课程设计(论文)-基于PLC的电加热炉温度控制系统设计
基于PLC控制的加热炉温度控制系统

以照此方法设计)。当加热炉刚启动加热时,由于测到的炉温为常
温,sp -pv=△ U为正值且较大,△U 为PID调节器的输入,此
时PID调节器中P起主要作用,使SCR为最大电压给加热炉加热。 当加热炉温度达到100oC 以上时,sp -pv =△ U 为负值,经PID
调节,使SCR输出电压减小,加热炉温度降低。当温度正好达到
Keyword: programmable logic controller; heating furnace; PID
1 引言
传统的加热炉电气控制系统普遍采用继电器控制技术,由于 采用固定接线的硬件实现逻辑控制,使控制系统的体积增大,耗电 多,效率不高且易出故障,不能保证正常的工业生产。随着计算机 控制技术的发展,传统继电器控制技术必然被基于计算机技术而 产生的PLC控制技术所取代。而PLC本身优异的性能使基于PLC 控制的温度控制系统变的经济高效稳定且维护方便。这种温度控 制系统对改造传统的继电器控制系统有相当的意义[1]。
Abstract: This paper introduces a temperature control system for an electric heating furnace based on the PLC technology and the electronic rectifier technology. The hardware and software of the system are also outlined.
参考文献:
[1] 秦曾煌.电工学上册[M].北京:高等教育出版社,1999 [2] 郁汉琪.电气控制与可编程序控制器应用技术[M].南京: 东南大学出版社.2003 [3] 胡文金,计算机测控应用技术[M].重庆:重庆大学出版社. 2003 [4] 刘卫民.电力电子技术[M].重庆:重庆大学出版社.2003
基于PLC的加热炉温控制系统设计

毕业设计(论文)题目:基于PLC的加热炉温控制系统设计学院:电子信息学院专业班级:06自动化(2)指导教师:康涛职称:讲师学生姓名:雷颖倩学号:40604010225摘要在现代工业生产过程中,一些温度等作为被控参数的过程,往往其容量滞后较大,控制要求又较高,若采用单回路控制系统,其控制质量无法满足生产要求。
本文针对锅炉的结构特点以及船机控制能够有效的改善过程的动态特性、提高工作频率、减小等效过程时间常数和加快响应速度等,提出了锅炉温度串级控制的解决方案。
本系统以电加热锅炉为被控对象,以锅炉出口水温为主被控参数,以炉膛内水温为福被控参数,以加热炉电阻丝电压为控制参数,以PLC为控制器,构成锅炉温度控制系统;完成了系统的硬件设计和PLC程序设计。
经过调试,PLC程序实现了数据采集、A/D转换、PID运算和D/A转换等,达到了设计要求。
关键词:锅炉,温度,串级控制,PLC,PIDABSTRACTIn modern industrial production,some course's capacity often lags behind relatively largely,control also expect relatively much regarding temperature,etc,if adopt the controlsystem of single circuit,its quality of control is unable to meet the production requirement.Because the bunches of control can improve the dynamic characteristic of the course effectively,improve operating frequency,reducing the time constant of the equivalent course and accelerating the response speed,etc.This text have proposed one bunch of solutions of control of boiler temperature.This system leaves target of accusing of on boiler with