机床进给系统设计
CK6140数控车床进给系统设计(全套图纸+论文)

摘要CK6140型数控机床,主运动系统采用1.26和1.58两种公比的混合公比传动系统,并用双速电机驱动,结构简单转速范围广。
合理地确定有关结构参数及动力参数,并对传动轴、齿轮、键等进行粗算及检验计算。
粗选步进电机及滚珠丝杠,构成开环控制系统。
关键词:数控;机床;开环控制第1章绪论1.1数控机床的发展趋势我国数控机床产量持续高速增长,根据市场需求和技术发展趋势,应重点推进高效、精密为核心的数控机床“”级工程,加强民展性能、高可靠性数控功能部件,积极开展复合加工机床、超精密数控机床和可重构制造系统的工程化研究等机械加工装备产业、构建数字化企业的重要基础,镄的民展一直备受人们关注。
数控机床以其卓越的柔性的自动化的性能、优异而稳定的精度、灵捷而多样化的功能引起世人瞩目。
它开创了机械产品向机电一体化发展的先河,因此数控技术成为先进成为先进制造技术的一项核心技术。
通过持续的开发研究以及对信息技术的深化应用,促进了数控机床性能和质量的进一步提升,使数控机床成为国民经济和国防建设发展的重要制造装备。
近6年来,我国数控金切机床(简称数控机床)产量一直以年均增长超过30%速度发展。
据初步统计,2004年数控机床的产量为51860台,事比增长40.8%,数控机床的消费量约74000台,事比增长32%。
数控机床需求的旺盛也促进了2004年内建的三资和民营机床厂以及数控机床品种的明显增加。
与此同时,甸进口的数控机床数量也在逐年同步增加,而且进口数控机床的消费额的增长趋势更快。
2004年数控机床的进口数量同比年增长30%,而进口消费额的增长却达52%,从而导致国产数控机床在国内市场消费额中的所占比例已不足30%。
之所以出现这一现象,其主要原因在于国内市场对技术和附加值高的高效、精密和高性能大型、重型数控机床需求增长,需要靠进口解决。
振兴我国数控机床市场占有率应着重于剖析数控机床及由其组成的制造系统(生产线)的技术现况及民展趋势,探讨使其能适应变批量,多品种、高质量、低成本以及具有快速响应的柔性和符合环保的未来生产模式的解决方案。
立式数控铣床进给传动系统设计

课程设计任务书目录1.概述 (3)1.1技术要求 (3)1.2总体设计方案 (3)2.滚珠丝杠螺母副的选型和计算 (3)2.1主切削力及其切削分力计算 (3)2.2导轨摩擦力的计算 (4)2.3计算滚珠丝杠螺母副的轴向负载力 (4)2.4滚珠丝杠的动载荷计算与直径估算 (5)3.工作台部件的装配图设计 (9)4.滚珠丝杠螺母副的承载能力校验 (9)4.1滚珠丝杆螺母副临界压缩载荷的校验 (9)4.2滚珠丝杆螺母副临界转速的校验 (9)4.3滚珠丝杆螺母副额定寿命的校验 (10)5.计算机械传动系统的刚度 (10)5.1机械传动系统的刚度计算 (10)5.2滚珠丝杠螺母副扭转刚度的计算 (11)6.驱动电动机的选型与计算 (11)6.1计算折算到电动机轴上的负载惯量。
(11)6.2计算折算到电动机轴上的负载力矩 (12)6.3 计算坐标轴折算到电动机轴上的各种所需力矩 (13)6.4选择驱动电动机的型号 (14)7.确定滚珠丝杠螺母副的精度等级和规格型号 (14)7.1确定滚珠丝杠螺母副的精度等级 (14)7.2滚珠丝杠螺母副的规格型号 (15)8. 课程设计总结 (15)9.参考文献 (15)1.概述1.1技术要求工作台、工件和夹具的总质量m=918kg,其中,工作台的质量510kg;工作台的最大行程Lp=600 mm;工作台快速移动速度18000mm/min;工作台采用贴塑导轨,导轨的动摩擦系数为0.15,静摩擦系数为0.12;工作台的定位精度为30μm,重复定位精度为15μm;机床的工作寿命为20000h(即工作时间为10年)。
机床采用主轴伺服电动机,额定功率为5.5kw,机床采用端面铣刀进行强力切削,铣刀直径125mm,主轴转速310r/min。
切削状况如下:数控铣床的切削状况1.2总体设计方案为了满足以上技术要求,采取以下技术方案:(1)工作台工作面尺寸(宽度×长度)确定为400mm×1200mm。
数控车床纵向进给传动系统设计(含全套CAD图纸)
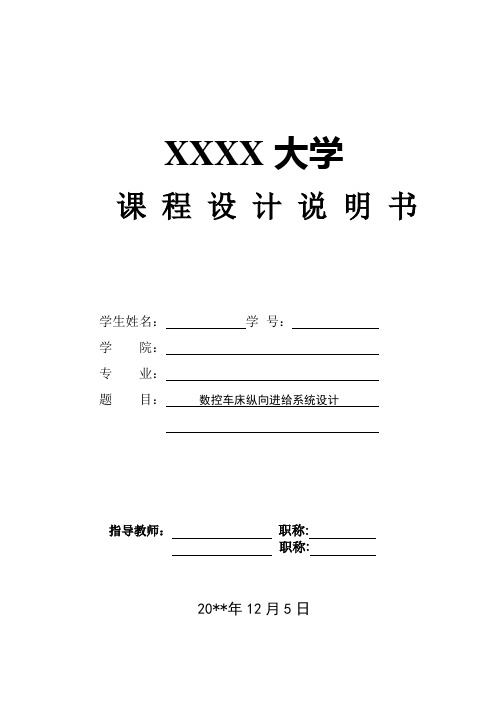
XXXX大学课程设计说明书学生姓名:学号:学院:专业:题目:数控车床纵向进给系统设计指导教师:职称:职称:20**年12月5日任务书学院专业班级学生:题目:数控车床纵向进给系统设计课程设计从20** 年12 月22 日起到20** 年1 月 5 日1、课程设计的内容和要求(包括原始数据、技术要求、工作要求等):课程设计的内容:(1)设计数控车床纵向进给系统传动设计;结构设计;主要零件设计(选择一个主要零件轴或齿轮)(2)编写设计说明书主要内容包括:机床的用途及主要技术参数,数控车床纵向进给系统传动的方案设计、动力计算、结构设计、零件设计、结果分析、设计体会及今后的改进等设计过程设计要求:车床控制精度:0.01mm(即为脉冲当量);最大进给速度:V max=5m/min。
