镍的物理性质
镍冶金
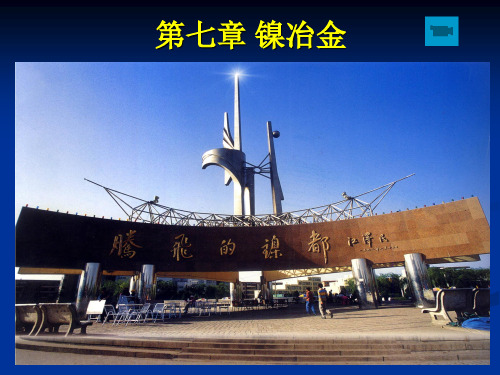
7.3.1.4 .3 缓冷工序的工艺原则 缓冷使相分离,并促进晶粒长大。控制从1200K到644K间的冷 却速度十分重要,特别是控制848K~793K间的冷却速度,有利 于 Cu2S和Cu-Ni合金相从固体Ni3S2基体中析出,并和已析出的 Cu2S和Cu-Ni合金相晶粒结合。冷却速度过快, Ni3S2基体中存 在Cu2S和Cu-Ni合金相的极细晶粒,不利于选矿分离。 7.3.1.4 .4 高镍硫的分离 缓冷后的高锍镍经过破碎、磨细、磁选和浮选,得到的Cu2S精 矿送铜冶炼系统处理; Ni3S2精矿经反射炉熔炼,浇铸成Ni3S2 阳极板,进行电解精炼生产电镍; Cu-Ni合金用于回收贵金属。
7.3.3 硫化镍的电解精炼 硫化镍阳极的隔膜电解工艺是我国目前主要的电解镍生产工 艺,其镍产量占总镍产量的90%以上。 电解精炼采用隔膜电解槽。用硫化镍板做阳极,阴极为镍始 极片,电解液用硫酸盐溶液和氯化盐混合溶液。 电解精炼的电极反应:
阳极
Ni3S2 – 2e = Ni2+ + 2NiS 2NiS - 4e=2Ni2++2S Ni2+ + 2e = Ni
7.1.2. 化学性质: 镍能抗氧锈蚀,因为其表面生成致密薄膜,能阻止进一 步氧化。也能抗强碱腐蚀,它在稀盐酸和硫酸中溶解很慢, 但稀硝酸能与之作用。
镍与氧生成三种化合物,即氧化亚镍(NiO),四氧化三镍 (Ni3O4)和三氧化二镍(Ni2O3),只有NiO在高温下稳定;镍与 硫生成四种化合物,即NiS2, Ni6S5,Ni3S2和NiS,在冶炼高温 下只有Ni3S2稳定。
Na2CO3=Na2O+CO2 2Na2O+3S=2Na2S+SO2 Na2O+SiO2=Na2SiO3
镍及其主要化合物的物理化学性质

世上无难事,只要肯攀登镍及其主要化合物的物理化学性质镍是元素周期表中第Ⅷ族的元素,其在元素周期表中的位置决定了镍及其化合物的一系列物理化学特性,镍的许多物理化学性质与危钴、铁相似;由于在元素周期表中与铜毗邻,因此在亲氧和亲硫性方面又较接近铜。
(一)镍的主要物理化学性质镍是一种银白色的金属,在20℃时的密度为8.908g.cm-3,熔点(1453℃)时液体镍的密度为7.9g·cm-3, 1500℃为7.76g·cm-3,其他镍产品的密度(g.cm-3)分别为:铸镍8.8,电镍8.9,镍丸8.4,化学纯致密镍9.04±0.03。
在20℃时镍的比电阻为6.9×10-6Ω/cm.镍基合金虽然广泛用于热元件,但由于易氧化的原因纯镍实际上无此用途。
热电性与铁、铜、银、金属不同,较铂为负,所以在冷端的电流由铂流向镍,因此,以镍作为热电元件时可产生高的电钢产动势。
室温下工业用镍最大饱和极化强度为0.61T,最低矫顽力为1.5A/cm,是许多磁性物料(由高导磁率的软磁合金至高矫顽磁性,它确定了镍磁性器件工作的上限温度。
单位体积的镍能吸收4.15 倍体积的氢气。
镍的原子序数28,原子量58.71,熔点(1453±1)℃,沸点2732℃。
镍在大气中不易生锈,能抵抗苛性碱的腐留尼旺岛蚀。
大气实验结果表明,99%纯度的镍在20 年内不生锈痕,无论在水溶液或溶盐内镍抵抗苛性碱的能力都很强;沸腾的50%苛性钠溶液中每年的蚀速度不超过25µm,对于盐类溶液,只容易受到氧化性盐类(如氧化高铁或次氧酸铁盐)的侵蚀。
在空气或氧气中,镍的电极位为-0.227V,25℃时为-0.231V,若溶液中有少量杂质,尤其是有硫存在时,镍即显著钝化。
(二)镍的主要化合物及其性质镍的化合物在自然界里有三种基本形态,即镍的氧化物、硫化物和砷化物。
它的氧化物有氧化亚镍(NiO)、四氧化三镍(Ni2O3)。
镍简介介绍
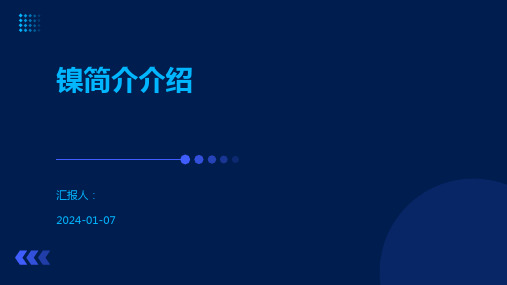
汇报人: 2024-01-07
目录
• 镍的物理性质 • 镍的化学性质 • 镍的来源和提取 • 镍的应用 • 镍对环境和健康的影响
01
镍的物理性质
镍的外观
01
镍是一种银白色的金属,具有金 属光泽,常温下不易氧化。
02
镍的表面容易形成氧化层,这有 助于保护内部金属不被进一步氧 化。
镍的密度
03
硝酸镍主要用于制造镍合金和
电镀等。
04
氧化镍是一种常见的催化剂和
颜料,也用于陶瓷和玻璃制造
等领域。
05
硫化镍是重要的矿物原料,可 用于提取镍和钴等金属元素。
06
03
镍的来源和提取
镍矿的类型
01
02
03
红土镍矿
红土镍矿是最常见的镍矿 类型,主要分布在热带地 区,如澳大利亚、印度尼 西亚和菲律宾。
04
镍的应用
镍的应用
• 镍是一种银白色的金属元素,具有高度耐 腐蚀性和延展性。它在地球上的储量丰富 ,是工业和科技领域中非常重要的金属之 一。
05
镍对环境和健康的影响
镍对环境和健康的影响
• 镍是一种银白色的金属元素,具 有高度耐腐蚀性和延展性。它在 自然界中以镍矿的形式存在,并 广泛应用于工业、制造业和电子 产品等领域。
镍的化学反应
镍具有较高的化学活性, 能够与多种元素进行反应 ,形成各种化合物。
镍与硫反应生成硫化镍, 与氯气反应生成氯化镍, 与氢气反应生成氢化镍等 。
ABCD
在空气中,镍容易氧化生 成坚固的氧化膜,保护内 部的镍不被进一步氧化。
在高温条件下,镍能够与 碳、一氧化碳等发生反应 ,生成碳化镍和羰基镍等 化合物。
镍的导电率
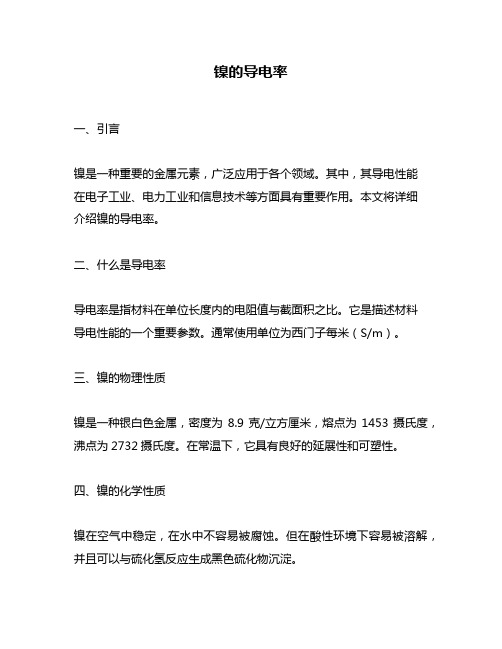
镍的导电率一、引言镍是一种重要的金属元素,广泛应用于各个领域。
其中,其导电性能在电子工业、电力工业和信息技术等方面具有重要作用。
本文将详细介绍镍的导电率。
二、什么是导电率导电率是指材料在单位长度内的电阻值与截面积之比。
它是描述材料导电性能的一个重要参数。
通常使用单位为西门子每米(S/m)。
