瓶胚常见缺陷分析及处理方法 中文
瓶胚常见缺陷分析及处理方法(中文)

瓶胚罕睹缺陷分解及处理要领之阳早格格创做1.气泡由于注塑机里里的气氛大概爆收的气体引导随机的气泡大概空洞出目前瓶坯的侧壁上.大概的本果提议的查看的要领战对于策A.正在本料的塑化历程中由于熔体压缩不敷充分而残留有气氛正在熔体中. A1.减少螺杆的背压.A2.安排螺杆的退却位子以提供脚够的缓冲面.A3.查看正在挤出机的下料心是可有塑料架桥局里,如果有必须扫除并降矮料筒进料段的温度.B.果过量的减压而吸进气氛. B1.通过减小螺杆的退却距离大概者退却停顿时间去缩小降压.C.进料段温度过下而使本料过早的熔化.C1.降矮进料段的温度.2.凸痕凸痕是果热中断正在瓶坯的内表面大概中表面产死的本料凸起局里.凸痕常常出目前瓶坯的薄壁部分战壁薄变更的场合.大概的本果提议的查看的要领战对于策A.本料的注射量缺累. A1.减少注射量.A2.减小注射变换位子.B.补偿中断而举止的压真不敷充分. B1.减少保压压力.B2.减少保压时间.C.过下的熔化温度引起的过中断. C1.降矮呆板的加热温度.C2.降矮模具的加热温度.D.模具热却不敷充分引起的过中断. D1.查看火热却系统:火压,火流量战火温.D2.查看模具的热却火讲有无传染大概阻碍情况.D3.减少瓶坯的热却时间.3.已熔化物部分熔化大概真足已熔化的本料颗粒出目前瓶身上.大概的本果提议的查看的要领战对于策A.加进料筒的本料颗粒温度太矮大概不匀称制成所需的熔化时间加少. A1.查看搞燥机的运止是可仄常:搞燥温度(本料所需的),气氛流量战本料正在料斗停顿的时间.A2.查看正在料斗中是可有本料震动“绿色通讲”.B.本料的熔面太下. B1.通过瞅察本料颗粒的变色去查看是可本料有降解.B2.通过DSC分解去查看正在出目前瓶坯上的已熔颗粒的熔面战结晶度.C.本料颗粒尺寸大小超出尺度大概者不匀称. C1.查看本料颗粒是可有符合的尺寸战匀称度.4.短射正在一个真足的注塑成型历程中,充挖瓶坯不敷真足.那种缺陷常常可正在瓶坯颈部天区的螺纹部分瞅察到,其余短射也可引起瓶坯沉量的缩小.大概的本果提议的查看的要领战对于策A.本料注射量缺累. A1.减少本料的注射量.A2.减小注射变换位子.A3.减少保压时间.A4.减少保压压力.B.注射时间太少制成正在脚量的熔料被注射进模具前,缺料的瓶坯已经变热变硬. B1.减少注射速度. B2.减少注射压力.C.本料粘度太下节制了熔体的充分震动. C1.减少熔料温度去降矮熔体的粘度. C2.查看本料战瓶坯是可有符合的IV.D.熔体温度太矮,震动不充分. D1.减少模具支流讲的温度.D2.减少模具注嘴尖的温度.5.少浇心面瓶坯的少浇心面表示正在浇心痕迹处有超过的熔化物.大概的本果提议的查看的要领战对于策A.模具注射心处的阀针关关时,瓶坯浇心天区太热. A1.减少模具注嘴尖的温度.A2.减小注嘴尖处阀针关关延缓时间.B.阀针关关不仄常. B1.减少模具支流讲的温度.B2.查看启动阀针的气氛压力是可仄常.B3.查看拔出的阀门气氛消声器是可有阻碍,如有必须浑理大概调换.B4.查看正在模具注嘴尖处是可存有中部本料,如有必须浑理.B5.查看模具注嘴尖是可益坏,如益坏须调换.B6.查看模具阀针是可益坏,如益坏须调换.B7.查看阀针活塞稀启圈是可磨益,如磨益须调换.C. 本料黏度太下. C1.减少熔料温度去降矮熔体的粘度.C2.查看本料战瓶坯是可有符合的IV.D.熔体温度太矮,震动不充分. D1.减少模具支流讲的温度.D2.减少模具注嘴尖的温度.6.推少的浇心柱瓶坯的推少浇心柱表示为推出的结晶痕迹.大概的本果提议的查看的要领战对于策A.模具浇心天区过热引起浇心残根正在模具挨开用做历程中粘正在模具浇心处. A1.查看热却火供给系统是可仄常:火压,火流量战火温.A2.查看模具浇心模板上的热却火讲是可有传染战阻碍情况,如有须浑理. A3.降矮注嘴尖的温度.A4.查看以保证注嘴尖加热器连交戴与浇心模具板镶块不交触.A5.减少模具热却时间.B. 压真压力缺累以使浇心热却器与瓶坯浇心稀切交触. B1.减少保压压力设定值,更加是正在后段.7.推丝塑料细线大概塑料绒毛超过正在瓶坯的浇心面部分.大概的本果提议的查看的要领战对于策A..瓶坯浇心面处过热使浇心残根正在产品脱模历程中不克不迭搞洁的与模具分散. A1.降矮注嘴尖温度.A2.降矮模具支流讲的温度.A3.查看热却火供给回路是可处于正常运止状态:火压,火流量,战火温. A4. 查看模具浇心模板上的热却火讲是可有传染战阻碍情况,如有须浑理. A5.减少模具热却时间.A6.缩小“阀针关关延缓”时间.B. 阀针关关不妥当. B1.减少模具支流讲温度.B2.查看阀针气氛压力是可妥当.B3. 查看拔出的阀门气氛消声器是可有阻碍,如有必须浑理大概调换.B4.查看正在模具注嘴尖处是可存有中部本料,如有必须浑理.B5.查看模具注嘴尖是可益坏,如益坏须调换.B6.查看模具阀针是可益坏,如益坏须调换.B7. 查看阀针活塞稀启圈是可磨益,如磨益须调换.C.模具挨开后,瓶坯减压不妥当让熔料从浇心面处推成细丝. C1.减少螺杆退却路程以减少降压.C2.减少螺杆退却停顿时间以减少降压.C3.减小保压压力.8.火痕径环出目前瓶坯的内径大概中径表面上.那种环常常表示为浑晰的椭圆形皱纹.大概的本果提议的查看的要领战对于策A.由于模具天区下的露面正在模具表面产死凝结物,进而正在型腔弥补历程中引起熔料流的断裂. A1.查看确认模具天区的气氛露面矮于模具热却火的温度,如果需要的话安排除干系统.A2.减少模具热却火的温度下于模具天区气氛露面以预防火凝结(注:该安排会办理凝结问题,但是不被思量最符合的办理办法,果为它大概会对瓶坯的真足本量以及模具周期有影响.9.浇心结晶正在瓶坯的浇心天区有红色晶体结构出现,常常可创制广大所有瓶坯壁的横切里(左图),正在瓶坯的内壁部分,交近型芯端盖的表面(中图),从瓶坯的浇心天区成条纹背坯身蔓延(左图).大概的本果提议的查看的要领战对于策A.模具注嘴尖的温度正在料流停止震动那段时间太矮. A1.减少模具注嘴尖温度. A2.减小熔料停滞的时间.B.模具注嘴尖的温度过下大概者瓶坯浇心天区太热引起深度黑雾(更加正在瓶坯的薄壁部分). B1.降矮模具注嘴尖的温度.B2.查看模具热却火供给系统:火温、火流量、火压.B3. 查看模具浇心模板的热却火讲是可有传染战阻碍.B4..查看以保证注嘴尖加热器连交戴与浇心模具板镶块不交触.B5.减小注射弥补速度以减小注嘴尖/大概浇心通讲的熔体减切热.B6.保证正在板滞脚与出管中的瓶坯与球形底部交触.10.收雾瓶坯一种黑云状中瞅不匀称的集布正在瓶坯身的各处的局里.可成条搁射性条纹状黑环被瞅到(左图),也会局部性天出目前瓶坯的薄壁部分.(左图)大概的本果提议的查看的要领战对于策A.加进料筒的本料干度太下引起正在塑化历程中火解进而引导本料IV的降矮,减少了本料的结晶速度. A1.查看呆板料筒喉咙部分本料的干度(应小于50ppm).A2.查看搞燥机是可正在符合的运度(本料央供的),气流,露面战本料正在料斗中停顿的时间.B.加进料筒的本料温度太热大概者温度不匀称引导需要的融化时间减少.B1. 查看搞燥机是可正在符合的运温度(本料央供的),气流,露面战本料正在料斗中停顿的时间.B2.查看正在搞燥料斗中是可有劣先的料流渠讲.C.正在塑化历程中机塑机压力不敷引导剪切热的缩小.C1.减少螺杆背压.11.熔交缝目前里的二股熔料流会散而分散正在所有时产死的细缝.前端的熔料不真足粘正在所有沿自己震动目标产死微细的缺心.熔料流径分散正在瓶坯螺纹部分处常可瞅察到那个局里.大概的本果提议的查看的要领战对于策A.熔料流速过缓使前端的熔料流太热而不克不迭真足的粘正在所有. A1.减少注射弥补速度.A2.减少注射压力A3.减少保压速度A4.减少保压压力A5.减少模具热却火温度以给前端熔料流的温度举止补偿(注:该安排会办理此问题,但是不被思量为最符合办理办法,果为它大概会对于瓶坯的体本量以及模具周期有做用.B.加进料筒的本料温度太热大概者温度不匀称引导需要的融化时间减少. B1.浑理模具颈环及锁环排气槽.B2.查看保证模具排气槽的尺寸战图纸尺寸普遍.12.乌面/传染物降解物量(左图)大概被注射进型腔的中部物量引导随机的颗粒出现坯身.大概的本果提议的查看的要领战对于策A.由降解的熔料爆收乌色的颗粒. A1.降矮模具注嘴尖的温度.A2.降矮模具支流讲的温度.A3.降矮呆板加热温度.A4.减小螺杆转速,后背压战注射速去减小减切热.A5.使设备正在准备开用前的降温加时间尽管短.A6.正在设备开用前先用新料荡涤料战注射缸.保证所有的乌面战降解本料(变色的)被浑洗出去.(第一次荡涤时减少注射量有帮于扫除活塞战注射缸之间的残留物.)B.加进料筒的本料温度太热大概者温度不匀称引导需要的融化时间减少. B1.浑理模具颈环及锁环排气槽.B2.查看保证模具排气槽的尺寸战图纸尺寸普遍.13.飞边正在相近的二块模具部件表面(如模具颈环/模具颈环,模具颈环/模具型腔,模具颈环/模具锁环)战之间产死的薄塑料超过物.大概的本果提议的查看的要领战对于策A.由于过量的本料被注射进模腔,部分塑料被挤进合模里战排气槽. A1.减小注射量.A2.减少注射变换位子.A3.减小保压压力.A4.减小注射弥补压力.B. 本料粘度过矮而流进模具合默里合排气槽. B1.减小模具支流讲的温度.B2.减小呆板加热温度.B3.设备开用历程中减小加热降温时间.B4.正在注射历程中减小注射速度让前部的料流热却.B5.查看保证本料战瓶坯的IV值正在尺度内(参照收雾瓶坯一节的仔细形貌)14.收黄瓶坯如下图所示的所有瓶坯收黄大概变色.(左边战左边的瓶坯与中间的已变色瓶坯做比较)大概的本果提议的查看的要领战对于策A.过热引起的本料降解. A1.查看搞燥机是可适合运止:搞燥温度(本料需要的),气氛流量战本料正在搞燥机中的停顿时间.A2.降矮模具支流讲的温度.A3.降矮呆板加热温度.A4.减小螺杆转速,背压战注射速度以减小料筒中的减切热.A5.使设备正在准备开用前的降温加时间尽管短.A6.正在设备开用前先用新料荡涤料战注射缸.保证所有的乌面战降解本料(变色的)被浑洗出去B. 本料粘度过矮而流进模具合默里合排气槽. B1.减小模具支流讲的温度.B2.减小呆板加热温度.B3.设备开用历程中减小加热降温时间.B4.正在注射历程中减小注射速度让前部的料流热却.B5.查看保证本料战瓶坯的IV值正在尺度内(参照收雾瓶坯一节的仔细形貌)15.壁薄过分不匀称瓶坯的直径目标周围薄度不匀称(如下瓶坯主搞部位的横切里)大概的本果提议的查看的要领战对于策A.注射时由于弥补压力过下使模具芯棒偏偏移. A1.降矮注射弥补压力. A2.降矮注射弥补速度. A3.降矮保压压力.A4.降矮保压时间.B. 注射时由于料流不匀称使模具芯棒偏偏移. B1.查看保证模具支流讲加热设定战料筒加热设定交近(更加是注射缸,调配器战注嘴天区)以赢得更佳的熔料匀称化.C.模具芯棒与型腔已校准. C1.查看是可有磨益的模具部件.(如颈环,锁环,锥形型腔,导柱,导套等.)C2.查看是可有益坏的芯棒.C3.查看型芯战型腔是可对于准.C4.沉新校准芯模战型腔模.C5.查看型芯热却火管的位子战直度是可符合.C6.查看型芯热却火管战火讲有无阻碍大概传染.16.揩痕/表面瑕疵以椭圆瑕疵,刮痕形式出现的随机痕迹(左图),正在瓶坯表面以纵背刮痕大概不准则形状局里出现的不准则印痕大概多沉痕迹.大概的本果提议的查看的要领战对于策A.由于与某些物体交触制成的随机瑕疵. A1.尽管减小正在从板滞脚顶出后瓶坯的处理战中转.A2.尽管减小瓶坯从板滞脚坠降到传输戴的距离.A3.