模具材料热处理工艺和技术要求
模具的技术要求

装配过程中零件不允许磕、碰、划伤和锈蚀。
螺钉、螺栓和螺母紧固时,严禁打击或使用不合适的旋具和扳手。紧固后螺钉槽、螺母和螺钉、螺栓头部不得损坏。
规定拧紧力矩要求的紧固件,必须采用力矩扳手,并按规定的拧紧力矩紧固。
同一零件用多件螺钉(螺栓)紧固时,各螺钉(螺栓)需交叉、对称、逐步、均匀拧紧。
补焊前必须将缺陷彻底清除,坡口面应修的平整圆滑,不得有尖角存在。
根据铸钢件缺陷情况,对补焊区缺陷可采用铲挖、磨削,炭弧气刨、气割或机械加工等方法清除。
补焊区及坡口周围20mm以内的粘砂、油、水、锈等脏物必须彻底清理。
在补焊的全过程中,铸钢件预热区的温度不得低于350°C。
在条件允许的情况下,尽可能在水平位置施焊。
补焊时,焊条不应做过大的横向摆动。
铸钢件表面堆焊接时,焊道间的重叠量不得小于焊道宽度的1/3。
10.锻件要求:
每个钢锭的水口、冒口应有足够的切除量,一以保证锻件无缩孔和严重的偏折。
锻件应在有足够能力的锻压机上锻造成形,以保证锻件内部充分锻透。
锻件不允许有肉眼可见的裂纹、折叠和其他影响使用的外观缺陷。局部缺陷可以清除,但清理深度不得超过加工余量的75%,锻件非加工表面上的缺陷应清理干净并圆滑过渡。
轴承外圈与开式轴承座及轴承盖的半圆孔不准有卡住现象。
轴承外圈与开式轴承座及轴承盖的半圆孔应接触良好,用涂色检查时,与轴承座在对称于中心线120°、与轴承盖在对称于中心线90°的范围内应均匀接触。在上述范围内用塞尺检查时,0.03mm的塞尺不得塞入外圈宽度的1/3。
轴承外圈装配后与定位端轴承盖端面应接触均匀。
cr12热处理工艺及硬度
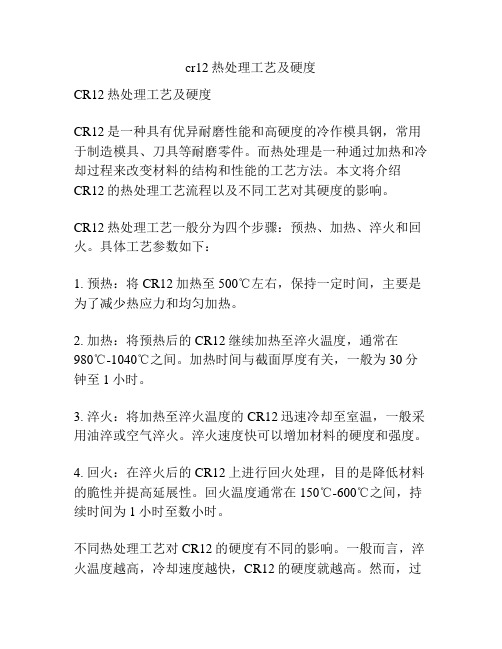
cr12热处理工艺及硬度CR12热处理工艺及硬度CR12是一种具有优异耐磨性能和高硬度的冷作模具钢,常用于制造模具、刀具等耐磨零件。
而热处理是一种通过加热和冷却过程来改变材料的结构和性能的工艺方法。
本文将介绍CR12的热处理工艺流程以及不同工艺对其硬度的影响。
CR12热处理工艺一般分为四个步骤:预热、加热、淬火和回火。
具体工艺参数如下:1. 预热:将CR12加热至500℃左右,保持一定时间,主要是为了减少热应力和均匀加热。
2. 加热:将预热后的CR12继续加热至淬火温度,通常在980℃-1040℃之间。
加热时间与截面厚度有关,一般为30分钟至1小时。
3. 淬火:将加热至淬火温度的CR12迅速冷却至室温,一般采用油淬或空气淬火。
淬火速度快可以增加材料的硬度和强度。
4. 回火:在淬火后的CR12上进行回火处理,目的是降低材料的脆性并提高延展性。
回火温度通常在150℃-600℃之间,持续时间为1小时至数小时。
不同热处理工艺对CR12的硬度有不同的影响。
一般而言,淬火温度越高,冷却速度越快,CR12的硬度就越高。
然而,过高的淬火温度和过快的冷却速度会引起内部应力和裂纹,降低材料的韧性和抗冲击性。
在实际应用中,CR12的硬度要根据具体需求进行选择。
过高的硬度可能导致材料易于产生裂纹,而过低的硬度则会影响其使用寿命和耐磨性能。
一般来说,CR12的硬度范围在58-64HRC之间,可以根据不同的工艺要求进行调整。
除了热处理工艺外,CR12的硬度还受其他因素的影响,如冷加工变形、化学成分、元素分布等。
因此,在进行CR12的热处理过程中,需要综合考虑工艺参数、材料性能和应用要求等因素,以获得最佳的硬度和性能组合。
总而言之,CR12的热处理工艺是一项关键的工艺,可以通过合理的预热、加热、淬火和回火过程来获得所需的硬度和性能。
通过不同的工艺参数和工艺控制,可以满足不同应用对CR12硬度的需求,提高材料的耐磨性能和使用寿命。
模具技术要求
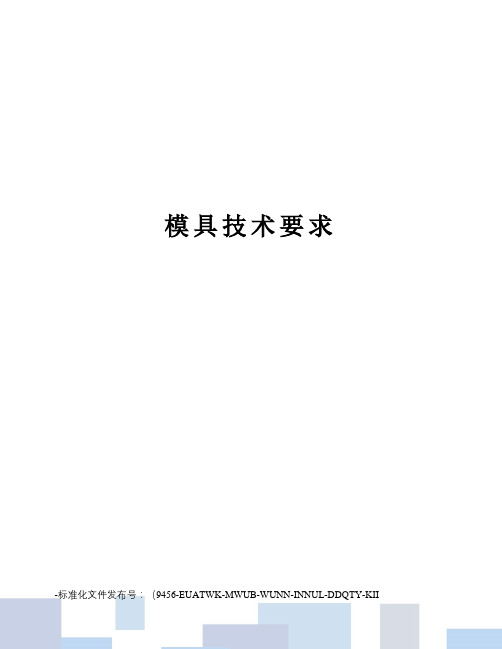
模具技术要求-标准化文件发布号:(9456-EUATWK-MWUB-WUNN-INNUL-DDQTY-KII模具技术要求一.模具材料及热处理要求1.拉延、成形类模具外板件拉延序凸模、凹模及压边圈使用GGG70L铸铁,淬火硬度HRC50-55;内板件凸模、凹摸及压边圈使用MoCr铸铁,淬火硬度HRC50-55。
特殊情况下须渗氮或TD处理(模具图纸会签时确认)。
变形剧烈及高强度钢板(抗拉强度≥350MPa)的制件应采用整体镶Cr12MoV;淬火硬度要达到HRC58—62。
基体采用HT300。
采用键槽与螺栓链接。
GGG70L铸件厂:天津虹岗或长城精工或经甲方认可的同等铸造品质铸造厂。
2.冲裁类模具普通板料零件料厚小于或等于1.2mm的刃口镶块可采用空冷钢(7CrSiMnMoV 或ICD-5),淬火硬度HRC55-60;料厚大于1.2mm的采用Cr12MoV材料,淬火硬度为HRC58~62。
料厚大于等于1.4mm的镶块采用波浪刃口。
高强度板的制件采用Cr12MoV材料,淬火硬度为HRC58~62。
所有凹模镶块、废料刀均采用背托,凹模采用镶块结构,凸模可采用整体结构。
模具基体采用HT300。
3.翻边、整形类模具中大型模具凹模镶块原则上应采用侧面固定式以便于调整;小型模具可采用整体式结构,料厚大于1.4mm的凹模采用镶块式。
零件料厚小于或等于1.2mm,材料可选用MoCr/7CrSiMnMoV;零件料厚大于1.2mm 的采用Cr12MoV或与之相当的材料(应取得甲方工艺认可,具体以会签为准)。
普通板料的制件凸模可采用合金铸铁,表面淬火硬度不低于HRC50;高强度板的制件采用Cr12MoV材料,淬火硬度为HRC58-62;如采用分体或镶块式基座(底板)可采用HT300的材料。