三、镍的物理性质镍是一种银白色金属,密度为8.9克/立方厘米,熔点为1453摄氏度,沸点为2732摄氏度。
在常温下,它具有良好的延展性和可塑性。
四、镍的化学性质镍在空气中稳定,在水中不容易被腐蚀。
但在酸性环境下容易被溶解,并且可以与硫化氢反应生成黑色硫化物沉淀。
五、镍的导电率1. 镍的导电率数值镍是一种良好的导体,在常温下具有较高的导电率。
根据数据统计,纯度为99.99%的镍的导电率为14.6×10^6西门子每米。
2. 镍的导电性能与温度的关系镍的导电率随着温度的升高而降低。
在常温下,镍的导电率较高,但当温度接近室温时,其导电率会逐渐降低。
当温度达到300摄氏度时,镍的导电率将降至原来的一半左右。
3. 镍合金的导电性能除了纯镍外,镍合金也具有较好的导电性能。
例如,铜镍合金、铁镍合金和钴镍合金等都具有良好的导电性能。
其中,铜镍合金是一种重要的结构材料,在船舶、海洋工程和化工等领域广泛应用。
六、影响镍导电率因素1. 温度随着温度升高,材料内部原子振动加剧,晶格缺陷增多,对载流子运动产生阻碍作用,从而使材料导体中载流子迁移受到阻碍。
因此,在高温条件下,材料的电阻值增大。
2. 杂质杂质对材料内部结构和晶格缺陷的影响是导致电阻值变化的主要原因之一。
杂质原子在晶格中占据位置,改变了晶体结构,从而影响了载流子的迁移和能量传递。
3. 晶体结构材料内部晶体结构的不同也会影响其导电性能。
例如,金属材料中存在多种晶体结构,其中面心立方结构、体心立方结构和六方密堆积结构等都具有较好的导电性能。
七、总结镍是一种重要的金属元素,在各个领域都有广泛应用。
镍的cas号
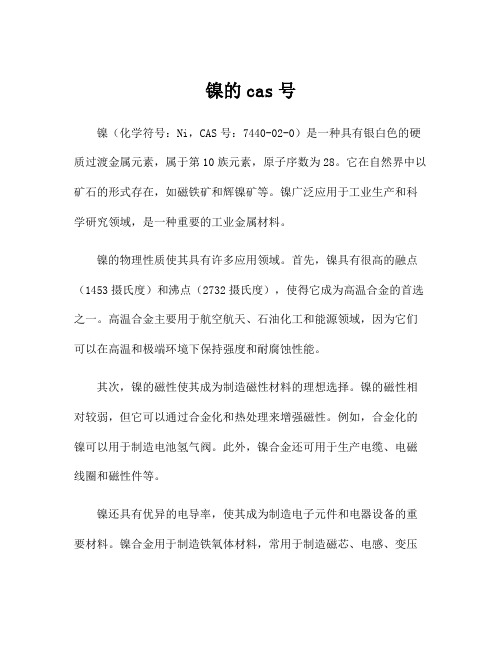
镍的cas号镍(化学符号:Ni,CAS号:7440-02-0)是一种具有银白色的硬质过渡金属元素,属于第10族元素,原子序数为28。
它在自然界中以矿石的形式存在,如磁铁矿和辉镍矿等。
镍广泛应用于工业生产和科学研究领域,是一种重要的工业金属材料。
镍的物理性质使其具有许多应用领域。
首先,镍具有很高的融点(1453摄氏度)和沸点(2732摄氏度),使得它成为高温合金的首选之一。
高温合金主要用于航空航天、石油化工和能源领域,因为它们可以在高温和极端环境下保持强度和耐腐蚀性能。
其次,镍的磁性使其成为制造磁性材料的理想选择。
镍的磁性相对较弱,但它可以通过合金化和热处理来增强磁性。
例如,合金化的镍可以用于制造电池氢气阀。
此外,镍合金还可用于生产电缆、电磁线圈和磁性件等。
镍还具有优异的电导率,使其成为制造电子元件和电器设备的重要材料。
镍合金用于制造铁氧体材料,常用于制造磁芯、电感、变压器等电子元件。
此外,镍也是电池中常见的电极材料,如镍镉电池和镍氢电池。
除了以上应用,镍还用于制造不锈钢和合金钢。
不锈钢中加入约8-10%的镍可以提高其耐锈蚀性和耐腐蚀性能。
这是因为镍与铁形成的镍铁合金可以防止氧气进一步发生反应。
不锈钢广泛应用于建筑、化工、医疗和食品加工等领域。
此外,镍在环境和能源领域也有重要应用。
例如,镍合金可以用于生产气体分离膜,例如用于制造氢气和氧气的电解槽。
此外,镍合金还可用于生产太阳能电池板、电池收集器和燃料电池。
虽然镍是一种重要的金属材料,但它也具有一定的危害性。
与镍及其化合物接触可能对人体健康造成不良影响。
例如,对职业暴露于镍粉尘和化合物的工人可能产生皮肤炎、气管炎、支气管炎等症状。
因此,在处理镍和镍化合物时应采取必要的防护措施。
总的来说,镍作为一种重要的工业金属材料,在许多领域都有广泛应用。
它的高温抗氧化性能、磁性、电导率和耐腐蚀性使其成为制造高温合金、磁性材料、电子元件和不锈钢的理想选择。
在未来,随着科学技术的进一步发展,镍可能会在更多的领域发挥重要作用。
镍化学符号
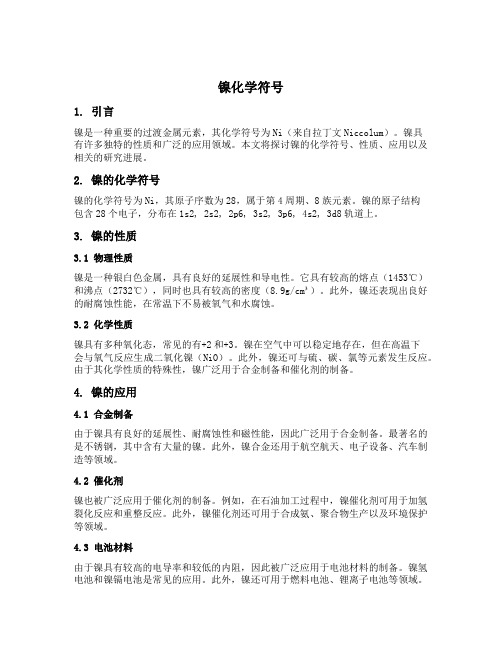
镍化学符号1. 引言镍是一种重要的过渡金属元素,其化学符号为Ni(来自拉丁文Niccolum)。
镍具有许多独特的性质和广泛的应用领域。
本文将探讨镍的化学符号、性质、应用以及相关的研究进展。
2. 镍的化学符号镍的化学符号为Ni,其原子序数为28,属于第4周期、8族元素。
镍的原子结构包含28个电子,分布在1s2, 2s2, 2p6, 3s2, 3p6, 4s2, 3d8轨道上。
3. 镍的性质3.1 物理性质镍是一种银白色金属,具有良好的延展性和导电性。
它具有较高的熔点(1453℃)和沸点(2732℃),同时也具有较高的密度(8.9g/cm³)。
此外,镍还表现出良好的耐腐蚀性能,在常温下不易被氧气和水腐蚀。
3.2 化学性质镍具有多种氧化态,常见的有+2和+3。
镍在空气中可以稳定地存在,但在高温下会与氧气反应生成二氧化镍(NiO)。
此外,镍还可与硫、碳、氯等元素发生反应。
由于其化学性质的特殊性,镍广泛用于合金制备和催化剂的制备。
4. 镍的应用4.1 合金制备由于镍具有良好的延展性、耐腐蚀性和磁性能,因此广泛用于合金制备。
最著名的是不锈钢,其中含有大量的镍。
此外,镍合金还用于航空航天、电子设备、汽车制造等领域。
4.2 催化剂镍也被广泛应用于催化剂的制备。
例如,在石油加工过程中,镍催化剂可用于加氢裂化反应和重整反应。
此外,镍催化剂还可用于合成氨、聚合物生产以及环境保护等领域。
4.3 电池材料由于镍具有较高的电导率和较低的内阻,因此被广泛应用于电池材料的制备。
镍氢电池和镍镉电池是常见的应用。
此外,镍还可用于燃料电池、锂离子电池等领域。
4.4 其他应用除了上述应用之外,镍还有许多其他的应用。
例如,在航空航天领域,镍被用于制造发动机叶片和涡轮叶片。
在化学工业中,镍可用于催化剂、催化剂载体和防腐蚀材料的制备。
5. 镍相关研究进展5.1 镍合金研究近年来,关于镍合金的研究取得了许多进展。
例如,通过调控合金组分和微观结构可以改变合金的力学性能和耐腐蚀性能。
