第一篇-材料成型与RT比
材料成型原理及工艺

材料成型原理及工艺材料成型是指将原料通过一定的工艺过程,使其获得所需形状的过程。
在材料成型中,最常见的方式包括热成型、冷成型和粉末冶金成型等。
这些成型工艺的原理和应用在各个领域都有广泛的应用。
热成型是指通过加热材料使其软化并塑性变形以达到所需形状的一种成型方法。
主要包括热压成型、热拉伸成型、热挤压成型等。
其原理是通过加热使材料达到一定的软化点或熔点,然后通过外力施加,使材料塑性变形并成型。
热成型适用于塑料、玻璃、金属等材料的成型,并且可以制造复杂形状的产品。
冷成型是通过机械力作用在室温下进行的成型方法。
冷成型主要包括挤压成型、压铸成型、冷轧成型等。
其中,冷挤压是常见的一种冷成型方式,主要应用于金属材料的成型。
其原理是通过施加机械力,使材料在室温下产生塑性变形,并达到所需形状。
具有高精度、高效率的特点。
粉末冶金成型是一种将粉末材料在一定温度下进行成型的方法。
其主要过程包括压制和烧结两个过程。
首先将粉末材料经过一定的工艺处理得到一定的物理性质,然后该粉末被用来制造一种新型的成型工艺。
原理是通过压制使粉末粒子结合,并在一定的温度下进行烧结,最终得到所需形状的产品。
其优点是可以制造复杂形状的产品,同时可以利用废料进行再利用。
在材料成型过程中,还有一些辅助工艺和辅助设备的应用,以实现更好的成型效果。
例如模具是实现材料成型的重要工具,通过对模具进行设计和制造,可以获得不同形状和尺寸的产品。
在热成型过程中,需要控制加热温度、保持时间、冷却速率等参数,以确保产品的质量。
在冷成型过程中,需要选择合适的冷却介质和冷却方式,以使产品达到所需的硬度和强度。
在粉末冶金成型过程中,需要控制压制力、压制时间和烧结温度等参数,以实现产品的致密度和力学性能。
总结起来,材料成型的原理和工艺非常丰富多样,根据不同材料和产品的要求选择合适的成型方式可以实现高效率、高质量的制造。
随着科技的进步和工艺的改进,材料成型在各个行业的应用也越来越广泛。
材料成型基本原理
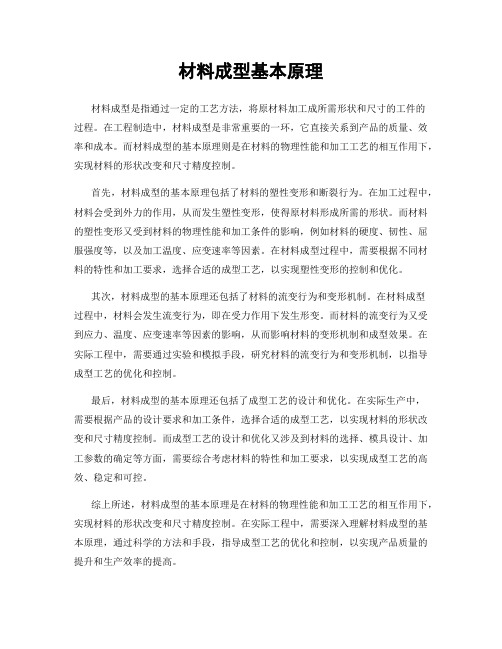
材料成型基本原理材料成型是指通过一定的工艺方法,将原材料加工成所需形状和尺寸的工件的过程。
在工程制造中,材料成型是非常重要的一环,它直接关系到产品的质量、效率和成本。
而材料成型的基本原理则是在材料的物理性能和加工工艺的相互作用下,实现材料的形状改变和尺寸精度控制。
首先,材料成型的基本原理包括了材料的塑性变形和断裂行为。
在加工过程中,材料会受到外力的作用,从而发生塑性变形,使得原材料形成所需的形状。
而材料的塑性变形又受到材料的物理性能和加工条件的影响,例如材料的硬度、韧性、屈服强度等,以及加工温度、应变速率等因素。
在材料成型过程中,需要根据不同材料的特性和加工要求,选择合适的成型工艺,以实现塑性变形的控制和优化。
其次,材料成型的基本原理还包括了材料的流变行为和变形机制。
在材料成型过程中,材料会发生流变行为,即在受力作用下发生形变。
而材料的流变行为又受到应力、温度、应变速率等因素的影响,从而影响材料的变形机制和成型效果。
在实际工程中,需要通过实验和模拟手段,研究材料的流变行为和变形机制,以指导成型工艺的优化和控制。
最后,材料成型的基本原理还包括了成型工艺的设计和优化。
在实际生产中,需要根据产品的设计要求和加工条件,选择合适的成型工艺,以实现材料的形状改变和尺寸精度控制。
而成型工艺的设计和优化又涉及到材料的选择、模具设计、加工参数的确定等方面,需要综合考虑材料的特性和加工要求,以实现成型工艺的高效、稳定和可控。
综上所述,材料成型的基本原理是在材料的物理性能和加工工艺的相互作用下,实现材料的形状改变和尺寸精度控制。
在实际工程中,需要深入理解材料成型的基本原理,通过科学的方法和手段,指导成型工艺的优化和控制,以实现产品质量的提升和生产效率的提高。
RT标准讲解

吉林亚新工程检测有限责任公司
1 范围 JB/4730的本部分规定了承压设备金属材料受压元件的熔化焊对接接头的 射线和 射线 范围: 的本部分规定了承压设备金属材料受压元件的熔化焊对接接头的X射线和 的本部分规定了承压设备金属材料受压元件的熔化焊对接接头的 射线和γ射线 检测技术和质量分级要求。 本部分适用于承压设备受压元件的制造、安装、在用检测中对接焊 检测技术和质量分级要求。 本部分适用于承压设备受压元件的制造、安装、 接接头的射线检测。用于制作焊接接头的金属材料包括碳素钢、低合金钢、不锈钢、铜及铜合 接接头的射线检测。用于制作焊接接头的金属材料包括碳素钢、低合金钢、 不锈钢、 铝及铝合金和钛及钛合金、镍及镍合金. 金、铝及铝合金和钛及钛合金、镍及镍合金