设计参数:最大加工直径为D max=400mm,工作台及刀架重:110㎏;最大轴向力=160㎏;导轨静摩擦系数=0.2;行程=1280mm;步进电机:110BF003;步距角:0.75°;电机转动惯量:J=1.8×10-2㎏.cm.s-2;主要参考资料:机床课程设计指导书,挂图,机床设计手册、数控机床等教材2、对课程设计成果的要求〔包括图表、实物等硬件要求〕:(1)图纸进给系统装配图A1一张;消隙齿轮箱装配图A1 一张;(2)说明书方案设计、运动设计、结构设计、零件设计、结果分析、体会及今后的改进、参考资料3目录一、数控机床进给系统概述 (1)二、主要设计任务参数 (3)三、数控车床纵向进给系统传动的方案设计 (3)1、纵向进给系统设计的基本要求 (3)1、带有齿轮传动的进给运动................................... (3)2、经同步带轮传动的进给运动 (4)3、电机通过联轴器直接与丝杠联接 (5)四、运动设计 (5)1、降速比计算 (5)2、减速齿轮的确定 (6)五、丝杠螺母机构的选择与计算 (6)1、动载强度计算 (6)2、静强度计算 (7)3、临界转速校核 (8)4、额定寿命的校核 (8)六、动力计算 (8)1、传动件转动惯量的计算 (8)2、电动机力矩的计算 (9)七、丝杠螺母机构的传动刚度计算 (10)八、结构设计 (11)1、滚珠丝杠的支承 (11)2、滚珠丝杠螺母副间隙消除和预紧 (12)九、主要结构性能及特点的分析 (12)十、总结与体会 (13)参考文献 (14)一、数控机床进给系统概述数控机床伺服系统的一般结构如图图1-1所示:图1-1数控机床进给系统伺服相对于传统机床,数控机床有以下明显的优越性:(1) 提高生产率。
热盘加工专用机床设计进给系统设计电控系统设计

摘要鉴于我国目前资金短缺,工业生产规模小的特点,用较小资金迅速改变机械工业落后的生产面貌,使之尽可能地提高自动化程度保证生产质量,减轻劳动程度提高经济效益。
而实现这一任务有效的、基本的途径就是普及以及应用经济型数控机床。
此次设计的热盘加工专用机床就是把普通机床和数控技术结合在一起。
机床的设计参考了立式铣床和龙门镗铣床的床身和加工方式,同时附加了数控技术。
可以实现加工的自动化,提高了加工的效率。
在热盘加工专用机床的设计中,我主要负责进给系统和电控系统设计。
进给系统是采用,步进电机,滚珠丝杠副和直线滚动导轨相结合的传递方式,利用步进电机转动,带动滚珠丝杠的旋转,从而实现工作台沿导轨方向运动。
电控系统主要是采用8031芯片,构成开环系统,利用芯片控制步进电机的转速和方向,实现自动化加工。
这次设计的机床虽然加工精度不是很高,但稳定性好,价格低廉,设备费用投入较少,满足企业发展初期的需要,适合我国目前国情。
关键词:数控化;步进电机;滚珠丝杠ABSTRACTIn view of the shortage of funds, and small-scale industrial production, smaller funds rapidly changing the face of Machinery Industry backward production, so as much as possible to improve the degree of automation to ensure production quality, reduce the degree of labor to improve economic efficiency. Effective to achieve this task, the basic way is universal and application of economical CNC.The design of the hot plate special machine is ordinary machine tools and CNC technologies together. The design of the machine reference bed and processing of vertical milling machine and gantry milling machine, and additional CNC technology. Can realize the automation of the processing, improve the processing efficiency.Hot plate special machine design, is mainly responsible for the feed system and electric control system design. The feed system is used, the stepper motor, ball screw and linear rolling guide rail combining the transfer mode, the use of stepper motor rotation, driven by the rotation of the ball screw, in order to achieve the direction of movement of the table along the guide rails. The electronic control system is using the 8031 