超临界机组防止高温氧化皮集聚脱落造成设备损害的技术措施
超超临界锅炉高温受热面氧化皮脱落与治理

超超临界锅炉高温受热面氧化皮脱落与治理超超临界锅炉是一种新一代的高效节能锅炉,其高温受热面处于极端的工作条件下,容易发生氧化皮脱落问题。
本文将探讨超超临界锅炉高温受热面氧化皮脱落的原因,并提出相应的治理措施。
1. 高温氧化作用:高温下,锅炉受热面的金属材料容易与氧气反应,形成氧化物。
这些氧化物会沉积在受热面上形成氧化皮,进而脱落。
2. 烟气侵蚀:锅炉燃料燃烧产生的烟气中含有大量的气体和颗粒物,其中包括酸性物质,如二氧化硫和二氧化氮等。
这些酸性物质会侵蚀受热面,导致氧化皮脱落。
3. 热应力作用:超超临界锅炉高温受热面由于长期承受高温烟气的冲击,会引起受热面的热胀冷缩。
这种热应力会使氧化皮与基材之间的结合变弱,从而加速氧化皮的脱落。
1. 材料选用:使用耐热、抗氧化性能好的材料作为受热面,以提高锅炉的耐温性和抗氧化性能。
常用的材料有铬钼钢和镍基高温合金等。
2. 涂层处理:在受热面表面涂覆一层抗氧化的涂层,以提高受热面的抗氧化性能和耐蚀性。
常用的涂层材料有铁铝高温涂层和陶瓷涂层等。
3. 清洗除锈:定期对受热面进行清洗除锈工作,以去除氧化皮和其他污垢,减少氧化皮的形成和脱落。
4. 热应力控制:通过优化锅炉的运行参数和调整受热面的结构设计,减少受热面的热应力,延缓氧化皮的脱落。
5. 烟气净化:增加烟气净化的设备,如脱硫装置和脱硝装置等,减少烟气中的酸性物质含量,减少受热面的侵蚀和氧化皮的脱落。
超超临界锅炉高温受热面氧化皮脱落是一个复杂的问题,需要综合考虑材料性能、涂层处理、清洗除锈、热应力控制和烟气净化等因素。
通过采取综合治理措施,可以有效延缓氧化皮的形成和脱落,提高锅炉的运行效率和安全性。
超临界机组电站锅炉氧化皮脱落的分析与防治

超临界机组电站锅炉氧化皮脱落的分析与防治超临界机组电站锅炉是目前较为常见和主要的电力发电设备之一,其运行过程中经常会出现氧化皮脱落的问题。
氧化皮的脱落会影响锅炉的正常运行,导致能效下降,甚至对设备的安全性产生严重威胁。
分析和防治超临界机组电站锅炉氧化皮脱落问题具有重要的理论和实践意义。
一、氧化皮脱落的原因1.1 温度梯度超临界机组锅炉工作过程中,受到高温高压蒸汽的冲击,锅炉管壁表面将产生较大的温度梯度。
不同部位的锅炉管壁温差过大,会导致金属材料产生不均匀的热应力,进而引发氧化皮层的脱落。
1.2 流体腐蚀蒸汽中的氧气和水分子会与金属表面发生反应,生成金属氧化物,形成氧化皮层。
当锅炉中腐蚀性物质较多时,会导致氧化皮层增厚和脱落,影响锅炉的热传导效果和安全性。
1.3 机械压力锅炉在运行过程中,受到蒸汽冲击和机械震动等力的作用,会产生机械压力。
当机械压力过大时,会使氧化皮层松动或脱落,需要及时修补和保养。
2.1 表面分析对锅炉管壁的氧化皮层进行表面分析,可以通过扫描电子显微镜等工具观察锅炉管壁表面的氧化皮脱落情况。
通过分析氧化皮的结构和形貌,可以判断其脱落的原因和程度,为防治提供依据。
2.2 金属温度分析对锅炉管壁的温度进行实时监测和记录,可以判断锅炉管壁温度梯度是否过大,从而引发氧化皮层的脱落。
合理调整锅炉的运行参数,降低温度梯度,可以有效减少氧化皮脱落的发生。
通过对锅炉内部金属材料和蒸汽的化学成分进行分析,可以判断蒸汽中是否存在腐蚀性物质。
并采取相应措施,如装置除氧器、水处理设备等,减少金属材料的氧化腐蚀,降低氧化皮层的脱落。
合理控制和调整超临界机组锅炉的运行参数,使锅炉管壁的温度梯度保持在一个合理的范围内。
可以通过增加锅炉管壁的保护层厚度、调整蒸汽流量等方式,减少锅炉管壁的温度应力和热应力,从而减少氧化皮层的脱落。
安装和使用除氧器、水处理设备等设施,减少锅炉腐蚀性物质的含量。
定期对锅炉内部进行清洗和维护,清除锅炉管壁表面的氧化皮层,及时修补和保养锅炉设备。
超超临界锅炉高温受热面氧化皮脱落与治理