在长度为在长度为12t的任意选定条形缺陷评定区内相邻缺陷间距不超过的任意选定条形缺陷评定区内在长度为的任意选定条形缺陷评定区内相邻缺陷间距不超过6l的任一组条形缺陷的累计长度应不超过但最小可为但最小可为4的任一组条形缺陷的累计长度应不超过但最小可为iii在长度为6t的任意选定条形缺陷评定区内在长度为的任意选定条形缺陷评定区内相邻缺陷间距不超过3l任一组条形缺陷的累计长度应不超过t但最小可为任一组条形缺陷的累计长度应不超过最小值的规定是考虑防止薄工件评定过严ii级母材小于最小值的规定是考虑防止薄工件评定过严级母材小于12mmiii小于9mm最大值是考虑防止厚工件评定过松级母材大于最大值是考虑防止厚工件评定过松ii级母材大于小于最大值是考虑防止厚工件评定过松级母材大于60mmiii母材大于45mm材大于在球罐设备环缝检测评定时要特别注意多张底片的联合评定在球罐设备环缝检测评定时要特别注意多张底片的联合评定标准规定任意选定条形评定区缺陷很可能跨越多张底片
《逆向工程及快速成型原理》讲义——RT篇

概 论
快速制模:
方法
直接法:
– 优点是制模工艺简单、精度较高、工期短,缺点是单件模 具成本较高,适用于样机、样件试制。 – 通过SLA 或SLS 法,直接用树脂、粉末塑料(如ABS)等 制成凸、凹模,可以作成薄板的简易冲模,汽车覆盖件成 形模等。这些简易模具的寿命是50~1000 件,适用于产 品试制阶段。 – 采用特殊的纸质利用 LOM 工艺方法可直接制造出纸质模 具,坚如硬木,可耐200℃高温,可用作低熔点合金的模 具或试制用注塑模以及精密铸造用的蜡模成形模,还可以 代替砂型铸造用的木模。 – 用FDM 法直接制成金属模。将不锈钢粉末用FDM 法制成 金属型后,经过烧结、渗铜等工艺渗铜等工艺制成了具有 复杂冷却液道的注塑模
SLA成形的树脂壳-铝填充环氧树脂衬模
成形部分采用SLA成形的型芯/型腔壳 采用铝填充环氧树脂填充壳背面
桥 模
铝填功能零件制造中可能存在材料的收缩,因此, 原型的形状和尺寸应该适当修正以补偿材料收缩引起的变 形。 – 另一个问题是由制模方法所决定的,用于制造环氧树脂模 具的快速原型应带有适当的拔模斜度。 – 首先由快速成形技术制作原型(实际最终零件)用作母模, 作为母模的原型件必须经过表面打磨和抛光
汽车保险杠ABS塑料件
硬塑料件、透明塑料 件和弹性塑料件
软 模
软模
应用
用硅橡胶模浇注的透明光学件
有许多密集小孔的网格式塑料件
硅橡胶模与浇注的蜡模
硅橡胶模和浇注的弹性件
形状复杂的塑料件及其硅橡胶模
材料成型技术基础知识点总结
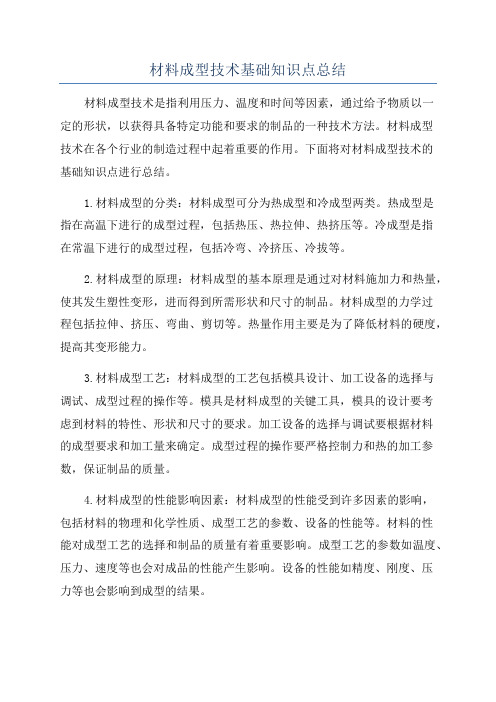
材料成型技术基础知识点总结材料成型技术是指利用压力、温度和时间等因素,通过给予物质以一定的形状,以获得具备特定功能和要求的制品的一种技术方法。
材料成型技术在各个行业的制造过程中起着重要的作用。
下面将对材料成型技术的基础知识点进行总结。
1.材料成型的分类:材料成型可分为热成型和冷成型两类。
热成型是指在高温下进行的成型过程,包括热压、热拉伸、热挤压等。
冷成型是指在常温下进行的成型过程,包括冷弯、冷挤压、冷拔等。
2.材料成型的原理:材料成型的基本原理是通过对材料施加力和热量,使其发生塑性变形,进而得到所需形状和尺寸的制品。
材料成型的力学过程包括拉伸、挤压、弯曲、剪切等。
热量作用主要是为了降低材料的硬度,提高其变形能力。
3.材料成型工艺:材料成型的工艺包括模具设计、加工设备的选择与调试、成型过程的操作等。
模具是材料成型的关键工具,模具的设计要考虑到材料的特性、形状和尺寸的要求。
加工设备的选择与调试要根据材料的成型要求和加工量来确定。
成型过程的操作要严格控制力和热的加工参数,保证制品的质量。
4.材料成型的性能影响因素:材料成型的性能受到许多因素的影响,包括材料的物理和化学性质、成型工艺的参数、设备的性能等。
材料的性能对成型工艺的选择和制品的质量有着重要影响。
成型工艺的参数如温度、压力、速度等也会对成品的性能产生影响。
设备的性能如精度、刚度、压力等也会影响到成型的结果。
5.材料成型的应用:材料成型技术广泛应用于诸多领域,如汽车制造、航空航天、电子、建筑等。
汽车制造中的车身、发动机零部件等都需要经过冲压成型、挤压成型等工艺。
航空航天中的飞机壳体、涡轮叶片等也需要通过成型工艺进行制作。
电子产品中的外壳、散热器等也需要通过成型技术来获得所需的形状。
建筑领域中的钢结构、混凝土构件等亦需要经过成型工艺来生产。
综上所述,材料成型技术是制造过程中不可或缺的一部分。
通过了解材料成型的分类、原理、工艺、性能影响因素和应用,可以更好地理解和应用材料成型技术,提高制品的质量和生产效率。
材料成型概论第二章材料成型的基础220110427资料

挤压模具
结构钢—工程结构钢、机械结构钢
工程结构钢:大多规定了钢的最低抗拉强度、最低屈 服强度,使钢具有一定的综合力学性能,保证材料设计 和使用中结构部件的最低安全要求。 工程结构钢分为: 1.通用工程结构钢—碳素结构钢、低合金高强度结构钢 2.专用工程结构钢—压力容器用钢、锅炉用钢、桥梁用 钢;焊接用钢、汽车大梁用钢;地质钻探钢管用钢、 钢轨、铆螺钢;船用钢、管线钢、锚链钢等。