对于部分易拉毛部位,必要时需进行TD处理。
4.压料(退料)顶出器可采用铸造结构,但应根据其强度要求,决定用铸铁或球铁或铸钢材料(工艺会签时,甲方根据具体结构决定)。
dc53热处理技术要求
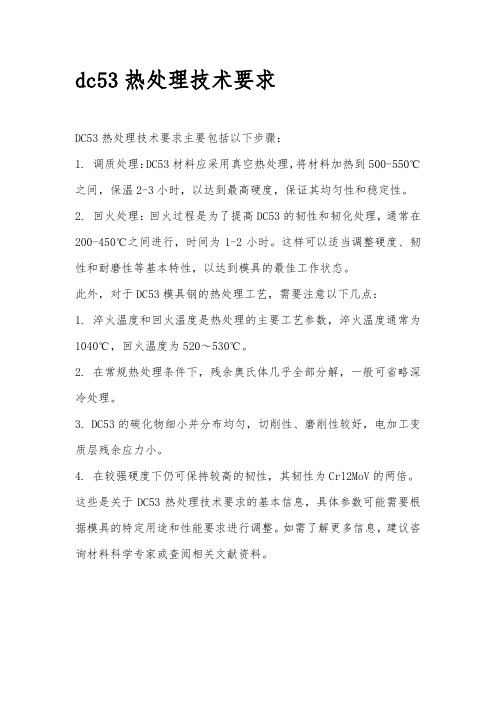
dc53热处理技术要求
DC53热处理技术要求主要包括以下步骤:
1. 调质处理:DC53材料应采用真空热处理,将材料加热到500-550℃之间,保温2-3小时,以达到最高硬度,保证其均匀性和稳定性。
2. 回火处理:回火过程是为了提高DC53的韧性和韧化处理,通常在200-450℃之间进行,时间为1-2小时。
这样可以适当调整硬度、韧性和耐磨性等基本特性,以达到模具的最佳工作状态。
此外,对于DC53模具钢的热处理工艺,需要注意以下几点:
1. 淬火温度和回火温度是热处理的主要工艺参数,淬火温度通常为1040℃,回火温度为520~530℃。
2. 在常规热处理条件下,残余奥氏体几乎全部分解,一般可省略深冷处理。
3. DC53的碳化物细小并分布均匀,切削性、磨削性较好,电加工变质层残余应力小。
4. 在较强硬度下仍可保持较高的韧性,其韧性为Crl2MoV的两倍。
这些是关于DC53热处理技术要求的基本信息,具体参数可能需要根据模具的特定用途和性能要求进行调整。
如需了解更多信息,建议咨询材料科学专家或查阅相关文献资料。
常用模具材料及热处理

常用模具材料及热处理常用的模具材料有许多种,每一种材料都具有独特的特点和适用范围。
而热处理则是在模具制造过程中必不可少的一步,可以提高材料的硬度、强度和耐磨性,从而提高模具的使用寿命。
以下是几种常用的模具材料和热处理方法。
一、常用的模具材料:1.铝合金:铝合金具有良好的导热性能和成型性能,重量轻,价格便宜。
适用于制造小型模具或高精度的塑料模具。
2.铝青铜:铝青铜具有良好的导热性能、耐磨性能和耐腐蚀性能,适用于制造高速冲压模和注塑模。
3.铜合金:铜合金具有良好的导热性能和热膨胀系数,适用于制造大型的冲压模和注塑模。
4.微晶玻璃钢:微晶玻璃钢具有高强度、耐磨性和抗腐蚀性能,适用于制造大型的冲压模和注塑模。
5.构造钢:构造钢具有高强度和耐磨性能,适用于制造大型的冲压模。
6.热作模具钢:热作模具钢具有优良的耐热性和抗热疲劳性能,适用于制造高温下工作的模具。
7.不锈钢:不锈钢具有良好的耐腐蚀性能和高温强度,适用于制造化学模具和食品模具。
二、热处理方法:1.淬火:淬火是常用的热处理方法之一,通过迅速冷却材料,使其获得高硬度和高强度。
淬火温度和冷却介质根据材料的不同而不同。
2.回火:回火是淬火后的一个步骤,通过加热材料到一定温度并保持一段时间,降低材料的硬度和脆性,提高其抗冲击性和韧性。
3.淬火回火:将材料先进行淬火然后回火的组合处理,既能获得高硬度也能提高韧性。
4.预淬火:预淬火是在热处理之前先进行一次淬火,然后再进行其他热处理工艺,可以提高热处理的效果。
5.淬火再回火:在完全淬火和回火的基础上,再进行一次淬火和回火,以进一步提高材料的性能。
6.等温淬火:将材料加热到一个特定温度并保持一段时间,然后进行快速冷却,可以使材料获得均匀细小的组织和高硬度。
7.渗碳:通过在材料表面渗入一定的碳元素,提高材料的表面硬度和耐磨性。
总结:常用的模具材料有铝合金、铝青铜、铜合金、微晶玻璃钢、构造钢、热作模具钢和不锈钢等。
热处理方法包括淬火、回火、预淬火、淬火回火、等温淬火、淬火再回火和渗碳等。
模具技术要求【范本模板】
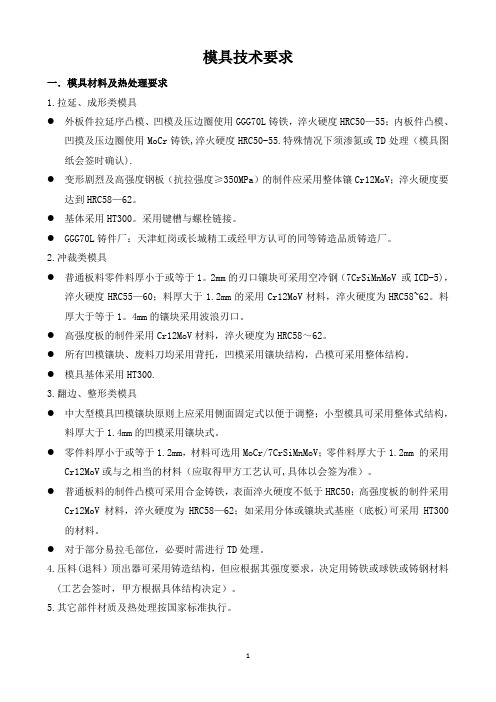
模具技术要求一.模具材料及热处理要求1.拉延、成形类模具●外板件拉延序凸模、凹模及压边圈使用GGG70L铸铁,淬火硬度HRC50—55;内板件凸模、凹摸及压边圈使用MoCr铸铁,淬火硬度HRC50-55.特殊情况下须渗氮或TD处理(模具图纸会签时确认).●变形剧烈及高强度钢板(抗拉强度≥350MPa)的制件应采用整体镶Cr12MoV;淬火硬度要达到HRC58—62。
●基体采用HT300。
采用键槽与螺栓链接。
●GGG70L铸件厂:天津虹岗或长城精工或经甲方认可的同等铸造品质铸造厂。
2.冲裁类模具●普通板料零件料厚小于或等于1。
2mm的刃口镶块可采用空冷钢(7CrSiMnMoV 或ICD-5),淬火硬度HRC55—60;料厚大于1.2mm的采用Cr12MoV材料,淬火硬度为HRC58~62。
料厚大于等于1。
4mm的镶块采用波浪刃口。
●高强度板的制件采用Cr12MoV材料,淬火硬度为HRC58~62。
●所有凹模镶块、废料刀均采用背托,凹模采用镶块结构,凸模可采用整体结构。
●模具基体采用HT300.3.翻边、整形类模具●中大型模具凹模镶块原则上应采用侧面固定式以便于调整;小型模具可采用整体式结构,料厚大于1.4mm的凹模采用镶块式。
●零件料厚小于或等于1.2mm,材料可选用MoCr/7CrSiMnMoV;零件料厚大于1.2mm 的采用Cr12MoV或与之相当的材料(应取得甲方工艺认可,具体以会签为准)。
●普通板料的制件凸模可采用合金铸铁,表面淬火硬度不低于HRC50;高强度板的制件采用Cr12MoV材料,淬火硬度为HRC58—62;如采用分体或镶块式基座(底板)可采用HT300的材料。
●对于部分易拉毛部位,必要时需进行TD处理。
4.压料(退料)顶出器可采用铸造结构,但应根据其强度要求,决定用铸铁或球铁或铸钢材料(工艺会签时,甲方根据具体结构决定)。
