以技术改造方式实现节能减排降本增效
燃气降本增效实施方案

燃气降本增效实施方案随着经济的快速发展和城市化进程的加快,燃气作为一种清洁、高效的能源,已经成为人们生活和生产中不可或缺的重要组成部分。
然而,燃气资源的有限和价格的不断上涨,给企业和个人的生产和生活带来了很大的压力。
因此,如何降低燃气成本,提高资源利用效率,成为当前亟待解决的问题。
一、技术改造升级。
首先,我们应该加大对燃气设备的技术改造和升级力度。
通过引进先进的燃气设备和技术,提高燃气的利用效率,降低生产成本。
比如,对燃气锅炉进行智能化改造,通过控制系统实现燃气的精准供应,避免能源浪费。
同时,对燃气管道进行检修和维护,消除漏气隐患,确保燃气的安全使用。
二、节能减排。
其次,我们要积极开展节能减排工作。
通过加强对燃气的节能利用,提高能源利用效率,减少能源浪费。
比如,推广燃气热电联产技术,将余热利用到发电中,提高能源利用率。
同时,加强燃气燃烧技术的研究和应用,减少燃气的排放,保护环境。
三、管理优化。
此外,我们还要加强燃气管理的优化。
通过建立科学的燃气管理体系,加强对燃气的监控和调度,提高资源利用效率。
比如,建立燃气使用台账,对燃气的使用情况进行统计和分析,找出能源浪费的原因,采取有效措施加以改进。
四、宣传教育。
最后,我们要加强对燃气降本增效实施方案的宣传教育。
通过开展各种形式的宣传活动,增强员工和居民对节能减排的认识和重视,形成人人参与的节能减排氛围,共同推动燃气降本增效工作的顺利实施。
总之,燃气降本增效实施方案是当前的迫切需要,只有通过技术改造升级、节能减排、管理优化和宣传教育等一系列措施的有机结合,才能有效降低燃气成本,提高资源利用效率,实现经济和社会的双赢。
希望通过我们的共同努力,能够为燃气降本增效工作贡献自己的一份力量。
节能创新降本增效心得体会

节能创新降本增效心得体会节能创新降本增效是企业在发展过程中必须重视的一个方面。
我在工作中也发现了一些关于节能创新降本增效的心得体会。
首先,节能创新降本增效可以为企业带来实际的经济利益。
通过引入新技术、新设备和新工艺,企业可以降低能源消耗和生产成本,从而提高企业的利润率。
例如,我们公司引进了一套新型的节能设备,通过优化能源利用效率,每年可以节约大量的电力消耗,从而减少用电成本,提高生产效率。
这样一来,企业在成本控制方面具有了明显的优势。
其次,节能创新降本增效还可以提升企业的竞争力。
随着全球经济的发展和竞争的加剧,企业要想在市场上立足,就必须具备一定的竞争力。
节能创新降本增效可以使企业的产品更具竞争力。
例如,我们公司在产品设计上注重节能环保,通过改进产品的结构和材料,使得产品更加节能高效,更加符合市场需求。
这样一来,我们的产品在市场上更具竞争力,能够满足消费者的需求,从而提高销售额和市场份额。
此外,节能创新降本增效还可以推动企业的可持续发展。
在全球气候变化日益严峻的背景下,节能减排已经成为了一种社会责任。
企业要想实现可持续发展,就必须致力于降低能源消耗和减少环境污染。
通过节能创新降本增效,企业可以从根本上改变传统高耗能、高污染的生产模式,采用低碳环保的生产方式。
例如,我们公司重视节能减排,将旧设备替换为节能型设备,改进生产工艺,通过节能减排的措施,既降低了生产成本,也减少了对环境的影响,实现了企业的可持续发展。
最后,我认为,节能创新降本增效是一项需要长期投入和持续改进的工作。
节能创新降本增效需要企业不断推陈出新,不断引进先进的技术和理念。
只有不断跟上时代的步伐,才能在激烈的市场竞争中立于不败之地。
同时,节能创新降本增效也需要全体员工的共同努力和参与。
只有全员参与,才能够形成一种节能降本增效的企业文化,使得节能创新成为企业的一种习惯和自觉行为。
综上所述,节能创新降本增效对于企业的发展具有重要意义。
通过节能创新降本增效,企业可以实现经济效益、提升竞争力、推动可持续发展,并且需要长期投入和全体员工的共同努力。
安全生产,绿色环保,节能减排,技术创新,降本增效,工匠精神的

安全生产,绿色环保,节能减排,技术创新,降本增效,工匠精神的节约能源、提高能源利用率,既是保障企业正常生产经营,实现企业健康可持续发展的长久之计,也是企业适应市场需要、降低成本、增加效益、改善环境,提高企业竞争力的必然选择。
每为公司节能降耗一分,也就是为公司增效一分。
为进一步增强公司职工的节能降耗意识,营造良好的企业氛围,公司工会办公室特向全体职工发出节能降耗的倡议,具体要求如下:一、做宣传节能减排的标兵牢固树立生态文明观和节能环保理念,不断增强节能减排的紧迫感和责任感,不断增强能源忧患意识和节约环保意识,积极倡导绿色办公和低碳生活,争做宣传节能减排的标兵,踊跃投身节能减排宣传活动。
同时,学习掌握节能减排知识与技能,广泛宣传节能环保政策法规,普及节能知识和方法,努力营造节能减排的浓厚氛围,带动全厂共同形成节能减排的新风尚。
二、做践行节能减排的楷模提倡简约的生活和工作习惯,减少生活和办公资源消耗,从节约每一度电、每一滴水、每一张纸、每一粒米的点滴小事做起,不铺张,不浪费,做自觉践行节能减排的楷模。
1、养成离开办公室及其他公共场所时随手关灯、关空调、关电脑的良好习惯,杜绝“长明灯〞现象;计算机、打印机、复印机等办公设备在不使用时及时关机,减少待机能耗。
2、办公室充分利用自然光和自然通风,不开或少开空调和照明灯。
会议室、办公室(家庭)做到空调在夏季室温达到26℃冬季低于0℃时开启;不得在室内空调开启情况下,随意开窗;下班前务必检查办公室所有电器,确保关闭后方可离开。
3、开展节水行动,随时关闭水龙头,做到人离水断,衣物集中洗涤,减少洗衣次数,洗涤剂要适星投放,避免过量用水。
4、节约用纸,减少使用一次性文具,积极推广“无纸办公”,提倡双面使用打印纸。
5、树立资源循环利用的意识,争取做到“一物多用〞。
逛街时带上购物袋,少用塑料袋,减少一次性用品(如纸巾、纸杯、筷子、方便碗等)的便用。
6、养成健康科学的饮食习惯,树立节俭文明的生活消费理念,节约粮食,反对浪费,提倡适度消费,不超前消费。
降本增效节能减排