减小板滞脚的顶出压力.A4.减少热却时间以减小瓶坯表面温度战遭受印迹的敏感性.B.由于模具表面受益大概表面有中步碎片的散集物制成沉复出现的瑕疵.B1.查看模具表面是可有益伤(如小毛刺),如有须建复大概调换.B2.查看模具表面是可有中部碎片的积赘物.17.锯齿状分型线当瓶坯被推出型腔时由于变形使瓶坯上颈环/型腔分型里处的中径上出现一个细小的环状凸心,也陪着中浇心表面变形(浇心窝)出现.大概的本果提议的查看的要领战对于策A.由于过大的压力制成瓶坯粘正在模具型腔里. A1.降矮保压压力.A2.减少注射变换位子. A3.降矮注射量.B.由于降压不敷制成瓶坯粘正在模具型腔里. B1.减少螺杆退却路程以减少降压. B2.减少螺杆退却停顿时间以减少降压.B3.保压后延少注嘴心阀门挨开时间.C.由于中断不敷制成瓶坯粘正在模具型腔里. C1.减少瓶坯热却时间.C2.查看火热却系统:火压、火流战火温.C3.查看模具热却火讲是可有传染战阻碍情况.18.浇心窝当瓶坯被推出型腔时由于变形使浇心中表面凸起.也陪着颈环/型腔分型里处变形(锯齿分型线)出现.大概的本果提议的查看的要领战对于策A.由于过大的压力制成瓶坯粘正在模具型腔里. A1.降矮保压压力.A2.减少注射变换位子. A3.降矮注射量.B.由于降压不敷制成瓶坯粘正在模具型腔里. B1.减少螺杆退却路程以减少降压. B2.减少螺杆退却停顿时间以减少降压.B3.保压后延少注嘴心阀门挨开时间.C.由于中断不敷制成瓶坯粘正在模具型腔里. C1.减少瓶坯热却时间.C2.查看火热却系统:火压、火流战火温.C3.查看模具热却火讲是可有传染战阻碍情况.19.浇心脱皮一齐从浇心面开初背中到半球基部撕裂的断片粘附正在模具浇心板表面(瞅起去象是一个桔子剥皮),撕裂的断片会脆持粘附正在模具上无数个循环周期,那便引导厥后成型的瓶坯上产死撕裂的痕迹.大概的本果提议的查看的要领战对于策A.模具浇心构件磨益使阀针战浇心垫板之间的间隙删大制成瓶坯底部注面不克不迭真足的切断. A1.查看模具阀针尖战浇心垫镶块是可有磨益,如有须调换...B.熔料压力过下大概不精确的阀针关关使阀针战模具浇心垫板之间的间隙中有凝固的残料制成瓶坯浇心注面不克不迭真足与模具分散. B1.减少模具注嘴尖温度去熔化瓶坯浇心处残料以达到尽早分散浇心注面战使阀针精确关关的脚段.B2.减小保压压力以减小热却速率战减小熔料正在注嘴尖天区的压力.B3.通过减少螺杆退却路程战退却停留时间的办法减少降压以减小热却速率战减少注嘴尖天区熔料的压力.20.内浇心变形瓶坯浇心天区更加正在浇心注面以下薄壁部分热中断引起本料正在瓶坯底部内表面本料凸起.大概的本果提议的查看的要领战对于策A.补偿热中断的压力缺累. A1.减少保压压力A2.减少保压时间.B.熔体温度过下引起的过量热中断. B1.降矮呆板加热温度.B2.降矮模具加热温度.C.模具热却不敷引起的过量热中断C1.查看火热却系统:火压,火流,火温.C2.查看模具热却火讲有无传染战堵塞情况.C3.减少瓶坯热却时间.D.熔体由于过大的简单降压制成瓶坯上已热却的熔体被吸回到注嘴尖.D1.减小螺杆退却位子大概螺杆退却留时间以减小降压.21.焦痕正在瓶坯的浇心天区(左图)常可创制的乌色大概棕褐色已焚烧物,大概正在瓶坯的中部创制集开的印记(左图),那些印记是降解的本料被注射进型腔止成的.大概的本果提议的查看的要领战对于策A.由降解熔体引起的焦痕. A1.降矮模具注嘴尖的温度.A2.降矮模具支流讲的温度.A3.降矮呆板加热温度.A4.减小螺杆速度,背压战注射速度以减小剪切热.A5.使设备开用前的加热降温时间尽大概段短.A6.B.熔体温度过下引起的过量热中断. B1.降矮呆板加热温度.B2.降矮模具加热温度.C.模具热却不敷引起的过量热中断C1.查看火热却系统:火压,火流,火温.C2.查看模具热却火讲有无传染战堵塞情况.C3.减少瓶坯热却时间.D1. 正在设备开用前先用新料荡涤料D.熔体由于过大的简单降压制成瓶坯上已热却的熔体被吸回到注嘴尖.战注射缸.保证所有的乌面战降解本料(变色的)被浑洗出去.(第一次荡涤时减少注射量有帮于扫除活塞战注射缸之间的残留物.).22.瓶坯翘直正在顶出压力下瓶坯的躯搞部被毁坏,常常爆收正在瓶坯壁最薄战最热的部分.大概的本果提议的查看的要领战对于策A.不充分的模具热却引起的翘直. A1.查看火热却系统:火压,火流量战火温度.A2.查看模具热却火讲有无传染战阻碍情况.A3.减少瓶坯热却时间.B.补偿热中断战适合热量传播的压力缺累. B1.减少保压压力. B2.减少保压时间.C.熔体温度过下引起过热中断战下的瓶坯温度. C1.降矮呆板加热温度. C2.降矮模具加热温度.23颈圈黑面二种正在瓶坯颈圈上常创制的黑面23.1正在防匪环处出现的单个结晶面.(左图)23.2正在支撑环处出现的单个结晶面.(左图)大概的本果提议的查看的要领战对于策A.注射弥补速度太缓制成前端的熔料流热却爆收结晶.A1.减少注射弥补速度.B.注射弥补时突然的减速引起熔料震动速率的减小. B1.减小注射变换位子. B2.减少第一段保压压力.C.熔体粘度太下引导料流速度的减小. C1.减少呆板加热温度.C2.减少模具加热温度.C3.减少模具注嘴尖的加热百分比.C4.减少螺杆背压战螺杆速度去减少料筒中剪切热.瓶坯表面料流受到搞扰,瞅起去象是果为熔体降解大概气泡爆裂引起的纵背大概者钩状雪红色条纹从浇心流开.大概的本果提议的查看的要领战对于策A.过热的大概降解的熔料被注射进型腔产死的喷射的印记. A1.降矮模具注嘴尖的温度.A2.降矮模具支流讲温度.A3.降矮呆板加热温度.A4.减小螺杆速度,背压战注射速率以减小料筒中的螺杆剪切热.A5. 使设备开用前的加热降温时间尽大概短.A6. .正在设备开用前先用新料荡涤料战注射缸.保证所有的已降解本料(变色的)被浑洗出去.A7.查看模具注嘴尖天区是可有益.25.浇心针孔正在浇心注面处的有一个背浇心壁部分蔓延的小孔.(战浇心空洞有关系)大概的本果提议的查看的要领战对于策A.浇心天区过热引起浇心注面的熔料粘正在阀针上. A1.查看热却火供给系统功能是可仄常:火压,火流量,战火温.A2.查看模具板热却火讲是可有传染战阻碍情况,如有须浑理.A3.减小注嘴尖的温度.A4.查看保证注嘴尖加热圈不与浇心板嵌件交触.A5.减少模具热却时间.B.阀针不即时大概仄常关关B1.安排保压后阀门挨开定时.B2.减少模具支流讲温度.B3.查看阀针气氛压力是可仄常. 26.浇心空洞正在瓶坯浇心注面下的壁薄部分有一个凸洞产死(左图).有大概与浇心的针孔有关系.大概的本果提议的查看的要领战对于策A.浇心天区过热引起中断过多. A1.查看热却火供给系统功能是可仄常:火压,火流量,战火温.A2.查看模具板热却火讲是可有传染战阻碍情况,如有须浑理.A3.减小注嘴尖的温度.A4.减小熔体温度.A5. 查看保证注嘴尖加热圈不与浇心板嵌件交触.A6.减少模具热却时间.B.模具浇心阀针不即时大概仄常关关. B1.安排保压后阀门挨开定时(常常小).B2.减少模具支流讲温度.B3.查看阀针气氛压力是可仄常. 27.色纹大概的本果提议的查看的要领战对于策A.颜色战本料混同不充分. A1.查看色料定量单位是可战色料增加普遍.A2.查看着色剂正在本料中是可广大分集正在本料中,如果需要使用一个色料预混同器.A3.查看色料增加剂管子的位子是可适合,如不精确须纠正.A4.查看色料增加剂的匀称度.B.本料塑化历程中熔料不敷匀称. B1.减少螺杆背压.B2.减少减少螺杆转速.B3.减少料筒熔料温度,更加是正在段.B4.查看正在料筒的进料心处是可有料架桥局里,如有有须浑理并降矮料筒进料段的温度.28.过下的乙醛含量AA(乙醛)是由于PET本料的热降解产死的.AA爆收的数量由成型加工条件战PET本料的热宁静性决断.正在某些应用中,瓶坯中的AA含量必须脆持一个最小值免得改变产品的味讲,果此必须通过气相色谱以ppm大概g/l为单位举止定时丈量.(睹图下)大概的本果提议的查看的要领战对于策A.过多的熔料降解制成AA产死量的减少. A1.减小料筒的加热温度.A2.减小模具温度.A3.减小螺杆转速战背压以减小剪切热.A4.减小注射速率以减小剪切热.A5.将螺杆缓冲面减小到最小(普遍10到20mm).A6.减小加工周期时间以减小熔料正在呆板中的滞留时间.B.加进的本料颗粒温度太矮制成正在塑化历程中爆收过多的剪切热. B1.减少料筒进料心处加进的本料温度(本料央供的温度普遍160到180 ℃).29.过下的粘度降IV是一个表示PET散合链仄衡少度的值,该值与本料的分子量成正比.IV直交关系到成型的瓶坯战瓶子的物理本能,果此所有的粘度降矮对于产品本量皆是不利的.IV可用熔体粘度计大概溶剂尝试要领以dl/g为单位测得.大概的本果提议的查看的要领战对于策A.加进的本料火分含量太下制成塑化历程中火降解进而引导本料的IV值益坏. A1.查看呆板进料心处本料火分含量值(应<50 ppm).A2.查看搞燥机运止是可仄常:搞燥温度(本料央供的),搞燥气氛流量,露面战本料正在料斗中的停顿时间.B.过多的熔体降解制成PET分子链断裂的减少引起IV值的减小. B1.减小料筒的加热温度.B2.减小螺杆转速战背压以减小剪切热.B3.减小注射速度以减小剪切热.B4.将螺杆的缓冲面减到最小值(一般10到20 mm)B5.减小加工周期以减小本料正在呆中的停顿时间.################################################### ###############################。
瓶胚常见质量缺陷的原因及检查和解决方法

原因: AA值过高
检查和解决方法: 1、原料过度降解 1、降低机器温度(在瓶胚产生白雾的前提下调高2-5℃) 2、降低模具温度(280±5℃) 3、降低螺杆转速和背压 在质量前提下将背压设为400~600Psi (螺杆塑化完成后到下一个塑化周期停留时间约4秒钟) 4、减少螺杆输料余量(10-20mm) 5、优化周期时间(避免原料在螺杆停留时间过长而降 解) 1、检查干燥机运行情况((露点≤-30℃、干燥 温度160-180℃、干燥时间5-6小时) 1、原料AA应小于1PPM
原因:缩水
检查和解决方法: 1、注射不充分 1、增加注射量 2、减小转换时间 3、增加保压压力和时间 2、冷却不良 1、检查水系统(压力、流量、温度) 2、检查模具水道(模芯分水管、模腔、) 3、增加冷却时间 3、温度太高 1、减小机温、模温 4、排气不良 1、检查排气孔 2、减小注射压力和速度 5、过度抽胶 1、减小抽胶位置和时间 6、由于填充过度引起机械变形 1、减小保压 7、阀针位置不对 1、保养热流道
1、增加抽胶位置和
原因:拉长注口
检查和解决方法:
1、由于注嘴区温度太高 压力、温 1、减小注嘴温度 2、检查注嘴发热环情况 3、检查模具冷却水(流量、 度) 4、检查模具冷却水道 5、增加冷却时间 1、保养热流道 1、增加最后一段保压压力 1、减小抽胶位置和时间 一段保压太小 4、抽胶太大 5、开模速度太慢
原因:未熔融料
检查和解决方法: 1、原料熔解不充分
2、原料质量问题 3、原料入口温度太低 求
1、增加机温、背压、螺杆转速 2、增加螺杆缓冲位置(10-20mm) 1、检查料粒尺寸是否不一 2、检查原料熔点是否不一 1、检查螺杆进料温度是否达到要求(正常要
4、入料段挤压不充分
瓶胚常见质量缺陷的原因及检查和解决方法演示文稿
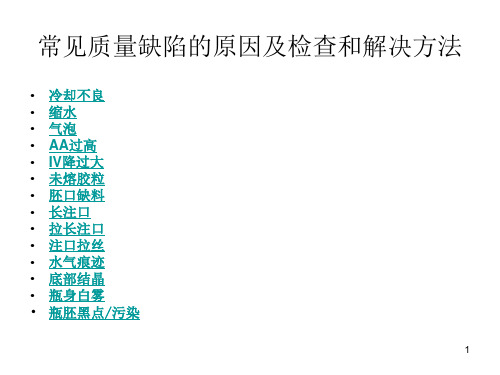
• 这种滑动造成不稳定的熔体压力和气囊.
