奔驰A级车身结构及连接工艺解析
全铝车身维修探讨——胶粘铆接技术
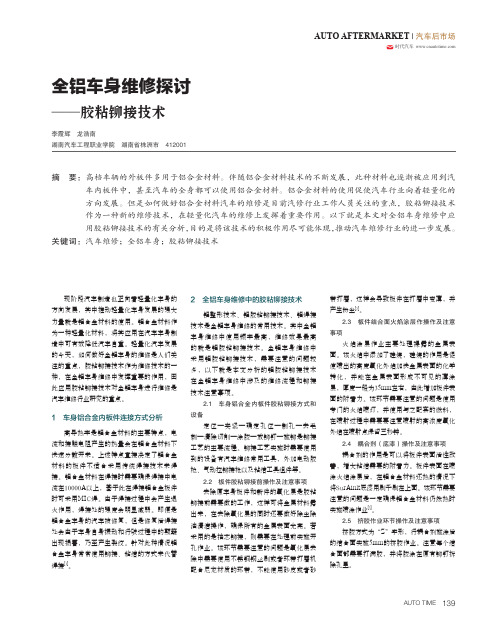
AUTO AFTERMARKET | 汽车后市场时代汽车 全铝车身维修探讨——胶粘铆接技术李霞辉 龙浩南湖南汽车工程职业学院 湖南省株洲市 412001摘 要: 高档车辆的外板件多用于铝合金材料。
伴随铝合金材料技术的不断发展,此种材料也逐渐被应用到汽车内板件中,甚至汽车的全身都可以使用铝合金材料。
铝合金材料的使用促使汽车行业向着轻量化的方向发展。
但是如何做好铝合金材料汽车的维修是目前汽修行业工作人员关注的重点,胶粘铆接技术作为一种新的维修技术,在轻量化汽车的维修上发挥着重要作用。
以下就是本文对全铝车身维修中应用胶粘铆接技术的有关分析,目的是将该技术的积极作用尽可能体现,推动汽车维修行业的进一步发展。
关键词:汽车维修;全铝车身;胶粘铆接技术现阶段汽车制造也正向着轻量化车身的方向发展,其中推动轻量化车身发展的强大力量就是铝合金材料的使用。
铝合金材料作为一种轻量化材料,将其应用在汽车车身制造中可有效降低汽车自重。
轻量化汽车发展的今天,如何做好全铝车身的维修是人们关注的重点,胶粘铆接技术作为维修技术的一种,在全铝车身维修中发挥重要的作用,因此应用胶粘铆接技术对全铝车身进行维修是汽车维修行业研究的重点。
1 车身铝合金内板件连接方式分析高导热率是铝合金材料的主要特点,电流和接触电阻产生的热量会在铝合金材料下快速分散开来。
上述特点直接决定了铝合金材料的板件不适合采用传统焊接技术来焊接。
铝合金材料在焊接时需要确保焊接中电流在10000A以上,基于此在焊接铝合金板件时可采用MIC焊。
由于焊接过程中会产生退火作用,焊接处的强度会明显减弱。
即便是铝合金车身的汽车被修复,但是修复后焊接处会由于车身自身振动和行驶过程中的颠簸出现损害,乃至产生裂纹。
针对此种情况铝合金车身常常使用铆接、粘结的方式来代替焊接[1]。
2 全铝车身维修中的胶粘铆接技术铝整形技术、铝胶粘铆接技术、铝焊接技术是全铝车身维修的常用技术。
其中全铝车身维修中使用频率最高,维修效果最高的就是铝胶粘铆接技术。
PS48300-3B-2900、PS48600-3B-2900、PS48300 -3B-1800用户手册

艾默生网络能源有限公司 地址:深圳市南山区科技工业园科发路一号 邮编:518057 公司网址: 客户服务热线:4008876510 E-mail: service@
交流电源设备的安装,必须遵守相关行业的安全规范,进行交流设备安装的人员,必须具有高压、交流电等作业资 格。 操作时严禁在手腕上佩带手表、手链、手镯、戒指等易导电物体。
发现机柜有水或潮湿时,请立刻关闭电源。在潮湿的环境下操作时,应严格防止水分进入设备。
安装过程中不能容许操作的开关和按扭上,必须挂上禁止标识牌。
负载下电与电池保护
本电源系统具有负载下电与电池保护功能。负载下电即电源系统交流停电,由电池供电的情况下,电池电压下降到 44V(负载下电电压值可设,设置方法见 4.8.2 设置电池参数中设置下电保护参数一节)时电源系统自动切断非重 要负载,以确保电池能更长时间地支持重要负载供电;电池保护为当电池电压下降到 43.2V(电池保护电压值可设, 设置方法见 4.8.2 设置电池参数中设置下电保护参数一节)时电源系统自动切断电池,以避免蓄电池因过放电而影 响电池寿命。 本系统出厂设置为启动电池保护与负载下电功能,意味着交流长时间停电或设备故障时可能出现负载下电与电池保 护。用户应根据负载重要性选择哪些负载为非重要负载,接入负载下电支路,启动负载下电功能;相对比较重要的 负载应接到电池保护支路。对于特别重要的负载,则应考虑硬件取消电池保护功能,以确保供电可靠性。 取消电池保护功能的方法为: 1.硬件取消电池保护:将 M500S 监控模块 J427 接口上的信号线拔下,并做好取消电池保护标识。M500S 监控模 块位置和接口说明见 2.4.2 连接信号线。 2.软件取消电池保护:将监控模块电池参数中的“电池保护允许”一项设置为“否”,具体方法见 4.8.2 设置电池 参数中设置下电保护参数一节。
车身A级(Class-A)曲面模型的构造
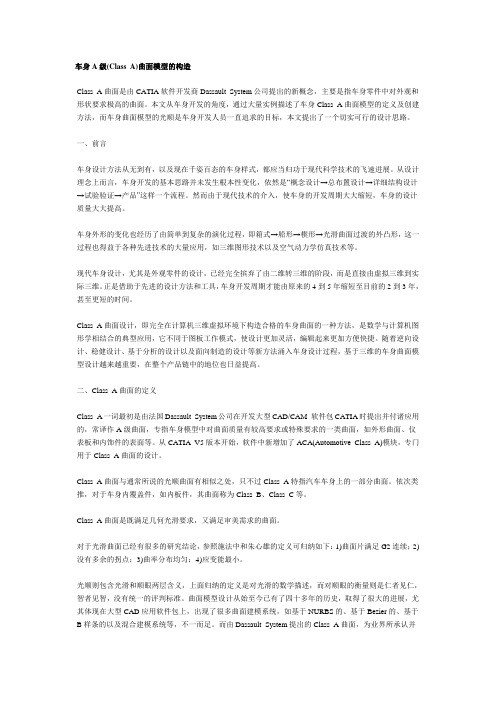
车身A级(Class A)曲面模型的构造Class A曲面是由CATIA软件开发商Dassault System公司提出的新概念,主要是指车身零件中对外观和形状要求极高的曲面。
本文从车身开发的角度,通过大量实例描述了车身Class A曲面模型的定义及创建方法,而车身曲面模型的光顺是车身开发人员一直追求的目标,本文提出了一个切实可行的设计思路。
一、前言车身设计方法从无到有,以及现在千姿百态的车身样式,都应当归功于现代科学技术的飞速进展。
