滚动轴承寿命与可靠性试验的评定方法
滚动轴承疲劳试验方案
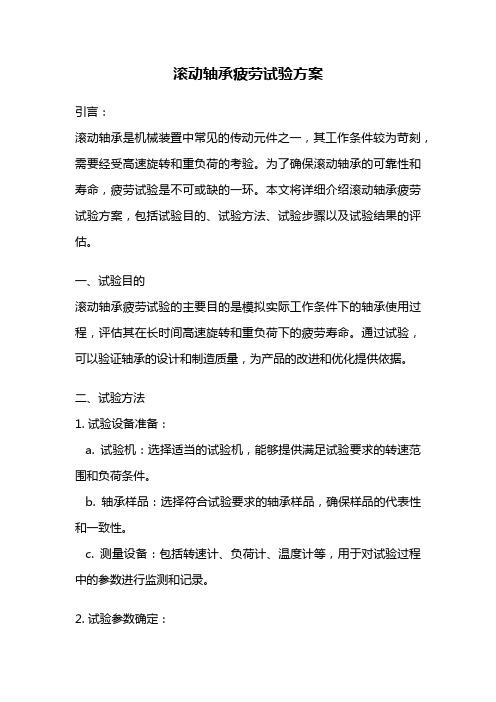
滚动轴承疲劳试验方案引言:滚动轴承是机械装置中常见的传动元件之一,其工作条件较为苛刻,需要经受高速旋转和重负荷的考验。
为了确保滚动轴承的可靠性和寿命,疲劳试验是不可或缺的一环。
本文将详细介绍滚动轴承疲劳试验方案,包括试验目的、试验方法、试验步骤以及试验结果的评估。
一、试验目的滚动轴承疲劳试验的主要目的是模拟实际工作条件下的轴承使用过程,评估其在长时间高速旋转和重负荷下的疲劳寿命。
通过试验,可以验证轴承的设计和制造质量,为产品的改进和优化提供依据。
二、试验方法1. 试验设备准备:a. 试验机:选择适当的试验机,能够提供满足试验要求的转速范围和负荷条件。
b. 轴承样品:选择符合试验要求的轴承样品,确保样品的代表性和一致性。
c. 测量设备:包括转速计、负荷计、温度计等,用于对试验过程中的参数进行监测和记录。
2. 试验参数确定:a. 转速范围:根据实际工作条件确定试验中的转速范围,考虑到轴承在高速旋转下的疲劳寿命变化规律。
b. 负荷条件:根据轴承的额定负荷和实际工作负荷确定试验中的负荷条件,考虑到轴承在重负荷下的疲劳寿命变化规律。
3. 试验步骤:a. 安装轴承样品:将选取的轴承样品正确安装在试验机上,确保轴承位置和轴向负荷的准确度。
b. 设置试验参数:根据试验要求,设定转速和负荷条件,确保试验过程中参数的稳定性。
c. 运行试验:启动试验机,使轴承样品在设定的转速和负荷条件下运行,连续工作一定时间。
d. 监测记录:在试验过程中,及时监测和记录轴承样品的转速、负荷和温度等参数。
e. 试验终止:根据试验要求,确定试验的终止条件,如达到设定的寿命或出现严重故障等。
f. 试验结果评估:根据试验数据和评估标准,对试验结果进行分析和评估,得出轴承的疲劳寿命。
三、试验结果评估根据试验的目的和要求,对试验结果进行评估是十分重要的。
评估的主要内容包括:1. 疲劳寿命:根据试验数据和评估标准,确定轴承的疲劳寿命,评估其是否符合设计要求和使用要求。
滚动轴承寿命与可靠性试验的评定方法

失效, 日本 JE T公 司开发的此类轴承的滚动体 TK 采 用高绝 缘 性 的 陶 瓷 材 料 , 有 的企 业 在 轴 承 外 也
表 面上涂 覆绝 缘材料 来解 决 电蚀 问题 。
[ ] 葳下义一 . 6 风力发 电机用滚 动轴承 [ ] 国外 轴承技 J.
术 ,09 4 : 5 . 2 0 ( )5 4— 9
对各 类轴 承抗 疲劳 制造 技术 的研究 和应 用 。
参 考文 献 :
[] 卢 1 刚. 动轴承 的抗 疲劳制 造 [ ] / 滚 c / 第五 届 中国 轴承论坛论文集 . 阳 : 洛 洛阳轴 承研究 所有 限公 司,
20 9 : 9 ~2 0 1 3.
止 了打滑 对轴 承造成 的损 伤 。
[ ] 刘 耀 中. 车 轴 承 的 材 料 及 热 处 理 长 寿命 技 术 7 汽 [ ] / 国汽 车轴 承技 术攻 关 专题 研讨 会论 文 集. C /全 洛 阳: 中国轴承工业 协会技术委员会 ,0 84 5 . 20 :7— 3 ( 编辑 : 温朝杰 )
4 结 束 语
温 渗硫 ( 离子渗 硫 、 液体渗 硫等 ) 的表面 改性 处 理 。
德 国 Sh e e 公 司从 2 0 caf r l f 0 8年起 供 应 的增 速 器 圆 柱滚 子轴 承 均采 用 复合 氧化 发 黑 处 理 , 效 地 防 有
术 的研究 及 应 用 , 以满 足 风 力 发 电机 组 对 配套 轴 承 长寿命 、 可靠性 的要求 ; 时推 动全 行 业 开展 பைடு நூலகம்高 同
当 前 , 技 界 倡 导 对 新 一 代 先 进 制 造 技 科
张
伟等: 滚动轴承寿命与可靠性试验 的评定方法
滚动轴承寿命预测技术的研究
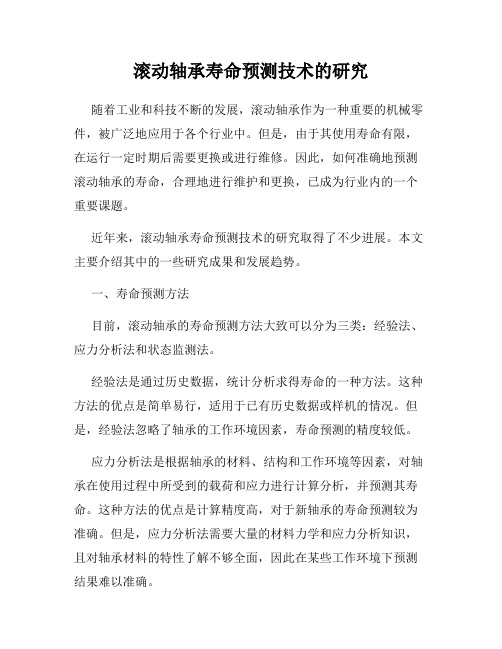
滚动轴承寿命预测技术的研究随着工业和科技不断的发展,滚动轴承作为一种重要的机械零件,被广泛地应用于各个行业中。
但是,由于其使用寿命有限,在运行一定时期后需要更换或进行维修。
因此,如何准确地预测滚动轴承的寿命,合理地进行维护和更换,已成为行业内的一个重要课题。
近年来,滚动轴承寿命预测技术的研究取得了不少进展。
本文主要介绍其中的一些研究成果和发展趋势。
一、寿命预测方法目前,滚动轴承的寿命预测方法大致可以分为三类:经验法、应力分析法和状态监测法。
经验法是通过历史数据,统计分析求得寿命的一种方法。
这种方法的优点是简单易行,适用于已有历史数据或样机的情况。
但是,经验法忽略了轴承的工作环境因素,寿命预测的精度较低。
应力分析法是根据轴承的材料、结构和工作环境等因素,对轴承在使用过程中所受到的载荷和应力进行计算分析,并预测其寿命。
这种方法的优点是计算精度高,对于新轴承的寿命预测较为准确。
但是,应力分析法需要大量的材料力学和应力分析知识,且对轴承材料的特性了解不够全面,因此在某些工作环境下预测结果难以准确。
状态监测法是通过监测轴承内部的振动、温度、油液清洁度等状态指标来判断轴承的工作状态和寿命,它是一种目前应用较广泛的寿命预测方法。
状态监测法的优点是操作简便,能够实时监测,反应灵敏,而且对于现场检测和实际应用情况具有很强的适应性。
但是,状态监测法的缺点是受监测指标的影响较大,准确性存在一定问题。
二、寿命预测技术的研究演进随着科技的进步和工业发展的需要,滚动轴承寿命预测技术也在不断地得到改进和完善。
下面简要介绍一下寿命预测技术的研究演进过程。
1. 经典寿命预测法经典寿命预测法是基于滚动轴承的材料和结构来进行寿命预测的方法。
这种方法主要考虑滚动体与架的接触和变形,通过计算轴承的应力和变形来预测其寿命。
2. 动态寿命预测法动态寿命预测法是根据对轴承实际运行情况的监测和分析,使用自适应控制技术来进行寿命预测的方法。
这种方法可以更精准地预测轴承的寿命,减少轴承寿命预测误差。
滚动轴承寿命预测与故障诊断

滚动轴承寿命预测与故障诊断滚动轴承是机械传动系统中常用的一种关键零部件,因其结构简单、可靠性高、运转稳定等特点被广泛应用于工业制造、交通运输、航天航空等领域。
然而,在长期的使用中,由于负载、转速、温度等因素的影响,滚动轴承很容易出现各种故障,严重影响机械设备的正常性能。
因此,预测滚动轴承的寿命并对其故障进行诊断具有极其重要的意义,不仅能够减少机器设备的维修成本,更能提高机器设备的运行效率和安全性。
一、滚动轴承寿命预测的基本理论滚动轴承寿命预测是指通过对滚动轴承在特定工况下的运行情况进行数学模型建立和系统分析,来预测滚动轴承在未来一段时间内的使用寿命。
其基本理论是寿命公式理论,即基于统计学原理,通过对有限数量的试验数据进行分析,来估计大量相似产品的寿命。
该理论最早由Weibull提出,现广泛应用于各种设备的寿命预测中。
滚动轴承的寿命是指在一定的负载、转速、温度等工况条件下,维持基本性能的使用寿命。