镍基础知识分析

镍基础知识分析镍是一种常见的金属元素,具有广泛的应用领域。
本文将对镍的基础知识进行分析。
物理性质- 原子序数:镍的原子序数是28,属于过渡金属元素。
原子序数:镍的原子序数是28,属于过渡金属元素。
- 密度:镍的密度为8.9克/立方厘米,是较重的金属。
密度:镍的密度为8.9克/立方厘米,是较重的金属。
- 熔点和沸点:镍的熔点为1453摄氏度,沸点为2732摄氏度。
熔点和沸点:镍的熔点为1453摄氏度,沸点为2732摄氏度。
- 颜色和外观:镍呈银白色,并具有光泽。
颜色和外观:镍呈银白色,并具有光泽。
- 导电性:镍是一种良好的导电金属。
导电性:镍是一种良好的导电金属。
化学性质- 化学符号:镍的化学符号是Ni,来自拉丁文"Nicolaus",即尼古拉斯。
化学符号:镍的化学符号是Ni,来自拉丁文"Nicolaus",即尼古拉斯。
- 反应性:镍相对稳定,在常温下不与空气直接反应,但可以与许多酸和碱反应。
反应性:镍相对稳定,在常温下不与空气直接反应,但可以与许多酸和碱反应。
- 耐腐蚀性:镍具有较好的耐腐蚀性,能够抵抗许多化学物质的侵蚀。
耐腐蚀性:镍具有较好的耐腐蚀性,能够抵抗许多化学物质的侵蚀。
- 合金形成:镍是许多合金的重要成分,如不锈钢、合金钢和镍合金等。
合金形成:镍是许多合金的重要成分,如不锈钢、合金钢和镍合金等。
应用领域镍作为一种重要的金属元素,在许多领域中发挥着重要作用:1. 电池制造:镍被广泛用于制造电池,如镍镉电池、镍氢电池等。
电池制造:镍被广泛用于制造电池,如镍镉电池、镍氢电池等。
2. 合金制造:镍合金具有优异的耐腐蚀性和高温强度,广泛用于航空航天、能源、化工等领域。
合金制造:镍合金具有优异的耐腐蚀性和高温强度,广泛用于航空航天、能源、化工等领域。
3. 催化剂:镍催化剂在化学反应中起到重要作用,促进反应速率。
催化剂:镍催化剂在化学反应中起到重要作用,促进反应速率。
金属元素镍

大
简介 性质 镍的回收 镍的催化应用
纲
• 公元前一世纪,“鋈” • 1751年瑞典矿物学家克朗斯塔特发现了镍 • 地壳中已知含镍矿物约50余种。其中硫化物,如镍黄铁 矿、紫硫镍铁矿等游离硫化镍形态存在。氧化镍矿的开 发利用是以镍红土矿为主,镍主要以镍褐铁矿形式存在 。 • 含镍废料的回收不仅有效利用废弃资源,补充镍的需求 ,而且具有很好的社会效益和经济效益。
3.从含镍废催化剂中回收镍及其他有价金属
4.从含镍冶炼废渣、废料及尾矿中回收镍及其他有价金属。 5.存在问题 • 再生镍原料少 • 处理工艺不成熟。火法工艺能耗大,湿法工艺流程多,还 不能做到三废零排放。
镍的催化应用
以苯硼酸和2—溴丙酸乙酯作为反应底物,碳酸钾作碱,甲苯做溶剂 的体系中,考察了过渡金属Cu、Co和Ni做催化剂的反应。
1. 物理性质简介 金属镍密度为8.902克/立方厘米,熔点为1453℃, 沸点为2732℃,是近似银白色、硬而有延展性、柔韧性 并具有铁磁性的金属,常被用来制作磁性合金跟形状记 忆合金。见于地壳局部,平均含量百万分之七十。能被
磨得光亮如镜,通常情况下绝不生锈。
2. 化学性质
化学符号为Ni,原子序数为28,相对原子质量为58.69,它属于Ⅷ 副族跟第四周期元素,也属过渡金属元素。镍在空气中不易被氧化,化 学性质很稳定,仅易溶于硝酸。
电子构型: 1s2 2s22p6 3s23p63d84s2
氧化态: 2,3
电子模型:
3、镍在生活中的应用 具有优良的抗腐蚀性,用于电镀,镍镉电池,也用作催化剂。 利用钛镍合金的转变温度,在低温下制作理想模型。
纯镍银光闪闪,不易锈蚀,主要用于电镀工业。
镍具有磁性,能被磁铁吸引。 氧化镍常用来制造铁镍碱性蓄电池。
镍

对人影响致敏性
镍是最常见的致敏性金属,约有20%左右的人对镍离子过敏,女性患者的人数 要高于男性患者,在与人体接触时,镍离子可以通过毛孔和皮脂腺渗透到皮肤 里面去,从而引起皮肤过敏发炎,其临床表现为皮炎和湿疹。一旦出现致敏, 镍过敏能常无限期持续。患者所受的压力、汗液、大气与皮肤的湿度和磨擦会 加重镍过敏的症状。镍过敏性皮炎临床表现为瘙痒、丘疹性或丘疹水疱性的皮 炎,伴有苔藓化。
元素中文名称:镍
元素英文名称:Nickel 相对原子质量:58.69 核内质子数:28 核外电子数:28 核电核数:28 质子质量:4.6844E-26 质子相对质量:28.196 好的机械强度和延展性,难熔、在空气中不氧化的特性。镍 是银白色金属。熔点为1726K,沸点为3005K,密度为8.902g/cm3。
瑞典化学家克隆斯特研究了这个矿物,他得到了少量与铜不同的金属。他在 1751年发表研究报告,认为这是一种新金属,就称它为nickel,这也就是镍的 拉丁名称niccolum和符号Ni的来源。镍在欧洲被发现后,德国人首先把它掺 入铜中,制成所谓日耳曼银,或称德国银,也就是我国的白铜。
产销分布:
2006年全球精炼镍产量约136万吨,主要产国分别为:俄罗斯(20%)、 日本(13%)、加拿大(11%)、澳大利亚(9%)、中国(7%)、挪 威(7%)。其中,日本对特殊钢的产量及需求量相当大,大量进口镍矿 以从事精炼镍生产,掌握原料来源,其产量跃居全球第二。
钛镍合金具有“记忆”的本领,而且记忆力很强,经过相当长的时间,重复上 千万次都准确无误。它的“记忆”本领就是记住它原来的形状,所以人们称它 为“形状记忆合金”。原来这种合金有一个特性转变温度,在转变温度之上, 它具有一种组织结构,而在转变温度之下,它又有另一种组织结构。结构不同, 性能也就不同。例如:一种钛镍记忆合金,当它在转变温度之上时,很坚硬, 强度大,而在这个温度以下,它却很软,容易冷加工。这样,当我们需要它记 忆什么形状时,就把它做成那种形状,这就是它的“永久记忆“形状,在转变 温度以下,由于它很软,我们便可以在相当大的程度内使其任意变形。而当需 要它恢复到原来形状时,只要把它加热到转变温度以上就行了。