从设计理念上而言,车身开发的基本思路并未发生根本性变化,依然是“概念设计→总布置设计→详细结构设计→试验验证→产品”这样一个流程。
然而由于现代技术的介入,使车身的开发周期大大缩短,车身的设计质量大大提高。
车身外形的变化也经历了由简单到复杂的演化过程,即箱式→船形→楔形→光滑曲面过渡的外凸形,这一过程也得益于各种先进技术的大量应用,如三维图形技术以及空气动力学仿真技术等。
现代车身设计,尤其是外观零件的设计,已经完全摈弃了由二维转三维的阶段,而是直接由虚拟三维到实际三维。
正是借助于先进的设计方法和工具,车身开发周期才能由原来的4到5年缩短至目前的2到3年,甚至更短的时间。
Class A曲面设计,即完全在计算机三维虚拟环境下构造合格的车身曲面的一种方法,是数学与计算机图形学相结合的典型应用,它不同于图板工作模式,使设计更加灵活,编辑起来更加方便快捷。
随着逆向设计、稳健设计、基于分析的设计以及面向制造的设计等新方法涌入车身设计过程,基于三维的车身曲面模型设计越来越重要,在整个产品链中的地位也日益提高。
二、Class A曲面的定义Class A一词最初是由法国Dassault System公司在开发大型CAD/CAM 软件包CATIA时提出并付诸应用的,常译作A级曲面,专指车身模型中对曲面质量有较高要求或特殊要求的一类曲面,如外形曲面、仪表板和内饰件的表面等。
从CATIA V5版本开始,软件中新增加了ACA(Automotive Class A)模块,专门用于Class A曲面的设计。
小家碧玉
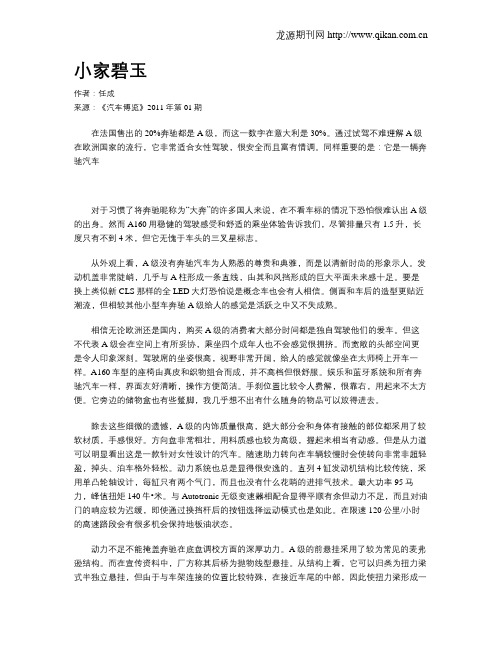
小家碧玉作者:任成来源:《汽车博览》2011年第01期在法国售出的20%奔驰都是A级,而这一数字在意大利是30%。
通过试驾不难理解A级在欧洲国家的流行,它非常适合女性驾驶,很安全而且富有情调。
同样重要的是:它是一辆奔驰汽车对于习惯了将奔驰昵称为“大奔”的许多国人来说,在不看车标的情况下恐怕很难认出A级的出身。
然而A160用稳健的驾驶感受和舒适的乘坐体验告诉我们,尽管排量只有1.5升,长度只有不到4米,但它无愧于车头的三叉星标志。
从外观上看,A级没有奔驰汽车为人熟悉的尊贵和典雅,而是以清新时尚的形象示人。
发动机盖非常陡峭,几乎与A柱形成一条直线,由其和风挡形成的巨大平面未来感十足。
要是换上类似新CLS那样的全LED大灯恐怕说是概念车也会有人相信。
侧面和车后的造型更贴近潮流,但相较其他小型车奔驰A级给人的感觉是活跃之中又不失成熟。
相信无论欧洲还是国内,购买A级的消费者大部分时间都是独自驾驶他们的爱车。
但这不代表A级会在空间上有所妥协,乘坐四个成年人也不会感觉很拥挤。
而宽敞的头部空间更是令人印象深刻。
驾驶席的坐姿很高,视野非常开阔,给人的感觉就像坐在太师椅上开车一样。
A160车型的座椅由真皮和织物组合而成,并不高档但很舒服。
娱乐和蓝牙系统和所有奔驰汽车一样,界面友好清晰,操作方便简洁。
手刹位置比较令人费解,很靠右,用起来不太方便。
它旁边的储物盒也有些蹩脚,我几乎想不出有什么随身的物品可以放得进去。
除去这些细微的遗憾,A级的内饰质量很高,绝大部分会和身体有接触的部位都采用了较软材质,手感很好。
方向盘非常粗壮,用料质感也较为高级,握起来相当有动感。
但是从力道可以明显看出这是一款针对女性设计的汽车。
随速助力转向在车辆较慢时会使转向非常非超轻盈,掉头、泊车格外轻松。
动力系统也总是显得很安逸的。
直列4缸发动机结构比较传统,采用单凸轮轴设计,每缸只有两个气门,而且也没有什么花哨的进排气技术。
最大功率95马力,峰值扭矩140牛•米。
奔驰乘用车最新车身技术
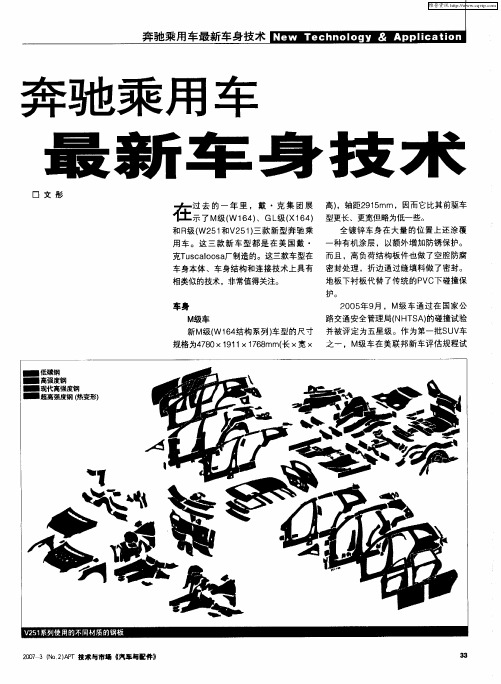
20 N )P 0 7 3( 2A T技术与市场 《 o 汽车与配件 》
3 3
维普资讯
霜夏
豆习 奔驰乘用 车最新车身技 术
G 车型量有M级车派生 出来 的 L
M级车已经做了更新揍代,现在以第二代产品 R 级车不久还将I2 种结构长度提供德国市场
保证长期品质和价值稳定) 基础上喷涂一 GL 级基 于一种 自承载 式车 身 。车 R 级车身涂蓝色标记的材料量双相钢。与纵梁 层耐刮划的清漆。 相连接的前横梁为挤压铝型材 身因对钢材做了明智的轻结构处理而达
到高碰撞性。高碰撞性的乘 员舱 以其前
后变形缓冲区而成为乘员保护系统的基
前部和尾部模件
G 车
奔驰GL 级车( 1 4 X 6 结构系列) 在其车 身结构中是一种加长的M级,并作为一种 高级7 座越野汽车提供。汽车的尺寸规格 为5 8 12 14 mm( X X高) 0 8 9 0 0 X X8 长 宽 ,
轴距3 7 m 0 5 m。
下衬板代替了传统P C下碰撞保护。汽 V 车的涂漆 。对于作为标准工艺 的所有涂 金属漆和单色漆 ,都在纳米( a o技术( N n)
为 “ 豪华运动型多功能车” ,一种应兼