超超临界锅炉高温受热面氧化皮脱落与治理近年来,随着能源需求不断增加,其高效安全利用的需求也越来越迫切。
超超临界锅炉作为新一代超临界锅炉的代表,其可提高燃料的利用效率和节能减排,已经成为我国火力发电工业技术的重要发展方向。
然而,超超临界锅炉在使用过程中,高温受热面氧化皮脱落成为了一个严重的问题。
一、高温受热面氧化皮脱落的形成原因超超临界锅炉,受热面高温氧化皮脱落是由于高温下的氧化作用和金属材料的应力松动以及锅炉结构设计不合理所导致的。
超超临界锅炉内部燃烧温度高、高温氧化环境严酷、冷却水与热表面水汽对流热传输强度大,认定为一种复杂的高温氧化腐蚀形式。
1.高温氧化作用高温下的金属材料容易氧化,其氧化层可能会脱落,从而形成氧化皮。
这些氧化皮,会增加受热面的热阻并阻塞燃烧产生火烟的通道,进而导致超超临界锅炉的发电效率降低。
2.金属材料容易应力松动超超临界锅炉是在高温高压及腐蚀环境下运行,受热面材料由于各种因素持续的受到外力和温度的挤压、拉伸、剪切、弯曲、变形、金属颗粒间的形变、位错等等诸多因素造成不断的塑性变形。
受热面金属材料在高温环境下变形则产生蠕变,蠕变后金属应力会逐渐累积到很高程度,使受热面外表面的氧化皮与基体之间发生剪切破裂。
3.锅炉结构设计不合理超超临界锅炉的受热面阶段数多、结构复杂,设计难度大。
在锅炉设计上,如果受热面的材料、结构等问题没有得到足够重视,就会导致锅炉在高温高压环境下受到各种力的作用而出现变形,进而形成局部热应力和冷应力,加剧了氧化皮脱落的发生。
高温受热面氧化皮脱落会严重影响超超临界锅炉的操作性能和发电效率,具体表现为:1.增加热阻高温受热面氧化皮脱落后会形成难以热传递的氧化皮层,阻碍水蒸汽与热表面的传热,增加了受热面的热阻,从而导致锅炉的热效率下降。
2.阻塞通道高温受热面氧化皮脱落通过堆积和凹凸不平的表面阻碍了火烟的通道,从而导致火烟流速下降,燃烧不充分,降低了燃烧产生的热量以及锅炉的热效率。
浅谈超临界直流供热机组防止氧化皮大量脱落运行控制技术措施
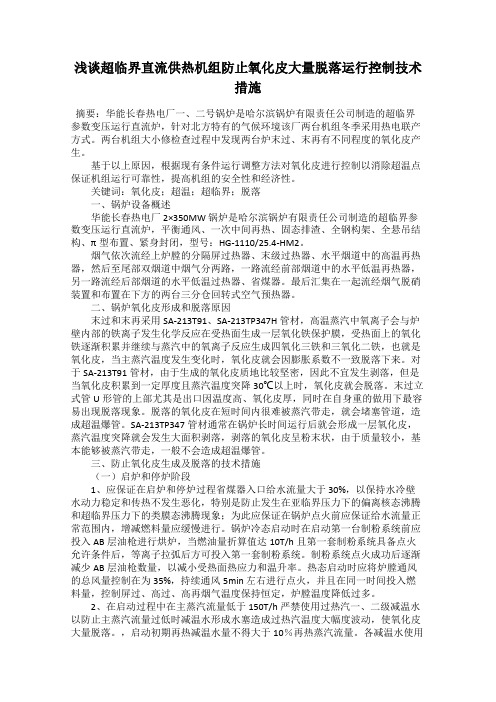
浅谈超临界直流供热机组防止氧化皮大量脱落运行控制技术措施摘要:华能长春热电厂一、二号锅炉是哈尔滨锅炉有限责任公司制造的超临界参数变压运行直流炉,针对北方特有的气候环境该厂两台机组冬季采用热电联产方式。
两台机组大小修检查过程中发现两台炉末过、末再有不同程度的氧化皮产生。
基于以上原因,根据现有条件运行调整方法对氧化皮进行控制以消除超温点保证机组运行可靠性,提高机组的安全性和经济性。
关键词:氧化皮;超温;超临界;脱落一、锅炉设备概述华能长春热电厂 2×350MW 锅炉是哈尔滨锅炉有限责任公司制造的超临界参数变压运行直流炉,平衡通风、一次中间再热、固态排渣、全钢构架、全悬吊结构、π型布置、紧身封闭,型号:HG-1110/25.4-HM2。
烟气依次流经上炉膛的分隔屏过热器、末级过热器、水平烟道中的高温再热器,然后至尾部双烟道中烟气分两路,一路流经前部烟道中的水平低温再热器,另一路流经后部烟道的水平低温过热器、省煤器。
最后汇集在一起流经烟气脱硝装置和布置在下方的两台三分仓回转式空气预热器。
二、锅炉氧化皮形成和脱落原因末过和末再采用SA-213T91、SA-213TP347H管材,高温蒸汽中氧离子会与炉壁内部的铁离子发生化学反应在受热面生成一层氧化铁保护膜,受热面上的氧化铁逐渐积累并继续与蒸汽中的氧离子反应生成四氧化三铁和三氧化二铁,也就是氧化皮,当主蒸汽温度发生变化时,氧化皮就会因膨胀系数不一致脱落下来。
对于SA-213T91管材,由于生成的氧化皮质地比较坚密,因此不宜发生剥落,但是当氧化皮积累到一定厚度且蒸汽温度突降30℃以上时,氧化皮就会脱落。
末过立式管U形管的上部尤其是出口因温度高、氧化皮厚,同时在自身重的做用下最容易出现脱落现象。
脱落的氧化皮在短时间内很难被蒸汽带走,就会堵塞管道,造成超温爆管。
SA-213TP347管材通常在锅炉长时间运行后就会形成一层氧化皮,蒸汽温度突降就会发生大面积剥落,剥落的氧化皮呈粉末状,由于质量较小,基本能够被蒸汽带走,一般不会造成超温爆管。
超临界机组电站锅炉氧化皮脱落的分析与防治
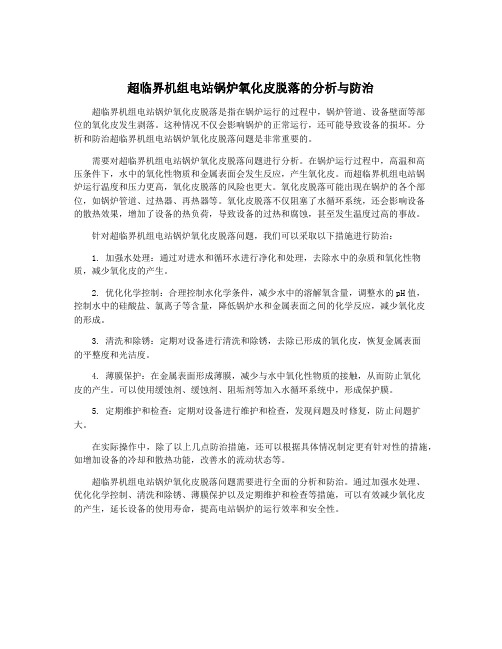
超临界机组电站锅炉氧化皮脱落的分析与防治超临界机组电站锅炉氧化皮脱落是指在锅炉运行的过程中,锅炉管道、设备壁面等部位的氧化皮发生剥落。
这种情况不仅会影响锅炉的正常运行,还可能导致设备的损坏。
分析和防治超临界机组电站锅炉氧化皮脱落问题是非常重要的。
需要对超临界机组电站锅炉氧化皮脱落问题进行分析。
在锅炉运行过程中,高温和高压条件下,水中的氧化性物质和金属表面会发生反应,产生氧化皮。
而超临界机组电站锅炉运行温度和压力更高,氧化皮脱落的风险也更大。
氧化皮脱落可能出现在锅炉的各个部位,如锅炉管道、过热器、再热器等。
氧化皮脱落不仅阻塞了水循环系统,还会影响设备的散热效果,增加了设备的热负荷,导致设备的过热和腐蚀,甚至发生温度过高的事故。
针对超临界机组电站锅炉氧化皮脱落问题,我们可以采取以下措施进行防治:1. 加强水处理:通过对进水和循环水进行净化和处理,去除水中的杂质和氧化性物质,减少氧化皮的产生。
2. 优化化学控制:合理控制水化学条件,减少水中的溶解氧含量,调整水的pH值,控制水中的硅酸盐、氯离子等含量,降低锅炉水和金属表面之间的化学反应,减少氧化皮的形成。
3. 清洗和除锈:定期对设备进行清洗和除锈,去除已形成的氧化皮,恢复金属表面的平整度和光洁度。
4. 薄膜保护:在金属表面形成薄膜,减少与水中氧化性物质的接触,从而防止氧化皮的产生。
可以使用缓蚀剂、缓蚀剂、阻垢剂等加入水循环系统中,形成保护膜。
5. 定期维护和检查:定期对设备进行维护和检查,发现问题及时修复,防止问题扩大。
在实际操作中,除了以上几点防治措施,还可以根据具体情况制定更有针对性的措施,如增加设备的冷却和散热功能,改善水的流动状态等。
超临界机组电站锅炉氧化皮脱落问题需要进行全面的分析和防治。
通过加强水处理、优化化学控制、清洗和除锈、薄膜保护以及定期维护和检查等措施,可以有效减少氧化皮的产生,延长设备的使用寿命,提高电站锅炉的运行效率和安全性。
超超临界锅炉高温受热面氧化皮脱落与治理