chip, constitute the open-loop system, take advantage of the speed and direction of the chip stepper motor control, automated processing.The design of the machine is not very high machining accuracy, good stability, low prices, equipment costs less input, to meet the needs of the early development of enterprises, suited to China's national conditions.Key words: CNC ;stepper motor ;ball screw目录摘要 (III)ABSTRACT .................................................................................................................................. I V 目录. (V)1 绪论 (1)1.1概述 (1)1.2 课题源公司的简介 (1)1.3 本设计任务相关要求 (1)1.4 热盘工件图样 (1)2 加工方法选择 (3)2.1 工艺方案的制定 (3)2.2 采用立式铣削加工的理由 (3)2.3 数控机床 (4)2.3.1 数控机床工作原理 (4)2.3.2 数控机床的组成 (4)2.3.3 数控编程坐标系的选取 (5)3 机床总体设计方案的拟定 (6)4 进给系统的设计 (9)4.1 工作台进给系统的设计 (9)4.1.1 传动部件的选择和分析 (9)4.1.2 导轨的选择与设计 (10)4.1.3 驱动电机的选择和分析 (12)4.1.4 轴承的选择 (16)4.1.5 工作台进给系统的结构 (18)4.2 横梁进给系统设计 (19)4.2.1 横梁进给系统的结构 (19)4.2.2 横梁结构的分析 (20)4.2.3 横梁进给系统零部件选择 (20)5 进给系统机械部分设计 (21)5.1工作台进给系统机械部分设计 (21)5.1.1 滚珠丝杠的机械特性计算 (21)5.1.2 导轨副的作用、计算与选择 (23)5.1.3 步进电机的选择 (23)5.1.4 联轴器的选择 (25)5.1.5 轴承的选择 (25)5.2横梁进给系统机械部分设计 (25)6 电控系统部分设计 (26)6.1 控制形式的选择和分析 (26)6.1.1 开环控制系统 (26)6.1.2 闭环控制系统 (26)6.1.3 半闭环控制系统 (26)6.2 控制系统方案确定 (27)6.2.1 数控系统基本硬件组成 (27)6.2.2 总体组成 (27)6.3 软、硬件任务合理分配 (27)6.4 主控器 (28)6.4.1 主控芯片选择 (28)6.4.2 MCS---51系列单片机介绍 (28)6.4.3 三总线结构 (29)6.4.4 存储器结构 (29)6.4.5 时序 (29)6.4.6 中断功能 (31)6.4.7 MCS---51单片机常用系统扩展芯片 (31)6.5 存储系统扩展设计 (31)6.5.1 芯片选择 (31)6.5.2 地址分配及译码 (32)6.6 机床中部分电机控制电路 (34)6.6.1 电动机正反转控制电路 (34)6.6.2 冷却泵的控制电路 (35)7 结论与展望 (37)7.1结论 (37)7.2不足之处及未来展望 (37)致谢 (38)参考文献 (39)热盘加工专机设计进给系统设计电控系统设计1绪论1.1概述毕业设计是对每个即将毕业的大学生在校四年学习情况的综合测评和考量,对每个要走向社会的我们具有非常重要的意义,是对学校和家长做出一次总结性的汇报,是对自我能力的一次展示,还是对自我不足的一种审查。
数控车床进给系统设计

数控车床进给系统设计一、进给系统的结构设计1.可靠性高:进给系统的关键零部件应采用优质的材料和加工工艺,以保证系统的稳定性和长寿命。
2.刚性好:进给系统的结构应具备足够的刚度,以保证在高速切削和大负载的工况下,机床能够保持稳定运行。
3.灵活性强:设计时应考虑到不同工件的加工要求,进给系统应能够快速调整和变换,以满足不同工件的加工需求。
二、进给系统的控制方法设计1.PTP控制方式:即点对点控制方式,根据工件形状和切削要求设计程序,实现工件形状的控制和切削路径的规划。
2.直线插补控制方式:通过数学模型进行直线切削路径的插补计算,实现工件形状的控制和切削路径的规划。
3.圆弧插补控制方式:通过数学模型进行圆弧切削路径的插补计算,实现工件形状的控制和切削路径的规划。
三、进给系统的传动方式设计传统数控车床进给系统的传动方式有液压传动和蜗杆传动两种,在设计进给系统时需要选择合适的传动方式,以满足不同加工工况的需求。
1.液压传动:液压传动以其可适应性强、能源利用率高等优点,在高负载和高速切削的工况下表现出较好的性能。
2.蜗杆传动:蜗杆传动以其结构简单、体积小、传动精度高等优点,在精密加工和高速加工的场合得到广泛应用。
四、进给系统的反馈装置设计进给系统的反馈装置是保证机床加工精度的重要组成部分,主要分为位置反馈和力反馈两种。