备一辆四门双排座高级运动车、S V U 、旅 行车和厢式车要求的汽车。 自承载式车身是由高强度和最高强度 的钢合金组成 。应满足奔驰在被动安全 性、可靠性、舒适性和轻结构等各个方 面的要求。这种车身应能在发生碰撞 , 事故时吸收高冲击力 ,并最大限度地提
投放市 场
验(s N A — e tb u — C P T s 5不仪在正面碰撞而 )
该车所有的车身面板均采用全镀锌 钢板 ,并视应用范围而补充做了有机涂 层。车身的某些高负荷 区额外地做 了空 腔 防腐密封保护。车身的焊接处特别做
汽车焊装课件

图1-1一系列新技术的应用使得车身上钢材得以减薄并提高了安全性
1.2.1镀层钢板
在现代汽车生产中,车身上使用得最多的还是普通低碳钢,低碳钢板具有很好的塑性 加工性能,强度和刚度也能满足汽车车身的要求,同时能满足车身拼焊的要求,因此 在汽车车身上应用很广(图1-2)。 图1-2 低碳钢板目前镀锌钢材已在汽车行业中被普遍采用,同时,各企业需要在产品与 利润之间找到一个平衡点,造成的现状是在高端车型上均采用双面镀锌钢板,在中级 家用经济型轿车上不同的厂家有不同的选择,有些车型上普遍采用双面镀锌钢材,有 些车型上部分零件(主要是门盖等覆盖件)采用双面镀锌或外表面单面镀锌钢材,入 门级轿车普遍采用冷轧钢材,极少一部分零件上采用单面镀锌钢材。镀锌钢材主要采 用电镀锌和热镀锌两种镀锌工艺。 电镀就是利用电解,在板材件表面形成均匀、致密、结合良好的金属或合金沉积层的 过程。一般电镀锌工艺处理后板材表面的镀锌层厚度为5~15μm,镀锌层内锌含量约在 95%左右,因为在电镀锌工艺过程中板材处于常温状态,所以也叫冷镀锌。电镀锌的 优势是镀层薄、镀锌量少、成本低。 热镀锌也叫热浸锌或热浸镀锌,是一种有效的金属防腐方式,主要用于各行业的金属 结构设施,是将除锈后的钢材浸入500℃左右的锌液中,使钢材表面附着锌层,从而起 到防腐的目的。 热镀锌工艺流程:成品酸洗-水洗-加助镀液-烘干-挂镀-冷却-钝化-清洗 -打磨-热镀锌完工。热镀锌是由较古老的热镀方法发展而来的,自从1836年法国把热
1.3车身总成结构
车身总成又叫白车身总成,是指焊装生产任务完结后的最终交付产品,是由车身各分 总成通过既定工艺连接而成的。简单来讲,车身总成是车身下部总成(地板总成)与 左右侧围总成、顶盖等通过定位焊、激光焊以及结构胶连接后,并将左前门、左后门、 右前门、右后门、发动机舱盖、行李舱盖以及左右前翼子板总成通过螺栓紧固联接安 装完成之后的产品 。 通过流程图(图1-3),可以很明了地看出车身总成与各分总成之间的关系。
汽车车身制造工艺
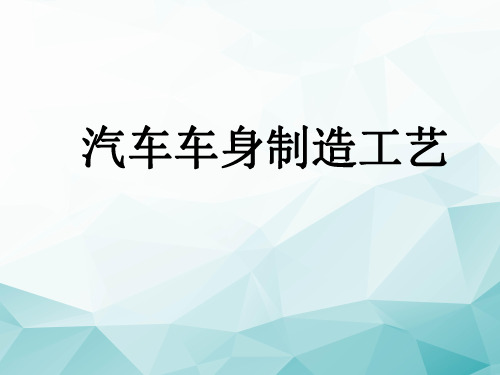
冲压 焊装 涂装 总装
重庆力帆冲压车间 2000吨的液压机
冲压 焊装 涂装 总装
重庆力帆冲压车间 切边、包边压机
冲压 焊装 涂装 总装
检具
零件冲压完成后,需要进行检验,以保证产品 的合格性,避免造成产品报废和后续工序的无 用。检具的尺寸要求和产品的理论数据一致或 留适当的公差。
冲压 焊装 涂装 总装
冲压工序中最重要的东西是冲压机床和模具,一般 的冲压 机床有2000吨、1600吨、1000吨、800吨、500吨位的,甚至还有 5000吨的,这个重量从高处砸下来相当于十架波音550座747的重 量。每一个工件都有一套模具,把各种模具装到冲压机床上就可 冲出各种的工件。每一个工序大多都是先经过冲压成形,然后再 经过冲孔、切边、翻边、整型等等工序,最后才会成为所需要的 工件。
冲压 焊装 涂装 总装
上海大众汽车三厂车身车间 左右侧框外板与底板,及侧框与车顶横梁的焊接拼焊线
冲压 焊装 涂装 总装
上海大众汽车三厂车身车间 左右侧框外板与底板,及侧框与车顶横梁的焊接拼焊线
冲压 焊装 涂装 总装
上海大众汽车三厂车身车间 左右侧框外板与车顶外板的激光焊接线
冲压 焊装 涂装 总装
冲压 焊装 涂装 总装
上海大众汽车二厂总装车间后桥装配
冲压 焊装 涂装 总装
上海大众汽车二厂总装车间五工段板链线 主要为产品车加液、注油
冲压 焊装 涂装 总装
上海大众汽车三厂总装车间的仪表板模块安装
冲压 焊装 涂装 总装
上海大众汽车三厂总装车间可旋转吊车架
冲压 焊装 涂装 总装
重庆力帆总装车间备件台
中华汽车焊装车间
由德国KUKA公司设计制造,38台机器人可进行大批量、系列化、多品 种、全柔性、混流生产,自动化率达到20%。
A级曲面全面介绍

A级曲面全面介绍(转贴)在整个汽车开发的流程中,有一工程段称为Class A Engineering,重点是在确定曲面的质量可以符合A级曲面的要求。
所谓A级曲面的定义,是必须满足相邻曲面间之间隙在0.005mm 以下(有些汽车厂甚至要求到0.001mm),切率改变( tangency Change ) 在0.16度以下,曲率改变(curvature change) 在0.005 度以下,符合这样的标准才能确保钣件的环境反射不会有问题。
