冲压件设计
冲压件模具设计常用公式

冲压件模具设计常用公式1. 材料和工艺参数计算公式1.1 冲击力的计算公式冲击力是冲压件模具设计中重要的参考指标之一,它可以用于确定模具的强度和稳定性。
冲击力的计算公式如下:F = K × A × T × σ其中,F表示冲击力,K表示冲击系数,A表示冲压件的有效面积,T表示冲压时间,σ表示材料的抗拉强度。
1.2 冲床力的计算公式冲床力是指冲床在冲压过程中对工件所产生的压力。
冲床力的计算公式如下:P = F / A其中,P表示冲床力,F表示冲击力,A表示冲压件的有效面积。
1.3 冲压时间的计算公式冲压时间是指冲床一次冲压周期所需的时间。
冲压时间的计算公式如下:T = (L / V) + t其中,T表示冲压时间,L表示冲压件的长度,V表示冲床的下行速度,t表示冲程停留时间。
1.4 最大冲床力的计算公式最大冲床力是指冲床所能承受的最大压力。
最大冲床力的计算公式如下:P_max = K × A × σ其中,P_max表示最大冲床力,K表示冲击系数,A表示冲压件的有效面积,σ表示材料的抗拉强度。
2. 模具结构设计公式2.1 模具剪切强度的计算公式模具剪切强度是指模具在剪切过程中所能承受的最大剪切力。
模具剪切强度的计算公式如下:P_shear = F / A_shear其中,P_shear表示模具剪切强度,F表示冲击力,A_shear表示模具剪切面积。
2.2 模具挤压强度的计算公式模具挤压强度是指模具在挤压过程中所能承受的最大挤压力。
模具挤压强度的计算公式如下:P_extrusion = F / A_extrusion其中,P_extrusion表示模具挤压强度,F表示冲击力,A_extrusion表示模具挤压面积。
2.3 模具弯曲强度的计算公式模具弯曲强度是指模具在弯曲过程中所能承受的最大弯曲力。
模具弯曲强度的计算公式如下:P_bending = F / A_bending其中,P_bending表示模具弯曲强度,F表示冲击力,A_bending表示模具弯曲面积。
冲压件模具设计常用公式

冲压件模具设计常用公式1. 冲裁力计算公式冲裁力是模具在冲裁过程中对工件施加的力的大小,可以使用以下公式进行计算:$$ P = K \\cdot T \\cdot L \\cdot S $$其中: - P 是冲裁力〔单位:N〕 - K 是系数〔根据材料和冲裁方式进行选择〕 - T 是材料的厚度〔单位:mm〕 - L 是冲裁长度〔单位:mm〕 - S 是材料强度的保险系数2. 冲孔力计算公式冲孔是冲压件模具中常见的一个工序,为了计算冲孔力,可以使用以下公式:$$ F = K \\cdot T \\cdot L \\cdot S $$其中: - F 是冲孔力〔单位:N〕 - K 是系数〔根据材料和冲孔方式进行选择〕 - T 是材料的厚度〔单位:mm〕 - L 是冲孔孔径〔单位:mm〕 - S 是材料强度的保险系数3. 模具开孔面积计算公式在冲压件模具设计中,开孔面积对模具的设计和选择起着重要的作用。
开孔面积可以通过以下公式计算:$$ A = L \\cdot W $$其中: - A 是开孔面积〔单位:mm²〕 - L 是模具的长度〔单位:mm〕 - W 是模具的宽度〔单位:mm〕4. 模具强度计算公式模具强度的计算是冲压件模具设计中的关键步骤之一。
可以使用以下公式计算模具的强度:$$ P_t = P \\cdot S_f $$其中: - P_t 是模具的强度〔单位:N〕 - P 是冲裁力或冲孔力〔单位:N〕 - S_f 是平安系数5. 模具寿命计算公式模具寿命的计算是冲压件模具设计过程中需要关注的一个重要指标。
可以使用以下公式计算模具寿命:$$ N_m = \\frac{S_m}{f \\cdot V_c} $$其中: - N_m 是模具的使用寿命〔单位:次〕 - S_m 是模具材料的疲劳强度〔单位:MPa〕 - f 是载荷系数 - V_c 是模具的速度〔单位:m/s〕6. 模具热应力计算公式模具在使用过程中会受到热应力的影响,为了进行热应力的计算,可以使用以下公式:$$ \\sigma = \\frac{Q}{A} $$其中: - σ 是热应力〔单位:MPa〕 - Q 是热量〔单位:J〕 - A 是模具横截面积〔单位:mm²〕7. 模具变形计算公式模具在使用过程中会发生一定的变形,为了进行变形的计算,可以使用以下公式:$$ \\delta = \\frac{{F \\cdot L}}{{E \\cdot A}} $$其中: - δ 是变形量〔单位:mm〕- F 是施加在模具上的力〔单位:N〕 - L 是模具的长度〔单位:mm〕 - E 是弹性模量〔单位:MPa〕 - A 是模具的截面积〔单位:mm²〕总结在冲压件模具设计过程中,常用的公式可以帮助工程师快速准确地进行相关计算,从而确保模具的性能和可靠性。
冲压件模具设计的常用公式

冲压件模具设计的常用公式
一、材料力学公式
1.应力公式:σ=F/A,其中σ为应力,F为受力,A为受力面积。
2.应力应变关系公式:σ=E×ε,其中E为杨氏模量,ε为应变。
3.屈服强度公式:σs=F/A0,其中σs为屈服强度,F为屈服点所受力,A0为初始横截面积。
二、材料成形公式
1. 塑性变形公式:ε = ln (h0 / hn) ,其中ε为塑性变形,h0为初始厚度,hn为最终厚度。
2.变形力公式:F=S×σs,其中F为变形力,S为变形面积,σs为屈服强度。
3.针对特定形状的材料成形公式,如直冲材料成形公式、弯曲材料成形公式等。
三、模具设计公式
1.强度计算公式:F=σ×A,其中F为受力,σ为应力,A为受力面积。
2. 弯曲应力公式:σ = M / (W × yc),其中σ为弯曲应力,M为弯矩,W为截面模量,yc为弯曲轴心距离。
四、装配公式
1.装配公差公式:A=A1+A2+A3,其中A为总公差,A1为尺寸公差,
A2为形位公差,A3为相对公差。
五、切削力公式
1. 切削功率公式:P = F × V × kc,其中P为切削功率,F为切
削力,V为切削速度,kc为切削功率系数。
以上是冲压件模具设计中的常用公式,通过这些公式的运用,可以对
冲压件进行力学、成形、模具设计、装配以及切削力等方面的优化和设计。
当然,具体的设计中还需要根据实际情况和不同材料的特性来选择合适的
公式。
冲压件模具设计常用公式