设计反馈装置时需要考虑以下几个因素:1.精度要求:根据机床加工的精度要求选择合适的反馈装置,以保证加工精度的稳定性。
2.反馈方式:根据加工工况选择合适的反馈方式,如光电编码器、脉冲等。
3.反馈信号的处理:对反馈信号进行合理的滤波和放大处理,以保证控制系统的稳定性和精度。
总之,数控车床进给系统的设计直接影响机床的加工精度和工作效率。
在设计进给系统时应考虑到结构、控制方法、传动方式和反馈装置等方面的因素,以满足不同加工要求。
同时,还需要对系统进行可靠性和稳定性分析,以确保数控车床的长期稳定运行。
数控机床横向进给设计
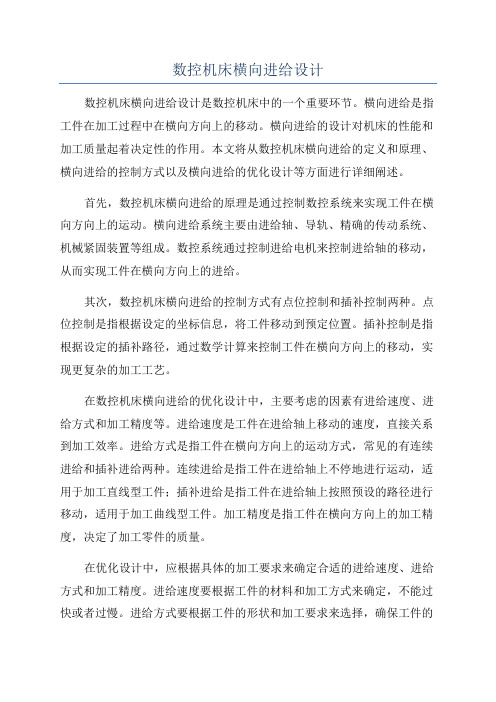
数控机床横向进给设计数控机床横向进给设计是数控机床中的一个重要环节。
横向进给是指工件在加工过程中在横向方向上的移动。
横向进给的设计对机床的性能和加工质量起着决定性的作用。
本文将从数控机床横向进给的定义和原理、横向进给的控制方式以及横向进给的优化设计等方面进行详细阐述。
首先,数控机床横向进给的原理是通过控制数控系统来实现工件在横向方向上的运动。
横向进给系统主要由进给轴、导轨、精确的传动系统、机械紧固装置等组成。
数控系统通过控制进给电机来控制进给轴的移动,从而实现工件在横向方向上的进给。
其次,数控机床横向进给的控制方式有点位控制和插补控制两种。
点位控制是指根据设定的坐标信息,将工件移动到预定位置。
插补控制是指根据设定的插补路径,通过数学计算来控制工件在横向方向上的移动,实现更复杂的加工工艺。
在数控机床横向进给的优化设计中,主要考虑的因素有进给速度、进给方式和加工精度等。
进给速度是工件在进给轴上移动的速度,直接关系到加工效率。
进给方式是指工件在横向方向上的运动方式,常见的有连续进给和插补进给两种。
连续进给是指工件在进给轴上不停地进行运动,适用于加工直线型工件;插补进给是指工件在进给轴上按照预设的路径进行移动,适用于加工曲线型工件。
加工精度是指工件在横向方向上的加工精度,决定了加工零件的质量。
在优化设计中,应根据具体的加工要求来确定合适的进给速度、进给方式和加工精度。
进给速度要根据工件的材料和加工方式来确定,不能过快或者过慢。
进给方式要根据工件的形状和加工要求来选择,确保工件的加工精度。
加工精度要根据工件的尺寸要求和加工精度要求来确定,必须保证工件的尺寸和形状与图纸要求一致。
此外,在数控机床横向进给的设计中,还要考虑进给轴的刚性和工件的稳定性。
进给轴的刚性要足够强,以确保工件在加工过程中的稳定性和精度。
工件的稳定性则要通过合适的夹持方式和工件支撑来保证,避免在加工过程中的振动和变形。
综上所述,数控机床横向进给的设计是数控机床中的一个关键环节。
大型曲轴车铣机床伺服进给系统设计研究

传 动机构 的数 学模 型 , 并运 用传 统 P D 算法对 所 设计 的进 给 系统进 行控 制 计算 , 用 MAT A I 利 L B对
系统 的动态性 能进行仿 真 , 并确 定 了伺服机构 的参 数 , 以此 又 给 出 了避 免 直线 双 驱动 过定 位 的条 并 件, 为大型 曲轴加 工机床进 给 系统的设计 提供 了理论 依据 。 关键 词 : 大型 曲轴 车铣机床 伺 服进给 系统 中 图分 类号 : P 7 T 23 文献标 识码 : A
t e s r o s co s d tr n d h e v e t ri ee mi e .Fi l h t h v i o d to ft e ln a o bl d r e f o ai n i ’ n t a ,t e a od c n iin o h i e rd u e- iv -o lc t s o o
万 吨轮 以上 的超大功 率低速 曲轴) 是一 个 国家  ̄1 H2 综合 制造能 力 的体 现 , 全世 界 只有极 少数 国家 能生产 。 超 大型 曲拐 的加 工 更是 超 大功 率 低速 } 轴 加 工 的 瓶 } } i
颈, 高效 、 高精超 大型 曲拐加工 机床 和 车铣 加工 见 图 1 所 示 。此类 机床 只德 国有 , 机 床 又依 据 车铣 这 一现 该 代加工 方法 设计 而成 。
我 国近几 年引进 了超大 型 曲轴 的精 加 工机 床 ( 图
2 。 目前 我 国 曲 拐还 是 采 用 传 统 普 通 的单 柱 立 车 进 ) 行车 削加工 , 加工 效率 和精度都很 低 , 制超大 型 曲 其 研
拐 加工 的车铣机 床就 显得 十分必要 。 由于单 曲拐的重 量 在 十几 吨 以上 , 加 工过 程 中 且 又 是偏心 安装 , 因而在加 工 中会 产生 很大 的离心力 ; 离
数控机床进给系统设计
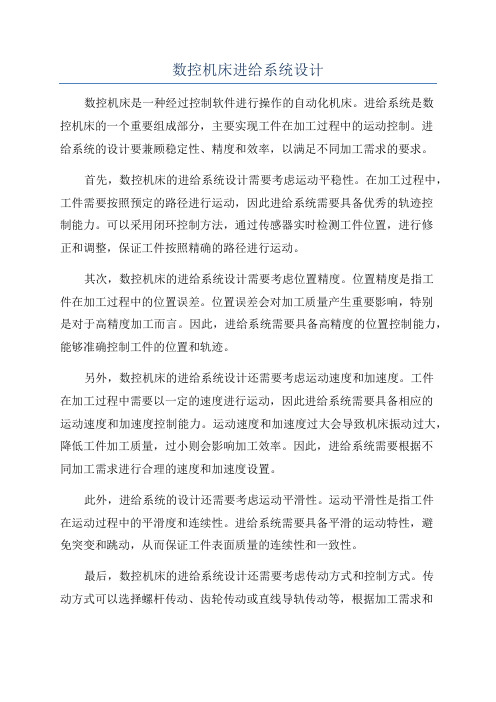
数控机床进给系统设计数控机床是一种经过控制软件进行操作的自动化机床。
进给系统是数控机床的一个重要组成部分,主要实现工件在加工过程中的运动控制。
进给系统的设计要兼顾稳定性、精度和效率,以满足不同加工需求的要求。
首先,数控机床的进给系统设计需要考虑运动平稳性。
在加工过程中,工件需要按照预定的路径进行运动,因此进给系统需要具备优秀的轨迹控制能力。
可以采用闭环控制方法,通过传感器实时检测工件位置,进行修正和调整,保证工件按照精确的路径进行运动。