超超临界锅炉高温受热面氧化皮脱落与治理超超临界锅炉是目前煤电行业的重要技术装备之一,具有高效、节能、环保等优势。
而在超超临界锅炉中,高温受热面氧化皮脱落问题一直存在,极大地影响了锅炉的安全稳定运行。
因此,本文将从氧化皮脱落原因出发,结合治理方法进行分析和探讨。
一、氧化皮脱落的原因(一)锅炉设备本身原因1.锅炉受热面设计不合理,导致高温部位温差大,容易导致氧化皮脱落。
2.使用不合适的材料,使受热面在高温和高压条件下易形变、易脆化,进而影响受热面的脱落问题。
3.受热面的加工质量不合格,如表面光洁度差、残留应力大,会导致受热面氧化皮质量差、易脱落等。
(二)运行条件原因1.过量热流通,超过受热面耐热极限,导致受热面温度过高,氧化皮形成与脱落问题突出。
2.燃料不纯,煤粉不能完全燃烧,会堆积在受热面上,导致脱落。
3.水质不良,水质中存在高浓度的溶解氧、CO2等物质,影响受热面材料的稳定性和抗氧化能力。
(三)操作原因1.启停操作频繁,使得锅炉设备更加容易受到温度、温差的变化,导致受热面氧化皮脱落。
2.锅炉的清洗不及时、清洗不彻底,导致受热面上的氧化皮积累,进而形成较大的氧化皮,加剧脱落问题。
二、治理方法针对氧化皮脱落的原因,可以采取以下治理方法:(一)锅炉设备本身治理1.改变受热面结构设计,避免锅炉扭曲、变形,尽量减少应力。
2.选用高温、高压下能够提高材料抗氧化、抗脱落能力的高温合金材料。
3.加强受热面的加工质量,提高表面光洁度,降低表面残余应力。
(二)运行条件治理1.加强热流量的控制,避免过量热流,将蒸汽压力、出口温度控制在正常范围内。
2.优化燃烧工艺,严格控制煤粉的燃烧效果,避免其堆积在受热面上。
3.严格控制水质,加强锅炉水处理,降低水质中的溶解氧、CO2等物质含量。
(三)操作治理1.采取合理的启停操作,避免锅炉受热面温度变化过大。
2.加强清洗和维护工作,定期对受热面进行清洗,保持受热面的干净和稳定。
综上所述,针对超超临界锅炉高温受热面氧化皮脱落问题,需要综合考虑锅炉设备本身、运行条件和操作等多个方面,采取科学合理的治理方法,才能有效地解决这一问题,确保锅炉的安全稳定运行。
超临界机组电站锅炉氧化皮脱落的分析与防治

超临界机组电站锅炉氧化皮脱落的分析与防治超临界机组电站锅炉是现代化的汽轮机发电装置,其关键部件之一即是锅炉。
锅炉的主要功能是将燃料的化学能转化为蒸汽能,并将蒸汽压力转化为机械能或电能。
在锅炉的运行过程中,由于锅炉进口水的含氧量、水质、水温等因素的影响,会产生氧化皮,影响锅炉的正常运行。
本文对氧化皮的形成原因、脱落的危害以及相应的防治措施进行分析。
一、氧化皮的形成原因在超临界机组电站锅炉运行中,锅炉的内壁与水接触,水中的氧气会与金属反应,产生一层氧化膜即氧化皮。
氧化皮生长速度受水中氧气浓度、水温、金属材料、水质等因素影响。
尤其是在高温高压条件下,氧化皮更容易产生和生长。
此外,由于水中掺杂有各种离子,如钙、镁、铁、铜等金属及其离子、硫酸盐、碳酸盐等化合物,在高温高压条件下,它们会沉积在锅炉内壁上,形成污垢和沉淀物,这也会引起氧化皮的生长。
二、氧化皮的危害1. 减小了热传递效率氧化皮的存在减小了锅炉的热传递效率。
经过氧化皮的内壁,热量需要穿过氧化层才能传递到水中,传热效率受到限制。
2. 降低了金属材料的强度氧化皮的形成不仅仅是一层膜,它还会继续生长,加速金属材料的老化、腐蚀和疲劳。
氧化皮层会加速金属材料的脆化、裂纹产生,降低材料强度,从而破坏锅炉的安全性能。
3. 影响水质氧化皮的流失和脱落会使得锅炉进口水中含氧量、金属杂质离子等因素发生变化,从而影响锅炉的水质的稳定性。
水质的不稳定对锅炉正常运行产生了负面影响,增加了锅炉的故障率和维护成本。
三、氧化皮的防治措施为了防止氧化皮的产生,需要对锅炉水质进行严格管理,排除水中氧气、二氧化碳等成分,同时要控制锅炉温度和压力,以减缓氧化皮的生成速度。
对于已经形成的氧化皮,需要定期进行清除和维护。
一般直接清除氧化皮是不可行的,需要了解氧化皮的性质和生长情况,采取适当的去氧化皮措施。
1. 喷水清洗法在锅炉运行时,通过器具喷洒水,实现对氧化皮的清洗。
但是,由于清洗时锅炉需要停机,影响发电量;此外,喷洒水会使得钢材的运动钝化层被冲掉,从而加速钢材的腐蚀速度。
防止超超临界锅炉受热面氧化皮生成和脱落的控制措施

玉环电厂编号:YXB-GL-017-2011 签发:张峰审核:张志挺承办:邵海波防止锅炉受热面氧化皮生成和脱落的控制措施我厂#1-4锅炉屏式过热器、高温过热器和高温再热器炉内受热面管材为TP347H、SUP304H、HR3C奥氏体不锈钢,机组长周期运行后炉管内壁高温氧化皮加厚是不可避免的,如管壁超温,则氧化皮的生成呈现加速趋势。
由于高温氧化皮与基体有着不同的热膨胀系数,在机组长周期运行后的停运过程中,若炉管温降过快,可能会出现大量氧化皮脱落的现象,锅炉再次启动时易堵塞爆管。
为防止氧化皮大量脱落堆积造成锅炉爆管,提高机组的安全经济性,特制定本措施。
一、正常运行:1.1 运行中严格按照主再热汽温定值(锅炉出口主汽温600℃、再热汽温603℃)控制,锅炉出口主汽温度超过605℃、再热汽温超过608℃或屏式过热器出口蒸汽温度超过550℃视为超温。
1.2 运行中加强各受热面的热偏差监视和调整,使锅炉运行中过热器出口蒸汽温度左右侧偏差不超过5℃,屏式过热器出口蒸汽温度左右偏差不超过10℃,再热器出口蒸汽温度左右侧偏差不超过10℃。
1.3 机组运行中正常升、降负荷时控制负荷变化速率不超过15MW/min,注意监视主汽温、再热汽温、屏式过热器出口汽温不超过1.1条中规定的温度,并注意监视屏式过热器进出口、高温过热器进出口、高温再热器进出口的汽温变化率不超过2℃/min,如由于升降负荷的扰动造成上述温度的变化率超过2℃/min或主、再热汽温和屏式过热器出口汽温超过1.1条中规定的温度,则要适当降低机组的升、降负荷速率或暂停升降负荷,待温度调整稳定后继续进行负荷变动操作。
1.4 严格控制屏式过热器、高温过热器和高温再热器各管壁温度不超限,受热面蒸汽温度的控制要服从金属温度要求,发现有任一点壁温超过限额时应降低蒸汽温度运行,待原因查明处理正常和各管壁金属温度均不超限后再恢复正常汽温运行。
(部件壁温报警温度、监视温度上限及材料极限温度见附件)1.5 正常运行中过热器一、二、三级减温水和再热器烟气挡板应处于可调整的中间位置,再热器事故减温水应处于良好的备用状态,防止炉膛热负荷扰动时受热面超温。
超超临界锅炉高温受热面氧化皮脱落与治理

超超临界锅炉高温受热面氧化皮脱落与治理超超临界锅炉是一种高效、节能的发电设备,其受热面为高温区域,容易产生氧化皮脱落问题。
本文将探讨超超临界锅炉高温受热面氧化皮脱落的原因以及治理方法。
超超临界锅炉受热面氧化皮脱落的主要原因有两个方面:材料的选择和操作过程中的问题。
材料的选择是影响氧化皮脱落的主要因素之一。
超超临界锅炉使用的高温受热面材料需要具备耐高温、抗氧化等特点。
由于材料的局限性,可能存在一定的脆性和不稳定性,随着时间的推移,会出现氧化皮的产生和脱落。
在操作过程中,超超临界锅炉的高温受热面通常处于高温高压环境下,蒸汽中含有一定的氧气和水蒸气,这些因素都会加速氧化皮形成和脱落。
针对超超临界锅炉受热面氧化皮脱落的问题,可以采取以下治理措施:材料的选择十分重要。
在超超临界锅炉的设计阶段,需要选择耐高温、抗氧化的受热面材料。
合理的材料选型可以降低氧化皮的产生和脱落的风险。
在操作过程中要加强对超超临界锅炉高温受热面的维护和保养。
定期进行清洗和检查,及时发现和处理氧化皮问题。
清洗操作应当谨慎,避免使用过于剧烈的清洗剂,以免损坏受热面材料。
控制锅炉运行参数也是一个重要的治理方法。
调整锅炉的运行参数可以改变高温受热面的工况条件,减少氧化皮的产生。
降低蒸汽中的氧气和水蒸气的含量,可以减少氧化皮的形成和脱落。
超超临界锅炉高温受热面氧化皮脱落是一个影响锅炉运行稳定性和性能的问题。
合理选择材料、定期清洗检查以及控制运行参数等治理方法可以有效解决这一问题,保障锅炉的安全稳定运行。
超超临界锅炉高温受热面氧化皮脱落与治理