冲压件模具设计常用公式一、前言冲压件模具设计是冲压加工实现自动化、高效生产的关键环节,冲压件模具设计的好坏直接影响冲压品质和生产效益。
因此,在冲压件模具设计过程中,必须掌握一些常用公式,以便在实践中更加精准地解决模具设计中的各种问题。
本文将围绕冲压件模具设计常用公式进行阐述,以期为读者提供一些实用、有效的模具设计知识和技巧。
二、冲压件模具设计常用公式分类1. 材料折弯空间S材料折弯空间S是指冲压时材料在弯曲过程中被拉长的长度,用于计算按照弯缘角度和弯曲半径计算成品长度。
公式如下:S=K*L*(180°-2α)/π 式中,L是材料长度,α是折弯角度,K 是常数,其值根据材料厚度和折弯角度而定。
2. 冲压件毛坯重量M冲压件毛坯重量M是指冲压件在未经加工之前的重量,用于计算材料消耗。
公式如下:M=ρ*L*w*t 式中,ρ是材料密度,L是边长,w是厚度,t 是数量。
3. 模具壁厚t模具壁厚t是指冲压件模具中金属材料的厚度,包括上、下、左、右四个方向的壁厚,一般与压力有关。
可按照最小切削层厚度取值,公式如下:t=K*H/24 式中,K是常数,一般为6~10,H是加工硬度。
4. 补料长度L补料长度L是指冲压件模具中需要加上的余量,保证成品尺寸精度和质量,公式如下:L=αt/K 式中,α是成品弯缘角度,t是壁厚,K是常数,一般为4~6。
5. 小孔冲孔孔距P小孔冲孔孔距P是指在被加工材料上,两相邻的小孔冲或冲孔之间的距离,用于计算模具孔距间距。
公式如下:P=p*t 式中,p是小孔冲孔孔距系数,t是壁厚。
6. 冲模的直径D冲模的直径D是指用以冲剪及压穿时所用的模具直径大小,用于计算冲模的耐用程度。
公式如下:D=0.7√t 式中,t是最薄材料厚度。
7. 冲孔直径d冲孔直径d是指冲剪和冲孔过程中冲头的直径大小,直接影响冲穿质量和模具的使用寿命。
公式如下:d=0.9√H 式中,H是加工硬度。
三、总结本文从材料折弯空间S、冲压件毛坯重量M、模具壁厚t、补料长度L、小孔冲孔孔距P、冲模的直径D和冲孔直径d等七个方面介绍了冲压件模具设计常用公式,并为读者提供了详细的公式计算方法和实用技巧。
冲压件设计要点

冲压件设计要点冲压件是冲压工艺中常用的一种零件加工方式,其特点是高效快速、成本低廉,广泛应用于汽车、电子、家电等行业。
在进行冲压件设计时,需要注意以下几个要点。
1. 材料选择:冲压件的材料选择直接影响到产品的质量和性能。
一般情况下,冲压件常用的材料有冷轧板、热轧板、不锈钢、铝合金等。
在选择材料时,要考虑到产品的实际使用环境、强度要求、耐腐蚀性等因素,确保材料的可靠性和经济性。
2. 孔洞设计:冲压件常常需要在板材上开设孔洞,用于连接、安装或通风等用途。
在进行孔洞设计时,需要考虑到孔洞的尺寸、位置和形状,确保其与其他零件的配合精度,并提供足够的强度和刚度。
3. 弯曲设计:冲压件常常需要进行弯曲加工,用于形成特定的形状或角度。
在进行弯曲设计时,需要考虑到板材的强度、弯曲角度、弯曲半径等因素,确保弯曲后的产品符合设计要求,并避免出现开裂或变形等问题。
4. 表面处理:冲压件的表面处理对于提高产品的质量和外观非常重要。
常用的表面处理方式包括镀锌、喷涂、电泳等。
在进行表面处理时,需要考虑到产品的使用环境和要求,选择合适的表面处理方式,并确保其与产品材料的相容性。
5. 模具设计:冲压件的模具设计是冲压工艺中的关键环节。
在进行模具设计时,需要考虑到产品的形状、尺寸和加工要求,确保模具的精度和稳定性。
同时,也要考虑到模具的制造成本和寿命,选择合适的材料和加工工艺。
6. 工艺规程:冲压件的加工过程需要制定详细的工艺规程,包括材料切割、冲孔、弯曲、表面处理等各个环节。
在制定工艺规程时,需要考虑到产品的加工难度、工艺稳定性和成本效益,确保产品的质量和交货期。
7. 检验要求:冲压件的质量检验是确保产品质量的重要环节。
在制定检验要求时,需要考虑到产品的尺寸精度、表面质量、材料性能等因素,选择合适的检验方法和标准,确保产品符合设计要求和客户需求。
8. 工装设计:冲压件的加工需要使用适当的工装和夹具。
在进行工装设计时,需要考虑到产品的形状、尺寸和加工要求,选择合适的工装类型和结构,确保产品的加工精度和稳定性。
冲压件工艺过程设计的内容及步骤
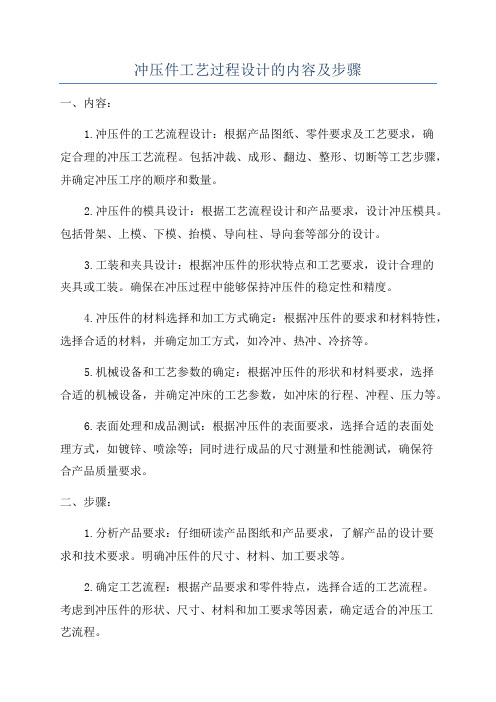
冲压件工艺过程设计的内容及步骤一、内容:1.冲压件的工艺流程设计:根据产品图纸、零件要求及工艺要求,确定合理的冲压工艺流程。
包括冲裁、成形、翻边、整形、切断等工艺步骤,并确定冲压工序的顺序和数量。
2.冲压件的模具设计:根据工艺流程设计和产品要求,设计冲压模具。
包括骨架、上模、下模、抬模、导向柱、导向套等部分的设计。
3.工装和夹具设计:根据冲压件的形状特点和工艺要求,设计合理的夹具或工装。
确保在冲压过程中能够保持冲压件的稳定性和精度。
4.冲压件的材料选择和加工方式确定:根据冲压件的要求和材料特性,选择合适的材料,并确定加工方式,如冷冲、热冲、冷挤等。
5.机械设备和工艺参数的确定:根据冲压件的形状和材料要求,选择合适的机械设备,并确定冲床的工艺参数,如冲床的行程、冲程、压力等。
6.表面处理和成品测试:根据冲压件的表面要求,选择合适的表面处理方式,如镀锌、喷涂等;同时进行成品的尺寸测量和性能测试,确保符合产品质量要求。
二、步骤:1.分析产品要求:仔细研读产品图纸和产品要求,了解产品的设计要求和技术要求。
明确冲压件的尺寸、材料、加工要求等。
2.确定工艺流程:根据产品要求和零件特点,选择合适的工艺流程。
考虑到冲压件的形状、尺寸、材料和加工要求等因素,确定适合的冲压工艺流程。
3.设计模具和工装:根据工艺流程设计和产品要求,设计合理的冲压模具和工装。
包括骨架、上模、下模、抬模、导向柱、导向套等部分的设计,并确保模具和工装的合理性和可行性。
4.选择材料和加工方式:根据冲压件的要求和材料特性,选择合适的材料,考虑材料的强度、硬度、韧性等性能要求。
同时,根据冲压件的形状和材料要求,确定适合的加工方式。
5.确定机械设备和工艺参数:根据冲压件的形状和材料要求,选择合适的机械设备,确定冲床的工艺参数。
包括冲床的行程、冲程、压力等参数。
6.表面处理和成品测试:根据冲压件的表面要求,选择合适的表面处理方式,如镀锌、喷涂等。
同时进行成品的尺寸测量和性能测试,确保冲压件符合产品质量要求。
冲压件模具设计的常用公式