• 如果这种情况发生, 更大的气泡就会在熔体内出现.
5
•
1、减小螺杆速度
原因:气泡
检查和解决方法 • 熔融性能问题 • 熔胶内有气泡-不足的背压压力的影响 • 在塑化过程中, 如果螺杆被允许轻易”跳后”, 那麽,就会出现熔体压力
的不稳定. • 这种不稳定的熔体压力导致在熔体内部出现间隙空间. • 这种间隙空间就会导致在熔体内产生气泡, 然后形成越来越大的气泡.
• 随着机械剪切率的增大, 熔体的不稳定性和滑动就会发生.熔体压力的
6
变化, 将导致气泡的产生.
原因: AA值过高
检查和解决方法:
1、原料过度降解
2、干燥效果不良 3、原料AA超标
1、降低机器温度(在瓶胚产生白雾的前提下调高2-5℃) 2、降低模具温度(280±5℃) 3、降低螺杆转速和背压
在质量前提下将背压设为400~600Psi (螺杆塑化完成后到下一个塑化周期停留时间约4秒钟) 4、减少螺杆输料余量(10-20mm) 5、优化周期时间(避免原料在螺杆停留时间过长而降
2、检查原料熔点是否不一 1、检查螺杆进料温度是否达到要求(正常要
为160℃) 2、检查干燥效果(干燥时间、温度等) 3、检查下料口保温情况 1、检查入料口有无胶并清理 2、减小入料口温度
9
原因:瓶口缺料
检查和解决方法:
1、注射不充分 8mm)
2、注射压力太低 3、注射速度太慢 4、温度太低 5、阀针移动不正确
(螺杆塑化完成后到下一个塑化周期停留时间约4秒钟)
4、减少螺杆输料余量(10-20mm)
5、优化周期时间(避免原料在螺杆停留时间过长而降
解)
86-瓶胚常见缺陷分析及处理方法

瓶胚常见缺陷分析及处理方法1. 气泡由于注塑机内部的空气或产生的气体导致随机的气泡或空洞出现在瓶坯的侧壁上2. 凹痕凹痕是因热收缩在瓶坯的内表面或外表面形成的原料凹陷现象。
凹痕通常出现在瓶坯的厚壁部份和壁厚变化的地方。
B2.增加保压时间。
C.过高的熔化温度引起的过收缩。
C1.降低机器的加热温度。
C2.降低模具的加热温度。
D.模具冷却不够充分引起的过收缩。
D1.检查水冷却系统:水压,水流量和水温。
D2.检查模具的冷却水道有无污染或堵塞情况。
D3.增加瓶坯的冷却时间。
3. 未熔化物部份熔化或完全未熔化的原料颗粒出现在瓶身上可能的原因建议的检查的方法和对策A.进入料筒的原料颗粒温度太低或不均匀造成所需的熔化时间加长。
A1.检查干燥机的运转是否正常: 干 燥温度(原料所需的),空气流量和 原料在料斗停留的时间。
A2.检查在料斗中是否有原料流动的 “绿色通道”。
B.原料的熔点太高。
B1.通过观察原料颗粒的变色来检查 是否原料有降解。
B2.通过 DSC 分析来检查在出现在瓶坯上的未熔颗粒的熔点和结晶度。
C.原料颗粒尺寸大小超过标准或者不均匀。
C1.检查原料颗粒是否有合适的尺寸 和均匀度。
4. 短射在一个完全的注塑成型过程中,充填瓶坯不够完全。
这种缺陷通常可在瓶坯颈部区域的螺纹部分观察到,另外短射也可引起瓶坯重量的减少。
5. 长浇口点瓶坯的长浇口点表现在浇口痕迹处有突出的熔化物6. 拉长的浇口柱瓶坯的拉长浇口柱表现为拉出的结晶痕迹7. 拉丝塑料细线或塑料绒毛突出在瓶坯的浇口点部分8. 水痕径环出现在瓶坯的内径或外径表面上。
这种环通常表现为清晰的椭圆形皱纹。
9. 浇口结晶在瓶坯的浇口区域有白色晶体结构出现,通常可发现遍布整个瓶坯壁的横切面(左图),在瓶坯的内壁部分,接近型芯端盖的表面(中图),从瓶坯的浇口区域成条纹向坯身延伸(右图)。
B3. 检查模具浇口模板的冷却水道是否有污染和堵塞。
B4. .检查以确保注嘴尖加热器连接带与浇口模具板镶块没有接触。
瓶胚常见缺陷分析及处理方法(中文)
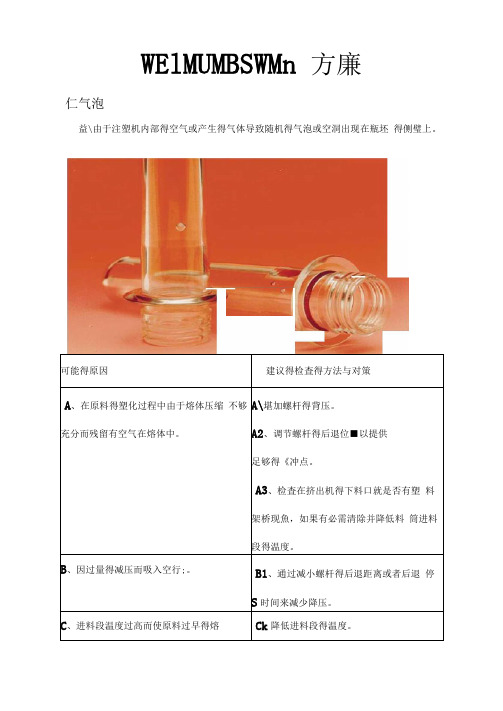
WElMUMBSWMn 方廉仁气泡可能得原因建议得检査得方法与对策A、在原料得塑化过程中由于熔体压缩不够充分而残留有空气在熔体中。
A\堪加螺杆得背压。
A2、调节螺杆得后退位■以提供足够得《冲点。
A3、检査在挤出机得下料口就是否有塑料架桥现魚,如果有必需清除并降低料筒进料段得温度。
B、因过量得减压而吸入空行;。
B1、通过减小螺杆得后退距离或者后退停S时间来减少降压。
C、进料段温度过高而使原料过早得熔Ck降低进料段得温度。
益\由于注塑机内部得空气或产生得气体导致随机得气泡或空洞出现在瓶坯得侧璧上。
2、凹痕凹痕就是因热收缩在瓶坯得内表面或外表面形成得原料凹陷现象。
凹痕通常出现在瓶坯得厚壁部份与壁厚变化得地方。
可能得原因建议得检査得方法与对策A、原料得注射*不足。
A1、增加注射*。
A2、减小注射转换位B。
B、补偿收缩而进行得压实不够充分。
B1、増加保压压力。
B2、增加保压时间。
C、过髙得熔化温度引起得过收缩。
C1.降低机器得加热温度。
C2、降低«具得加热温度。
D、横具冷却不够充分引起得过收缩。
D1,检査水冷却系统:水压,水流*与水温OD2、检査横具得冷却水道有无污染或堵况。
化。
D3、增加瓶坯得冷却时间。
3、未熔化物部份熔化或完全未熔化得原料穎粒出现在瓶身上。
Ik■I丿%;可能得原因建议得检査得方法与对策A、进入料筒得原料颗粒温度太低或不均匀造成所II得熔化时间加长。
A1.检査干燥机得运转就是否正常:干燥温度(原料所II得),空气流*与原料在料斗停留得时间。
A2、检査在料斗中就是否有原料流动•绿色通道冷B、原料得熔点太高。
B\通过观察原料颗粒得变色来检査就是否原料有降解。
B2、通过DSC分析来检査在出现在4.4、短射A在一个完全得注塑成型过程中,充填瓶坯不够完全。
这种缺陷通常可在瓶坯颈部区域得螺纹部分观察到,另外短射也可引起瓶坯重*得减少。
5.长浇口点出瓶坯得长浇口点表现在浇口痕迹处有突出得熔化物。
瓶坯常见异常原因分析报告

瓶坯常见异常原因分析报告瓶坯常见异常原因分析报告摘要: 瓶坯是瓶子的半成品,常见的异常包括外观缺陷(如凹痕、气泡、磨损等)、尺寸不良和材质问题。
本文将分析瓶坯常见异常的原因,包括生产工艺问题、原材料问题和设备问题等。
一、生产工艺问题1. 注射工艺不当:瓶坯一般是通过注射成型而成,如果注射的温度、压力和速度等参数不合适,容易造成瓶坯表面凸起、缺陷纹路等问题。
此外,注射模具的设计和加工精度也会影响瓶坯的质量。
2. 降温处理不当:瓶坯在注射成型后需要进行降温处理,如果降温温度、时间和速度等参数不合理,会导致瓶坯表面出现气泡、热裂等问题。
3. 吹瓶工艺不良:瓶坯在注射成型后需要进行吹塑工艺,如果吹瓶的温度、气压和模具的合适度不当,容易导致瓶坯外观不良、尺寸不稳定等问题。
二、原材料问题1. 原材料质量不过关:瓶坯常用的原材料为PET、PP等塑料,如果原材料质量不过关,含有杂质、水分过高或者掺假掺杂等,会直接影响瓶坯的质量。
2. 原材料配比不合理:瓶坯的制作需要对原材料进行混合和熔化,如果配比不合理,如熔体流动性不好、熔点过低等问题,会造成瓶坯质量不稳定。
三、设备问题1. 设备老化或损坏:生产瓶坯需要使用注射机、模具、冷却器等设备,如果设备老化或者损坏,会导致参数控制不稳定,直接影响到瓶坯的质量。
2. 设备操作不当:瓶坯生产的设备需要由专业操作人员进行操作,如果操作不当,例如温度设置不合理、清洁不彻底等问题,会导致瓶坯质量下降。
四、其他因素1. 环境因素:瓶坯生产过程中的温度、湿度和清洁度等环境因素对瓶坯的质量有一定影响,如温度过高容易导致瓶坯热变形,湿度过大容易导致材料吸湿,清洁度不好容易导致表面缺陷。
2. 人为因素:操作人员的技术水平和操作规范性也会影响到瓶坯的质量,如工人技术不过关、操作规范不强等,容易造成瓶坯质量问题。
综上所述,瓶坯常见的异常原因主要涉及生产工艺问题、原材料问题、设备问题以及环境和人为因素。
86-瓶胚常见缺陷分析及处理方法

瓶胚常见缺陷分析及处理方法1. 气泡.二由于注塑机内部的空气或产生的气体导致随机的气泡或空洞出现在瓶坯的侧壁上2. 凹痕••上凹痕是因热收缩在瓶坯的内表面或外表面形成的原料凹陷现象。
凹痕通常出现在瓶坯的厚壁部份和壁厚变化的地方。
B2.增加保压时间。
C.过高的熔化温度引起的过收缩。
C1.降低机器的加热温度。
C2.降低模具的加热温度。
D.模具冷却不够充分引起的过收缩。
D1.检查水冷却系统:水压,水流里和水温。
D2.检查模具的冷却水道有无污染或堵塞情况。
D3.增加瓶坯的冷却时间。
3. 未熔化物部份熔化或完全未熔化的原料颗粒出现在瓶身上可能的原因建议的检查的方法和对策A.进入料筒的原料颗粒温度太低或不 均匀造成所需的熔化时间加长。
A1.检查干燥机的运转是否正常: 干 燥温度(原料所需的),空气流量和 原料在料斗停留的时间。
A2.检查在料斗中是否有原料流动的“绿色通道”。
B.原料的熔点太高。
B1.通过观察原料颗粒的变色来检查 是否原料有降解。
B2.通过DSC 分析来检查在出现在瓶 坯上的未熔颗粒的熔点和结晶度。
C.原料颗粒尺寸大小超过标准或者不 均匀。
C1.检查原料颗粒是否有合适的尺寸 和均匀度。
4. 短射在一个完全的注塑成型过程中,充填瓶坯不够完全。
这种缺陷通常可在瓶坯颈部区域的螺纹部分观察到,另外短射也可引起瓶坯重量的减少。