electricity,export water temperature.With boiler for accuse of parameter mainly,regard the burner hearth water temperature as one pair of parameters of accusing of,regard voltage of resistance wire of the heating furnace as the control parameter,regard PLC as the controller, form one bunch of control systems of boiler temperature;Finish the designing of systematic hardware and the program with PLC.Through debugging,PLC procedure has realized the data gathering,A/D changing,PID operation and D/A changing,etc,has reached the designing requirement.KEYWORDS:boiler,temperature,bunches of control,plc,pid前言随着我国国民经济的快速发展,锅炉的使用范围越来越广泛。
基于PLC的温度控制系统的设计
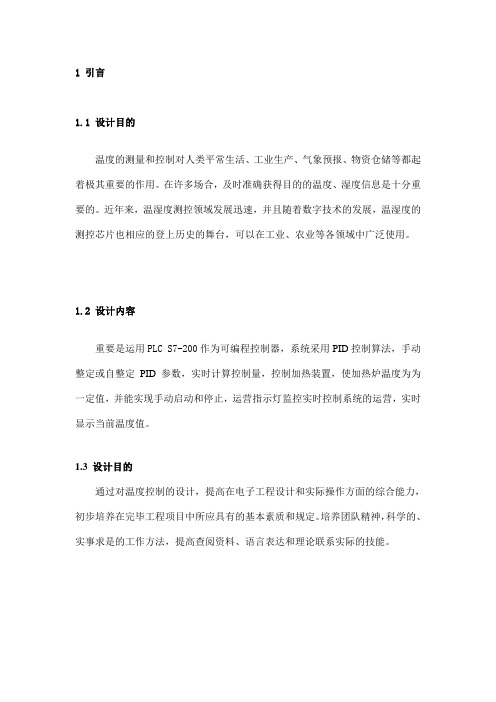
1 引言1.1 设计目的温度的测量和控制对人类平常生活、工业生产、气象预报、物资仓储等都起着极其重要的作用。
在许多场合,及时准确获得目的的温度、湿度信息是十分重要的。
近年来,温湿度测控领域发展迅速,并且随着数字技术的发展,温湿度的测控芯片也相应的登上历史的舞台,可以在工业、农业等各领域中广泛使用。
1.2 设计内容重要是运用PLC S7-200作为可编程控制器,系统采用PID控制算法,手动整定或自整定PID参数,实时计算控制量,控制加热装置,使加热炉温度为为一定值,并能实现手动启动和停止,运营指示灯监控实时控制系统的运营,实时显示当前温度值。
1.3 设计目的通过对温度控制的设计,提高在电子工程设计和实际操作方面的综合能力,初步培养在完毕工程项目中所应具有的基本素质和规定。
培养团队精神,科学的、实事求是的工作方法,提高查阅资料、语言表达和理论联系实际的技能。
2 系统总体方案设计2.1 系统硬件配置及组成原理2.1.1 PLC型号的选择本温度控制系统采用德国西门子S7-200 PLC。
S7-200 是一种小型的可编程序控制器,合用于各行各业,各种场合中的检测、监测及控制的自动化。
S7-200系列的强大功能使其无论在独立运营中,或相连成网络皆能实现复杂控制功能。
因此S7-200系列具有极高的性能/价格比。
2.1.2 PLC CPU的选择S7-200 系列的PLC有CPU221、CPU222、CPU224、CPU226等类型。
S7-200PLC 硬件系统的组成采用整体式加积木式,即主机中涉及定数量的I/O端口,同时还可以扩展各种功能模块。
S7-200PLC由基本单元(S7-200 CPU模块)、扩展单元、个人计算机(PC)或编程器,STEP 7-Micro/WIN编程软件及通信电缆等组成。
表2.1 S7-200系列PLC中CPU22X的基本单元本设计采用的是CUP226。
它具有24输入/16输出共40个数字量I/O点。
基于PLC的加热反应炉电气控制系统的设计
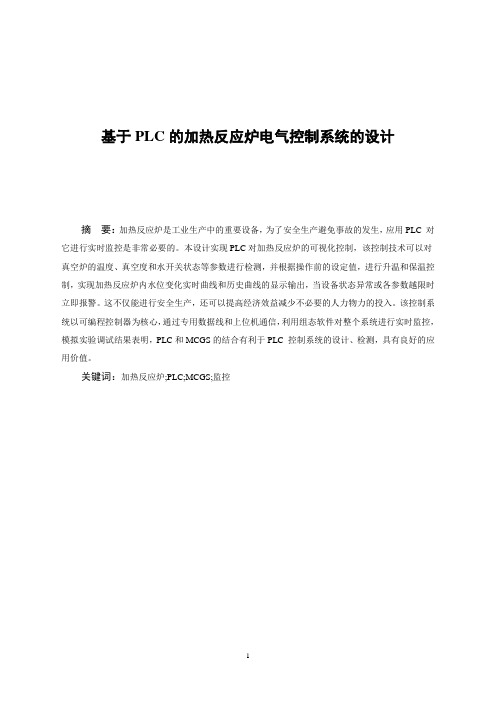
基于PLC的加热反应炉电气控制系统的设计摘要:加热反应炉是工业生产中的重要设备,为了安全生产避免事故的发生,应用PLC 对它进行实时监控是非常必要的。
本设计实现PLC对加热反应炉的可视化控制,该控制技术可以对真空炉的温度、真空度和水开关状态等参数进行检测,并根据操作前的设定值,进行升温和保温控制,实现加热反应炉内水位变化实时曲线和历史曲线的显示输出,当设备状态异常或各参数越限时立即报警。
这不仅能进行安全生产,还可以提高经济效益减少不必要的人力物力的投入。
该控制系统以可编程控制器为核心,通过专用数据线和上位机通信,利用组态软件对整个系统进行实时监控,模拟实验调试结果表明,PLC和MCGS的结合有利于PLC 控制系统的设计、检测,具有良好的应用价值。
