CA6140_车床对开螺母体下部说明书
(完整版)CA6140型卧式车床的操作.doc

项目一CA6140 型卧式车床的操作一、教学目标1、能熟练操作CA6140 型卧式车床;2、懂得 CA6140 型卧式车床的各组成部分及作用;3、初步培养学生团结协作,谦虚好学的精神,懂得熟能生巧的道理。
二、工作任务1、学会 CA6140 型卧式车床通电操作;2、看懂主轴变速盘,并学会主轴变速。
3、看懂进给速度铭牌,并学会进给变速和能较均匀地进行手、自进给移动。
4、能较熟练操纵主轴操纵杆,会进行主轴启动、停止、变向、变速控制。
三、操作步骤和要求1、车床的启动操作(1)检查车床各变速手柄是否处于空档位置,离合器是否处于正确位置,操纵杆是否处于停止状态,确认无误后,合上车床电源总开关。
(2)按下床鞍上的绿色启动按扭,电动机启动。
(3)向上提起溜板箱右侧的操纵杆手柄,主轴正转;操纵杆手柄回到中间位置,主轴停止转动;操纵杆向下压,主轴反转。
(4)主轴正反转的转换要在主轴停止转动后进行,避免因连续转换操作使瞬间电流过大而发生电器故障。
(5)按下床鞍上的红色停止按钮,电动机停止工作。
2、主轴箱的变速操作通过改变主轴箱正面右侧的两个叠套手柄的位置来控制。
前面的手柄有 6 个挡位,每个有 4 级转速,由后面的手柄控制,所以主轴共有24 级转速,如下图所示。
主轴箱正面左侧的手柄用于是螺纹的左右旋向变换和加大螺距,共有 4 个挡位,即右旋螺纹、左旋螺纹加大螺距和左旋加大螺距螺纹,其挡位如图所示3、进给箱的变速操作C6140 型车床上进给箱正面左侧有一个手轮,手轮有8个挡位;右侧有前、后叠装的两个手柄,前面的手柄是丝杆、光杆变换手柄,后面的手柄有Ⅰ、Ⅱ、Ⅲ、Ⅳ 4 个挡位,用业与手轮配合,用以调整螺距或进给量。
根据加工要求调整所需螺距或进给量时,可通过查找进给箱油池盖上的调配表来确定手轮和手柄的具体位置。
其挡位如上图所示4、溜板箱的操作溜板部分实现车削时绝大部分的进给运动:床鞍及溜板箱作纵向移动,中滑板作横向移动,小滑板可作纵向或斜向移动。
CA6140车床法兰盘夹具设计说明书(完整版).

工艺装备课程设计说明书设计题目:车床法兰盘CA6140零件加工工艺规程及工装夹具设计班级学生同组学生指导教师学院2013年月日学院工艺装备课程设计任务书题目: CA6140法兰盘零件加工工艺规程及工装夹具设计设计内容:1.零件图1张2.毛坯图1张3.机械加工工艺规程1套(含工艺路线卡和工序卡)4.工艺装备结构设计1套(含装配图和若干零件图)5.课程设计说明书1份(不少于5000字)设计要求:1.按大批生产、通用加工装备设计。
2.同一课题组为3-4人,要求分工明确,同时也要有合作精神。
3.每人要独立完成一份课程设计说明书及至少画一张图纸。
专业:机械设计制造及其自动化指导教师:班级:姓名:同组学生名单:本人分工:产品零件图:参与√绘制 ;毛坯图:参与√绘制 ;工艺:参与 编制√;夹具装配图:参与 设计√;夹具零件图:参与 设计√;设计说明书:参与 编写√。
课题发给日期:2013.5.30 课题完成日期:2013.7.12法兰盘只是一个统称,通常是指在一个类似盘状的金属体的周边开上几个固定用的孔用于连接其它东西。
法兰联接在机械上应用很广泛,所以样子也千奇百怪的。
本文主要是针对CA6140车床法兰盘的加工工艺以及主要孔的工艺装备设计进行论述。
通过本文可以了解该法兰盘的构造和它的整个加工过程以及各注意事项,同时可以从侧面了解到针对于4Xφ9孔的专用钻床夹具的整个设计流程。
从各组件的选择到加工参数的确定反映了目前该零件的市场价值以及发展前景。
关键词法兰盘工艺装备专用夹具钻套第一章机械加工工艺规程的制定一.零件的分析 (3)1.零件的用途 (3)2.零件的结构 (3)3.确定零件的生产纲领 (3)4.零件的工艺分析 (3)4.1 CA6140车床法兰盘共有两处加工表面 (3)4.2加工表面间有一定位置要求 (4)二. 工艺规程的设计 (4)1.确定毛坯的制造形式 (4)2.定位基准的选择 (4)2.1粗基准的选择 (4)2.2精基准的选择 (5)3.表面加工方法的选择 (5)4.制定工艺路线 (6)4.1工艺路线方案 (6)4.2机械加工余量、工序尺寸及毛坯尺寸的确定 (8)4.3确定切削用量及基本用时 (12)第二章钻床夹具设计1.问题的提出 (18)2.夹具设计 (18)2.1定位基准及定位元件的选择 (18)2.2夹紧机构设计 (18)2.3对定元件的选择 (19)2.4零件加工误差的分析 (20)总结 (21)参考文献 (21)第一章机械加工工艺规程的制定一.零件的分析1.零件的用途CA6140车床法兰盘为盘类零件,用于卧式车床上。
CA6140说明书

前言机械制造技术基础课程设计是我们在学完了大学的全部基础课,专业基础课以及专业课后进行的。
这是我们在进行毕业设计之前对所学的各科课程一次深入的综合性总复习,也是一次理论联系实际的训练。
因此,他在我们的大学三年生活中占有重要的地位。
机械加工工艺规程是规定产品或零部件机械加工工艺过程和操作方法等的工艺文件。
对加工工艺规程的设计,可以了解了加工工艺对生产、工艺水平有着极其重要的影响。
生产规模的大小、工艺水平的高低以及解决各种工艺问题的方法和手段都要通过机械加工工艺来体现。
对专用夹具的设计,可以了解机床夹具在切削加工中的作用:可靠地保证工件的加工精度,提高加工效率,减轻劳动强度,充分发挥和扩大机床的给以性能。
本夹具设计可以反应夹具设计时应注意的问题,如定位精度、夹紧方式、夹具结构的刚度和强度、结构工艺性等问题。
就我个人而言,我希望通过这次课程设计对自己未来将从事的工作进一步适应性的训练,希望自己在设计中能锻炼自己的分析问题、解决问题、查资料的能力,为以后的工作打下良好的基础。
由于能力有限,设计尚有很多不足之处,希望各位老师给予指导。