5.其它部件材质及热处理按国家标准执行。
二.模具结构及技术要求1.模具结构1。
8566模具钢热处理工艺

8566模具钢热处理工艺模具钢是指用于制造模具的钢种,其中8566模具钢是一种常见的模具钢种。
热处理是模具制造过程中不可或缺的一环,它直接影响模具的硬度、耐磨性、抗拉强度等性能。
本文将介绍8566模具钢热处理的工艺流程和注意事项。
一、工艺流程1.淬火淬火是将加热至适当温度的8566模具钢迅速浸入水中或油中,使其迅速冷却,以改善其硬度和耐磨性。
淬火温度一般为840-880℃,淬火介质根据要求可选择水或油。
淬火后的8566模具钢应迅速进行回火处理。
2.回火回火是将淬火后的8566模具钢加热至一定温度,然后冷却至室温,以消除淬火时产生的应力,提高其塑性和韧性。
回火温度一般为200-400℃,回火时间根据要求可选择1-2小时。
回火后的8566模具钢应进行表面处理。
3.表面处理表面处理是将回火后的8566模具钢进行打磨、抛光等处理,以提高其表面光洁度和使用寿命。
表面处理应根据模具的使用要求进行选择。
二、注意事项1.合理控制加热温度8566模具钢加热温度过高易造成晶粒长大,影响其力学性能。
加热温度过低又会导致淬火后的硬度不足。
因此,在热处理过程中应合理控制加热温度,以达到最佳的力学性能。
2.淬火介质的选择水的淬火速度快,能使8566模具钢的硬度和耐磨性得到提高,但易产生内应力,导致变形和裂纹。
油的淬火速度慢,能使8566模具钢的硬度和耐磨性得到提高,并且能减少内应力,但淬火效果不如水快。
因此,在选择淬火介质时应根据具体情况进行选择。
3.回火温度和时间的选择回火温度和时间的选择直接影响8566模具钢的塑性和韧性。
过高的回火温度会导致硬度下降,而过低的回火温度又会使应力得不到完全消除。
因此,在选择回火温度和时间时应根据具体情况进行选择。
4.表面处理的选择表面处理直接影响8566模具钢的使用寿命和表面光洁度。
不同的表面处理方法适用于不同的模具。
例如,电火花加工适用于高精度模具,而冷却水淬火适用于大型模具。
因此,在选择表面处理方法时应根据具体情况进行选择。
冲压模具金属材料及热处理工艺技术要点

冲压模具金属材料及热处理工艺技术要点摘要:冲压模具常用金属材料热处理工艺,需要严格控制各个环节质量,保证金属材料性能的基础上,经过热处理后经过冲压处理成为设备零部件,促进设备抗磨损与耐压性能提升,延长设备使用寿命。
但金属材料热处理过程中容易出现变形问题,变形严重时直接造成材料开裂,影响到材料质量,本文就此展开论述。
关键词:冲压模具;热处理工艺;技术控制1、冷冲压模具常用金属材料1.1碳素工具钢材料在我国碳素工具钢的产量非常大,使用也非常广泛。
这主要是因为碳素工具钢具备一些显而易见的优点:第一,可锻性好,方便锻造成所需的形状;第二、退火易软化,退火之后迅速软化,便于下一步的加工流程;第三、切削加工性好,因为碳素工具钢硬度小,非常容易进行切削处理;第四、价格便宜,这是决定碳素工具钢得以广泛使用的根本原因。
但同时,碳素工具钢也还存在许多不足之处,比如淬透性低,需额外通过水作为加工过程中的冷却剂,如此就会造成碳素工具钢发生更多的变形及断裂等问题。
因为碳素工具钢具备的这些优缺点,它适用的模具一般都具有这样的特点:尺寸较小,受力不大,形状较为简单,且对形状的变行要求不是很高,用碳素工具钢制作这样的模具,可以节省大量资源,但对于那些大受力、形状复杂、形状变形要求高的模具用碳素工具钢并不适合。
1.2高碳高铬模具钢材料与碳素工具钢相比,高碳高铬模具钢表现出了更好的淬硬性、淬透性、耐磨性,高碳高铬模具钢因为本身不容易发生变形等特性,被看作是高耐磨及微变形模具钢,高碳高铬模具钢要比高速钢在承载能力方面稍低。
高碳高铬模具钢的缺点是碳化物有比较严重的偏析问题,在实际冲压过程中必须对其反复进行改锻、镦拔,以逐步改善材料内碳化物的均匀水平,如此才会提升高碳高铬模具钢的使用性能。
1.3高速钢材料目前使用的高速钢,多是通过添加钼系元素等方式锻造出来的,高速钢因而具有非常优秀的使用性能,优势最明显的地方就是热塑性及强韧性都非常高,也因此获得非常大的发展空间,在冷作模具高精度及大批量工业化生产中,占有非常重要的地位。
模具材料及热处理新工艺新技术

模具材料及热处理新工艺新技术模具材料及热处理是现代制造业中非常重要的关键技术。
随着制造业的不断发展和进步,对模具材料和加工工艺的要求也越来越高。
新的工艺和技术在模具材料的选用和热处理工艺上有着重要的应用和意义。
下面将介绍一些模具材料及热处理新工艺新技术的应用和发展。
首先,关于模具材料的选用,传统的模具材料主要包括工具钢、冷作模具钢、高速钢等。
这些材料具有一定的硬度和耐磨性,但在一些特殊环境下存在一些问题。
例如,高速钢在高温条件下容易软化,而工具钢和冷作模具钢在高温应力作用下容易发生开裂。
因此,为了解决这些问题,一些新型模具材料开始被广泛应用。
新型模具材料主要包括硬质合金、陶瓷材料和复合材料等。
硬质合金具有高硬度、高强度和优异的耐磨性,广泛用于冲压模和挤压模等高磨损模具。
陶瓷模具材料具有优异的高温性能和化学稳定性,广泛用于注塑模、压铸模和玻璃模等高温环境下的模具。
复合材料具有优异的机械性能、耐磨性和抗腐蚀性能,广泛应用于塑料模具、铸造模具和压力机模具等。
其次,关于模具材料热处理工艺的发展,传统的热处理工艺主要包括淬火、回火和正火等。
然而,随着模具工艺的不断发展,传统的热处理工艺已经无法满足对模具材料性能的要求。
因此,一些新的热处理工艺开始被广泛应用。