其次,数控机床的进给系统设计需要考虑位置精度。
位置精度是指工件在加工过程中的位置误差。
位置误差会对加工质量产生重要影响,特别是对于高精度加工而言。
因此,进给系统需要具备高精度的位置控制能力,能够准确控制工件的位置和轨迹。
另外,数控机床的进给系统设计还需要考虑运动速度和加速度。
工件在加工过程中需要以一定的速度进行运动,因此进给系统需要具备相应的运动速度和加速度控制能力。
运动速度和加速度过大会导致机床振动过大,降低工件加工质量,过小则会影响加工效率。
因此,进给系统需要根据不同加工需求进行合理的速度和加速度设置。
此外,进给系统的设计还需要考虑运动平滑性。
运动平滑性是指工件在运动过程中的平滑度和连续性。
进给系统需要具备平滑的运动特性,避免突变和跳动,从而保证工件表面质量的连续性和一致性。
最后,数控机床的进给系统设计还需要考虑传动方式和控制方式。
传动方式可以选择螺杆传动、齿轮传动或直线导轨传动等,根据加工需求和机床类型进行选择。
控制方式可以选择基于位置、速度或力控制等,根据具体应用进行选择。
综上所述,数控机床的进给系统设计需要兼顾运动平稳性、位置精度、运动速度和加速度、运动平滑性、传动方式和控制方式等因素。
通过合理的设计和调试,可以提高数控机床的加工质量和效率,满足不同加工需求的要求。
数控机床进给系统设计
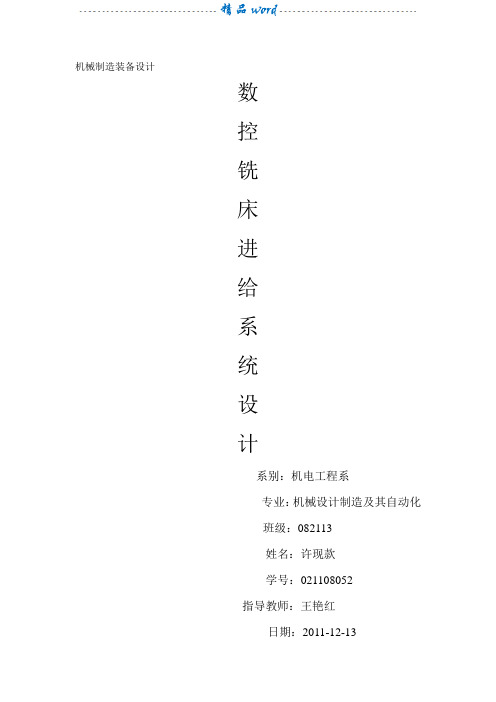
机械制造装备设计数控铣床进给系统设计系别:机电工程系专业:机械设计制造及其自动化班级:082113姓名:许现款学号:021108052指导教师:王艳红日期:2011-12-13数控机床进给系统设计1总体方案设计1.1对进给伺服系统的基本要求带有数字调节的进给驱动系统都属于伺服系统,进给伺服系统不仅是数控机床的一个重要组成部分,也是数控机床区别于一般机床的一个特殊部分。
数控机床对进给伺服系统的性能指标可归纳为:定位精度要高;跟踪指令信号响应要快;系统的稳定性要好。
1.2进给伺服系统的设计要求机床的位置调节对进给伺服系统提出了很高的要求,其中在静态设计方面:(1)能够克服摩擦力和负载,当加工中最大切削力为20000N——30000N时,电机轴上的转矩需要10N.m——40N.m;;(2)很小的进给移动量。
目前最小分辨率为0.1m(3)高的静态扭转刚度;(4)足够的调速范围;(5)进给速度均匀,在速度很低是无爬行现象。
在动态设计方面有:(1)具有足够的加速和制动装矩,以便快速的完成启动和制动;(2)具有良好的动态传递性能,以保证在加工中获得高的轨迹精度和满意的表面质量;(3)负载引起的轨迹误差尽可能小。
对数控机床机械传动部件则有以下要求:(1)被加速的运动部件具有较高的惯量;(2)高的刚度和良好的阻尼;(3)传动部件在拉压刚度、扭转刚度、摩擦阻尼特性和间隙等方面具有尽可能小的非线性。
1.3总体方案进给伺服系统总体方框图如下图3.1所示。
2进给伺服系统机械部分设计进给伺服系统机械部分的计算与选型内容包括:确定脉冲当量,计算切削力,滚珠丝杆螺母副的设计、计算与选型,齿轮传动计算,步进电机的计算和选型等。
微机光电隔离光电隔离光电隔离功率放大功率放大功率放大步进电机步进电机步进电机向向向图3.1进给伺服系统总体方框图2.1确定脉冲当量,计算切削力1确定系统的脉冲当量脉冲当量是指一个进给脉冲使机床执行部件产生的进给量,它是衡量数控机床加工精度的一个重要参数,因此。
立式数控铣床工作台进给传动系统的设计
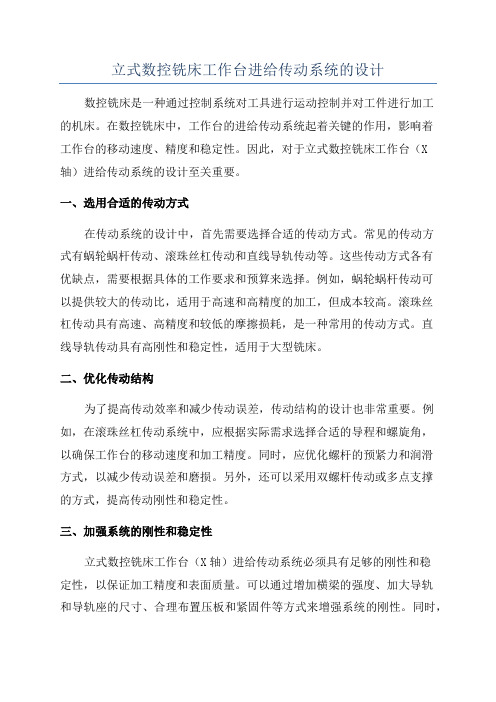
立式数控铣床工作台进给传动系统的设计数控铣床是一种通过控制系统对工具进行运动控制并对工件进行加工的机床。
在数控铣床中,工作台的进给传动系统起着关键的作用,影响着工作台的移动速度、精度和稳定性。
因此,对于立式数控铣床工作台(X 轴)进给传动系统的设计至关重要。
一、选用合适的传动方式在传动系统的设计中,首先需要选择合适的传动方式。
常见的传动方式有蜗轮蜗杆传动、滚珠丝杠传动和直线导轨传动等。
这些传动方式各有优缺点,需要根据具体的工作要求和预算来选择。
例如,蜗轮蜗杆传动可以提供较大的传动比,适用于高速和高精度的加工,但成本较高。
滚珠丝杠传动具有高速、高精度和较低的摩擦损耗,是一种常用的传动方式。
直线导轨传动具有高刚性和稳定性,适用于大型铣床。
二、优化传动结构为了提高传动效率和减少传动误差,传动结构的设计也非常重要。
例如,在滚珠丝杠传动系统中,应根据实际需求选择合适的导程和螺旋角,以确保工作台的移动速度和加工精度。
同时,应优化螺杆的预紧力和润滑方式,以减少传动误差和磨损。
另外,还可以采用双螺杆传动或多点支撑的方式,提高传动刚性和稳定性。
三、加强系统的刚性和稳定性立式数控铣床工作台(X轴)进给传动系统必须具有足够的刚性和稳定性,以保证加工精度和表面质量。
可以通过增加横梁的强度、加大导轨和导轨座的尺寸、合理布置压板和紧固件等方式来增强系统的刚性。
同时,还可以通过使用高精度的轴承和精密的配合来减小系统的摩擦和间隙,提高系统的稳定性。
四、选择适当的驱动和控制系统立式数控铣床工作台(X轴)进给传动系统的驱动和控制系统也需要根据实际需求来选择。
可以选择伺服电机驱动系统,通过与编码器和控制器的配合,实现精确的位置控制和速度调节。