目录1、杠杆加工工艺规程设计............................................................................................................ - 3 -1.1零件的分析....................................................................................................................... - 3 -2、选择毛坯,确定毛坯尺寸,设计毛坯图 ........................................................................ - 4 -2.1确定毛坯的制造形式....................................................................................................... - 4 -2.2确定机械加工余量,毛坯尺寸和公差 ........................................................................... - 4 -3.1基面的选择....................................................................................................................... - 5 -4、机械加工余量、工序尺寸及毛坯尺寸的确定 ........................................................................ - 7 -5、确定切削用量............................................................................................................................ - 7 -6、确定基本工时.......................................................................................................................... - 17 -7、工艺卡片.................................................................................................................................. - 22 -8、专用夹具设计.......................................................................................................................... - 22 -8.1加工工艺孔Φ25夹具设计............................................................................................ - 22 -8.2小结................................................................................................................................. - 26 - 总结................................................................................................................................................ - 27 - 参考文献........................................................................................................................................ - 28 - 致谢.............................................................................................................................................. - 30 -1、杠杆加工工艺规程设计1.1零件的分析1.1.1零件的作用题目所给的零件是CA6140车床的杠杆。
6140说明书

前言毕业设计是学校对我们在大学中所学知识的一个检验,它几乎包含了我们学习的全部专业知识。
课程设计工作做的好坏,直接体现了个人现阶段实力的强弱,我们必须拿出百分之百的热情,用心搞好毕业设计。
随着科技的进步和生产的发展,机械产品和机械制造技术的内涵正在不断的发生变化。
在企业的生产第一线,从事机电产品设计、制造、质量、销售、服务、维修等技术和管理工作的人员,强调要有较宽的知识面和跨学科综合解决工程实际问题的能力。
因此,在高等教育的专业技术人才培养上,不仅要求他们学习和掌握计算机技术等多方面的新知识、新技术,而且对切削原理、切削机床和机械制造工艺等必备的理论和知识,要运用全新的观念,重新进行科学的优化组合,以形成新的课程体系与结构。
而随着机械技术、微电子技术的飞速发展与应用,机械技术与微电子技术的相互渗透,则标志着机电有机结合的机电一体化技术也在飞速发展。
机电有机结合的本质是从系统的观点出发,用机械技术与微机控制技术构造最佳的一体化系统,从而实现系统或产品的短小轻薄和智能化,达到节能省源,节省材料,多功能、高性能和高可靠性的目的。
机床技术是70年代发展起来的一种机床自动控制技术。
数控机床是典型的机电一体化产品,是高新技术的重要组成部分。
采用数空机床,提高机械工业的自动化生产水平和产品质量,是当前机械制造业技术改造的必由之路。
现代数控机床是柔性制造单元,柔性制造系统乃至计算机集成组成制造系统中不可缺少的基础设备。
目前被广泛应用的数控机床就是典型的机电结合。
数控,即数字控制(NumbericalControl,NC),在机床领域是指用数字华信号对机床运动及其加工过程进行控制的一种方法。
如果采用存储程序的专用计算机来实现部分或全部基本数控功能,则称为计算几数控(Computeized Numerical Control,CNC)。
数控机床即是采用了数控技术的机床,或者说是装备了数控系统的机床。
数控机床是综合应用计算机、自动控制、自动检测及精密机械等高新技术产物,是技术密集度及自动化程度很高的典型机电一体化加工设备。
ca6140车床课程设计说明书

目录一、零件的分析 (2)1.1零件的作用 (2)1.2零件的工艺分析 (2)二、工艺规程设计 (2)2.1确定毛坯的制造形式 (2)2.2基面的选择 (2)2.3制定工艺路线 (3)2.4加工基本工时 (5)三、夹具设计 (16)四、总结 (16)一、零件的分析1.1零件的作用CA6140车床的拨叉位于车床变速机构中,主要起换档,使主轴回转运动按照工作者的要求工作,获得所需的速度和扭矩的作用。
