次氯酸钠清净乙炔操作规程
次氯酸钠操作规程
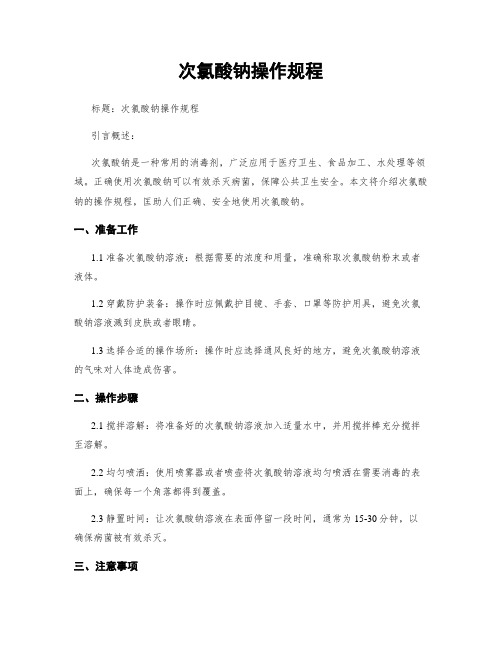
次氯酸钠操作规程标题:次氯酸钠操作规程引言概述:次氯酸钠是一种常用的消毒剂,广泛应用于医疗卫生、食品加工、水处理等领域。
正确使用次氯酸钠可以有效杀灭病菌,保障公共卫生安全。
本文将介绍次氯酸钠的操作规程,匡助人们正确、安全地使用次氯酸钠。
一、准备工作1.1 准备次氯酸钠溶液:根据需要的浓度和用量,准确称取次氯酸钠粉末或者液体。
1.2 穿戴防护装备:操作时应佩戴护目镜、手套、口罩等防护用具,避免次氯酸钠溶液溅到皮肤或者眼睛。
1.3 选择合适的操作场所:操作时应选择通风良好的地方,避免次氯酸钠溶液的气味对人体造成伤害。
二、操作步骤2.1 搅拌溶解:将准备好的次氯酸钠溶液加入适量水中,并用搅拌棒充分搅拌至溶解。
2.2 均匀喷洒:使用喷雾器或者喷壶将次氯酸钠溶液均匀喷洒在需要消毒的表面上,确保每一个角落都得到覆盖。
2.3 静置时间:让次氯酸钠溶液在表面停留一段时间,通常为15-30分钟,以确保病菌被有效杀灭。
三、注意事项3.1 防止混合:次氯酸钠溶液与酸性物质、有机物质等不可混合,以免产生有毒气体或者爆炸。
3.2 避免直接接触:操作时应避免直接接触次氯酸钠溶液,如不慎接触应即将用清水冲洗。
3.3 储存注意:次氯酸钠溶液应存放在阴凉干燥处,远离光线和热源,避免溶液失效。
四、急救措施4.1 眼部接触:如次氯酸钠溶液溅入眼睛,应即将用大量清水冲洗,必要时就医。
4.2 皮肤接触:如次氯酸钠溶液溅到皮肤上,应即将用清水冲洗,并使用中性洗剂清洗皮肤。
4.3 意外吸入:如不慎吸入次氯酸钠溶液的气雾,应迅速转移到通风处呼吸新鲜空气,必要时就医。
五、废弃处理5.1 废液处理:使用完的次氯酸钠溶液应按规定的废液处理程序处理,不可直接倒入下水道或者随意丢弃。
5.2 容器处理:空的次氯酸钠容器应清洗干净后,按规定分类投放垃圾桶。
5.3 环保意识:在使用次氯酸钠时,应保持环保意识,避免对环境造成污染。
结语:正确使用次氯酸钠是保障公共卫生安全的重要举措,希翼通过本文的介绍,能够匡助大家掌握次氯酸钠的操作规程,做到安全、高效地使用该消毒剂。
乙炔工艺操作规程(次钠)及安全性说明
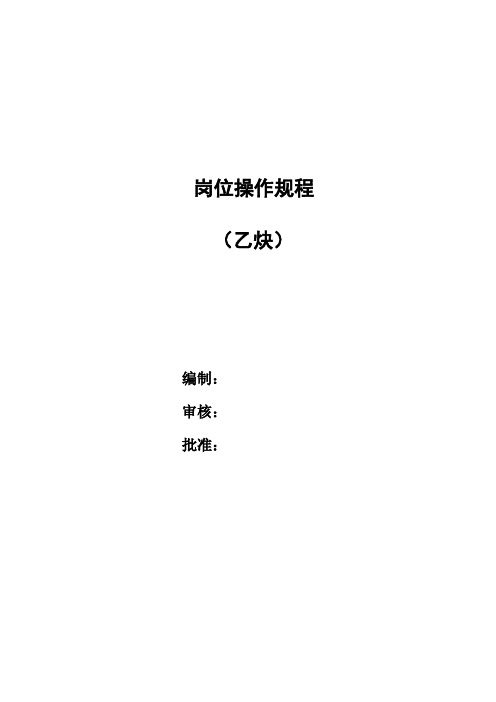
岗位操作规程(乙炔)编制:审核:批准:目录一、产品说明…………………………………………………………………2页二、原料说明…………………………………………………………………5页三、生产原理…………………………………………………………………8页四、生产工艺流程……………………………………………………………13页五、岗位操作………………………………………………………………15页六、安全注意事项……………………………………………………………25页七、分析检验控制一览表……………………………………………………26页八、设备一览表………………………………………………………………27页1一、产品说明1、产品简介化学名称:乙炔俗称:电石气英文名:Acetylene分子式:C2H2结构式:H-C≡C-H分子量:26.0262、性质2.1、乙炔在常温常压下为无色气体,含有硫化物,磷化物时有特殊的刺激性嗅味,极易燃烧爆炸,微溶于水及乙醇,能溶于丙酮、氯仿和苯。
2.2、乙炔与水接触时,在适宜条件下生成C2H2·6H2O雪花状白色晶体。
2.3、乙炔分子化学性质活泼,易发生加成、聚合、取代等多种反应。
2.4、理化常数:密度:(0℃,105Pa) 1.171g/l比重:ⅰ)对空气:0.9056ⅱ)对氧气:0.8194比热:(20℃,105Pa)ⅰ)等压比热(C P):1680.36 J/kg℃ⅱ)等容比热(C V):1358.5 J/kg℃溶点(或凝固点):(1.2×105Pa)-85℃沸点(或冷凝点):(1.2×105Pa)-83.66℃闪点:-17.78℃闭口自燃点:305℃气化热:827640 J/kg生成热:225720 J/mol产生最大爆炸压力的浓度:14.5%2最大爆炸压力: 1.01MPa燃烧热(25℃): 1298349.8J/ mol最小引燃能量: 1.9×10-5J临界温度:35.5℃临界压力:62.5×105Pa乙炔在各种溶剂中的溶解度(1体积溶剂中乙炔体积)如以下各表:表1乙炔在水中的溶解度温度℃溶解度温度℃溶解度温度℃溶解度0 1.73 25 0.93 70 0.255 1.49 30 0.84 80 0.1510 1.31 40 0.65 90 0.0515 1.15 50 0.5020 1.03 60 0.37表2乙炔在丙酮中的溶解度温度℃溶解度温度℃溶解度温度℃溶解度-20 52 0 33 20 20 -15 47 5 29 25 18 -10 42 10 26 30 16 -5 37 15 23 35 14.5表3乙炔在多种溶剂中的溶解度溶剂温度℃溶解度溶剂温度℃溶解度饱和食盐水25 0.32 苯15 4.0 石灰乳15 0.75 乙醇18 6.0 汽油15 5.7 工业醋酸甲酯 5 14.82.5、危险特性:2.5.1遇火有燃烧爆炸危险。
次氯酸钠操作规程

次氯酸钠操作规程次氯酸钠是一种广泛应用的消毒剂,常用于食品加工、水处理、医疗卫生等领域。
使用次氯酸钠进行消毒时,需要按照一定的操作规程进行操作,以确保安全性和消毒效果。
下面是一份次氯酸钠操作规程,其中包括操作前准备、操作过程和操作后处理等内容。
一、操作前准备1.熟悉次氯酸钠的物理化学性质,了解其毒性和危害性,掌握正确的使用方法和注意事项。
2.穿戴个人防护装备,包括防护眼镜、防护口罩、防护手套和防护服。
确保个人防护装备的完整性和合适性。
3.准备所需的次氯酸钠溶液、容器、工具等。
确保容器和工具清洁无杂质,并与次氯酸钠不发生反应。
4.安排好工作场所,确保操作环境的整洁和卫生。
二、操作过程1.将所需量的次氯酸钠溶液加入清洁的容器中。
根据需要调节浓度,注意加入适量的次氯酸钠粉末或溶液。
2.在加入次氯酸钠溶液时,要小心搅拌,避免产生溅射。
搅拌要均匀,使溶液中次氯酸钠均匀分布。
3.使用过程中避免将次氯酸钠溶液接触皮肤和眼睛,如不慎接触到皮肤或眼睛,应立即用大量清水冲洗,并及时就医。
4.次氯酸钠溶液在储存和使用过程中会分解、失去活性,因此在使用过程中要尽量避免直接暴露于阳光下,储存时要密封。
5.在使用次氯酸钠溶液进行消毒时,应根据需要调整浓度和接触时间。
不同的消毒对象和环境要求有所不同,可以参考相关标准和指南。