冲压件模具设计的常用公式1. 强度和刚度计算公式1.1 拉伸强度计算冲压件在工作过程中会受到拉伸力的作用,因此计算冲压件的拉伸强度是非常重要的。
拉伸强度的计算公式如下:F = σ × A其中,F表示拉伸力,σ表示材料的抗拉强度,A表示冲压件的截面积。
1.2 刚度计算刚度是指冲压件在受力下的变形程度,计算冲压件的刚度可以确定其在工作过程中是否会发生过度变形。
刚度的计算公式如下:K = (E × A) / L其中,K表示刚度,E表示材料的弹性模量,A表示冲压件的截面积,L表示冲压件的长度。
2. 冲压参数计算公式2.1 冲头压力计算冲头压力是冲压件在冲床上受到的压力,计算冲头压力可以确定冲床的最小压力要求。
冲头压力的计算公式如下:P = F / A其中,P表示冲头压力,F表示冲压件的拉伸力,A表示冲头的截面积。
2.2 厚度计算冲压件的厚度是冲压件的重要参数之一,计算冲压件的厚度可以确定其制备过程中所需的原材料量。
厚度的计算公式如下:t = V / (A × L)其中,t表示冲压件的厚度,V表示冲压件的体积,A表示冲压件的截面积,L表示冲压件的长度。
3. 离型力计算公式冲压件在离型过程中需要克服一定的摩擦力,计算离型力是确定冲压模具设计是否合理的重要指标。
离型力的计算公式如下:F = μ × N其中,F表示离型力,μ表示冲压件和模具之间的摩擦系数,N表示冲压件的法线力。
4. 寿命计算公式冲压模具在工作过程中会受到疲劳载荷的影响,因此计算冲压模具的寿命可以指导模具的选材和使用。
寿命的计算公式如下:N = (S / K) × (F / σf)^b其中,N表示模具寿命的预测次数,S表示冲压次数,K表示对应于S次冲压的磨损系数,F表示冲压力,σf表示冲压件的疲劳强度,b表示指数。
结论以上是冲压件模具设计过程中常用的计算公式。
这些公式可以帮助工程师在设计冲压模具时进行强度、刚度、参数和寿命等方面的计算,以确保模具的设计合理和稳定性。
冲压件设计

冲压件设计一、冲压的基本成形工艺、应用领域按工艺分类,可分为分离工序与成形工序两大类。
应用领域:(1)汽车行业的冲压;(2)汽车等行业零部件类冲压;(3)电器件冲压;(4)生活日用品冲压;(5)家用电器部件冲压;(6)特种冲压二、冲压模具的基本分类、特点依模具的工作方式分类:单工序冲模与多工序冲模两种,多工序冲模由于设计方式的不同又可区分为复合冲模、组合冲模与连续冲模三种。
依产品的加工方法分类:可将模具分成冲剪模具、弯曲模具、拉深模具、成形模具与压缩模具等五大类三、冲压件设计的基本原则四、冲压件设计的注意事项1.冲裁冲压件的工艺性1).尽量避免冲裁比料厚还要小的孔2).凸出与凹入的地方(如:悬臂与狭槽)的宽度与长度与材料厚度的比例要适当3).孔与孔之间,孔与边缘之间的距离a,受模具强度与冲裁件质量的限制,其值不能过小4).冲压件上尽量不要出现清角,线与线交接的地方要用圆弧过度,其半径R≥0.2。
5).冲压件的形状包括折弯展开的形状,要能符合材料合理排样,尽量减少废料。
6).在弯曲与拉深件上冲孔时,其孔的边缘与冲压件的直壁的距离不能小于如下图所示,如果距离过小7).若用条料冲裁两端带圆弧的工件,其圆弧半径R应大于条料宽度的一半,否则会产生凸肩。
8).对于冲压件上重要的配合孔(包括圆孔与异形孔),不管材料多厚,其冲裁后的断面总归是有三带一毛刺(圆角带、光亮带、断裂带与毛刺),所以尽量避免全光亮带的要求。
9).冲裁件的毛刺与冲裁间隙有关,所以在设计冲裁件的时候要同时兼顾其毛刺的高度与其断面的光亮带。
10).冲裁件的精度一般可以分为精密级与经济级两类,精密级是冲压工艺技术上所允许的精度,而经济级是指可以用较经济手段达到的精度。
2.弯曲件的冲压工艺性1).弯曲件的圆角半径2).弯曲件的弯曲高度不要太长,同时H也不可以过小3).弯曲件的弯曲线尽量不要设计在宽度突变的地方(如图2-6),以避免撕裂。
4).对于有孔的弯曲件,如果孔位于弯曲的附近,弯曲的时候会使孔变形。
冲压件模具设计的常用公式