新的热处理工艺主要包括表面改性技术和热处理参数优化技术等。
表面改性技术包括氮化、渗碳、氧化和涂层等。
这些技术能够在材料表面形成一层硬度高、耐磨性好和抗腐蚀性强的保护层,提高模具的使用寿命和工作性能。
热处理参数优化技术通过对热处理工艺参数的优化调整,可以使模具材料在保持高硬度的同时,具有更好的韧性和抗裂性能等。
总之,模具材料及热处理新工艺新技术在现代制造业中有着非常重要的应用和发展。
通过选用新型模具材料和优化热处理工艺参数,可以提高模具的使用寿命和工作性能,从而降低生产成本,提高生产效率。
随着制造业的不断发展和进步,模具材料及热处理新工艺新技术将会得到进一步的完善和应用。
p20模具钢热处理工艺

p20模具钢热处理工艺P20模具钢热处理工艺一、引言模具是工业生产中不可或缺的重要工具,而模具钢的热处理工艺对于模具的性能和寿命有着重要的影响。
P20模具钢是一种常用的模具钢材料,其具有优良的切削性能、硬度和耐磨性。
本文将探讨P20模具钢的热处理工艺,以期提高模具的使用寿命和性能。
二、工艺流程P20模具钢的热处理工艺主要包括退火、淬火和回火三个步骤。
以下将详细介绍每个步骤的具体工艺参数和操作方法。
1. 退火退火是为了消除材料内部的应力和组织缺陷,提高材料的韧性和可加工性。
P20模具钢的退火温度一般为780℃-820℃,保温时间为2-4小时。
退火后,需要将材料冷却至室温。
2. 淬火淬火是为了提高材料的硬度和耐磨性。
P20模具钢的淬火温度一般为850℃-880℃,保温时间为30分钟-1小时。
在保温结束后,将材料迅速冷却至室温,可以选择水淬、油淬或空气冷却等方式。
3. 回火回火是为了降低材料的脆性,提高材料的韧性和强度。
P20模具钢的回火温度一般为200℃-400℃,保温时间为2-4小时。
回火结束后,将材料冷却至室温。
三、工艺参数的选择与控制在进行P20模具钢的热处理工艺时,需要根据具体的模具形状和尺寸,选择合适的工艺参数。
以下是一些常用的参数选择与控制方法。
1. 温度控制在进行退火、淬火和回火过程中,温度的选择和控制非常重要。
过高的温度可能导致材料过度软化或烧损,而过低的温度则可能导致材料硬度不达标。
因此,需要根据材料的特性和要求,合理选择和控制温度。
2. 保温时间控制保温时间的选择和控制也是影响热处理效果的重要因素。
保温时间过短可能导致材料未完全转变组织,保温时间过长则可能导致材料的性能下降。
因此,需要根据实际情况,合理选择和控制保温时间。
3. 冷却方式选择淬火的冷却方式对于材料的硬度和组织结构有着重要的影响。
快速冷却可以使材料达到较高的硬度,但可能会导致材料出现裂纹和变形。
因此,需要根据具体要求和条件,选择合适的冷却方式。
模具的热处理

模具的热处理模具是工业生产中不可或缺的一种工具,它的质量直接影响到产品的质量和生产效率。
而模具的热处理是模具制造过程中不可或缺的一环,它可以提高模具的硬度、耐磨性和耐腐蚀性,从而延长模具的使用寿命。
本文将从模具的热处理原理、热处理工艺和热处理后的模具质量三个方面来介绍模具的热处理。
一、模具的热处理原理模具的热处理是指将模具加热到一定温度,然后在一定时间内保温,最后冷却到室温的过程。
热处理的目的是改变模具的组织结构和性能,从而达到提高模具硬度、耐磨性和耐腐蚀性的目的。
模具的热处理原理主要包括以下几个方面:1.相变原理:模具的热处理过程中,当温度达到一定值时,模具内部的晶体结构会发生相变,从而改变模具的性能。
2.固溶原理:模具的热处理过程中,将模具加热到一定温度,使其中的合金元素溶解在基体中,从而提高模具的硬度和强度。
3.析出原理:模具的热处理过程中,将模具加热到一定温度,使其中的合金元素析出在基体中,从而提高模具的硬度和耐磨性。
二、模具的热处理工艺模具的热处理工艺是指模具在热处理过程中所需要的温度、时间和冷却方式等参数。
不同的模具材料和要求需要不同的热处理工艺。
一般来说,模具的热处理工艺包括以下几个步骤:1.预热:将模具加热到一定温度,使其中的水分和氧化物等杂质挥发掉,从而减少模具表面的氧化和脱碳。
2.加热:将模具加热到一定温度,使其中的合金元素溶解在基体中或析出在基体中,从而提高模具的硬度和强度。
3.保温:将模具保持在一定温度下,使其中的合金元素充分溶解或析出,从而达到最佳的热处理效果。
4.冷却:将模具冷却到室温,使其中的合金元素固定在基体中,从而保持模具的硬度和耐磨性。
三、热处理后的模具质量模具的热处理后,其质量主要表现在以下几个方面:1.硬度:模具的硬度是指模具表面的抗压能力,硬度越高,模具的耐磨性和耐腐蚀性就越好。
2.耐磨性:模具的耐磨性是指模具表面的抗磨损能力,耐磨性越好,模具的使用寿命就越长。
模具热处理工艺

模具热处理工艺模具热处理是指将模具制造过程中的金属材料经过一定的加热、保温、冷却等工艺处理,以改善其组织性能和机械性能,以达到更高的使用寿命和更好的加工效果的目的。
模具热处理工艺是模具制造中非常重要的一个环节,对模具的质量、寿命和稳定性等方面均有着直接的影响。
本文将详细介绍模具热处理工艺。
模具热处理工艺主要分为常规热处理和表面处理两类。
1、常规热处理常规热处理是指对模具材料进行正火、淬火、回火等热处理工艺,使模具材料获得更优良的机械性能和耐磨性能,提高模具的使用寿命和稳定性。
常规热处理的工艺往往需要经过加热、保温、冷却等几个步骤,每一步的工序都需要严格控制温度、时间、冷却速度等参数,以达到理想的热处理效果。
2、表面处理表面处理是指对模具表面进行特殊处理,以提高其表面性能,如耐磨性、防腐性、硬度等等。