三、操作后处理1.使用完毕后,将未使用的次氯酸钠溶液密封储存,避免直接暴露于阳光下。
如有残余溶液,应按规定方式处理。
2.清洗使用过的容器和工具,使用清水和肥皂清洗干净,确保无明显残留物。
储存清洁的容器和工具,以备下次使用。
3.拆卸个人防护装备,如手套、口罩、防护服等。
安全处理废弃的防护装备,包括焚烧、填埋或专门处理设施处理。
4.操作结束后,及时清洗双手。
使用肥皂和清水彻底清洗双手,确保无次氯酸钠残留,并彻底擦干。
以上是一份次氯酸钠操作规程,其中涵盖了操作前准备、操作过程和操作后处理的要点。
在使用次氯酸钠进行消毒时,要遵循正确的操作规程,确保操作安全,有效完成消毒任务。
乙炔车间清净工序操作规程
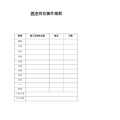
清净岗位操作规程职责部门及岗位名称签名日期编制审核审核审核审核审核审核审核审核……批准生效日期公司名称修订记录修订日期修订人修订内容目录1 总体工艺描述 ..................................................................................... 错误!未定义书签。
2 操作参数 ............................................................................................. 错误!未定义书签。
3 安全、职业健康、环保提示及要求 ................................................. 错误!未定义书签。
4 开车准备 ............................................................................................. 错误!未定义书签。
5 原始开车(冷启动) ............................................................................... 错误!未定义书签。
6 年度检修后开车 ................................................................................. 错误!未定义书签。
7 紧急停车后开车 ................................................................................. 错误!未定义书签。
8 正常操作 ............................................................................................. 错误!未定义书签。
次氯酸钠 安全操作规程

3、次氯酸钠溅到皮肤或眼内时,立即用大量清水。
警示标识
次氯酸钠 安全操作规程
危险因素
1、操作不当可造成次氯酸钠泄漏、灼烫事故。
2、作业人员将次氯酸钠倒入酸洗环境下可能导致中毒事故。
3、作业人员未穿戴劳动防护用品作业可能导致灼烫事故。
4、次氯酸钠运输车进入厂内车辆超速行驶可能引发车辆伤害事故。
操
作
规
程
1、穿戴好劳动安全防护用品。戴好安全防护手套、化学安全防护面罩、穿耐酸碱橡胶皮靴、穿工作服(防腐材料制作)、工作现场严禁进食和饮水。
2、操作人员必须遵守公司各项安全管理制度,严格遵守操作规程,服从安排,严格管理。
3、准确登记次氯酸钠储存量,使用量,准确记录上报公司及相关部门。
4、次氯酸钠有毒有害,具有一定的腐蚀性,应预防滴、漏造成对人体的伤害。
5、装卸时应准备好妥善应急用水,做好安全防范措施,保障安全工作。
6、定期检查次氯酸桶装情况,是否盖严实,是否有泄漏情况,落实好防泄漏措施。
7、装卸次氯酸钠时,场所内5米严禁无关人员靠近。
8、次氯酸钠不得在酸洗环境下进行作业,否则可能会有氯气放出,人员吸入后可能导致中毒事故。
9、各操作人员应严格遵守以上各操作规程,安全管理制度,严格遵守危险化学品有关法律、法规。保障生产安全、人生安全、设备安全,保障生产正常进行。
应急措施
1、隔离泄漏污染区,周围设警告标志,限制出入。建议应急处理人员戴好防毒面具(全面罩),穿防酸碱工作服。不要直接接触泄漏物
次氯酸钠操作规程
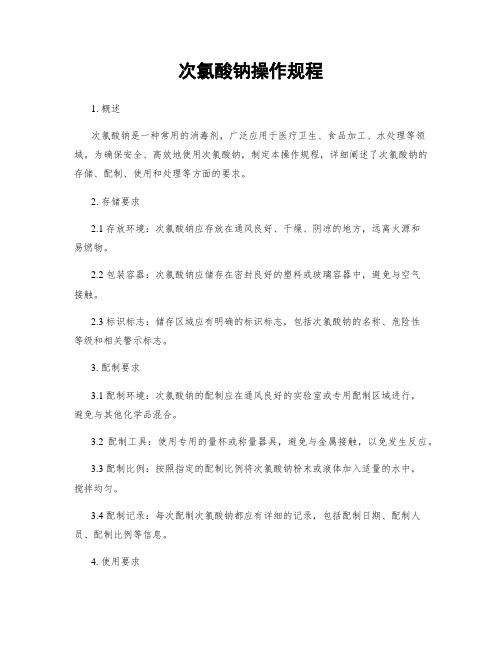
次氯酸钠操作规程1. 概述次氯酸钠是一种常用的消毒剂,广泛应用于医疗卫生、食品加工、水处理等领域。
为确保安全、高效地使用次氯酸钠,制定本操作规程,详细阐述了次氯酸钠的存储、配制、使用和处理等方面的要求。
2. 存储要求2.1 存放环境:次氯酸钠应存放在通风良好、干燥、阴凉的地方,远离火源和易燃物。
2.2 包装容器:次氯酸钠应储存在密封良好的塑料或玻璃容器中,避免与空气接触。
2.3 标识标志:储存区域应有明确的标识标志,包括次氯酸钠的名称、危险性等级和相关警示标志。
3. 配制要求3.1 配制环境:次氯酸钠的配制应在通风良好的实验室或专用配制区域进行,避免与其他化学品混合。
3.2 配制工具:使用专用的量杯或称量器具,避免与金属接触,以免发生反应。
3.3 配制比例:按照指定的配制比例将次氯酸钠粉末或液体加入适量的水中,搅拌均匀。
3.4 配制记录:每次配制次氯酸钠都应有详细的记录,包括配制日期、配制人员、配制比例等信息。
4. 使用要求4.1 人员防护:在使用次氯酸钠前,操作人员应佩戴防护眼镜、手套和防护服,确保安全操作。
4.2 使用工具:使用专用的喷雾器、洗涤器等工具,避免与其他化学品接触。
4.3 使用方法:根据实际需要,将配制好的次氯酸钠均匀喷洒或涂布在需要消毒的表面,保持一定的接触时间。
4.4 使用范围:次氯酸钠适用于消毒各类硬表面,如地板、墙壁、器具等,但不适用于食品直接接触表面。
5. 处理要求5.1 废液处理:使用后的次氯酸钠废液应按照相关法规进行处理,避免直接排放到水源或污水系统中。
5.2 包装废物:将使用过的次氯酸钠包装容器彻底清洗干净,分类投放到相应的垃圾桶中。
5.3 泄漏应急处理:若发生次氯酸钠泄漏事故,应立即采取应急措施,包括戴好防护装备、封堵泄漏源、清除泄漏物等。
6. 应急措施6.1 人员伤害:如不慎接触次氯酸钠,应立即用大量清水冲洗受影响部位,并及时就医。
6.2 火灾事故:次氯酸钠为氧化剂,遇火易燃烧,发生火灾时应立即采取适当的灭火措施,如二氧化碳灭火器等。
次氯酸钠操作规程

次氯酸钠操作规程一、引言次氯酸钠是一种常用的消毒剂,广泛应用于医疗、食品加工、水处理等领域。