金属压力加工产品标准和技术要求
内容包括: 3 验收试验标准—验收规则、做试验时的取样部位、
试样形状和尺寸、试验条件和试验方法。 4 交货标准—钢材交货时的包装和标志方法,以及资
料证明书内容等。
2.2.1 钢铁材料的种类及编号
工程上常采用的分类方法主要有:
按主要性能及用途分类 按化学成分分类 按合金元素种类分类 按质量等级分类 按冶炼方法分类 按金相组织分类
材料成型概论
第一章 材料成型概述 第二章 材料塑性成型的基础 第三章 轧制成型 第四章 挤压成型 第五章 拉拔成型 第六章 锻造成型 第七章 冲压成型 第八章 陶瓷成型
2.2 金属材料的种类及编号
2.2.1 钢铁材料的种类及编号 2.2.2 铝 铝合金及铜 铜合金 2.2.3 钛及钛合金
高级优质钢 ≤0.030 ≤0.030 ≤0.025 ≤0.025
特级优质钢 ≤0.025 ≤0.020 ≤0.025 ≤0.015
3. 钢材按用途分类
工程用钢 建筑、桥梁、船舶、车辆
结构钢
滚动轴承钢
刃具钢
工 具 钢 模具钢
量具钢
特 殊 性 不锈钢 能 钢 耐热钢
耐磨钢
2.钢材按质量分类
钢的质量是以磷、硫的含量来划分的。
材料成型工艺基础
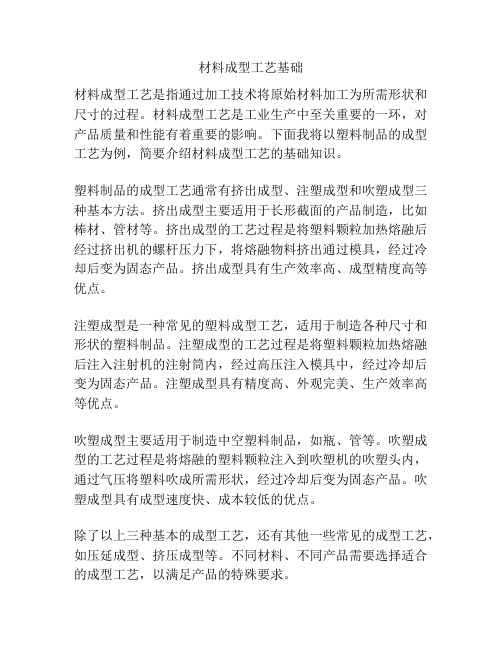
材料成型工艺基础材料成型工艺是指通过加工技术将原始材料加工为所需形状和尺寸的过程。
材料成型工艺是工业生产中至关重要的一环,对产品质量和性能有着重要的影响。
下面我将以塑料制品的成型工艺为例,简要介绍材料成型工艺的基础知识。
塑料制品的成型工艺通常有挤出成型、注塑成型和吹塑成型三种基本方法。
挤出成型主要适用于长形截面的产品制造,比如棒材、管材等。
挤出成型的工艺过程是将塑料颗粒加热熔融后经过挤出机的螺杆压力下,将熔融物料挤出通过模具,经过冷却后变为固态产品。
挤出成型具有生产效率高、成型精度高等优点。
注塑成型是一种常见的塑料成型工艺,适用于制造各种尺寸和形状的塑料制品。
注塑成型的工艺过程是将塑料颗粒加热熔融后注入注射机的注射筒内,经过高压注入模具中,经过冷却后变为固态产品。
注塑成型具有精度高、外观完美、生产效率高等优点。
吹塑成型主要适用于制造中空塑料制品,如瓶、管等。
吹塑成型的工艺过程是将熔融的塑料颗粒注入到吹塑机的吹塑头内,通过气压将塑料吹成所需形状,经过冷却后变为固态产品。
吹塑成型具有成型速度快、成本较低的优点。
除了以上三种基本的成型工艺,还有其他一些常见的成型工艺,如压延成型、挤压成型等。
不同材料、不同产品需要选择适合的成型工艺,以满足产品的特殊要求。
材料成型工艺的基础包括材料的选择、模具设计、工艺参数的设定等。
材料的选择是成型工艺的基础,不同的材料有不同的特性和性能,需要根据产品的要求选择合适的材料。
模具的设计是保证产品形状和尺寸精度的关键,需要考虑产品的外形、内部结构等因素。
工艺参数的设定直接影响成型工艺的稳定性和效果,如温度、压力、速度等参数需要根据产品的要求进行调整。
总之,材料成型工艺是工业生产中的重要环节,掌握材料成型工艺的基础知识对于提高产品的质量和效率具有重要意义。
以上是关于材料成型工艺基础的简要介绍,希望对您有所帮助。
材料成型原理
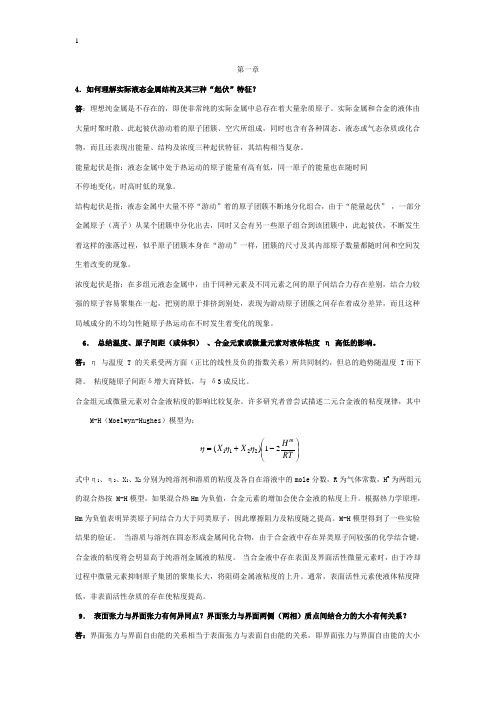
第一章4.如何理解实际液态金属结构及其三种“起伏”特征?答:理想纯金属是不存在的,即使非常纯的实际金属中总存在着大量杂质原子。
实际金属和合金的液体由大量时聚时散、此起彼伏游动着的原子团簇、空穴所组成,同时也含有各种固态、液态或气态杂质或化合物,而且还表现出能量、结构及浓度三种起伏特征,其结构相当复杂。
能量起伏是指:液态金属中处于热运动的原子能量有高有低,同一原子的能量也在随时间 不停地变化,时高时低的现象。
结构起伏是指:液态金属中大量不停“游动”着的原子团簇不断地分化组合,由于“能量起伏” ,一部分金属原子(离子)从某个团簇中分化出去,同时又会有另一些原子组合到该团簇中,此起彼伏,不断发生着这样的涨落过程,似乎原子团簇本身在“游动”一样,团簇的尺寸及其内部原子数量都随时间和空间发生着改变的现象。
浓度起伏是指:在多组元液态金属中,由于同种元素及不同元素之间的原子间结合力存在差别,结合力较强的原子容易聚集在一起,把别的原于排挤到别处,表现为游动原子团簇之间存在着成分差异,而且这种局域成分的不均匀性随原子热运动在不时发生着变化的现象。
6. 总结温度、原子间距(或体积) 、合金元素或微量元素对液体粘度 η 高低的影响。
答:η 与温度 T 的关系受两方面(正比的线性及负的指数关系)所共同制约,但总的趋势随温度 T 而下降。
粘度随原子间距δ增大而降低,与 δ3成反比。
合金组元或微量元素对合金液粘度的影响比较复杂。