通常将运转时间作为寿命评定标准,其评定方法有两种,即L10寿命和L50寿命。
其中L10寿命是指在有10%以上的滚动轴承失败的情况下所需要的运转时间,L50寿命则是指在有50%以上的滚动轴承失败的情况下所需的运转时间。
滚动轴承寿命预测的方法一般有以下几种:1、基于模型的预测法该方法是在通过对相关参数的观测和测量得到大量样本数据的基础上,建立滚动轴承故障模型,对其进行数学分析和计算,从而提出一定的预测理论。
该方法的优点是可以快速准确地预测滚动轴承的寿命,缺点是在模型建立过程中,需要考虑多种因素的影响,模型的建立难度较高。
2、基于统计模型的预测法该方法是通过统计分析大量实测数据,确定影响滚动轴承寿命的关键因素,建立相应的统计模型,并通过多种分析方法,包括生存分析、半参数估计和回归分析等来预测滚动轴承的寿命。
该方法的优点是具有较强的实用性和普适性,但缺点是要求样本数据的质量和数量均较高,在实际操作中要具备较为广泛的背景知识和大量的经验。
滚动轴承寿命与可靠性试验的评定方法
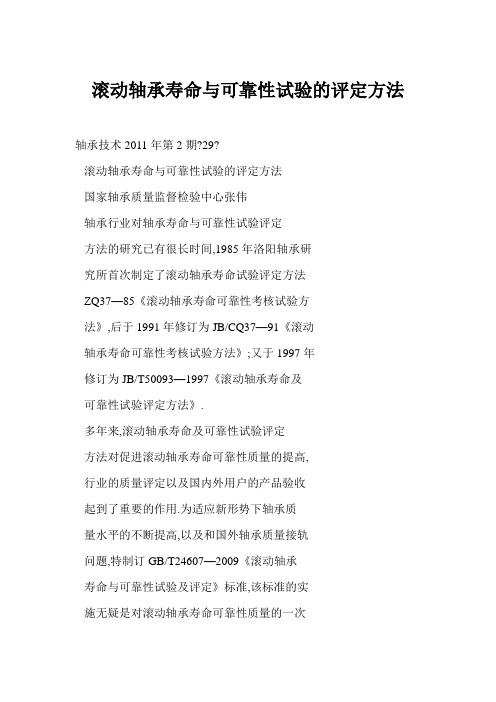
滚动轴承寿命与可靠性试验的评定方法轴承技术2011年第2期?29?滚动轴承寿命与可靠性试验的评定方法国家轴承质量监督检验中心张伟轴承行业对轴承寿命与可靠性试验评定方法的研究已有很长时间,1985年洛阳轴承研究所首次制定了滚动轴承寿命试验评定方法ZQ37—85《滚动轴承寿命可靠性考核试验方法》,后于1991年修订为JB/CQ37—91《滚动轴承寿命可靠性考核试验方法》;又于1997年修订为JB/T50093—1997《滚动轴承寿命及可靠性试验评定方法》.多年来,滚动轴承寿命及可靠性试验评定方法对促进滚动轴承寿命可靠性质量的提高,行业的质量评定以及国内外用户的产品验收起到了重要的作用.为适应新形势下轴承质量水平的不断提高,以及和国外轴承质量接轨问题,特制订GB/T24607—2009《滚动轴承寿命与可靠性试验及评定》标准,该标准的实施无疑是对滚动轴承寿命可靠性质量的一次促进,势必将对提高我国滚动轴承的寿命可靠性水平起到积极的作用.1合格评定轴承寿命可靠性试验原始数据经数据处理后得到相关参数,对参数进行一系,即达到Lm/Li的倍数值.2试验数据处理常规试验数据处理一般依据二参数韦布尔(Weibul1)分布函数进行分析处理,使用图估计法和参数估计法,图估计法较简便直观,一般可优先采用图估计法;而对试验数据较少的或无失效数据的情况一般采用序贯试验评定方法.2.1Weibul1分布图估计法1)图估计目的通过对试验轴承样品的完全试验,截尾试验等,得出试验数据,根据图估计法在Weibul1 分布图上估计出分布参数,并得出试验结果及评定结果.2)Weibul1分布图轴承寿命服从二参数韦布尔(Weibul1)分布函数:f)=1一e一(詈)作变换得:其对数形式是:1lnlnblnL—blnv令),lnln南,ln,B—bin则就把上式变成x—Y直角坐标系中一条直线方程:Y=bX+B这是一条以b为斜率的直线,若能求出参数b,v,则直线唯一确定.?3O?轴承技术2011年第2期坐标点(x,Y)对应于1(1nL,lnln)X=lnLL=ex根据L=e的与L=e的对应关系和,(L)=1一e的F()与y的对应关系分别把对应的值记在轴上,把y的对应值记在y轴上(横轴为,纵轴为F),由上述原理即可制成Weibul1分布概率图.轴承寿命Weibul1分布曲线是以b为斜率,以t,为特征寿命的一条直线,b表示轴承寿命的离散程度或轴承寿命质量的稳定性,t,是当F()=0.632时的轴承寿命,求出参数6,t,直线可唯一确定.3)一般的图估计一般对于失败数据不少于6个的试验数据评定,可用图估计方法.失效数据越少,图估计的精度就越低.横坐标为厶(即各试验数据),纵坐标为F一n(厶)(即失效概率),在Weibu11分布图上依次描点,然后按照各点的位置,配置分布直线.配置直线时,各点须交错,均匀地分布在直线两边,且F()=0.3~0.7附近的数据点与分布直线的偏差应尽可能地小.由直线可求Weibul1分布斜率b(直线上某点的纵坐标与横坐标之比).斜率b越大,说明轴承寿命数据较集中,轴承寿命质量稳定; 反之斜率b越小,轴承寿命数据离散,轴承寿命质量不稳定.由直线可求特征寿命,是当F()=0.632(纵轴为63.2%)时的轴承寿命,即破坏概率为63.2%时的轴承寿命.由参数6,,再分别求出基本额定寿命的试验值.(纵轴为10%),中值额定寿命的试验值L卯(纵轴为50%),计算出可靠度e等.4)分组淘汰图估计分组淘汰试验方法可缩短试验周期,但试验风险比一般完全试验和定时(数)截尾试验大.试验中,每一分组中出现一个失效样品即停止试验,然后用各组的最短寿命数据在Weibul1分布概率纸上描点,配置直线,再由该直线求得该批样品的分布直线.5)图估计实例例1:某厂生产的深沟球轴承L..=100h,N=8套,试验结束,得到8个失效数据,分别是80h,110h,155h,170h220h,240h300h380h用Weibul1分布图估计参数b及,LL50,Re 等值.a)由8个失效数据,配置直线A(见图1).i,纵坐标为F()=矗,故8个点的坐标值分别为:(8O,0.083),(1lO,0.202)……(380,0.917),将其描在Weibul1分布概率纸上,配置直线A.b)由直线A求出6,t,,Llot,.Lsot-,Re等值.b=2,=250h,L10=85h,Lso=200h,Re=86%c)L10l/L10–85/100<1.4,故判定该批轴承样品不合格.例2:某厂生产的深沟球轴承L,0–100h,N=32套,分8组7//,=8,每组4套同时上机试验N=4套.每组有一套轴承失效即停机,试验结束,得到8个分组的最短寿命分别为10h, 110h,155h,170h,220h,24Oh,300h,380h.用Weibul1分布图估计参数b及,150,e等.本例为分组淘汰图估计例.先按例1求出分布直线A,再由分布直线A求分布直线B.a)由于每组有4套轴承,故将待求的直线B上M点的纵坐标记为F()=}=0.159.b)作三条平行线:过F()=50%作横轴平行线与直线A交于点c,过C作纵轴平行线与过F(L)=0.159的横轴平行线交于点M. (在直线A上取纵坐标为F()=50%的点C,轴承技术2011年第2期?3l?由C做纵轴平行线,并与过F(L)=0.159的横轴平行线交于点M0)C)过M点做平行与直线A的平行线B.也可由解析法求直线B:N当为每组套数时,B的特征寿命”B=×z虿=250×4-r=500h.由直线B求出6,,L,Re等.b=2,=500h,Ll0=160h,L1ol=400h,Re=96%345L/h图1Weibul1分布图估计a)t1m/L0–160/100>1.4,故判定该批轴承样品合格.2.2WeibuU分布参数估计1)Weibul1分布参数估计的目的通过试验轴承样品的完全试验,载尾试验,得出试验数据,根据Weibul1分布数据处理估计出分布的参数,并得出试验结果及评定结果.截尾试验失效数据一般应不少于6个.