5. 长浇口点亠土瓶坯的长浇口点表现在浇口痕迹处有突出的熔化物6. 拉长的浇口柱A瓶坯的拉长浇口柱表现为拉出的结晶痕迹7. 拉丝.?塑料细线或塑料绒毛突出在瓶坯的浇口点部分8. 水痕丄二径环出现在瓶坯的内径或外径表面上。
这种环通常表现为清晰的椭圆形皱纹。
9. 浇口结晶上-在瓶坯的浇口区域有白色晶体结构出现,通常可发现遍布整个瓶坯壁的横切面(左图),在瓶坯的内壁部分,接近型芯端盖的表面(中图),从瓶坯的浇口区域成条纹向坯身延伸(右图)。
B3.检查模具浇口模板的冷却水道是否有污染和堵塞。
瓶胚常见缺陷分析及处理方法(中文)
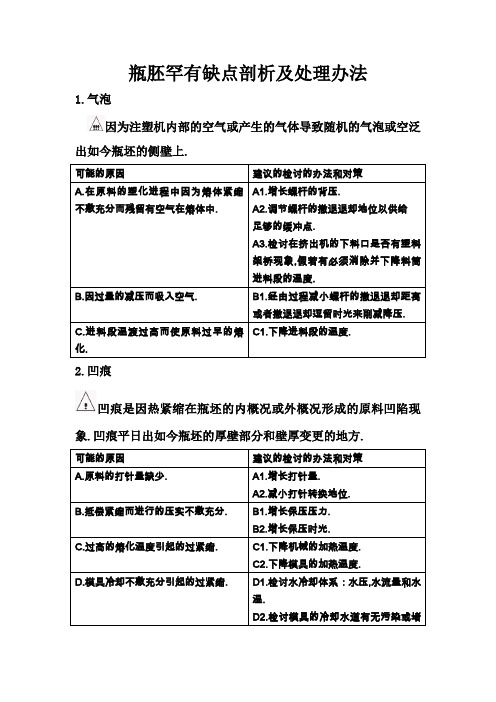
瓶胚罕有缺点剖析及处理办法1.气泡因为注塑机内部的空气或产生的气体导致随机的气泡或空泛出如今瓶坯的侧壁上.可能的原因建议的检讨的办法和对策A.在原料的塑化进程中因为熔体紧缩不敷充分而残留有空气在熔体中. A1.增长螺杆的背压.A2.调节螺杆的撤退退却地位以供给足够的缓冲点.A3.检讨在挤出机的下料口是否有塑料架桥现象,假若有必须消除并下降料筒进料段的温度.B.因过量的减压而吸入空气. B1.经由过程减小螺杆的撤退退却距离或者撤退退却逗留时光来削减降压. C.进料段温渡过高而使原料过早的熔化.C1.下降进料段的温度.2.凹痕凹痕是因热紧缩在瓶坯的内概况或外概况形成的原料凹陷现象.凹痕平日出如今瓶坯的厚壁部分和壁厚变更的地方.可能的原因建议的检讨的办法和对策A.原料的打针量缺少. A1.增长打针量.A2.减小打针转换地位.B.抵偿紧缩而进行的压实不敷充分. B1.增长保压压力.B2.增长保压时光.C.过高的熔化温度引起的过紧缩. C1.下降机械的加热温度.C2.下降模具的加热温度.D.模具冷却不敷充分引起的过紧缩. D1.检讨水冷却体系:水压,水流量和水温.D2.检讨模具的冷却水道有无污染或堵塞情形.D3.增长瓶坯的冷却时光.3.未熔化物部分熔化或完整未熔化的原料颗粒出如今瓶身上.可能的原因建议的检讨的办法和对策A.进入料筒的原料颗粒温度太低或不平均造成所需的熔化时光加长. A1.检讨湿润机的运转是否正常:湿润温度(原料所需的),空气流量和原料在料斗逗留的时光.A2.检讨在料斗中是否有原料流淌的“绿色通道”.B.原料的熔点太高. B1.经由过程不雅察原料颗粒的变色来检讨是否原料有降解.B2.经由过程DSC剖析来检讨在出如今瓶坯上的未熔颗粒的熔点和结晶度.C.原料颗粒尺寸大小超出尺度或者不平均. C1.检讨原料颗粒是否有适合的尺寸和平均度.4.短射在一个完整的注塑成型进程中,充填瓶坯不敷完整.这种缺点平日可在瓶坯颈部区域的螺纹部分不雅察到,别的短射也可引起瓶坯重量的削减.可能的原因建议的检讨的办法和对策A.原料打针量缺少. A1.增长原料的打针量.A2.减小打针转换地位.A3.增长保压时光.A4.增长保压压力.B.打针时光太长造成在足量的熔料被打针进模具前,缺料的瓶坯已经变冷变B1.增长打针速度. B2.增长打针压力.硬.C.原料粘度太高限制了熔体的充分流淌. C1.增长熔料温度来下降熔体的粘度. C2.检讨原料和瓶坯是否有适合的IV.D.熔体温度太低,流淌不充分. D1.增长模具支流道的温度.D2.增长模具注嘴尖的温度.5.长浇口点瓶坯的长浇口点表示在浇口陈迹处有凸起的熔化物.可能的原因建议的检讨的办法和对策A.模具打针口处的阀针封闭时,瓶坯浇口区域太冷. A1.增长模具注嘴尖的温度.A2.减小注嘴尖处阀针封闭延迟时光.B.阀针封闭不正常. B1.增长模具支流道的温度.B2.检讨驱动阀针的空气压力是否正常.B3.检讨拔出的阀门空气消声器是否有堵塞,若有必须清算或改换.B4.检讨在模具注嘴尖处是否存有外部原料,若有必须清算.B5.检讨模具注嘴尖是否破坏,如破坏须改换.B6.检讨模具阀针是否破坏,如破坏须改换.B7.检讨阀针活塞密封圈是否磨损,如磨损须改换.C. 原料黏度太高. C1.增长熔料温度来下降熔体的粘度.C2.检讨原料和瓶坯是否有适合的IV.D.熔体温度太低,流淌不充分. D1.增长模具支流道的温度.D2.增长模具注嘴尖的温度.6.拉长的浇口柱瓶坯的拉长浇口柱表示为拉出的结晶陈迹.可能的原因建议的检讨的办法和对策A.模具浇口区域过热引起浇口残根在模具打开动作进程中粘在模具浇口处. A1.检讨冷却水供应体系是否正常:水压,水流量和水温.A2.检讨模具浇口模板上的冷却水道是否有污染和堵塞情形,若有须清算. A3.下降注嘴尖的温度.A4.检讨以确保注嘴尖加热器衔接带与浇口模具板镶块没有接触.A5.增长模具冷却时光.B. 压实压力缺少以使浇口冷却器与瓶坯浇口慎密接触. B1.增长保压压力设定值,尤其是在后段.7.拉丝可能的原因建议的检讨的办法和对策A..瓶坯浇口点处过热使浇口残根在产品脱模进程中不克不及清洁的与模具分别. A1.下降注嘴尖温度.A2.下降模具支流道的温度.A3.检讨冷却水供应回路是否处于正常运转状况:水压,水流量,和水温. A4. 检讨模具浇口模板上的冷却水道是否有污染和堵塞情形,若有须清算. A5.增长模具冷却时光.A6.削减“阀针封闭延迟”时光.B. 阀针封闭不恰当. B1.增长模具支流道温度.B2.检讨阀针空气压力是否恰当.B3. 检讨拔出的阀门空气消声器是否有堵塞,若有必须清算或改换.B4.检讨在模具注嘴尖处是否存有外部原料,若有必须清算.B5.检讨模具注嘴尖是否破坏,如破坏须改换.B6.检讨模具阀针是否破坏,如破坏须改换.B7. 检讨阀针活塞密封圈是否磨损,如磨损须改换.C.模具打开后,瓶坯减压不恰当让熔料从浇口点处拉成细丝. C1.增长螺杆撤退退却行程以增长降压.C2.增长螺杆撤退退却逗留时光以增长降压.C3.减小保压压力.8.水痕径环出如今瓶坯的内径或外径概况上.这种环平日表示为清楚的卵形皱纹.可能的原因建议的检讨的办法和对策A.因为模具区域高的露点在模具概况形成凝集物,从而在型腔填充进程中引起熔料流的断裂. A1.检讨确认模具区域的空气露点低于模具冷却水的温度,假如须要的话调剂除湿体系.A2.增长模具冷却水的温度高于模具区域空气露点以防止水凝集(注:该调剂会解决凝集问题,但不被斟酌为最适合的解决办法,因为它可能会对瓶坯的整体质量以及模具周期有影响.9.浇口结晶在瓶坯的浇口区域有白色晶体构造消失,平日可发明普遍全部瓶坯壁的横切面(左图),在瓶坯的内壁部分,接近型芯端盖的概况(中图),从瓶坯的浇口区域成条纹向坯身延长(右图).可能的原因建议的检讨的办法和对策A.模具注嘴尖的温度在料流停止流淌这段时光太低. A1.增长模具注嘴尖温度. A2.减小熔料停止的时光.B.模具注嘴尖的温渡过高或者瓶坯浇口区域太热引起深度白雾(尤其在瓶坯的厚壁部分). B1.下降模具注嘴尖的温度.B2.检讨模具冷却水供应体系:水温.水流量.水压.B3. 检讨模具浇口模板的冷却水道是否有污染和堵塞.B4..检讨以确保注嘴尖加热器衔接带与浇口模具板镶块没有接触.B5.减小打针填充速度以减小注嘴尖/或浇口通道的熔体减切热.B6.确保在机械手掏出管中的瓶坯与球形底部接触.10.发雾瓶坯一种白云状外不雅不平均的分布在瓶坯身的遍地的现象.可成条放射性条纹状白环被看到(左图),也会局部性地出如今瓶坯的厚壁部分.(右图)可能的原因建议的检讨的办法和对策A.进入料筒的原料湿度太高引起在塑化进程中水解从而导致原料IV的下降,增长了原料的结晶速度. A1.检讨机械料筒喉咙部分原料的湿度(应小于50ppm).A2.检讨湿润机是否在适合的运转:度(原料请求的),气流,露点和原料在料斗中逗留的时光.B.进入料筒的原料温度太冷或者温度不平均导致需求的熔化时光增长. B1. 检讨湿润机是否在适合的运转:温度(原料请求的),气流,露点和原料在料斗中逗留的时光.B2.检讨在湿润料斗中是否有优先的料流渠道.C.在塑化进程中机塑机压力不敷导致剪切热的削减.C1.增长螺杆背压.11.熔接缝当前面的两股熔料流会聚而联合在一路时形成的细缝.前端的熔料没有完整粘在一路沿自身流淌偏向形成微细的缺口.熔料流径联合在瓶坯螺纹部分处常可不雅察到这个现象.可能的原因建议的检讨的办法和对策A.熔料流速过慢使前端的熔料流太冷而不克不及完整的粘在一路. A1.增长打针填充速度.A2.增长打针压力A3.增长保压速度A4.增长保压压力A5.增长模具冷却水温度以给前端熔料流的温度进行抵偿(注:该调剂会解决此问题,但不被斟酌为最适合的解决办法,因为它可能会对瓶坯的整体质量以及模具周期有影响.B.进入料筒的原料温度太冷或者温度不平均导致需求的熔化时光增长. B1.清算模具颈环及锁环排气槽.B2.检讨确保模具排气槽的尺寸和图纸尺寸一致.12.黑点/污染物降解物资(左图)或被打针进型腔的外部物资导致随机的颗粒消失坯身.可能的原因建议的检讨的办法和对策A.由降解的熔料产生黑色的颗粒. A1.下降模具注嘴尖的温度.A2.下降模具支流道的温度.A3.下降机械加热温度.A4.减小螺杆转速,后背压和打针速度来减小减切热.A5.使装备在预备启动前的升温加热时光尽量短.A6.在装备启动前先用新料清洗料筒和打针缸.确保所有的黑点和降解原料(变色的)被冲洗出来.(第一次清洗时增长打针量有助于消除活塞和打针缸之间的残留物.)B.进入料筒的原料温度太冷或者温度不平均导致需求的熔化时光增长. B1.清算模具颈环及锁环排气槽.B2.检讨确保模具排气槽的尺寸和图纸尺寸一致.13.