a-class包括多方面评测标准,比如说反射是不是好看、顺眼等等。
当然,G2可以说是一个基本要求,因为g2以上才有光顺的反射效果。
但是,即使G3了,也未必是a-class,也就是说有时虽然连续,但是面之间出现褶皱,此时就不是a-class通俗一点说,class-A就必须是G2以上连接。
G3连续的面不一定是CLASS-A曲面。
汽车业界对于a class要求也有不同的标准,GM要求比TOYOTA,BMW等等要低一些,也就是说gap和angle要求要松一些。
关于A-class surfaces,涉及曲面的类型的二个基本观点是位置和质量。
位置——所有消费者可见的表面按A-Surface考虑。
汽车的console(副仪表台)属于A-surf,内部结构件则是B-surf。
质量——涉及曲面拓扑关系、位置、切线、曲面边界处的曲率和曲面内部的patch结构。
有一些意见认为“点连续”是C类,切线连续是B类,曲率连续是A类。
而我想更加适当地定义为C0、C1和C2,对应于B样条曲线方程和它的1阶导数(相切=C1)和它2阶导数(曲率=C2)。
因此一个A-surf有可能是曲率不连续的,如果那是设计的意图,甚至有可能切线不连续,如果设计意图是一处折痕或锐边,(而通常注塑或冲压不能有锐边,因此A-suuf一定是切线连续(C1)的)。
第二种思想以汽车公司和白车身制造方面的经验为基础,做出对A-surf更深刻的理解。
铝车身连接工艺方法大全
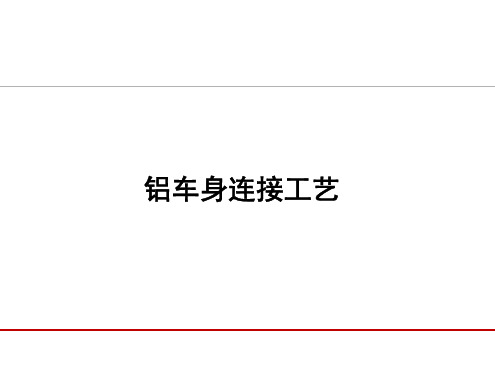
D
铝点焊焊接形式及焊接原理与普通钢板点焊相同只是焊接设 备控制功能不同
D
2、普通铝点焊焊接设备
普通铝点焊对钣件焊接边宽度要求更宽D=20~25mm(普通钢板14~16),其它 焊钳通过空间同普通钢板点焊
4、普通铝点焊焊接特点及优点
1、结合铝特性,普通铝点焊焊接铝板厚度有限(小于2mm),普通铝点焊只 适合焊接门盖(如:克莱斯勒RS前盖,福特F150前盖)等铝薄板焊接;且容易产生 焊接质量问题;
结合铝本身焊接特性,要求铝焊接设备主要输出参数具备如下特征: 1、焊接电流: 30KA~50KA(普通点焊8KA~15KA) 2、焊接压力:500~700公斤力(普通点焊: 200~450 ) 3、焊接时间:5~10周波(普通点焊8~25) 控制更迅速、精确 4、电极头及时清理防止 氧化物粘连,电极水冷速度是普通点焊的2倍 以上要求对焊接控制器要求极高,目前国内只有进口美国梅达铝点焊 焊接控制器
钢板
铝型材 铝型材 铝冲压件 CT6前保:铝型材拉弯成形 CT6侧边梁:铝型材
整体铸铝件
特斯拉铝下车身
铝车身连接工艺— 车身结构
铝车身连接工艺— 焊装工序及工艺方法
1、铝车身结构 结合现有几款铝车身:
1)前后4个减震器座 均采用整体铸铝加工件, 2)前后纵梁采用普通铝型材(捷豹XFL后纵梁采用热成型高强钢板) 3)电动车地板结构简单(横平竖直) 侧边梁,横梁 直接采用铝型材 4)发苍部分横梁 采用铝型材 拉弯 ,结构复杂的 采用铸铝加工件 5)上车身因造型复杂 大部分 采用 铝冲压件 6)B柱加强板 采用高强钢板 或热成型高强钢板
2 3 4 5 6 7
流钻工艺FDS 冷金属过渡焊 接CMT 普通铝点焊 DeltaSpot电 阻焊 Clinch连接 /TOX连接 铝板连接黏合 剂
奔驰豪华商傍车制造技术解密

奔驰豪华商傍车制造技术解密作者:来源:《汽车与运动》2012年第04期3月2日,福建奔驰举行首届技术开放日活动,全面展示了梅赛德斯一奔驰严谨精湛的造车工艺,作为戴姆勒集团亚洲、大洋洲地区惟一的商务车制造基地,也是产品线最全的基地,福建奔驰生产的商务车完全依据梅赛德斯一奔驰研发系统(MDS)和梅赛德斯一奔驰生产系统(MPS)的标准进行制造,保证了福建奔驰与梅赛德斯一奔驰全球标准的统一。
车身焊接工艺——车身强度和精度的基石焊接工艺是将一个个车身部件连接在一起构成车身本体。
焊接工艺决定了车身的强度和精度,当碰撞不可避免地发生时,除了安全带、安全气囊等,车身结构才是最本质、最重要的。
而且,车身精度是决定整车装配质量的基础。
福建奔驰在车身精度控制上执行“一毫米工程”,即白车身整车尺寸精度要控制在正负一毫米内。
对于车身长度为7345mm的大型商务车凌特也不例外。
福建奔驰是国内商务车制造领域中惟一使用激光焊接技术的企业,而凌特也是国内惟一使用该技术的商务车。
凌特的激光焊缝长达35米,主要用于顶盖、侧围以及底板的拼焊,与9133多个焊点相结合,保证了凌特整体尺寸的精确性和车身强度。
涂装工艺——车身美观及车身耐用性的保障涂装工艺不仅仅关系着美观的面子问题,更重要的是关系着车辆的防腐、减噪等实际问题。
在这里我印象最为深刻的就是PVC自动喷涂工艺。
汽车在高速行驶过程中,路面的砂石不可避免地会对车身底板及车身下部产生撞击和冲刷,使车身底板尤其是轮罩等部位的表面涂层受损而失去防腐蚀能力。