若失效数据太少,参数估计的精度就降低.通过数据处理确定Weibul1分布的两个参数b,v.样本容量Ⅳ,经试验后得到的实际寿命为: 完全试验≤L2……≤厶……≤i=1,2……Ⅳ;定数截尾试验£1≤三2……≤厶≤L,i=1.2……r<N分组淘汰试验L,≤:…………≤i=1,2……;m=Ⅳ/Ⅳ对于完全试验和定数截尾试验,纵坐标(失效概率)(厶)=对于其他非完全试验,计算破坏概率F (厶)时,应将上式的i进行修正.修正方法见表2.轴承寿命Weibul1分布参数6,的估计,当Ⅳ≤25时,用最佳线性不变估(BLIE)方法;当N>25时,用最大似然估计(ML)方法(略).2)最佳线性不变估计(BLIE):完全试验:b=[_∑c1(J7v,N,i)lnL]1n13=∑D1(Ⅳ,N,i)1nLi定数截尾试验:b_一∑c1(Ⅳ,r,i)lnL]1nv=∑D1(Ⅳ,r,i)lnLi当r=N时即为完全试验.分组淘汰试验:b=[三c(m,m,i)lnL]1nv=-~-1nN+∑D1(m,m,)lnLiui=1一当N=1时即为完全试验.最佳线性不变估计系数CD见《可靠性试验用表》.3)依据b,1J,估计L1o,L50及Re当F(三)=0.10时,基本额定寿命的试验值:L1=(0.10536)当F(L)=0.50时,中值寿命:L5.=?(0.69315)当L:Lloh,可靠度:Re=e一()(时刻对应的可靠度)4)参数估计实例∞酏∞∞m4,2求,(,I‰?32-轴承技术2011年第2期例3:对例1的数据用Weibun分布估计参数b及t,,并计算L.,£Re等值.本例为完全试验,最佳线性不变估计系数为C1(Ⅳ,N,i),D1(N,N,i).若为定数截尾试验,失效数一般不能少于试验样品容量的2/3,即r<N,且按失效数据大小排列,一般未失效样品数据均大于失效样品数据,最佳线性不变估计系数为C(Ⅳ,r,),D (Ⅳ,r,).参数估计列于表1,并完成各项计算.表1WeibuU分布参数估计表t一4%厶lnLC,(N,N,i)C,lnLD1(N,N,)D,lnLⅣ+.18.33804.3820—0.0933一O.4O88O.034l0.1494 220.2311O4.7006—0.0989—0.46490.0536O.2519 332.141555.0434—0.0940—0.47410.07350.3707 444.O51705.1358—0.0798—0.40980.09510.4884 555.952205.3936—0.0539—0.29070.1198O.6462 667.862405.4806—0.0102—0.05590.14990.8215 779.7630o5.70380.06930.39530.19121.0906 891.673805.94020.36072.14260.28291.6805NN∑0.4337∑5.4992i1i1b=[∑C1(N,N,i)lnL]~=2.3057N==11nt,=∑D1(Ⅳ,Ⅳ,)lnL=5.4992=245hL1m=?(O.10536)=92hL5m=?(0.69315)=210hRe:e一(了LlOh):e一()?姗:88%o/L.–92/100<1.4,故判定该批轴承样品不合格.例4:对例2的数据用Weibul1分布估计参数b及t,,并计算舶等值.对样本容量为Ⅳ的试验样品进行试验时,因为有各种各样的原因使某一试样中停试验, 此数据就是未失效数据(按数据大小排列,未失效数据可能在失效数据之间),一般数据处理方法是不考虑未失效数据,这样就不能真实的反映整体的情况,影响轴承质量水平评价. 所以含有未失效数据的处理要对失效数据进行位置修正.本例为非完全试验(分组淘汰试验),同样也含有未失效数据.其修正位置增量: △=(这里的为全部试验样本容量,即为32)=Ii一1+△当=OJ『=O(即,0=O):非完全试验时i的修正值:非完全试验时,实际寿命由小到大排列的统计量序列△:非完全试验修正时的位置增量非完全试验F()的修正值的计算见表2.最佳线性不变估计系数为c(m,m,),D. (m,m,),参数估计见表3.轴承技术2011年第2期?33?表2非完全试验时,(厶)的修正值J厶L△iItF(L=()%1801112.16511O21.1O342.1O345.57915531.23593.33939.381317041.41244.7517l3.741722051.66176.4134l8.872124062.O4518.458525.182530o72.726811.185333.6O2938084.362915.548247.06表3非完全试验WeibuH分布参数估计表)(%厶lnLfCJ(m,m,i)C,1nLiD,(m,m,i)D,lnLf12.16804.3820—0.0933—0.40880.03410.149455.571l04.7005一O.O989—0.46490.05360.2519 99.381555.0434—0.0940—0.47410.07350.3707l313.7417O5.1358一O.O798—0.4O980.09510.4884 1718.8722O5.3936—0.0539—0.29O70.1198O.6462 2125.1824O5.4806—0.0102—0.05590.14990.8215 2533.6030o5.70380.06930.39530.19121.0906 2947.O63805.94020.36072.14260.28291.6805mm∑0.43375.4992i1b=[c,(m,m,i)lnLi]~=2.30571nv={_Ⅳ+三D,(m,m,)lnLiDi=1’’+5?4992-o.61004=446hL10f=?(0.10536)=170h=?(0.69315)=380hRe:e一(LlOh):e一()?姗:97%0/L.=170/100>1.4,故判定该批轴承样品合格.2.3序贯试验方法本标准所选取的后验序贯抽样检验方案,是序贯抽样检验的一种.它适用性强,可利用原有试验设备,特别是当疲劳破坏数据较少时,也可给判定结论,便于考核及订户验收;方?34?轴承技术2011年第2期法简便,运算少,数据处理程序化,表格化,便于推广应用.完全试验,截尾试验一般时间较长才能得出结果,而对小子样失效数据,无失效数据的处理易采用序贯试验验,较短时间就能得出结果.序贯试验用于试验设计而不是试验判定.第一套轴承如果出门或不人门,则直接判合格或不合格;如果在继续检验区,则用替换轴承继续检验.1)替换试验试验采用有替换试验序贯检验,按失效顺序一套一套逐次进行检验判定.当有5套轴承样品失效时停试,并做出合格与否的判定.试验中替换轴承坪品的换效数据也参与判定. 这种方法用于小于样或无失效数据的处理. Ⅳ(有替换同时试验的轴承套数)套轴承同时上机试验,当第一套轴承试到上q时间失效(这时其他一l套轴承也试到时间,但未失效),为保证套轴承同时上机试验状态,需换上一套待试样品继续试验,该样品称为替换轴承.