金属镍材料参数
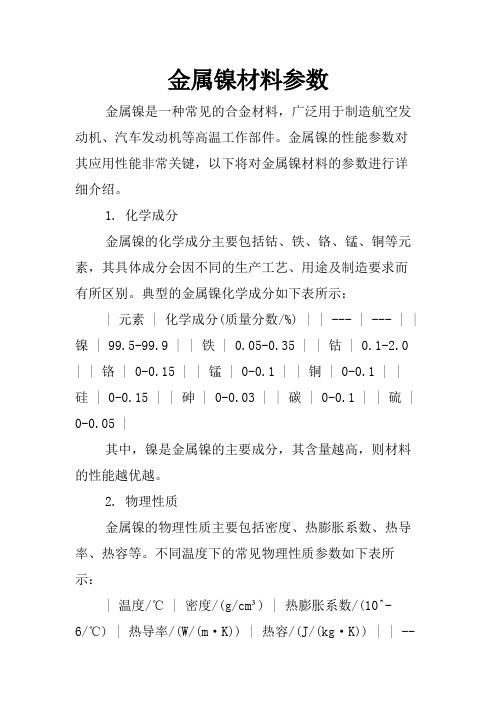
金属镍材料参数金属镍是一种常见的合金材料,广泛用于制造航空发动机、汽车发动机等高温工作部件。
金属镍的性能参数对其应用性能非常关键,以下将对金属镍材料的参数进行详细介绍。
1. 化学成分金属镍的化学成分主要包括钴、铁、铬、锰、铜等元素,其具体成分会因不同的生产工艺、用途及制造要求而有所区别。
典型的金属镍化学成分如下表所示:| 元素 | 化学成分(质量分数/%) | | --- | --- | | 镍 | 99.5-99.9 | | 铁 | 0.05-0.35 | | 钴 | 0.1-2.0 | | 铬 | 0-0.15 | | 锰 | 0-0.1 | | 铜 | 0-0.1 | |硅 | 0-0.15 | | 砷 | 0-0.03 | | 碳 | 0-0.1 | | 硫 | 0-0.05 |其中,镍是金属镍的主要成分,其含量越高,则材料的性能越优越。
2. 物理性质金属镍的物理性质主要包括密度、热膨胀系数、热导率、热容等。
不同温度下的常见物理性质参数如下表所示:| 温度/℃ | 密度/(g/cm³) | 热膨胀系数/(10^-6/℃) | 热导率/(W/(m·K)) | 热容/(J/(kg·K)) | | --- | --- | --- | --- | --- | | 20 | 8.9 | 13.3 | 70-100 | 445-450 | | 600 | 8.0 | 14.5 | 57-84 | 576 | | 800 | 7.7 | 14.9 | 52-76 | 622 | | 1000 | 7.4 | 15.4 | 47-68 | 657 |可见,随着温度的升高,金属镍的密度逐渐下降,热膨胀系数逐渐增大,其热导率和热容则先升高后稳定。
3. 机械性能金属镍的机械性能主要包括强度、硬度、韧性等指标。
不同条件下的机械性能参数如下表所示:|条件| 抗拉强度/(MPa) | 屈服强度/(MPa) | 伸长率/% | 硬度/(HV) | |---|---|---|---|---| | 室温 | 590-690 | 200-400 | 10-60 | 150-300 | | 800℃ | 85 | 55 | >30 | 80 |在高温环境下,金属镍的强度大幅下降,但其韧性增加。
1镍

一镍金属简介(一)镍的性质和用途1、镍的性质镍是一种银白色的铁磁性金属。
密度8.9g/cm3,熔点1455℃。
古代埃及、中国和巴比伦人都曾用含镍量很高的陨铁作器物。
可以说,镍是既“古老”又“年轻”的金属。
镍具有磁性,是许多磁性材料的主要组成成分。
镍还具有良好的抗氧化性,在空气中,镍表面形成NiO薄膜,可阻止进一步氧化。
(1)镍的物理性质镍是一种银白色的金属,其物理性质与金属钴、铁有相当一致的地方,重要表现在:A、镍的比重:在20℃时为8.908,可靠数值为8.9~8.908,熔点时液体镍的比重为7.9。
B、镍的比热:在0~1000℃的温度范围内变动于420~620焦耳/公斤·K,在居里点或其附连有一显著的高峰,此温度下失去铁磁性。
C、镍的电阻:在20℃时按其纯度99.99~99.8%变动于6.8~9.9微欧厘米(10~8Ωm)。
镍基合金虽然广泛用于热电元件,但由于氧化关系纯镍实际上无此用途。
D、镍的热电性与铁、铜、银、金等金属不同,较铂为负,所以在冷端的电流由铂流向镍,因此,以镍作为热电元件时可产生高的电动势。
E、镍具有磁性,是许多磁性物料(由高导磁率的软磁合金至高矫顽力的永磁合金)的主要组成部分,其含量常为10~20%。
(2)镍的化学性质金属镍是元素周期表第8族铁磁金属之一,原子序数28,原子量58.71,熔点1453±1℃,沸点2800℃。
天然生成的金属镍有五种稳定的同位素:Ni5867.7%、Ni6026.2%、Ni611.25%、Ni623.66%、Ni641.66%。
其主要化学性质有:A、稀硫酸与盐酸能缓慢溶解镍,稀硝酸与镍作用快,但浓硝酸使镍钝化,镍与碱不起作用。
镍能抵抗所有的有机化合物。
B、纯镍具有银白色的光泽,当其与水蒸气及空气中的氧作用时,镍表面上形成一层NiO薄膜,可防止进一步氧化。
含硫的气体对镍有严重腐蚀,尤其在镍与硫化镍Ni3S2共晶温度在643℃以上时更是如此。
第五章镍冶金

5.2.4、高铜冰镍的磨浮分离 磨浮分离是用浮选的方法来分离高 铜冰镍,得到纯的硫化镍和硫化铜精 矿,为此将吹炼产出的高铜冰镍注入7 -8吨的保温模内,缓冷72小时,以使 其中的铜硫化物、铜镍合金和镍硫 化物相分别结晶,有利于下一步相互 分离。
5.3氧化镍矿的火法冶炼
5.3.1、炉料的准备 包括烧结或制团,其中 烧结法规模最大,应用的也较普遍。因为 它不需要将矿石预先干燥,获得的烧结块 强度大,透气性好,烧结过程在烧结机上 进行。氧化镍矿的烧结主要是还原烧结, 配入焦粉作为热源和还原剂;如果用黄铁 矿作硫化剂时,也可在烧结时配入。依靠 脉石所生成的低熔点硅酸盐作为粘结剂。 烧结机的生产率按合格块料计算为17~19吨 /米2.日
3NiO+2FeS+Fe=Ni3S2+3FeO
3NiSiO3+2FeS+Fe=Ni3S2+1.5Fe2SiO4+1.5SiO2 NiO+Fe=Ni+FeO 2NiSiO3+2Fe=2Ni+Fe2SiO4+SiO2
5.3.3、冰镍的吹炼 冰镍是由镍、铁、硫组成的合金, 三元成分占98-99%。工业实践指 出,冰镍金属化程度很高(34- 36%),有60%的镍成金属状态, 28-42%的铁成铁镍合金,因此吹 炼时的反应为: 2Fe+O2+SiO2=2FeO.SiO2 2FeS+3O2+SiO2=2FeO.SiO2+2SO2
• 2. 羰基法生产镍的原理 40~120℃ 生成气态Ni(CO)4