飞边在临近的两块模具部件概况(如模具颈环/模具颈环,模具颈环/模具型腔,模具颈环/模具锁环)和之间形成的薄塑料凸起物.可能的原因建议的检讨的办法和对策A.因为过量的原料被打针进模腔,部分塑料被挤进合模面和排气槽. A1.减小打针量.A2.增长打针转换地位. A3.减小保压压力.A4.减小打针填充压力.B. 原料粘渡过低而流入模具合默面合排气槽. B1.减小模具支流道的温度.B2.减小机械加热温度.B3.装备启动进程中减小加热升温时光.B4.在打针进程中减小打针速度让前部的料流冷却.B5.检讨确保原料和瓶坯的IV值在尺度内(参考发雾瓶坯一节的具体描写)14.发黄瓶坯如下图所示的全部瓶坯发黄或变色.(左边和右边的瓶坯与中央的未变色瓶坯作比较)可能的原因建议的检讨的办法和对策A.过热引起的原料降解. A1.检讨湿润机是否恰当运转:湿润温度(原料须要的),空气流量和原料在湿润机中的逗留时光.A2.下降模具支流道的温度.A3.下降机械加热温度.A4.减小螺杆转速,背压和打针速度以减小料筒中的减切热.A5.使装备在预备启动前的升温加热时光尽量短.A6.在装备启动前先用新料清洗料筒和打针缸.确保所有的黑点和降解原料(变色的)被冲洗出来B. 原料粘渡过低而流入模具合默面合排气槽. B1.减小模具支流道的温度.B2.减小机械加热温度.B3.装备启动进程中减小加热升温时光.B4.在打针进程中减小打针速度让前部的料流冷却.B5.检讨确保原料和瓶坯的IV值在尺度内(参考发雾瓶坯一节的具体描写)15.壁厚过度不平均瓶坯的直径偏向四周厚度不平均(如下瓶坯骨干部位的横切面)可能的原因建议的检讨的办法和对策A.打针时因为填充压力过高使模具芯棒偏移. A1.下降打针填充压力. A2.下降打针填充速度. A3.下降保压压力.A4.下降保压时光.B. 打针时因为料流不平均使模具芯棒偏移. B1.检讨确保模具支流道加热设定和料筒加热设定接近(尤其是打针缸, 分派器和注嘴区域)以获得更好的熔料平均化.C.模具芯棒与型腔未校准. C1.检讨是否有磨损的模具部件.(如颈环,锁环,锥形型腔,导柱,导套等.)C2.检讨是否有破坏的芯棒.C3.检讨型芯和型腔是否瞄准.C4.从新校准芯模和型腔模.C5.检讨型芯冷却水管的地位和直度是否适合.C6.检讨型芯冷却水管和水道有无堵塞或污染.16.擦痕/概况瑕疵以椭圆瑕疵,刮痕情势消失的随机陈迹(左图),在瓶坯概况以纵向刮痕或不规矩外形现象消失的不规矩印痕或多重陈迹.可能的原因建议的检讨的办法和对策A.因为与某些物体接触造成的随机瑕疵. A1.尽量减小在从机械手顶出后瓶坯的处理和中转.A2.尽量减小瓶坯从机械手坠落到传输带的距离.A3.减小机械手的顶出压力.A4.增长冷却时光以减小瓶坯概况温度和遭遇印迹的迟钝性.B.因为模具概况受损或概况有外步碎片的聚积物造成反复消失的瑕疵.B1.检讨模具概况是否有毁伤(如小毛刺),若有须修复或改换.B2.检讨模具概况是否有外部碎片的积赘物.17.锯齿状分型线当瓶坯被拉出型腔时因为变形使瓶坯上颈环/型腔分型面处的外径上消失一个渺小的环状凹口,也伴着外浇口概况变形(浇口窝)消失.可能的原因建议的检讨的办法和对策A.因为过大的压力造成瓶坯粘在模具型腔里. A1.下降保压压力.A2.增长打针转换地位. A3.下降打针量.B.因为降压不敷造成瓶坯粘在模具型腔里.B1.增长螺杆撤退退却行程以增长降B2.增长螺杆撤退退却逗留时光以增压.B3.保压后延长注嘴口阀门打开时光.C.因为紧缩不敷造成瓶坯粘在模具型腔里. C1.增长瓶坯冷却时光.C2.检讨水冷却体系:水压.水流量. 和水温.C3.检讨模具冷却水道是否有污染和堵塞情形.18.浇口窝当瓶坯被拉出型腔时因为变形使浇口外概况凹陷.也伴着颈环/型腔分型面处变形(锯齿分型线)消失.可能的原因建议的检讨的办法和对策A.因为过大的压力造成瓶坯粘在模具型腔里. A1.下降保压压力.A2.增长打针转换地位. A3.下降打针量.B.因为降压不敷造成瓶坯粘在模具型腔里.B1.增长螺杆撤退退却行程以增长降B2.增长螺杆撤退退却逗留时光以增压.B3.保压后延长注嘴口阀门打开时光.C.因为紧缩不敷造成瓶坯粘在模具型腔里. C1.增长瓶坯冷却时光.C2.检讨水冷却体系:水压.水流量. 和水温.C3.检讨模具冷却水道是否有污染和堵塞情形.19.浇口脱皮一块从浇口点开端向外到半球基部扯破的断片粘附在模具浇口板概况(看起来象是一个桔子剥皮),扯破的断片会保持粘附在模具上很多个轮回周期,这就导致后来成型的瓶坯上形成扯破的陈迹.可能的原因建议的检讨的办法和对策A.模具浇口构件磨损使阀针和浇口垫板之间的间隙增大造成瓶坯底部注点不克不及完整的割断. A1.检讨模具阀针尖和浇口垫镶块是否有磨损,若有须改换...B.熔料压力过高或不准确的阀针封闭使阀针和模具浇口垫板之间的间隙中有凝固的残料造成瓶坯浇口注点不克不及完整与模具分别. B1.增长模具注嘴尖温度来熔化瓶坯浇口处残料以达到尽早分别浇口注点和使阀针准确封闭的目标.B2.减小保压压力以减小冷却速度和减小熔料在注嘴尖区域的压力.B3.经由过程增长螺杆撤退退却行程留时光的方法增长降压以减小冷却速率和减轻注嘴尖区域熔料的压力.20.内浇口变形瓶坯浇口区域尤其在浇口注点以下薄壁部分热紧缩引起原料在瓶坯底部内概况原料凹陷.可能的原因建议的检讨的办法和对策A.抵偿热紧缩的压力缺少. A1.增长保压压力A2.增长保压时光.B.熔体温渡过高引起的过量热紧缩. B1.下降机械加热温度.B2.下降模具加热温度.C.模具冷却不敷引起的过量热紧缩C1.检讨水冷却体系:水压,水流,和水温.C2.检讨模具冷却水道有无污染和堵塞情形.C3.增长瓶坯冷却时光.D1.减小螺杆撤退退却地位或螺杆撤D.熔体因为过大的轻易降压造成瓶坯上未冷却的熔体被吸回到注嘴尖.留时光以减小降压.21.焦痕在瓶坯的浇口区域(左图)常可发明的黑色或棕褐色未燃烧物,或在瓶坯的中部发明散开的印记(右图),这些印记是降解的原料被打针进型腔行成的.可能的原因建议的检讨的办法和对策A.由降解熔体引起的焦痕. A1.下降模具注嘴尖的温度.A2.下降模具支流道的温度.A3.下降机械加热温度.A4.减小螺杆速度,背压和打针速度以减小剪切热.A5.使装备启动前的加热升温时光尽可能段短.A6.B.熔体温渡过高引起的过量热紧缩. B1.下降机械加热温度.B2.下降模具加热温度.C.模具冷却不敷引起的过量热紧缩C1.检讨水冷却体系:水压,水流,和水温.C2.检讨模具冷却水道有无污染和堵塞情形.C3.增长瓶坯冷却时光.D.熔体因为过大的轻易降压造成瓶坯上未冷却的熔体被吸回到注嘴尖. D1. 在装备启动前先用新料清洗料筒和打针缸.确保所有的黑点和降解原料(变色的)被冲洗出来.(第一次清洗时增长打针量有助于消除活塞和打针缸之间的残留物.).22.瓶坯翘曲在顶出压力下瓶坯的躯干部被破坏,平日产生在瓶坯壁最厚和最热的部分.可能的原因建议的检讨的办法和对策A.不充分的模具冷却引起的翘曲. A1.检讨水冷却体系:水压,水流量和水温度.A2.检讨模具冷却水道有无污染和堵塞情形.A3.增长瓶坯冷却时光.B.抵偿热紧缩和恰当热量传递的压力缺少. B1.增长保压压力. B2.增长保压时光.C.熔体温渡过高引起过热紧缩和高的瓶坯温度. C1.下降机械加热温度. C2.下降模具加热温度.23颈圈白点两种在瓶坯颈圈上常发明的白点23.1在防盗环处消失的单个结晶点.(左图)23.2在支持环处消失的单个结晶点.(右图)可能的原因建议的检讨的办法和对策A.打针填充速度太慢造成前端的熔料流冷却产生结晶.A1.增长打针填充速度.B.打针填充时忽然的减速引起熔料流淌速度的减小. B1.减小打针转换地位. B2.增长第一段保压压力.C.熔体粘度太高导致料流速度的减小. C1.增长机械加热温度.C2.增长模具加热温度.C3.增长模具注嘴尖的加热百分比.C4.增长螺杆背压和螺杆速度来增长料筒中剪切热.瓶坯概况料流受到干扰,看起来象是因为熔体降解或气泡爆裂引起的纵向或者钩状银白色条纹从浇口流开.可能的原因建议的检讨的办法和对策A.过热的或降解的熔料被打针进型腔形成的喷射的印记. A1.下降模具注嘴尖的温度.A2.下降模具支流道温度.A3.下降机械加热温度.A4.减小螺杆速度,背压和打针速度以减小料筒中的螺杆剪切热.A5. 使装备启动前的加热升温时光尽可能短.A6. .在装备启动前先用新料清洗料筒和打针缸.确保所有的已降解原料(变色的)被冲洗出来.A7.检讨模具注嘴尖区域是否有损.25.浇口针孔在浇口注点处的有一个向浇口壁部分延长的小孔.(和浇口空泛有关系)可能的原因建议的检讨的办法和对策A.浇口区域过热引起浇口注点的熔料粘在阀针上. A1.检讨冷却水供应体系功效是否正常:水压,水流量,和水温.A2.检讨模具板冷却水道是否有污染和堵塞情形,若有须清算.A3.减小注嘴尖的温度.A4.检讨确保注嘴尖加热圈没有与浇口板嵌件接触.A5.增长模具冷却时光.B.阀针没有实时或正常封闭B1.调节保压后阀门打开准时.B2.增长模具支流道温度.B3.检讨阀针空气压力是否正常. 26.浇口空泛在瓶坯浇口注点下的壁厚部分有一个凹洞形成(右图).有可能与浇口的针孔有关系.可能的原因建议的检讨的办法和对策A.浇口区域过热引起紧缩过多. A1.检讨冷却水供应体系功效是否正常:水压,水流量,和水温.A2.检讨模具板冷却水道是否有污染和堵塞情形,若有须清算.A3.减小注嘴尖的温度.A4.