替换轴承(L2)失效时,这时总试验时间为+,另_Ⅳ一1套轴承的试验时间均为+2o2)检验判定参数综合国内外资料,取韦布尔分布斜率:b=1.5检验水平:根据选取的,风险值分为四组,检验水平由宽到严.一般用户验收的试验取水平I或Ⅱ,行业及第三方认证机构的试验取水平Ⅱ或Ⅲ,制造厂内部的试验取水平Ⅲ或Ⅳ,如表4所示.表4检验水平检验水平IⅡⅢⅣ0.2O.2O.2O.1风险0.20.3O.5O.7:合格风险,接受风险或显着性水平,1一称置信度.:不合格风险,拒绝风险.本标准判定检验时配合使用.有时称为使用方风险.3)检验判定门限对不同的值可以组成多个检验水平,图2为不同检验区示意图.由图可以看出,水平I,Ⅱ, Ⅲ接受区一样,但拒收区增加,即继续检验区减小;水平Ⅳ接收区减小,拒收区增加.这样从检验水平Ⅳ检验水平逐步加严.螽培数N12lO8642O=IC玎L0n3000_,ln£,,,,y’,,一///,1,椎自蜮j,//墩’.,/./j’队bJ鼍I/2468l012l4l6l3202224图2检验区示意图(A是,B是)与表4的,口对应的门限系数,见表5.从图2及表5看出,如果取=0.3,=0.7,即两条检验判定线重合,说明检验严,要么合格,要么不合格,中间没有继续检验区.表中给出了一个i=0的点,在判断格式里为tlO点,即无失效门限tlO,r=0时的接受门限值,该点尤其适用于军品轴承试验套数少, 而又要求无失效试验的特点.4)检验判定格式实际考核时,第i个轴承样品失效时的接受门限t1=(L/N).第i个轴承样品失效时的拒绝门限t2i=L/N8T6令:=Z.t,=Z’/JlOh轴承技术2011年第2期?35?检验判定格式见表6.表5与o~,13对应的门限系数,值t012345O.12.3023.8905.3226.68l7.9949.274 0.21.6102.9944.2795.5156.7217.906 0.31.2o42.4393.6164.7625.8907.0o6 0.20.8241.5352.2973.0903.904O.31.0981.9142.7643.6344.5l70.51.7782.6743.6724.7615.6700.72.4393.6l64.7625.8907.0o6表6检验判定格式O12345£”tlo£l1£l213t14t15l2f21f22t255)检验判定式N.(~LslN)为试验时间,即h,尚无失效轴承出现, 这时l2套轴承均试至200h.因:(军12/):)~:200’~=2828>t】o=2806,合格停试. 判定该批轴承样品合格.(未完接下期)摘自《滚动轴承标准化》2010年第3期。
机械轴承寿命评估与寿命预测方法研究
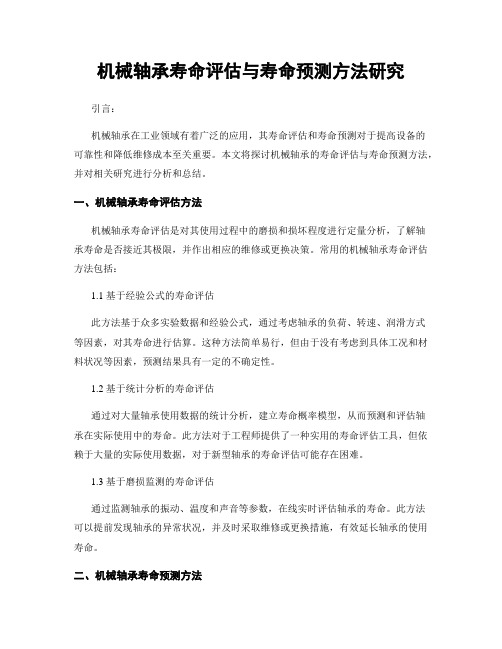
机械轴承寿命评估与寿命预测方法研究引言:机械轴承在工业领域有着广泛的应用,其寿命评估和寿命预测对于提高设备的可靠性和降低维修成本至关重要。
本文将探讨机械轴承的寿命评估与寿命预测方法,并对相关研究进行分析和总结。
一、机械轴承寿命评估方法机械轴承寿命评估是对其使用过程中的磨损和损坏程度进行定量分析,了解轴承寿命是否接近其极限,并作出相应的维修或更换决策。
常用的机械轴承寿命评估方法包括:1.1 基于经验公式的寿命评估此方法基于众多实验数据和经验公式,通过考虑轴承的负荷、转速、润滑方式等因素,对其寿命进行估算。
这种方法简单易行,但由于没有考虑到具体工况和材料状况等因素,预测结果具有一定的不确定性。
1.2 基于统计分析的寿命评估通过对大量轴承使用数据的统计分析,建立寿命概率模型,从而预测和评估轴承在实际使用中的寿命。
此方法对于工程师提供了一种实用的寿命评估工具,但依赖于大量的实际使用数据,对于新型轴承的寿命评估可能存在困难。
1.3 基于磨损监测的寿命评估通过监测轴承的振动、温度和声音等参数,在线实时评估轴承的寿命。
此方法可以提前发现轴承的异常状况,并及时采取维修或更换措施,有效延长轴承的使用寿命。
二、机械轴承寿命预测方法机械轴承寿命预测是基于轴承的设计参数、工作条件和使用状况,结合材料科学、磨损学和可靠性工程等理论,对轴承的剩余寿命进行预测。
目前常用的机械轴承寿命预测方法包括:2.1 基于统计学的寿命预测利用大量轴承实验数据,建立寿命概率模型,并通过统计学方法,对轴承的剩余寿命进行预测。
该方法适用于大批量轴承的寿命预测,但无法考虑到具体工况和材料状况等因素对寿命的影响。
2.2 基于数学模型的寿命预测通过建立数学模型,仿真轴承的磨损和损坏过程,从而预测轴承的寿命和失效模式。
这种方法可以考虑到轴承的工况、材料和设计参数等因素,但需要准确的输入数据和复杂的数学计算,对于复杂轴承结构的寿命预测可能存在困难。
2.3 基于人工智能的寿命预测利用人工智能技术,如神经网络、遗传算法等,对轴承的寿命进行预测。
滚动轴承动力学失效分析与寿命评估
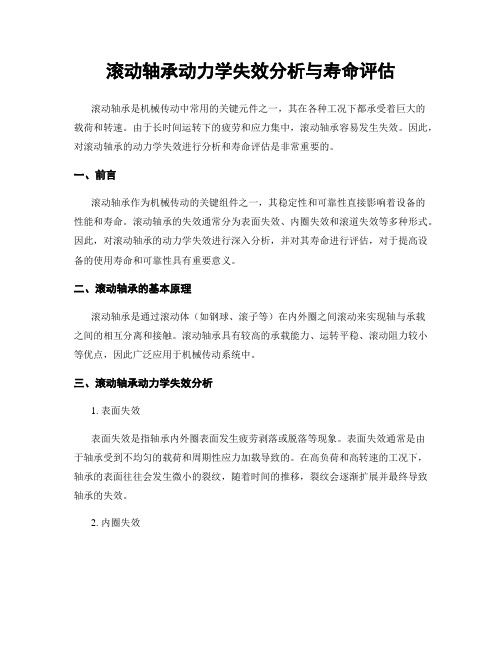
滚动轴承动力学失效分析与寿命评估滚动轴承是机械传动中常用的关键元件之一,其在各种工况下都承受着巨大的载荷和转速。
由于长时间运转下的疲劳和应力集中,滚动轴承容易发生失效。
因此,对滚动轴承的动力学失效进行分析和寿命评估是非常重要的。
一、前言滚动轴承作为机械传动的关键组件之一,其稳定性和可靠性直接影响着设备的性能和寿命。
滚动轴承的失效通常分为表面失效、内圈失效和滚道失效等多种形式。
因此,对滚动轴承的动力学失效进行深入分析,并对其寿命进行评估,对于提高设备的使用寿命和可靠性具有重要意义。
二、滚动轴承的基本原理滚动轴承是通过滚动体(如钢球、滚子等)在内外圈之间滚动来实现轴与承载之间的相互分离和接触。
滚动轴承具有较高的承载能力、运转平稳、滚动阻力较小等优点,因此广泛应用于机械传动系统中。
三、滚动轴承动力学失效分析1. 表面失效表面失效是指轴承内外圈表面发生疲劳剥落或脱落等现象。
表面失效通常是由于轴承受到不均匀的载荷和周期性应力加载导致的。
在高负荷和高转速的工况下,轴承的表面往往会发生微小的裂纹,随着时间的推移,裂纹会逐渐扩展并最终导致轴承的失效。
2. 内圈失效内圈失效是指轴承内圈出现裂纹、断裂或塑性变形等失效形式。
内圈失效通常是由载荷过大、轴承材料缺陷或装配不当等原因导致的。
内圈失效一般会引起设备的停机,对生产造成严重影响。
3. 滚道失效滚道失效是指轴承滚道出现疲劳剥落、腐蚀或齿槽形成等情况。
滚道失效通常是由于滚动体在滚道上的不均匀载荷和过大的摩擦力导致的。
滚道失效会使轴承的运行不稳定,产生异常声音和振动,从而严重影响设备的正常运转。
四、滚动轴承寿命评估方法滚动轴承寿命评估是通过对轴承的动力学失效进行分析和计算,从而预测轴承的使用寿命。
常用的评估方法有以下几种:1. 经验公式法经验公式法是根据过去的实验和应用经验建立的数学模型,通过计算得到轴承的寿命。
这种方法简单快捷,但其精度较低,在实际应用中通常用于初步估算。
滚动轴承寿命及可靠性试验评定方法研究_楼洪梁

记作 X ~ E V(μ, σ), μ是其位置参数 , σ是其
尺度参数 .