降本增效节能减排随着全球环境和资源问题的日益突出,人们对于低碳生活、绿色环保的追求也变得越来越强烈。
在这种大环境下,企业也不得不面对节能减排、降本增效的重大课题。
降本增效节能减排,成为了中国企业近年来的一项重要工作。
本文将从以下几个方面进行探讨。
一、降本增效降本增效的目的是提高企业的效率和经济效益。
在实践中,通常采取以下措施:生产流程的优化、节约原材料、降低运营成本、提高员工素质等。
这些措施可以有效地提高生产效率、降低成本,增强企业的市场竞争力。
尤其对于当前国内外市场竞争激烈的环境来说,降低成本、提高生产效率是企业稳定发展的必要条件。
二、节能减排节能减排是企业社会责任的内在要求。
节能减排不仅能够降低污染,减少环境的破坏,而且还能够节约能源,减少能源的消耗。
尤其当前,国家规划将节能减排纳入国家发展的主要战略,各种政策性文件也对节能减排进行了明确的规定,这无疑对企业形成了巨大的压力。
而实践证明,节能减排可以从长远的角度来看,为企业发展和社会发展提供更加可持续的支持。
三、降本增效与节能减排的关系降本增效和节能减排的关系密不可分。
从另一个角度来看,两者的实现手段和目的是一致的,都是实现可持续发展的具体方式之一。
例如,企业优化生产流程、提高员工素质等可以加强内部管理水平,进而提高生产效率,降低成本;而购买节能型设备、优化能源结构等可以在实际生产过程中,降低用能成本,提高用能效率,从而减少能源消耗、节约能源、降低排放,达到节能减排的目的。
因此,降本增效与节能减排在实践中是相辅相成的。
四、降本增效节能减排的实践案例作为不同行业不同规模的企业,降本增效节能减排的实践案例是多种多样的。
例如:1. 无锡一家机械工程公司,在进行企业改革时,通过引进先进的工业设计软件,优化了生产流程,降低了成本,提高了产品性能,达到了降本增效的目的。
2. 厦门一家化工企业,通过淘汰老旧设备,购买节能型设备,优化能源结构,减少原材料消耗和废水排放,从而实现了节能减排和降本增效的目的。
建筑施工节能减排降本增效方案

建筑施工节能减排降本增效方案在当今社会,建筑行业作为能源消耗和环境污染的大户,面临着巨大的节能减排压力。
同时,随着市场竞争的加剧,降本增效也成为建筑企业提升竞争力的关键。
为实现建筑施工过程中的节能减排和降本增效,制定一套科学合理的方案势在必行。
一、节能减排措施1、能源管理与优化(1)建立详细的能源消耗监测系统,对施工现场的电、水、气等能源进行实时监测和记录,以便及时发现能源浪费的环节。
(2)合理规划施工设备的使用时间和功率,避免设备空转和过度运行。
例如,根据施工进度和工作量,合理安排塔吊、搅拌机等大型设备的运行时间。
2、采用节能型设备和技术(1)在设备采购时,优先选择节能型的施工设备,如节能型塔吊、电焊机等。
这些设备在运行过程中能够有效降低能源消耗。
(2)推广使用新型节能技术,如太阳能照明、空气能热水器等,在满足施工需求的同时减少对传统能源的依赖。
3、优化施工工艺(1)通过优化施工流程和工艺,减少不必要的能源消耗。
例如,在混凝土浇筑过程中,采用合理的浇筑顺序和振捣方法,既能保证施工质量,又能降低能源消耗。
(2)采用预制构件和装配式施工方法,减少现场作业量,降低施工过程中的能源消耗和废弃物产生。
4、加强施工现场管理(1)制定严格的能源管理制度,对施工人员进行节能培训,提高其节能意识,使其在工作中养成良好的节能习惯。
(2)加强对施工现场的巡查,及时发现和纠正能源浪费行为,对节能表现优秀的班组和个人进行奖励,激励全体施工人员积极参与节能工作。
二、降本增效措施1、成本预算与控制(1)在项目开工前,进行详细的成本预算,包括人工、材料、设备租赁、管理费等各项费用,明确成本控制目标。
(2)建立成本监控机制,定期对项目成本进行核算和分析,及时发现成本超支的原因,并采取相应的控制措施。
2、材料管理与优化(1)加强材料采购管理,通过集中采购、招标采购等方式,降低材料采购成本。
同时,选择质量可靠、价格合理的材料供应商,建立长期稳定的合作关系。
技术降本增效的方法和措施