为提高车身的使用寿命、乘坐的舒适性和车身缝隙间的耐腐蚀性,需要在车身底板下表面,尤其是易受石击的轮罩和挡泥板表面,增涂具有抗石击性能的PVC 或防音漆。
福建奔驰的车身底板采用机器人自动喷涂PVC和防音漆。
设备能够自动识别车型,并自动控制喷涂流量。
PVC和防音漆材料的覆盖范围和厚度,均严格按照梅赛德斯一奔驰的标准进行实施,可使福建奔驰产品车身底盘的防腐蚀、防撞击、降噪音等功能达到一流水平。
汽车装配的工艺线路

汽车装配的工艺线路汽车装配的工艺线路是指按照一定的顺序和步骤,将各种零部件和组件装配到汽车车身上的一条装配生产线。
下面我将详细介绍汽车装配的工艺线路。
汽车装配的工艺线路一般分为车身车间、总装车间和整车调试三个阶段。
车身车间是指将各种车身焊接件的装配成型,总装车间是指将车身和其他组件进行总装,整车调试是指对已组装完成的汽车进行各项功能性和性能性的调试。
首先是车身车间的装配工艺线路。
在车身车间,主要是将前后两个焊接工位分开进行汽车车身的组装和焊接。
首先,在焊接工位上,通过自动焊接机器进行车身的拼接和焊接,确保车身的稳固性和结构的完整性。
接下来,将经过焊接的车身进行质量检验,确保焊接质量达到要求。
然后,将车身送入装配工位,装配座椅、车门、车窗等车身附件。
最后,车身送入喷涂工位,进行汽车车身的涂装。
接下来是总装车间的装配工艺线路。
总装车间是将车身和其他组件进行总装的地方。
首先,将车身通过电梯或者传送带送入总装线,并将车身与发动机进行连接。
然后,安装座椅、仪表盘、方向盘、中央控制台等内饰装置。
接下来,按照顺序逐步安装车门、车窗、雨刷器、车灯等外部附件。
然后,安装车轮、制动器等底盘配件。
最后,进行电器设备的安装和连接,并进行引擎的测试。
最后是整车调试的装配工艺线路。
整车调试是对已经装配完成的汽车进行功能性和性能性的调试。
首先,进行车身检查,确保车身的外观质量和内部结构的完整性。
然后对电气系统进行测试,包括灯光、音响、空调等。
接下来,进行发动机的启动和性能测试,测试动力输出和燃油消耗情况。
然后,进行底盘和悬挂系统的测试,检查制动器、悬挂和转向系统的正常工作。
最后,进行整车的检测和测试,包括行驶稳定性、安全性等。
总的来说,汽车装配的工艺线路涵盖了车身车间、总装车间和整车调试三个阶段,每个阶段都有相应的装配工序和步骤。
通过这一连串的装配工艺,汽车零部件和组件被有序地组装到汽车车身上,最终形成一辆完整的汽车。
这些工艺流程不仅需要高效的机器设备和生产线,也需要高水平的工艺技术和操作技能,以确保汽车的质量和安全性。
全球最先进的量产车电子电气架构——奔驰STAR3分析
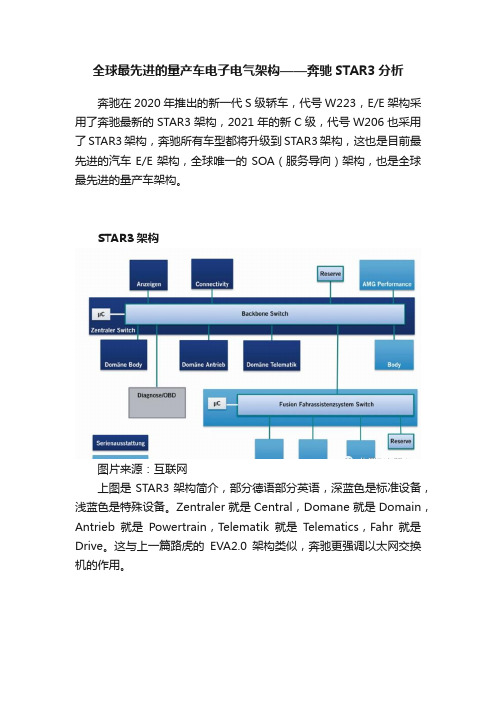
全球最先进的量产车电子电气架构——奔驰STAR3分析奔驰在2020年推出的新一代S级轿车,代号W223,E/E架构采用了奔驰最新的STAR3架构,2021年的新C级,代号W206也采用了STAR3架构,奔驰所有车型都将升级到STAR3架构,这也是目前最先进的汽车E/E架构,全球唯一的SOA(服务导向)架构,也是全球最先进的量产车架构。
STAR3架构图片来源:互联网上图是STAR3架构简介,部分德语部分英语,深蓝色是标准设备,浅蓝色是特殊设备。
Zentraler就是Central,Domane就是Domain,Antrieb就是Powertrain,Telematik就是Telematics,Fahr就是Drive。
这与上一篇路虎的EVA2.0架构类似,奔驰更强调以太网交换机的作用。
图片来源:互联网奔驰STAR3架构,还是英语和德语混合,Fahrwerk就是底盘Chassis。
图片来源:互联网与SOA对应的是信号导向型架构,典型如特斯拉的Model 3,也就是左图。
这是奔驰以舒适网络ECU做的对比,服务导向型与信号导向型对比。
还是德语和英语混杂,德语的k基本可对应英语的c,Bedien是Operator,anforderungen就是requirement。
奔驰升级网关ECU到带有多个以太网交换器的ECU,内部包含了任务调度功能。
图片来源:互联网理解SOA需要深入了解AUTOSAR。
上图就是用AUTOSAR的方式解释SOA。
AUTOSAR标准制定的目标之一,是希望在应用程序级别能做到可复用性,也就是说,我们可以基于现有的模型去创建更多,更复杂,或者基于特定项目需求的模型资源,而无需从零开始设计每一个部分。
基于这个想法,衍生出了类型-原型(type-prototype)的概念。
同时,开发人员也能创建出软件组件的分层模型,无论你的设计有何种的复杂度,软件组件SWC的任意设计,都不会对整个系统运行时的行为有任何影响,实际行为完全定义在一个个独立的软件组件当中。
2022款奔驰A级配置解读,入门级豪华品牌轿车,哪款更具性价比?