冲压件模具设计的常用公式随着现代工业的发展,冲压件的应用越来越广泛,从家电到汽车、航空航天等领域都离不开冲压件的制造。
而冲压件的制造离不开模具的设计和制造。
在冲压件模具设计中,使用一些公式能够更好的指导设计过程,提高模具设计的效率和准确性。
本文将介绍一些冲压件模具设计中的常用公式。
1.冲压件的扁平公式在冲压件的设计中,往往需要先根据产品的图纸计算出其扁平尺寸。
用于判断冲压件的设计尺寸是否合理。
冲压件的扁平公式为:S=π(D+d)/2×√((D-d)/2)×F其中,S表示冲压件的扁平尺寸,D和d分别为模具的上模和下模的直径,F为强度系数。
2.模具的强度公式在冲压过程中,模具需要承受很大的压力和撞击力,因此模具的强度是非常重要的。
冲压件模具的强度公式为:σ= (K×(F×L))/((a-b)×b)其中,σ为应力,K为强度试验样本的应力系数,F为金属材料的屈服极限,L为冲压件的长度,a和b分别为上模和下模的外径。
3.折弯件的受载公式在冲压件的制造中,折弯件的制作也是非常重要的一个过程。
折弯件的受载公式为:M=W×L/2×sinα×t^2其中,M为折弯件的扭矩,W为载荷,L为支撑距离,α为折弯角度,t为材料的厚度。
4.齿轮的模数公式在冲压齿轮的设计中,需要根据参数计算出齿轮的模数。
齿轮的模数公式为:m=D/Z其中,m为模数,D为齿轮的直径,Z为齿轮的齿数。
5.模具内角的计算公式在冲压件模具的设计中,模具内角的大小和形状是非常重要的。
模具内角的计算公式为:Ψ=2arctan(0.5B/L)其中,Ψ为内角,B为压头直径(冷模),压头直径补偿(热模),L为模具凸部的长度。
以上就是冲压件模具设计中的一些常用公式。
通过使用这些公式,能够更好地指导冲压件模具的设计,提高冲压件的生产效率和质量。
冲压件工艺过程设计方案内容及步骤

第二章冲压件工艺过程设计的内容及步骤不论冲压件的几何形状和尺寸大小如何,其生产过程一般都是从原材料剪切下料开始,经过各种冲压工序和其他必要的辅助工序(如退火,酸洗,表面处理等)加工出图纸所要求的零件。
对于某些组合冲压件或精度要求较高的冲压件,还需要经过切削,焊接或铆接等加工,才能完成。
冲压件工艺过程的制定和模具设计是冷冲压课程设计的主要内容。
进行冲压设计就是根据已有的生产条件,综合考虑影响生产过程顺利进行的各方面因素,合理安排零件的生产工序,最优地选用,确定各工艺参数的大小和变化范围,设计模具,选用设备等,以使零件的整个生产过程达到优质,高产,低耗,安全的目的。
2.1 工艺过程设计的基本内容冲压工艺规程是模具设计的依据,而良好的模具结构设计,又是实现工艺过程的可靠保证,若冲压工艺有改动,往往会造成模具的返工,甚至报废。
冲制同样的零件,通常可以采用几种不同方法。
工艺过程设计的中心就是依据技术上先进,经济上合理,生产上高效,使用上安全可靠的原则,使零件的生产在保证符合零件的各项技术要求的前提下,达到最佳的技术效果和经济效益。
冲压件工艺过程设计的主要内容和步骤是:一. 分析零件图(冲压件图)产品零件图是分析和制定冲压工艺方案的重要依据,设计冲压工艺过程要从分析产品的零件图人手。
分析零件图包括技术和经济两个方面:1. 冲压加工的经济性分析冲压加工方法是一种先进的工艺方法,因其生产率高,材料利用率高,操作简单等一系列优点而广泛使用。
由于模具费用高,生产批量的大小对冲压加工的经济性起着决定性作用,批量越大,冲压加工的单件成本就越低,批量小时,冲压加工的优越性就不明显,这时采用其他方法制作该零件可能有更好的经济效果。
例如在零件上加工孔,批量小时采用钻孔比冲孔要经济;有些旋转体零件,采用旋压比拉深会有更好的经济效果。
所以,要根据冲压件的生产纲领,分析产品成本,阐明采用冲压生产可以取得的经济效益。
2. 冲压件的工艺性分析冲压件的工艺性是指该零件在冲压加工中的难易程度。
冲压件结构设计的注意事项

冲压件结构设计的注意事项冲压件结构设计是制造业中常见且重要的工作,它影响着产品的质量和性能。
在进行冲压件结构设计时,有一些重要的注意事项需要考虑,这些注意事项将有助于确保冲压件的可靠性和稳定性,提高产品的生产效率和经济效益。
1.材料选择:在进行冲压件结构设计时,需要选择适合的材料。
材料的选择将直接影响冲压件的力学性能和耐用性。
常用的冲压件材料包括低碳钢、不锈钢、铝合金等。
选择合适的材料要考虑产品的使用环境、要求的强度和硬度等因素。
2.孔洞和孔纹设计:在冲压件结构设计中,需要根据实际需要合理设计孔洞和孔纹。
孔洞的设计应考虑材料的应力分布,尽量减小应力集中。
孔纹的设计要考虑冲压件的连接方式和拆卸需求,以方便后续的组装和维修。
3.壁厚和型腔设计:冲压件的壁厚设计要符合力学强度和工艺性的要求。
壁厚过大会导致材料浪费和制造成本增加,壁厚过小会影响结构的承载能力。
型腔的设计要充分考虑冲压工艺的特点,确保冲压过程中材料的流动和变形。
4.凸缘和边缘设计:在冲压件结构设计中,凸缘和边缘的设计要考虑产品的装配和使用需求。
凸缘的设计要保证其与其他部件的连接牢固和密封性能。
边缘的设计要注意避免锋利的边缘或突起,以防止工人在操作时受伤。
5.流线型设计:在冲压件结构设计中,流线型设计可以降低空气阻力,减少能耗和噪音。
流线型设计还可以提高产品的外观美观性,提升产品的市场竞争力。
6.加工工艺:在进行冲压件结构设计时,需要充分考虑冲压工艺。
合理的结构设计能够提高冲压件的一次成型率和工艺稳定性,减少废品和二次加工的发生。
7.耐久性和可维修性:冲压件结构设计还应考虑产品的耐久性和可维修性。
耐久性设计要求材料具有良好的腐蚀性能和抗疲劳性能,以延长产品的使用寿命。
可维修性设计要求冲压件的拆卸和维修过程简单、方便。
8.成本问题:在进行冲压件结构设计时,还需要考虑到成本问题。
合理的结构设计可以降低材料和制造成本,提高产品的市场竞争力。
总之,冲压件结构设计是一项复杂而重要的工作。
冲压件设计及表面处理工艺