技术降本增效的方法和措施技术降本增效的方法和措施正文如下:一、引言随着科技的快速发展,企业对降低成本、提高效率的需求日益迫切。
技术降本增效已成为企业提升竞争力的重要手段。
本文将详细介绍技术降本增效的方法和措施。
二、技术降本增效的方法1. 自动化生产自动化生产是降低人力成本、提高生产效率的有效途径。
通过引入自动化设备和智能化技术,实现生产过程的自动化控制,减少人工操作环节,提高生产效率和产品质量。
2. 信息化管理信息化管理可以提高企业运营效率和决策水平。
通过建立信息化平台,实现信息共享、数据分析和业务协同,提高企业内部管理效率和外部市场竞争力。
3. 节能减排技术采用先进的节能减排技术,可以降低企业能源消耗和环境污染,从而降低生产成本,提高经济效益。
4. 研发创新加强研发创新,推动技术进步,是降低生产成本、提高产品质量的重要途径。
企业应加大研发投入,研发新产品、新工艺、新技术,提高生产效率和产品质量。
三、技术降本增效的措施1. 制定科学的降本目标企业应结合实际情况,制定科学的降本目标。
目标要明确、具体、可行,并分解为短期和长期目标,逐步实施。
2. 建立成本管理体系建立成本管理体系,实现成本管理的科学化、规范化、精细化。
通过成本核算、成本分析、成本控制等环节,降低生产成本,提高经济效益。
3. 加强员工培训和学习提高员工技能和素质,是企业提高生产效率和质量的关键。
企业应加强对员工的培训和学习,提高员工技能和素质,使员工更好地适应自动化生产和信息化管理的需求。
4. 建立激励机制和考核制度建立合理的激励机制和考核制度,激发员工降本增效的积极性和创造力。
通过奖励先进、考核绩效等方式,引导员工关注成本、提高效率。
四、技术与管理的结合技术降本增效需要技术与管理的紧密结合。
企业应注重技术创新和管理创新的协同发展,将先进的技术和管理理念引入到企业的日常运营中,实现技术与管理的深度融合。
五、总结技术降本增效是企业提升竞争力的重要手段。
工程项目降本增效的60项技术措施
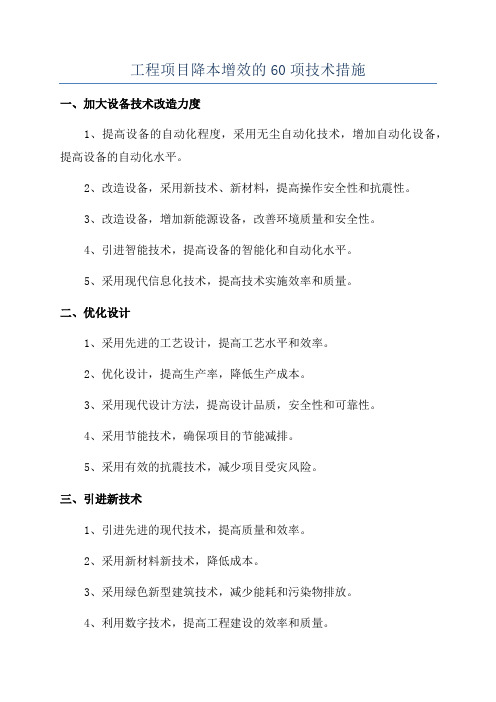
工程项目降本增效的60项技术措施
一、加大设备技术改造力度
1、提高设备的自动化程度,采用无尘自动化技术,增加自动化设备,提高设备的自动化水平。
2、改造设备,采用新技术、新材料,提高操作安全性和抗震性。
3、改造设备,增加新能源设备,改善环境质量和安全性。
4、引进智能技术,提高设备的智能化和自动化水平。
5、采用现代信息化技术,提高技术实施效率和质量。
二、优化设计
1、采用先进的工艺设计,提高工艺水平和效率。
2、优化设计,提高生产率,降低生产成本。
3、采用现代设计方法,提高设计品质,安全性和可靠性。
4、采用节能技术,确保项目的节能减排。
5、采用有效的抗震技术,减少项目受灾风险。
三、引进新技术
1、引进先进的现代技术,提高质量和效率。
2、采用新材料新技术,降低成本。
3、采用绿色新型建筑技术,减少能耗和污染物排放。
4、利用数字技术,提高工程建设的效率和质量。
5、采用智能化控制技术,提高自动化水平。
四、优化工艺流程
1、优化工艺流程,提高生产效率,同时降低成本。
2、采用多元化生产技术,实现工艺品质和质量控制。
3、灵活的工艺设计。
公司节能降耗工作总结

公司节能降耗工作总结公司节能降耗工作总结1,毛巾二公司围绕企业降本增效战略,以“节能降耗”为抓手,组织员工深入开展“查跑冒滴漏、比节能创新、看节约贡献”活动,引导员工围绕节能降耗进行工艺、技术、设备的创新和改进,大力钻研资源节约、资源循环利用技术,积极开展“五小”及合理化建议活动。
在各级公司领导的支持、关心和帮助下,节能降耗工作不断进步,取得了一定的成绩,现总结如下:一、引进先进设备,实现技术创新1、染整车间2月份安装了2台第斯溢流机,该机载重400公斤,具有使用低浴比(浴比1:6),染色效率高,操作方便等优点,节能效果好,具体如下:立信第斯值(元)合计深色645元,浅色607元水(吨)深色11059浅色7940166电(千蒸汽(吨)其他瓦)4109前处理助剂节约15%,染色助剂节约40%,染化料节约3%。
290(估算)6.363378节约价204同时,由于该机具有高温排放功能和预备附缸,因此缩短了排水时间和主机升温时间,染深色产品仅需用7.2小时,浅色用4.6小时,效率相比立信提高了40%以上。
按照上半年第斯溢流机干400吨产品计算,可节约费用24万余元。
2、毛巾二公司年底新上节能项目漂染车间废水余热回收工程,通过安装相关热交换设备,可使用21C的冷水温度平均升高20度以上,可节约大量蒸汽。
从漂染车间使用情况来看,每天可以大约200吨热水,节约蒸汽约40吨,上半年漂染车间余热回收装置可节约费用约63万元。
3、织造三车间于5月份引进安装了潍坊瑞斯照明节电装置,经测算,节电率可达20%以上,每天可节电300度,月可节约4500度电,上半年可节约费用约4000元。
二、大胆工艺改进,实现溢流机小浴比染色立信溢流机1:8浴比改造。
立信溢流机原先采用1:10浴比,我们联系立信公司,将高温高压系列机型降低最低水位控制,改进工艺,采用1:8浴比,6月初已经将加软、增白、水洗工艺实验成功,目前,除染色步骤外,其余步骤均采用小浴比,现在已经在车间内全部推广使用,仅此一项,溢流染色所用的水电汽消耗就可降低18%。
降本增效的十条办法