超超临界锅炉高温受热面氧化皮脱落与治理超超临界锅炉是一种高效、节能的燃煤锅炉,其受热面温度高达700摄氏度以上,因此受热面氧化皮脱落是其常见问题之一。
这种问题不仅影响了锅炉的正常工作,还可能对环境造成污染,因此需要有效的治理措施。
超超临界锅炉高温受热面氧化皮脱落的原因主要包括以下几点:一、受热面温度高,焚烧介质中含有一定的硫、氧等元素,在高温条件下易发生氧化反应,导致氧化皮的脱落。
二、锅炉内部高温高压环境容易造成材料疲劳和腐蚀,进而导致受热面氧化皮的产生和脱落。
三、煤种的选择和燃烧稳定性等因素也会影响受热面氧化皮的生成和脱落。
受热面氧化皮脱落的问题一旦发生,将直接影响超超临界锅炉的运行效率和安全性。
对于受热面氧化皮的治理十分重要。
下面将从预防和治理两方面进行详细介绍。
预防措施:1、选择合适的材料。
在设计和选材的过程中,需要考虑锅炉的工作温度、压力等因素,选择耐高温、耐腐蚀的材料,以减少氧化皮的生成和脱落。
2、燃料的选择和燃烧的稳定性。
选择低硫、低灰分的煤种,并保持良好的燃烧条件,避免煤灰中的硫等元素过量进入受热面,减少氧化皮的产生。
3、加强设备维护和保养,及时清理受热面。
定期对受热面进行清洗和检查,及时发现和处理氧化皮的问题,避免其脱落导致其他问题的发生。
治理措施:1、采取有效的防脱固化措施。
使用化学品对受热面进行浸渍或涂覆处理,形成一层坚固的覆盖层,防止氧化皮脱落。
2、采取表面处理技术。
利用喷涂、镀覆等技术对受热面进行表面处理,提高其抗氧化性和耐磨性,延长受热面的使用寿命。
3、优化燃烧控制。
通过优化燃烧系统和控制设备,减少煤灰中的有害元素进入受热面,降低氧化皮的产生。
超超临界锅炉高温受热面氧化皮脱落是一个需要重视和解决的问题。
预防和治理措施需要多方面合力,包括材料选用、燃料选择、设备维护、化学处理等方面,才能有效地延长受热面的使用寿命,保证锅炉的安全稳定运行。
希望借助技术的不断发展和进步,能够找到更加有效的预防和治理方法,为超超临界锅炉的运行提供更多的保障。
350MW超临界机组防止氧化皮生成及脱落技术措施

350MW超临界机组防止氧化皮生成及脱落技术措施在高温高压下,过、再热器管壁内表面容易产生氧化皮,在锅炉启停和快速变工况过程中往往会导致氧化皮脱落,造成部分受热面管壁通流部分变小甚至堵塞,从而导致受热面冷却不足而局部超温,进而导致锅炉爆管、蠕胀事故的发生。
为防止锅炉氧化皮脱落导致锅炉爆管、蠕胀等异常事故的发生,保证锅炉安全稳定运行,特制定措施如下:一、机组启动过程控制措施1.水质要求:1)锅炉上水水质标准:Fe<50μg/L,硬度≈0μmol/L,SiO2<30μg/L,PH值9.2~9.6。
2)冷态冲洗结束时锅炉点火水质标准:贮水箱排水中铁量<100μg/l,硬度≈0μmol/L,SiO2≤10μg/L,PH值9.2~9.6。
3)汽水分离器压力0.5MPa以上,分离器出口蒸汽温度190℃左右时,进行锅炉热态冲洗。
热态冲洗结束标准:贮水箱排水中含铁量<50μg/l。
2.锅炉上水温度及速度要求:1)在具备条件时,应提前投入除氧器加热,尽可能保持较高给水温度。
2)冷态上水温度控制在20~70℃,且高于水冷壁外壁温20~40℃。
3)冬季上水时间不小于4小时,夏季不小于2小时,上水速度控制在30-55t/h。
3.升温升压要求:4.锅炉点火至过、再热器建立蒸汽流量前,严格控制炉膛出口烟温<538℃。
5.高、低压旁路的控制:1)锅炉点火后,高压旁路控制不小于30%开度,低旁控制在不小于50%开度;主汽压力升至1MPa时,高压旁路随着主汽压力逐渐开至不小于60%,低旁开至80-100%。
2)汽机冲转前可通过尽可能开大高低旁开度(保证低旁减温器后温度≤60℃)对锅炉受热面系统进行大流量低压冲洗,以将沉积的氧化皮冲走。
6.减温水控制:1)当主、再热汽温大于360℃,投入过、再热器减温水控制汽温平缓。
投入减温水后,要注意喷水后汽温的变化,禁止减温水出现突增突减现象。
2)过热器减温水控制要以一级减温为主,二级减温为辅。
超临界机组电站锅炉氧化皮脱落的分析与防治

超临界机组电站锅炉氧化皮脱落的分析与防治超临界机组电站锅炉是一种高效、能耗低、环保的发电设备。
因其具有反应速度快、效率高等优点,对火电站的发电效率和环保指标有着极高的要求。
然而,锅炉在使用过程中容易发生氧化皮脱落现象,严重影响锅炉使用效率,甚至对环境造成污染。
因此,及时发现氧化皮脱落现象并采取相应措施进行防治十分重要。
一、氧化皮脱落的原因超临界机组电站锅炉氧化皮脱落的原因主要有两个方面:一是炉内高温氧化反应引起管子的氧化皮层剥落,二是炉内的化学成分沉积在管子表面形成氧化皮层,然后因管子受高温加热而脱落。
氧化皮脱落是一种自然现象,但是其对锅炉的影响却十分严重。
在高温高压下,氧化皮脱落会进入锅炉内部,造成如下问题:1. 浪费能源。
氧化皮脱落会降低锅炉的传热效率,使得发电效率降低。
2. 加速设备的磨损。
氧化皮脱落沉积在设备内部,会增加设备部件的摩擦,进一步加剧设备的磨损。
3. 污染环境。
氧化皮脱落后的残留物质可以堵塞排放口,导致烟气排放不畅,从而造成环境污染。
二、氧化皮脱落的检查和分析方法如何及时发现锅炉内的氧化皮脱落现象是防治氧化皮脱落的关键。
下面介绍一些基本的检查和分析方法:1. 外观检查通过外观检查可以初步了解锅炉的整体情况。
对于氧化皮脱落现象,可以通过裸眼观察锅炉的内外表面是否存在锈蚀、变形、裂纹等异常情况来初步判断锅炉是否存在氧化皮脱落现象。
2. 金属变色法利用金属变色法可以检测锅炉内部的炉膛、水侧等处是否有氧化皮脱落现象。
具体方法是在锅炉内部喷洒变色剂,通过观察变色情况来判断锅炉内部是否有氧化皮脱落。
3. 声学检测法通过声学检测可以探测锅炉内部存在的氧化皮脱落现象。
通过震动信号采集设备对锅炉内部进行扫描,可以通过对信号的反应判断锅炉内部存在的氧化皮脱落情况。
1. 定期清洗定期清洗锅炉内部是防止氧化皮脱落的重要措施。
通过清洗可以去除锅炉内部残留的颗粒物和化学物质,有效遏制氧化皮脱落的发生。
2. 防腐蚀防止锅炉内部产生复杂的化学反应也是防止氧化皮脱落的重要手段。
超临界机组电站锅炉氧化皮脱落的分析与防治