Ni(固)+ 4CO (气)
50℃
Ni(CO)4(气)
5.5硫化镍精矿的湿法冶金
• 5.5.1硫化镍精矿的加压氨浸 • 1、浸出过程 NiS+2O2+6NH3=Ni(NH3)6SO4 4FeS+9O2+8NH3+4H2O=2Fe2O3+8NH+4 +4SO2-4
镍的电位差问题回答
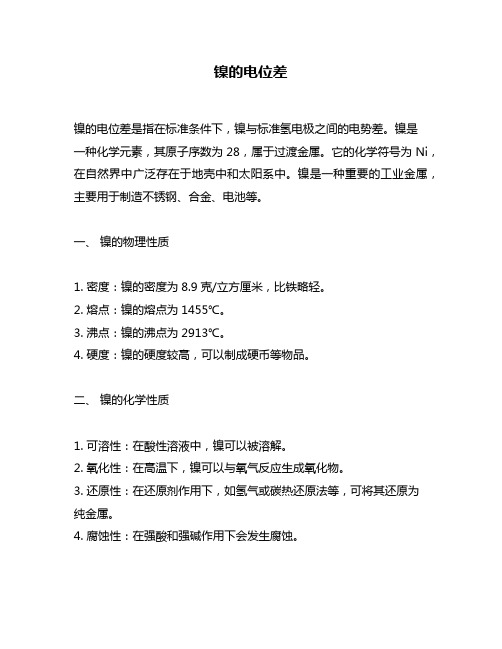
镍的电位差镍的电位差是指在标准条件下,镍与标准氢电极之间的电势差。
镍是一种化学元素,其原子序数为28,属于过渡金属。
它的化学符号为Ni,在自然界中广泛存在于地壳中和太阳系中。
镍是一种重要的工业金属,主要用于制造不锈钢、合金、电池等。
一、镍的物理性质1. 密度:镍的密度为8.9克/立方厘米,比铁略轻。
2. 熔点:镍的熔点为1455℃。
3. 沸点:镍的沸点为2913℃。
4. 硬度:镍的硬度较高,可以制成硬币等物品。
二、镍的化学性质1. 可溶性:在酸性溶液中,镍可以被溶解。
2. 氧化性:在高温下,镍可以与氧气反应生成氧化物。
3. 还原性:在还原剂作用下,如氢气或碳热还原法等,可将其还原为纯金属。
4. 腐蚀性:在强酸和强碱作用下会发生腐蚀。
三、镍的电位差1. 定义:镍的电位差是指在标准条件下,镍与标准氢电极之间的电势差。
2. 测定方法:可以使用电化学实验方法进行测定,如循环伏安法、线性扫描伏安法等。
3. 影响因素:镍的电位差受到温度、浓度、氧化还原状态等因素的影响。
4. 应用:镍的电位差可以用于制备合金、制造电池等领域。
四、镍的应用1. 制造不锈钢:镍是不锈钢中重要的合金元素,可以提高其耐腐蚀性和强度。
2. 制造合金:镍可以与其他元素形成多种合金,如铜镍合金、铬镍合金等,这些合金具有良好的耐腐蚀性和机械强度。
3. 制造电池:在镉镍电池和镉氢化物电池中,都需要使用到纯度较高的镍质材料。
4. 其他应用:除此之外,还有制造硬币、催化剂等。
五、镍对人体健康的影响1. 吸入镍粉末或镍化合物会对呼吸系统造成危害,引起支气管炎、肺炎等。
2. 镍与皮肤接触会引起过敏反应和皮炎等皮肤病。
3. 镍是一种致癌物质,长期接触会增加患癌的风险。
六、结论镍是一种重要的工业金属,在不锈钢、合金、电池等领域有广泛应用。
其电位差可以用于制备合金、制造电池等领域。
但是,长期接触镍会对人体健康造成危害,需要注意防护措施。
镍材料的物理和化学性质分析

镍材料的物理和化学性质分析镍是一种重要的金属材料,常用于制造钢铁、电池、合金及其他化工产品等。
它的物理和化学性质与医疗器械、电子、航空航天等行业的发展密切相关,因此我们有必要对镍材料的性质做出进一步的了解和分析。
一、物理性质1. 密度和比热镍的密度为8.9克/立方厘米,比热为0.44焦耳/克•摄氏度。
这些参数使它具有优异的加工性能,可以轻松地制造各种形状的零件和产品。
2. 相变温度和热膨胀系数镍具有较高的相变温度和热膨胀系数,这使得它在高温环境中使用时能够维持稳定的性能和尺寸。
例如,在航空航天器制造中,镍合金常用于制造高温部件,如涡轮叶片、燃烧室等。
3. 导电性和磁性镍是一种优异的导电体,具有优异的电子传输和电流稳定性。
此外,它还是一种被广泛应用的磁性材料,常用于制造电机、变压器等电器设备。
二、化学性质1. 腐蚀和抗蚀性能镍具有良好的抗腐蚀性能,能够在高温和强酸/碱环境下保持其稳定性和性能。
这使得它被广泛用于制造化工设备、医疗器械器材以及耐高温耐腐蚀的合金材料等。
2. 氧化和还原性镍与许多元素都能形成不同的氧化物和化合物,因而也有非常广泛的领域用途。
例如,许多电池中使用的镍氢电池或锂离子电池都是以镍为正极材料,其还原反应使电池放电放能。
三、应用领域镍材料的性质决定了它在许多领域中的应用广泛。
以下是几个常见的应用领域:1. 电子设备镍的高导电和低磁阻特性使其成为一种常用的电子元件材料。
例如,镍用于制造铁氧体材料和磁铁,在计算机、手机等设备中有广泛应用。
2. 航空航天航空航天器制造需要高强度、高温及耐腐蚀的材料。
镍合金是一种常用的材料,用于制造涡轮叶片、燃烧室、喷气发动机等高温部件。
3. 医疗器械镍材料在医疗器械领域中应用广泛,包括人工假肢、人工关节、种植物等,其优异的生物相容性和耐腐蚀性都是重要的考虑因素。
4. 化工领域镍在化学反应催化剂中有广泛应用,可用于生产化肥、合成氨、氯化氢等工业原料。
在这些领域中,镍材料的物理和化学性质的差异及优异的应用性能都是非常关键的。
ni的熔点
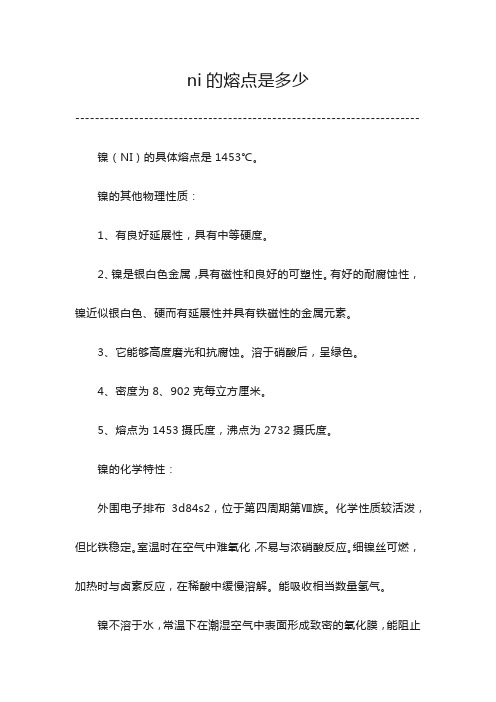
ni的熔点是多少---------------------------------------------------------------------- 镍(NI)的具体熔点是1453℃。
镍的其他物理性质:1、有良好延展性,具有中等硬度。
2、镍是银白色金属,具有磁性和良好的可塑性。
有好的耐腐蚀性,镍近似银白色、硬而有延展性并具有铁磁性的金属元素。
3、它能够高度磨光和抗腐蚀。
溶于硝酸后,呈绿色。
4、密度为8、902克每立方厘米。
5、熔点为1453摄氏度,沸点为2732摄氏度。
镍的化学特性:外围电子排布3d84s2,位于第四周期第Ⅷ族。
化学性质较活泼,但比铁稳定。
室温时在空气中难氧化,不易与浓硝酸反应。
细镍丝可燃,加热时与卤素反应,在稀酸中缓慢溶解。
能吸收相当数量氢气。
镍不溶于水,常温下在潮湿空气中表面形成致密的氧化膜,能阻止本体金属继续氧化。
在稀酸中可缓慢溶解,释放出氢气而产生绿色的正二价镍离子Ni2+;耐强碱。
镍可以在纯氧中燃烧,发出耀眼白光。
同样的,镍也可以在氯气和氟气中燃烧。
对氧化剂溶液包括硝酸在内,均不发生反应。
镍是一个中等强度的还原剂。
镍盐酸、硫酸、有机酸和碱性溶液对镍的浸蚀极慢。
镍在稀硝酸缓慢溶解。