关键词:加热反应炉;PLC;MCGS;监控Design of Heating Reactor Electrical Control System Based on PLCAbstract:Heating reactor furnaces are important equipment in factory. In order to avoid the happening of the production safety accidents, the application of the real-time monitoring PLC is very necessary . The visual control of heating reactor is realized in this paper by using common configuration software programmable logic controller. The furnace control technology for temperature, vacuum, water switch status testing. And according to the settings before the operation, to control the heating and insulation. The heating the reactor to achieve real-time water level changes within the historical curve and the curve shows the output. It can also alarm with equipment state abnormal or various parameters on the limit. This not only for safety, but also increase economic efficiency to reduce unnecessary investment in human and material resources. The control system uses programmable logic controller as the core. Programmable logic controller through the dedicated data lines and the host computer communication. Using the configuration software for real-time monitoring of the entire system.The simulation experiment debugging results show that, the combination of PLC and MCGS is conducive to the PLC design, testing, and has a good value.Key words: Heating reactor; PLC; MCGS; technology monitor目录摘要 (1)关键词 (1)1前言 (2)1.1研究加热反应炉的目的和意义 (2)1.2加热反应炉国内外研究现状 (2)1.3加热反应炉研究的内容 (2)2 PLC与MCGS组态软件简介 (3)2.1P LC的定义 (3)2.2P LC的特点 (3)2.3P LC的通信联网 (3)2.4 P LC的应用领域 (5)2.5 MCGS组态软件简介 (6)2.5.1 MCGS组态软件新增特性 (6)2.5.2组态软件特点 (7)3加热反应炉简介 (8)3.1加热反应炉的输入输出设备表 (9)3.2加热反应炉原理图 (9)4控制系统的设计 (10)4.1加热反应炉对电气控制系统的要求 (10)4.1.1进料控制 (10)4.1.2加热反应控制 (10)4.1.3泄放控制 (10)4.2系统设计方案 (10)4.2.1根据系统对象选型 (10)4.2.2根据控制对象选型 (11)4.3对象和范围的确定 (12)4.3.1 PLC容量的选择与确定 (13)4.3.2 PLC外设的选择与确定 (13)4.3.3 PLC的生产厂家的确定 (13)4.4系统硬件图设计 (13)4.5控制系统的软件设计 (17)4.6温度的PID控制 (20)5控制画面的创建 (22)5.1工程的建立 (22)5.2变量的定义 (23)5.3控制画面的设计与制作 (22)5.4动画连接 (24)5.5控制程序的编写 (25)5.6数据显示画面的设计与制作 (28)6系统抗干扰措施 (29)6.1电磁干扰的类型及其影响 (29)6.2电磁干扰主要来源 (30)6.2.1来自空间的辐射干扰 (30)6.2.2 来自系统外引线的干扰 (30)6.2.3 来自PLC系统内部的干扰 (30)6.3加热反应炉控制系统的抗干扰措施 (30)7结论 (32)参考文献 (32)致谢 (33)附录 (34)1 前言1.1 研究加热反应炉的目的和意义加热反应炉是工业生产中常用的重要设备,过去仅依靠人工经验进行操作,往往存在送料、温度、压力等条件变化时不能实施有效控制的问题,产品质量不稳定甚至出现次品,造成原料浪费,给企业带来经济损失。
基于PLC控制的加热炉温度控制系统设计

基于PLC控制的加热炉温度控制系统设计概述加热炉是工业生产中常见的设备之一,其主要作用是提供高温环境用于加热物体。
为了确保加热炉的稳定性和安全性,需要设计一个可靠的温度控制系统。
本文将介绍一个基于PLC(可编程逻辑控制器)控制的加热炉温度控制系统设计方案。
系统设计原理在加热炉温度控制系统中,PLC作为核心控制器,通过监测温度传感器的输出信号,根据预设的温度设定值和控制策略,控制加热炉的加热功率,从而实现对加热炉温度的稳定控制。
以下是系统设计的主要步骤:1.硬件设备选择:选择适合的温度传感器和控制元件,如热电偶、温度控制继电器等。
2.PLC选型:根据实际需求,选择合适的PLC型号。
PLC需要具备足够的输入输出点数和计算能力。
3.传感器连接:将温度传感器接入PLC的输入端口,读取实时温度数据。
4.温度控制策略设计:根据加热炉的特性和工艺需求,设计合适的温度控制策略。
常见的控制策略包括比例控制、积分控制和微分控制。
5.控制算法实现:根据温度控制策略,编写PLC程序,在每个采样周期内计算控制算法的输出值。
6.加热功率控制:使用控制继电器或可调功率装置,控制加热炉的加热功率。
7.温度反馈控制:通过监测实际加热炉温度和设定值之间的差异,不断修正加热功率控制,使加热炉温度稳定在设定值附近。
系统硬件设计基于PLC控制的加热炉温度控制系统的硬件设计主要包括以下几个方面:1.温度传感器:常用的温度传感器有热电偶和热敏电阻。
根据加热炉的工艺需求和温度范围,选择适合的温度传感器。
2.PLC:选择适合的PLC型号,根据实际需求确定PLC的输入输出点数和计算能力。
3.控制继电器或可调功率装置:用于控制加热炉的加热功率。
根据加热炉的功率需求和控制方式,选择合适的继电器或可调功率装置。
4.运行指示灯和报警器:用于显示系统的运行状态和报警信息。
PLC程序设计PLC程序是基于PLC的加热炉温度控制系统的关键部分,其主要功能是实现温度控制算法。
课程设计报告论文-基于PLC的电加热炉温度控制系统设计
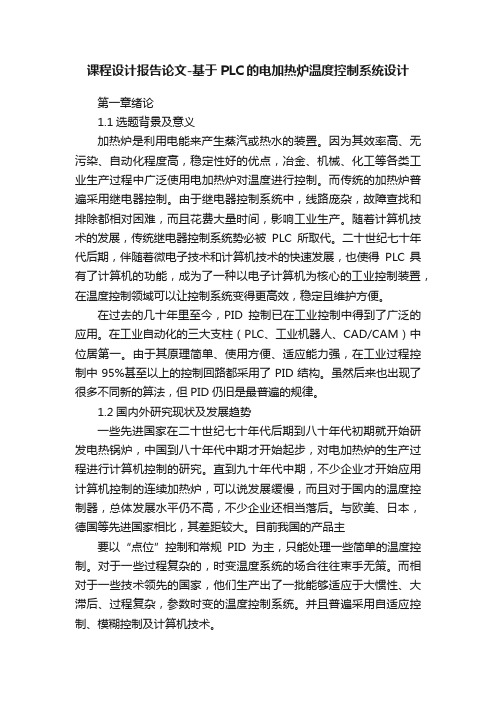
课程设计报告论文-基于PLC的电加热炉温度控制系统设计第一章绪论1.1选题背景及意义加热炉是利用电能来产生蒸汽或热水的装置。
因为其效率高、无污染、自动化程度高,稳定性好的优点,冶金、机械、化工等各类工业生产过程中广泛使用电加热炉对温度进行控制。
而传统的加热炉普遍采用继电器控制。
由于继电器控制系统中,线路庞杂,故障查找和排除都相对困难,而且花费大量时间,影响工业生产。
随着计算机技术的发展,传统继电器控制系统势必被PLC所取代。
二十世纪七十年代后期,伴随着微电子技术和计算机技术的快速发展,也使得PLC 具有了计算机的功能,成为了一种以电子计算机为核心的工业控制装置,在温度控制领域可以让控制系统变得更高效,稳定且维护方便。
在过去的几十年里至今,PID控制已在工业控制中得到了广泛的应用。
在工业自动化的三大支柱(PLC、工业机器人、CAD/CAM)中位居第一。
由于其原理简单、使用方便、适应能力强,在工业过程控制中95%甚至以上的控制回路都采用了PID结构。
虽然后来也出现了很多不同新的算法,但PID仍旧是最普遍的规律。
1.2国内外研究现状及发展趋势一些先进国家在二十世纪七十年代后期到八十年代初期就开始研发电热锅炉,中国到八十年代中期才开始起步,对电加热炉的生产过程进行计算机控制的研究。