另外,还可以选择闭环步进电机驱动系统,具有简单、易用和成本低的优势。
需要根据加工要求和预算来选择适当的驱动和控制系统。
总之,立式数控铣床工作台(X轴)进给传动系统的设计对于加工质量和效率至关重要。
加工中心XY向进给系统结构设计

加工中心XY向进给系统结构设计加工中心是一种高效率的机械设备,广泛应用于工业生产中。
其XY向进给系统的结构设计对于设备的稳定性和精度有着重要的影响。
在设计这一系统时,需要考虑到以下几个方面:运动方式、传动方式、导轨系统、控制系统等。
运动方式是XY向进给系统的关键。
常见的运动方式有直线运动和曲线运动。
在加工中心中,直线运动比较常见且普遍。
因此,XY向进给系统应设计为直线运动。
直线运动可以通过闭环系统来实现,闭环反馈可以帮助实现系统的高精度定位和跟踪。
在闭环控制系统中,运动控制器向驱动器发送指令,然后驱动器将信号转化为电信号,通过电机控制机构实现运动。
传动方式在XY向进给系统中起着关键作用。
常用的传动方式有螺旋传动、直线传动和齿轮传动等。
螺旋传动和直线传动适用于小范围、高重复精度的直线运动。
齿轮传动适用于中、大范围的直线运动。
在设计传动方式时,需要根据具体的工作条件和要求进行合理选择,以确保系统的稳定性和工作精度。
导轨系统也是XY向进给系统设计的重要方面。
导轨系统包括滑块、导轨和导轨座等组件。
滑块通过固定在机床上来实现运动,导轨和导轨座提供了滑动方向,保证系统运动的平稳性和稳定性。
在设计导轨系统时,需要考虑导轨材料的选择,如何减少磨损和摩擦,以及如何确保系统的刚性和精度。
控制系统是XY向进给系统设计中的另一个重要方面。
控制系统包括运动控制器、传感器和控制算法等。
运动控制器负责向驱动器发送指令,控制驱动器的运动。
传感器用于检测系统的位置和速度等信息,并将其反馈给运动控制器,以实现闭环控制。
控制算法决定了系统的运动轨迹和运动方式。
在设计控制系统时,需要考虑系统的响应速度、精度和稳定性,以及如何解决运动过程中的干扰和噪声等问题。
在XY向进给系统结构设计中,还有许多其他的因素需要考虑,如工作台的稳定性、工作环境的要求、安全性和维护便捷性等。
因此,在实际设计过程中,需要充分考虑这些因素,进行合理的设计和优化。
数控机床进给传动系统设计方案分析
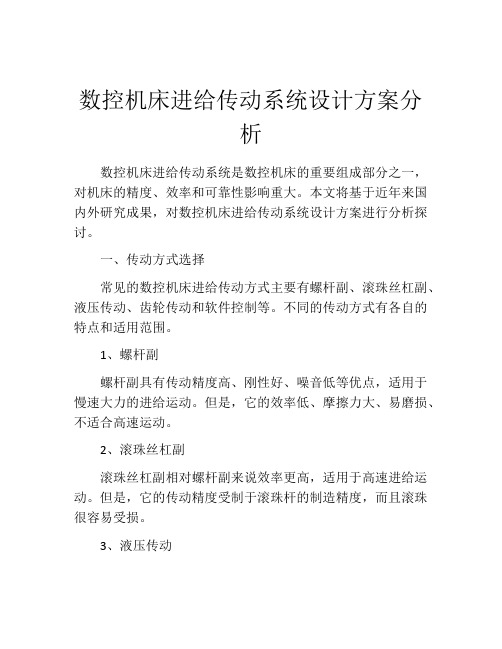
数控机床进给传动系统设计方案分析数控机床进给传动系统是数控机床的重要组成部分之一,对机床的精度、效率和可靠性影响重大。
本文将基于近年来国内外研究成果,对数控机床进给传动系统设计方案进行分析探讨。
一、传动方式选择常见的数控机床进给传动方式主要有螺杆副、滚珠丝杠副、液压传动、齿轮传动和软件控制等。
不同的传动方式有各自的特点和适用范围。
1、螺杆副螺杆副具有传动精度高、刚性好、噪音低等优点,适用于慢速大力的进给运动。
但是,它的效率低、摩擦力大、易磨损、不适合高速运动。
2、滚珠丝杠副滚珠丝杠副相对螺杆副来说效率更高,适用于高速进给运动。
但是,它的传动精度受制于滚珠杆的制造精度,而且滚珠很容易受损。
3、液压传动液压传动具有传动力矩大、响应速度快等优点,在铣削和切削加工中有较好的适应性。
但是,液压传动的系统复杂,维护不易,而且液压油需要定期更换。
4、齿轮传动齿轮传动的优点是传动精度高、能承受较大的力矩,适用于高速进给运动。
但是,它的噪音较大,容易出现波动,而且需要灵活的齿轮摆动机构。
5、软件控制软件控制是一种新的进给传动方式,它通过精确的计算控制电机的旋转角度和速度,精确实现进给精度。
但是,软件控制的成本较高,需要高精度的编码器。
根据不同的机床类型和加工工艺,选择合适的传动方式,可以在传动效率、精度和可靠性之间取得平衡。
二、传动控制技术传动方式是进给传动系统的核心,而控制技术也是影响系统性能的关键因素之一。
常见的传动控制技术包括闭环控制和开环控制两种。
1、闭环控制闭环控制是指传感器将实际位置反馈给控制器,通过对设定值和实际值的差进行比较和调整,控制伺服电机的转速和转角,以实现精确控制。
闭环控制具有稳定性好、精度高等优点,但是需要更多的硬件和软件支持,成本较高。
2、开环控制开环控制是指系统只控制电机的转速,不对传感器信号进行反馈调整,只能通过实验调节来实现控制精度。
开环控制具有简单、成本低等优点,但是精度和稳定性不如闭环控制,容易受到噪声和温度等环境影响。
机床进给系统设计与优化考核试卷
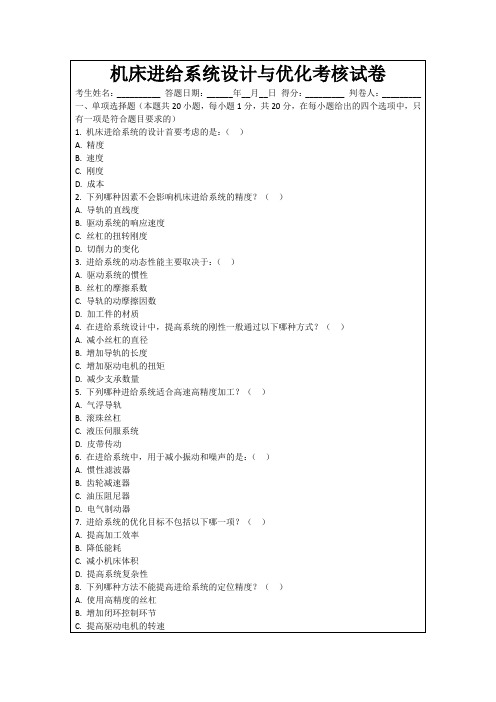
D.提高操作工技能
11.在进给系统设计中,以下哪些因素会影响丝杠的选用?()
A.加工速度
B.切削力
C.精度要求
D.丝杠的成本
12.以下哪些是直线导轨的优点?()
A.刚性好
B.运动平稳
C.维护方便
D.成本低
13.以下哪些因素可能导致机床进给系统出现不稳定现象?()
A.系统控制参数设置不当
16.以下哪些是机床进给系统设计中需要考虑的安全因素?()
A.防护装置
B.紧急停止按钮
C.系统的可靠性
D.机床的颜色
17.以下哪些措施可以减小进给系统的反向间隙?()
A.调整丝杠的预紧力
B.优化驱动电机的控制策略
C.使用高精度的导轨
D.增加丝杠的长度
18.以下哪些因素会影响机床进给系统的热变形?()
答案:
标准答案
