查,采取临时性安全措施后,方可进行操作。
4、工作前必须穿戴好防护用品,操作时(包括打渣)所有工作人员必须戴好防护眼镜或面罩。
仰面焊接应扣紧衣领,扎紧袖口,戴好防火帽。
5、对受压容器、密闭容器、各种有桶、管道,沾有可燃气体和溶液的工件进行操作时,必须事先进行检查,并经过冲洗除掉有毒、有害、易燃、易爆物质,解除容器及管道压力,消除容器密闭状态(敞开口、施开盖),再进行工作。
6、在焊接、切割密闭空心工件时,必须留有出气孔。
在容器内焊接,外面必须设人监护,并有良好通风措施,照明电压应采有12伏。
禁止在已做油漆或叶涂过塑料的容器内焊接。
7、电焊机接地零线及电焊工作回线都不准搭在易燃、易爆的物品上,也不准接在管道和机床设备上。
工作台回线应绝缘良好,机壳接地必须符合安全规定。
8、在有易燃、易爆物的车间、场所或煤气管附近焊接时,必须取得消防部门的同意并与煤气站联系好。
工作时应采取严密措施,防止火星飞溅引起火灾。
9、工作完毕,应检查场地。
灭绝火种、切断电源才能离开。
10、助手必须懂得电焊、气焊的安全常识。
操作者必须注意助手的安全。
二、手工电弧焊工操作规程1、焊工应掌握一般电气知识、遵守一般安全规程;还应熟悉灭火技术、触电急救及人工呼吸方法。
2、工作前应检查焊机电源线、引出线及接线点是否良好;线路横越车行道应架空或加保护盖;焊机二次线路及外壳必须有良好接地;焊条的夹钳绝缘必须良好。
3、下雨天不准露天电焊,在潮湿地带工作时,应站在铺有绝缘物品的地方并穿好绝缘鞋。
压力管道焊接工艺卡

焊道/焊层
焊接方法
填充金属
焊接电流
电弧电压(V)
焊接速度(cm/min)
线能量(kj/cm)
牌号
直径
极性电流(A)正1来自GTAWER50-6
φ2.5
直正
95~105
12~13
7~8
/
正2
SMAW
J422
φ3.2
直反
110~120
21~22
17~18
/
技术措施:
摆动焊或不摆动焊盖面层轻微摆动摆动参数/
焊前清理和层间清理角向磨光机背面清根方法/
单道焊或多道焊(每面)多道单丝焊或多丝焊/.
导电嘴至工件距离(mm)/锤击/
其他:无
编制/日期
审核/日期
批准/日期
FeS-1-2
FeT-1-1
电特性:
电流种类直流极性正接/反接
焊接电流范围(A)100~110;110~120电弧电压(V)13~14;21~22
焊接速度(范围)7~8cm/min;17~18cm/min
钨极类型及直径铈钨/φ2.0喷嘴直径(mm)φ8
焊接电弧种类(喷射弧、短路弧等)短路弧/焊丝送进速度(cm/min)/
填充金属:
保护气体:
焊材类别:
焊丝
焊条
气体种类混合比流量(L/min)
保护气Ar/6~10
尾部保护气///
背面保护气///
焊材标准:
GB/T8110及
NB/T47018
GB/T5117及
NB/T47018
填充金属尺寸:
φ2.5
φ3.2
焊材型号:
ER50-6
压力管道焊接工艺评定(样式)

背弯
侧弯
焊缝
热影响区
2
/
/
/
4
3
3
宏观金相:/
微观金相:/
接头硬度分布测定:/
熔敷金属化学成分:/
其他项目:/
编制:审核:日期:2017-11-10
焊接作业指导书
单位名称:陕西建工安装集团有限公司编制人:批准人:
焊接工艺指导书编号:YHGPZ-10日期:2017-10-11焊接工艺评定报告编号:D-B1-6HP010
衬垫:/
详图:
母材:
标准号:GB/T3274
牌号:20#
类、组别号:P1、1-1与类、组别号:P1、1-1相焊
厚度:δ=6mm
直径:/
焊后热处理:
热处理温度:/℃
保温时间:/h
保护气体:
尾部保护气:/流量/L/min
背面保护气:/流量/L/min
焊接材料:
焊条标准:GB5117
焊条牌号、直径:J422、Ф3.2、Ф4.0
试验编号
试样类型
试样厚度
(mm)
弯心直径
(mm)
弯曲角度
(°)
试验结果
WQ01-1
侧弯
10
40
180
合格
WQ01-2
侧弯
10
40
180
合格
WQ02-1
侧弯
10
40
180
合格
WQ02-2
侧弯
10
40
180
合格
冲击试验试验报告编号:031017
冲击试验按GB2650、GB2106规定的试样形式、尺寸和试验方法进行。
焊接方法:焊条电弧焊(SMAW)机械化程度(手工、半自动、自动):手工
压力管道焊接工艺规程