降本增效的十条办法以《降本增效的十条办法》为标题,面对日趋激烈的市场竞争,很多企业都需要在有限的投入促进收益及资源的有效利用,即要做到“降本增效”。
本文将介绍降本增效的十条办法,以促进企业健康、持续发展。
首先,强化技术改造。
技术改造是企业节约成本的首要措施,可使企业的生产技术水平得到极大的提高,从而节约资源,提高生产效率。
因此,企业需要积极引进先进技术,应用最新的管理模式,进行有效的技术改造,发挥节约资源、提高生产效率的效果。
其次,把握项目投资比例。
企业要在投资项目时要把握好投资比例,尽可能将投资收益最大化,避免资金过多或过少的分配。
这样可以节约资金,充分调动投资活力,并可更充分的将资源分配到能够实现最大效益的领域。
第三,科学管理。
企业要按照科学的管理原则,完善内部机构,强化知识管理,降低管理层次,建立起科学、高效、符合国际标准的管理模式。
这样可以使企业更有效、高效地把握市场信息,实现降本增效。
第四,重视生产节约。
促进节约生产是企业节约成本的重要措施,因此,企业应该深入分析生产活动中的资源消耗,采取灵活的措施,积极采取节约的技术手段,如减少损耗、提高利用率,有效控制生产成本,从而实现降本增效。
第五,加强市场营销工作。
市场营销是企业重要的获利措施,它可以增加企业的销售额,提高营业利润率。
因此,企业要重视市场营销工作,积极开发新市场,利用营销的手段拓展市场,在提高产品的销售量的同时,有效降低产品的成本,实现降本增效的目的。
第六,加强人力资源管理。
企业要按照需求在招聘人员时做准备,以保证企业的生产力得到充分发挥,从而使企业在做出以最少的投入,获得最大的收益。
同时,企业还要采取激励机制,对贡献突出的员工给予奖励,以激发员工的工作热情。
第七,控制物资成本。
物资成本控制是企业节约成本的重要方法,企业要积极开发供应商,建立供应关系,降低采购运输成本,控制原材料消耗,实现节约物资成本。
第八,完善财务管理。
财务管理是企业节约成本的重要环节,企业要建立合理的财务制度,做好日常财务管理,提高财务活动的效率,节约财务成本,实现降本增效。
电力成套企业降本增效措施方案范文

电力成套企业降本增效措施方案范文一、引言在当前市场竞争日益激烈的环境下,电力成套企业面临着巨大的经营压力。
为了保持企业的竞争力,实现可持续发展,降本增效成为企业亟待解决的问题。
本方案旨在通过一系列措施,降低企业成本,提高生产效率,从而实现降本增效的目标。
二、降低成本措施1.优化采购管理采购成本是企业成本的重要组成部分,优化采购管理是实现降本增效的关键环节。
企业可以通过以下措施降低采购成本:(1)建立稳定的供应商合作关系:与信誉良好、价格合理的供应商建立长期合作关系,确保采购渠道的稳定性和价格优势。
(2)实行集中采购:通过集中采购,提高采购规模,降低单位产品的采购成本。
(3)加强库存管理:建立完善的库存管理制度,合理控制库存水平,避免库存积压和浪费。
2.提高生产效率提高生产效率是降低企业成本的有效途径。
企业可以通过以下措施提高生产效率:(1)引进先进设备和技术:投入资金引进先进的生产设备和技术,提高生产自动化水平,降低人工成本。
(2)优化生产流程:对生产流程进行全面梳理和优化,消除生产瓶颈,提高生产效率。
(3)加强员工培训:定期开展员工技能培训,提高员工操作水平和生产效率。
3.降低能源消耗电力成套企业作为能源消耗大户,降低能源消耗对于降本增效具有重要意义。
企业可以通过以下措施降低能源消耗:(1)提高设备能效:选用能效高的设备和材料,降低单位产品的能源消耗。
(2)实施节能技术改造:对现有设备进行节能技术改造,提高设备运行效率,降低能源消耗。
(3)加强能源管理:建立完善的能源管理制度,实时监测能源消耗情况,及时发现和解决能源浪费问题。
4.减少废品和损耗减少废品和损耗是降低企业成本的重要措施。
企业可以通过以下途径减少废品和损耗:(1)优化产品设计:从产品设计阶段开始考虑减少废品和损耗的可能性,提高产品的可制造性和可靠性。
(2)加强生产过程控制:对生产过程进行全面监控和管理,及时发现和处理可能导致废品和损耗的问题。
水泥企业降本增效措施

水泥企业降本增效措施在当前市场竞争激烈的情况下,水泥企业降低生产成本、提高生产效率是确保企业持续发展的关键。
为此,水泥企业可以采取以下措施来降本增效:一、技术改造和设备升级:1.引进高效节能的水泥生产设备,采用新一代的节能技术,如选用高效烧结炉、高效节能磨机等,减少能源消耗,提高生产效率。
2.优化生产工艺,采用新型原料和新增辅料,降低成本,提高产品质量。
3.引进自动化生产线,减少人工操作和人为失误,提高生产效率。
二、管理创新与生产管理优化:1.提高员工技能水平,加强员工培训,确保生产操作规范化、标准化。
2.优化供应链管理,建立合理的物流体系,降低运输成本和时间,提高配送效率。
3.优化生产计划和排产,减少停机时间,提高设备利用率。
4.强化质量管理,建立完善的质量控制体系,降低产品缺陷率,减少生产废品。
三、能源节约与环保措施:1.开展能源管理和节能改造工作,提高设备的能源利用率,减少能源浪费。
2.优化燃烧工艺,合理选择燃料和燃烧方式,减少二氧化碳排放。
3.强化废气治理和粉尘控制,使用尾排技术、除尘装置等,改善生产环境,减少对环境的污染。
4.积极开展节能环保宣传和教育,提高员工的环保意识和自觉性。
四、市场营销创新与销售管理优化:1.加强产品研发和创新,开发新型水泥产品,满足市场需求,提高市场竞争力。
2.创新销售模式,扩大市场份额,提高销售额。
3.发展电商平台,拓宽销售渠道,提高销售效益。
4.加强品牌宣传和市场营销,提高产品的知名度和美誉度。
五、降低管理成本和财务管理优化:1.优化企业组织结构,减少中间管理层,降低管理成本。
2.引进先进的管理信息系统,实现信息共享和流程优化,提高管理效率。
3.健全财务管理制度,加强财务风险控制和成本控制,实现财务效益最大化。
总之,水泥企业降本增效是一项长期而艰巨的任务。
只有通过技术改造、管理创新、环保节能、市场营销创新和财务管理优化等一系列措施的综合应用,才能最大限度地减少生产成本,提高生产效率,实现企业的可持续发展。
60项技术措施助力工程项目降本增效

60项技术措施助力工程项目降本增效
技改可以说是工程建设项目的一种共同表现。
它既是改进工艺流程,
完善产品性能,提高劳动生产率,降低成本,提高竞争力,提高综合效益,促进社会和经济发展的重要手段,也是提高社会产出水平,满足市场需求,促进经济发展的必然选择。
现在,要实现工程项目降本增效,以下是60项技术措施:
1.优化结构设计,合理设计结构,减少材料耗用,缩小面积,降低
制造和安装成本。
2.开展合理技术审查,前期设计研究,减少不必要的设计,材料和
工序,使项目回报期更快,节省资金。
3.完善工艺流程,改进加工工艺,提高工艺生产率,降低生产成本,提高商品质量。
4.提高先进工艺装备水平,采用先进的设备和技术,减少职工劳动
强度,提高劳动生产率。
5.优化信息系统,采用现代信息技术,实现网络管理,提高工作效率,降低管理成本。
6.开展集成化施工,有效规避因项目工程量增加,施工周期耽误而
带来的高昂成本。
7.采用模块化施工,利用工厂生产环境,大批量生产,迅速汇总,
加速施工进度,降低投资成本。
8.施节能减排技改,改变原有方式。
建筑企业降本增效措施