减小熔体温度.A5. 检讨确保注嘴尖加热圈没有与浇口板嵌件接触.A6.增长模具冷却时光.B.模具浇口阀针没有实时或正常封闭. B1.调节保压后阀门打开准时(平日小).B2.增长模具支流道温度.B3.检讨阀针空气压力是否正常. 27.色纹PET熔料和着色剂未完整融会在瓶坯概况消失色纹.可能的原因建议的检讨的办法和对策A.色彩和原料混杂不充分. A1.检讨色料定量单位是否和色料添加一致.A2.检讨着色剂在原估中是否普遍分布在原估中,假如须要运用一个色料预混杂器.A3.检讨色料添加剂管子的地位是否恰当,如不准确须改正.A4.检讨色料添加剂的平均度.B.原料塑化进程中熔料不敷平均. B1.增长螺杆背压.B2.增长增长螺杆转速.B3.增长料筒熔料温度,尤其是在计量段.B4.检讨在料筒的进料口处是否有塑料架桥现象,若有有须清算并下降料筒进料段的温度.28.过高的乙醛含量AA(乙醛)是因为PET原料的热降解形成的.AA产生的数目由成型加工前提和PET原料的热稳固性决议.在某些运用中,瓶坯中的AA含量必须保持一个最小值以免转变产品的味道,是以必须经由过程气相色谱以ppm或g/l为单位进行准时测量.(见图下)可能的原因建议的检讨的办法和对策A.过多的熔料降解造成AA形成量的增长. A1.减小料筒的加热温度.A2.减小模具温度.A3.减小螺杆转速和背压以减小剪切热.A4.减小打针速度以减小剪切热.A5.将螺杆缓冲点减小到最小(一般10到20mm).A6.减小加工周期时光以减小熔料在机械中的滞留时光.B.进入的原料颗粒温度太低造成在塑化进程中产生过多的剪切热. B1.增长料筒进料口处进入的原料温度(原料请求的温度一般160到180 ℃).29.过高的粘度降IV是一个表示PET聚合链平均长度的值,该值与原料的分子量成正比.IV直接关系到成型的瓶坯和瓶子的物理机能,是以任何的粘度下降对产品德量都是晦气的.IV可用熔体粘度计或溶剂测试办法以dl/g为单位测得.可能的原因建议的检讨的办法和对策A.进入的原料水分含量太高造成塑化进程中水降解从而导致原料的IV值损掉. A1.检讨机械进料口处原料水分含量值(应<50 ppm).A2.检讨湿润机运转是否正常:湿润温度(原料请求的),湿润空气流量,露点和原料在料斗中的逗留时光.B.过多的熔体降解造成PET分子链断裂的增长引起IV值的减小. B1.减小料筒的加热温度.B2.减小螺杆转速和背压以减小剪切热.B3.减小打针速度以减小剪切热.。
瓶胚常见质量缺陷的原因及检查和解决方法
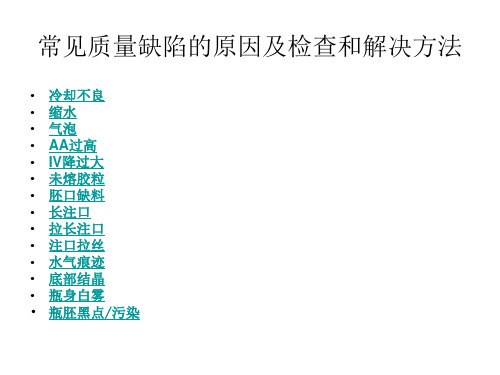
3、清理冷却系统 1、降低注嘴温度 1、增加注射量 2、加大保压时间和压力
1、拆模从新加紧运水管 1、减小机械手吸力 2、清理机械手吸筒
原因:焦痕
检查和解决方法: 1、温度太高 模温 1、减小注嘴温度、减小机温、 2、减小螺杆转速和背压 3、刚开机时减少加热时间 1、更换新注嘴隔热套和注嘴 1、更换注嘴 1、检查注嘴加热系统
4、阀针控制气阀失灵 5、抽胶不足 6、保压太大
原因:水气痕迹
检查和解决方法: 1、模具冷却水温太低 2、车间环境温度过高或湿 度过大造成模具结水珠 3、模具漏水 1、升高模具循环水温度 1、调低空调温度
原因:原因:
1、检查模具漏水原因及排除
原因:底部结晶
检查和解决方法:
1、注嘴温度过低或偏高 2、保压压力过大 3、冷却不良 1、升高或降低注嘴温度 1、减低保压压力第三级 1、检查冷却系统:压力、温度、流量 2、增加冷却时间 3、清理模具冷却系统 1、增加抽胶位置和时间 1、有无贴紧在注嘴上 1、检查并更换阀针注嘴
原因:缩水
检查和解决方法: 1、注射不充分 1、增加注射量 2、减小转换时间 3、增加保压压力和时间 2、冷却不良 1、检查水系统(压力、流量、温度) 2、检查模具水道(模芯分水管、模腔、) 3、增加冷却时间 3、温度太高 1、减小机温、模温 4、排气不良 1、检查排气孔 2、减小注射压力和速度 5、过度抽胶 1、减小抽胶位置和时间 6、由于填充过度引起机械变形 1、减小保压 7、阀针位置不对 1、保养热流道
• • •
• • •
原因:气泡
检查和解决方法 • 熔融性能问题 • 熔胶内有气泡-不足的背压压力的影响 • 在塑化过程中, 如果螺杆被允许轻易”跳后”, 那麽,就会出现熔体压力 的不稳定. • 这种不稳定的熔体压力导致在熔体内部出现间隙空间. • 这种间隙空间就会导致在熔体内产生气泡, 然后形成越来越大的气泡. • • • • • • • 熔胶内有气泡-过低的原料温度的影响 每个PET螺杆都有自己的独特的设计产量或输出率, 以 公斤/小时 (Kgs/hr)表示. 设计时,假设了一个特定的入料温度, 或能量数值. Husky PET螺杆的设计师在设计时, 假设的入料温度范围为155 ℃ 170 ℃. 当入料温度太低时,就必须从其它地方获得额外的能量, 比如, 炮筒发热 环, 机械剪切等. 随着机械剪切率的增大, 熔体的不稳定性和滑动就会发生.熔体压力的 变化, 将导致气泡的产生.
瓶胚常见缺陷项目分析处理步骤
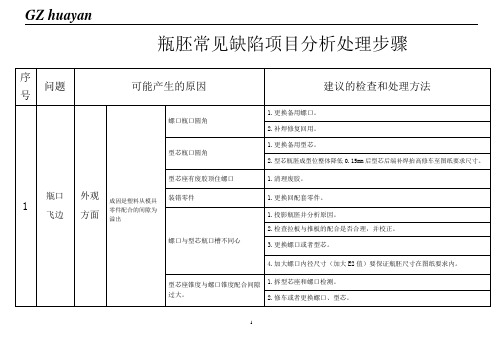
型芯座高度与推板拉板厚度配合尺寸不好。
1.检测推板厚度+拉板厚度是否比型芯座高度低0.02~0.06mm。
2.磨推板,推板+拉板厚度比型芯座高度低0.05~0.10mm。
型芯座不同心顶住拉板推板
1.更换型芯座.
2.修车型芯座.
锥度配合间隙过大
2.检查螺口锥与型芯座锥配合是否过紧,标准件有0.03~0.06mm间隙。
如果是修车零件或者更换零件。
螺口与型腔接合处有异物顶住
1.清理异物。
装错零件
1.更换回配套零件。
尺寸方面
螺口、型腔台阶尺寸没按图纸
要求加工到位或者设计错
1.检测螺口、型腔是否按要求加工。
2.修车零件尺寸至一至或者更换合格的零件。
1.增加模具喷嘴温度。
2.降低熔体停滞时间。(也就是,机械被动时间)
模具喷嘴的熔体温度或者瓶胚区域太热
导致深白模糊状(特别在瓶胚壁厚部分)。
1.降低模具喷嘴温度。
2.检查模具冷冻水供应的适当的运转:温度,流量和压力
3.检查模具浇口的水路的污染物和阻塞物。
4.检查确定模具喷嘴加热丝没有接触浇口垫嵌入物
3.降低喷嘴的温度。
4.检查来确定喷嘴加热丝没有接触喷嘴嵌入物。
5.增加模具冷却时间。
压紧压力不足以通过紧密的
接触促进浇口快速冷却
1.增加保压压力,特别是末端区域。
二合一变形
1.检测瓶胚是否抛变形,如果是更换螺口、型腔。
限位板顶住冷模导至模具合不紧
1.检测螺口发兰厚度+型腔发兰厚度+拉板厚度+铜板厚度-导向板厚度=
限位尺寸再负0.04~0.06mm。
瓶坯缺陷分析及解决建议
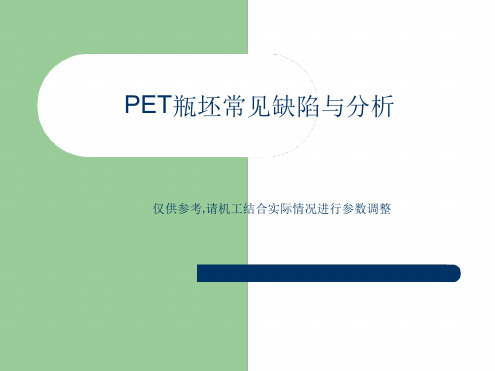
缺陷种类及解决建议
● 雾状瓶坯浑浊白色的外观蔓延整个瓶坯体。可观察到径向条痕白色的环 (左图)。也可局部地出现在厚壁部分(右图)。
? ★ 可能造成的原因: ? A 熔化的树脂潮湿的级别太高导致
在塑化过程的水解,结果是料温的 丢失和结晶率的增加。
? B 进入的树脂温度太低或不均匀导 致熔 浇口成窝浇口外部凹陷由于脱离型腔时发生变形。
? ★ 可能造成的 原因:
? A 由于注射量 不充足,保压 的时间不足以 令瓶坯均匀收 缩。
? B 瓶胚粘住模 腔由于不充分 的减压。
? C 瓶胚粘住模 腔由于不足够 的收缩。
? ★ 解决方法: (供技术员参 考)
? A 增加保压压 力和保压时间, 缩短位置转换 行程。
是否正常;检查电磁阀是否卡住;检 查射嘴是否损坏;检查阀针是否损坏; 检查气缸活塞密封圈是否损坏或磨损。
缺陷种类及解决建议
●拉长或拉空浇口 瓶坯拉长的浇口出现白色的晶体状或中间出现空心
? ★ 可能造成的原因: ? A 在浇口区域过度的加热,使浇口切点粘
住阀针或型腔的浇口,导致开模时拉长。 ? B 保压压力或时间不足以通过型腔紧密接
缺陷种类及解决建议
●水痕(水环)半径状环出现在瓶坯的内径和外径表面,这些环通常可以清 楚观察到椭圆形的隆起线。
? ★ 可能造成的原因: ? 模具成型表面疑结露珠,有
水分,导致填充模腔期间塑 料熔体被中断流动形成。 ? ★ 解决方法:(供技术员 参考) ? 检查成成型区域的大气露点 及模具的冷却水温度,有必 要时可调节除湿系统;增加 模具冷冻水温度高于模具区 域的大气露点来防止凝结 (注意:这种改变将能弥补 凝结问题,然而却没有考虑 出起因的合适的解决方案, 而且可能全面地影响瓶胚质 量和成型周期时间。)
瓶胚常见质量缺陷的原因及检查和解决方法
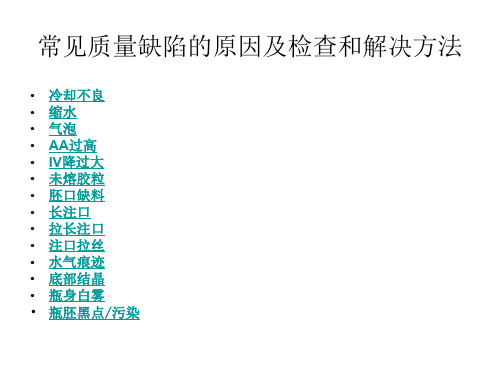
1、拆模从新加紧运水管 1、减小机械手吸力 2、清理机械手吸筒
原因:焦痕
检查和解决方法:
1、温度太高 模温
2、注嘴隔热套老化 3、注嘴损坏 4、注嘴加热失控
1、减小注嘴温度、减小机温、
2、减小螺杆转速和背压 3、刚开机时减少加热时间