发烟硝酸能使镍表面钝化而具有抗腐蚀性。
镍同铂、钯一样,钝化时能吸大量的氢,粒度越小,吸收量越大。
镍的重要盐类为硫酸镍和氯化镍。
实验室中也常用到硝酸镍,带有结晶水,化学式为Ni(NO3)2·6H2O,绿色透明的颗粒,易吸收空气中的水蒸汽。
与铁,钴相似,在常温下对水和空气都较稳定,能抗碱性腐蚀,故实验室中可以用镍坩埚熔融碱。
硫酸镍(NiSO4)能与碱金属硫酸盐形成矾Ni(SO4)·6H2O(MI 为碱金属离子)。
+2价镍离子能形成配位化合物。
常压下,镍即可与一氧化碳反应,形成剧毒的四羰基镍(Ni(CO)4),加热后它又会分解成金属镍和一氧化碳。
纯镍的密度

纯镍的密度1. 密度的定义和计算公式密度是物质的质量和体积的比值,用来描述物质的紧密程度。
它是一个物质的固有属性,可以通过实验测量得到。
密度的计算公式如下:密度=质量体积2. 纯镍的性质和用途纯镍是一种金属元素,化学符号为Ni,原子序数为28。
它是一种银白色的有光泽的金属,具有良好的延展性和韧性。
纯镍具有很高的熔点和沸点,熔点为1455°C,沸点为2913°C。
它的电导率和热导率都很高,是一种良好的导电和导热材料。
纯镍在工业上有广泛的应用。
由于其良好的耐腐蚀性能,纯镍常用于制作化学反应器、催化剂和电池等。
此外,纯镍还广泛应用于航空航天、电子、化工等领域,如制造飞机发动机、燃料电池和电子器件等。
3. 纯镍的密度与实验测量为了确定纯镍的密度,可以通过实验测量来获得准确的数值。
下面介绍一种常用的实验方法:浮法测量。
浮法测量是一种间接测量密度的方法,利用物体在液体中的浮力来推断其密度。
具体操作步骤如下:1.准备一个容器,装满足够的液体(如水)。
2.在容器中放入一个称量精确的容器(如烧杯),并记录容器的质量。
3.将纯镍样品放入容器中,记录容器和纯镍样品的总质量。
4.观察纯镍样品在液体中的浮沉情况,如果纯镍样品浮在液体表面,则需要适当调整液体的体积。
5.当纯镍样品浮在液体中时,记录容器和液体的总质量。
6.根据浮力原理,可以计算出纯镍样品的密度。
4. 纯镍的密度数值根据实验测量,纯镍的密度约为8.9 g/cm³。
这是一个平均值,实际的密度值可能会有一定的误差。
可以通过多次实验测量来提高测量结果的准确性。
5. 纯镍密度的影响因素纯镍的密度受到一些因素的影响,下面介绍几个主要因素:5.1 温度温度是影响物质密度的重要因素之一。
一般情况下,随着温度的升高,物质的密度会减小。
对于纯镍来说,随着温度的升高,其原子的热振动增强,导致原子间的平均距离增大,从而使密度降低。
5.2 合金成分纯镍是一种纯净的金属,但在实际应用中,常常与其他金属元素形成合金。
镍元素的符号

镍元素的符号1. 镍元素的基本信息镍(Nickel)是一种化学元素,原子序数为28,化学符号为Ni。
它是一种过渡金属,位于第4周期和8族元素。
镍元素的原子质量为58.6934,密度为8.908g/cm³,熔点为1455°C,沸点为2913°C。
镍是一种银白色的金属,具有良好的延展性和可塑性。
2. 镍元素的发现历史镍元素于1751年被瑞典化学家Axel Fredrik Cronstedt发现。
当时,Cronstedt从一种含有镍的矿石中分离出了一种新的金属。
他将这种金属命名为“nickel”,这个词来自于德语“Kupfernickel”,意为“小恶魔的铜”。
这是因为当时人们发现从这种矿石中提取金属时,会产生有毒的气味,导致工人们生病甚至死亡。
3. 镍元素的性质和用途3.1 物理性质镍是一种延展性和可塑性很好的金属,具有良好的导电和导热性能。
它的熔点较高,可以在高温下保持较好的强度和稳定性。
镍还具有较高的磁导率和磁饱和磁感应强度,因此被广泛应用于制造磁性材料和电子元器件。
3.2 化学性质镍在常温下相对稳定,不易与空气中的氧气反应。
然而,在高温下,镍会与氧气反应生成镍的氧化物。
镍还容易与硫、磷等非金属元素形成化合物。
此外,镍具有良好的耐腐蚀性,可以抵御大部分酸、碱和盐的侵蚀。
3.3 应用领域镍是一种重要的工业金属,广泛用于各个领域。
以下是镍的主要应用领域:•镍铁合金:镍铁合金是一种重要的磁性材料,常用于制造电动机、发电机、变压器等电子设备。
镍铁合金还具有高温强度和耐腐蚀性,被广泛应用于航空航天、化工等领域。
•不锈钢:镍是不锈钢中的重要合金元素,可以提高不锈钢的耐腐蚀性和机械性能。
不锈钢广泛应用于建筑、汽车、厨具等领域。
•电池材料:镍在电池材料中具有重要作用。
镍氢电池和镍镉电池是目前常用的可充电电池,它们具有高能量密度和长寿命。
•化学催化剂:镍在化学反应中具有催化作用,被广泛应用于化学工业中的催化剂制备。
ni原子半径

ni原子半径镍是一种重要的金属元素,具有良好的机械性能、耐腐蚀性和高温强度。
它广泛应用于电子、航空、航天、化工、医药等领域。
了解镍的基本性质对于研究它的应用具有重要意义。
其中,镍原子半径是一个重要的物理量,本文将对其进行介绍。
镍的基本性质镍是一种银白色的金属,密度为8.9克/立方厘米,熔点为1455℃,沸点为2730℃。
它是一种贵金属,价格较高,但是比银、金等贵金属便宜。
镍的化学性质比较稳定,不易被氧化,但是在强酸和强碱条件下会腐蚀。
它具有良好的磁性,是铁、钴、镍三种元素中唯一具有磁性的非铁磁金属。
镍的结构和原子半径镍的原子序数为28,它的原子结构为1s 2s 2p 3s 3p 3d 4s。
镍原子的中心是原子核,由28个质子和中子组成。
电子以能级的形式绕着原子核运动,外层电子的运动轨道是由四个量子数来描述的。
其中,主量子数n表示电子所处的能级,角量子数l表示电子的轨道形状,磁量子数m表示电子的运动方向,自旋量子数s表示电子自转方向。
镍原子的半径是指从原子核到最外层电子轨道的距离。
镍原子的半径为149皮米,与铁、钴的原子半径相近,说明它们的物理性质具有相似性。