为了确保次氯酸钠的安全使用,提高操作人员的操作技能和安全意识,制定本操作规程。
二、适用范围本操作规程适用于所有使用次氯酸钠进行消毒操作的场所和人员。
三、操作人员要求1. 操作人员应接受相关的安全培训,了解次氯酸钠的性质、危害和安全操作规程。
2. 操作人员应穿戴个人防护装备,包括防护眼镜、防护口罩、防护手套和防护服等。
3. 操作人员应具备良好的身体健康状况,不得有皮肤疾病、呼吸道疾病等不适宜操作的情况。
四、设备和材料准备1. 次氯酸钠应存放在干燥、通风良好的地方,避免与有机物、酸性物质等接触。
2. 准备好适量的次氯酸钠溶液,浓度根据具体使用要求进行调整。
3. 操作区域应有足够的插座、水源和排水设施。
五、操作步骤1. 确保操作区域整洁,无杂物和易燃物。
2. 戴上个人防护装备,包括防护眼镜、防护口罩、防护手套和防护服。
3. 将次氯酸钠溶液倒入消毒容器中,根据需要调整浓度。
4. 使用专用工具将次氯酸钠溶液均匀涂抹在待消毒的表面上,确保完全覆盖。
5. 根据需要,可以使用刷子或布进行擦拭,以增加消毒效果。
6. 操作完成后,将使用过的工具和材料进行清洁和消毒,确保不留下次氯酸钠残留。
7. 操作人员应及时洗手,并注意个人卫生。
六、安全注意事项1. 次氯酸钠具有刺激性气味,操作时应确保通风良好,避免长时间暴露。
2. 次氯酸钠溶液应避免与有机物、酸性物质等接触,以免产生有害物质。
3. 操作人员应避免将次氯酸钠溶液溅入眼睛或口腔,如不慎溅入,应立即用清水冲洗。
4. 操作人员应避免长时间接触次氯酸钠溶液,以免对皮肤造成刺激和损伤。
5. 操作人员应定期检查次氯酸钠溶液的浓度,如有需要及时进行调整。
6. 操作人员应遵守相关的法律法规和操作规程,确保操作安全。
七、紧急处理措施1. 如不慎将次氯酸钠溶液溅入眼睛或口腔,应立即用清水冲洗,并及时就医。
次氯酸钠清净乙炔操作规程
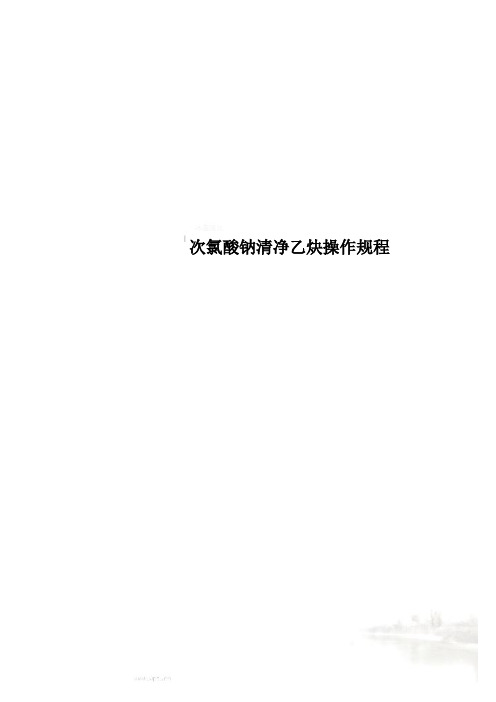
次氯酸钠清净乙炔操作规程次氯酸钠代替浓硫酸净化乙炔气操作规程(暂行)1、产品介绍化学名称:乙炔分子式:C2H2结构式:H—C≡C—H分子量:26.0381.1乙炔的物理性质乙炔是炔烃中最简单的一个化合物,其性质非常活泼,容易进行加成和聚合以及其他化学反应,因此乙炔在有机合成中得到广泛的应用,是化学工业的重要原料之一。
乙炔在常温常压下是比空气略轻,能溶于水和有机溶剂的无色气体,工业乙炔因含有杂质(特别是磷化氢、硫化氢)而带有刺激性臭味。
1.2危险特性:乙炔属易燃易爆品,性能上和氢气相似。
乙炔在高温、加压或与某些物质存在时,具有强烈的爆炸能力。
如压力在1.5表压的气体温度超过550℃即产生爆炸。
特别在高压液态乙炔稍经震动便会爆炸,为避免爆炸危险,一般可用浸有丙酮的多孔物质吸收乙炔一起储存在钢瓶中,以便运输与使用。
乙炔与空气能在很宽的范围内形成爆炸混合物即2.3~81%(其中7~13%最容易爆炸,最适宜的混和比为13%)。
乙炔与氧气形成爆炸混合物范围为2.5~93%(其中30%最容易爆炸)。
与铜、汞、银等形成爆炸性化合物,与氟、氯发生爆炸性反应。
1.3 乙炔产品质量指标1.3.1纯度指标:≥80~85%(V)含氧≤0.2%(V)1.3.2清净效果:不含S、P杂质(AgNO3试纸不变色)2、生产乙炔用原、辅材料规格2.1.1原料电石(学名:碳化钙)碳化钙的分子式:CaC22.1.2理化常数:比重:2.0~2.8(随CaC2减小而增高)含CaC280%时比重为2.324,熔点约为2300℃。
2.1.3 危险特性:由于本品往往含有S、P等杂质与水作用放出硫化氢与磷化氢,当磷化氢含量大于0.08%,硫化氢大于0.15%,易引起自燃爆炸,且本品与水作用生成大量乙炔气,在一定条件下会发生危险。
化学纯的碳化钙几乎是无色透明的结晶体,通常说电石是指工业碳化钙,即除了含大部分碳化钙外,还有少部分其它杂质。
电石的颜色则随之所含的碳化钙纯度不同而不同,有灰色、棕黄色或黑色。
次氯酸钠清净乙炔操作规程
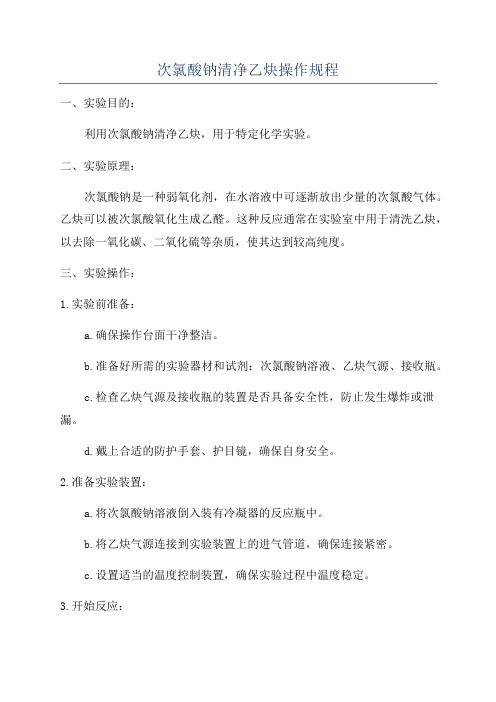
次氯酸钠清净乙炔操作规程一、实验目的:利用次氯酸钠清净乙炔,用于特定化学实验。
二、实验原理:次氯酸钠是一种弱氧化剂,在水溶液中可逐渐放出少量的次氯酸气体。
乙炔可以被次氯酸氧化生成乙醛。
这种反应通常在实验室中用于清洗乙炔,以去除一氧化碳、二氧化硫等杂质,使其达到较高纯度。
三、实验操作:1.实验前准备:a.确保操作台面干净整洁。
b.准备好所需的实验器材和试剂:次氯酸钠溶液、乙炔气源、接收瓶。
c.检查乙炔气源及接收瓶的装置是否具备安全性,防止发生爆炸或泄漏。
d.戴上合适的防护手套、护目镜,确保自身安全。
2.准备实验装置:a.将次氯酸钠溶液倒入装有冷凝器的反应瓶中。
b.将乙炔气源连接到实验装置上的进气管道,确保连接紧密。
c.设置适当的温度控制装置,确保实验过程中温度稳定。
3.开始反应:a.打开乙炔气阀门,将乙炔气导入装有次氯酸钠溶液的反应瓶中。
b.观察反应过程中是否有气体生成,确保反应进行。
c.当乙炔气泡不再冒出时,关闭乙炔气源阀门。
4.收集产物:a.打开反应瓶中的出气阀,使反应瓶内的气体进入接收瓶。
b.观察反应产物的状态和量,记录实验结果。
c.关闭出气阀,取出接收瓶,小心操作,防止产物泄漏。
5.安全操作:a.确保乙炔气源阀门关闭,避免气体泄漏。
b.实验结束后,将使用过的次氯酸钠溶液以及实验产物妥善处理。
c.清洗实验器材,并放回指定位置。
d.整理实验台面,确保实验室环境整洁。
四、实验注意事项:1.保持实验环境干净整洁,防止发生意外。
2.穿戴个人防护装备,包括防护手套、护目镜等。
3.确保乙炔气源及接收装置具备安全性,防止爆炸或泄漏。
4.操作过程中注意使用防护措施,避免接触次氯酸钠溶液或反应产物。
5.实验结束后,及时清洗器材、处理废弃物,维护实验室卫生。
五、实验结果及分析:实验结束后,得到的产物可通过适当的分析方法进行定性和定量分析,以验证清洁乙炔的效果,确保达到预期目标。
六、实验安全性评估:进行此实验时,应注意实验操作的安全性,确保实验过程中不会发生危险事故。
次氯酸钠操作规程

次氯酸钠操作规程一、引言次氯酸钠是一种常用的消毒剂,广泛应用于医疗、食品加工、饮用水处理等领域。
为了确保次氯酸钠的安全使用和操作规范,制定本操作规程,以指导操作人员正确使用次氯酸钠,保障工作场所的安全和环境的卫生。
二、适合范围本操作规程适合于所有使用次氯酸钠的场所和操作人员。