压力管道焊接工艺规程一、引言压力管道是指承受内外压力的管道,一般用于输送石油、天然气、水等高压流体。
因为其工作环境的复杂性,它的结构和规格都要求非常高,所以在其生产和使用过程中,焊接技术显得尤为重要。
本篇文档将介绍压力管道的焊接工艺规程,以保证焊接质量和安全性。
二、焊接前的准备在进行管道焊接之前,应该做好以下准备工作:1.做好钢材的检查和选材–对钢材的含碳量、硫、磷含量进行检查,确保符合要求的标准–采用相应牌号的钢材2.在管道拼接处进行切割和加工–利用切割机对管道进行切割,确保口径符合要求,切口平整–使用砂轮机或其它工具对切割口进行除锈、磨平和倒角–对管道表面进行清洗,去掉油脂、灰尘和其它杂物3.确保焊接的钢管部位没有残留物和缺陷–在进行焊接之前,应该使用比例关系对钢管进行拼接,一旦确认无错后,在进行焊接–检查钢管的内外部是否平直,确保没有变形,否则要及时进行调整三、焊接工艺规程3.1 焊接方法的选择压力管道焊接的方法通常有以下几种:1.电弧焊–适用于大直径高压管道的焊接,同时也是氢气炸裂等危险工作的实用方法–可以通过内底弧焊、管顶焊、环缝焊等方法来完成2.气焊–具有较高的工效和密封性,在金属表面制造氧化皮和焊缝时,适用于小规模的管道生产–按照气焊的工作步骤来进行管理是非常重要的3.焊接接头和开裂检测–监控焊接过程的质量,及时检测出潜在的开裂问题–可以通过X射线、超声波等检测方法来识别开裂的存在3.2 焊接温度的控制焊接的温度是决定焊缝质量的一个重要因素,需要严格掌控,以确保焊接的正确性和稳定性。
1.预热温度–预热温度是指在进行焊接之前,为钢材提前加热,使其达到制定的温度范围,以减少冷却时的应力变形和裂纹–具体的预热温度应该在方案中规定2.焊接温度–焊接温度应该根据钢材的性质、厚度和管径来决定,一般在规定范围内进行控制3.均热保温–均热保温是指在焊接之后,对钢管进行保温,使其缓慢冷却,减少应力针对压力管道的特殊性,焊接工艺的设计和管理非常重要。
压力管道焊接工艺评定
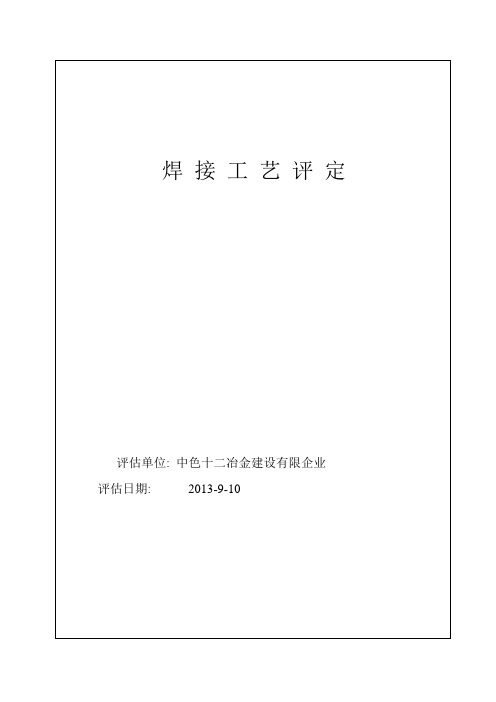
委托编号: YHGPS-10
名称:焊接工艺评估试件
工艺评估编号: D-B1-6HP010
试件编号: 1、2
材料牌号: Q235-B
材料规格: T=6mm
焊接材料: J422
焊接措施:手工
焊接位置:平位
坡口型式: Y形
焊工编号: TS6JTYN120529
热处理状态: /
直径: /
直径:/
焊后热处理:
热处理温度: /℃
保温时间: / h
保温时间:/h
保护气体:
尾部保护气: /流量/ L/min
背面保护气: /流量/ L/min
背面保护气:/流量/L/min
焊接材料:
焊条原则: GB5117
焊条牌号、直径: J422、Ф3.2.Ф4.0
焊丝牌号、直径: /
焊剂牌号: /
结论:本评估按GB50236-98规定焊接试件、检查试样,测定性能,确认试验记录对旳,评估成果:合格
结论:本评估按GB50236-98规定焊接试件、检查试样,测定性能,确认试验记录对旳,评估成果:合格
施焊:施焊日期: 2023.09.10
填表:日期: 2023.09.10
日期: 2023.09.10
焊缝
常温
80.0
合格
4
475.9
断母材
焊缝
常温
78.0
合格
5
6
7
8
9
试验原则:GB/T228, GB/T232, GB/T229
结论:该试件,经检查合格
试验:
无损探伤报告
编号: 030701
产品名称:焊接工艺评估试件
产品编号: YHGPS-05
焊接工艺卡

16~44
焊接方法或焊接工艺
GTAW
焊缝金属厚度mm
≤6
SMAW
≤38
焊接位置
6G
层-道
焊接方法
填充金属
焊接电流
电弧电压
V
焊接速度
cm∕min
线能量
kj∕cm
施焊技术
摆动
牌号
直径
极性
电流(A)
预热温度(℃)
250(200)
1
GTAW
TIG-R31
2.5
直流正接
120~140
11~12
6~8
/
4.RT25%Ⅱ(按设计要求,如设计未说明依据相关规范标准执行)
图号
接头名称
管道接头
接头编号
焊接工艺评定
报告编号
Y2016011
焊工持证项目
GTAW-FeⅢ-6G-3/159-Fefs-02/11/12
SMAW-FeⅢ-6G(K)-9/159-Fef3j
检
验
序号
本厂
监检单位
第三方或用户
母材代号
12Cr1MoVG
日期
2018.7.1
审核
王雅玮
日期
2018.7.1
批准
高栋
日期
2018.7.1
GTAW-FeⅢ-6G-3/159-Fefs-02/11/12
SMAW-FeⅢ-6G(K)-9/159-Fef3j
检
验
序号
本厂
监检单位
第三方或用户
母材代号
12Cr1MoVG
厚度mm
7~14
焊接方法或焊接工艺
GTAW
焊缝金属厚度mm