镍原子的半径受到原子核电荷数、外层电子数量和能级等因素的影响。
一般来说,原子核电荷数越大,原子半径越小;外层电子数量越多,原子半径越大;能级越高,原子半径越大。
镍的应用镍是一种重要的金属元素,广泛应用于电子、航空、航天、化工、医药等领域。
其中,电子领域是镍的主要应用领域。
镍可以作为电子元器件的材料,例如电容器、电感等。
镍还可以作为电池的材料,例如镍镉电池、镍氢电池等。
此外,镍还可以作为催化剂的材料,例如合成氨、加氢裂化等化学反应中需要使用的催化剂。
结论镍原子半径是一个重要的物理量,它可以反映出镍的基本性质。
了解镍的原子半径可以帮助我们更好地理解它的物理性质,并在应用中更好地利用它的优势。
镍是一种重要的金属元素,具有广泛的应用领域,在未来的发展中将会发挥更加重要的作用。
- 1、下载文档前请自行甄别文档内容的完整性,平台不提供额外的编辑、内容补充、找答案等附加服务。
- 2、"仅部分预览"的文档,不可在线预览部分如存在完整性等问题,可反馈申请退款(可完整预览的文档不适用该条件!)。
- 3、如文档侵犯您的权益,请联系客服反馈,我们会尽快为您处理(人工客服工作时间:9:00-18:30)。
课程设计说明书题目名称: 10万吨镍冶炼厂工艺流程系部:机械工程系专业班级:冶金技术12-1班学生姓名:周进学号:2012232076指导教师:赵宝平完成日期:2014.6.27新疆工程学院课程设计评定意见设计题目10万吨镍冶炼厂工艺流程系部___机械工程系__ 专业班级冶金技术12-1班学生姓名____周进_______ 学生学号2012232076 评定意见:评定成绩:指导教师(签名):2014年6月27日新疆工程学院机械工程系(部)课程设计任务书2013—2014学年2 学期2014年 6 月20 日专业冶金技术班级12-1 课程名称重金属冶金设计设计题目10万吨镍冶炼厂工艺流程指导教师赵宝平起止时间2014.06.22~2014.06.29周数1周设计地点学校设计目的:1、通过课程设计能让学生系统的了解有色金属冶金原理、设备选型、工艺流程,培养学生发现问题,解决问题的能力,满足工程应用型人才培养需求。
2、设计过程中,培养了学生查找、甄别、运用相关资料的能力。
3、提高学生的运算能力,以及阅读图纸和绘制图纸的能力。
设计任务:1、完成整个相关金属冶炼工艺的介绍。
2、完成配料计算。
3、完成物料平衡计算。
4、设计进度与要求:2014.06.22~2014.06.23 研究任务书,查阅相关资料,提出设计构思和方案;2014.06.24~2014.06.26 指导老师讲解设计和计算方法;2014.06.27~2014.06.28 完成设计和计算,期间指导老师答疑问题;2014.06.29~2014.06.29 答辩。
主要参考书及参考资料:刘秉义.《有色金属工业设计总设计师手册》第一版(第二册).北京:冶金工业出版社1989.8张健.《重有色金属冶炼设计手册》第一版.北京:冶金工业出版社.1996.5 教研室主任(签名)系(部)主任(签名)目录摘要: (1)第二章镍的综述 (2)2.1镍的性质,用途: (2)2.1.1镍的性质 (2)2.1.2镍的用途: (2)2.1.3不锈钢中镍的作用及需求 (2)2.2硫化镍矿的分类和冶炼方法 (2)2.2.1硫化镍矿的分类 (2)2.2.2硫化镍精矿的火法冶炼 (3)2.2.3 镍硫的吹炼 (4)2.2.4 高镍硫缓冷工序的目的 (4)2.3 硫化镍的电解精炼 (5)2.3.1 工艺原理 (6)2.3.2 羰化反应时各元素的行为 (6)2.3.3羰基法生产镍的实践 (6)2.4 硫化镍精矿的湿法冶炼 (7)2.4.1 硫化镍精矿的加压氧氨浸出 (7)2.4.2 硫化镍精矿的硫酸化焙烧-浸出法: (8)2.5 氧化镍矿(红土矿)的湿法浸出: (8)2.5.1 红土矿的还原-氨浸 (8)2.5.2 红土矿的热压酸浸: (9)第三章镍火法冶炼电炉熔炼 (9)3.1设计的冶炼方法 (9)3.2 物料的熔化 (9)3.3 熔炼反应及产物 (11)3.3.1熔炼反应 (11)3.3.2熔炼产物 (11)第四章镍冶炼的冶金计算 (14)4.1硫化铜镍精矿流态化焙烧冶金计算 (14)4.1.1 精矿物相组成计算 (14)4.1.2 焙烧矿产量及脱硫率计算 (15)4.1.3焙烧矿物相组成计算 (16)4.1.4 焙烧反应及物料量 (17)摘要:目前,由于不锈钢产业的迅猛发展,全球对金属镍的需求不断增加,然而硫化镍矿资源日益匮乏,使得镍产量的扩大将主要来源于红土镍矿。
红土镍矿大致分为铁含量高的褐铁矿型和腐植土型两类,前者镍含量较低,宜采用高压酸浸湿法冶金工艺处理,而对于镍含量较高的腐植土型红土镍矿,电炉还原熔炼是其主流工艺。
采用电炉还原熔炼工艺从红土镍矿中提取用于制造不锈钢的镍铁合金,研究了还原剂(焦粉)用量、熔剂(石灰石)用量、熔炼温度和熔炼时间对合金中镍的品位和金属回收率的影响在自然界中,镍主要以硫化镍矿和氧化镍矿状态存在。
由于元素亲氧及亲硫性的差异,在熔融岩浆中,当有硫元素存在时,镍能优先形成硫化矿物,并富集形成硫化物矿床。
硫化镍矿如镍黄铁矿、紫硫镍铁矿中的镍以游离硫化镍形态存在,有相当一部分以类质同象赋存于磁黄铁矿中。
部分氧化镍矿是由硫化镍矿岩体风化浸淋蚀变富集而成,镍主要以镍褐铁矿(很少结晶或不结晶的氧化铁)形式存在。
红土镍矿是含镁铁硅酸盐矿物的超基性岩经长期风化产生的矿石,在风化过程中,镍自上层浸出,而后在下层沉淀,NiO取代了相应硅酸盐和氧化铁矿物晶格中的MgO和FeO。
第二章镍的综述2.1镍的性质,用途:2.1.1镍的性质镍是一种银白色的铁磁性金属。
镍的熔1453±1℃,沸点约2800℃。
比重为8.9g/cm3。
具有良好的导电导热性。
具有良好的延展性,可制成很薄的镍片(厚度小于0.02mm)。
镍能与许多金属组成合金,这些合金包括耐高温合金、不锈钢、结构钢、磁性合金和有色金属合金等。