零件上方的φ22孔与操纵机构相连,二下方的φ55半孔则是用于与所控制齿轮所在的轴接触。
通过上方的力拨动下方的齿轮变速。
两件零件铸为一体,加工时分开。
1.2零件的工艺分析CA6140车床共有两处加工表面,其间有一定位置要求。
分述如下:1. 以φ22为中心的加工表面这一组加工表面包括:φ22 的孔,以及其上下端面,上端面与孔有位置要求,孔壁上有一个装配时钻铰的锥孔,一个M6的螺纹孔。
这三个都没有高的位置度要求。
2. 以φ55为中心的加工表面这一组加工表面包括:φ55 的孔,以及其上下两个端面。
这两组表面有一定的位置度要求,即φ55 的孔上下两个端面与φ22 的孔有垂直度要求。
由上面分析可知,加工时应先加工一组表面,再以这组加工后表面为基准加工另外一组。
二、工艺规程设计2.1确定毛坯的制造形式零件材料为HT200。
考虑零件在机床运行过程中所受冲击不大,零件结构又比较简单,故选择铸件毛坯。
考虑到零件年产量为4000件,已达到中批生产的水平,故采用金属型铸造毛坯。
2.2基面的选择基面选择是工艺规程设计中的重要工作之一。
基面选择得正确与合理可以使加工质量得到保证,生产率得以提高。
否则,加工工艺过程中回问题百出,更有甚者,还会造成零件的大批报废,是生产无法正常进行。
(1)粗基准的选择。
对于零件而言,尽可能选择不加工表面为粗基准。
而对有若干个不加工表面的工件,则应以与加工表面要求相对位置精度较高的不加工表面作粗基准。
根据这个基准选择原则,首先选取工件底面作为粗基准,以支撑板大平面支撑底面作为主要定位面,限制3个自由度,铣削上下端面。
CA6140杠杆设计说明书

目录1 绪论 (2)2 杠杆加工工艺规程设计 (2)2.1 零件的分析 (2)2.1.1 零件的作用 (2)2.1.2 零件的工艺分析 (2)2.1.3杠杆的技术要求 (3)2.2杠杆加工的主要问题和工艺过程设计所应采取的相应措施 (3)2.2.1 确定毛坯的制造形式 (3)2.2.2基面的选择 (3)2.2.3 制定工艺路线 (4)2.2.4机械加工余量、工序尺寸及毛坯尺寸的确定 (6)2.2.5确定切削用量 (7)2.2.6确定加工工时 (7)3夹具设计 (8)3.1粗精铣宽度为30mm的下平台夹具设计 (8)3.1.1定位基准的选择 (8)3.1.2定位元件的设计 (8)3.1.3定位误差分析: (9)3.1.4夹具体槽形与对刀装置设计 (9)3.1.5夹紧装置及夹具体的设计 (12)3.1.6夹紧力计算 (12)3.1.7夹具设计及操作的简要说明 (13)参考文献 (13)1 绪论加工工艺及夹具毕业设计是对所学专业知识的一次巩固,是在进行社会实践之前对所学各课程的一次深入的综合性的总复习,也是理论联系实际的训练。
机床夹具已成为机械加工中的重要装备。
机床夹具的设计和使用是促进生产发展的重要工艺措施之一。
随着我国机械工业生产的不断发展,机床夹具的改进和创造已成为广大机械工人和技术人员在技术革新中的一项重要任务2 杠杆加工工艺规程设计2.1 零件的分析 2.1.1 零件的作用题目所给定的零件是CA6140车床的杠杆。
它位于车床制动机构中,主要起制动作用。
杠杆一端与制动带连接,另一端通过刚球与齿条轴的凸起(或凹槽)相接触,当离合器脱开时,齿条轴与杠杆下端接触,是起逆时针方向摆动,将制动带拉紧;当左右离合器中任一个接合时,杠杆都顺时针方向摆动,使制动带放松,从而达到制动的目的。
2.1.2 零件的工艺分析1、主要加工面:(1)、钻Φ0.023025+孔以及与此孔相通的Φ14阶梯孔、M8螺纹孔; (2)、钻Φ0.1012.7+锥孔及铣Φ0.1012.7+锥孔表面;(3)、钻2—M6螺纹孔及其上表面; (4)、铣杠杆底面。
CA6140 车床对开螺母体下部说明书

CA6140 车床对开螺母体下部说明书学号:姓名:专业:机械工程指导教师:二○一二年十二月设计要求与设计任务任务:1、C6140车床对开合螺母下座工艺规程2、钻2-Ø12H7孔钻模(钻床夹具)设计零件年生产纲领:500件/年应完成:1、开合螺母(下)座工艺卡(1套**)2、夹具装配图A1(841x1189)3、课程设计说明书(A4纸打印或课程设计说明书专用纸手写,但须仿宋体字)一、零件的分析 (3)1.1开合螺母上座体零件图 (3)1.2零件的功能: (3)二、开合螺母座设计 (4)2.1确定毛坯的材料 (4)2.2确定铸造方法 (4)2.3毛坯的浇注方式 (4)2.4画毛坯图 (4)三、工艺规程设计 (6)3.1性能要求 (6)3.2工艺路线的拟定 (6)3.3工艺路线方案: (7)3.4机械加工余量、工序尺寸及毛坯尺寸的确定 (7)3.5确定切削用量及基本工时 (8)3.5.1粗铣燕尾 (8)3.5.2精铣燕尾 (8)3.5.3 铣退刀槽 (9)3.5.4粗铣端面 (9)3.5.5精铣端面 (9)3.5.6 钻Φ52H7孔并倒角1.5×45º (10)3.5.7钻2×Φ12孔 (11)3.5.8车端面 (12)3.5.9切断 (13)四、机床夹具设计 (14)4.1工序尺寸精度分析 (14)4.2定位方案确定 (14)4.3定位误差分析计算 (14)4.4夹紧方案及元件的确定 (15)五、体会总结 (16)参考文献 (17)一、零件的分析1.1开合螺母上座体零件图如下所示:1.2零件的功能:题目所给定的零件是CA6140车床对开螺母体下部。
对开螺母体是用于接通和断开从丝杠传来的运动。
车削螺纹时,将开合螺母合上,丝杠通过对开螺母体传动溜板箱和刀架;否则就将对开螺母体脱开。
车削螺母时,顺时针方向转动手柄,通过轴带动曲线槽盘转动,曲线槽盘上的曲线槽盘形状,通过圆柱销带动上半螺母在溜板箱体后面的燕尾形导轨内上下移动,使其相互靠拢,将对开螺母体和丝杠啮合。
CA6140A型车床的基本操作

教案首页车外圆车孔车端面车削时工件上形成的三个表面三、CA6140A型卧式车床的操作手柄图上编号名称图上编号名称1,2 主轴变速(长,短)手柄14 尾座套筒移动手轮3 加大螺距及左、右螺纹变换手柄15 尾座快速紧固手柄4 电源总开关(有开和关两个位置)16 机动进给手柄及快速移动按钮5 电源开关锁(有1和0两个位置)17 尾座套筒固定手柄6 冷却泵总开关18 小滑板移动手柄7,8 进给量和螺距变换手轮、手柄19 刀架转位及固定手柄9 螺纹种类及丝杠、光杠变换手柄20 中滑板手柄10,13 主轴正反转操纵手柄21 中滑板刻度盘11 停止(或急停)按钮(红色)22 床鞍刻度盘12 启动按钮(绿色)23 床鞍手轮小结练习一、刀架部分和尾座的手动操作1.刀架部分的手动操作:(1)床鞍(2)中滑板(3)小滑板(4)刀架当刀架上装有车刀时,转动刀架,其上的车刀也随之转动,应避免车刀与工件、卡盘或尾座相撞。