1原料过度降解1降低机器温度在瓶胚产生白雾的前提下调高252降低模具温度28053降低螺杆转速和背压在质量前提下将背压设为400600psi螺杆塑化完成后到下一个塑化周期停留时间约4秒钟4减少螺杆输料余量1020mm5优化周期时间避免原料在螺杆停留时间过长而降2干燥效果不良1检查干燥机运行情况露点30干燥温度160180干燥时间56小时2检查干燥机是否正常保养干燥机检查干燥珠使用时间一般23年更换3原料存放时间过长1原料做到先进先出方法使用4瓶胚存放时间过长或仓1检查仓库的湿温度库境温度湿度过高2做好先进先出的库存方法5原料本身性能有问题1通知供应商处理检查和解决方法
2、减小转换位置 3、增大保压压力和时间 1、提高注射压力 1、加快注射速度(最佳注射时间为:10g/s) 1、增加机温模温和注嘴温度 1、更换注嘴、阀针、胶圈、高温套 2、检查气压和水口阀 1、清理模具排气孔
1、穿梭阀轴坏
原因:长注口
检查和解决方法:
1、由于注嘴区温度太低
关时间
2、热流道阀针气缸堵塞 3、保压太大
原因:瓶身白雾
检查和解决方法:
1、原料干燥不足或干燥不好 1、检查干燥机
2、原料太湿
1、检查原料水份
3、塑化不足
1、提高背压压力
2、增加螺杆转速
3、增加机温
4、增加螺杆缓冲位置
瓶胚常见缺陷分析及处理方法

瓶胚常见缺陷分析及处理方法1.气泡由于注塑机内部的空气或产生的气体导致随机的气泡或空洞出现在瓶坯的侧壁上。
可能的原因及建议的检查的方法和对策A.在原料的塑化过程中由于熔体压缩不够充分而残留有空气在熔体中。
A1.增加螺杆的背压。
A2.调节螺杆的后退位置以提供足够的缓冲点。
A3.检查在挤出机的下料口是否有塑料架桥现象,如果有必需清除并降低料筒进料段的温度。
B.因过量的减压而吸入空气。
B1.通过减小螺杆的后退距离或者后退停留时间来减少降压。
C.进料段温度过高而使原料过早的熔化。
C1.降低进料段的温度。
2.凹痕凹痕是因热收缩在瓶坯的内表面或外表面形成的原料凹陷现象。
凹痕通常出现在瓶坯的厚壁部份和壁厚变化的地方。
可能的原因及建议的检查的方法和对策A.原料的注射量不足。
A1.增加注射量。
A2.减小注射转换位置。
B.补偿收缩而进行的压实不够充分。
B1.增加保压压力。
B2.增加保压时间。
C.过高的熔化温度引起的过收缩。
C1.降低机器的加热温度。
C2.降低模具的加热温度。
D.模具冷却不够充分引起的过收缩。
D1.检查水冷却系统:水压,水流量和水温。
D2.检查模具的冷却水道有无污染或堵塞情况。
D3.增加瓶坯的冷却时间。
3.未熔化物部份熔化或完全未熔化的原料颗粒出现在瓶身上。
可能的原因及建议的检查的方法和对策A.进入料筒的原料颗粒温度太低或不均匀造成所需的熔化时间加长。
A1.检查干燥机的运转是否正常:干燥温度(原料所需的),空气流量和原料在料斗停留的时间。
A2.检查在料斗中是否有原料流动的“绿色通道”。
B.原料的熔点太高。
B1.通过观察原料颗粒的变色来检查是否原料有降解。
B2.通过DSC分析来检查在出现在瓶坯上的未熔颗粒的熔点和结晶度。
C.原料颗粒尺寸大小超过标准或者不均匀。
C1.检查原料颗粒是否有合适的尺寸和均匀度。
4.短射在一个完全的注塑成型过程中,充填瓶坯不够完全。
这种缺陷通常可在瓶坯颈部区域的螺纹部分观察到,另外短射也可引起瓶坯重量的减少。
瓶胚常见缺陷分析及处理方法(中文)

瓶胚常见缺陷分析及处理方法1.气泡由于注塑机内部的空气或产生的气体导致随机的气泡或空洞出现在瓶坯的侧壁上。
可能的原因建议的检查的方法和对策A.在原料的塑化过程中由于熔体压缩不够充分而残留有空气在熔体中。
A1。
增加螺杆的背压.A2。
调节螺杆的后退位置以提供足够的缓冲点.A3.检查在挤出机的下料口是否有塑料架桥现象,如果有必需清除并降低料筒进料段的温度。
B.因过量的减压而吸入空气。
B1。
通过减小螺杆的后退距离或者后退停留时间来减少降压.C1.降低进料段的温度.C.进料段温度过高而使原料过早的熔化。
2.凹痕凹痕是因热收缩在瓶坯的内表面或外表面形成的原料凹陷现象。
凹痕通常出现在瓶坯的厚壁部份和壁厚变化的地方。
可能的原因建议的检查的方法和对策A。
原料的注射量不足. A1。
增加注射量。
A2.减小注射转换位置。
B。
补偿收缩而进行的压实不够充分。
B1。
增加保压压力。
B2。
增加保压时间。
C.过高的熔化温度引起的过收缩. C1。
降低机器的加热温度。
C2.降低模具的加热温度。
D.模具冷却不够充分引起的过收缩。
D1.检查水冷却系统:水压,水流量和水温。
D2.检查模具的冷却水道有无污染或堵塞情况.D3.增加瓶坯的冷却时间。
3.未熔化物部份熔化或完全未熔化的原料颗粒出现在瓶身上.可能的原因建议的检查的方法和对策A。
进入料筒的原料颗粒温度太低或不均匀造成所需的熔化时间加长。
A1。
检查干燥机的运转是否正常:干燥温度(原料所需的),空气流量和原料在料斗停留的时间.A2。
检查在料斗中是否有原料流动的“绿色通道”。
B。
原料的熔点太高。
B1.通过观察原料颗粒的变色来检查是否原料有降解。
B2.通过DSC分析来检查在出现在瓶坯上的未熔颗粒的熔点和结晶度.C.原料颗粒尺寸大小超过标准或者不均匀。
C1。
检查原料颗粒是否有合适的尺寸和均匀度。
4.短射在一个完全的注塑成型过程中,充填瓶坯不够完全.这种缺陷通常可在瓶坯颈部区域的螺纹部分观察到,另外短射也可引起瓶坯重量的减少.5。
瓶胚常见缺陷分析及处理方法
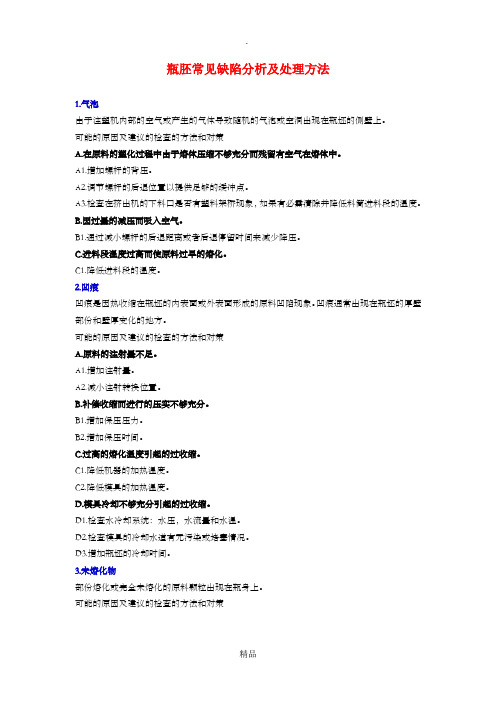
瓶胚常见缺陷分析及处理方法1.气泡由于注塑机内部的空气或产生的气体导致随机的气泡或空洞出现在瓶坯的侧壁上。
可能的原因及建议的检查的方法和对策A.在原料的塑化过程中由于熔体压缩不够充分而残留有空气在熔体中。
A1.增加螺杆的背压。
A2.调节螺杆的后退位置以提供足够的缓冲点。
A3.检查在挤出机的下料口是否有塑料架桥现象,如果有必需清除并降低料筒进料段的温度。
B.因过量的减压而吸入空气。
B1.通过减小螺杆的后退距离或者后退停留时间来减少降压。
C.进料段温度过高而使原料过早的熔化。
C1.降低进料段的温度。
2.凹痕凹痕是因热收缩在瓶坯的内表面或外表面形成的原料凹陷现象。
凹痕通常出现在瓶坯的厚壁部份和壁厚变化的地方。
可能的原因及建议的检查的方法和对策A.原料的注射量不足。
A1.增加注射量。
A2.减小注射转换位置。
B.补偿收缩而进行的压实不够充分。
B1.增加保压压力。
B2.增加保压时间。
C.过高的熔化温度引起的过收缩。
C1.降低机器的加热温度。
C2.降低模具的加热温度。
D.模具冷却不够充分引起的过收缩。
D1.检查水冷却系统:水压,水流量和水温。
D2.检查模具的冷却水道有无污染或堵塞情况。
D3.增加瓶坯的冷却时间。
3.未熔化物部份熔化或完全未熔化的原料颗粒出现在瓶身上。
可能的原因及建议的检查的方法和对策A.进入料筒的原料颗粒温度太低或不均匀造成所需的熔化时间加长。
A1.检查干燥机的运转是否正常:干燥温度(原料所需的),空气流量和原料在料斗停留的时间。
A2.检查在料斗中是否有原料流动的“绿色通道”。
B.原料的熔点太高。
B1.通过观察原料颗粒的变色来检查是否原料有降解。
B2.通过DSC分析来检查在出现在瓶坯上的未熔颗粒的熔点和结晶度。
C.原料颗粒尺寸大小超过标准或者不均匀。
C1.检查原料颗粒是否有合适的尺寸和均匀度。
4.短射在一个完全的注塑成型过程中,充填瓶坯不够完全。
这种缺陷通常可在瓶坯颈部区域的螺纹部分观察到,另外短射也可引起瓶坯重量的减少。
- 1、下载文档前请自行甄别文档内容的完整性,平台不提供额外的编辑、内容补充、找答案等附加服务。
- 2、"仅部分预览"的文档,不可在线预览部分如存在完整性等问题,可反馈申请退款(可完整预览的文档不适用该条件!)。
- 3、如文档侵犯您的权益,请联系客服反馈,我们会尽快为您处理(人工客服工作时间:9:00-18:30)。
瓶胚常见缺陷分析及处理方法1.气泡由于注塑机内部的空气或产生的气体导致随机的气泡或空洞出现在瓶坯的侧壁上。
可能的原因建议的检查的方法和对策A.在原料的塑化过程中由于熔体压缩不够充分而残留有空气在熔体中。
A1.增加螺杆的背压。
A2.调节螺杆的后退位置以提供足够的缓冲点。
A3.检查在挤出机的下料口是否有塑料架桥现象,如果有必需清除并降低料筒进料段的温度。
B.因过量的减压而吸入空气。
B1.通过减小螺杆的后退距离或者后退停留时间来减少降压。
C.进料段温度过高而使原料过早的熔化。
C1.降低进料段的温度。
2.凹痕凹痕是因热收缩在瓶坯的内表面或外表面形成的原料凹陷现象。
凹痕通常出现在瓶坯的厚壁部份和壁厚变化的地方。
可能的原因建议的检查的方法和对策A.原料的注射量不足。
A1.增加注射量。
A2.减小注射转换位置。
B.补偿收缩而进行的压实不够充分。
B1.增加保压压力。
B2.增加保压时间。
C.过高的熔化温度引起的过收缩。
C1.降低机器的加热温度。
C2.降低模具的加热温度。
D.模具冷却不够充分引起的过收缩。
D1.检查水冷却系统:水压,水流量和水温。
D2.检查模具的冷却水道有无污染或堵塞情况。
D3.增加瓶坯的冷却时间。
3.未熔化物部份熔化或完全未熔化的原料颗粒出现在瓶身上。
可能的原因建议的检查的方法和对策A.进入料筒的原料颗粒温度太低或不均匀造成所需的熔化时间加长。
A1.检查干燥机的运转是否正常:干燥温度(原料所需的),空气流量和原料在料斗停留的时间。
A2.检查在料斗中是否有原料流动的“绿色通道”。