超临界机组电站锅炉氧化皮脱落的分析与防治超临界机组电站锅炉是燃煤发电厂中常见的一种发电设备,它具有高效、节能、环保等特点。
随着锅炉运行时间的逐渐增加,锅炉内壁会产生氧化皮,导致锅炉性能下降,甚至出现严重的安全隐患。
对于超临界机组电站锅炉氧化皮脱落的分析与防治显得十分重要。
1.高温腐蚀。
在高温高压环境下,煤燃烧引发的高温烟气中含有大量酸性物质,这些酸性物质会对锅炉内壁材料进行腐蚀,导致氧化皮的产生。
2.焚烧煤灰成分。
煤燃烧所产生的煤灰中含有硫、氯等元素,这些元素会与高温下的水蒸汽和氧气发生化学反应,产生腐蚀性气体,加剧了氧化皮的形成。
3.操作和管理不当。
锅炉的操作和管理不当会导致煤燃烧不充分,烟气温度不稳定等问题,从而加速了氧化皮的产生。
以上原因导致锅炉内壁的氧化皮逐渐增多,一旦氧化皮脱落,将会造成锅炉运行不稳定、热效率下降、甚至引发爆炸等严重后果。
1.优化燃烧控制。
做好燃煤燃烧时的控制,保证燃烧充分,减少燃煤产生的有害气体和煤灰,降低氧化皮的产生。
2.改善烟气排放系统。
合理设计和优化烟气排放系统,加强烟气的洁净处理,减少对锅炉内壁的腐蚀,延长锅炉寿命。
3.定期清洗维护。
定期对锅炉进行清洗维护,及时清除氧化皮,保持锅炉内壁的清洁,减少氧化皮脱落的风险。
4.采用防腐涂层。
在锅炉内壁采用防腐涂层,有效隔离锅炉内壁和腐蚀性气体的直接接触,减缓氧化皮的产生。
5.加强运行监测。
建立健全的锅炉运行监测系统,对锅炉的运行情况进行实时监测和分析,及时发现问题并采取相应的措施。
通过以上一系列的防治措施,可以有效降低超临界机组电站锅炉氧化皮脱落的风险,保证锅炉的安全稳定运行,提高锅炉的经济效益和环保水平。
三、结语超临界机组电站锅炉氧化皮脱落问题是影响锅炉运行的重要因素之一,必须引起足够的重视。
只有通过对氧化皮脱落的原因进行深入分析,并采取相应的防治措施,才能保证锅炉的安全稳定运行。
锅炉制造商、运营商和监管部门也应积极合作,共同推进锅炉氧化皮脱落问题的解决,为我国燃煤发电行业的可持续发展贡献力量。
超超临界锅炉高温受热面氧化皮脱落与治理

超超临界锅炉高温受热面氧化皮脱落与治理超超临界锅炉是目前一种比较先进的高效率、低排放的燃煤锅炉,其超高的锅炉出口蒸汽参数和大容量的燃烧室使得其燃烧效率和热效率都得到了显著提高。
然而,随着使用时间的累积和高温受热面的氧化,锅炉壁面会出现大量氧化皮脱落和积灰,进而影响锅炉的正常运行和安全性。
本文将就超超临界锅炉高温受热面氧化皮脱落现象及其治理进行分析探讨。
一、氧化皮脱落的原因超超临界锅炉受热面高温区域由于受到长期的高温高压水蒸气冲击和化学腐蚀,锅炉钢材表面开始氧化,并产生了一层厚度不一的氧化皮。
因为氧化皮对钢材的防护,所以锅炉设计中一般会在钢材表面添加一些抗氧化剂以减缓氧化速度。
然而,氧化皮会因为多种原因导致脱落,造成大面积的积灰和氧化皮。
主要的原因如下:1. 过高温度。
在超超临界锅炉运行过程中,因为发电效率等多种因素诱导,高温区域的温度经常会在合理范围内趋近上限值。
一旦超出温度极限,就会加速钢材表面氧化皮的形成,过厚氧化皮会导致它出现不均匀热膨胀和层状剥落。
2. 渣侵蚀。
烟气中存在的氧化物和酸性气体与高温区域耐火材料形成化学反应,生成的氧化物和硫化物形成强酸或强碱物,并会带着高温颗粒物和水汽冲刷耐火材料表面,在锅炉受热面形成厚度不一的皮脱落,极大影响锅炉的运行寿命。
3. 振动冲击。
锅炉受热面由于烟气流动、煤渣灰渣清理等原因,会受到外界的振动冲击,这会使得钢材表面氧化皮的附着性下降,皮层出现脱落现象。
4. 设计不合理。
锅炉的结构设计和施工质量等因素也会导致氧化皮脱落。
比如,锅炉管孔的装配工艺不良或者管板结构设计不当,都可能会导致高温受热面氧化皮层脱落或掉块。
二、治理方法1. 坚持设备日常保养。
对于高温受热面,要定期检查消除可能引起氧化皮脱落的因素,比如恰当设置高温应力降,完善联机检修程序等设备保养工作。
2. 清洗积灰和氧化皮。
清洗装置对于积灰和氧化皮的清洗都能够起到改善设备环境、缩短停台时间、提高操作效率的作用。
660MW超临界机组防止受热面氧化皮脱落技术措施
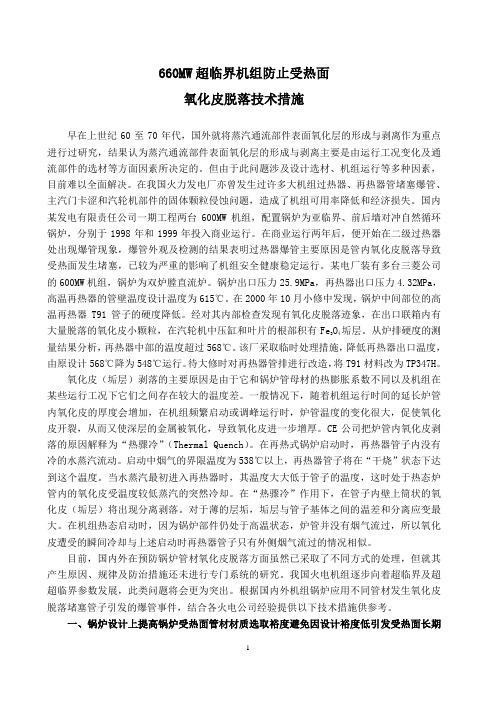
660MW超临界机组防止受热面氧化皮脱落技术措施早在上世纪60至70年代,国外就将蒸汽通流部件表面氧化层的形成与剥离作为重点进行过研究,结果认为蒸汽通流部件表面氧化层的形成与剥离主要是由运行工况变化及通流部件的选材等方面因素所决定的。
但由于此问题涉及设计选材、机组运行等多种因素,目前难以全面解决。
在我国火力发电厂亦曾发生过许多大机组过热器、再热器管堵塞爆管、主汽门卡涩和汽轮机部件的固体颗粒侵蚀问题,造成了机组可用率降低和经济损失。
国内某发电有限责任公司一期工程两台600MW机组,配置锅炉为亚临界、前后墙对冲自然循环锅炉,分别于1998年和1999年投入商业运行。
在商业运行两年后,便开始在二级过热器处出现爆管现象,爆管外观及检测的结果表明过热器爆管主要原因是管内氧化皮脱落导致受热面发生堵塞,已较为严重的影响了机组安全健康稳定运行。
某电厂装有多台三菱公司的600MW机组,锅炉为双炉膛直流炉。
锅炉出口压力25.9MPa,再热器出口压力4.32MPa,高温再热器的管壁温度设计温度为615℃。
在2000年10月小修中发现,锅炉中间部位的高温再热器T91管子的硬度降低。
经对其内部检查发现有氧化皮脱落迹象,在出口联箱内有大量脱落的氧化皮小颗粒,在汽轮机中压缸和叶片的根部积有Fe3O4垢层。
从炉排硬度的测量结果分析,再热器中部的温度超过568℃。
该厂采取临时处理措施,降低再热器出口温度,由原设计568℃降为548℃运行。
待大修时对再热器管排进行改造,将T91材料改为TP347H。
氧化皮(垢层)剥落的主要原因是由于它和锅炉管母材的热膨胀系数不同以及机组在某些运行工况下它们之间存在较大的温度差。
一般情况下,随着机组运行时间的延长炉管内氧化皮的厚度会增加,在机组频繁启动或调峰运行时,炉管温度的变化很大,促使氧化皮开裂,从而又使深层的金属被氧化,导致氧化皮进一步增厚。
CE公司把炉管内氧化皮剥落的原因解释为“热骤冷”(Thermal Quench)。
超超临界锅炉高温受热面氧化皮脱落与治理