要求在刀架转位前就把中滑板向后退出适当距离。
2.刻度盘的操作:(1)床鞍刻度盘(2)中滑板刻度盘(3)小滑板刻度盘现象:由于丝杠与螺母之间的配合存在间隙,会产生空行程。
要求:使用刻度盘时,要先反向转动适当角度,消除配合间隙,再正向慢慢转动手柄,带动刻度盘转到所需的格数,如左下图所示。
消除措施:如果刻度盘多转动了几格,绝不能简单地退回,如下中图所示,而必须向相反方向退回全部空行程(通常反向转动1/2圈),再转到所需要的刻度位置。
消除刻度盘空行程的方法3.尾座的操作:(1)尾座套筒的进退和固定(2)尾座位置的固定二、车床的变速操作和空运转练习1.车床启动前的准备步骤1)检查车床开关、手柄和手轮是否处于中间空挡位置。
2)将交换齿轮保护罩前面开关面板上的电源开关锁旋至“1”位置。
3)向上扳动电源总开关由“OFF”至“ON”位置,即电源由“断开”至“接通”状态,车床得电。
同时,床鞍上的刻度盘照明灯亮。
4)按下照明灯开关按钮,使车床照明灯亮。
最新CA6140 车床对开螺母体下部说明书汇总

C A6140车床对开螺母体下部说明书CA6140 车床对开螺母体下部说明书学号:姓名:专业:机械工程指导教师:二○一二年十二月设计要求与设计任务任务:1、C6140车床对开合螺母下座工艺规程2、钻2-Ø12H7孔钻模(钻床夹具)设计零件年生产纲领:500件/年应完成:1、开合螺母(下)座工艺卡(1套**)2、夹具装配图A1(841x1189)3、课程设计说明书(A4纸打印或课程设计说明书专用纸手写,但须仿宋体字)一、零件的分析 (3)1.1开合螺母上座体零件图如下所示: (3)1.2零件的功能: (4)二、开合螺母座设计 (4)2.1确定毛坯的材料 (4)2.2确定铸造方法 (4)2.3毛坯的浇注方式:两箱铸造侧面浇注(见下图) (5)2.4画毛坯图 (5)三、工艺规程设计 (7)3.1性能要求 (7)3.2工艺路线的拟定 (8)3.3工艺路线方案: (8)3.4机械加工余量、工序尺寸及毛坯尺寸的确定 (9)3.5确定切削用量及基本工时 (10)3.5.1 粗铣燕尾 (11)3.5.2 精铣燕尾 (12)3.5.3 铣退刀槽 (13)3.5.4 粗铣端面 (14)3.5.5 精铣端面 (16)3.5.6 钻Φ52H7孔并倒角1.5×45º (17)3.5.7 钻2 ×Φ12孔 (19)3.5.8 车端面 (22)3.5.9 切断 (26)四、机床夹具设计 (28)4.1工序尺寸精度分析 (28)4.2定位方案确定 (29)4.3定位误差分析计算 (29)4.4夹紧方案及元件的确定 (29)五、体会总结 (32)参考文献 (33)一、零件的分析1.1开合螺母上座体零件图如下所示:1.2零件的功能:题目所给定的零件是CA6140车床对开螺母体下部。
对开螺母体是用于接通和断开从丝杠传来的运动。
车削螺纹时,将开合螺母合上,丝杠通过对开螺母体传动溜板箱和刀架;否则就将对开螺母体脱开。
拨叉(CA6140车床)说明书

目录1零件的工艺分析及生产类型的确定 (2)1.1零件的作用 (2)1.2零件的工艺分析 (2)2确定毛胚 (2)2.1确定毛胚种类 (2)2.2确定铸件加工余量及形状 (2)2.3绘制铸件零件图 (3)3工艺规程设计 (3)3.1 确定毛坯制造形式 (3)3.2 基面的选择 (3)3.3 制定工艺路线 (3)3.4 机械加工余量、工序尺寸及毛坯尺寸的确定 (5)4确定切削用量及基本工具 (6)5夹具设计 (10)5.1 任务的提出 (10)5.2 定位方案及定位装置的设计计算 (10)5.3 夹紧方案及装置的设计计算 (11)设计总结 (12)参考文献 (12)1 零件的工艺分析及生产类型的确定1.1 零件的作用题目所给的零件是CA6140车床的拨叉,它位于车床变速机构中,主要起换挡,使主轴回转运动按工作者的要求工作,获得所需的速度和扭矩的作用。
零件上方的φ22孔语操作机构相连,下方的φ55半孔则是用于所控制齿轮所在的轴接触。
通过上方的力波动下方的齿轮变速。
两件铸为一体,加工时分开。
1.2 零件的工艺分析零件的材料为HT200,灰铸铁的生产工艺简单,铸造性能优良,但塑性较差、脆性高,和适合磨削,为此以下是拨叉需要加工表面以及加工表面之间的位置要求。
需要加工的表面:1.小孔的上端面、大孔的上下端面;2.小头孔φ22mm以及与此孔相通的φ8mm的锥孔、M8螺纹孔;3.大头半圆孔φ55mm;位置要求:小头孔上端面与小头空中心线的垂直度误差为0.05mm,打孔的上下断面与小头孔的中心线的垂直度误差为0.07mm。
由上面分析可知,可以粗加工拨叉底面,然后依次作为粗基准,采用专用夹具进行加工,并且保证位置精度要求。
再根据加工方法的经济精度及机床所能达到的位置精度,并且此拨叉零件没有复杂的加工曲面,所以根据上述技术要求采用常规加工工艺均可保证。
2 确定毛坯2.1 确定毛坯种类:零件材料为HT200。
考虑零件在机床运行过程中所受冲击不大,零件结构又比较简单,生产类型为大批生产,故选择铸件毛坯。
C6140车床使用说明

C6140车床使用说明I.车床的组成部分:1.主轴箱部分:包括主轴、主轴箱座、齿轮、传动及润滑装置。
2.床身部分:包括床身、床头盘、弹簧滑板、滑板床轨等。
3.刀架部分:包括刀架底座、刀架、刀架滑轨等。
4.进给机构部分:包括齿轮箱、进给丝杠、移动卡尺、弹簧等。
II.C6140车床的操作步骤:1.准备工作:a.检查车床各部分的润滑情况,确保润滑良好。
b.检查机床是否接地良好。
c.检查刀具及刀架是否安装正确。
2.开机操作:a.打开电源,并调整主轴的速度范围。
b.确认主轴和进给机构处于停止状态。
c.打开主轴油泵,以保证主轴的润滑。
d.调整进给机构的速度范围。
e.打开冷却泵,以保证切削加工时的冷却。
3.加工操作:a.确定工件的加工要求和工艺参数。
b.将工件夹紧在滑板上,并确保夹紧力适中。
c.根据工艺要求选择合适的刀具,并安装在刀架上。
d.调整刀具的高度、方向和角度。
e.设置进给速度和切削深度。
f.启动主轴和进给装置,进行切削加工。
4.关机操作:a.关闭冷却泵,停止冷却液的供给。
b.停止主轴和进给装置的运转。
c.关闭主轴油泵。
d.关闭电源,并断开电源插头。
III.注意事项:1.使用前必须检查机床各部分的润滑情况,确保润滑良好。
2.操作前要检查刀具及刀架是否安装正确。
3.操作中要保持清洁,防止铁屑、切屑对机床造成损害。
4.加工过程中要注意切削速度和进给速度的合理搭配,避免过快或过慢引起的问题。
5.切削时要注意切削刃的状态,定期检查并更换磨损的刀具。