表面处理工艺有电镀、镀膜、喷涂、氮化等多种形式,每一种形式都有各自的工艺流程和特点,可以根据实际需要进行选择。
常规热处理主要包括正火、淬火和回火三个步骤。
1、正火正火主要是对模具材料进行加热,使其达到一定的温度,然后进行保温,使其结晶粗化、晶粒均匀化,以获得更高的硬度和强度。
正火的温度、时间、冷却速度等因素对热处理效果有着决定性的影响,需要进行严格的控制。
2、淬火淬火是将正火后的模具材料快速冷却,以使其组织结构发生相变,从而获得更高的硬度和强度。
淬火的冷却速度很快,一般采用水、油、盐水等淬火介质,以达到理想的淬火效果。
淬火后的模具材料仍然存在一定的脆性,需要进行回火处理。
3、回火回火主要是对淬火后的模具材料进行加热,温度一般在200-600度之间,然后进行保温,使其组织结构重新变得稳定,降低其硬度和强度,提高其韧性和抗冲击性,以减少其脆性,从而达到更好的使用效果。
表面处理工艺主要包括电镀、镀膜、喷涂、氮化等多种形式。
1、电镀电镀主要是通过电解沉积的方法,在模具表面形成一层金属膜,以提高模具表面的硬度、耐磨性和防腐性能。
模具热处理工艺技术规范
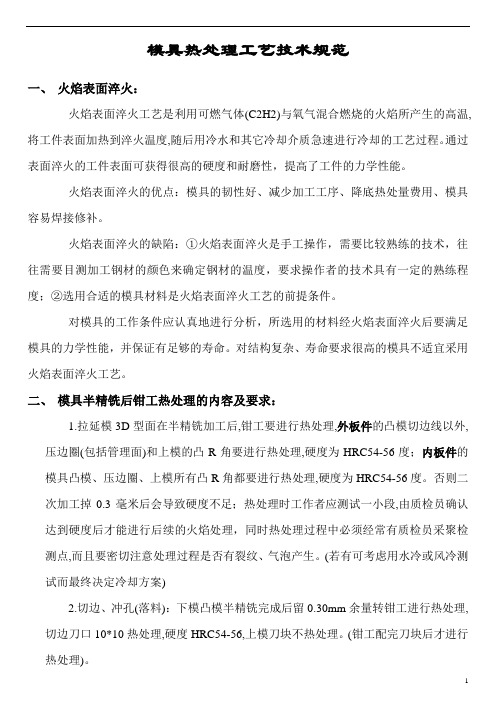
模具热处理工艺技术规范一、火焰表面淬火:火焰表面淬火工艺是利用可燃气体(C2H2)与氧气混合燃烧的火焰所产生的高温,将工件表面加热到淬火温度,随后用冷水和其它冷却介质急速进行冷却的工艺过程。
通过表面淬火的工件表面可获得很高的硬度和耐磨性,提高了工件的力学性能。
火焰表面淬火的优点:模具的韧性好、减少加工工序、降底热处量费用、模具容易焊接修补。
火焰表面淬火的缺陷:①火焰表面淬火是手工操作,需要比较熟练的技术,往往需要目测加工钢材的颜色来确定钢材的温度,要求操作者的技术具有一定的熟练程度;②选用合适的模具材料是火焰表面淬火工艺的前提条件。
对模具的工作条件应认真地进行分析,所选用的材料经火焰表面淬火后要满足模具的力学性能,并保证有足够的寿命。
对结构复杂、寿命要求很高的模具不适宜采用火焰表面淬火工艺。
二、模具半精铣后钳工热处理的内容及要求:1.拉延模3D型面在半精铣加工后,钳工要进行热处理,外板件的凸模切边线以外,压边圈(包括管理面)和上模的凸R角要进行热处理,硬度为HRC54-56度;内板件的模具凸模、压边圈、上模所有凸R角都要进行热处理,硬度为HRC54-56度。
否则二次加工掉0.3毫米后会导致硬度不足;热处理时工作者应测试一小段,由质检员确认达到硬度后才能进行后续的火焰处理,同时热处理过程中必须经常有质检员采聚检测点,而且要密切注意处理过程是否有裂纹、气泡产生。
(若有可考虑用水冷或风冷测试而最终决定冷却方案)2.切边、冲孔(落料):下模凸模半精铣完成后留0.30mm余量转钳工进行热处理,切边刀口10*10热处理,硬度HRC54-56,上模刀块不热处理。
(钳工配完刀块后才进行热处理)。
3.翻边、整型:凸模半精铣完成后留0.30mm余量转钳工进行热处理,硬度HRC54-56,侧面、整型面的工作面要进行热处理,上模刀块半精铣完成后留0.30mm 余量转钳工进行热处理,硬度HRC54-56。
三、模具材料及热处理硬度:⑴拉延模:板料厚度t≤1.2mm,凸、凹模及压边圈采用Mo-Cr合金铸铁(GM246或GM241),表面火焰处理,其硬度不低于HRC50。
热作模具材料及热处理热作模具材料及热处理

热作模具材料及热处理热作模具材料及热处理●热作模具主要用于高温条件下的金属成形,使加热的金属或金属获得所需要的形状。
●按用途可分为热锻模、热镦模、热挤压模、压铸模和高速成形模具等。
●通常在反复受热和冷却的条件下工作,变形加.上的时间越长,受热就越严重。
模具面温升常达300—700°C之间,要求有较高的热强性、热疲劳性和韧性,常选用中碳(wc=0.3%一0.6%)合金钢来制作。
第一节热作模具材料的主要性能要求●工作特点:热作模具是在机械载荷和温度均发生循环变化情况下工作的。
●热作模具材料分类:按照工作温度和失效形式不同,可将热作模具材料分为低耐热高韧性钢(350一370°C)、中耐热韧性钢(550—600°C)、高耐热钢(600—650°C)等。
有特殊要求的热作模具也可以采用奥氏体型耐热钢、高温合金或硬质合金,甚至是难熔合金来制造。
热作模具材料的使用性能要求●评价热作模具钢的性能指标:室温和高温使用条件下的硬度!强度!韧度等。
●热作模具材料使用时一般有七个方面的性能要求。
(1)硬度热作模具钢的硬度为40—52HRC。
通常模具钢的硬度取决于马氏体中的碳含量、钢的奥氏体化温度和保温时间。
应该指出的是:钢的最佳淬火温度要通过该钢的“淬火温度一晶粒度一硬度”关系曲线来选择。
马氏体中的二次硬化则与钢的合金化程度有关系,随着回火温度的升高,马氏体中的碳含量虽然降低,但如果特殊碳化物呈弥散析出并促使残余奥氏体转变成马氏体,则模具钢的高温硬度将会提高。
(2)强度强度是模具整个截面或某个部位在服役时抵抗静载断裂的抗力。
在压缩条件下工作的模具,可测试其抗压强度。
用拉伸试验测定一定温度下的抗拉强度σb,和屈服点σs,一般模具不允许发生永久的塑性变形,所以要求具有高的屈服强度。
而当模具钢的塑性较差时,一般不用抗拉强度而用抗弯强度σbb作为力学指标,抗弯试验产生的应力状态与许多模具工作表面所处的应力状态极其相似,能精确地反映构料的成分和组织对性能的影响。
模具钢的选材及热处理工艺
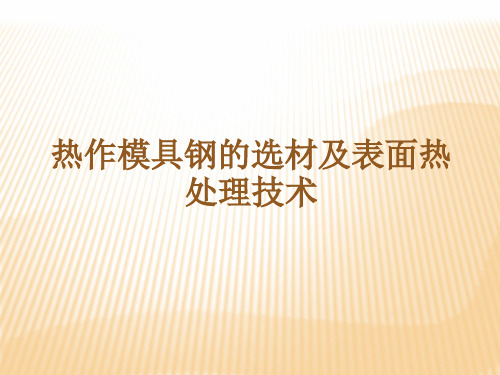
谢谢观看!