许多研究者曾尝试描述二元合金液的粘度规律,其中M-H (Moelwyn-Hughes )模型为:⎪⎪⎭⎫ ⎝⎛-+=RT H X X m 21)(2211ηηη 式中η1、η2、X 1、X 2 分别为纯溶剂和溶质的粘度及各自在溶液中的mole 分数,R 为气体常数,H m为两组元的混合热按 M-H 模型,如果混合热Hm 为负值,合金元素的增加会使合金液的粘度上升。
根据热力学原理,Hm 为负值表明异类原子间结合力大于同类原子,因此摩擦阻力及粘度随之提高。
材料成型及其热处理

材料成型及其热处理一、引言材料成型及其热处理是现代材料工艺中非常重要的一个环节。
材料成型是指将原材料经过一系列的加工工艺,经过一定形状和尺寸的加工成形。
而热处理是指通过控制材料的温度、时间和冷却速度等参数,来改善材料的组织结构和性能。
本文将从材料成型的基本原理、成型工艺、热处理的基本原理及热处理工艺等方面进行阐述。
二、材料成型的基本原理材料成型的基本原理是通过施加外力使材料发生塑性变形,从而获得所需形状和尺寸的工件。
在材料成型的过程中,材料必须经历加热、塑性变形和冷却等阶段。
材料成型的方式主要包括锻造、压铸、冷挤压、热挤压等。
不同的成型方式对最终工件的性能有很大的影响,因此在选择成型方式时需要根据材料的类型、形状和用途进行权衡。
三、材料成型的工艺1. 锻造锻造是一种将金属材料置于模具中,然后施加压力,使其发生塑性变形而获得所需形状和尺寸的工艺。
锻造可以分为冷锻、热锻和温锻等多种方式,可以根据材料的性质和形状来选择不同的锻造方式。
锻造工艺可以提高材料的密度和强度,同时也能改善其组织结构,提高其耐磨性和抗疲劳性。
2. 压铸压铸是一种将金属液态或半固态材料通过高压射入模具,然后在特定的压力和温度下冷却凝固,获得所需形状和尺寸的工艺。
压铸工艺可以制造各种复杂形状的铸件,同时还能保持较高的表面光洁度和尺寸精度。
3. 冷挤压冷挤压是一种将金属坯料置于挤压机中,并在常温下施加高压,使其发生塑性变形而获得所需形状和尺寸的工艺。
冷挤压工艺可以制造高精度、高强度的金属零部件,同时还能提高材料的耐磨性和疲劳寿命。
4. 热挤压热挤压是一种将金属坯料置于加热的挤压机中,然后施加一定的压力使其发生塑性变形而获得所需形状和尺寸的工艺。
热挤压工艺可以降低材料的变形阻力,提高成形精度和表面质量,同时还能改善材料的组织结构和性能。
四、热处理的基本原理热处理是指通过控制材料的温度、时间和冷却速度等参数,来改善材料的组织结构和性能的工艺。
材料成型基本原理知识点总结
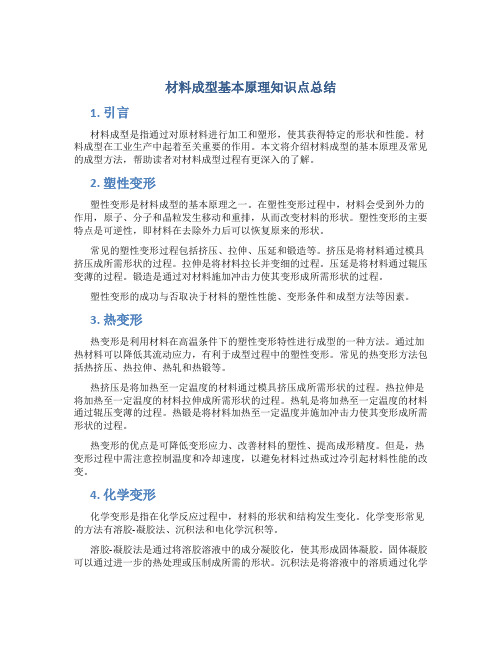
材料成型基本原理知识点总结1. 引言材料成型是指通过对原材料进行加工和塑形,使其获得特定的形状和性能。
材料成型在工业生产中起着至关重要的作用。
本文将介绍材料成型的基本原理及常见的成型方法,帮助读者对材料成型过程有更深入的了解。
2. 塑性变形塑性变形是材料成型的基本原理之一。
在塑性变形过程中,材料会受到外力的作用,原子、分子和晶粒发生移动和重排,从而改变材料的形状。
塑性变形的主要特点是可逆性,即材料在去除外力后可以恢复原来的形状。
常见的塑性变形过程包括挤压、拉伸、压延和锻造等。
挤压是将材料通过模具挤压成所需形状的过程。
拉伸是将材料拉长并变细的过程。
压延是将材料通过辊压变薄的过程。
锻造是通过对材料施加冲击力使其变形成所需形状的过程。
塑性变形的成功与否取决于材料的塑性性能、变形条件和成型方法等因素。
3. 热变形热变形是利用材料在高温条件下的塑性变形特性进行成型的一种方法。
通过加热材料可以降低其流动应力,有利于成型过程中的塑性变形。
常见的热变形方法包括热挤压、热拉伸、热轧和热锻等。
热挤压是将加热至一定温度的材料通过模具挤压成所需形状的过程。
热拉伸是将加热至一定温度的材料拉伸成所需形状的过程。
热轧是将加热至一定温度的材料通过辊压变薄的过程。
热锻是将材料加热至一定温度并施加冲击力使其变形成所需形状的过程。
热变形的优点是可降低变形应力、改善材料的塑性、提高成形精度。
但是,热变形过程中需注意控制温度和冷却速度,以避免材料过热或过冷引起材料性能的改变。
4. 化学变形化学变形是指在化学反应过程中,材料的形状和结构发生变化。
化学变形常见的方法有溶胶-凝胶法、沉积法和电化学沉积等。
溶胶-凝胶法是通过将溶胶溶液中的成分凝胶化,使其形成固体凝胶。
固体凝胶可以通过进一步的热处理或压制成所需的形状。
沉积法是将溶液中的溶质通过化学反应沉积在衬底上形成薄膜或形状。
电化学沉积是利用电化学反应使溶液中的溶质在电极表面沉积成薄膜或形状。
第01讲 材料成型热过程.ppt
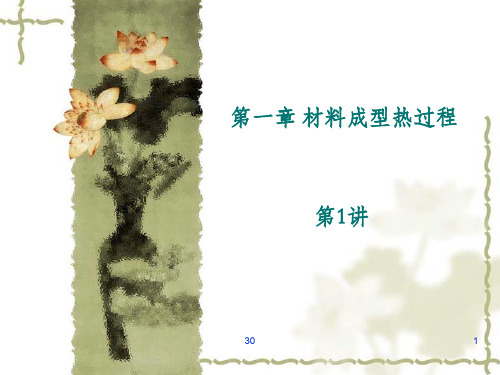
T
c
2T x2
2T y 2
2T z 2
a2T
(1-3)
式中:a——导热系数或热扩散率,cm2/s,; c——比热容;J/(g·℃); ρ——密度,g/cm3; T——温度,℃; τ——时间,s。
30
15