建筑企业要实现降本增效,可以采取以下措施:
1. 优化项目管理:通过精细化管理,减少不必要的浪费,提高资源利用效率。
例如,采用项目管理软件来跟踪进度,确保项目按时按预算完成。
2. 采购管理优化:集中采购材料和设备以降低成本,同时确保质量。
与供应商建立长期合作关系,争取更优惠的价格和付款条件。
3. 节能减排:在施工过程中采用节能设备和技术,减少能源消耗。
同时,合理安排施工时间,避免高峰期用电。
4. 技术创新:采用新技术、新材料和新工艺,提高施工速度和质量,降低人工和材料成本。
5. 培训员工:提高员工技能和效率,减少错误和事故,降低返工和维修成本。
6. 精益施工:借鉴精益生产理念,消除施工过程中的浪费,比如过度加工、库存积压、不必要的运输等。
7. 质量控制:加强质量管理,减少缺陷和返修,提高客户满意度,避免因质量问题导致的额外成本。
8. 信息化建设:利用信息技术提高管理水平和决策效率,比如使用BIM(建筑信息模型)技术进行设计和施工管理。
9. 流程优化:简化和优化工作流程,减少不必要的步骤和环节,提高工作效率。
10. 供应链管理:优化供应链管理,确保材料供应及时且成本效益最优。
通过这些措施,建筑企业可以在保证工程质量的前提下,有效降低成本,提高市场竞争力。
广西联通开展“降本增效、节能减排”行动

两 级 专 项 工 作 机 构 。区公 司 各 部 门和 各 级 分 公 司 负
责 人根 据 公 司要 求 统 一 部 署 , 一 步 梳 理 了 区 Nhomakorabea市 两 进
是 在 网 间 结 算 支 出上 , 经 营 分 析 系统 建 立 在
机 制 , 化 目标 管 理 、 程 控 制 、 核 评 价 , 压 力 强 过 考 将
优 先 通 过 责 任 人 催 缴 话 费。 三 是 在营 业费 用上 , 强代 理 佣金 管控 , 行 加 实
层层传递 , 将责 任层层落 实 , 确保 可控 、 在控和 有效
实施 。
最 后 , 过 阶 段 性 总 结 , 时 发 现 问题 , 效 梳 通 及 有 理 成 果 , 进 “ 化 流 程 , 升 管 理 ” 良性 循 环 。 促 优 提 的 同 时 , 托 E P I系统 , 断 提 升 成 本 费 用 管王 信 依 R 和 T 不 里
增 效 , 高成 本 费 用 使 用 效 率 ; 理 成 本 、运 维 成 本 提 管 要 以 “ 本 ”为主 ,目标 是 实 现 资源 的合 理 匹 配 , 过 降 通 对用 户结 构 、 业务 结 构 、 入 结 构 、成 本 结 构 、 道 结 收 渠
构 、 员结 构 的调 整 , 高公 司精  ̄ ( 管理 水 平 。 人 提 - 8 1 1
组 进行 汇报 : 区公 司 降 本 增 效 办 公 室 建 立 工作 月 报
节 能 减 排 ”专 项 行 动 。广 西 联 通 按 照 活 动 的 部 署 要 求 , 准 七 大 目标 , 立 了深 化 管 理 、 进 资 源 协 同 瞄 建 促 的 工作 机 制 , 全 区1 个市 级 分 公 司 组 织 开 展 了此专 在 4
炼铁厂降本增效总结5篇
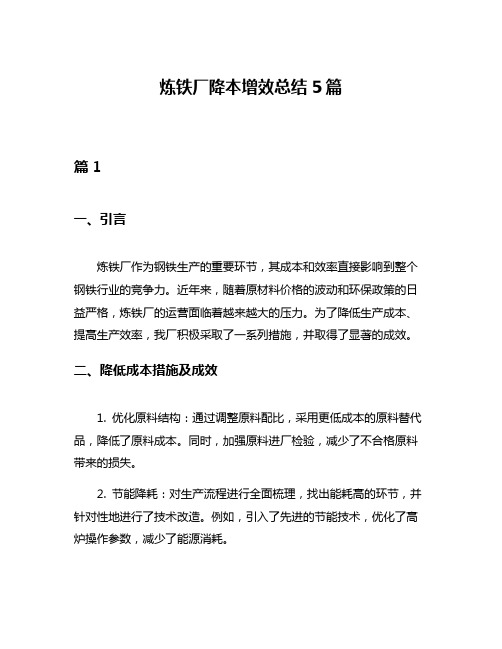
炼铁厂降本增效总结5篇篇1一、引言炼铁厂作为钢铁生产的重要环节,其成本和效率直接影响到整个钢铁行业的竞争力。
近年来,随着原材料价格的波动和环保政策的日益严格,炼铁厂的运营面临着越来越大的压力。
为了降低生产成本、提高生产效率,我厂积极采取了一系列措施,并取得了显著的成效。
二、降低成本措施及成效1. 优化原料结构:通过调整原料配比,采用更低成本的原料替代品,降低了原料成本。
同时,加强原料进厂检验,减少了不合格原料带来的损失。
2. 节能降耗:对生产流程进行全面梳理,找出能耗高的环节,并针对性地进行了技术改造。
例如,引入了先进的节能技术,优化了高炉操作参数,减少了能源消耗。
3. 降低维护成本:建立了完善的设备维护保养制度,加强了设备的日常巡检和维护,减少了设备故障率。
同时,采用了性价比较高的备件和材料,降低了维护成本。
4. 强化生产组织:通过优化生产流程,合理安排生产计划,减少了生产过程中的等待和浪费。
同时,加强了生产现场的管理,提高了生产人员的操作技能和效率。
三、提高效率措施及成效1. 引入自动化技术:对生产线进行了自动化改造,引入了先进的自动化控制系统和智能检测设备。
例如,高炉自动化控制系统的应用,提高了高炉操作的稳定性和效率。
2. 优化生产布局:根据生产需要和市场变化,对生产布局进行了优化调整,减少了生产环节的冗余和浪费。
同时,采用了更高效的物流配送方式,降低了生产成本。
3. 加强员工培训:定期对员工进行技能培训和岗位练兵活动,提高了员工的操作技能和效率。
同时,建立了激励机制,激发了员工的工作积极性和创造力。
4. 强化现场管理:通过加强现场巡检和监督力度,及时发现问题并解决问题。
同时,推行5S管理法,改善了现场环境和工作条件,提高了生产效率。
四、总结与展望通过采取一系列降低成本和提高效率的措施,我厂在生产经营方面取得了显著成效。
不仅降低了生产成本、提高了生产效率,还增强了企业的市场竞争力。
未来,我们将继续关注行业发展趋势和竞争对手情况,不断优化生产流程和管理制度,以保持领先优势。
2024年开源节流降本增效工作总结