冲压件设计及表面处理工艺冲压件成形原理:冲压是靠压力机和模具对板材、带材、管材和型材等,施加外力,使之产生塑性变形或分离,从而获得所需形状和尺寸的工件(冲压件)的成形加工方法。
工艺分类:冲压主要是按工艺分类,可分为分离工序和成形工序两大类。
分离工序(冲裁工序):其目的是使冲压件沿一定轮廓线从板料上分离,同时保证分离断面的质量要求。
分离工序:冲裁(落料、冲孔)、剪切、切口、切边、剖切。
冲裁时板料的变形过程变形过程:模具间隙正常时,金属材料的冲裁过程可分三个阶段:1)弹性变形阶段板料产生弹性压缩,弯曲和拉伸等变形。
材料在受到外力作用时产生变形或者尺寸的变化,而且能够恢复的变形叫做弹性变形。
2)塑性变形阶段板料的应力达到屈服极限,板料开始产生塑性剪切变形。
是指材料在外力作用下产而在外力去除后不能恢复的那部分变形。
3)断裂分离阶段已成形的裂纹沿最大应变速度方向向材料内延伸,呈楔形状发展冲裁后板料断面分为四个部分成形工序:是使板料在不破坏的条件下发生塑性变形,制成所需形状和尺寸的工件。
成形工序:弯曲、卷圆、扭曲、拉深、变薄拉深、翻边(孔的翻边、外缘翻边)、缩口、扩口、起伏、卷边、涨形、旋压、整形、校平、压印、挤压(正挤压、反挤压、复合挤压)。
冲压件设计注意事项冲裁冲压件的冲压工艺性1).冲裁件的形状和角度:冲裁件的形状设计应尽可能简单、对称,使排样时废料最少。
冲裁件拐角应避免锐角,宜有适当的圆角2).冲孔最小孔径(冲孔时孔径不宜太小)最小尺寸如下表冲裁件的结构尺寸(如孔径、孔距等)必须考虑材料的厚度。
3). 最小孔间距和孔边距冲裁件的孔与孔之间、孔与边缘之间的距离不应过小。
4). 凸出悬臂和凹槽的最小宽度弯曲件的冲压工艺性1).材料弯曲时,弯曲圆角当超过材料的极限强度时,就会产生裂缝和折断,应避免过小的弯曲圆角半径2)R角的设定最好不要大于其自身1.5倍材料厚度。
因为R角过大弯曲过后其回弹也很大。
3).弯曲件的弯曲高度不要太长,同时H也不可以过小,特别是材料t>2mm的时候h过小(切记),会使弯曲困难,很难得到形状准确的零件。
冲压件设计的通用规则

冲压件设计的通用规则,掌握这一张图可解
决大部分的冲压问题
冲压工艺是现代生产工艺中非常成熟、应用非常广泛的生产工艺,大家经常会看一些冲压件(钣金件)设计规范,很多结构上要注意一些尺寸的设计,避免模具不易加工、容易损坏、产品质量不高等问题,而且不同设计位置有不同的公式限制,很难记住,我们将常见的冲压件设计孔距参数的要求进行整理,把这些规则整理到一张图上,如下图:
图中a尺寸:孔与孔之间最小孔间距,孔与边缘之间的最小距离,凸出和凹入的地方(如:悬臂和狭槽)的最小宽度,取值不能过小,常规设计取a≥2t即可,必要时可根据情况再取小一点;当然这个数值跟材质也有一定关系:
当冲压件为高碳钢的时候:
a≥2t,必要时可取a=(1.3-1.5)t,(t<1mm时按t=1mm计算);
当冲压件为黄铜、纯铜、软钢时:
a≥1.5t,必要时可取a=(0.9-1.0)t,(t<1mm时按t=1mm计算);当冲压件为铝、锌时:
a≥1.0t,必要时可取a=(0.75-0.8)t,(t<1mm时按t=1mm计算);。
冲压件设计

冲压(Stamping)冲压是在常温下运用压力机并依靠模具对金属材料剪切,使之变形获得所需形状的工艺。
压力机属于锻压机的一类,冷冲压的压力机有机械压力机和液压压力机,常用的是机械压力机(冲床)。
冲压工艺(Stamping Process)(1)落料Cutting落料:从材料上沿着封闭轮廓分离出工件初胚的工艺。
(2)冲孔Punching冲孔:从工件上沿着封闭轮廓分离出废料,获得所需要的带孔零件的工序。
(3)压凸/压筋Embossing压凸/压筋:用凸模挤入工件的一面,迫使材料流入对面凹坑以形成凸起的一种冲压工序。
用途:a)增强产品强度b)代替其他子件(4)弯曲Bending弯曲:弯曲是把板材加工成具有一定的角度和形状的零件成形方法,材料在模具的作用下产生弯曲变形。
(5)卷边和翻边Revolving and Hemming卷边: 对板、圆筒或圆形容器或圆形容器的端部进行圆形卷边的加工。
翻边: 翻边是沿外形曲线周边将材料翻成侧立短边的一种冲压工序。
(6)冲沉孔Chamfering冲沉孔: 可借助模具在零件孔侧压出锥形沉孔或圆柱形沉孔, 一般用于装配沉头螺丝或去除毛刺。
(7)翻孔Turns Hole翻孔: 沿内圆孔周边将材料翻成侧立凸缘的冲压工序,一般用于薄片攻螺纹孔。
(8)切舌与切开/冲桥位Part Cutting & Bridge Forming切舌: 将材料沿轮廓局部而不是完全分离的一种冲压工序。
被局部分离的材料,具有工件所规定的一定位置,不再位于分离前所处的平面上。
切开/冲桥位: 将材料沿敞开轮廓局部而不是完全分离的一种冲压工序。
被切开而分离的材料位于或基本位于分离前所处的平面。
(9)拍披锋Deburring拍披锋: 运用模具清除剪切带来的锋利毛刺。
(10)拉深Deep Draw拉深: 把平直毛料或工序件变为空心件,或者把空心件进一步改变形状和尺寸的一种冲压工序。
拉深时空心件重要依靠位于凸模底部以外的材料流入凹模而形成的。
冲压件的设计考虑和优化方法