式(1-3)从理论上得出了物体上坐标、温度和时间三 者的关系,它表示给定点温度变化速度同拉普拉斯 运算符号成正比,换言之,在某时刻τ、物体上给定 点P(x,y,z)邻近的温度分布越不均匀,则该点的温 度变化也越快。导热的结果,温度不均匀性将逐渐 减小,温度变化速度也要降低。
方程,即其特解为
T (r,t)
Q
exp( r 2 )
c (4at)3 / 2
4at
(1-5)
30
26
如果热源瞬时作用于半无限大物体,如图1-2中的 abcd表面上的O点,并假定此表面为绝热面,则该 点受到热作用的温度将为无限大物体内部热源作用 时的一倍,因而式(1-5)应该写成
2Q
规则及材料物性量不是常数等复杂情况,往往无法
分析求解 。
30
17
数值解法 是将方程离散化后得到代数方程组,可以利用
计算机进行求解,对于实际问题有很大的适应性。 如对于复杂的几何形状、变化的热物理参量等情况, 用数值解法都能较好地加以解决。
所采用的离散化方法主要有:有限差分法和有 限元素法。
30
30
13
二、Laplace热传导微分方程式
热传导微分方程式是根据能量守恒定律(热力学第 一定律)和傅里叶定律推导得出的。它揭示了连续 温度场在空间与时间领域里的内在联系。
材料成型基本原理

材料成型基本原理
材料成型是指将原料经过一定的加工工艺,使其形成所需的形状和结构的过程。
在工程制造中,材料成型是非常重要的一环,它直接影响着制品的质量和性能。
材料成型的基本原理包括塑性变形、断裂和破碎、流变变形等多个方面,下面我们就来详细介绍一下。
首先,塑性变形是材料成型中的重要原理之一。
塑性变形是指在材料受到外力
作用下,原子和分子重新排列,使材料形成永久性变形的过程。
这种变形是可逆的,也就是说在去除外力后,材料还能保持一定的形状和结构。
塑性变形是材料成型中最常见的一种变形方式,通常通过挤压、拉伸、压缩等方式实现。
其次,断裂和破碎是材料成型中需要避免的问题。
在材料成型过程中,如果受
到过大的外力作用,材料就会发生断裂和破碎。
这种现象会导致制品的质量下降甚至无法使用。
因此,在材料成型过程中,需要控制外力的大小和方向,以避免材料的断裂和破碎。
另外,流变变形也是材料成型中的重要原理之一。
流变变形是指在材料受到外
力作用下,其形状和结构发生可逆性变化的过程。
这种变形通常发生在高温下,材料处于液态或半固态状态时。
在流变变形过程中,材料的粒子会发生流动,从而改变其形状和结构。
综上所述,材料成型的基本原理包括塑性变形、断裂和破碎、流变变形等多个
方面。
在实际工程制造中,需要根据不同的材料和成型要求,选择合适的成型工艺和方法,以确保制品的质量和性能。
同时,也需要加强对材料成型原理的研究,不断提高成型工艺的水平,为工程制造提供更好的技术支持。
基于快速成型技术(RP)的快速模具制造(RT)技术的研究

基于快速成型技术(RP)的快速模具制造(RT)技术的研究摘要:快速成型技术(RP)的发展带来了一系列的创新制造技术,其中快速模具制造(RT)是一项重要的技术。
RT技术利用RP技术制造出的模具,可以在短时间内快速制造出符合要求的零部件,为制造业的高效生产提供了有力支持。
本文将对RT技术的原理、技术分类和发展趋势进行探讨,并分析了RT技术在现代制造业中的应用,并对其未来的发展方向做出了展望。
关键词:快速成型技术;快速模具制造;RP技术;制造业一、引言随着全球市场的不断扩大和竞争的日益激烈,企业需要加快产品设计和制造的速度,以便更快地满足市场需求。
快速成型技术(RP)的应用为实现这一目标提供了创新的手段,可以在短时间内制造出符合要求的零部件或模型。
然而,RP技术的制造成本较高,并且一些材料的机械性能还不够理想,这都限制了其在实际生产中的应用。
因此,快速模具制造(RT)技术应运而生。
RT技术是一项将RP 技术应用于模具制造的新技术,可以在短时间内制造出符合要求的模具,以便进行大批量零件的生产。
相对于传统的模具制造技术,RT技术具有制造周期短、成本低、设计灵活等优点,并且可以制造出更加复杂的模具。
二、RT技术的原理RT技术主要利用RP技术制造出的模具进行制造。
在传统的模具制造过程中,需要先设计、制造模具,再使用模具制造出零部件。
而在RT技术中,只需要在计算机中设计出模具,然后利用RP技术将模具制造出来,再使用模具制造出零部件。
从而将制造周期大幅缩短,提高制造效率。
RT技术涉及到多种RP技术,例如光固化RP技术、激光快速成型技术、喷墨3D打印技术等。
这些技术都可以用于制造模具,以便在短时间内快速制造出符合要求的零件。
三、RT技术的分类RT技术可以分为直接RT和间接RT两种。
直接RT是指将模具制造完成后,直接在模具内制造零件。
直接RT技术又可以分为热成型、注塑成型、压铸成型等不同的生产工艺。
间接RT是指先通过RP技术制造出原型模具,然后用原型模具制造出硅胶模具,最后再使用硅胶模具制造出生产模具。
材料成形基本原理难度-概述说明以及解释

材料成形基本原理难度-概述说明以及解释1.引言1.1 概述材料成形是指通过对材料施加力或温度等外部条件,使材料发生形变和变形,最终得到所需形状和尺寸的工艺过程。