6.加工不同材料时,要选择合适的刀具和加工参数,避免过度磨损。
通过以上的车床使用说明,您将能够正确操作C6140车床,并在金属加工过程中获得良好的加工效果。
为了保证操作安全,请严格按照操作步骤和注意事项进行操作。
CA6140车床操作规程完整

CA6140型车床安全操作规程1.操作者必须熟悉本设备结构和性能,经过考试合格取得操作证后,方可独立操作。
2.操作者要认真做到“三好”(管好、用好、修好)、“四会”(会检查、会保养、会使用、会排除故障)。
3.操作者必须遵守使用设备的“五项纪律”和维护设备的“四项要求”的规定。
4.操作者要随时按照“巡回检查容”的要求对设备进行检查。
5.严格按照“设备润滑图表”规定进行加油,做到“五定”(定点、定时、定量、定质、定人)。
注油后应将油杯(池)的盖子盖好。
6.严禁超规、超负荷使用设备。
7.停车八小时以上再开动设备时,先低速运转三至五分钟。
确认润滑系统畅通,各部运转正常后,方能开始工作。
8.工作前必须正确安装刀具,并注意下列几点:①卡紧刀具时,注意伸出训份尽量短一些;②车刀下面不得垫大小不同的垫片,垫片要平直、大小与刀杆相等;③磨钝了的刀具,严禁继续使用;④刀具装卡要牢固安全。
9.装卸工件时,必须采取安全措施,防止碰伤设备。
加工偏重工件必须加以平衡。
10.用吊车装缺卸工件时,必须根据工件重量和形状选用安全的吊具和方法,同时在导轨面上要垫上方木。
11.各导轨面严禁放置工具及其它金属物品。
不使用的导轨面应定期保养以防锈蚀。
12.禁止在运转中变速。
变速时要观察信号灯指示是否正常,否则不得开车。
13.严禁使用反车制动。
14.加工铸铁件或进行磨削加工时,要防止砂子和冷却液进入导轨及床头箱、溜板箱。
加工完毕后要彻底清擦干净。
15.移动尾座及尾座套筒前,必须先松开卡紧装置,擦净导轨,加注润滑油,移动完后定好位重新给予紧固。
16.严禁在设备上焊补或校直工件。
17.禁止踩踏设备导轨面、丝光杆、油盘及油漆表面。
必须踩踏时要垫木板等保护物。
18.使用尾座顶尖顶持工件时,要按工件重量调整好顶尖套筒的压力。
19.禁止用铁棒顶击主轴孔的顶尖(用铜棒)。
20.禁止在不切削螺纹时使用丝杠。
21.禁止在主轴和尾座锥孔安装与其锥度不符或锥面有刻痕、不清洁的工具。
ca6140 831007说明书
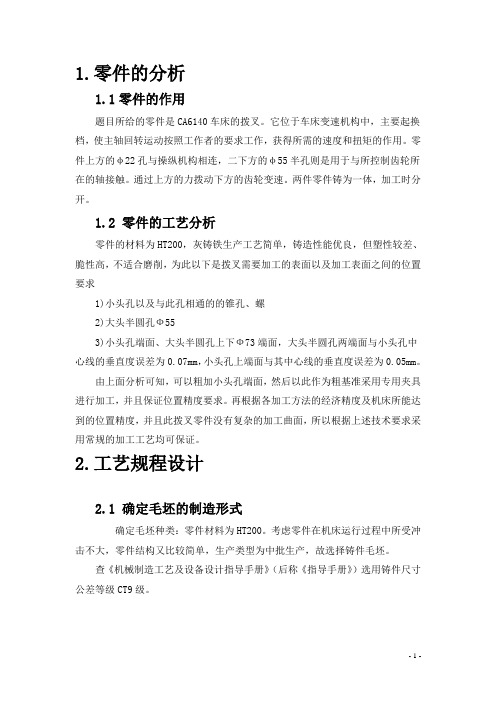
1.零件的分析1.1零件的作用题目所给的零件是CA6140车床的拨叉。
它位于车床变速机构中,主要起换档,使主轴回转运动按照工作者的要求工作,获得所需的速度和扭矩的作用。
零件上方的φ22孔与操纵机构相连,二下方的φ55半孔则是用于与所控制齿轮所在的轴接触。
通过上方的力拨动下方的齿轮变速。
两件零件铸为一体,加工时分开。
1.2 零件的工艺分析零件的材料为HT200,灰铸铁生产工艺简单,铸造性能优良,但塑性较差、脆性高,不适合磨削,为此以下是拨叉需要加工的表面以及加工表面之间的位置要求1)小头孔以及与此孔相通的的锥孔、螺2)大头半圆孔Ф553)小头孔端面、大头半圆孔上下Ф73端面,大头半圆孔两端面与小头孔中心线的垂直度误差为0.07mm,小头孔上端面与其中心线的垂直度误差为0.05mm。
由上面分析可知,可以粗加小头孔端面,然后以此作为粗基准采用专用夹具进行加工,并且保证位置精度要求。
再根据各加工方法的经济精度及机床所能达到的位置精度,并且此拨叉零件没有复杂的加工曲面,所以根据上述技术要求采用常规的加工工艺均可保证。
2.工艺规程设计2.1 确定毛坯的制造形式确定毛坯种类:零件材料为HT200。
考虑零件在机床运行过程中所受冲击不大,零件结构又比较简单,生产类型为中批生产,故选择铸件毛坯。
查《机械制造工艺及设备设计指导手册》(后称《指导手册》)选用铸件尺寸公差等级CT9级。
2.2基面的选择定位基准是影响拨叉零件加工精度的关键因素。
基准选择得合理可以使加工质量得到保证,生产率得以提高。
否则,加工过程中将问题百出,更有甚者,造成零件的大批报废,使生产无法正常进行。
(1)粗基准的选择。
对于零件而言,尽可能选择不加工表面为粗基准。
而对有若干个不加工表面的工件,则应以与加工表面要求相对位置精度较高的不加工表面作粗基准。
根据这个基准选择原则,现选取φ22 孔的不加工外轮廓表面作为粗基准,利用一组共两块V形块支承这两个φ40作主要定位面,限制5个自由度,再以一个销钉限制最后1个自由度,达到完全定位,然后进行铣削。
CA6140车床手柄座说明书(姜昆)

一建立三维模型1、打开PRO/E软件,点击文件—新建,弹出窗口(图片1-1),选择零件,名称为chechuangshoubingzuo,点击缺省模板,点击确定,选择mmns_part_solid,点击确定。
图片1-1 新建文件图片1-2 草绘2、点击草绘,选择TOP面,点击草绘。
草绘如下图(图片1-2)。
点击完成。
3、点击拉伸,高度为43,点击完成,模型如下图所示(图片1-3)图片1-3 模型图图片1-4 模型图4、点击斜度,点击参照,拔模曲面选择曲面和2个侧面,拔模枢轴选择TOP面,斜度为2.73度,点击完成,如下图所示(图片1-4)。
5、点击草绘,选择零件的底面,点击草绘,如下图所示(图片1-5),点击确定。
图片1-5 草绘零件图片1-6 草绘零件6、点击拉伸,高度为43,点击完成,如下图所示(图片6)。
7、点击基准平面工具,选择FRONT面,平移16,形成DTM1面,如下图所示(图片7)。
图片1-7 建立基准图片1-8 草绘图8、点击拉伸,选择DTM1面,点击草绘,草绘如下图(图片8),点击完成,高度为12,点击完成,模型如下图所示(图片9)。
图1-9 模型图图1-10 建立基准9、点击基准平面工具,选择圆柱小端面,向上平移5,形成DTM2面,如下图所示(图片10)。
图片1010、点击拉伸,选择DTM2面,点击草绘,草绘如下图(图片11),点击完成,高度为12,点击完成,模型如下图所示(图片12)。
图片11图片1211、点击基准平面工具,选择圆柱小端面,向上平移17,形成DTM3面,如下图所示(图片13)。
图片1312、点击拉伸,选择DTM3面,点击草绘,草绘如下图(图片14),点击完成,高度为14,点击去除材料,点击完成,模型如下图所示(图片15)。
图片14图片1513、点击拉伸,选择DTM3面,点击草绘,草绘如下图(图片16),鱼片16图片1714、选择镜像,选择步骤12所拉伸实体,选择TOP面,最终实体如下图所示(图片18)。
CA6140说明书

序言在学完大学的全部基础课、技术基础课以及大部分专业课的基础上,我们进行了机械制造技术基础课程设计。