2 滚动轴承可靠性评价方法
由于 X ~ EV(μ, σ), 是位置尺度族 , 故其无 信息先验概率密度函数为[ 3 , 9] :
12 6
中 国 计 量 学 院 学 报
第 22 卷
π(m , φ)= φ-1 m-2
Key words:rolling bea ring s;sma ll sample ;life test
【收稿日期】 2010-11-01 【基金项目】 浙江省自然科学基金资助项目(N o.Y107738) 【作者简介】 楼洪梁(1963 ), 男 , 浙江省东阳人 , 博士 .主要研究方向为可靠性工程 .
1 滚动轴承寿命分布形式
滚动轴承寿命服从 Weibull 分布 , 其概率密
度函数与分布函数有两种形式 , 一是基于形状参
数 m 与特征寿命 η的形式 : f T(t)= mη-mt m-1 e-(t/ η)m
FT (t)=1 -ex p[ -(t/ η)m] , m , η, t >0 二是基于形状参数 m 与尺度参数 φ=η-m 的
r
m-1
r
滚动轴承标准
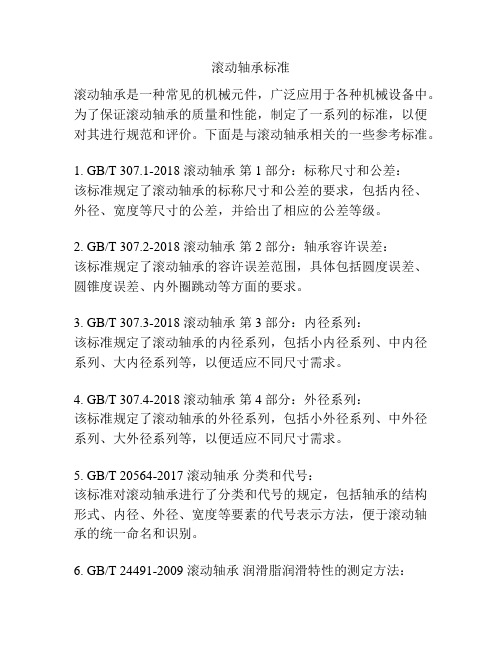
滚动轴承标准滚动轴承是一种常见的机械元件,广泛应用于各种机械设备中。
为了保证滚动轴承的质量和性能,制定了一系列的标准,以便对其进行规范和评价。
下面是与滚动轴承相关的一些参考标准。
1. GB/T 307.1-2018 滚动轴承第1部分:标称尺寸和公差:该标准规定了滚动轴承的标称尺寸和公差的要求,包括内径、外径、宽度等尺寸的公差,并给出了相应的公差等级。
2. GB/T 307.2-2018 滚动轴承第2部分:轴承容许误差:该标准规定了滚动轴承的容许误差范围,具体包括圆度误差、圆锥度误差、内外圈跳动等方面的要求。
3. GB/T 307.3-2018 滚动轴承第3部分:内径系列:该标准规定了滚动轴承的内径系列,包括小内径系列、中内径系列、大内径系列等,以便适应不同尺寸需求。
4. GB/T 307.4-2018 滚动轴承第4部分:外径系列:该标准规定了滚动轴承的外径系列,包括小外径系列、中外径系列、大外径系列等,以便适应不同尺寸需求。
5. GB/T 20564-2017 滚动轴承分类和代号:该标准对滚动轴承进行了分类和代号的规定,包括轴承的结构形式、内径、外径、宽度等要素的代号表示方法,便于滚动轴承的统一命名和识别。
6. GB/T 24491-2009 滚动轴承润滑脂润滑特性的测定方法:该标准规定了滚动轴承用润滑脂润滑特性的测试方法,包括外观、滴点、凝固点、流动性等指标的检测,以保证润滑脂的质量。
7. ISO 281:2007 Rolling bearings - Dynamic load ratings and rating life:这是国际标准组织ISO制定的滚动轴承动载荷额定值和额定寿命的标准,其中定义了一些计算滚动轴承额定寿命和额定动载荷的方法和公式。
8. DIN 620-1 Rolling bearings - Dimensions, boundary dimensions, tolerances:这是德国标准化协会制定的滚动轴承的尺寸、边界尺寸和公差的标准,与其他标准类似,该标准规定了滚动轴承的标准尺寸和公差范围。
滚动轴承 疲劳寿命及可靠性强化试验技术现状及发展

式中 . 卜
轴承使用寿命
料疲劳 极限应 力和考 虑应力体积 内 各 点应力及其深 度的情况下 ,给出 了I 模型 ,该模 型比LP 型考 虑 — H —模 的 更加 细 致 和 接 近 实 际情 况 。但
Zaes yE V认为该模 型高估 了轴 r tk
rr 最大动态剪切应 力振 厂一
1
, .
. ●
-
一
l
■
疲劳寿命及 可靠性强化试验技术 现状及发展
滚动轴 承是 广泛应 用的重要机 械 基础件 ,其 质量的好坏直 接影 响 到主机性能 的优劣 ,而轴承 的寿命 则是轴承 质量的综合反映 ,在中 国 轴承行业 “ 十一 五”发 展规 划中 , 重点要求开 展提高滚动轴承 寿命和 可靠性工程技术攻关 。 j 比轴承寿命 强化试验更 为广泛的 内 涵 ,它不仅 在寿命试验 方面 ,而且 在寿命试验 的设计 ,寿命数据的处 应 力 r、应 力循环 次数Ⅳ 受应 力 和 体积 啪 关系 :
维普资讯
■ 杭州轴承试验研 究中心有限公司/ 兴林 殷建军 李 ■ 瓦房店轴承 集团有限公 司/ 盈忠 谢 ■ 宁 波摩士轴承研 究院/ 刘和义 张玉环 ■ 重庆长江 轴承工 业有限公司/ 兴新 赵 ■ 中国石化润 滑油公司天 津分公司/ 吴宝杰
■ 杭 州诚信 汽车轴承有限公司/ 陈炳顺
结果的可靠性差,而强化试验则在 i
下 ,大大地缩短试 验时间 ,降低 了
保持接触疲劳失效机理一致的前提 j 动轴承 的疲劳寿 命服 从某一概率 分
布 ,这 就是 后 来 以其 名 字 命 名 的 We u 分布 ,认 为疲 劳裂纹产生于 il b1 滚 动表 面下最大 剪切应 力处 ,扩展 到表 面 ,产生疲劳剥落 ,We u 给 il bl 出 了生 存概 率 与表 面下 最大 剪切
轴承寿命预测和寿命评估技术研究
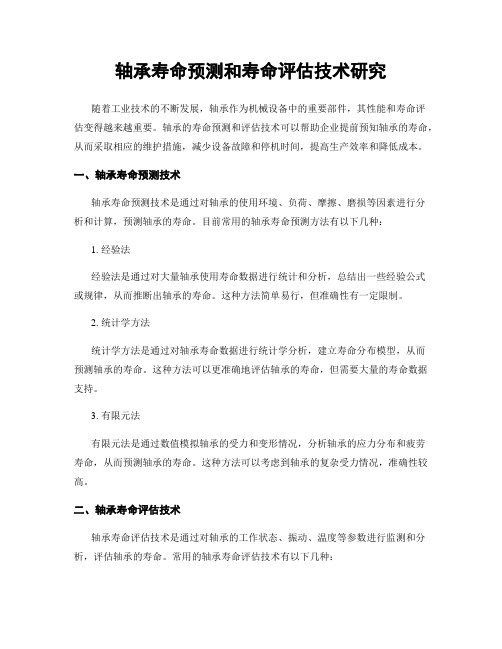
轴承寿命预测和寿命评估技术研究随着工业技术的不断发展,轴承作为机械设备中的重要部件,其性能和寿命评估变得越来越重要。
轴承的寿命预测和评估技术可以帮助企业提前预知轴承的寿命,从而采取相应的维护措施,减少设备故障和停机时间,提高生产效率和降低成本。
一、轴承寿命预测技术轴承寿命预测技术是通过对轴承的使用环境、负荷、摩擦、磨损等因素进行分析和计算,预测轴承的寿命。
目前常用的轴承寿命预测方法有以下几种:1. 经验法经验法是通过对大量轴承使用寿命数据进行统计和分析,总结出一些经验公式或规律,从而推断出轴承的寿命。
这种方法简单易行,但准确性有一定限制。
2. 统计学方法统计学方法是通过对轴承寿命数据进行统计学分析,建立寿命分布模型,从而预测轴承的寿命。
这种方法可以更准确地评估轴承的寿命,但需要大量的寿命数据支持。
3. 有限元法有限元法是通过数值模拟轴承的受力和变形情况,分析轴承的应力分布和疲劳寿命,从而预测轴承的寿命。
这种方法可以考虑到轴承的复杂受力情况,准确性较高。
二、轴承寿命评估技术轴承寿命评估技术是通过对轴承的工作状态、振动、温度等参数进行监测和分析,评估轴承的寿命。
常用的轴承寿命评估技术有以下几种:1. 振动监测技术振动监测技术是通过对轴承振动信号进行采集和分析,判断轴承的工作状态和寿命。