冲压件的设计考虑和优化方法冲压件(Stamping Parts)是广泛应用于汽车、电子、家电等工业领域的重要零件。
其设计的考虑和优化方法对于产品质量、成本和效率等方面具有重要影响。
本文将介绍冲压件设计的考虑因素以及优化方法,希望能够对读者有所启发。
首先,冲压件的设计需要考虑以下几个重要因素:材料选择、几何形状、工艺工序和模具设计。
材料选择是冲压件设计的首要因素之一。
选择合适的材料可以保证产品的强度、韧性和耐腐蚀性能,并且在生产过程中具有良好的可加工性。
在选择材料时,需要考虑产品使用环境、负荷条件以及成本等因素,以确保设计的冲压件满足产品的功能和性能要求。
几何形状的设计是冲压件设计的核心。
合理的几何形状设计可以确保产品的装配和使用功能,并且最大程度上减少材料的损耗和加工成本。
在几何形状设计过程中,需要考虑产品的结构强度、模具的可制造性以及产品的外观要求等因素。
同时,通过模拟分析和优化设计等方法,可以进一步提高产品的设计效果。
工艺工序是冲压件设计的重要考虑因素之一。
不同的冲压工艺需要设计相应的工序来实现产品的加工和成型。
在工艺工序设计中,需要考虑产品所需的冲压力、冲床的选型、模具的制造和维护等因素。
同时,合理的工艺选择可以最大程度上提高产品的生产效率和质量稳定性。
模具设计是冲压件设计中不可忽视的因素。
模具的设计质量直接影响到产品的成型质量和加工效率。
在模具设计中,需要考虑产品的几何形状、工艺工序、材料和模具的可制造性等因素。
合理的模具设计可以降低模具的制造成本,并提高产品的加工精度和质量稳定性。
除了以上提到的设计考虑因素外,冲压件设计还可以通过以下优化方法进行改进:1. 材料利用率的优化:通过几何形状的优化设计,可以最大程度地减少材料的浪费,提高材料的利用率。
例如,在设计冲孔件时,可以选择合适的孔型和布局,以减少剪切边缘的浪费。
2. 强度和刚度的优化:通过优化几何形状和加强筋的设计,可以提高冲压件的强度和刚度。
冲压件设计

冲压与模具设计说明书1.冲压件工艺性分析该冲压件材料为08钢,具有良好的冲压性能,适合冲裁。
该冲压件结构相对简单,孔径为10mm,孔与边缘之间的最小距离为7mm,所有尺寸均满足冲压工艺的要求,适合冲裁。
所有尺寸公差取IT13级,满足普通冲裁的经济精度要求。
综合上述,该冲压件的冲压工艺性良好,适合冲压加工。
图1-12.模具工艺方案的确定由图1-1可以看出,生产该冲压件的冲压工序为落料和冲孔。
根据上述工艺分析的结果,可以采用下述几种方案。
方案一:先落料,后冲孔,采用单工序模生产。
方案二:落料冲孔复合冲压,采用复合模生产。
方案三:冲压、落料级进行冲压,采用级进模生产。
方案一的模具结构简单,但生产效率低,不能满足大量生产对效率的要求。
方案二的冲压件精度及生产效率都高,但模具比较复杂,制造难度大,而且难以实现自动化。
方案三的生产效率高,操作方便,易于实现自动化,冲压精度也能满足要求。
因此,选择方案三。
3.模具结构形式确定(1)模具类型的选择根据上述方案,选用级进模。
(2)凹模结构形式采用整体凹模(3)定位方式的选择利用导料板倒料和侧刃定距。
(4)卸料、出件方式的选择采用弹性卸料和下出件方式。
(5)导向方式的选择选用对角导柱的滑动导向方式。
4. 主要设计计算(1)排样设计 由于该工件为冲裁件,且外形与孔型结构都比较简单,因此可以直接进行排样设计。
根据工件的结构,选用有废料的单直排,由表查的搭边值为2mm ,侧搭边值为2.5mm ,则条料宽度为B=26mm+12mm+1.5×2.5+1×1.5=43.25mm(侧刃定距时,条料宽度的计算公式为B=(L+1.5a+nb),a 市侧搭边值;n 是侧刃数量,这里取1)进距为L=12mm+12mm+2mm=26mm图1-2此工件只需落料和冲孔两道工序,因此在排样时,第一工位利用侧刃冲去等于进距的料边进行定距,第二工位冲孔,第三工位空位,第四工位落料,空位的目的是增大冲ф5mm 孔凹模和落外形凹模之间的壁厚,以保证凹模强度。
冲压件结构设计的注意事项

冲压件结构设计的注意事项序号图例注意事项改进前改进后、1、落料件节约金属合理设计工件形状,以利于节料避免尖角工件如有细长尖角,易产生飞边或塌角】工件不宜过窄工件太窄,冲模制造困难且寿命低开口槽不宜过窄/圆弧边与过渡边不宜相切节约金属和避免咬边2、切口件.切口处应有斜度避免工件从凹模中退出时舌部与凹模内壁摩擦3、弯曲件弯曲处切口窄料小半径弯曲时,为防止弯曲处变宽,工件弯曲处应有切口预冲月牙槽弯曲带孔的工件时,如孔在弯曲线附近,可预冲出月牙槽或孔,以防止孔变形,预冲防裂槽在局部弯曲时,预冲防裂槽或外移弯曲线,以免交界处撕裂)形状尽量对称弯曲件形状尽量对称,否则工件受力不均,不易达到预定尺寸弯曲部分压筋`可增加工件刚度,减小回弹坯料形状简单工件外形利于简化展开料形状)弯曲部分进行预切防止弯曲部分起皱增加支承孔刚度为保证弯曲后支承孔同轴,在弯曲时翻出短边、4、拉深件形状尽量简单并对称圆筒形、锥形、球形、非回转体、空间曲面,成形难度依次增加>法兰边宽度应一致拉伸困难,需增加工序,金属消耗大法兰边直径过大拉伸困难5、起伏件$压肋应与零件外形相近或对称压肋与零件外形相近压肋应对称6、组合冲压件以冲压件代替锻件制造简单、精度高。
冲压设计手册

冲压设计手册冲压是一种常见的金属加工工艺,广泛应用于汽车、电子、航空航天等行业中。
冲压设计手册是为了帮助工程师和设计师更好地理解冲压工艺,并提供设计准则和规范,以确保产品的冲压加工质量。
本手册将介绍冲压的基本原理、设计注意事项、常见问题及解决方案等内容,以期为冲压设计工作提供参考依据。
一、冲压原理冲压是通过冲压模具对金属板材进行加工,将板材进行变形成所需形状。
冲压过程包括拉伸、弯曲、压边、成形等工艺,需要考虑材料性能、模具设计、设备选择等因素。
在冲压过程中,需要注意材料的拉伸和压缩变形,以及冲压件的表面质量和尺寸精度。
二、冲压设计注意事项1. 材料选择:冲压件的材料选择需考虑其拉伸性能、塑性变形及硬度等因素,同时需满足产品的强度和耐磨要求。
2. 模具设计:冲压模具的设计需考虑成形工艺、模具结构、材料选择等因素,以确保冲压加工的精度和效率。
3. 设计几何:冲压件的设计几何需考虑成形难度、形状复杂度、壁厚变化等因素,以降低冲压成形难度。
4. 工艺规范:冲压工艺包括拉伸、压边、弯曲等工序,需制定合理的工艺规范,确保产品质量和生产效率。
5. 表面处理:冲压件的表面处理需考虑防锈、提高表面平整度等要求,选择合适的表面处理工艺。
三、常见问题及解决方案1. 材料断裂:材料断裂可能是由于成形难度大、材料本身缺陷等原因,可通过材料改进、模具结构优化等方式解决。
2. 冲压件翘曲:冲压件翘曲可能是由于冲压过程中内应力释放引起,可通过热处理、优化冲压工艺等方式解决。
3. 表面质量问题:冲压件的表面质量问题可能是由于模具结构不合理、冲压过程控制不当等原因,可以通过优化模具设计、规范冲压工艺等方式解决。
4. 尺寸精度问题:冲压件的尺寸精度问题可能是由于模具磨损、设备精度等原因,可以通过定期维护模具、使用高精度设备等方式解决。
四、结论冲压设计手册对于工程师和设计师来说是一份重要的参考资料,能够帮助他们更好地理解冲压工艺,有效地解决冲压设计中的各种问题。
冲压件设计要点