这是我们在进行毕业设计之前对所学各课程的一次深入的综合性总复习,汇总了所学的专业知识。
在理论与实践上有机结合,使我们对各科的作用更加深刻的熟悉与理解,并为以后的实际工作奠定坚实的基础!在些次课程设计中我主要是设计CA6140拨叉的机械加工工艺规程以及铣削加工时的夹具。
在此次课程设计期间查阅了大量的书籍,并且得到了有关老师的悉心指点。
由于能力所限,设计尚有许多不足之处,恳请各位老师给予指教。
一、零件的分析(一)零件的作用题目所给的零件时CA6140车床的拨叉(见附图1——零件图),它位于车床变速机构中,主要起换档,使主轴回转运动按照工作者的要求进行工作。
(二)零件的工艺分析CA6140拨叉共有两组加工表面。
现分析如下:1.拨叉大端平面的加工2.以花键孔的中心线为基准的加工面这一组面包括Ø25+0.0250 mm的六齿方花键孔、Ø22+0.210 mm花键底孔两端的150倒角、距花键孔轴线22mm的平面和拨叉下端的18+0.110 mm的槽。
二、工艺规程设计(一)确定毛坯的制造形式零件材料为HT200。
因为零件为大批量生产,而且零件的轮廓尺寸不大,故可采用铸造成型。
这从提高生产率、保证加工精度上考虑,也是应该的。
(二)基面的选择基面选择是工艺规程设计中的重要工作之一。
基面选择得正确与合理,可以使加工质量得到保证,生产率得到提高。
否则,加工工艺过程中会问题百出,更有甚者,还会造成零件大批报废,使生产无法正常进行。
1.粗基准的选择。
对于零件而言,尽可能选择不加工表面为粗基准而对有若干个不加工表面的工件,则应以与加工表面要求相对位置精度较高的不加工表面作粗基准。
所以选择右端R20的端面为粗基准。
2.精基准的选择。
精基准的选择有利于保证加工精度,并使工件装夹方便。
在选择时,主要应该考虑基准重合、基准统一等问题。
CA6140车床拨叉说明书
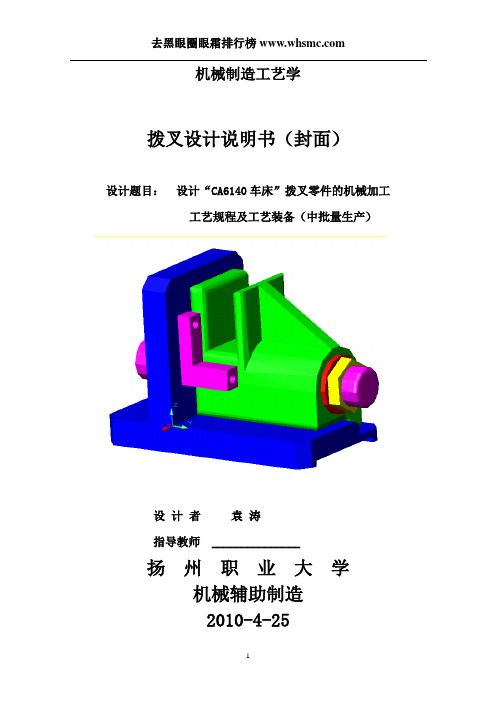
机械制造工艺学拨叉设计说明书(封面)设计题目:设计“CA6140车床”拨叉零件的机械加工工艺规程及工艺装备(中批量生产)设计者袁涛指导教师 _______________扬州职业大学机械辅助制造2010-4-25机械工程学院机床拨叉夹具设计说明书题目设计“CA6140车床”拨叉零件的机械加工工艺规程及工艺装备(中批量生产)内容 1.零件图一张 2.毛坯图一张3.机械制造加工工艺过程综合卡片一张4.机械制造加工工艺工序卡片七张4.结构设计装配图二张5.结构设计零件图一张6.毕业设计说明书一份前言通过机床工艺及夹具设计,汇总所学专业知识如一体(如《公差于配合》、《机械零件设计》、《金属切削机床》、《机械制造工艺》等)。
让我们对所学的专业课得以巩固、复习及实用,在理论与实践上有机结合;使我们对各科的作用更加深刻的熟悉与理解,并为以后的实际工作奠定坚实的基础!在些次设计中我们主要是设计CA6140拨叉的铣床夹具。
在此次课程设计过程中,我小组成员齐心协力、共同努力完成了此项设计。
在此期间查阅了大量的书籍,并且得到了有关老师的指点。
设计的目的:机械制造工艺学课程设计,是在学完机械制造工艺学及夹具设计原理课程,经过生产实习取得感性知识后进行的一项教学环节;在老师的指导下,要求在设计中能初步学会综合运用以前所学过的全部课程,并且独立完成的一项工程基本训练。
同时,也为以后搞好毕业设计打下良好基础。
通过课程设计达到以下目的:1、能熟练的运用机械制造工艺学的基本理论和夹具设计原理的知识,正确地解决一个零件在加工中的定位,夹紧以及合理制订工艺规程等问题的方法,培养学生分析问题和解决问题的能力。
2、通过对零件某道工序的夹具设计,学会工艺装备设计的一般方法。
通过学生亲手设计夹具(或量具)的训练,提高结构设计的能力。
3、毕业计过程也是理论联系实际的过程,并学会使用手册、查询相关资料等,增强学生解决工程实际问题的独立工作能力。
CA6140车床操作注意事项PPT课件
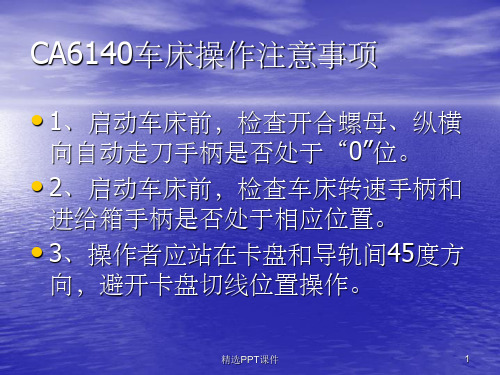
保无误。
精选PPT课件
2
66使用用开合螺母车螺纹时在合螺使用用开合螺母车螺纹时在合螺母前使刀尖离工件一段距离以确母前使刀尖离工件一段距离以确保无误
CA6140车床操作注意事项
• 1、启动车床前,检查开合螺母、纵横
向自动走刀手柄是否处于“0”位。
• 2、启动车床前,检查车床转速手柄和
进给箱手柄是否处于相应位置。
• 3、操作者应站在卡盘和导轨间45度方
向,避开卡盘切线位置操作。
精选PPT课件
1
CA6140车床操作注意事项
• 4、启动车床时,先启动红色急停按钮,
再提操纵杆。切削结束后,在测量、
拆卸工件和转换刀架时,必须先停车,
再按柄时,
必须先想好,再操作,严禁错误操作。
• 6、使用用开合螺母车螺纹时,在合螺
- 1、下载文档前请自行甄别文档内容的完整性,平台不提供额外的编辑、内容补充、找答案等附加服务。
- 2、"仅部分预览"的文档,不可在线预览部分如存在完整性等问题,可反馈申请退款(可完整预览的文档不适用该条件!)。
- 3、如文档侵犯您的权益,请联系客服反馈,我们会尽快为您处理(人工客服工作时间:9:00-18:30)。
机械制造技术与装备课程设计说明书设计题目:C6140车床对开合螺母下座工艺规程及钻2-Ø12H7孔加工夹具设计专业:机械设计及其制造班级:学号:设计者:指导教师:日期2014年6月20日一、零件的分析 (3)1.1开合螺母上座体零件图 (3)1.2零件的功能: (3)二、开合螺母座设计 (4)2.1确定毛坯的材料 (4)2.2确定铸造方法 (4)2.3毛坯的浇注方式 (4)2.4画毛坯图 (4)三、工艺规程设计 (6)3.1性能要求 (6)3.2工艺路线的拟定 (6)3.3工艺路线方案: (7)3.4机械加工余量、工序尺寸及毛坯尺寸的确定 (7)3.5 确定切削用量及基本工时 (8)3.5.1 粗铣燕尾 (8)3.5.2 精铣燕尾 (8)3.5.3 铣退刀槽 (8)3.5.4 粗铣端面 (9)3.5.5 精铣端面 (9)3.5.6 钻Φ52H7孔并倒角1.5×45º (10)3.5.7 钻2 × Φ12孔 (10)3.5.8 车端面 (12)3.5.9 切断 (13)四、机床夹具设计 (13)4.1工序尺寸精度分析 (13)4.2定位方案确定 (14)4.3定位误差分析计算 (14)4.4夹紧方案及元件的确定 (14)五、体会总结 (15)参考文献 (16)一、零件的分析1.1开合螺母上座体零件图如下所示:1.2零件的功能:题目所给定的零件是CA6140车床对开螺母体下部。
对开螺母体是用于接通和断开从丝杠传来的运动。