度最高,但是回火韧性最差,所以应避免在500℃附近回火。 (2)回火保温时间系数为3 min/mm,并且不能少于2h。 (3)两次回火,第二次回火比第一次回火温度低20℃。
铬系热作模具钢淬火后有一些残余奥氏体,一次回火后残余奥氏 体分解,其转变产物韧性差,比较脆,容易造成模具开裂,必须两次 回火。 (4)4Cr5MoSiV1钢在630 ℃高温回火后得到回火索氏体+回火托氏体。
4Cr5MoSiV1 3Cr2W8V 4CrMnSiMoV 5Cr4W5Mo2V
4Cr5MoSiV1 3Cr2W8V 3Cr3Mo3W2V
4Cr5MoSiV1 4Cr3Mo3SiV
3、压铸模具用钢的选用
压铸模具在服役条件下不断承受高速、高压喷射、金属的冲 刷腐蚀和加热作用,从总体上看,压铸模具用钢的使用性能要求 与热挤压模具用钢相近,即以要求耐磨性、高的回火稳定性与抗 热疲劳性为主。所以通常所选用的钢种大体上与热挤压模具用钢 相同。
热作模具在热处理时,尤其在淬火过程中,要产生体积、形状变化, 为保证模具质量,要求模具钢的热处理变形小,各方向变化相近似,且组 织稳定。它主要取决于热处理工艺和钢的冶金质量等。 (4)脱碳敏感性
热作模具如果在无保护气氛下加热,其表面会发生氧化、脱碳现象, 就会使其硬度、耐磨性、使用性能和使用寿命降低。因此,要求模具钢的 氧化、脱碳敏感性好。对于某些氧化、脱碳敏感性强的热作模具钢,可采 用特种热处理,如真空热处理、可控气氛热处理等。
Zn合金压铸模具:4Cr5MoSiV,4Cr5W2VSi钢等; Al和Mg合金压铸模具:4Cr5MoSiV1,3Cr3Mo3W2V钢等; Cu合金压铸模具:3Cr3Mo3W2V,3Cr2W8V钢。
模具的热处理

模具的热处理
模具热处理是模具制造中不可或缺的一环。
模具热处理主要是针对金属材料进行的一种加热和冷却处理,通过改变材料的组织结构和性能,从而达到提高模具耐磨性、延长使用寿命等目的。
模具热处理主要分为四个步骤:加热、保温、冷却和回火。
其中加热和冷却是最关键的两个步骤,也是决定加工效果的关键因素。
在加热过程中,要根据模具的材料、形状和尺寸来确定加热温度和时间。
通常情况下,加热温度会比材料的转变温度高出一定的范围,以确保材料充分加热并达到理想的组织结构。
同时,加热时间也要足够长,以确保整个模具达到相同的温度,从而避免热应力的产生。
保温阶段是为了让模具内部的温度充分均匀化和稳定化。
保温时间取决于模具的厚度和体积,通常情况下,保温时间为每毫米厚度需要1分钟。
在冷却阶段,要根据模具的材料和要求来选择冷却方式。
通常情况下,冷却方式有水淬、油淬、空气冷却等。
需要注意的是,冷却速度过快会使材料出现变形、裂纹等问题,因此冷却速度也需要适当控制。
回火是为了缓解模具在热处理过程中所产生的残余应力,使模具更加稳定和坚固。
回火温度和时间也需要根据材料的类型和要求来确
定。
在模具热处理过程中,需要严格控制各个环节的参数和工艺,以确保模具的质量和性能。
同时,还需要对热处理过程中产生的气体、污染物等进行处理,以保证环境的安全和健康。
模具热处理是模具制造中不可或缺的一环,通过合理的加热和冷却方式,可以改变模具的组织结构和性能,从而达到提高模具耐磨性、延长使用寿命等目的。
在实际操作中,需要严格控制各个环节的参数和工艺,以确保模具的质量和性能。
冷冲压模具的热处理工艺

冷冲压模具的热处理工艺冷冲压模具是一种常用于金属加工的模具,其中热处理工艺是冷冲压模具制造过程中非常重要的一步。
本文将详细介绍冷冲压模具的热处理工艺。
一、热处理的概念在冷冲压模具制造中,热处理是指采用一定的加热、保温、冷却等方法,将制作好的模具材料进行改善其内部组织结构的工艺。
简单来说,热处理可以使模具材料的性能更加稳定、硬度更加均匀、适应性更加广泛,提高模具的使用寿命和耐磨性能。
二、热处理的分类热处理通常分为三类,即退火、正火和淬火。
1.退火:退火是将模具材料加热到一定温度,保温一段时间,然后缓慢冷却的工艺。
退火可以改善模具材料的塑性和韧性,并且使其组织结构得到松弛与改善。
2.正火:正火是将模具材料加热到一定温度(通常高于910℃),保温一段时间,然后迅速冷却的工艺。
正火使模具材料的硬度得到大幅提高,但对于一些高温合金钢,正火不一定适用。
3.淬火:淬火是将模具材料加热到一定温度,保温一段时间,然后迅速浸入油、水等冷却介质中,使温度迅速降低,加速钢材的晶体转变和相变。
淬火可以使钢材达到极高的硬度,但如果淬火温度过高或时间过长,就会导致钢材出现裂纹或变形等缺陷。
三、冷冲压模具的热处理工艺冷冲压模具的热处理工艺通常分为两个阶段:预热和精炼。
1.预热:在制造冷冲压模具的过程中,首先需要将钢材进行预热。
预热的目的是去除材料表面的氧化物、炭化物等附着物,使表面变得光滑,并减少热应力。
预热时温度通常控制在300℃左右,保温时间大约为2小时。
2.精炼:在预热完成后,需要进行精炼工艺。
该工艺包括退火、正火和淬火三种方式,具体选择哪种方式要根据冷冲压模具的材料和具体使用环境来确定。
(1)退火热处理工艺:退火热处理工艺分为两种,分别是软化退火和回火处理。
软化退火是将模具材料加热到较高的温度(通常为800℃-900℃),保温一段时间,然后缓慢冷却的工艺。
软化退火可以改善模具材料的韧性,增强其可塑性,并改善其冷变性。
该工艺一般适用于硬度较高的钢材。
模具钢的热处理与表面处理技术

模具钢的热处理与表面处理技术一、预热处理预热处理是模具钢热处理的第一步,其主要目的是消除模具钢在锻造、铸造过程中产生的内应力,防止在后续的热处理过程中产生变形和裂纹。
预热处理通常采用高温回火或等温退火的方法进行。
二、锻造锻造是模具钢热处理的另一个重要步骤,其主要目的是通过改变模具钢的显微组织结构,提高其力学性能和抗冲击能力。
锻造过程中,模具钢的加热温度、变形程度和冷却速度都会对其最终的组织结构和性能产生重要影响。