2022款奔驰A级配置解读,入门级豪华品牌轿车,哪款更具性价比?作为BBA阵营入门级车型的奔驰A级三厢轿车,虽然在国内人气上不如同级别的奥迪A3,但凭借更亲民的价格和奔驰品牌的号召力,还是吸引了不少年轻消费者。
本文将针对目前在售的国产2022款版奔驰A级整体,以及全系不同版本车型之间配置差异进行详细对比解读,希望能够给消费者提供一些参考价值。
2022款奔驰A级继续提供四个版本车型,包含180L和200L两种动力,售价区间21.48-26.48万元,部分市场终端有着较大幅度优惠,其中顶配A 200L 运动轿车时尚型经过配置调整,相比之前增配电动座椅以及腰托功能,车辆的售价同步迎来变化,售价变更为26.48万元。
车系中的A 180L 运动轿车和A 200L运动轿车动感型,相对为更多消费者所关注。
车身配色2022款奔驰A级全系共提供7种车身配色,作为一款主要面对年轻消费者的紧凑型轿车,配色类型比较丰富,同时包含常规的白、银、黑,以及山灰、宝石蓝、熔岩红等个性化配色,其中入级的A180L轿车没有熔岩红和瑰砾金两种配色。
外观外观方面,2022款奔驰A级继续保持着之前设计,车型主打年轻运动风格,虽然尺寸上相比C级要缩水不少,但在整体轮廓和诸多细节部分的处理,依然融入了经典的奔驰元素,具有相当高的品牌辨识度。
全系除入门版的A 180L外,其它三款配置车型外观均加入了运动套件,包括中网、车身包围、轮毂的位置都有所不同,视觉效果较A 180L显得更时尚化一些。
车头部分,这一代奔驰A级借鉴了大哥CLS上的设计,尤其是全包式前脸,配合扁平化的六边形中网和两侧上扬的大灯,营造出几分怒视感。
A 180L中网内部采用密集的黑色网格,车标为普通镂空样式;三款运动轿车中网升级为更流行的点阵式镀铬结构,中间车标也调整为封闭样式,看起来更显档次。
除此之外,虽然A 180L车前包围也采用的是三段式设计,但运动轿车两侧更大的导风槽,配合内部两根黑色辐条和下格栅底部凸出的边框,进一步提升前脸的视觉张力。
汽车制造中的连接技术整理
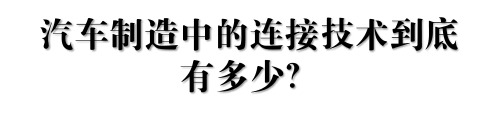
1 2 3 4 5 6 7 8研究表明:钢铝连接接头成本约为白车身成本的10%~20%,连接技术的正确使用对车身降成本意义重大。
积累钢铝混合连接技术设计开发/CAE/Safety/同步工程经验,有利于支持后续类似新车型开发。
汽车轻量化已成为汽车行业发展趋势,钢铝混合车身的设计开发已经在部分汽车公司开始研究和实施应用。
研究表明:钢铝连接接头成本约为白车身成本的10%~20%,连接技术的正确使用对车身降成本意义重大。
积累钢铝混合连接技术设计开发/CAE/Safety/同步工程经验,有利于支持后续类似新车型开发。
1. 铝合金点焊焊接接头形式,如图1 所示。
铝合金熔点低、热膨胀率及导电率高,表面易氧化,铝点焊需大电流、短时间、多脉冲、大电极压力,对焊机、变压器及焊枪的供电要求高,大电极压力需要焊枪结构坚固可靠[1]。
因此,铝合金点焊设备费用很高,国内汽车制造厂应用较少。
通用汽车在量产车型中应用,由于焊钳体积较大,无法手持,需要机器人自动化实现。
图2 示出铝合金点焊焊钳。
图1 铝合金电焊接头形式图2 铝合金点焊焊钳2. 铝弧焊(MIG)焊接接头形式,如图3 所示。
铝熔点低,550~660 ℃,热膨胀系数是钢的2 倍,导热性是钢的4 倍,因此,焊接变形及焊接应力增加,需要采用低热输入量焊接工艺(如CMT 技术)。
由于铝合金吸热后极容易热应力集中,造成板件开裂。
目前主要采用2 种方式减少MIG 焊时所产生的热量,即机械截断式和电源截断式,通过引弧-熄弧-再引弧的重复方式减小热量的输入。
图3 MIG接头形式目前,MIG 在车身上应用比较广泛,如全铝前防撞梁、吸能盒等碰撞安全关键零部件;另外,铝铸件与铝型材之间也可以通过MIG 进行连接,图4 示出MIG 产品。
图4 MIG产品3.自穿钉铆接(SPR)SPR(Self-piercing rivet)属于冷连接技术,接头形式,如图5 所示。
其独特的连接方式,使其可以有效克服铝合金、镁合金、钛合金等轻金属材料导电、导热性快,热容小,易氧化,难以采用传统的连接方法进行焊接的缺点。
汽车五大阶段研发及制造的四大工艺详解

汽车五大阶段研发及制造的四大工艺详解汽车材料网2017-05-04以前有个朋友问过我,国内的很多车型都是抄袭的,为什么还需要那么多研发人员,研发过程为什么还需要那么多时间?在此向各位车友讲述国内一个车企造车的故事,然后你就会明白,造车真不是很简单的。
想当年这家企业刚进入汽车业,就夸下了“2010年做到中国第一,2015年做到世界第一”的“豪言壮语”。
于是举全公司之力,完全自主设计了一款车型,样品完成后,广邀其全国经销商对这款车进行评价,99%的经销商都太“震惊”了,这车也能卖,他们对这款车没有点滴信息?好在这家公司做出了很英明的决定,没有把此款车型投向市场。
很快这几公司认识到模仿是必须经历的过程,从copy 到change再到design,这也是日韩汽车走过的过程。
此后,此公司做出了一个战略选择,他们开始了大力copy工作,copy的车型从A00级车到C级车,从MPV到SUV一共十几款车,而且这么多车型的研发工作基本上都是同时进行的,并再次提出了一年研发3—4款车型的“豪言壮语”。
但是他们没有认识到copy并不是那么简单,同样copy也需要积累的。
当他们把他们copy的第一款车拿到车展的时候,业内的人都笑了,太粗糙了吧?这个车型只会把自己的品牌永远的毁掉。
但是这款车连模具都开了,继续向市场推广,还是废掉重来?这可是好几亿。