轴承在寿命接近尽头时,振动信号会有明显的变化,通过监测振动信号可以提前发现轴承故障,及时维修或更换。
2. 温度监测技术温度监测技术是通过对轴承温度进行实时监测和分析,评估轴承的工作状态和寿命。
轴承在磨损和故障时,会产生过热现象,通过监测轴承温度可以及时发现问题,采取相应的措施。
3. 油液分析技术油液分析技术是通过对轴承润滑油进行采样和分析,评估轴承的工作状态和寿命。
轴承在磨损和故障时,会产生金属颗粒和污染物,通过分析油液中的物质含量和性质变化,可以判断轴承的寿命和健康状态。
三、轴承寿命预测和评估技术的应用前景轴承寿命预测和评估技术的应用前景十分广阔。
滚动轴承寿命与可靠性试验的评定方法

对图估 计 、 参数 估 计 , 轴 承 L / I ≥ 球 。L 仇 14为合格 , . 即超过 L。 4 %为合格 ; 的 0 滚子轴 承 L, 。 lL o ≥12为合格 , / . 即超过 Lo 0 的2 %为 h
合格 。
到合格倍数 的值 ( K值 ) 即达 到 z 的倍数值 ; , 相应 的可靠度 R 等。 e
=
图估计 、 数估 计 , 以 给 出试 验 评定 结果 ; 参 可 对 于小 子样 失 效 数据 、 失 效 数据 的处理 采 用序 无
贯 试 验 , 短 时 间 就 能得 出评 定 结 果 , 以大 较 可
大提 高试 验 的效 率 。 ( 全文续 完 )
0 2 : . ) 最小无 失 效 时 间为 18 ; = . , 03 , 4hz
0 15 6 03 0 15 6 .03
一
Re=e一 ttlh — 0t ) ( /O b:e一 邪 l— 28 =4 5 0一 68
=9 8%
t <T 2 2<t , 33 2 l 即 36<T 2 2<75 , 续 试 48 继
验。
3 试 验验证
假设某 轴 承 Lo=10 , h 0 h N=1 和 N=8 2套 套, b:15 在 不 同 质 量 系数 、 同检 验 水平 风 ., 不
由于序贯试验风险较大 , 以判定加严。 所
N=1 时 , 轴 承 Z =14 检 验 水平 ( 2套 球 .、
=
Re e一
=e一
=9 2%
情况 3 当 L : 1=10 , I 1 I’ 续 试 8h t <T <t 继 2 J
验。 当 L = 2 h T 2 0 : 2 3 T <T2 2 2 0 ,2= 2 3 6 , 2 2 :
滚动轴承的检验标准

滚动轴承的检验标准一.轴承质量检测振动标准1.振动加速度国家标准(俗称Z标)该标准制定比较早,以测量轴承旋转时的振动加速度值,来判定轴承的质量等级,分为Z1、Z2、Z3由低到高三个质量等级。
目前国内轴承制造厂家仍然在使用,以振动加速度值来衡量轴承的优劣,仅仅简单地反映了INA轴承的疲劳寿命。
2.振动速度标准(俗称V标)由于原振动加速度标准还没有废除,所以该标准是以机械工业部颁标准出现的,是参考欧洲标准结合我国实际情况和需要制定的,以检测轴承振动速度来划分轴承的质量等级(等同于国家标准)。
分为V、V1、V2、V3、V4五个质量等级。
各种球轴承质量等级从低到高为V、V1、V2、V3、V4;辊子轴承(圆柱、圆锥)质量等级从低到高为V、V1、V2、V3四个质量等级。
它是以检测轴承不同频率段(低频、中频、高频)的振动速度来反映轴承的质量。
可以大体分析出轴承是否存在几何尺寸问题(如钢圈椭圆)、滚道/滚动体的质量问题,保持架的质量问题,比以振动加速度来考察轴承质量有了显著地进步。
目前国内出口欧洲的轴承、我国军方和航天工业均按照该标准进行轴承质量检测,同时检测欧洲INA进口轴承质量和分辨假冒进口轴承提供了可行的手段。
目前轴承质量检测存在两个标准并行的局面,而“Z标”质量等级很高的轴承,以“V标”检测时未必有好的质量表现,两者之间没有任何对应关系。
这在轴承的质量检测中是要特别注意的。
二.以振动测量仪检测在用轴承INA进口轴承在运行中,ISO2372标准虽然是以振动速度来判断振动是否超标,但在现场实际中要特别关注轴承加速度值的变化,轴承的损坏过程大多是初期表现为疲劳损伤,这点一般可以表现为明显的加速度升高,随着疲劳的发展,逐渐出现振动速度和位移的升高,预示着轴承出现了疲劳破坏。
特别对于轴承进行检测时,要细心关注振动值是否出现不稳定地摆动(建议使用模拟量的指针式仪器,可以观察的非常明显),如果出现摆动,预示着出现了不稳定的振动信号,加速度也大,特别是速度同时增大,极有可能存在轴承“耍套”故障。
滚动轴承的测量和检验的原则及方法(一讲)

总结滚动轴承的测量和检验的原则及方法
测量和检验的重要性
滚动轴承的测量和检验是确保其性能 和质量的关键环节,通过精确测量和 全面检验,可以评估滚动轴承的各项 性能指标,如旋转精度、摩擦阻力、 振动等。
测量和检验的原则
在滚动轴承的测量和检验中,应遵循 以下几个原则,即准确性、可靠性、 重复性和一致性。准确性是指测量和 检验的结果应与实际值相符,可靠性 则要求测量和检验的结果应稳定可靠 ,重复性和一致性则要求测量和检验 的方法和过程应保持一致,以确保结 果的准确性和可靠性。
声音检验法
总结词
通过听取轴承运转时的声音,判断其是否正常。
详细描述
声音检验法是通过听取滚动轴承运转时的声音来判断其质量状况。经验丰富的检验员可以通过听声音 来判断轴承是否存在异常,如不正常的噪音、振动或其他异响。这种方法需要检验员具备丰富的实践 经验和听力辨别能力。
振动分析法
总结词
通过分析轴承运转时的振动信号,判断 其是否存在故障或异常。
比较测量法
将待测滚动轴承与标准样 品进行比较,通过对比得 出测量结果。
间接测量法
通过测量与滚动轴承相关 联的其他参数,间接推算 出滚动轴承的某些参数值。量设备的选择通用测量设备
适用于大多数滚动轴承的测量, 如卡尺、千分尺等。
专业测量设备
针对特定类型或规格的滚动轴承 ,需要使用专业的测量设备进行 精确测量。
对于大型或特殊结构的轴承,应采用相应的专用检验设备和方法进行测量和检验。
在选择检验方法时,应充分考虑其准确性和可靠性,同时还应考虑其操作简便性和 经济性。
检验设备的选择
根据确定的检验方法, 选择合适的检验设备。
对于大型或特殊结构 的轴承,应选择专用 的检验设备进行测量 和检验。
滚动轴承寿命与可靠性试验方法

滚动轴承寿命与可靠性试验方法
张伟;汤洁
【期刊名称】《轴承》
【年(卷),期】2010(000)011
【摘要】通过对GB/T 24607-2009<滚动轴承寿命与可靠性试验及评定>标准的详解,介绍了滚动轴承寿命及可靠性试验方法,提供给生产企业、用户、第3方认证机构一个统一的试验规范.