超超临界锅炉高温受热面氧化皮脱落与治理超超临界锅炉是目前燃煤发电设备中最先进的一种锅炉,其工作效率高、能源利用率高、污染排放低等优点使得其在发电行业得到了广泛应用。
随着设备运行时间的增长,超超临界锅炉高温受热面氧化皮脱落问题逐渐凸显出来,这严重影响了设备的安全性和经济性。
本文将探讨超超临界锅炉高温受热面氧化皮脱落的原因及治理措施。
一、问题分析1. 高温受热面氧化皮脱落的原因超超临界锅炉高温受热面主要由炉墙、炉顶和炉膛组成。
这些受热面在长时间高温、高压、高湿环境下容易产生氧化皮,且由于受热面受到高温烟气的冲击和流速变化,氧化皮容易脱落。
氧化皮脱落不仅会导致受热面温度升高,还会造成受热面的腐蚀和损坏,严重影响设备的使用寿命和安全性。
2. 影响氧化皮脱落会导致受热面的温度升高,增加炉膛内部的温度和烟气侧的温度,降低了锅炉的热效率,增加了设备的能耗成本。
氧化皮脱落会导致受热面的腐蚀和损坏,进一步危害设备的安全性和经济性。
二、治理措施1. 预防措施(1)优化燃烧系统采用先进的燃煤技术和燃烧控制系统,可以降低燃煤的氮氧化物含量和硫氧化物排放,减少受热面的腐蚀和氧化皮的生成。
(2)控制烟气流速通过优化锅炉设计和降低烟气流速,可以减缓烟气对受热面的冲击和损伤,减少氧化皮的产生和脱落。
(3)加强受热面保护采用先进的受热面材料和涂层技术,提高受热面的抗氧化和抗腐蚀性能,延长受热面的使用寿命。
2. 治理措施(1)清理氧化皮定期对受热面进行清洗和除锈,清除氧化皮和积灰,恢复受热面的热传导和散热性能,提高锅炉的热效率。
(3)监控系统建立完善的锅炉运行监控系统,及时分析监测受热面的温度、压力和氧化皮的脱落情况,预警和处理可能的问题,保证锅炉的安全和稳定运行。
三、结语超超临界锅炉高温受热面氧化皮脱落是一个严重影响设备安全性和经济性的问题,需要采取一系列预防措施和治理措施来解决。
通过优化燃烧系统、控制烟气流速、加强受热面保护和完善监控系统等措施,可以有效降低氧化皮脱落的风险,延长受热面的使用寿命,提高设备的安全性和经济性。
超(超)临界机组氧化皮生成、剥落机理与防治措施

超(超)临界机组氧化皮生成、剥落机理与防治措施锅炉水/蒸汽流通系统中氧化皮的生成、剥落与沉积主要集中在炉前高压给水系统、水冷壁、过热器、再热器、主汽调门中。
氧化皮的生成、剥落与沉积受温度、压力、蒸汽参数(密度、离子积、介电常数、PH、氢电导率、阴离子含量、比电导率、氧化还原电位)、蒸汽溶氧量、蒸汽含铁量、蒸汽铬酸根含量等多种参数共同控制。
在锅炉不同位置氧化皮的生成、剥落、沉积机理不同,炉前高压给水系统和水冷壁中的氧化皮的沉积主要是流动加速腐蚀所致。
再热器、过热器与主汽调门中的氧化皮形成、剥落与沉积机理更加复杂,总的来说控制蒸汽含铁量、控制蒸汽氧化还原电位、降低蒸汽溶氧量有助于减少氧化皮的形成、剥落与沉积。
图1 电厂系统图一、生成、剥落与沉积原理1.1、氧化皮在炉前和水冷壁中的生成、剥落与沉积机理碳钢在水中不稳定,有腐蚀倾向,只有在钢表面形成稳定的氧化膜后,才能保持稳定。
在不同温度条件下,氧化膜的形成机制不同,其微观结构也不同。
在较低温度条件下形成的磁性铁氧化膜是多孔、疏松的。
在较低温度下,氧化膜的形成分为3步:第一步:Fe的氧化和H+的还原:Fe→Fe2++2e-;2H++2e-→H2;总反应为:Fe+2H2O→Fe2++2(OH-)+H2 (1)第二步:Fe2+和2(OH-)极易发生反应生成Fe(OH)2;Fe2++2(OH-)→Fe(OH)2 (2)第三步:Fe(OH)2被氧化生成Fe3O4;3Fe(OH)2→Fe3O4+4H2O+H2↑由式(1)可见,在较低温度下,氧化膜的形成需要有一定量的铁离子和氢氧根。
钢表面上的铁离子是由腐蚀过程扩散至表面的,而氢氧根则与水的PH值有关。
磁性氧化铁的形成通常受形成和溶解2个反应动力学控制。
任何条件的变化导致此动力学状态改变时,都会影响磁性氧化铁的稳定。
扩散系数和介电常数等因素会综合影响碳钢的腐蚀速率。
图2 给水系统管道腐蚀控制因素根据温度和压力的不同,碳钢表面可以分3个区域:第1个区域是磁性氧化铁稳定区;第2个区域是磁性氧化铁溶解区;第3个区域是磁性氧化铁沉积区。
超临界机组电站锅炉氧化皮脱落的分析与防治
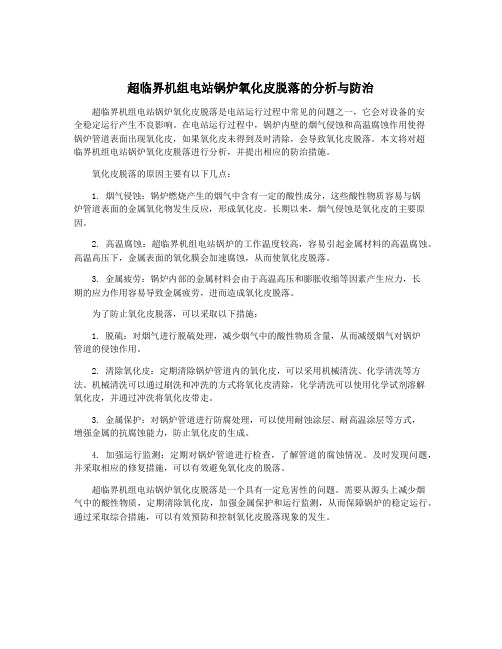
超临界机组电站锅炉氧化皮脱落的分析与防治超临界机组电站锅炉氧化皮脱落是电站运行过程中常见的问题之一,它会对设备的安全稳定运行产生不良影响。
在电站运行过程中,锅炉内壁的烟气侵蚀和高温腐蚀作用使得锅炉管道表面出现氧化皮,如果氧化皮未得到及时清除,会导致氧化皮脱落。
本文将对超临界机组电站锅炉氧化皮脱落进行分析,并提出相应的防治措施。
氧化皮脱落的原因主要有以下几点:1. 烟气侵蚀:锅炉燃烧产生的烟气中含有一定的酸性成分,这些酸性物质容易与锅炉管道表面的金属氧化物发生反应,形成氧化皮。
长期以来,烟气侵蚀是氧化皮的主要原因。
2. 高温腐蚀:超临界机组电站锅炉的工作温度较高,容易引起金属材料的高温腐蚀。
高温高压下,金属表面的氧化膜会加速腐蚀,从而使氧化皮脱落。
3. 金属疲劳:锅炉内部的金属材料会由于高温高压和膨胀收缩等因素产生应力,长期的应力作用容易导致金属疲劳,进而造成氧化皮脱落。
为了防止氧化皮脱落,可以采取以下措施:1. 脱硫:对烟气进行脱硫处理,减少烟气中的酸性物质含量,从而减缓烟气对锅炉管道的侵蚀作用。
2. 清除氧化皮:定期清除锅炉管道内的氧化皮,可以采用机械清洗、化学清洗等方法。
机械清洗可以通过刷洗和冲洗的方式将氧化皮清除,化学清洗可以使用化学试剂溶解氧化皮,并通过冲洗将氧化皮带走。
3. 金属保护:对锅炉管道进行防腐处理,可以使用耐蚀涂层、耐高温涂层等方式,增强金属的抗腐蚀能力,防止氧化皮的生成。
4. 加强运行监测:定期对锅炉管道进行检查,了解管道的腐蚀情况。
及时发现问题,并采取相应的修复措施,可以有效避免氧化皮的脱落。
超临界机组电站锅炉氧化皮脱落是一个具有一定危害性的问题。
需要从源头上减少烟气中的酸性物质,定期清除氧化皮,加强金属保护和运行监测,从而保障锅炉的稳定运行。
通过采取综合措施,可以有效预防和控制氧化皮脱落现象的发生。
超临界机组电站锅炉氧化皮脱落的分析与防治