三、安全注意事项1. 次氯酸钠具有一定的腐蚀性,请佩戴防护手套、防护眼镜和防护口罩等个人防护装备。
2. 在操作过程中,应避免次氯酸钠接触皮肤和眼睛,如不慎接触,请即将用水冲洗,并寻求医疗匡助。
3. 次氯酸钠不可与酸性物质混合,以免产生有毒气体。
在储存和使用过程中,请与酸性物质分开存放。
4. 次氯酸钠不可与有机物、还原剂等物质混合,以免发生化学反应。
5. 使用次氯酸钠时,请确保操作区域通风良好,以避免次氯酸钠蒸气积聚。
6. 操作人员应定期接受安全培训,了解次氯酸钠的危害性和应急处理措施。
四、操作流程1. 准备工作a. 穿戴个人防护装备,包括防护手套、防护眼镜和防护口罩。
b. 确保操作区域通风良好。
c. 检查次氯酸钠的储存条件和有效期,确保无异常。
d. 准备好所需的工具和设备。
2. 配制次氯酸钠溶液a. 根据需要的浓度和用途,准确称量次氯酸钠和水的比例。
b. 先将一部份水倒入容器中,再将次氯酸钠缓慢加入水中,搅拌均匀。
c. 注意避免溅出,以免对操作人员造成伤害。
3. 使用次氯酸钠溶液a. 根据需要,将配制好的次氯酸钠溶液倒入使用容器中。
b. 使用时,根据具体要求,选择合适的方法进行消毒或者清洁。
4. 储存次氯酸钠溶液a. 将剩余的次氯酸钠溶液密封保存,避免与其他物质接触。
b. 储存区域应干燥、通风,并远离酸性物质和有机物。
五、事故应急处理1. 溅入眼睛:即将用大量清水冲洗眼睛,持续15分钟,并即将就医。
2. 溅入皮肤:即将脱去受污染的衣物,用大量清水冲洗皮肤,如有症状浮现,请就医。
3. 吸入:迅速转移到通风良好的地方,并保持呼吸道通畅,如有呼吸难点,请就医。
次氯酸钠清净乙炔操作规程

次氯酸钠代替浓硫酸净化乙炔气操作规程(暂行)1、产品介绍化学名称:乙炔分子式:C2H2结构式:H—C≡C—H分子量:26.0381.1乙炔的物理性质乙炔是炔烃中最简单的一个化合物,其性质非常活泼,容易进行加成和聚合以及其他化学反应,因此乙炔在有机合成中得到广泛的应用,是化学工业的重要原料之一。
乙炔在常温常压下是比空气略轻,能溶于水和有机溶剂的无色气体,工业乙炔因含有杂质(特别是磷化氢、硫化氢)而带有刺激性臭味。
1.2危险特性:乙炔属易燃易爆品,性能上和氢气相似。
乙炔在高温、加压或与某些物质存在时,具有强烈的爆炸能力。
如压力在1.5表压的气体温度超过550℃即产生爆炸。
特别在高压液态乙炔稍经震动便会爆炸,为避免爆炸危险,一般可用浸有丙酮的多孔物质吸收乙炔一起储存在钢瓶中,以便运输与使用。
乙炔与空气能在很宽的范围内形成爆炸混合物即2.3~81%(其中7~13%最容易爆炸,最适宜的混和比为13%)。
乙炔与氧气形成爆炸混合物范围为2.5~93%(其中30%最容易爆炸)。
与铜、汞、银等形成爆炸性化合物,与氟、氯发生爆炸性反应。
1.3 乙炔产品质量指标1.3.1纯度指标:≥80~85%(V)含氧≤0.2%(V)1.3.2清净效果:不含S、P杂质(AgNO3试纸不变色)2、生产乙炔用原、辅材料规格2.1.1原料电石(学名:碳化钙)碳化钙的分子式:CaC22.1.2理化常数:比重:2.0~2.8(随CaC2减小而增高)含CaC280%时比重为2.324,熔点约为2300℃。
2.1.3 危险特性:由于本品往往含有S、P等杂质与水作用放出硫化氢与磷化氢,当磷化氢含量大于0.08%,硫化氢大于0.15%,易引起自燃爆炸,且本品与水作用生成大量乙炔气,在一定条件下会发生危险。
化学纯的碳化钙几乎是无色透明的结晶体,通常说电石是指工业碳化钙,即除了含大部分碳化钙外,还有少部分其它杂质。
电石的颜色则随之所含的碳化钙纯度不同而不同,有灰色、棕黄色或黑色。
次氯酸钠操作规程

次氯酸钠操作规程标题:次氯酸钠操作规程引言概述:次氯酸钠是一种常用的消毒剂,正确的操作规程对于保障人员安全和消毒效果至关重要。
本文将详细介绍次氯酸钠的操作规程,包括操作前的准备工作、正确的操作步骤、注意事项等内容。
一、操作前的准备工作1.1 确认次氯酸钠的浓度和用途:根据具体的消毒对象和需要的消毒效果,选择合适的次氯酸钠浓度和用途。
1.2 准备好必要的个人防护用具:包括手套、护目镜、口罩等,确保操作时不会接触到次氯酸钠。
1.3 检查消毒设备和器具:确保消毒设备和器具的完好无损,无漏氯现象,以确保消毒效果。
二、正确的操作步骤2.1 按照规定的浓度将次氯酸钠溶液配制好:根据需要消毒的对象和消毒的要求,按照规定的比例将次氯酸钠溶液配制好。
2.2 将配制好的次氯酸钠溶液均匀地涂抹在消毒对象表面:确保消毒液均匀地覆盖到所有需要消毒的部位。
2.3 按照规定的时间进行消毒:根据次氯酸钠的浓度和消毒对象的不同,确定消毒的时间,确保消毒效果。
三、注意事项3.1 避免与其他化学物质混合使用:次氯酸钠与其他化学物质混合可能产生有毒气体,应避免混合使用。
3.2 避免长时间接触次氯酸钠:长时间接触次氯酸钠可能引起皮肤过敏或灼伤,应避免长时间接触。
3.3 注意通风和排水:在操作次氯酸钠时,应保持良好的通风,确保操作环境中有足够的新鲜空气流通,同时要及时排除消毒废液。
四、事故处理4.1 发生溅洒事故时应立即用清水冲洗:如果次氯酸钠溶液不慎溅洒到皮肤或眼睛上,应立即用清水冲洗,并及时就医。
4.2 发生误食事故时应立即就医:如果误食次氯酸钠,应立即就医,并告知医生所误食的次氯酸钠浓度和量。
4.3 发生泄漏事故时应及时处理:如果次氯酸钠溶液泄漏,应立即采取措施进行泄漏处理,避免对环境造成污染。
五、清洗和存储5.1 清洗消毒设备和器具:在完成消毒任务后,应及时清洗消毒设备和器具,确保无残留的次氯酸钠溶液。
5.2 存储次氯酸钠溶液:次氯酸钠溶液应存放在阴凉干燥的地方,避免阳光直射和高温。
次氯酸钠操作规程

次氯酸钠操作规程一、引言次氯酸钠是一种常用的消毒剂,广泛应用于医疗、食品加工、水处理等领域。
为确保次氯酸钠的安全使用,提高操作人员的工作效率,制定本操作规程。
二、适用范围本操作规程适用于所有使用次氯酸钠进行消毒的场所,包括但不限于医院、食品加工厂、水处理厂等。
三、操作人员要求1. 操作人员必须接受相关培训,了解次氯酸钠的性质、危害以及正确操作方法。
2. 操作人员必须具备良好的健康状况,无传染病史和对次氯酸钠过敏的情况。
3. 操作人员必须佩戴个人防护装备,包括护目镜、防护口罩、防护服和手套等。
4. 操作人员必须严格遵守操作规程,不得擅自修改操作步骤或忽略安全要求。
四、设备和材料1. 次氯酸钠:确保次氯酸钠的纯度符合标准要求。
2. 水:使用纯净水或经过处理的水。
3. 容器:使用耐腐蚀性能良好的容器,避免次氯酸钠与其他物质发生反应。