一、单项选择题
1. A
2. D
3. C
4. C
5. C
6. C
7. D
8. C
9. A
10. C
11. D
12. D
13. D
14. B
15. C
16. B
17. B
18. C
19. D
20. D
二、多选题
1. ABC
2. ABC
3. ABCD
4. AB
5. ABC
6. ABC
7. ABCD
8. ABCD
9. ABC
10. ABC
11. ABCD
12. ABC
13. ABC
14. ABC
15. ABC
16. ABC
17. ABD
机械机床毕业设计66数控车床纵向进给系统设计

目录第1章概述 (1)1.1设计目的 (1)1.2进给系统概述 (1)第2章运动设计 (2)2.1传动方案拟定 (2)2.2丝杠螺母副的选择与计算 (2)2.2.1丝杠螺母副的选择 (2)2.2.2丝杠螺母副的计算 (3)2.2.3滚珠丝杠螺母副的验算 (4)第3章动力计算 (8)3.1电动机的验算 (8)3.2齿轮的计算 (10)3.3轴的设计 (13)总结 (19)参考文献 (20)数控车床纵向进给系统设计第1章概述1.1.设计目的机床课程设计是在金属切削机床之后进行的实践性环节,其目的在于通过机床进给运动机械变速传动系统的结构设计,使学生在拟定传动和变速的结构方案过程中,得到结构构思、方案分析、结构工艺性、机械制图、零件设计、编写技术文件和查阅技术资料的等方面的综合训练,树立正确的设计思想,掌握基本的设计方法,并培养学生具有初步的结构分析、结构设计与计算能力。
1.2.进给系统概述进给系统的特点是速度低、消耗功率少、受力小,而速度越低越易出现爬行现象,而一般的捣鬼由于受摩擦力下降特性的影响,很难满足高精度的要求,特别是对于数控而言更不能适应精度要求。
而滚珠丝杠副基本上是滚动摩擦,摩擦阻力小,切摩擦阻力的大小几乎与运动速度完全无关,这样就有效的保证了运动的平稳性,克服了爬行现象的产生。
而且滚珠丝杠摩擦损失小,传动效率高,运动灵敏、低速时无爬行现象、轴向刚度高、寿命长、维护简单且具有传动可逆性并反向精度高等优点故而选用滚珠丝杠螺母副传动。
陕西科技大学课程设计说明书第2章运动设计2.1.传动方案拟定2.1.1.总体传动框图如下图:2.1.2.具体的分析过程:因设计要求系统为开环系统从而使系统简化,若直接将电机与滚珠丝杠联必会引起丝杠温度过高即磨损加剧使其寿命降低。
故在其两者之间加一消隙齿轮箱,一是使丝杠速度降低,而则是消除系统传动中的间隙,提高传动精度,并有效减少反向运动死区现象,消息齿轮箱与丝杠可采用联轴器形式连接,这样便确定了如上图所示的传动方案。
数控机床进给系统设计

数控机床进给系统设计数控机床是一种利用数字控制技术来操作机床进行加工的设备。
其中,进给系统是数控机床的核心部件之一,主要负责实现机床轴向运动的精确控制。
本文将从设计原理、系统构成和性能要求三个方面,对数控机床进给系统进行详细阐述。
一、设计原理数控机床进给系统的设计基于三轴坐标系,即X轴、Y轴和Z轴。
当工件需要在不同方向上进行加工时,可以通过对这三个坐标轴的控制,实现工件在平面和立体方向上的运动。
进给系统的基本原理是将需要控制的轴运动距离和速度转换为数字信号,通过数字控制器产生的脉冲信号驱动伺服电机,实现机床的精确控制。
二、系统构成数控机床进给系统由三个主要组成部分构成:数字控制器、伺服驱动器和伺服电机。
数字控制器是整个系统的大脑,负责生成运动指令、计算速度和位置等参数,并将其转换为脉冲信号。
伺服驱动器接收数字控制器发送的脉冲信号,将其转换为电流信号,并通过电机的转矩控制反馈实现机床运动控制。
伺服电机则是进给系统的执行机构,根据伺服驱动器的控制信号,转化为机床轴向的运动。
三、性能要求数控机床进给系统在设计中需要具备多项重要性能要求,以满足机床加工的精度和效率要求。
首先,系统需要具备高速响应能力,能够快速准确地响应指令并实时控制机床轴向运动。
其次,系统需要具备高精度定位能力,能够实现亚微米级的定位精度,以满足精密加工的要求。
此外,系统还需具备较大的负载能力,能够承受较大的加工力矩,以应对各种加工过程中的需求。
同时,在设计中还需要考虑系统的稳定性和可靠性,以确保系统的长期稳定运行,并减少维护和故障排除的成本。
总结起来,数控机床进给系统是数控机床的核心组成部分之一,其设计原理基于三轴坐标系的控制,通过数字控制器、伺服驱动器和伺服电机的协同工作,实现机床轴向运动的精确控制。
进给系统的设计需要满足高速响应、高精度定位、较大负载和稳定可靠等多项性能要求,以保障机床加工的高效精度。
- 1、下载文档前请自行甄别文档内容的完整性,平台不提供额外的编辑、内容补充、找答案等附加服务。
- 2、"仅部分预览"的文档,不可在线预览部分如存在完整性等问题,可反馈申请退款(可完整预览的文档不适用该条件!)。
- 3、如文档侵犯您的权益,请联系客服反馈,我们会尽快为您处理(人工客服工作时间:9:00-18:30)。
进给传动系统传动精度
传动精度是指机床内联系传动链两端件之 间相对运动的准确性。
误差来源 误差传递规律 提高传动精度措施和内联系传动链设计原则
缩短传动链 合理分配传动副的传动比 合理选择传动件 合理确定各传动副精度 采用校正装置
液压传动 电气传动
进给系统设计要求