这个时候,这家企业真正意识到“模仿也不是个简单的活”,他们立即停止了对奔驰等车型的仿制工作,全部精力投入到一款A级车的研发中来,他们用几个亿RMB和三年的时间,买了一个重要的教训。
给大家讲述这个故事的目的是说明:汽车研发是一个很复杂的系统工程,甚至需要上千人花费几年的时间才能完成;一款汽车从研发到投入市场一般都需要5年左右的时间。
不过随着技术的不断进步,研发的周期也在缩短,当然,我们说的是正向设计,事实上很多国内的厂家都是逆向设计,但即使是逆向设计同样也需要很多的时间。
我们可以仿制别人的外观,但是我们无法仿制别人的工艺,我们依然需要进行大量的机构分析、材料分析、力学分析等,依然需要去试制、测试、检测等等,这些研发的过程是无法省略的。
奔驰A级轿车发动机盖采用生物基聚酰胺材料制作
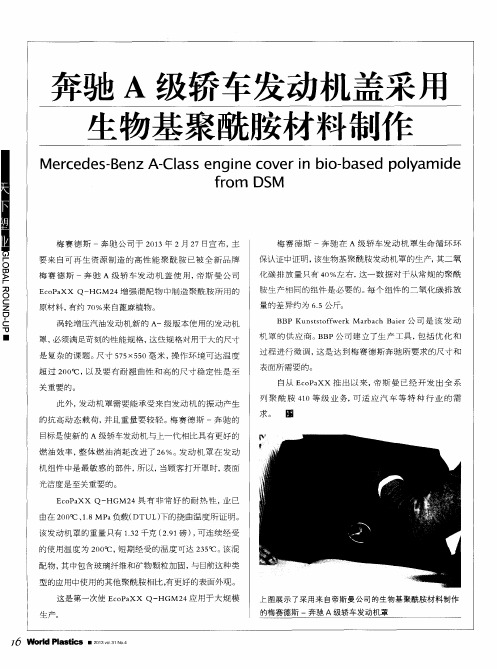
奔驰 A级轿车发动机盖采 用 生物基 聚酰 胺材 料制 作
Me r c e d e s — B e n z A— - Cl a s s e n gi n e c o v e r i n bi o - - b a s e d p ol y a mi d e
f r Om 丁
o
C Z 口
l
原材 料, 有约 7 0 %来 自蓖 麻植物 。 涡轮 增 压汽 油发 动 机新 的 A一级 版本使 用的 发动 机
罩, 必 须满 足苛 刻的性 能规 格 , 这些 规 格对用 于大 的尺寸
量 的差 异 约为 6 . 5公斤。
B B P Ku n s t s t o f f we r k Ma r b a c h Ba i e r 公 司 是 该 发 动 机 罩 的 供 应 商。B B P公 司 建 立了生 产工 具 , 包 括 优 化 和
梅 赛 德 斯 一奔 驰 公司 于 2 0 1 3年 2月 2 7日宣 布 , 主
广
梅 赛 德 斯 一奔 驰 在 A级 轿 车 发动 机 罩 生命 循 环 环
。
叩
要 来 自可 再 生 资源 制 造 的 高 性 能 聚 酰 胺 已被 全 新 品 牌 梅 赛 德 斯 一奔 驰 A 级 轿 车 发 动 机 盖 使 用 , 帝 斯 曼公 司
列 聚酰 胺 4 1 0等 级 业 务, 可 适 应 汽 车 等 特 种 行 业 的 需
关重 要 的。
此 外, 发动 机 罩 需要 能 承受 来 自发动 机 的振 动 产生
的 抗 高动 态 载 荷 , 并且 重 量 要 较 轻 。 梅 赛德 斯 一奔 驰 的 目标是 使 新 的 A级轿 车发动 机 与上一 代相 比 具有 更好 的 燃 油 效率 , 整 体 燃 油 消 耗 改 进了 2 6 %。发 动 机 罩 在 发动 机 组件 中是 最 敏 感的 部件 , 所以, 当顾 客打 开罩 时 , 表面 光洁度 是 至关 重要 的。 E c o P a XX Q— HG M2 4具 有 非 常 好 的耐 热 性 , 业 已 由在 2 0 0  ̄ ( 2 、 1 . 8 MP a 负载 ( DTUL ) 下 的挠 曲温 度 所 证 明。 该发 动机 罩的 重量 只有 1 . 3 2千克 ( 2 . 9 1 磅) , 可 连续 经 受 的使 用温 度 为 2 0 0  ̄ ( 2 , 短 期 经受 的 温 度可 达 2 3 5  ̄ C。 该 混
【汽车材料分析】2014年欧洲车身会议(ECB)奔驰新C级车身用材及工艺解析

【汽车材料分析】2014年欧洲车身会议(ECB)奔驰新C级车身用材及工艺解析1一、奔驰新C级车型概况第一代奔驰C-glass为2014年欧洲白车身会议亚军车型图1 2014年ECB会议车型评分结果第一代奔驰C-glass于1982年上市,经过三十多年的发展,历经W201、W202、W203、W204车型,现已发展到第五代车型W205——2014新C级,如图2所示。
奔驰C-glass作为一款中型豪华轿车,一直受到消费者的青睐,是奔驰系列车型中销量最大的车型,也是奔驰所有车系中车型最全的一类。
图2 奔驰C-glass车型的发展历程历经了5代车型的发展,最新款奔驰C-glass拥有迎合了消费者注重汽车外观的消费潮流,是具有流畅大气的外观,且操控性能强的经典车型。
1.1车型尺寸新一代奔驰C级在车型长度、宽度、轴距轮距等参数上均有所增加,而在高度上则略有降低,如图3所示。
得益于更加流畅的线条设计,其风阻系数由上一代车型的0.26降低为0.24,阻力面积减少了5%,在空气动力学上来说这是非常重要的,可以显著减少汽车生命周期中CO2气体的排放。
车型长度车型宽度车型高度前轮距后轮距轴距奔驰新C级 4.686m 1.810m 1.442m 1.588m 1.570m 2.840m与上一代车型变+95mm +40mm -5mm +39mm +18mm +80mm化车身脚印面积:= (前轮距+后轮距)/2*轴距=4.48m2图3 新一代奔驰C级的尺寸1.2白车身重量白车身总重量(包含四门两盖等覆盖件的非油漆车身):362 kg;白车身骨架重量:293kg;1.3车身轻量化系数该白车身的静态扭转刚度达到了28770 Nm/°,根据公开的数据,按照车身轻量化系数的公式:进行计算,得到其轻量化系数为2.26。
奔驰C级五代车型的轻量化系数如下图4所示。
由图可以看出,从1982年上市的第一代车型到现在的车型,其安全性能不断提升,但是轻量化系数却一直在降低。
车身铆接工艺
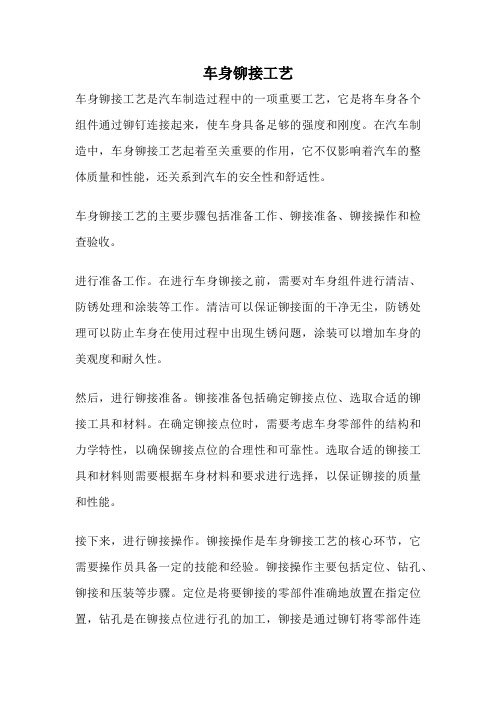