化学性质:镍能抗氧锈蚀,因为其表面生成致密薄膜,能阻止进一步氧化。
也能抗强碱腐蚀,它在稀盐酸和硫酸中溶解很慢,但稀硝酸能与之作用。
镍与氧生成三种化合物,即氧化亚镍(NiO),四氧化三镍(Ni3O4)和三氧化二镍(Ni2O3),只有NiO 在高温下稳定;镍与硫生成四种化合物,即NiS2, Ni6S5,Ni3S2和NiS,在冶炼高下只有Ni3S2稳定。
冶金上最有意义的是镍与CO生成的羰基镍Ni(CO)4,它是挥发性化合物,沸点为43℃,分解温度为180℃。
2.1.2镍的用途:(1)作金属材料。
镍具有良好的机械强度和延展性,难熔耐高温,并能在表面形成致密的氧化镍膜,因此具有很高的化学稳定性,是一种十分重要的有色金属原料,被用来制造包括不锈钢、耐热合金钢、合金结构钢等3000多种合金,广泛用于飞机、雷达、导弹、坦克、舰艇、宇宙飞船、原子反应堆等领域。
(2)用作镀镍,主要是在钢材及其他金属材料的基体上覆盖一层耐用、耐腐蚀的表面层,其防腐蚀性要比镀锌层高20~25%。
(3)用作催化剂,应用于石油化工的氢化等过程。
(4)用作化学电源,如工业上已生产的Cd-Ni、Fe-Ni、Zn-Ni等电池和H2-Ni 密封电池。
这类电池充电性能好,理论比能量较高,价格较便宜。
(5)制作颜料和染料,其最重要的是制作一种以钛酸镍为主要组分的黄橙色颜料,该颜料覆盖能力强,不易被其他颜料污染且化学性能稳定。
(6)镍钴合金是一种永磁材料,广泛用于电子遥控、原子能工业等领域。
2.1.3不锈钢中镍的作用及需求镍对钢的性能有良好的影响,钢中加入镍后,强度显著提高。
镍在不锈钢中的主要作用在于它改变了钢的晶体结构——从体心立方(BCC)结构(铁氧体)转变为面心立方(FCC)结构(奥氏体),从而改善不锈钢的主要性能:可成形性、焊接性、韧性、耐腐蚀性、光泽和高温性能等,因此镍被称为奥氏体形成元素,成为不锈钢中必不可少的添加元素2.2硫化镍矿的分类和冶炼方法2.2.1硫化镍矿的分类硫化镍矿约占20%,主要为镍黄铁矿和镍磁黄铁矿。
含有铜、钴和铂族元素。
硫化矿为主要炼镍原料,矿石品位为0.3%~1.5%,冶炼前需经选将品位提高到4%~8%。
氧化矿占80%,分两类,一类是高硅镁质的镍矿,包括硅酸镁镍矿和暗蛇纹石( NiSO3.mMgSiO3.nH2O);另一类为红土矿是镍(含量1%)铁(含量40%~50%)氧化物组成的共矿。
氧化镍矿难选,故它目前占镍产量比重不大(只有40%),但氧化矿占镍储藏量大,特别是红土矿(占氧化矿的80%),因此它是未来镍的主要来源。
镍的生产方法分为火法和湿法。
2.2.2硫化镍精矿的火法冶炼占硫化矿提镍的86%,其处理方法是先进行造锍熔炼制取低镍硫,然后再送转炉对低镍硫进行吹炼产出高镍硫;经缓冷后进行破碎、磨细;通过浮选、磁选产出高品位硫化镍精矿、硫化铜精矿和铜镍合金。
类似于火法炼铜工艺。
生产熔炼(1)鼓风炉熔炼:鼓风炉熔炼是最早的炼镍方法,我国在20世纪60~70年代主要采用此方法,目前随着生产规模的扩大,冶炼技术的进步以及环保要求,此法已逐步被淘汰。
(2)电炉熔炼:主要用于低镍锍的生产,我国的金川公司也用矿热电炉处理硫化镍精矿。
(3)闪速熔炼:我国熔炼硫化镍精矿生产低镍锍的主要方法。
生产工艺包括精矿的深度干燥、配料、闪速熔炼、转炉吹炼和炉渣贫化等过程。
2.2.2.1 闪速熔炼原理镍闪速熔炼与铜的闪速熔炼基本相同,闪速冶炼工厂将闪速炉与炉渣贫化炉合为一体,反应塔尺寸(直径×高)为ф600×6400mm、沉淀池面积为98m2。
2.2.2.2 闪速熔炼产物闪速熔炼的产物为铜镍锍和炉渣。
(1)铜镍锍铜锍镍主要由Ni3S2、Cu2S和FeS组成,含少量钴的硫化物、游离金属和铂族元素。
铜镍硫的性质与铜锍大致相同,Ni+Cu的总含量为45%~50%。
(2)炉渣炼镍炉渣中含FeO、CaO、SiO2和大量MgO,熔点为1473K。
2.2.2.3 镍闪速熔炼的技术指标镍闪速熔炼的主要指标为:(1)精矿处理量50t/h。
(2)反应塔耗油量1733kg/h,沉淀池耗油1400kg/h。
(3)主要金属回收率为:Ni97.16%,Cu98.48 % ,Co65.46 %,硫回收率高于95%。
2.2.3 镍硫的吹炼镍锍的吹炼是使其中的FeS 氧化造渣,除去铁和部分硫,产出主要与Ni2S2和Cu2S组成并富集了贵金属的高镍锍。
一般高镍锍含Ni+Cu的总和为70%~75%,含硫为18%~24%。
镍锍吹炼原理镍锍吹炼只有造渣过程:2Fe+O2+SiO2=2FeO.SiO22FeS+3O2+SiO2=2FeO.SiO2+2SO2吹炼直到产出高镍锍为止,而没有造金属过程,因为反应:Ni3S2+4NiO=7Ni+2SO2要在1773K高温才能进行,而空气吹炼温度为1623K。
2.2.4 高镍硫缓冷工序的目的高镍锍的缓冷是将转炉产出的高镍锍熔体注入8~20t的保温模内,缓冷72h,以使其中的铜锍化物和镍锍化物和铜镍合金相分别结晶,有利于下一步相互分离。
2.2.4.1 高镍硫缓冷过程的降温秩序(1)温度在1200K以上时,锍镍中的各组分完全混熔。
温度降到1200K以下时,Cu2S开始结晶,温度越低,液相中Cu2S析出的越多,缓冷使Cu2S趋向于生成粗粒晶体。
(2)熔体降温到约973K时,金属相铜、镍合金开始结晶。
(3)当温度降到848K时,Ni3S2开始结晶。
同时液态熔体完全冷固。
该温度点为铜、镍、硫三元共晶液相的共晶点。
此时,镍在Cu2S中含量<0.5%,铜在Ni3S2中含量约6%。
(4)固体温度降到793K时,Ni3S2完成结构转化,由高温的β型转化为低温的β′型。
析出部分Cu2S和Cu-Ni合金,铜在β′基体中的含量下降为2.5%,793K 也是三元系共晶点。
(5)温度继续下降,Ni3S2相中不断析出Cu2S和Cu-Ni合金相,直至644K为止。