五、操作步骤1. 准备工作a. 检查次氯酸钠的包装是否完好,确认纯度符合要求。
b. 准备所需的个人防护装备。
c. 清洁操作区域,确保无杂物和污染。
2. 配制次氯酸钠溶液a. 根据需要的浓度和用途,计算所需次氯酸钠和水的比例。
b. 使用称量器具准确称取次氯酸钠和水。
c. 将次氯酸钠逐渐加入水中,搅拌均匀,直至完全溶解。
3. 操作过程a. 戴上护目镜、防护口罩、防护服和手套。
b. 将配制好的次氯酸钠溶液倒入使用容器中。
c. 使用专用喷雾器或喷洒器将次氯酸钠溶液均匀喷洒在需要消毒的表面上。
d. 注意避免次氯酸钠溶液接触皮肤和眼睛,如有意外接触,立即用大量清水冲洗。
4. 消毒结束a. 消毒时间根据需要和要求进行控制。
b. 消毒结束后,使用清水彻底清洗消毒区域,确保无残留次氯酸钠溶液。
六、安全注意事项1. 次氯酸钠具有一定的腐蚀性,避免与皮肤和眼睛直接接触。
2. 操作过程中应避免次氯酸钠溶液喷洒到人体或其他物体上。
3. 操作过程中应保持良好的通风环境,避免次氯酸钠溶液的蒸气浓度过高。
次氯酸钠操作规程

次氯酸钠操作规程一、引言次氯酸钠是一种常用的消毒剂,广泛应用于医疗、饮用水处理、食品加工等领域。
为确保次氯酸钠的安全使用和有效消毒,制定本操作规程,以指导操作人员正确操作。
二、适用范围本操作规程适用于所有使用次氯酸钠进行消毒的场所和人员。
三、操作人员要求1. 操作人员应接受相关培训,了解次氯酸钠的性质、危害和安全操作方法。
2. 操作人员应具备良好的健康状况,无任何传染性疾病和过敏反应。
3. 操作人员应佩戴个人防护装备,包括防护眼镜、口罩、手套和防护服。
四、设备和材料准备1. 次氯酸钠溶液:按照制定的浓度配制次氯酸钠溶液,确保浓度准确。
2. 消毒设备:根据需要选择合适的消毒设备,如喷雾器、喷洒器等。
3. 清洁用具:准备清洁用具,如刷子、抹布等,用于清洁被消毒物体表面。
五、操作步骤1. 检查设备和材料:确认次氯酸钠溶液浓度准确,检查消毒设备和清洁用具的完好性。
2. 确定消毒对象:根据需要确定消毒对象,如工作台面、器械等。
3. 预处理:将消毒对象表面的杂物清除干净,确保表面干燥。
4. 次氯酸钠溶液使用:将适量的次氯酸钠溶液倒入消毒设备中,根据需要调整喷雾或喷洒的浓度和量。
5. 开始消毒:将消毒设备保持适当距离,均匀喷洒或喷雾次氯酸钠溶液于消毒对象表面,确保覆盖全面。
6. 消毒时间:根据需要,保持次氯酸钠溶液在消毒对象表面停留一定时间,确保消毒效果。
7. 清洁处理:使用清洁用具清洁被消毒物体表面,将残留的次氯酸钠溶液彻底清除。
8. 完成消毒:确认消毒对象表面干燥,无次氯酸钠残留后,方可使用。
六、安全注意事项1. 次氯酸钠溶液具有一定腐蚀性,操作人员应佩戴防护装备,避免直接接触皮肤和眼睛。
2. 操作人员应遵循正确的操作方法,避免溅射和吸入次氯酸钠溶液。
3. 操作人员在操作过程中应注意通风,确保室内空气流通。
4. 次氯酸钠溶液应存放在阴凉干燥的地方,远离火源和易燃物。
5. 操作人员应定期检查消毒设备和清洁用具的完好性,如发现损坏应及时更换。
次氯酸钠操作规程
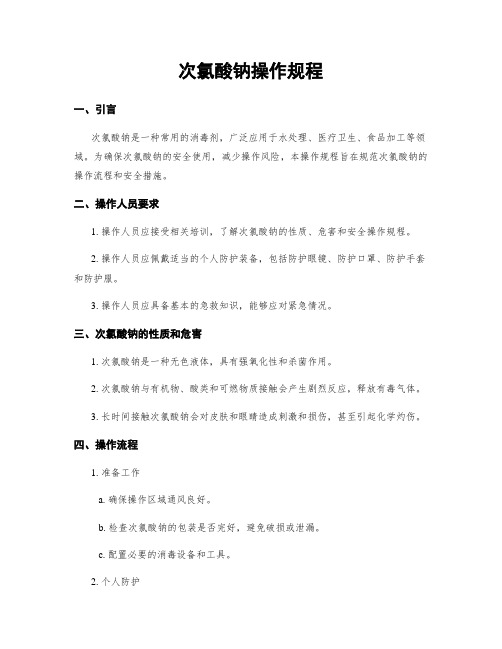
次氯酸钠操作规程一、引言次氯酸钠是一种常用的消毒剂,广泛应用于水处理、医疗卫生、食品加工等领域。
为确保次氯酸钠的安全使用,减少操作风险,本操作规程旨在规范次氯酸钠的操作流程和安全措施。
二、操作人员要求1. 操作人员应接受相关培训,了解次氯酸钠的性质、危害和安全操作规程。
2. 操作人员应佩戴适当的个人防护装备,包括防护眼镜、防护口罩、防护手套和防护服。
3. 操作人员应具备基本的急救知识,能够应对紧急情况。
三、次氯酸钠的性质和危害1. 次氯酸钠是一种无色液体,具有强氧化性和杀菌作用。
2. 次氯酸钠与有机物、酸类和可燃物质接触会产生剧烈反应,释放有毒气体。
3. 长时间接触次氯酸钠会对皮肤和眼睛造成刺激和损伤,甚至引起化学灼伤。
四、操作流程1. 准备工作a. 确保操作区域通风良好。
b. 检查次氯酸钠的包装是否完好,避免破损或泄漏。
c. 配置必要的消毒设备和工具。
2. 个人防护a. 戴上防护眼镜,防止次氯酸钠溅入眼睛。
b. 戴上防护口罩,防止吸入次氯酸钠的气体。
c. 戴上防护手套,避免直接接触次氯酸钠。
d. 穿戴防护服,保护皮肤免受次氯酸钠的损伤。
3. 次氯酸钠的配制a. 根据需要的浓度和用途,准确称量次氯酸钠粉末。
b. 将粉末加入适量的水中,搅拌溶解。
c. 配制好的次氯酸钠溶液应密封保存,避免与空气接触。
4. 次氯酸钠的使用a. 在使用前,先检查次氯酸钠溶液的浓度是否符合要求。
b. 使用专用的喷雾器、喷洒器等工具进行喷洒或消毒操作。
c. 注意避免次氯酸钠溅入眼睛、口腔或皮肤,如有接触应立即用清水冲洗。
5. 次氯酸钠的存储a. 将次氯酸钠存放在干燥、通风、避光的地方。
b. 避免与有机物、酸类和可燃物质存放在一起。
六、事故应急处理1. 如发生次氯酸钠泄漏或溅入眼睛、口腔或皮肤,应立即采取以下措施:a. 迅速将受伤人员移到通风处,保持呼吸道通畅。
b. 如有眼部接触,立即用大量清水冲洗至少15分钟。
c. 如有皮肤接触,立即脱去污染的衣物,用大量清水冲洗至少15分钟。
次氯酸钠操作规程

次氯酸钠操作规程一、引言次氯酸钠是一种常用的消毒剂,广泛应用于水处理、卫生防疫和食品加工等领域。
为确保次氯酸钠的安全使用和操作规范,制定本操作规程。
二、适用范围本操作规程适用于所有使用次氯酸钠的工作场所和操作人员。
三、安全要求1. 操作人员应经过专业培训,熟悉次氯酸钠的性质、危害和安全操作方法。
2. 操作人员应佩戴个人防护装备,包括防护眼镜、防护口罩、防护手套和防护服等。
3. 操作人员应定期接受健康体检,确保身体状况适宜从事次氯酸钠操作工作。
4. 操作场所应通风良好,避免次氯酸钠蒸气积聚。
5. 次氯酸钠应储存在干燥、阴凉、通风的地方,远离可燃物和有机物。
四、操作流程1. 准备工作a. 确认操作场所的通风情况,并开启通风设备。
b. 检查次氯酸钠储存容器的密封性和标识,确保无泄漏和混淆。
c. 穿戴个人防护装备,包括防护眼镜、防护口罩、防护手套和防护服等。
2. 配制次氯酸钠溶液a. 根据需要的浓度,准确称量次氯酸钠和水的比例。
b. 先向容器中加入适量的水,再将次氯酸钠缓慢加入,并充分搅拌溶解。
c. 配制好的溶液应立即使用,不得长时间存放。
3. 使用次氯酸钠溶液a. 在使用前,先检查溶液的浓度和pH值是否符合要求。
b. 使用时应佩戴手套,并避免溅入眼睛和口鼻。
c. 根据需要,将次氯酸钠溶液喷洒、擦拭或浸泡在需要消毒的物体表面。