直到九十年代中期,不少企业才开始应用计算机控制的连续加热炉,可以说发展缓慢,而且对于国内的温度控制器,总体发展水平仍不高,不少企业还相当落后。
与欧美、日本,德国等先进国家相比,其差距较大。
目前我国的产品主要以“点位”控制和常规PID为主,只能处理一些简单的温度控制。
对于一些过程复杂的,时变温度系统的场合往往束手无策。
而相对于一些技术领先的国家,他们生产出了一批能够适应于大惯性、大滞后、过程复杂,参数时变的温度控制系统。
并且普遍采用自适应控制、模糊控制及计算机技术。
近年来,伴随着科学技术的不断快速发展,计算机技术的进步和检测设备及性能的不断提升,人工智能理论的实用化。
基于PLC控制的加热炉温度控制系统设计
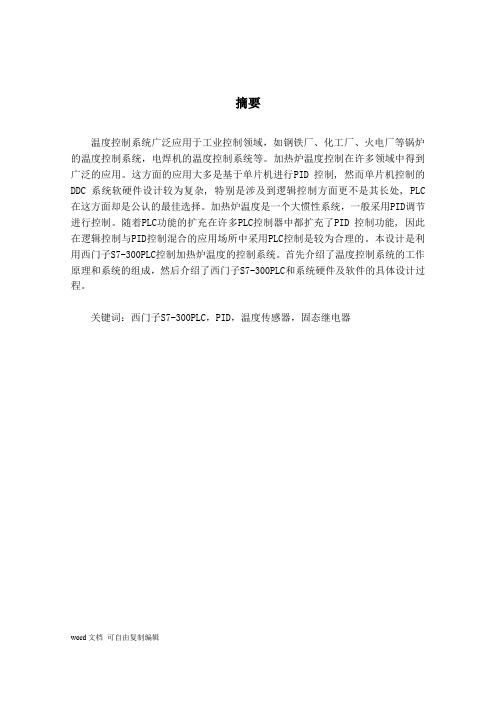
摘要温度控制系统广泛应用于工业控制领域,如钢铁厂、化工厂、火电厂等锅炉的温度控制系统,电焊机的温度控制系统等。
加热炉温度控制在许多领域中得到广泛的应用。
这方面的应用大多是基于单片机进行PID 控制, 然而单片机控制的DDC 系统软硬件设计较为复杂, 特别是涉及到逻辑控制方面更不是其长处, PLC 在这方面却是公认的最佳选择。
加热炉温度是一个大惯性系统,一般采用PID调节进行控制。
随着PLC功能的扩充在许多PLC控制器中都扩充了PID 控制功能, 因此在逻辑控制与PID控制混合的应用场所中采用PLC控制是较为合理的。
本设计是利用西门子S7-300PLC控制加热炉温度的控制系统。
首先介绍了温度控制系统的工作原理和系统的组成,然后介绍了西门子S7-300PLC和系统硬件及软件的具体设计过程。
关键词:西门子S7-300PLC,PID,温度传感器,固态继电器目录摘要 (I)Abstract .......................................... 错误!未定义书签。
第一章引言 . (1)1.1 系统设计背景 (IV)1.2 系统工作原理 (IV)1.3 系统设计目标及技术要求 (IV)1.4 技术综述 (IV)第二章系统设计 (V)2.1 控制原理与数学模型 (V)2.1.1 PID控制原理 (V)2.1.2 PID指令的使用注意事项 (VIII)2.2 采样信号和控制量分析 (IX)2.3 系统组成 (IX)第三章硬件设计 ................................................... X I3.1 PLC的基本概念 (XI)3.1.1 模块式PLC的基本结构 (XII)3.1.2 PLC的特点 (XIII)3.2 PLC的工作原理 (XIV)3.2.1 PLC的循环处理过程 (XIV)3.2.2 用户程序的执行过程 (XVI)3.3 S7-300 简介 (XVI)3.3.1 数字量输入模块 (XVII)3.3.2 数字量输出模块 (XVII)3.3.3 数字量输入/输出模块 (XVII)3.3.4 模拟量输入模块 (XVII)3.3.5 模拟量输出模块 (XVIII)3.4 温度传感器 (XVIII)3.4.1 热电偶 (16)3.4.2 热电阻 (17)3.5 固态继电器 (XX)3.5.1 概述 (18)3.5.2 固态继电器的组成 (18)3.5.3 固态继电器的优缺点 (19)第四章软件设计 ................................................. X XII4.1 STEP7编程软件简介 (XXII)4.1.1 STEP7概述 (XXII)4.1.2 STEP7的硬件接口 .......................... .. (XXII)4.1.3 STEP7的编程功能 (XXII)4.1.4 STEP7的硬件组态与诊断功能 (XXIII)4.2 STEP7项目的创建 (XXIV)4.2.1 使用向导创建项目 (XXIV)4.2.2 直接创建项目 (XXIV)4.2.3 硬件组态与参数设置 (XXIV)4.3 用变量表调试程序 (XXVI)4.3.1 系统调试的基本步骤 (XXVI)4.3.2 变量表的基本功能 (XXVII)4.3.3 变量表的生成 (XXVIII)4.3.4 变量表的使用 (XXVIII)4.4 S7-300的编程语言 (XXIX)4.4.1 PLC编程语言的国际标准 (XXIX)4.4.2 STEP7中的编程技术 (XXX)结束语 ......................................................... X XXIV 致谢 (33)参考文献 (34)附录 (35)1.1系统设计背景近年来,加热炉温度控制系统是比较常见和典型的过程控制系统,温度是工业生产过程中重要的被控参数之一,冶金﹑机械﹑食品﹑化工等各类工业生产过程中广泛使用的各种加热炉﹑热处理炉﹑反应炉,对工件的处理均需要对温度进行控制。