2024年开源节流降本增效工作总结2024年,开源节流降本增效是我所在公司的重要工作方向,旨在优化资源利用,提升生产效率,降低成本,增加利润。
在过去的一年里,我们通过开源节流降本增效工作的实施,取得了显著的成效。
以下是对2024年工作的总结:一、开源方面:1. 推动开放式创新:在2024年,我们继续推动开放式创新,通过与合作伙伴的合作,共享创新资源和知识,激发员工的创新意识和能力,实现项目的快速迭代。
我们与多家科研机构及高校建立了合作关系,通过技术交流和人才培养合作,在新产品开发和技术革新方面取得了突破性进展。
2. 强化知识产权保护:我们加强了知识产权保护工作,对已有的技术和创新成果进行专利申请,并建立了内部的知识产权管理体系。
这不仅有助于提高我们对核心技术的掌控能力,还为公司的长期发展提供了保障。
3. 联合采购:我们与同行业的其他公司进行联合采购,通过集中采购的方式降低了原材料的采购成本,提高了采购效率。
这种合作方式不仅可以共享资源,还可以在供应商谈判时获得更有力的议价权。
二、节流方面:1. 提高能源利用效率:我们对生产线的能源利用进行了全面的诊断和改进,通过优化生产工艺和设备改造,降低了能源消耗,实现了节能减排的目标。
2. 减少废物产生:我们加强了生产过程中废弃物的管理和分类处理,通过回收利用、减少浪费等措施,降低了废物处理的成本,提高了资源的回收利用率。
3. 优化供应链:我们与供应商进行密切合作,减少库存,并与其协商制定了更加合理的供应计划,降低了运输和仓储成本。
同时,我们还开展了供应商绩效评估,优化供应链的结构,提高了供应链的稳定性和灵活性。
三、降本增效方面:1. 工艺改进:我们对各个环节的生产工艺进行了深入的研究和改进,通过优化工艺流程、提高生产效率和质量水平,降低了生产成本。
2. 人力资源管理改革:我们对员工进行了职业培训和素质提升,提高了员工的专业知识和技能水平,增强了团队的凝聚力和战斗力。
神华国能集团有限公司煤矿节能管理制度

神华国能集团有限公司煤矿节能管理制度第一章总则为深入贯彻落实科学发展观,坚持降低能源消耗强度、减少主要污染物排放总量、合理控制能源消费总量,加强节能减排管理,提高能源利用效率,实现节能减排、保护环境、降本增效的可持续发展目标,加快建设资源节约型、环境友好型企业,依据《中华人民共和国节约能源法》、国务院《关于加强节能工作的决定》及神华集团有关要求,特制订本制度。
本办法所称煤矿节能,是指通过加强管理,采取技术上可行、经济上合理以及环境和社会可以承受的措施,实现最大程度的节约和利用。
节能减排管理原则(一)坚持开发与节约并举,节约优先的原则,以效率为本,突出节能减排工作的战略地位;(二)坚持优化结构、多能互补的原则,依靠加强管理、结构调整、科技创新、技术改造,实现节能工作的持续有效开展;(三)坚持节能减排与降本增效相结合,源头控制,依法管理与政策激励相结合,突出重点与全面推进相结合;(四)坚持节能减排与发展相互促进的原则,实现节能减排和发展双赢目标。
本办法适用于神华国能集团有限公司(以下简称“公司”)和所属煤矿。
第二章组织与职责煤矿节能管理工作由公司统一领导,实行分级管理。
公司成立煤矿节能工作领导小组,煤矿节能工作领导小组办公室设在煤炭管理部,主任由煤炭管理部总经理兼任。
公司所属煤矿要成立节能领导小组、建立节能管理网络,明确节能管理归口部门、设置节能管理岗位,负责本单位的节能管理日常工作。
公司煤矿节能工作领导小组主要职责。
(一)贯彻执行国家、煤炭行业、神华集团节能相关的法律法规、规程、标准等;(二)审查公司煤矿节能管理制度、管理标准、节能发展规划等;(三)结合煤矿规划、基建、生产、经营工作实际,统一部署、协调和督导公司节能工作;(四)为开展节能工作,提供人力资源保障,节能技术改造、技术研发、人员培训、节能宣传与成果展示等费用投入;(五)以绩效考核、专项奖励等方式对煤矿的节能工作进行奖励、考核,对贡献突出的集体和个人进行表彰;(六)研究、协调、决策其他重大节能事项。
降本增效总结_节能降本增效工作总结