d. 操作结束后,应及时清洗工具和设备,避免溶液残留。
五、急救措施1. 眼部接触:立即用大量清水冲洗眼睛,至少持续15分钟,并寻求医疗救助。
2. 皮肤接触:立即脱去被污染的衣物,用大量清水冲洗皮肤,如有刺激或不适,及时就医。
3. 吸入:将患者移至通风处,保持呼吸道通畅,如有呼吸困难,立即进行人工呼吸或CPR,并立即就医。
4. 食入:立即给予大量清水漱口,并立即就医。
六、事故应急处理1. 发生泄漏或溢出时,应立即停止操作,迅速撤离人员,并采取措施防止扩散。
2. 小范围泄漏可使用吸附剂或稀释剂进行清理,大范围泄漏应呼叫专业清洁公司进行处理。
次氯酸钠操作规程
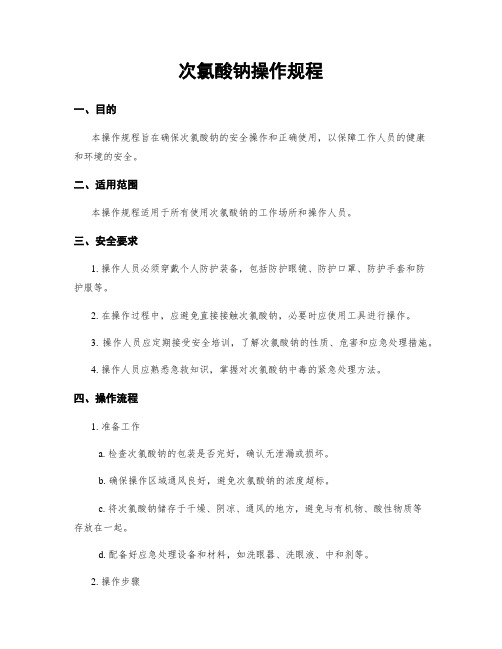
次氯酸钠操作规程一、目的本操作规程旨在确保次氯酸钠的安全操作和正确使用,以保障工作人员的健康和环境的安全。
二、适用范围本操作规程适用于所有使用次氯酸钠的工作场所和操作人员。
三、安全要求1. 操作人员必须穿戴个人防护装备,包括防护眼镜、防护口罩、防护手套和防护服等。
2. 在操作过程中,应避免直接接触次氯酸钠,必要时应使用工具进行操作。
3. 操作人员应定期接受安全培训,了解次氯酸钠的性质、危害和应急处理措施。
4. 操作人员应熟悉急救知识,掌握对次氯酸钠中毒的紧急处理方法。
四、操作流程1. 准备工作a. 检查次氯酸钠的包装是否完好,确认无泄漏或损坏。
b. 确保操作区域通风良好,避免次氯酸钠的浓度超标。
c. 将次氯酸钠储存于干燥、阴凉、通风的地方,避免与有机物、酸性物质等存放在一起。
d. 配备好应急处理设备和材料,如洗眼器、洗眼液、中和剂等。
2. 操作步骤a. 戴上个人防护装备,确保安全。
b. 使用准确的计量器具,按照所需的浓度和用量准确称取次氯酸钠。
c. 将次氯酸钠溶解于适量的水中,搅拌均匀直至溶解完全。
d. 在操作过程中,避免次氯酸钠溶液的飞溅和喷洒,注意操作的平稳和稳定。
e. 操作完成后,将废液进行正确处理,避免对环境造成污染。
五、应急处理1. 气味刺激:如次氯酸钠溶液的气味刺激到眼睛和呼吸道,应立即远离污染源,并用清水冲洗受到污染的部位,如有必要,就医治疗。
2. 溶液溅入眼睛:如次氯酸钠溶液溅入眼睛,应立即用大量清水冲洗眼睛,至少冲洗15分钟,并及时就医。
3. 溶液接触皮肤:如次氯酸钠溶液接触皮肤,应立即用大量清水冲洗受到污染的皮肤,如有必要,使用中和剂中和溶液,并及时就医。
4. 溶液误服:如次氯酸钠溶液误服,应立即漱口,并给予大量清水稀释。
不要催吐,立即就医。
六、储存和运输1. 次氯酸钠应储存在干燥、阴凉、通风的库房中,远离有机物、酸性物质等。
2. 储存区域应设有明显的标识,禁止与其他物品混放。
次氯酸钠操作规程

次氯酸钠操作规程一、引言次氯酸钠是一种常用的消毒剂,广泛应用于医疗、食品加工、水处理等领域。
为了确保次氯酸钠的安全使用和操作,制定本操作规程,以指导操作人员正确、安全地使用次氯酸钠。
二、适用范围本操作规程适用于所有使用次氯酸钠进行消毒的场所,包括但不限于医院、实验室、食品加工厂、游泳池等。
三、安全注意事项1. 操作人员必须穿戴个人防护装备,包括防护眼镜、防护口罩、防护手套和防护服等。
2. 操作人员应接受相关培训,了解次氯酸钠的性质、危害和正确操作方法。
3. 次氯酸钠应存放在干燥、阴凉、通风良好的地方,远离可燃物和有机物。
4. 操作过程中应避免与皮肤直接接触,如不慎接触,应立即用大量清水冲洗,并及时就医。
5. 操作人员应定期检查次氯酸钠的储存条件和有效期,如发现异常应及时更换。
四、操作步骤1. 准备工作a. 检查次氯酸钠储存条件和有效期,确保正常可用。
b. 穿戴个人防护装备,包括防护眼镜、防护口罩、防护手套和防护服等。
c. 准备好消毒所需的工具和器材,如喷雾器、拖把等。
2. 稀释次氯酸钠a. 根据需要的浓度,将适量的次氯酸钠溶解于清水中,搅拌均匀。
b. 注意稀释过程中的安全,避免溅出和直接接触。
3. 操作消毒a. 使用喷雾器将稀释后的次氯酸钠均匀喷洒在需要消毒的表面上,确保覆盖全面。
b. 如需消毒大面积地板,可使用拖把蘸取稀释后的次氯酸钠,均匀涂抹在地板上。
c. 注意避免喷洒到电器、食品和敏感物品上,避免直接接触皮肤。
4. 消毒时间a. 根据消毒对象的不同,设定不同的消毒时间,确保消毒效果。
b. 在消毒时间内,操作人员应离开消毒区域,避免直接接触消毒剂。
5. 清洗和处理a. 消毒结束后,使用清水彻底清洗消毒区域,确保次氯酸钠残留物被彻底清除。
b. 将使用过的工具和器材进行清洗和消毒,以防止交叉感染。
c. 次氯酸钠的废弃物应按照相关规定进行分类和处理。
五、事故应急处理1. 如发生次氯酸钠溅入眼睛或皮肤接触,应立即用大量清水冲洗,并及时就医。
次氯酸钠操作规程

次氯酸钠操作规程一、引言次氯酸钠是一种常用的消毒剂,广泛应用于医疗、食品加工、水处理等领域。
为了确保次氯酸钠的安全使用,本操作规程旨在规范次氯酸钠的操作流程,保障操作人员的安全和工作效率。
二、适用范围本操作规程适用于所有使用次氯酸钠进行消毒的场所和操作人员。
三、安全注意事项1. 次氯酸钠具有一定的腐蚀性和氧化性,操作人员在操作过程中应佩戴防护手套、护目镜、防护服等个人防护装备。
2. 操作人员应对次氯酸钠的性质、特点和操作流程进行充分了解,遵守操作规程,严禁擅自更改操作步骤。
3. 次氯酸钠应存放在阴凉、干燥、通风良好的地方,远离火源和可燃物。
4. 操作人员在操作过程中应保持清醒状态,禁止饮食、吸烟等行为。
5. 操作结束后,应及时清理操作区域,将使用过的器材进行妥善处理。
四、操作流程1. 准备工作a. 检查次氯酸钠的包装是否完好,确认有效期是否过期。
b. 准备个人防护装备,包括防护手套、护目镜、防护服等。
c. 确保操作区域干净整洁,无杂物和可燃物。
2. 配制次氯酸钠溶液a. 根据需要的浓度和用途,准确称量次氯酸钠和水的比例。
b. 将准确称量的次氯酸钠加入适量的水中,搅拌至溶解。
3. 操作过程a. 穿戴个人防护装备,确保安全。
b. 将配制好的次氯酸钠溶液倒入使用容器中。
c. 根据需要,使用喷雾器、拖把等工具将溶液均匀地喷洒或涂抹在待消毒的表面上。
d. 等待一定时间,确保次氯酸钠溶液对目标区域进行充分消毒。
e. 使用清水将消毒区域进行彻底清洗,确保次氯酸钠残留物被彻底清除。
5. 操作结束a. 关闭次氯酸钠容器,确保密封。
b. 将使用过的个人防护装备进行清洗和消毒。
c. 清理操作区域,将使用过的器材进行妥善处理。
d. 将次氯酸钠的包装进行妥善保存,避免阳光直射和潮湿环境。