【总页数】4页(P55-58)
【作者】张伟;汤洁
【作者单位】洛阳轴承研究所有限公司,河南,洛阳,471039;洛阳轴承研究所有限公司,河南,洛阳,471039
【正文语种】中文
【中图分类】TH133.33
【相关文献】
1.ABLT滚动轴承寿命及可靠性强化试验机载荷校准 [J], 卓继志;严春声;李兴林
2.滚动轴承寿命与可靠性试验方法 [J], 张伟
3.滚动轴承寿命与可靠性试验的评定方法 [J], 张伟
4.滚动轴承寿命与可靠性试验的评定方法 [J], 张伟
5.滚动轴承寿命及可靠性试验监测诊断技术实践 [J], 李兴林;张仰平;曹茂来;张燕辽;陆水根;陈炳顺
因版权原因,仅展示原文概要,查看原文内容请购买。
滚动轴承质量的经验鉴定方法
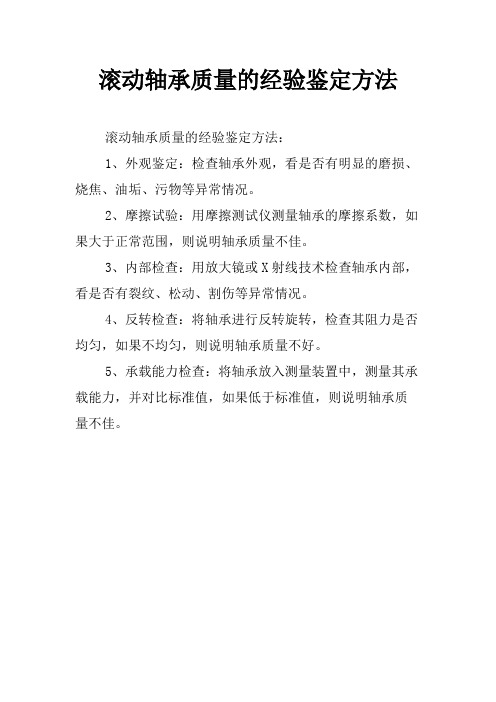
滚动轴承质量的经验鉴定方法
滚动轴承质量的经验鉴定方法:
1、外观鉴定:检查轴承外观,看是否有明显的磨损、烧焦、油垢、污物等异常情况。
2、摩擦试验:用摩擦测试仪测量轴承的摩擦系数,如果大于正常范围,则说明轴承质量不佳。
3、内部检查:用放大镜或X射线技术检查轴承内部,看是否有裂纹、松动、割伤等异常情况。
4、反转检查:将轴承进行反转旋转,检查其阻力是否均匀,如果不均匀,则说明轴承质量不好。
5、承载能力检查:将轴承放入测量装置中,测量其承载能力,并对比标准值,如果低于标准值,则说明轴承质量不佳。
- 1、下载文档前请自行甄别文档内容的完整性,平台不提供额外的编辑、内容补充、找答案等附加服务。
- 2、"仅部分预览"的文档,不可在线预览部分如存在完整性等问题,可反馈申请退款(可完整预览的文档不适用该条件!)。
- 3、如文档侵犯您的权益,请联系客服反馈,我们会尽快为您处理(人工客服工作时间:9:00-18:30)。
滚动轴承寿命与可靠性试验的评定方法轴承技术2011年第2期?29?滚动轴承寿命与可靠性试验的评定方法国家轴承质量监督检验中心张伟轴承行业对轴承寿命与可靠性试验评定方法的研究已有很长时间,1985年洛阳轴承研究所首次制定了滚动轴承寿命试验评定方法ZQ37—85《滚动轴承寿命可靠性考核试验方法》,后于1991年修订为JB/CQ37—91《滚动轴承寿命可靠性考核试验方法》;又于1997年修订为JB/T50093—1997《滚动轴承寿命及可靠性试验评定方法》.多年来,滚动轴承寿命及可靠性试验评定方法对促进滚动轴承寿命可靠性质量的提高,行业的质量评定以及国内外用户的产品验收起到了重要的作用.为适应新形势下轴承质量水平的不断提高,以及和国外轴承质量接轨问题,特制订GB/T24607—2009《滚动轴承寿命与可靠性试验及评定》标准,该标准的实施无疑是对滚动轴承寿命可靠性质量的一次促进,势必将对提高我国滚动轴承的寿命可靠性水平起到积极的作用.1合格评定轴承寿命可靠性试验原始数据经数据处理后得到相关参数,对参数进行一系,即达到Lm/Li的倍数值.2试验数据处理常规试验数据处理一般依据二参数韦布尔(Weibul1)分布函数进行分析处理,使用图估计法和参数估计法,图估计法较简便直观,一般可优先采用图估计法;而对试验数据较少的或无失效数据的情况一般采用序贯试验评定方法.2.1Weibul1分布图估计法1)图估计目的通过对试验轴承样品的完全试验,截尾试验等,得出试验数据,根据图估计法在Weibul1 分布图上估计出分布参数,并得出试验结果及评定结果.2)Weibul1分布图轴承寿命服从二参数韦布尔(Weibul1)分布函数:f)=1一e一(詈)作变换得:其对数形式是:1lnlnblnL—blnv令),lnln南,ln,B—bin则就把上式变成x—Y直角坐标系中一条直线方程:Y=bX+B这是一条以b为斜率的直线,若能求出参数b,v,则直线唯一确定.?3O?轴承技术2011年第2期坐标点(x,Y)对应于1(1nL,lnln)X=lnLL=ex根据L=e的与L=e的对应关系和,(L)=1一e的F()与y的对应关系分别把对应的值记在轴上,把y的对应值记在y轴上(横轴为,纵轴为F),由上述原理即可制成Weibul1分布概率图.轴承寿命Weibul1分布曲线是以b为斜率,以t,为特征寿命的一条直线,b表示轴承寿命的离散程度或轴承寿命质量的稳定性,t,是当F()=0.632时的轴承寿命,求出参数6,t,直线可唯一确定.3)一般的图估计一般对于失败数据不少于6个的试验数据评定,可用图估计方法.失效数据越少,图估计的精度就越低.横坐标为厶(即各试验数据),纵坐标为F一n(厶)(即失效概率),在Weibu11分布图上依次描点,然后按照各点的位置,配置分布直线.配置直线时,各点须交错,均匀地分布在直线两边,且F()=0.3~0.7附近的数据点与分布直线的偏差应尽可能地小.由直线可求Weibul1分布斜率b(直线上某点的纵坐标与横坐标之比).斜率b越大,说明轴承寿命数据较集中,轴承寿命质量稳定; 反之斜率b越小,轴承寿命数据离散,轴承寿命质量不稳定.由直线可求特征寿命,是当F()=0.632(纵轴为63.2%)时的轴承寿命,即破坏概率为63.2%时的轴承寿命.由参数6,,再分别求出基本额定寿命的试验值.(纵轴为10%),中值额定寿命的试验值L卯(纵轴为50%),计算出可靠度e等.4)分组淘汰图估计分组淘汰试验方法可缩短试验周期,但试验风险比一般完全试验和定时(数)截尾试验大.试验中,每一分组中出现一个失效样品即停止试验,然后用各组的最短寿命数据在Weibul1分布概率纸上描点,配置直线,再由该直线求得该批样品的分布直线.5)图估计实例例1:某厂生产的深沟球轴承L..=100h,N=8套,试验结束,得到8个失效数据,分别是80h,110h,155h,170h220h,240h300h380h用Weibul1分布图估计参数b及,LL50,Re 等值.a)由8个失效数据,配置直线A(见图1).i,纵坐标为F()=矗,故8个点的坐标值分别为:(8O,0.083),(1lO,0.202)……(380,0.917),将其描在Weibul1分布概率纸上,配置直线A.b)由直线A求出6,t,,Llot,.Lsot-,Re等值.b=2,=250h,L10=85h,Lso=200h,Re=86%c)L10l/L10–85/100<1.4,故判定该批轴承样品不合格.例2:某厂生产的深沟球轴承L,0–100h,N=32套,分8组7//,=8,每组4套同时上机试验N=4套.每组有一套轴承失效即停机,试验结束,得到8个分组的最短寿命分别为10h, 110h,155h,170h,220h,24Oh,300h,380h.用Weibul1分布图估计参数b及,150,e等.本例为分组淘汰图估计例.先按例1求出分布直线A,再由分布直线A求分布直线B.a)由于每组有4套轴承,故将待求的直线B上M点的纵坐标记为F()=}=0.159.b)作三条平行线:过F()=50%作横轴平行线与直线A交于点c,过C作纵轴平行线与过F(L)=0.159的横轴平行线交于点M. (在直线A上取纵坐标为F()=50%的点C,轴承技术2011年第2期?3l?由C做纵轴平行线,并与过F(L)=0.159的横轴平行线交于点M0)C)过M点做平行与直线A的平行线B.也可由解析法求直线B:N当为每组套数时,B的特征寿命”B=×z虿=250×4-r=500h.由直线B求出6,,L,Re等.b=2,=500h,Ll0=160h,L1ol=400h,Re=96%345L/h图1Weibul1分布图估计a)t1m/L0–160/100>1.4,故判定该批轴承样品合格.2.2WeibuU分布参数估计1)Weibul1分布参数估计的目的通过试验轴承样品的完全试验,载尾试验,得出试验数据,根据Weibul1分布数据处理估计出分布的参数,并得出试验结果及评定结果.截尾试验失效数据一般应不少于6个.若失效数据太少,参数估计的精度就降低.通过数据处理确定Weibul1分布的两个参数b,v.样本容量Ⅳ,经试验后得到的实际寿命为: 完全试验≤L2……≤厶……≤i=1,2……Ⅳ;定数截尾试验£1≤三2……≤厶≤L,i=1.2……r<N分组淘汰试验L,≤:…………≤i=1,2……;m=Ⅳ/Ⅳ对于完全试验和定数截尾试验,纵坐标(失效概率)(厶)=对于其他非完全试验,计算破坏概率F (厶)时,应将上式的i进行修正.修正方法见表2.轴承寿命Weibul1分布参数6,的估计,当Ⅳ≤25时,用最佳线性不变估(BLIE)方法;当N>25时,用最大似然估计(ML)方法(略).2)最佳线性不变估计(BLIE):完全试验:b=[_∑c1(J7v,N,i)lnL]1n13=∑D1(Ⅳ,N,i)1nLi定数截尾试验:b_一∑c1(Ⅳ,r,i)lnL]1nv=∑D1(Ⅳ,r,i)lnLi当r=N时即为完全试验.