车削螺纹时,将开合螺母合上,丝杠通过对开螺母体传动溜板箱和刀架;否则就将对开螺母体脱开。
车削螺母时,顺时针方向转动手柄,通过轴带动曲线槽盘转动,曲线槽盘上的曲线槽盘形状,通过圆柱销带动上半螺母在溜板箱体后面的燕尾形导轨内上下移动,使其相互靠拢,将对开螺母体和丝杠啮合。
若逆时针方向转动手柄,则两半螺母相互分离,对开螺母体和丝杠脱开。
槽盘的曲线槽是一段圆弧,此圆弧在接近槽盘中心部分的倾斜角比较小,目的是使对开螺母体闭合能自锁,不会而自动脱开。
二、开合螺母座设计2.1确定毛坯的材料根据零件图所标出的零件材料,可知该零件为选用毛坯的材料为HT2002.2确定铸造方法根据零件的年生产纲领,可知此零件为中批量零件,可知选取铸造方法为手工铸造中的砂型铸造,选用的砂型类别为湿型;可知造型材料选用粘土砂,灰铸铁的尺寸公差等级为13-15级,选取等级为14级。
2.3毛坯的浇注方式:两箱铸造侧面浇注(见下图)2.4画毛坯图1)毛坯精度等级和在加工表面加放机械加工余量选取:根据【1】P3-13表3.1-26可知,要求的机械加工余量等级为F-H级,则取等级为G级,根据【1】P3-14表3.1-27可知,铸件的最大尺寸为120mm,要求的机械加工余量等级为G级,则要求的加工余量为2.2mm。
2)确定毛坯的基本的尺寸:(毛坯图示例见下图)毛坯余量是在零件图基础上加放;根据零件图上的基本尺寸可以确定毛坯图的基本尺寸,具体见如下尺寸:包括105、75.2、33、18及φ52H7的孔:注:1.孔的精度等级要比铸件的精度等级降一级,孔的机械加工余量等级也要较铸件等级低一级;① CT值(公差数值)均根据【1】P3-12表3.1-21查得,余量值均是根据【1】P3-14表3.1-27;②不加工表面不加放余量,也不标注公差;③查表时,表中的公称尺寸是零件图上对应的实际尺寸。
毛坯图示例:三、工艺规程设计3.1性能要求·上下螺母动作同步的要求·螺母与丝杠的同轴度要求·两螺母相对丝杠轴心的径向位置可调要求(两半螺母相互分离程度可调)·两半螺母对合时与丝杠中心线的对称度要求对齐并在允许的公差范围内。
(1)主要技术要求与分析主要技术条件的选择及分析是指:定性分析加工精度要求较高的表面之尺寸精度、相互位置精度、表面粗糙度等;能分析出若达不到要求,将会对机构的工作性能要求产生何种影响,以此做为今后工艺安排的依据之一。
[确定各加工表面符号以便于分析]·Ø52H7孔轴心线对C面平行度要求的分析;·Ø52H7孔轴心线对两B面垂直度要求的分析;·E面对Ø52H7孔轴心线的端面跳动要求的分析;·B1与B2面平行度要求的分析;·Ø12H7孔对C面垂直度要求的分析;2、审查零件的结构工艺性·零件的类型:中型支架类(切开后属叉架类);·具有燕尾结构,是零件的主要设计基准之一;·Ø52H7孔具有薄壁;·Ø52H7孔两端面处相对燕尾有凸台(作用);·调节螺钉孔M10底孔为深孔,且螺钉应保证和上螺母座接触面具有良好接触;由以上分析加工时是否便于进刀、退刀;是否便于装夹及减少装夹次数等。
3、由零件的生产纲领决定生产类型生产纲领是企业在计划期内应当生产的产品产量和进度计划。
零件在计划期内一年的生产纲领包含了备品、废品在内的生产数量。
按中型机械,根据零件年生产纲领,生产类型为成批生产中的中批生产范围。
3.2工艺路线的拟定(先粗后精原则、先面后孔原则等):一.预先热处理——粗刨(铣) C面、B面、D面——铣1X3退刀槽——粗加工两E面——粗镗(Ø52)孔二、——半精刨(铣)C面、B面——精刨(铣)C面、B面——刮研C面、B面[手工加工]三、——精加工两E面——半精镗(Ø52 )孔——精镗Ø52H7孔——钻、铰Ø12H7孔四、——铣切(5mm)分离上下螺母座——钻M10底孔(Ø8.5)——攻M10螺纹——钻2- Ø7及锪孔五、——清理去毛刺——检验3.3工艺路线方案:工序Ⅰ. 铸造。
Ⅱ. 热处理。
Ⅲ. 粗,铣底面Ⅳ. 铣1×3退刀槽Ⅴ. 粗铣两E面Ⅵ. 粗镗Φ50孔Ⅶ. 半精铣C面、B面,精铣C面、B面Ⅷ. 刮研C面、B面使粗糙度达1.6Ⅸ. 精铣两E面使对Φ52孔轴心线的端面跳动符合要求Ⅹ. 精镗Φ52孔并使轴心线与C面平行度符合要求Ⅺ. 钻Φ11.5孔深20,并使对C面垂直度符合要求Ⅻ. 铰Φ12H7孔并使轴心线与C面垂直度符合要求铣切分离上下螺母座钻M10底孔、攻M10螺纹、钻2-Φ7孔、锪90°锥孔2.精基准选择与分析以预铸孔Ø44为主要定位基准,这样加工C、B后以它们为精基准加工Ø52孔时,使孔的加工余量均匀。
2)加工燕尾上2-Ø12H7孔的定位基准C面为第一定位基准,限制3个不定度(保证与C面垂直度的要求);B面为第二定位基准,限制2个不定度(保证两孔连线与Ø52H7 孔轴线在水平面的垂直度要求);Ø52H7孔以削边销定位,限制1个不定度(保证两孔对中)3)主要加工面1、平面加工[主要是燕尾导轨的加工]2、孔加工[主要是Ø52H7、2-Ø12H7孔的加工]确定加工方法时,先从最终工序的加工方法所能达到的经济精度等级向前道工序推。
3.4机械加工余量、工序尺寸及毛坯尺寸的确定“对开螺母体”零件材料为HT200灰铸铁。
毛坯重量为4公斤,生产类型为中批生产,采用砂型铸造毛坯。
根据上述原始材料及加工工艺,分别对各加工表面的机械加工余量、工序尺寸及毛坯尺寸确定如下:1. Φ52H7孔精铰至Φ52H7,表面粗糙度为Ra1.6um,工序余量为2z=0.08;粗铰至51.92mm 2z=0.42;精车至51.5mm 2z=1.5;粗车第二次至50mm 2z=3;粗车至47m 2z=7;2. 2 ×Φ12孔铰至Φ12mm 2z=0.15;扩钻至Φ11.85mm 2z=0.85;钻至Φ11 2z=11;3. 一端面精车至97 2z=0.8;半精车至97.8 2z=1.2;粗车至99 2z=6;4. 