基于PLC的电炉控制设计毕业论文

基于PLC的电炉控制设计毕业论文1 前言 (1)1.1选题背景 (1)1.2国外国研究现状 (2)1.3系统要求与工艺流程 (2)2硬件概述 (3)2.1PLC简介 (3)2.2PLC结构 (4)2.3PLC类型 (4)2.4PLC简史 (5)3软件概述 (5)3.1组态王简介 (5)3.2组态王和I/O设备 (6)3.2组态王仿真方法 (6)4硬件的选型与设计 (6)4.1PLC控制的设计原则 (6)4.2PLC控制设计步骤 (7)4.3PLC型号与硬件配置 (8)4.3.1 PLC型号选定 (8)4.3.2 热电偶 (9)4.3.4 可控硅 (9)4.3.2 系统整体方案与硬件连接图 (10)5软件设计 (11)5.1下位机程序说明 (11)5.1程序截图 (14)6组态画面设计 (16)6.1组态工程的建立 (16)6.2建立新的工程 (16)6.2建立工程画面 (18)6.3建立主画面 (18)6.3.1 建立趋势曲线画面 (19)6.3.2 建立数据报表 (21)6.3.3 建立报警窗口 (21)6.3.4 手动控制面板 (22)7组态系统运行 (23)7.1主画面运行 (23)7.2实时趋势曲线 (23)7.3历史趋势曲线 (24)7.4数据报表 (25)7.5历史报警窗口 (26)7.6退出组态王运行系统 (27)结论 (28)参考文献 (29)致谢 (30)1前言1.1选题背景随着科技不断的发展,工业对于温度控制需求也逐渐的增高,在加上个人计算机的普及,计算机领域发展迅速,我们进入一个高速的信息时代,技术要求也在一天天增加,导致我们对于控制要求更高。
同时还要可以留有晋升的空间,便于我们升级更新换代。
计算机控制系统在这个方面就可以满足我们的要求,所以我现在的工业之中运用了大量自动化装置,这也是紧跟着时代步伐的一种体现,工业化的今天,我们享受着数字化、智能化给我带来的各种好处之外,我们也在生活生产之中不断地提高着,我们的设备的技术水平和我们个人的技术水平,从而我们的进步加快了生产过程的集成化,进一步提高产品质量,确保了生产的安全性与可靠性。
- 1、下载文档前请自行甄别文档内容的完整性,平台不提供额外的编辑、内容补充、找答案等附加服务。
- 2、"仅部分预览"的文档,不可在线预览部分如存在完整性等问题,可反馈申请退款(可完整预览的文档不适用该条件!)。
- 3、如文档侵犯您的权益,请联系客服反馈,我们会尽快为您处理(人工客服工作时间:9:00-18:30)。
第一章绪论1.1选题背景及意义加热炉是利用电能来产生蒸汽或热水的装置。
因为其效率高、无污染、自动化程度高,稳定性好的优点,冶金、机械、化工等各类工业生产过程中广泛使用电加热炉对温度进行控制。
而传统的加热炉普遍采用继电器控制。
由于继电器控制系统中,线路庞杂,故障查找和排除都相对困难,而且花费大量时间,影响工业生产。
随着计算机技术的发展,传统继电器控制系统势必被PLC所取代。
二十世纪七十年代后期,伴随着微电子技术和计算机技术的快速发展,也使得PLC 具有了计算机的功能,成为了一种以电子计算机为核心的工业控制装置,在温度控制领域可以让控制系统变得更高效,稳定且维护方便。
在过去的几十年里至今,PID控制已在工业控制中得到了广泛的应用。
在工业自动化的三大支柱(PLC、工业机器人、CAD/CAM)中位居第一。
由于其原理简单、使用方便、适应能力强,在工业过程控制中95%甚至以上的控制回路都采用了PID结构。
虽然后来也出现了很多不同新的算法,但PID仍旧是最普遍的规律。
1.2国内外研究现状及发展趋势一些先进国家在二十世纪七十年代后期到八十年代初期就开始研发电热锅炉,中国到八十年代中期才开始起步,对电加热炉的生产过程进行计算机控制的研究。
直到九十年代中期,不少企业才开始应用计算机控制的连续加热炉,可以说发展缓慢,而且对于国内的温度控制器,总体发展水平仍不高,不少企业还相当落后。
与欧美、日本,德国等先进国家相比,其差距较大。
目前我国的产品主要以“点位”控制和常规PID为主,只能处理一些简单的温度控制。
对于一些过程复杂的,时变温度系统的场合往往束手无策。