材料成形技术广泛应用于各个工业领域,如汽车制造、航空航天、电子电器等。
在实际生产中,材料成形的基本原理是一个非常重要的环节。
准确理解和掌握材料成形的基本原理,对于提高制造过程的效率、降低成本、保证产品质量具有重要意义。
材料成形的基本原理可以概括为力学原理、塑性变形原理和热变形原理。
力学原理是指施加外力到材料上,使其发生形变和变形。
塑性变形原理是指材料在外力作用下,超过其弹性极限后会发生塑性变形,即材料以塑性流动的方式改变形状。
热变形原理是指通过加热材料,使其软化或变为液态,再施加外力,从而得到所需形状。
然而,材料成形的基本原理也存在一定的难度。
首先,不同材料的成形行为具有较大的差异,需要针对不同材料的特性和性能进行分析和选择合适的成形方法。
其次,材料成形还受到各种因素的影响,如温度、力度、速度等,需要深入研究和把握。
此外,材料成形的过程中还容易出现一些问题,如材料断裂、表面缺陷等,需要及时发现和解决。
在未来的发展中,随着材料科学和制造技术的不断进步,材料成形的基本原理也将不断得到完善和创新。
例如,采用先进的数值模拟方法和计算机辅助设计技术,可以更准确地预测和优化材料成形的过程。
此外,结合材料基因工程、纳米材料等新兴技术,也将为材料成形带来更多可能性和挑战。
综上所述,材料成形的基本原理是一个复杂而重要的问题。
准确理解和掌握材料成形的基本原理,对于提高制造过程的效率、降低成本、保证产品质量具有重要意义。
未来,我们需要继续深入研究和创新,推动材料成形技术的发展和进步。
1.2文章结构文章结构部分的内容可以包括以下内容:文章结构部分旨在说明本文的整体组织结构,让读者能够更好地了解文章的内容和逻辑关系。
本文按照以下结构展开:1. 引言:对材料成形基本原理难度的问题进行概述,引起读者的兴趣和思考。
材料成型概论第二章材料成型的基础1
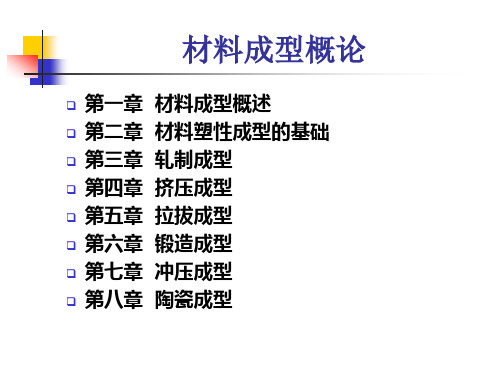
3.晶粒出现方向性;
4.除晶粒内部变形外,在晶界上 也发生变形。
31
加工过程中的硬化
加工硬化
多晶体塑性变形将导致金属的力学、物理和化学
性能的改变。随着变形程度↑,则有: 1.变形抗力(σS σb 硬度)↑ 2.塑性(伸长率 压缩率 )↓ 3.同时使电阻升高、抗腐蚀性和导热性↓
32
加工过程中的软化
2.Mises屈服条件: 形变能定值理论。
当变形金属内的变形剪切能达到一个临界值时,
金属就由弹性变形进入塑性变形。
(1 2 )2 ( 2 3 )2 (1 3 )2 2 s2
又称精确塑性条件。 对于板带轧制,简化为:σ1-σ3 = 1.15σS=K K:平面变形抗力。
35
金属的冷变形和热变形
(0.25~0.3)TM ℃
只有加工硬化作用而无回复与再结晶现象的变形
过程叫冷变形。加工温度低于材料的再结晶回复
温度的塑性加工方法。 冷变形特点如下: 冷变形后的产品尺寸精度高,表面光洁,可以生 产极细的丝、极薄的箔和细薄的管; 材料经冷变形变形后呈现加工硬化,变形抗力增
高,塑性下降,加工过程中需退火,增加能耗;
性能都近于冷加工的优良产品。
38
2.1.2.2 金属的塑性
塑性变形 :
形状和尺寸的不可逆变化是通过原子的定向位移实 现的.
多晶体塑性变形的主要机制:位错的运动 金属和合金的塑性取决于: 一是:自然属性
应力超过弹性极限,材料发生的不可逆的永久变形。
二是:塑性加工过程外界条件
变化
39
塑性变形的不均匀性原因与后果
内力产生的原因:
1)平衡外力;
2)由于工件的整体性,各部分的不均匀变形、不 均匀加热和冷却、不均匀相变等必将互相限制, 因此物体内部出现了自相平衡的内力。 • 如加热不均;
材料成型概论 第一讲 概述
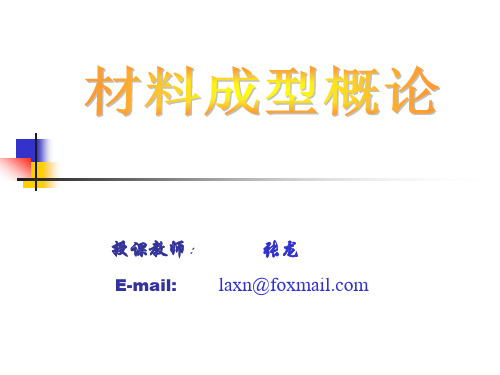
提高钢的强度和 硬度 提高钢的强度和 硬度 形成热淬性,降 低钢的强度 塑性和韧性急剧 下降
钢中的化学成分
钒和钛:是钢中的合金元素,能提高钢的强度和
抗腐蚀性能,又不显著降低钢的塑性。
铜 :可显著提高钢的抗腐蚀性能,也可以提 高钢的强度,但对焊接性能有不利影响。
汽车主要使用的材料
各种材料在先进汽车中占的重量百分比
平时作业课堂讨论课后复习期末考试第一讲材料成型概述第二讲炼钢炼铁生产第三讲材料塑性成型的基础第四讲钢坯型钢生产第五讲线棒材生产第六讲板带钢生产第七讲钢管生产第八讲挤压拉拔生产第九讲锻压冲压生产第十讲材料成型的发展及应用材料的发展与分类111材料的发展112材料的分类材料成型的方法和特点121材料成型的方法和特点122金属塑性成型的方法和特点123金属成型需考虑的基本原则1112材料是人类用来制造各种机器构件和产品的物质是人类生产和生活的物质基础
(汽车、钢铁、水泥、船舶、电解铝、稀土、电子信息、医 药、农业产业化龙头企业) 钢铁行业到2015年,前10家钢铁企业集团产业集中度达到 60%左右,形成3-5家具有核心竞争力和较强国际影响力的