三、退火退火是模具钢热处理中常用的一种方法,其主要目的是通过将模具钢加热到一定温度,保温一定时间,然后缓慢冷却,以获得理想的显微组织和机械性能。
退火过程中的加热温度和冷却速度对模具钢的性能有着重要影响。
四、淬火淬火是模具钢热处理中非常关键的一步,其主要目的是通过快速冷却,使模具钢的表面和心部同时达到临界点以下,获得马氏体组织,从而提高模具钢的硬度、强度和耐磨性。
淬火过程中的冷却速度对模具钢的显微组织和性能有着重要影响。
五、回火回火是模具钢热处理的另一个重要步骤,其主要目的是通过将模具钢加热到一定温度,保温一定时间,然后缓慢冷却,以调整模具钢的显微组织结构,提高其韧性和抗冲击能力。
回火过程中的加热温度和保温时间对模具钢的性能有着重要影响。
六、深冷处理深冷处理是模具钢热处理的一种方法,其主要目的是通过将模具钢冷却到零下70℃以下,提高模具钢的硬度、强度和耐磨性。
深冷处理过程中的冷却速度和冷却时间对模具钢的性能有着重要影响。
七、表面强化处理表面强化处理是模具钢热处理的一种方法,其主要目的是通过物理或化学手段,提高模具钢表面的硬度和抗磨性。
表面强化处理的方法有很多种,包括渗碳、渗氮、高频淬火等。
八、渗氮渗氮是模具钢表面强化处理的一种方法,其主要目的是通过将模具钢表面渗入氮元素,提高其表面的硬度和抗磨性。
渗氮处理后的模具钢具有较高的耐腐蚀性和耐磨性。
九、渗碳渗碳是模具钢表面强化处理的一种方法,其主要目的是通过将模具钢表面渗入碳元素,提高其表面的硬度和抗磨性。
2316模具钢热处理工艺
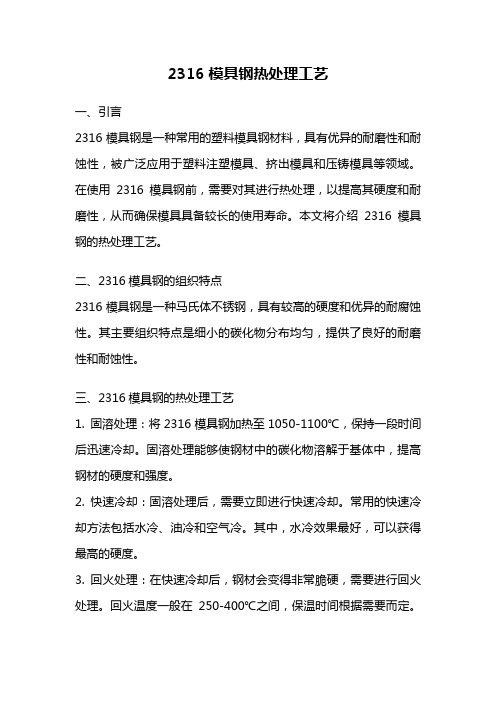
2316模具钢热处理工艺一、引言2316模具钢是一种常用的塑料模具钢材料,具有优异的耐磨性和耐蚀性,被广泛应用于塑料注塑模具、挤出模具和压铸模具等领域。
在使用2316模具钢前,需要对其进行热处理,以提高其硬度和耐磨性,从而确保模具具备较长的使用寿命。
本文将介绍2316模具钢的热处理工艺。
二、2316模具钢的组织特点2316模具钢是一种马氏体不锈钢,具有较高的硬度和优异的耐腐蚀性。
其主要组织特点是细小的碳化物分布均匀,提供了良好的耐磨性和耐蚀性。
三、2316模具钢的热处理工艺1. 固溶处理:将2316模具钢加热至1050-1100℃,保持一段时间后迅速冷却。
固溶处理能够使钢材中的碳化物溶解于基体中,提高钢材的硬度和强度。
2. 快速冷却:固溶处理后,需要立即进行快速冷却。
常用的快速冷却方法包括水冷、油冷和空气冷。
其中,水冷效果最好,可以获得最高的硬度。
3. 回火处理:在快速冷却后,钢材会变得非常脆硬,需要进行回火处理。
回火温度一般在250-400℃之间,保温时间根据需要而定。
回火处理可以减轻钢材的内应力,提高其韧性和塑性。
四、2316模具钢的热处理效果经过上述热处理工艺后,2316模具钢的硬度得到显著提高,耐磨性和耐蚀性得到增强。
同时,通过适当的回火处理,钢材的韧性和塑性也得到改善。
这些热处理效果使得2316模具钢在使用过程中具有更长的使用寿命和更好的性能表现。
五、2316模具钢热处理工艺的注意事项1. 温度控制:在进行热处理过程中,需要严格控制加热温度、保温时间和回火温度,以确保钢材的性能达到要求。
2. 冷却介质选择:不同的冷却介质对钢材的硬度和韧性有不同的影响,需要根据具体情况选择合适的冷却介质。
3. 热处理设备:热处理设备的性能和控制精度对热处理效果有重要影响,需要选择合适的设备进行处理。
六、结论2316模具钢是一种常用的塑料模具钢材料,经过适当的热处理工艺可以提高其硬度、耐磨性和耐蚀性。
热处理过程中需要控制好温度、时间和冷却介质,以获得理想的热处理效果。
- 1、下载文档前请自行甄别文档内容的完整性,平台不提供额外的编辑、内容补充、找答案等附加服务。
- 2、"仅部分预览"的文档,不可在线预览部分如存在完整性等问题,可反馈申请退款(可完整预览的文档不适用该条件!)。
- 3、如文档侵犯您的权益,请联系客服反馈,我们会尽快为您处理(人工客服工作时间:9:00-18:30)。
工具钢:用来制造各种工具的钢。根据工具用途不同可分为刃具钢、模具钢与量具钢。
特殊性能钢:是具有特殊物理化学性能的钢。可分为不锈钢、耐热钢、耐磨钢、磁钢等。
二. 按化学成分分类
按钢材的化学成分可分为碳素钢和合金钢两大类。
碳素钢:按含碳量又可分为低碳钢(含碳量≤0.25%);中碳钢(0.25%<含碳量<0.6%);高碳
等的残余应力。如果这些应力不予消除,将会引起钢件在一定时间以后,或在随后的切削加工过程中产
生变形或裂纹。
淬火 目的:提高机件强度及耐磨性。但淬火后引起内应力,使钢变脆,所以淬火后必须回火。 流程: 预热(500-550C)+(750—800C) 奥氏体化温度(1000—1050C) 保温 急冷 二.淬火时,最常用的冷却介质是盐水,水和油。盐水淬火的工件,容易得到高的硬度和光洁的表面, 不容易产生淬不硬的软点,但却易使工件变形严重,甚至发生开裂。而用油作淬火介质只适用于过冷奥 氏体的稳定性比较大的一些合金钢或小尺寸的碳钢工件的淬火。
此外,还有按冶炼炉的种类,将钢分为平炉钢(酸性平炉、碱性平炉),空气转炉钢(酸性转炉、
碱性转炉、氧气顶吹转炉钢)与电炉钢。按冶炼时脱氧程度,将钢分为沸腾钢(脱氧不完全),镇静钢(脱
氧比较完全)及半镇静钢。
钢厂在给钢的产品命名时,往往将用途、成分、质量这三种分类方法结合起来。如将钢称为普通碳
素结构钢、优质碳素结构钢、碳素工具钢、高级优质碳素工具钢、合金结构钢、合金工具钢等。
第1页共7页
2. 球化退火
球化退火主要用于过共析的碳钢及合金工具钢(如制造刃具,量具,模具所用的钢种)。其主要目的在于
降低硬度,改善切削加工性,并为以后淬火作好准备。
3. 去应力退火 (650—700C)
1H/25mm
去应力退火又称低温退火(或高温回火),这种退火主要用来消除铸件,锻件,焊接件,热轧件,冷拉件
模具材料热处理工艺
热处理----
我们用不同的加热--冷却的方法来改变钢的组织和性能的方法,就叫钢的热处理.