另一端面精车至95 2z=0.5;半精车至96.5 2z=0.5;粗车至96 2z=1;3.5 确定切削用量及基本工时工序Ⅰ:铣燕尾及空刀槽3.5.1 粗铣燕尾v=6m/min(0.1m/s)ns=1000v/πdw =1000×× 40 =0.8r/s(47.8r/min)按机床选取nw=0.79 r/s (47.5r/min)∴实际切削速度切削工时:l1=8.7(表1-11-12)t0==158.3s(2.64min)3.5.2 精铣燕尾v=6m/min(0.1m/s)(表1-10-151)ns= =0.8r/s(47.8r/min)按机床选取nw=0.79 r/s (47.5r/min)∴实际切削速度v=πdw nw/1000=3.14×40×0.79/1000=0.43m/s 切削工时:l1=6.3(表1-11-12)t0==153s(2.6min)3.5.3 铣退刀槽s=0.02~0.03(表1-10-142)选s=0.02mmv=47m/min(0.78m/s)(表1-10-144)ns= =4.14r/s(248r/min)按机床选取nw=4 r/s (240r/min)∴实际切削速度v= =0.75m/s(45m/min)切削工时:l1=5.9,l2=4(表1-11-12)sm=sz z n=0.02× 4×36=2.88t0==3.785s(0.06min)3.5.4 粗铣端面选择高速钢套式面铣刀每齿进给量:sz=0.1-0.2(10-113)选sz=0.1mmv=56m/min(0.92m/s)ns= =3.7r/s(222r/min)按机床选取nw=4.2r/s (252r/min)∴实际切削速度v= =1.01m/s(61m/min)切削工时:l1=37.5,l2=2(表1-11-15)sm=sz z n=0.1× 18 × 3.7=0.37t0=(=185s(3min)3.5.5 精铣端面铣刀每转进给量0.10~0.12选s0=0.12mmv=56m/min=0.9m/sns==3.7r/s(222r/min)按机床选取nw=4.2r/s (252r/min)∴实际切削速度v= =1.01m/s(61m/min)切削工时:l1=37.5,l2=2(表1-11-15)sm=sz z n=0.1 × 18× 3.7=0.37t0==185s(3min)3.5.6 钻Φ52H7孔并倒角1.5×45º(1) 粗镗第一次至47mm选择硬质合金可调节浮动镗刀 B=25,H=12(表8-32)进给量S=1.6-2.0,选S=1.6mm/r(10-97)v=62.6m/min,n=398r/min(6.63r/min)(表10-98)切削工时l1=1.7,l2=3.0, l=105(表11-9)t=(D-d1)/2=(47-40)/2=3.5mmt0==10.34s(0.17min)①粗镗第二次至50mmS=1.6-2.0,选S=2.0mm/r(10-97)v=56.6m/min,n=360r/min(6r/min)(表10-98)切削工时l1=0.87, l=105(表11-9)t=(D-d1)/2=(50-47)/2=1.5mmt0==9.07s(0.15min)②精镗至52mS=1.6-2.0,选S=1.6mm/r(10-97)v=62.6m/min,n=398r/min(6.63r/min)(表10-98)切削工时l1=0.58, l=105(表11-9)t=(D-d1)/2=(51.5-50)/2=0.75mmt0= =10.24s(0.17min)3.5.7 钻2 ×Φ12孔选择直柄麻花钻(GB1436-78)④钻到11.0mmS=0.22-0.28,S=0.25mm/r(10-67)v=28m/min(0.47m/s),n=894r/min(7.95r/s)ns=1000v/切削工时l1=0.05,l2=39,l=105(表11-10)t=(D-d1)/2=(52-51.92)/2=0.04mmns==13.6r/s(816r/min)按机床选取nw=800r/s (13.3r/min)∴实际切削速度v = = 0.46m/s 切削工时:l1=3.4,l2=1.5,L=20(表11-6)t0==7.49s(0.13min)②扩孔钻至11.85S=0.7-0.9,S=0.7mm/r(10-75)v=22.2m/min,n=472r/min(表10-76)按机床选取nw=460r/min=7.67r/s实际切削速度=0.29m/s 切削工时l1=0.58,l2=1.5,l=20=4.11s(0.07min)③铰至Φ12选用锥柄机用铰刀D=12(表8-34)S=1.7 mm/r(10-81)v=10m/min,n=318r/min(5.3r/s)(表10-84)切削工时l1=0.05,l2=18,l=20=5.14s(0.09min)3.5.8 车端面①粗车至99mmS=(0.3~0.5) mm/r (10-19)选s=0.4 mm/rV=118m/min(1.97m/s)=9.65r/s(597r/min)按机床选取nw=8.6r/s(516 r/s)∴实际切削速度为=1.76m/s(105m/min)l=(105-99)/2=3mm,l1=3,l2=2 ,l3=5(11-4)L=d/2+ l1+ l2 + l3=32.5+3+2+5=42.5mmt0=(L/s.n ).i =(42.5/0.4×8.6)×2=24.72s(0.4min)②半精镗至97.8mmS=(0.3~0.5) mm/r (10-19)选s=0.3 mm/rV=35m/min(0.58m/s)=2.84r/s(171r/min)按机床选取nw=2.5r/s(150 r/s)∴实际切削速度为=0.51m/s(30.615m/min)l=0.6,l1=1,l2=1 ,l3=5(11-4)L=d/2+ l1+ l2 + l3=32.5+1+1+5=39.5mmt0=(L/s.n ).i =(39.5/0.3×2.5)×1=52.7s(0.88min)③精车至97mmS=(0.3~0.5) mm/r (10-19)选s=0.3 mm/rV=35m/min(0.58m/s)=2.84r/s(171r/min)按机床选取nw=2.5r/s(150 r/s)∴实际切削速度为=0.51m/s(30.615m/min)l=0.4,l1=1,l2=1 ,l3=5(11-4)L=d/2+ l1+ l2 + l3=32.5+1+1+5=39.5mmt0=(L/s.n ).i =(39.5/0.3×2.5)×1=52.7s(0.88min)④倒角1.5×45°S=(0.15~0.25) mm/r (10-90)选s=0.2 mm/rv=(12~25)m/min(0.58m/s),选v=20 m/min=0.33m/m=2.02r/s(121r/min)按机床选取nw=120r/min(2 r/s)l=0.75,l1=0.4(11-9)tm=(l+ l1)/nw .s=(0.75+0.4)/(2×0.2)=2.87min(172.5s)3.5.9 切断选用锯片铣刀,D=175mm(8-38),齿数(8~38)S=(0.03~0.04) mm/r (10-142)选s=0.03 mm/rv=34m/min(0.57m/s),=2.412r/s(144r/min)∴实际切削速度为=0.59m/s(35m/min)l1=6 ,l2=4mm(11-12)Sm= Sz·Z·n=0.03×40×2.5=3mm=49s(0.82min)四、机床夹具设计4.1工序尺寸精度分析由工序图知,本道工序为钻、锪两个φ6.5径向孔。