企业集团,6-7家具有较强区域市场竞争力的企业集团。
大幅减少企业数量,提高钢铁产业集中度。
1.1.1 材料的发展
在轻量化的推 动下,铝合金 材料应用技术 发展很快,在 近年来出现的 全铝车身以铝 密集型汽车(如 福特P2000)中, 铝的比例更高 达37%
橡 胶 Al Fe 塑 料 其 它
磁 玻 材 璃 料
聚 碳 酸 酯
Ti
碳 纤 维
材料
波音767飞机所用的各种材料比例
1.1.2 材料的分类 (按用途分)
原料消耗少, 能制备复杂形状产品;
第一篇-材料成型与RT比

鎧蔚企業有限公司Metalex Enterprise Co., Ltd.材料成型與R/T比前題隨著電子消費性產品走向微小化的關係,內部的金屬零件首先面對的是成型上所帶來的問題。
越來越多客戶提到,由於產品空間先天的限制,使得端子或彈片在折彎上較為嚴苛,這使得金屬超過所能承受的最大塑形極限,導致產生裂痕,進而影響到正向力(NORMAL FORCE)及壽命(LIFE)的表現,嚴重時,在沖壓成型時就發生斷裂的情況,以下我們就來討論一下,會影響材料成型的因素。
R/T Ratios要了解帶材銅合金的成型性,可透過R/T比來判斷其優劣,它說明了彎曲內半徑(R)的建議最小量,大部分的材料SPEC都會有這一個數據,但有些高強度的材料並沒有完整寫出,其中有一很可能的理由是,"折彎表現太爛了,不如不寫"。
具有良好成型性材料的R/T比較小,而成型性較差的材料的R/T比較大。
理論上來說,如果R/T比等於零,即表示此材料的折彎表現極優,即使折彎的內R=0,也不會產生裂痕(圖一),但要注意,一般材料SPEC所顯示的都是90度折彎的數據,只有少數會Show出180度的折彎數據。
90°V-shape diePunch with bending radiusro鎧蔚企業有限公司( Metalex Enterprise Co., Ltd ) 地址:台北縣三重市中興北街155巷12號 (圖一)180°U-shaperoPunch with bending radiusspecimenr = 0當然,工程師所設計的內R角度,不一定會剛好90度,有可能只有60度,也有可能會達到180度,但R/T比可以讓工程師很快的判斷此材料的折彎表現,是很重要的參考數據。
當然,內R越大成功成型機會越高,這道理很簡單,因為成型應變和應力都均勻的分佈在折彎處的整個彎弧上,均勻分佈的應力可以將失敗的可能性降到最小。
(P.S 不一樣的製造商,有不一樣的測試標準,有可能會影響到此數據的表現。
《材料成型与制造业》PPT课件
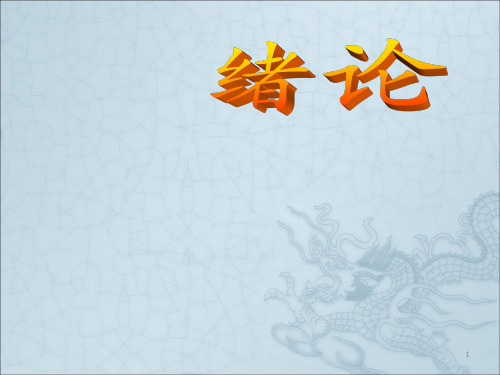
材料加工的主要方法
冷加工 —— 车、铣、刨、钳、磨
加工 热加工
铸 —— 凝固(液态)成形 锻 —— 塑性(高温、室温)成形 焊 —— 连接成形
热处理、表面加工、粉冶加工
9
二、 材料成形的专业内涵
材料基本理论……加工对象 机电控制理论……加工设备 各类工艺知识……加工过程
10
凝固成形 塑性成形 焊接成形
16
本章结束
17
感谢下 载
1
一、材料成形与制造业 二、材料成形的专业内涵 三、本课程的教学目的与内容
2
一、 材料成形与制造业
切削加工
凝固成形
凝固成形 塑性成形
塑性成形 焊接成形
表面加工
原材料 焊接成形
毛坯
零件 装配 机器
(锭料、轧材)
切削加工
热处理 切削加工
3
大型运输机
4
航空母舰 5
大型客机
6
❖服装
高速列车
7
自动化生装备
11
[凝固成形]: 熔炼金属,并将 熔融金属浇注、压射或吸入铸型型 腔中,凝固成为一定形状和性能的 铸件。
12
[塑性成形]:利用金属能够产生塑 性变形的能力,使金属在外力作用下, 加工成一定形状的成形方法。
13
[焊接] :通过加热或加压,或两者 并用,并且用或不用填充材料,使焊 件达到原子结合的一种加工方法。
14
《材料成形原理》课程教学目的与内容
学习
铸造 焊接
锻压 过程中的
金属学原理 冶金原理 物化原理 热力学原理 塑性力学原理
15
第第七一章章 液液态态金金属属与的气结相构的和相性互质作用 第八第章二章液态凝金固属温与度渣场相的相互作用 第九第章三章液态金金属属凝的固净热化力与学精与炼动力学 第十第章四章焊接单热相影及响多区相的合组金织的与结性晶能 第十第一五章章 凝铸固件缺宏陷观及组控织制及其控制 第十第二六章章 粉特末殊冶条金件中下原的理凝固与成形
- 1、下载文档前请自行甄别文档内容的完整性,平台不提供额外的编辑、内容补充、找答案等附加服务。
- 2、"仅部分预览"的文档,不可在线预览部分如存在完整性等问题,可反馈申请退款(可完整预览的文档不适用该条件!)。
- 3、如文档侵犯您的权益,请联系客服反馈,我们会尽快为您处理(人工客服工作时间:9:00-18:30)。
鎧蔚企業有限公司
Metalex Enterprise Co., Ltd.