足够的静刚度和动刚度 良好的快速响应性,低速运动不爬行 良好的抗振性 足够宽的调速范围 较高的传动精度和定位精度 机构简单、加工工艺性好
进给系统设计特点
速度低,功耗小,恒转矩传动 计算转速 变速系统设计原则
传动副“前少后多” 降速“前快后慢” 传动线“前疏后密”
滚珠丝杠副设计
主要尺寸 标称直径、导程、螺旋升角等。 精度等级 根据JB316.2-91《滚珠丝杠副精度》标准规定分为5个
等级:1、2、3、4、5级(有的参考书称7个等级,另外有7、10 级),1级最高,5级最低。一般动力传动选4、5级。数控机床、 精密机械或仪器选1、2、3级。 标注方法
滚珠丝杠副设计
500MPh ) 103
GI
V300
伺服系统降速传动设计
降速传动比的计算
开环系统——i=φPh/360δ
φ—脉冲当量,mm/p δ—步进电机步距角
闭环和半闭环——i=vmax/nmaxPh
vmax —工作台最大进给速度mm/min nmax —电动机额定转速,r/min
消除齿轮传动间隙的措施
机床进给系统设计
主要内容
进给系统组成分类,设计要求与特点 进给系统传动精度 伺服进给传动系统设计 滚珠丝杠副设计 伺服系统降速传动设计
进给系统分类及组成
进给系统根据机床的类型、传动精度、运动平稳性和生 产率等要求的不同 机械传动
动力源 变速机构 换向机构 运动分配机构 过载保险机构 运动转换机构 快速传动机构
按功率而是根据以下
指标
转
矩
加减速区
最大切削负载转矩不得 (
N*m
超过电动机的额定转矩
)
电动机的转子惯量JM应 与折算到电机轴上负载
额定转矩
断续工作区
等效惯量JeL匹配
连续工作区
快移时的加速性能
进给伺服系统传动机构
传动类型
齿轮齿条传动
同步带传动
丝杠传动
设计要求
灵敏度 稳定性
提高刚度、降低惯量
滚珠丝杠副主要支撑方式
一端固定、另一端自由 一端固定、另一端简支 两端固定 两端固定、多轴承支撑
滚珠丝杠副设计
滚珠丝杠副主要支撑方式
一端固定、另一端自由 一端固定、另一端简支 两端固定 两端固定、多轴承支撑
滚珠丝杠副设计
滚珠丝杠副主要支撑方式
一端固定、另一端自由 一端固定、另一端简支 两端固定 两端固定、多轴承支撑
滚珠丝杠副设计
轴向间隙调整方法
双螺母垫片式预紧
根据垫片厚度不同分成两种形式,当垫片厚度较厚时 即产生“预拉应力”,而当垫片厚度较薄时即产生 “预压应力”以消除轴向间隙。
滚珠丝杠副设计
轴向间隙调整方法
双螺母螺纹式预紧
滚珠丝杠副设计
轴向间隙调整方法
双螺母齿差式预紧
滚珠丝杠副设计
轴向间隙调整方法
单螺母变导程式预紧
变导程法原理如图所示,
仅仅是在螺母中部将其导程
增加一个预压量Δ,以达到
预紧的目的。
预拉方向
预拉方向
导程
导程+Δ
导程
螺母侧
丝杠侧
滚珠丝杠副设计
滚珠丝杠副主要尺寸、精度与标注方法
d0-公称直径,d1-丝杠公称直径,d2-丝杠螺纹底径 Ph-公称直径,D1-螺母螺纹内径,D2-螺母螺纹底径 Dw-滚珠直径,e-滚道圆弧偏心距,Rr-螺母滚道圆弧半径, Rs-螺纹滚道圆弧半径,a-接触角
刚性调整法
偏心轴套调整法 齿轮轴间垫片调整法 双片斜齿轮轴间垫片调整法
以, 但齿侧间隙调整后不能自动补偿.
图图22..2256 偏轴心向套垫法片法 1-齿电轮动机2-2齿-轮偏心3套-垫片
柔性调整法
双片直齿轮弹簧力错 齿调整法
双片斜齿轮轴向压簧 调整法
柔性调整法
轴向压簧调整法 周向压簧调整法
图2.30 锥齿轮轴向压簧调整法 1、2-锥齿 3-压簧 4-螺母 5-传动轴
图2.31 锥齿轮周向弹簧调整法 1、2-锥齿轮 3-镶块 4-弹
簧5-螺钉 6-凸爪
齿轮齿条加载调整法
径向加载调整法 轴向加载调整法
重点掌握
滚珠丝杠副主要技术参数的确定
L=60nT/106
滚珠丝杠的导程 Ph=1000Vmax/nmax 当量载荷与当量转速
额定动载荷 Ca>Cam
滚珠丝杠名义直径D0 螺母及支撑轴承选择
稳定性计算 刚度验算 Fk 导程精度验算
fk 2 EI
K ls 2
Fmax
( K 1000Fmax EA
精度 减小摩擦,减小间隙
滚珠丝杠副设计
工作原理、特点及分类
摩擦损失小,传动效率高 运动平稳,摩擦阻力小 可以预紧,丝杠螺母之间进行
消隙或预紧,定位精度高、轴 向刚度大 运动可逆 不能自锁
滚珠丝杠副设计
工作原理、特点及分类 截面形状 滚珠循环方式 消除轴向间隙、调整 预紧力方式
数控机床的伺服进给系统
按有无检测反馈装置分为: 开环系统、闭环系统、半闭环系统
工作台
* 位置数比控较装器置 速度控制步电进路电机伺服电动*机 *
工作台
位置反馈
速度反馈
位置反馈
进给伺服系统动力源
类型和特点
步进电动机 直流伺服电动机 交流伺服电动机 直线伺服电动机
伺服电动机的选择
伺服电动机的主参数 是功率,选择时不是 最大转矩
补偿热膨胀,减小自重 造成的下垂,两端固定 支撑需进行预拉伸处理。
滚珠丝杠的预拉伸 确定丝杠预拉伸量应考虑的因素
预拉伸力应大于最大工作载荷的0.35倍 丝杠的预拉伸量应能补偿丝杠的热变型
滚珠丝杠的设计计算
滚珠丝杠的载荷计算(动载荷Cam与静载荷Coa)
工作载荷 F
最小载荷 Fmin 最大载荷 Fmax 当量载荷 Fm=(2Fmax+ Fmin)/3 滚珠丝杠当量动载荷Cam=Fmfw3 L /fafk 滚珠丝杠当量静载荷Coa=SFmax