六、应急措施1. 如意外溅入眼睛,应立即用大量清水冲洗眼睛,必要时就医。
2. 如误食或误吸入,应立即向医生求助,并告知医生次氯酸钠的成分和浓度。
次氯酸钠操作规程
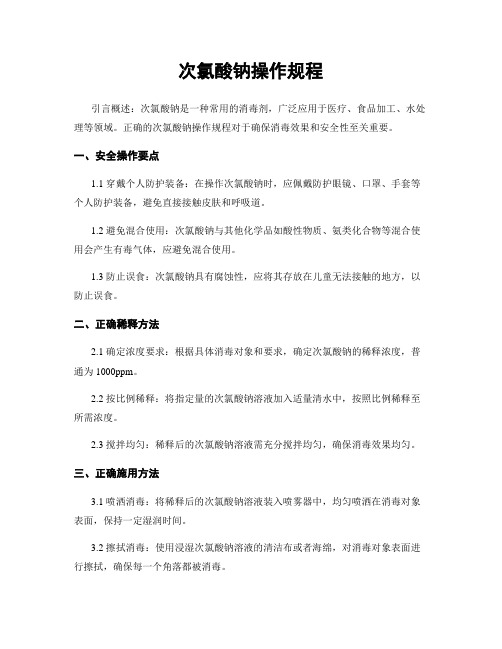
次氯酸钠操作规程引言概述:次氯酸钠是一种常用的消毒剂,广泛应用于医疗、食品加工、水处理等领域。
正确的次氯酸钠操作规程对于确保消毒效果和安全性至关重要。
一、安全操作要点1.1 穿戴个人防护装备:在操作次氯酸钠时,应佩戴防护眼镜、口罩、手套等个人防护装备,避免直接接触皮肤和呼吸道。
1.2 避免混合使用:次氯酸钠与其他化学品如酸性物质、氨类化合物等混合使用会产生有毒气体,应避免混合使用。
1.3 防止误食:次氯酸钠具有腐蚀性,应将其存放在儿童无法接触的地方,以防止误食。
二、正确稀释方法2.1 确定浓度要求:根据具体消毒对象和要求,确定次氯酸钠的稀释浓度,普通为1000ppm。
2.2 按比例稀释:将指定量的次氯酸钠溶液加入适量清水中,按照比例稀释至所需浓度。
2.3 搅拌均匀:稀释后的次氯酸钠溶液需充分搅拌均匀,确保消毒效果均匀。
三、正确施用方法3.1 喷洒消毒:将稀释后的次氯酸钠溶液装入喷雾器中,均匀喷洒在消毒对象表面,保持一定湿润时间。
3.2 擦拭消毒:使用浸湿次氯酸钠溶液的清洁布或者海绵,对消毒对象表面进行擦拭,确保每一个角落都被消毒。
3.3 等待干燥:消毒完成后,让消毒对象自然晾干,不要用水冲洗,以保持消毒效果。
四、正确处理废液4.1 废液处理:次氯酸钠溶液在使用后属于废液,应按照当地环保法规进行处理,不可直接排放到下水道或者环境中。
4.2 中和处理:可以使用中和剂中和废液中的次氯酸钠,然后按照规定的程序进行处理。
4.3 定期清洁:消毒器具和容器应定期清洁,避免次氯酸钠残留导致交叉污染。
五、存储注意事项5.1 避光存储:次氯酸钠应存放在阴凉、干燥、避光的地方,避免阳光直射导致其失效。
5.2 隔离存放:次氯酸钠应与食品、饮料等物品隔离存放,避免交叉污染。
5.3 定期检查:定期检查次氯酸钠的存储条件和有效期,确保其质量和效果。
结语:遵循正确的次氯酸钠操作规程,不仅可以确保消毒效果,还可以保障操作人员的安全。
- 1、下载文档前请自行甄别文档内容的完整性,平台不提供额外的编辑、内容补充、找答案等附加服务。
- 2、"仅部分预览"的文档,不可在线预览部分如存在完整性等问题,可反馈申请退款(可完整预览的文档不适用该条件!)。
- 3、如文档侵犯您的权益,请联系客服反馈,我们会尽快为您处理(人工客服工作时间:9:00-18:30)。
次氯酸钠清净乙炔操作规程————————————————————————————————作者:————————————————————————————————日期:次氯酸钠代替浓硫酸净化乙炔气操作规程(暂行)1、产品介绍化学名称:乙炔分子式:C2H2结构式:H—C≡C—H分子量:26.0381.1乙炔的物理性质乙炔是炔烃中最简单的一个化合物,其性质非常活泼,容易进行加成和聚合以及其他化学反应,因此乙炔在有机合成中得到广泛的应用,是化学工业的重要原料之一。
乙炔在常温常压下是比空气略轻,能溶于水和有机溶剂的无色气体,工业乙炔因含有杂质(特别是磷化氢、硫化氢)而带有刺激性臭味。
1.2危险特性:乙炔属易燃易爆品,性能上和氢气相似。
乙炔在高温、加压或与某些物质存在时,具有强烈的爆炸能力。
如压力在1.5表压的气体温度超过550℃即产生爆炸。
特别在高压液态乙炔稍经震动便会爆炸,为避免爆炸危险,一般可用浸有丙酮的多孔物质吸收乙炔一起储存在钢瓶中,以便运输与使用。
乙炔与空气能在很宽的范围内形成爆炸混合物即2.3~81%(其中7~13%最容易爆炸,最适宜的混和比为13%)。
乙炔与氧气形成爆炸混合物范围为2.5~93%(其中30%最容易爆炸)。
与铜、汞、银等形成爆炸性化合物,与氟、氯发生爆炸性反应。
1.3 乙炔产品质量指标1.3.1纯度指标:≥80~85%(V)含氧≤0.2%(V)1.3.2清净效果:不含S、P杂质(AgNO3试纸不变色)2、生产乙炔用原、辅材料规格2.1.1原料电石(学名:碳化钙)碳化钙的分子式:CaC22.1.2理化常数:比重:2.0~2.8(随CaC2减小而增高)含CaC280%时比重为2.324,熔点约为2300℃。
2.1.3 危险特性:由于本品往往含有S、P等杂质与水作用放出硫化氢与磷化氢,当磷化氢含量大于0.08%,硫化氢大于0.15%,易引起自燃爆炸,且本品与水作用生成大量乙炔气,在一定条件下会发生危险。
化学纯的碳化钙几乎是无色透明的结晶体,通常说电石是指工业碳化钙,即除了含大部分碳化钙外,还有少部分其它杂质。
电石的颜色则随之所含的碳化钙纯度不同而不同,有灰色、棕黄色或黑色。
碳化钙含量高时呈现紫色。
2.1.4碳化钙的技术要求:安全试验方法,检验规则及标志,包装、运输、贮存等,都必须符合中华人民共和国标准GB10665—89的要求。
指标名称(发气量L/Kg)指标优级品一级品二级品三级品粒度mm 81~15051~8025~50 305 295 280 255 305 295 280 255 300 290 275 250乙炔中磷化氢%(V)≤0.06 0.08 0.08 0.08乙炔中硫化氢%(V)≤0.10 0.10 0.15 0.153、乙炔的生产原理3.1电石水解反应原理在湿式发生器中电石加入液相水中,即水解反应生成乙炔气体,其反应如下: CaC2+2H2O = Ca(OH)2+CH≡CH ↑+130KJ/mol (3lkCal/mol)由于工业品电石有杂质,在发生器液相中也有相应发生副反应,生成磷化氢,硫化氢等杂质气体,其反应如下:CaO+H2O = Ca(OH)2+63.6KJ/mol (15.2kCal/mol)CaS+2H2O = Ca(OH)2 +H2SCa3N2+6H2O = 3Ca(OH)2+2NH3Ca3P2+6H2O = 3Ca(OH)2+2PH3Ca2Si+4H2O = 2Ca(OH)2+SiH4Ca3AS2+6H2O = 3Ca(OH)2+2AsH3因此,发生器排出的粗乙炔气体中含有上述副反应产生的磷化氢、硫化氢、氨等杂质气体。
水解反应生成大量的氢氧化钙副产物,使系统呈碱性。
由于硫化氢在水中溶解度大于磷化氢,使粗乙炔气中有较多的磷化氢(如数百PPm)及较少的硫化氢(数十至数百PPm),磷化物尚能以P2H4形式存在,它在空气中自燃。
由于湿式发生器温度控制在80℃以上,有双分子乙炔加成反应生成乙烯基及乙硫醚的可能,这两种杂质一般可达到数10PPm以上。