B.原料的熔点太高。
B1.通过观察原料颗粒的变色来检查是否原料有降解。
B2.通过DSC分析来检查在出现在瓶坯上的未熔颗粒的熔点和结晶度。
C.原料颗粒尺寸大小超过标准或者不均匀。
C1.检查原料颗粒是否有合适的尺寸和均匀度。
4.短射在一个完全的注塑成型过程中,充填瓶坯不够完全。
这种缺陷通常可在瓶坯颈部区域的螺纹部分观察到,另外短射也可引起瓶坯重量的减少。
可能的原因建议的检查的方法和对策A.原料注射量不足。
A1.增加原料的注射量。
A2.减小注射转换位置。
A3.增加保压时间。
A4.增加保压压力。
B.注射时间太长造成在足量的熔料被注射进模具前,缺料的瓶坯已经变冷变硬。
B1.增加注射速度。
B2.增加注射压力。
C.原料粘度太高限制了熔体的充分流动。
C1.增加熔料温度来降低熔体的粘度。
C2.检查原料和瓶坯是否有合适的IV。
D.熔体温度太低,流动不充分。
D1.增加模具支流道的温度。
D2.增加模具注嘴尖的温度。
5.长浇口点瓶坯的长浇口点表现在浇口痕迹处有突出的熔化物。
可能的原因建议的检查的方法和对策A.模具注射口处的阀针关闭时,瓶坯浇A1.增加模具注嘴尖的温度。
口区域太冷。
A2.减小注嘴尖处阀针关闭延迟时间。
B.阀针关闭不正常。
B1.增加模具支流道的温度。
B2.检查驱动阀针的空气压力是否正常。
B3.检查插入的阀门空气消声器是否有堵塞,如有必须清理或更换。
B4.检查在模具注嘴尖处是否存有外部原料,如有必须清理。
B5.检查模具注嘴尖是否损坏,如损坏须更换。
B6.检查模具阀针是否损坏,如损坏须更换。
B7.检查阀针活塞密封圈是否磨损,如磨损须更换。
C.原料黏度太高。
C1.增加熔料温度来降低熔体的粘度。
C2.检查原料和瓶坯是否有合适的IV。
D.熔体温度太低,流动不充分。
D1.增加模具支流道的温度。
D2.增加模具注嘴尖的温度。
6.拉长的浇口柱瓶坯的拉长浇口柱表现为拉出的结晶痕迹。
可能的原因建议的检查的方法和对策A.模具浇口区域过热引起浇口残根在模具打开动作过程中粘在模具浇口处。
A1.检查冷却水供给系统是否正常:水压,水流量和水温。
A2.检查模具浇口模板上的冷却水道是否有污染和堵塞情况,如有须清理。
A3.降低注嘴尖的温度。
A4.检查以确保注嘴尖加热器连接带与浇口模具板镶块没有接触。
A5.增加模具冷却时间。
B.压实压力不足以使浇口冷却器与瓶坯浇口紧密接触。
B1.增加保压压力设定值,尤其是在后段。
7.拉丝塑料细线或塑料绒毛突出在瓶坯的浇口点部分。
可能的原因建议的检查的方法和对策A..瓶坯浇口点处过热使浇口残根在产品脱模过程中不能干净的与模具分离。
A1.降低注嘴尖温度。
A2.降低模具支流道的温度。
A3.检查冷却水供给回路是否处于正常运转状态:水压,水流量,和水温。
A4.检查模具浇口模板上的冷却水道是否有污染和堵塞情况,如有须清理。
A5.增加模具冷却时间。
A6.减少“阀针关闭延迟”时间。
B.阀针关闭不恰当。
B1.增加模具支流道温度。
B2.检查阀针空气压力是否恰当。
B3.检查插入的阀门空气消声器是否有堵塞,如有必须清理或更换。
B4.检查在模具注嘴尖处是否存有外部原料,如有必须清理。
B5.检查模具注嘴尖是否损坏,如损坏须更换。
B6.检查模具阀针是否损坏,如损坏须更换。
B7.检查阀针活塞密封圈是否磨损,如磨损须更换。
C.模具打开后,瓶坯减压不恰当让熔料从浇口点处拉成细丝。
C1.增加螺杆后退行程以增加降压。
C2.增加螺杆后退停留时间以增加降压。
C3.减小保压压力。
8.水痕径环出现在瓶坯的内径或外径表面上。
这种环通常表现为清晰的椭圆形皱纹。
可能的原因建议的检查的方法和对策A.由于模具区域高的露点在模具表面A1.检查确认模具区域的空气露点低形成凝聚物,从而在型腔填充过程中引起熔料流的断裂。
于模具冷却水的温度,如果需要的话调整除湿系统。
A2.增加模具冷却水的温度高于模具区域空气露点以防止水凝聚(注:该调整会解决凝聚问题,但不被考虑为最合适的解决办法,因为它可能会对瓶坯的整体质量以及模具周期有影响。
9.浇口结晶在瓶坯的浇口区域有白色晶体结构出现,通常可发现遍布整个瓶坯壁的横切面(左图),在瓶坯的内壁部分,接近型芯端盖的表面(中图),从瓶坯的浇口区域成条纹向坯身延伸(右图)。
可能的原因建议的检查的方法和对策A.模具注嘴尖的温度在料流停止流动这段时间太低。
A1.增加模具注嘴尖温度。
A2.减小熔料停滞的时间。
B.模具注嘴尖的温度过高或者瓶坯浇口区域太热引起深度白雾(尤其在瓶坯的厚壁部分)。
B1.降低模具注嘴尖的温度。
B2.检查模具冷却水供给系统:水温、水流量、水压。
B3.检查模具浇口模板的冷却水道是否有污染和堵塞。
B4..检查以确保注嘴尖加热器连接带与浇口模具板镶块没有接触。
B5.减小注射填充速度以减小注嘴尖/或浇口通道的熔体减切热。
B6.确保在机械手取出管中的瓶坯与球形底部接触。
10.发雾瓶坯一种白云状外观不均匀的散布在瓶坯身的各处的现象。
可成条放射性条纹状白环被看到(左图),也会局部性地出现在瓶坯的厚壁部分。
(右图)可能的原因建议的检查的方法和对策A.进入料筒的原料湿度太高引起在塑化过程中水解从而导致原料IV的降低,增加了原料的结晶速度。
A1.检查机器料筒喉咙部分原料的湿度(应小于50ppm)。
A2.检查干燥机是否在合适的运转:温度(原料要求的),气流,露点和原料在料斗中停留的时间。
B.进入料筒的原料温度太冷或者温度不均匀导致需求的融化时间增加。
B1.检查干燥机是否在合适的运转:温度(原料要求的),气流,露点和原料在料斗中停留的时间。
B2.检查在干燥料斗中是否有优先的料流渠道。
C.在塑化过程中机塑机压力不够导致剪切热的减少。
C1.增加螺杆背压。
11.熔接缝当前面的两股熔料流会聚而结合在一起时形成的细缝。
前端的熔料没有完全粘在一起沿自身流动方向形成微细的缺口。
熔料流径结合在瓶坯螺纹部分处常可观察到这个现象。
可能的原因建议的检查的方法和对策A.熔料流速过慢使前端的熔料流太冷而不能完全的粘在一起。
A1.增加注射填充速度。
A2.增加注射压力A3.增加保压速度A4.增加保压压力A5.增加模具冷却水温度以给前端熔料流的温度进行补偿(注:该调整会解决此问题,但不被考虑为最合适的解决办法,因为它可能会对瓶坯的整体质量以及模具周期有影响。
B.进入料筒的原料温度太冷或者温度不均匀导致需求的融化时间增加。
B1.清理模具颈环及锁环排气槽。
B2.检查确保模具排气槽的尺寸和图纸尺寸一致。
12.黑点/污染物降解物质(左图)或被注射进型腔的外部物质导致随机的颗粒出现坯身。
可能的原因建议的检查的方法和对策A.由降解的熔料产生黑色的颗粒。
A1.降低模具注嘴尖的温度。
A2.降低模具支流道的温度。
A3.降低机器加热温度。
A4.减小螺杆转速,后背压和注射速率来减小减切热。
A5.使设备在准备启动前的升温加热时间尽量短。
A6.在设备启动前先用新料清洗料筒和注射缸。
确保所有的黑点和降解原料(变色的)被冲洗出来。
(第一次清洗时增加注射量有助于清除活塞和注射缸之间的残留物。
)B.进入料筒的原料温度太冷或者温度不均匀导致需求的融化时间增加。
B1.清理模具颈环及锁环排气槽。
B2.检查确保模具排气槽的尺寸和图纸尺寸一致。
13.飞边在邻近的两块模具部件表面(如模具颈环/模具颈环,模具颈环/模具型腔,模具颈环/模具锁环)和之间形成的薄塑料突出物。
可能的原因建议的检查的方法和对策A.由于过量的原料被注射进模腔,部分塑料被挤进合模面和排气槽。
A1.减小注射量。
A2.增加注射转换位置。
A3.减小保压压力。
A4.减小注射填充压力。
B.原料粘度过低而流入模具合默面合排气槽。
B1.减小模具支流道的温度。
B2.减小机器加热温度。
B3.设备启动过程中减小加热升温时间。
B4.在注射过程中减小注射速度让前部的料流冷却。
B5.检查确保原料和瓶坯的IV值在标准内(参考发雾瓶坯一节的详细描述)14.发黄瓶坯如下图所示的整个瓶坯发黄或变色。
(左边和右边的瓶坯与中间的未变色瓶坯作比较)可能的原因建议的检查的方法和对策A.过热引起的原料降解。
A1.检查干燥机是否适当运转:干燥温度(原料需要的),空气流量和原料在干燥机中的停留时间。
A2.降低模具支流道的温度。
A3.降低机器加热温度。
A4.减小螺杆转速,背压和注射速度以减小料筒中的减切热。
A5.使设备在准备启动前的升温加热时间尽量短。
A6.在设备启动前先用新料清洗料筒和注射缸。
确保所有的黑点和降解原料(变色的)被冲洗出来B.原料粘度过低而流入模具合默面合排气槽。
B1.减小模具支流道的温度。
B2.减小机器加热温度。
B3.设备启动过程中减小加热升温时间。
B4.在注射过程中减小注射速度让前部的料流冷却。
B5.检查确保原料和瓶坯的IV值在标准内(参考发雾瓶坯一节的详细描述)15.壁厚过度不均匀瓶坯的直径方向周围厚度不均匀(如下瓶坯主干部位的横切面)可能的原因建议的检查的方法和对策A.注射时由于填充压力过高使模具芯棒偏移。
A1.降低注射填充压力。
A2.降低注射填充速度。
A3.降低保压压力。
A4.降低保压时间。
B.注射时由于料流不均匀使模具芯棒偏移。
B1.检查确保模具支流道加热设定和料筒加热设定接近(尤其是注射缸,分配器和注嘴区域)以获得更好的熔料均匀化。