车身铆接工艺车身铆接工艺是汽车制造过程中的一项重要工艺,它是将车身各个组件通过铆钉连接起来,使车身具备足够的强度和刚度。
在汽车制造中,车身铆接工艺起着至关重要的作用,它不仅影响着汽车的整体质量和性能,还关系到汽车的安全性和舒适性。
车身铆接工艺的主要步骤包括准备工作、铆接准备、铆接操作和检查验收。
进行准备工作。
在进行车身铆接之前,需要对车身组件进行清洁、防锈处理和涂装等工作。
清洁可以保证铆接面的干净无尘,防锈处理可以防止车身在使用过程中出现生锈问题,涂装可以增加车身的美观度和耐久性。
然后,进行铆接准备。
铆接准备包括确定铆接点位、选取合适的铆接工具和材料。
在确定铆接点位时,需要考虑车身零部件的结构和力学特性,以确保铆接点位的合理性和可靠性。
选取合适的铆接工具和材料则需要根据车身材料和要求进行选择,以保证铆接的质量和性能。
接下来,进行铆接操作。
铆接操作是车身铆接工艺的核心环节,它需要操作员具备一定的技能和经验。
铆接操作主要包括定位、钻孔、铆接和压装等步骤。
定位是将要铆接的零部件准确地放置在指定位置,钻孔是在铆接点位进行孔的加工,铆接是通过铆钉将零部件连接起来,压装是为了确保铆接点位的紧密连接。
进行检查验收。
检查验收是为了确保铆接质量和性能的合格。
检查验收包括外观检查、尺寸检查和力学性能检测等。
外观检查主要是检查铆接点位的表面质量和连接状态,尺寸检查主要是检查铆接点位的尺寸精度和位置精度,力学性能检测主要是检测铆接点位的强度和刚度。
车身铆接工艺具有以下几个特点:铆接连接具有高强度和刚度。
由于铆接点位采用铆钉连接,相比于其他连接方式,具有更高的强度和刚度,可以更好地满足汽车的使用需求。
铆接连接具有良好的密封性。
铆接点位采用铆钉连接后,能够形成一个密封的连接,可以有效防止外界杂质进入车身内部,保证车内环境的清洁和安全。
铆接连接具有较好的耐腐蚀性。
铆接点位通常采用不锈钢或者防腐涂层进行处理,能够有效抵抗氧化、腐蚀和水蚀等因素的侵蚀,延长车身的使用寿命。
- 1、下载文档前请自行甄别文档内容的完整性,平台不提供额外的编辑、内容补充、找答案等附加服务。
- 2、"仅部分预览"的文档,不可在线预览部分如存在完整性等问题,可反馈申请退款(可完整预览的文档不适用该条件!)。
- 3、如文档侵犯您的权益,请联系客服反馈,我们会尽快为您处理(人工客服工作时间:9:00-18:30)。
奔驰A级车身结构及连接工艺解析
奔驰A级是奔驰的系列车系之一,是在全球销量达到110万辆的情况下推出了更具诱惑和创新意识的新款A系列,以期望能够延续A系列的神话。
白车身重277.7kg,车身重365.3kg,下图为与同级别车型的尺寸对比图。
奔驰A级在车身长度及轴距处于领先位置。
车型尺寸对比图
车身材料
奔驰A级白车身材料以钢为主,以铝为辅,该车在材料应用上并没有和奔驰其他车型一样采用铝铸件,其中:
低强钢占比24.6%
高强钢占比26.4%
先进高强钢占比35.3%
超高强钢0.7%
热成型钢9.5%
6系铝板占比1.7%
5系铝板占比1.5%
奔驰车身用钢材通常按不同抗拉强度进行如下分类:
低碳钢:抗拉强度小于300N/mm²;
高强度钢:抗拉强度在300N/mm²- 550 N/mm²;
现代高强度钢:抗拉强度在550N/mm²- 1000 N/mm²;
超高强度钢:抗拉强度超过1000N/mm²;
热成型超高强度钢:抗拉强度超过1500N/mm²;
白车身材料分布图
车身结构
首先我们看一下车身的前碰和侧碰的传力图,目前乘用车车体结构都会大量应用环状结构,在设计过程会对不同部位的能量吸收比例有一定要求,通过结构强弱,传力路径,分析反馈优化来实现,从而减少乘员伤害值。
车身传力图
为提高静态扭转刚度,在前围板处进行结构优化,为降低前轴噪声,前副车架进一步优化,在后桥处对CD柱进行优化,最后静态扭转刚度达到27.5kNm/°。
白车身骨架图
风窗上横梁材料改为DP600HD,材料厚度由0.8优化到0.7,前围板下横梁及轮罩材料改为DP800HD,厚度由1.35改为0.7。
整体实现降重6.5kg。
前舱细节图
为提升视野,对ABC柱进行优化,A柱通过门框结构优化、减少A柱止口长度,减少胶圈宽度,内饰结构、流水宽度减少,B柱通过门框结构优化、B柱护板宽度增加实现止口减少的互补、调整安全带布置来优化对应结构。
C柱通过优化门框结构、止口宽度减少、截面优化、对C柱间隙位置优化。
从而使盲区由97.2°降低到86.7°。
驾驶员视野图
连接工艺
奔驰A级作为一款钢主铝辅的车身,连接工艺达到了10种,分别为点焊、螺柱焊、凸焊、MIG、激光焊接、激光钎焊、无铆(tox)、包边、螺接、胶接。
其中
螺柱焊393个
凸焊150个
无铆87个
螺接63个
下面我们一起通过一些图片来看一下他的连接细节。
白车身整体图
由图可以看见在前舱各个部位遍布较多的螺柱及凸焊标准件,其中吸能盒采用插入式结构,为方便拆卸,采用螺栓连接,在副车架与车身的连接中,螺接是必备的连接工艺(取决于连接稳定性及生产线工序)
前舱细节图
在管梁与白车身的连接中,车身先凸焊好螺母,然后管梁与车身螺接,分别于左右A柱及中通道螺接。
由下图,在驾驶舱内部应用了螺柱焊,螺柱最明显的一个特点就是周圈会有黑色,为拉弧式螺柱焊,为内饰、电器、线束等安装提供辅助。
总结
本文主要通过材料、结构、连接对奔驰A级进行了简单的介绍,数据显示,第一代奔驰A 级车共计售出了110万台;第二代产品推出后,自2008年起销量达到了70万辆;而2012年诞生的第三代奔驰A级车,至今已经售出超过110万。
良好的消费者基础加上车型的不断更新优化是奔驰A级车家族发展壮大的根本原因。