超临界机组电站锅炉氧化皮脱落的分析与防治超临界机组电站锅炉是一种高效节能的发电设备,其锅炉部分承担着转化化石能源为电能的重要任务。
其中,锅炉的安全、稳定运行是保障发电厂运行的重要前提之一。
然而,在锅炉长期使用过程中,锅炉内部容易出现的一个问题就是氧化皮的脱落,这会引起一系列的连锁反应,对电站运行安全造成严重影响。
本文主要探讨超临界机组电站锅炉氧化皮脱落的原因、特征,以及如何有效的预防和治理这种现象。
一、氧化皮形成的原因锅炉的材质多是铁合金等金属材料,长期高温高压下,锅炉表面易出现氧化皮,这主要由以下原因导致:1、锅炉内部能量受限,产生较大热负荷,造成表面局部过热,从而发生氧化皮。
2、装置中存在一些缺陷,如气孔,层状缺陷,交界区缺陷等,加之局部应力集中,会使孔隙处易于产生氧化皮。
3、大气环境因素也是造成锅炉氧化皮的重要原因之一,腐蚀、污染等环境因素会大大加剧锅炉氧化皮的产生过程。
二、氧化皮脱落的特征锅炉内部存在有氧化皮,它会影响锅炉的安全性和运行效率,主要表现在以下几个方面:1、导致锅炉内部烟道堵塞,严重影响烟气排出和气流过程。
2、产生铁锈,使水质变劣。
3、降低了锅炉表面的光泽。
4、在烟囱周围形成污染物,使附近居民的生活和健康受到影响。
三、预防与治理措施为了预防和治理锅炉氧化皮脱落现象,超临界机组电站锅炉需要采取以下措施:1、加强锅炉表面的清洗和维护,防止氧化皮过度脱落。
2、有效避免锅炉起火的过程中产生过度的热负荷,一定程度上减少氧化皮的产生。
3、及时排放排污,保障锅炉内部水质的良好。
4、加强管理,设立专门的锅炉维护检测团队,对锅炉的状态进行全面的分析和检测,及时发现问题并解决。
综上,超临界机组电站锅炉氧化皮脱落问题需要有效防范和控制。
必须加强锅炉内部的管理和维护工作,严格按照标准要求,加强对氧化皮的清洗和护理。
同时也要加强锅炉的检测,及时解决锅炉内部存在的问题,确保超临界机组电站锅炉的运行安全、高效。
超临界机组电站锅炉氧化皮脱落的分析与防治