在85℃反应温度下,由于水的大量蒸发汽化,使粗乙炔气夹带大量的水蒸汽。
一般水蒸汽:乙炔≈ 1:1电石的水解反应是液固相反应,电石与水的接触面积越大,即电石粒度越小时,其水解速度也越快。
但粒度也不宜过小,否则水解速度太快,使反应放出的热量不能及时移走,易发生局部过热而引起乙炔分解和热聚,进而使温度剧升而发生爆炸。
粒度过大,加料时,容易卡住,并且水解反应缓慢,发生器底部间歇排出渣浆中容易夹带未水解的电石,造成电石消耗定额上升。
发生器的结构(如挡板层数、搅拌转速、耙齿角度等)对电石在发生器中停留时间和电石表面生成的氢氧化钙的移去速度有较大影响,所以,对一定粒度的电石,既应该保证其完全水解的停留时间,又需将电石表面的Ca(OH)2“膜”及时移去,使电石表面与水有不断更新的接触表面。
一般对于三至六层挡板连续搅拌的发生器,电石的停留时间较长,水解反应比较完全;但一些小型的摇篮式发生器,水解过程就缓慢得多,排渣中易发现未水解的“生电石”。
但是,即使结构非常完善的发生器,排出电石渣中仍含有超过反应温度下饱和溶解度的乙炔,因此,根据目前发生器结构及电石破碎损耗等因素考虑,粒度宜控制在80mm以下,如对于4~6层挡板者可选用80mm 以下,而2-3层挡板宜选用50mm以下。
除上述电石粒度外,温度对于电石水解反应速度的影响也是显著的。
经实验发现在50℃以下每升高1℃使水解速度加快1%,而在-35℃以下的寒冷地区,电石在盐水中的反应是非常缓慢的。
理论上,每吨电石水解需要0.56吨的水,在绝热反应(无外冷却)下,水解反应热会使系统温度急剧升到几百度以上。
因此,在湿式发生器中都采用过量水来移去反应热,并稀释副产物Ca(OH)2以利于管道排放。
总加水量与电石投料量之比值称作水比,实验证明,系统中渣浆含固量在0~20%范围内,电石水解速度含固量影响不大,含固量超过此范围时,因电石表面与水的接触受到显著阻碍,如含固量达60%左右,水解速度减慢到几倍,发气量也只有原来的1/5。
因此在湿式反应器中,反应温度是和水比相对应的,工业生产上就是借减少加水量(即水比)来提高反应温度,其控制的极限是不使水比过低,造成渣浆含固量过高,以至排渣系统造成沉淀堵塞。
通过热量衡算,可得到不同反应温度时对应的水比及乙炔在发生器中的总损失,其结果列下表反应温度对水解反应的影响反应温度℃电石发气量l/Kg加水量(t水/t电石)电石渣含固量%乙炔损失%40 24427530017.2818.5919.446.455.975.725.55.25.060 2442753008.158.619.1012.7512.0311.462.01.91.880 2442753004.384.554.7721.3720.5719.800.910.840.80由上表可见,反应温度越高,则乙炔总损失越少,而发生器排出的电石渣浆含固量也相应上升。
过高的反应温度将导致排渣困难。
另外粗乙炔气中的水蒸汽含量相应增加,造成冷却负荷加大,以及从安全生产方面考虑,不宜使温度控制过高,一般根据已有生产经验以80~90℃范围为好。
3.2乙炔的清净原理如前所述,由于电石内杂质的存在,使粗乙炔气中常含有硫化氢、磷化氢、氨、砷化氢等杂质气体。
它们会对合成反应造成较大影响。
其中磷化氢(特别是P2H4)会降低乙炔气自燃点,与空气接触会自燃,因此从生产及安全角度上看都必须除去乙炔气中的杂质。
净化乙炔的方法很多,其原理是一样的,即利用氧化剂以氧化除去乙炔中的杂质。
目前多数工厂采用次氯酸钠液体清净剂。
次氯酸钠分子式:NaClO,分子量:74.5,在受热时易分解,是一种强氧化剂,有强烈的刺激性,对人体有害。
NaClO作清净剂的原理是:利用NaClO的氧化性将乙炔中的硫化氢、磷化氢等杂质氧化成酸性物质而除去,其反应式如下:PH3+4NaClO = H3PO4+4NaClH2S+4NaClO = H2SO4+4NaClSiH4+4NaClO = SiO2+2H2O+4NaClAsH3+4NaClO = H3AsO4+4NaCl清净过程的反应产物磷酸,硫酸等由以后的碱洗过程予以中和为盐类,再由废碱液排出:2NaOH+H2SO4 = Na2SO4+2H2O3NaOH+H3PO4 = Na3PO4+3H2O3NaOH+H3AsO4 = Na3AsO4+3H2O2NaOH+SiO2 = Na2SiO3+H2O2NaOH+CO2 = Na2CO3+H2O关于液体清净剂次氯酸钠溶液浓度和PH值的选择,主要考虑到清净效果及安全因素两个方面。
实验结果表明,当次氯酸钠溶液有效率在0.05%以下和PH值在8以上(见下表),则清净(氧化)效果下降。
而当有效率在0.15%以上(特别在PH值低时),容易生成氯乙炔而发生爆炸。
次氯酸钠PH值对清净效果的影响溶液PH值硫化氢含量% 磷化氢含量%7.18 0.00478 0.002808.25 0.00775 0.003719.22 0.00841 0.0039510.24 0.01174 0.0046211.18 0.01130 0.00560当有效氯达到0.25%以上时,无论在气相还是在液相中,均容易发生上述激烈反应而爆炸,阳光将促进这一反应过程。
上述氯乙炔是极不稳定的化合物,遇空气也易着火和爆炸,如中和塔换碱时,或次氯酸钠废水排放时,以及开车前设备管道内空气未排净时均容易发生。
对于有效氯(含量为0.06~0.15%)的多次试验,未发现爆炸现象,且清净效果在中性或微碱性时也较好。
此外,尚对有效氯含量0.06~0.15%次氯酸钠溶液的清净系统,进行直接补加1%左右浓次氯酸钠试验,发现有火花及爆炸发生。
因此,根据上述诸多因素,以及采样测定有效氯的可能误差,塔内次氯酸钠溶液的有效氯含量不低于0.06%,而补充新鲜溶液的有效氯控制在0.08~0.12%范围内,PH值在7~8为宜。
4、生产工艺流程4.1工艺流程图见附图。
4.2工艺流程简述自破碎合格的电石装桶进入电石存放间,密封储存。
由人工运至发生器房,通过电葫芦吊至发生器平台上,间歇加入发生器内,电石遇发生器内水反应生成乙炔气从发生器顶部逸出经填料塔,进入正水封,从正水封出来的气体进入水洗塔、5℃水冷却器、低压干燥器,然后进入清净系统。
电石水解放出大量的热,因此需要不断地向发生器内加水,电石水解后稀电石渣浆经溢流管排出,发生器底部较浓渣浆定期由排渣阀排放。
从发生器来的乙炔气经过水洗塔,采用深井水进行冷却。
从水洗塔出来的乙炔气经一级5℃水冷却器冷却后进入一级低压干燥(内部装填无水氯化钙),然后进入一级清净塔、二级清净塔脱除S、P等杂质,再至一级、二级、三级碱塔中和处理后进入气柜。