材料成型與R/T比
前題
隨著電子消費性產品走向微小化的關係,內部的金屬零件首先面對的是成型上所帶來的問題。
越來越多客戶提到,由於產品空間先天的限制,使得端子或彈片在折彎上較為嚴苛,這使得金屬超過所能承受的最大塑形極限,導致產生裂痕,進而影響到正向力(NORMAL FORCE)及壽命(LIFE)的表現,嚴重時,在沖壓成型時就發生斷裂的情況,以下我們就來討論一下,會影響材料成型的因素。
R/T Ratios
要了解帶材銅合金的成型性,可透過R/T比來判斷其優劣,它說明了彎曲內半徑(R)的建議最小量,大部分的材料SPEC都會有這一個數據,但有些高強度的材料並沒有完整寫出,其中有一很可能的理由是,"折彎表現太爛了,不如不寫"。
具有良好成型性材料的R/T比較小,而成型性較差的材料的R/T比較大。
理論上來說,如果R/T比等於零,即表示此材料的折彎表現極優,即使折彎的內R=0,也不會產生裂痕(圖一),但要注意,一般材料SPEC所顯示的都是90度折彎的數據,只有少數會Show出180度的折彎數據。
90°
V-shape die
Punch with bending radius
r
o
鎧蔚企業有限公司
( Metalex Enterprise Co., Ltd ) 地址:台北縣三重市中興北街155巷12號 (圖一)
180°
U-shape
r
o
Punch with bending radius
specimen
r = 0
當然,工程師所設計的內R角度,不一定會剛好90度,有可能只有60度,也有可能會達到180度,但R/T比可以讓工程師很快的判斷此材料的折彎表現,是很重要的參考數據。
當然,內R越大成功成型機會越高,這道理很簡單,因為成型應變和應力都均勻的分佈在折彎處的整個彎弧上,均勻分佈的應力可以將失敗的可能性降到最小。
(P.S 不一樣的製造商,有不一樣的測試標準,有可能會影響到此數據的表現。
有時候真的很Ttricky~)
折彎方向
Bending direction
Bending direction
good way
bad way
Rolling direction
材料的折彎表現與折彎的方向有絕對關係。
一般來說,在好的方向(Good Way, GW)會比壞的方向(Bad Way, BW)有較好的表現(圖二),此乃因為材料在進行冷加工時
的方向即為GW,這使得材料的組成單
位"晶粒"在發生差排運動(Dislocation)時的程度不同所造成,下次的討論我們會再談到這個部
份,但這次先以運用面為
主。
但一般來說,由於沖壓模具的關係,大部分的折彎方向皆為BW,所以一般來說可能要比較注意材料在BW所能承受的最大極限。
R/T比的計算
所謂的R(Radius)就是折彎的內徑,T(Thickness)就是使用材料的厚度,有一些材料會提供W/T比,W(Width)就是折彎處的寬度,畢竟折彎寬度也是非常之重要低,但由於大多材料只有提供R/T比,所以以下的例子還是用R/T比的計算來說明。
EX:
一端子的折彎為90度,內R=0.3mm ,T=0.15mm ,透過(圖二)的公式,可算出一個值A,此例中A=2,而使用材料所提供的R/T比必須比A值小,才是安全範圍。
例如C5210-SH 的材料GW=4、BW=6,如果使用於此折彎上,基本上不管從那個方向折彎都是不行的,但如果用軟一點的C5210H或許可以,但是你要面對的是強度不足所帶來的正向力下降,材料發生降伏(產生永久塑形形變)及壽命不足的問題。
材料SPEC上的R/T比必須比算出的值小,才是安全範圍。
(Bending Radius)
T (Thickness)R (Bending Radius)
(圖三)
*請注意,R/T比只是用來表示相對成型性的良好指標,並不是一個絕對值。
其他影響成型的因素
上面提到R/T比是一個用來判斷成型的良好指標,但是還有許多因素會影響材料的成型,有時候這些因素甚至是成型失敗的主要原因。
以下舉出幾點會影響成型的因素:
1) 材料的厚薄: 薄的板材可接受較小的彎曲半徑而不破裂。
2) 材料的寬窄: 端子或彈片寬度少於材料厚度的8倍,一般能夠接受更小的 半徑而不發生斷裂。
寬度是很重要低。
3)彎角成型的過程: 許多彎角都只用一次折彎行程完成。
然而,如果彎曲是使用漸進式折彎行程完成,將會減少發生斷裂的可能性(尤其是內R小且折彎幅度大)。
在各個漸進式階段所需要的應變量,大大少於僅使用一個步驟成型所需要的應變量。
多階段的成型也可較嚴密的控制反彈。
另外,折彎速度也有可能影響折彎的表現,速度慢的表現會比速度快好。
4)延展率: 延展性與強度成反比,高強度材料的成型性大多比低強度的差。
全軟材或O材可以得到材料最好的成型性,但也由於以上的通識,使得許多工程人員陷入延展率差折彎表現就差的迷思。
其實連接器的設計,大多只是單純的使材料彎曲,鮮少拉伸抽引,所以與其要用延展率來判斷折彎的表現,不如用R/T比還比較客觀。
5)晶粒大小: 如果不拉伸材料而使彎曲形成,晶粒越小的其成型性越好。
如在彎曲時材料被拉伸抽引,則大的晶粒可提供更好的成型性。
但多數的連接器設計,多為單純折彎,較少拉伸抽引。
以下照片(圖四,五)顯示晶粒小的材料,在相同條件下,有較好的折彎表現。
0,15 mm 180° 折彎 with r= 0,2 mm, badway
C5210-H B18-SUPRALLOY-R685
(圖四) 晶粒較小的材料,在相同條件下,依然完美且表面平滑!!
r
晶粒較大的材料,在相同
條件下,已產生裂痕!!
此為C5210H 的晶粒照片
(圖五)
此為B18-SUPRALLOY-R685的晶粒照片
B18-SUPRALLOY
說了這摸多,還是要介紹一下我們的產品,B18-SUPRALLOY就是一種小晶粒的材料,其實這種材料除了優異的折彎表現外,還有非常好的疲勞強度,是一般磷青銅的1.5倍(以後再說明疲勞強度的重要)對於需要高壽命的連接器很有幫助,而且小晶粒同時也代表著多晶界(Grain Boundary),也會提升材料的強度,重點是它不貴~~~
Alloy Temper Yield
Strength
Rp0.2
Mpa Tensile Strength Mpa Min Bending Radius 90° GW Min Bending Radius 90° BW Electrical
Cond. % IACS
HV
C5210 EH min 650685-785 2 4 12 210-260 C5210
SH
min 700735-835 4
6 12 230-270B18-SUPRALLOY EH
R685 min 650685-785 0
0.5 13 210-260B18-SUPRALLOY SH
R735 min 700735-835 0
2 1
3 230-270B18-SUPRALLOY ESH
R800 min 775800-900 1
4
13
250-290
**此篇文章由 鎧蔚-林昭明-Chris 於相關資料中所整理編寫,歡迎傳閱指教**
Reference
1)http://www.wieland.de/
2)/
3)/
4)金屬材料吳啟岳,三民
5)連續沖壓模具設計之基礎與應用陳玉心/著,全華科技
6)金屬加工王文雄,三民
7)機械工程手冊3-金屬材料機械工程手冊電機工程手冊編輯委員會,五南
8)金屬材料及試驗法徐景褔/編著,台南復文書局。