降本增效总结_节能降本增效工作总结今年,我们公司在降本增效方面取得了长足的进展。
在全体员工的共同努力下,各项工作取得了优异成绩,为公司的可持续发展提供了坚实的基础。
下面,我将对这一阶段的工作进行总结。
一、强化节能意识作为节能降本增效工作的基础,我们公司加大了节能宣传力度,不断提高员工的节能意识。
通过组织各类培训和宣讲活动,加强了员工对节能的认识,培养了他们的节能习惯和节约意识。
在办公楼和生产车间等地方设置了节能标识和提示牌,提醒员工随时节约用电和用水,形成了全员参与的良好氛围。
二、优化能源消耗结构为降低生产成本,我们对能源消耗结构进行了全面的优化。
通过技术改造和设备更新,更新了一批能效更高的设备,降低了能源消耗。
进行了能源系统的全面检测和维护,及时处理了潜在的能耗问题,进一步减少了能源浪费。
我们还充分利用优秀的能源管理软件,对能源消耗进行动态监测和分析,及时发现和解决问题,提高了能源利用效率。
三、加大节约用水力度水资源是宝贵的,我们公司高度重视节约用水工作。
在今年,我们在全公司范围内开展了节约用水的宣传和培训,通过讲座、宣传册等形式,普及了用水知识和技巧。
我们加大了设备的改造,优化了生产工艺流程,减少了废水的排放。
通过这些措施的实施,我们成功将用水量降低了10%,节约了大量的水资源,起到了良好的社会效益和经济效益。
四、实行精细化管理为提高生产效率,我们在今年实施了精细化管理的措施。
我们优化了生产计划和排程,充分利用设备和人员,减少了闲置时间和待机损耗。
我们实行了设备定期保养和维修的制度,保证设备的正常运行和有效利用。
我们对生产过程进行了精细化分析,找出了存在的问题,并采取了相应的措施加以解决。
通过这些工作,我们成功提高了生产效率,降低了生产成本,使公司获得了更好的经济效益。
今年我们公司在节能降本增效方面取得了显著成绩。
通过加强节能意识、优化能源消耗结构、加大节约用水力度和实行精细化管理等措施,我们成功降低了能源和水资源的消耗,提高了生产效率,减少了生产成本,取得了良好的经济效益和社会效益。
工作总结财务成本控制与降本增效