而相对于一些技术领先的国家,他们生产出了一批能够适应于大惯性、大滞后、过程复杂,参数时变的温度控制系统。
并且普遍采用自适应控制、模糊控制及计算机技术。
近年来,伴随着科学技术的不断快速发展,计算机技术的进步和检测设备及性能的不断提升,人工智能理论的实用化。
因此,高精度、智能化、人性化必然是国内外必然的发展趋势。
1.3项目研究内容以PLC控制为核心,PLC将加热炉温度设定值与温度传感器的测量值之间的偏差,经过PID运算后得到的信号控制输出电压的大小,采用PID算法,运用PLC编程语言编程,从而调节加热器加热,实现温度的自动控制。
由两个或两个以上的控制器串联,一个控制器的输出是另一个控制器的设定而组成的串级控制系统。
改善了主回路的响应速度。
主调节器具有“细调”作用,副调节器具有“粗调”作用,从而改善了系统的品质。
第二章系统设计2.1系统的过程控制设计在本系统中若采用以原料出口温度为被控量的单回路系统,由于在加热炉的过程控制中存在着时间滞后和容量滞后,系统不能立即感知。
直到经过大容量滞后,才能反映到原料的温度变化。
系统的控制作用才开始反映,但为时已晚。
同样,控制器的动作也必须经过较大的容量滞后才能开始对输出的改变做出调整,导致系统的品质变差。
因此,增设炉膛温度作为另一个被控参量,构成串级控制系统,如图5-1图5-1 串级系统控制框图当原料温度变化时,首先使得炉膛温度C2发生变化。
而出口处的原料温度C1还没有发生变化。
因此,主调节器输出不变,炉膛温度测量值发生变化。
通过副变送器反馈到副调节器。
通过可控硅控制加热元件的电流大小,使电炉保持在设定的温度工作状态。
与此同时,炉膛温度的变化也会引起管壁的温度变化,从而影响出口C1温度的变化,使主调节器的输出发生变化。
由于主调节器的输出就是副调节器的输入,而副调节器的输出直接控制可控硅导通角的大小,进一步加速了控制系统的调节过程,使主被控量即加热炉出口温度恢复到设定值。
2.1.1控制系统的性能[1]⑴对二次扰动的抑制能力强,当二次扰动产生后,副被控量首先检测到扰动的影响并及时控制操作变量,使副被控量恢复到设定值。
从而使扰动对主被控量的影响减小,即副回路对扰动进行粗调,主回路对扰动进行细调。
⑵串级控制系统由于有副回路的存在改善副对象的动态特性,从而提高了整个系统的动态特性。
⑶串级控制系统由于副回路性能的改善,主控制器的比例带可以变得更窄,从而提高了系统的工作频率,即提高了系统的快速响应能力。
⑷有一定的自适应能力。
在副回路的作用下,包括控制阀在内的副对象在操作条件和负荷变化时,其特性变化对系统的影响显著地削弱了。
2.2 控制器的设计2.2.1 控制器的控制规律选择PID控制器是应用最广泛的一种控制器。
包括P控制器、PD控制器,PI控制器及完整的PID控制器。
P的作用是增加开环增益,降低系统的稳态误差,提高控制精度,但缺点是会使系统变得不稳定。
I的作用是消除静差,但有过调现象且不及时。
D的作用是增加系统的稳定性,但同时也放大了系统的高频噪声。
可见,合理运用才能使系统的效益最大化。
1)比例(P)控制比例控制是最简单的工作方式。
其控制器输入与输出的误差信号成比例关系。
比例控制器的传递函数为:G c (S)=KP(2.1)其中:Kp称为比例系数或增益。
其倒数称为比例带,也称比例度。
2)比例积分(PI)控制具有比例加积分的控制规律的控制称为比例积分控制,即PI控制。
可减少或消除系统的稳态误差,改善系统的稳态性能,但存在过调现象而且不及时,存在滞后。
PI控制的传递函数及输出信号为:G c (S)=KP+KP/Ti·1/S=KP(S+1/Ti)/S (2.2)u(t)=Kp e(t)+KP/Ti∫t e(t)d(t) (2.3)其中:Kp为比例系数 Ti称为积分时间常数3)比例微分(PD)控制具有比例加微分的控制规律的控制称为比例微分控制,即PD控制。
它能改善系统的动态特性,但具有放大高频噪声的缺点。
PD控制的传递函数及输出信号为:G c (s)=KP+KPτS (2.4)u(t)=KP e(t)+KPτde(t)/dt (2.5)其中:KP为比例系数τ为微分时间常数4)比例积分微分(PID)控制具有比例加微分和积分的控制规律的控制称为比例积分微分控制,即PID控制。
PID控制具有提高系统稳定性能的优点外,还可以还改善系统的动态性能,消除误差,缩小超调量,加快反映速度。