冲压件设计要点冲压件是一种常见的零件加工方法,广泛应用于汽车、航空航天、家电等行业。
冲压件的设计关键在于确保零件的功能、质量和成本的平衡,下面将介绍冲压件设计的要点。
一、材料选择在冲压件设计中,材料的选择是非常重要的。
需要考虑到材料的强度、韧性、耐腐蚀性等性能。
同时,还需要考虑到材料的可加工性和可用性,以确保生产过程的顺利进行。
二、冲压工艺冲压工艺是冲压件设计的核心。
需要根据零件的形状、尺寸和要求,选择合适的冲压方法和工艺参数。
冲压工艺包括模具设计、冲床选择、冲头选型、冲压顺序等方面。
三、模具设计模具是冲压件生产的关键工具。
模具设计需要考虑到零件的形状、尺寸和材料等因素。
合理的模具设计可以提高生产效率,减少材料浪费和工艺问题。
四、结构设计冲压件的结构设计要考虑到零件的功能需求和装配要求。
需要合理设计零件的形状、尺寸和连接方式,以确保零件的功能完整和装配可靠。
五、材料利用率材料利用率是冲压件设计的重要指标之一。
需要通过合理设计零件形状、减少余料和废料的产生,提高材料利用率,减少材料成本和环境污染。
六、工艺优化工艺优化是冲压件设计的关键环节。
通过优化冲床的工艺参数、改进模具结构和加工方法,可以提高生产效率,降低成本,提高零件的质量和一致性。
七、成本控制成本控制是冲压件设计的重要考虑因素。
需要在满足功能和质量要求的前提下,尽量降低材料、工艺和设备等成本,提高生产效率和经济效益。
八、质量控制质量控制是冲压件设计的重要目标。
需要通过合理设计零件形状、优化工艺参数和加强检验控制,确保零件的尺寸、形状和性能达到要求,提高产品质量和可靠性。
九、安全考虑安全是冲压件设计的重要方面。
需要考虑到操作人员的安全和设备的安全,合理设计工艺流程和工作环境,减少事故的发生。
十、环保要求环保要求是冲压件设计的重要考虑因素。
需要选择环保材料,减少废料和污染物的产生,提高资源利用率和环境保护意识。
总结起来,冲压件设计的要点包括材料选择、冲压工艺、模具设计、结构设计、材料利用率、工艺优化、成本控制、质量控制、安全考虑和环保要求等方面。
- 1、下载文档前请自行甄别文档内容的完整性,平台不提供额外的编辑、内容补充、找答案等附加服务。
- 2、"仅部分预览"的文档,不可在线预览部分如存在完整性等问题,可反馈申请退款(可完整预览的文档不适用该条件!)。
- 3、如文档侵犯您的权益,请联系客服反馈,我们会尽快为您处理(人工客服工作时间:9:00-18:30)。
冲压(Stamping)冲压是在常温下利用压力机并依靠模具对金属材料剪切,使之变形获得所需形状的工艺。
压力机属于锻压机的一类,冷冲压的压力机有机械压力机和液压压力机,常用的是机械压力机(冲床)。
冲压工艺(Stamping Process)(1)落料Cutting落料:从材料上沿着封闭轮廓分离出工件初胚的工艺。
(2)冲孔Punching冲孔:从工件上沿着封闭轮廓分离出废料,获得所需要的带孔零件的工序。
(3)压凸/压筋Embossing压凸/压筋:用凸模挤入工件的一面,迫使材料流入对面凹坑以形成凸起的一种冲压工序。
用途:a)增强产品强度b)代替其他子件(4)弯曲Bending弯曲:弯曲是把板材加工成具有一定的角度和形状的零件成形方法,材料在模具的作用下产生弯曲变形。
(5)卷边和翻边Revolving and Hemming卷边:对板、圆筒或圆形容器或圆形容器的端部进行圆形卷边的加工。
翻边:翻边是沿外形曲线周围将材料翻成侧立短边的一种冲压工序。
(6)冲沉孔Chamfering冲沉孔:可借助模具在零件孔侧压出锥形沉孔或圆柱形沉孔,一般用于装配沉头螺丝或去除毛刺。
(7)翻孔Turns Hole翻孔:沿内圆孔周围将材料翻成侧立凸缘的冲压工序,一般用于薄片攻螺纹孔。
(8)切舌与切开/冲桥位Part Cutting & Bridge Forming切舌:将材料沿轮廓局部而不是完全分离的一种冲压工序。
被局部分离的材料,具有工件所要求的一定位置,不再位于分离前所处的平面上。
切开/冲桥位:将材料沿敞开轮廓局部而不是完全分离的一种冲压工序。
被切开而分离的材料位于或基本位于分离前所处的平面。
(9)拍披锋Deburring拍披锋:利用模具清除剪切带来的锋利毛刺。
(10)拉深Deep Draw拉深:把平直毛料或工序件变为空心件,或者把空心件进一步改变形状和尺寸的一种冲压工序。
拉深时空心件主要依靠位于凸模底部以外的材料流入凹模而形成的。
(11)切边Cutting切边:为了得到精确的形状的零件,按预定的切断线将废料从零件上切去的加工。
冲压件设计的注意事项(一)材料选用及零件布局(1)材料选用根据厚度,强度,弹性要求,不同的应用场合选择合适的材料。
(2)冲压零件的布局优化设计,合理布局,争取采用无废料或少废料的排布方法。
(3)冲压件的形状在满足产品需求的情况下,尽可能简单,对称,使排样废料最少。
(二)零件厚度与加强筋(1)厚度为保证模具的寿命,产品的质量及材料在市场上的订购,冲压材料的厚度应取以下范围:铁料/不锈钢: 0.1≤t≤3 (mm)铜/铝:0.1≤t≤4 (mm)(2)加强筋对于较大或较长的钣金件,为提高其强度,应适当设计加强筋。
另外,在弯曲件的弯角处再作弯折,能起到筋条的加强作用。
(三)弯曲弯曲是依靠材料流动而不依靠材料分离,使用弯曲改变角度或形状的成形方法。
大多数需要成形的零件可以在普通压力机上用模具实现,也可以利用折弯机等专用设备进行成形加工。
材料在成形的作用下产生弯曲变形,变形区主要集中在下图abc区域内。
金属受拉力及应力作用,其过程可分为弹性变形阶段和塑性变形阶段。
弹性变形阶段:材料在成形的初始阶段,弯曲力不大,材料的内外层金属受拉应力作用未达到屈服极限产生弹性变形(图a)。