工作总结财务成本控制与降本增效工作总结:财务成本控制与降本增效一、背景分析及目标设定在这个竞争激烈的市场环境下,企业必须不断探索降本增效的方法,以提高竞争力和可持续发展能力。
财务成本控制是实现降本增效的关键手段之一。
本次工作着重于财务成本控制和降本增效方面的工作总结,以期对公司的财务经营起到积极的推动作用。
二、方法与措施1. 定期开展成本分析:通过定期对各个成本项目进行深入分析和评估,找出成本高的项目和异常花费,并进行合理化的优化和调整。
2. 加强预算管理:建立科学合理的预算体系,并根据预算进行经营活动和支出的规划和控制,同时对实际结果进行定期对比和分析,及时调整预算方案。
3. 提高采购效率:优化供应商管理,通过与供应商的有效合作,降低采购成本和库存成本,并积极推行供应链管理,实现供应链上下游的高效协同。
4. 推广节能减排技术:积极引入节能减排技术,优化能源使用结构,通过技术改造和管理优化,降低能源和环保成本。
5. 加强员工培训教育:加强财务意识培养,提高员工对成本控制和效益管理的认识和理解,不断优化员工素养结构,提高整体的效率和业绩水平。
三、工作成果与效益1. 成本控制效果显著:通过以上措施的不断实施,公司在财务成本控制方面取得了初步的成效,各项成本得到了较大幅度的控制,有效降低了企业的经营成本。
2. 降本增效取得明显进展:通过财务成本的控制,企业整体经营效益有所提升,达到了预期的目标。
同时,提高各项工作的效能,进一步增强了企业的核心竞争力。
3. 持续改进和创新:在降本增效方面,我们不仅注重当前的工作成果,更加重视长期的发展。
通过持续改进和创新,我们积极探索更高效的成本控制策略,并与最新科技和管理方法相结合,不断提升公司的核心竞争力。
四、经验总结与展望通过本次工作,我深刻认识到财务成本控制与降本增效的重要性,也明确了实施成本控制和降本增效的关键措施。
同时,也从中总结出以下经验:1. 财务成本控制需要全员参与:成本控制工作需要每位员工都具备财务意识和节约意识,并通过不断学习和交流,共同提高成本控制的能力。
- 1、下载文档前请自行甄别文档内容的完整性,平台不提供额外的编辑、内容补充、找答案等附加服务。
- 2、"仅部分预览"的文档,不可在线预览部分如存在完整性等问题,可反馈申请退款(可完整预览的文档不适用该条件!)。
- 3、如文档侵犯您的权益,请联系客服反馈,我们会尽快为您处理(人工客服工作时间:9:00-18:30)。
以技术改造方式实现节能减排降本增效
王翔张琼
(山西天泽煤化工集团股份公司048026)
山西天泽煤化工集团股份公司是山西省最大的尿素生产企业,现具有年产84万吨合成氨、140万吨尿素、30万吨甲醇、3万吨甲醛、1.5万吨三聚氰胺的综合生产能力。
近两年来,公司在克服原材料价格持续暴涨、国内尿素产能严重过剩、销售市场低迷、低碳经济和节能减排任务繁重的困境,为保证企业健康稳步发展,不断地加大节能降耗,加大环境保护投资力度,新上一批节能环保和低碳、循环经济项目,可进一步降低生产成本,增强抵御市场风险能力。
现总结如下:
1.12+6MW 吹风气回收余热发电低碳节能项目
低碳经济的实质是能源高效利用、清洁能源开发。
为此,我公司在煤气化厂“50.40”项目和永丰公司“18.30”项目中,分别配套实施了12MW、6MW余热发电项目。
将造气生产过程中排放的吹风气;合成氨、甲醇生产过程中排放的可燃尾气集中回收燃烧后产生3.82MPa 蒸汽,通过发电机组背压发电后,产生的0.4MPa低压蒸汽返供造气生产,使能量达到递级利用和循环利用,既解决了有害气体对环境造成的污染,又提高了资源利用率。
由于受电力进网审批手续办理程序复杂的影响,煤气化厂“50.40”项目配套12MW吹风气余热发电项目于2009年10月试车并网;永丰公司配套6MW吹风气余热发电项目于2010年3月开工,计划9月投运。
该项目总投资4590万元, 建成后年可利用吹风气量共18360×105Nm3,发电10541万度,节标煤36894吨。
该项目被列入山西省和晋城市重点节能工程,并获得了经济补偿。
2. 2×220万m3/年污水治理及回用项目
公司下属厂生产中废水来自于造气、尿素、甲醇精馏等主要工段,原系统配套的废水处理措施,只能达标排放,排放的废水中有些物质会对当地水质造成环境污染,并造成水资源的浪费。
为节约珍贵的水资源,保护生态环境,在三个厂分别配套实施了两套220万m3/年(设计能力300 m3/h)污水处理及回用项目。
该项目选用以生物处理与物化处理和反渗透处理为主体的工艺路线,其中生物处理选择一级“短程硝化反硝化”生物脱氮工艺和二级“反硝化脱氮”+“曝气生物滤池”工艺;物化处理采用“混凝沉淀”+“过滤”工艺;脱盐工艺采用“纳滤(NF)”工艺。
经过多重工艺深度处理后的水可用作循环水补水使用。
项目投运后年可削减COD 1280吨,NH3-N 534吨,SS 642吨,节约一次水338万m3。
煤气化厂污水处理项目于2008年11月首先建成达标排放工程后效果明显,中水回用工
程计划2010年7月开工,年底建成投运。
化工厂、永丰公司污水处理项目达标排放于2010年3月份完成并投入运行,中水回用工程2010年6月建成投运后,现有150 m3/h达标水返回脱盐水经混床处理后进入脱盐水系统,缓解了新鲜水供应紧张不能保证生产的局面。
煤气化厂污水回用工程正在建设中,预计2010年底建成试车。
3. 三套尿素装置的解吸废水回用项目
原公司三套尿素装置的解析废水约3×30m3/h,只能达标排放,为节约珍贵的水资源,变废为宝,公司于2010年4月在化工厂、永丰公司、煤气化厂建成了三套30m3/h尿素解吸废水回用项目。
该项目利用徐州水处理研究所“尿素解吸废液深度处理回用技术”。
通过添加专用药剂,可将深度水解后废液回收充作脱盐水用在造气夹套、余热回收锅炉。
项目于2010年4月份现在永丰、化工厂投入运行,三套装置仅投资13万元,年可共节约脱盐水64.8万吨。
通过生产运行,避免了因一次水紧张,夏季高温季节对生产造成的影响,社会、经济效益良好。
4. 2.7Mpa等压变换装置节能降耗项目
化工厂合成氨变换受当时技术水平的影响,主要利用北京顺义化肥厂闲置的3万吨中串低变换设备,于2002年经过改造并采用0.8Mpa全低温变换工艺,生产能力扩大至6万吨/年合成氨。
通过近几年来的生产运行,该装置存在着系统阻力偏大、能耗高、设备安全性能差等弊端。
为贯彻国家节能降耗精神,保障安全生产,公司确定采用2.7Mpa等压变换工艺来淘汰原装置,使化工厂合成氨能耗进一步降低。
本节能技术改造主要通过对提高变换压力,使变换与脱碳等压,可以减少约30%的CO2气返回压缩机的功耗。
采用2.7Mpa无饱和热水塔、喷水增湿节能型全低温变换和湿式栲胶变脱工艺。
该技术的实施,吨氨可节电40度,相当于年节标煤 2520吨。
该项目总投资2400万元,已于2009年8月建成投运。
5. 16000m3/h脱碳闪蒸气回收节能项目
公司下属化工厂、永丰化肥公司现有4套碳丙脱碳装置,生产中闪蒸气中含有20%左右的H2、CO有用气体成分全部被放空,造成能源浪费。
本项目采用由成都天立化工科技公司开发的变压吸附法建成16000 m3/h的装置,对该部分有效气体进行回收利用。
项目总投资800万元,项目于2010年7月建成投运后,产品气CO2控制在5%~8%,H2控制在70%,CO控制在3.2%,回收气量为5400m3/h,可增产合成氨43.2吨/日,年可节约标煤13600吨,
节能效果和经济效益明显。
6.化工厂循环水、合成氨挖潜改造项目
化工厂2003年建成投产的第一套“18.30”装置,是兼并原解放军总后第6013工厂后分期改造建成的。
2004年改造后达到“24.40”生产规模,为实现节能降耗,降低生产成本,将采取先进的技术进行挖潜技改,使装置能力达到“30.52”的生产能力,针对合成氨系统循环水供水能力和地下管网管道偏小,氨合成循环机和氮氢压缩机供气能力存在瓶颈等问题进行了挖潜改造。
循环水系统将冷冻系统由循环水改为蒸发式水冷器,节约循环水约2400m3/h;优化改造循环水管网,消除制约瓶颈;循环机扩缸改造后单机能力由8m3/min 增至103/min,并拆迁老厂一台5m3/min循环机,提高氨合成能力;拆迁老厂一台110m3/min 氮氢压缩机,使合成氨生产能力达到日产960吨/日,满足日产1700吨尿素扩改要求。
循环水系统5月份改造后,在7~8月份高温季节,日产910吨合成氨的生产状况下,循环水可满足生产要求。
7.尿素系统改加双氧水节能改造
在我公司三套CO2汽提尿素工艺中,为防止高压圈设备腐蚀和阻止氢气进入爆炸区域,通过在CO2气体中添加4~6%的空气,保证进入汽提塔前O2含量在0.7~0.9%,但是也带入大量氮气。
由于氮气基本不参加反应,从而导致高压系统放空量增大,影响物耗、能耗。
系统改加H2O2后,防腐空气量大幅度减少,CO2中的O2含量由0.7~0.9%降为0.35~0.50%,高压合成尾气放空阀和中压尾气放空阀开度大幅度减小,对降低尿素的物耗能耗有明显效果。
(1)由于系统空气量减少,在操作压力不变时,高压系统惰气分压下降,实际反应压力上升,合成转化率有所上升;(2)在同样的出口流量下,CO2实际流量增加,提高了生产负荷。
(或在同样的CO2流量下,打气量下降,可减少压缩机功耗);(3)合成转化率提高,工艺消耗的中压蒸汽量有所下降;(4)放空气减少,氨耗降低。
该项目于2010年10月份先在永丰公司、煤气化厂两套尿素装置完成安装并投入试车,根据试车情况再在化工厂
实施。
利用部分闲置设备,两项目投资约50万元。
8.废油实施回收再利用
在生产过程中的氮氢压缩机、二氧化碳压缩机、冰机、循环机等运转设备在运行过程中有废油水排放。
据统计,我公司三个生产厂每年废油回收量约500多吨(约占年用油总量的60%)。
目前通过隔油池回收后,以约2000元/吨低价出售给废油加工企业。
依据油烃分
族不同的物理,化学属性等,在再生助剂精制工艺条件下,将各类废油中碳氧化产物及中间混合物加工处理后加工成基础油,经添加各种添加剂调整润滑油成份达到国家润滑油质量技术标准要求返回系统重新使用。
利用闲置设备在永丰、煤气化厂新建两套200吨/年废油回收再利用装置,总投资:≤100万元,加工成本4500元/吨,比外购润滑油11000元/吨,年新增利润260万元。
该项目在保护环境的同时又达到资源循环利用,社会、经济效益显著。