钢材的种类
钢是以铁、碳为主要成分的合金,它的含碳量一般小于 2.11% 。钢是经济建设中极为重要的金属材料。
钢按化学成分分为碳素钢(简称碳钢)与合金钢两大类。碳钢是由生铁冶炼获得的合金,除铁、碳为其
镀镍 目的:防腐蚀、美化验室 流程: 用电解方法,在钢件表面镀一层镍
镀铬 目的:提高表面硬度、耐磨性和耐蚀能力,也用于修复零件上磨损了的表面 流程: 用电解方法,在钢件表面镀一层铬
硬度 目的:检验材料经热处理后的力学性能---硬度 HB 用于退火、正火、 流程: 机件精加工前,加热到 100—150。C 后 保温 5---20H 空气冷却
主要成分外,还含有少量的锰、硅、硫、磷等杂质。碳钢具有一定的机械性能,又有良好的工艺性能,
且价格低廉。因此,碳钢获得了广泛的应用。但随着现代工业与科学技术的迅速发展,碳钢的性能已不
能完全满足需要,于是人们研制了各种合金钢。合金钢是在碳钢基础上,有目的地加入某些元素(称为
合金元素)而得到的多元合金。与碳钢比,合金钢的性能有显着的提高,故应用日益广泛。
第3页共7页
渗碳处理的选材 (二)渗碳表面硬化处理: 1.选材:低碳钢或低碳低合金钢 *低碳钢:S09CK、S15CK、S20CK *合金钢:SCr415、420;SCM415、418、420、421、822;SNCM220、415、420、616、815 *含碳量 0.15%之钢种,渗碳—淬火后母材内部硬度在 HRC30 以下,韧性较佳,含强度稍低。 *含碳量 0.20%之钢则硬度在 HRC30 以上,强度较高而韧性稍差。两者必须视其用途而区分,切勿混用。 2.加工程序: *粗加工→应力消除退火→精加工→渗碳→淬火→低温回火→精磨 3.渗碳—淬火处理及回火处理: *渗碳后必须扩散处理,将最表层含碳量降至约 0.8%,并将渗入之碳往内部扩散,以期缓和硬度分布曲 线之陡度,增加有效硬化层厚度。渗碳,扩散后,宜降温至 800~850℃出炉油淬至 100~150℃(碳钢) 或 150~200℃(合金钢),然后空冷至 50~60℃,适时送入回火炉(150~200℃)回火。 4.渗碳处理时间、厚度及硬化层性质: *渗碳处理时间视所需有效硬化层度而定,通常处理 1~10 小时,有效厚度 0.3 ㎜~㎜,最表层硬度均 在 HRC60 以上(合金钢 HRC61~62)。与渗氮处理比较,处理温度较高,且须淬冷,故变形量较大,表面 硬度也较低,耐磨耗性,耐热性,耐蚀性及耐熔蚀性等均较差;但其处理时间短,有效硬化层叫厚,能 承受较大之负载。 (三)渗氮(氮化)处理 1.选材:中碳合金钢或高碳合金钢。 *最常用之中碳合金钢为 SACM645 及 SKD61,高碳合金钢则为 SKD11、DC53、SKH51 等。SCM440 或 SNCM439 等中碳低合金钢也可以渗氮,但效果不佳。 *碳钢除了离子渗氮,不能作渗碳处理。 2.加工程序: *粗加工→应力消除退火→精加工→淬火→高温回火→精磨→渗氮处理→抛光 3.淬火—高温回火(调质): *渗氮处理件必须先施予调质(至该钢种合理之使用硬度),其回火温度必须高于渗氮处理温度。 *SACM645:HRC32~35、SKD61:HRC45~49、SKD11:HRC56~58,DC53:HRC58~61、SKH51:HRC62~64。 4.渗碳处理温度、时间、厚度及硬化层性质: *渗氮处理通常在 500~600℃温度范围进行,但必须稍低于母材调质时之回火温度,以免变形量加大。 常见之渗氮时间为 40~100 小时,可获有效硬化层厚度 0.02~0.3 ㎜。 渗氮层之最表层为氮化物层,硬度高达 HV1000 以上,但厚度仅为.010 ㎜(10μm)以下。最外层为ε— 氮化铁 Fe2-3N,较硬且脆;次层为γ’—氮化铁 Fe4N,较软较韧。氮化物层之内部为扩散层,最高硬度 达 HRC60 以上。 *渗氮层之硬度高、耐磨耗性、耐蚀性、耐热性(500℃以上才分解)、耐熔蚀性等均优于渗碳处理层, 处理温度较低且不需淬冷,故其变形量甚微;唯其处理时间较长,且有效硬化层厚度很薄,故不能承受 较大之负载。
退火 目的:用来消除铸\锻\焊零件的内应力,降低硬度,以利切削加工,细化晶粒,改善组织,增加韧性. 流程: 加热(650—700C) 保温 1H/25mm 随炉冷却 一.退火的种类 1. 完全退火和等温退火 完全退火又称重结晶退火,一般简称为退火,这种退火主要用于亚共析成分的各种碳钢和合金钢的铸, 锻件及热轧型材,有时也用于焊接结构。一般常作为一些不重工件的最终热处理,或作为某些工件的预 先热处理。
由于钢材品种繁多,为了便于生产、保管、选用与研究,必须对钢材加以分类。按钢材的用途、化学成
分、质量的不同,可将钢分为许多类:
钢材的种类
一、 按用途分类
按钢材的用途可分为结构钢、工具钢、特殊性能钢三大类。
结构钢:1、用作各种机器零件的钢。它包括渗碳钢、调质钢、弹簧钢及滚动轴承钢。
2、用作工程结构的钢。它包括碳素钢中的甲、乙、特类钢及普通低合金钢。
第2页共7页
轮。 流程: 用高频电流将零件表面加热 急速冷却
渗碳淬火 目的:提高机件表面的硬度及耐磨性、抗拉强度等适用于低碳、中碳(C〈0.4%)结构钢的中小型零件 流程: 将零件在渗碳剂中加热,使碳渗入钢的表面后 再淬火回火 渗碳深度:0.5—2mm
钢的氮化及碳氮共渗 钢的氮化(气体氮化) 概念:氮化是向钢的表面层渗入氮原子的过程,其目的是提高表面硬度和耐磨性,以及提高疲劳强度和 抗腐蚀性。 它是利用氨气在加热时分解出活性氮原子,被钢吸收后在其表面形成氮化层,同时向心部扩散。 氮化通常利用专门设备或井式渗碳炉来进行。适用于各种高速传动精密齿轮、机床主轴(如镗杆、磨床 主轴),高速柴油机曲轴、阀门等。
氮化 氮化工件工艺路线:锻造-退火-粗加工-调质-精加工-除应力-粗磨-氮化-精磨或研磨。 由于氮化层薄,并且较脆,因此要求有较高强度的心部组织,所以要先进行调质热处理,获得回火索氏 体,提高心部机械性能和氮化层质量。 钢在氮化后,不再需要进行淬火便具有很高的表面硬度大于 HV850)及耐磨性。 氮化处理温度低,变形很小,它与渗碳、感应表面淬火相比,变形小得多
淬火的方法
(一)物理冶金法
1.火焰淬火
2.高周波淬火
3.电子束淬火 4.雷射淬火
(二)化学冶金法
1.渗碳处理
2.渗碳氮化处理
3.渗氮碳化(软氮化)处理
4.渗氮(氮化)处理
5.离子渗氮处理
6.渗硫、渗硼处理
7.金属渗透处理(如渗铝、铬、钒等)
(三)被覆法
1.硬质金属(如ቤተ መጻሕፍቲ ባይዱ)
2.被覆熔焊
3.金属(陶瓷)熔射
三、选材及问题探讨
(一)高洲波表面淬火硬化
1.选材:
*中碳刚、中碳低和金刚、铸钢、铸铁等均可施予高周波表面硬化处理。
2.加工程序:
*粗加工→应力消除退火→精加工→淬火→高温回火→粗磨→预热→高周波加热淬火→低温回火→精磨
3.淬火—高温回火(俗称〝调质〞):
*常用钢种及其调质硬度
*S45C:HRC26±2,
4.爆炸被覆
(四)机械冶金法
1.珠击法
2.冷轧法
第5页共7页
二、选择表面硬化处理方法考虑因素: (1)选用之钢类种类—低碳刚、中碳刚、合金钢、工(模)具钢 (2)用途及寿限—负载、耐蚀、耐热…等级使用寿限 (3)尺寸及形状—大、小、细长、实心、空心…… (4)数量—大量生产、少量生产、或量少而种类多 (5)加工程序—含前加工、前处理及后续加工等 (6)公安环保—工业安全、环保卫生等公害问题 (7)成本与交货期—省钱、省工
钢
(含碳量≥0.6%)。
合 金 钢 : 按 合 金 元 素 含 量 又 可 分 为 低 合 金 钢 ( 合 金 元 素 总 含 量 ≤ 5% ); 中 合 金 钢 ( 合 金 元 素 总 含 量
=5%--10%);高合金钢(合金元素总含量>10%)。此外,根据钢中所含主要合金元素种类不同,也可分为