PID控制的传递函数及输出信号为:G c (S)=KP+KP/Ti·S+KPτs (2.6)u(t)=KP e(t)+KP/Ti∫t e(t)dt+Kpτde(t)/dt (2.7)其中:KP为比例系数 Ti称为积分时间常数τ称为微分时间常数三者都是可调常数。
因为采用串级控制,所以有主副调节器之分。
主调节器起定值作用,副调节器起随动作用。
原料的出口温度是系统的重要指标,它的允许波动的范围小,且温度控制系统是容量滞后较大的系统,故主控制器选用PID控制,而副控制量采用P控制,因为副被控量的控制范围在工艺上要求不是太严格,允许有余差,故副控制器选用P控制就行。
这时如果引入积分就可能会降低副回路反应的快速性影响控制效果。
2.2.2 主、副控制器的正反作用选择副调节器作用方式的确定:从锅炉的设备和安全出发,一旦系统故障就应自动切断燃料供应。
所以可控硅输出电压选用气开式,调节阀的静态放大系数Kv 大于0。
然后确定副被控过程的K2。
当可控硅的导通角增大,电压增大,炉膛水温上升,被控对象为正作用,所以K2大于0。
再确定副调节器,为保证回路是负反馈,各环节的静态放大系数极性相乘必须为负,所以副调节器K2小于0,副调节器的作用方式为反作用方式主调节器作用方式的确定:炉膛水温升高,出口温度也升高,被控对象为正作用,所以K1大于0。
为保证主回路为负反馈,各环节的放大系数相乘必须为负,所以主调节器的放大系数K1小于0。
主调节器的作用方式为反作用方式。
2.3 系统组成本系统的结构框如图2-2所示图2-2 系统组成的结构框图系统选用S7-300PLC为控制器,用热电偶检测炉温,温度变送器将热电偶输出的微弱信号转换为标准信号。
然后送给模拟量输入模块,经A/D转换成数字量。
CPU将它与温度设定值作比较,并按PID控制算法对误差进行运算,将结果送给模拟量输出模块,经D/A转换变为模拟信号。
用来控制可控硅的导通角大小,从而调节电热丝的加热,改变温度大小。
第三章硬件设计及网络结构3.1可编程控制器概述可编程控制器简称PLC,它几乎完全占领了工业控制领域。
由于PLC的应用面广、功能强大、使用维护方便,已经成为当代工业自动化的主要支柱之一,在工业生产的所有领域得到了广泛的使用。
PLC有两种工作状态,即运行(RUN)状态和停止(STOP)。
其中运行状态是执行应用程序的状态,在CPU执行启动操作时,清除没有保持功能的位存储器,定时器和计数器,清除堆栈内容等。
再执行一次启动组织块OB100,它由用户编写,即完成对指定的初始化操作。
之后反复不断地重复执行用户程序。
停止状态一般用于程序的编制与修改。
除了执行用户程序外,PLC还要完成启动循环时间监,数据写入输出模块,读取输入模块状态,并存入输入过程映像区;在系统循环结束时,接着执行所有挂起的任务。
最后返回第一阶段。
各个阶段如图3-1所示图3-1 扫描过程PLC的特点如下:⏹可靠性高,抗干扰能力强,适应性强。
⏹系统的安装、设计和调试工作量小,维护方便。
⏹硬件配套齐全,编程方便易学,操作方便。
⏹体积小,功能强大,能耗低,性价比高。
3.2 S7-300的输入输出模块S7-300属于模块式PLC,主要由CPU模块、电源模块、输入输出模块组成(图3-2)。
各种模块安装在机架上,通过通信模块,PLC可以与计算机,其他PLC或其他设备进行通信。
图3-2 PLC基本结构➢模拟量输入模块在温度控制系统中,传感器将检测到的温度信号转换成4~20mA的电流信号。
模拟量输入模块SM331用于将模拟量信号转换为CPU内部处理的数字信号。
其主要组成部分是A/D转换器。
模拟量输入模块的输入信号一般是模拟量变送器的标准输出信号。
为了减少电磁干扰,传送模拟信号时使用双绞屏蔽电缆。
模拟信号电缆的屏蔽层两端接地,如果电缆两端存在电位差,将会造成对模拟信号的干扰。
在这种情况下,将电缆的屏蔽层一点接地。
➢模拟量输出模块模拟量输出模块SM332用于将CPU送给执行元件的数字信号转换成成比例的电流信号,其主要部件是D/A转换器、模拟量输出模块为负载和执行器提供电流或电压,模拟信号使用屏蔽电缆或双绞线电缆来传送。
➢数字量输入模块数字量输入模块SM321用于连接外部的机械触点和电子式传感器,比如接近开关,二线式开关等。
数字量输入模块把外部传来的数字信号转换为PLC的内部信号,输入电路中一般含有RC滤波器,防止由于外部干扰而引起的错误信号输入。
输入电流一般为几毫安。
➢数字量输出模块数字量输出模块SM322用于驱动接触器,灯等小功率电机负载。
数字量输出模块将PLC的内部信号转换为控制过程所需的外部信号。