分组淘汰试验:b=[三c(m,m,i)lnL]1nv=-~-1nN+∑D1(m,m,)lnLiui=1一当N=1时即为完全试验.最佳线性不变估计系数CD见《可靠性试验用表》.3)依据b,1J,估计L1o,L50及Re当F(三)=0.10时,基本额定寿命的试验值:L1=(0.10536)当F(L)=0.50时,中值寿命:L5.=?(0.69315)当L:Lloh,可靠度:Re=e一()(时刻对应的可靠度)4)参数估计实例∞酏∞∞m4,2求,(,I‰?32-轴承技术2011年第2期例3:对例1的数据用Weibun分布估计参数b及t,,并计算L.,£Re等值.本例为完全试验,最佳线性不变估计系数为C1(Ⅳ,N,i),D1(N,N,i).若为定数截尾试验,失效数一般不能少于试验样品容量的2/3,即r<N,且按失效数据大小排列,一般未失效样品数据均大于失效样品数据,最佳线性不变估计系数为C(Ⅳ,r,),D (Ⅳ,r,).参数估计列于表1,并完成各项计算.表1WeibuU分布参数估计表t一4%厶lnLC,(N,N,i)C,lnLD1(N,N,)D,lnLⅣ+.18.33804.3820—0.0933一O.4O88O.034l0.1494 220.2311O4.7006—0.0989—0.46490.0536O.2519 332.141555.0434—0.0940—0.47410.07350.3707 444.O51705.1358—0.0798—0.40980.09510.4884 555.952205.3936—0.0539—0.29070.1198O.6462 667.862405.4806—0.0102—0.05590.14990.8215 779.7630o5.70380.06930.39530.19121.0906 891.673805.94020.36072.14260.28291.6805NN∑0.4337∑5.4992i1i1b=[∑C1(N,N,i)lnL]~=2.3057N==11nt,=∑D1(Ⅳ,Ⅳ,)lnL=5.4992=245hL1m=?(O.10536)=92hL5m=?(0.69315)=210hRe:e一(了LlOh):e一()?姗:88%o/L.–92/100<1.4,故判定该批轴承样品不合格.例4:对例2的数据用Weibul1分布估计参数b及t,,并计算舶等值.对样本容量为Ⅳ的试验样品进行试验时,因为有各种各样的原因使某一试样中停试验, 此数据就是未失效数据(按数据大小排列,未失效数据可能在失效数据之间),一般数据处理方法是不考虑未失效数据,这样就不能真实的反映整体的情况,影响轴承质量水平评价. 所以含有未失效数据的处理要对失效数据进行位置修正.本例为非完全试验(分组淘汰试验),同样也含有未失效数据.其修正位置增量: △=(这里的为全部试验样本容量,即为32)=Ii一1+△当=OJ『=O(即,0=O):非完全试验时i的修正值:非完全试验时,实际寿命由小到大排列的统计量序列△:非完全试验修正时的位置增量非完全试验F()的修正值的计算见表2.最佳线性不变估计系数为c(m,m,),D. (m,m,),参数估计见表3.轴承技术2011年第2期?33?表2非完全试验时,(厶)的修正值J厶L△iItF(L=()%1801112.16511O21.1O342.1O345.57915531.23593.33939.381317041.41244.7517l3.741722051.66176.4134l8.872124062.O4518.458525.182530o72.726811.185333.6O2938084.362915.548247.06表3非完全试验WeibuH分布参数估计表)(%厶lnLfCJ(m,m,i)C,1nLiD,(m,m,i)D,lnLf12.16804.3820—0.0933—0.40880.03410.149455.571l04.7005一O.O989—0.46490.05360.2519 99.381555.0434—0.0940—0.47410.07350.3707l313.7417O5.1358一O.O798—0.4O980.09510.4884 1718.8722O5.3936—0.0539—0.29O70.1198O.6462 2125.1824O5.4806—0.0102—0.05590.14990.8215 2533.6030o5.70380.06930.39530.19121.0906 2947.O63805.94020.36072.14260.28291.6805mm∑0.43375.4992i1b=[c,(m,m,i)lnLi]~=2.30571nv={_Ⅳ+三D,(m,m,)lnLiDi=1’’+5?4992-o.61004=446hL10f=?(0.10536)=170h=?(0.69315)=380hRe:e一(LlOh):e一()?姗:97%0/L.=170/100>1.4,故判定该批轴承样品合格.2.3序贯试验方法本标准所选取的后验序贯抽样检验方案,是序贯抽样检验的一种.它适用性强,可利用原有试验设备,特别是当疲劳破坏数据较少时,也可给判定结论,便于考核及订户验收;方?34?轴承技术2011年第2期法简便,运算少,数据处理程序化,表格化,便于推广应用.完全试验,截尾试验一般时间较长才能得出结果,而对小子样失效数据,无失效数据的处理易采用序贯试验验,较短时间就能得出结果.序贯试验用于试验设计而不是试验判定.第一套轴承如果出门或不人门,则直接判合格或不合格;如果在继续检验区,则用替换轴承继续检验.1)替换试验试验采用有替换试验序贯检验,按失效顺序一套一套逐次进行检验判定.当有5套轴承样品失效时停试,并做出合格与否的判定.试验中替换轴承坪品的换效数据也参与判定. 这种方法用于小于样或无失效数据的处理. Ⅳ(有替换同时试验的轴承套数)套轴承同时上机试验,当第一套轴承试到上q时间失效(这时其他一l套轴承也试到时间,但未失效),为保证套轴承同时上机试验状态,需换上一套待试样品继续试验,该样品称为替换轴承.替换轴承(L2)失效时,这时总试验时间为+,另_Ⅳ一1套轴承的试验时间均为+2o2)检验判定参数综合国内外资料,取韦布尔分布斜率:b=1.5检验水平:根据选取的,风险值分为四组,检验水平由宽到严.一般用户验收的试验取水平I或Ⅱ,行业及第三方认证机构的试验取水平Ⅱ或Ⅲ,制造厂内部的试验取水平Ⅲ或Ⅳ,如表4所示.表4检验水平检验水平IⅡⅢⅣ0.2O.2O.2O.1风险0.20.3O.5O.7:合格风险,接受风险或显着性水平,1一称置信度.:不合格风险,拒绝风险.本标准判定检验时配合使用.有时称为使用方风险.3)检验判定门限对不同的值可以组成多个检验水平,图2为不同检验区示意图.由图可以看出,水平I,Ⅱ, Ⅲ接受区一样,但拒收区增加,即继续检验区减小;水平Ⅳ接收区减小,拒收区增加.这样从检验水平Ⅳ检验水平逐步加严.螽培数N12lO8642O=IC玎L0n3000_,ln£,,,,y’,,一///,1,椎自蜮j,//墩’.,/./j’队bJ鼍I/2468l012l4l6l3202224图2检验区示意图(A是,B是)与表4的,口对应的门限系数,见表5.从图2及表5看出,如果取=0.3,=0.7,即两条检验判定线重合,说明检验严,要么合格,要么不合格,中间没有继续检验区.表中给出了一个i=0的点,在判断格式里为tlO点,即无失效门限tlO,r=0时的接受门限值,该点尤其适用于军品轴承试验套数少, 而又要求无失效试验的特点.4)检验判定格式实际考核时,第i个轴承样品失效时的接受门限t1=(L/N).第i个轴承样品失效时的拒绝门限t2i=L/N8T6令:=Z.t,=Z’/JlOh轴承技术2011年第2期?35?检验判定格式见表6.表5与o~,13对应的门限系数,值t012345O.12.3023.8905.3226.68l7.9949.274 0.21.6102.9944.2795.5156.7217.906 0.31.2o42.4393.6164.7625.8907.0o6 0.20.8241.5352.2973.0903.904O.31.0981.9142.7643.6344.5l70.51.7782.6743.6724.7615.6700.72.4393.6l64.7625.8907.0o6表6检验判定格式O12345£”tlo£l1£l213t14t15l2f21f22t255)检验判定式N.(~LslN)为试验时间,即h,尚无失效轴承出现, 这时l2套轴承均试至200h.因:(军12/):)~:200’~=2828>t】o=2806,合格停试. 判定该批轴承样品合格.(未完接下期)摘自《滚动轴承标准化》2010年第3期。