塑性变形阶段:当弯曲力继续增大,材料的弯曲率半径随着变小,材料的内外层金属由弹性变形阶段进入塑性变形阶段,然后塑性变形区逐步从材料的内外层金属向材料的厚度中心扩展变形,由弹性变形过渡为塑性变形(图bc)。
(1)常用折弯模具为了延长模具的寿命,零件设计时,尽可能采用圆角。
(2)折弯半径折弯过程中,内层压缩,外层拉伸,R角过大或过小皆不宜,过大回弹,过小则破裂。
随着折弯工艺的不断完善,很多厂商目前都可以做到零R角。
(3)折弯直边高度当弯曲90˚角时,弯曲件圆角区以外的直边高度H>2t时才能保证其质量。
(4)避免折弯在斜边上防止侧面(梯形)弯曲时产生裂纹或畸形。
应设计预留切槽,或将根部改为阶梯形。
槽宽K≥2t,槽深L≥t+R+K/2。
(5)U形折弯在U形弯曲件上,两弯曲边最好等长,以免弯曲时产生向一边移位。
如不允许,可设一工艺定位孔。
(6)确保足够的圆弧空间当a<R时,弯曲后,b面靠a处仍然有一段残余圆弧,为了避免残余圆弧,必须使a≥R。
(7)预留切口为防止圆角在弯曲时受压产生挤料后起皱,应设计预留切口。
(四)冲切与冲孔(1)最小冲孔直径和最小方孔边长(2)孔间距,孔边距,孔到折弯的距离以上距离通常取C≥3t(3)冲切缺口原则冲切缺口应尽量避免尖角,尖角形式容易减短模具使用寿命,且尖角处容易产生裂纹。
因此,产品设计尽可能加圆角。
(4)悬臂或狭槽结构/凸出或凹入部分冲切件的形状应尽量简单,尽量避免冲切件上的过长的悬臂狭槽。
对于一般钢A≥1.5t,对于合金钢A≥2t,对于黄铜或铝A≥1.2t。
(5)常用自攻螺钉底孔,翻边孔直径及翻边高度(五)冲压力的计算F=L t S*1.3F=Cutting pressure (冲压力)L=Shear plane border (剪切面周界)t=Material thickness (材料厚度)S=Shearing strength of by the punching shear material (被冲剪材料的抗剪强度kgf/mm²)EG:假如材料为SPCC,片材抗剪强度为35 kgf/mm²,最小冲剪力为:F=L t S*1.3=[(100+50)*2+(80+30)*2]*2.0*35*1.3=47320 kgf(六)冲切断面与毛刺(1)冲切断面因板材经模具剪切后,断面会有两种状态:平滑剪切面(光亮带)和剪切撕破断面(断面带)。
一般图纸在技术要求中极少注明冲切断面的要求,极少精密零件会要求光亮带的范围。
t - material thickness材料厚度A - smooth cutting face (bright band)光亮带B - tears face ( section belt)断面带R - tears radius剪切半径a - section angle断裂角C - burr height毛刺高度(2)拍披锋,去除毛刺注意毛刺的方向,避免伤人。
在加工生产时可以通过拍披锋工序去除毛刺。
(3)披锋/毛刺高度若设计未指定披锋要求,通常按以下披锋高度控制。
铜/铝: ≤12%t铁料: ≤10%t不锈钢: ≤8%t(七)表面处理方式电镀,拉丝,喷砂,烤漆,抛光,氧化等。
表面处理的标示方法详见GB/T 13911-2008。
(八)尺寸标注与公差(1)公差原则钣金件的公差需考虑产品的性能和经济两方面,可参考以下公差原则:(a)冲压件的设计尺寸基准尽可能与制造的定位基准相重合,这样可以避免尺寸的制造误差。
(b)冲压件的孔位尺寸基准,应尽可能选择在冲压过程中自始至终不参加变形的面或线上,且不要与参加变形的部位联系起来。
(c)对于采用多工序在不同模具上分散冲压的零件,要尽可能采用同一个定位基准。
(2)冲压件未注公差未注尺寸公差: GB/T 13914-92未注角度公差: GB/T 13915-92未注形位公差: GB/T 13916-92(九)冲压件的连接(1)焊接点焊(电阻焊),电弧焊,气体保护焊(CO2,Ar),激光焊,气焊等。
(2)铆接螺母铆接螺母常见的形式有压铆螺母柱,压铆螺母,拉铆螺母,涨铆螺母,浮动压铆螺母。
影响铆接质量的因素主要有:基材性能,底孔尺寸,铆接方式。
因此使用铆接螺母时注意以下事项:a)不要在铝板阳极氧化或表面处理之前安装钢或不锈钢铆装紧固件。
b)同一直线上压铆过多,被挤压的材料没有地方可流动,会产生很大的应力,使工件弯曲成弧形。
c)尽量保证在板的表面镀覆处理后再安装铆装紧固件。
d)M5,M6,M8,M10的螺母一般要点焊,太大的螺母一般要求强度较大,可采用弧焊,M4(含M4)以下尽量选用涨铆螺母,如是电镀件,可选用未电镀的涨铆螺母。
e)当在折弯边上铆压螺母时,为保证铆压螺母的铆接质量,需注意:铆孔边到折弯边的距离必须大于折弯的变形区;铆装螺母中心到折弯边内侧的距离L应大于铆装螺母外圆柱半径与折弯内半径之和,即L>D/2+r。
(3)凸焊螺母/点焊螺母凸焊螺母(点焊螺母)在钣金件结构设计中应用非常广泛,推荐使用焊接六角螺母GB/T 13681-92,焊接时有自定位结构。
(4)翻孔攻丝翻孔攻丝具有安装容易,拆卸方便,操作简单的优点。
常用的粗牙螺纹翻孔尺寸如下:(5)抽孔铆接抽孔铆接是钣金之间的铆接铆接方式,主要用于涂层钢板或者不锈钢板的连接,采用其中一个零件冲孔,另一个零件冲孔翻边,通过铆接使之成为不可拆卸的连接体。
优点:翻边与直孔相配合,本身具有定位功能,铆接强度高,通过模具铆接效率也比较高。
另外,为提高产品的强度和密封要求,可将其优化为:(6)托克斯铆接托克斯铆接是将两个板叠放在一起,利用模具进行冲压拉伸,主要用于涂层钢板或者不锈钢板的连接,它具有节省能源、环保、效率高等优点,以前通讯行业的机箱中采用这种铆接较多,但批量生产的质量控制较为困难,现在已经应用较少,不推荐采用。