超临界机组电站锅炉氧化皮脱落的分析与防治超临界机组电站锅炉是目前发电行业中使用最为广泛的一种锅炉。
这种锅炉有着高效、节能、环保等优点,同时也有一些缺点,比如对水质要求高、管子受热容易脱落等问题。
其中,在使用过程中,锅炉内部可能产生氧化皮,这对锅炉的安全和稳定运行都会造成严重危害。
氧化皮的产生和脱落氧化皮是指金属表面由于氧化反应而产生的一层薄膜。
超临界锅炉中,锅炉管道在高压、高温下运行,内壁受热膨胀、冷缩,表面产生张应力和压应力,此时管道表面的氧化皮会随着这种应力变化而形成和分裂。
当应力超过氧化皮的强度时,氧化皮就会脱落。
这种脱落现象可能产生划伤、切割管道或喷射高速氧化皮的碎片,造成管路遭受撞击打击或者再次被烧损等情况。
氧化皮的危害和防治氧化皮的产生和脱落会给锅炉带来一系列的安全隐患和稳定性问题。
首先,氧化皮具有硬度较高、易剥脱、斑块较大等特点,这些特性尤其在制造过程中加工不当时易于形成,极易造成管道损伤和泄露事故。
同时,氧化皮脱落的碎片会携带一定能量、速度和射程,如果撞击到周边的管道或设备上,极易造成这些设备的故障和损坏。
有效措施为了有效防治超临界锅炉内氧化皮的产生和脱落,需要采取以下措施:1.严格控制水质:氧化皮的产生和脱落与水质、雾化水分造成的挥发物和含氧及其它因素有很大关系,所以加强水质控制,减少管道受损,对于防治氧化皮的产生和脱落具有重要意义。
2.加强检修:定期对锅炉进行检修,及时发现氧化皮及时清除,更换不良的管路元件,修复损坏的部位。
3.提高制造质量:超临界锅炉的制造过程中,需要加强质量管理,在金属成形、焊接、热处理、清洗等关键环节环节上加强控制品质,确保零件不出现明显质量问题。
4.改善运行条件:为了使锅炉在高效、节能、环保的同时避免氧化皮脱落问题的发生,还需要改善运行条件,优化锅炉的操作过程,保证锅炉的运行在一个稳定的状态下。
总之,超临界锅炉在使用过程中出现氧化皮的现象,必须给予高度重视。
- 1、下载文档前请自行甄别文档内容的完整性,平台不提供额外的编辑、内容补充、找答案等附加服务。
- 2、"仅部分预览"的文档,不可在线预览部分如存在完整性等问题,可反馈申请退款(可完整预览的文档不适用该条件!)。
- 3、如文档侵犯您的权益,请联系客服反馈,我们会尽快为您处理(人工客服工作时间:9:00-18:30)。
防止高温氧化皮脱落对机组造成危害的技术措施高温氧化皮是指金属与高温蒸汽中的氧发生氧化反应而生成的氧化物。
在我国高温氧化皮研究是在2000年以后正式被提上议程,随着超临界发电机组在国内的不断投产,防止高温氧化皮生成、脱落对机组安全运行造成的危害越来越被重视。
一、高温氧化皮的特性
1、高温氧化皮生成具有阶段性:高温蒸汽管道的氧化皮在560℃以下生成非常慢,在560℃~590℃之间生成较快,超过590℃~620℃之间生成速度很快(超临界机组设备厂家和运行规程规定,锅炉主汽温度禁止超过590℃,一是考虑金属应力变形,二是考虑氧化皮问题),620℃以上又呈下降趋势。
也就是说高温氧化皮生成具有阶段性。
以前125MW机组、200MW 及300MW强制循环机组,由于温度不超过560℃,很少考虑氧化皮问题。
2、高温氧化皮随着机组连续运行时间延长厚度会逐渐增加,达到一定厚度会脱落,特别是在温度突变时,脱落速度会加快且成片脱落。
3、高温氧化皮开始生成速度较快,当形成氧化膜层后,生成速度逐渐减缓。
4、不同钢材抗氧化皮性能所有不同。
二、氧化皮脱落的危害及处理
1、机组连续运行时间越长,氧化皮层越厚,氧化皮脱落的可能性越大;温度反复突变,氧化皮越容易脱落。
运行中氧化皮脱落,对汽轮机喷嘴、阀芯、叶片等部件产生冲击,容易损坏汽机部件。
锅炉停炉及点火过程中,由于管道没有蒸汽流动或蒸汽量很小,脱落的氧化皮就会沉积在管道的下部或联箱的底部,容易造成部分管道的流通面积减小,在机组并网后锅炉燃料增加,烟温逐渐升高,部分流通面减小的过热器管因得不到蒸汽的充分冷却,就会超温,金属的分子结构发生改变,强度下降最后爆管。
2、防止氧化皮大面积快速脱落,一是保持温度升降平稳,避免大起大落,也就是在正常运行调整中,避免给水量大幅变化、减温水阀门突开突关;二是机组连续运行一段时间后(一般为2200小时),采用降温降压大流量冲刷一次,使已形成一定厚度但量不是太大的氧化皮脱落,随着蒸汽带走。
这里所说的降温降压大流量冲洗,是指汽机调门全开,主汽和再热汽温度降至520℃,维持85%左右额定负荷运行4~6个小时。
为什么选择这样的参数,原因如下:一、这样的参数,锅炉已达额定蒸汽量即大流量;二、降温降压的目的是增大蒸汽流量,提高锅炉管道蒸汽的流速,增强冲洗效果;三、汽机调门全开目的是降低进入汽轮机叶片等设备的流速,减少蒸汽携带的固态氧化皮对设备的冲击而可能造成的损害;四、主汽温度选
择520℃是为保证汽轮机末级叶片不受蒸气湿度的侵害,同时考虑氧化皮不致快速脱落而伤害汽轮机叶片;五、4~6个小时,考虑金属缓慢降至520℃,主蒸汽管道和再热蒸汽管道的内外壁由于冷却不同步及氧化皮大部分脱落所需要的大概时间。
(由于#2机组主气门临时滤网未拆,为防止氧化皮堵塞滤网,当前阶段正常运行时暂不执行大流量冲洗)
3、处置沉积在锅炉过热器和再热器管道中的氧化皮的常用方法。
①氧化皮严重一般是请专业清洗公司在机组大修中进行酸洗,此法效果明显,但成本高、工作量大、耗用时间较长,环境污染较大,虽然酸洗的废液可以排入渣灰系统中和部分废液但不可能完全反应。
②进行反吹扫,有的锅炉在过热器和再热器联箱上预留接口,可以用压缩空气或临炉的蒸汽通过接口进行反向吹扫,通过疏水、361阀和水冷壁放水排除氧化皮。
③水冲洗,从减温器向过热器进水,通过疏水、361阀和水冷壁放水排除氧化皮。
④停炉前吹扫,停机不停炉,利用汽机高低压旁路升压减压进行吹扫,可以除去部分氧化皮。
⑤冲转前冲洗,机组停运后金属冷却收缩,管道内的氧化皮会大量脱落沉积在过热器管道内,加之停炉保护不当,管道内又会发生低温腐蚀铁锈,锅炉点火升温升压过程中,金属膨胀,又有部分氧化皮脱落,很容易造成管道堵塞,当炉膛温度达到一定程度时,管子就会超温,如继续升负荷,管道就会超温爆管。
所以氧化皮堵塞爆管一般都在机组并网后的1~2日内发生。
因此冲转前进行冲管是清除沉积氧化皮,防止管道爆破的有效而简单的方法。
此方法就是把汽温升至410℃~~420℃,压力升至6.5MPa左右,然后全开汽机高低压旁路迅速降压至4MPa左右,反复多次,对蒸汽管道进行快速降压冲洗,以冲走管道中沉积的氧化皮和冲管时压力突变而脱落的氧化皮。
从而确保机组不因氧化皮脱落堵塞过热器、再热器管道所引发的爆管事故。
三、正常运行时控制氧化皮生成速度及防止集聚脱落的具体措施
1.机组正常运行中加强对受热面的热偏差监视和调整,严格控制受热面蒸汽温度和金属温
度,任何情况下严禁锅炉超温运行。
2.锅炉正常运行时,主、再热蒸汽温度必须控制在设备厂家及运行规程规定的范围内。
两
侧温差不超过10℃,发现异常及时处理,为减缓氧化皮的生成速度,主汽温度现暂维持在550℃~560℃之间运行。
3.正常运行时,为防止屏式过热器超温,应严格控制屏过出口汽温不大于540℃。
4.正常运行时屏过出口管壁温度小于580℃,末级过热器、再热器出口管壁温度小于605℃。
报警值降低10~20℃
5.运行期间主蒸汽温度调整以水煤比作为主要调整手段,辅以减温水和风量调整。
再热蒸
汽以烟气挡板调整为主,尽量减少减温水使用量。
6.正常运行时,在调整减温水过程中要根据汽温偏离的大小及减温器后温度变化趋势进行
调整,减温水调门操作要缓慢,防止出现减温水调门大幅开关。
正常情况下减温水调整门开度每次调整幅度不超过10%,如需再次调整,则要间隔1~2分钟左右。
一级减温器后温度变化速率不超过4℃/min,幅值不大于12℃,二级减温器后温度变化速率不大于3℃/min,幅值不超过9℃,过热器出口温度变化速率不大于2℃/min,幅值不超过6℃。
机组在正常运行中一级减温器后温度必须高于饱和温度10℃以上,二级减温器出口温度必须高于饱和温度20℃;再热蒸汽事故减温器后出口温度必须高于饱和温度20℃,防止再热器U型管下部积水。
7.负荷≤80MW时,尽量避免使用过热器二级减温水和再热器减温水,如确需使用减温水,
务必间断、小幅投入,不得连续、大开大关减温水调节门,具体限值参照第6条正常运行时的规定。
8.在蒸汽温度调整过程中要加强受热面金属温度监视,蒸汽温度的调整要以金属温度不超
限为前提,金属温度超限必须适当降低蒸汽温度或降低机组负荷并查找原因进行处理。
9.机组负荷300MW以上时升降负荷速率不超过5MW/min,负荷小于300MW时升降速率不超
过3MW/min,当前升降负荷应按照《#2机CCS方式下负荷升降及定滑压运行方案》执行。
10.锅炉燃烧调整以压力偏置,水煤比偏置,升降负荷速率协同控制。
11.锅炉运行中在进行负荷调整、启、停制粉系统、投停气枪、炉膛或烟道吹灰等操作以及
煤质发生变化时都将对蒸汽系统产生扰动,在上述情况下要特别注意蒸汽温度和壁温的监视和煤水比调整。
12.当机组负荷较高,烟温超过680℃时且有管壁超温现象,应及时投入炉膛吹灰,同时通
过开大燃烬风门,减小上层磨煤量、增大水煤比、增加下层磨煤量,适当减小风量的方法控制管壁温度,通过以上操作,管壁温度仍超温,应立即汇报项目部和业主领导,采用降低负荷,调整磨煤机运行方式或降低给水温度等方法进行处理并组织分析,找出原因,采取对策。
13.严格执行锅炉炉本体吹灰规定,确保各受热面清洁,减少热偏差。